Нефтехимия, 2020, T. 60, № 6, стр. 773-780
ПАРОВОЙ РИФОРМИНГ МЕТАНОЛА В РЕАКТОРЕ с Pd–Cu-МЕМБРАНОЙ НА Ni–Cu-КАТАЛИЗАТОРЕ
Е. Ю. Миронова 1, *, А. А. Лыткина 1, М. М. Ермилова 1, Н. В. Орехова 1, Н. А. Жиляева 1, Н. Р. Рошан 2, В. М. Иевлев 2, А. Б. Ярославцев 1, **
1 Институт нефтехимического синтеза им. А.В. Топчиева РАН
119991 Москва, Россия
2 Институт металлургии и материаловедения им. А.А. Байкова РАН
119334 Москва, Россия
* E-mail: palukas@ips.ac.ru
** E-mail: yaroslav@igic.ras.ru
Поступила в редакцию 16.04.2020
После доработки 12.05.2020
Принята к публикации 13.07.2020
Аннотация
В процессе парового риформинга метанола (ПРМ) на катализаторе Ni0.2–Cu0.8/Ce0.3Zr0.7O2-δ в традиционном и мембранном реакторах установлено, что выход водорода в реакторе с Pd–Cu-мембраной повышается по сравнению с традиционным проточным реактором. Показано, что мембрана из сплава Pd–Cu обладает высокой проницаемостью по водороду. ПРМ в мембранном реакторе позволяет получать водород высокой чистоты, поскольку из зоны пермеата выводится поток чистого водорода, свободного от каких-либо примесей. Проведено измерение водородопроницаемости мембраны из фольги сплава Pd–Cu в мембранном реакторе до и после катализа.
Водород считается одним из наиболее перспективных источников энергии благодаря его низкой массе, высокой энергоемкости и экологичности [1]. Особое внимание уделяется производству водорода высокой чистоты с минимальным уровнем содержания монооксида углерода, что делает возможным его использование в качестве источника энергии в низкотемпературных топливных элементах [2, 3]. Водород в чистом виде в природе не встречается. Наиболее распространенным способом его промышленного получения является риформинг углеводородов (УВ) или спиртов. Растущий в последние годы спрос на возобновляемые источники энергии привел к разработке технологий производства из биомассы различных видов биотоплив, таких как биометанол, биоэтанол и биометан [4, 5]. Спирты имеют ряд преимуществ, среди которых можно отметить удобство транспортировки и хранения, поскольку они представляют собой жидкости. Кроме того, при ПРМ [6] водород образуется в гораздо более мягких условиях, чем при паровом риформинге метана.
ПРМ включает в себя следующие реакции:
(1)
$\begin{gathered} {\text{C}}{{{\text{H}}}_{{\text{3}}}}{\text{OH}} + {{{\text{H}}}_{{\text{2}}}}{\text{O}} \leftrightarrow {\text{C}}{{{\text{O}}}_{2}} + 3{{{\text{H}}}_{2}}, \\ \Delta H_{{298\,\,{\text{K}}}}^{0} = 49.7\,\,{\text{кДж}}\,\,{\text{мол}}{{{\text{ь}}}^{{ - 1}}}, \\ \end{gathered} $(2)
$\begin{gathered} {\text{C}}{{{\text{H}}}_{{\text{3}}}}{\text{OH}} \leftrightarrow {\text{CO}} + 2{{{\text{H}}}_{2}}, \\ \Delta H_{{298\,\,{\text{K}}}}^{0} = 90.8\,\,{\text{кДж}}\,\,{\text{мол}}{{{\text{ь}}}^{{ - 1}}}, \\ \end{gathered} $(3)
$\begin{gathered} {\text{CO}} + {{{\text{H}}}_{{\text{2}}}}{\text{O}} \leftrightarrow {\text{C}}{{{\text{O}}}_{2}} + {{{\text{H}}}_{2}}, \\ \Delta H_{{298\,\,{\text{K}}}}^{0}~ = - 41.1\,\,{\text{кДж}}\,\,{\text{мол}}{{{\text{ь}}}^{{ - 1}}}. \\ \end{gathered} $Для получения водорода методом ПРМ чаще других используют катализаторы на основе меди, обладающие высокой каталитической активностью и селективностью [7]. Однако для них характерны низкая термическая стабильность и, как следствие, дезактивация. Существует целый ряд подходов к повышению каталитической активности и стабильности медных катализаторов путем варьирования носителей металла, добавления промоторов [8–12], а также совершенствования способов приготовления [13–17].
Исследования влияния диоксида циркония на эффективность медных катализаторов [8, 18, 19] показали, что этот структурный промотор повышает селективность медных катализаторов по CO2. Промотирующее действие CeO2, обусловившее более высокую активность катализаторов с носителями на основе CeO2 и СeхZr1 –хO2 по сравнению с ZnO, Zn(Al)O и Al2O3, по мнению авторов, объясняется высокой дисперсностью наночастиц металла и сильным взаимодействием “металл–носитель” [20–25].
Проблема получения водорода высокой чистоты может быть успешно решена с использованием мембранного катализа благодаря селективному удалению водорода через Pd-содержащую мембрану, избирательно проницаемую только для водорода [26, 27]. За последнее десятилетие был опубликован ряд работ, посвященных реализации процесса парового риформинга спиртов в мембранных реакторах [28–32]. Основные преимущества такого подхода – увеличение выхода водорода и высокая чистота продукта.
Среди сплавов палладия, предлагаемых для использования в мембранных реакторах для получения высокочистого водорода, большой интерес представляют плотные и композитные мембраны на основе сплавов Pd–Cu [33]. Возможность изготовления композиционных мембран для систем очистки водорода методом магнетронного напыления тонкого слоя сплава Pd–Cu на пористую керамику (Al2O3) была недавно показана в работах [27, 34]. Авторами были также исследованы структурные превращения и водородопроницаемость образцов тонкой фольги на основе сплава 60% Pd−Cu в процессе термического циклирования [34–36].
Цель данной работы – исследование процесса парового риформинга метанола с использованием катализатора на основе Cu и Ni на оксидном носителе в мембранном реакторе с мембраной из сплава 60% Pd−Cu.
ЭКСПЕРИМЕНТАЛЬНАЯ ЧАСТЬ
Приготовление катализатора и Pd–Cu-мембран
Носитель для катализатора Ni0.2–Cu0.8/ Ce0.3Zr0.7O2-δ (CuNi/ZrCe) был приготовлен методом соосаждения из оксинитрата циркония ZrO(NO3)2 (99% ALDRICH) и нитрата церия Ce(NO3)3 ⋅ 6H2O (99.995%). Полученные гидратированные оксиды были отожжены в течение 5 ч при температуре 600°С для формирования твердого раствора оксидов со структурой флюорита. Затем образцы были поочередно пропитаны водными растворами Сu(NO3)2 · 3H2O (>98%) и Ni(NO3)2 · 6H2O (≥98.5% ALDRICH) в количествах, рассчитанных так, чтобы суммарное содержание металлов составило 20% от массы носителя. Соотношение никеля и меди в образцах составило 1 : 4. Полученный катализатор был отожжен на воздухе при 400°С в течение 3 ч. Далее он был обработан потоком газовой смеси Н2 (5%)/Ar (20 мл/мин) в течение 3 ч при 350°С для восстановления металлов.
Для выплавки заготовок сплава 60% Pd–Cu использовали в соответствующем соотношении компоненты чистотой не менее 99.95 мас. %, избегая тем самым образования включений дефектов и примесей. Заготовки выплавляли в электродуговой печи с нерасходуемым подом в инертной атмосфере.
Фольгу сплава Pd–Cu готовили холодной прокаткой на вакуумном прокатном стане ДУО-170, 4-х валковом стане КВАРТО 110/320 × 300 и лабораторном 20-ти валковом стане с промежуточными отжигами и вакуумированием. Деформацию заготовки проводили в вакууме 5 × 10–3 Па при температуре 1323 → 1123 K с толщины 10 мм до 30 мкм за несколько десятков проходов с периодическим повтором циклов “деформация–отжиг”.
Перед экспериментами полученную фольгу последовательно промывали ацетоном, этиловым спиртом, дистиллированной водой и высушивали до постоянного веса.
Физико-химические исследования катализатора и мембран
Рентгенофазовый анализ (РФА) образцов осуществляли с помощью рентгеновского дифрактометра Rigaku D/Max-2200 (CuKα1-излучение) в режиме пошагового сканирования. Для обработки спектров и качественного анализа использовался пакет программ Rigaku Application Data Processing. Идентификацию фазового состава осуществляли соотнесениемпозиции и интенсивности линий на рентгенограмме с базой данных.
Средний размер кристаллитов оценивали по уширению дифракционных рефлексов в соответствии с уравнением Дебая–Шеррера (область когерентного рассеяния, ОКР):
(4)
$d = \frac{{k{\lambda }}}{{{{{\left( {{{B}^{2}} - {{b}^{2}}} \right)}}^{{{1 \mathord{\left/ {\vphantom {1 2}} \right. \kern-0em} 2}}}}\cos \theta }},$Измерения площади и пористости образца катализатора проводили методом низкотемпературной адсорбции азота на поромере ASAP-2020N фирмы Micromeritics (США). Величину удельной поверхности определяли методом БЭТ по результатам измерений в интервале относительных давлений Р/Р0 = 0–1 с использованием уравнения для полимолекулярной адсорбции пара. Средний размер частиц по БЭТ-методу оценивали по методике, описанной в [37]. В дальнейшем этом подход использовали для оценки степени агломерации кристаллитов, формирующих катализатор, при сопоставлении с областью когерентного рассеяния [38].
Исследование состава образцов мембран из сплава Pd–Cu проводили методом рентгеноспектрального флуоресцентного элементного анализа (РСФА) на приборе Performix с родиевым анодом рентгеновской трубки. Ошибка измерения составляла ±0.8 мас. %.
Измерение водородопроницаемости и проведение каталитических экспериментов
Для тестирования на водородопроницаемость фольги толщиной 34 мкм использовали мембранно-каталитический реактор в виде цилиндра из нержавеющей стали, представляющий собой два одинаковых фланца, стягиваемых четырьмя болтами (рис. 1). Герметичность мембранного реактора обеспечивали с помощью прокладок из меди и углеродного материала графлекс.
Мембрана разделяла реактор на две одинаковые несообщающиеся камеры ретентата и пермеата. Активная площадь мембраны после герметизации в реакторе составляла 1.1 см2. Каждая камера снабжена входным и выходным патрубками из нержавеющей стали. Имеющиеся в камере ретентата полости позволяют помещать в них катализатор парового риформинга метанола в количестве 0.3 г, превращая мембранный реактор из диффузионной ячейки в мембранно-каталитическую систему.
Измерения проводили в мембранном реакторе в температурном интервале от 170 до 400°С, температуру контролировали регулятором OVEN TRM 201 и хромель-копелевой термопарой. В камеру ретентата подавали водород (особой чистоты) со скоростью 20 см3/мин, а в камеру пермеата – газ-носитель аргон, со скоростью 20 см3/мин. При этом часть водорода диффундировала в камеру пермеата в поток газа-носителя. Использованная скорость газа-носителя в зоне пермеата была выбрана на основании ранее проведенных исследований ПРМ в традиционном проточном реакторе.
Концентрацию водорода в камере ретентата и пермеата определяли на хроматографе Chrom-4 с детектором по теплопроводности и цеолитной колонкой (фаза CaAZeosorb, газ-носитель Ar), откалиброванным по смесям водород–аргон известного состава. Хроматограммы обрабатывали с помощью программы Ecochrom.
Степень извлечения водорода рассчитывали по формуле:
(5)
$R = {{{{\omega }_{{{{{\text{H}}}_{2}}{\text{перм}}}}}} \mathord{\left/ {\vphantom {{{{\omega }_{{{{{\text{H}}}_{2}}{\text{перм}}}}}} {{{\omega }_{{{{{\text{H}}}_{2}}{\text{сум}}}}}}}} \right. \kern-0em} {{{\omega }_{{{{{\text{H}}}_{2}}{\text{сум}}}}}}},$Коэффициент проницаемости водорода J, рассчитывали по формуле:
(6)
$J = {{\left( {Q\delta } \right)} \mathord{\left/ {\vphantom {{\left( {Q\delta } \right)} {\left( {S\left( {\sqrt {{{Р}_{1}}} - \sqrt {{{Р}_{2}}} } \right)} \right)}}} \right. \kern-0em} {\left( {S\left( {\sqrt {{{Р}_{1}}} - \sqrt {{{Р}_{2}}} } \right)} \right)}}\left[ {{{\left( {{\text{с}}{{{\text{м}}}^{3}}\,{\text{см}}} \right)} \mathord{\left/ {\vphantom {{\left( {{\text{с}}{{{\text{м}}}^{3}}\,{\text{см}}} \right)} {\left( {{\text{с}}{{{\text{м}}}^{2}}\,{\text{с}}\,{\text{ат}}{{{\text{м}}}^{{{1 \mathord{\left/ {\vphantom {1 2}} \right. \kern-0em} 2}}}}} \right)}}} \right. \kern-0em} {\left( {{\text{с}}{{{\text{м}}}^{2}}\,{\text{с}}\,{\text{ат}}{{{\text{м}}}^{{{1 \mathord{\left/ {\vphantom {1 2}} \right. \kern-0em} 2}}}}} \right)}}} \right],$Для проведения каталитических исследований навеску образца массой 0.3 г смешивали с фракцией кварца 1–3 мм и засыпали в трубчатый проточный реактор из нержавеющей стали внутренним диаметром 8 мм и длиной 220 мм. Нагрев реактора осуществляли в электропечи в температурном диапазоне 220–400°С.
Смесь метанола с водой в мольном соотношении 1 : 1 подавали в испаритель со скоростью 1 см3/ч жидкостным инфузионным насосом 1235N фирмы “AtomMedicalCorporation” (Япония), откуда пары спирта и воды поступали на катализатор в потоке газа-носителя (Ar) со скоростью 20 см3/мин.
Конденсируемые продукты реакции сжижали на выходе из реактора в стеклянном приемнике, охлаждаемом до температуры таяния льда. Газовый поток направляли на хроматографический анализ. Оксиды углерода анализировали на колонке с активированным углем этого же хроматографа, а водород – на колонке с цеолитом СаА-Цеосорб хроматографа Chrom-4 с детектором по теплопроводности. Запись хроматограмм и их расчет осуществляли с помощью программы Ecochrom.
Величины конверсии метанола Х (мол. %) и селективности процесса риформинга S (%) рассчитывались по результатам анализа с использованием следующих уравнений:
(7)
${{X}_{{{\text{C}}{{{\text{H}}}_{{\text{3}}}}{\text{OH}}}}} = \frac{{{{n}_{{{\text{C}}{{{\text{H}}}_{{\text{3}}}}{\text{OH}},{\text{in}}}}} - {{n}_{{{\text{C}}{{{\text{H}}}_{{\text{3}}}}{\text{OH}},{\text{out}}}}}}}{{{{n}_{{{\text{C}}{{{\text{H}}}_{{\text{3}}}}{\text{OH}},{\text{in}}}}}}} \times 100\% ,$(8)
$S = \frac{{{{n}_{{{\text{C}}{{{\text{O}}}_{{\text{2}}}}{\text{,out}}}}}}}{{{{n}_{{{\text{C}}{{{\text{O}}}_{2}},{\text{out}}}}} + {{n}_{{{\text{CO}},{\text{out}}}}}}} \times 100\% ,$РЕЗУЛЬТАТЫ И ИХ ОБСУЖДЕНИЕ
На рентгенограмме катализатора CuNi/ZrCe максимумы рефлексов сплава Cu–Ni располагаются между позициями, характерными для индивидуальных металлов. Параметр кубической элементарной ячейки для сплава Cu–Ni составляет 3.6162 ± 0.0007 Å. Рефлексы, соответствующие структуре кубического оксида циркония, стабилизированного церием, характеризуются существенно большим уширением, а параметр его элементарной ячейки составляет 5.255 ± 0.005 Å.
Некоторые параметры, характеризующие микроструктуру катализатора CuNi/ZrCe, полученные с помощью БЭТ и РФА, сведены в табл. 1. Можно полагать, что площадь поверхности в первую очередь определяется содержанием оксида, количество которого в катализаторе значительно больше. Причем размер частиц оксида циркония, рассчитанный на основании данных БЭТ, более чем в 20 раз превышает величину ОКР. Это обусловлено агломерацией частиц катализаторов, типичной для наноразмерных материалов. Срастание частиц приводит к формированию небольшого количества пор.
Таблица 1.
Значения площади поверхности и размера наночастиц полученного катализатора
Катализатор | Площадь поверхности, м2/г | Размер частиц ОКР, нм | Средний размер частиц по БЭТ, нм | Объем пор, м3/г | |
---|---|---|---|---|---|
металлов | МхZrO2х–δ | ||||
Ni0.2–Cu0.8/Ce0.3Zr0.7O2–δ (Cu–Ni/Zr–Ce) |
43 ± 2 | 26 ± 1 | 6 ± 1 | 140 | 0.047 |
Согласно исследованию состава мембраны методом рентгеноспектрального флуоресцентного элементного анализа содержание палладия и меди в мембране составляло 62.7 и 37.3 мас. %, соответственно.
При измерении водородопроницаемости мембраны с ростом температуры от 170 до 300°С наблюдался медленный рост потока водорода в камере пермеата. Дальнейшее нагревание до 400°С вызывало существенное нарастание потока водорода через мембрану (рис. 2). Степень извлечения водорода с ростом температуры также существенно повышается и при температуре 400°С превышает 60% (рис. 3). При охлаждении ниже 400°С наблюдался гистерезис проницаемости водорода – величина потока водорода через мембрану при охлаждении значительно превышала таковую в ходе нагревания при тех же температурах (рис. 2). Можно полагать, что это связано с одновременным присутствием в изучаемом интервале температур двух фаз сплава Pd–Cu (α и β), соотношение между которыми по-разному изменяется при подъеме и спуске температуры. Авторы работы [33] объяснили наблюдаемое явление заторможенностью перехода от α- к β-модификации сплава Pd–Cu при охлаждении. Кроме того, представляется целесообразным отметить, что исходный образец после прокатки является двухфазным, предельно высокодисперсным. При этом адсорбция водорода на межфазных границах существенно снижает проницаемость. В ходе нагревания превращение α ↔ β завершается, происходит рекристаллизация материала с укрупнением зерен. В результате проницаемость увеличивается, и при охлаждении доля упорядоченной структуры остается выше, чем при тех же температурах при нагревании, существенно уменьшается доля границ зерен, что объясняет медленный спад проницаемости при охлаждении.
Рис. 2.
Гистерезис водородопроницаемости образца сплава фольги Pd–Cu. Стрелками указано направление изменения температуры.
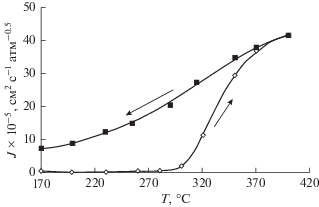
Рис. 3.
Температурная зависимость степени извлечения водорода через мембрану из фольги Pd–Cu в ходе нагревания.
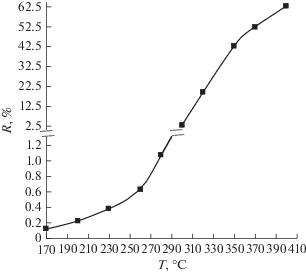
Аррениусовская температурная зависимость коэффициента проницаемости водорода через исследуемую мембрану (рис. 4) показала изменение наклона линейных зависимостей проницаемости от обратной температуры, обусловленное упомянутым выше “заторможенным” фазовым переходом.
Рис. 4.
Температурная зависимость водородопроницаемости сплава Pd–Cu толщиной 34 мкм в координатах Аррениуса.
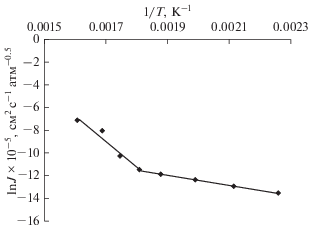
Рассчитанные значения энергии активации проницаемости водорода составили 38 кДж/моль в интервале температур 170–300°С и 190 кДж/моль в интервале температур 300–370°С.
В процессе ПРМ в мембранном реакторе на катализаторе Cu–Ni/Zr–Ce основными продуктами были водород и диоксид углерода при селективности по основному процессу не менее 97% (уравнение (1)).
Использование мембраны позволяет повысить выход водорода по сравнению с величиной, достигаемой в традиционном проточном реакторе. На рис. 5 представлены потоки водорода в традиционном реакторе и суммарные потоки водорода в зонах пермеата и ретентата в мембранном реакторе c Pd–Cu-мембраной на катализаторе Cu–Ni/Zr–Ce. Суммарный выход водорода в мембранном реакторе при температурах выше 280°С оказался больше, чем в традиционном проточном реакторе.
Рис. 5.
Температурные зависимости, А: 1 – выход водорода в традиционном реакторе; 2 – выход водорода в зоне пермеата; 3 – суммарный выход водорода при проведении процесса ПРМ в мембранном реакторе с катализатором.
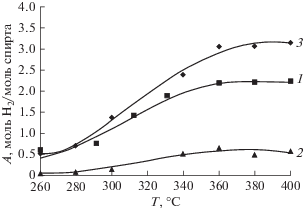
С ростом температуры выход водорода возрастает, достигая значения, соответствующего полному превращению метанола. При этом выход СО не превышает 0.015 моль СО/моль спирта (рис. 6, кривая 1). Селективность ПРМ по водороду снижается с ростом температуры (рис. 6, кривая 2) за счет возрастания вероятности протекания реакции (2) при высоких температурах.
Рис. 6.
Температурные зависимости: 1 – выход CO; 2 – селективность протекания ПРМ на катализаторе Cu–Ni/Zr–Ce в мембранном реакторе.
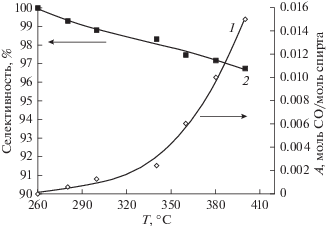
Для выяснения возможного вклада в ПРМ собственной каталитической активности палладиево-медной мембраны был проведен процесс без катализатора. Водород в этом эксперименте также присутствовал в выходящем из реактора потоке (рис. 7), что свидетельствует о каталитической активности металлов, входящих в состав мембраны, в процессе парового риформинга метанола. Однако суммарный выход водорода из реактора в отсутствие катализатора был более, чем на порядок ниже, чем в реакторе с нанесенным на оксид катализатором (рис. 5, кривая 3). Это объясняется значительно меньшей активностью материала мембраны по сравнению с нанесенным на оксид катализатором Cu–Ni, вследствие гораздо меньшей удельной поверхности мембраны.
Рис. 7.
Температурные зависимости: 1 – выхода водорода в зоне пермеата; 2 –суммарный выход водорода при проведении процесса ПРМ в мембранном реакторе без катализатора.
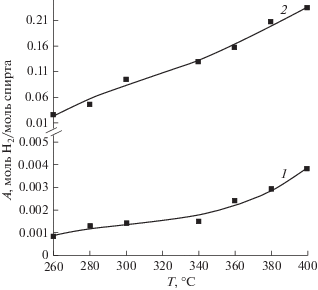
Следует подчеркнуть, что процесс в мембранном реакторе с катализатором Cu–Ni/Zr–Ce практически не дает CO, а получаемый на выходе из зоны пермеата водород вовсе не содержит примесей. Кроме того, использование мембраны позволяет повысить суммарный выход водорода в мембранном реакторе при температурах выше 280°С, который оказался почти в 1.5 раза выше, чем в традиционном проточном реакторе. Причиной этого является то, что избирательное извлечение водорода из зоны ПРМ через мембрану из сплава Pd–Cu сдвигает равновесие реакций (1) и (3) в сторону образования водорода.
Водородопроницаемость мембраны после проведения длительных каталитических экспериментов может снижаться в 3–4 раза. Это объясняется тем, что при температурах, выше 300°С происходит образование монооксида углерода, который отравляет мембрану, снижая ее проницаемость. После регенерации мембраны смесью водорода (5 об. %) в аргоне при 350°С в течение двух часов водородопроницаемость мембраны возвращается к исходным значениям.
ЗАКЛЮЧЕНИЕ
Показан гистерезис водородопроницаемости мембраны из сплава Pd–Cu за счет заторможенного протекания фазового перехода от α- к β-модификации сплава Pd–Cu, за счет чего соотношение фаз по-разному изменяется при подъеме и понижении температуры. Степень извлечения водорода через мембрану при нагревании возрастает и превышает 60% при 400°С.
На основании проведенных экспериментов можно заключить, что мембрана из сплава Pd–Cu, обладая высокой проницаемостью по водороду, представляется перспективной для получения водорода высокой чистоты в процессе ПРМ в присутствии катализатора Cu–Ni/Zr–Ce при температурах от 260 до 370°С. ПРМ в мембранном реакторе позволяет получать особо чистый водород с селективностью не менее 97% и повышать эффективность процесса ПРМ в полтора раза за счет сдвига равновесия в сторону образования водорода при его избирательном извлечении.
Список литературы
Dawood F., Anda M., Shafiullah G.M. // Int. J. Hydrogen Energy. 2020. V. 45. № 7. P. 3847.
Garland N.L., Papageorgopoulos D.C., Stanford J.M. // Energy Procedia. 2012. V. 28. P. 2.
Yaroslavtsev A.B., Stenina I.A., Golubenko D.V. // Pure Appl. Chem. 2020. doi.org/.https://doi.org/10.1515/pac-2019-1208
Цодиков М.В., Чистяков А.В., Яндиева Ф.А., Жмакин В.В., Гехман А.Е., Моисеев И.И. // Катализ в промышленности. 2010. № 5. С. 32.
Hasegawa F., Yokoyama S., Imou K. // Bioresource Technology. 2010. V. 101. № 1. P. S109.
Kempegowda R.S, PannirSelvam P.V., Skreiberg $O/'{\text{.,}}$ Trana K.-Q. // J. Chem. Technol. Biotechnol. 2012. V. 87. P. 897.
Mironova E.Yu., Lytkina A.A., Ermilova M.M., Efimov M.N., Zemtsov L.M., Orekhova N.V., Karpacheva G.P., Bondarenko G.N., Muraviev D.N., Yaroslavtsev A.B. // Int. J. Hydrogen Energy. 2015. V. 40. P. 3557.
Jeong H., Kim K.I., Kim T.H., Ko C.H., Park H.C., Song I.K. // J. Power Sources. 2006. V. 159. P. 1296.
Wu G.-S., Mao D.-S., Lu G.-Z., Cao Y., Fan K.-N. // Catal. Lett. 2009. V. 130. P. 177.
Yong-Feng L., Xin-Fa D., Wei-Ming L. // Int. J. Hydrogen Energy. 2004. V. 29. P. 1617.
Ma L., Gong B., Tran T., Wainwright M.S. // Catal. Today. 2000. V. 63. P. 499.
Lytkina A.A., Orekhova N.V.,Ermilova M.M., Petriev I.S., Baryshev M.G., Yaroslavtsev A.B. // Int. J. Hydrogen Energy. 2019. V. 44. № 26. P. 13 310.
Yao C.-Z., Wang L.-C., Liu Y.-M., Wu G.-S., Cao Y., Dai W.-L., He H.-Y., Fan K.-N. // Appl. Catal. A: General. 2006. V. 297. P. 151.
Shen J.-P., Song C. // Catal. Today. 2002. V. 77. P. 89.
Shishido T., Yamamoto Y., Morioka H., Takaki K., Takehira K. // Appl. Catal. A: General. 2004. V. 263. P. 249.
Jakdetchai O., Takayama N., Nakajima T. // Kinet. Catal. 2005. V. 46. P. 56.
Águila G., Jiménez J., Guerrero S., Gracia F., Chornik B., Quinteros S., Araya P. // Appl. Catal. A: General. 2009. V. 360. P. 98.
Agrell J., Birgersson H., Boutonnet M., Melián-Cabrera I., Navarro R.M., Fierro J.L.G. // J. Catal. 2003. V. 219. P. 389.
Лыткина A.A., Орехова Н.В., Ермилова М.М., Петриев И.С., Барышев М.Г. // Мембраны и мембранные технологии. 2017. Т. 7. С. 398.
Yang S., Zhou F., Liu Y., Zhang L., Chen Yu. Wang H., Tian Y., Zhang C., Liu D. // Int. J. Hydrogen Energy. 2019. V. 44. № 14–15. P. 7252.
Valdés-Solís T., Marbán G., Fuertes A.B. // Catal. Today. 2006. V. 116. P. 354.
Papavasiliou J., Avgouropoulos G., Ioannides T. // Appl. Catal. B. Environmen. 2007. V. 69. P. 226.
Zhang X., Shi P. // J. Mol. Catal. A. Chem. 2003. V. 194. P. 99.
Liu Y., Hayakawa T., Tsunoda T., Suzuki K., Hamakawa S., Murata K., Shiozaki R., Ishii T., Kumagai M. // Top. Catal. 2003. V. 22. P. 205.
Lytkina A.A., Orekhova N.V., Ermilova M.M., Yaroslavtsev A.B. // Int. J. Hydrogen Energy. 2018. V. 43. № 1. P. 198.
Rahimpour M.R., Samimi F., Babapoor A., Tohidian T., Mohebi S. // Chem. Engineering&Processing: Process Intensification. 2017. V. 121. P. 24.
Al-Mufachi N.A., Rees N.V., Steinberger-Wilkens R. // Renew. Sustain. Energy Rev. 2015. V. 47. P. 540.
Лыткина A.A., Орехова Н.В., Ярославцев А.Б. // Мембраны и мембранные технологии. 2018. Т. 8. С. 301.
Kim S., Yun S.-W., Lee B., Heo J., Kim K., Kim Y.-T., Lim H. // Int. J. Hydrogen Energy. 2019. V. 44. № 4. P. 2330.
Mironova E.Yu., Ermilova M.M., Orekhova N.V., Muraviev D.N., Yaroslavtsev A.B. // Catal. Today. 2014. V. 236. P. 64.
Iulianelli A., Ribeirinha P., Mendes A., Basile A. // Renew. Sustain. Energy Rev. 2014. V. 29. P. 355.
Iulianelli A., Longo T., Basile A. // J. Membr. Sci. 2008. V. 323. P. 235.
Zhang K., Way J.D. // Separation. Purification Technol. 2017. V. 186. P. 39.
Ievlev V.M., Solntsev K.A., Sitnikov A.I., Chernyavskiy A.S., Maksimenko A.A., Dontsov A.I. // Inorganic Materials: Applied Research. 2016. V. 7. № 4. P. 586.
Иевлев В.М., Максименко А.А., Каныкин С.В., Белоногов Е.К., Володина М.С., Рошан Н.Р. // Конденсированные среды и межфазные границы. 2016. № 4. С. 521.
Иевлев В.М., Солнцев К.А., Донцов А.И., Максименко А.А., Канныкин С.В. // Журн. техн. физики. 2016. Т. 86. № 3. С. 149.
Arvaniti E.C, Juenger M.C.G., Bernal S.A., Susan A., Duchesn J., Courard L., Leroy S., Provis J.L., Klemm A., De Belie N. // Materials and Structures. 2015. V. 48. P. 3687.
Stenina I.A., Kulova T.L., Skundin A.M., Yaroslavtsev A.B. // Materials Research Bulletin. 2016. V. 75. P. 178.
Дополнительные материалы отсутствуют.