Неорганические материалы, 2023, T. 59, № 4, стр. 451-467
Микроструктура и ударная вязкость игольчатого феррита в сварных соединениях низколегированной стали по результатам множественных испытаний на ударный изгиб
М. М. Кантор 1, В. В. Судьин 1, *, В. А. Боженов 1, К. А. Солнцев 1
1 Институт металлургии и материаловедения им. А.А. Байкова
Российской академии наук
119991 Москва, Ленинский пр., 49, Россия
* E-mail: vsudyin@imet.ac.ru
Поступила в редакцию 09.01.2023
После доработки 28.02.2023
Принята к публикации 01.03.2023
- EDN: GLTAYG
- DOI: 10.31857/S0002337X23040024
Аннотация
Путем анализа результатов испытания на ударный изгиб большого количества образцов исследовано разрушение металла сварного шва, преимущественно состоящего из игольчатого феррита. Исследованный металл обладает очень широким интервалом вязко-хрупкого перехода, начинающимся при +20 и заканчивающимся ниже –60°C. В пределах исследованных температур наблюдаются 3 стабильных уровня ударной вязкости, переходы между которыми с понижением температуры определяют рассеяние работы разрушения образцов. Фрактографически вязко-хрупкий переход осуществляется за счет однократного изменения с вязкого механизма разрушения на скол. Зарождение трещин скола происходит на крупных зернах игольчатого феррита, различное взаиморасположение которых в очаге скола определяет уровень ударной вязкости образца. Путем сопоставления динамических кривых разрушения и макростроения излома показано, что трещины скола зарождаются в вершине стабильно растущей вязкой трещины. При этом на изломах можно выделить отдельные события скола, наблюдаемые на динамической кривой.
ВВЕДЕНИЕ
В сварных соединениях низколегированных сталей возможно образование нескольких составляющих микроструктуры. Важнейшими из них являются различные модификации феррита и неметаллические включения [1]. Предпочтительной составляющей рассматривается игольчатый феррит (ИФ), само существование которого впервые было установлено именно в металле сварных соединений. Было показано, что трещина в ИФ возникает позже, чем в других структурных составляющих [2, 3]. Экспериментально установлено повышение ударной вязкости сварных соединений при увеличении в них объемной доли ИФ [4–10]. Образование ИФ протекает с низкой скоростью диффузии железа, и в некоторых работах ИФ рассматривается как вид бейнита [3]. Однако образование карбидов на границах зерен ИФ говорит о достаточно высокой скорости диффузии углерода [11, 12]. Особенностями ИФ являются малый размер и вытянутая форма зерна.
Согласно современным представлениям, обобщенным в ряде обзоров [3, 13, 14], образуется ИФ следующим образом: в процессе гамма–альфа-превращения в результате специфических условий на поверхности внутризеренных неметаллических включений подходящего типа образуются зародыши ИФ. Большое количество неметаллических включений в сварном шве приводит к одновременному образованию множества зародышей. Вследствие этого внутри зерна исходного аустенита возникает множество зерен ИФ, размер которых лимитируется пространством для роста, ограниченным соседними зародышами и границами аустенитного зерна. Одновременно происходит процесс формирования феррита на границах зерен исходного аустенита, в результате которого образуются крупные зерна зернограничного феррита. Конкуренция между процессами образования ферритных фаз внутри или по границам аустенитных зерен во многом определяет микроструктуру и свойства получаемого сварного соединения.
Особенности разрушения металла сварных швов, содержащих ИФ, также связаны со взаимодействием между неметаллическими включениями, крупнозернистыми структурными составляющими и ИФ. Деформация, возникающая на ранних этапах деформирования образца, неравномерна [2]. Более прочный ИФ [15] деформационно упрочняется после того, как произойдет упрочнение менее прочного зернограничного феррита. Хрупкие неметаллические включения, находящиеся в деформирующихся зернах, разрушаются с образованием микроскопических трещин скола [2]. Последующий переход трещины скола в ферритное зерно может являться критическим событием [2, 16 ], после которого наступает макроскопическое хрупкое разрушение.
Склонность к хрупкому разрушению оценивают по температурам перехода от вязкого разрушения к хрупкому. Температуру такого перехода можно оценить по повышенному рассеянию значений ударной вязкости, уровню ударной вязкости, соотношению вязкой и хрупкой составляющих излома. На основе изучения рассеяния ударной вязкости показано очень неравномерное распределение ударной вязкости и пластичности в основном металле [17]. Также показана микроструктурная природа неравномерного распределения вязкости в околошовной зоне [18]. Очаги скола, ассоциированные с неметаллическими включениями, описаны почти во всех работах, где обсуждается фрактография разрушения сварных швов [2, 16, 19–25]. Напряжение скола, измеренное в испытаниях на трещиностойкость, тем меньше, чем больше размер неметаллического включения в фокусе очага скола [16, 21, 24]. Это наблюдение согласуется с тем, что на крупных включениях трещины зарождаются с большей вероятностью [20]. Аналогичным образом напряжение скола связано с размером очаговой фасетки [19]. В целом такое поведение согласуется с представлениями о зависимости между напряжением скола и размером ячейки разрушения, определяемым границами свободного движения дислокаций (1). В случае исследованного металла в роли такой ячейки может выступать неметаллическое включение или ферритное зерно [26]:
(1)
$\sigma = \sqrt {\frac{{E\gamma }}{{\pi \left( {1 - {{\vartheta }^{2}}} \right)d}}} {\kern 1pt} ,$Возможность остановки трещины скола, возникшей в зернограничном феррите, во многом определяется локальной микроструктурой окружения этого зерна. Так, в ряде работ отмечено образование отдельных фасеток скола в области стабильного роста первоначальной вязкой трещины [23, 24] и очаговых фасеток скола в области хрупкого излома, со всех сторон окруженных гребнями вязкого ямочного излома [19].
После возникновения трещины ее распространение в основном проходит по цепи зерен зернограничного феррита [2, 27], что свидетельствует о более высокой сопротивляемости ИФ распространению трещин скола. При этом, в некоторых работах отмечается, что оставшиеся после роста трещин скола участки ИФ могут разрушаться вязко [2, 28]. Повышенную сопротивляемость ИФ сколу обычно связывают с малым размером зерна и высокой разориентацией между соседними зернами, обусловленной ориентационными соотношениями γ–α-превращения [29].
Обычно помимо ИФ микроструктура сварного соединения содержит другие структурные составляющие на основе α-Fe. Это обстоятельство затрудняет понимание свойств ИФ, в т. ч. в переходном интервале.
Важнейшим свойством любого материала на основе α-Fe, в т. ч. ИФ, является склонность к хрупкому разрушению, определяемая особенностями температурного интервала вязко-хрупкого перехода. Температурный интервал перехода ИФ изучен недостаточно из-за того, что в объектах экспериментальных исследований всегда присутствовало большое количество других ферритов. Известно влияние размера зерен феррита на ударную вязкость. В работе [30] экспериментально установлено, что при измельчении зерен феррита вплоть до 1 мкм температурный интервал перехода от вязкого к хрупкому состоянию смещается в область низких температур, а также увеличиваются абсолютные значения работы разрушения как на верхней, так и на нижней полках.
В последнее время были развиты представления о том, что поведение ферритно-перлитных сталей в переходном интервале зависит не только от размеров и природы элементов микроструктуры, но также и от соотношения более хрупкой и более пластичной структурных составляющих. В низколегированных сталях, содержащих достаточное количество перлита, наблюдали двухстадийную картину вязко-хрупкого перехода [31]. Представления о двухстадийном переходе и ранее связывали с двухстадийностью изменения механизма разрушения [32].
Показано, что даже в основном металле вязкость и пластичность распределены неравномерно [17]. Это обстоятельство не учитывается в большинстве исследований, хотя такая неравномерность может приводить к неоднозначности фрактографических наблюдений, которые справедливы только для индивидуальных пар “измеренное значение ударной вязкости–морфология излома”. В настоящей работе были проведены множественные испытания образцов сварного соединения низколегированной стали, микроструктура которого состояла преимущественно из ИФ.
Целью данной работы являлось количественное изучение микроструктуры сварного соединения с преобладанием ИФ, определение интервала вязко-хрупкого перехода для полученной микроструктуры и их связи с поведением ИФ в переходном интервале.
ЭКСПЕРИМЕНТАЛЬНАЯ ЧАСТЬ
Для исследования были использованы сварные соединения листов стали 09Г2С после закалки с отпуском. Двухстороннее стыковое сварное соединение пластин стального проката толщиной 14 и длиной 1500 мм выполнялось в вертикальном положении.
Сварка всех слоев шва (корневого, заполняющих, облицовочных, шва с обратной стороны стыка) производилась с подогревом кромок методом механизированной сварки порошковой проволокой в смеси аргона и углекислого газа.
Концентрации углерода и серы измеряли методом инфракрасной спектроскопии по количеству газообразных CO2 и SO2, выделившихся при окислительном плавлении в керамическом тигле в индукционной печи с плавнем на анализаторе Leco CS-600.
Концентрации химических элементов, кроме углерода, определяли при помощи атомно-эмиссионного спектрометра тлеющего разряда Leco GDS-850A. Составы металла сварного шва и основного металла представлены в табл. 1.
Таблица 1.
Составы металла сварного шва и основного металла
Образец | Содержание элементов, мас. % | |||||||||||
---|---|---|---|---|---|---|---|---|---|---|---|---|
Si | Mn | Ni | P | Cu | Cr | Al | C | Ti | Nb | S | Zr | |
Сварной шов | 0.481 | 1.507 | 0.258 | 0.010 | 0.083 | 0.040 | 0.017 | 0.061 | 0.030 | 0.014 | 0.0048 | 0.013 |
Основной металл | 0.587 | 1.543 | 0.059 | 0.010 | 0.111 | 0.044 | 0.038 | 0.104 | 0.006 | 0.010 | 0.0017 | 0.014 |
Примечание. Остальное железо. |
Макроструктура полученного сварного соединения представлена на рис. 1. Наблюдается несколько слоев сварного шва, причем их ширина увеличивается от корневого к облицовочным.
Средние значения механических свойства основного металла и металла сварного шва, определенные по результатам испытания трех образцов, представлены в табл. 2.
Таблица 2.
Сравнение механических свойств при статическом растяжении сварного шва и основного металла
Образец | σв, МПа | σ0.2, MПa | δ, % | ψ, % |
---|---|---|---|---|
Сварной шов | 561 ± 4 | 425 ± 7 | 18 ± 1 | 80 ± 2 |
Основной металл | 561 ± 6 | 456 ± 6 | 23 ± 2 | 80 ± 2 |
Для испытаний на ударный изгиб были использованы стандартные образцы размером 10 × × 10 × 55 мм с V-образным надрезом, изготовленные по ГОСТ 9454-78. Образцы были вырезаны перпендикулярно сварному шву. Надрез наносился по оси шва перпендикулярно толщине листа.
Испытания на ударный изгиб были проведены на инструментированном маятниковом копре Roell Amsler RKP-450 (Zwick/Roell). Энергия маятника копра составляла 450 Дж, скорость – маятника 5.24 м/с. Множественные испытания проводились при температурах –60, –40, –20, 0, и +20°C по 15 образцов на температуру. При этом руководствовались требованиями к испытаниям при минимальной температуре, возможной при строительстве и эксплуатации конструкции из низколегированной стали в арктических условиях [33]. Для каждого образца была записана динамическая кривая разрушения в координатах усилие–прогиб образца.
Для образцов, испытанных на ударный изгиб, были получены изображения изломов с помощью макрофотографической станции на основе Canon (EOS 6D + Macro Photo Lens MP-E 65mm). На изображениях были выделены области вязкого и хрупкого разрушения и рассчитана доля вязкой составляющей как отношение площади вязкой части излома ко всей площади излома. При этом вязкий излом не разделялся на область под надрезом, боковые крылья и долом, а измерялась его суммарная площадь. Для всех образцов по цифровым снимкам было измерено расстояние между вершиной надреза и началом участка хрупкой трещины.
Поверхности разрушения образцов исследовали с использованием двухлучевой системы CrossBeam 1540 EsB (Carl Zeiss) при ускоряющем напряжении 15 кВ. Определение очагов зарождения скола проводили, анализируя направления распространения разрушения по виду речного узора на фасетках. Для установления состава неметаллических включений, обнаруживаемых на изломе, использовали приставку для рентгеноспектрального микроанализа Inca X-Act (Oxford Instruments) с комплексом программного обеспечения Aztec (Oxford Instruments). Для ориентационного картирования методом дифракции отраженных электронов (ДОЭ) использовали приставку Nordlyss S (Oxford Instruments). Первичную обработку дифракционных данных проводили с использованием комплекса программного обеспечения HKL Channel 5 (Oxford Instruments).
РЕЗУЛЬТАТЫ ЭКСПЕРИМЕНТА
С точки зрения микроструктуры сварной шов можно разделить на несколько областей, относящихся либо к первично закристаллизованному металлу, либо к металлу, подвергшемуся после первичной кристаллизации нагреву от наложения последующих проходов шва.
Область первичной кристаллизации металла сварного шва преимущественно состоит из игольчатого феррита (рис. 2) с вкраплениями отдельных зерен зернограничного феррита.
Рис. 2.
Микроструктура области первичной кристаллизации сварного шва (стрелками отмечены отдельные зерна зернограничного феррита).
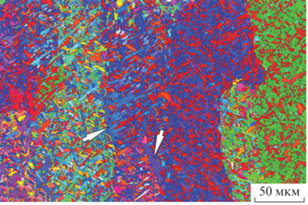
Поскольку картирование методом ДОЭ дает информацию непосредственно о каждом отдельном зерне, для более информативной характеризации микроструктуры определяли средневзвешенный по площади размер зерна. Для этого каждому зерну присваивался вес, равный его площади, и среднее значение определялось по следующей формуле:
Рис. 3.
Распределение средневзвешенного по площади размера зерна для всех областей сварного шва (серое) и для области, состоящей только из игольчатого феррита (красное).
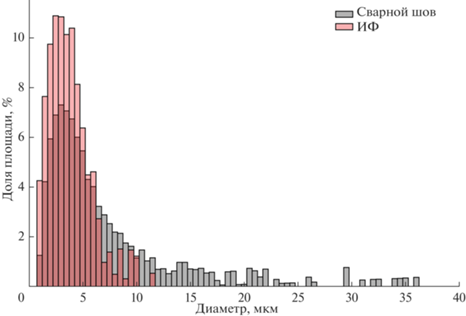
Микроструктура сварного шва неоднородна, и в первично закристаллизованном металле присутствуют области, содержащие отдельные крупные зерна зернограничного феррита. В областях, состоящих только из ИФ, модальный размер составляет 2.9 мкм, медианный – 3.4 мкм, при этом практически отсутствуют зерна с эквивалентным диаметром более 10 мкм. Таким образом, по данным ДОЭ, диапазон размеров зерен зернограничного феррита составляет 10–40 мкм.
Распределение разориентации границ зерен отличается от случайного. В нем преобладают границы с углом разориентации менее 20° и более 45° (рис. 4а). При этом распределение таких границ в микроструктуре случайно, без явных кластеров (рис. 4б).
Рис. 4.
Распределение углов разориентации кристаллитов для всех областей сварного шва (а) и карта разориентации границ кристаллитов (синим цветом обозначены границы с углом разориентации более 10°, черным – более 20°, красным – более 35°) (б).
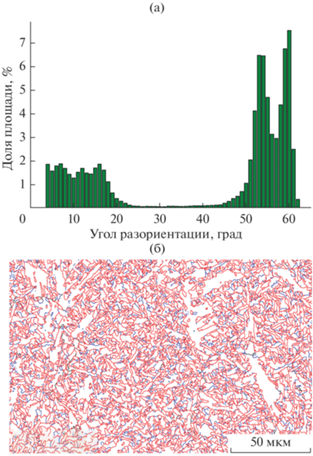
Распределение соотношения осей эквивалентных элипсов (СОЭЭ) указывает на вытянутость зерен. Так, 50% зерен имеют СОЭЭ более 2.3. Это соответствует наблюдаемой форме зерен как ИФ, так и зернограничного феррита.
В области первичной кристаллизации встречаются отдельные образования зернограничного феррита. Эти образования имеют вытянутую форму, при этом непрерывная сетка зернограничного феррита по всему сварному шву не образуется (рис. 5).
Рис. 5.
Формы присутствия зернограничного феррита в исследованном сварном шве: а – оптическая микроскопия, б – растровая электронная микроскопия, в – ориентационное картирование.
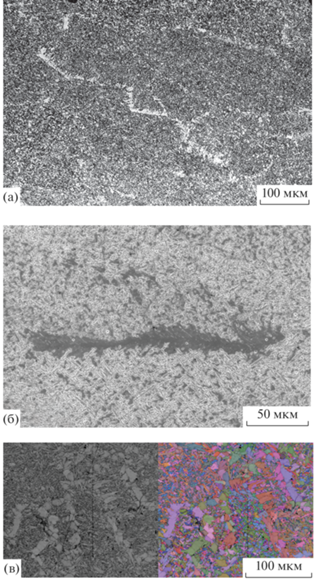
В зоне термического воздействия последующих проходов сварки на металл первичной кристаллизации наблюдается образование тонких полос частично полигонизированного феррита (рис. 6).
Неметаллические включения сварного шва имеют округлую форму и состоят преимущественно из силиката марганца с крупными выделениями оксида титана.
На рис. 7 представлено распределение значений ударной вязкости при температурах от –60 до +20°C на скрипичной диаграмме. Ширина закрашенной области на графике соответствует плотности вероятности нахождения значения ударной вязкости на соответствующем уровне, вычисленной по методу, изложенному в [34] при помощи библиотеки методов SciPy языка программирования Python, точками обозначены экспериментально определенные значения. В совокупной выборке можно провести верхнюю и нижнюю огибающие, проходящие соответственно через верхний и нижний уровни ударной вязкости. Верхний уровень при температуре испытания +20°C совпадает с верхней полкой – 100% вязкого разрушения – и соответствует вязкости 250 Дж/см2. Нижний уровень составляет 90 при +20 и 25 Дж/см2 при –60°C.
Рис. 7.
Сериальная кривая испытаний на ударный изгиб металла сварного шва в виде скрипичных диаграмм.
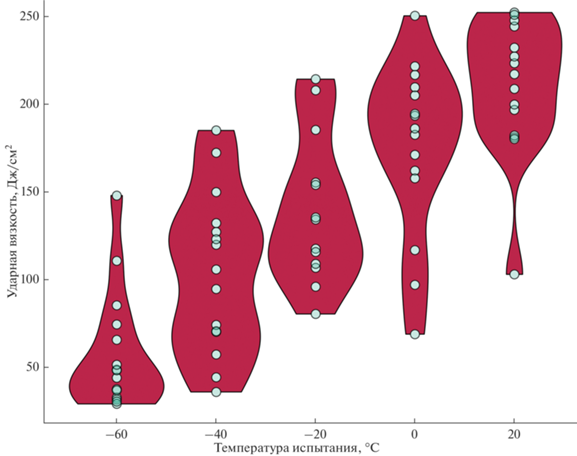
Факт уменьшения максимальных значений при понижении температуры позволяет утверждать, что с понижением температуры испытаний ударная вязкость понижается. Однако, несмотря на то что в данном исследовании изучали микроструктуру, преимущественно состоящую только из одной структурной составляющей, имеет место значительное рассеяние результатов измерений, что является важной особенностью переходного интервала. Размах рассеяния составляет порядка 120 Дж/см2 при всех температурах испытания. Рассеяние величин ударной вязкости является важным признаком переходного интервала хладноломкости и результатом неравномерного распределения вязкости в микроструктуре [17].
Фрактографическое исследование изломов показало, что при температуре +20°C часть образцов разрушается с образованием излома, на 20% состоящего из фасеток скола, что говорит о не полном переходе к вязкому разрушению. С понижением температуры доля вязкого излома снижается, доходя до 40% при –60°C (рис. 8).
Таким образом, переход от вязкого разрушения к хрупкому, по результатам измерения ударной вязкости, исходя из рассеяния ее величин начинается при температуре +20°C. Ориентируясь на появление в изломах областей фасеток скола, составляющих до 20% площади поверхности, также можно утверждать, что переход от вязкого к хрупкому разрушению происходит уже при +20°C. Высокое рассеяние значений ударной вязкости при температуре –60°C и доля вязкого излома около 40% говорят о том, что переход от вязкого разрушения к хрупкому заканчивается при температуре ниже –60°C и при дальнейшем снижении температуры испытания следует ожидать более низких значений ударной вязкости. Известно, что значения температуры перехода, определенные по ударной вязкости и по соотношению хрупко-вязкой составляющей в изломах, могут не совпадать [35]. Учитывая неопределенность экспериментальной оценки температуры перехода от вязкого разрушения к хрупкому, ее величину рассматривают как условную и являющуюся предметом соглашения [36–38]. Принимая во внимание, что в данном случае важно расположение температурного интервала испытаний относительно температуры перехода, считаем эту температуру большей или равной +20°C. Иными словами считаем, что температуры испытаний от –60 до +20°C лежат внутри переходного интервала.
При микрофрактографическом анализе изломов мы считаем признаком хрупкого разрушения наблюдение фасеток скола, а признаком вязкого разрушения наблюдение ямок. При этом скол определяли по образованию плоских участков излома с характерными линиями речного узора. Гребни рассматриваем как деформационную особенность транскристаллитного распространения трещин скола, обусловленную несовпадением плоскостей скола в соседних зернах [28, 39].
Строение поверхности хрупкого разрушения изученных образцов различается в зависимости от структурной составляющей, через которую распространялась трещина.
В ИФ из-за малого размера зерна размер гребней вязкого излома, образующихся между фасетками, близок к размеру самих фасеток. Фрактографически картина разрушения такой микроструктуры выглядит как хаотично расположенные области с речным узором, разделенные гребнями и областями вязкого ямочного излома так, что суммарно плоские участки составляют менее 30% занимаемой площади (рис. 9). Исследование сечений изломов вблизи поверхности разрушения показало, что в отличие от фасеток скола в полигональном феррите области пластической деформации не локализованы вблизи границ зерен, а образуют непрерывную пластическую зону под изломом глубиной порядка 15 мкм (рис. 10). Такую деформацию некоторые авторы связывают с разрушением по механизму квазискола [31]. При этом наблюдаемые деформационные особенности появляются уже после образования фасеток [39], механизм формирования которых можно охарактеризовать как транскристаллитный скол по кристаллографическим плоскостям на основе наблюдения линий речного узора на таких фасетках. Также определенная деформация зерен создается при макроскопическом изменении формы образца. Наличие деформации под поверхностью фасеток, обусловленной макроскопическим изгибом, также не может указывать на их образование по механизму квазискола.
Рис. 10.
Ориентационная карта области вблизи поверхности разрушения ИФ: cлева – цветовая кодировка ориентации кристаллитов в координатах обратных полюсных фигур, справа – цветовая кодировка локальной разориентации.
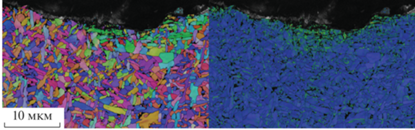
При прохождении трещины через отдельное зерно зернограничного феррита образуется крупная фасетка, окруженная областью разрушенного ИФ (рис. 11).
Рис. 11.
Характерный вид поверхности хрупкого излома единичного зерна зернограничного феррита, окруженного ИФ.
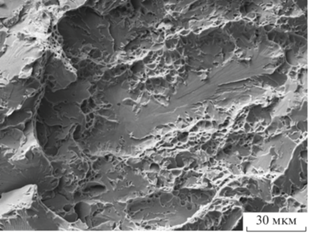
Распространение трещины скола через полигонизированную микроструктуру, образованную при термическом воздействии повторных проходов сварки на микроструктуру ИФ, приводит к образованию излома, состоящего из отдельных хорошо разделимых фасеток размером порядка 5–10 мкм (рис. 12).
Различия между микроскопическим строением отдельных фасеток, образовавшихся при различных температурах, не наблюдали. При всех температурах фасетки обладают речным узором, что позволяет охарактеризовать механизм их разрушения как скол. Также изменение температуры испытания не приводит к изменению вида гребней вязкого излома между фасетками.
Для изученных изломов характерно образование большого количества очагов зарождения скола – десятки на излом. Характерный очаг скола сварного шва имеет вид фасетки с речным узором, расходящимся от ее центра к краям во все стороны с неметаллическим включением в точке пересечения линий речного узора. Такие неметаллические включения представляют собой оксид титана в смеси с алюмосиликатом марганца (рис. 13), они обычно расколоты – части включения наблюдаются на обеих ответных половинах образца.
Фасетки, составляющие очаги скола, расположенные в области макроскопического хрупкого излома, обычно крупнее окружающих фасеток (рис. 14).
Характерной особенностью является появление отдельных фасеток скола или областей, состоящих из нескольких объединенных фасеток, внутри вязкого излома некоторых образцов, не образующих заметных оптическими методами участков макроскопического хрупкого излома (рис. 15).
Размер таких микроскопических областей скола зависит от температуры испытания. С повышением температуры их размер увеличивается. Если при температуре испытания –60°C наблюдаются лишь одиночные фасетки диаметром 10–50 мкм, то при +20°C в областях вязкого разрушения могут быть обнаружены участки скола, объединяющие 10–20 фасеток со средним суммарным размером порядка 200 мкм (рис. 16).
Рис. 16.
Отдельные фасетки скола в области вязкого излома при различных температурах испытания: –60 (а), +20°C (б).
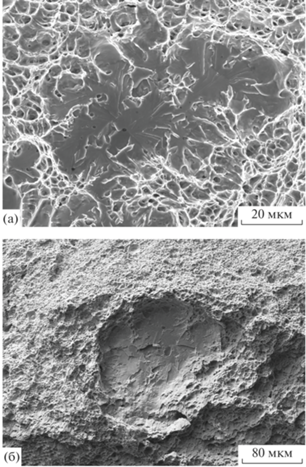
Линии речного узора в таких фасетках, расположенных среди вязкого излома, сходятся на неметаллических включениях, в которых зарождались трещины скола, перешедшие в ближайшие зерна феррита.
При этом исследование сечений, проходящих через отдельные фасетки в области вязкого излома, показало, что такие фасетки образуются в отдельных крупных зернах зернограничного феррита, окруженных мелкозернистым ИФ (рис. 17).
Образование отдельных фасеток в области первоначальной вязкой трещины может рассматриваться как элементарный акт зарождения и остановки трещины скола. При этом разрушение образцов сопровождается чередованием таких стадий зарождения и остановки трещины и на макроскопическом уровне.
На динамической кривой информация о распространении трещины скола представлена вертикальной ступенькой, абсцисса которой характеризует положение бойка в момент возникновения и остановки трещины скола (или прогиб образца). Положение верхней точки ступеньки показывает усилие, приложенное к образцу в момент возникновения трещины скола, а положение нижней точки ступеньки – усилие, приложенное к образцу в момент остановки трещины скола. Разность между этими значениями в первом приближении характеризует уменьшение рабочего сечения образца.
На рис. 18а, 18в представлены динамические кривые разрушения, на которых отмечено несколько последовательных резких спадов усилия, отделенных друг от друга участками стабильного снижения нагрузки. С использованием цифровых снимков была построена зависимость расстояния между надрезом и ближайшей точкой области скола от прогиба образца в момент образования первой ступеньки спада усилия. Построенная зависимость приведена на рис. 19. Высокая корреляция измеренных величин подтверждает, что ступеньки связаны именно с образованием участков трещин скола, а также что трещина скола зарождается в непосредственной близости от границы фронта растущей вязкой трещины, что соотносится с фрактографическими наблюдениями. При этом один участок скола, окруженный вязким изломом, образует одну ступеньку. С использованием построенной кривой на изломах образцов, разрушение которых сопровождалось образованием нескольких ступенек на динамической кривой, были отмечены точки предполагаемой остановки и зарождения новых участков макроскопического хрупкого излома (рис. 18б, 18г).
Рис. 18.
Динамические кривые (а, в) и изображения изломов с отмеченными точками скола (б, г): а, б – образец, разрушенный при –20, в, г – при –40°C.
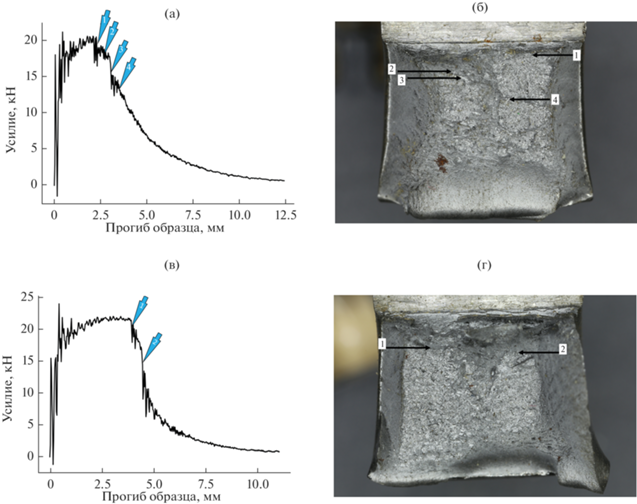
Примечательно, что на изображениях изломов предсказанные расстояния от надреза до области хрупкого излома совпадают с реальными для второго и последующих повторных зарождений трещины скола. При этом наблюдаются как циклы зарождения-остановки при росте трещины в одном направлении, так и независимое зарождение трещин скола в разных частях образца в разные моменты времени с последующей их остановкой.
На полученных динамических кривых при этом наблюдается протяженная область плавного снижения усилия после нескольких или одного скачкообразного падения. Измерение отношения работы, затраченной до образования первой трещины скола, к общей работе разрушения показывает, что вязкий долом составляет в среднем 40% от общей энергии разрушения образца сварного соединения.
Исследование образцов методом микрофрактографии и анализ динамических кривых дают представление о разрушении в разных масштабах. На динамических кривых не отражаются отдельные события скола, которые можно наблюдать на поверхности разрушения при помощи РЭМ, т. к. они приводят к слишком маленькому изменению сечения образца.
ОБСУЖДЕНИЕ РЕЗУЛЬТАТОВ
Из рассмотрения отдельных результатов измерения при одной и той же температуре испытания можно прийти к заключению о существовании трех уровней вязкости. При температурах от +20 до –20°C наблюдается переход от верхнего уровня к промежуточному, сопровождающийся рассеянием значений между этими двумя уровнями (250–125 Дж/см2). При температурах от –20 до –60°C наблюдается переход от промежуточного уровня к нижнему (125–30 Дж/см2), также сопровождающийся рассеянием. Рассеяние величин ударной вязкости при одной и той же температуре испытаний является следствием локальной неоднородности пластической деформации. Примечательной чертой промежуточного уровня являются одинаковые величины вязкости. Уровень вязкости от 90 до 120 Дж/см2 можно наблюдать при всех температурах испытаний от –60 до 0°C. Верхний уровень вязкости отражает предельную вязкость феррита без учета охрупчивающего влияния неоднородностей микроструктуры и неметаллических включений. Нижний уровень вязкости приводит к разрушению, поглощенная энергия которого в определяющей степени зависит от макроскопической вязкой деформации. Промежуточный уровень характеризуется наибольшим рассеянием ударной вязкости.
Наглядно распределение значений ударной вязкости представлено на скрипичной диаграмме (рис. 7). Также 3 моды наблюдаются и на частотном распределении значений ударной вязкости суммарной совокупности всех результатов испытаний (рис. 20). Аналогичные результаты были получены ранее при множественных испытаниях на ударный изгиб основного металла той же стали [40]. На рис. 21 приведено распределение значений ударной вязкости основного металла стали 09Г2С в состоянии после закалки с отпуском, построенное по результатам множественных испытаний при температурах от –60 до +20°C (по 75 образцов на температуру). В распределении наблюдаются две моды – 220 и 300 Дж/см2. Разрушения одинаковой энергоемкости при разных температурах испытаний наблюдали и на горячекатаном металле стали той же плавки. В частности, значения от 120 до 175 Дж/см2 наблюдали при температурах от –60 до –20°C. Наблюдение разрушений одинаковой энергоемкости является признаком двухстадийного разрушения в переходном интервале температур. Различия в механизмах разрушения стали с изменением микроструктуры описаны и в других работах [31, 41 ].
Рис. 20.
Частотное распределение значений ударной вязкости для всех температур испытаний сварного шва.
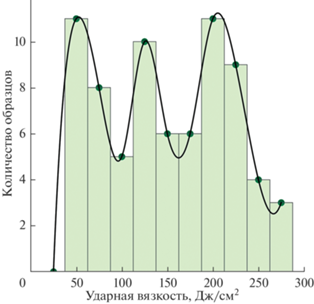
Рис. 21.
Частотное распределение значений ударной вязкости для всех температур испытаний основного металла стали 09Г2С.
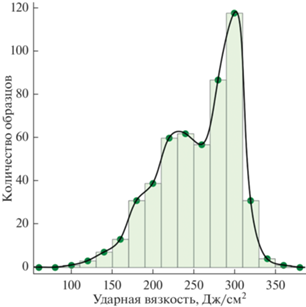
Наивысшие величины ударной вязкости ИФ, достижимые при каждой температуре испытаний, можно рассматривать как предельную вязкость ИФ без учета охрупчивающего влияния неоднородностей микроструктуры и неметаллических включений [40]. Эти величины составляют верхнюю огибающую. Минимальные значения при каждой температуре испытаний определяются степенью макроскопической вязкой пластической деформации, предшествующей разрушению, и составляют нижнюю огибающую.
Можно предположить, что образование среднего плато ударной вязкости внутри интервала вязко-хрупкого перехода является общим явлением для микроструктур, содержащих две составляющие, заметно отличающиеся по температуре перехода от вязкого разрушения к хрупкому. В нашей работе хрупкой составляющей, трещины скола в которой зарождаются легче, является зернограничный феррит, а более вязкой – ИФ. В работах [31, 41], в качестве таких составляющих выступали феррит и перлит, а в работе [40] – феррит и бейнит. Во всех указанных случаях общим является существование разрушений одинаковой энергоемкости при различных температурах испытаний. Это может быть объяснено существованием в металле структурных составляющих, которые отличаются по температуре перехода от вязкого разрушения к хрупкому. При этом происходит образование нескольких уровней ударной вязкости с соответствующим разделением общего переходного интервала на части, каждая из которых соответствует переходу между выделенными уровнями.
Разрушение металла исследованного сварного соединения происходит с остановкой трещины скола задолго до полного разрушения образца, что не характерно для основного металла или металла околошовной зоны [42]. На динамических кривых, приведенных на рис. 18, это проявляется в длинном хвосте спада усилия после ступенек, соответствующих образованию хрупкого излома. Температурные зависимости для значений работы, произведенной до образования и после остановки макроскопической трещины скола, представлены на рис. 22.
Рис. 22.
Температурные зависимости работы, совершенной до (а) и после (б) образования трещины скола.
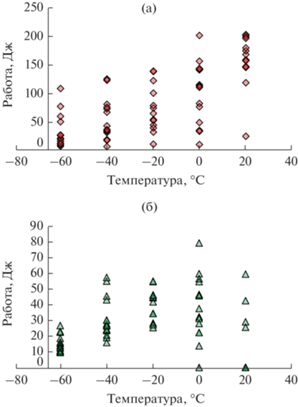
На температурных зависимостях отмечается рассеяние значений энергии, затраченной на разрушение образца как до образования трещины скола, так и в области вязкого долома – после остановки трещины скола. Связь рассеяния значений ударной вязкости с различиями в прогибе, при котором образуется трещина скола в образцах, испытанных при одной температуре, была показана ранее [42, 43]. Новым наблюдением является рассеяние значений ударной вязкости после остановки трещины скола. Поскольку высокая энергия долома не характерна для низколегированных сталей, рассеяние этой энергии при их испытаниях ранее не наблюдалось. При этом в случае разрушения ИФ эта часть рассеяния ударной вязкости вносит существенный вклад в общее рассеяние. Увеличение суммарного рассеяния происходит из-за того, что значения работы до образования трещины скола и после ее остановки имеют очень низкую корреляцию (корреляционная диаграмма показана на рис. 23), вследствие чего на обычной сериальной кривой рассеяния этих величин суммируются. Важно отметить, что работа разрушения до образования трещины скола также имеет три характерных уровня внутри переходного интервала.
Таким образом, рассеяние значений ударной вязкости при разрушении сварного шва с микроструктурой ИФ определяется не только моментом зарождения трещины скола, как в микроструктуре основного металла, но и во многом моментом остановки трещины скола.
Причины возникновения рассеяния значений ударной вязкости, связанные с зарождением трещины скола, обсуждались в ряде работ [44–48]. Явление рассеяния связывают с наличием в микроструктуре участков с различным напряжением скола. В металле исследованного сварного шва структурными составляющими с существенно отличающимся напряжением скола являются ИФ с характерным размером 3 мкм и зернограничный феррит с характерным размером 10–40 мкм. Макроскопическое хрупкое разрушение образца происходит при образовании дефекта определенного размера, развитию которого микроструктура не может сопротивляться. Дефект, образование которого приводит к макроскопическому хрупкому разрушению, принято называть критическим дефектом. Снижение пластичности феррита с понижением температуры приводит к тому, что размер критического дефекта снижается за счет уменьшения напряжения в вершине трещины, необходимого для перехода через барьеры в микроструктуре, например границы зерен. На примере исследованного сварного соединения снижение размера критического дефекта проявляется в снижении размера отдельных областей скола, образовавшихся, но не приведших к макроскопическому хрупкому разрушению, с понижением температуры. Максимальный размер такой фасетки соответствует нижней границе размеров критического дефекта.
Микроструктура исследованного сварного шва неоднородна, наблюдаются области с различным содержанием зернограничного феррита, что сказывается на взаимном расположении его зерен. Зернограничный феррит может либо отсутствовать полностью, либо образовывать отдельные зерна, полностью окруженные ИФ, либо образовывать непрерывную сетку. В зависимости от температуры образование трещины скола в областях с различным взаиморасположением зерен зернограничного феррита может приводить или не приводить к макроскопическому хрупкому разрушению. При высоких температурах (+20°C) образование трещины скола в зернограничном феррите с размером области его непрерывной сетки порядка 200 мкм не критично и оставляет после себя отдельную микроскопическую область скола внутри вязкого излома. По мере снижения температуры уменьшение размера критического дефекта приводит к тому, что скол отдельного единичного зерна зернограничного феррита дает начало макроскопическому хрупкому разрушению. По результатам микрофрактографического исследования, при температуре –60°С уровень ударной вязкости определяется именно таким событием. По всей видимости, образование отдельных уровней ударной вязкости связано с тем, что размер зерен зернограничного феррита достаточно велик для того, чтобы трещины скола, распространившиеся на области, содержащие 1, 2 или большее количество соединенных зерен зернограничного феррита, становились критическими дефектами существенно разного масштаба, создающими отдельные уровни вязкости. Можно предположить и наличие еще одного уровня ударной вязкости в области температур ниже –60°C, для которого критическим будет скол зерна игольчатого феррита. Данный подход является развитием подхода оценки хладноломкости металла путем анализа вторичных трещин, предложенного в работе [49], за тем отличием, что в случае большого количества игольчатого феррита, блокирующего рост трещины скола, становится возможным наблюдение непосредственно отдельных фасеток скола, размер которых меньше критического дефекта. Наличие непрерывной сетки зернограничного феррита делает возможным образование крупных дефектов, поскольку трещина скола распространяется через такую микроструктуру значительно легче, чем через игольчатый феррит, что можно заметить по росту вторичных трещин (рис. 24).
Интересно отметить, что обсуждаемый во многих работах малый размер зерна игольчатого феррита не приводит к значениям ударной вязкости существенно более высоким, чем у прочих малоуглеродистых сталей. Средневзвешенный по площади размер зерна основного металла, использованного для получения исследованного сварного соединения, составляет 10 мкм, в то время как максимальный уровень ударной вязкости, соответствующий образцу с полностью вязким изломом, составляет 270–300 Дж/см2. В исследованном же сварном соединении при размере зерна в 3 мкм этот уровень составляет всего 250 Дж/см2. Вероятно, столь существенное отличие объясняется повышенным содержанием неметаллических включений в сварном соединении. Температура перехода от вязкого разрушения к хрупкому для основного металла ниже, чем для металла сварного шва. Начало переходного интервала в основном металле приходится на температуру ‒40°С, при которой появляются первые образцы с фасетками скола на поверхности разрушения. Такое различие может быть связано с тем, что максимальный размер зерна в основном металле составляет порядка 15–20 мкм, что соответствует размеру ферритного зерна в ферритно-бейнитной микроструктуре, а в сварном шве – около 40 мкм, что соответствует зернограничному ферриту. Это приводит к образованию существенно различных по размеру дефектов при сколе единичного зерна. При этом аналогичное несоответствие свойств и микроструктуры наблюдается и при сравнении прочности, которая у основного металла выше, чем у сварного шва.
Причиной рассеяния работы долома, по всей видимости, является неоднородность микроструктуры в плане сопротивления росту трещины скола. В этом случае остановка макроскопического хрупкого разрушения может быть связана с переходом из рекристаллизованной зоны или области с локальной сеткой зернограничного феррита в область чистого игольчатого феррита. Расположение таких областей связано с расположением границ проходов сварки, что делает его близким к случайному в пределах одного образца.
ЗАКЛЮЧЕНИЕ
Исследованы микроструктурные особенности разрушения сварного шва с высокой долей ИФ на большом количестве образцов. Результаты исследования позволяют сделать следующие выводы.
1. Микроструктура металла изученного сварного соединения состоит из двух составляющих, представляющих собой две различные модификации феррита: на 97% из ИФ и на 3% из более крупнозернистого зернограничного феррита. Модальный размер зерен ИФ составляет 2.9 мкм, диапазон размеров зерен зернограничного феррита – 10–40 мкм.
2. Исследованный металл сварного шва обладает очень широким переходным интервалом хладноломкости, температуры от –60 до +20°C, по результатам испытания на ударный изгиб, находятся в переходном интервале. Для определения переходного интервала при испытании на ударный изгиб допустимо использование в качестве критерия как поглощенной энергии, так и соотношения хрупкой и вязкой составляющих изломов.
3. Рассеяние значений ударной вязкости в исследованной микроструктуре в основном определяется различиями прогиба при зарождении и остановке трещины скола от образца к образцу. При этом корреляция между этими событиями низка и каждое из них вносит отдельный вклад в рассеяние значений ударной вязкости. Внутри переходного интервала исследованного сварного шва наблюдаются три уровня ударной вязкости.
4. Фрактографически уменьшение ударной вязкости при понижении температуры испытания связано с возрастанием доли излома, занятой фасетками скола. При всех температурах низкоэнергетичный излом состоит из фасеток скола с характерным речным узором, объединенных вязкими гребнями в местах несовпадения плоскостей скола в соседних зернах. Наблюдается одностадийное изменение механизма разрушения от вязкого к сколу.
5. Высокая корреляция между прогибом в момент скола и глубиной первоначальной вязкой трещины подтверждает зарождение трещины скола в вершине растущей вязкой трещины. С использованием этой зависимости возможно локализовать очаги скола на изломе. Распределение нижних величин ударной вязкости, в частности, сильно зависит от степени исходной макроскопической вязкой деформации и находит свое отражение в ходе нижней огибающей.
6. Из сопоставления результатов испытаний на ударный изгиб металла сварного соединения с микроструктурой ИФ и основного металла следует, что при испытании образцов основного металла с ферритно-перлитной и ферритно-бейнитной микроструктурами наблюдали случаи разрушений в широком интервале температур с одинаковой энергоемкостью.
7. Низколегированные стали в зависимости от микроструктуры могут разрушаться как материалы, состоящие только из одной либо из двух структурных составляющих, каждая из которых может быть модификацией одной и той же фазы (феррита), отличающейся от другой по прочности и пластичности.
Список литературы
Easterling K. Introduction to the Physical Metallurgy of Welding. N. Y.: Elsevier, 2013.
Tweed J.H., Knott J.F. Micromechanisms of Failure in C–Mn Weld Metals // Acta Metall. Mater. 1987. V. 35. № 7. P. 1401–1414. https://doi.org/10.1016/0001-6160(87)90087-3
Ohkita S., Horii Y. Recent Development in Controlling the Microstructure and Properties of Low Alloy Steel Weld Metals // ISIJ Int. 1995. V. 35. № 10. P. 1170–1182. https://doi.org/10.2355/isijinternational.35.1170
Svensson L.E., Gretoft B. Microstructure and Impact Toughness of C–Mn Weld Metals // Weld. J. 1990. V. 69. № 12. P. 454.
Fattahi M. et al. Effect of Ti-Containing Inclusions on the Nucleation of Acicular Ferrite and Mechanical Properties of Multipass Weld Metals // Micron. 2013. V. 45. P. 107–114. https://doi.org/10.1016/j.micron.2012.11.004
Sung H.K. et al. Effects of Oxides on Tensile and Charpy Impact Properties and Fracture Toughness in Heat Affected Zones of Oxide-Containing API X80 Linepipe Steels // Metall. Mater. Trans. A. 2014. V. 45. № 7. P. 3036–3050. https://doi.org/10.1007/s11661-014-2240-2
Zhao L. et al. Influence of Ti on Weld Microstructure and Mechanical Properties in Large Heat Input Welding of High Strength Low Alloy Steels // J. Iron Steel Res. Int. 2015. V. 22. № 5. P. 431–437. https://doi.org/10.1016/S1006-706X(15)30023-6
Xiong Z. et al. The Contribution of Intragranular Acicular Ferrite Microstructural Constituent on Impact Toughness and Impeding Crack Initiation and Propagation in the Heat-Affected Zone (HAZ) of Low-Carbon Steels // Mater. Sci. Eng. A. 2015. V. 636. P. 117–123. https://doi.org/10.1016/j.msea.2015.03.090
Choi B.C. et al. Effect of Microstructure on Low-Temperature Fracture Toughness of a Submerged-Arc-Welded Low-Carbon and Low-Alloy Steel Plate // Metals. 2021. V. 11. № 11. P. 1839. https://doi.org/10.3390/met11111839
Jiménez-Jiménez A. et al. CVN Impact Energy and Fracture Characteristics Correlations with Different Oxide Nanoparticles Improving Submerged Arc Welds // Mater. Res. Express. 2021. V. 8. № 1. P. 016536. https://doi.org/10.1088/2053-1591/abdaf2
Farrar R.A., Harrison P.L. Acicular Ferrite in Carbon-Manganese Weld Metals: an Overview // J. Mater. Sci. 1987. V. 22. № 11. P. 3812–3820. https://doi.org/10.1007/BF01133327
Madariaga I., Gutierrez I., Bhadeshia H. Acicular Ferrite Morphologies in a Medium-Carbon Microalloyed Steel // Metall. Mater. Trans. A. 2001. V. 32. № 9. P. 2187–2197. https://doi.org/10.1007/s11661-001-0194-7
Bhadeshia H., Svensson L.E. Modelling the Evolution of Microstructure in Steel Weld Metal // Math. Model. Nat. Phenom. 1993. V. 1. P. 109–182.
Loder D., Michelic S.K. Systematic Investigation of Acicular Ferrite Formation on Laboratory Scale // Mater. Sci. Technol. 2017. V. 33. № 2. P. 162–171. https://doi.org/10.1080/02670836.2016.1165902
Costin W.L., Lavigne O., Kotousov A.A. Study on the Relationship between Microstructure and Mechanical Properties of Acicular Ferrite and Upper Bainite // Mater. Sci. Eng. A. 2016. V. 663. P. 193–203. https://doi.org/10.1016/j.msea.2016.03.103
Chen J.H., Wang G.Z., Ma H. Fracture Behavior of C-Mn Steel and Weld Metal in Notched and Precracked Specimens: Part II. Micromechanism of Fracture // Metall. Mater. Trans. A. 1990. V. 21. № 1. P. 321–330. https://doi.org/10.1007/BF02782412
Kantor M.M., Vorkachev K.G., Bozhenov V.A., Solntsev K.A. The Role of Splitting Phenomenon under Fracture of Low-Carbon Microalloyed X80 Pipeline Steels during Multiple Charpy Impact Tests // Appl. Mech. 2022. 3(3): 740–756. https://doi.org/10.3390/applmech3030044
Sudin V.V. et al. Correlation of the Microstructural Factors Influence on the Impact Strength of the Weld Affected Zone of K60* Strength Class Welded Pipes // Steel Transl. 2022. V. 52. № 1. P. 121–128.
Ishikawa T., Haze T. Significance of Fracture Facet Size in Cleavage Fracture Process of Welded Joints // Mater. Sci. Eng. A. 1994. V. 176. № 1–2. P. 385–391. https://doi.org/10.1016/0921-5093(94)91003-0
Lee M. et al. Effects of Inclusion Size and Acicular Ferrite on Cold Cracking for High-Strength Steel Welds of YS 600 MPa Grade // Sci. Technol. Weld. Join. 2016. V. 21. № 8. P. 711–719. https://doi.org/10.1080/13621718.2016.1178833
Bose Filho W.W., Carvalho A.L.M., Bowen P. Micromechanisms of Cleavage Fracture Initiation from Inclusions in Ferritic Welds: Part I. Quantification of Local Fracture Behaviour Observed in Notched Testpieces // Mater. Sci. Eng. A. 2007. V. 460. P. 436–452. https://doi.org/10.1016/j.msea.2007.01.115
Hytönen N. et al. Effect of Weld Microstructure on Brittle Fracture Initiation in the Thermally-Aged Boiling Water Reactor Pressure Vessel Head Weld Metal // Int. J. Miner. Metall. 2021. V. 28. № 5. P. 867–876. https://doi.org/10.1007/s12613-020-2226-6
Diaz-Fuentes M., Iza-Mendia A., Gutierrez I. Analysis of Different Acicular Ferrite Microstructures in Low-Carbon Steels by Electron Backscattered Diffraction. Study of their Toughness Behavior // Metall. Mater. Trans. A. 2003. V. 34. № 11. P. 2505–2516. https://doi.org/10.1007/s11661-003-0010-7
Lan L. et al. Influence of Microstructural Aspects on Impact Toughness of Multi-Pass Submerged Arc Welded HSLA Steel Joints // Mater. Des. 2016. V. 90. P. 488–498. https://doi.org/10.1016/j.matdes.2015.10.158
Terashima S., Bhadeshia H. Changes in Toughness at Low Oxygen Concentrations in Steel Weld Metals // Sci. Technol. Weld. Join. 2006. V. 11. № 5. P. 509–516. https://doi.org/10.1179/174329306X113299
Curry D.A., Knott J.F. Effects of Microstructure on Cleavage Fracture Stress in Steel // Met. Sci. J. 1978. V. 12. № 11. P. 511–514.
Shi Z. et al. Mechanism of BN-Promoting Acicular Ferrite Nucleation to Improve Heat-Affected Zone Toughness of VN-Ti Microalloyed Offshore Steel // J. Mater. 2022. V. 15. № 4. P. 1420. https://doi.org/10.1016/0001-6160(86)90222-1
Yanagimoto F. et al. Local Stress in the Vicinity of the Propagating Cleavage Crack Tip in Ferritic Steel // Mater. Des. 2018. V. 144. P. 361–373. https://doi.org/10.1016/j.matdes.2018.02.037
Gourgues A.F. Microtexture Induced by the Bainitic Transformation in Steels during Welding. Effect on the Resistance to Cleavage Cracking // Mater. Sci. Forum. 2003. V. 426. P. 3629–3634.
Calcagnotto M. et al. Effect of Grain Refinement on Strength and Ductility in Dual-Phase Steels // Proc. 2d Int. Sym. Steel Sci (ISSS 2009), Kyoto. 2009. P. 21–24.
Kawata H., Umezawa O. Effect of Pearlite Volume Fraction on Two-Step Ductile to Brittle Transition in Ferrite+ Pearlite Structure Steel Sheets // ISIJ Int. 2019. P. ISIJINT-2018-764. https://doi.org/10.2355/isijinternational.ISIJINT-2018-764
Шевандин Е.М., Разов И.А. Хладноломкость и предельная пластичность металлов в судостроении. Ленинград: Судостроение, 1965.
Graville B.A., Tyson W.R. Toughness Requirements for Welded Structures in the Arctic // Weld. J. 1992. V. 71. P. 437.
Scott D.W. Multivariate Density Estimation: Theory, Practice, and Visualization // Wiley, N. Y.: 1992. https://doi.org/10.1002/9780470316849
Bishop T.A., Markworth A.J., Rosenfield A.R. Analyzing Statistical Variability of Fracture Properties // Metall. Mater. Trans. A. 1983. V. 14. № 3. P. 687–693.
Штремель М.А. Разрушение. М.: Издательский дом МИСиС, 2014. Кн. 2. С. 456–478.
Кудря А.В., Кузько Е.И., Соколовская Э.А. Об оценке хладноломкости конструкционных сталей по результатам сериальных ударных испытаний // Деформация и разрушение материалов. 2013. № 12. С. 36–45.
Кудря А.В., Соколовская Э.А. Неоднородность разномасштабных структур и сопротивление разрушению конструкционных сталей // Изв. Рос. академии наук. Сер. физ. 2004. Т. 68. № 10. С. 1495–1502.
Кантор М.М., Судьин В.В., Солнцев К.А. Деформационные особенности распространения трещин скола в ферритно-перлитной микроструктуре в интервале вязко-хрупкого перехода // Неорган. материалы. 2021. Т. 57. № 6. С. 670–682. https://doi.org/10.31857/S0002337X2106004X
Кантор М.М., Боженов В.А. Рассеяние значений ударной вязкости низколегированной стали в критическом интервале хладноломкости // Материаловедение. 2013. № 11. С. 3–14.
Kawata H., Umezawa O. Middle Shelf during Ductile to Brittle Transition on Ferrite + Pearlite Structure Steel Sheet // Mater. Sci. Forum. 2018. V. 941. P. 453–457. doi: 10.4028/www.scientific.net/MSF.941.453
Sudin V.V., Kantor M.M., Solntsev K.A. Features of Weld Metal Brittle Fracture in Charpy Tests // Procedia Struct. Integr. 2020. V. 28. P. 1637–1643. https://doi.org/10.1016/j.prostr.2020.10.135
Sudin V.V., Kantor M.M., Solntsev K.A. Analysis of the Relationship between the Load-Displacement Curve and Characteristics of Fracture of Low-Alloy Steel by Neural Networks // Inorg. Mater.: Appl. Res. 2020 V. 11. № 4. P. 893–902. https://doi.org/10.1134/S2075113320040176
Tanguy B., Besson J., Piques R., Pineau A. Ductile to Brittle Transition of an A508 Steel Characterized by Charpy Impact Test: Part I: Experimental Results // Eng. Fract. Mech. 2005. V. 72. № 1. P. 49–72. https://doi.org/10.1016/j.engfracmech.2004.03.010
Martin-Meizoso A. et al. Modelling Cleavage Fracture of Bainitic Steels // Acta Metall. Mater. 1994. V. 42. № 6. P. 2057–2068. https://doi.org/10.1016/0956-7151(94)90031-0
Lambert-Perlade A. et al. Mechanisms and Modeling of Cleavage Fracture in Simulated Heat-Affected Zone Microstructures of a High-Strength Low Alloy Steel // Metall. Mater. Trans. A. 2004. V. 35. № 13. P. 1039–1053. https://doi.org/10.1007/s11661-004-0030-y
Pineau A. Practical Application of Local Approach Methods // Comprehensive Structural Integrity. Oxford: Elsevier, 2003. Chapter 7.05. V. 7. P. 177–225.
Chen J.H., Zhu L., Ma H. On the Scattering of the Local Fracture Stress σf* // Acta Metall. Mater. 1990. V. 38. № 12. P. 2527–2535. https://doi.org/10.1016/0956-7151(90)90264-H
Кантор М.М., Воркачев К.Г., Солнцев К.А. Природа микротрещин в ферритных сталях в условиях разрушения при температурах критического интервала хладноломкости // Неорган. материалы. 2018. Т. 54. № 10. С. 1133–1140. https://doi.org/10.1134/S0002337X18100093
Дополнительные материалы отсутствуют.
Инструменты
Неорганические материалы