Физикохимия поверхности и защита материалов, 2021, T. 57, № 6, стр. 660-664
Электрохимическое осаждение и свойства композиционных покрытий никель–хром–оксид графена
В. Н. Целуйкин 1, *, А. С. Джумиева 1, А. В. Яковлев 1, А. С. Мостовой 1
1 Энгельсский технологический институт (филиал) ФГБОУ ВО “Саратовский государственный технический университет им. Ю.А. Гагарина”
413100 Саратовская обл., Энгельс, пл. Свободы, 17, Россия
* E-mail: tseluikin@mail.ru
Поступила в редакцию 21.12.2020
После доработки 29.04.2021
Принята к публикации 11.05.2021
Аннотация
Получены композиционные электрохимические покрытия (КЭП) на основе сплава никель–хром, модифицированные многослойным оксидом графена (ОГ). Изучена кинетика процесса электроосаждения указанных покрытий в потенциодинамическом и гальваностатическом режимах. Исследованы структура и состав КЭП никель–хром–ОГ методами сканирующей электронной микроскопии и лазерного микроспектрального анализа. Установлено, что при включении частиц ОГ в состав электролитических осадков сплава никель–хром возрастает их микротвердость.
ВВЕДЕНИЕ
Электрохимическое осаждение сплавов – один из частных случаев протекания параллельных электродных реакций при их значительном взаимном влиянии. В связи с этим, получение гальванических покрытий сплавами является технически более сложным процессом по сравнению с катодным выделением индивидуальных металлов. Однако, электролитические сплавы, как правило, обладают лучшими эксплуатационными характеристиками чем их отдельные компоненты. Поэтому они находят применение в различных отраслях промышленности. Одними из наиболее распространенных являются сплавы на основе никеля [1–10]. В частности, электролитические сплавы никель–хром, которые используют в качестве твердых и износостойких покрытий [11, 12].
Функциональные свойства гальванических металлов и сплавов можно повысить, внедряя в их матрицу различные дисперсные частицы. Для этого используется метод осаждения композиционных электрохимических покрытий (КЭП) из электролитов-суспензий [13–15]. Эффективность практического применения КЭП в значительной степени определяются природой и свойствами дисперсной фазы. В настоящее время исследуются композиционные покрытия, модифицированные различными углеродными материалами: наноалмазы [16], фуллерен С60 [17], углеродные нанотрубки [18, 19] и др. Отдельный интерес в качестве дисперсных фаз, используемых при получении КЭП, представляют графит и его производные. Графит обладает слоистой структурой, и способен выступать как донор электронов в реакциях с окислителями [20, 21]. При взаимодействии графита с сильными неорганическими кислотами (например, H2SO4) формируется оксид графена (ОГ), представляющий собой графеновые слои с которыми связаны кислородсодержащие функциональные группы (гидроксильные, эпоксидные, карбонильные и др.) [21].
Цель настоящей работы – получить КЭП никель–хром–ОГ, исследовать кинетические закономерности процесса их электроосаждения, структуру и физико-механические свойства данных покрытий.
МЕТОДИКА ЭКСПЕРИМЕНТА
Композиционные покрытия никель–хром–ОГ осаждали на стальную основу (сталь 45) из электролита состава, г/л: NiSO4 ⋅ 7H2O 30; Cr2(SO4)3 ⋅ 6H2O 150; H3BO3 20; (NH4)2SO4 40; оксид графена 10. Процесс осаждения КЭП проводили при температуре 50°С с постоянным перемешиванием электролита. Чистый сплав никель–хром получали из приведенного выше раствора без дисперсной фазы.
Многослойный оксид графена синтезировали электрохимическим способом в гальваностатическом режиме путем анодного окисления порошка природного графита GB/T 3518-95 (Китай) при сообщении емкости 700 А ч/кг. Электролитом служила 83% H2SO4 (о. с. ч.) [21]. Для получения композиционных покрытий использовали фракцию ОГ с размером частиц не более 10 мкм.
Микротвердость осадков по Виккерсу (HV) измеряли с помощью прибора ПМТ-3 (АО “ЛОМО”, Россия). В электролитические осадки статически вдавливалась четырехгранная алмазная пирамида под нагрузкой 100 г. Расстояние между отпечатками составляло не менее двух диагоналей. Форма отпечатка – квадрат. На основании проведенных испытаний определялись величины обеих диагоналей отпечатка. Расчет HV проводился по данным пяти параллельных опытов. Погрешность измерений составляла 3%.
Структурные исследования осуществляли при помощи сканирующего электронного микроскопа со встроенным энергодисперсионным анализатором EXplorer (Aspex, США).
Состав композиционных покрытий изучали методом лазерного микроспектрального анализа [22]. Использовался лазерный спектроаналитический комплекс включающий в себя лазер на Nd : YAG (длина волны 1.06 мкм), работающий в режиме гигантского импульса (длительность импульса 9 нс). Частота следования импульсов 25 Гц. Система регистрации – дифракционный спектрограф ДФС-458С и ПЗС-приставка МИРС (Россия), включающая в себя блок из восьми ПЗС-приемников, плату сопряжения с компьютером и программное обеспечение “SPEKTRAN 8”, позволяющее производить качественный и количественный спектральный анализ, а также математическую обработку данных.
Электрохимические измерения выполняли на импульсном потенциостате P–30J (Элинс, Россия). Потенциалы задавали относительно насыщенного хлоридсеребряного электрода сравнения и пересчитывали по стандартному водородному электроду (с. в. э.).
РЕЗУЛЬТАТЫ И ИХ ОБСУЖДЕНИЕ
Потенциодинамические поляризационные кривые осаждения сплава никель–хром и композиционных покрытий на его основе показывают, что введение оксида графена в электролит сплавообразования облегчает катодный процесс (рис. 1). Сплав никель–хром в присутствии дисперсных частиц выделяется на катоде при менее отрицательных значениях потенциалов. Токи электроосаждения КЭП никель–хром–ОГ увеличиваются по сравнению с покрытиями чистым сплавом, и это свидетельствует о возрастании скорости катодного процесса.
Рис. 1.
Потенциодинамические поляризационные кривые осаждения сплава никель–хром: 1 – без добавки; 2 – совместно с оксидом графена (скорость развертки потенциала Vр = 8 мВ/с).
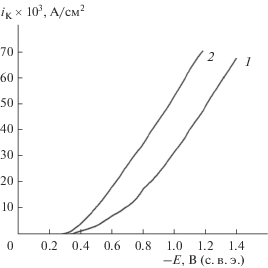
При осаждении сплава никель–хром в гальваностатическом режиме также наблюдается сдвиг потенциалов в положительную сторону при введении в объем электролита дисперсной фазы ОГ (рис. 2), что подтверждает результаты потенциодинамических исследований. В отличие от гальваностатической кривой композиционного покрытия, на кривой чистого сплава в начальный момент времени наблюдаются выраженные скачки потенциала. Это можно объяснить тем, что в отсутствии дисперсии ОГ при включении тока необходимы большие затраты энергии на образование зародышей металла. Частицы оксида графена обладают слоистой структурой с развитой поверхностью [21], на которой может происходить адсорбция катионов из раствора электролита, что приводит к формированию положительного заряда дисперсной фазы. Поэтому перенос ОГ к катоду происходит не только вследствие конвекции, но и, вероятно, под действием электрофоретических сил. Катионы, адсорбированные на ОГ, участвуют в “мостиковом” связывании с электродной поверхностью. Данное связывание ослабляет расклинивающее давление жидкостной прослойки между частицей ОГ и катодом, усиливая адгезию [23–25].
Рис. 2.
Гальваностатические кривые осаждения сплава никель–хром без добавки (1) и совместно с оксидом графена (2) при iK = 7 А дм–2.
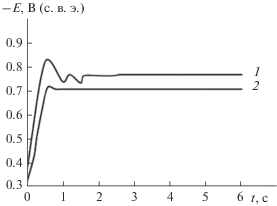
Из начальных участков E, t – кривых, с помощью выражения
Таблица 1.
Значения поляризационной емкости С × 104, Ф/см2 процесса электроосаждения сплава никель–хром и КЭП никель–хром–ОГ
i, А/дм2 | С × 104, Ф/см2 | |
---|---|---|
никель–хром | никель–хром–ОГ | |
20 | 5.0 | 4.3 |
30 | 5.9 | 4.9 |
40 | 7.0 | 5.3 |
50 | 8.0 | 6.4 |
60 | 23.0 | 9.0 |
70 | 43.0 | 14.0 |
80 | 53.0 | 21.0 |
При переходе от сплава никель–хром, не содержащего дисперсной фазы (рис. 3а), к КЭП никель–хром–ОГ (рис. 3б) заметно изменяется микротопография поверхности. Композиционное покрытие обладает упорядоченной мелкозернистой структурой по сравнению с чистым сплавом. КЭП является плотным и равномерным, тогда как на никель–хромовом сплаве без дисперсной фазы наблюдаются микротрещины. Вероятно, на катодной поверхности частицы ОГ выступают в качестве центров кристаллизации, определяя формирование и дальнейший рост электролитического осадка.
Рис. 3.
СЭМ-изображения поверхности сплава никель–хром (а) и КЭП никель–хром–ОГ (б), полученных при iK = 10 А/дм2. Увеличение ×5000.
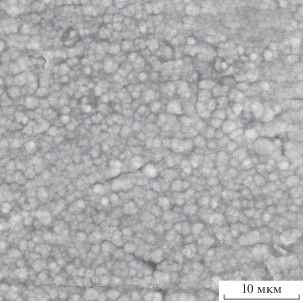
Включение дисперсной фазы в гальваническое покрытие влечет изменение не только его состава и структуры, но также эксплуатационных свойств. Существенный интерес в практическом отношении представляют физико-механические характеристики металлических поверхностей, в частности, их микротвердость. Исследование КЭП никель–хром–ОГ методом лазерного микроспектрального анализа показало, что содержание углерода в них увеличивается по мере продвижения от подложки к поверхности (рис. 4). Кроме того, в поверхностных слоях изученных покрытий возрастает содержание хрома, что должно сказываться на их твердости. Действительно, с ростом катодной плотности тока происходит увеличение микротвердости никель–хромовых сплавов (табл. 2). Вероятно, это обусловлено включением в осадки водорода и гидроксидов, ведущим к деформированию и сжатию кристаллов покрытия. Согласно данным лазерного микроспектрального анализа, с ростом катодной плотности тока происходит обогащение изученных сплавов хромом, что также способствует увеличению их микротвердости. Как отмечалось выше, включение дисперсной фазы оксида графена в никель–хромовые осадки приводит к их уплотнению и формированию мелкокристаллических покрытий (рис. 3а, 3б). Потому имеет место рост микротвердости КЭП никель–хром–ОГ по сравнению с чистыми сплавами (табл. 2), независимо от режима электролиза.
ЗАКЛЮЧЕНИЕ
На основании проведенных исследований установлено, что при введении дисперсии многослойного оксида графена в электролит осаждения сплава никель–хром формируются композиционные покрытия. Включение частиц ОГ в состав никель–хромовых осадков приводит к изменению структуры их поверхности и физико-механических свойств. Значения микротвердости изученных КЭП возрастают с увеличением катодной плотности тока.
Список литературы
Liquin Z., Quinpeng Z., Jianhua L. // Metal Finishing. 2001. V. 99. № 7. P. 28–30.
Meenu S., Grips V.K., Rajam K.S. // J. Applied Electrochemistry. 2008. V. 38. № 5. P. 669–677.
Nayana O., Venkatesha T.V. // Bulletin of Materials Science. 2014. V. 37. № 5. P. 1137–1146.
Целуйкин В.Н., Корешкова А.А. // Физикохимия поверхности и защита материалов. 2016. Т. 52. № 6. С. 650–653.
Torabinejad V., Aliofkhazraei M., Assareh S., Allahyarzadeh M.H., Sabour Rouhaghdam A. // J. Alloys and Compounds. 2017. V. 691. P. 841–859.
Rahmani H., Aliofkhazraei M., Karimzadeh A. // Canadian Metallurgical Quarterly. 2018. V. 57. № 1. P. 99–108.
Целуйкин В.Н., Корешкова А.А. // Физикохимия поверхности и защита материалов. 2018. Т. 54. № 3. С. 293–296.
Beltowska-Lehmana E., Bigosa A., Indykab P., Chojnackaa A., Drewienkiewiczc A., Zimowskid S., Kotd M., Szczerbaa M.J. // J. Electroanalitical Chemistry. 2018. V. 813. P. 39–51.
Rekha M.Y., Srivastava C. // Metallurgical and Materials Transactions A. 2019. V. 50. № 12. P. 5896–5913.
Бурляев Д.В., Тинаева К.Е., Тинаева А.Е., Козадеров О.А. // Гальванотехника и обработка поверхности. 2020. Т. 28. № 3. С. 4–12.
Виноградов С.Н., Синенкова О.К. // Журн. прикладной химии. 2007. Т. 80. № 10. С. 1638–1640.
Целуйкин В.Н. // Неорганические материалы. 2019. Т. 55. № 7. С. 702–704.
Low C.T.J., Wills R.G.A., Walsh F.C. // Surface & Coatings Technology. 2006. V. 201. № 1–2. P. 371–383.
Целуйкин В.Н. // Физикохимия поверхности и защита материалов. 2009. Т. 45. № 3. С. 287–301.
Винокуров Е.Г., Марголин Л.Н., Фарафонов В.В. // Изв. вузов. Химия и хим. технология. 2020. Т. 63. № 8. С. 4–38.
Makarova I., Dobryden I., Kharitonov D., Kasach A., Ryl J., Repo E., Vuorinen E. // Surface & Coatings Technology. 2019. V. 380. P. 125063.
Целуйкин В.Н. // Физикохимия поверхности и защита материалов. 2017. Т. 53. № 3. С. 278–281.
Giannopoulos F., Chronopoulou N., Bai J., Zhao H., Pantelis D.I., Pavlatou E.A., Karatonis A. // Electrochimica Acta. 2016. V. 207. P. 76–86.
Hatipoglu G., Kartal M., Uysal M., Cetinkaya T., Akbulut H. // Tribology International. 2016. V. 98. P. 59–73.
Фиалков А.С. Углерод, межслоевые соединения и композиты на его основе. М.: Аспект-пресс, 1997. 718 с.
Яковлев А.В., Яковлева Е.А., Целуйкин В.Н., Краснов В.В., Мостовой А.С., Рахметулина Л.А., Фролов И.Н. // Электрохимия. 2019. Т. 55. № 12. С. 1463–1470.
Павлычева Н.К., Пеплов А.А., Демин А.П. // Оптический журнал. 2007. Т. 74. № 3. С. 29–32.
Сайфуллин Р.С. Физикохимия неорганических полимерных и композиционных материалов. М.: Химия, 1990. 240 с.
Сайфуллин Р.С., Абдуллин И.А. // Российский химический журнал. 1999. Т. 63. № 3–4. С. 63–67.
Целуйкин В.Н. Корешкова А.А. // Физикохимия поверхности и защита материалов. 2018. Т. 54. № 6. С. 582–584.
Дополнительные материалы отсутствуют.
Инструменты
Физикохимия поверхности и защита материалов