Неорганические материалы, 2023, T. 59, № 2, стр. 128-138
Исследование структурных характеристик и деформационного поведения пористого титана, полученного методом спекания
С. Г. Аникеев 1, *, Н. В. Артюхова 1, М. И. Кафтаранова 1, В. Н. Ходоренко 1, А. С. Гарин 1, Е. С. Марченко 1
1 Национальный исследовательский Томский государственный университет
634050 Томск,
пр. Ленина, 36, Россия
* E-mail: Anikeev_Sergey@mail.ru
Поступила в редакцию 07.07.2022
После доработки 28.11.2022
Принята к публикации 29.11.2022
- EDN: YCHYQN
- DOI: 10.31857/S0002337X2302001X
Аннотация
Проведено исследование структурных особенностей порошков ПТМ-1 и ПТС-1 и пористых материалов на их основе, полученных методом спекания. Определены количественные характеристики порового пространства спеченных образцов. Показана связь макро- и микроструктурных особенностей полученных пористых сплавов с их деформационно-прочностными параметрами. Использованы методы растровой электронной микроскопии, рентгенографического анализа, стереометрические методики, прочностные характеристики исследованы в экспериментах на сжатие. Обнаружено, что пористый материал, полученный спеканием порошка титана марки ПТМ-1, имеет более высокие значения основных прочностных и деформационных характеристик. Это связано с меньшей пористостью по сравнению с образцами ПТC-1, а также с процессами дисперсного упрочнения частицами фазы TiC при его структурообразовании.
ВВЕДЕНИЕ
Изделия на основе титана успешно используются во многих областях: машиностроении, металлургии, медицинской промышленности [1–9]. Среди разнообразных способов получения материалов порошковая металлургия занимает особое место, т.к. позволяет не только производить изделия сложной формы с минимальными допусками на обработку, но и создавать принципиально новые материалы [8–12]. Высокая коррозионная стойкость титана, коррозионно-механическая прочность, эрозионно-кавитационная стойкость, удельная прочность, хладноломкость, немaгнитность и ряд других физико-механических характеристик придают титановым сплавам полезные свойства разнообразных материалов [1, 2, 8–19].
Свойства изделий на основе титана, полученных методами порошковой металлургии, в некоторых случаях превосходят свойства материала, полученного литьем [1, 12–22]. Из порошка титана возможно изготовление беспористых спеченных материалов с высокой плотностью, например, для титановых корпусов подшипников реактивных двигателей, втулок, фланцев и др. [14]. Использование таких изделий из порошков титана в условиях, требующих высоких эксплуатационных свойств, возможно при благоприятном сочетании структурных и физико-механических свойств. В отдельных случаях для решения различных задач медицинского назначения требуется сохранение пористости, но при этом необходимо формирование качественных контактов между частицами [5]. В связи с этим выбор титанового порошка, пригодного для изготовления изделий медицинского назначения, также является весьма актуальной задачей.
Известно, что структура, морфология частиц порошков, их гранулометрический состав оказывают влияние на структурные и прочностные свойства конечного спеченного материала [9, 12, 14, 22–26]. Не менее важными параметрами, влияющими на результат спекания материала из титановых порошков, являются их способ производства и фазово-химический состав. Последний фактор определяет наличие в них примесей, их количество и характер распределения. На сегодняшний день достаточно большое количество работ посвящено исследованию структуры и свойств титановых сплавов, полученных различными методами, что доказывает актуальность и перспективность данного исследования [1, 2, 6]. Многообразие особенностей сформированной структуры пористых материалов определяет изменение их физико-механических свойств в широких пределах. Из этого следует, что путем всестороннего изучения и последующей оптимизации структуры пористого сплава на основе титана можно добиться существенного повышения его деформационно- прочностных характеристик.
Целью данной работы является проведение сравнительного анализа макро- и микроструктурных характеристик пористых сплавов, полученных спеканием порошков титана ПТМ-1 и ПТС-1 различного гранулометрического состава, механизмов формирования структуры данных сплавов, а также их деформационного поведения в условиях сжатия.
ЭКСПЕРИМЕНТАЛЬНАЯ ЧАСТЬ
В работе исследовали пористые сплавы (С-ПТМ-1, С-ПТС-1), полученные методом спекания порошков титана (ПТМ-1, ПТС-1). В качестве исходного материала для создания экспериментальных пористых образцов использовали порошки титана марок ПТМ-1 и ПТС-1 с фракциями 30–60 и 50–150 мкм соответственно (АО “Полема”, Россия, г. Тула). Используемые порошки Ti были получены методом гидридно-кальциевого восстановления. В ходе этого метода реализуется восстановление диоксида титана (TiO2) гидридом кальция (СаН2) в гидрид титана (TiH2) и разложение последнего на Н и Ti. Частицы порошка имеют иррегулярную губчатую форму и развитую поверхностную структуру с множеством углублений и выступов.
Для изготовления пористых спеченных образцов порошки титана свободно засыпали в кварцевую трубку диаметром 12–13, длиной 170 мм. Засыпку подвергали вибрационному воздействию, уплотняя порошок до показателя пористости не менее 75–80%, с целью получения более равномерного распределения пор и увеличения количества контактов между частицами.
Спекание всех заготовок проводили в вакуумной печи типа Nabertherm в вакууме не менее 14 × 10–6 Па при температуре 950°С и времени выдержки 80 мин. Формы для спекания представляли собой кварцевые трубки с заглушками из губчатого титана, которые укладывали в печи горизонтально. Среднюю скорость нагрева обеспечивали автоматической системой управления электровакуумной печи, она составляла не более 10°С/мин.
Температурный режим спекания порошков ПТМ-1 и ПТС-1 подобран исходя из данных о спекании титановых гранул [9]. Установлено, что при 800°С спекания отдельных частиц порошка не происходит. При 850°С начинают образовываться контакты между частицами и формироваться пористый каркас. Структура экспериментальных образцов, полученных при 950°С, являлась удовлетворительной по качеству контактов, степени однородности распределения пор в спеченной системе, их открытости и величине пористости образцов. Образцы, полученные выше 950°С (до 1050°С), имели более плотное строение, их регулярная пористая структура утрачивалась, приближаясь к состоянию монолитного тела. Подбор времени спекания основывается на условии получения качественных контактов между отдельными частицами порошка в составе пористого тела. Согласно [9], спекание в течение 5 мин при температуре 820°С приводит к началу процесса исчезновения границ между частицами, а при более длительной высокотемпературной выдержке толщина оксидной пленки уменьшается настолько, что не может препятствовать диффузионному спеканию и значимому росту контактных шеек. Доведение времени выдержки до 80 мин в настоящей работе связано с получением оптимальной степени спекания, необходимой для достижения высокой прочности наряду с сохранением регулярной пористой структуры. Таким образом, оптимальным режимом спекания является температура и время выдержки 950°С и 80 мин соответственно для обоих типов порошков.
Морфологические особенности и микроструктуру порошков (ПТМ-1, ПТС-1) и образцов (С-ПТМ-1, С-ПТС-1) исследовали методом растровой электронной микроскопии на микроскопах Teskan Mira 3 LM и Thermo Fisher Axia ChemiSEM при ускоряющих напряжениях электронного пучка 10–20 кВ. Концентрационный состав фаз определяли с помощью энергодисперсионного микроанализатора EDAX ECON IV. Исследование фазового состава проводили на дифрактометре XRD-6000 с использованием CuKα-излучения. Средний размер пор и долю частиц TiC определяли стереометрическим способом с использованием программных пакетов ImageJ. Коэффициент пористости устанавливали методом взвешивания с использованием весов AND GR-200, рассчитывая по формуле
(1)
${\text{П}} = \left( {1 - \frac{{{{\rho }_{{{\text{пор}}}}}}}{{{{\rho }_{{{\text{мон}}}}}}}} \right) \times 100\% ,$Объем V полученного цилиндрического образца определяли по формуле
где r – радиус основания, h – высота.Построены гистограммы распределения пор и частиц порошка по размерам. Статистический анализ и построение графических материалов выполнено при помощи программного обеспечения OriginPro.
Металлографические шлифы получали по стандартной методике на шлифовальной машине MoPao 160 с использованием бумаги с зернистостью P600, P1000, P2500, P3000. Для выявления структурных особенностей выполнено травление в смеси кислот 10 мл HF + 40 мл HNO3.
Прочностные характеристики (модуль Юнга, предел текучести, предел прочности) пористых образцов были исследованы сжатием на испытательной машине Instron 5969. Образцы для испытания были получены методом электроэрозионной резки исходных спеченных цилиндрических образцов и имели форму прямоугольного параллелепипеда. Размер образцов, участвующих в испытаниях, составлял 6 × 3 × 3 мм, скорость деформирования – 0.36 мм/мин. Количество экспериментальных образцов каждой фракции порошков составило 10 шт.
РЕЗУЛЬТАТЫ И ОБСУЖДЕНИЕ
В ходе структурных исследований установлено, что частицы порошка ПТМ-1 с фракцией 30–60 мкм имеют компактную и губчатую структуру, неправильную геометрическую форму, узкий интервал размеров (рис. 1). Установлено, что средний размер частиц порошка составляет 54.9 мкм при стандартном отклонении σ = 32.83 мкм и медианном значении ME = 48.01 мкм, что соответствует паспортным данным на порошковый материал. В отдельных частицах отмечаются спрямленные тройные границы зерен, которые сформированы при слиянии отдельных титановых зерен в процессе восстановительной реакции между диоксидом титана и гидридом кальция в ходе получения порошка.
Морфологически структура порошка ПТС-1 схожа с вышеописанной. В отличие от ПТМ-1 частицы порошка ПТС-1 (фракция 50–150 мкм) имеют более разветвленную структуру и больший разброс по размерам (рис. 2). Отличие заключается в размерном диапазоне частиц порошка. Установлено, что средний размер частиц составляет 79.51 мкм при стандартном отклонении σ = 70.56 мкм и медианном значении ME = 57.03 мкм. Показано, что с увеличением среднего размера частиц порошка локальный максимум распределения практически не смещается в сторону больших размеров, но доля частиц порошка, размеры которых составляют более 60 мкм, существенно увеличивается. Наряду с мелкими гранулами наблюдали крупные губчатые частицы неправильной геометрической формы.
На энергодисперсионных спектрах, полученных при исследовании химического состава порошков ПТМ-1 и ПТС-1, явно выражены пики основного элемента Ti и примесных элементов O и C (рис. 3). Анализ данных спектров показал, что в обоих типах порошков содержится практически одинаковое количество легких примесей O и C. В области малых энергий спектра около Ti(Lα) = 0.452 кэВ наблюдается уширение локального максимума O(Kα) = = 0.523 кэВ из-за их наложения, что увеличивает ошибку определения данных элементов.
Установлено, что химический состав порошков ПТМ-1 и ПТС-1 качественно идентичен (табл. 1). Титан является основным химическим элементом в структуре материала. Количество С и O завышено, что является особенностью метода EDX, который имеет высокую погрешность при определении легких элементов. Об их содержании можно судить только качественно, наличие примесных элементов объясняется высокой склонностью титана к окислению и распространенностью углерода в технологическом процессе получения. Можно полагать, что по причине сходства химического состава исходных порошков свойства спеченных из них материалов будут определяться в основном морфологическими особенностями и гранулометрическими характеристиками данных порошков.
Таблица 1.
Химический состав исходных порошков ПТМ-1 и ПТС-1
Марка | Химический состав, мас. % | ||
---|---|---|---|
Ti | C | O | |
ПТМ-1 | 76.4 | 14.4 | 9.2 |
ПТС-1 | 78.5 | 13.1 | 8.4 |
В ходе исследования структуры пористых спеченных материалов на основе порошков Ti (C-ПТМ-1 и C-ПТС-1) показано, что для обоих образцов характерно одномодальное распределение пор по размерам, что типично для мелкопористых материалов (рис. 4). Пористость (П) экспериментальных образцов C-ПТМ-1 составляет 65%, C-ПТС-1 – 72.5%. Установлено, что при использовании порошка с более крупными частицами (ПТС-1) пористость образцов после спекания (C-ПТС-1) выше. Развитая структура мелкодисперсных частиц ПТM-1 способствует получению порошковой заготовки с большей плотностью [7]. Это приводит к получению образцов с бóльшим значением коэффициента пористости (C-ПТС-1).
Рис. 4.
Гистограммы распределения пор по размерам в спеченных образцах титана С-ПТМ-1 (а) и С-ПТС-1 (б).
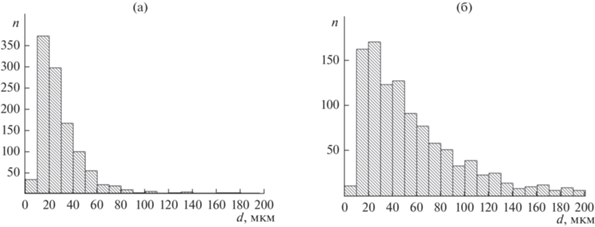
Средний размер пор для пористого материала С-ПТМ-1 составил dпор = 30 мкм при стандартном отклонении σ = 20 мкм и медианном значении ME = 25 мкм, в то время как для С-ПТС-1 dпор = 55 мкм, σ = 40 мкм и ME = 45 мкм. Установлено, что в поровом пространстве образцов С-ПТМ-1 наблюдали более однородное строение поровых каналов. Размеры пор в С-ПТМ-1 составляют в основном до 90 мкм, в то время как в С-ПТС-1 до 200 мкм. Форма пор в полученных образцах имеет неправильные контуры (рис. 5).
Исходя из анализа макроструктуры, а также порового пространства полученных образцов можно сделать предположение о процессах структурообразования и механизмах его реализации при спекании пористого сплава на основе однокомпонентного порошка титана. Поскольку в нашем случае при получении материала не достигнута температура плавления Ti, которая составляет 1668°С, и весь процесс лимитирован температурой 950°С, то спекание проходит без образования жидкой фазы и структурообразование пористого сплава на основе Ti определяется только процессами самодиффузии в твердой фазе.
На начальной стадии спекания формируются связи между частицами порошка Ti и растет число контактов между ними. Затем зоны контакта между частицами, возникающие на начальной стадии, расширяются. Образование, рост и упрочнение контактов связаны с основным механизмом переноса вещества – поверхностной диффузией [1, 9, 12]. Перенос массы по этому механизму не приводит к усадке образцов, однако он обеспечивает перемещение атомов с поверхности более крупной поры на поверхность более мелкой сообщающейся с ней порой, т.е. переводит всю систему в положение большей термодинамической устойчивости. При повышении температуры до 950°С и выдержке механизм поверхностной диффузии меняется на объемный, который начинает преобладать с увеличением температуры. Это приводит к сближению центров спекаемых частиц и уплотнению порошковой насыпки.
Уплотнение частиц титана в процессе спекания образцов наблюдается как в случае ПТМ-1, так и ПТС-1. Межчастичные поры в сплавах уменьшаются за счет ползучести частиц титана. Качество контактов Ti–Ti от периферии к центру не меняется. Таким образом, плотность образцов после спекания растет во всем объеме равномерно. Отличие заключается только в величине среднего размера пор образцов. Аттестация пористой структуры спеченных образцов подтвердила однородное распределение пор во всем объеме материала.
Анализ структуры спеченных пористых сплавов на основе титановых порошков ПТМ-1 и ПТС-1 показал, что их микроструктура практически идентична. На поверхности шлифов наблюдается нерегулярная зеренная структура, которая проявляется в отдельных областях (рис. 6). Это связано с остаточной структурой зерен исходного порошка титана после спекания. Локально границы зерен имеют следы кислорода, который содержался в исходных порошках Ti. В произвольных местах встречаются крупные частицы сферической формы порядка 8–10 мкм, состав которых не определен. Их объемная доля в пористом спеченном образце С-ПТС-1 больше, чем в образце С-ПТМ-1. Можно предположить, что данные частицы являются выделениями фазы, содержащей углерод, наличие которой фиксируется данными XRD (рис. 7). В работах [25–28] частицы округлой формы идентичных размеров имели следы углерода и титана.
Рис. 6.
Нерегулярная зеренная структура спеченных образцов С-ПТС-1 (а) и С-ПТМ-1 (б): 1 – остаточная зеренная структура, 2 – области, свободные от зерен.
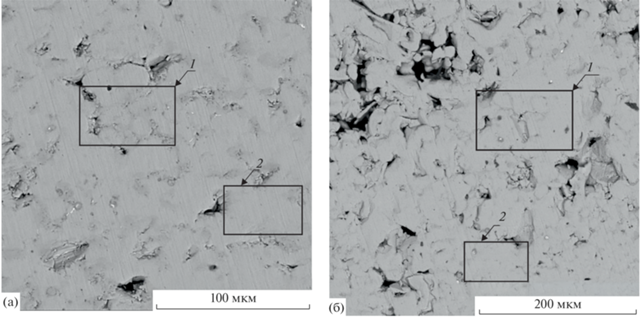
Более детальное изучение микроструктурных особенностей пористых образцов обоих типов выявило наличие крупных частиц Ti2C порядка 2–3 мкм с содержанием титана и углерода в соотношении 2 : 1 (рис. 8) [27, 28], а также светлые мелкодисперсные частицы TiC размером 0.1–0.3 мкм (табл. 2). Крупные частицы типа Ti2C могут оказывать охрупчивающее действие. Мелкодисперсные частицы, напротив, упрочняют материал за счет сохранения когерентной межфазной границы с α-Ti.
Таблица 2.
Химический состав обнаруженных частиц Ti2C и TiC в пористых образцах на основе Ti (1 и 2 на рис. 8)
Частица | Химический состав, ат. % | |
---|---|---|
C | Ti | |
Ti2C | 33.3 | 66.8 |
TiC | 47.1 | 52.9 |
Методом XRD установлено, что фазовый состав спеченных пористых сплавов может быть описан как совокупность α-Ti, TiH2, TiC (рис. 9). Фаза α-Ti является основной в структуре и имеет гексагональную плотноупакованную кристаллическую решетку с параметрами а = 2.9503 Å, с = 4.683 Å. Кристаллы фазы TiH2 имеют гранецентрированную кубическую решетку (пр. гр. Fm3m) с параметром a = 4.454 Å. Интерметаллид TiC имеет гранецентрированную кубическую решетку (пр. гр. Fm3m) с параметром a = 4.328 Å. Результаты рентгеновских исследований указывают на наличие следов частиц TiC, их объемная доля определена по стереометрической методике и составляет для С-ПТМ-1 и С-ПТС-1 около 8.5 и 4.4 об. % соответственно. Достоверно различимых рефлексов фазы Ti2C не обнаружено, поэтому их негативным влиянием можно пренебречь.
Фазовый состав сплавов обусловлен способом получения исходных порошков методом гидридно-кальциевого восстановления. Фаза TiH2 в структуре спеченных материалов является следами продукта восстановительной реакции [3, 4]
Исследование химического состава пористых образцов С-ПТМ-1 и С-ПТС-1 установило их качественное соответствие. Зафиксированы титан как основной элемент (85–87 мас. %) и примесные кислород и углерод (до 15 мас. %). Анализ карт распределения химических элементов для пористых сплавов на основе титановых порошков ПТМ-1 и ПТС-1 показывает их локализацию в структуре и подтверждает малое содержание в твердом растворе α-Ti. Такое неоднородное распределение элементов связано с ограниченным массопереносом при спекании. Кислород был зафиксирован как в твердом растворе, так и в составе отдельных фаз, которые расположены локально по границам зерен.
Для исследования деформационных и прочностных характеристик пористого спеченного титана проводились испытания на разрушение сжатием. Кривые напряжение–деформация при сжатии для образцов C-ПТМ-1 и C-ПТС-1 подобны (рис. 10а). Каждую из них можно разделить на 4 этапа деформирования. Рассмотрим более подробно данные этапы на примере диаграммы разрушения для образца C-ПТМ-1.
Рис. 10.
Кривые напряжение–деформация при сжатии: экспериментальные результаты (а) и этапы деформирования (сплошная линия – экспериментальная кривая для C-ПТМ-1, пунктирная линия – схематическая кривая сжатого пористого образца) (б).
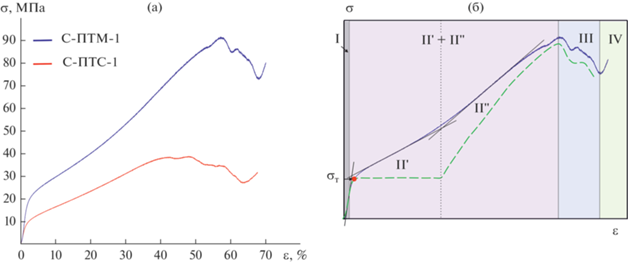
Первый этап деформирования (I) связан с линейно-упругой деформацией. На данной стадии при сжатии межпоровые перемычки пористого образца упруго изгибаются.
После достижения предела текучести (σт) деформационное поведение образца меняется и начинается второй этап, который представлен двумя стадиями: плато текучести (II') и компактной стадией (уплотнение) (II''). Наличие двух стадий и их четкое разделение характерны для типичной кривой напряжение–деформация сжатого пенометалла [29, 30]. Схематично кривая для таких материалов представлена на рис. 10б (пунктирная линия). Совмещение стадий (II' + II''), возможно, связано со скоростью нагружения в ходе эксперимента (рис. 10а). Снижение скорости, предположительно, может привести к разделению этих стадий при деформировании, которое можно выполнить графически с помощью построения касательных к кривой напряжение–деформация и определения их точки пересечения (рис. 10б).
На этапе плато (II') в процессе деформации в структуре поверхности пор образца появляются микротрещины, а исходные поры уплощаются. В этот период образец подвергается пластической деформации. На схематическом изображении кривой напряжение–деформация (пунктирная линия) этот этап характеризуется постоянством значения напряжения при возрастающей деформации. На компактной стадии (II'') образуется большое число трещин в перемычках пористого образца, которые увеличиваются и в некоторых случаях локально приводят к их разрушению и компактированию образца. С макроскопической точки зрения это является причиной искривления перемычек, но не разрушения образца в целом. Образец принимает форму “бочки”. На III этапе напряжение достигает критической величины, при которой происходит потеря устойчивости образца, что сопровождается массовым разрушением опорных перемычек. IV этап характеризуется окончательным смятием образца.
Несмотря на подобие деформационных кривых пористых образцов C-ПТМ-1 и C-ПТС-1, они имеют разные значения прочностных и деформационных характеристик, что связано с их макроструктурными и микроструктурными особенностями (табл. 3). Меньшие значения модуля Юнга (767.75 МПа), предела упругости (6.81 МПа), а также предела текучести (9.9 МПа) для сплава C-ПТС-1 в сравнении с C-ПТМ-1 связаны с большим значением пористости (72.5%) относительно C-ПТМ-1 (65%). Корреляция этих характеристик с пористостью деформируемой системы подтверждается с моделью Гибсона–Эшби [31].
Таблица 3.
Прочностные и деформационные характеристики спеченных пористых сплавов С-ПТМ-1 и С-ПТС-1
Сплав | E, МПа | σупр, МПа | σт, МПа | σв, МПа | εв, % |
---|---|---|---|---|---|
C-ПТМ-1 | 1415.71 ± 70.8 | 14.52 ± 0.7 | 20.79 ± 1.0 | 91.52 ± 4.6 | 57.17 ± 2.9 |
C-ПТС-1 | 767.75 ± 38.4 | 6.81 ± 0.7 | 9.9 ± 0.5 | 38.72 ± 1.9 | 48.07 ± 2.4 |
Модуль Юнга характеризует жесткость системы. Таким образом, мы предполагаем, что его значение должно также коррелировать с числом связей, формирующихся в процессе спекания. Для пористого сплава, синтезируемого из мелкой фракции порошка титана, таких связей будет больше, это определяет большее значение Е = 1415.71 МПа для C‑ПТМ-1. Пористость и количество связей также влияют на прочность и характеристику предела прочности σв образца. Рост пористости и количества связей приводит к повышению σв, что прослеживается в сплаве C-ПТМ-1: σв = 91.52 МПа по сравнению с σв = 38.72 МПа для C-ПТС-1 (см. табл. 3). Значение деформации при разрушении коррелирует с пределом прочности для каждого из сплавов.
Наряду с параметрами макроструктуры следует учитывать особенности микроструктуры пористых сплавов C-ПТМ-1 и C-ПТС-1, влияющие на прочностные и деформационные характеристики. Первостепенным фактором в данном случае является доля мелкодисперных частиц карбида титана (TiC) в твердом растворе α-Ti. Оценка с применением стереометрических методик показывает большую долю частиц TiC в пористом сплаве C-ПТМ-1 (8.5 об. %), как указывалось ранее.
Высокое значение всех деформационно-прочностных параметров сплава C-ПТМ-1 напрямую связано с долей мелкодисперсных частиц фазы TiC в структуре образцов. Известно, что в пересыщенном твердом растворе углерода в титане часть энергии взаимодействия между атомами основной фазы (α-Ti) тратится на взаимодействие с атомами углерода, что снижает модуль Юнга [32]. В процессе спекания (отжига) углерод, присутствующий в исходном порошке, выделяется из твердого раствора α-Ti и формируются частицы карбида титана TiC. Таким образом, количество углерода в основной фазе α-Ti снижается при образовании частиц TiC, тем самым повышая модуль Юнга. Так как доля мелкодисперсных частиц TiC в сплаве C-ПТМ-1 выше по сравнению с C-ПТС-1, следовательно, его модуль Юнга имеет большее значение (см. табл. 3).
Начало плато текучести задается точкой σт, значение которой, кроме макроструктуры, определяется наличием частиц вторичных фаз в сплаве. Область текучести характеризуется скольжением дислокаций в структуре материала [33]. Примеси и формирующиеся на их основе мелкодисперсные вторичные фазы препятствуют их однородному скольжению, повышая тем самым предел текучести. Большая доля частиц мелкодисперсной фазы TiC в образце C-ПТМ-1 по сравнению с C-ПТС-1 говорит о большем искажении решетки основной фазы. Чем больше искажена решетка, тем более высокие напряжения требуются для движения дислокаций. Это является причиной повышения предела текучести сплава C-ПТМ-1 в два раза по сравнению с C-ПТС-1: 20.79 и 9.9 МПа соответственно. Большее упрочнение частицами вторичных фаз сплава C-ПТМ-1 также объясняет бóльшую величину предела прочности σв относительно сплава C-ПТС-1.
ЗАКЛЮЧЕНИЕ
Показано влияние различного состояния исходных порошков ПТМ-1 и ПТС-1 на структурные особенности и деформационно-прочностные характеристики пористых материалов на их основе, полученных методом спекания. Исследованы гранулометрический состав, морфология частиц, химический состав порошков. Установлено, что химический состав порошков ПТМ-1 и ПТС-1 качественно идентичен. Определены количественные характеристики порового пространства спеченных образцов. Пористость материала C-ПТМ-1 составляет 65%, C-ПТС-1 – 72.5%. Установлено, что поровое пространство образцов С-ПТМ-1 имеет более однородное строение поровых каналов. Методом XRD установлено, что фазовый состав пористых сплавов, полученных методом диффузионного спекания порошка Ti, может быть описан как совокупность фаз α-Ti, TiH2, TiC.
На основе исследования деформационных и прочностных характеристик пористого спеченного титана сжатием до разрушения выделены четыре этапа деформирования. Показано, что уменьшение пористости и дисперсное упрочнение частицами фазы TiC в материале C-ПТМ-1 приводит к повышению предела прочности и деформации разрушения.
Список литературы
Jackson M.J., Kopac J., Balazic M., Bombac D., Brojan M., Kosel F. Titanium and Titanium Alloy Applications in Medicine // Surg. Tools Med. Devices. 2016. P. 475–517. https://doi.org/10.1007/978-3-319-33489-9_15
Ik-Hyun O., Haruhiko S., Naoyuki N., Shuji H. Microstructures and Mechanical Properties of Porosity-Graded Pure Titanium Compacts // Mater. Trans. 2003. V. 44. № 4. P. 657–660. https://doi.org/10.2320/matertrans.44.657
Zschommler Sandim H.R., Morante B.V., Suzuki P.A. Kinetics of Thermal Decomposition of Titanium Hydride Powder Using in situ High-Temperature X-ray Diffraction (HTXRD) // J. Mater. Res. 2005. V. 8. № 3. P. 293–297. https://doi.org/10.1590/S1516-14392005000300012
In-Shup A., Tek-Kyoung S., Sung-Yeal B., Ho-Jung C., Dong-Kyu P. Synthesis of Titanium Carbide by Thermo-Chemical Methods with TiH2 and Carbon Black Powders // Met. Materials Int. 2006. V. 12. № 3. P. 249–253. https://doi.org/10.1007/BF03027539
Vasconcellos L.-M.-R., Leite D.-de O., Nascimento F.-O., de Vasconcellos L. G.-O., etc. Porous Titanium for Biomedical Applications: An Experimental Study on Rabbits // Med. Oral, Patol. Oral Cirygia Bucal. 2010. V. 15. № 2. P. 407–412. https://doi.org/10.4317/medoral.15.e407
Frykholm R., Brash B. Press and Sintering of Titanium // Key Eng. Mater. 2015. P. 1–11. doi: 10.4028/www.scientific.net/KEM.704.369
Krinitcyn M.G., Pribytkov G.A., Korosteleva E.N. Structure of Sintered Ti – TiC Materials // Appl. Mech. Mater. 2014. V. 682. P. 127–131. https://doi.org/10.4028/www.scientific.net/AMM.682.127
Назаренко В.А. Материалы на основе титана, полученные методами порошковой металлургии // Вестн. донбасской машинообувной технологии. 2010. Т. 2. № 19. С. 203–207.
Stráský J., Kozlík J., Bartha K., Preisler D., Chráska T. Sintering of Ti-Based Biomedical Alloys with Increased Oxygen Content from Elemental Powders // The 14th World Conference on Titanium. MATEC Web of Conferences 321. 2020. 05010. https://doi.org/10.1051/matecconf/202032105010
Milenov T., Terziyska P., Avdeev G. et al. Structure and Phase Composition Study of Heavy Doped with Carbon Thin Films of TiO2: C Deposited by RF Magnetron Sputtering // Russ. J. Inorg. Chem. 2022. V. 67. P. 1509–1520. https://doi.org/10.1134/S0036023622100333
Kamynina O.K., Kravchuk K.S., Lazov M.A. et al. Effect of Surface Roughness on the Properties of Titanium Materials for Bone Implants // Russ. J. Inorg. Chem. 2021. V. 61. P. 1073–1078. https://doi.org/10.1134/S0036023621080106
Pease L.F. III, West W.G. Fundamentals of Powder Metallurgy: Metal Powder Industries Federation, 2002. 452 p. https://doi.org/10.2298/SOS0401054P
Zhao Q., Bolzoni L., Chen Y., Xu Y., Torrens R., Yang F. Processing of Metastable Beta Titanium Alloy: Comprehensive Study on Deformation Behavior and Exceptional Microstructure Variation Mechanisms // J. Mater. Sci. Technol. 2022. V. 126. P. 22–43. https://doi.org/10.1016/j.jmst.2022.02.050
Шаповалова О.М., Бабенко Е.П. Исследование структуры и свойств кристаллов рафинированного титана повышенной частоты при нагреве // Вестн. двигателестроения. 2009. № 1. С. 134–138.
Шаповалова О.М., Бабенко Е.П. Система исследования порошковых материалов // Проблемы cовременного материаловедения. 2001. С. 33–34.
Кисеев В.М., Непомнящий А.С. Способ получения пористого титана. RU 2407817 C2, 2010.
Krishna E.S., Suresh G. Bioactive Titanium-Hydroxyapatite Composites by Powder Metallurgy Route // Biointerface Res. Appl. Chem. 2022. V. 12. № 4. P. 5375–5383. https://doi.org/10.33263/BRIAC124.53755383
Сенкевич К.С. Способ получения пористых изделий из быстрозакаленных порошков титана и его сплавов. RU 2641592 C2, 2018.
Vander Voort G. Metallographic Preparation of Titanium and its Alloys // Solutions Mater. Prep., Test. Anal. 2014. V. 3. № 3. P. 828–834.
Froes F.H., Mashl S.J., Moxson V.S., Hebeisen J.C., Duz V.A. The Technologies of Titanium Powder Metallurgy // J. Minerals. 2004. V. 56. P. 46–48.
Robertson I.M., Schaffer G.B. Comparison of Sintering of Titanium and Titanium Hydride Powders // Powder Metall. 2010. V. 53. № 1. P. 12–19. https://doi.org/10.1179/003258909X12450768327063
Blaine D.C., Heleon H.B., Laubscher H.H. Process Models for Press-and-Sinter Titanium // Adv. Mater. Res. 2014. V. 1019. P. 231–240. doi: 10.4028/www.scientific.net/AMR.1019.231
Sun P., Fang Z.Z., Zhang Y., Xia Y. Review of the Methods for Production of Spherical Ti and Ti Alloy Powder // JOM. 2017. V. 15. P. 1853–1860. https://doi.org/10.1007/s11837-017-2513-5
Whittaker D. Powder Processing, Consolidation and Metallurgy of Titanium // Powder Metall. 2012. V. 55. № 1. P. 6–10. https://doi.org/10.1179/174329012X13297486041231
Lei Ch., Du Y., Zhu M., Huo W., Wu H., Zhang Y. Microstructure and Mechanical Properties of in situ TiC/Ti Composites with a Laminated Structure Synthesized by Spark Plasma Sintering // Mater. Sci. Eng., A. 2021. V. 812. P. 141136. https://doi.org/10.1016/j.msea.2021.141136
Шляпин С.Д., Серов М.М., Гусев Д.Е., Федорова Л.В. Получение, структура и свойства пористых материалов из титановых волокон и проволоки // Изв. вузов. Порошковая металлургия и функциональные покрытия. 2016. T. 4. С. 76–85. https://doi.org/10.17073/1997-308X-2016-4-76-85
Gonçalves V.R.M., Çaha I., Alves A.C., Toptan F., Rocha L.A. Improved Tribocorrosion Behavior Obtained by in-situ Precipitation of Ti2C in Ti–Nb Alloy // Metals. 2022. V. 12. P. 2–17. https://doi.org/10.3390/met12060908
Priti W., Drew R., Root J., Yue S. Evidence for Stable Stoichiometric Ti2C at the Interface in TiC Particulate Reinforced Ti Alloy Compounsites // Acta Mater. 2020. V. 48. № 7. P. 1443–1450. https://doi.org/10.1016/S1359-6454(99)00453-X
Zhang C., Zhang L., Liu L., Linwei Lv., Gao L., Liu N., Wang X., Ye J. Mechanical Behavior of a Titanium Alloy Scaffold Mimicking Trabecular Structure // J. Orthop. Surg. Res. 2020. V. 15. № 40. P. 1–11. https://doi.org/10.1186/s13018-019-1489-y
Li B.Q., Wang C.Y., Lua X. Effect of Pore Structure on the Compressive Property of Porous Ti Produced by Powder Metallurgy Technique // Mater. Des. 2013. V. 50. P. 613–619. https://doi.org/10.1016/j.matdes.2013.02.082
Chai H.W., Xie Z.L., Feng Z.D., Luo S.N., Huang J.Y. Three-Dimensional Deformation Dynamics of Porous Titanium under Uniaxial Compression // Mater. Charact. 2021. V. 182. 111494. https://doi.org/10.1016/j.matchar.2021.111494
Симонов Ю.Н., Георгиев М.Н., Симонов М.Ю. Основы физики и механики разрушения. Пермь: Изд-во Перм. нац. исслед. политехн. ун-та, 2012. 203 с.
Hull D., Bacon D.J. Introduction to Dislocations. Amsterdam: Elsevier, 2011. P. 272.
Дополнительные материалы отсутствуют.
Инструменты
Неорганические материалы