Расплавы, 2022, № 2, стр. 172-180
Термодинамическое моделирование восстановления меди из расплава B2O3–CaO–FeO–CuО монооксидом углерода и водородом
А. С. Вусихис a, *, Е. Н. Селиванов a, Л. И. Леонтьев a
a Институт металлургии УрО РАН
Екатеринбург, Россия
* E-mail: vas58@mail.ru
Поступила в редакцию 11.11.2020
После доработки 01.10.2021
Принята к публикации 30.10.2021
- EDN: ASHUPN
- DOI: 10.31857/S0235010622020104
Аннотация
Для описания процессов совместного восстановления железа и меди из оксидного расплава (1273–1773 К) системы B2O3–CaO–FeO–CuO монооксидом углерода и водородом применена методика термодинамического моделирования в приближении к открытым системам, с дробным введением СО (Н2) и периодическим выводом металлической фазы и газов из состава рабочего тела. Расчеты проведены с учетом диспропорционирования FeO на Fe и Fe3O4. Для рассмотренных составов расплава, имеющих соотношение FeO/CuO равное 10, диспропорционирование низшего оксида железа и его взаимодействие с СuO позволяет при низких температурах перевести медь в металлическое состояние на 20–80%. Выявлены взаимосвязи содержаний оксидов железа и меди в оксидном расплаве, степеней их восстановления и состава образующегося сплава от температуры и количества введенного восстановителя. Показано, что необходимое количество водорода на восстановление металлов до фиксированной степени металлизации меди существенно ниже, чем монооксида углерода. Полученные сведения полезны для прогнозирования термоэкстракционных процессов, протекающих при извлечении полезных компонентов из шлаков цветной металлургии.
ВВЕДЕНИЕ
Сведения по оксидным системам, содержащим CuO и Cu2O, значимы для совершенствования технологических процессов переработки медьсодержащих руд, концентратов и вторичного сырья. В частности, для оптимизации составов шлаков медеплавильных производств предложены варианты переработки концентратов и штейнов с добавками оксидов кальция [1, 2], бора [3–5], цинкового клинкера [6, 7] и других компонентов [8], что обеспечивает сокращение потерь меди со шлаком и рафинирование выделяемого металла. Для предварительной оценки межфазного распределения элементов широко используются методы термодинамического моделирования [9–13]. Приближения результатов моделирования к реальным пирометаллургическим процессам [14–17] добиваются путем дробного введения восстановителя в состав рабочего тела и выводом из расчетов образующихся газа и металла.
Цель работы состоит в выявлении особенностей барботажного восстановления меди и железа из расплава системы B2O3–CaO–FeO–CuO с использованием методики термодинамического моделирования ТДМ а также сопоставлении достигаемых показателей в ходе использования монооксида углерода и водорода в качестве восстановителей.
В представленной работе с использованием методики ТДМ проведена оценка показателей процессов взаимодействия оксидного расплава системы B2O3–CaO–FeO–CuO с монооксидом углерода и водородом, для выявления особенностей восстановления металлов из расплава B2O3–CaO–FeO–ZnO водородом и монооксидом углерода.
МЕТОДИКА РАСЧЕТОВ
Математическая модель ТДМ предусматривает следующие допущения.
1. Скорость взаимодействия восстанавливаемых оксидов с газом-восстановителем настолько велика, что при всплывании пузыря газа в слое в нем достигается равновесие.
2. После взаимодействия с очередной порцией газа концентрация оксидов меняется мгновенно и по всему объему расплава.
Расчет дробится на циклы, в каждом последующем из которых предусмотрено участие только оксидной фазы с достигнутым содержанием оксидов восстанавливаемых металлов и выводом из системы газа и металлической составляющей. Расчет проводится по (Z) последовательным циклам с введением восстановителя в количестве (n) молей в единичной порции.
Расчет ведут следующим образом:
Задаются исходные составы расплава и газа и их количество
(1)
$\sum\limits_{j{\kern 1pt} = {\kern 1pt} 1}^{j{\kern 1pt} = {\kern 1pt} n} {N_{{0,j}}^{{(s)}}} ,\,\,\,\,\sum\limits_{i{\kern 1pt} = {\kern 1pt} 1}^{i{\kern 1pt} = {\kern 1pt} m} {N_{i}^{{\{ g\} }},} $Производится расчет равновесия в системе
(2)
$\sum\limits_{j{\kern 1pt} = {\kern 1pt} 1}^{j{\kern 1pt} = {\kern 1pt} n} {N_{{0,j}}^{{(s)}}} + \sum\limits_{i{\kern 1pt} = {\kern 1pt} 1}^{i{\kern 1pt} = {\kern 1pt} m} {N_{i}^{{\{ g\} }}} \to \sum\limits_{j{\kern 1pt} = {\kern 1pt} 1}^{j{\kern 1pt} = {\kern 1pt} n} {N_{{1,j}}^{{(s)}}} + \sum\limits_{b{\kern 1pt} = {\kern 1pt} 1}^{b{\kern 1pt} = {\kern 1pt} c} {N_{{1,b}}^{{[s]}}} + \sum\limits_{i{\kern 1pt} = {\kern 1pt} 1}^{i{\kern 1pt} = {\kern 1pt} m} {N_{{i,1}}^{{\{ g\} }},} $Задается новый исходный состав оксидного расплава, количество оксидов в котором равно равновесному содержанию
(3)
$\sum\limits_{j{\kern 1pt} = {\kern 1pt} 1}^{j{\kern 1pt} = {\kern 1pt} n} {N_{{1,j}}^{{(s)}}.} $Повторяется расчет равновесия системы с новыми исходными данными (состав газа-восстановителя, подаваемого в систему, и его количество не меняются, а компоненты системы, находящиеся в металлическом состоянии, выводятся из системы и при расчете равновесия не учитываются).
(4)
$\sum\limits_{j{\kern 1pt} = {\kern 1pt} 1}^{j{\kern 1pt} = {\kern 1pt} n} {N_{{1,j}}^{{(s)}}} + \sum\limits_{i{\kern 1pt} = {\kern 1pt} 1}^{i{\kern 1pt} = {\kern 1pt} m} {N_{i}^{{\{ g\} }}} \to \sum\limits_{j{\kern 1pt} = {\kern 1pt} 1}^{j{\kern 1pt} = {\kern 1pt} n} {N_{{2,j}}^{{(s)}}} + \sum\limits_{b{\kern 1pt} = {\kern 1pt} 1}^{b{\kern 1pt} = {\kern 1pt} c} {N_{{2,b}}^{{[s]}}} + \sum\limits_{i{\kern 1pt} = {\kern 1pt} 1}^{i{\kern 1pt} = {\kern 1pt} m} {N_{{i,2}}^{{\{ g\} }}} .$Цикл повторяется до тех пор, пока количество восстанавливаемых оксидов в расплаве не уменьшится до заданной величины.
Применение методики позволяет определять, в зависимости от количества введенного газа-восстановителя (Vg), следующие величины: содержание оксидов (CMeO) в шлаке и металлов (CMe) в сплавах, коэффициенты перехода компонентов в элементное состояние (φMe) и межфазное распределение элементов. Расчеты проведены с использованием программного комплекса и базы данных ИВТАНТЕРМО.
Для расчетов взято рабочее тело, отвечающее системе B2O3–CaO–FeO–CuO с содержанием компонентов, мас. %: 58.5 В2О3; 19.5 СаО; 20.0 FeO; 2.0 CuО. Моделирование проведено в интервале температур 1273–1773 К и давлении – 0.098 МПа. Для приближения к реальным процессам, реализуемым при барботажной обработке расплавов, моделирование вели с дробным введением восстановителя, а также периодическим выводом металлической фазы и газов из состава рабочего тела [15]. Количество газа-восстановителя (СО и Н2) в единичной порции принято равным 1.44 дм3 на 1 кг массы конденсированной составляющей рабочего тела. В ходе расчетов определяли содержания оксидов меди (CCuO, ${{C}_{{{\text{C}}{{{\text{u}}}_{2}}{\text{O}}}}}$) и железа (CFeO, ${{{\text{C}}}_{{{\text{F}}{{{\text{e}}}_{{\text{3}}}}{{{\text{O}}}_{{\text{4}}}}}}}$) в ферритно-кальциевом боратном расплаве, степени металлизации (φCu и φFe) и долю меди в сплаве (СCu) при изменении количества введенного газа (VСО и ${{V}_{{{{{\text{Н}}}_{{\text{2}}}}}}}{\text{,}}$ дм3/кг) и температуры. Степени металлизации определены как отношения масс образованных металлов к введенным в рабочее тело.
Поскольку железо лишь частично растворимо в меди [18], а используемая для ТДМ программа не позволяла вести одновременный учет сплавов Cu–Fe и Fe–Cu с предельным содержанием второго компонента, расчеты завершали при содержании железа в единичной порции сплава $(С_{{{\text{Fe}}}}^{'}),$ близком к пределу растворения при заданной температуре. Для упрощения расчетов все растворы приняты идеальными.
РЕЗУЛЬТАТЫ И ИХ ОБСУЖДЕНИЕ
Нагрев рабочего тела, отвечающего системе B2O3–CaO–FeO–CuО в инертной среде (аргон) сопровождается протеканием реакций:
(6)
$2{\text{CuO}} + 3{\text{FeO}} = {\text{C}}{{{\text{u}}}_{2}}{\text{O}} + {\text{F}}{{{\text{e}}}_{{\text{3}}}}{{{\text{O}}}_{4}},$(7)
${\text{CuO}} + 3{\text{FeO}} = {\text{F}}{{{\text{e}}}_{{\text{3}}}}{{{\text{O}}}_{4}} + {\text{Cu}},$(8)
${\text{C}}{{{\text{u}}}_{{\text{2}}}}{\text{O}} + {\text{Fe}} = 2{\kern 1pt} {\text{Cu}} + {\text{FeO}},$(9)
${\text{C}}{{{\text{u}}}_{{\text{2}}}}{\text{O}} + 3{\text{FeO}} = 2{\kern 1pt} {\text{Cu}} + {\text{F}}{{{\text{e}}}_{{\text{3}}}}{{{\text{O}}}_{4}}.$В результате происходит изменение состава продуктов взаимодействия (табл. 1): к имеющимся компонентам B2O3, CaO, FeO и CuО добавляются Cu2O, Fe3O4, Fe и Cu. Как показали результаты моделирования, в рассматриваемой системе возможно формирование металлической меди даже без введения восстановителя. Так при 1273 К 80.2% CuО восстанавливается до металла и 19.2% – до Cu2О. Процесс протекает за счет взаимодействия CuO с FeO, а также железом, образовавшимся в результате диспропорционирования его оксида. Металлическое железо, в основном, взаимодействует с оксидами меди и переходит в сплав Cu–Fe, где его доля не превышает 0.6%. Степень металлизации железа в системе составляет 0.04%, а меди – 80%. С повышением температуры состав продуктов взаимодействия несколько меняется. Содержания исходных компонентов (СFeO и СCuO), а также образующегося Cu2O $({{С}_{{{\text{C}}{{{\text{u}}}_{{\text{2}}}}{\text{O}}}}})$ увеличиваются, а Fe3O4 $({{С}_{{{\text{F}}{{{\text{e}}}_{{\text{3}}}}{{{\text{O}}}_{{\text{4}}}}}}}),$ металлических железа (CFe) и меди (CCu) уменьшаются. При температуре выше 1673 К металлические железо и медь в продуктах взаимодействия отсутствуют, доли FeO и CuO составляют 87 и 5.5% от сумм соответствующих оксидов.
Таблица 1.
Состав продуктов взаимодействия в системе B2O3–CaO–FeO–CuО–Ar при температурах 1273–1773 К
Т, К | 1273 | 1373 | 1473 | 1573 | 1673 | 1773 |
---|---|---|---|---|---|---|
СCuO, мас. % | 0.01 | 0.03 | 0.05 | 0.07 | 0.09 | 0.14 |
${{С}_{{{\text{C}}{{{\text{u}}}_{2}}{\text{O}}}}},$ мас. % | 0.35 | 0.69 | 1.03 | 1.52 | 1.73 | 1.68 |
CFeO, мас. % | 15.3 | 15.8 | 16.45 | 17.1 | 17.4 | 17.5 |
${{C}_{{{\text{F}}{{{\text{e}}}_{3}}{{{\text{O}}}_{4}}}}},$ мас. % | 5.3 | 4.7 | 4.1 | 3.2 | 2.8 | 2.7 |
φCu, % | 80.2 | 60.8 | 40.8 | 12.5 | 0.00 | 0.00 |
φFe, % | 0.04 | 0.03 | 0.02 | 0.01 | 0.00 | 0.00 |
Приведенные данные позволяют обосновать температурный интервал формирования частиц металлической меди при охлаждении шлаков, например, автогенной плавки сульфидных медных руд [19]. Исходя из расчетов, полнота перехода меди в металлические состояния зависит от соотношения СFeO/CCuO. Повышение этого соотношения при постоянном С, обеспечивает большие значения φCu. Выделение дисперсной меди при охлаждении шлака можно интерпретировать как изменение “металлической” растворимости с температурой [20, 21 ] . На наш взгляд, такое состояние системы отвечает вторичному минералообразованию, регулированием которого добиваются [22 ] высоких показателей по флотационному извлечению меди из медленно охлажденных шлаков.
Полученные данные использованы при моделировании процессов совместного восстановления меди и железа монооксидом углерода (рис. 1). Введение СО в рабочее тело сопровождается развитием реакций:
(10)
${\text{F}}{{{\text{e}}}_{{\text{3}}}}{{{\text{O}}}_{4}} + {\text{СО}} = 3{\text{FeO}} + {\text{С}}{{{\text{О}}}_{2}},$(13)
${\text{C}}{{{\text{u}}}_{{\text{2}}}}{\text{O}} + {\text{CO}} = 2{\kern 1pt} {\text{Cu}} + {\text{C}}{{{\text{O}}}_{2}}.$Рис. 1.
Изменение содержания оксидов железа (а, б) и меди (в, г) в расплаве, степени восстановления меди (д) и доли железа в единичном сплаве Cu–Fe (е) в зависимости от количества введенного СО (VCO), при температурах 1273–1773 K.
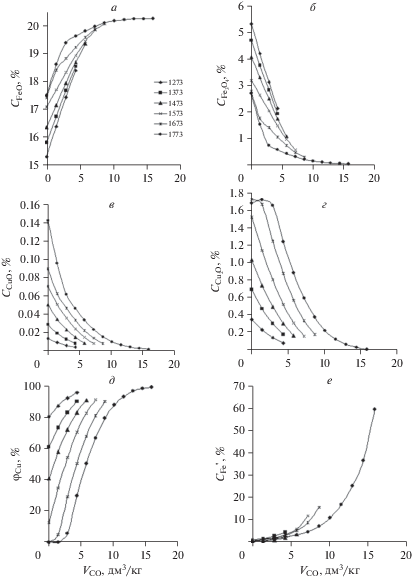
Введение монооксида углерода (VCO) в объеме до 15 дм3/кг расплава способствует росту значений СFeO в расплаве, но снижению ${{С}_{{{\text{F}}{{{\text{e}}}_{{\text{3}}}}{{{\text{O}}}_{{\text{4}}}}}}},$ СCuO и ${{С}_{{{\text{C}}{{{\text{u}}}_{{\text{2}}}}{\text{О}}}}}.$ Лишь при температуре 1773 К, когда диспропорционирование FeO не приводит к формированию металлической фазы, за счет восстановления CuO до Cu2O, происходит повышение значений ${{С}_{{{\text{C}}{{{\text{u}}}_{{\text{2}}}}{\text{O}}}}}.$ Дальнейшее повышение VCO ведет к образованию металлической меди и монотонному уменьшению ${{С}_{{{\text{C}}{{{\text{u}}}_{{\text{2}}}}{\text{O}}}}}.$ Повышенным температурам соответствуют меньшие величины ${{C}_{{{\text{F}}{{{\text{e}}}_{3}}{{{\text{O}}}_{4}}}}}$, но большие – СFeO, СCuO и ${{С}_{{{\text{C}}{{{\text{u}}}_{{\text{2}}}}{\text{О}}}}}$ в расплаве. Такая ситуация сохраняется во всем температурном интервале при равных VСО. Содержание железа $(C_{{{\text{Fe}}}}^{{\text{П}}})$ в единичном сплаве, близкое к пределу его растворения в меди, достигается при определенных VСО, увеличивающихся с температурой. Степень металлизации железа (φFe) меняется с 0.06% при 1273 К до 0.86% при 1773 К.
Степени металлизации меди (φCu) при 1273 К и VCO около 4.32 дм3/кг составляет 95%, из которых до 80% сформировано за счет реакций (1)–(5) и лишь 15% с участием монооксида углерода. С повышением температуры доля меди, образующейся в ходе восстановительных реакций, увеличивается. Однако, доля металла, образованного за счет реакций (1)–(5) уменьшается, что влияет на степень металлизации меди в интервале температур 1373–1673 К, когда снижается до 90%. При 1773 К и VCO равном 15.9 дм3/кг значения φCu приближаются к 99%. Так как количество металлического железа, образующегося в ходе восстановления, возрастает с температурой, что характерно для каждого единичного цикла расчетов, содержание меди в суммарном конечном сплаве (СCu) меняется с 99.4 (1273 К) до 92.2% (1773 К). При этом в заключительных единичных циклах расчетов СFe достигает 60%.
Обобщенные результаты восстановления меди и железа из расплавов B2O3–CaO–FeO–CuО по заключительному циклу расчетов представлены в табл. 2. Как следует из приведенных данных, для более полного перевода меди в металлическое состояние целесообразно поддерживать пониженные температуры расплава. Однако, учитывая необходимость плавления и перегрева образующегося сплава в промышленных агрегатах, температура должна быть не ниже 1473 К. Для сохранения φCu в этом интервале температур требуется введение большего количества восстановителя (VCO) – не менее 10–15 дм3/кг. При этом остаточное содержание меди в шлаке составит 0.1–0.15%.
Таблица 2.
Параметры восстановления металлов монооксидом углерода в системе B2O3–CaO–FeO–CuО по заключительному циклу расчетов
Т, К | 1273 | 1373 | 1473 | 1573 | 1673 | 1773 |
---|---|---|---|---|---|---|
$C_{{{\text{Fe}}}}^{{\text{'}}},$ % | 2.45 | 2.09 | 3.47 | 5.92 | 15.5 | 59.2 |
VСО, дм3/кг | 4.32 | 4.32 | 5.76 | 7.20 | 10.08 | 15.9 |
φCu, % | 95.4 | 89.8 | 90.6 | 90.9 | 89.7 | 98.8 |
φFe, % | 0.06 | 0.07 | 0.1 | 0.18 | 0.41 | 0.86 |
СCuO, % | 0.003 | 0.007 | 0.008 | 0.007 | 0.004 | 0.0008 |
${{С}_{{{\text{C}}{{{\text{u}}}_{2}}{\text{O}}}}},$ % | 0.082 | 0.18 | 0.17 | 0.16 | 0.09 | 0.008 |
CFeO, % | 18.4 | 18.5 | 19.4 | 19.8 | 20.2 | 20.2 |
${{C}_{{{\text{F}}{{{\text{e}}}_{3}}{{{\text{O}}}_{4}}}}},$ % | 2.1 | 1.9 | 1.1 | 0.55 | 0.16 | 0.03 |
СCu, % | 99.4 | 99.3 | 98.9 | 98.1 | 96.0 | 92.2 |
Введение Н2 в рабочее тело сопровождается развитием реакций:
(14)
${\text{F}}{{{\text{e}}}_{{\text{3}}}}{{{\text{O}}}_{4}} + {{{\text{Н}}}_{2}} = 3{\text{FeO}} + {{{\text{Н}}}_{{\text{2}}}}{\text{О}},$(17)
$7{\text{C}}{{{\text{u}}}_{{\text{2}}}}{\text{O}} + {{{\text{Н}}}_{2}} = 2{\text{Cu}} + {{{\text{Н}}}_{{\text{2}}}}{\text{О}}.$Параметры взаимодействия рассматриваемого расплава с водородом качественно не отличаются от представленных для монооксида углерода (рис. 2). Увеличение доли водорода (${{V}_{{{{{\text{H}}}_{2}}}}}$) в рабочем теле сопровождается повышением значений СFeO и уменьшением содержания остальных рассматриваемых оксидов. Количественные отличия (табл. 3) указывают на то, что водород является немного, но более эффективным восстановителем по отношению к меди, чем монооксид углерода. Если при температурах 1273–1373 К отличия в φCu незначительны, то в области повышенных температур (1673–1773 К) степень металлизации по меди достигает 94.9–99.7% при меньшем количестве введенного газа-восстановителя.
Рис. 2.
Изменение содержания оксидов меди в расплаве, степени восстановления меди в зависимости от количества введенного газа-восстановителя (Vг, дм3/кг), при температурах 1273 (а) и 1773 K (б).
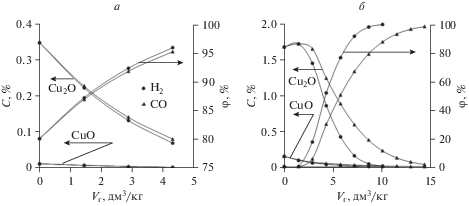
Таблица 3.
Параметры восстановления металлов водородом в системе B2O3–CaO–FeO–CuО по заключительному циклу расчетов
Т, К | 1273 | 1373 | 1473 | 1573 | 1673 | 1773 |
---|---|---|---|---|---|---|
$C_{{{\text{Fe}}}}^{{\text{'}}},$ % | 2.85 | 2.56 | 8.91 | 5.77 | 15.4 | 63.5 |
${{V}_{{{{{\text{Н}}}_{2}}}}},$ дм3/кг | 4.32 | 4.32 | 5.76 | 5.76 | 7.2 | 10.1 |
φCu, % | 96.0 | 91.6 | 94.7 | 90.7 | 94.9 | 99.7 |
φFe, % | 0.07 | 0.08 | 0.14 | 0.19 | 0.48 | 1.25 |
СCuO, % | 0.003 | 0.06 | 0.005 | 0.008 | 0.004 | 0.001 |
${{С}_{{{\text{C}}{{{\text{u}}}_{2}}{\text{O}}}}},$ % | 0.07 | 0.15 | 0.09 | 0.17 | 0.09 | 0.006 |
CFeO, % | 18.6 | 18.8 | 19.7 | 19.8 | 20.2 | 20.1 |
${{C}_{{{\text{F}}{{{\text{e}}}_{3}}{{{\text{O}}}_{4}},}}}$ % | 1.9 | 1.7 | 0.67 | 0.56 | 0.17 | 0.023 |
СCu, % | 99.3 | 99.2 | 98.6 | 98.0 | 95.3 | 89.1 |
Полученные результаты показывают, что достаточно полного восстановления меди из оксидного расплава можно добиться без существенного перевода железа в металлическое состояние (φFe менее 1.3%) при относительно небольшом количестве введенного восстановителя.
ВЫВОДЫ
Методами термодинамического моделирования показана необходимость учета вариабельности состава системы B2O3–CaO–FeO–CuО в области температур 1273–1773 К за счет диспропорционирования FeO и взаимодействия низших оксидов железа с оксидом меди(II). Пониженные температуры способствуют формированию Fe3O4 и металлической меди. На формы нахождения меди в расплаве влияют температура, количество введенного восстановителя и, вероятно, соотношение СFeO/CCuO. Лучшие показатели по металлизации меди достигнуты при низких температурах и использовании водорода в качестве восстановителя. Особенности перехода меди в металлическое состояние следует учитывать при моделировании процессов, интерпретации достигнутых результатов и их использования для оптимизации пирометаллургических процессов.
Работа выполнена при поддержке Российского фонда фундаментальных исследований проект № 18-29-24 093мк.
Список литературы
Селиванов Е.Н., Окунев А.И., Моисеев Г.К., Фазовые превращения при охлаждении шлаков плавки медных концентратов на богатый штейн // Расплавы. 2000. № 2. С. 18–24.
Парецкий В.М., Чахотин В.С., Довченко В.А., Селиванов Е.Н. Изучение потерь меди со шлаками при факельно-барботажной плавке // Цветная металлургия. 1996. № 11–12. С. 19–21.
Topçu M.A., Rüşen A., Derin B. Minimizing of copper losses to converter slag by a boron compound addition // J. Materials Research and Technology. 2019. 8. № 6. P. 6244–6252
Rüșen A., Gevec A., Topkaya Y.A. Minimization of copper losses to slag in matte smelting by colemanite addition // Solid State Sciences. 2012. 14. № 11–12. P. 1702–1704.
Белоусов А.А., Селиванов Е.Н., Беляев В.В., Литовских С.Н. Применение борсодержащих флюсов для повышения качества черновой меди // Цветная металлургия. 2003. № 10. С. 13–17.
Yusupkhodjaev A.A., Khojiev Sh.T., Berdiyarov B.T., Yavkochiva D.O., Ismailov J.B. Technology of processing slags of copper production using local secondary technogenic formations // International J. Innovative Technology and Exploring Engineering. 2019. 9. № 11. P. 5461–5471.
Saidova M.S., Karimova T.P., Aribjonova D.E., Matkarimov S.T., Beknazarova G.B., Bakhodirova N.K. Use of clinker reducing potential for reduction of copper losses with waste slags on the converter process // J. Critical Reviews 2020. 7. № 12. P. 593–596.
Chikashi H.M. Influence of slag composition on reduction control and operations of the slag-cleaning furnace at KCM, Zambia // Southern African Pyrometallurgy 2011. № 3. P. 185–198.
Ватолин Н.А., Моисеев Г.К., Трусов Б.Г. Термодинамическое моделирование в высокотемпературных неорганических системах. М.: Металлургия, 1994.
Белов Г.В., Трусов Б.Г. Термодинамическое моделирование химически реагирующих систем. М.: МГТУ им. Н.Э. Баумана, 2013.
Boronenkov V., Zinigrad M., Leontiev L., Pastukhov E., Shalimov M., Shanchurov S. Phase interaction in the metal-oxide melts-gas system. The modeling of structure, properties and processes. Heidelberg, Springer-Verlag, Berlin, 2012.
Sohn H.Y. Process modeling in non-ferrous metallurgy // In: Treatise on Process Metallurgy: Industrial Processes. Oxford: Elsevier Ltd. 2014. P. 701–838.
Тюшняков С.Н., Селиванов Е.Н. Термодинамическое моделирование восстановления цинка из медеплавильного шлака // Бутлеровские сообщения. 2015. 43. № 9. С. 108–115.
Vusikhis A.S., Dmitriev A.N., Kudinov D.Z., Leontiev L.I. The study of liquid and gas phases interaction during the reduction of metal oxides from the melts by gas reductant in bubbled layer // The Third International Conference on Mathematical Modeling and Computer Simulation of Materials Technologies. Ariel, Israel. 2004. P. 1-72-77.
Dmitriev A.N., Vusikhis A.S., Sitnikov V.A., Leontiev L.I., Kudinov D.Z. Thermodynamic modeling of iron oxide reduction by hydrogen from the B2O3–CaO–FeO melt in bubbled layer // Israel J. Chemistry. 2007. 47. № 3–4. P. 299–302.
Вусихис А.С., Леонтьев Л.И., Селиванов Е.Н., Ченцов В.П. Mоделирование процесса газового восстановления металлов из многокомпонентного оксидного расплава в барботируемом слое // Бутлеровские сообщения. 2018. 55. № 7. С. 58–63.
Банных О.А., Будберг П.Б., Алисова С.П. и др. Диаграммы состояния двойных и многокомпонентных систем на основе железа. Металлургия, 1986.
Вайсбурд С.Е. Физико-химические свойства и особенности строения сульфидных расплавов. М.: Металлургия, 1996.
Селиванов Е.Н., Гуляева Р.И., Зелютин Д.Н и др. Влияние скорости охлаждения на структуру шлака от плавки медно-цинковых концентратов в печи Ванюкова // Цветные металлы. 2009. № 12. С. 27–31.
Юсупходжаев А.А., Маткаримов С.Т., Очилдиев К.Т. Малоотходные технологии в медном производстве. Ташкент: ТашГТУ.
Дополнительные материалы отсутствуют.