Физикохимия поверхности и защита материалов, 2021, T. 57, № 6, стр. 624-630
Повышение устойчивости к коррозии пассивирующихся металлов путем электрохимического нанесения локальных наноразмерных покрытий
А. Ф. Дресвянников 1, *, А. Н. Ахметова 1, **, А. Е. Денисов 1
1 Казанский национальный исследовательский технологический университет
420015 Казань, ул. Карла Маркса, 68, Республика Татарстан, Россия
* E-mail: a.dresvyannikov@mail.ru
** E-mail: akhmetovaanna18@gmail.com
Поступила в редакцию 20.04.2021
После доработки 12.07.2021
Принята к публикации 13.07.2021
Аннотация
Предложен способ повышения устойчивости пассивирующихся металлов (в частности, нержавеющих сталей) к коррозии, основанный на использовании принципа катодного легирования путем электролитического нанесения локальных палладиевых нанопокрытий. Установлено, что потенциал коррозии образцов стали AISI 321 в растворе 0.1 М NaCl, электрохимически обработанных при плотности тока 1 мкА/см2 и частоте 0.06 Гц в хлоридсодержащих растворах с 0.1% Pd2+, смещается в сторону более положительных значений почти на 150 мВ. Также методами растровой электронной микроскопии и Оже-спектроскопии показано, что в процессе электрохимической поляризации имеет место осаждение на поверхности стали AISI 321 субиндивидов новой фазы (Pd) c размерами порядка 5–80 нм, формирование которых и обусловливает облагораживание потенциала исследуемых образцов. Установлено, что наибольшее скопление субиндивидов новой фазы (Pd) наблюдается на участках, имеющих искусственно созданные дефекты поверхности (царапины).
ВВЕДЕНИЕ
При защите пассивирующихся металлов от коррозии в агрессивных средах применяется метод катодного легирования нержавеющих сталей, титана, его сплавов и других пассивирующихся металлов, получивший подтверждение и развитие в работах Н.Д. Томашова, Стерна, Фишера, Цвикера, Грина, Шлейхера, Рюдигера и др. Суть катодного легирования заключается в повышении эффективности катодных процессов в пассивирующихся системах, в результате чего потенциал системы смещается в сторону положительных значений, и она переходит в пассивное состояние. В качестве катодных легирующих добавок применяют небольшие количества (0.1–0.5%) палладия, платины, рутения и др. [1].
Основным условием достижения положительного эффекта при катодном легировании сплава является необходимость смещения его потенциала в данных условиях коррозии в область устойчивой пассивности, т.е. в область между потенциалами полной пассивации (Епп) и транспассивности (Ет) или питтингообразования (Епт).
Эффективность различных металлов, применяемых в качестве катодных добавок, различна. Чем более положителен стационарный потенциал металла катодной добавки и чем меньше его катодная поляризуемость, тем более эффективно пассивирующее действие. Меньшей катодной поляризуемости будет соответствовать меньшее перенапряжение катодного деполяризующего процесса (например, перенапряжение выделения водорода в условиях коррозии и меньшая склонность к повышению перенапряжения во времени, вследствие, например, наводороживания) [2].
Модифицирование пассивирующихся сплавов добавками катодноактивного электроположительного металла (Pd, Pt, Ru) оказывает сильное влияние на повышение пассивируемости и коррозионной стойкости даже при малом содержании катодного компонента в сплаве (доли процента). Такой эффект катодных добавок объясняется электрохимическим механизмом действия добавок и накоплением электроположительного легирующего элемента в начальный период активной коррозии на поверхности сплава.
Повышение концентрации катодного компонента на поверхности сплава в начальный период коррозии можно проследить по характеру изменения скорости коррозии этих сплавов во времени. Как правило, в начальный период коррозии катоднолегированные сплавы имеют более высокую скорость коррозии. Однако, после обогащения поверхности благородным металлом в количестве, необходимом для пассивации в исследуемых условиях, происходит резкое снижение скорости коррозии. Электронномикроскопическим методом установлено, что накопление на поверхности сплава легирующего компонента (Pd) происходит не в виде сплошного слоя, а в виде отдельных малых частиц [2].
В патентной литературе, например, [3], описаны и другие методы защиты пассивирующихся металлов от коррозии путем легирования малой площади поверхности (не более 1%) металлами семейства платины. Поверхностное легирование осуществляется разными способами [4], среди которых – облучение поверхности ионами металлов, обладающих высокой энергией [5], либо с помощью сварки, либо путем нанесения локальных покрытий из газовой фазы. Все эти методы энергозатратны и предполагают использование специализированного уникального оборудования, что препятствует широкому применению подобных подходов.
В этой связи задачей настоящего исследования является разработка простого и надежного способа поверхностного легирования, заключающегося в осаждении наноразмерных точечных покрытий из благородных металлов, например, палладия. Функция палладия заключается в снижении перенапряжения выделения водорода до значений, соизмеримых с таковыми на чистом палладии, и тем самым, смещению потенциала всей системы в область пассивации стали [6]. По данным ряда авторов [7] на защищаемом металле образуется слой пассивирующегося оксида, самопроизвольно регенерирующийся при его повреждении. Кроме того, атомы палладия способны выполнять функцию донора электронов в полупроводниковом пассивирующемся оксиде, образующемся на поверхности металла в коррозионной среде.
ЭКСПЕРИМЕНТАЛЬНАЯ ЧАСТЬ
В качестве пассивирующегося металла использовали высоколегированную хромоникелевую сталь аустенитного типа марки AISI 321.
Образцы стали размером 50 × 20 мм и толщиной 1 мм обезжиривали в стандартном растворе химического обезжиривания, промывали дистиллированной, далее – бидистиллированной водой.
Электрохимические исследования проводили в стандартной электрохимической ячейке ЯСЭ-2 при температуре 20 ± 1°С. В качестве рабочей среды использовали 0.1 М раствор хлорида натрия с введением в него хлорида палладия в количествах, не превышающих сотые доли процента. Раствор готовили из реактивов квалификации “х. ч.” на бидистиллированной воде. В качестве электрода сравнения использовали хлоридсеребряный электрод марки ЭВЛ – IМЗ; вспомогательным электродом служил проволочный платиновый электрод. Экспериментальная установка состояла из потенциостата – гальваностата IPC – Pro, генератора сигналов специальной формы Г6-27 и персонального компьютера. Исследуемые образцы поляризовали анодным током плотностью 1 мкА/см2 с наложением синусоидальной составляющей с частотой, кратной 0.01 Гц. Для контроля динамики процесса фиксировали изменение потенциала исследуемого электрода во времени. После обработки в указанном режиме, образцы тестировали на предмет оценки коррозионных свойств посредством поляризационных измерений в растворе 0.1 M NaCl [8]. Все измеренные в настоящем исследовании значения электрохимического потенциала приведены относительно хлоридсеребряного электрода сравнения.
Морфологию поверхности исследуемых образцов, элементный состав поверхности и приповерхностных слоев, распределение элементов по глубине определяли методами растровой электронной микроскопии, Оже-электронной спектроскопии с использованием Оже-микрозонда JAMP-9500F (JEOL) в соответствии с методикой ASTM E 827 08. Режим исследования: ускоряющее напряжение до 10 кВ; ток первичного электронного пучка 5 × 10–10 А; пространственное разрешение (диаметр электронного пучка) – не хуже 0.01 мкм; давление в аналитической камере – не ниже 1 × 10–9 мм рт. ст. (сверхвысокий вакуум). Из исследуемых объектов вырезали прямоугольные образцы размером 17 × 27 мм (образец стали AISI 321-№ 1 – свидетель, не подвергнутый электрохимической обработке) и 18 × 23 мм (образец № 2). Перед проведением исследований образцы промывали в ультразвуковой ванне в ацетоне (“о. с. ч. 9-5”) и, далее, в изопропиловом спирте (“х. ч.”), после чего высушивали в потоке сухого воздуха.
РЕЗУЛЬТАТЫ И ИХ ОБСУЖДЕНИЕ
Поляризация слабыми токами применена исходя из фактов протекания локальных процессов на поверхности пассивирующегося металла в хлоридсодержащих средах, приводящих к появлению локальных субмикронных очагов растворения [9], а использование низкочастотной составляющей обусловлено предположением возникновения в “катодный” полупериод (максимум значений тока которого характеризуется наиболее отрицательными значениями), в растворах, содержащих ионы благородного металла, фаз нулевой размерности, представляющих собой группы атомов металла, сконцентрировавшихся вокруг микроскопических дефектов (изломов, поверхностных дислокаций и пр.). Последнее, согласно литературным данным, обусловливает сдвиг потенциала в область более положительных значений [10].
Хронопотенциограммы, полученные в процессе поляризации образцов стали AISI 321 в рабочем растворе, представлены на рис. 1. Очевидно, что при соблюдении вышеуказанных условий наблюдается колебательное изменение потенциала и имеет место смещение среднего тренда зависимости потенциал–время (E–t) в сторону более положительных значений. Это косвенно свидетельствует об изменении поверхностного слоя стали и, в частности, о формировании поверхностных структур, обеспечивающих повышение устойчивости поверхности металла к коррозии. Наложение переменной составляющей тока, по нашему мнению, способствует вытравливанию поверхностных примесей или нивелированию потенциала поверхности в полупериод, максимум значений тока которого наиболее положителен, и локальному осаждению благородного металла (Pd) в противоположный полупериод.
Рис. 1.
Хронопотенциограммы стали AISI 321, полученные в растворе состава: 0.1 M NaCl + 0.01% PdCl2 при поляризации током плотностью j = 1 мкА/см2 и частотой: (а) f = 0.03 Гц в течение τ = 3600 c, (б) f = = 0.06 Гц в течение τ = 3600 c.
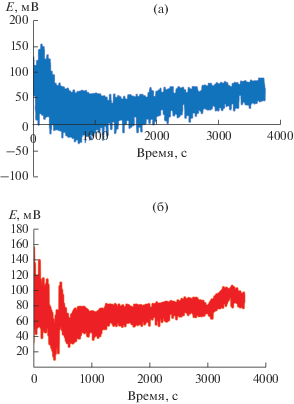
После электрохимической поляризации стали, характеризуемой указанными параметрами, проводили оценку коррозионной стойкости модифицированных образцов посредством измерений потенциала коррозии этих образцов в растворе 0.1 М NaCl. Результаты эксперимента представлены в табл. 1.
Таблица 1.
Результаты эксперимента
№ п/п | Частота, Гц | Плотность тока, мкА/см2 | Время поляризации, с | Еcor образца сравнения, мВ | Еcor образца с модифицированной поверхностью, мВ |
---|---|---|---|---|---|
1 | 0.03 | 1.0 | 600 | –120 | –110 |
2 | 0.03 | 3600 | –123 | –50 | |
3 | 0.06 | 3600 | –130 | +15 |
Установлено, что образцы, поляризованные при плотности тока 1 мкА/см2 и частоте 0.06 Гц, имеют потенциал свободной коррозии Ecor (измерения проводили в соответствии с ГОСТ 9.912-89) в хлоридсодержащем растворе, равный +15 мВ, что почти на 150 мВ положительнее значения, зафиксированного в случае образцов – свидетелей стали AISI 321, не подвергавшихся электрохимической обработке.
Исследуемые образцы были аттестованы методами растровой электронной микроскопии и Оже-спектрометрии. На рис. 2 представлены микроизображения поверхности исследуемых объектов: стали AISI 321 (№ 1 – образец-свидетель, № 2 – образец, подвергнутый электрохимической обработке) с указанием зон (точек) анализа.
Рис. 2.
Микроизображение исследуемых образцов: (а) образец № 1. Зоны (точки) анализа: № 1, 2 и 3. Диаметр зон (точек) анализа: зона 1 – 1 мкм, зона 2 – 30 мкм (расфокусированный пучок), точка 3 – ≤0.01 мкм (сфокусированный пучок), изображение во вторичных электронах (SEI). Приборное увеличение ×2000; (б) образец № 2. Зоны (точки) анализа № 1, 2 и 3. Диаметр зон анализа: зоны 1 и 2 – 1 мкм, зона 3 – 60 мкм (расфокусированный пучок), изображение поверхности во вторичных электронах (SEI). Приборное увеличение ×1000.
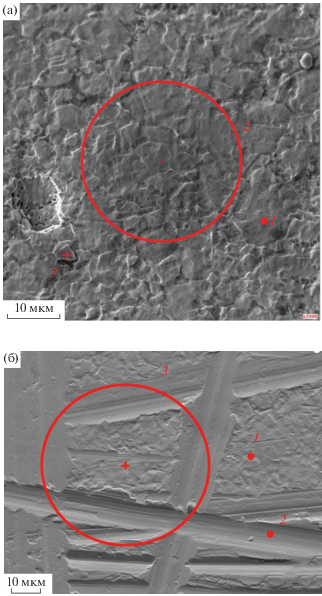
Результаты исследований образца № 1 демонстрируют наличие на поверхности в зонах анализа 1–3 до ионного травления (в порядке убывания амплитуды Оже-пиков) – элементов: O, C, Fe, Cr, Ni, S, P, Ti, N, причем источниками O, C, N являются адсорбированные молекулы атмосферных газов и оксидные/карбидные/нитридные включения и пленки на поверхности образца; Fe, Cr, Ni, Ti – элементы, составляющие основу нержавеющей стали AISI 321.
Другая картина наблюдается при анализе образца, подвергнутого электрохимической обработке. Имеет место “увеличение” концентрации Pd (даже по истечению 5 с ионного травления). Одной из вероятных причин является поверхностная диффузия (миграция) атомов Pd, выравнивающая концентрацию (плотность) атомов в верхнем поверхностном слое. Так, в зонах анализа 1–3 на гладком участке поверхности стали до ионного травления (в порядке убывания амплитуды Оже-пиков) присутствуют O, C, Fe, Cr, Ni, S, Pd и, возможно, N, P. Как уже упоминалось выше, O, C, N входят в состав адсорбированных молекул атмосферных газов и оксидных/карбидных/нитридных поверхностных образований (рис. 3а).
Рис. 3.
Оже-электронные спектры поверхности образца № 2: (а) в зонах анализа 1, 2 и 3 до ионного травления, (б) в зоне анализа 2 до и после ионного травления Ar+ (1 и 3 кэВ), (в) в зоне анализа 3 до и после ионного травления Ar+ (1 и 3 кэВ). Расположение зон анализа приведено в соответствии с изображением на рис. 2б.
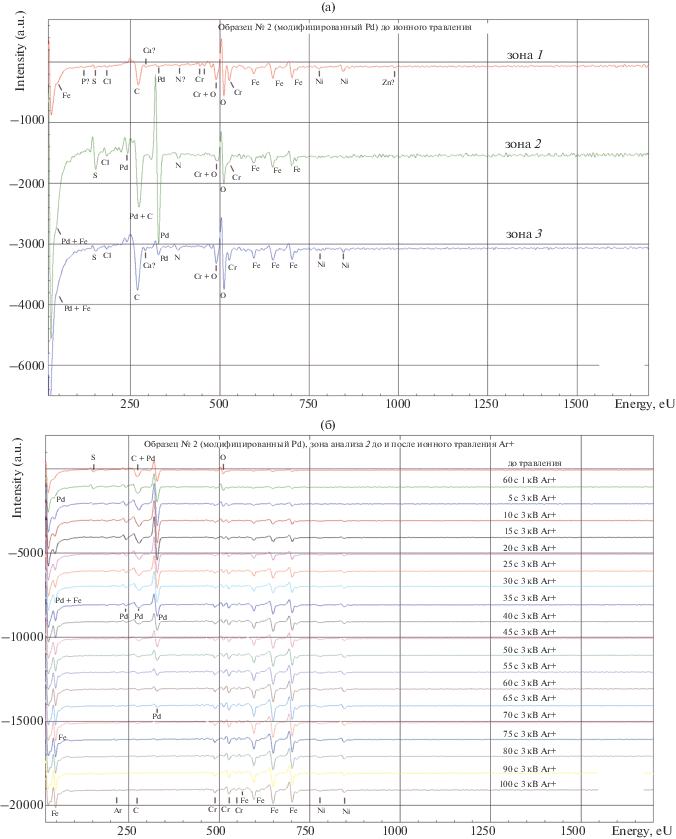
Рис. 3.
Окончание
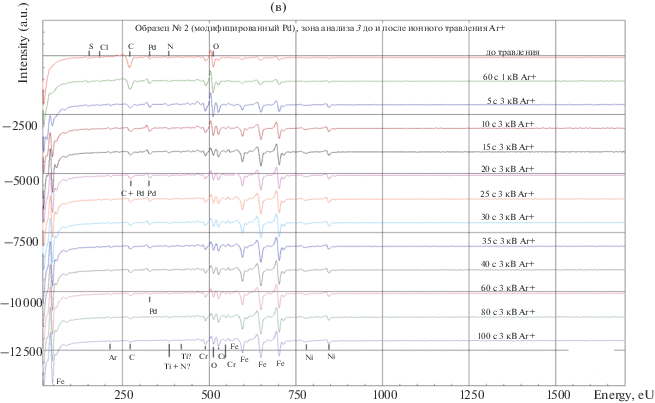
Элементный состав поверхности на гладком и дефектном участках (искусственно нанесенная царапина) в зоне анализа 2 после ионного травления Ar+ в течение 100 с при энергии 3 кэВ (в порядке убывания амплитуды Оже-пиков) следующий: Fe, Cr, Ni, Ar и C, где C – адсорбированные молекулы газов остаточной атмосферы в вакуумной камере спектрометра (CO2, CH4 и др.), с учетом способности углерода накапливаться при воздействии электронного пучка на поверхности большинства материалов (источники: остаточная атмосфера, поверхностная диффузия, внутренние поры и межзеренные границы); Ar – атомы аргона, имплантированные в поверхность при воздействии ионного пучка в процессе ионного травления образца. Изменение концентрации элементов по глубине в соответствии со временем ионного травления можно оценить по спектрам (ориентировочная скорость ионного травления Ar+ нержавеющей стали составляет примерно 20–25 нм/мин, для Pd – около 100–130 нм/мин) (рис. 3б).
Аналогично, можно продемонстрировать элементный состав поверхности интегрально (включая дефектные и гладкие участки) в зоне анализа 3 после ионного травления Ar+ в течение 100 с при энергии 3 кэВ (в порядке убывания амплитуды Оже-пиков): Fe, Cr, Ni, O, Ar, Cu, Ti (рис. 3в).
Результаты распределения концентрации Fe и Pd по глубине (зависимости концентрации элементов от времени травления) в зонах 1 и 2 поверхности модифицированного образца стали представлены на рис. 4. Очевидно, что атомы осаждаемого металла (Pd) концентрируются преимущественно в поверхностном и приповерхностном слоях стального образца. Можно заметить, что концентрация палладия в пределах искусственного созданного дефекта (царапины) существенно выше.
Рис. 4.
Зависимости концентрации Fe и Pd от времени травления (глубины) для образца № 2 (сталь AISI 321, модифицированная Pd) в зонах анализа 1 и 2 (исходная поверхность (1) и дно дефекта (царапина, 2), соответственно).
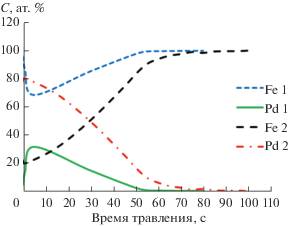
На рис. 5 представлено микроизображение поверхности образца, подвергнутого электрохимической обработке слабым током инфранизкой частоты. Очевидно, что на поверхности формируются субиндивиды новой фазы (Pd) c размерами порядка 5–80 нм, имеющие преимущественно сглаженную форму. Наибольшее их скопление обнаружено на участках, имеющих искусственно созданные дефекты поверхности (царапины).
ЗАКЛЮЧЕНИЕ
Таким образом, на основании результатов экспериментального исследования можно констатировать:
1. Разработан способ поверхностного легирования нержавеющих сталей, основанный на использовании режимов, характеризуемых током плотностью порядка 1 мкА/см2 и частотой, кратной Х ×10–2 Гц (Х = 0.1–10), реализуемых в хлоридсодержащих средах в присутствии иона благородного металла (Pd2+).
2. Установлено, что образцы стали AISI 321, поляризованные при плотности тока 1 мкА/см2 и частоте 0.06 Гц имеют потенциал коррозии в хлоридсодержащем растворе (0.1 М NaCl), равный +15 мВ, что почти на 150 мВ положительнее значения, полученного на образцах – свидетелях, не подвергавшихся электрохимической обработке.
3. Показано, что облагораживание потенциала исследуемых образцов обусловлено присутствием на поверхности стали AISI 321 субиндивидов новой фазы (Pd) c размерами порядка 5–80 нм, имеющих сглаженную форму, причем наибольшее их скопление наблюдается на участках, имеющих искусственно созданные дефекты поверхности (царапины).
Работа выполнена на оборудовании ЦКП “Наноматериалы и нанотехнологии” Казанского национального исследовательского технологического университета.
Список литературы
Рачев Х., Стефанова С. Справочник по коррозии / Пер. с болг. Нейковского С.И. под ред. и с предисл. Н.И. Исаева. М.: Мира, 1982. 520 с.
Томашов Н.Д., Чернова Г.П. Коррозия и коррозионностойкие сплавы. Серия “Успехи современного металловедения”. М.: Металлургия, 1973. 232 с.
Граумэн Джеймс С., Миллер Джеймс Дж., Эдамс Рой И. / Пат. 2336366 Рос. Федерация, МПК C23C 26/00, С23С 16/06, С23С 4/08, С23С 14/14, С23F 13/00 //; заявл. 24.09.2003, опубл. 10.04.2005. Бюл. № 29. С. 8.
Будовских Е.А., Карпий С.В., Громов В.Е. // Известия РАН. Серия физическая. 2009. Т. 73. № 9. С. 1324–1327.
Братушка С.Н., Маликов Л.В. // Вопросы атомной науки и техники. Серия: Вакуум, чистые материалы, сверхпроводники. 2011. № 6(19). С. 126–140.
Томашов Н.Д., Ташлыков И.С., Жильцова О.А. и др. // Защита металлов. 1987. Т. 23. № 5. С. 791–795.
Tanga J., Zhanga Zh.,Wanga Y. et al. // Corrosion Science. 2018. V. 135. P. 222–232.
Anantha K.H.,Ornek C., Ejnermark S. et al. // J.Electrochemical Society. 2017. V. 164(4). P. 85–93.
Розенфельд И.Л. Коррозия и защита металлов (локальные коррозионные процессы). М.: Металлургия, 1970. 448 с.
Budevski E., Staikov G., Lorenz W. // J. Electrochimica Acta. 2000. V. 45. P. 2559–2574.
Дополнительные материалы отсутствуют.
Инструменты
Физикохимия поверхности и защита материалов