Физикохимия поверхности и защита материалов, 2021, T. 57, № 5, стр. 543-560
Исследование диффузионно-барьерных свойств, термической стабильности и жаростойкости покрытий TiAlSiCN, TiAlSiCN/AlOx и TiAlSiCN/SiBCN
Ф. В. Кирюханцев-Корнеев 1, *, К. А. Купцов 1, Н. Ю. Табачкова 1, Н. В. Андреев 1, Т. Б. Сагалова 1, M. Golizadeh 2, А. В. Бондарев 1
1 Национальный исследовательский технологический университет “МИСиС”
119049 Москва, Ленинский просп., 4, Россия
2 M2Montanuniversitat Leoben
8700 Leoben, Franz-Josef-Strasse, 18, Austria
* E-mail: kiruhancev-korneev@yandex.ru
Поступила в редакцию 02.12.2020
После доработки 27.04.2021
Принята к публикации 11.05.2021
Аннотация
Изучены диффузионно-барьерные свойства, стойкость к термоциклированию, жаростойкость и термическая стабильность однослойных покрытий TiAlSiCN и многослойных покрытий TiAlSiCN/SiBCN и TiAlSiCN/AlOx. Покрытия получены с помощью вакуумной ионно-плазменной технологии, комбинирующей магнетронное и ионное распыление керамических мишеней TiAlSiCN, Si42B45C13 или Al2O3 с высокоэнергетической ионной имплантацией растущего покрытия ионами Ti2+. Исследование структуры и свойств покрытий в исходном состоянии выполнено с использованием методов оптической эмиссионной спектроскопии тлеющего разряда, просвечивающей электронной микроскопии высокого разрешения, сканирующей электронной микроскопии высокого разрешения, энерго-дисперсионной спектроскопии, наноиндентирования. Для оценки высокотемпературных характеристик были выполнены изотермические и неизотермические отжиги, ступенчатый нагрев и термоциклирование в среде воздуха и в вакууме. Установлено, что покрытие TiAlSiCN сохраняет специфическую наноколонную структуру nc-TiAlCN/a-SiCN и сверхвысокую твердость 37–49 ГПа в диапазоне температур 20–1300°С, жаростойкость до 1000°С, диффузионно-барьерные свойства ограниченные температурой 800°С. По сравнению с базовым покрытием TiAlSiCN многослойные покрытия TiAlSiCN/SiBCN имеют более высокую термическую стабильность до 1400°С (TiAlSiCN/SiBCN), жаростойкость до 1100°С, стойкость к диффузии элементов из подложки до 1000°С, стойкость к термоциклированию при 1000°С (TiAlSiCN/SiBCN, TiAlSiCN/AlOx).
1. ВВЕДЕНИЕ
Наиболее распространенным твердым износо- и коррозионно-стойким покрытием, получаемым на настоящий момент с помощью методов PVD и CVD по-прежнему остается нитрид титана TiN [1–3]. Связано это в основном с его низкой себестоимостью и простотой изготовления. Покрытие TiN обладает твердостью на уровне 20–25 ГПа, износостойкостью около (1–20) × 10–6 мм3 Н–1 м–1 и жаростойкостью до 500–600°С [4–8], высокими декоративными свойствами. Повышение эксплуатационных характеристик TiN может быть обеспечено за счет легирования различными металлическими и неметаллическими элементами, например Zr [9], Hf [10], Ta [11], V [12], W [13], Se [14] и др. Однако использование дорогостоящих компонентов [15] сильно ограничивает практическое применение подобных покрытий. С этой точки зрения перспективным является введение в состав более доступных элементов, таких как Al, Cr, C, Si. Ti–Al–N является на настоящий день достаточно популярным промышленно-выпускаемым покрытием, имеющим твердость до 40 ГПа, высокую износостойкость и рабочую температуру на уровне 900–1000°С [16]. Покрытия Ti–Al–C–N демонстрируют более высокие триботехнические характеристики чем Ti–Al–N, что связано с формированием фазы алмазоподобного углерода, выполняющего роль твердой смазки [17]. Введение в Ti–Al–N малых добавок Si позволяет существенно модифицировать структуру покрытий. Нанокомпозиционные покрытия в системе Ti–Al–Si–N, содержащие кристаллиты ГЦК-фазы на основе (Ti, Al)N, диспергированные в матрице аморфной фазы Si : N, имеют твердость до 40–50 ГПа, высокую коррозионную стойкость, жаростойкость до 1000–1100°С, а также отличную термическую стабильность до тех же температур, высокую износостойкость в различных условиях трения [18–24]. В работе [25] были впервые описаны покрытия Ti–Al–Si–C–N, характеризовавшиеся твердостью 45 ГПа, также изучено влияние соотношения Ti/Al на механические и трибологические свойства покрытий. Более поздние работы [26–30] выявили ряд преимуществ данной системы, включая экстремально высокую термическую стабильность до 1300–1400°С [30], антикоррозионные свойства, высокую износостойкость в условиях скольжения и ударных циклических нагрузок, а также сообщали о положительных результатах промышленных испытаний режущего инструмента с покрытием. Тем не менее, надо отметить отсутствие данных по исследованию диффузионно-барьерных свойств покрытий Ti–Al–Si–C–N, часто определяющих возможности практического применения разрабатываемых покрытий [31].
Наиболее существенным недостатком покрытий Ti–Al–Si–C–N является их относительно низкая жаростойкость, ограниченная T = 1000°C, что не позволяет полностью реализовать их потенциал, связанный с высокой термической стабильностью до 1400°С. Применение дополнительных верхних слоев Al/AlOx было успешно апробировано с целью повышения жаростойкости Ti–Al–Si–C–N до 1100°С [32]. Дальнейшая оптимизация характеристик Ti–Al–Si–C–N может быть направлена на создание многослойных покрытий, содержащих слои основного состава и вспомогательные слои, обладающие высокой жаростойкостью и препятствующие проникновению кислорода вглубь покрытий. Подобный подход был использован в работах [33–35]. Среди перспективных составов вспомогательных слоев могут выступать AlOx [36] и SiBCN [37–42], показавшие высокую жаростойкость. Подслои SiBC были ранее апробированы при создании покрытий MoSiB/SiBC и ZrSiB/SiBC [43, 44].
Целью данной работы является сравнительное исследование диффузионно-барьерных свойств, жаростойкости и термической стабильности покрытий TiAlSiCN, TiAlSiCN/AlOx, TiAlSiCN/SiBCN.
2. МЕТОДИКА ЭКСПЕРИМЕНТА
Для изготовления покрытий применялась вакуумная установка, оснащенная магнетронными и ионными распылительными источниками, а также имплантором высокоэнергетических ионов металла, схема представлена в работе [14]. Однослойные покрытия TiAlSiCN толщиной 1.6–1.8 мкм осаждались с помощью магнетронного распыления мишени TiAlSiCN диаметром 120 мм и толщиной 8 мм состава, ат. %: 42.2 Ti, 21.5 Al, 10.1 Si, 12.2 C, 14.0 N, полученной методом самораспространяющегося высокотемпературного синтеза [45]. Осаждение выполнялось при мощности около 1.1 кВт.
Многослойные покрытия наносились путем поочередного магнетронного распыления мишени TiAlSiCN и ионного распыления монокристаллической мишени Al2O3 стехиометрического состава или горячепрессованной SiBC состава Si42B45C13 [46]. Параметры магнетронного распыления сохранялись теми же, а дополнительные слои осаждались при подаче на ионный источник, напряжения 3 кВ при токе 80 мА. Толщина каждого отдельного слоя для многослойных покрытий была постоянной и равнялась 170 нм (слой TiAlSiCN) и 60–65 нм (слой SiBCN или AlOx). Для получения общей толщины многослойных покрытий TiAlSiCN/AlOx и TiAlSiCN/SiBCN на уровне 1.8–1.9 мкм осаждалось 8 пар слоев.
В качестве подложек использовались диски из никелевого сплава ХН65ВМТЮ диаметром 30 мм и толщиной 4 мм, диски из твердого сплава ВК6М того же размера, а также модельные подложки в виде пластин из поликристаллического Al2O3 марки ВК-100-1 размером 20 × 40 × 1 мм. Перед осаждением подложки подвергались ультразвуковой очистке в изопропиловом спирте в течение 5 мин, а затем проводилась ионная очистка непосредственно в вакуумной камере в течение 10 мин с помощью ионного источника при напряжении 3 кВ и токе 50 мА. Для увеличения адгезии перед осаждением производилась бомбардировка подложки высокоэнергичными ионами в течение 5 мин с помощью ионного имплантера типа MEVVA с энергией ионов Ti2+ равной приблизительно 70 кэВ. Ускоряющее напряжение, ионный ток и ионный поток сохранялись постоянными на уровне 35 кВ, 10 мА, и 2 × 1014 см–2 с–1, соответственно. Принцип получения многослойных покрытий представлен в работе [14].
Нанесение всех покрытий происходило в газовой смеси аргона и азота при соотношении N2/(N2 + Ar) равном 15% при давлении 0.1 Па, напряжение смещения на подложке поддерживалось на уровне –50 В и температура подложки составляла приблизительно 350°C.
Покрытия исследовались с применением методов оптической эмиссионной спектроскопии тлеющего разряда (ОЭСТР) на приборе Profiler-2 Horiba JY [47, 48] и растровой электронной микроскопии (РЭМ) на микроскопе JSM‑7600F JEOL, оснащенном модулем для энергодисперсионной спектроскопии (ЭДС). Рентгенофазовый анализ (РФА) выполняли на дифрактометре D8 Advanced Bruker с использованием CuКα излучения. Фольги для просвечивающей электронной микроскопии готовились с применением ионного травления на приборе FIB Strata 201 FEI Company (Нидерланды) при энергии пучка 30 кВ (ионы галлия). Просвечивающая электронная микроскопия (ПЭМ) проводилась на микроскопе JEM-2100 Jeol, также оснащенном ЭДС-спектрометром. Измерение твердости (H), модуля упругости (E) и упругого восстановления (W) производили методом наноиндентирования с использованием прецизионного нанотвердомера Nanohardness tester (CSM Instruments), оснащенного алмазным индентором Берковича, нагрузка составляла 8 мН. Перечисленные методы детально описаны в работе [49].
Для исследования диффузионно-барьерных свойств использовались покрытия, нанесенные на подложки из никелевого сплава. Покрытия ступенчато отжигались в муфельной печи типа SNOL на воздухе при температурах 800–1200°C с шагом в 100°C, время изотермической выдержки составляло 1 ч по аналогии с [50]. Дополнительно при 1000 и 1100°C, выдержке 1 ч, была оценена жаростойкость покрытий нанесенных на Al2O3. Для оценки термической стабильности покрытия на подложках из оксида алюминия отжигались в вакуумной печи ВакЭто при температурах 900–1600°C в течение 1 ч. Остаточное давление во время вакуумного отжига было ниже 10–2 Па. Термически обработанные покрытия были повторно исследованы с применением вышеперечисленных методов.
3. РеЗУЛЬТАТЫ И ИХ ОБСУЖДЕНИЕ
3.1. Структура и свойства исходных покрытий
На рис. 1 представлены микрофотографии поперечных изломов покрытий, осажденных на подложки из Al2O3. Покрытия обладали плотной малодефектной структурой. Для многослойных покрытий толщина индивидуальных слоев составляла ~170 нм для TiAlSiCN (более светлые области на микрофотографии) и 60–65 нм для SiBCN или AlOx (более темные области). Общие толщины покрытий TiAlSiCN, TiAlSiCN/AlOx и TiAlSiCN/SiBCN на подложках из поликора равнялись 3, 2 и 1.9 мкм соответственно.
Рис. 1.
РЭМ-изображения изломов осажденных на подложки Al2O3 исходных покрытий TiAlSiCN (а), TiAlSiCN/SiBCN (б), TiAlSiCN/AlOx (в).
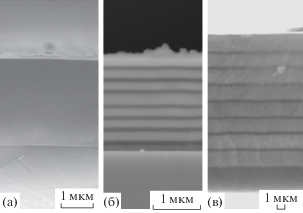
На дифрактограммах покрытий, снятых в диапазоне 2Θ = 20°–90°, линии соответствующие материалу покрытия находились в более узком интервале углов (рис. 2) По данным РФА основной составляющей покрытий TiAlSiCN является ГЦК-фаза на основе TiAlCN с сильной текстурой в направлении (111). Пики, выявляемые для ряда покрытий в положении 2Θ = 37.0°–37.5° соответствуют оксидам титана Ti2O (картотека PDF2 карточка 00-011-0218), Ti3O5 (00-009-0309) или SiO2 (01-082-1569). РФА образцов однослойных покрытий SiBCN и Al2O3 на подложках из поликора и кремния, аналогичных отдельным слоям в многослойных покрытиях, выявил их аморфную структуру. Таким образом, многослойные покрытия представляли собой структуры с чередованием слоев композиционного строения (nc-TiAlCN/a-SiCN) и аморфных слоев (a-SiBCN или a-AlOx). Размер кристаллитов фазы TiAlCN, оцененный по формуле Шеррера в однослойных и многослойных покрытиях существенно не отличался и составлял 8–10 нм. Период решетки фазы TiAlCN, определенный по линии (111) для покрытий TiAlSiCN, TiAlSiCN/AlOx и TiAlSiCN/SiBCN составлял 0.428–0.429 нм.
По данным ПЭМ покрытие TiAlSiCN содержит столбчатые кристаллиты ГЦК-фазы на основе карбонитрида титана с растворенными в нем атомами Al, разделенные аморфными прослойки на основе фазы SiCN, толщиной 2–3 нм (рис. 3). Поперечный размер зерен составляет 10–30 нм, а длина соответствует толщине покрытия. Многослойные покрытия содержат слои состава TiAlSiCN, перемежающиеся аморфными слоями AlOx и SiBCN. Важно отметить, что структура слоев TiAlSiCN неоднородна. В области, примыкающей к аморфному слою формируется нанокомпозиционная колонная структура nc-TiAlCN/a-SiCN, характерная для однослойных покрытий TiAlSiCN, а затем, по мере роста, образуется мелкозернистая равноосная структура из кристаллитов размером 5–20 нм (рис. 3).
Рис. 3.
Результаты ПЭМ исходных покрытий TiAlSiCN (вид сверху и поперечное сечение) и TiAlSiCN/SiBCN на подложках Al2O3.

Согласно данным спектроскопии комбинационного рассеяния и рентгеновской фотоэлектронной спектроскопии [28, 30] однослойные покрытия состоят из фаз nc-TiAlCN и a-SiCN.
Элементные профили покрытий, осажденных на никелевый сплав, полученные с помощью ОЭСТР, представлены на рис. 4. На элементном профиле однослойного покрытия TiAlSiCN, нанесенного на ХН65ВМТЮ можно выделить три зоны: первая, содержащая преимущественно Ni и Cr, – соответствует подложке из никелевого сплава, вторая (сигнал от Ti, Al, Si, C, N) – покрытию и третья, с высокой концентрацией примесей кислорода и углерода – приповерхностному слою. Интенсивность сигнала Ni в основном слое невелика (3.4 ат. %) и может быть вызвана влиянием шероховатости образца на результаты измерений или локальными отслоениями. В случае покрытий TiAlSiCN/SiBCN на ОЭСТР-профилях четко прослеживаются слои TiAlSiCN и SiBCN. Наблюдаются колебания концентраций азота и углерода из-за их различного содержания в каждом слое. Верхний слой соответствует SiBCN. Концентрация никеля в основном слое не превышает 3.0 ат. %. В покрытиях TiAlSiCN/AlOx также выявляются слои соответствующих компонентов, об аморфных слоях можно судить по пикам алюминия повышенной интенсивности. Концентрация кислорода в них невысока, а содержание азота находится на том же уровне, что и для слоев TiAlSiCN. Концентрация Ni в покрытии составляет 2.2 ат. %. Схожие тенденции обнаруживаются и при анализе распределения хрома (табл. 1). Важно отметить, что слоистая структура покрытий на подложках из никелевого сплава и модельных подложках из поликора идентична.
Таблица 1.
Диффузионно-барьерные свойства покрытий
Концентрация никеля, ат. % | |||||
---|---|---|---|---|---|
T = 20°C | T = 800°C | T = 900°C | T = 1000°C | T = 1100°C | |
TiAlSiCN | 3.4 | 3.5 | 7.8 | 8.5 | 16.2 |
TiAlSiCN/SiBCN | 3.0 | 2.4 | 3.3 | 9.0 | 26.2 |
TiAlSiCN/AlOx | 2.2 | 2.1 | 2.5 | 2.9 | 4.6 |
Концентрация хрома, ат. % | |||||
T = 20°C | T = 800°C | T = 900°C | T = 1000°C | T = 1100°C | |
TiAlSiCN | 1.0 | 0.9 | 1.2 | 2.6 | 6.7 |
TiAlSiCN/SiBCN | 0.2 | 0.5 | 0.8 | 1.9 | 9.9 |
TiAlSiCN/AlOx | 0.5 | 0.4 | 0.5 | 0.7 | 38.9 |
Покрытия в исходном состоянии имели следующие механические свойства: H = 41.5 ГПа, E = = 450 Па, W = 56% (TiAlSiCN), H = 23.5 ГПа, E = = 320 ГПа, W = 60% (TiAlSiCN/AlOx), H = 33.6 ГПа, E = 350 ГПа, W = 67% (TiAlSiCN/SiBCN).
3.2. Термическая стабильность
Данные РФА для покрытий TiAlSiCN после термообработки в вакууме в диапазоне температур 1000–1600°C представлены на рис. 2. Во всех случаях, независимо от температуры отжига, обнаруживается единственный пик (111), принадлежащий сильно текстурованной кубической фазе типа NaCl. Обзорные рентгенограммы (20° < 2Θ < 65°) покрытий TiAlSiCN также не показали других пиков, кроме относящихся к кубической фазе [28]. Особенно следует отметить, что даже после отжига при 1400°С не наблюдалось значимых отражений от фазы h-AlN, что типично для покрытий на основе TiAlN [51] и говорит о высокой термической стабильности исследуемых покрытий TiAlSiCN. В целом эволюцию пика (111) при отжиге можно разделить на три стадии. После отжига в температурном диапазоне 1000–1200°С пик смещался в сторону более высоких значений 2Θ, период решетки уменьшался с 0.428 до 0.423 нм, размер кристаллитов покрытий TiAlSiCN, увеличился соответственно с 8 до 18 нм (значения показаны на рис. 2). В диапазоне температур от 1200 до 1500°С пик смещается в противоположном направлении к более низким значениям 2Θ. Из-за роста кристаллитов с 18 до 41 нм, пик становится более узким. После отжига при 1600°С пик (111) переместился в положение, близкое к положению TiN (0.425 нм), что связано с заметной потерей углерода из кубической фазы. Размер кристаллитов увеличивается до 45 нм. Уменьшение периода решетки ГЦК-фазы между 25 и 1200°С можно объяснить релаксацией сжимающих напряжений и незначительными структурными превращениями из-за перераспределения элементов в пределах кристаллической и аморфной фаз. Увеличение периода решетки кубической фазы после термообработки между 1200 и 1500°C, может быть связано с изменением состава кубической фазы, которая становится более стехиометрической при высоких температурах.
Данные РФА многослойных покрытий после отжига в вакууме при 1300 и 1400°С показаны на рис. 2. После вакуумного отжига при 1300°С в покрытии TiAlSiCN/AlOx обнаружилось дополнительное отражение от фазы ГЦК-фазы (Ti, Al)(C, N) (200), подразумевающее начало перекристаллизации и переориентации зерна. Эти процессы сопровождались значительным ростом зерна от 10 до 34 нм. Кроме того, рентгенограммы покрытий TiAlSiCN/AlOx, записанные после термообработки при 1300 и 1400°С, показали небольшой (100) пик фазы h-AlN, расположенной при 2Θ = 33.2°, что подтверждает начало распада ГЦК-фазы. Более низкая термостабильность многослойных покрытий TiAlSiCN/AlOx по сравнению с покрытиями TiAlSiCN [30] может быть объяснена двумя факторами: наличием промежуточных слоев AlOx, ухудшивших термостабильность, и относительно небольшой толщиной промежуточных слоев TiAlSiCN. Дополнительное исследование показало, что кристаллизация однослойных покрытий AlOx в вакууме происходила ниже 1300°С, причем кристаллизация сопровождалась образованием большого количества пор и границ зерен. В случае покрытий TiAlSiCN/AlOx кристаллизация промежуточных слоев AlOx обеспечивает многочисленные пути для диффузии Si и Al к поверхности. Толщина отдельного слоя TiAlSiCN в многослойной структуре составляла десятую часть толщины покрытия TiAlSiCN, тем самым обеспечивая более короткие пути диффузии Si и Al внутри каждого промежуточного слоя TiAlSiCN без каких-либо дополнительных диффузионных барьеров на границах раздела TiAlSiCN/AlOx. После отжига покрытия TiAlSiCN/AlOx при 1400°С наблюдали появление нового пика при 2Θ = 26.5°, который может быть отнесен к Al2TiO5. Ранее сообщалось о образовании этого сложного оксида для обогащенных Al покрытий TiAlN и TiAlHfN после термообработки на воздухе при 1400 [52] и 1550°С [53] соответственно. Кроме того, при повышении температуры было обнаружено, что интенсивность пика AlN выше, что указывает на увеличение объемной доли фазы h-AlN. Параметр решетки кубической фазы возрос с 0.427 (1300°C) до 0.428 нм (1400°C), что может быть связано с потерей Al из фазы (Ti, Al) (C, N). Как показал ЭДС анализ, содержание Al в кубической фазе уменьшалось с 15 (исходное покрытие) до 11 и затем до 5 ат. % после отжига при 1300 и 1400°С соответственно. Также стоит отметить, что пики кубической фазы стали более узкими из-за роста кристаллитов от 30 до 40 нм.
На рентгенограмме образца TiAlSiCN/SiBCN после отжига при 1300°С выявляется дополнительное отражение (200) от фазы (Ti, Al)(C, N), указывающее на переориентацию зерна. В отличие от покрытий TiAlSiCN/AlOx, процесс перекристаллизации не сопровождался значительным ростом зерна. Результаты ЭДС анализа показали отсутствие значительной диффузии элементов через покрытие TiAlSiCN/SiBCN во время отжига при 1300°С. Таким образом, структурные модификации внутри покрытий TiAlSiCN/SiBCN могут происходить из-за перегруппировки элементов на короткие расстояния внутри каждого промежуточного слоя. Наблюдаемое уменьшение параметра решетки с 0.428 до 0.426 нм, по-видимому, обусловлено образованием более стехиометрических и свободных от микродеформации зерен после частичной перекристаллизации. Детальная интерпретация структурных превращений в покрытиях TiAlSiCN/SiBCN после отжига при 1400°C затруднена, поскольку процесс перекристаллизации включает только несколько верхних слоев. Основные изменения, наблюдаемые в рентгенограмме образца TiAlSiCN/SiBCN, были связаны с фазовыми превращениями, происходящими в верхней части покрытия. Во-первых, процесс перекристаллизации сопровождался образованием фазы h-AlN. Во-вторых, РФА выявил несколько характерных пиков при 2Θ = 27.7°, 34.2° и 44.5°, которые могут были отнесены к фазе TiB2 (карта ICDD № 00-035-0741). Этот результат согласуется с данными ЭДС, показывающими формирование TiB2 фазы в результате поверхностного обогащения Ti и B. Размер кристаллитов увеличивается с 13 (1300°С) до 30 (1400°С) нм.
Результаты СЭМ для покрытия TiAlSiCN, после отжигов в вакууме при температурах 1000, 1400, 1500 и 1600°С в течение 1 ч показаны на рис. 5. Видимых изменений по сравнению с исходным состоянием после его термообработки при 1000°С не наблюдалось. Однако при 1400°С можно предположить некоторую рекристаллизацию с ростом зерен до размеров 80–150 нм (рис. 5). При 1500°С наблюдалось образование крупных кристаллитов, а также поверхностной пленки толщиной 100 нм, состав которой был близок к AlN. Нагрев до 1600°С вызывал формирование грубой структуры с размером кристаллитов 50–250 нм.
В случае отжига покрытия TiAlSiCN/AlOx при 1300°С происходит полная перестройка структуры, включая рекристаллизацию внутри слоев TiAlSiCN и кристаллизацию слоев AlOx (рис. 5). ЭДС анализ показал, что процесс отжига сопровождался значительной потерей Si, от 6 до 1 ат. %. Этот результат указывает на то, что интенсивная диффузия Si к поверхности покрытия происходила при более низкой температуре отжига, чем в однослойном покрытии. Кроме того, было обнаружено, что размер рекристаллизованных зерен на границе раздела покрытие/подложка выше, чем в верхней части покрытия. Поскольку слой, прилегающий к подложке, осаждался с помощью высокоэнергетической ионной бомбардировки, он состоял из относительно грубых столбчатых зерен и содержал большое количество вызванных имплантацией дефектов, которые ухудшали термическую стабильность. Отжиг покрытия TiAlSiCN/AlOx при 1400°С привел к ускорению диффузионных процессов и дальнейшему укрупнению зерна, потере слоистой структуры. Результаты ЭДС показали совместное присутствие зерен (Ti, Al)(C, N) и Al2O3. Пониженное содержание Al в зернах (Ti, Al)(C, N), а также отсутствие Si указывают на их сублимацию из покрытия. Следует отметить, что высокое количество кислорода в фазе (Ti, Al)(C, N) может быть обусловлено его включением в ГЦК-решетку при проникновении из Al2O3, аналогично [24].
В отличие от покрытий TiAlSiCN/AlOx образцы TiAlSiCN/SiBCN, отожженные при 1300°C, полностью сохранили свою многослойную структуру с четкими границами между слоями (рис. 5). Мы не наблюдали никаких микроструктурных изменений ни сверху, ни снизу покрытий. ЭДС также не выявил заметных изменений в распределении элементов по толщине покрытия. Таким образом, превосходная термостабильность покрытий TiAlSiCN/SiBCN по сравнению с их аналогами TiAlSiCN/AlOx может быть обусловлена более высокой термостабильностью и лучшими диффузионно-барьерными характеристиками аморфных промежуточных слоев SiBCN, которые подавляли диффузию элементов из TiAlSiCN. Разницу можно объяснить пористой микроструктурой слоев оксида алюминия по сравнению с плотной структурой слоев SiBCN. После отжига при 1400°С рекристаллизация покрытия TiAlSiCN/SiBCN наблюдалась только в пяти верхних слоях покрытия, в то время как другая часть покрытия сохраняла первоначальную микроструктуру (рис. 5). Следует отметить, что процесс рекристаллизации, инициированный на поверхности, был завершен на границе раздела между соседними промежуточными слоями, что играло роль диффузионного барьера. Это наблюдение показало, что рекристаллизация протекала послойно, начиная с поверхности, и регулировалась диффузией. По данным ЭДС по Si, Ti, N и C внутри сохранившихся слоев не было значительных изменений, но процесс отжига сопровождался диффузией Al и B по направлению к поверхности, что приводило к обогащению верхних слоев. Интересно, что атомы Al в основном накапливались в разложенных слоях SiBCN и, вероятно, образовывали фазу AlN. На поверхности образца наблюдались также отдельные островки, которые согласно ЭДС, могут быть отнесены к TiB2.
На рис. 6 представлены данные ПЭМ для покрытия TiAlSiCN, отожженного при 1000 и 1300°С в течение 1 ч. Видно, что после термообработки мелкозернистая столбчатая структура оставалась в основном неизменной, при ширине нанозерен колонного типа на уровне 10–25 нм, разделенной тонкими аморфными прослойками толщиной 1–3 нм. При этом результаты ПЭМ хорошо согласуются со средним размером кристаллитов, определенным из рентгенограммы этого образца. Разложение и рекристаллизация наноколонной структуры в случае покрытий TiAlSiCN происходили только выше 1300°С.
Исследования методом ПЭМ были также проведены для отожженных многослойных покрытий. Была выбрана система TiAlSiCN/SiBCN, обладающая более высокой термической стабильностью, чем TiAlSiCN/AlOx (рис. 6). Измерения были проведены при разных временах травления фольги ионным пучком на стадии пробоподготовки. После отжига сохраняется слоистая структура. Повышение длительности ионной обработки приводит к сильному вытравливанию аморфных слоев SiBCN. В слоях TiAlSiCN наблюдаются кристаллиты ГЦК-фазы размером от 10 до 300 нм. Попадаются отдельные индивидуальные зерна с размером до 500 нм. Локальный ЭДС анализ показал, что кристаллиты содержат преимущественно титан и углерод. Отсутствие сигнала азота в данном случае можно связать со сложностью обнаружения легких элементов методом ЭДС и спецификой детектора. В ряде кристаллитов в дополнение к титану и углероду обнаруживаются также алюминий и кремний. В верхних слоях идентифицированы кристаллиты с повышенным содержанием Al (вероятно на основе фазы AlN). Фрагменты сохранившихся аморфных прослоек (высокая концентрация Si) присутствуют между слоями TiAlSiCN.
На рис. 7 показаны зависимости механических свойств покрытий от температуры вакуумного отжига. Покрытия TiAlSiCN показали небольшое увеличение твердости с 41 до 43 ГПа между 25 и 900°C. Выраженная пиковая твердость 49 ГПа наблюдалась после термообработки покрытия при 1000°С. С дальнейшим повышением температуры до 1100°C, твердость снизилась до 40 ГПа и оставался выше 37 ГПа до 1300°C. После отжига в вакууме при 1400°С в течение 1 ч твердость упала до значения 26 ГПа, что является типичным значением для осажденных покрытий TiN [54]. Отметим, что после 1500 и 1600°С твердость составляла 19 и 12 ГПа.
Рис. 7.
Зависимость твердости (H), модуля упругости (Е) и упругого восстановления (W) от температуры вакуумного отжига (T). На вставках показаны удельные значения, выраженные через отношение величины после отжига (ann) к начальному (in).
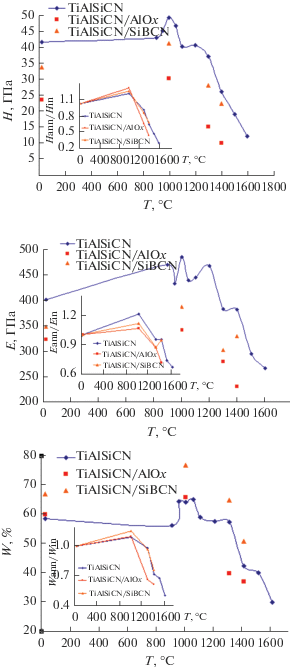
Значения твердости нанесенных покрытий TiAlSiCN/SiBCN и TiAlSiCN/AlOx составляли 34 и 24 ГПа соответственно, что ниже, чем у однослойного материала TiAlSiCN (42 ГПа). Снижение твердости осажденных многослойных покрытий можно объяснить наличием аморфных промежуточных слоев [55, 56] с относительно низкой твердостью, 12 (AlOx) и 24 ГПа (SiBCN). Кроме того, верхний слой в многослойной структуре вносит значительный вклад в твердость материала, которым в нашем случае является AlOx или SiBCN. После отжига при 1000°С твердость увеличивалась до 30 (TiAlSiCN/AlOx) и 40 ГПа (TiAlSiCN/SiBCN), аналогично тому, что наблюдалось в покрытиях TiAlSiCN увеличение твердости после вакуумного отжига было обусловлено перераспределением элементов в соседних фазах, как описано ранее [30]. При дальнейшем повышении температуры отжига наблюдалось снижение твердости обоих многослойных покрытий. Падение твердости покрытий TiAlSiCN/AlOx при 1300°С было вызвано главным образом разложением промежуточных слоев TiAlSiCN, сопровождающимся значительным увеличением размера зерен, и высокой пористостью, обусловленной кристаллизацией слоя AlOx. Дальнейшее снижение твердости при 1400°С связано с сильным ростом зерна и значительной потерей Al из фазы (Ti, Al)(C, N). При отжиге твердость покрытий TiAlSiCN/SiBCN снизилась с 40 (1000°C) до 27 ГПа (1300°C). Учитывая, что многослойная структура была полностью сохранена во время термообработки, падение твердости, по-видимому, связано со структурными изменениями внутри каждого отдельного промежуточного слоя из-за диффузии на короткие расстояния. Рентгенограммы отожженных образцов указывают на переориентацию зерен в слоях TiAlSiCN. Текстурированность может способствовать росту твердости материала [57]. После отжига при 1400°С твердость покрытия TiAlSiCN/SiBCN была значительно выше по сравнению с TiAlSiCN/AlOx и была почти равна твердости однослойного покрытия TiAlSiCN. Следует отметить, что глубина проникновения индентора во время измерений твердости покрытий TiAlSiCN/SiBCN составляла около 300 нм, что хорошо совпадало с толщиной верхнего рекристаллизованного слоя. Твердость (H) сохранившейся части многослойного покрытия TiAlSiCN/SiBCN может быть выше. Зависимость модуля Юнга (E) и упругого восстановления (W) многослойных покрытий от температуры отжига показана на рис. 7. Покрытия TiAlSiCN/SiBCN продемонстрировали высокое значение отношения H/E (~0.09) в осажденном состоянии, которое слегка увеличивалось до 0.1 после отжига при 1000°С, а затем постепенно уменьшалось до 0.07 при 1400°С. Покрытия TiAlSiCN/SiBCN также показали высокое упругое восстановление выше 60% в широком диапазоне температур 25–1300°C. Напротив, покрытия TiAlSiCN/AlOx демонстрировали более низкие значения H/E и W. Данные о термической стабильности покрытий могут быть наглядно выражены через отношения значений механических свойств после отжига к исходным (рис. 7, вставки). Для однослойных покрытий TiAlSiCN и многослойных покрытий TiAlSiCN/SiBCN этот показатель достаточно близок. Результаты относительного изменения твердости, модуля упругости и упругого восстановления идентичны. В то же время, для TiAlSiCN/AlOx после нагрева до температур, превышающих 1000°С, происходит резкое снижение удельных характеристик, что связано с процессами рекристаллизации и исчезновением слоистой структуры при нагреве до 1300–1400°С. Обобщая данные структурных исследований и результаты наноиндентирования, покрытий после вакуумных отжигов можно сделать заключение о том, что покрытия TiAlSiCN/SiBCN превосходят по термической стабильности базовое покрытие TiAlSiCN, поскольку при 1400°С в нем процессы рекристаллизации менее выражены, а уровень удельных характеристик такой же. Введение в структуру слоев оксида алюминия снижает термическую стабильность покрытий TiAlSiCN.
3.3. Жаростойкость покрытий
Данные РЭМ, ОЭСТР и ЭДС для покрытий TiAlSiCN, TiAlSiCN/SiBCN, TiAlSiCN/AlOx, нанесенных на подложки из оксида алюминия, после отжигов на воздухе при 1000 и 1100°С представлены на рис. 8. Можно видеть, что после отжига при 1000°С покрытие TiAlSiCN окислялось лишь частично, причем толщина оксидного слоя составляла около 15% от общей толщины покрытия. Анализ ОЭСТР показал, что после высокотемпературной выдержки в течение 1 ч формировалась оксидная пленка с последовательностью слоев: TiO2 → Al2O3 → TiO2, под пленкой находился неокисленный слой. Отожженное при 1100°С покрытие TiAlSiCN окислялось на всю глубину. Фиксировалась та же последовательность оксидных слоев, но без резких границ раздела между ними: за TiO2 слоем следовали два высокопористых слоя Al2O3 и TiO2. Самый нижний оксидный слой состоял из смеси SiO2 и TiO2 фаз. Полученные результаты показали, что, хотя большая часть атомов Al диффундирует в верхнюю часть покрытия и взаимодействует с кислородом с образованием Al2O3, этот оксидный слой не способен эффективно защищать покрытие от дальнейшего окисления из-за повышенной пористости.
Покрытие TiAlSiCN/AlOx после отжига на воздухе при 1100°C было частично окислено (70% толщины покрытия сохранилось). Таким образом введение промежуточных слоев AlOx может значительно повысить стойкость к окислению покрытия TiAlSiCN. Последовательность оксидных слоев была аналогична базовому покрытию TiAlSiCN, а именно TiO2 → Al2O3 → TiO2 → TiO2 + + SiO2, за исключением того, что слой Al2O3 был плотным, с четкими границами раздела и без включений других оксидов. Данные ЭДС показали, что химический состав каждого отдельного слоя в неокисленной части покрытия оставался почти постоянным. Это доказывает, что прослойки AlOx играли роль диффузионных барьеров. Таким образом, усиленная защита от окисления покрытий TiAlSiCN/AlOx обеспечивалась главным образом первоначальным плотным слоем α – AlOx. Напротив, в однослойном покрытии TiAlSiCN защитная пленка Al2O3 образовалась на поверхности образца в результате интенсивной диффузии Al к поверхности. Этот процесс зависел от температуры и времени; поэтому плотная и однофазная пленка Al2O3 не образовывалась.
Добавление промежуточных слоев SiBCN также улучшило стойкость к окислению покрытий TiAlSiCN/SiBCN по сравнению с однослойным образцом TiAlSiCN. Можно видеть, что после воздействия воздуха при 1100°С самые нижние слои TiAlSiCN и SiBCN не подвергались окислению. Слоистая структура в средней части образца также сохранялась, хотя концентрация Al, C, N и B снижалась из-за их диффузии. Согласно ЭДС от поверхности в глубину формировались: внешний слой, состоящий из отдельных зерен TiO2, слой, состоящий фаз Al2O3 и TiO2, многослойный оксид SiO2/TiO2, который не мог обеспечить достаточную защиту от проникновения кислорода.
Обсуждая механизм и кинетику окисления, важно подчеркнуть роль плотности слоя AlOx, образующегося на поверхности покрытия. Исследования, проведенные с помощью ОЭСТР показали, что на поверхности покрытия TiAlSiCN во время отжига при 1000°С уже через 1 мин образовывался тонкий Al2O3. Дальнейшая выдержка образца в течение 6 мин приводила к увеличению толщины Al2O3, достаточное количество Al поступало из глубины покрытия. Многочисленные прямые границы зерен между кристаллическими и аморфными составляющими в наноколонной структуре обеспечивают простые и быстрые пути для диффузии атомов Al к поверхности, тем самым поддерживая рост пленки Al2O3. Через 13 мин воздействия при 1000°С наблюдалось образование толстого слоя, обедненного Al, непосредственно под слоем Al2O3. Это указывает на то, что поток Al уже не может дополнительно поддержать рост Al2O3. Кроме того, из-за нехватки Al кислород взаимодействует с Ti с образованием его оксидов. Известно, что рост TiO2 сопровождается значительным увеличением объема, что, в свою очередь, вызывает микрорастрескивание внутри соседнего слоя Al2O3, тем самым усиливая диффузию элементов внутрь и наружу [58]. Это явление ясно объясняет образование значительного количества фазы TiO2 как выше, так и ниже слоя Al2O3. Было обнаружено, что покрытие TiAlSiCN полностью окисляется при 1100°C. Можно видеть, что TiO2, образуется внутри зоны обедненной Al, и растет в толстой пленке Al2O3. Поскольку эксперименты по отжигу при 1000°С показали, что сначала формировался тонкий Al2O3 поверхностный слой, разумно предположить, что окисление при нагревании до температуры 1100°С также началось с образования Al2O3 фазы. Наши результаты, однако, ясно показали, что этот поверхностный слой Al2O3 не может защитить покрытия от полного окисления из-за его несовершенной микроструктуры. Важным условием для роста плотной окисной пленки является то, что алюминий может быстро диффундировать на поверхность, приводя к росту новых зерен окиси алюминия снаружи первоначально образованной окисной пленки. Разница в пористости оксидной пленки, образующейся при различных температурах, также может быть обусловлена более высокой постоянной параболической скорости окисления при 1100°С по сравнению с температурой при 1000°С [59], что приводит к более быстрому росту Al2O3, но с повышенной пористостью. Более пористый слой Al2O3 слабо защищает от окисления, поскольку атомы кислорода могут легко диффундировать через пористую микроструктуру, что приводит к дальнейшему быстрому окислению внутри зоны, обедненной Al. Зерна TiO2 растут в слое Al2O3, тем самым дополнительно разрушая его целостность и способствуя дальнейшему окислению.
Введение промежуточных слоев AlOx в покрытие TiAlSiCN значительно улучшило стойкость материала к окислению. Прежде всего, наличие верхнего слоя AlOx в многослойном покрытии TiAlSiCN/AlOx предотвращало или замедляло диффузию кислорода внутрь с самого начала процесса нагревания, что, облегчает образование термически выращенного оксида алюминия на поверхности. Кристаллический слой Al2O3 может облегчить селективное окисление Al путем обеспечения предпочтительных центров зародышеобразования для кристаллитов новых оксидов, аналогичных тем, которые наблюдались для композитов Al2O3/TiAl [60]. Промежуточные слои AlOx предотвращают диффузию Ti наружу при высоких температурах, тем самым, снижая скорость роста кристаллитов TiO2 ниже слоя Al2O3. Последнее хорошо объясняет образование более тонкой и плотной микроструктуры TiO2 после термообработки покрытий TiAlSiCN/AlOx при 1100°С по сравнению с TiAlSiCN (рис. 8). Стоит подчеркнуть, что этот подход устраняет потребность в высоком содержании Al в покрытии для эффективной защиты от окисления при таких высоких температурах.
Несколько более низкие защитные характеристики покрытий TiAlSiCN/SiBCN по сравнению с TiAlSiCN/AlOx можно объяснить следующим. Оказалось, что слои SiBCN предотвращали диффузию Al наружу во время процесса окисления и таким образом замедляли формирование защитного слоя Al2O3. На рис. 8 видно, что оксидный слой под верхним слоем TiO2 состоит из смеси TiO2 и Al2O3 по сравнению с плотной и четко определяемой пленкой Al2O3, наблюдаемой в случае TiAlSiCN/AlOx. Тем не менее наблюдался и положительный эффект слоев SiBCN с точки зрения стойкости к окислению. Образование при 1100°С плотного верхнего слоя SiO2 толщиной ~200 нм может защитить многослойные покрытия TiAlSiCN/SiBCN от быстрого начального окисления (рис. 8). Внутри покрытия TiAlSiCN/SiBCN при нагреве также вместо слоев SiBCN образуется SiO2, что является дополнительной защитой.
3.4. Диффузионно-барьерные свойства
Для оценки диффузионно-барьерных свойств покрытий были проведены ступенчатые отжиги с повышением температуры на каждом шаге на 100°С для образцов на никелевой подложке. Элементные профили покрытий после отжигов при 800, 900, 1000 и 1100°С показаны на рис. 9 и 10. Количественно оценить диффузионные свойства можно, ориентируясь на концентрации элементов подложки (никеля и хрома) в слое, соответствующем покрытию (табл. 1). Чем ниже эти значения, тем выше стойкость материала покрытия к диффузии.
После нагрева базового покрытия TiAlSiCN на подложке из никелевого сплава до 800°С образуется поверхностный слой, толщиной около 1 мкм, обогащенный кислородом. Концентрация Ni и Cr незначительно отличается от исходного состояния. Необходимо принять во внимание что толщина окисленного слоя может быть определена с погрешностью при высокой пористости оксидного слоя, поскольку это ведет к проникновению компонентов воздуха в разрядный промежуток ОЭСТР-спектрометра. Также играет роль и шероховатость, которая заметно выше при использовании в качестве подложки никелевого сплава. С другой стороны, повышенная концентрация элементов подложки в слое покрытия может быть связна не только с диффузионными процессами, но и с отслоениями, вследствие чего сигналы компонентов подложки могут регистрироваться уже на поверхности покрытия. Для понимания правильной трактовки результатов необходимо анализировать поведение различных компонентов подложки, обладающих большим различием в коэффициентах диффузии. В нашем случае – это никель и хром. Для покрытия TiAlSiCN/SiBCN толщина оксидного слоя не превышала 0.3 мкм, для TiAlSiCN/AlOx – 1.1 мкм. Значения концентраций Ni и Cr в пределах ошибки измерений для многослойных покрытий существенно не изменялись по сравнению с исходным состоянием. Действительно известно, что диффузионные процессы активизируются при температуре 900°С и выше [61].
При 900°С для базового покрытия наблюдалось формирование оксидной пленки на основе Al2O3 и TiO2 с суммарной толщиной около 1.3 мкм. Заметно резкое, по сравнению с исходным состоянием и случаем после отжига при 800°С увеличение концентрации никеля в слое покрытия. Наблюдается рост более, чем в два раза: с 3.4–3.5 до 7.8 ат. % Ni. Для покрытия TiAlSiCN/SiBCN при той же температуре 900°С четко прослеживается образование оксидного поверхностного слоя на основе SiO2 толщиной около 0.8 мкм. Диффузионные процессы не выражены. Концентрация никеля 3.3 ат. % практически совпадает со значением для исходного образца (3.0 ат. %). Анализ ОЭСТР-профилей показал, что слой SiBCN играет роль диффузионного барьера для Ni. Наблюдается падение концентрации Ni на участках спектра, соответствующих SiBCN (вставка на рис. 9). Для TiAlSiCN/AlOx в исходном состоянии и после отжига при 900°С концентрации никеля близки и находятся в диапазоне 2.2–2.5 ат. %. Интересно отметить, что в случае TiAlSiCN/AlOx после окисления при 900°С поверхностная оксидная структура толщиной 2.9 мкм состоит из слоев Al2O3 (ближе к поверхности покрытия) и TiO2. Слоистая структура сильно деградировала – наблюдается не более 5 пар слоев.
При повышении температуры отжига до 1000°С в случае базового покрытия распределение основных элементов покрытия меняется незначительно по сравнению с 900°С. Можно отметить, что атомы хрома, также как и атомы никеля заметно диффундируют вглубь покрытия, достигая поверхностного оксидного слоя. Причем в отличие от ситуации с 900°С при 1000°С атомы никеля проникают непосредственно в оксидный слой. С этим можно связать снижение общей толщины оксидной пленки, поскольку никель может формировать плотные оксидные слои с высокими защитными характеристиками. Концентрация никеля в покрытии близка к ситуации с 900°С (табл. 1), тогда как концентрация хрома повышается с 1.2 до 2.6 ат. %. Для многослойного покрытия TiAlSiCN/SiBCN при 1000°С на ОЭСТР-спектре заметен участок, соответствующий оксидному слою. Толщину слоя определить не удается, поскольку из-за высоких пористости и шероховатости в разрядный промежуток при измерении попадет кислород воздуха. Измеряемая концентрации нарушается, данные по содержанию элементов и толщина искажаются. Действительно, на участке спектра, соответствующем поверхностному слою из-за проникновения воздуха четко виден сигнал от азота (40 ат. %), чего не наблюдалось при всех ранее описанных случаях. Диффузия Ni и Cr для TiAlSiCN/SiBCN менее выражена, чем для базового покрытия. Элементы подложки проникают в нижние 4 пары слоев, но до поверхности покрытия не доходят. Усредненная по толщине концентрация никеля (9 ат. %) близка к значению для TiAlSiCN (8.5 ат. %), в то время, как по хрому наблюдаются более низкие значения (1.9 против 2.6 ат. %). Отметим, что слоистая структура сохраняется. Для TiAlSiCN/AlOx из всех образцов наблюдаются минимальные концентрации никеля и хрома в покрытии, составляющие 2.9 и 0.7 ат. % соответственно. Заметна деградация слоистой структуры – выявляются два слоя TiAlSiCN и один AlOx в неокисленной зоне. Как в случае многослойного покрытия TiAlSiCN/AlOx, так и в случае TiAlSiCN/SiBCN при 1000°С никель в оксидный слой не проникает, что свидетельствует об их более высоких диффузионно-барьерных свойствах по сравнению с однослойным покрытием TiAlSiCN.
Нагрев покрытий TiAlSiCN, TiAlSiCN/SiBCN и TiAlSiCN/AlOx на подложках из никелевого сплава до максимальной температуры 1100°С приводит к их полному разрушению, вследствие интенсивной диффузии и окисления. Однако характер деградации покрытий сильно отличается. В базовом покрытии заметно формирование поверхностной оксидной пленки переменного состава, содержащей алюминий, титан и никель. Между оксидом и подложкой присутствует слой с низким содержанием кислорода, содержащий компоненты покрытия Ti, Al, N, а также компоненты сплава (хром и никель). Можно было бы говорить о сохранности тонкого слоя в покрытии, однако отсутствие углерода, высокие концентрации Ni (16.2 ат. %) и Cr (6.7 ат. %) свидетельствуют о деградации покрытия. Компоненты покрытия TiAlSiCN/SiBCN при 1100°С активно взаимодействуют с компонентами подложки, суммарная концентрация которых составляет 36 ат. %. Ранее растворение покрытия в подложке из никелевого сплава было описано в работе [31]. Высокие защитные свойства оксидов хрома и никеля, диффундирующих в обратном направлении в сторону поверхности способствуют торможению окисления, толщина оксидного слоя не превышает 1 мкм. В случае покрытия TiAlSiCN/AlOx замечена аномально высокая диффузия атомов хрома (38.9 ат. %) к поверхности при незначительной диффузии никеля (4.6 ат. %).
Известно, что химический, фазовый состав, механические и физические характеристики подложки оказывают значительное влияние на поведение покрытий при различных типах воздействий [8, 31, 62–64]. Отметим, что в нашем случае более низкая жаростойкость покрытий, зафиксированная при использовании в качестве подложек никелевого сплава, помимо протекания активного диффузионного взаимодействия с подложкой на основе Ni, может быть обусловлена отличием схемы отжигов. Для покрытий, нанесенных на поликор, время изотермической выдержки составляло 1 ч. В то время, как покрытия на никелевом сплаве отжигались ступенчато с повышением температуры и суммарная выдержка при повышенных температурах соответствовала 4 ч. Кроме того, характер данного испытания (схема 20-800-20-900-20-1000-20-1100-20°С) был близок к условиям термоциклирования. Для лучшего понимания перечисленных процессов были выполнены эксперименты по циклическому нагреву и охлаждению покрытий.
3.5. Стойкость к термоциклированию
Стойкость покрытий на подложках из оксида алюминия к термоциклированию определялась следующим образом. Образцы в тиглях помещались в предварительно разогретую до рабочей температуры 1000°С муфельную печь типа SNOL, выдерживались в течение 5 мин, затем извлекались и охлаждались в течение ~5 мин до 20°С за счет обдува струей воздуха. Подобный цикл повторялся 100 раз. После каждых 20, 50 и 100 циклов проводилось исследование поперечных изломов покрытий на растровом электронном микроскопе 3400S Hitachi и определялась толщина оксидного слоя. Результаты приведены на рис. 11.
Рис. 11.
Зависимость толщины верхнего окисленного слоя (мкм) от количества теплосмен (термоциклирование в режиме 20-1000-20°С на воздухе).
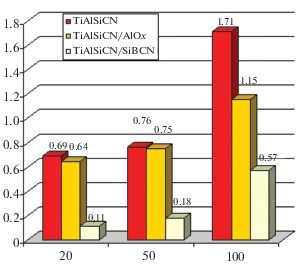
В случае базового однослойного покрытия TiAlSiCN глубина окисления при увеличении числа циклов с 20 до 100 закономерно возрастает с 0.69 до 1.71 мкм. В целом близкие значения на уровне 0.64, 0.75 и 1.15 мкм для 20, 50 и 100 циклов соответственно было зафиксированы для многослойного покрытия TiAlSiCN/AlOx. Таким образом, глубина окисления снижается по сравнению с базовым покрытием на 1–7% при 20 и 50 циклах и на 33% при 100 циклах теплосмен. Самые низкие значения глубины окисления были обнаружены для многослойных покрытий TiAlSiCN/SiBCN. При 20, 50 и 100 циклах эти значения составляли 0.11, 0.18 и 0.57 мкм, соответственно. Важно, что это приблизительно в три раза ниже, чем глубины окисления при тех же условиях для базового однослойного покрытия TiAlSiCN и образца TiAlSiCN/AlOx.
ЗАКЛЮЧЕНИЕ
Методом магнетронного и ионного распыления, совмещенного с ионной имплантацией, были получены одно- и многослойные покрытия TiAlSiCN, TiAlSiCN/AlOx и TiAlSiCN/SiBCN на подложках из оксида алюминия и никелевого жаростойкого сплава. В исходном состоянии структура покрытий TiAlSiCN состояла из наноколонн ГЦК-фазы nc-(Ti,Al)CN диаметром до 50 нм и длиной, соответствующей толщине покрытия, разделенных аморфными прослойками a-SiCN шириной 1–3 нм. В многослойных покрытиях слои TiAlSiCN, структура которых схожа с однослойными покрытиями, были разделены аморфными слоями a-SiBCN и a-AlOx. Удельные значения механических характеристик (твердости, модуля упругости, упругого восстановления) при нагреве в вакууме меняются одинаково для покрытий TiAlSiCN и TiAlSiCN/SiBCN. В то же время слоистая структура TiAlSiCN/SiBCN сохраняется до 1400°С, тогда как наноколонная структура TiAlSiCN стабильна лишь до 1300°С. Образец TiAlSiCN/AlOx имел относительно низкую термическую стабильность, однако так же, как и TiAlSiCN/SiBCN способствовал повышению жаростойкости с 1000°С (для базового покрытия) до 1100°С. Слои a-SiBCN и a-AlOx в многослойных покрытиях препятствуют диффузии металлических элементов из подложки при нагреве до 1000°С, что на 200°С выше, чем для однослойного покрытия TiAlSiCN. Стойкость к термоциклированию на воздухе возрастала в ряду TiAlSiCN → TiAlSiCN/AlOx → TiAlSiCN/SiBCN.
Список литературы
Xiao W., Deng H., Zou S. et al. // J. Nuclear Materials. 2018. V. 509. P. 542–549.
Xi Y., Bai Y., Gao K. et al. // Ceramics International. 2018. V. 44. P. 15851–15858.
Li J., Zhang Y., Zhao Y. // J. Alloys and Compounds. 2017. V. 724. P. 34–44.
Bashir M.I., Shafiq M., Naeem M. et al. // Surface and Coatings Technology. 2017. V. 327. P. 59–65.
Malvajerdi S.S., Malvajerdi A.S., Ghanaatshoar M. // Ceramics International. 2019. V. 45. P. 3816–3822.
Yan Z., Jiang D., Gao X. et al. // Tribology International. 2018. V. 124. 61–69.
https://www.platit.com/sites/default/files/pdf/coating-guide-ev21-lowres.pdf
Kiryukhantsev-Korneev F.V., Petrzhik M.I., Sheveiko A.N. et al. // Physics of Metals and Metallography. 2007. V. 104. P. 167–174.
Niu E.W., Li L., Lv G.H. et al. // Applied Surface Science. 2008. V. 254. P. 3909–3914.
Andreev A., Beresnev V.M., Volosova M.A. et al. // J. Friction and Wear. 2013. V. 34. № 3. P. 175–182.
Feng W., Zhou H., Yang S.-Z. // Materials Chemistry and Physics. 2010. V. 124. P. 287–290.
Ichimiya N., Onishi Y., Tanaka Y. // Surface and Coatings Technology. 2005. V. 200. P. 1377–1382.
Severo V., Vilhena L., Silva P.N. et al. // J. Materials Processing Technology. 2009. V. 209. P. 4662–4667.
Shtansky D.V., Sheveyko A.N., Sorokin D.I. et al. // Surface and Coatings Technology. 2008. V. 202. P. 5953–5961.
Li B., Liu Q., Chen M. et al. // Surface and Coatings Technology. 2018. V. 354. P. 175–183.
PalDey S., Deevi S.C. // Materials Science and Engineering. 2003. V. 342. P. 58–79.
Zhang X., Jiang J., Yuqiao Z. et al. // Surf. Coat. Technol. 2008. V. 203. P. 594–597.
Jeong Y.K., Kang M.C., Kwon S.H. et al. // Current Applied Physics. 2009. V. 9. P. S141–S144.
Yoo Y.H., Le D.P., Kim J.G. et al. // Thin Solid Films. 2008. V. 516. P. 3544–3548.
Derflinger V.H., Schütze A., Ante M. // Surf. Coat. Technol. 2006. V. 200. P. 4693–4700.
Veprek S., Männling H.-D., Jilek M., Holubar P. // Materials Science and Engineering A. 2004. V. 366. P. 202–205.
Holubar P., Jilek M., Sima M. // Surf. Coat. Technol. 2000. V. 133–134. P. 145–151.
Park I.-W. et al. // J. Korean Physical Society. 2003. V. 42. P. 783–786.
Vennemann A., Stock H.-R., Kohlscheen J. et al. // Surf. Coat. Technol. 2003. V. 174–175. P. 408–415.
Kiryukhantsev-Korneev F.V., Kuptsov K.A., Sheveyko A.N. et al. // Russian J. Non-Ferrous Metals. 2013. V. 54 P. 330–335.
Kuptsov K.A., Kiryukhantsev-Korneev Ph.V., Sheveyko A.N., Shtansky D.V. // Surface and Coatings Technology. 2013. V. 216. P. 273–281.
Shtansky D.V., Kuptsov K.A., Kiryukhantsev-Korneev Ph.V. et al. // Surface and Coatings Technolog. 2011. V. 205. P. 4640–4648.
Shtansky D.V., Kuptsov K.A., Kiryukhantsev-Korneev Ph.V., Sheveyko A.N. // Surface and Coatings Technology. 2012. V. 206. P. 4840–4849.
Bondarev A.V., Kiryukhantsev-Korneev Ph.V., Sheveyko A.N., Shtansky D.V. // Applied Surface Science. 2015. V. 327. P. 253–261.
Kuptsov K.A., Kiryukhantsev-Korneev Ph.V., Sheveyko A.N., Shtansky D.V. // Acta Materialia. 2015. V. 83. P. 408–418.
Kiryukhantsev-Korneev F.V., Sheveiko A.N., Komarov V.A. et al. // Russian J. Non-Ferrous Metals. 2011. V. 52. P. 311–318.
Kuptsov K.A., Kiryukhantsev-Korneev Ph.V., Sheveyko A.N., Shtansky D.V. // Applied Surface Science. 2015. V. 347. P. 713–718.
Riedl H., Aschauer E., Kolleret C.M. et al. // Surface and Coatings Technology. 2017. V. 328. P. 80–88.
Aschauer E., Sackl S., Schachinger T. et al. // Surface and Coatings Technology. 2018. V. 349. P. 480–487.
Jeong J.J., Lee C.M. // Applied Surface Science. 2003. V. 214. P. 11–19.
Raab R. et al. // Surface and Coatings Technology. 2017. V. 324. P. 236–242.
Zeman P., Capek J., Cerstvy R., Vlcek J. // Thin Solid Films. 2010. V. 519. P. 306–311.
He J., Zhang M., Jiang J. et al. // Thin Solid Films. 2013. V. 542. P. 167–173.
Kiryukhantsev-Korneev Ph.V., Sheveyko A.N., Lemesheva M. et al. // Protection of Metals and Physical Chemistry of Surfaces. 2017. V. 53. № 5. P. 873–878.
Feng Z., Guo Z., Biao L. et al. // Key Engineering Materials. 2014. V. 602–603. P. 393–396.
Guo X., Wang D., Guo Z. et al. // Surface and Coatings Technology. 2018. V. 350. P. 101–109.
Kiryukhantsev-Korneev Ph.V., Sheveyko A.N., Levashov E.A., Shtansky D.V. // Russian J. Non-Ferrous Metals. 2015. V. 56. P. 540–547.
Kiryukhantsev-Korneev Ph.V., Potanin A.Yu. // Russian J. Non-Ferrous Metals. 2018. V. 59. № 6. P. 698–708.
Kiryukhantsev-Korneev F.V., Lemesheva M.V., Shvyndina N.V. et al. // Protection of Metals and Physical Chemistry of Surfaces. 2018. V. 54. № 6. P. 1147–1156.
Levashov E.A., Kurbatkina V.V., Patsera E.I. et al. // Rus. J. Non. Fer. Met. 2010. V. 51. P. 403–433.
Potanin A.Yu., Zvyagintseva N.V., Pogozhev Y.S. et al. // Int. J. Self-Propag. High-Temp.Synth. 2015. V. 24. P. 119–127.
Kiryukhantsev-Korneev F.V. // Russ. J. Non-Ferr. Met. 2014. V. 55. № 5. P. 494–504.
Kiryukhantsev-Korneev Ph.V. // Protection of Metals and Physical Chemistry of Surfaces. 2012. V. 48. № 5. P. 585–590.
Levashov E.A., Shtansky D.V., Kiryukhantsev-Korneev Ph.V. et al. // Russian Metallurgy (Metally). 2010. V. 2010. № 10. P. 917–935.
Kiryukhantsev-Korneev F.V., Novikov A.V., Sagalova T.B. et al. // Physics of Metals and Metallography. 2017. V. 118. № 11. P. 1136–1146.
Horling A., Sjolen J., Karlsson L. et al. // J. Vac. Sci. Technol. A. 2002. V. 20. P. 1815–1823.
Chen L., Paulitsch J., Du Y., Mayrhofer P.H. // Surf. Coat. Technol. 2012. V. 206. P. 2954–2960.
Xu Y.X., Chen L., Pei F. et al. // Thin Solid Films. 2014. V. 565. P. 25–31.
Ljungcrantz H., Engström C., Hultman L. et al. // J. Vac. Sci. Technol., A. 1998. V. 16. № 5. P. 3104.
Gao C.K, Yan J.Y., Dong L., Li D.J. // Appl. Surf. Sci., Part B. 2013. V. 285. P. 287–292.
Houška J., Vlček J., Potocký Š., Peřina V. // Diam. Relat. Mater. 2007. V. 16. P. 29–36.
Musil J., Hruby H. // Thin Solid Films. 2000. V. 365. P. 104–109.
Taniguchi S., Fujimoto S., Katoh T., Shibata T. // Mater. High Temp. 2000. V. 17. P. 35–40.
Lee D.B., Nguyen T.D., Kim S.K. // Surf. Coat. Technol. 2009. V. 203. P. 1199–1204.
Ai T., Wang F., Feng X. // Sci. China Ser. E: Technol. Sci. 2009. V. 52. P. 1273–1282.
Hultman L. // Vacuum. 2000. V. 57. P. 1–30.
Shtansky D.V., Gloushankova N.A., Sheveiko A.N. et al. // Surf. Coat. Technol. 2010. V. 205. P. 728–739.
Shtansky D.V., Petrzhik M.I., Bashkova I.A. et al. // Physics of the Solid State. 2006. V. 48. № 7. P. 1301–1308.
Kiryukhantsev–Korneev Ph.V., Sheveiko A.N. // Protection of Metals and Physical Chemistry of Surfaces. 2018. V. 54. № 5. P. 963–968.
Дополнительные материалы отсутствуют.
Инструменты
Физикохимия поверхности и защита материалов