Физикохимия поверхности и защита материалов, 2023, T. 59, № 2, стр. 188-194
Коррозионное поведение аморфного сплава Fe80.22Si8.25Nb10.09Cu1.44 в щелочных растворах c добавками роданида калия
В. А. Федоров 1, *, Д. В. Балыбин 1, Т. Н. Плужникова 1, Д. Ю. Федотов 1, А. Д. Березнер 1, М. В. Бойцова 1
1 Федеральное государственное бюджетное образовательное учреждение высшего образования
“Тамбовский государственный университет имени Г.Р. Державина”
392000 Тамбов, ул. Интернациональная, 33, Россия
* E-mail: fedorov-tsu.tmb@inbox.ru
Поступила в редакцию 09.11.2022
После доработки 25.11.2022
Принята к публикации 09.12.2022
- EDN: SZEMWF
- DOI: 10.31857/S0044185623700237
Аннотация
Изучено электрохимическое и коррозионное поведение аморфного металлического сплава (АМС) Fe80.22Si8.25Nb10.09Cu1.44 в щелочных водных растворах с добавками роданида калия. При концентрациях КSCN 0.5; 1.0; 10.0 мМ отмечено увеличение скоростей электродных процессов (стимулирование) по сравнению с фоновым раствором. При концентрации 5.0 мМ наблюдается торможение как катодного, так и анодного процессов (ингибирование). Это объяснено в рамках механизма электрохимических процессов и особенностей строения материала электрода. Исследовано изменение механических свойств АМС после воздействия щелочной среды состава 0.5 М КОН + yмM KSCN, где y = 0.5; 1.0; 5.0, 10.0. Установлено изменение шероховатости поверхности. Изменяется характер разрушения от хрупкого скола, без воздействия среды, до пластического, с ветвлением трещин, образованием складчатых структур для всех используемых растворов. При воздействии раствора 0.5 М КОН + 5 мM KSCN наблюдается двукратное снижение предела прочности и модуля Юнга. Рост концентрации KSCN приводит к увеличению микротвердости поверхности.
ВВЕДЕНИЕ
Расширение областей применения аморфных металлических сплавов (АМС) или металлических стекол стимулирует практический интерес к их коррозионной стойкости. АМС на основе железа более устойчивы к коррозии по сравнению с их кристаллическими аналогами [1], что обусловлено отсутствием в аморфной структуре характерных для кристаллических фаз дефектов [2].
Коррозионная стойкость может быть повышена в результате структурной релаксации, что связано со снижением остаточных напряжений, и предполагаемым увеличением энергии активации, перераспределением химических элементов на поверхности [3] и, следовательно, уменьшением количества активных областей коррозии [4].
Изучение поведения ленточных образцов АМС на основе железа в растворе Рингера показало, что коррозионная стойкость значительно увеличивается с ростом содержания ниобия [5–7], хрома [8]. В сплаве, содержащем молибден, частичная замена его на ниобий также повышает коррозионную стойкость [9]. Кроме того, в содержащие молибден аморфные сплавы на основе железа вводят такие легирующие элементы как вольфрам, иттрий, марганец, азот [10, 11], что приводит к повышению коррозионной стойкости за счет образования дополнительных оксидных, нитридных фаз в пассивирующем слое. Эффект влияния молибдена на коррозионные характеристики аморфных сплавов на основе железа также зависит от уровня кислотности коррозионной среды [12–14].
На коррозионную стойкость влияют и аморфизирующие добавки. Так, например, фосфор более эффективен для повышения коррозионной стойкости, чем бор. Наличие углерода в составе объемных металлических сплавов ускоряет активное растворение сплавов [15], тогда как кремний повышает коррозионную стойкость [16–21].
Из вышеизложенного следует, что коррозионная стойкость АМС на основе железа остается малоизученным явлением.
Цель работы: установить влияние щелочных сред и концентрации в них роданида калия на электрохимические, и адсорбционные процессы, протекающие в аморфных сплавах на основе железа, а также на изменение их механических свойств.
МЕТОДИКА
Объектом исследования выбран аморфный сплав АМАГ – 200 (Fe – 80.22%; Si – 8.25%; Nb – 10.09%; Cu – 1.44%), полученный методом спиннингования. Размеры образцов 50 × 3.35 × 0.020 мм.
Для оценки скоростей парциальных электрохимических реакций использовали поляризационные измерения. Измерения проведены на неподвижном электроде в потенциостатическом режиме на комплексе, состоящем из анализатора частотного отклика и потенциостата Solartron 1287. Для оценки коррозионной стойкости и электрохимического поведения аморфных сплавов на основе железа использовали щелочную среду состава 0.5 М КОН + y мM KSCN, где y = = 0.5; 1.0; 5.0, 10.0. Время выдержки 30 мин. Роданид калия вводили с целью изучения адсорбции поверхностно-активного роданид – иона на поверхности аморфного сплава. Электрод для электрохимических измерений с рабочей поверхностью 0.5 см2, армированный в оправку из эпоксидной смолы ЭД-5 с полиэтиленполиамин отвердителем, перед экспериментом обезжиривался ацетоном. В исследованиях была использована трехэлектродная электрохимическая ячейка из стекла “Пирекс” с разделенными катодным и анодным пространствами. Электрод сравнения – насыщенный хлоридсеребряный, вспомогательный – Pt. Потенциалы пересчитаны по стандартной водородной шкале. Поляризацию проводили из катодной области в анодную посредством потенциодинамической поляризации со скоростью развертки 0.66 мВ/с.
Механические испытания обработанных образцов проводили на электромеханической машине для статических испытаний Instron-5565. Морфологию поверхности разрушения образцов исследовали на растровом электронном микроскопе Jeol. Рельеф поверхности исследовали на сканирующем зондовом микроскопе ФемтоСкан. Микротвердость измеряли на микротвердомере ПМТ-3М.
ЭКСПЕРИМЕНТАЛЬНЫЕ РЕЗУЛЬТАТЫ И ИХ ОБСУЖДЕНИЕ
Результаты электрохимических измерений на АМАГ-200 в щелочных растворах, содержащих добавки КSСN
Поляризационные кривые, снятые на образцах АМАГ-200, имеют характерный вид для материалов из железа и его сплавов. Введение минимальных количеств добавки КSСN (0.5 и 1.0 мМ) в щелочные растворы качественно не изменяет характер катодной и анодной ветвей поляризационной кривой, на которой в катодной области можно выделить участок с диффузионным контролем, а в анодной области участки пассивации и активного растворения (рис. 1).
Рис. 1.
Электрохимическое поведение сплава АМАГ-200 в растворе 0.5 М КОН при различных концентрациях КSСN. 1 – фоновый раствор, 2 – 0.5 мM KSCN, 3 – 1 мM KSCN, 4 – 5 мM KSCN, 5 – 10 мM KSCN.
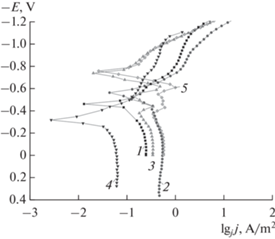
В щелочной среде катодный процесс восстановления кислорода имеет вид:
Процесс анодного растворения железа протекает через несколько стадий (Б.Н. Кабанов, Д.И. Лейкис, Р.Х. Бурштэйн, А.М. Фрумкин) [22, 23].
Очевидно, что в рассмотренной последовательности реакций замедленной является стадия переноса второго электрона с образованием адсорбционного оксида железа, а стадия последней химической реакции является квазиравновесной (быстрой).
Однако, содержание 0.5 и 1.0 мМ добавки КSСN приводит к существенным изменениям в количественных характеристиках. Так, при введении 0.5 мМ КSСN происходит смещение потенциала коррозии в катодную область (из-за адсорбции роданид-ионов на поверхности АМС), скорость катодной реакции при этом изменяется незначительно, а анодной – существенно возрастает. Этот факт можно объяснить тем, что принципиально механизм катодного и анодного процессов не меняется, но увеличивается скорость парциальных электродных реакций за счет увеличения скоростей квазиравновесных стадий из-за влияния адсорбции поверхностно-активных роданид-ионов. Следует отметить, что характер лимитирующей стадии при этом не изменяется, в противном случае изменялись бы и тафелевские [24] углы наклонов соответствующих участков поляризационной кривой.
При содержании 5 мМ KSCN наблюдается смещение потенциала в анодную область и значительное замедление как катодного, так и анодного процесса по сравнению с фоновым раствором и растворами, содержащими 0.5 и 1.0 мМ добавки KSCN. При этом качественно ход кривой практически не меняется, следовательно, в условиях эксперимента 5 мМ может является пороговой концентрацией, при которой происходит изменение роли добавки со стимулирующей на ингибирующую.
При введении 10 мМ добавки KSCN вновь наблюдается стимулирование анодного процесса и, практически, не изменяется скорость катодного по сравнению с фоновым раствором. Это подтверждает, что 5 мМ KSCN может являться пороговой концентрацией, при которой происходит изменение характера влияния роданид-ионов на электрохимическое поведение сплава АМАГ-200. Это можно объяснить влиянием четырех факторов.
1. Известно [25], что компонент системы меняет свое влияние со стимулирующего на ингибирующее в зависимости от концентрации в растворе. В этом случае принципиальное значение приобретает механизм электрохимического процесса, который подробно рассмотрен в [26]. Подобное явление описывается при определенных значениях порядков реакции по частицам добавки, выполняющим роль стимулятора/ингибитора по формуле [27]:
Следует отметить, что увеличение скорости коррозии может наблюдаться и при торможении одного из частных процессов. Так, например, если $n_{k}^{{{\text{инг}}}}$ = 1, $n_{a}^{{{\text{инг}}}} = - 1$, то добавка все-таки будет стимулятором, поскольку, как правило, ${{b}_{k}} > {{b}_{a}}$. Именно поэтому ускорение под влиянием поверхностно-активных веществ катодного процесса чаще всего приводит к увеличению скорости коррозии, несмотря на значительное замедление анодного процесса.
2. Существенный вклад вносит процесс адсорбции поверхностно-активного иона SCN– на аморфной металлической поверхности. По мере увеличения концентрации ионов SCN– в растворе происходит частичное пассивирование поверхности электрода, и анодная реакция протекает лишь на части поверхности. Значительная часть электрода выводится из сферы анодной реакции [25]. В этом случае возникает вопрос о концентрации 5 мМ KSCN добавки, поскольку торможение анодного процесса здесь наибольшее. Вероятно, при данном соотношении концентраций ионов SCN– и ОН– происходит максимальное заполнение ионами активных центров, что способствует их блокировке за счет образования трудно растворимых соединений железа, в результате чего происходит сильное торможение анодного процесса и уменьшение тока пассивации.
3. Роданид-ионы, являясь поверхностно-активными, способны не только адсорбироваться на активных центрах поверхности, но и принимать участие в электрохимических процессах, в частности, в стадиях анодного растворения железа наравне с ионами ОН–. К примеру, при пороговой концентрации KSCN, наряду с лимитирующей стадией
В этом случае две приведенные реакции могут являться лимитирующими и протекать с соизмеримыми скоростями, при этом, если при некотором значении анодной поляризации одна из реакций становится квазиравновесной, то вторая продолжает лимитировать процесс и обусловливать пассивное состояние электрода. Естественно, характер влияния каждой из стадий будет в значительной мере определяться стабильностью образующегося адсорбционного комплекса. В первом приближении, можно считать, что устойчивость Fe(OН)SCN выше, чем FeOадс, так как, по сравнению с фоновым раствором, происходит значительное уменьшение скорости анодного процесса.
4. Существенное изменение скорости анодного процесса, может определяться аморфным строением материала электрода. Важной характеристикой аморфных структур является свободный объем. Его можно определить, например, через величину относительного свободного объема $f\left( T \right) = {{\left( {V\left( T \right) - V\left( 0 \right)} \right)} \mathord{\left/ {\vphantom {{\left( {V\left( T \right) - V\left( 0 \right)} \right)} {V\left( 0 \right)}}} \right. \kern-0em} {V\left( 0 \right)}}$ [28], где $V\left( T \right)$ и $V\left( 0 \right)$ – объем материала соответственно при температуре T и при 0 К. Свободный объем может быть распределен равномерно или сосредоточен в виде микропор. В случае пороговой концентрации добавки 5 мМ KSCN может происходить максимальное заполнение в поверхностном и приповерхностном слоях свободного объема аморфной структуры. В результате уменьшается как скорость анодного растворения электрода, так и ток пассивации. Дальнейшая активация анодного процесса при увеличении концентрации добавки KSCN до 10 мМ может быть объяснена тем, что из-за избыточной концентрации ионов SCN– в анодной реакции начинает протекать процесс их окисления с частичным освобождением свободного объема аморфного сплава в поверхностном и приповерхностном слоях. В этом случае анодный процесс будет аналогичен растворению электрода, протекающему в фоновом растворе.
Таким образом, следует учитывать каждый из перечисленных факторов при рассмотрении смены роли добавки роданида калия со стимулятора на ингибитор при пороговой концентрации 5 мМ KSCN. Лимитирующий фактор выделить не представляется возможным в условиях настоящего эксперимента. Очевидно, наблюдается комплексное их влияние, как на интегральную скорость электрохимических процессов, так и скорость парциальных электродных реакций в рассматриваемых условиях.
РЕЗУЛЬТАТЫ ИССЛЕДОВАНИЯ МЕХАНИЧЕСКИХ СВОЙСТВ АМАГ-200 ПОСЛЕ ВЫДЕРЖКИ В ЩЕЛОЧНЫХ РАСТВОРАХ, СОДЕРЖАЩИХ ДОБАВКИ КSСN
В результате воздействия растворов 0.5 М КОН + y мM KSCN, где y = 0.5; 1.0; 5.0, 10.0 поверхность материала существенно меняется. Наблюдается образование более выраженного поверхностного рельефа (рис. 2). На необработанных образцах величины шероховатости составляют 3.5–4 нм. При воздействии указанных растворов величина шероховатости меняется от 6 до 40 нм.
Рис. 2.
АСМ поверхности сплава АМАГ-200 (а) в исходном состоянии; (б) после выдержки в растворе 0.5 М КОН + + 10 мM KSCN.
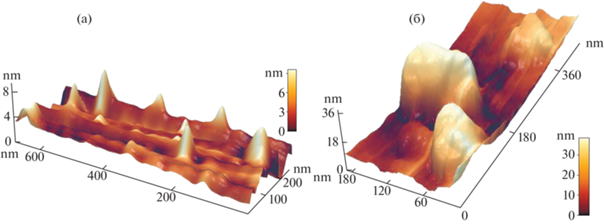
Аморфные сплавы после выдержки в растворах подвергали одноосной деформации в электромеханической машине Instron-5565 со скоростью движения траверсы 0.1 мм/мин. Разрушение аморфного сплава на основе железа без воздействия указанных сред происходит хрупко, ветвлений трещин и складчатых структур не наблюдается (рис. 3).
Рис. 3.
Разрушение аморфного сплава АМАГ-200 после деформации в исходном состоянии без воздействия растворов: (а) траектория трещины на поверхности наблюдения; (б) поверхность разрушения (отмечено стрелками).
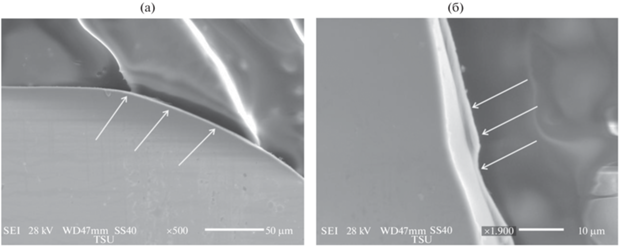
После выдержки сплавов в указанных растворах картина деформации существенно меняется. При действии раствора 0.5 М КОН + 5 мM KSCN наблюдается расслоение материала по поверхности излома (рис. 4а), образование полос сдвига и ступенчатых структур (рис. 4б) на поверхности наблюдения. После воздействия раствора 0.5 М КОН + 10 мM KSCN образуются трещины, ответвляющиеся от траектории магистральной (рис. 5а), а на поверхности излома формируются чешуйчатые структуры (рис. 5б).
Рис. 4.
Разрушение аморфного сплава АМАГ-200 после деформации и выдержки в растворе 0.5 М КОН + 5 мM KSCN: (а) утяжки материала на поверхности излома; (б) образование складчатых структур.
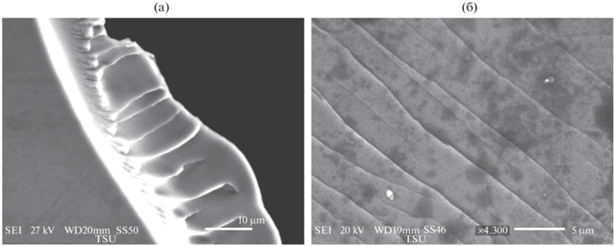
Рис. 5.
Разрушение аморфного сплава АМАГ-200 после деформации и выдержки в растворе 0.5 М КОН + 10 мM KSCN: (а) образование ответвляющихся трещин; (б) чешуйчатые структуры на поверхности излома.

Предел прочности аморфного сплава АМАГ-200 в исходном состоянии составляет 2200 МПа. После воздействия щелочной среды состава 0.5 М КОН + y мM KSCN, где y = 0.5; 1.0; 10.0 он не меняется (рис. 6). Исключение составляет только значение предела прочности, который падет в два раза при концентрации раствора 0.5 М КОН + 5 мM KSCN, и составляет около 1100 МПа (рис. 6).
Рис. 6.
Диаграмма нагружения для сплава АМАГ-200: 1 – без воздействия растворов; 2 – после выдержки в растворе 0.5 М КОН + 10 мM KSCN; 3 – после выдержки в растворе 0.5М КОН + 5 мM KSCN.
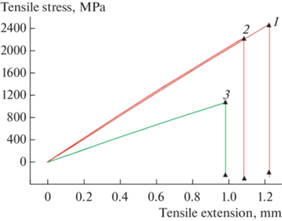
Модуль Юнга аморфного сплава АМАГ-200 для всех указанных растворов составляет около 109 ГПа, кроме раствора 0.5 М КОН + 5 мM KSCN, после воздействия которого, модуль Юнга падает до 55 ГПа.
Роданид-ионы являются поверхностно-активными ионами и в рассматриваемых системах адсорбируются на активных центрах поверхности вместе с ионами ОН– и молекулами растворителя. Так как качественный состав рассматриваемых систем не меняется, то эффект наблюдаемый при использовании раствора 5 мM KSCN можно объяснить только соотношением концентраций компонентов системы. При содержании 5 мM KSCN в растворе соотношение частиц SCN– и ОН– в растворе приводит к изменению соотношения занимаемых ими активных центров поверхности. В щелочных средах образование адсорбированного атомарного водорода на поверхности рабочего электрода происходит в результате электрохимического процесса Н2О + е → Надс + ОН–. Затем ад-атомы водорода могут образовывать молекулы в зависимости от того, по какому маршруту реализуется процесс и какая форма Надс на поверхности электрода преобладает. Согласно теории форм-водорода [29–31] на металлической поверхности реализуется равновесие: Hs ↔ Hr, где Hs (подповерхностный) – форма атомарного водорода, ответственная за его твердофазную диффузию, а Hr (надповерхностный) – форма, ответственная за молизацию водорода. Таким образом, при 5 мM KSCN наблюдается изменение числа активных центров поверхности ответственных за адсорбцию и дальнейшую твердофазную диффузию адсорбированного атомарного водорода (Hs). Введение в фоновые растворы роданида калия концентрацией 5 мM приводит не только к изменению энергии активных центров, но и, по-видимому, к смещению равновесия форм адсорбированного атомарного водорода в сторону подповерхностного водорода Hs, за счет определенного соотношения поверхностно активных частиц в системе. Такое влияние приводит к увеличению скорости процесса наводороживания аморфного сплава, в следствие чего, заполняется свободный объем аморфного сплава, в котором водород молизуется и вызывает охрупчивание материала, что подтверждается экспериментальными результатами.
Исследование микротвердости (рис. 7) показало, что при выдержке в указанных растворах значение твердости существенно возрастает. Это объясняется тем, что при увеличении концентрации добавки KSCN, наблюдается более заметное его влияние на поверхностный слой материла. При увеличении добавки до 5 и 10 мМ роданида калия происходит образование соединений железа на поверхности материала, которые увеличивают значение микротвердости по сравнению с исходной структурой.
ЗАКЛЮЧЕНИЕ
1. Введение роданида калия (0.5; 1.0 и 10.0 мМ) в фоновый раствор приводит к существенному увеличению скоростей электродных процессов, следовательно, в указанных концентрациях добавка оказывает стимулирующее действие на процесс коррозии сплава АМАГ-200 в щелочной среде.
2. 5 мМ роданида калия в фоновом растворе является пороговой концентрацией, т.к. приводит к уменьшению скоростей электродных процессов и уменьшению тока пассивации, что может быть объяснено как с точки зрения смены механизма процесса анодного растворения, так и с точки зрения особенностей аморфного строения материала электрода.
3. После воздействия щелочной среды состава 0.5 М КОН + y мM KSCN, где y = 0.5; 1.0; 5.0, 10.0 на поверхность аморфного сплава АМАГ-200 наблюдается изменение шероховатости поверхности с 4 нм в исходном состоянии до 40 нм после воздействия раствора. Наблюдается смена механизма разрушения от хрупкого скола без воздействия сред до ветвления трещин и образования складчатых структур после воздействия растворов.
4. Предел прочности и модуль Юнга при воздействии раствора 0.5 М КОН + 5 мM KSCN понижается практически в два раза, что может быть связано с процессами твердофазной диффузии водорода в материал. При увеличении концентрации KSCN значения микротвердости увеличиваются за счет образования на поверхности АМС пленки из труднорастворимых соединений (оксиды, гидроксиды железа).
Работа выполнена при финансовой поддержке гранта РНФ № 22-22-00226, результаты частично получены с использованием оснащения Центра коллективного пользования научным оборудованием ТГУ имени Г.Р. Державина.
Список литературы
Souza C., Ribeiro D.V., Kiminami C.S. // J. Non-Crystalline Solids. 2016. V. 442. P. 56.
Belkhaoudaa M., Bazzia L., Benlhachemib A., Salghic R., Hammoutid B., Kertite S. // J. Appl. Surf. Sci. 2006. V. 252. P. 7921.
Chattoraj I., Baunack S., Stoica M., Gebert A. // Mater. Corros. 2004. V. 55. P. 36.
Вьюгов П.Н., Дмитренко О.Е. // Вопросы атомной науки и техники. 2004. № 6. С. 185.
Zohdi H., Shahverdi H.R., Hadavi S.M.M. // Electrochem. Commun. 2011. V. 13. P. 840.
Souza C.A.C., May J.E., Oliveira M.F., Kuri S.E., Kiminami C.S., Carlos I.A. // J. Non-Cryst. Solids. 2002. V. 304. P. 210.
Zhai F., Pineda E., Duarte M.J., Crespo D. // J. Alloys Compd. 2014. V. 604. P. 157.
Botta W.J., Berger J.E., Kiminami C.S., Roche V., Nogueir R.P., Bolfarini C. // Journal of Alloys and Compounds. 2014. V. 586. P. S105.
Pang S.J., Zhang T., Asami K., Inoue A. // Mater. Trans. JIM. 2001. V. 42. P. 376.
Gostin P.F., Gebert A., Schultz L. // Corros. Sci. 2010. V. 52. P. 273.
Kuznetsov V.V., Filatova E.A., Telezhkina A.V., Kruglikov S.S. // J. Solid State Electrochemistry. 2018. V. 22. P. 2267.
Liqun M., Inoue A. // Mater. Lett. 1999. V. 38. P. 58.
Inoue A., Takeuchi A. // Intermetallics. 2010. V. 18. P. 1779.
Lu Z.P., Liu C.T., Porter W.D. // Appl. Phys. Lett. 2003. V. 83. P. 2581.
Gostin P.F., Oswald S., Schultz L., Geber A. // Corros. Sci. 2012. V. 62. P. 112.
Guo R.Q., Zhang C., Yang Y., Peng Y., Liu L. // Intermetallic. 2012. V. 30. P. 94.
Lopez M.F., Escudero M.L., Vida E. // Electroquim. Acta. 1997. V. 42. P. 659.
Movahedi B., Enayati M., Wong C. // J. Therm. Spray Technol. 2010. V. 19. P. 1093.
Souza C.A.C., Bolfarini C., Botta F.W.J., Andrade Lma L.R.P., Oliveira M.F., Kiminami C.S. // Mater. Res. 2013. V. 16. P. 1.
Wang S.L., Li H.X., Zhang X.F., Yi S. // Mater. Chem. Phys. 2009. V. 113. P. 878.
Zhang Z.C., CLong Z.L., Peng J., Wei H.Q., Tang P., Li X.G. // Rare Metal Mater. Eng. 2010. V. 39. P. 162.
Кабанов Б.Н., Лейкис Д.И. // Доклады АН СССР. 1947. V. 58. № 8. P. 1685.
Кабанов Б.Н., Бурштейн P.X., Фрумкин А.К. // Dis. Faraday Soс. 1947. V. l. P. 259.
Дамаскин Б.Б., Петрий О.А., Цирлина Г.А. Электрохимия. М.: Химия, КолосС, 2006. С. 496.
Розенфельд И.Л. Ингибиторы коррозии. М.: Химия, 1977. С. 252.
Вигдорович В.И., Цыганкова Л.Е. Кинетика и механизм электродных реакций в процессах коррозии металлов. Тамбов: Издательство Першина Р.В., 2010. С. 50.
Цыганкова Л.Е., Вигдорович В.И. Ингибиторы коррозии металлов. Тамбов: Издательство Першина Р.В., 2010. С. 136.
Рябов А.В., Окишев К.Ю. Новые металлические материалы и способы их производства. Издательство ЮУрГУ, Челябинск, 2007. С. 11.
Гохштейн А.Я. // Электрохимия. 1970. Т. 6. № 7. С. 979.
Хориути Д., Тоя Т. Хемособция водорода. Поверхностные свойства твердых тел / Под. ред. Грина М. М.: Мир, 1972. С. 1.
Тоя Т., Ито Т., Иши Ш. // Электрохимия. 1978. Т. 14. № 5. С. 703.
Дополнительные материалы отсутствуют.
Инструменты
Физикохимия поверхности и защита материалов