Физикохимия поверхности и защита материалов, 2020, T. 56, № 6, стр. 667-672
Износостойкие и антикоррозионные покрытия на основе карбида хрома Cr7C3, полученные электроискровым осаждением
А. А. Бурков 1, *, М. А. Кулик 1
1 Институт материаловедения Хабаровского НЦ Дальневосточного отделения Российской академии наук
680042 Хабаровск, Тихоокеанская, 153, Россия
* E-mail: burkovalex@mail.ru
Поступила в редакцию 02.09.2019
После доработки 19.09.2019
Принята к публикации 26.09.2020
Аннотация
Работа посвящена нанесению порошка карбида хрома Cr3C2 на сталь 35 электроискровой обработкой в среде титановых гранул. Было приготовлено три смеси гранул с содержанием порошка Cr3C2 от 7.4 до 15.6 об. %. Рентгенофазовый анализ покрытий показал преобладание фазы Cr7C3, которая является продуктом декарбидизации карбида хрома Cr3C2 при его взаимодействии с железом подложки. С ростом содержания порошка в смеси гранул повышалась микротвердость покрытий от 8.2 до 9.8 ГПа. Средний коэффициент трения покрытий находились в диапазоне от 0.42 до 0.68. Износостойкость покрытий в режиме сухого износа была от 20 до 57 раз выше, чем у стали 35. Поляризационные испытания покрытий в 3.5% растворе NaCl показали значительно более низкий потенциал и ток коррозии, и более высокое сопротивление поляризации по сравнению со сталью 35. Изучение жаростойкости при температуре 700°С показало, что применение покрытий на стали 35 повышает стойкость ее поверхности к высокотемпературной газовой коррозии в 14–18 раз за 100 часов испытаний. Проведенные испытания показали, что оптимальное содержание порошка Cr3C2 в смеси с гранулами находится в интервале 11.7―15.6 об. %.
1. ВВЕДЕНИЕ
Инженерия поверхности является одним из наиболее эффективных путей улучшения коррозионных и триботехнических свойств материалов. В последнее десятилетие наиболее распространенными методами нанесения покрытий являются физическое осаждение в паровой фазе, газопламенное напыление, лазерная наплавка и электроискровое легирование (ЭИЛ) [1–5]. Преимуществами лазерной наплавки и ЭИЛ являются высокая плотность энергии, снижающая размер зоны термического влияния на материал основы и высокая адгезия покрытия к подложке по сравнению с методами термического напыления [6–8]. Отличительной особенностью технологии ЭИЛ является простота, компактность, низкая стоимость оборудования и возможность нанесения покрытий на любые токопроводящие материалы без особых требований к подготовке поверхности. При ЭИЛ материал анода подвергается электрической эрозии в условиях воздействия электрических разрядов, переносится на катод, перемешивается и образует покрытие, металлургически связанное с подложкой [9, 10]. В последнее время проводится много исследований по развитию электроискрового технологии нанесения покрытий. Так в работе [11] предложена программно-аппаратная компоновка фрезерного станка и электроискровой установки, c целью автоматизации ЭИЛ при обработке криволинейной поверхности. Кроме того, разрабатываются новые порошковые электродные материалы, применяются источники ультразвука [12], изучаются комбинации ЭИЛ обработки с лазерными [13], дуговыми и магнетронными источниками с целью улучшения качества покрытий [14, 15].
В качестве развития метода ЭИЛ нами была предложена методика электроискрового осаждения покрытий в среде гранул (ЭИЛГ) из осаждаемого материала, выполняющих функцию рабочего электрода-инструмента (анода) [16]. При этом, обрабатываемая деталь (катод) погружена в гранулы, и соответственно, покрытие формируется на всей ее поверхности контактирующей с гранулами одновременно. Данный подход позволяет автоматизировать процесс нанесения покрытий в т.ч. на подложки с криволинейной поверхностью. Кроме того, ЭИЛГ хорошо подходит для нанесения порошковых материалов в среде металлических гранул с целью получения металлокерамических покрытий [17], поскольку при традиционном ЭИЛ существуют ограничения по концентрации керамического компонента в покрытиях. Во-первых, это высокое электрическое сопротивление и низкая прочность электродных материалов с высокой объемной долей керамики, а во вторых неизбежное участие металла подложки в составе покрытия, где его доля может достигать 60 вес. %.
Особенность нанесения металлокерамических покрытий методом ЭИЛГ заключается в использовании керамического порошка (оксиды, карбиды, силициды металлов или чистых неметаллов и т.п.), который засыпается в реактор электроискровой установки вместе с металлическими гранулами. При прохождении разрядов между гранулами и подложкой происходит внедрение порошка в поверхность последней. Высокие температуры в области воздействия разряда обеспечивают плавление, конвективное и диффузионное перемешивание компонентов порошка, гранул и подложки и протекание сопутствующих химических взаимодействий.
Карбиды вольфрама и хрома являются наиболее распространенным материалом для металлокерамических покрытий, поскольку сочетают высокую твердость и износостойкость с уникальными окислительными свойствами, благодаря образованию плотной гомогенной оксидной пленки Cr2O3 [18]. В частности карбид хрома Cr7C3 известен сильной ковалентной атомной связью, высокой твердостью, и отличной стабильностью при высокой температуре, что делает его превосходным кандидатом в качестве армирующей фазы для износостойких композиционных покрытий [19]. Поэтому целью настоящей работы является изучение условий формирования и свойств покрытий на стали 35, полученных электроискровой обработкой в смеси титановых гранул с добавлением разного количества порошка карбида хрома Cr3C2. В качестве металлической связки будут выступать железо из подложки, титан, переносимый из гранул, и хром как продукт частичного обезуглероживания карбида хрома. Присутствие металлической связки Fe–Ti–Cr, призвано улучшить ударную вязкость покрытия.
2. МЕТОДИКА
Схема установки для осаждения покрытий в смеси гранул с порошком подробно описана в работе [17]. Порошок карбида хрома Cr3C2 (ТУ 6-09-03-10-75) имел средний размер частиц 8 мкм. Гранулы изготавливались путем нарезания титановой проволоки марки ВТ1-00 диаметром 4 ± 0.5 мм на кусочки длиной 4 ± 1 мм. Были приготовлены три смеси из гранул титанового сплава ВТ1-00 и порошка карбида хрома с содержанием последнего от 7.4 до 15.6 об. % (табл. 1). Гранулы и порошок засыпались в стальной контейнер установленный под углом 40° и соединенный с двигателем. Частота вращения контейнера с гранулами составляла 1 об с–1. Цилиндрическая подложка из стали 35, диаметром 12 мм и высотой 10 мм, размещалась в центре контейнера, и подключалась к отрицательному выводу генератора импульсов. Подложка также подсоединялась к двигателю для вращения с аналогичной контейнеру частотой, но в противоположном направлении. Положительный вывод генератора подсоединялся к стенкам контейнера. Генератор импульсов IMES-40 вырабатывал импульсы тока прямоугольной формы амплитудой 110 А при напряжении 30 В, длительностью (τ) 100 мкс с частотой 1000 Гц. В контейнер подавался защитный газ – аргон со скоростью 10 л мин–1 для предотвращения окисления и азотирования образцов.
Таблица 1.
Обозначение образцов и объемная доля порошка карбида хрома в смеси гранул
№ | Обозначение покрытий | Концентрация порошка Cr3C2, об. % |
---|---|---|
1 | C7 | 7.4 |
2 | C11 | 11.7 |
3 | C15 | 15.6 |
Фазовый состав и структура покрытий исследовались с применением рентгеновского дифрактометра ДРОН-7 в CuKα-излучении. Твердость покрытий измерялась на микротвердомере ПМТ-3М при нагрузке 0.5 Н по методу Виккерса. Износостойкость покрытий исследовались по стандарту ASTM G99 при сухом трении скольжения, с применением контртела в виде диска из быстрорежущей стали Р6М5 на скорости 0.47 мс–1 при нагрузках 25 и 70 Н. Было проведено не менее трех измерений для каждого образца. Износ измеряли гравиметрическим способом с точностью 0.1 мг и рассчитывали интенсивность изнашивания по формуле: W = ∆m/(ρPl), где ∆m – потеря массы образца при истирании; ρ – плотность покрытия, которая принималась равной плотности стали 35; P – нагрузка и l – длина пути трения. Образцы подвергались трению попеременно после каждого акта измерения массы для устранения погрешности, вводимой возможным изменением свойств поверхности контртела. Поляризационные испытания проводились в трехэлектродной ячейке, после 20, минутной выдержки образцов в 3.5%-ном растворе NaCl, с использованием потенциостата 8P-nano со скоростью сканирования 30 мВ с–1. Площадь образцов контактирующая с раствором электролита составляла 1 см2. Контр-электрод представлял собой платиновый электрод “ЭТП-02”, а электродом сравнения выступал стандартный хлорсеребряный электрод. Потенциал коррозии, а также плотность тока коррозии были извлечены с участков методом экстраполяции Тафеля. Испытания на жаростойкость проводили в печи при температуре 700°С. Общее время тестирования составляло 100 ч. Образцы выдерживали при заданной температуре в течение ~6 ч, затем удаляли и охлаждали в эксикаторе до комнатной температуры. Во время испытания образцы помещались в корундовый тигель для учета массы отслоившихся оксидов. Изменение массы всех образцов измеряли с использованием лабораторных весов с чувствительностью 0.1 мг.
3. РЕЗУЛЬТАТЫ И ИХ ОБСУЖДЕНИЕ
При осаждении покрытий в смеси титановых гранул и порошка Cr3C2 наблюдалось увеличение массы подложек в результате отложения материала из гранул и порошка на катод (рис. 1а). С увеличением времени обработки он замедлялся. Поэтому оптимальное время осаждения MG покрытий составило 8 мин. Привес подложек увеличивался с ростом содержания порошка в смеси с гранулами. Это свидетельствует о слабом переносе титана из гранул на стальную подложку и об активном участии порошка в формировании покрытий.
Рис. 1.
Кинетика привеса подложек в процессе электроискровой обработки в смеси титановых гранул с порошком Cr3C2 (а) и рентгеновские спектры полученных покрытий (б).
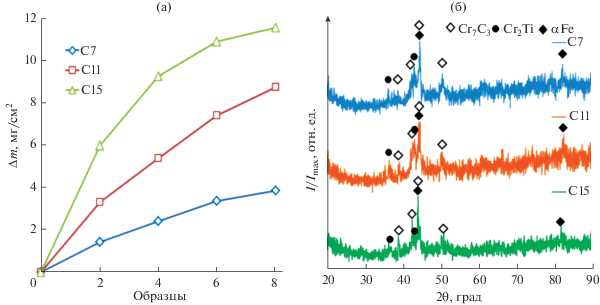
Рентгенофазовый анализ полученных покрытий показал, что в их составе преобладает карбид хрома Cr7C3 (рис. 1б). Помимо него были обнаружены αFe и интерметаллид Cr2Ti. Интенсивность рефлексов фазы Cr7C3 повышалась с увеличением доли карбида хрома в смеси гранул на фоне рефлексов остальных фаз. Формирование карбида Cr7С3 и интерметаллида Cr2Ti в процессе электроискровой обработки происходило в результате обезуглероживания Cr3C2 при его взаимодействии с железом, согласно реакциям (1) и (2), соответственно:
(1)
$7{\text{C}}{{{\text{r}}}_{3}}{{{\text{C}}}_{2}} + 15{\text{Fe}} = 3{\text{C}}{{{\text{r}}}_{7}}{{{\text{C}}}_{3}} + 5{\text{F}}{{{\text{e}}}_{3}}{\text{C,}}~$(2)
$2{\text{C}}{{{\text{r}}}_{3}}{{{\text{C}}}_{2}} + 12{\text{Fe}} + 3{\text{Ti}} = 3{\text{C}}{{{\text{r}}}_{2}}{\text{Ti}} + 4{\text{F}}{{{\text{e}}}_{3}}{\text{C}}{\text{.}}$Эти результаты согласуются с данными из литературных источников для подобных систем. Так в работе [20], где было сообщено о полном превращении Cr3C2 в Cr7C3 при лазерной наплавке порошковой смеси NiCr и Cr3C2 на нержавеющую сталь ASTM 0Cr18Ni9. К аналогичным результатам пришли в работе [21] было отмечено формирование Cr7C3 и TiC после лазерной наплавки порошковой смеси Cr3C2–50 вес. % NiCr на подложке TiAl, в то время как никаких признаков Cr3C2 не было обнаружено на рентгенограмме сформированного плакированного материала.
Средняя твердость покрытий возрастала от 8.2 до 9.8 ГПа с увеличением концентрации порошка Cr3C2 в смеси гранул (рис. 2). Это выше чем у стали 35 в 5–6 раз ГПа. Кинетика изменения коэффициента трения образцов при испытании на износ в режиме сухого скольжения при нагрузках 25 и 70 Н показана на рис. 3а. Средние значения коэффициента трения покрытий находились в диапазоне от 0.42 до 0.68, что на 25–50% ниже, чем у стали 35. Такое снижение коэффициента трения объясняется более высокой твердостью покрытий. Более того, в случае стали без покрытия наблюдался высокий уровень шума на кривых коэффициента трения. Шум объясняется периодическим отложением и отслоением переносимого между трущимися поверхностями материала. При обеих нагрузках, наиболее низкие значения коэффициента трения наблюдались у образца С11. Результаты испытания образцов на износостойкость показаны на рис. 3б. Из него следует, что скорость износа покрытий находилась в диапазоне 1.0–2.4 × 10–7 и 0.9–2.1 × 10–7 мм3/Нм при нагрузках 25 и 70 Н, соответственно. Наиболее низкие значения скорости износа показали покрытия С11 и С15 при обеих нагрузках. Скорость износа образцов была ниже, чем у стали 35 от 20 до 57 раз. Характерно, что при нагрузке 70 Н скорость износа снижалась при повышении концентрации Cr3C2 до 11.7 об. %, а сверх этого значения возросла почти двукратно. Вероятно, это вызвано снижением объема металлической связки в покрытии С15 и нарастающей хрупкостью в условиях трения под большей нагрузкой. Таким образом, оптимальная концентрация порошка карбида Cr3C2 в смеси гранул, при осаждении покрытий для триботехнических применений, находится в интервале от 11.7 до 15.6 об. %.
Рис. 3.
Коэффициент трения (а) и скорость износа (б) покрытий при нагрузках 25 и 70 Н по сравнению со сталью 35.
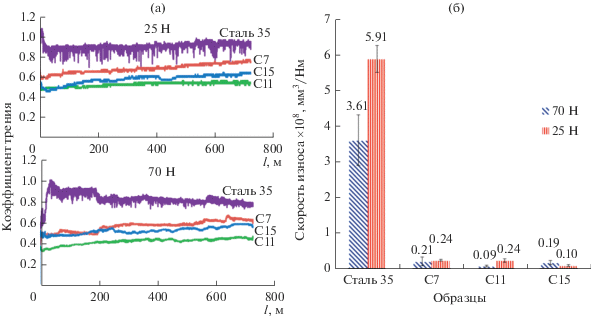
На рис. 4а показаны потенциодинамические поляризационные кривые покрытий и стали 35 в 3.5% растворе NaCl при комнатной температуре. На основе этих данных были рассчитаны ток коррозии Icorr, потенциал коррозии Ecorr и сопротивление поляризации Rp (табл. 2). Rp было рассчитано используя упрощенное выражение (3):
(3)
${{R}_{p}} = \frac{{{{b}_{a}}{{b}_{c}}}}{{2.303{{I}_{{{\text{corr}}}}}\left( {{{b}_{a}} + {{b}_{c}}} \right)}},$Рис. 4.
Тафелевские поляризационные спектры (а) и жаростойкость покрытий при температуре 700°С (б) по сравнению со сталью 35.
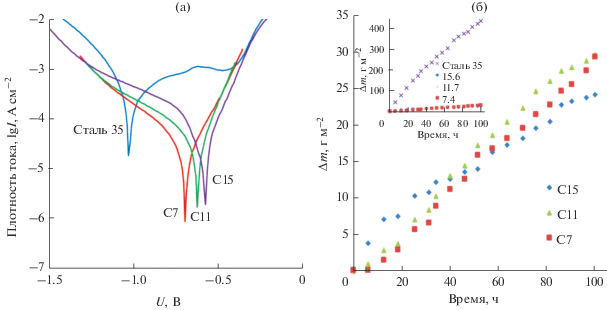
Таблица 2.
Коррозионные характеристики образцов, извлеченные из поляризационных кривых
Параметр | Образцы | |||
---|---|---|---|---|
Сталь 35 | C7 | C11 | C15 | |
Ecorr, V vs. Ag/AgCl | –1.02 | –0.69 | –0.62 | –0.57 |
Icorr, µA см–2 | 271 | 24 | 37 | 60 |
Rp, кОм см–2 | 6.5 | 75 | 29 | 17 |
На рис. 4б показана кинетика изменения массы образцов с покрытиями при температуре 700°С. Привес образцов обусловлен фиксацией кислорода на поверхности образцов в виде оксида железа в модификации гематита Fe3O4. Кинетические кривые привеса всех покрытий имели близкие значения, однако кривая покрытия С15 имела более пологий наклон. Поэтому лучшие защитные свойства продемонстрировало покрытие, осажденное с наибольшим содержанием порошка Cr3C2. За 100 ч испытаний образцы с покрытиями в 14–18 раз меньше подверглись окислению, чем сталь 35 (вставка к рис. 4б). Это объясняется ограничением контакта кислорода с подложкой за счет формирования тонкой пленки оксида хрома(III) и титансодержащей связки, поскольку титан устойчив к окислению при температурах до 800.
4. ЗАКЛЮЧЕНИЕ
Получены композиционные покрытия из карбида хрома Cr7C3 в металлической связки Fe–Cr–Ti на стали 35 методом электроискровой обработки в смеси титановых гранул и порошка Cr3C2. В процессе осаждения карбид Cr3C2 взаимодействует с расплавом железа и полностью декарбидизируется до Cr7C3, содержание которого повышается в составе покрытий с ростом содержания карбида в смеси гранул. Полученные покрытия продемонстрировали высокую твердость устойчивость к износу, коррозии и высокотемпературному окислению при 700°С. Таким образом, технология электроискровой обработки стали 35 в смеси титановых гранул с порошком карбида хрома может быть успешно применена для нанесения защитных покрытий на детали подверженные воздействию агрессивных сред, высоких температур или трению.
Список литературы
Miorin E., Montagner F., Zin V. et al. // Surface and Coatings Technology. 2019. V. 377. № 124890.
Cheng J., Wang B., Liu Q. et al. // J. Alloys and Compounds. 2017. V. 716. P. 88.
Vijay S., Wang L., Lyphout C. et al. // Applied Surface Science. 2019. V. 493. P. 956.
Farotade G.A., Adesina O.S., Popoola A.P.I. et al. // Metallography, Microstructure, and Analysis. 2019. V. 8. P. 349.
Bazhin P.M., Kostitsyna E.V., Stolin A.M. et al. // Ceramics International. 2019. V. 45. P. 9297.
Burkov A.A., Pyachin S.A., Ermakov M.A. et al. // J. Materials Engineering and Performance. 2017. V. 26. P. 901.
Kusinski J., Kac S., Kopia A. et al. // Bulletin of the Polish Academy of Sciences: Technical Sciences. V. 60. P. 711.
Santo L. // International J. Surface Science and Engineering. 2008. V. 2. P 327.
Li Z., Gao W., He Y. // Scripta Materialia. 2001. V. 45. P. 1099.
Burkov A.A., Zaitsev A.V., Zaikova E.R. et al. // Protection of Metals and Physical Chemistry of Surfaces. 2019. V. 55. P. 102.
Wang X.-R., Wang Z.-Q., Li W.-S. et al. // Materials Letters. 2017. V. 197. P. 143.
Zhao H., Gao C., Wu X. et al. Ceramics International. 2019. https://doi.org/10.1016/j.ceramint.2019.07.279
Radek N., Scendo M., Pliszka I. et al. // Powder Metallurgy and Metal Ceramics. 2018. V. 57. P. 316.
Kuptsov K.A., Sheveyko A.N., Zamulaeva E.I. et al. // Materials and Design. 2019. V. 167, № 107645. https://doi.org/10.1016/j.matdes.2019.107645
Kiryukhantsev-Korneev P.V., Sheveyko A.N., Shvindina N.V. et al. // Ceramics International. 2018. V. 44. P. 7637.
Burkov A.A., Pyachin S.A. // Materials and Design. 2015. V. 80. P. 109.
Burkov A.A., Kulik M.A. // Letters on Materials. 2019. V. 9. P. 243.
Bulloch J.H., Henderson J.L. // International J. Pressure Vessels and Piping. 1994. V. 58. P. 321.
Aghili S.E., Shamanian M. // Optics and Laser Technology. 2019. V. 119. № 105652.
Yang M.S., Liu X.B., Fan J.W. et al. // Applied Surface Science. 2012. V. 258. P. 3757.
Liu X.B., Wang H.M. // Applied Surface Science. 2006. V. 252. P. 5735.
Дополнительные материалы отсутствуют.
Инструменты
Физикохимия поверхности и защита материалов