Физикохимия поверхности и защита материалов, 2021, T. 57, № 6, стр. 650-659
Влияние длительности импульсов на структуру, механические, триботехнические и оптические характеристики покрытий Zr–B–N, полученных методом PMS
Ф. В. Кирюханцев-Корнеев 1, *, А. Д. Сытченко 1, Е. А. Левашов 1
1 Национальный исследовательский технологический университет “МИСиС”
119049 Москва, Ленинский пр-т, 4, Россия
* E-mail: kiruhancev-korneev@yandex.ru
Поступила в редакцию 24.01.2021
После доработки 12.07.2021
Принята к публикации 13.07.2021
Аннотация
Исследовано влияние длительности обратного импульса (0.4, 0.7 и 1.1 мкс) при импульсном магнетронном напылении (Pulsed Magnetron Sputtering) на частоте 350 кГц на структуру и свойства оптически-прозрачных покрытий Zr–B–N. Определены химический состав, морфология, оптический коэффициент пропускания, адгезионная прочность, твердость, модуль упругости, упругое восстановление, трещиностойкость, коэффициент трения, износо-, эрозионная и абразивная стойкость покрытий, а также их стойкость к циклическому ударному нагружению. Установлено, что наилучший комплекс характеристик достигается при 0.7 мкс.
ВВЕДЕНИЕ
Тугоплавкие соединения циркония, такие как ZrB2 и ZrN, широко применяются в качестве функциональных покрытий в различных областях техники: для повышения ресурса работы металлообрабатывающего инструмента – благодаря их высокой твердости ~35–45 ГПа и износостойкости [1–6], для защиты деталей химической промышленности благодаря их высокой коррозионной стойкости в агрессивных средах (NaCl, H2SO4 и др.) [7, 8], для защиты деталей газотурбинных двигателей и изделий ракетно-космической техники благодаря высокой эрозионной- и жаростойкости, а также термической стабильности [9–14], в микроэлектронике благодаря низкому коэффициенту электросопротивления [15, 16]. Покрытия в системе Zr–B–N интересны также с точки зрения их декоративных свойств – благодаря изменению содержания азота и бора можно гибко изменять цветовые координаты, отталкиваясь от ZrN, имеющего золотистый цвет [17–19]. При высоком содержании азота могут быть обеспечены уникальные оптические свойства покрытий Zr–B–N, включая высокий коэффициент пропускания 99–100% [20–22], что делает перспективным их использование в качестве защитного износо- и эрозионностойкого слоя в солнечных элементах.
Одним из перспективных способов нанесения покрытий является магнетронное напыление, которое можно проводить при постоянном токе [23] или в импульсном режиме PMS (pulsed magnetron sputtering) [24, 25]. Переход к импульсному режиму позволяет подавить образование микродуг, влияющих на качество покрытий, и снизить отравление мишени [26, 27]. Ключевыми параметрами процесса осаждения для управления свойствами PMS покрытий являются частота и скважность [28, 29]. Частота импульсов влияет на фазовый состав, микроструктуру, механические свойства и электропроводность покрытий [24–27, 30–32]. Важно отметить, что при исследованиях PMS покрытий основное внимание, как правило, уделяется такому технологическому параметру, как частота электропитания, тогда как влияние длительности обратных импульсов при использовании PMS на структуру и свойства покрытий является малоизученным. Ранее нами были проведены комплексные исследования покрытий Zr–B–N, полученных методом PMS при частотах 0, 50 и 350 кГц и фиксированной длительности импульсов [21]. Целью данной работы является исследование влияния длительности импульсов на структуру, состав, оптические, механические и трибологические свойства, а также абразивную, эрозионную стойкость и стойкость к циклическим ударным нагрузкам покрытий Zr–B–N, полученных методом импульсного магнетронного распыления.
МЕТОДИКА ЭКСПЕРИМЕНТА
Покрытия Zr–B–N были получены методом импульсного магнетронного напыления (PMS, pulsed magnetron sputtering) с использованием СВС-мишени ZrB2 при подаче мощности с блока Pinnacle Plus 5 × 5 (Advanced Energy, USA). Принципиальная схема установки для нанесения покрытий представлена в работе [33]. Мощность составляла 1 кВт, сила тока и напряжение находились на уровне 2 А и 400–500 В, частота составляла 350 кГц, а длительность импульсов варьировалась от 0.4 до 1.1 мкс. Реакционное распыление проводилось в среде N2 (99.9998%) в течение 40 мин. В качестве подложек использовались пластины из монокристаллического кремния (100) (для структурных исследований покрытий), стекла (ГОСТ 683-75) (определение оптических характеристик) и твердого сплава ВК6М (исследование механических, трибологических свойств, трещиностойкости, эрозионной и абразивной стойкости). Предварительно подложки очищались в изопропиловом спирте с помощью ультразвукового диспергатора УЗДН-2Т. Затем осуществлялось их травление в вакууме ионами Ar+ с энергией 1.5–2 кэВ в течение 20 мин с помощью ионного источника щелевого типа.
Структурные исследования покрытий выполнялись с помощью растровой электронной микроскопии (РЭМ), энергодисперсионной спектроскопии (ЭДС) на микроскопе “Hitachi” S-3400N оснащенном прибором NORAN 7 Thermo, и оптической эмиссионной спектроскопии тлеющего разряда (ОЭСТР) на установке PROFILER-2 (Horiba Jobin Yvon) [34]. Рентгенофазовый анализ (РФА) покрытий осуществлялся с использованием CuKα излучения на дифрактометре Phaser D2 Bruker в интервале углов 2θ = 20°–110°. Коэффициенты пропускания покрытий определяли на приборе КФК-3 (Россия) при одновременном измерении образца покрытия на стеклянной пластине и непокрытой подложки. Для определения механических свойств покрытий использовался нанотвердомер Nano-Hardness Tester (CSM Instruments), при этом нагрузка на индентор Берковича составляла 4 мН. Адгезионная прочность оценивалась с помощью прибора Revetest (CSM Instruments) при царапании поверхности алмазным индентором Роквелла радиусом 0.2 мм при возрастающей нагрузке. Трибологические испытания покрытий проводились на автоматизированной машине трения Tribometer (CSM Instruments), работающей по схеме “стержень–диск”, с использованием контр-тела в виде шарика Al2O3 диаметром 6 мм при нормальной нагрузке 1 Н и скорости 10 см/с. Испытания на стойкость к циклическим ударно-динамическим нагрузкам осуществлялись с помощью прибора Impact Tester CemeCon при нагрузках 300, 500 и 700 Н. Принципиальная схема установки показана в работе [35]. Для определения геометрических размеров дорожек износа и кратеров после динамических испытаний использовали оптический профилометр WYKO-NT1100 фирмы Veeco. Оценка трещиностойкости покрытий проводилась путем индентирования пирамидой Виккерса на твердомере HVS-50 (Китай) при нагрузках 10 и 50 Н и последующих исследований с помощью оптического микроскопа Axiovert Carl Zeiss (Германия) с применением цифровой фотокамеры Cannon 350D. Абразивную стойкость образцов оценивали с использованием прибора calowear-tester (НИИТАвтопром) [36] при нагрузках 10, 15 и 25 Н и скорости вращения 153 и 247 об./мин в течение 5 мин. В качестве контр-тела использовали стальной шарик 100Cr6 диаметром 27 мм. Суспензию, содержащую частицы алмаза размером 15 мкм, наносили на поверхность образца перед испытаниями. Эрозионные испытания проводили на диспергаторе УЗДН-2Т согласно методике, указанной в [36]. В качестве абразива использовали порошки B4C и SiO2 (фракция >1 мм) весом 5 г. Потеря массы образцов покрытий вследствие эрозионного воздействия была определена с использованием аналитических весов AND GR202 (точность 0.01 мг).
РЕЗУЛЬТАТЫ И ИХ ОБСУЖДЕНИЕ
Номера и составы покрытий, полученных при различной длительности импульсов (τ), указаны в табл. 1. Покрытие 1 показало максимальное содержание Zr 16.0 ат. %, при этом концентрации В и N составили 45.4 и 38.6 ат. % соответственно. Увеличение τ до 0.7 мкс привело к снижению концентрация Zr на 19% и увеличению N на 6%, концентрация бора при этом практически не изменилась. Содержание Zr, В и N в покрытии 3 составило 12.9, 47.4 и 39.7 ат. % соответственно. Типичный ОЭСТР-профиль покрытия, представлен на рис. 1а. Атомы циркония, бора и азота были равномерно распределены по глубине покрытий, концентрация примеси С находилась для покрытий 1–3 в пределах 0.7–1.8%. Скорость роста рассчитывалась путем измерения толщины покрытия по элементным профилям. Образец 1, полученный при τ = 0.4 мкс, показал толщину ~1.28 мкм и скорость роста 32 нм/мин. Увеличение длительности импульсов до 0.7 привело к росту толщины и скорости на ~22%. Дальнейшее увеличение τ до 1.1 мкс снизило толщину и скорость роста покрытия 3 до 1.35 мкм и 34 нм/мин соответственно. Более низкая скорость роста покрытия 1 вероятно связана с отравлением мишени в процессе реактивного магнетронного напыления и малой продолжительностью обратного импульса, которого не хватает для стравливания азотированного слоя [26]. В свою очередь снижение скорости роста при переходе от 0.7 к 1.1 мкс можно объяснить тем, что происходит уменьшение общего времени осаждения, при котором магнетрон работает на прямом импульсе [37, 38]. Таким образом, наибольшая толщина и скорость осаждения наблюдались для покрытия, полученного при длительности импульсов 0.7 мкс.
Таблица 1.
Элементный состав, толщина и скорость роста покрытий
№ | Длительность импульса, мкс | Состав, ат. % | Толщина, мкм | Скорость роста, нм/мин | ||
---|---|---|---|---|---|---|
Zr | B | N | ||||
1 | 0.4 | 16.0 | 45.4 | 38.6 | 1.28 | 32 |
2 | 0.7 | 13.0 | 45.9 | 41.1 | 1.55 | 39 |
3 | 1.1 | 12.9 | 47.4 | 39.7 | 1.35 | 34 |
РЭМ-исследование поперечных изломов образцов показало, что все покрытия обладали плотной однородной структурой без выраженных столбчатых элементов (рис. 1б), что является характерным для покрытий ZrBN с высоким содержанием азота [21]. Согласно данным РФА, покрытия 1–3 являются рентгеноаморфными.
График зависимости коэффициента пропускания (T) покрытий 1–3 от длины волны представлен на рис. 2. Характер кривых свидетельствует о том, что покрытия являются интерференционными. На участке 350–450 нм образец 1 показал высокий Т, возрастающий от 40 до 80%, что может быть связано с малой толщиной покрытия. Аналогичное значение Т = 80% для покрытий 2 и 3 было достигнуто только при 500 нм. В диапазоне длин волн от 550 до 950 нм все образцы имеют схожие значения Т на уровне 84–88%. При максимальной длине волны значение Т образца 1 составило 80%, в то время как покрытия 2 и 3 показали высокое значение Т = 98%. Ранее в работе [20] нами было показано, что покрытия Zr12B49N39 и Zr11B45N44 толщиной 0.4–0.5 мкм, полученные в режиме постоянного тока, характеризуются высоким коэффициентом пропускания 97 и 100% соответственно. В свою очередь покрытия Zr–B–N толщиной 0.56–0.61, полученные методом PMS при различной частоте, показали Т на уровне 98.6% [21].
Покрытия 1–3 показали близкие значения твердости (Н) 10.2–10.5 ГПа, модуля упругости (Е) 123–138 ГПа и упругого восстановления (W) 56–58% (табл. 2). По данным наноиндентирования можно судить об отсутствии влияния длительности импульсов на механические свойства покрытий. На основании результатов наноиндентирования были также определены характеристики H/E и H 3/E 2, которые могут служить показателями износостойкости покрытий [39]. Из этих данных можно сделать прогноз того, что из образцов 1–3 покрытие 2 будет обладать максимальной износостойкостью благодаря высоким значениям параметров H/E и H 3/E 2. Отметим, что покрытия Zr–B–N, полученные ранее методом DCMS и PMS при частоте 50 кГц, также показали относительно низкие значения твердости 10–11 ГПа и модуля упругости – 132–133 ГПа [21].
Таблица 2.
Свойства покрытий
№ | H, ГПа | E, ГПа | W, % | H/E | H3/E2, ГПа | В, мкм | V × 103 мкм3 | Lc, Н | |||
---|---|---|---|---|---|---|---|---|---|---|---|
300 Н | 500 Н | 700 Н | Lc2 | Lc3 | |||||||
1 | 10.5 | 138 | 56 | 0.076 | 0.061 | 425 | 3.89 | 1.56 | 17.31 | 1 | 2.2 |
2 | 10.2 | 123 | 58 | 0.083 | 0.070 | 300 | 0.44 | 0.55 | 3.85 | 4.8 | >31 |
3 | 10.3 | 128 | 57 | 0.080 | 0.067 | 325 | 0.17 | 0.59 | 1.10 | 7.2 | >31 |
На рис. 3 представлены данные скратч-тестирования для покрытий Zr–B–N на подложках ВК6М, в табл. 2 приведены нагрузки, соответствующие началу отслоения (Lc2) и касанию подложки индентором (Lc3). Для всех покрытий при увеличении ×200 растрескивания не наблюдалось. На кривой акустической эмиссии (АЕ) образца 1 при нагрузке 1 Н возникают скачки, соответствующие отслоению покрытия, что говорит об адгезионном разрушении. Стабильность АЕ и коэффициента трения (µ) после 2.2 Н свидетельствует о том, что покрытие полностью разрушилось и контакт происходит между индентором и подложкой. В случае покрытия 2 всплески сигнала AЭ, соответствующие началу отслоения, возникали при Lc2 = 4.8 Н. Для образца 2 критическая нагрузка Lc3 составила >31 Н. Адгезионное разрушение образца 3 началось при Lc2 = 7.2 Н. После нагрузки 11.6 Н происходило резкое усиление акустического сигнала и небольшое колебание µ, связанное с интенсивным отслоением покрытия. Критическая нагрузка Lc3 для образца 3 также составила >31 Н. Быстрое разрушение образца, полученного при минимальной τ, можно связать с его малой толщиной. Покрытия 2 и 3, полученные при τ = 0.7 и 1.1 мкс, показали лучшую адгезионную прочность.
Рис. 3.
Зависимости глубины (h), AE и μ от нагрузки при скратч-тестировнии и типичные микрофотографии царапин для покрытий 1–3.
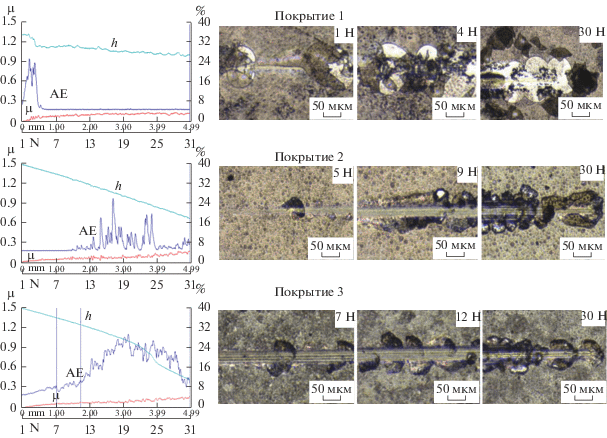
Результаты испытаний по определению коэффициента трения покрытий, полученных на подложках ВК6М при разной длительности импульса, показаны на рис. 4. Для покрытия 1 наблюдался рост µ от 0.17 до 0.73 на пробеге 0–15 м, после чего µ стабилизировался и составил ~0.74. Покрытия 2 и 3 показали схожее поведение μ. Наблюдался скачок µ от 0.80–0.92 до 0.98–1.04 на пробеге 0–20 м. На протяжении оставшейся дистанции коэффициент трения был стабилен и составил 0.90 и 0.98 для покрытий 2 и 3 соответственно. Анализ литературных источников показал, что покрытия в системе Zr–B–N обычно обладают достаточно высоким коэффициентом трения на уровне 0.7–0.75 [40, 41].
Рис. 4.
Зависимость коэффициента трения от пробега. На вставках показаны микрофотографии дорожек износа покрытий 1–3.
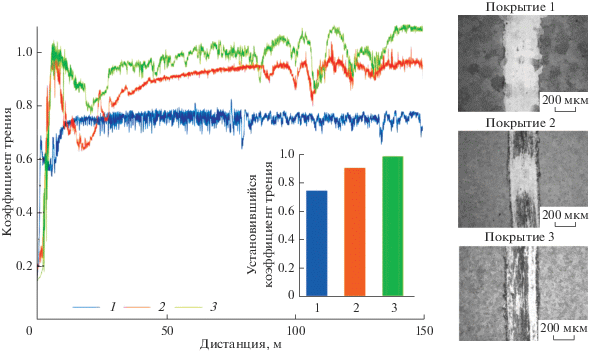
Исследование дорожек износа с помощью оптической профилометрии было затруднено из-за оптической прозрачности покрытий, поэтому оценку износа проводили на оптическом микроскопе. Результаты представлены на рис. 4. Износостойкость покрытий сравнивали по ширине полученных в результате трибоконтакта дорожек. Ширина дорожки (В) снижалась на ~30% при увеличении длительности импульсов с 0.4 до 0.7 мкс (табл. 2). Покрытие 3, осажденное при максимальной τ, показало В = 325 мкм, что на ~23% ниже значений, полученных для образца 1. Таким образом, изменение длительности импульсов от 0.4 до 1.1 мкс привело к линейному увеличению коэффициента трения. При этом зависимость износостойкости от τ носила экстремальный характер с максимумом при τ = 0.7 мкс.
Анализ 3D профилей после циклических ударно-динамических испытаний при нагрузке 300 Н покрытий Zr–B–N на подложках ВК6М показал, что в образце 1 происходил глубинный износ (h = 7 мкм), сопровождающийся отслоением покрытия (риc. 5). Объем кратера (V) составил 3.89 × 103 мкм3 (табл. 2). Для покрытия 2 наблюдался преимущественно латеральный износ, фиксировалось скопление продуктов износа по границам кратера. При этом V составил 0.44 × 103 мкм3. Образец 3 практически не износился (V ≤ 0.17 × ×103 мкм3), наблюдался небольшой рост шероховатости поверхности в зоне контакта за счет налипания продуктов взаимодействия контр-тел. При нагрузке 500 Н V образца 1 снизился за счет уменьшения глубины (h = 2 мкм) и составил 4.6 × 103 мкм3. Износ покрытий 2 и 3 сопровождался налипанием продуктов разрушения, при этом V были близки и составили 0.55 × 103 и 0.59 × 103 мкм3 соответственно. Испытания покрытия 1 при нагрузке 700 Н показали V = 17.31 × 103 мкм3. При увеличении τ до 0.7 мкс объем кратера снизился в 4.5 раза и составил 3.85 × 103 мкм3. Покрытие 3 характеризовалось минимальным V = 1.10 × 103 мкм3. Следует отметить, что подложка может оказывать влияние на стойкость покрытий к ударно-динамическим воздействиям. Поэтому для покрытия с малой толщиной ожидалась лучшая стойкость из-за положительного влияния твердой подложки (ВК6М) [35]. Однако в данной работе был замечен противоположный эффект, исключающий влияние подложки: образец 1 толщиной 1.28 мкм показал низкую стойкость при ударном нагружении. Увеличение длительности импульсов приводит к уменьшению объема кратера, а, следовательно, – к росту стойкости покрытий к ударно-динамическим испытаниям.
Рис. 5.
3D профили кратеров, полученных после ударно-динамических испытаний покрытий 1 (а), 2 (б) и 3 (в) при нагрузках 300–700 Н.
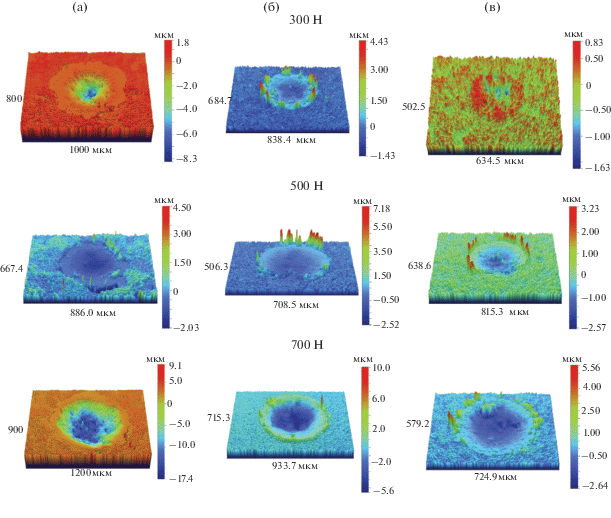
Одним из важных свойств, определяющих поведение покрытий в условиях трибоконтакта является трещиностойкость [42]. Результаты испытаний представлены на рис. 6. На поверхности образца 1 при нагрузках 10 и 50 Н наблюдалось полное отслоение, что свидетельствует о низкой адгезионной прочности покрытия и не позволяет определить собственно трещиностойкость. Разрушение покрытия возникает в результате действия сжимающих напряжений, которые приводят к вздутию и отслоению [43]. При нагрузке 10 Н для покрытия 2 было характерно частичное отслоение без образования трещин, однако при увеличении нагрузки до 50 Н по краям отпечатка образовались радиальные трещины длиной ~17 мкм. При 10 и 50 Н наблюдалось отслоение покрытия 3.
Результаты эрозионных испытаний показаны на риc. 7. В случае абразива В4С для покрытий 1 и 2 наблюдается снижение массы на 1.6 и 1.2 мг соответственно, однако визуально следы разрушения покрытия не обнаруживались при выдержках 5–25 мин. Образец 3 показал рост массы на 5 мг, что может быть связано с налипанием абразива на поверхность покрытия. Отметим, что подобное взаимодействие нежелательно, поскольку оно в конечном итоге негативно сказывается на долговечности материала [44]. Более жесткие условия для испытания образцов достигаются при использовании порошка SiO2 крупной фракции (рис. 7б). Для покрытия 1 наблюдалось снижение массы на 2 мг за 25 мин эрозионного воздействия. Изменение массы образца 2 не превышало 0.2 мг. Во время испытания покрытия 3 в период времени 0–5 мин происходило обильное налипание материала, в результате которого масса выросла на 2 мг. После чего масса снизилась, и к концу испытания приблизилась к начальной массе образца. Можно сделать вывод, что лучшей стойкостью к эрозионному воздействию частицами В4С и SiO2 обладало покрытие, осажденное при τ = 0.7 мкс. Полученные результаты, вероятно, можно объяснить высокой адгезионной прочностью и максимальной толщиной покрытия 2.
Рис. 7.
Зависимости изменения массы покрытий 1–3 от времени эрозионного воздействия абразива B4C (а) и SiO2 (б).
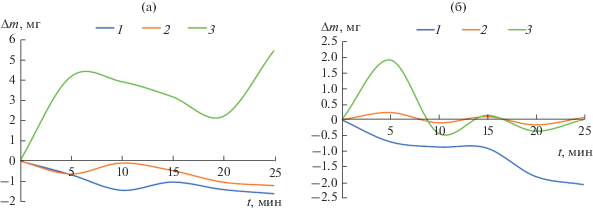
Для покрытий 2 и 3, показавших лучшую адгезию и стойкость к циклическим ударным нагрузкам, были проведены дополнительные абразивные испытания (рис. 8). При нагрузке 10 Н диаметр пятна разрушения в зоне контакта для покрытий 2 и 3 составил ~400 и 900 мкм соответственно. При этом характер разрушения покрытия 2 не обладал выраженными особенностями. В то время как покрытие 3 износилось неравномерно: наблюдались зоны с выраженными царапинами от алмазных частиц и участки без следов износа. При увеличении нагрузки до 15 Н покрытие 2 износилось до подложки (светлое пятно в центре на микрофотографии, рис. 8). Износ покрытия 3 сопровождался интенсивными царапинами, при этом диаметр пятна износа был в ~2 раза выше по сравнению с образцом 2. При максимальной нагрузке оба покрытия износились с одинаковой интенсивностью – диаметр пятна разрушения не отличался. Таким образом при нагрузках 10 и 15 Н покрытие 2 показало лучшую абразивную стойкость, что может быть объяснено как его наибольшей толщиной, так и максимальными значениями показателей H/E и H3/E2 (табл. 2).
ЗАКЛЮЧЕНИЕ
Методом импульсного магнетронного распыления были получены покрытия Zr16B45.4N38.6, Zr13B45.9N41.1 и Zr12.9B47.4N39.7 толщиной 1.28, 1.55 и 1.35 мкм соответственно. Покрытия обладали плотной однородной структурой без выраженных столбчатых зерен и равномерным распределением элементов по глубине. Все покрытия показали рентгеноаморфную структуру. Скорость осаждения покрытия, полученного при длительности импульсов 0.7 мкс, составила 39 нм/мин, что на 22 и 13% выше скоростей образцов, полученных при τ = 0.4 и 1.1 мкс. Оценка оптических свойств показала, что покрытие 1 обладало наибольшим коэффициентом пропускания в диапазоне длин волн 350–550 нм, в то время как при длинах волн 550–950 нм лучшим коэффициентом пропускания ~98% характеризовались покрытия 2 и 3, осажденные при τ = 0.7 и 1.1 мкс. Покрытия показали твердость на уровне ~10 ГПа и модуль упругости в диапазоне 120–140 ГПа.
Покрытие τ = 0.4 мкс имело низкий комплекс трибологических свойств вследствие низкой адгезии (Lc2 = 1.0 Н) и малой толщины (1.28 мкм). Покрытие, осажденное при τ = 1.1 мкс, характеризовалось лучшей адгезионной прочностью (Lc2 = 7.2 Н) и повышенной стойкостью к ударно-динамическому нагружению при 300 Н. Оптимальный комплекс свойств имел образец, осажденной при τ = 0.7 мкс. Он характеризовался максимальной толщиной (1.55 мкм), удовлетворительной адгезионной прочностью (Lc2 = 4.8 Н), наибольшими параметрами H/E = = 0.083 и H3/E2 = 0.070 ГПа, что в конечном итоге позволило обеспечить максимальные: износостойкость, эрозионную и абразивную стойкостью, стойкость к ударно-динамическим циклическим воздействиям.
Список литературы
Holzschuh H. // Thin Solid Films. 2004. V. 469–470. P. 92–98.
von Stebut J., Darbeida A., Lepage J. et al. // Surface and Coatings Technology. 1994. V. 68–69. P. 762–769.
Jianxin D., Jianhua L., Jinlong Z. et al. // Wear. 2008. V. 264. P. 298–307.
Vereschaka A., Tabakov V., Grigoriev S. et al. // Surface and Coatings Technology. 2019. V. 357. P. 218–234.
Kiryukhantsev-Korneev F.V., Lemesheva M.V., Shvyndina N.V. et al. // Protection of Metals and Physical Chemistry of Surfaces. 2018. V. 54. P. 1147–1156.
Tengdelius L., Broitman E., Lu J. et al. // Acta Materialia. 2016. V. 111. P. 166–172.
Yi P., Zhu L., Dong C., Xiao K. // Surface and Coatings Technology. 2019. V. 363. P. 198–202.
Huang J.-H., Kuo K.-L., Yu G.-P. // Surface and Coatings Technology. 2019. V. 358. P. 308–319.
Kudryashov A.E., Kiryukhantsev-Korneev Ph.V., Petrzhik M.I., Levashov E.A. // CIS Iron and Steel Review. 2019. V. 18. P. 46–51.
Kiryukhantsev-Korneev P.V., Kudryashov A.E., Sheveyko A.N. et al. // Letters on Materials. 2020. V. 10(4). P. 371–376.
Muralikrishna P.V.S., Kishore P.S., Ramanaiah N., Pathanjali V.V.S.P.K. // Materials Today: Proceedings. 2021. V. 39. P. 1287–1290.
Kablov E.N., Muboyadzhyan S.A. // Russian Metallurgy. 2017. P. 494–504.
Yang X., Wei L., Song W.,et al. // Composites Part B: Engineering. 2013. V. 45. P. 1391–1396.
Ali Akbarpour Shalmani S., Sobhani M., Mirzaee O., Zakeri M. // Ceramics International. 2020. V. 46(16). P. 25106–25112.
Pilloud D., Dehlinger A.S., Pierson J.F. et al. // Surface and Coatings Technology. 2003. V. 338. P. 174–175.
Khan S., Ahmed I., Khalid N. et al. // Materials Science in Semiconductor Processing. 2015. V. 39. P. 530–535.
https://www.platit.com/en/products/coating-guide/#
Übleis A., Mitterer C., Ebner R. // Surface and Coatings Technology. 1993. V. 60. P. 571–576.
Niyomsoan S., Grant W., Olson D.L., Mishra B. // Thin Solid Films. 2002. V. 415. P. 187–194.
Kiryukhantsev-Korneev Ph.V., Levashov E.A. // Technical Physics Letters. 2020. V. 46. P. 179–181.
Kiryukhantsev-Korneev P., Levashov E. // 7th International Congress on Energy Fluxes and Radiation Effects (EFRE), Tomsk, Russia. 2020. P. 1290–1293.
Kiryukhantsev-Korneev Ph.V., Kozlova N.S., Levashov E.A. // J. Physics: Conference Series. 2020. V. 1692. № 012022.
Shtansky D.V., Kiryukhantsev-Korneev F.V., Sheveiko A.N. et al. // Physics of the Solid State, V. 47(2). 2005. P. 252–262.
Audronis M., Leyland A., Matthews A. et al. // Plasma Processes and Polymers. 2007. V. 4(S1). S687–S692.
Kiryukhantsev-Korneev P.V. // Protection of Metals and Physical Chemistry of Surfaces. 2020. V. 56. P. 343–357.
Belkin A., Freilich A., Lopez J. et al. // New J. Physics. 2005. V. 7. № 90.
Kelly P.J., Abu-Zeid O.A., Arnell R.D., Tong J. // Surface and Coatings Technology. 1996. V. 86–87. P. 28–32.
Nowakowska-Langier K., Chodun R., Minikayev R. et al. // Thin Solid Films. 2018. V. 645. P. 32–37.
Vetushka A., Karkari S.K., Bradley J.W. // J. vacuum science and technology A. 2004. V. 22(6). P. 2459–2468.
Schroeder M.V.F., Recco A.A.C., Garzón C.M. // Materials Letters. 2018. V. 230. P. 20–23.
Wicher B., Chodun R., Nowakowska-Langier K. et al. // Applied Surface Science. 2018. V. 456. P. 789–796.
Nowakowska-Langier K., Chodun R., Minikayev R. et al. // Nuclear Instruments and Methods in Physics Research Section B: Beam Interactions with Materials and Atoms. 2017. V. 409. P. 167–170.
Shtansky D.V., Sheveyko A.N., Sorokin D.I. et al. // Surface and Coatings Technology. 2008. V. 202. P. 5953–5961.
Kiryukhantsev-Korneev F.V. // Russian J. Non-Ferrous Metals. 2014. V. 55(5). P. 494–504.
Kiryukhantsev-Korneev Ph.V., Sytchenko A.D. // Protection of Metals and Physical Chemistry of Surfaces. 2020. V. 56(5). P. 981–989.
Kiryukhantsev-Korneev Ph.V., Phiri J., Gladkov V.I. et al. // Protection of metals and physical chemistry of surfaces. 2019. V. 55. P. 913–923.
Belkind A., Freilich A., Scholl R. // Surface and Coatings Technology. 1998. V. 108–109. P. 558–563.
Sproul W.D., Christie D.J., Carter D.C. // Thin Solid Films. 2005. V. 491. P. 1–17.
Musil J., Kunc F., Zeman H., Poláková H. // Surface and Coatings Technology. 2002. V. 154. P. 304–313.
Dorcioman G., Socol G., Craciun D. et al. // Applied Surface Science. 2014. V. 306. P. 33–36.
Dong Y., Wang T.-G., Yan B. et al. // Procedia Manufacturing. V. 26. 2018. P. 806–817.
Kiryukhantsev-Korneev Ph.V., Pierson J.F., Kuptsov K.A., Shtansky D.V. // Applied Surface Science. 2014. V. 314. P. 104–111.
Evans A.G., Hutchinson J.W. // International J. Solids and Structures. 1984. V. 20. P. 455–466.
Prashar G., Vasudev H., Thakur L. // Engineering Failure Analysis. 2020. V. 115. № 10462.
Дополнительные материалы отсутствуют.
Инструменты
Физикохимия поверхности и защита материалов