Доклады Российской академии наук. Химия, науки о материалах , 2021, T. 501, № 1, стр. 43-48
Синтез керамики Ta4HfC5 с субмикронной структурой методом электротеплового взрыва под давлением
В. А. Щербаков 1, *, А. Н. Грядунов 1, И. Е. Семенчук 1, Д. Ю. Ковалев 1, А. Е. Сычев 1, член-корреспондент РАН М. И. Алымов 1
1 Институт структурной макрокинетики
и проблем материаловедения Российской академии наук им. А.Г. Мержанова
142432 Черноголовка, Московская обл., Россия
* E-mail: vladimir@ism.ac.ru
Поступила в редакцию 11.08.2021
После доработки 08.11.2021
Принята к публикации 11.11.2021
Аннотация
Методом электротеплового взрыва под давлением из порошковой смеси 4Ta + Hf + 5С получена ультратугоплавкая керамика Ta4HfC5 с субмикронной структурой. Исследовано влияние длительности механической активации смеси порошков 4Ta + Hf на структуру образующегося прекурсора. Показано, что при механической активации в гексане в течение 40–60 мин происходит аморфизация металлов и зарождение кристаллитов карбидной фазы с кубической структурой. Это позволило в процессе электротеплового взрыва синтезировать однофазный твердый раствор карбидов тантала и гафния с субмикронной структурой.
ВВЕДЕНИЕ
Карбиды тантала и гафния, обладающие рекордно высокими температурами плавления и высокой прочностью, представляют интерес для использования в аэрокосмической, ядерной, металлообрабатывающей промышленности и др. Характерная особенность этих карбидов – образование непрерывного ряда твердых растворов, физико-механические свойства которых превосходят характеристики монокарбидов [1]. К данному классу ультратугоплавких керамик относятся твердые растворы на основе системы ТаС–HfC [2, 3]. В работах [3–5] установлено, что максимальная температура плавления твердого раствора Ta4HfC5 составляет ~3990°C. Высокая тугоплавкость, электрохимическая активность и стабильность твердого раствора TaC–HfC позволяют использовать его в аэрокосмической технике, энергетике и катализе [6, 7].
Керамические материалы на основе твердых растворов карбидов получают в основном методом горячего изостатического прессования (ГИП) [3, 8, 10], искровым плазменным спеканием (ИПС) [1, 2, 10], комбинированным методом самораспространяющегося высокотемпературного синтеза (СВС) ИПС [10, 11] и золь-гель методом [12]. Все эти методы являются энергозатратными и требуют сложного оборудования. Ранее был разработан эффективный одностадийный метод получения ультратугоплавких керамик [13], сочетающий экзотермический синтез в режиме электротеплового взрыва (ЭТВ) и консолидацию горячего продукта в условиях квазиизостатического сжатия. При ЭТВ происходит нагрев реакционной смеси за счет пропускания тока. При достижении температуры воспламенения инициируется экзотермическое взаимодействие реагентов в объеме смеси. Одновременно с воспламенением смеси к образцу прикладывается давление, в результате которого происходит консолидация горячего продукта. Метод обладает высокой эффективностью, так как позволяет исключить промежуточные стадии синтеза монокарбидов, их измельчения и фракционирования с последующим горячим прессованием или искровым плазменным спеканием.
Особенностью этого процесса является практически безынерционный нагрев синтезируемого продукта до температуры, обеспечивающей полное превращение исходных реагентов в конечный продукт равновесного состава и его эффективную консолидацию. Ранее этот метод использовали для синтеза двойных карбидов Ta4ZrC5 и Hf4ZrC5 [13].
Цель работы заключалась в получении методом ЭТВ под давлением консолидированной ультратугоплавкой керамики Ta4HfC5 с субмикронной структурой, включающей использование коммерческих металлов порошков, предварительно подвергнутых механоактивации (МА) в планетарной мельнице.
Реакционные смеси готовили с использованием коммерческих порошков тантала (марка ТаПМ-5Б, дисперсность <6 мкм; Россия), гафния (марка ГФМ‑1, дисперсность 60–80 мкм; Россия) и сажи (марка П804-Т, дисперсность <0.2 мкм; Россия). Соотношение компонентов смеси рассчитывали исходя из реакции:
(1)
$4({\text{Ta}} + {\text{C}}) + ({\text{Hf}} + {\text{C}}) \to {\text{T}}{{{\text{a}}}_{{\text{4}}}}{\text{Hf}}{{{\text{C}}}_{5}}.$Смешивание порошков проводили в две стадии. На первой стадии порошки Ta и Hf смешивали в гексане в течение 5, 20, 40 и 60 мин в шаровой планетарной мельнице АГО-2 (Россия) при скорости вращения 2220 об. мин–1. Материал мельничных барабанов – сталь 40X13 (Россия), шаров – сталь ШX-15 (Россия). В каждый барабан объемом 150 мл загружали 30 г смеси 4Ta + Hf, 35 мл гексана и 240 г шаров диаметром 8 мм. На второй стадии к полученной смеси добавляли сажу в соответствии с реакцией (1) и дополнительно перемешивали 4 мин. Далее смесь сушили на воздухе в шкафу СНОЛ при 60°C в течение 2 ч.
Синтез карбидной керамики осуществляли на установке ЭТВ, описанной в [9]. Приготовленную шихту в количестве 30 г помещали в керамическую пресс-форму диаметром 21 мм. К ней прикладывали давление 100 МПа и нагревали пропусканием электрического тока для осуществления экзотермического взаимодействия реагентов в режиме теплового взрыва. После завершения реакции синтезированный продукт выдерживали под давлением в течение 3 с.
Микроструктуру образцов изучали с помощью автоэмиссионного сканирующего электронного микроскопа сверхвысокого разрешения Zeiss Ultra plus (Германия). Рентгенофазовый анализ (РФА) проб порошков, отбираемых в течение первого этапа смешивания, а также синтезированной керамики проводили на дифрактометре ДРОН-3 (Россия) на излучении CuKα. Для РФА синтезированных образцов использовали шлифы. Параметры элементарной ячейки карбидной фазы рассчитывали по 5 рефлексам, профиль которых аппроксимировался функцией псевдо-Фойгта.
Измерение микротвердости проводили на твердомере ПМТ-3 (Россия) по методу Виккерса при нагрузке 100 г согласно ГОСТ 2999-75. Плотность керамики определяли методом гидростатического взвешивания по ГОСТ 25281-82 на аналитических весах с точностью 1 × 10–4 г.
Содержание связанного углерода определяли методом окислительного плавления в керамическом тигле в индукционной печи по количеству выделившегося углекислого газа методом инфракрасной адсорбции с использованием прибора CS600 фирмы “LECO” (США). Точность анализа 0.01 мас. %.
На рис. 1 представлены дифрактограммы смесей 4Ta + Hf, полученных на первой стадии предварительной механической активации в сравнении со смесью, полученной при ручном смешивании в течение 10 мин. На дифрактограмме смеси без активационной обработки наблюдаются рефлексы Ta и Hf, а также гидридов гафния, которые присутствуют в порошке Hf.
Рис. 1.
Дифрактограммы смесей 4Ta + Hf, полученных при ручном смешивании и МА в планетарной мельнице.
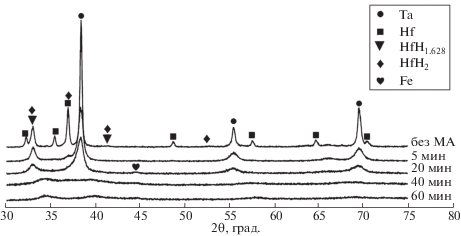
На дифрактограммах смесей, полученных после 5 и 20 мин МА, рефлексы гафния отсутствуют, а интенсивность рефлексов Ta существенно снижается, и их ширина увеличивается (рис. 1). Таким образом, в кристаллической форме в смеси присутствуют фазы Ta и HfH2, а Hf переходит в аморфное состояние.
Уширение рефлексов Ta и HfH2 указывает на дефектность их кристаллической структуры и уменьшение размера областей когерентного рассеяния. Очевидно, что изменение структурного состояния и фазового состава смеси металлов происходит в результате деформационного воздействия при высокоэнергетической обработке.
При МА более 40 мин происходит полная аморфизация кристаллической структуры исходных металлов. Рефлексы Ta, Hf и HfH2 исчезают, а вид дифрактограммы свидетельствует об отсутствии дальнего порядка структуры Ta, Hf и HfH2.
Вместе с тем на дифрактограмме смеси 4Ta + Hf после 60 мин МА в области углов 2θ примерно 34.5°, 40° и 58° наблюдаются размытые рефлексы, интенсивность которых близка к фоновым. Угловое положение этих рефлексов соответствует положению рефлексов 111, 200 и 220 TaC, что указывает на формирование кристаллических зародышей карбидной фазы. Необходимо отметить, что на первом этапе МА смеси 4Ta + Hf проводили без добавления сажи.
Образование карбидной фазы на этой стадии можно объяснить взаимодействием тантала и гафния с углеродом, который выделяется при разложении гексана в процессе МА [14, 15]. Значительная погрешность определения углового положения рефлексов прекурсора не позволяет достоверно определить параметр элементарной ячейки карбида и оценить соотношение Ta/Hf по правилу Вегарда.
Образование карбида при МА смеси в гексане подтверждается данными химического анализа. Показано, что при МА в течение 60 мин содержание связанного углерода Ссв достигает 1.6 мас. %, что соответствует 25% превращению металлов в карбидную фазу. Таким образом, можно заключить, что в результате 60 мин MA смеси 4Ta + Hf в гексане формируется прекурсор, содержащий аморфную металлическую фазу и кристаллиты карбидной фазы.
Объемное воспламенение осуществляли пропусканием через образец электрического тока. Процесс включает стадии предвзрывного нагрева и теплового взрыва. Стадия предвзрывного нагрева завершается при достижении температуры воспламенения. На стадии теплового взрыва происходит экзотермическое взаимодействие реагентов с резким ростом температуры. Длительность первой стадии составляет несколько секунд, а второй – несколько десятков миллисекунд. Адиабатическая температура горения смеси 4Ta + Hf + С, рассчитанная по программе “THERMO” [16], составляет около 3000°С.
В табл. 1 представлены параметры консолидации и физико-механические характеристики карбидной керамики, полученные в настоящей работе и известные в литературе [1–3, 10, 17, 19]. Относительная плотность синтезированной карбидной керамики составила 90%, что уступает керамике Ta4HfC5, полученной горячим изостатическим прессованием и электроискровым спеканием.
Таблица 1.
Параметры консолидации и характеристики керамики Ta4HfC5
Метод синтеза | Давление, МПа | Температура, °C | Время, мин | ρотн, % | $H{v}$, ГПа | Ссылка |
---|---|---|---|---|---|---|
ИПС | 32–55 | 2350 | 20 | 97.7 | 17.1 | [1] |
ИПС | 60 | 1850 | 10 | 97.8 | 16.4 | [2] |
ГИП | 105 | 1500 | 60 | 97.7 | 19 | [3] |
ГИП | 50 | 2000 | 10 | 91 | 27.4 | [10] |
ИПС | 50 | 2000 | 10 | 93 | 24 | [10] |
ИПС | 80 | 1900 | 10 | 98.7 | 19.65 | [17] |
Золь-гель синтез + ИПС | 80 | 1400–1500 | 10 | 98.7 | 19.8 | [19] |
ЭТВ | 100 | ~3000 | 0.05 | 90 | 14.5 | настоящая работа |
Вследствие высокой остаточной пористости микротвердость синтезированной керамики составляет ~14.5 ГПа. Высокая пористость синтезированной керамики обусловлена недостаточным временем выдержки образца под давлением, которое в условиях эксперимента составляло около 3 с.
Отметим, что небольшое время консолидации, составляющее при ЭТВ несколько секунд по сравнению с методами ГИП и ИПС, является существенным преимуществом. Для уменьшения остаточной пористости образцов необходимо уменьшить теплоотвод, что приведет к увеличению времени нахождения материала в пластичном состоянии и позволит увеличить время консолидации.
РФА образцов консолидированной керамики после ЭТВ показал, что предварительная МА смеси металлов в гексане обеспечила формирование однофазного материала. На всех дифрактограммах керамики (рис. 2), полученной из МА смесей, присутствуют рефлексы карбидной фазы, кристаллическая структура которой относится к кубической сингонии (пространственная группа Fm–3m).
Рис. 2.
Дифрактограммы карбидной керамики, полученной при ЭТВ смесей 4Ta + Hf + 5С с различной длительностью МА.
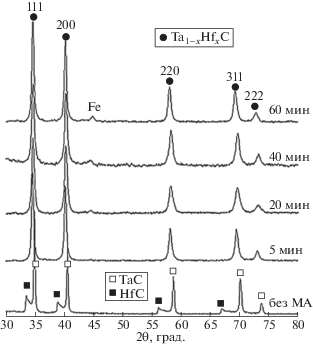
Дифракционные рефлексы карбида существенно уширены, что может быть связано как с малым размером областей когерентного рассеяния, так и с искаженностью кристаллической структуры Ta1 – хHfхC, вызванной различием атомных радиусов Hf (0.167 нм) и Ta (0.149 нм).
С увеличением длительности МА от 5 до 60 мин на дифрактограммах отмечается рефлекс 110 α-Fe, появление которого связано с намолом железа от стенок барабанов и мелющих шаров.
Дифрактограмма карбидной керамики, полученной из смеси ручного приготовления, принципиально отличается от дифрактограмм керамик, полученных из предварительно МА смесей (рис. 3). В первом случае синтезированная керамика не является однофазной. Она содержит фазы, параметры которых близки к параметрам элементарной ячейки монокарбидов TaC и HfC (табл. 2). Кроме того, наличие размытых рефлексов в угловых интервалах между узкими рефлексами TaC и HfC свидетельствует о частичном формировании твердого раствора карбидов Ta1 – хHfхC.
Рис. 3.
Влияние стехиометрии твердого раствора Ta1 – хHfхC на параметр его элементарной ячейки. $ \bullet $ – экспериментальные и $\blacktriangledown $ – литературные данные.
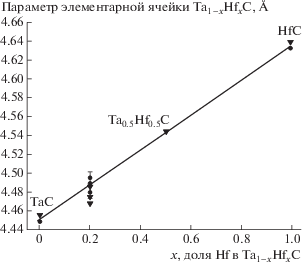
Таблица 2.
Параметры элементарной ячейки карбидов Ta1 – хHfхC
Фаза | Время МА, мин | Параметры ячейки, Å | Ссылка |
---|---|---|---|
TaC | 0 | 4.4506(2)а | настоящая работа |
HfC | 4.6323(7)а | ||
Ta1 – хHfхC | 5 | 4.4892(5) | |
20 | 4.4803(6) | ||
40 | 4.4796(9) | ||
60 | 4.4951(8) | ||
TaC | 4.4547 | PDF2 #35-0801 | |
Ta0.8Hf0.2C | 4.486 | [2] | |
4.4730 | [3] | ||
4.487 | [10] | ||
4.4680 | [18] | ||
4.4854 | [19] | ||
4.49018 | [20] | ||
Ta0.5Hf0.5C | 4.5430 | PDF2 #65-8216 | |
HfC | 4.6376 | PDF2 #39-1491 |
Параметры элементарной ячейки однофазной карбидной керамики в зависимости от времени МА и литературные данные представлены в табл. 2.
Полученные значения параметров ячеек близки к известным параметрам твердого раствора Ta0.8Hf0.2C [2, 3, 10, 18–20]. Изменение метрики элементарной ячейки в ряду твердых растворов TaC–HfC линейно, т.е. подчиняется правилу Вегарда (рис. 3).
На основе полученных данных можно заключить, что в процессе ЭТВ предварительной МА порошковых смесей металлов синтезирован однофазный твердый раствор карбидов тантала и гафния, состав которого соответствует формуле Ta4HfC5.
Результаты РФА согласуются с данными микроструктурного анализа. На рис. 4 представлена микроструктура карбидной керамики, полученной при ЭТВ из реакционной смеси, подвергнутой МА в течение 64 мин. Размер частиц карбида менее 500 нм, причем они имеют характерную для кубической кристаллической структуры огранку.
ЗАКЛЮЧЕНИЕ
Таким образом, впервые методом электротеплового взрыва под давлением из порошковой смеси 4Ta + Hf + 5С получена консолидированная ультратугоплавкая керамика Ta4HfC5 на основе однофазного твердого раствора с субмикронной структурой. Для синтеза однофазной карбидной керамики использовали смесь металлов Ta и Hf после предварительной МА в планетарной мельнице. Показано, что время МА смеси порошков 4Ta + Hf существенно влияет на структуру образующегося прекурсора. МА приводит к изменению структурного состояния и фазового состава смеси металлов в результате деформационного воздействия. При МА в гексане в течение 40–60 мин происходит аморфизация металлов и зарождение кристаллитов карбидной фазы с кубической структурой. Формирование карбида связано с взаимодействием Ta и Hf с углеродом, образующимся в результате разложения гексана. При ЭТВ реакционной смеси, содержащей прекурсор и необходимое количество сажи, формируется однофазный твердый раствор карбидов тантала и гафния. Параметр элементарной ячейки карбида в зависимости от времени МА металлов составил 4.4796(9)–4.4951(8) Å и соответствует параметру ячейки карбида Ta0.8Hf0.2C. Синтезированная керамика характеризуется субмикронной структурой, твердость по Виккерсу составляет 14.5 ГПа при пористости 10%.
Список литературы
Cedillos-Barraza O., Grasso S., Al Nasiri N., Jayaseelan D.D., Reece M.J., Lee W.E. // J. Eur. Ceram. Soc. 2016. V. 36. № 7. P. 1539–1548. https://doi.org/10.1016/j.jeurceramsoc.2016.02.009
Zhang C., Gupta A., Seal S., Boesl B., Arvind Agarwal A. // J. Am. Ceram. Soc. 2017. V. 100. № 5. P. 1853–1862. https://doi.org/10.1111/jace.14778
Gaballa O., Cook B.A., Russell A.M. // Int. J. Refract. Met. Hard Mater. 2013. V. 41. P. 293–299. https://doi.org/10.1016/j.ijrmhm.2013.04.018
Ghaffari S.A., Faghihi-Sani M.A., Golestani-Fard F., Nojabayy M. // Int. J. Refract. Met. Hard Mater. 2013. V. 41. P. 180–184. https://doi.org/10.1016/j.ijrmhm.2013.03.009
Гусев А.И. // ЖФХ. 1985. Т. 59. № 3. С. 579–584.
Valencia D.P., Yate L., Aperador W., Yanguang Li Y., Coy E. // J. Phys. Chem. C. 2018. V. 122. № 44. P. 25433–25440. https://doi.org/10.1021/acs.jpcc.8b08123
Coy E., Babacic V., Yate L., Załęski K., Kim Y., Repa-raz J.S., Dörling B., Graczykowski B., Iatsunsky I., Siuzdak K. // Chem. Eng. J. 2021. V. 415. 128987. https://doi.org/10.1016/j.cej.2021.128987
Guo S. // Adv. Appl. Ceram. 2021. V. 120. № 2. P. 117–126. https://doi.org/10.1080/17436753.2021.1892363
Ghaffari S.A., Faghihi-Sani A., Golestani-Fard F., Mandal H. // J. Eur. Ceram. Soc. 2013. V. 33. № 8. P. 1479–1484. https://doi.org/10.1016/j.jeurceramsoc.2013.01.017
Kurbatkina V.V., Patsera E.I., Levashov E.A., Timofe-ev A.N. // Ceram. Int. 2018. V. 44. № 4. P. 4320–4329. https://doi.org/10.1016/j.ceramint.2017.12.024
Пацерa E.И., Курбаткина В.В., Левашов E.А., Тимофеев А.Н. // Изв. вузов. Порошковая металлургия и функциональные покрытия. 2017. № 2. С. 55–63. https://doi.org/10.17073/1997-308X-2017-2-55-63
Симоненко Е.П., Симоненко Н.П., Петричко М.И., Севастьянов В.Г., Кузнецов Н.Т. // ЖНХ. 2019. Т. 64. № 11. С. 1127–1135. https://doi.org/10.1134/S0044457X19110199
Щербаков В.А., Грядунов А.Н., Вадченко С.Г., Алымов М.И. // Докл. АН. 2019. Т. 488. № 2. С. 153–156. https://doi.org/10.31857/S0869-56524882153-156
Лубнин А.Н., Дорофеев Г.А., Никонова Р.М., Мухгалин В.В., Ладьянов В.И. // Физ. тв. тела. 2017. Т. 59. № 11. С. 2206–2217.
Еремина М.А., Ломаева С.Ф., Бурнышев И.Н., Калюжный Д.Г., Коныгин Г.Н. // ЖНХ. 2018. Т. 63. № 10. С. 1257–1265. https://doi.org/10.1134/S0044457X18100069
Shiryaev A.A. // Int. J. Self-Propag. High-Temp. Synth. 1995. V. 4. № 4. P. 351–362.
Ha D., Kim J., Han J., Kang S. // Ceram. Int. 2018. V. 44. № 16. P. 19247–19253. https://doi.org/10.1016/j.ceramint.2018.07.149
Andrievskii R.A., Strel’nikova N.S., Poltoratskii N.I., Kharkhardin E.D., Smirnov V.S. // Soviet Powder Metallurgy and Metal Ceramics. 1967. V. 6. № 1. P. 65–67. https://doi.org/10.1007/BF00773385
Simonenko E.P., Ignatov N.A., Simonenko N.P., Ezhov Yu.S., Sevastyanov V.G., Kuznetsov N.T. // Russ. J. Inorg. Chem. 2011. V. 56. № 11. P. 1681–1687. https://doi.org/10.1134/S0036023611110258
Jiang J., Wang S., Li W. // J. Am. Ceram. Soc. 2016. V. 99. № 10. P. 3198–3201. https://doi.org/10.1111/jace.14436
Дополнительные материалы отсутствуют.
Инструменты
Доклады Российской академии наук. Химия, науки о материалах