Нефтехимия, 2020, T. 60, № 6, стр. 793-801
Трехмерное гидродинамическое моделирование и оптимизация цилиндрического реактора с пористым слоем для получения водорода паровым риформингом метана
S. B. Haghi 1, G. Salehi 2, *, M. T. Azad 3, A. L. Nichkoohi 4, **
1 Energy System Group, Faculty of Marine Science, Islamic Azad University, North Tehran Branch
1651153311 Tehran, Iran
2 Department of Mechanical Engineering, Islamic Azad University, Central Tehran Branch
1419953492 Tehran, Iran
3 Department of Physical Oceanography, Faculty of Marine Science, Islamic Azad University, North Tehran Branch
165115338 Tehran, Iran
4 Department of Mechanical Engineering, Islamic Azad University, Nowshahr Branch
Nowshahr, Iran
* E-mail: rezasalehi20@gmail.com
** E-mail: Lohrasbi@iauns.ac.ir
Поступила в редакцию 19.08.2018
После доработки 30.04.2020
Принята к публикации 10.07.2020
Аннотация
Паровой риформинг метана, в результате которого происходит конверсия природного газа в ценные продукты с использованием каталитического реактора, является наиболее экономически выгодным методом получения водорода на нефтеперерабатывающих заводах. Основное внимание в данном исследовании уделяется созданию модели реактора парового риформинга метана методами вычислительной гидродинамики. С этой целью создана стационарная гетерогенная трехмерная модель на основе законов сохранения массы, частиц, импульса и энергии. Модель использована для определения эффективности теплообмена в двух реакторах с пористым слоем с различными конфигурациями нагревательных трубок. Изучено влияние температуры нагревательных трубок на входе в реактор, соотношения CH4/H2O и конфигурации нагревательной трубки на выход водорода. Показано, что повышению конверсии метана способствует повышение температуры нагревательных трубок на входе, а также увеличение их количества; соотношение CH4/H2O при этом составляет 0.25. При таком сочетании параметров пористость ниже 0.35 не влияет на конверсию метана. Также показано, что результаты моделирования соответствуют литературным данным. Таким образом, данное исследование может быть использовано для разработки промышленных реакторов риформинга природного газа.
В последние годы усилилась необходимость разработки способов уменьшения потребления ископаемых ресурсов и влияния на климат, вызванного выбросами парниковых газов [1, 2]. Одним из экологически безвредных источников топлива и энергии является водород [3, 4], источником которого могут служить вода, углеводороды, биомасса, сероводород и гидриды бора [5]. В США около 95% водорода вырабатывается в промышленных масштабах при паровом риформинге метана в каталитических реакторах [6, 7]. В этом процессе метан превращается в смесь водорода и оксида углерода (синтез-газ), для получения водорода высокой чистоты можно использовать реакцию водяного газа [8, 9].
В целом, крупномасштабные реакторы риформинга с мощностью по водороду 0.5–500 МВт дают меньшую экономическую прибыль по сравнению с маломасштабными реакторами (<500 кВт) [10]. Таким образом, больше внимания следует уделять маломасштабным технологиям для создания эффективных, компактных, транспортабельных и гибких систем парового риформинга. Маломасштабные установки для парового риформинга метана можно купить у известных компаний, которые в основном производят крупномасштабные реакторы парового риформинга метана для химической и нефтяной промышленности. Основнe требования для этих систем – высокие производительность, надежность и чистота водорода (в зависимости от сферы применения). Реакторы риформинга такого типа производят компании Haldor-Topsøe, Howe-Baker, Hydrochem, KTI и Foster Wheeler [11–13]. Проведено множество исследований с использованием как численных [14, 15], так и экспериментальных [16, 17] подходов. Поскольку эндотермические и экзотермические реакции в каталитическом слое проходят быстро, FD моделирование этих процессов является сложной задачей [18]. Основными преимуществами вычислительных методов являются низкая стоимость и высокое качество визуализации представленных результатов [19].
Количество исследований, посвященных трехмерным численным измерениям характеристик парового риформинга метана и сосредоточенных на изучении воздействия температуры нагревательных элементов на входе в реактор, пористости слоя катализатора, соотношении смеси CH4/H2O и конфигурации трубки теплообменника, достаточно невелико.
Цель данного исследования – прогнозирование и оптимизация этих воздействий с помощью трехмерного численного моделирования цилиндрического реактора с пористым слоем с двумя различными конфигурациями нагревательных трубок, которые служат для подачи тепла, необходимого для эндотермической реакции метана и водяного пара. Для моделирования и получения фундаментального понимания поведения потока и скорости реакции методом численного моделирования с использованием программного обеспечения COMSOL 5.3 была создана комплексная трехмерная модель. Для описания схемы вычислений использовалась связанная система уравнений частиц, массы, энергии и импульса. Результаты вычислений сравнили с результатами, полученными в предыдущей работе [20], чтобы оценить их точность. Анализ предыдущих исследований парового риформинга метана, выполненных методами вычислительной гидродинамики, показывает, что эффективность катализатора имеет большое значение, но этого недостаточно; также необходимо тщательное проектирование и изготовление установки риформинга для высокой тепловой интеграции. Длина канала играет важную роль в определении эффективности работы теплообменника [21]. Эти особенности более подробно были изучены в данной работе.
В статье рассмотрено численное моделирование реактора риформинга, включающее его геометрию, моделирование химических реакций и численные аспекты, а также представлены результаты и рекомендации для продолжения этого исследования.
СХЕМА ВЫЧИСЛЕНИЙ
Реакторы и сетки. Паровой риформинг метана исследовали в реакторе с неподвижным пористым слоем, заполненном никелевым катализатором. Геометрические особенности установки показаны на рис. 1. Высота риформера (цилиндра) в обеих конфигурациях составляет 150 мм.
Рис. 1.
Схематическое изображение парового риформера, использованного в этой работе (все размеры указаны в мм).
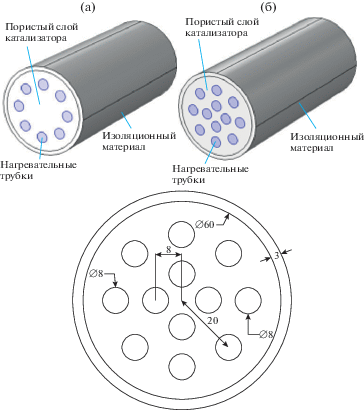
Из рис. 1 видно, что риформинг метана происходит в реакторе с пористым каталитическим слоем, где для подачи тепла для эндотермической реакции используется набор нагревательных трубок. Стенка риформера имеет толщину около 3 мм и покрыта изоляционным материалом. Водяной пар и метан смешивали в разных соотношениях и вводили через входное отверстие реактора. Для подвода тепла горячий воздух подавали в противоположном направлении через несколько трубок, проходящих сквозь реактор. Такой подход уже описан в [20].
Поскольку рабочая область в данном исследовании симметрична, зона моделирования была сокращена до четверти полного геометрического построения, покрытого сеткой, параметры которой кратко описаны в табл. 1.
Таблица 1.
Параметры сетки, используемой для данного исследования
Минимальное разрешение | Элементы в виде призмы | Шестигранные элементы | Трехгранные элементы | Четырехгранные элементы | Максимальное разрешение | |
---|---|---|---|---|---|---|
Значение | 0.0001352 | 14160 | 19647 | 480 | 10 578 | 0.002 |
Кинетическое моделирование в пористом слое. Как показано в работах [4, 9, 22–26], процесс парового риформинга метана состоит в основном из двух обратимых реакций: эндотермического парового риформинга и экзотермической реакции водяного пара:
(1)
$\begin{gathered} {\text{С}}{{{\text{Н}}}_{4}} + {{{\text{Н}}}_{{\text{2}}}}{\text{О}} \leftrightarrow {\text{СО}} + 3{{{\text{Н}}}_{2}}, \\ \Delta {{Н}_{{\text{r}}}} = 206.6\,\,{{{\text{кДж}}} \mathord{\left/ {\vphantom {{{\text{кДж}}} {{\text{моль}}}}} \right. \kern-0em} {{\text{моль}}}}, \\ \end{gathered} $(2)
$\begin{gathered} {\text{СO}} + {{{\text{Н}}}_{{\text{2}}}}{\text{О}} \leftrightarrow {\text{С}}{{{\text{О}}}_{2}} + {{{\text{Н}}}_{2}}, \hfill \\ \Delta {{Н}_{{\text{r}}}} = --41.1\,\,{{{\text{кДж}}} \mathord{\left/ {\vphantom {{{\text{кДж}}} {{\text{моль}}}}} \right. \kern-0em} {{\text{моль}}}}, \hfill \\ \end{gathered} $(3)
${{r}_{{{\text{MSR}}}}} = {{K}_{{{\text{MSR}}}}}\left( {{{p}_{{{\text{C}}{{{\text{H}}}_{{\text{4}}}}}}}{{p}_{{{{{\text{H}}}_{{\text{2}}}}{\text{O}}}}} - \frac{{{{p}_{{{\text{CO}}}}}p_{{{{{\text{H}}}_{{\text{2}}}}}}^{3}}}{{{{K}_{{{\text{eqMSR}}}}}}}} \right),$(4)
${{r}_{{{\text{WGS}}}}} = {{K}_{{{\text{WGS}}}}}\left( {{{p}_{{{\text{CO}}}}}{{p}_{{{{{\text{H}}}_{{\text{2}}}}{\text{O}}}}} - \frac{{{{p}_{{{\text{C}}{{{\text{O}}}_{{\text{2}}}}}}}{{p}_{{{{{\text{H}}}_{{\text{2}}}}}}}}}{{{{K}_{{{\text{eqWGS}}}}}}}} \right),$(5)
${{K}_{{{\text{MSR}}}}} = 2395\exp \left( {\frac{{ - 231{\kern 1pt} {\kern 1pt} 266}}{{{{R}_{{\text{u}}}}T}}} \right),$(6)
${{K}_{{{\text{WGS}}}}} = 0.0171\exp \left( {\frac{{ - 103{\kern 1pt} {\kern 1pt} 191}}{{{{R}_{{\text{u}}}}T}}} \right),$(7)
$\begin{gathered} {{K}_{{{\text{eqMSR}}}}} = 01.0267 \times {{10}^{{10}}}\exp ( - 0.2513{{Z}^{4}} + \\ + \,\,0.36665{{Z}^{3}} + 0.5810{{Z}^{2}} - 27.134Z + 3.277), \\ \end{gathered} $(8)
$\begin{gathered} {{K}_{{{\text{eqWGS}}}}} = \exp ( - 0.2935{{Z}^{3}} + 0.6351{{Z}^{2}} + \\ + \,\,1.1788Z + 3169), \\ \end{gathered} $Основные уравнения. Закон сохранения в пористом слое. В данном исследовании моделирование проводилось на основе коммерческого программного обеспечения COMSOL 5.3. Для решения использовали трехмерный метод конечных элементов. Как показано в [28], уравнение На-вье–Стокса в твердом каталитическом слое может быть упрощено до уравнения Бринкмана в тензорной форме и записано следующим образом:
(10)
$\begin{gathered} \frac{\rho }{{{{\varepsilon }_{p}}}}\left( {{{u}_{k}}{{\partial }_{k}}} \right)\frac{{{{u}_{i}}}}{{{{\varepsilon }_{p}}}} = {{\partial }_{k}}\left( { - {{\partial }_{i}}p{{\delta }_{{jk}}} + \frac{\mu }{{{{\varepsilon }_{p}}}}\left( {{{\partial }_{i}}{{u}_{k}} + {{\partial }_{i}}{{u}_{k}}} \right) - } \right. \\ - \,\,\left. {\frac{{2\mu }}{{3{{\varepsilon }_{p}}}}\left( {{{\partial }_{j}}{{u}_{j}}{{\delta }_{{ki}}}} \right) - \frac{\mu }{{{{k}_{{pr}}}}}{{u}_{i}}} \right), \\ \end{gathered} $Уравнения сохранения массы. Поскольку поле течения в данном исследовании является стационарным и слабо сжимаемым, уравнение сохранения массы упрощается следующим образом:
Уравнения переноса вещества. Поскольку реакции, описанные в этом исследовании, проходят в каталитическом слое, уравнение (12) для компонентов (H2, H2O, CO2, CO, CH4) решается с использованием уравнения диффузии и конвекции Максвелла−Стефана для стационарного состояния:
(12)
$\begin{gathered} {{\partial }_{k}}\left( {\rho {{Y}_{i}}{{u}_{k}} - \rho {{Y}_{i}}\sum\limits_{j = 1}^5 {{{D}_{{ij}}}({{\partial }_{k}}{{X}_{j}} + {{({{X}_{j}} - {{Y}_{j}}){{\partial }_{k}}p} \mathord{\left/ {\vphantom {{({{X}_{j}} - {{Y}_{j}}){{\partial }_{k}}p} p}} \right. \kern-0em} p}} } \right) = {{r}_{i}} \\ i = 1{\text{--}}4, \\ \end{gathered} $Уравнения энергии в пористом слое. Для описания среднего распределения температуры в пористом слое используется уравнение энергии для установившегося состояния без учета вязкостного рассеивания, как показано в уравнении (13):
(13)
${{\partial }_{j}}\left( { - k{{\partial }_{j}}T} \right) + \left( {\rho {{C}_{p}}} \right){{u}_{i}}{{\partial }_{i}}T - \Delta {{H}_{{\text{r}}}}r = 0.$Граничные условия. Термодинамические и гидравлические характеристики пористого слоя, трубки теплообменника и изоляционного материала представлены в табл. 2–4.
Таблица 2.
Информация о граничных условиях для пористого слоя
Граничное условие | Значение |
---|---|
Теплопроводность | 0.1 Вт/м К |
Теплоемкость | 2800 Дж/кг К |
Вязкость | 2.7е × 10–5 Па с |
Температура на входе в реактор | 700 К |
Снижение давления в слое | ∆p = 75 Па |
Пористость | $0.15 < {{\varepsilon }_{p}} < 0.45$ |
Пропускающая способность | 10–9 м2 |
Соотношениеметана и пара на входе в пористый слой | $0.2 < {{{\text{C}}{{{\text{H}}}_{4}}} \mathord{\left/ {\vphantom {{{\text{C}}{{{\text{H}}}_{4}}} {{{{\text{H}}}_{{\text{2}}}}{\text{O}}}}} \right. \kern-0em} {{{{\text{H}}}_{{\text{2}}}}{\text{O}}}} < 1$ |
РЕЗУЛЬТАТЫ И ОБСУЖДЕНИЕ
Влияние температуры нагревательных трубок. Рассмотрено влияние температуры на входе нагревательных трубок на риформинг метана с соотношением метан/пар 0.25 и пористостью 0.25 при конфигурации нагревательных трубок, описанной на рис. 1. Температуру нагревательных трубок изменяли в интервале $1000 < T < 1400$. Кроме того, оценены концентрации метана, оксида углерода, диоксида углерода, водорода, воды и температурный профиль. Конверсия метана вдоль осевой линии риформера (или вдоль оси Z), отображена в соответствии с [29, 30]:
(14)
${\text{Конверсия}}\,\,{\text{метана}},\,\,\% = \frac{{Y_{{{\text{C}}{{{\text{H}}}_{{\text{4}}}}}}^{0} - {{Y}_{{{\text{C}}{{{\text{H}}}_{{\text{4}}}}}}}}}{{Y_{{{\text{C}}{{{\text{H}}}_{{\text{4}}}}}}^{0}}} \times 100,$Результаты, показанные на рис. 2, соответствуют данным [20]. Кроме того, при увеличении температуры на входе нагревательных трубок риформинг метана идет с большей скоростью. Можно отметить, что температура входящего газа (метана и пара) составляет около 700 К.
Рис. 2.
Остаточное содержание метана вдоль осевой линии риформера при различных температурах нагревательных трубок.
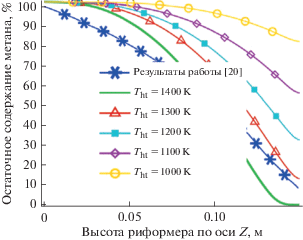
Заметная конверсия достигается при температуре трубок свыше 1200 К. Зависимость других параметров от температуры реакции представленa на рис. 3.
Рис. 3.
Массовая доля компонентов вдоль осевой линии риформера для различных температур нагревательных трубок.
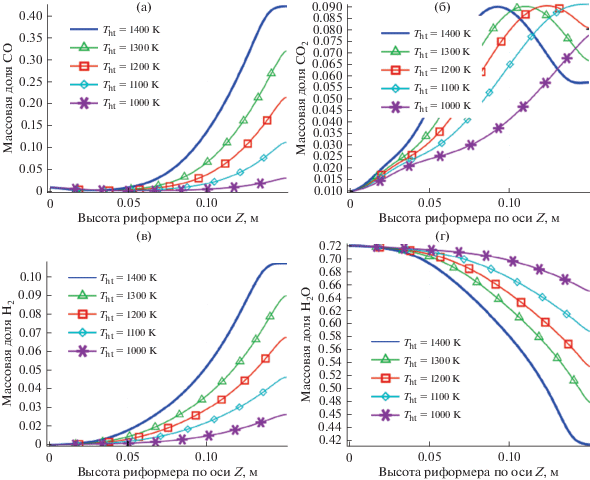
Как показано на рис. 3а, на выходе из реактора при температуре нагревательных трубок Tht = =1400 K концентрация оксида углерода примерно в 2 раза выше, чем концентрация других компонентов. Хотя эта температура оптимальна с точки зрения выхода водорода, при проектировании каталитических реакторов следует учитывать проблему интенсивного образования CO. Оптимальная температура на входе нагревательных трубок для образования CO2 составляет Tht = 1100 K (рис. 3б). Видно, что при уменьшении ${{T}_{{{\text{ht}}}}}$ выход CO2 увеличивается до достижения указанной температуры. При дальнейшем уменьшении температуры выход CO2 снижается, как описано в других публикациях [22–25]. Зависимость выхода водорода на выходе из каталитического слоя реактора от температуры показана на рис. 3в. Его массовая доля при Tht = 1400 K в 1.7 раза выше, чем при Tht = 1200 K; при более низкой температуре выход достаточно низок, что экономически невыгодно для проектирования. Зависимость массовой доли водяного пара от температуры показана на рис. 3г. Видно, что при повышении температуры нагревательных трубок концентрация пара снижается.
Влияние соотношения CH4/пар. На рис. 4 показана зависимость производительности реактора от соотношения концентраций подаваемых газов на входе в риформер.
Рис. 4.
Зависимость остаточного содержания метана (а), массовой доли СО2 (б) и температуры вдоль осевой линии риформера от различных соотношений СН4/пар.
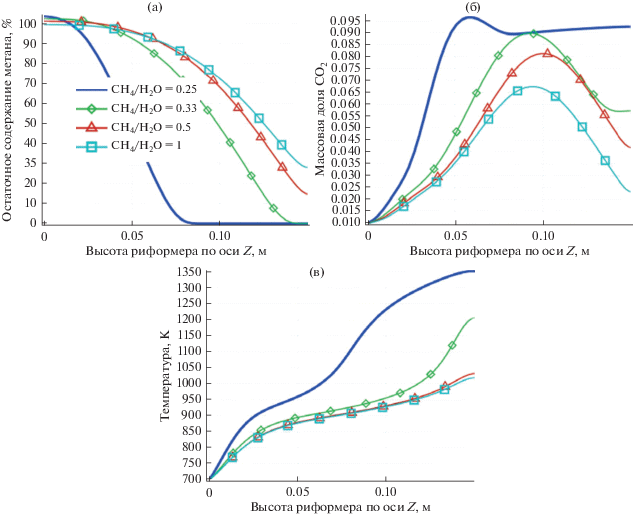
Как показано на рис. 4а, когда значения отношения реагентов выше стехиометрических, процесс риформинга идет быстрее, хотя для соотношений 0.25 < CH4/пар < 0.33 остаточное содержание метана на выходе из слоя катализатора может достигать таких же значений (конверсия до 98%). Но при меньших значениях отношения реагентов его эффективность снижается до 70%. Также было показано, что при соотношении метан/пар = = 0.25 риформинг протекает до конца уже на половине длины риформера, и это является наилучшим условием для подбора длины риформера: при уменьшении размеров риформера увеличивается его эффективность.
На рис. 4б показано изменение массовой доли CO2 вдоль оси симметрии реактора. Показано, что для соотношения 0.25 значение выше остальных, что соответствует литературным данным [23–26].
Этот результат соответствует графику температуры вдоль оси симметрии риформера (рис. 4с). Видно, что для соотношения 0.25 температура выше, чем для остальных, что способствует процессу риформинга.
Влияние конфигурации нагревательных трубок. С экономической точки зрения в процессе парового риформинга метана обеспечение нагрева является важным и сложным фактором. Результаты исследований показывают, что повышение температуры нагревательных трубок способствует процессу риформинга, но при этом увеличивается и образование монооксида углерода. Поэтому, с точки зрения экологии, этот вариант неприемлем. Альтернативным способом увеличения конверсии может быть изменение количества трубок, однако, при этом могут наблюдаться негативные эффекты. При увеличении количества трубок пространство, занимаемое катализатором, уменьшается, что может привести к снижению эффективности процесса риформинга. Как показано на рис. 1, внутри риформера может быть заключено до 12 нагревательных трубок. На рис. 5 показано сравнение результатов процесса риформинга при двух различных конфигурациях реактора. В обеих сериях экспериментов с различными конфигурациями одинаковая пористость и соотношение CH4/пар.
Рис. 5.
Остаточное содержание метана (a), массовой доли H2 (б) и температуры (в) вдоль осевой линии риформера для различных конфигураций трубок теплообменника.

Как показано на рис. 5a, остаточное содержание метана при Tht = 1200 K в 8-трубной конфигурации намного выше, чем в 12-трубной конфигурации по всей длине реактора. Такой же эффект наблюдается для выхода водорода. При такой конфигурации снижается температура, необходимая для риформинга, что идеально для проектирования и эксплуатации реактора. При сравнении риформинга в 8-трубном реакторе при 1200 К и риформинга в 12-трубном реакторе при 1000 К показано, что повышение температуры более эффективно, чем увеличение количества трубок теплообменника. На рис. 5в показана температура слоя риформера вдоль оси симметрии каталитического слоя. Как показано, в 12-трубной конфигурации температура пористого слоя увеличилась. Таким образом, процесс риформинга объективно стал более эффективным.
Оптимизация параметров процесса риформинга. Были рассчитаны оптимальные значения температуры на входе и соотношения CH4/пар, а также конфигурация нагревательных трубок для наилучшего проведения риформинга метана и получения водорода. В ходе оптимизации стремились получить максимальную конверсию метана, максимальное соотношения H2/CO2 и минимальные концентрацию CO2 и температуру на выходе из реактора. Результаты оптимизации показаны на рис. 6. Оптимизированные значения параметров на выходе из риформера представлены в табл. 5.
Таблица 5.
Оптимизированные значения на выходе из риформера
Остаточное содержание метана, % | Массовая доля H2 | Массовая доля CO2 | Массовая доля СО | Массовая доля H2O | Температура, К | |
---|---|---|---|---|---|---|
Оптимизированные значения | 1.2 | 0.112 | 0.06 | 0.41 | 0.37 | 1171 |
Таким образом, в данной работе при помощи программного обеспечения COMSOL 5.3 Multiphysics был оптимизирован процесс парового риформинга метана для двух конфигураций реактора с пористым каталитическим слоем и нагревательными трубками. В статье рассмотрены паровой риформинг метана и реакция водяного газа. Нагревательные трубки функционируют при температурах от 1000 до 1400 К, а отношение CH4/пар составляет от 0.25 до 1. Рассмотрены две конфигурации риформера из 8 и 12 нагревательных трубок. Результаты моделирования показывают, что конверсии метана способствуют повышение температуры нагревательных трубок, отношение CH4/H2O около 0.25 и увеличение количества нагревательных трубок в реакторе. Кроме того, при сравнении риформинга в реакторах, оборудованных 8 и 12 нагревательными трубками, при одинаковой температуре выяснилось, что повышение температуры более эффективно, чем увеличение числа нагревательных трубок. Также результаты показывают, что процесс риформинга более эффективен в 12-трубном реакторе и проходит с той же глубиной на более коротком расстоянии от входа в риформер. Можно сделать вывод, что результаты моделирования имеют положительную корреляцию с литературными данными, поэтому данное исследование может быть использовано для разработки промышленных реакторов конверсии природного газа.
Список литературы
Inbamrung P., Sornchamni T., Prapainainar C., Tungkamani S., Narataruksa P., Jovanovic G.N. // Energy. 2018. V. 152. P. 383.
Pashchenko D. // Energy. 2018. V. 143. P. 478.
Li L., Tang D., Song Y., Jiang B., Zhang Q. // Energy. 2018. V. 149. P. 937.
Taji M., Farsi M., Keshavarz P. // Int. J. Hydrogen Energy. 2018. V. 43. № 29. P. 13 110.
Dincer I., Joshi A.S. Solar Based Hydrogen Production Systems, Ch. 2. Hydrogen Production Methods, pp. 7−20 (Springer Briefs in Energy book series, 2013).
T-Raissi A., Block D.L. // IEEE Power and Energy Magazine. 2004. V. 2. № 6. P. 40. https://doi.org/10.1109/MPAE.2004.1359020
Nieva M.A., Villaverde M.M., Monzón A., Garetto T.F., Marchi A.J. // Chem. Eng. J. 2014. V. 235. P. 158.
Kolb G. // Chem. Eng. Process. 2013. V. 65. P. 1.
Butcher H., Quenzel C.J.E., Breziner L., Mettes J., Wilhite A.B., Bossard P. // Int. J. Hydrogen Energy. 2014. V. 39. № 31. P. 18 046.
Amin A.M., Croiset E., Epling W. // Int. J. Hydrogen Energy 2011. V. 36. № 4. P. 2904.
Ogden J.M. Report for the International Energy Agency Agreement on the Production and Utilization of Hydrogen, IEA/H2/TR-02/002 (2001).
Ferreira Aparicio P., Benito M.J., Sanz J.L. // Catal. Rev. Sci. Eng. 2005. V. 47. № 4. P. 491.
Zhai X., Cheng Y., Zhang Z., Jin Y., Cheng Y. // Int. J. Hydrogen Energy. 2011. V. 36. № 12. P. 7105.
Watanabe F., Kaburaki I., Shimoda N., Satokawa S. // Fuel Process. Technol. 2016. V. 152. P. 15.
Herce C., Cortes C., Stendardo S. // Fuel Process. Technol. 2017. V. 167. P. 747.
Wang H., Blaylock D.W., Dam A.H., Liland S.E., Rout K.R., Zhu Y.A. // Catal. Sci. Technol. 2017. V. 7. № 8. P. 1713.
Yoon Y., Kim H., Lee J. // J. Power Sources. 2017. V. 359. P. 450.
Chen J., Yan L., Song W., Xu D. // Int. J. Hydrogen Energy. 2017. V. 42. № 5. P. 664.
Pashchenko D. // Int. J. Hydrogen Energy. 2018. V. 43. № 18. P. 8662.
Gateau P. Proceedings of the COMSOL User’s Conference Grenoble, 2007.
Chen J., Gao X., Yan L., Xu D. // Int. J. Hydrogen Energy. 2018. V. 43. № 29. P. 12 948.
Haberman B.A., Young J.B. // Int. J. Heat Mass Transfer. 2004. V. 47. P. 3617.
Jiwanuruk T., Putivisutisak S., Ponpesh P., Bumroongsakulsawat P., Tagawa T., Yamada H., Assabumrungrat S. // Chem. Eng. J. 2016. V. 293. P. 319.
Xu J., Froment G.F. // AIChE J. 1989. V. 35. P. 88.
Nerat M., Jurici D. // Int. J. Hydrogen Energy. 2016. V. 41. № 5. P. 3613.
Palma V, Miccio M., Ricca A., Meloni E., Ciambelli P. // Fuel. 2014. V. 138. P. 80.
Wilhite B.A., Breziner L., Mettes J., Bossard P. // Energy Fuels. 2013. V. 27. № 8. P. 4403.
Nield D.A., Bejan A. Convection in Porous Media, 3rd Ed. New York. Springer Verlag, 2006.
Sadooghi P., Rauch R. // J. Nat. Gas Sci. Eng. 2013. V. 11. P. 46.
Mundhwa M., Thurgood C.P. // Fuel Process. Technol. 2017. V. 158. P. 57.
Дополнительные материалы отсутствуют.