Акустический журнал, 2021, T. 67, № 1, стр. 55-64
Влияние пористости на статистическое распределение амплитуд обратнорассеянных ультразвуковых импульсов в металломатричных композитах, изготовленных методом реакционного литья
Н. Б. Подымова a, *, А. А. Карабутов b, c, d
a МГУ имени М.В. Ломоносова, физический факультет
119991 Москва, ГСП-1, Ленинские горы 1, стр. 2, Россия
b МГУ имени М.В. Ломоносова, Международный учебно-научный лазерный центр
119991 Москва, ГСП-1, Ленинские горы 1, стр. 62, Россия
c Национальный исследовательский технологический университет “МИСиС”
119991 Москва, Ленинский пр-т 4, Россия
d ИПЛИТ РАН – филиал ФНИЦ “Кристаллография и фотоника” РАН
117342 Москва, ул. Бутлерова 17А, Россия
* E-mail: npodymova@mail.ru
Поступила в редакцию 01.09.2020
После доработки 01.09.2020
Принята к публикации 08.09.2020
Аннотация
Изучено влияние локальной пористости в изотропных дисперсно-упрочненных металломатричных композиционных материалах, изготовленных методом реакционного литья, на статистическое распределение амплитуд обратнорассеянных широкополосных импульсов продольных ультразвуковых волн. Для этой цели применяется специальный лазерный оптико-акустический преобразователь, который позволяет реализовать лазерное возбуждение и пьезоэлектрическую регистрацию ультразвука при одностороннем доступе к образцу или изделию. Исследованы две серии алюмоматричных композиционных материалов: упрочненных только in situ синтезированными Al3Ti интерметаллидными частицами в различной объемной концентрации (0.04–0.115), а также Al3Ti с добавлением наночастиц синтетического алмаза в объемной концентрации 0.002. Последние ускоряют процесс синтеза Al3Ti частиц и приводят к модификации их формы и размеров. Для обеих серий композитов распределение амплитуд обратнорассеянных ультразвуковых импульсов аппроксимируется гауссовской функцией распределения, применимой для большого числа статистически независимых величин. Эмпирически полученная зависимость полуширины этого распределения от локальной пористости композитов двух серий аппроксимируется одной и той же близкой к линейной функцией независимо от размера и концентрации упрочняющих частиц. Эта функциональная зависимость может использоваться для количественно оценки локальной пористости композиционного материала как на стадии его изготовления, так и в процессе эксплуатации деталей и изделий.
ВВЕДЕНИЕ
Металломатричные композиционные материалы (МКМ) обладают рядом уникальных физико-механических характеристик, которые обуславливают их преимущества для изготовления различных ответственных деталей и узлов, таких как, например, автомобильные приводные валы, роторы тормозов высокоскоростных поездов и компоненты авиационных двигателей. Такими характеристиками являются относительно низкий удельный вес в сочетании с высокой прочностью и жесткостью, а также высокой вязкостью разрушения, термостойкостью и износостойкостью [1–3]. Возможности оптимального выбора материалов матрицы и армирующего наполнителя, а также технологии их совмещения и обработки позволяют создать МКМ, наиболее полно отвечающие требованиям конкретных условий эксплуатации деталей и узлов (см., например, [4–7]).
В последние десятилетия успешно развивается производство МКМ методом так называемого реакционного литья − in situ синтеза армирующих фаз непосредственно в процессе изготовления материала. Эти фазы формируются в виде тугоплавких высокопрочных интерметаллидных соединений в результате экзотермических реакций взаимодействия расплава матрицы и добавок реакционно-активных металлов или их оксидов [8–12]. Химические реакции in situ формируют в матрице термодинамически стабильные армирующие фазы, имеющие прочную связь с матрицей за счет лучшего решеточного соответствия, а также свободные от загрязнений поверхности раздела. Однако в таких МКМ возможно появление некоторой “усадочной” пористости наряду с неоднородно распределенной пористостью, образованной газами, растворенными в расплавленной смеси и “захваченными” в материале после кристаллизации [8, 9].
Неравномерное распределение пористости по объему готового материала является основным и наиболее критическим производственным дефектом любых МКМ, изготовленных методом литья. Оно не только приводит к локальному разупрочнению случайных областей в материале [13], но и играет ключевую роль в эволюции процесса повреждения под действием внешних нагрузок, поскольку в металлических материалах в условиях нагружения поры действуют как центры зарождения и развития трещин (см., например, [14]). Таким образом, разработка оперативных неразрушающих методов контроля и количественной оценки локальной пористости литых МКМ имеет большое значение как для совершенствования технологии их изготовления, так и для мониторинга изменений структуры и оценки остаточного ресурса материала в процессе эксплуатации изделий.
Среди различных современных методов неразрушающего контроля металлов, сплавов и МКМ наиболее популярными являются ультразвуковые методы благодаря своей относительной простоте, оперативности, безопасности и высокой чувствительности к наличию пористости. Последнее обусловлено высокой эффективностью рассеяния ультразвуковых волн на газовых порах, существенно зависящей от соотношения размеров пор и длины зондирующей волны (см., например, [15–17]). Таким образом, количественная оценка пористости в МКМ, формируемой порами размером от десятков микрометров до нескольких миллиметров в зависимости от условий изготовления композита, требует измерения характеристик рассеянных ультразвуковых волн в широком спектральном диапазоне от долей до десятков мегагерц [18]. Для реализации таких измерений в указанном частотном диапазоне целесообразно применение лазерного термооптического механизма возбуждения ультразвука – оптико-акустического эффекта [19]. При поглощении импульсов традиционных лазеров с модуляцией добротности в металлах, сплавах и композиционных материалах амплитуда возбуждаемых зондирующих ультразвуковых импульсов может достигать десятков атмосфер при длительности импульса от единиц до сотен наносекунд (в зависимости от длительности лазерного импульса и теплофизических характеристик поглощающей среды). Применение таких ультразвуковых импульсов позволяет существенно повысить достоверность диагностики структуры, а также точность измерений механических и акустических свойств различных твердых тел, в том числе сильно поглощающих и рассеивающих ультразвук композиционных материалов (см., например, [20–25]).
Целью настоящей работы является разработка лазерной оптико-акустической методики количественной оценки локальной пористости металломатричных композиционных материалов, полученных методом реакционного литья на основе алюминия, упрочненного in situ синтезированными интерметаллидными частицами Al3Ti в различной концентрации, а также модифицированного наночастицами синтетического алмаза. Методика основана на анализе статистического распределения амплитуд широкополосных импульсов продольных ультразвуковых волн, обратнорассеянных на случайно распределенных порах в прозвученном объеме композита и зарегистрированных при одностороннем доступе к образцу. Основная идея заключается в получении эмпирического функционального соотношения между локальной пористостью в прозвученном участке образца и шириной статистического распределения амплитуд обратнорассеяннных импульсов в этом участке для МКМ с различной объемной концентрацией интерметаллидных частиц Al3Ti. Поскольку при этом не требуется прецизионных измерений толщины образцов, данная методика может применяться для оперативной диагностики возникновения и роста локальной пористости в изделиях сложной формы в процессе эксплуатации.
Таблица 1.
Характеристики исследованных образцов Al/Al3Ti композитов
№ образца | Время выдержки расплава τ, мин |
Объемная концентрация компонентов | Расчетная плотность ${{\rho }_{0}}$, кг/м3 |
Измеренная плотность ρ, кг/м3 |
Средняя пористость $\left\langle P \right\rangle $, % |
|||
---|---|---|---|---|---|---|---|---|
Al | Ti | Al3Ti | C | |||||
1-1 | 0 | 0.94 | 0.02 | 0.04 | – | 2751 | 2741 ± 14 | 0.36 ± 0.51 |
1-2 | 20 | 0.929 | 0.016 | 0.055 | – | 2753 | 2685 ± 14 | 2.47 ± 0.51 |
1-3 | 60 | 0.902 | 0.006 | 0.092 | – | 2762 | 2725 ± 14 | 1.34 ± 0.51 |
1-4 | 90 | 0.885 | 0.000 | 0.115 | – | 2766 | 2748 ± 14 | 0.65 ± 0.51 |
2-1 | 0 | 0.946 | 0.022 | 0.03 | 0.002 | 2751 | 2739 ± 14 | 0.44 ± 0.51 |
2-2 | 20 | 0.937 | 0.019 | 0.042 | 0.002 | 2753 | 2661 ± 14 | 3.34 ± 0.51 |
2-3 | 60 | 0.913 | 0.01 | 0.075 | 0.002 | 2759 | 2634 ± 14 | 4.53 ± 0.51 |
2-4 | 90 | 0.891 | 0.003 | 0.104 | 0.002 | 2766 | 2627 ± 14 | 5.02 ± 0.51 |
ИССЛЕДОВАННЫЕ ОБРАЗЦЫ КОМПОЗИТОВ
Исследованные МКМ (далее Al/Al3Ti композиты) были изготовлены методом реакционного литья и подробно описаны в [11]. Первая серия образцов (1) была получена путем механического замешивания порошка титана со средним размером частиц 200–400 мкм (объемная концентрация 0.03) в расплав алюминия марки А99 (ГОСТ 11069-2001). Вторая серия образцов (2) отличалась от первой добавлением в смесь расплава Al с порошком Ti частиц синтетического алмаза со средним размером порядка 50 нм и объемной концентрацией 0.002. Для обеих серий время выдержки τ полученной смеси при температуре 750°С перед разливкой в графитовые формы составляло 0, 20, 60 и 90 минут для четырех различных образцов композитов в каждой серии. Введение в расплав алюминия реакционно-активного титана приводит в результате in situ экзотермической реакции к образованию интерметаллидных фаз согласно фазовой диаграмме состояния Al–Ti; при данных условиях образуется преимущественно триалюминид титана Al3Ti. При увеличении времени выдержки смеси в расплаве растет объемная концентрация и средний размер частиц Al3Ti в полученном композите [11]. Для одного и того же времени выдержки добавление наночастиц алмаза приводит к ускорению роста и модификации распределения по размерам частиц Al3Ti в образцах серии 2 по сравнению с образцами серии 1. Также влияние наночастиц алмаза проявляется в улучшении трибологических характеристик полученных композитов [11].
Все исследованные образцы представляли собой плоскопараллельные шлифованные диски диаметром D = (50 ± 0.1) мм и толщиной H = (5 ± 0.005) мм. Пористость $\left\langle P \right\rangle $ (объемная концентрация газовых пор) в образце, усредненная по всему его объему, рассчитывалась как $\left\langle P \right\rangle = \left( {1 - {\rho \mathord{\left/ {\vphantom {\rho {{{\rho }_{0}}}}} \right. \kern-0em} {{{\rho }_{0}}}}} \right) \times 100\% $, где фактическая плотность образца ρ определялась по результатам его гидростатического взвешивания в дистиллированной воде, плотность ${{\rho }_{0}}$ твердой фазы образца (без пор) рассчитывалась по известным плотностям и объемным концентрациям компонентов конкретного композита согласно правилу смесей. Погрешности при расчете пористости образцов определялись погрешностью при вычислении их плотности (14 кг/м3), которая, в свою очередь, есть результат суммарной погрешности измерений массы и габаритов образцов. Характеристики исследуемых образцов двух серий представлены в таблице; первая цифра в номере образца соответствует серии, вторая – конкретному времени выдержки смеси в расплаве. Во всех образцах обеих серий распределение упрочняющих частиц по объему было практически равномерным [11], поэтому образцы считались изотропными по акустическим свойствам.
Распределение пористости во всех образцах композитов серии 1 было практически равномерным, что подтверждалось лазерно-ультразвуковыми измерениями дисперсии фазовой скорости продольных акустических волн в пяти произвольно выбранных областях в каждом образце [26]. Результаты лазерно-ультразвукового определения локальной пористости P в пяти произвольно выбранных областях каждого образца серии 2 тем же методом представлены на рис. 1. Видно, что распределение пористости в образцах этой серии существенно неравномерное. По-видимому, это обусловлено неоднородным увеличением скорости экзотермической реакции синтеза Al3Ti в локальных областях расплава при добавлении наночастиц алмаза и соответствующим неоднородным перегревом этих областей, приводящим к образованию избыточной локальной пористости в кристаллизованном материале.
ЛАЗЕРНЫЙ ОПТИКО-АКУСТИЧЕСКИЙ ПРЕОБРАЗОВАТЕЛЬ
Блок-схема экспериментальной установки для реализации количественной оценки локальной пористости в МКМ при одностороннем доступе к образцу или изделию представлена на рис. 2.
Рис. 2.
Блок-схема экспериментальной установки с лазерно-ультразвуковым преобразователем для количественной оценки локальной пористости металломатричных композиционных материалов.
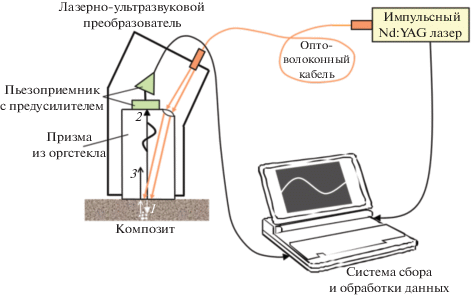
Для лазерного термооптического возбуждения широкополосных ультразвуковых импульсов и их пьезоэлектрической регистрации в эхо-импульсном режиме использовался лазерно-ультразвуковой преобразователь, подробно описанный в [27, 28]. Лазерный импульс, передаваемый по оптоволоконному кабелю, падает на лицевую поверхность образца или изделия из МКМ; при поглощении этого импульса происходит нестационарный нагрев и последующее тепловое расширение приповерхностного слоя композита. Это приводит к возникновению двух одинаковых импульсов продольных ультразвуковых волн, распространяющихся в противоположных направлениях. Один импульс, отмеченный цифрой 1 на рис. 2, распространяется “вперед” вглубь композита (зондирующий импульс), а второй (опорный) импульс 2 распространяется “назад” через призму-звукопровод к широкополосному пьезоприемнику. Акустический контакт обеспечивается посредством тонкого слоя дистиллированной воды между лицевыми поверхностями призмы и образца при их плотном ручном прижиме друг к другу.
Для возбуждения ультразвука в работе использовался Nd:YAG лазер с диодной накачкой и модуляцией добротности: энергия в импульсе 95–100 мкДж, характерная длительность импульса 9–10 нс, частота повторения импульсов 1 кГц, поперечное распределение интенсивности в лазерном пучке близко к гауссовому. Лазерный пучок, выходящий из встроенного в преобразователь разъема оптоволоконного кабеля, формируется собирающей линзой в практически коллимированный пучок с характерным радиусом ${{a}_{0}}$ ≈ 2–3 мм на облучаемой поверхности композита. Характерный радиус зондирующего ультразвукового пучка на лицевой поверхности композита совпадает с радиусом лазерного пучка и равен ${{a}_{0}}$. Для параметров лазерного излучения, используемого в экспериментах, реализуется термоупругий механизм возбуждения ультразвука без повреждения облучаемой поверхности композита [19].
При распространении в композите зондирующий импульс 1 частично рассеивается в обратном направлении на случайно распределенных неоднородностях структуры материала в прозвучиваемом объеме образца (газовые поры, упрочняющие частицы, зерна-кристаллиты матрицы). Совокупность таких рассеянных ультразвуковых импульсов обозначена цифрой 3 на рис. 2 и представляет собой так называемый “структурный шум”. Если пористость не превышает нескольких процентов, в композите реализуется режим однократного рассеяния ультразвуковых волн на порах (см., например, [29] и имеющиеся там ссылки). В этом случае полная амплитуда рассеянного сигнала от каждой конкретной области в образце является когерентной суммой амплитуд сигналов, рассеянных на всех порах, локализованных в этой области. Другими словами, амплитуда обратнорассеянного сигнала зависит от объемной концентрации пор (пористости).
МЕТОДИКА ОБРАБОТКИ УЛЬТРАЗВУКОВЫХ СИГНАЛОВ
На рис. 3а показаны примеры нормированных временных профилей U(t) ультразвуковых сигналов, возбуждаемых при поглощении лазерного импульса в произвольно выбранной области практически беспористой матрицы из алюминия и в областях с различной пористостью P в образце № 2–3 (области 2 и 3 на рис. 1). Зарегистрированный профиль опорного импульса определяется в основном поглощением и дифракцией ультразвуковых волн в призме-звукопроводе [19]. Незначительное отличие на временном отрезке 3.5–4 мкс сигналов, возбуждаемых в матрице и двух областях образца, обусловлено возможной вариацией акустического контакта при прижиме призмы к поверхности образца, а также некоторой нестабильностью временного профиля интенсивности лазерных импульсов. Влияние последнего фактора обусловлено тем, что при данных условиях временной профиль возбуждаемого ультразвукового импульса в композите повторяет огибающую интенсивности лазерного импульса [19].
Рис. 3.
(a) – Нормированные временные профили ультразвуковых импульсов, возбуждаемых в матрице из алюминия и двух областях образца Al/Al3Ti композита с различной пористостью P; на врезке в увеличенном масштабе показан структурный шум. (б) – Нормированный амплитудный спектр зарегистрированного опорного сигнала, возбуждаемого в алюминиевой матрице.
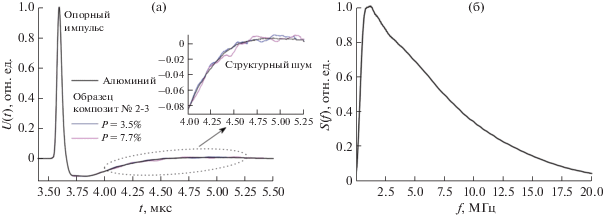
На рис. 3б показан пример нормированного амплитудного спектра S(f) зарегистрированного опорного ультразвукового импульса, возбуждаемого в алюминиевой матрице (f – частота ультразвуковой волны). Точно такой же спектр имеет зондирующий импульс, возбуждаемый в приповерхностном слое любого образца МКМ и распространяющийся вглубь этого образца. Рабочая полоса частот по уровню 1/e составляет 0.25–9 МГц.
Характерный размер интерметаллидных частиц во всех исследуемых образцах (5–20 мкм [11]) много меньше длин ультразвуковых волн λ для рабочей полосы частот (λ ≈ 1.3 мм на частоте f = 5 МГц, фазовая скорость продольных ультразвуковых волн в алюминиевой матрице C = 6350 м/с, в Al/Al3Ti композитах C = 6250–6550 м/с [26]). Поэтому во всех образцах реализуется рэлеевский режим рассеяния ультразвука на частицах (см., например, [30]). В приближении однократного рассеяния коэффициент рассеяния на неоднородностях на определенной частоте определяется как произведение поперечного сечения рассеяния на этой частоте для отдельной неоднородности на число неоднородностей в единице объема. Мы оценили сечение рассеяния продольных ультразвуковых волн на частице Al3Ti максимального радиуса (≈10 мкм) на частоте верхней границы рабочей полосы (9 МГц) с использованием формул (27) и (28) из [30], а также рассчитали соответствующий коэффициент рассеяния α на этой частоте для максимальной объемной концентрации частиц Al3Ti (0.115). Полученный результат составил α ≈ 0.01 см–1. Очевидно, в рабочей полосе частот практически не будет зарегистрировано ультразвуковых сигналов, рассеянных на частицах Al3Ti. В то же время сигналы, рассеянные на порах с характерными размерами в десятки и сотни микрометров, типичными для литых алюминиевых сплавов [29], могут достоверно регистрироваться в рабочей полосе частот используемого лазерно-ультразвукового преобразователя. Таким образом, зарегистрированный структурный шум в исследованных композитах формируется сигналами от пор различных размеров, эффективно рассеивающих ультразвуковые волны в рабочей полосе частот.
Рабочее временное окно для полного ультразвукового сигнала на рис. 3а соответствует времени пробега зондирующего импульса от границы призма‑образец до тыльной поверхности образца и обратно. Для дальнейшего анализа не требуется регистрировать сигнал, отраженный от тыльной поверхности образцов или изделий; соответственно, отсутствует требование на наличие у них плоскопараллельных поверхностей. При распространении в образце зондирующий импульс частично рассеивается на порах, расположенных на разных глубинах в прозвучиваемой области образца. Обратнорассеянные сигналы регистрируются как нерегулярные пики на “хвосте” опорного импульса (врезка на рис. 3а) и образуют структурный шум. Амплитуда A обратнорассеянного сигнала в конкретный момент времени t зависит от размера и концентрации пор, локализованных на глубине d = Ct/2, где C − фазовая скорость продольных ультразвуковых волн в исследуемом образце [27].
Для количественной оценки влияния пористости на амплитудное распределение обратнорассеянных ультразвуковых сигналов предлагается анализировать разность между сигналом структурного шума в каждом конкретном образце композита и сигналом, зарегистрированным на том же временном интервале от практически беспористой матрицы из алюминия. Такая разность позволяет исключить влияние дифракции и поглощения ультразвука в призме-звукопроводе на зарегистрированную амплитуду рассеянных сигналов, поскольку при распространении в призме сигналы и от матрицы, и от композита дифрагируют и поглощаются одинаково. Анализ указанной разности сигналов начинается от 4 мкс по временной шкале (см. рис. 3а) для исключения возможного расхождения реализаций временных профилей опорных сигналов, возбуждаемых в матрице и образцах. Время t = 4 мкс соответствует приходу сигнала с глубины порядка 1.3 мм в композитах с учетом времени пробега ультразвука в призме (3.6 мкс). Таким образом, диапазон сканирования по глубине в исследуемых композитах составляет 1.3–5 мм (5 мм – толщина всех образцов). На рис. 4 показана соответствующая разность сигналов, полученная для двух областей образца № 2–3 с пористостями 3.5 и 7.7% и усредненная по 20-ти временным точкам; по оси X отложена глубина d в образце. Здесь же показана так называемая “базовая линия”, соответствующая разности двух сигналов, зарегистрированных в двух произвольно выбранных областях беспористого образца матрицы из алюминия. Ненулевая разность обусловлена электрическими шумами и шумами дискретизации сигнала, а также возможной вариацией акустического контакта для разных реализаций, и представляет собой “аппаратный шум”, детектируемый даже в беспористых материалах.
Рис. 4.
Распределения обратнорассеянных сигналов по глубине d в двух областях образца Al/Al3Ti композита с различной пористостью P. “Базовая линия” соответствует разности сигналов в двух областях образца алюминиевой матрицы.
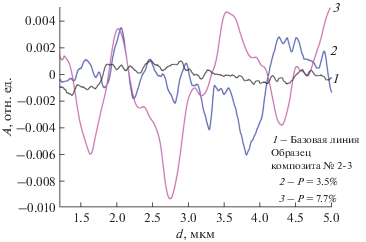
На рис. 4 видно, что увеличение пористости приводит к возрастанию амплитуды обратнорассеянных сигналов. Это объясняется принципом суперпозиции: ультразвуковой сигнал с амплитудой A, приходящий с каждой конкретной глубины в прозвучиваемом участке композита, представляет собой сумму сигналов элементарных актов рассеяния на порах, локализованных на этой глубине. Чем выше пористость, тем больше амплитуда A обратнорассеянных сигналов, “производимых” каждым поперечным сечением образца при прохождении зондирующего ультразвукового импульса. Таким образом, чем выше пористость образца, тем больше ширина распределения N(A), где N – это суммарное число сигналов (точек) с данной конкретной амплитудой A на всем временном треке зарегистрированного структурного шума. Иллюстрация этих рассуждений приведена на рис. 5, где показаны распределения N(A) для структурного шума в обсуждаемых выше областях образца № 2–3 с пористостями 3.5 и 7.7%. Как видно, амплитудное распределение N(A) для более пористой области практически в два раза шире, поскольку оно содержит сигналы с амплитудами, вообще отсутствующими в структурном шуме от менее пористой области. Также здесь показано амплитудное распределение для “базовой линии”, соответствующей разности обратнорассеянных сигналов в двух областях матрицы из алюминия (рис. 4).
Рис. 5.
Распределения амплитуд обратнорассеянных ультразвуковых сигналов в беспористой матрице из алюминия и двух областях образца Al/Al3Ti композита с различной пористостью P. Сплошные линии – гауссовские аппроксимации (1) соответствующих распределений.
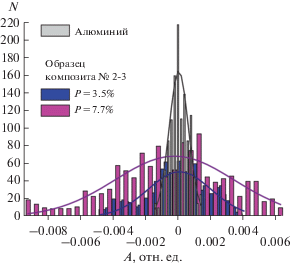
Для реализации количественной оценки пористости предлагается использовать соотношение между величиной пористости P и полушириной ΔA по уровню 1/e амплитудного распределения N(A) для всех исследованных образцов композитов. Поскольку акты рассеяния на случайно распределенных порах являются статистически независимыми, согласно центральной предельной теореме экспериментально полученные распределения N(A) могут быть аппроксимированы гауссовской функцией распределения
где y соответствует числу N сигналов с данной амплитудой x на всем временном треке структурного шума, ΔA – полуширина распределения по уровню 1/e. Такие гауссовские аппроксимации всех рассмотренных выше распределений показаны на рис. 5 сплошными линиями.ЭКСПЕРИМЕНТАЛЬНЫЕ РЕЗУЛЬТАТЫ И ОБСУЖДЕНИЕ
На рис. 6 представлены распределения амплитуд N(A) обратнорассеянных сигналов в образцах Al/Al3Ti композитов серии 1. Показанные распределения для каждого образца являются результатом усреднения по распределениям, полученным в пяти случайно выбранных областях (так называемое усреднение по ансамблю). Такое усреднение правомерно, поскольку, как указывалось выше, в образцах серии 1 наблюдалось равномерное распределение пористости. Масштаб на рис. 6 по оси X, соответствующей амплитудaм обратнорассеянных сигналов, выбран одинаковым для всех распределений для наглядной демонстрации их уширения при возрастающей пористости образца.
Рис. 6.
Распределения амплитуд обратнорассеянных ультразвуковых сигналов в образцах Al/Al3Ti композитов серии 1: (a) – 1-1, (б) – 1-2, (в) – 1-3, (г) – 1-4. Значения средней пористости $\left\langle P \right\rangle $ образца и параметры соответствующих гауссовских аппроксимаций показаны на каждом рисунке.
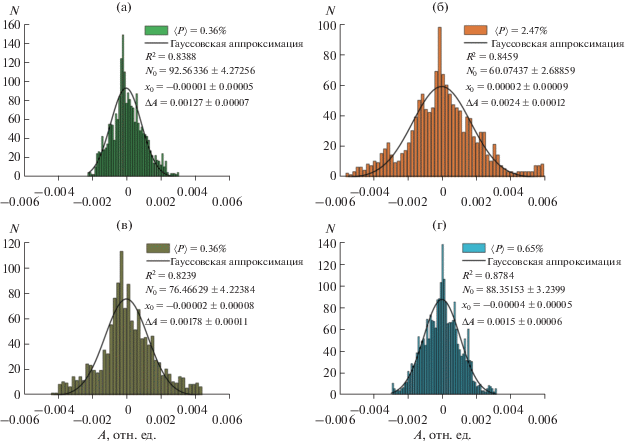
Для образцов серии 2 аналогичные распределения N(A) были получены для каждой из пяти областей с измеренной локальной пористостью P в каждом образце. На рис. 7 показаны примеры таких распределений, полученных без усреднения по ансамблю. Распределения N(A) для областей 2 и 3 в образце № 2–3 были рассмотрены выше при описании процедуры обработки ультразвуковых сигналов.
Рис. 7.
Примеры распределений амплитуд обратнорассеянных ультразвуковых сигналов в образцах Al/Al3Ti композитов серии 2: (a) – 2-1, (б) – 2-2, (в) – 2-3, (г) – 2-4. Значения локальной пористости P в прозвученной области образца и параметры соответствующих гауссовских аппроксимаций показаны на каждом рисунке.
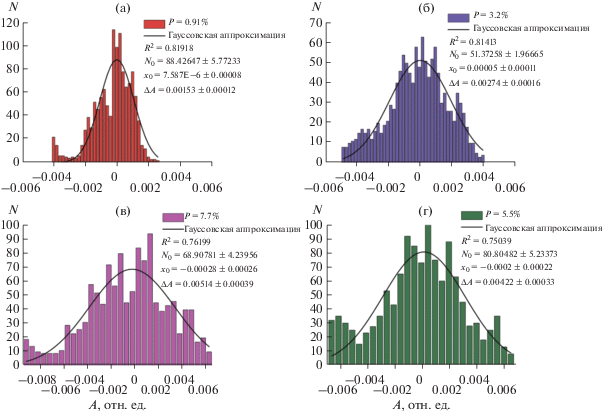
Результаты, представленные на рис. 6 и 7, подтверждают, что для обеих серий образцов композитов ширина распределений амплитуд обратнорассеянных ультразвуковых сигналов не зависит от объемной концентрации интерметаллидных частиц Al3Ti, а определяется исключительно пористостью в прозвученной области образца. Так, увеличение локальной пористости в ≈ 8 раз приводит к возрастанию полуширины распределения ΔA практически в три раза при одинаковой максимальной концентрации Al3Ti в образцах № 1–4 и № 2–4 (рис. 6г и 7г соответственно). Также для образца № 1–4 с максимальной объемной концентрацией частиц Al3Ti и практически минимальной пористостью величина ΔA существенно меньше (рис. 6г), чем для образцов № 1–2 и № 1–3 с меньшими концентрациями Al3Ti, но с большими пористостями (рис. 6б и 6в).
На рис. 8 показана экспериментально полученная зависимость ΔA(P) (точки) для всех прозвученных областей с различной пористостью в образцах Al/Al3Ti композитов обеих серий; величины ΔA были взяты из результатов аппроксимации гауссовской функцией (1) экспериментальных распределений N(A). В качестве погрешностей для ΔA были взяты соответствующие данные всех аппроксимаций, погрешности для средней пористости образцов серии 1 соответствуют данным из таблицы, для локальной пористости образцов серии 2 – данным рис. 1. Величина ΔA при P = 0 соответствует полуширине амплитудного распределения “аппаратного шума”, полученного для матрицы из алюминия. Видно, что для двух разных серий образцов экспериментальная зависимость ΔA(P) в пределах погрешностей может быть аппроксимирована по методу наименьших квадратов одной и той же функцией, близкой к линейной:
Рис. 8.
Соотношение между полушириной амплитудного распределения обратнорассеянных ультразвуковых сигналов и локальной пористостью в образцах Al/Al3Ti композитов двух серий. Точки – экспериментальные результаты, символ (*) для P = 0 соответствует полуширине распределения “аппаратного шума”, сплошная линия – функция аппроксимации (2).
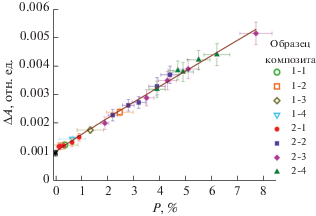
Относительная погрешность определения параметров аппроксимации в (2) не превышает 8%. В выражении (2) значение независимой переменной x соответствует пористости P образца, выраженной в процентах, значение переменной y соответствует полуширине распределения ΔA.
Для расчета фактической пористости P в прозвученной области композита функция (2) была преобразована в зависимость P(ΔA):
из которой величина P определяется в процентах.Функциональные зависимости (2) и (3) были получены для образцов Al/Al3Ti композитов толщиной 5 мм. Поэтому они могут использоваться для количественной оценки локальной пористости в прозвученных областях образцов и изделий практически такой же толщины и изготовленных из того же материала. При использовании данной методики для оценки пористости в композитных изделиях большей или меньшей толщины аналогичные “калибровочные” зависимости (2) и (3) должны быть получены для образцов-свидетелей соответствующей толщины.
ЗАКЛЮЧЕНИЕ
В работе проведены экспериментальные исследования влияния локальной пористости в изотропных дисперсно-упрочненных металломатричных композиционных материалах, изготовленных методом реакционного литья, на статистическое распределение амплитуд обратнорассеянных широкополосных импульсов продольных ультразвуковых волн. Предложенная методика позволяет исследовать образцы или изделия при одностороннем доступе к объекту контроля без измерения его толщины и регистрации донных ультразвуковых эхо-сигналов. Исследованы образцы алюмоматричных композиционных материалов с различной объемной концентрацией (0.04–0.115) in situ синтезированных интерметаллидных частиц Al3Ti и пористостью (0.13–7.7%), равномерно и неравномерно распределенной по объему образцов. Ширина статистического распределения амплитуд обратнорассеянных ультразвуковых сигналов (структурного шума), аппроксимируемого гауссовской функцией, определяется исключительно величиной пористости в прозвученной области материала и не зависит от объемной концентрации упрочняющих частиц в этой области. Для двух серий исследованных образцов Al/Al3Ti композитов полученное эмпирическое соотношение между полушириной амплитудного распределения структурного шума и пористостью в прозвученной области композита аппроксимируется одной и той же функцией, близкой к линейной. С использованием этой функции была получена расчетная формула для определения локальной пористости в Al/Al3Ti композитах. Локальность тестирования в поперечном направлении (по плоскости образца) составляет 2–3 мм, что дает возможность выявлять участки с повышенной пористостью в сильно неоднородных по структуре материалах. Предложенная методика может использоваться для обнаружения потенциально опасных дефектных областей с повышенной пористостью в металломатричных композиционных материалах перед изготовлением деталей и изделий, а также может быть интегрирована в систему оперативного мониторинга структуры материала в процессе эксплуатации изделий.
Список литературы
Clyne T.W., Withers P.J. An introduction to metal matrix composites. Cambridge: Cambridge University Press, 1995. 528 p.
Mileiko S.T. Metal and ceramic based composites. Amsterdam: Elsevier, 1997. 691 p.
Чернышова Т.А., Курганова Ю.А., Кобелева Л.И., Болотова Л.К. Литые дисперсно-упрочненные алюмоматричные композиционные материалы: изготовление, свойства, применение. Ульяновск: УлГТУ, 2012. 295 с.
Lloyd D.J. Particle reinforced aluminium and magnesium matrix composites // Int. Mater. Rev. 1994. V. 39. P. 1–23.
Kainer K.U. Basics of metal matrix composites. In: Kainer K.U. (ed.) Metal matrix composites: custom-made materials for automotive and aerospace engineering. Weinheim: Wiley-VCH Verlag GmbH & Co, 2006. P. 1–54.
Чернышова Т.А., Михеев Р.С., Калашников И.Е., Акимов И.В., Харламов Е.И. Разработка и апробация композиционных материалов систем Al–SiC, Al–TiC в узлах трения нефтедобывающего оборудования // Физика и химия обработки материалов. 2010. № 5. С. 78–86.
Коновалов А.В., Смирнов С.В. Современное состояние и направления исследований металломатричных композитов системы Al/SiC (обзор) // Конструкции из композиционных материалов. 2015. № 1. С. 30–35.
Tjong S.C., Ma Z.Y. Microstructural and mechanical characteristics of in situ metal matrix composites // Mater. Sci. Eng. R. 2000. V. 29. P. 49–113.
Varin R.A. Intermetallic-reinforced light-metal matrix in situ composites // Metall. Mater. Trans. A. 2002. V. 33. P. 193–201.
Wang X., Jha A., Brydson R. In situ fabrication of Al3Ti particle reinforced aluminium alloy metal–matrix composites // Mater. Sci. Eng. A. 2004. V. 364. P. 339–345.
Чернышова Т.А., Болотова Л.К., Калашников И.Е., Кобелева Л.И., Быков П.А. Влияние тугоплавких наночастиц на модификацию структуры металломатричных композитов // Металлы. 2007. № 3. С. 79–84.
Мурашева В.В., Бурковская Н.П., Севостьянов Н.В. Способы получения высокотемпературных Nb–Si in-situ композитов (обзор) // Конструкции из композиционных материалов. 2015. № 2. С. 27–38.
Campbell J. Porosity. In: Complete Casting Handbook. Metal Casting Processes, Metallurgy, Techniques and Design. Amsterdam: Butterworth-Heinemann, Elsevier, 2015. P. 341–415.
Rohatgi P.K., Alaraj S., Thakkar R.B., Daoud A. Variation in fatigue properties of cast A359-SiC composites under total strain controlled conditions: Effects of porosity and inclusions // Compos. Part A. 2007. V. 38. № 8. P. 1829–1841.
Vary A. Material property characterization. In: Nondestructive Testing Handbook. Ultrasonic Testing. Ed. Moore P.O. Columbus: ASTM, 2007. P. 365−431.
Глушков Е.В., Глушкова Н.В., Фоменко С.И. Влияние пористости на характеристики волн рэлеевского типа в многослойном полупространстве // Акуст. журн. 2011. Т. 57. № 2. С. 234−245.
Кольцова И.С., Хомутова А.С., Дейнега М.А. Скорость ультразвуковых волн при структурных перестройках дисперсных сред // Акуст. журн. 2016. Т. 62. № 2. С. 187−193.
Fitting D.W., Adler L. Ultrasonic spectral analysis for nondestructive evaluation. New York: Plenum Press, 1981. 354 p.
Гусев В.Э., Карабутов А.А. Лазерная оптоакустика. М.: Наука, 1991. 304 с.
Карабутов А.А., Подымова Н.Б. Неразрушающий контроль усталостных изменений структуры композитов лазерным ультразвуковым методом // Механика композитных материалов. 1995. Т. 31. № 3. С. 405–410.
Девиченский А.Ю., Ломоносов А.М., Жаринов С.Е., Михалевич В.Г., Лямшев М.Л., Иванова Т.О., Меркулова Н.С. Диагностика остаточных напряжений в металлах с помощью широкополосных поверхностных акустических импульсов // Акуст. журн. 2009. Т. 55. № 1. С. 39–46.
Калашников И.Е., Подымова Н.Б., Карабутов А.А., Болотова Л.К., Кобелева Л.И., Колмаков А.Г. Локальные упругие модули дисперсно-наполненных композиционных материалов на основе баббита Б83, изготовленных методами порошковой металлургии // Неорганические материалы. 2016. Т. 52. № 4. С. 473–478.
Карабутов А.А., Подымова Н.Б. Влияние пористости на дисперсию фазовой скорости продольных акустических волн в изотропных металломатричных композитах // Акуст. журн. 2017. Т. 63. № 3. С. 265–274.
Жаринов А.Н., Карабутов А.А., Миронова Е.А., Пичков С.Н., Саватеева Е.В., Симонова В.А., Шишулин Д.Н. Лазерно-ультразвуковое исследование остаточных напряжений в трубах из аустенитной стали // Акуст. журн. 2019. Т. 65. № 3. С. 372–381.
Воробьев Р.И., Сергеичев И.В., Карабутов А.А., Миронова Е.А., Саватеева Е.В., Ахатов И.Ш. Применение оптоакустического метода для оценки влияния пустот на трещиностойкость конструкционных углепластиков // Акуст. журн. 2020. Т. 66. № 2. С. 148–153.
Podymova N.B., Kalashnikov I.E., Bolotova L.K., Kobeleva L.I. Laser-ultrasonic nondestructive evaluation of porosity in particulate reinforced metal-matrix composites // Ultrasonics. 2019. V. 99. P. 105959.
Karabutov A.A., Podymova N.B. Nondestructive porosity assessment of CFRP composites with spectral analysis of backscattered laser-induced ultrasonic pulses / J. Nondestruct. Eval. 2013. V. 32. № 3. P. 315–324.
Соколовская Ю.Г., Подымова Н.Б., Карабутов А.А. Лазерный оптико-акустический метод количественной оценки пористости углепластиков на основе измерения их акустического импеданса // Акуст. журн. 2020. Т. 66. № 1. С. 86–94.
Adler L., Rose J.H., Mobley C. Ultrasonic method to determine gas porosity in aluminum alloy castings: Theory and experiment // J. Appl. Phys. 1986. V. 59. P. 336–347.
Ying C.F., Truell R. Scattering of a plane longitudinal wave by a spherical obstacle in an isotropically elastic solid // J. Appl. Phys. 1956. V. 27. P. 1086–1097.
Дополнительные материалы отсутствуют.
Инструменты
Акустический журнал