Физикохимия поверхности и защита материалов, 2023, T. 59, № 2, стр. 211-220
Циклоалифатическая эпоксидная матрица в разработке антикоррозионных покрытий, содержащих различные модифицирующие добавки
Н. К. Голубева 1, 2, Ю. А. Кондратенко 1, *, А. Г. Иванова 1, В. Л. Уголков 1, О. А. Загребельный 1, Т. А. Кочина 1
1 Институт химии силикатов им. И.В. Гребенщикова РАН
199034 Санкт-Петербург, наб. Макарова, 2, Россия
2 Санкт-Петербургский государственный технологический институт (технический университет)
190013 Санкт-Петербург, Московский пр., 26, Россия
* E-mail: kondratencko.iulia@yandex.ru
Поступила в редакцию 24.05.2022
После доработки 25.09.2022
Принята к публикации 10.10.2022
- EDN: SZMAIW
- DOI: 10.31857/S0044185623700262
Аннотация
Изучено влияние условий отверждения, природы наполнителя и органического модификатора на физико-механические свойства покрытий на основе циклоалифатической эпоксидной матрицы, наполненной слюдой-мусковитом и TiO2. Представлена зависимость значений твердости и угла смачивания от количества отвердителя полиэфирамина (20–50 мас. %). Изучено влияние природы отвердителя и добавок измельченного гранита и микросфер SiO2 на значения твердости, адгезии, прочности при ударе и изгибе эпоксидного покрытия. Определены четыре оптимальных состава эпоксидных покрытий для изучения термической устойчивости и антикоррозионных свойств. Показано, что покрытия, содержащие олигоэтоксисилоксаны в качестве органического модификатора, характеризуются низкой степенью защиты от коррозии.
1. ВВЕДЕНИЕ
В настоящее время использование защитных покрытий является основным и наиболее эффективным методом борьбы с такой масштабной проблемой, как коррозия [1, 2]. Для защиты материалов от коррозии наиболее часто применяют антикоррозионные полимерные покрытия, среди которых эпоксидные покрытия наиболее распространены. Однако основным недостатком эпоксидных покрытий является образование микропор и дефектов, которые формируются в процессе отверждения покрытий и приводят к ухудшению их устойчивости к коррозии. Одним из наиболее эффективных подходов к повышению защитных свойств эпоксидных покрытий является введение в их состав различных добавок - наполнителей и пигментов. Пигменты действуют как ингибиторы, повышая стойкость металлических поверхностей к коррозии [3]. Некоторые пигменты действуют путем улучшения барьерных свойств покрытий. Другие пигменты проявляют химическую активность − снижают активность как анодных, так и катодных процессов путем высвобождения пассивирующих ионов или вступают в реакцию со смолой, образуя соединения, уменьшающие коррозию металла [4, 5]. Диоксид титана широко используется в качестве белого нерастворимого пигмента в лакокрасочной промышленности. Его широкое использование связано с тем, что TiO2 эффективно рассеивает видимый свет, тем самым придает белизну, яркость, непрозрачность и улучшает светостойкость и грязеустойчивость покрытий [6]. Оксиды цинка, железа, алюминия и др. также используются в составах антикоррозионных покрытий [7–9]. Слоистые силикаты играют важную роль в разработке функциональных материалов [10]. Слюда мусковит (KAl2(AlSi3O10)(OH)2) является традиционным наполнителем органосиликатных покрытий (ОСП). Благодаря слоистому строению силикатов и наличию в них силанольных групп в сочетании с полисилоксанами после отверждения формируется единая пространственно сшитая структура [11]. Образование подобной структуры способствует улучшению целостности и долговечности ОСП.
Важную роль в разработке защитных антикоррозионных покрытий играют органические модификаторы, которые вводят в состав покрытия как для улучшения физико-механических свойств, так и для повышения защитных антикоррозионных свойств. Например, для получения гидрофобных покрытий (краевой угол смачивания >90°) на основе эпоксидных олигомеров используют модификаторы с низкой поверхностной энергией, среди которых можно выделить фторсодержащие органосилоксаны [12, 13]. Для получения гидрофильных покрытий (краевой угол смачивания <90°) часто используют подход, основанный на модификации полимерной матрицы или специальных добавок − наноразмерных частиц (например, SiO2) различными полярными группами (−OH, −COOH, −NH2 и др.) [14, 15]. В работах [16–18] показано, что введение кремнийорганических соединений (полиорганосилоксанов, полисилазанов и др.) в качестве модификаторов придает материалам гидрофильные свойства.
Цель настоящей работы заключалась в изучении влияния условий отверждения, природы наполнителя и органического модификатора на физико-механические свойства эпоксидных покрытий. Ранее нами был разработан состав, содержащий в качестве полимерной матрицы модифицированную эпоксидным каучуком циклоалифатическую эпоксидную смолу. Данный состав показал высокую устойчивость к атмосферной коррозии в условиях влажного тропического климата [19]. В связи с этим в данном исследовании в качестве полимерной матрицы была выбрана циклоалифатическая эпоксидная смола.
2. МАТЕРИАЛЫ И МЕТОДЫ
Покрытия составов 1–12, представленные в табл. 1, были получены нанесением соответствующей предварительно полученной композиции с отвердителем: полиэфирамином Т-403 (ПЭА), смесью ПЭА с изофорондиамином (ИФДА) или с полиэтиленполиамином (ПЭПА), на подложки из стекла, алюминия или стали. Отверждение покрытий после внесения соответствующего отвердителя достигалось “холодным” (сушка при комнатной температуре (КТ)) или “горячим” методом. В случае “горячего отверждения” покрытие после нанесения выдерживали 1 ч при комнатной температуре и далее помещали в печь, которую нагревали до 80°С со скоростью нагрева до 2–3°С/мин и выдерживали в течение 3 ч.
Таблица 1.
Состав и условия отверждения покрытий 1–12
Состав | Полимерная матрица | Мас. % полимерной матрицы | Наполнители | Мас. % наполнителей | Отвердитель | Мас. % отвердителя | Условия отверждения* |
1а | 1) ST-3000 2) Экан-3 |
1) 55 2) 5 |
1) Мусковит 2) TiO2 |
1) 35 2) 5 |
ПЭА | 20 | КТ |
1б | 25 | ||||||
1в | 30 | ||||||
1г | 35 | ||||||
1д | 40 | ||||||
1е | 45 | ||||||
1ж | 50 | ||||||
1з | 1) ПЭА 2) ПЭПА |
1) 35 2) 8 |
|||||
1и | ИФДА | 28 | 80°С | ||||
1к | 1) ИФДА 2) ПЭА |
1) 20 2) 20 |
80°С | ||||
1л | 1) ИФДА 2) ПЭА |
1) 20 2) 20 |
КТ | ||||
2 | 1) ST-3000 2) Экан-3 |
1) 55 2) 5 |
1) Мусковит 2) TiO2 3) изм. гранит |
1) 30 2) 5 3) 5 |
ПЭА | 40 | |
3 | 1) ST-3000 2) Экан-3 |
1) 55 2) 5 |
1) Мусковит 2) TiO2 3) изм. гранит |
1) 25 2) 5 3) 10 |
|||
4 | 1) ST-3000 2) Экан-3 |
1) 45.8 2) 4.2 |
1) Мусковит 2) TiO2 3) SiO2 |
1) 35 2) 5 3) 10 |
|||
5 | 1) ST-3000 2) Экан-3 |
1) 55 2) 5 |
1) Мусковит 2) TiO2 3) SiO2 |
1) 15 2) 5 3) 20 |
|||
6 | 1) ST-3000 2) Экан-3 |
1) 55 2) 5 |
1) Мусковит 2) TiO2 3) SiO2 |
1) 25 2) 5 3) 10 |
|||
7 | 1) ST-3000 2) ЭС-40 |
1) 90 2) 10 |
– | – | |||
8 | 1) ST-3000 2) ЭТС-40 |
1) 80 2) 20 |
– | – | |||
9 | 1) ST-3000 2) ЭТС-40 |
1) 70 2) 30 |
– | – | |||
10 | 1) ST-3000 2) ЭТС-40 |
1) 58.5 2) 6.5 |
1) Мусковит 2) TiO2 |
1) 30 2) 5 |
|||
11 | 1) ST-3000 2) ЭТС-40 |
1) 52 2) 13 |
1) Мусковит 2) TiO2 |
1) 30 2) 5 |
|||
12 | 1) ST-3000 2) ЭТС-40 |
1) 45 2) 20 |
1) Мусковит 2) TiO2 |
1) 30 2) 5 |
Композиции – предшественники покрытий 1–12, были получены внесением соответствующих компонентов: циклоалифатической смолы ST-3000 (“KUKDO Chemical Co., Ltd.”), эпоксидного каучука ЭКАН-3 (ООО НПК “СТЭП”) или смеси олигоэтоксисилоксанов (Этилсиликат-40 (ЭТС-40), АО “ЛенРеактив”), наполнителей, представленных в табл. 1, растворителя – толуола (ХЧ, АО “ЛенРеактив”) в шаровую фарфоровую мельницу объемом 0.5 л с фарфоровыми шарами (объемом 0.15–0.2 л) для получения однородной суспензии с массовой долей нелетучих компонентов равной 60%. После 48 ч вращения шаровой мельницы полученную композицию выгружали и определяли массовую долю нелетучих компонентов согласно ГОСТ 31939-2012 “Материалы лакокрасочные. Определение массовой доли нелетучих веществ”.
Краевой угол смачивания на поверхности покрытий был определен с использованием прибора гониометр ЛК-1. Твердость покрытий была определена на маятниковом приборе типа ТМЛ с маятником Персоза согласно ГОСТ Р 52166-2003 “Материалы лакокрасочные. Определение твердости покрытия по времени уменьшения амплитуды колебаний маятника”. Адгезия покрытия к металлу определялась методом решетчатых надрезов с помощью адгезиметра-решетка “Константа АР” согласно ГОСТ 31149-2014 “Материалы лакокрасочные. Определение адгезии методом решетчатого надреза”. Размер решетки составил 3 × 3 мм при толщине покрытий от 121 до 250 мкм. Прочность покрытия, нанесенного на алюминиевую пластину (100 × 100 × 1.5 мм) при ударе определяли с помощью прибора У-1А согласно ГОСТ 4765-73 “Материалы лакокрасочные. Метод определения прочности при ударе”. Эластичность покрытия, нанесенного на алюминиевую ленту размером 20 × 150 × 0.2 мм, при изгибе вокруг цилиндрического стрежня определена согласно ГОСТ 6806-73 “Материалы лакокрасочные. Метод определения эластичности пленки при изгибе”.
Электронная микрофотография частиц SiO2 была получена с использованием сканирующего электронного микроскопа Phenom XLG2 (ThermoFisher Scientific).
Кривые термогравиметрического анализа (ТГ) и дифференциальной сканирующей калориметрии (ДСК) были сняты на установке синхронного термоанализатора Netzsch STA 429 СD в интервале температур 40–650°С. Квадрупольный масс-спектрометр QMS 403 C (Netzsch) был использован для анализа продуктов деструкции.
Для проверки коррозионной стойкости защитных покрытий 2, 5 и 10 (табл. 1) были проведены электрохимические испытания с использованием методов потенциодинамической поляризации и импедансной спектроскопии. Потенциодинамические поляризационные кривые и спектры импеданса регистрировали в трехэлектродной электрохимической ячейке, подключенной к потенциостату Р-8S (“Electrochemical Instruments”) или к импендсметру Z-1500J (“Electrochemical Instruments”). Электрохимическая ячейка представляла собой стеклянную трубку цилиндрической формы с внутренним диаметром 3 см, которая была наклеена торцевой стороной на поверхность покрытия, нанесенного на стальную пластину (сталь 08ПС, 50 × 85 × 2 мм). Точно такая же стеклянная трубка была наклеена и на стальную пластину без покрытия. Образовавшееся при этом “дно” цилиндра, являлось рабочим электродом, площадь которого составляла 7.1 см2. Вспомогательный электрод – платиновая проволока и электрод сравнения – серебряная проволока, располагались в цилиндре, не соприкасаясь с его “дном”. В качестве электролита использовался 3% раствор NaCl.
Измерение электрохимических параметров при скорости развертки потенциала 10 мВ/с в диапазоне потенциалов –1–0 В проводили 1 раз в неделю в течение трех месяцев при постоянной выдержке поверхности покрытий в 3% растворе NaCl. Перед началом измерений в потенциодинамическом режиме проводили измерение потенциала рабочего электрода при разомкнутой электрической цепи в течение 200 с.
Для определения тока коррозии (Iк) и потенциала коррозии (Eк) экстраполировали линейные участки катодной и анодной поляризационных кривых до их пересечения. Поляризационные кривые были построены в полулогарифмических координатах (lgI–E). Координаты точки пересечения линейных участков поляризационных кривых соответствуют на оси абсцисс – потенциалу коррозии, а на оси ординат – плотности тока коррозии [20].
Эффективность ингибиторной защиты покрытий (θ) была рассчитана по формуле [21, 22]:
Измерение импеданса стальных пластин с покрытием проводились в диапазоне частот от 0.01 Гц до 3 МГц при определенном значении потенциала коррозии. Расчет элементов эквивалентной схемы при аппроксимации экспериментальных импедансов покрытий 5 и 10 проводился в программе ZView.
3. РЕЗУЛЬТАТЫ И ИХ ОБСУЖДЕНИЕ
На первом этапе было изучено влияние количества добавленного отвердителя ПЭА на значения твердости и краевого угла смачивания состава 1 на основе циклоалифатической эпоксидной смолы, модифицированной эпоксидным каучуком с наполнителями (слюда-мусковит, TiO2). Количество добавляемого отвердителя варьировалось в диапазоне от 20 до 50 мас. % (составы 1а–1ж, табл. 1). Было обнаружено, что значения краевого угла смачивания слабо зависят от количества отвердителя и варьируются в узком диапазоне 68°–73° (рис. 1). Однако количество введенного отвердителя ПЭА оказывало существенное влияние на значения твердости покрытия. Наиболее высокие значения твердости покрытий (>0.4 усл. ед.) были достигнуты при введении 30–40 мас. % ПЭА. В остальных случаях наблюдался замедленный процесс отверждения, как в случае пониженного содержания отвердителя (≤30 мас. %), так и в его избытке (≥45 мас. %). Таким образом, в дальнейшем 40 мас. % отвердител ПЭА было выбрано как наиболее оптимальное количество.
Рис. 1.
Зависимость значений твердости (7 сут после нанесения) и краевого угла смачивания от количества ПЭА (мас. %) покрытий 1а–1ж.
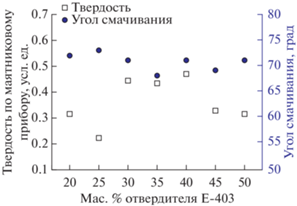
На втором этапе было исследовано влияние состава отвердителя и условий отверждения на физико-механические свойства покрытия 1. В качестве отвердителей были использованы: ПЭА (состав 1д), смесь ПЭА с ПЭПА (состав 1з), ИФДА (состав 1и), смесь ПЭА с ИФДА (составы 1к и 1л). Как можно заметить (табл. 2), природа отвердителя оказывает существенное влияние на физико-механические свойства покрытия 1. Использование ИФДА в качестве отвердителя или соотвердителя приводило к незначительному увеличению краевого угла смачивания, улучшению прочности при ударе (составы 1и и 1к), но существенному ухудшению прочности при изгибе. Максимальную прочность при изгибе (<1 мм) удалось достигнуть только с использованием в качестве отвердителя ПЭА. Было обнаружено, что краевой угол смачивания слабо зависит от условий отверждения за исключением состава 1з (59°), в котором в качестве соотвердителя использовался ПЭПА.
Таблица 2.
Некоторые физико-механические свойства разработанных составов на основе циклоалифатической эпоксидной матрицы
Состав | Твердость по маятниковому прибору, усл. ед. | Угол смачивания, ° | Адгезия, (решетчатый надрез), балл | Прочность при ударе, см | Прочность при изгибе, мм |
---|---|---|---|---|---|
1д | 0.62 | 71 | 1 | 35 | <1 |
1з | 0.55 | 59 | 0 | 50 | 10 |
1и | 0.76 | 74 | 1 | 40 | >20 |
1к | 0.60 | 76 | 1 | 40 | >20 |
1л | 0.62 | 74 | 1 | 25 | 20 |
2 | 0.60 | 65 | 0 | 50 | 5 |
3 | 0.61 | 76 | 2 | 50 | 3 |
4 | 0.45 | 70 | 1 | 25 | 20 |
5 | 0.40 | 81 | 1 | 50 | 1 |
6 | 0.62 | 67 | 1 | 35 | <1 |
10 | 0.47 | 72 | 1 | 40 | >20 |
11 | 0.29 | 70 | 1 | 30 | >20 |
12 | 0.21 | 66 | 1 | 40 | 1 |
Далее нами было изучено влияние добавок, таких как измельченный гранит (гранитная пыль) (составы 2 и 3) и микросферы SiO2 (составы 4–6) на физико-механические свойства покрытий. Было обнаружено, что введение 5 и 10 мас. % измельченного гранита приводит к существенному увеличению прочности покрытия при ударе (50 см), однако наблюдалось небольшое ухудшение прочности при изгибе (с 1 до 5 мм). Введение SiO2 микросфер со средним диаметром 150 мкм (рис. 2) в состав покрытия за счет снижения содержания полимерной матрицы (состав 4) привело к уменьшению показателей твердости, прочности при ударе и изгибе. Введение 20 мас. % микросфер SiO2 (состав 5) за счет снижения содержания слюды-мусковита привело к существенному увеличению краевого угла смачивания (81°) и прочности при ударе (50 см). При этом значение прочности при изгибе практически не изменилось по сравнению с составом 1д.
На следующем этапе в состав циклоалифатической эпоксидной матрицы в качестве органического модификатора были введены олигоэтоксисилоксаны (ЭТС-40) при мас. соотношении 90 : 10 (состав 7); 80 : 20 (состав 8) и 70 : 30 (состав 9) вместо эпоксидного каучука. Было обнаружено, что введение ЭТС-40 приводит к существенному изменению краевого угла смачивания и твердости покрытий (рис. 3). Минимальное значение краевого угла смачивания, равное 32°, удалось достигнуть при соотношении связующих 90 : 10 (состав 7). С увеличением содержания ЭТС-40 наблюдалось возрастание краевого угла смачивания (рис. 3) и уменьшение значений твердости: 0.47 (состав 7), 0.29 (состав 8) и 0.16 (состав 9). При введении в данные составы наполнителей (составы 10–12) – слюды-мусковита (30 мас. %) и TiO2 (5 мас. %) наблюдалось существенное возрастание краевого угла смачивания по сравнению с составами без наполнителей (табл. 2). При этом значения твердости покрытий практически не изменились (табл. 2). Покрытия с ЭТС-40 характеризуются средней прочностью к удару (30–40 см), но низкой прочностью при изгибе (>20 мм).
Таким образом, на основании полученных данных были выбраны составы 1д, 2, 5 и 10 для дальнейшего изучения их термической устойчивости и антикоррозионных свойств.
Термический анализ показал, что начало потери массы покрытий вне зависимости от состава наступает сразу после 200°С, что, вероятно, связано с деструкцией циклоалифатической эпоксидной матрицы. Характер термической деструкции составов 1д, 2, 5 и 10 схож друг с другом (рис. 4а). На ТГ кривых можно выделить три отдельные стадии потери массы в интервале температур 200–320, 320–430 и 430–600°С. ДСК кривые (рис. 4б) характеризуются заметными уширенными экзотермическими эффектами в интервале температур 189–293°С и сильными экзотермическими эффектами с максимумами в области 448–463°С. Наиболее сильный экзотермический эффект был зафиксирован в случае состава 5, где в качестве добавки были использованы SiO2 микросферы. На последней стадии в интервале температур 430–600°С с помощью масс-спектрометрического детектора было зафиксировано сильное выделение воды и углекислого газа в качестве основных продуктов деструкции.
Электрохимические коррозионные испытания стальных пластин с покрытиями 2, 5 и 10 в 3%-ном растворе NaCl в течение 3 мес. показали наличие тока коррозии (рис. 5, табл. 3). Наименьший ток коррозии показала пластина с покрытием 2 (рис. 5). Важно отметить, что после 7 суток испытаний ток коррозии не удалось зафиксировать вследствие достаточно высокой антикоррозионной защиты покрытия 2. После 3-х месяцев испытаний величина плотности тока коррозии не превышала 2 × 10–11 А/см2. Вероятно, наличие в составе покрытия измельченного гранита в качестве наполнителя и эпоксикаучук-эпоксидной матрицы способствует образованию более плотной структуры и увеличению коррозионной устойчивости покрытия (рис. 6).
Рис. 5.
Потенциодинамические поляризационные кривые стальных пластин с покрытием 2 (а) 5 (б) и 10 (в) после 7 (I), 60 (II) и 90 (III) суток выдержки в 3% растворе NaCl и стальной пластины без покрытия после выдержки в 3% растворе NaCl в течение суток (IV).
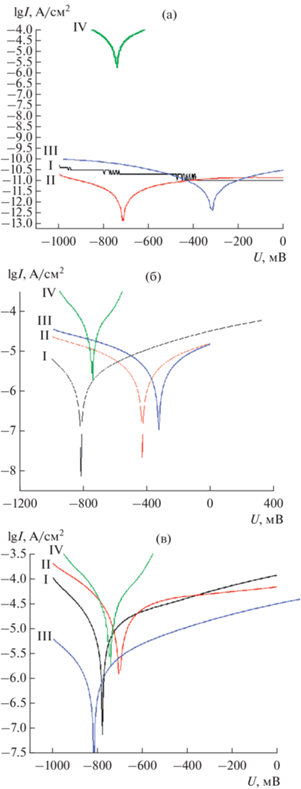
Таблица 3.
Электрохимические параметры стальных пластин с покрытиями 2, 5 и 10 после выдержки покрытий в 3% растворе NaCl в течение 7, 60 и 90 сут, и стальной пластины без покрытия после ее выдержки в 3%-ном растворе NaCl в течение суток
Покрытие | Ек, мВ | Iк, А/см2 | Эффективность ингибиторной защиты, % | ||||||
---|---|---|---|---|---|---|---|---|---|
Период воздействия, сутки | |||||||||
7 | 60 | 90 | 7 | 60 | 90 | 7 | 60 | 90 | |
Пластина без покрытия* | –860 | – | – | 6.5 × 10–5 | – | – | – | – | – |
2 | – | –710 | –510 | – | 1.8 × 10–12 | 2 × 10–11 | – | 99.99 | 99.99 |
5 | –800 | –400 | –350 | 1 × 10–6 | 2.5 × 10–6 | 3 ×10–6 | 98 | 96 | 95 |
10 | –780 | –700 | –810 | 5 × 10–6 | 2 × 10–5 | 1 × 10–6 | 92 | 69 | 98 |
Рис. 6.
Фотография стальных пластин с покрытиями 2 (а), 5 (б) и 10 (в) после электрохимических испытаний.
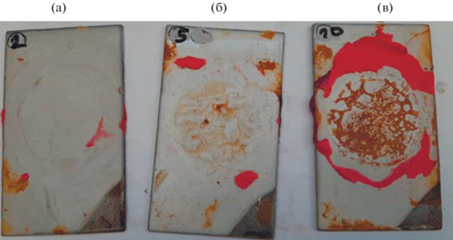
В случае пластины без покрытия и пластины с составом 10, где в качестве органического модификатора использовалась смесь олигоэтоксисилоксанов, был зафиксирован наибольший ток коррозии (рис. 5в, табл. 3). При этом, после третьего месяца испытания пластины с составом 10 было зарегистрировано некоторое уменьшение величины плотности тока коррозии с 2 × 10–5 до 1 × 10–6А/см2. По-видимому, образование пленки из продукта коррозии – Fe(OH)3 под покрытием и на его поверхности временно снижает скорость коррозии (рис. 6) [23].
Введение в состав покрытия 5 SiO2 микросфер в качестве наполнителя не способствует усилению антикоррозионной защиты. По силе антикоррозионной защиты покрытие 5 занимает промежуточное положение между покрытиями 2 и 10 (табл. 3, рис. 6).
Тип антикоррозионной защиты можно определить по значению потенциала коррозии (Ек). Повышение потенциала коррозии стальных пластин с покрытиями 2 и 5 в течение 3 мес испытаний, в отличие от пластины без покрытия свидетельствует об анодной защите этих покрытий (табл. 3).
Образование гидроксидной пленки на поверхности покрытия 10 и под ним, определяет потенциал коррозии (–810 мВ), приближенный к потенциалу коррозии пластины без покрытия (–860 мВ).
Импеданс покрытия 2 не удалось зафиксировать в течение 3 мес. испытаний из-за достаточно высокого сопротивления покрытия, превышающего входное сопротивление регистрируемого прибора. Импеданс покрытий 5 и 10 представлен на рис. 8.
Рис. 7.
Эквивалентная электрическая схема, где Rs – сопротивление электролита, Rc – сопротивление слоя, образуемого покрытием, Rct – сопротивление переноса заряда в окислительно-восстановительных реакциях на границе металл-электролит, CPEc – емкость покрытия и CPEdl – емкость двойного слоя на границе металл–электролит.
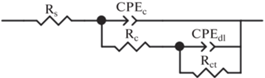
Рис. 8.
Импеданс покрытия 5 (а) и 10 (б). Сплошная линия – экспериментальный импеданс. Пунктирная линия – аппроксимация импеданса в программе ZView.'
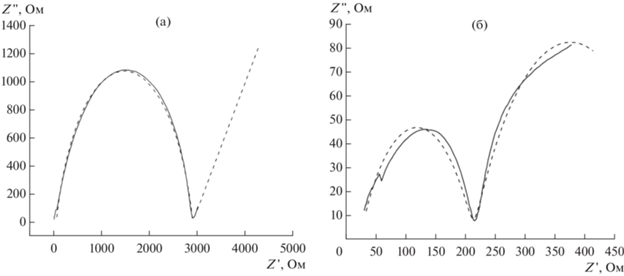
В случае, когда коррозионный раствор через дефекты проникает внутрь покрытия и образует границу раздела раствор-металл, для моделирования импеданса электролитической системы используется эквивалентная электрическая схема с двумя постоянными времени [24], представленная на рис. 7.
Элементы CPE с постоянной фазой, аппроксимирующие поведение емкости с распределенными параметрами, используются из-за неоднородности и пористости поверхности образцов. При замене емкости на элемент CPE центр полуокружности на годографе импеданса смещается ниже оси абсцисс. Элемент CPE характеризуется двумя параметрами: фактором пропорциональности CPE-T и экспоненциальным показателем CPE-P. При CPE-P равном единице импеданс элемента с постоянной фазой эквивалентен импедансу конденсатора.
Рис. 9.
Внешний вид покрытий 1д (а) и 10 (б) после экспозиции в течение 6 (а) и 4 (б) месяцев на открытом испытательном стенде (Ханой, СР Вьетнам).
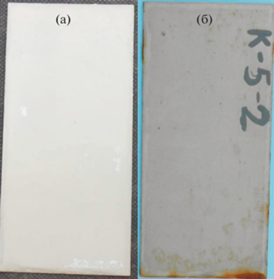
Сопротивление покрытия Rc и сопротивление переноса заряда Rct снижаются с увеличением доступности металла для коррозионно-активных веществ. Увеличение доступности металла может быть обусловлено прохождением электролита внутрь матрицы покрытия [25], нарушением его целостности, а также повреждением адгезионных связей между покрытием и подложкой [24]. Более низкое значение Rc, Rct свидетельствует о том, что коррозионно-активные ионы проходят через покрытие с меньшими препятствиями, обуславливая таким образом более высокую скорость коррозии [26].
Величина модуля импеданса на низких частотах, стремящаяся к сумме Rc и Rct, используется для количественной оценки стойкости покрытия. Rc определяет ширину высокочастотной дуги годографа импеданса, Rct – низкочастотной. Из полученных на основании импедансометрии результатов (табл. 4) можно сделать вывод, что защитные свойства покрытия 5 значительно выше, чем покрытия 10.
Таблица 4.
Значения параметров элементов эквивалентной схемы с учетом аппроксимации экспериментальных импедансов для покрытий 5 и 10
Состав | Rs, Ом | Rc, Ом | CPEc-T | CPEc-P | Rct, Ом | CPEdl-T | CPEdl-P |
---|---|---|---|---|---|---|---|
5 | 67.66 | 2839 | 5.7437E–08 | 0.82687 | 1E20 | 0.0079322 | 0.46808 |
10 | 22.83 | 191.6 | 3.7376E–06 | 0.57791 | 325 | 0.0039799 | 0.5966 |
Таким образом, электрохимические испытания показали, что антикоррозионная защита разработанных покрытий 2, 5 и 10 усиливается в ряду: 10 < 5 < 2.
Полученные результаты хорошо согласуются с результатами натурных испытаний пластин на открытой площадке в условиях влажного тропического климата (СР Вьетнам, г. Ханой). Так, покрытие состава 1д на основе циклоалифатической эпоксидной матрицы, модифицированной эпоксидным каучуком, с наполнителями (слюда-мусковит, TiO2) показало высокую устойчивость к атмосферной коррозии. В течение более 6 месяцев экспозиции на поверхности покрытия 1д следов коррозии не было зафиксировано за исключением небольших участков по краю пластин (краевой эффект). При этом в случае состава 10 коррозия развивалась значительно активнее. Так, после 4 мес. экспозиции по всей поверхности пластины с составом 10 наблюдалось образование точечной коррозии. Особенно сильно коррозия развивалась по краю пластины в результате частичного отслоения покрытия от подложки.
4. ВЫВОДЫ
Таким образом, изучено влияние природы отвердителя, условий отверждения, органических модификаторов (эпоксидный каучук, ЭТС-40), неорганических добавок (слюда-мусковит, TiO2, SiO2 микросферы, измельченный гранит) на физико-механические свойства, термическую устойчивость и антикоррозионные свойства покрытий на основе циклоалифатической матрицы. Полиэфирамин (30–40 мас. %) является оптимальным отвердителем, который обеспечивает высокую твердость и прочность при изгибе покрытиям на основе циклоалифатической матрицы. Введение дополнительных наполнителей, таких как SiO2 микросферы (20 мас. %) и измельченный гранит (5, 10 мас. %), приводило к увеличению прочности при ударе (50 см), но небольшому ухудшению показателя прочности при изгибе. Кроме того, введение 20 мас. % SiO2 микросфер способствовало повышению гидрофобных свойств поверхности.
Замена эпоксидного каучука на ЭТС-40 привела к существенному уменьшению краевого угла смачивания (до 32°, без наполнителей). Однако введение наполнителей (слюда-мусковит, TiO2) привело к повышению гидрофобности (62°–68°). По сравнению с составами, содержащими эпоксидный каучук, существенно уменьшилась твердость и прочность при изгибе.
Состав наполнителей и органических модификаторов не оказывает существенного влияния на характер термической деструкции, которая наступает около 200°С. Во всех случаях термическая деструкция сопровождается сильными экзотермическими эффектами в области температур 448–463°С.
Электрохимические и натурные испытания показали, что замена органического модификатора эпоксидного каучука на смесь олигоэтоксисилоксанов приводит к значительному ухудшению антикоррозионных свойств. Антикоррозионная защита разработанных покрытий 2, 5 и 10 усиливается в ряду: 10 < 5 < 2.
Список литературы
Sorensen P.A., Kiil S., Dam-Johansen K. et al. // J. Coat. Technol. Res. 2009. V. 6. P. 135–176.
Кочина Т.А., Кондратенко Ю.А., Шилова О.А. и др. // Физикохимия поверхности и защита материалов. 2022. Т. 58. № 1. С. 86–112.
Turner G.P.A. Introduction to Paint Chemistry and Principles of Paint Technology. N.Y.: Chapman & Hall, 1988.
Kalendova A. // Anti-corros. Meth. Mater. 1998. V. 45. P. 344–349.
Gimeno M.J., Chamorro S., March R. et al. // Prog. Org. Coat. 2014. V. 77. P. 2024–2030.
Ahmed N.M., Abdel-Fatah H.T.M. Chapter 15. Study on the Anticorrosive Behavior of New Hygiene Structured Pigment Based on Waste Core and Nano Shell in Alkyd Paints / In: Developments in Corrosion Protection // IntechOpen, London, United Kingdom, 2014.
Johnson J.A., Heidenreich J.J., Mantz R.A. et al. // Prog. Org. Coat. 2003. V. 47. P. 432–442.
Touazi Y., Abdi A., Leshaf A. et al. // Prog. Org. Coat. 2020. V. 139. Article № 105458.
Михайлов М.М., Соколовский А.Н. // Изв. высш. уч. завед. Физика. 2007. Т. 50. № 7. С. 90–92.
Gerasimova L.G., Maslova M.V., Shchukina E.S. // Materials. 2021. V. 14. Article № 3369.
Кочина Т.А., Буслаев Г.С., Кондратенко Ю.А. // ФХС. 2020. Т. 46. № 1. С. 27–43.
Солдатов М.А., Шереметьева Н.А., Калинина А.А. и др. // Изв. АН. Сер. Хим. 2014. № 1 С. 267–272.
Givenchy E., Amigoni S., Martin C. et al. // Langmuir. 2009. V. 25. P. 6448–6453.
Lin B., Zhou S. // Prog. Org. Coat. 2017. V. 106. P. 145–154.
Bamane P.B., Jagtap R.N. //Colloid Interface Sci. Commun. 2021. V. 43. Article № 100444.
Васнев В.А., Измайлов Б.А., Баранов О.В. и др. // Патент РФ 2531818. Заявл. 07.12.2011. Опубл. 27.10.2014 Бюл. № 30.
Дирдорф А., Либе Х., Вакер А. и др. // Патент РФ 2006128576. Заявл. 16.12.2004. Опубл. 21.07.2005.
Chojnowski J., Slomkowski S., Fortuniak W. et al. // J. Inorg. Organomet. Polym. 2020. V. 30. P. 56–68.
Кондратенко Ю.А., Голубева Н.К., Иванова А.Г. и др. // ЖПХ. 2021. Т. 94. № 10–11. С. 1309–1319.
Mattsson E. Basic Corrosion Technology for Scientists and Engineers. Ellis Horwood, 1989. 193 p.
Маттссон Э. Электрохимическая коррозия / пер. со швед. под ред. Колотыркина Я.М. М.: Металлургия, 1991. 158 с.
Семенова И.В., Флорианович Г.М., Хорошилов А.В. Коррозия и защита от коррозии / Под ред. Семеновой И.В. М.: Физматлит, 2002. 336 с.
Tamura H. // Corrosion Science. 2008. V. 50. P. 1872–1883.
Bahremand F., Shahrabi T., Ramezanzadeh B. // J. Hazard. Mater. 2021. V. 403. Article № 123722.
Deyab M.A., El Bali B., Mohsen Q. et al. // Sci. Rep. 2021. V. 11. Article № 8182.
Chhetri S., Samanta P., Murmu N. et al. // J. Compos. Sci. 2019. V. 3. Article № 11.
Дополнительные материалы отсутствуют.
Инструменты
Физикохимия поверхности и защита материалов