Физикохимия поверхности и защита материалов, 2023, T. 59, № 2, стр. 181-187
Окалиностойкость порошковых композитов “силицид титана Ti5Si3–алюминид титана TiAl3”
Г. А. Прибытков 1, *, В. В. Коржова 1, И. А. Фирсина 1, А. В. Барановский 1, В. П. Кривопалов 1
1 ФГБУН Институт физики прочности и материаловедения Сибирского отделения Российской академии наук (ИФПМ СО РАН)
634055 Томск, пр. Академический, 2/4, Россия
* E-mail: gapribyt@mail.ru
Поступила в редакцию 08.02.2022
После доработки 10.05.2022
Принята к публикации 25.05.2022
- EDN: SZBLFM
- DOI: 10.31857/S0044185623700225
Аннотация
Исследована микроструктура, фазовый состав и стойкость к окислению при нагреве на воздухе в интервале температур 600–1100°С композитов, синтезированных в режиме безгазового горения реакционных порошковых смесей титана, алюминия и кремния. Также исследованы силицид Ti5Si3 и триалюминид титана TiAl3, синтезированные из двухкомпонентных смесей. Продукты горения трехкомпонентных смесей содержат Ti5Si3 и TiAl3, соотношение которых зависит от содержания алюминия в реакционных смесях. Окалиностойкость синтезированных порошковых композитов в большей степени определяется микроструктурой гранул, чем их фазовым составом. Определен состав реакционной порошковой смеси, продукты горения которой имеют окалиностойкость в 1.5–3 раза выше, чем продукты горения остальных исследованных составов.
ВВЕДЕНИЕ
Титан и его сплавы являются перспективными конструкционными материалами современной техники. Благодаря высокой удельной прочности и стойкости в агрессивных средах они широко применяются в медицине, в аэрокосмической и химической промышленности. Один из существенных недостатков титана и его сплавов – низкая коррозионная стойкость при нагреве на воздухе или в кислородсодержащих средах [1]. При взаимодействии с кислородом на поверхности образуется рыхлая окалина из TiO2 (рутил), которая не препятствует проникновению кислорода к поверхности металла [2]. Для улучшения окалиностойкости титановых сплавов применяют легирование. При этом некоторые из легирующих элементов одновременно повышают прочность сплавов. Наиболее значимое полезное влияние на окалиностойкость титановых сплавов и алюминидов титана оказывает кремний [3, 4], ниобий [5, 6], хром [7].
Другой способ повышения стойкости к окислению изделий из титана и его сплавов – нанесение защитных (барьерных) покрытий на их поверхности, подверженные воздействию кислорода. Силициды титана являются наиболее функционально и технологически оправданным материалом для окалиностойких покрытий на титане. Силициды металлов имеют высокую стойкость к окислению [3] благодаря образованию на их поверхности плотной окалины SiO2, препятствующей проникновению кислорода к металлической поверхности. Силицидные покрытия на титане наносятся различными способами: силицированием при высокотемпературной выдержке в порошке кремния [8], оплавлением лазером слоя из порошковой смеси Ti и Si, нанесенной на поверхность [9]. В работе [10] покрытие получали в процессе экзотермической реакции синтеза в нанесенной на поверхность порошковой смеси состава, соответствующего силициду Ti5Si3. Продукт синтеза состоял из наружного слоя силицида Ti5Si3 и нижележащего слоя эвтектики, который обеспечивал прочное сцепление покрытия с титановой подложкой.
Более стойкие к окислению гибридные покрытия на титане получены диффузионным отжигом в вакууме при 900–1100°С после кратковременного погружения титанового образца в расплав Al–20% Si [11]. При окислении на воздухе при 850°С в покрытии образуется плотная окалина из Al2O3, препятствующая проникновению кислорода к поверхности металла. Создание на поверхности барьерного слоя Al2O3 особенно актуально для алюминидов титана, которые являются перспективными материалами для деталей двигателей авиационной и ракетной техники, работающих в реактивных газовых средах при температурах выше 1000°С. Однако из трех алюминидов титана, присутствующих на двойной равновесной диаграмме, только на поверхности TiAl3 при окислении образуется однослойное покрытие Al2O3 [2, 12]. На Ti3Al и TiAl окалина многослойная и содержит в основном, двойные и тройные оксиды титана [13, 14], которые не обладают защитными свойствами. По этой причине предпринимаются попытки создания Al2O3 покрытий на титановых сплавах и алюминидах титана.
Наряду с исследованиями влияния легирования на окалиностойкость алюминидов титана ведутся работы по созданию композитов с алюминидной матрицей. Наибольший интерес в качестве третьего элемента при разработке таких композитов представляет кремний. При малом содержании кремния в сплаве при кристаллизации выпадают дисперсные частицы Ti5Si3, которые служат упрочняющей фазой в алюминидной матрице [15–17]. При большом содержании кремния в смесях с титаном и алюминием образуется композит, состоящий из алюминидов титана и силицида титана Ti5Si3, объемная доля которого определяется содержанием кремния в сплаве.
Для получения композитов “силицид титана–алюминид титана” обычно применяют порошковые технологии: реакционное спекание [18, 19] или самораспространяющийся высокотемпературный синтез (СВС) в реакционных порошковых смесях Ti–Al–Si [20, 21]. Состав реакционных смесей рассчитывают из условия образования силицида Ti5Si3 и одного из конструкционных алюминидов титана, в основном TiAl. При горении образуется пористый спек, для уплотнения которого применяют различные методы: длительный отжиг, горячее прессование, искровое плазменное спекание (SPS). При дополнительной термической обработке одновременно с уплотнением происходит установление равновесного фазового состава продуктов синтеза. Беспористые или малопористые композиты “силицид титана – алюминид титана” представляют практический интерес как конструкционные материалы с высокой удельной прочностью для применения при высоких температурах. Композиционные порошки – продукты СВС можно использовать для напыления и наплавки износостойких и защитных покрытий. Однако в известной нам литературе имеются лишь единичные работы как по методам синтеза композитов “силицид титана–алюминид титана”, так и по исследованию их свойств.
Поэтому в настоящей работе исследован фазовый состав, микроструктура и окалиностойкость порошковых продуктов синтеза в реакционных смесях титан–алюминий–кремний. Практической целью исследований было установить составы реакционных смесей, продукты синтеза в которых обладают наибольшей стойкостью к окислению.
МАТЕРИАЛЫ И МЕТОДЫ ИССЛЕДОВАНИЙ
Для проведения СВС были приготовлены реакционные смеси составов, указанных в табл. 1. Там же приведен расчетный целевой состав продуктов синтеза (при условии образования при синтезе силицида Ti5Si3 стехиометрического состава). Реакционные смеси готовили из порошков титана (ТПП-8; <160 мкм; 99.4%), алюминия (ПА-4, <100 мкм; 99.3%) и кремния (Кр-00; <40 мкм; 99.45%). Порошки смешивали 4 часа всухую и прессовали в цилиндрические образцы ∅ 20 × 25 мм пористостью 32–36%. В случае необходимости смеси подвергали механоактивации (МА) в планетарной мельнице при скорости вращения 480 об./мин (16 g) и при соотношении масс шаров и смеси равном 20. Время МА зависело от состава смеси и было минимальным, необходимым для устойчивого горения прессовок в волновом режиме. Синтез проводили в герметичном реакторе в среде аргона с избыточным давлением 0.5 атм. Горение инициировали нагревом поджигающей таблетки молибденовой спиралью, через которую пропускали электрический ток. С целью измерения температуры горения посередине высоты прессовки просверливали глухое отверстие диаметром 2 мм, в которое помещали спай термопары ВР5-ВР20 с диаметром термоэлектродов 100 мкм. Максимальную температуру при прохождении фронта горения определяли из термограмм автоматической записи сигнала с термопары.
Таблица 1.
Шихтовый состав реакционных смесей и целевой состав продуктов
Номер смеси |
Целевой состав продуктов СВС |
Состав смесей, мас. % | Подготовка смесей | ||
---|---|---|---|---|---|
Ti | Si | Al | |||
1 | Ti5Si3 + 10% Al | 66.57 | 23.43 | 10 | Смешивание |
2 | Ti5Si3 + 20% Al | 59.18 | 20.82 | 20 | Смешивание + МА 10 мин |
3 | Ti5Si3 + 30% Al | 51.78 | 18.22 | 30 | Смешивание + МА 15 мин |
4 | Ti5Si3 + 40% Al | 44.38 | 15.62 | 40 | Смешивание + МА 30 мин |
5 | Ti5Si3 | 73.97 | 26.03 | – | Смешивание |
6 | Al3Ti | 37.2 | – | 62.8 | Смешивание |
Полученный рыхлый спек из продуктов синтеза дробили и рассеивали на фракции. Для испытания на стойкость к окислению использовали фракцию гранул СВС продукта 80–200 мкм. Пробы порошка массой 2 г насыпали слоем толщиной 3–5 мм в керамические лодочки из окиси алюминия. Лодочки с порошком помещали в печь СНОЛ, предварительно разогретую до необходимой температуры и выдерживали в течение 3–12 ч. После каждого трехчасового цикла лодочки вынимали из печи. Привес с точностью до 1 мг определяли взвешиванием лодочек до и после очередного цикла. Опыт повторяли на трех отдельных партиях навесок, величину привеса усредняли. В предварительных опытах было установлено, что вес пустых лодочек, выдержанных в печи 12 ч при температурах 600–1100°С, не изменяется. Таким образом вносить поправку на изменение веса лодочек нет необходимости.
Исходные и окисленные порошки исследовали на оборудовании Центра коллективного пользования “Нанотех” ИФПМ СО РАН методом рентгеноструктурного анализа (дифрактометр (ДРОН-3, CuKα-излучение), оптической металлографии (AXIOVERT-200MAT, Zeiss, Germany). Идентификацию фаз по результатам рентгеноструктурного анализа проводили с применением базы рентгеновских данных ASTM, а обработку первичных результатов – с использованием программ RENEX и PDWIN. Образцы для металлографических исследований готовили шлифовкой и полировкой алмазными пастами гранул СВС продукта, залитых в эпоксидную смолу.
РЕЗУЛЬТАТЫ И ОБСУЖДЕНИЕ
Фазовый состав и микроструктура продуктов синтеза
Для обеспечения устойчивого волнового режима горения смеси с 20, 30 и 40% алюминия подвергали механоактивации (см. табл. 1). Прессовки из остальных составов устойчиво горели без предварительной механоактивации реакционных смесей. Температура горения зависит от содержания алюминия в реакционных смесях: с увеличением содержания алюминия Тг монотонно уменьшается (рис. 1).
Фазовый состав продуктов синтеза, полученный на основе результатов обработки рентгенограмм, приведен в табл. 2. Видно, что в результате СВС в двухкомпонентных порошковых смесях образуются однофазные продукты: силицид титана Ti5Si3 (смесь № 5) и триалюминид титана TiAl3 (смесь № 6). В смесях, содержащих порошок алюминия, основными продуктами синтеза являются силицид титана Ti5Si3 и триалюминид титана TiAl3. Обнаруживается также присутствие примеси оксида алюминия, содержание которой наибольшее в продуктах синтеза из смесей с 40 и 50 мас. % алюминия. Вероятное происхождение оксида алюминия наряду с окисной пленкой на порошке – окисление алюминия в процессе обработки в планетарной мельнице в среде аргона технической чистоты. При увеличении содержания алюминия в смесях содержание силицида монотонно уменьшается с одновременным увеличением содержания триалюминида титана и становится примерно равным при содержании 40% алюминия в реакционной смеси.
Таблица 2.
Фазовый состав продуктов СВС (об. %)
№ смеси | Целевой состав продуктов СВС | Ti5Si3 | TiAl3 | Al2O3 |
---|---|---|---|---|
1 | Ti5Si3 + 10% Al | 79 | 21 | – |
2 | Ti5Si3 + 20% Al | 73 | 27 | – |
3 | Ti5Si3 + 30% Al | 65 | 26 | 9 |
4 | Ti5Si3 + 40% Al | 52 | 41 | 7 |
5 | Ti5Si3 | 100 | – | – |
6 | TiAl3 | – | 100 | – |
Наблюдается сильная зависимость дисперсности и морфологии продуктов синтеза от содержания алюминия в реакционных смесях (рис. 2). Продукт горения двухкомпонентной смеси титан – кремний состоит из крупных ограненных зерен силицида с редкими включениями эвтектики (рис. 2а). Грубодисперсная структура силицида объясняется высокой температурой горения этого состава (рис. 1). Благодаря широкому температурному интервалу существования расплава, который простирается от температуры на фронте реакции до температуры эвтектической кристаллизации (1330°С), на стадии охлаждения происходит ничем не ограниченный рост силицидных зародышей до крупных ограненных кристаллов. Характерным признаком структуры гранул силицида являются многочисленные поры различного размера (рис. 2а). В отличие от силицида триалюминид титана в процессе синтеза образует плотные беспористые зерна округлой формы и конгломераты из более мелких зерен (рис. 2е).
Рис. 2.
Микроструктура продуктов синтеза в реакционных смесях с различным содержанием алюминия (мас. %): (а) 0%; (б) 10%; (в) 20%; (г) 30%; (д) 40%; (е) состав смеси 3Al + Ti.
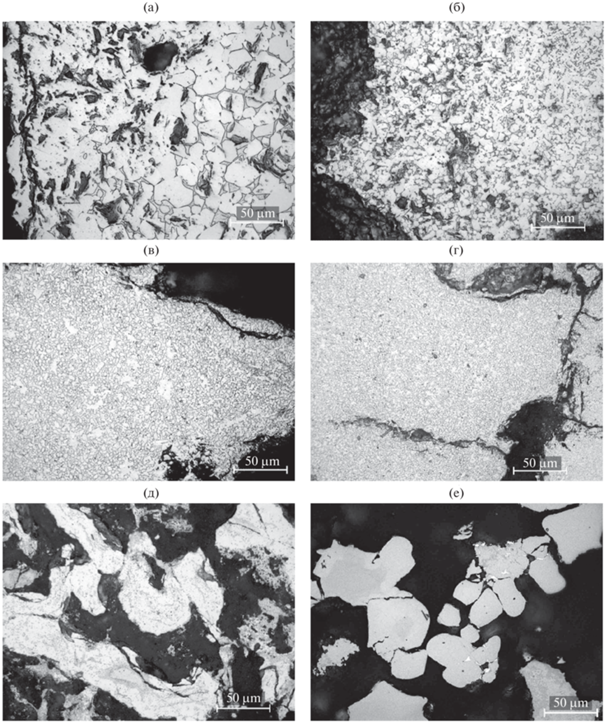
Дисперсность продуктов синтеза в трехкомпонентных смесях увеличивается при увеличении содержания алюминия в смесях до 30% включительно. Измельчение структуры объясняется, с одной стороны сужением интервала существования расплава из-за понижения температуры горения (рис. 1), а с другой – стесненными условиями роста силицидных зародышей. Препятствием для их роста являются кристаллы триалюминида титана, которые появляются при температуре 1395°С. Объемная доля кристаллов TiAl3 вытянутой формы (whiskers) наибольшая (около 50% согласно результатам рентгеноструктурного анализа) в продуктах горения смеси с 30% алюминия (см. рис. 2г).
Кинетика окисления и фазовый состав продуктов окисления
Кинетические кривые увеличения привеса порошков при выдержке на воздухе при температурах от 600 до 1100°С приведены на рис. 3. При всех исследованных температурах скорость окисления максимальна в первые 3 ч выдержки, а затем монотонно уменьшается при увеличении времени выдержки. Линейная зависимость привеса от времени выдержки наблюдается только в единственном случае: при окислении при 1000°С композита, синтезированного из смеси № 1 (см. табл. 1). Согласно таблице 2 фазовый состав этого композита качественно и количественно мало отличается от других композитов, синтезированных из трехкомпонентных смесей (№ 2, 3, 4), однако он имеет сильно дефектную, пористую структуру (рис. 2а). Возможно, что эта дефектность и является причиной аномального линейного роста при температуре 1000°С.
Имея в виду многокомпонентность и дефектность структуры исследованных нами порошков, не ставилась задача установить кинетический закон роста окалины. Поэтому привес при длительности окисления менее 3 ч не определялся. Фазовый состав и скорость роста окалины на поверхности двух основных фаз (силицида и триалюминида) в структуре композиционных порошков должны отличаться. Кроме того из-за ускоренной диффузии по межфазным границам величина привеса может зависеть от площади удельной межфазной поверхности, то есть от дисперсности структуры композита. Также на величину привеса влияют открытые поры и трещины в гранулах, которые облегчают доступ кислорода к поверхности.
Согласно рис. 3 стойкость к окислению исследованных порошков зависит от их состава и температуры. Далее приведена сравнительная характеристика окалиностойкости всех исследованных порошков. При минимальной температуре (600°С) наибольшую стойкость имеет триалюминид титана, привес которого на порядок меньше привеса остальных порошков (рис. 3а).
При более высоких температурах стойкость TiAl3 к окислению мало отличается от окалиностойкости остальных порошков: кинетические кривые привеса порошка TiAl3 располагаются примерно посередине массива остальных кривых (рис. 3). Кинетические кривые привеса силицида и триалюминида титана для температур 1000 и 1100°С располагаются рядом, но стойкость Ti5Si3 выше, чем у TiAl3. После выдержки 12 часов при 800°С привес порошков этих соединений одинаков, при этом ход кинетических кривых сильно отличается (рис. 3б).
Из трехкомпонентных композитов наименьшую скорость высокотемпературного (1000 и 1100°С) окисления имеет СВС порошок, синтезированный из смеси № 2. Величина привеса этого композита после выдержки на воздухе до 12 ч в 1.5–3 раза меньше, чем у остальных исследованных порошков, включая порошки силицида и триалюминида титана (рис. 3). Так как фазовый состав этого порошка мало отличается от фазового состава остальных трехкомпонентных СВС порошков, то основной причиной его более высокой окалиностойкости может быть плотная беспористая структура гранул (рис. 2в).
Фазовый состав продуктов окисления был определен методом рентгеноструктурного анализа. Рентгенограммы приведены на рис. 4а результаты обработки рентгенограмм – в табл. 3. Видим, что после 12 часов окисления при 1000°С в окалину, состоящую из оксидов Al2O3 и TiO2, переходит от 30 до 50% от исходного объема порошков. Продукты окисления Ti5Si3 содержат только TiO2. Оксида SiO2, который согласно [3] образует плотный защитный слой на силицидах, не обнаружено. Продукты окисления порошка TiAl3 наряду с основным Al2O3 содержат также TiO2. Окалина, образующая на трехкомпонентных композитах, примерно на две трети состоит из Al2O3, остальное – TiO2. Соотношение содержания оксидов Al2O3/TiO2 в окалине в целом увеличивается по мере увеличения соотношения TiAl3/Ti5Si3 в окисляемых композиционных порошках (см. табл. 3).
Рис. 4.
Рентгенограммы с порошков, окисленных 12 ч при 1000°С. (а) Композиционные порошки, синтезированные из смесей с содержанием алюминия (мас. %): 1 – 10%; 2 – 20%; 3 – 30%; 4 – 40%. (б) Порошки, синтезированные из двухкомпонентных смесей.
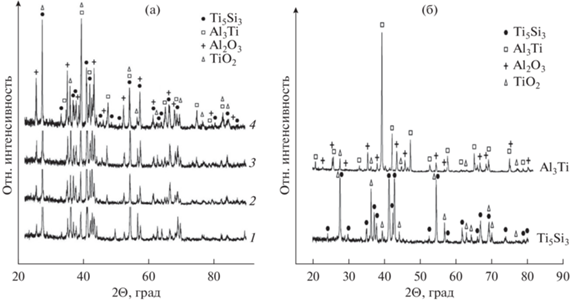
Таблица 3.
Фазовый состав (об. %) после 12 ч окисления при 1000°С
№ | Целевой состав продуктов СВС |
Фактическое содержание фаз после окисления | |||
---|---|---|---|---|---|
Ti5Si3 | Ti Al3 | Al2O3 | TiO2 | ||
1 | Ti5Si3 + 10% Al | 47 | 2 | 33 | 18 |
2 | Ti5Si3 + 20% Al | 45 | 7 | 35 | 13 |
3 | Ti5Si3 + 30% Al | 31 | 12 | 40 | 17 |
4 | Ti5Si3 + 40% Al | 27 | 16 | 41 | 16 |
5 | Ti5Si3 | 65 | – | – | 35 |
6 | TiAl3 | – | 71 | 21 | 8 |
ВЫВОДЫ
1. Продукты синтеза в порошковых смесях титана, кремния и алюминия представляют собой композит из двух тугоплавких соединений: силицид титана Ti5Si3 и триалюминид титана TiAl3. Относительное содержание силицида и алюминида, дисперсность структуры и степень дефектности гранул композита зависят от содержания алюминия в реакционных порошковых смесях.
2. Величина привеса порошковых композитов при выдержке на воздухе при температурах 600–1100°С определяется в бóльшей степени дефектностью структуры гранул (поры и трещины), а не их фазовым составом.
3. Установлен состав реакционной смеси, продукты синтеза в которой имеют окалиностойкость в 1.5–3 раза выше, чем у других исследованных композитов, а также у однофазных силицида и триалюминида. Композиционные порошки, синтезированные из смеси этого состава, представляют практический интерес в качестве фидстоков для напыления окалиностойких покрытий на титан и его сплавы.
Список литературы
Головко Э.И. Высокотемпературное окисление металлов и сплавов. Справочник. Киев: Наук. Думка, 1980. 296 с.
Dai J., Zhu J., Chen C., Weng F. // J. Alloys and Compounds. 2016. V. 685. P. 784–798.
Mitra R. // Internal Materials Reviews. 2006. V. 51. P. 13–64.
Pribytkov G.A., Krinitsyn M.G., Korzhova V.V. et al. // Prot. Met. Phys. Chem. Surf. 2022. V. 58. P. 70–75.
Yoshihara M.M., Miura K. // Intermetallics. 1995. V. 3. P. 351–363.
Quiang S., Liu B., Li J. et al. // Materials Science and Engineering. Powder metallurgy. 2015. V. 20(4). P. 616–622.
Dong Z., Jiang H., Feng X., Wang Z. // Trans. Nonferrous Met. Soc. China. 2006. V. 16. P. 2004–2008.
Liang W., Zhao X.G. // Scripta mater. 2001. V. 44. P. 1049–1054.
Wu Y., Wang A.H., Zhang Z. et al. // Applied Surface Science. 2014. V. 305. P. 16–23.
Riley D.P. // Intermetallics. 2006. V. 14. P. 770–775.
Vojtech D., Kubatik T., Pavlickova M., Maixner J. // Intermetallics. 2006. V. 14. P. 1181–1186.
Udayashankar N.K., Rajasekaran S., Nayak Jagannath // Trans. Indian Inst. Met. 2008. V. 61. № 2–3. P. 231–233.
Li Z., Gao W., He Y., Li S. // High Temperature Materials and Processes. 2002. V. 21. № 1–2. P. 35–45.
Lavrenko V.O., Firstov S.O., Panasyuk A.D. et al. // Powder Metallurgy and Metal Ceramics. 2003. V. 42. № 3–4. P. 184–188.
Sun F.S., Kim S.E., Cao C.X. et al. // Scripta Materialia. 2001. V. 456. P. 383–389.
Sun F.S., Froes F.H. (Sam) // Materials Science and Engineering A. 2003. V. 345. P. 262–269.
Tkachenko S., Datskevich O., Dvorak K., Kulak L. // J. Alloys and Compounds. 2017. V. 694. P. 1098–1108.
Nov’ak P., Michalcov’a A., Šeráak J. et al. // J. Alloys and Compounds. 2009. V. 470. P. 123–126.
Novak P., Pruša F., Šerak J. et al. // J. Alloys and Compounds. 2010. V. 504. P. 320–324.
Zha M., Wang H.Y., Li S.T. et al. // Materials Chemistry and Physics. 2009. V. 114. P. 709–715.
Zha M., Wang H.Y., Li S.T. et al. // ISIJ International. 2009. V 49. № 3. P. 453–457.
Дополнительные материалы отсутствуют.
Инструменты
Физикохимия поверхности и защита материалов