Электрохимия, 2019, T. 55, № 5, стр. 574-586
Приготовление и характеристики электрода из диоксида марганца на графитовой подложке для непрямого электрохимического удаления фенола
Р. Х. Салман a, М. Х. Хафиз b, А. С. Аббас b, *
a Багдадский университет
Багдад, Ирак
b Университет Аль Иракиа
10052 Багдад, Ирак
* E-mail: ammarabbas@coeng.uobaghdad.edu.iq
Поступила в редакцию 19.02.2018
После доработки 08.07.2018
Принята к публикации 27.08.2018
Аннотация
Цилиндрический электрод из диоксида марганца приготовлен путем анодного осаждения на графитовую подложку из раствора MnSO4 с добавкой 0.918 M H2SO4. Систематически исследовано влияние различных рабочих параметров (концентрация MnSO4, плотность тока, время электролиза, скорость вращения электрода) на структуру и морфологию осажденной пленки MnO2. Структуру и размер кристаллов определяли методами рентгено-дифракционного анализа, морфологию исследовали методом сканирующей электронной микроскопии и атомно-силовой микроскопии. Основной продукт процесса осаждения – γ-MnO2. Показано, что на структуру, морфологию и шероховатость приготовленного осадка MnO2 влияют четыре параметра. Размер кристаллов увеличивается с ростом концентрации MnSO4. Шероховатость же уменьшается с ростом всех четырех перечисленных параметров. Оптимальные условия для приготовления вращающегося MnO2-электрода с наименьшим размером кристаллов, небольшой шероховатостью и пониженным растрескиванием таковы: 0.33 M раствор MnSO4, плотность тока 6 мA/cм2, время 2 ч, скорость вращения электрода 200 об./мин. Было исследовано электрохимическое окисление фенола в реакторе периодического действия в присутствии NaCl с целью изучить работу приготовленного MnO2-электрода по разрушению фенола и любых органических побочных продуктов при различной плотности тока. Полученные результаты показывают, что с ростом плотности тока с 25 до 100 мA/cм2 химическая потребность в кислороде (мера эффективности удаления фенола) увеличилась с 59.26 до 99.90%. Были исследованы кинетика и влияние температуры на изменение химической потребности в кислороде. Показано, что химическая потребность в кислороде уменьшается со временем и с ростом температуры; порядок реакции равняется 1.
ВВЕДЕНИЕ
Исследование альтернативных способов разрушения вредных материалов становится жизненно важным, поскольку отходы промышленности и местных субъектов все прибывают [1]. Более 2500 светлых нефтепродуктов, получаемых из сырой нефти в нефтеперерабатывающей промышленности и загрязняющих сточные воды нефтеперерабатывающих заводов, имеют значения химической потребности в кислороде приблизительно от 300 до 600 ppm; у фенола это значение лежит между 20 и 200 ppm [2]. С другой стороны, нефтеперерабатывающие и коксовые заводы – это главные источники фенольных сточных вод. фенольные сточные воды образуются также в производствах красителей, пластмасс, лекарств, в гальванических процессах, на предприятиях переработки угля, в производстве нефтехимических продуктов, резины, спортивной формы, косметики и при перегонке каменноугольных смол [3–6].
Для разрушения и удаления органических веществ разработаны многие процессы окисления. Электрохимическое окисление – новая альтернатива в обработке сточных вод, заменяющая все традиционные процессы [5]. Оно представляет уникальные преимущества электрохимических методов по сравнению с другими технологиями, в том числе: бережное отношение к окружающей среде, гибкость, энергетическая эффективность, избирательность, возможность автоматизации и дешевизна [7].
Электрохимическое окисление можно проводить как прямым, так и непрямым путем. Непрямое окисление предпочтительнее прямого потому, что оно не связано с загрязнением электрода, предотвращает прямой электронный обмен между органическим веществом и поверхностью анода и использует электрокаталитический потенциал других анодных материалов [8, 9]. В этом методе загрязнители окисляются до CO2 и H2O под действием сильного окислителя, генерируемого электрохимически на поверхности анода. Поскольку в сточных водах присутствуют ионы хлора, это делает хлор самым обычным электрохимическим окислителем, образующимся в результате окисления хлорида на аноде [1, 8].
Фенол рассматривают, как одну из наиболее проблемных органических молекул в том, что касается электрохимического окисления. В зависимости от природы используемого анода и значения pH, известны различные пути реакции окисления фенола, ее промежуточные и побочные продукты [10].
Ходом любого электрохимического процесса управляет много факторов, главные из которых – это электродные материалы и потенциал электрода [11]. Таким образом, при выборе электрода для анодного окисления органических и неорганических загрязнителей необходимо принимать во внимание устойчивость электродного материала, его цену, экологическую безопасность и избирательность [7]. Низкая скорость реакции и ее эффективность, загрязнение и отравление активных электродов и их коррозия – вот причины возникающих ограничений [10]. Наиболее часто встречающиеся электродные материалы для очистки сточных вод – это графит, свинец и диоксид свинца, никель и платина, SnO2–Sb и легированный бором алмаз [1, 4]
Но у этих электродов есть недостатки; поэтому такими важными кажутся исследования более дешевых материалов с аналогичными свойствами. Среди них оксиды марганца (MnOx) представляют привлекательное семейство материалов для производства электродов. Причина этого – их уникальная структура, хорошие электрохимические и электрокаталитические свойства, относительно низкая цена, низкая токсичность, распространенность в природе, химическая устойчивость и экологическая безопасность, – лучшие в сравнении с оксидами других переходных металлов [6]. Благодаря этим уникальным физическим и химическим свойствам MnO2, этот оксид нашел свою широкую область применений; он менее опасен для здоровья, чем другие материалы, используемые в аккумуляторах – такие, как кадмий, – в суперконденсаторах и в других случаях, где имеет место электрохимическая обработка токсичных материалов. MnO2 с различными структурой и морфологией изготавливают электрохимическими и химическими методами; исследованы его электрохимические свойства [12–15].
Диоксид марганца может существовать в нескольких стабильных валентных состояниях и кристаллических структурах, таких как α-, β-, γ- и δ-MnO2; именно эти кристаллографические формы MnO2 и создают его уникальные свойства. Как показано в ряде работ [16–19], изо всех кристаллических типов диоксида марганца наилучшей каталитической активностью обладает γ-MnO2.
На работу электрода существенное влияние оказывает способ его приготовления. Пленки MnOx осаждают на подходящие подложки разными способами, которые разработаны для синтеза различных кристаллографических форм MnO2. Самый эффективный метод приготовления электродов из диоксида марганца – это электроосаждение, потому что оно позволяет непосредственно получать оксидные пленки на электродах [12, 20].
Метод электроосаждения широко используется для синтеза диоксида марганца благодаря дешевизне оборудования и удобному контролю толщины осаждаемых пленок [5]. Помимо этого, электроосаждение – это простой и “чистый” метод [13], экологичный и легко поддающийся масштабированию [21]. Электрическое поле в процессах электроосаждения можно прикладывать четырьмя различными способами: постоянный ток (гальваностатический режим), постоянное напряжение (потенциостатический режим), переменное поле (потенциодинамический режим) [21] и импульсное осаждение [13]. Эти четыре типа приложения электрического поля существенно влияют на морфологию поверхности и кристаллическую структуру [22]. При анодном осаждении пленок диоксида марганца получается γ‑MnO2 (называемый также электролитическим диоксидом марганца) [21].
MnO2 осаждают на различные подложки. Графитовые материалы, благодаря присущей им пористости, хорошо удерживают осажденные на них пленки. Осажденный материал может проникать в поры на поверхности графита и служить “якорем”, что предотвращает отслаивание, а осадок выдерживает даже растрескивание [17]. осаждению MnO2 на графитовые подложки посвящено лишь несколько работ, а влияние контролируемых параметров на эффективность процесса изучено относительно слабо.
Предшествующая работа [23] была посвящена вращающемуся аноду из диоксида марганца, приготовленному анодным осаждением, который использовался для окисления щавелевой кислоты в присутствии хлорида натрия. Было показано, что на MnO2-аноде можно успешно провести “сжигание” щавелевой кислоты с эффективностью около 97% после четырехчасового электролиза.
Цель настоящей работы – приготовление пленок диоксида марганца из раствора MnSO4 методом гальваностатического анодного осаждения на графитовую подложку и исследование влияния четырех главных факторов на структуру и морфологию получаемой пленки MnO2. Эти факторы – концентрация раствора MnSO4, продолжительность электроосаждения, плотность пропускаемого тока и скорость вращения анода. Характеристики пленок MnO2 исследовали методами рентгено-дифракционного анализа, сканирующей электронной микроскопии (СЭМ) и атомно-силовой микроскопии (АФМ). Эксплуатационные характеристики приготовленного анода изучали на примере удаления фенола и других органических побочных продуктов путем их электрохимического окисления в электрохимическом реакторе периодического действия. Поскольку фенол превращается в другие органические соединения, удобнее определять химическую потребность в кислороде (ХПК), чем измерять концентрацию фенола.
ЭКСПЕРИМЕНТАЛЬНАЯ ЧАСТЬ
Химические реактивы
Все реактивы имели квалификацию “ч. д. а.” и не нуждались в дополнительной очистке. Использовались MnSO4.H2O (Thomas Baker), H2SO4 (Riedel–deHaën), фенол (LOBA Chemie); все растворы готовили на дважды перегнанной воде.
Электроосаждение
Электроды из диоксида марганца получали методом электроосаждения. Ячейка содержала два графитовых электрода: один графитовый стержень диаметром 1.8 см и длиной 8 см в качестве анода и другой – полый цилиндр с внешним диаметром 10 см, внутренним диаметром 8 см и длиной 15 в качестве катода; они были укреплены в стеклянной электролитической ячейке. Графитовые подложки вначале кипятили в дистиллированной воде при 100°C в течение 30 мин, затем активировали в электролите (0.918 M раствор H2SO4) при плотности тока 14 мA/cм2 в течение 30 мин. Электролит нагревали с помощью магнитной мешалки – горячей пластинки (LABINCO, модель L-81). По окончании электролиза электрод промывали дистиллированной водой. Анодное осаждение MnO2 проводили в растворе электролита MnSO4 + 0.918 M H2SO4 общим объемом 1.15 л при температуре 363 K. Эксперименты повторяли дважды.
Мы исследовали влияние различных переменных на пленку электроосажденного MnO2, при этом в некоторых экспериментах графитовый стержень вращали с заданной скоростью с помощью электрической мешалки с коробкой скоростей (Heidolph), используя электронный тахометр. Использовали источник постоянного тока UNI-T: UTP3315TF-L с выходным напряжением 0–30 В и током на выходе 0–5 A. Исследованные переменные – это концентрация MnSO4 (0.33, 0.5, 0.83 M), плотность пропускаемого через анод тока (6, 9, 12, 15 мA/cм2), скорость вращения электрода (0, 200, 400 об./мин) и время электроосаждения (1, 2, 3 ч). На рис. 1 показана схема электролизера.
Структурные характеристики
Кристаллографические характеристики MnO2 изучали методом рентгено-дифракционного анализа на порошковом дифрактометре Brucker-D2 PHASER с CuKα-излучением в качестве источника рентгеновских лучей (λ = 1.54056 Å). Морфологию и химический состав поверхности пленки MnO2 исследовали с помощью сканирующего электронного микроскопа (FEI company, Нидерланды) с приставкой X-Ray EDS для энергодисперсионного анализа. АФМ-анализ проводили на приборе SPM-AA3000 (Angestrom Advanced Inc., США) в контактной моде. АФМ-изображения записывали в сканируемой области размером 2 × 2 мкм.
Кинетика окисления фенола
Эксплуатационные характеристики приготовленных электродов оценивали по уменьшению химической потребности в кислороде в водном растворе фенола (концентрация 150 ppm, что эквивалентно 315 ppm ХПК) в присутствии 0.017 M NaCl и 0.1M H2SO4 в качестве индифферентного электролита. Объем раствора в этом эксперименте – 0.5 л, температуру в опытах по удалению фенола поддерживали при 298 K. При исследовании кинетики опыты по электрохимическому удалению фенола проводили при следующих рабочих условиях: плотность тока 100 мA/cм2, начальная концентрация фенола 150 ppm, время электролиза до 5 ч, скорость вращения MnO2-электрода 200 об/мин. Исследовали изменение химической потребности в кислороде, как функцию температуры (293–323 K). Для определения химической потребности в кислороде использовали стандартизованный колориметрический метод (Lovibond water testing), данные собирались в ходе процесса электролиза.
РЕЗУЛЬТАТЫ И ОБСУЖДЕНИЕ
Результаты рентгено-дифракционного анализа
На рис. 2 показаны рентгеновские дифрактограммы осадка MnO2, полученного при различных концентрациях MnSO4 (с их брегговскими отражениями или кристаллографическими индексами Миллера). MnO2 существует во многих кристаллических формах, и если диоксид марганца готовили путем электрохимического окисления в присутствии кислых электролитов, то его называют электрохимическим диоксидом марганца (EMD), и он существует либо как γ-структура, либо как аморфное вещество [14]. Согласно предшествующей работе [24], γ-MnO2 – это главный продукт, который получается при использовании электролита на основе MnSO4. При концентрации MnSO4 0.33 M, на рентгеновской дифрактограмме видны пики орторомбического EMD (рис. 2, a). Они расположены при следующих значениях 2θ: 37.35° (0 2 1), 56.724° (2 2 1), 59.776° (2 0 0), 67.851° (0 6 1) и 72.276° (0 6 2). При возрастании концентрации MnSO4 до 0.5 M пики располагаются при следующих значениях 2θ: 37.679° (0 2 1), 43.021° (1 2 1), 56.724° (2 2 1) и 67.319° (0 6 1) (см. рис. 2, б). При концентрации MnSO4 равной 0.83 М эти пики, как показано на рис. 2, в, находятся при следующих значениях 2θ: 38.12° (2 3 0), 44.112° (0 0 2), 57.01° и 68.367° (0 0 3).
Рис. 2.
Рентгеновские дифрактограммы пленки MnO2 на графитовой подложке приM MnSO4: a – 0.33, б – 0.5, в – 0.83, плотность тока 6 мA/cм2, время 2 ч, без перемешивания.
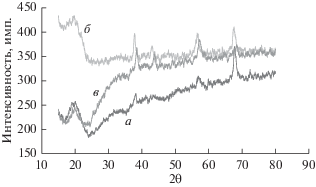
Все эти пики находятся в хорошем согласии с данными для γ-MnO2 (JCPDS No. 14-0644). Средний размер кристаллов (или размер зерна) в осадке MnO2 при всех исследованных параметрах был найден по формуле Шеррера [25], $D = {{0.9\quad\lambda } \mathord{\left/ {\vphantom {{0.9\quad\lambda } {\beta \quad{\text{cos}}\left( \theta \right)}}} \right. \kern-0em} {\beta \quad{\text{cos}}\left( \theta \right)}},$ где λ равняется 1.54056 Å, а β – это уширение дифракционной линии, измеренное на половине максимальной интенсивности (в радианах). Оценка значения β и размера кристаллов была выполнена с применением программного обеспечения EVA-1, прилагавшегося к прибору для рентгено-дифракционного анализа. Было установлено, что размер кристаллов при трех концентрациях (0.33, 0.5 и 0.83 M) составил, соответственно, 16, 25.1 и 28.9 нм, т.е. он увеличивается с ростом концентрации MnSO4. На рис. 3 показано влияние плотности тока на дифрактограмму осадка MnO2. При плотности тока равной 9 мA/cм2 пики EMD (рис. 3, a) находятся при следующих значениях 2θ: 37.02° (0 2 1) и 66.31°(0 6 1). Если плотность пропускаемого тока увеличить до 12 мA/cм2, то мы увидим пики при значениях 2θ равных 38.031° (2 3 0) и 67.321° (0 6 1), как показано на рис. 3, б. С ростом плотности тока до 15 мA/cм2 получаются пики с низкой интенсивностью, за исключением пика при 2θ равном 67.338° (0 6 1) (рис. 3, в), т.е. относящегося к агломерациям первичных частиц и кристаллов, который растет с ростом плотности пропускаемого тока. Положение всех этих пиков находится в хорошем согласии с данными для γ-MnO2 (JCPDS No. 14-0644). Размер кристаллов в осадке MnO2 для четырех значений плотности пропускаемого тока (6, 9, 12 и 15 мA/cм2), соответственно, таков: 16, 22.6, 32.7 и 38.8 нм, т.е. размер кристаллов увеличивается с ростом плотности пропускаемого тока; этот результат подтверждается работой [26].
Рис. 3.
Рентгеновские дифрактограммы пленки MnO2 на графитовой подложке при плотности тока, мA/cм2: a – 9, б – 12, в – 15, раствор 0.33 M MnSO4, время электролиза 2 ч, без перемешивания.
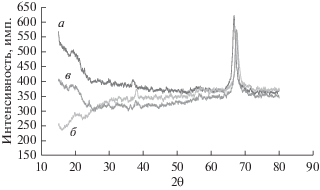
Рис. 4 иллюстрирует влияние времени процесса электроосаждения на рентгеновскую дифрактограмму осадка MnO2. Если это время равняется 3 ч, то пики на дифрактограмме MnO2 (рис. 4, a) находятся при значениях 2θ равных 37.553° (0 2 1), 56.127° (2 2 1) и 67.14° (0 6 1). Если же время уменьшить до 1 ч, то, как показано на рис. 4, б, получаются пики при следующих значениях 2θ: 37.252° (0 2 1), 42.687° (3 0 0), 56.321° (2 2 1) и 67.126° (0 6 1). И здесь положение пиков находится в хорошем согласии с данными для γ-MnO2 (JCPDS No. 14-0644). Размер кристаллов для трех значений продолжительности электролиза (1, 2 и 3 ч) равен, соответственно, 28.5, 16 и 16.7 нм. Как видно, размер кристаллов быстро увеличивается при временах меньше, чем 2 ч, и слегка увеличивается при временах больше 2 ч. Рис. 5 показывает, как влияет на рентгеновскую дифрактограмму осадка MnO2 скорость вращения анода. При скорости вращения 200 об./мин пики на дифрактограмме (рис. 5a) наблюдаются при значениях 2θ, равных 37.422° (0 2 1), 56.10° (2 2 1) и 67.281° (0 6 1). Увеличение скорости вращения до 400 об./мин сдвинуло эти пики к значениям 2θ, равным 37.561° (0 2 1), 42.51° (3 0 0), 56.085° (2 2 1) и 67.380° (0 6 1), как показано на рис. 5б. И эти пики находятся в хорошем согласии с известными данными для γ-MnO2 (JCPDS No. 14-0644). Размер кристаллов для этих трех скоростей вращения (0, 200 и 400 об./мин) таков: 16, 16.6 и 32.7 нм соответственно. В общем и целом, размер кристаллов растет при увеличении скорости вращения анода, но если сравнить размер кристаллов в неподвижном растворе с таковым при скорости вращения электрода 200 об./мин, то оказывается, что большой разницы между этими значениями нет. Размер кристаллов увеличивается быстрее, когда скорость вращения достигает 400 об./мин. Причина этого – увеличение скорости роста с увеличением скорости вращения.
Данные сканирующей электронной микроскопии
Предшествующие исследования показали, что силы сжатия между осадком и подложкой во время сушки электродов по окончании процесса осаждения приводят к растрескиванию и уменьшению проводимости MnO2, поэтому трудно приготовить толстые пленки диоксида марганца [19, 27, 28]. Вышеописанное влияние других параметров на морфологию поверхности осадка MnO2 было исследовано методом сканирующей электронной микроскопии. СЭМ-изображение (рис. 7) демонстрирует сильнейшее влияние концентрации MnSO4 на морфологию осажденной пленки: при концентрации выше 0.5 M в осадке наблюдаются агломераты. На всех изображениях видны трещины, но при более высокой концентрации образуются узкие трещины, и это дает гладкую поверхность.
Рис. 6.
СЭМ-микрофотографии MnO2 на графитовой подложке (1 – 100, 2 – 10 мкм) при концентрации, M MnSO4: a – 0.33, б – 0.5, в – 0.83, плотность тока 6 мA/cм2, время электролиза 2 ч, без перемешивания.
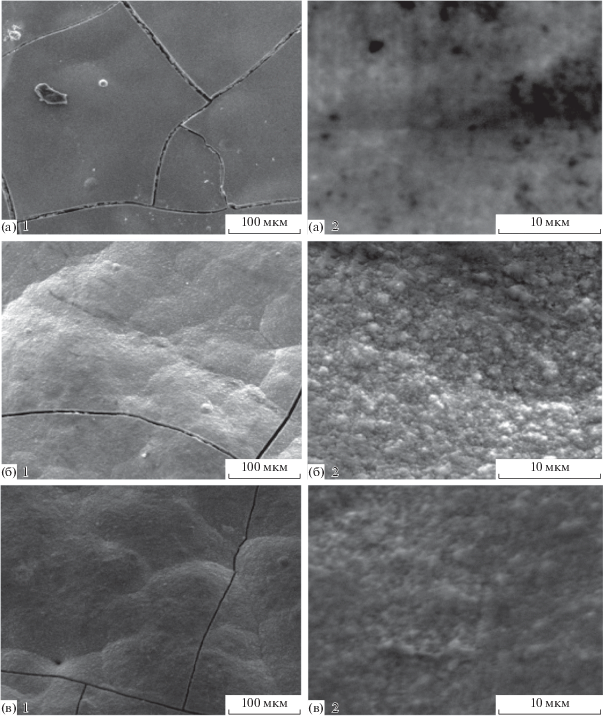
Рис.7.
СЭМ-микрофотографии пленки MnO2 на графитовой подложке (1 – 100, 2 – 10 мкм) при мA/cм2: a – 9, б ‒ 12, в – 15, раствор 0.33 M MnSO4, время электролиза 2 ч, без перемешивания.
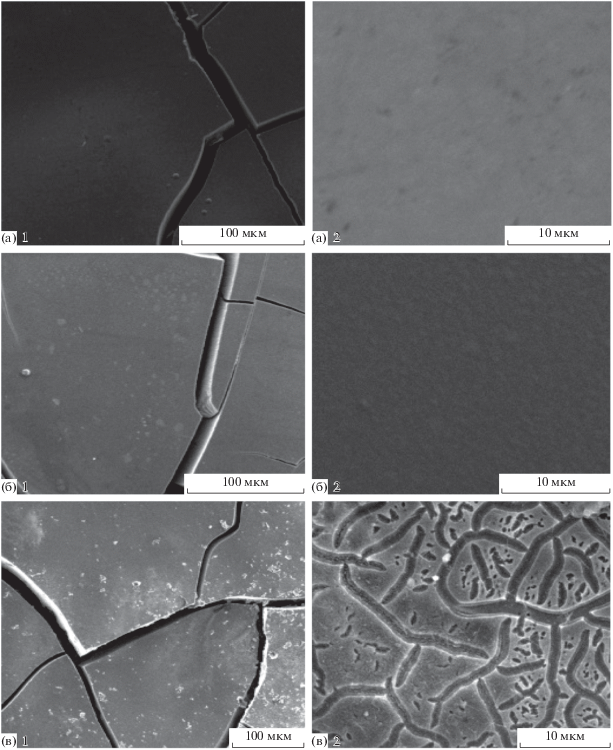
Плотность пропускаемого тока не оказывает видимого влияния на морфологию осадка MnO2 (рис. 7). При высокой плотности тока во время процесса электроосаждения имеют место небольшие осажденные частицы и быстрое зародышеобразование [29]. Ясно, что по мере роста плотности тока, осажденные пленки MnO2 становятся более гладкими, наблюдается меньше трещин, потому что образуются более толстые пленки. Однако, когда плотность тока достигает 15 мA/cм2, трещины увеличиваются с образованием полосок из-за выделения O2, которое считается главной конкурирующей реакцией по отношению к процессу электроокисления. В этом случае плотность тока превышает предельное значение. На рис. 8 показаны СЭМ-микрофотографии осадков MnO2, полученных за разное время электроосаждения. На пленках появляется структура типа “растрескавшейся глины”, и становится ясно, что по мере роста продолжительности электроосаждения поверхность растрескивается меньше, и при времени электроосаждения больше 2 ч можно получить однородную структуру (рис. 6a).
Рис. 8.
СЭМ-микрофотографии пленки MnO2 на графитовой подложке (1 – 100, 2 – 10 мкм) при времени электролиза: a – 3 ч, б – 1 ч, раствор 0.33 M MnSO4, 6 мA/cм2, без перемешивания.
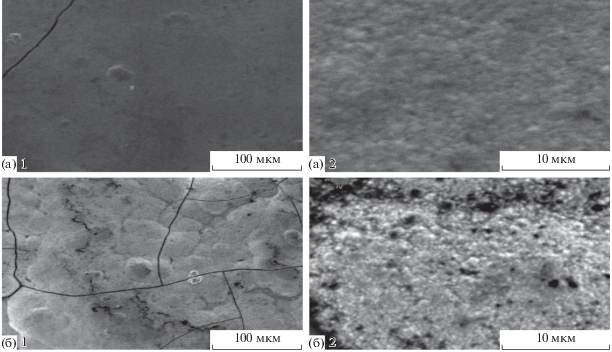
На рис. 9 показано влияние скорости вращения анода на морфологию осадка. Видно, что с ростом скорости вращения образуется все меньше трещин. это можно объяснить ускорением массопереноса к аноду (вследствие уменьшения толщины диффузионного слоя), что приводит к ускорению кристаллизации и зародышеобразования, поэтому при небольших скоростях вращения осадок агломерируется. В неподвижном растворе на электроде образуются большие трещины (см. рис. 6a).
Данные атомно-силовой микроскопии
Данные атомно-силовой микроскопии, полученные при варьировании различных параметров, исследованных в настоящей работе, приведены в табл. 1. На шероховатость осадка MnO2 (среднеквадратичное значение) оказывает влияние рост концентрации MnSO4. С ростом концентрации шероховатость уменьшается; это можно объяснить тем, что на начальной стадии процесса осаждения преобладает прогрессирующее зародышеобразование. Это наблюдение согласуется с предшествующим исследованием [30] и СЭМ-микрофотографиями.
Таблица 1.
Результаты атомно-силовой микроскопии при различных параметрах
Параметры | Значение | Среднеквадратичное значение, нм | Условия |
---|---|---|---|
Концентрация MnSO4, M | 0.33 | 2.38 | Плотность тока 6 мA/cм2 Время 2 ч Без вращения |
0.50 | 2.04 | ||
0.83 | 1.36 | ||
Плотность тока, мA/cм2 | 6 | 2.38 | Концентрация MnSO4 0.33 M Время 2 ч Без вращения |
9 | 2.02 | ||
12 | 1.7 | ||
15 | 3.12 | ||
Время, ч | 1 | 4.55 | Концентрация MnSO4 0.33 M Плотность тока = = 6 мA/cм2 Без вращения |
2 | 2.38 | ||
3 | 1.52 | ||
Скорости вращения электрода, об./мин | 0 | 2.38 | Концентрация MnSO4 0.33 M Плотность тока = = 6 мA/cм 2 Время 2 ч |
200 | 1.89 | ||
400 | 1.08 |
Рост плотности тока приводит к уменьшению шероховатости осадка MnO2 вплоть до плотности тока 12 мA/cм2. При высоком пропускаемом токе в ходе электроосаждения получаются мелкие частицы и происходит быстрое зародышеобразование, что подтверждается и другими авторами [31]. При плотности тока 15 мA/cм2 шероховатость увеличивается из-за побочной реакции – выделения O2 [25].
С другой стороны, главное влияние на шероховатость оказывает время электролиза: рост этого времени дает более гладкие осадки, благодаря ускорению зародышеобразования. Это наблюдение подтверждено в работе [31]. Также ясно видно, что значительное влияние на шероховатость осадка MnO2 оказывает скорость вращения электрода. Установлено, что с ростом скорости вращения шероховатость уменьшается. Причина этого – ускорение зародышеобразования, как результат уменьшения толщины пограничного слоя. Предшествующие исследования показали, что с уменьшением размера кристаллов возрастает активность электрода [32]. На основе размеров кристаллов в осадке MnO2 можно заключить, что самые маленькие кристаллы (16 нм) получаются при следующих рабочих условиях: 0.33 M раствор MnSO4, плотность тока 6 мA/cм2, время электролиза 2 ч, без вращения. Однако, приблизительно такой же размер кристаллов получается и при вращении электрода со скоростью 200 об./мин, при этом растрескивание и шероховатость меньше. Поэтому можно рекомендовать вышеописанные условия с перемешиванием для приготовления MnO2-электродов для разложения фенола.
Удаление фенола
Эксплуатационные характеристики приготовленного MnO2-электрода изучали на примере электроокисления фенола (концентрация 150 ppm) в присутствии NaCl (0.017 M) и 0.1 M H2SO4 в качестве индифферентного электролита. MnO2-электрод вращали со скоростью 200 об./мин. На рис. 10 приведена кривая изменения во времени химической потребности в кислороде для четырех значений плотности тока от 25 до 100 мA/cм2. Видно, что с ростом плотности тока значение химической потребности в кислороде уменьшается. Эффективность удаления фенола и побочных продуктов его разложения при продолжительности электролиза 5 ч составила 59.26, 68.40, 83.79 и 99.9% при плотностях тока, соответственно, 25, 50, 75 и 100 мA/cм2. Это говорит о том, что скорость реакции контролируется активностью хлора, а не массопереносом фенола к аноду. Этот результат согласуется с предшествующими исследованиями [5, 23]. В сопоставлении с вышеупомянутыми предшествующими работами, результат настоящей работы является многообещающим в том, что касается электрохимического разложения фенола с использованием дешевого MnO2-электрода.
Рис. 10.
Зависимость химической потребности в кислороде (ХПК) от времени электролиза на вращающемся MnO2-электроде (скорость вращения электрода 200 об./мин) при различной плотности тока, мА/см2: 1 – 25, 2 – 50, 3 – 75, 4 – 100 мA/cм2, CODo = = 315 мг/л, скорость вращения электрода 200 об./мин, T = 298 K.
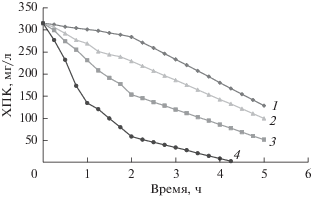
Кинетика уменьшения химической потребности в кислороде и влияние на нее температуры
Знание того влияния, которое температура электрохимического процесса оказывает на скорость уменьшения химической потребности в кислороде, необходимо для получения полного кинетического уравнения скорости. На рис. 11 представлено изменение уменьшения химической потребности в кислороде, как функция температуры. Из рисунка ясно видно, что химическая потребность в кислороде уменьшается со временем, а при увеличении температуры она тоже увеличивается. Таким образом, температура оказывает положительное влияние на окислительное разложение органических веществ. Кинетику изменения химической потребности в кислороде, или удаления фенола, можно описать следующим образом:
где rate – скорость, COD – химическая потребность в кислороде.Рис. 11.
Изменение химической потребности в кислороде с температурой при плотности тока 100 мA/cм2, скорости вращения электрода 200 об./мин, концентрации фенола 150 ppm (315 ppm химической потребности в кислороде).
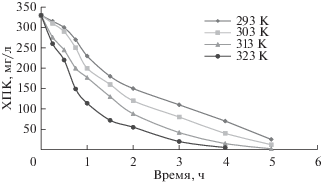
Уравнение нелинейной регрессии получили с помощью поиска решения нелинейных задач методом приведенного градиента [33]. Оно было использовано для решения кинетического уравнения для химической потребности в кислороде (уравнение (1)) с целью найти значение константы скорости реакции (k) для каждой температуры при порядке реакции, равном 1. В результате получилось, что химическая потребность в кислороде меняется по экспоненте. В табл. 2 суммированы результаты, полученные методом регрессии.
Таблица 2.
Значения 1/T и ln k при различных температурах
Температура, K | 1/T, K–1 | k, ч–1 | ln k |
---|---|---|---|
293 | 0.0034 | 0.36 | –1.02 |
303 | 0.0033 | 0.48 | –0.73 |
313 | 0.0031 | 0.78 | –0.24 |
323 | 0.0030 | 0.84 | –0.17 |
Мы исследовали изменение константы скорости реакции с температурой, используя уравнение Аррениусовского типа. С этой целью отложили величину ln k против 1/T, согласно закону Аррениуса:
Здесь E – энергия активации реакции (Дж/моль), а A – частотный фактор [34]. График зависимостиg ln k от 1/T, как видно из рис. 12, является прямой линией; линейный фитинг дает хороший результат (R2 = 0.9577), с величиной E, равной 20.53 кДж/моль и A около 1584 ч–1. Довольно низкое значение энергии активации указывает на то, что эта реакция мало чувствительна к температуре, и что процесс – физический и не контролируется реакцией [34]. Этот результат находится в хорошем согласии с предшествующими исследованиями [35–37]. В работе [5] было найдено, что величина E для реакции удаления фенола на угольном электроде в присутствии NaCl при различных температурах равняется 10.9 кДж/моль. Найденное в настоящей работе значение E выше, что может указывать на более эффективный катализ электрохимической реакции удаления фенола, а в механизме реакции преобладает окисление, а не полимеризация.ЗАКЛЮЧЕНИЕ
Успешно приготовлен и испытан вращающийся цилиндрический MnO2-электрод для разложения фенола. Метод рентгеновской дифракции подтвердил преобладание фазы со структурой γ‑MnO2 во всех осадках, благодаря использованию кислого раствора сульфата в качестве электролита. Размер кристаллов увеличивается с ростом плотности пропускаемого тока, времени электролиза и скорости вращения электрода. Метод сканирующей электронной микроскопии показал наличие трещин во всех приготовленных пленках MnO2. Это обычно является результатом растрескивания в процессе сушки пленок. Рекомендованы рабочие условия приготовления MnO2, которые уменьшают растрескивание и шероховатость при сохранении почти такого же размера кристаллов. MnO2-электрод продемонстрировал высокую эффективность в уменьшении химической потребности в кислороде, благодаря высвобождению активного хлора. Таким образом, разработанный электрод весьма перспективен для удаления различных органических загрязнителей из сточных вод путем электрохимического непрямого окисления. Исследование кинетики уменьшения химической потребности в кислороде показало, что химическая потребность в кислороде уменьшается во времени и увеличивается с ростом температуры. Уравнение нелинейной регрессии, полученное с помощью метода приведенного градиента, показало, что уменьшение химической потребности в кислороде протекает с кинетикой первого порядка. Полученное значение энергии активации указывает на то, что эта реакция мало чувствительна к температуре. При времени электролиза от 2 до 5 ч реакция контролируется плотностью пропускаемого тока.
Список литературы
Britto-Costa, P.H. and Ruotolo, L.A.M., Phenol removal from wastewaters by electrochemical oxidation using boron doped diamond (BDD) and Ti/Ti0.7 Ru0.3O2, Brazilian J. Chem. Eng., 2012, vol. 29, p. 763.
Yavuz, Y., Koparal, A.S., and Bak, Ü., Treatment of petroleum refinery wastewater by electrochemical methods, Desalination, 2010, vol. 258, p. 201.
Chirkst, D.E., Cheremisina, O.V., Sulimova, M.A., Kuzhaeva, A.A., and Zgonnik, P.V., Kinetics of oxidation of phenol with manganese dioxide, Russ. J. Gen. Chem., 2011, vol. 81, p. 704.
Rajkumar, D., Kim, J.G., and Palanivelu, K., Indirect electrochemical oxidation of phenol in the presence of chloride for wastewater treatment, Chem. Eng. Technol., 2005, vol. 28, p. 98.
Korbahti, B.K., Salih, B., and Tanyolaç, A., Electrochemical conversion of phenolic wastewater on carbon electrodes in the presence of NaCl, J. Chem. Technol. Biotechnol., 2002, p. 70.
Nakayama, M., Shamoto, M., and Kamimura, A., Surfactant-induced electrodeposition of layered manganese oxide with large interlayer space for catalytic oxidation of phenol, Chem. Mater., 2010, vol. 22, p. 5887.
Rajeshwar, K. and Ibanez, J.G., Environmental Electrochemistry : Fundamentals and Applications in Pollution Sensors, Elsevier Science & Technology Books, 1997.
Martìnez-Huitle, C.A. and Ferro, S., Electrochemical oxidation of organic pollutants for the wastewater treatment: direct and indirect processes., Chem. Soc. Rev., 2006, vol. 35, p. 1324.
Anglada, A., Urtiaga, A., and Ortiz, I., Contributions of electrochemical oxidation to waste-water treatment: Fundamentals and review of applications, J. Chem. Technol. Biotechnol., 2009, vol. 84, p. 1747.
Hagans, P.L., Natishan, P.M., Stoner, B.R., and O’Grady, W.E., Electrochemical oxidation of phenol using boron-doped diamond electrodes, J. Electrochem. Soc., 2001, vol. 148, p. E298.
Ibrahim, D.S., Devi, P.S., and Balasubramanian, N., Electrochemical Oxidation Treatment of Petroleum Refinery Effluent, Int. J. Sci. Eng. Res., 2013, vol. 4, p. 1.
Sotgiu, G., Foderà, M., Marra, F., Petrucci, E., Ingegneria, D., Tre, R., and Volterra, V.V., Production and characterization of manganese oxide-based electrodes for anodic oxidation of organic compounds, Chem. Eng. Trans., 2014, vol. 41, p. 115.
Xiao, F. and Xu, Y., Pulse electrodeposition of manganese oxide for high-rate capability supercapacitors, Int. J. Electrochem. Sci., 2012, vol. 7, p. 7440.
Suhasini, Effect of deposition method and the surfactant on high capacitance of electrochemically deposited MnO2 on stainless steel substrate, J. Electroanal. Chem., 2013, vol. 690, p. 13.
Gan, T., Shi, Z., Deng, Y., Sun, J., and Wang, H., Morphology-dependent electrochemical sensing properties of manganese dioxide-graphene oxide hybrid for guaiacol and vanillin, Electrochim. Acta, 2014, vol. 147, p. 157.
Chen, Y., Duan, Z., Min, Y., Shao, M., and Zhao, Y., Synthesis, characterization and catalytic property of manganese dioxide with different structures, J. Mater. Sci. Mater. Electron., 2011, vol. 22, p. 1162.
Broughton, J.N. and Brett, M.J., Variations in MnO2 electrodeposition for electrochemical capacitors, Electrochim. Acta, 2005, vol. 50, p. 4814.
Wei, C., Xu, C., Li, B., Du, H., and Kang, F., Preparation and characterization of manganese dioxides with nano-sized tunnel structures for zinc ion storage, J. Phys. Chem. Solids, 2012, vol. 73, p. 1487.
Yu, Z.M., Hu, J.X., Zhao, J., and Niu, Y.S., The Preparation, Texture and electrodeposition mechanism of reticular MnO2 catalytic materials with high porosity, Adv. Mater. Res., 2011, vol. 311–313, p. 1784.
Lee, H., Lee, K., and Kim, C., Electrodeposition of manganese-nickel oxide films on a graphite sheet for electrochemical capacitor applications, Materials, 2014, vol. 7, p. 265.
Dubal, D.P., Dhawale, D.S., Gujar, T.P., and Lokhande, C.D., Effect of different modes of electrodeposition on supercapacitive properties of MnO2 thin films, Appl. Surf. Sci., 2011, vol. 257, p. 3378.
Song, H.Y., Kondrikov, N.B., Kuryavy, V.G., and Kim, Y.H., Preparation and characterization of manganese dioxide electrodes for highly selective oxygen evolution during diluted chloride solution electrolysis, J. Ind. Eng. Chem., 2007, vol. 13, p. 545.
Abbar, A.H., Salman, R.H., and Abbas, A.S., Electrochemical incineration of oxalic acid at manganese dioxide rotating cylinder anode : role of operative parameters in the presence of NaCl, J. Electrochem. socity, 2016, vol. 163, p. E333.
Adelkhani, H., The effect of acidity of electrolyte on the porosity and the nanostructure morphology of electrolytic manganese dioxide, Appl. Surf. Sci., 2012, vol. 258, p. 6232.
Vinila, V.S., Jacob, R., Mony, A., Nair, H.G., and Issac, S., “XRD studies on nano crystalline ceramic superconductor pbsrcacuo at different treating temperatures, Cryst. Struct. Theory Appl., 2014, vol. 3, p. 1.
Guo, H., Zhu, B., Li, X., Zhang, X., Wang, Z., Peng, W., and Liu, L., Effects of current density on preparation of grainy electrolytic manganese dioxide, J. Cent. South Univ. Technol., 2005, vol. 12, p. 667.
Jacob, G.M. and Zhitomirsky, I., Microstructure and properties of manganese dioxide films prepared by electrodeposition, Appl. Surf. Sci., 2008, vol. 254, p. 6671.
Chang, J.K., Chen, Y.L., and Tsai, W.T., Effect of heat treatment on material characteristics and pseudo-capacitive properties of manganese oxide prepared by anodic deposition, J. Power Sources, 2004, vol. 135, p. 344.
Ryu, W., Yoon, J., and Kwon, H., Morphological control of highly aligned manganese dioxide nanostructure formed by electrodeposition, Mater. Lett., 2012.
Sarac, U. and Baykul, M.C., Comparison of microstructural and morphological properties of electrodeposited Fe–Cu thin films with low and high Fe : Cu ratio, Adv. Mater. Sci. Eng., 2013, vol. 2013, p. 1.
Kassim, A., Nagalingam, S., Min, H.S., and Karrim, N., XRD and AFM studies of ZnS thin films produced by electrodeposition method, Arab. J. Chem., 2010, vol. 3, p. 243.
Esswein, A.J., Mcmurdo, M.J., Ross, P.N., Bell, A.T., and Tilley, T.D., Size-dependent activity of Co3O4 Nanoparticle Anodes for Alkaline Water Electrolysis, J. Phys. Chem. C, 2009, vol. 113, p. 15068.
Lente, G., Deterministic Kinetics in Chemistry and Systems Biology, Springer, 2015.
Levenspiel, O., Chemical Reaction Engineering, Wiley, 1999.
Atwater, J.E., Akse, J.R., McKinnis, J.A., and Thompson, J.O., Low temperature aqueous phase catalytic oxidation of phenol, Chemosphere, 1997, vol. 34, p. 203.
Rivas, F.J., Kolaczkowski, R.S.T., Beltras, F.J., and Mclurgh, D.B., Development of a model for the wet air oxidation of phenol based on a free radical mechanism, Chem. Eng. Sci., 1998, vol. 53, p. 2575.
Beltran-Heredia, J., Torregrosa, J., Dominguez, J.R., and Peres, J.A., Kinetics of the reaction between ozone and phenolic acids present in agro-industrial wastewaters, Water Res., 2001, vol. 35, p. 1077.
Дополнительные материалы отсутствуют.