Физикохимия поверхности и защита материалов, 2022, T. 58, № 4, стр. 442-448
Влияние карбида хрома на коррозионное сопротивление плазменного покрытия NiCrBSi
А. Е. Балановский 1, Нгуен Ван Чьеу 1, *
1 Иркутский национальный исследовательский технический университет
Иркутск, Россия
* E-mail: vantrieu.xumuk@gmail.com
Поступила в редакцию 14.12.2020
После доработки 07.11.2021
Принята к публикации 11.11.2021
- EDN: SBTKRF
- DOI: 10.31857/S0044185622040076
Аннотация
Проведены исследования оценки влияния карбида хрома на корозионную стойкость покрытий, полученных при плазменном нагреве смесей порошка сплава NiCrBSi и покрытия ОК 84.78 на поверхности стали Ст3. Установлено, что повышение содержания карбида хрома в исходном составе покрытия приводит к увеличению микротвердости модификационных покрытий, но одновременно увеличивается и вероятность возникновения трещин и пор. Увеличение содержания карбида хрома в составе покрытия влияет на механизм формирования зеренной структуры поверхностного слоя. Исследования коррозии покрытий в 3% растворе NaCl показало, что при повышении содержания хрома в составе покрытия, потенциал коррозии уменьшается, а при увеличении содержания углерода, плотность тока коррозии повышается.
ВВЕДЕНИЕ
Легирование поверхности металлических деталей, машин и инструментов – один из методов, который помогает снизить затраты и повысить долговечность нелегированной подложки по сравнению с использованием легированных сталей. В результате этого обеспечивается достижение важных свойств эксплуатации: высокая твердость, износостойкость, коррозионная стойкость и т.п. Среди экономически доступных для коррозионностойких и износостойких покрытий широко применяются сплавы на основе никеля, благодаря их высокой износо- и коррозионной стойкости при высоких температурах, так относительно низкой стоимости [1–5]. Покрытия на основе никеля широко используются для улучшения качества поверхностей, которые подвергаются суровым трибологическим условиям эксплуатации, таким как угольные котлы, теплообменники, турбины, инструменты, экструдеры, плунжеры, валки для прокатных станов, сельскохозяйственная техника и т.д. [6]. Среди существующих в настоящее время технологий обработки поверхности, обсуждавшихся ранее [7–9], плазменный нагрев неплавящимся электродом в инертном газе (ТИГ – TIG) считается ключевым фактором в развитии технологии модификации поверхности благодаря: простоте, гибкости и невысокой стоимости [8, 9]. В последние годы, чаще применяют метод TIG для формирования поверхностных покрытий на металлы, в частности, цементированные, хромированные, хромоникелерованные составы покрытий [7–9]. Полуавтоматический процесс плазменной обработки дает быстрый нагрев, устраняет недостатки низкой температуры и ограничения рабочего пространства для деталей характерных для процессов печного нагрева. Однако, неравномерное распределение температурного градиента при плазменном нагреве по поверхности может приводить к нестабильности процесса диффузии. Несмотря на успешное получение поверхностных слоев сплавом типа NiCrBSi, последние имеют незначительно высокую твердость по сравнению с твердостью зоны закалки стали Ст3 [7].
Во многих исследованиях [1–6, 10–19], наметилась тенденция использования смесей для приготовления покрытий, например сочетания состава NiCrBSi и упрочняющих добавок [7]. Важным фактором в оплавлении поверхности стали методом плазменного нагрева дугой является выбор наплавленного базового сплава и добавки. Металлокерамические композиты или металлокерамика, как известно, сочетают в себе твердость керамики и вязкость металлов при разрушении. В частности, соединения карбидов такие, как WC, TiC, SiC, широко используются для приготовления упрочняющих поверхностных покрытий с помощью различных методов [10–13]. Среди них, карбиды хрома широко используются во многих отраслях. По сравнению с другими карбидами металлов, низкая температура плавления приводит к сокращению теплового расхода в процессе оплавления, а близость температурного коэффициента линейного расширения к коэффициенту сталей, приводит к снижению напряжений в переходном слое при нанесении покрытий на стальную основу [14].
Вид исходного состава смеси NiCrBSi и карбида хрома является типичным для создания упрочняющих поверхностных покрытий при применении высококонцентрированных источников [5, 15–17]. Самым распространенным карбидом для исследования является Cr3C2 [1–5, 12–19]. При сочетании сплава NiCr и Cr3C2 с помощью плазменного напыления полученные покрытия имеют высокую твердость (600–850 HV), но много дефектов (поры, присутствие оксидов, не расплавляемых частиц) [18]. В работе [19] отмечается, что увеличение содержания Cr3C2 в исходном составе NiCrBSi + Cr3C2 приводит к повышению микротвердости покрытий, но износостойкость повышается до содержания 20% в покрытии, а с 30%‑ым содержанием уже уменьшается. Карбид в виде Cr7C3 найден в качестве армирующей фазы для композитных покрытий [20, 21]. Хотя такая добавка дает повышение твердости композитным покрытиям, но одновременно также увеличивает вероятность образования дефектов, таких как трещины, пустоты за счет формирования хрупких фаз. Сочетание сплава никеля и Cr7C3 уже исследовано в работе [22]. Было обнаружено, что коррозионная стойкость покрытия Cr3C2–NiCr снижается либо наличием пористости [23] либо присутствием карбидов [24]. В работе [25] авторы показали, что такие дефекты, как поры и трещины, играют ключевую роль в целостности системы покрытие-подложка и могут отрицательно влиять на коррозионную стойкость, поскольку они действуют как основные пути, по которым электролит проходит через покрытие и достигает подложки. В этом случае, если подложка более активна, чем покрытие, то между покрытием и подложкой образуется гальваническая пара, что приводит к коррозии подложки, повреждению компонента и уменьшению срока службы компонента.
В данной работе поставлена цель провести оценку влияния карбида хрома на коррозионную стойкость покрытий, полученных из смесей сплава ПР-Н80Х13С2Р и покрытия сварочного электрода ОК 84.78.
ЭКСПЕРИМЕНТАЛЬНАЯ ЧАСТЬ
В качестве сплава системы NiCrBSi использован ПР-Н80Х13С2Р (ГОСТ 21448), а сплава карбидов хрома – порошковое покрытие сварочного электрода ОК 84.78 (ЕSAB). Содержание сплавов в составах покрытий представлено в табл. 1. Исследуемая подложка – сталь Ст3 (ГОСТ 380-2005). Смеси порошка ПР-Н80Х13С2Р и ОК 84.78 смешивали с канцелярским клеем до консистенции пасты. Размер частиц порошка сплавов, определен лазерным анализатором ANALYSETTE 22, рис. 1. Приготовленную смесь наносили на поверхность стали Ст3 с фиксируемой толщиной 0.25, 0.5 мм. После сушки обмазки, проводили плазменную обработку образцов. Режим плазменного нагрева: ток – 140 А; скорость движения образцов – 2.7 мм/с; скорость подачи газа Аргона 10 л/мин, зазор между слоем обмазки и электродом 4–5 мм.
Таблица 1.
Химический состав сплавов и содержания компонентов в смесях
Эл. | 1 | 2 | 3 | 4 | 6 | |||
---|---|---|---|---|---|---|---|---|
NiCrBSi | NiCrBSi | OK 84.78 | NiCrBSi | OK 84.78 | NiCrBSi | OK 84.78 | OK 84.78 | |
100% | 90% | 10% | 80% | 0% | 70% | 30% | 100% | |
Ni | 80 | 72 | 64 | 56 | 0 | |||
Cr | 14 | 20.87 | 27.74 | 34.61 | 2.7 | |||
Fe | 1.8 | 1.62 | 1.44 | 1.26 | 0 | |||
B | 1.5 | 1.35 | 1.2 | 1.05 | 0 | |||
Si | 2.4 | 2.36 | 2.32 | 2.28 | 2 | |||
C | 0.3 | 1.4 | 2.5 | 3.6 | 1.3 | |||
Mn | 0 | 0.38 | 0.76 | 1.14 | 3.8 |
Для контроля процесса коррозии исследуемых образцов использовали потенциостат–гальваностат “ПИ-50-Pro” и 3% раствор NaCl. Покрываемые образцы полировали водостойкой абразивной бумагой марки Eagle с зернистостью 1000, после этого промывали дистиллированной водой, этиловым спиртом. Режим работы: стартовый потенциал –1400 мВ; максимальный потенциал 100 мВ; минимальный потенциал –1500 мВ; конечный потенциал 100 мВ; диапазон тока 2000 мА; диапазон потенциала 50 В; скорость развертки 26.932 мВ/с. Работа с помощью программы PS_Pack2 по типу эксперимента “Линейная развертка”.
РЕЗУЛЬТАТЫ И ИХ ОБСУЖДЕНИЯ
Для изучения микроструктуры полученных покрытий после обработки, выбирали и отрезали части образцов, которые находятся в середине по длине линии. Их поперечное сечение представлено в рис. 2 с распределением микротвердости по глубине. Видно, что покрытия № 4, 5 имеют трещины, это может быть связано с формированием хрупких карбидных фаз (для № 4 – 30% ОК 84.78), и сильной разности термического расширения между сплавом и сталями при быстром охлаждении в воде (для № 5 – NiCrBSi). Микротвердость измерили с помощью твердомера серии НММ – G.
Рис. 2.
Распределение микротвердости поперечного сечения полученных покрытий по глубине после плазменной обработки.
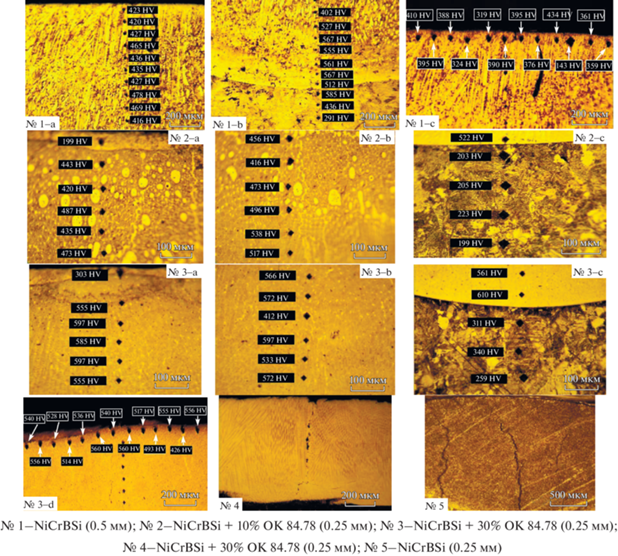
Распределение значения твердости по глубине на рис. 3 показывает большую разницу между покрытиями только из сплава NiCrBSi и покрытиями, содержащими карбид хрома. Видно, что покрытие NiCrBSi с исходным толстым слоем имеет наибольшую глубину легирования, остальные покрытия, содержащие карбид хрома мало отличаются друг от друга по толщине покрытий. Несмотря на толстый слой обмазки, образец с покрытием NiCrBSi имеет наибольшую ширину зоны термического влияния с высокой твердостью по сравнению с остальными образцами покрытий. Это можно объяснить тем, что сплав никеля более пластичен и содержит мелкие частицы, имеет низкую температуру плавления (около 1000°С), а покрытия содержащие составы ОК 84.78 имеют более твердые, грубые частицы и температуру плавления около 2000оС. Это снижает теплопередачу внутри последовательных зон подложки. За счет неполного насыщения, в покрытиях № 3, 4 существуют верхние подслои с низкой твердостью.
Распределения микротвердости верхней зоны насыщенной части покрытия представлены дисперсией, показанной в рис. 4. Большая разница значений дисперсии между двумя покрытиями показала, что участие карбида в образовании твердых фаз приводит к значительному снижению содержания γ-Ni, которое обладает низкой твердостью. Это не наблюдается не только по глубине, но и по ширине упрочненного слоя. Большинство значений микротвердости образцов покрытия (NiCrBSi и 20% ОК 84.78) выше, чем у образцов покрытия NiCrBSi. Значения микротвердости повышаются с увеличением содержания в покрытии дополнительной смеси ОК 84.78.
Рис. 5.
Типичная форма расплавленного покрытия. d = B/(B + F) × 100%, где d – коэффициент разбавления; B и F – площади расплавленного металла подложки и плакированного покрытия соответственно.
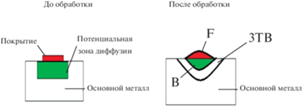
Помимо участия легирующего компонента, влияющего на изменение твердости, необходимо также учитывать разбавление подложки при расплавлении поверхностного слоя в процессе плазменной обработки, выражаемое коэффициентом разбавления (показано на рис. 6). Независимо от толщины покрытия, подложка сильнее разбавляется сплавом NiCrBSi, чем в покрытиях на основе смеси NiCrBSi и ОК 84.78. Высокий коэффициент разбавления в случае покрытия NiCrBSi объясняется тем, что этот сплав имеет низкую температуру плавления, что ускоряет теплопередачу к подложке. В случае добавления ОК 84.78, присутствие карбидов, имеющих более высокую температуру плавления (выше 2000°С), приводит к более сильному поглощению энергии при их расплавлении, что одновременно предотвращает теплопередачу к подложке.
Рис. 6.
Зависимость коэффициента разбавления подложки от содержания электрода ОК 84.78 в исходном составе.
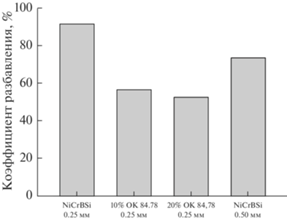
В другом результате, добавление карбида сильно изменяет микроструктуру покрытий, как показано на рис. 7. Покрытие из 0.25 мм NiCrBSi при охлаждении водой быстро превращается в структуру основного мартенсита, который обладает большой вероятностью возникновения трещин. В случае увеличения толщины слоя, сплав NiCrBSi не полностью трансформируется в мартенсит, в покрытии еще имеет чередующиеся светлые участки с низкой микротвердостью, а основные жесткие фазы обладают ячеистыми, дендритными и столбчатыми структурами.
В случае добавления карбидов хрома, зоны чередующихся светлых участок понижены, основные твердые фазы обладают ячеистыми и равноосными структурами, даже существуют трещины внутри покрытия, которые заполнены фазой γ-Ni. В картинах (рис. 8) показаны структурные фазы аустенитно-мартенситного типа с более большой площадью зон аустенита для покрытия только из сплава NiCrBSi, в покрытии при сочетании NiCrBSi и ОК 84.78 фазы тоже в аустенитно-мартенситном типе но с пониженной площадь аустенита. Это можно сопоставить с увеличением хрома, углерода и уменьшением никеля в исходных составах смесей. Даже отношение между толщиной обмазки и мощностью тоже влияет на формирование структурных фаз, что сопровождается изменением твердости полученного покрытия.
Сплав NiCrBSi и покрытие ОК 84.78 чаще рекомендуются для повышения коррозионной стойкости поверхности металлов. Соответствующая оценка поведения коррозии выполнена с помощью потенциостат–гальваностата “ПИ-50-Pro” в 3% растворе NaCl.
Снятые кривые потенциал – ток (Е–I) приведены на рис. 9. Очевидно, линии зависимости для всех покрытий имеют участок посередине, параллельный горизонтальной оси, а затем ток коррозии резко возрастает для NiCrBSi в диапазоне потенциалов –400–(–300) мВ, для остальных в диапазоне –300–(–200) мВ. Форма этих линий доказала, что все покрытия обладают более высокой коррозионной стойкостью и наибольшая стойкость у сплава NiCrBSi + 20% ОК 84.78.
Рис. 9.
Зависимости силы тока (мА) от потенциала (мВ) относительно хлорсеребряного электрода сравнения для покрытий NiCrBSi, NiCrBSi-10% OK 84.78, NiCrBSi-20% OK 84.78, NiCrBSi-30% OK 84.78.
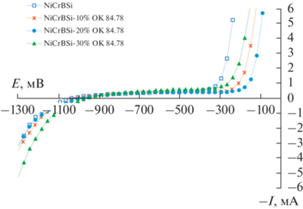
Контроль коррозии производился повторением 6 раз для каждого покрытия. С помощью аппроксимирующей кривой с величиной достоверности аппроксимации получены средние значения тока и потенциала коррозии, приведенные в табл. 2. Известно, что хром в стали повышает коррозионное сопротивление за счет его пассивации в агрессивных средах. Из табл. 1, 2 выяснилось, что увеличение потенциала коррозии соответствовало увеличению хрома, а повышение тока коррозии – увеличению углерода в исходном составе (рис. 10). В случае 30% ОК 84.78, ток коррозии сильнее повышен, может из-за существования микротрещин в покрытии, вследствие подложка быстрее прикасается при контакте с коррозионной средой.
ЗАКЛЮЧЕНИЕ
В работе отмечено, что добавление порошка покрытия электрода ОК 84.78 сильно влияет на изменение структуры и сопротивления от коррозии покрытия системы сплава NiCrBSi.
В общем случае, из всех составов, содержащих покрытие электрода ОК 84.78 понижает коэффициент разбавления подложки, ширину зоны термического влияния и приводит к формированию мягких аустенитных фаз.
Увеличение хрома приводит к повышению потенциала коррозии, но высокое содержание углерода повышает вероятность возникновения дефектов (поры, трещины) из жестких фаз карбидов, вследствие этого понижается ток коррозии.
При увеличении содержания хрома, покрытия обладают более высокой пассивацией, ток коррозии резко возрастает при диапазоне –300–(–200) мВ, а для NiCrBSi при диапазоне потенциалов –400–(–300) мВ.
Список литературы
Yu J., Song B. // Results in Physics. 2018. V. 11. P. 105–111.
Sun W., Bhowmik A., Tan A.W.Y., Xue F., Marinescu I., Li F., Liu E. // Surface & Coatings Technology. 2019. V. 358. P. 1006–1012.
Saeedi R., Shoja-Razavi R., Bakhshi S.-R., Erfanmanesh M., Ahmadi-Bani A. // Ceramics International. 2021. V. 47. Is. 3. P. 4097–4110.
Bhosale D.G., Rathod W.S., Rukhande S.W. // Materials Today: Proceedings. 2021. V. 41. Part 4. P. 780–785.
Yang M.S., Liua X.B., Fan J.W., He X.M., Shi S.H., Fu G.Y., Wang M.D., Shu-Fa Chen S.F. // Applied Surface Science. 2012. V. 258. P. 3757–3762.
Makarov A.V., Soboleva N.N., Kharanzhevskiy E.V. // J. Crystal Growth. 2019. V. 525. P. 125200.
Чьеу Н.В. // Вестник ИрГТУ. 2020. Т. 24. № 1. С. 52–63.
Balanovskii A.E. // High Temperature. 2019. V. 57. № 6. P. 784–797.
Balanovskii A.E., Vu V.H. // Letters on materials. 2017. V. 7. № 2. P. 175–179.
Saeedi R., Shoja-Razavi R., Bakhshi S.-R., Erfanmanesh M., Ahmadi-Bani A. // Ceramics International. 2021. V. 47. Issue 3. P. 4097–4110.
Bhosale D.G., Rathod W.S., Rukhande S.W. // Materials Today: Proceedings. 2020. P. 1–6.
Wang P., Li S., Geng X., Zhang J., Wei C. // Journal of Alloys and Compounds. 2020. V. 843. P. 156084.
Yang M.S., Liua X.B., Fan J.W., He X.M., Shi S.H., Fu G.Y., Wang M.D., Shu-Fa Chen S.F. // Surface Science. 2012. V. 258. P. 3757–3762.
Zikin A., Hussainova I., Katsich C., Badisch E., Tomastik C. // Surface and Coatings Technology. 2012. V. 206. № 19–20. P. 4270–4279.
Wang D., Xie Y., Yang Y., Wang M., Wang W., Cheng X., Lu D. // Materials Characterization. 2016. V. 115. P. 46–54.
Liu Q., Wang Y., Bai Y., Li Z.D., Tan G.L., Bao M.Y., Li X.J., Zhan H., Sun Y.W., Chong N.J., Wang R.J., Ma Y.S. // Surface & Coatings Technology. 2020. V. 397. P. 126052.
Shankar R., Balasubramanian K.R., Sivapirakasam S.P. // Materials Today: Proceedings. 2021. V. 46. Part 19. P. 9529–9536.
Glasnik V. // Military Technical Courier. 2014. V. 62. № 2. P. 7–26.
Xuelong P. // Surface Review and Letters. 2019. V. 26(06). P. 1–10.
Liu X.B., Wang H.M. // Wear. 2007. V. 262. P. 514–521.
Cheng F., Wang Y., Yang T. // Materials Characterization. 2008. V. 59 (4). P. 488–492.
Singh B., Zafar S. // Wear. 2019. V. 426–427 (A). P. 491–500.
Yamada K., Mohri M. // Silicon Carbide Ceramics 1. Springer, Dordrecht. 1991. P. 13–44.
Friedrich C., Berg G., Broszeit E., Berger C., Datensammlung zu Hartstoff-eigenschaften. // Mat-wiss u Werkstofftech. 1997. V. 28(2). P. 59–76.
Sadeghimeresht E., Markocsan N. // Coatings. 2017. V. 7. P. 162.
Дополнительные материалы отсутствуют.
Инструменты
Физикохимия поверхности и защита материалов