Физикохимия поверхности и защита материалов, 2021, T. 57, № 6, стр. 631-639
Особенности коалесценции золота на поверхности различных носителей в ходе каталитического окисления CO
И. В. Лукиянчук 1, *, М. С. Васильева 1, 2, А. А. Сергеев 3, А. В. Непомнящий 3, М. М. Серов 4, Б. Л. Крит 4
1 Федеральное государственное бюджетное учреждение науки Институт химии Дальневосточного отделения Российской академии наук
690022 Владивосток, пр-т 100‑летия Владивостока, 159, Россия
2 Федеральное государственное автономное образовательное учреждение высшего образования
Дальневосточный федеральный университет
690922 Приморский край, Владивосток, о. Русский, п. Аякс, 10, Россия
3 Федеральное государственное бюджетное учреждение науки Институт автоматики и процессов управления Дальневосточного отделения Российской академии наук
690041 Владивосток, ул. Радио, 5, Россия
4 Федеральное государственное бюджетное образовательное учреждение высшего образования
Московский авиационный институт (национальный исследовательский университет)
125993 Москва, Волоколамское шоссе, 4, Россия
* E-mail: lukiyanchuk@ich.dvo.ru
Поступила в редакцию 09.06.2020
После доработки 20.06.2020
Принята к публикации 03.07.2020
Аннотация
На поверхность различных носителей методом электронно-лучевого напыления были нанесены ультратонкие (толщиной 10 нм) пленки золота. В качестве носителей использовали волокна из титана и циркония, сформированные методом экстракции висящей капли расплава, и титановые пластины, подвергнутые плазменно-электролитическому оксидированию. Композиты Au/Zr, Au/Ti (на основе волокон) и Au/TiO2/Ti (на основе оксидированного титана) были протестированы в реакции окисления CO. Показано, что нанесение золота увеличивает каталитическую активность волокон из титана, циркония, но мало влияет на активность оксидированного титана. Установлено, что при контакте с газовой смесью при температурах до 500°С частицы золота собираются в капли, размер и число которых зависят от природы металла и толщины оксидной пленки на его поверхности.
1. ВВЕДЕНИЕ
Катализаторы на металлических носителях представляют практический интерес вследствие их высоких механической прочности и теплопроводности, возможности создания на их основе монолитов с более тонкими стенками, увеличенным числом ячеек и меньшим перепадом давлений, а также реакторов для проведения сопряженных реакций [1, 2]. Дизайн катализаторов, носителей и каталитических фильтров в виде изготовленных из фольги сотовых структур [3], проволочных сеток [4, 5], в том числе тканных и вязаных [6, 7] волокнистых материалов, металлических ват [8], имеющих значительную геометрическую поверхность и низкое гидродинамическое сопротивление потоку газов или жидкостей, позволяет проводить процессы при малых временах контакта, достигая при этом полного превращения реагентов. Эти качества создают преимущества таким катализаторам по сравнению с традиционными монолитными, гранулированными или порошковыми.
К одним из технологичных способов получения неорганических волокон и пористых материалов на их основе относится метод высокоскоростного затвердевания расплава и его разновидность – метод экстракции висящей капли расплава (ЭВКР) [9]. Используя точное регулирование подачи материала в зону плавления и управляя адгезионным взаимодействием расплава и диска, этот метод позволяет формировать длинномерные волокна с эквивалентным диаметром 30–80 мкм, а также дискретные частицы длиной 3–10 мм или пористые листовые нетканые материалы [9]. Благодаря бестигельной плавке можно получать волокна из тугоплавких и химически активных металлов, а также жаростойких, коррозионностойких и трудно-деформируемых сталей и сплавов [10–12]. Поскольку вытягивание волокна из расплава происходит при высоких скоростях охлаждения (до 106 К/с), то на поверхности волокон наблюдается большое число дефектов и повышенная концентрация легирующих или примесных элементов, что благоприятно для применения в катализе. По данным [13, 14] применение методов высокоскоростного затвердевания расплавов приводит к повышению их каталитической активности по сравнению с исходными массивными сплавами на основе никеля или железа. В работе [15] исследована каталитическая активность в окислении CO ряда волокнистых образцов, полученных методом ЭВКР. Из них наименьшей активностью обладали титановые образцы. В работе [16] было показано, что активность титановых волокон можно увеличить с помощью нанесения на их поверхность каталитически активных компонентов, например, меди.
В последние годы большое внимание уделяют получению и исследованию Au-содержащих катализаторов [17, 18]. Такие катализаторы с нанесенными на поверхность оксидных носителей наноразмерными частицами благородных металлов показывают активность в ряде окислительно-восстановительных реакций уже при комнатных температурах. Однако при повышенных температурах эти частицы спекаются, что приводит к увеличению их размеров, снижению площади их поверхности и активности катализатора. Поскольку золото имеет более низкую температуру плавления и меньшее сродство к оксидам металлов по сравнению с Pd и Pt, его довольно трудно нанести в виде наночастиц на подложки из оксидов металлов методами импрегнирования [17]. В связи с этим, мы наносили на поверхности металлических волокон тонкую золотую плeнку.
Для нанесения золотых нанопленок на поверхность металлических волокон, мы использовали метод электронно-лучевого напыления, который позволяет точно контролировать толщину нанесенного слоя, совместим с подложками большой площади, может использоваться для целого ряда материалов, включая чистые металлы, сплавы и оксидные полупроводники, и может применяться для разработки различных устройств [19, 20].
Такие же слои золота были нанесены на оксидный слой, предварительно сформированный на поверхности титана методом плазменно-электролитического оксидирования (ПЭО). Суть метода – в электрохимическом оксидировании вентильных металлов и сплавов при напряжениях, вызывающих искровые и микродуговые электрических разряды на их поверхности [21, 22].
Следует отметить, что из-за контакта с кислородом воздуха на поверхности металлических волокон всегда присутствует очень тонкая (толщиной 5–50 нм) естественная оксидная пленка [23, 24]. Толщина оксидного слоя, сформированного методом ПЭО, составляет десятки микрон [21, 22]. Логично предположить, что толщина оксидного слоя способна оказывать влияние на адгезию золота и активность получаемых композитов.
Целью данной работы является получение каталитически активных композитов на основе волокон из титана, циркония, а также ПЭО-слоев на титане, путем нанесения на их поверхность ультратонких пленок золота методом электронно-лучевого испарения, а также сравнение особенностей коалесценции наночастиц золота на поверхности оксидированного титана и металлических волокон в процессе каталитического окисления СО.
2. МАТЕРИАЛЫ И МЕТОДЫ
Композиты Au/Zr, Au/Ti готовили на основе волокон, полученных методом ЭВКР, а композит Au/TiO2/Ti – на основе титановой пластинки, предварительно оксидированной методом ПЭО.
Волокна из титана и циркония предварительно не обрабатывали, их поверхность была покрыта естественной оксидной пленкой. Пластинки технического титана ВТ1–0 размером 2.0 × 2.0 × 0.1 см механически шлифовали, затем химически полировали в смеси концентрированных кислот HF : HNO3 = 1 : 3 при 60–80°С в течение 2–3 с, промывали дистиллированной водой и сушили на воздухе.
ПЭО-обработку титановых пластин проводили при эффективной плотности анодного тока 0.1 А/см2 в течение 10 мин в водном электролите, содержащем 0.1 моль/л Na2SO4. Электрохимическая ячейка для формирования ПЭО-слоев представляла собой термостойкий стакан объемом 1000 мл. Катодом служил полый змеевик из нержавеющей стали, через который пропускали воду для охлаждения электролита. В качестве источника питания использовали тиристорный преобразователь ТЕР4‑100/460Н (Россия) с униполярным импульсным током. Электролит перемешивали с помощью магнитной мешалки. Температура раствора в ходе ПЭО не превышала 35°С.
Слои золота толщиной ~10 нм были нанесены как на металлические волокна, так и на ПЭО-покрытие, используя систему VACLEADER для испарения электронным пучком (ADVAVAC Surface Technologies). Во время испарения Au давление, максимальная температура и средняя скорость осаждения Au в вакуумной камере составлял ~0.45 Па, 54°C и 1.5 А/с, соответственно. Отметим, что в результате такой операции золото наносилось только на одну сторону титановой пластины и на те участки металлических волокон, которые были обращены к мишени.
Измерения толщины d металлических волокон проводили помощью микрометра, среднее значение рассчитывали на основании 5–15 измерений. Удельную поверхность Sуд рассчитывали геометрическим методом по формуле: Sуд = 4/ρd, где ρ – плотность сплава, полагая, что площадь торцов волокон много меньше их боковой поверхности. Допускали, что нанесение золота на поверхность образцов не изменяет их площадь, и покрытая золотом поверхность составляет ½ от общей поверхности волокон. Диаметр металлических волокон, плотность сплава, расчетная удельная геометрическая поверхность приведены в табл. 1.
Таблица 1.
Характеристики образцов и результаты каталитических испытаний до и после напыления золота на их поверхность
Образец | l, см | d, мм | ρ, г/см3 | Sуд. геом, см2/г | m, г | S, см2 | SAu, см2 | T50, °C | X500, % | ||
---|---|---|---|---|---|---|---|---|---|---|---|
1 | 2 | 1 | 2 | ||||||||
Au/Zr | 0.4108 | 50.5 | 25.3 | $\frac{{450}}{{431.4}}$ | $\frac{{452.9}}{{456.8}}$ | 66.7 | 60.00 | ||||
Zr | 10–20 | 0.05 ± 0.01 | 6.506 | 123 | 0.4146 | 51.0 | 25.5 | Не достигается | 16.9 | – | |
Au/Ti | 0.4023 | 50.4 | 25.2 | $\frac{{478.0}}{{450}}$ | $\frac{{435.5}}{{424.1}}$ | 59.3 | 64.4 | ||||
Ti | 10–30 | 0.07 ± 0.02 | 4.505 | 125 | 0.4461 | 55.9 | 28.0 | Не достигается | 4.0 | – | |
Au/TiO2/Ti | 1.2431 | 11.5 | 5.8 | Не достигается | 8.2 | – |
Примечания: l – длина волокон; d – диаметр волокон; Sуд. геом = 4/ρd – удельная геометрическая поверхность Zr и Ti волокон; m – масса образца в реакторе; S – геометрическая площадь поверхности образца в реакторе; SAu = 1/2 S – геометрическая площадь поверхности, покрытой золотом; T50 – температура полуконверсии CO; X500 – конверсия CO при 500°С.
Толщину ПЭО-покрытий определяли как среднее значение из не менее чем 10 измерений на обеих сторонах образца с помощью вихретокового толщиномера ВТ201 (Россия). Рентгенограммы покрытых золотом титановых образцов с ПЭО-покрытиями были получены на рентгеновском дифрактометре Bruker D8 ADVANCE (Германия) в СuКα-излучении, используя съемку с накоплением сигнала при инкрементном сканировании каждые 0.02о и времени накопления сигнала в точке 15 с. При выполнении рентгенофазового анализа (РФА) использовали программу поиска “EVA” с банком данных “PDF-2”. Выполнить РФА образцов спрессованных волокон не представлялось возможным в виду большого количества шумов, возникающих из-за их неровной поверхности.
Данные о морфологии поверхности и элементном составе образцов получали с помощью сканирующего электронного микроскопа (СЭМ) высокого разрешения Hitachi S5500 (Япония), оснащенного приставкой для энергодисперсионного рентгеноспектрального анализа (Thermo Scientific (США). Глубина проникновения зондирующего луча ~1 мкм. Средний элементный состав композиций определяли при сканировании не менее пяти площадок размерами ~25 × 25 мкм.
Каталитическую активность образцов волокон в реакции окисления CO в CO2 оценивали на основании зависимости конверсии CO от температуры аналогично [15]. По графикам зависимости X = f(T) рассчитывали значения температур полуконверсии T50 и конверсии при 500°С X500. Навески металлических волокон для каталитических испытаний подбирались таким образом, чтобы площадь их поверхности составляла около 50 см2 (табл. 1). Поскольку диаметр реактора составлял около 0.8 см, титановую пластину с нанесенным слоем золота (Au/TiO2/Ti), разрезали на 3 части перед тем, как поместить в реактор. Во всех случаях полагали, что геометрическая площадь покрытой золотом поверхности составляла половину их общей площади. Подготовленные образцы (волокна или пластину) помещали в реакционную зону трубчатого кварцевого реактора между слоями кварцевого песка. Условия каталитических испытаний: проточная каталитическая установка BI-CATflow 4.2(A) (Институт катализа СО РАН, Россия), состав исходной газовой смеси: 5% CO + + воздух, скорость потока газа через реактор объемом 3 см3 – 50 мл/мин. При каждой температуре образец предварительно выдерживали 20 мин для установления равномерного распределения температуры по объему образца, после чего выполняли измерения концентраций СО и CO2 на входе и выходе из реактора, используя ИК-газоанализатор Тест-1 (ООО Бонэр, Россия).
3. РЕЗУЛЬТАТЫ И ОБСУЖДЕНИЕ
Внешний вид волокон и ПЭО-покрытий после нанесения золота показан на рис. 1. Поскольку волокна и ПЭО-покрытия морфологически неоднородны, после нанесения золота методом электронно-лучевого испарения на их поверхности образуются отдельные частицы или гранулы. Анализ данных на рис. 1д показывает, что гранулы обогащены золотом. Учитывая, что при выполнении энергодисперсионного анализа затрагиваются также и нижележащие слои образцов, можно уверенно утверждать, что гранулы – это частицы золота. Наличие металлического золота на поверхности ПЭО-покрытий подтверждается методом РФА (рентгенограмма 1 на рис. 2). Усредненный состав поверхности и гранул приведен в табл. 2. Во всех случая в гранулах концентрация золота выше, чем на поверхности. При этом в гранулах на поверхности волокон концентрация кислорода выше. Возможно, золото собирается в капли на дефектных участках поверхности волокон, например, на участках с более толстой оксидной пленкой (естественной или образованной при охлаждении волокон в процессе их получения).
Рис. 1.
СЭМ-изображения покрытых золотом волокон и ПЭО-покрытий: Au/Zr (а, г), Au/Ti (б, д), Au/TiO2/Ti (в) и данные энергодисперсионного анализа для участков 1, 2 и 3 на поверхности волокон Au/Ti (д).
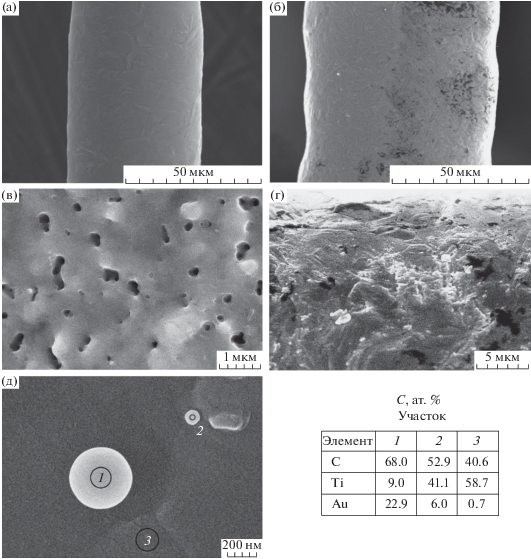
Таблица 2.
Средние составы поверхности и гранул для образцов Au/Zr, Au/Ti и Zu/TiO2/Ti до и после каталитических испытаний согласно данным энерго-дисперсионного анализа
Образец | Исходные образцы | После катализа | ||
---|---|---|---|---|
поверхность | гранулы | поверхность | гранулы | |
Au/Zr | 58.8 C | 60.0 C | 25.8 C | 29.9 C |
4.0 N | 1.5 N | |||
11.8 O | 19.5 O | 58.2 O | 57.1 O | |
0.5 P | 0.2 P | |||
24.8 Zr | 18.5 Zr | 16.0 Zr | 12.4 Zr | |
0.1 Au | 0.3 Au | 0.1 Au | 0.7 Au | |
Au/Ti | 20.0 C | 29.8 C | 17.8 C | 22.7 C |
2.9 N | 4.6 N | 5.8 N | ||
46.3 O | 31.2 O | 32.5 O | ||
79.2 Ti | 46.4 Ti | 37.5 Ti | ||
0.8 Au | 3.1 Au | 0.04 Au | 1.4 Au | |
Au/TiO2/Ti | 11.0 С | 5.6 С | 22.7 C | |
2.6 N | 3.5 N | 5.8 N | ||
52.5 O | 50.2 O | 55.6 O | 32.5 O | |
32.2 Ti | 37.8 Ti | 43.3 Ti | 37.5 Ti | |
1.7 Au | 2.9 Au | 1.1 Au | 1.4 Au |
Результаты каталитических испытаний в реакции окисления CO в CO2 для образцов с напыленной золотой пленкой и без приведены на рис. 3 и в табл. 1. Отметим изменение цвета циркониевых и титановых волокон в ходе каталитических испытаний: циркониевые волокна становятся черными, а титановые – синими. Учитывая температуру нагрева реактора (до 500°С), синий цвет титановых волокон после каталитических испытаний, а также данные работы [25], можно предположить, что толщина термической оксидной пленки, образованной в таких условиях, составляет ~50 нм (5 × 10–8 м). Толщина ПЭО-покрытий, измеренная с помощью вихретокового толщиномера, составляет 5 ± 1 мкм (5 × 10–6 м). То есть заведомо толщина ПЭО-покрытия TiO2 на титане на два порядка больше, чем толщина термической оксидной пленки на титановых волокнах. Циркониевые волокна как с нанесенным золотом, так и без после каталитических испытаний приобретают черный цвет. Согласно данным работы [26] защитная черная оксидная пленка на цирконии представляет собой твердый раствор циркония в ZrO2.
Рис. 3.
Зависимости конверсии от температуры образцов Au/Zr и Zr (а); Au/Ti, Ti и Au/TiO2/Ti (б). Цифры 1 и 2 относятся к первому и второму циклам каталитических испытаний.
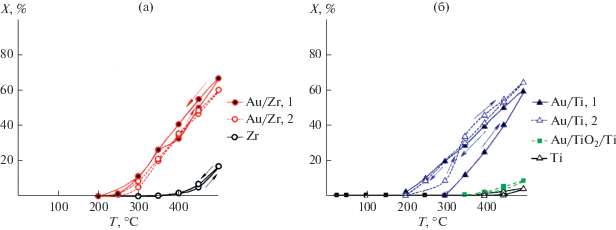
Как видно по кривым зависимости конверсии CO от температуры (рис. 3), напыление золота однозначно увеличивает активность циркониевых (рис. 3а) и титановых волокон (рис. 3б). В первом цикле каталитических испытаний образцы Au/Ti и Au/Zr активируются: температура полуконверсии T50 при понижении температуры уменьшается (табл. 1), наблюдается петля гистерезиса “против часовой стрелки”, при этом образцы Au/Zr активнее, чем Au/Ti. Более высокая активность Au/Zr по сравнению с Au/Ti соответствует более высокой активности исходных волокон без Au-пленки (рис. 3а, 3б, зависимости X = f(T) для образцов Ti и Zr). В втором цикле каталитических испытаний уже титановые образцы активнее, чем циркониевые: для них ниже температуры полуконверсии и выше конверсия при 500°С (Х500). Учитывая, что при каталитических испытаниях происходит окисление волокон, такая ситуация соответствует литературным данным, согласно которым при равном размере и количестве наночастиц на поверхности катализаторы Au/TiO2 активнее, чем Au/ZrO2 [27]. Активность ПЭО-покрытий после напыления золота не высока (рис. 3б): конверсия CO при 500°С не достигает даже 10% (табл. 1). Такая низкая активность образцов Au/TiO2/Ti может быть связана с тем, что их геометрическая поверхность в 4.3 раза меньше по сравнению с волокнами. В то же время если пересчитать X500 для образца Au/TiO2/Ti на площадь поверхности, сравнимую с волокнами (X500 × 4.3 = 35.6%), то и тогда конверсия CO будет почти в 2 раза ниже.
СЭМ-изображения поверхности образцов волокон Au/Ti, Au/Zr, а также плоских образцов Au/TiO2/Ti после каталитических испытаний показывают, что на их поверхности имеются участки с большим количеством белых частиц (рис. 4), обогащенных золотом (табл. 2). Следовательно, в ходе каталитических испытаний, т.е. при высокотемпературном (T = 500°C) взаимодействии с реакционной газовой смесью (CO + CO2 + воздух), нанослои золота на поверхности волокон и ПЭО‑покрытий собираются в капли. При этом, согласно РФА (рентгенограмма 2 на рис. 2), не происходит изменений фазового состава образцов, и золото остается в металлическом состоянии. По данным [28] из-за высокого поверхностного натяжения пленка напыленного золота толщиной 5–100 нм является нестабильной, и в процессе отжига при температурах, когда подвижность атомов металла становится достаточно высокой, превращается в островковую. Причиной коалесценции частиц, образующих пленку, служит более высокое поверхностное натяжение золота по сравнению с адгезией его к оксиду металла основы. Напомним, что на поверхности всех металлических волокон, контактирующих с воздухом, имеется естественная оксидная пленка, а золото обладает слабой адгезией к оксидам металлов, поскольку имеет слабое сродство к кислороду [29], и для него адгезия определяется силами Ван-дер-Ваальса. Адгезия в системе металл–оксид растет с ростом сродства металла пленки (то есть золота) к кислороду. Можно считать, что химическое взаимодействие металла с оксидом тем сильнее, чем менее прочной является связь между атомами металла и кислорода в оксиде [29]. Поскольку связь Zr–O прочнее ($\Delta {{G}_{{{\text{Zr}}{{{\text{O}}}_{{\text{2}}}}}}}$ = –1043 кДж/моль), чем Ti–O ($\Delta {{G}_{{{\text{Ti}}{{{\text{O}}}_{{\text{2}}}}}}}$ = –889 кДж/моль) [30], сродство к кислороду для циркония также выше, чем для титана, то адгезия золота к оксиду титана должна быть выше, чем к оксиду циркония. При равной исходной толщине золотой пленки на титановых и циркониевых волокнах следует ожидать большую степень растекания золота по титану. Учитывая большую толщину оксида титана в ПЭО-покрытии по сравнению с термической пленкой TiO2 на поверхности титановых волокон, можно было бы ожидать его меньшую смачиваемость золотом. Однако, анализ распределения частиц золота по размерам (рис. 5), выполненный на основании отдельных СЭМ-изображений, показывает, что степень заполнения гранулами золота поверхности циркониевых, титановых волокон и ПЭО-покрытия составляет 25, 16 и 24%, соответственно, то есть, вполне сопоставима по величине. Возможно, на степень заполнения в данном случае большее влияние оказывает толщина исходной золотой пленки. В то же время размер и плотность Au-частиц, очевидно, зависят как от материала основы, так и от толщины оксидного слоя. Преимущественный диаметр Au-частиц составляет 11, 14 и 38 нм, а их максимальная плотность (число на единицу поверхности) – 1.3 × 1014, 6.4 × × 1013 и 3.7 × 1012 нм для образцов Au/Zr, Au/Ti и Au/TiO2/Ti, соответственно. То есть, на поверхности титановых и циркониевых волокон золото собирается в капли более мелкого размера, чем на поверхности оксидированного титана, а число этих капель на 1–2 порядка больше. Учитывая размерный фактор, который показывает, что с увеличением размера кластера доля доступных для катализа поверхностных атомов уменьшается [31], следует ожидать, что образцы, на поверхности которых золото собирается в более крупные капли, будут менее активными. Иными словами, меньшая активность образца Au/TiO2/Ti по сравнению с Au/Ti связана не только с меньшей площадью поверхности, но и с образованием более крупных наночастиц золота в ходе каталитических испытаний.
Рис. 4.
СЭМ-изображения поверхности волокон Au/Zr (a, б), Au/Ti (в, г) и композитов Au/TiO2/Ti (д, е) после каталитических испытаний.
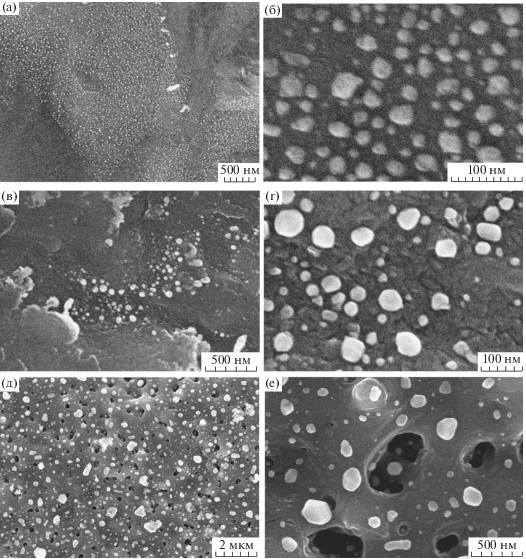
Рис. 5.
Примеры распределения частиц золота по размеру на образцах Au/Zr, Au/Ti (а) и Au/TiO2/Ti (б) после каталитических испытаний.
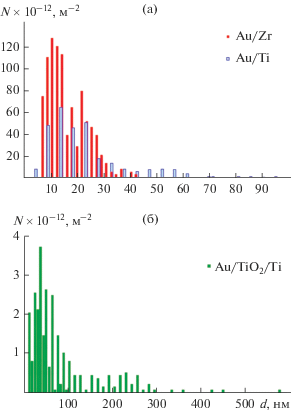
Отметим, что выполненные оценки весьма приблизительны, поскольку исходная толщина золотого слоя на поверхности волокон была не одинакова: если на фронтальной поверхности толщина Au-слоя составляла ~10 нм, то на боковых поверхностях она была от 0 до 10 нм, а на обратной стороне волокон, а также на участках, экранированных другими волокнами, золото отсутствовало. Очевидно, что размер частиц золота, образующихся при отжиге, будет зависеть от исходной толщины золотого слоя на том или ином участке волокна. На участках с более толстым слоем эти частицы могут быть крупнее. На боковых поверхностях волокон, где слой нанесенного золота тоньше, это будут частицы более мелкого размера. Возможно, что основной вклад в каталитическую активность волоконных образцов вносит золото на боковой поверхности волокон. В этом случае даже при спекании оно образует более мелкие частицы.
ЗАКЛЮЧЕНИЕ
Таким образом, в настоящей работе показано, что нанесение золота методом электронно-лучевого напыления увеличивает каталитическую активность металлических волокон из титана и циркония. Контакт с реакционной газовой смесью (CO + CO2 + воздух) при температуре до 500°С приводит к коалесценции золота на поверхности металлических волокон и оксидированного титана, снижению степени ее заполнения до 16–25% за счет образования Au-частиц, размер и число которых зависят от природы металла и толщины оксидной пленки на поверхности металла, толщины и равномерности золотого слоя. Наименьший размер капель и наибольшее их число наблюдаются для волокон из циркония (dmax = 11 нм, Nmax = 1.3 × 1014 м–2), далее следуют волокна из титана (dmax = 14 нм, Nmax = 6.4 × 1013 м–2) и покрытые золотом ПЭО-слои на титане (dmax = = 38 нм, Nmax = 3.7 × 1012 м–2).
Список литературы
Avila P., Montes M., Miro E.E. // Chem. Eng. J. 2005. V. 109. № 1–3. P. 11–36.
Tonkovich A.L.Y., Yang B., Perry S.T. et al. // Catal. Today. V. 120. № 1. P. 21–29.
Tikhov S.F., Chernykh G.V., Sadykov V.A. et al. // Catal. Today. 1999. V. 53. № 4. P. 639–646.
Kierzkowska-Pawlak H., Tracz P., Redzynia W., Tyczkowski J. // J. CO2 Util. 2017. V. 17. P. 312–319.
Li Y.F., Li Y., Yu Q., Yu L. // Catal. Commun. 2012. V. 29. P. 127–131.
Neagoe C., Boffito D.C., Ma Z.N. et al. // Catal. Today. 2016. V. 270. P. 43–50.
Kolodziej A., Lojewska J., Tyczkowski J. et al. // Chem. Eng. J. 2012. V. 200. P. 329–337.
Benito P., de Nolf W., Nuyts G. et al. // ACS Catal. 2014. V. 4. № 10. P. 3779–3790.
Васильев В.А., Митин Б.С., Пашков И.Н., Серов М.М., Скуридин A.A., Лукин A.A., Яковлев В.Б. Высокоскоростное затвердевание расплава (теория, технология и материалы) / Под ред. Митина Б.С. М: СП ИНТЕРМЕТ ИНЖИНИРИНГ, 1998. 400 с.
Борисов Б.В., Серов М.М. // Изв. Вуз.: Порошковая металлургия и функциональные покрытия. 2011. № 4. С. 36–40.
Antsyferov V., Serov M. Manufacturing of a rapid solidification materials and fibers. LAP LAMBERT Academic Publising, 2014, 62 p.
Volfkovich Y.M., Filippov A.N., Bagotsky V.S. Structural properties of porous materials and powders used in different fields of science and technology, in: Eng. Mater. Process. Springer-Verlag London Ltd., 2014, 328 p.
Zhang H.F., Wang A.M., Li H. et al. // Mater. Lett. 2001. V. 48. № 6. P. 347–350.
Fan J.G., Zong B.N., Zhang X.X. et al. // Ind. Eng. Chem. Res. 2008. V. 47. № 16. P. 5918–5923.
Руднев В.С., Лукиянчук И.В., Серов М.М. и др. // Физикохимия поверхности и защита материалов. 2017. Т. 53. № 2. С. 185–191.
Lukiyanchuk I.V., Rudnev V.S., Serov M.M. et al. // Appl. Surf. Sci. 2018. V. 436. P. 1–10.
Haruta M. // Gold Bull. 2004. V. 37. № 1–2. P. 27–36.
Ma Z., Dai S. // ACS Catal. 2011. V. 1. № 7. P. 805–818.
Иванов А., Смирнов Б. // Наноиндустрия. 2012. Т. 36. № 6. С. 28–34.
Sivakumar K., Rossnagel S.M. // J. Vac. Sci. Technol. A. 2010. V. 28. № 4. P. 515–522.
Мамаев А.И., Мамаева В.А. Сильнотоковые микроплазменные процессы в растворах электролитов. Новосибирск: издательство СО РАН, 2005. 255 с.
Эпельфельд А.В., Белкин П.Н., Борисов А.М., Васин В.А., Крит Б.Л., Людин В.Б., Сомов О.В., Сорокин, В.А. Суминов И.В., Францкевич В.П. / Современные технологии модификации поверхности материалов и нанесения защитных покрытий: в 3 т. Т. I: Микродуговое оксидирование. М.; СПб.: Реноме, 2017. 648 с.
Сайфуллин Р.С. Физикохимия неорганических полимерных и композиционных материалов. М.: Химия, 1990. 239 с.
Лаворко П.К. Оксидирование металлов. Киев, М.: Машгиз, 1951. 112 с.
Бай А.С., Лайнер Д.И., Слесарева Е.Н., Цыпин М.И. Окисление титана и его сплавов. М.: Металлургия, 1970. 320 с.
Саркисов Э.С., Чеботарев Н.Т., Невзорова А.А., Зверьков А.И. // Атомная энергия. 1958. Т. 5. № 5. С. 550–553.
Grunwaldt J.D., Kiener C., Wogerbauer C., Baiker A. Preparation of supported gold catalysts for low-temperature CO oxidation via “size-controlled” gold colloids // J. Catal. 1999. V. 181. № 2. P. 223–232.
Naidich Y.V., Gab I.I., Stetsyuk T.V., Kostyuk B.D. Kinetics of dispersion-coagulation during annealing of metal nanofilms deposited onto the surface of non-metallic materials. In: Fesenko O., Yatsenko L. (Eds.) Nanoplasmonics, Nano-Optics, Nanocomposites, and Surface Studies. Springer Proceed. Phys. 2015. V. 167. P. 25–34.
Шауцуков А.Г. // Прикладная физика. 2006. № 5. P. 16–21.
Ахметов Н.С. Общая и неорганическая химия. Учеб. для вузов. 4-е изд., испр. М.: Высш. шк., Изд. центр “Академия”, 2001. 743 с.
Aiken J.D., Finke R.G. // J. Mol. Catal. A-Chem. 1999. V. I45. № 1–2. P. 1–44.
Дополнительные материалы отсутствуют.
Инструменты
Физикохимия поверхности и защита материалов