Физикохимия поверхности и защита материалов, 2022, T. 58, № 1, стр. 54-60
Структура и окалиностойкость порошковых композитов “силицид титана Ti5Si3–титановая связка”
Г. А. Прибытков 1, *, М. Г. Криницын 1, В. В. Коржова 1, И. А. Фирсина 1, Е. Н. Коростелева 1
1 ФГБУН “Институт физики прочности и материаловедения Сибирского отделения Российской академии наук” (ИФПМ СО РАН)
634055 Томск, просп. Академический, 2/4, Россия
* E-mail: gapribyt@mail.ru
Поступила в редакцию 12.03.2021
После доработки 09.06.2021
Принята к публикации 29.09.2021
- EDN: XRIZAY
- DOI: 10.31857/S0044185622010168
Аннотация
В режиме безгазового горения порошковых смесей титана и кремния синтезированы и исследованы металломатричные композиты “силицид титана Ti5Si3 – титановая связка. Структура композитов состоит из силицидных зерен, разделенных прослойками титановой связки толщиной, зависящей от содержания титана в реакционных смесях. При окислении на воздухе при температурах до 1000°С происходит преимущественное окисление титановой связки с образованием оксида титана TiO2 (рутил).
ВВЕДЕНИЕ
Сплавы титана широко используются в качестве конструкционных в судостроительной, аэрокосмической, химической промышленности благодаря коррозионной стойкости и высокой удельной прочности, в том числе при повышенных температурах [1, 2]. Недостатками титана и его сплавов является низкая износостойкость в трибосопряжениях и при воздействии абразива, а также высокая скорость окисления при нагреве на воздухе выше 400°С [3]. Целью легирования титана является, в основном, повышение прочностных свойств, что достигается за счет твердорастворного упрочнения. Влияние такого легирования на износостойкость и коррозионную стойкость, в большинстве случаев слабое. В последние годы ведутся интенсивные исследования влияния легирования кремнием, бором и углеродом на механические свойства титана и его сплавов. Небольшие (до 5%) добавки этих элементов приводит к образованию дисперсных выделений тугоплавких соединений (Ti5Si3, TiB или TiC), которые увеличивают прочность при одновременном снижении пластичности [4, 5]. Легированные неметаллическими элементами сплавы получают либо литьем [6, 7], либо с применением порошковых технологий, среди которых наиболее часто используют изостатическое горячее прессование (HIP) [8] и искровое плазменное спекание (SPS) [9]. При всех применяемых технологиях получения титановых сплавов в качестве присадок обычно используют не чистые кремний, углерод или бор, а тугоплавкие соединения (B4C, TiB2, SiC, SiN4). Эти соединения при высоких температурах превращаются в борид, карбид или силицид, находящиеся в равновесии с β-титаном. При использовании B4C или SiC получают титановый сплав с гибридным упрочнением: частицами моноборида и карбида титана для B4C или силицида и карбида титана для SiC.
Наряду с упрочнением дисперсные выделения указанных тугоплавких соединений положительно влияют на окалиностойкость титановых сплавов. Согласно [10, 11] cкорость окисления литых титановых сплавов с содержанием 10 об. % (TiB + TiC) частиц примерно вдвое меньше в интервале 700–1000°С. При этом отмечается, что положительное влияние моноборида и карбида титана на окалиностойкость титана ограничено недостаточной стойкостью к окислению этих соединений.
Более перспективными в отношении влияния на стойкость к окислению представляются силициды титана, в частности Ti5Si3, который всегда присутствует в титановых сплавах, легированных кремнием [12]. Введение 1.4% кремния в сложнолегированный титановый сплав в 1.5–2 газа уменьшает скорость параболического роста продуктов при окислении на воздухе при 700°С до 250 ч [13]. Силициды металлов имеют высокую стойкость к окислению [14] благодаря образованию на их поверхности плотной окалины SiO2, препятствующей проникновению кислорода к металлической поверхности. Силициды титана широко используются в качестве барьерных покрытий на титане и его сплавах. Эти покрытия наносятся различными способами: силицированием при высокотемпературной выдержке в порошке кремния [15, 16], оплавлением лазером слоя из порошковой смеси Ti и Si, нанесенной на поверхность [17]. В работе [18] получали толстое покрытие, состоящее из наружного слоя силицида Ti5Si3 и нижележащего слоя эвтектики, который обеспечивал прочное сцепление покрытия с титановой подложкой. Покрытие получали в процессе экзотермической реакции синтеза в нанесенной на поверхность порошковой смеси состава, соответствующего силициду Ti5Si3.
Силицидные покрытия на титане склонны к растрескиванию из-за присущей силицидам хрупкости [14] и из-за различия коэффициентов теплового расширения с подложкой. Поэтому представляют интерес композиционные покрытия, состоящие из силицидных включений в пластичной титановой матрице. Целью настоящей работы было исследование структуры и стойкости к окислению при нагреве на воздухе композиционных порошков Ti5Si3–Ti матрица, полученных самораспространяющимся высокотемпературным синтезом (СВС) из порошковых смесей титана и кремния [19]. Композиционные порошки со структурой металломатричного композита удобно использовать для нанесения покрытий методами наплавки [20] или напыления [21]. Полученные покрытия имеют более однородную структуру и стабильные свойства, по сравнению с покрытиями, полученными с применением смесей из элементарных порошков [22].
МАТЕРИАЛЫ И МЕТОДЫ ИССЛЕДОВАНИЙ
Для проведения синтеза были приготовлены реакционные смеси составов, указанных в табл. 1. Там же приведен расчетный целевой состав продуктов синтеза (при условии образования при синтезе силицида Ti5Si3 стехиометрического состава). Реакционные смеси готовили из порошков титана (ТПП-8; <160 мкм; 99.4%) и кремния (Кр-00; <40 мкм; 99.45%). Порошки смешивали 4 ч всухую и прессовали в цилиндрические образцы ∅20 × 25 мм пористостью 32–36%. Синтез проводили в герметичном реакторе в среде аргона с избыточным давлением около 0.5 атм. Горение инициировали нагревом поджигающей таблетки молибденовой спиралью, через которую пропускали электрический ток. Полученный рыхлый спек из продуктов синтеза дробили с рассевом на фракции.
Таблица 1.
Шихтовый состав реакционных смесей и целевой состав продуктов
Целевой состав СВС продукта | Состав реакционных смесей мас. % | |
---|---|---|
Ti | Si | |
Ti5Si3 | 73.97 | 26.03 |
Ti5Si3 + 10 об. % Ti | 76.71 | 23.29 |
Ti5Si3 + 20 об. % Ti | 79.39 | 20.61 |
Ti5Si3 + 30 об. % Ti | 82.04 | 17.96 |
Ti5Si3 + 40 об. % Ti | 84.68 | 15.32 |
Для испытания на стойкость к окислению на воздухе использовали фракцию 80–200 мкм. Пробы порошка насыпали слоем толщиной 3–5 мм в ванночки, изготовленные из фольги из нержавеющей стали 12Х18Н9Т. Ванночки с порошком и пустую ванночку помещали в печь СНОЛ, предварительно разогретую до конкретной температуры и выдерживали 2 ч. Привес с точностью до 1 мг определяли взвешиванием ванночек до и после выдержки в печи. Для исключения ошибки, вносимой окислением стальных ванночек, из суммарного привеса вычитали привес пустой ванночки.
Исходные и окисленные порошки исследовали на оборудовании Центра коллективного пользования “Нанотех” ИФПМ СО РАН методом рентгеноструктурного анализа (дифрактометр (ДРОН-3, CuKα-излучение) и растровой электронной микроскопии (EVO 50, Zeiss, Germany). Образцы для металлографического исследования готовили шлифовкой и полировкой алмазными пастами гранул СВС продукта, залитых в эпоксидную смолу.
РЕЗУЛЬТАТЫ И ОБСУЖДЕНИЕ
Фазовый состав и микроструктура исходных СВС порошков
Согласно результатам рентгеноструктурного анализа (рис. 1) продукты синтеза содержат две фазы: силицид титана Ti5Si3 и непрореагировавший титан, который находился в реакционной порошковой смеси в избытке.
Рис. 1.
Рентгенограммы продуктов синтеза в реакционных смесях титана и кремния. Целевое содержание (об. %) титановой связки: 1 – 10%; 2 – 20%; 3 – 30%; 4 – 40%.
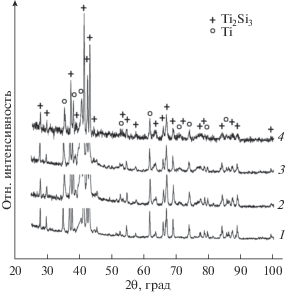
Микроструктура композитов, синтезированных из смесей, различающихся элементным составом, показана на рис. 2, а на рис. 3 и 4 приведены карты распределения титана и кремния, с помощью которых были идентифицированы структурные составляющие на рис. 2. Силицидные зерна в структуре всех продуктов СВС окружены светлыми прослойками титановой связки. При увеличении содержания титановой связки толщина прослоек увеличивается, а размер силицидных зерен уменьшается. Это является следствием уменьшения температурного интервала существования жидкометаллического раствора, в котором происходит рост силицидных зерен [19]. Изменяется также и морфология силицидных включений (рис. 2). При содержании титановой связки 10 и 20% зерна преимущественно равноосные. В композите с 30% связки появляются зерна вытянутой формы, а в композите с 40% связки наряду с равноосными имеется много игольчатых силицидных включений (рис. 2г). Эта неоднородность структуры продукта синтеза объясняется пространственной неоднородностью концентрации жидкого Ti–Si раствора, из которого кристаллизуются силицидные зерна. В областях с концентрацией меньше средней возникают немногочисленные силицидные зародыши, которые беспрепятственно растут, приобретая характерную для Ti5Si3 вытянутую форму.
Кинетика и фазовый состав продуктов окисления
На рис. 5 приведены результаты испытаний на окисление СВС композиционных порошков силицид Ti5Si3 – титановая связка. Относительный привес (отношение прибавки веса к начальному) после выдержки при 600°С не превышает 5% и не зависит от состава порошка. Прогрессирующее увеличение привеса с ростом температуры начинается с 700°С. Относительный привес тем больше, чем больше содержание титановой связки в порошке. Это означает, что происходит преимущественное окисление титана. Привес титанового порошка после окисления при 900 и 1000°С не различается. Это является признаком полного израсходования титана в реакции окисления. Привес порошка из силицида в интервале 600– 1000°С увеличивается незначительно.
Рентгенограммы продуктов окисления порошков при 900°С приведены на рис. 6, а результаты их расшифровки – в табл. 2. Согласно результатам рентгенофазового анализа (РФА) продукты окисления, кроме исходных фаз (титан и силицид), содержат единственный окисел титана TiO2 (рутил). Наложение линий на рентгенограммах от различных фаз затрудняет точность определения количественного содержания, поэтому в табл. 2 приведены средние значения с указанием разброса. Из-за большого разброса указанные средние значения нельзя считать надежными и достоверными, а поэтому какого либо влияния исходного фазового состава порошков на фазовый состав после окисления не выявлено. Остаточное содержание титана после окисления для всех образцов не превышает 2.7 об. %.
Рис. 6.
Рентгенограммы продуктов окисления СВС-порошков 2 ч на воздухе при 900°С. Целевое содержание (об. %) титановой связки: 1 – 0% (Ti5Si3); 2 – 10%; 3 – 20%; 4 – 30%; 5 – 40%.
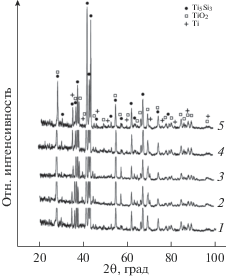
Таблица 2.
Относительное содержание фаз (об. %) в СВС-порошках, окисленных 2 ч на воздухе при 900°С
Окисленные порошки | Ti5Si3 (29-1362)* | TiO2 (21-1276)* | Ti (5-682)* |
---|---|---|---|
Титан ТПП-8 | – | 75.0 | 25.0 |
Ti5Si3 | 72.1 ± 15.7 | 28.0 ± 15.7 | – |
Ti5Si3 + 10% Ti | 56.9 ± 20.7 | 42.4 ± 21.3 | 0.7 ± 0.7 |
Ti5Si3 + 20% Ti | 62.0 ± 17.7 | 36.3 ± 19.3 | 1.7 ± 1.7 |
Ti5Si3 + 30% Ti | 57.9 ± 20.1 | 39.4 ± 22.2 | 2.7 ± 2.1 |
Ti5Si3 + 40% Ti | 63.5 ± 15.9 | 33.8 ± 17.3 | 2.7 ± 1.2 |
Возможности точного количественного определения фазового состава исследованных нами порошков дисперсностью 80–200 мкм методами рентгеноструктурного анализа ограничены также тем, что глубина анализируемого слоя для исследованных нами порошков не превышает 23 мкм [19]. То есть, полученные нами результаты определения фазового состава методом РФА относятся к поверхностному слою порошков, а не к интегральному фазовому составу. Это подтверждается, например, тем, что согласно результатам РФА при окислении силицида при 900°С он почти на треть превращается в оксид (табл. 2). Однако привес при этом составляет около 4% (рис. 5).
ВЫВОДЫ
1. Продукты синтеза в режиме волнового горения смесей порошков титана и кремния, содержащих избыток титана, имеют структуру металломатричного композита, в которой силицидные зерна разделены прослойками титана с толщиной, зависящей от содержания титана в реакционных смесях.
2. Единственным продуктом окисления композиционных порошков “Ti5Si3–Ti связка” является TiO2 (рутил), который образуется преимущественно при окислении титановых прослоек, разделяющих силицидные зерна.
3. Окалиностойкость порошков ухудшается с увеличением содержания титановой связки, что делает нецелесообразным применение порошков для нанесения защитных покрытий на титане.
Авторы благодарят В.П. Кривопалова за помощь при проведении синтеза порошков и испытаний на окалиностойкость.
Работа выполнена при финансовой поддержке Российского научного фонда (грант № 17-19-01425-П).
Список литературы
Горынин И.В., Чечулин Б.Б. Титан в промышленности. М.: Маш-е, 1990. 400 с.
Zwikker Ulrich. Titan und Titanlegirungen. Springer-Verlag. 1974. 717 p.
Головко Э.И. Высокотемпературное окисление металлов и сплавов. Справочник. Киев: Наук. Думка. 1980. 296 с.
Tjong S.C., Mai Yiu-Wing // Composites Science and Technology. 2008. V. 68. P. 583–601.
Hayat M.D., Singh H., He Z., Cao P. // Composites Part A. 2019. V. 121. P. 418–438.
Wang M., Lu W., Qin J. et al. // Scripta Materialia. 2006. V. 54. P. 1955–1959.
Sun S., Wang M., Wang L. et al. // Composites: Part B. 2012. V. 43. P. 3334–3337.
Jiao Y., Huang L.J., Geng L. et al. // Materials Science & Engineering A. 2017. V. 701. P. 359–369.
Benamor A., Hadji Y., Chiker N. et al. // Ceramics International. 2019. V. 45. P. 21781–21792.
Yadav P., Lee D.B. // Advances in Technology Innovation. 2017. V. 2. № 4. P. 130–132.
Kim Y.J., Yadav P., Hahn J. et al. // Metals and Materials International. 2019. V. 25. P. 627–632.
Huang X., Gao Y., Li Q. et al. // Corrosion Science. 2021. V. 181. P. 109235.
Tkachenko S., Datskevich O., Dvorak K., Kulak L. // J. Alloys and Compounds. 2017. V. 694. P. 1098–1108.
Mitra R. // Int. Mater. Rev. 2006. V. 51. P. 13–64.
Liang W., Zhao X.G. // Scripta mater. 2001. V. 44. P. 1049–1054.
Vojtech D., Kubatik T., Pavlickova M., Maixner J. // Intermetallics. 2006. V. 14. P. 1181–1186.
Wu Y., Wang A.H., Zhang Z. et al. // Applied Surface Science. V. 305. P. 16–23.
Riley D.P. // Intermetallics. 2006. V. 14. P. 770–775.
Прибытков Г.А., Криницын М.Г., Коржова В.В. // Химическая физика и мезоскопия. 2020. Т. 22. № 3. С. 269–280.
Krinitcyn M., Pribytkov G., Korzhova V., Firsina I. // Surface and coatings technology. 2019. V. 358. P. 706–714.
Pribytkov G.A., Kalita V.I., Komlev D.I. et al. // Inorganic materials: Applied research. 2018. V. 9. № 3. P. 442–450.
Fomin V.M., Golyshev A.A., Kosarev V.F. et al. // Phys. Mesomech. 2020. V. 23. № 4. P. 291–300.
Дополнительные материалы отсутствуют.
Инструменты
Физикохимия поверхности и защита материалов