Электрохимия, 2019, T. 55, № 7, стр. 864-872
Электрохимические характеристики топливных ячеек с пленочным электролитом CaZr0.9Y0.1O3 – δ на несущем никель-керметном аноде
В. М. Куимов a, *, А. Ш. Халиуллина a, А. А. Панкратов a, Б. Д. Антонов a, Л. А. Дунюшкина a
a Институт высокотемпературной электрохимии УрО РАН
620137 Екатеринбург, ул. Академическая, 20, Россия
* E-mail: Kvazighaboid@yandex.ru
Поступила в редакцию 23.11.2018
После доработки 20.12.2018
Принята к публикации 29.01.2019
Аннотация
Исследованы электрохимические характеристики топливных ячеек с пленкой CaZr0.9Y0.1O3 – δ на несущем аноде Ni-CaZr0.95Sc0.05O3 – δ. Выявлено, что диффузия никеля из несущего электрода влечет увеличение электронной проводимости электролита. Установлено, что для обеспечения достаточно высоких чисел переноса ионов толщина пленочного электролита CZY должна быть не менее 4 мкм. Сделано заключение, что основной причиной снижения мощности топливной ячейки с пленочным электролитом являются поляризационные потери на аноде.
ВВЕДЕНИЕ
В связи с ростом потребления электроэнергии актуальным является разработка эффективных и экологически чистых способов ее производства. Один из таких способов – использование твердооксидных топливных элементов (ТОТЭ), достоинством которых является прямое преобразование химической энергии топлива в электрическую энергию. ТОТЭ имеют множество других достоинств: экологичность, толерантность к топливу и др. [1–4], однако их массовое производство сдерживает невысокий ресурс функционирования и высокая стоимость получаемой электроэнергии, связанные с высокими рабочими температурами (800–1000°С). Снижение рабочей температуры ТОТЭ до 500–600°С возможно при уменьшении толщины электролита до нескольких микрометров. При этом снижается внутреннее сопротивление элемента и увеличивается его мощность. В связи этим использование пленочных электролитов в ТОТЭ представляет большой интерес.
Тенденция к снижению рабочих температур ТОТЭ приводит к тому, что при низких температурах вместо классического кислородно-ионного электролита ZrO2 перспективнее использовать протонный электролит, поскольку он обладает меньшей энергией активации проводимости. К тому же в ТОТЭ на протонном электролите возможна практически полная утилизация топлива, если в качестве такого используется водород [5]. Перспективными протонными электролитами для ТОТЭ являются цирконаты кальция, они демонстрируют достаточный уровень протонной проводимости [6], являются химически устойчивыми и термически стабильными в широком интервале рО2 [7].
В ТОТЭ пленочный электролит должен быть получен на несущем пористом электроде, что является непростой задачей. При синтезе пленок возможна диффузия ионов подложки, что влечет изменение состава и свойств пленки и может привести к деградации электрохимического устройства. Например, диффузия кобальта из электрода La0.8Sr0.2Mn0.8Co0.2O3 – δ в электролит La0.9Sr0.1Ga0.8Mg0.2O3 – δ после совместного спекания при 1300°С в течение 300 ч на воздухе приводит к увеличению электронной проводимости электролита [8]. В работе [9] диффузия кальция из электрода Y0.8Ca0.2Cr0.8Co0.2O3 – δ (YCCC) в электролит YSZ привела к образованию продукта взаимодействия, что стало причиной сильного роста омического и поляризационного сопротивления электрохимической ячейки Pt/YSZ/YCCC/Pt.
Ранее была изучена возможность получения пленки электролита CaZr0.9Y0.1O3 – δ (CZY) химическим растворным методом на композиционных подложках – CuO-CaZr0.95Sc0.05O3 – δ (CuO-CZS), Fe2O3-CZS и NiO-CZS [10]. Данные рентгенофазового анализа (РФА), сканирующей электронной микроскопии (СЭМ) и элементного анализа показали, что железо и медь, содержащиеся в подложках CuO-CZS и Fe2O3-CZS, диффундируют в пленку при отжиге, в результате чего образуются неоднофазные пленки с высоким содержанием оксидов металлов. Пленки, полученные на Ni-CZS однофазны, поэтому композит Ni-CZS можно использовать в качестве материала несущего анода для пленок CZY.
При разработке топливных ячеек с пленкой на несущем электроде, основной проблемой, приводящей к низкой мощности, становится вклад поляризационных потерь, который увеличивается с понижением температуры. Авторы [11] показали, что при 700°С в топливной ячейке Ni-BaCe0.8Sm0.2O2.9 (BSCO)/пленка BCSO/Ba0.5Sr0.5Co0.8Fe0.2O3 – δ-BCSO может быть достигнута мощность в 340 мВт/см2, тогда как при снижении температур до 450°С этого не удается сделать из-за высокого поляризационного сопротивления электродов. В работе [12] топливная ячейка Pt|пленка BaCe0.8Y0.2O3 – δ|Ni-BaCe0.8Y0.2O3 – δ по причине высокого поляризационного сопротивления показала мощность 80 мВт/см2 при 600°С.
Электрохимические характеристики топливных ячеек с пленкой CZY на несущем никель-керметном аноде еще ранее не исследовались, что представляет интерес. В работе были измерены спектры импеданса, напряжение разомкнутой цепи (НРЦ) и вольт-амперные зависимости топливных ячеек. Основной целью работы являлось изучить влияние взаимодействия пленочного электролита CZY с несущим никель-керметным анодом на электрохимические характеристики топливных ячеек.
ЭКСПЕРИМЕНТАЛЬНАЯ ЧАСТЬ
Получение пленок
Для получения пленок использовали подложки NiO-CZS, спеченные при 1400°С на воздухе в течение 2 ч. Открытая пористость NiO-CZS составила 23%. Согласно данным РФА и СЭМ, композит NiO-CZS был представлен исходными фазами [10].
Пленки CZY получали химическим растворным методом. В качестве прекурсоров использовали спиртовые растворы солей (пленкообразующий раствор) и спиртовые суспензии. Для приготовления пленкообразующего раствора готовили индивидуальные растворы солей ZrOCl2, Ca(NO3)2 и Y(NO3)3 в этаноле, смешанные в строго определенном соотношении, чтобы получить CaZr0.9Y0.1O3 – δ. Суспензии готовили из пленкообразующего раствора и порошка, полученного из этого раствора путем высушивания и отжига при 550°С, в количестве 0.025 г на 1 мл раствора. Нанесение пленок CZY проводили по технологии dip-coating. Для этого подложки погружали в контейнер с пленкообразующим раствором или суспензией, вытягивали со скоростью 2 мм/мин, сушили в течение 5 мин, затем синтезировали пленки CZY на воздухе при температуре 1000°С.
Путем 30-кратного повторения процедуры окунания–сушки–отжига получали пленки из раствора солей. Суспензии в отличие от пленкообразующих растворов обладают большей вязкостью, меньше впитывается в пористую подложку и быстрее формирует сплошное покрытие на поверхности. Поэтому для получения пленок из суспензии проводили 4-кратное нанесение суспензии с последующим 4-кратным нанесением пленкообразующего раствора для “залечивания” микро- и нанодефектов – трещин и пор. После каждого нанесения раствора или суспензии проводили термообработку при 1000°С в течение 1 ч.
Методы аттестации образцов
Фазовый состав пленок изучали с помощью метода РФА на дифрактометре Dmax 2200 (Rigaku, Япония) в медном Кα-излучении (λ = 1.54056 Å). Анализ рентгеновских данных проводили с помощью автоматизированного поиска по базе JCPDS.
Микроструктуру и элементный состав пленок исследовали методом СЭМ на микроскопе MIRA 3 LMU (TESCAN, Чехия) с приставкой для элементного анализа методом энергодисперсионной рентгеновской спектроскопии.
Величину открытой пористости композитов рассчитывали по методу гидростатического взвешивания в керосине (ГОСТ 2409-95, ИСО 5017-88).
Газопроницаемость образцов определяли с помощью компьютеризированной установки АГП (Межгосударственный стандарт ГОСТ 11573-98).
Измерения спектров импеданса и вольт-амперных зависимостей топливных ячеек проводили с помощью импульсного потенциостата-гальваностата P-45X (Elins, Россия) со встроенным модулем частотного анализатора для измерения электрохимического импеданса. Вольт-амперные зависимости измеряли в потенциостатическом режиме со скоростью развертки потенциала 0.5 мВ/с. Измерения электрохимического импеданса топливной проводились в интервале частот 0.1 Гц–500 кГц при амплитуде переменного напряжения 30 мВ.
Изготовление топливных ячеек
Были изготовлены ячейки с несущим анодом – рО2(2),Pt|Ni-CZY|CZY|Pt,рО2(1) – и несущим электролитом – рО2(2),Pt|CZS|Pt,рО2(1). Ячейка с несущим электролитом на основе цирконата кальция (CZS) и платиновыми электродами была изготовлена для более достоверной интерпретации электрохимических характеристик топливных ячеек с пленочным электролитом. Обозначения и конфигурации топливных ячеек приведены в табл. 1.
Таблица 1.
Конфигурация и обозначения топливных ячеек
Электролит | Конфигурация ячейки | Обозначение ячейки |
---|---|---|
CZY пленка 2 мкм |
рО2(2),Pt|Ni-CZY|CZY|Pt,рО2(1) | С1 |
CZY пленка 4 мкм |
рО2(2),Pt|Ni-CZY|CZY|Pt,рО2(1) | С2 |
CZS 880 мкм |
рО2(2),Pt|CZS|Pt,рО2(1) | С3 |
Схема установки для проведения измерений приведена на рис. 1. Образцы прикрепляли и герметизировали к торцу YSZ-трубки, имеющей два отверстия (для подвода и отвода газа), с помощью стеклогерметика помещали в трубчатую печь, имеющую свой газовый контур, нагревали до температуры стеклования (950°С, скорость нагрева 100 град/ч), выдерживали 10 мин и охлаждали до 800°С (скорость охлаждения 50 град/ч).
Восстановление NiO до металлического никеля в композите NiO-CZS проводили по следующей схеме: сначала на образец подавали влажный аргон (рН2О = 3169 Па) в течение двух часов с расходом аргона 2 л/ч, затем подавали смесь с соотношением 10% Н2 (расход 0.2 л/ч) + 90% Ar (расход 1.8 л/ч), далее с шагом в 10% увеличивали концентрацию водорода по отношению к аргону, затем подавали чистый водород с расходом 2 л/ч. В каждой из атмосфер для достижения равновесия с газовой фазой образец выдерживали в течение одного часа. Соотношение аргона к водороду в смеси задавали с помощью регуляторов расхода газа РРГ-12, регулируемых блоком управления БУИП 3 (Элточприбор, Россия).
РЕЗУЛЬТАТЫ И ОБСУЖДЕНИЕ
Фазовый состав и микроструктура пленок
Согласно данным РФА (рис. 2), пленки, синтезированные из раствора и суспензии при 1000°С, являются однофазными. Присутствие линий NiO обусловлено откликом подложки.
Рис. 2.
Рентгенограммы пленки CZY на композите NiO-CZS, снятые в стандартном режиме: внизу – пленка из раствора, вверху – пленка из суспензии после синтеза 1000°С на воздухе.
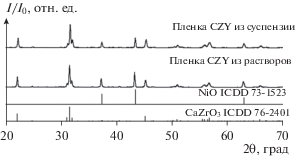
Согласно данным СЭМ (рис. 3а), пленка, полученная после 30-кратного синтеза из растворов солей, выглядит плотной, а ее толщина составляет 4 мкм (рис. 3б). На рис. 4 приведены микрофотографии пленки CZY, полученной из суспензии. Пленка имеет плотную зернистую структуру (рис. 4а) и обладает толщиной 2 мкм (рис. 4б). Таким образом, получение пленок из суспензии позволило сократить число нанесений прекурсора с 30 до 8 раз.
Рис. 3.
Микрофотографии пленки CZY на композите NiO-CZS: (а) поверхность пленки СZY; (б) поперечное сечение образца “пленка CZY/ NiO-CZS”.
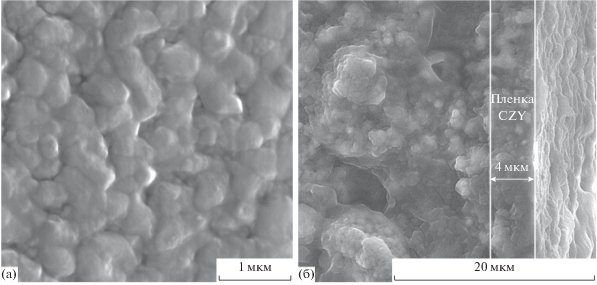
Рис. 4.
Микрофотографии пленки CZY на композите NiO-CZS (пленка, полученная из суспензии): (а) поверхность пленки; (б) поперечное сечение образца “пленка CZY/NiO-CZS”.
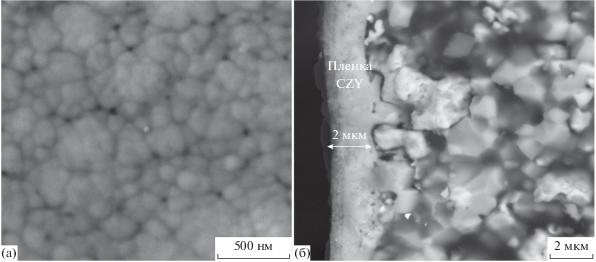
Элементный состав пленок CZY на композитах NiO-CZS был изучен методом энергодисперсионной рентгеновской спектроскопии. Было обнаружено, что в процессе синтеза пленки происходит диффузия никеля, а его концентрация в пленке уменьшается по мере увеличения толщины пленки. На поверхности пленки толщиной 2 мкм содержится 1.5 ат. % никеля (рис. 4а), тогда как в пленке 4 мкм концентрация никеля не превышает 0.5 ат. % (рис. 3а).
В работе проводились исследования газопроницаемости пленки CZY толщиной 2–4 мкм на подложках NiO-CZS. Газопроницаемость подложки NiO-CZS до нанесения пленки составляла 4.6 × 10–3 мкм2, а после нанесения пленки толщиной 2–4 мкм снижалась до нуля, что указывает на высокую газоплотность пленки.
Числа переноса ионов в пленочном электролите CZY на несущем аноде Ni-CZS
Для установления равновесия с газовой фазой топливные ячейки с пленкой толщиной 2 и 4 мкм (С1 и С2) и ячейку с несущим электролитом (С3) выдерживали в течении 24 ч при температуре 800°С и постоянной подаче влажного воздуха на катод и влажного водорода на анод (рН2О = 3169 Па).
Годографы импеданса топливных ячеек можно разделить на две части: высокочастотный полукруг, отсекающий на реальной оси импеданса омическое сопротивление электролита и низкочастотная полуокружность, соответствующая поляризационному сопротивлению электродов (рис. 5). Видно, что поляризационное и омическое сопротивление ячейки С1 сопоставимы, тогда как в ячейке С2 преобладает вклад поляризационного сопротивления.
Причиной такого поведения ячеек С1 и С2 может быть разная доля электронная проводимости электролита. Для того чтобы проверить это предположение, были измерены числа переноса ионов в пленочных электролитах ячеек С1, С2 и С3.
Числа переноса ионов определяли с помощью измерения НРЦ и спектров импеданса топливной ячейки, как описано в работе [13]. Теоретическое значение ЭДС (ЕN) рассчитывали по формуле Нернста:
(1)
${{E}_{{\text{N}}}} = \frac{{RT}}{{4F}}\ln \frac{{p{{{\text{O}}}_{2}}(1)}}{{p{{{\text{O}}}_{2}}(2)}},$Из рис. 6 можно видеть, что с понижением температуры теоретическое значение ЭДС Нернста и НРЦ ячейки с несущим электродом увеличивается, тогда как измеряемое НРЦ топливных ячеек с пленкой снижается. Высокая газоплотность пленок СZY (газопроницаемость составляла ~5 × 10–5 мкм2 для пленок толщиной 2 и 4 мкм) позволяет исключить причину снижения НРЦ, связанную с дефектностью пленки.
Для изучения влияния негерметичности ячейки С1 на величину НРЦ были проведены измерения при разных скоростях подачи водорода – от 2 до 4 л/ч. Из рис. 7 и 8 видно, что НРЦ ячейки изменяется незначительно, а годографы импеданса остаются практически неизменными. Таким образом, снижение НРЦ, связанное с негерметичностью ячеек, незначительно по сравнению с величиной его отклонения от теоретических значений.
Числа переноса ионов можно рассчитать как отношение измеряемого НРЦ (ЕМ) к теоретическому значению ЭДС Нернста (ЕN) по формуле:
Следует отметить, что формулой (2) можно пользоваться только в случае идеально поляризуемых электродов, что на практике встречается довольно редко. Наличие электронной проводимости в электролите и поляризационного сопротивления электродов топливного элемента будет приводить к занижению чисел переноса ионов по сравнению с формулой (2), что необходимо учитывать для корректной оценки чисел переноса ионов. В работе Liu [13] показано отличие реальных чисел переноса ионов от рассчитанных по формуле (2).
Liu разработал подход по определению чисел переноса в смешанных проводниках с учетом поляризации электродов [14]. Суть подхода заключается в использовании комбинации методов – метода электрохимического импеданса и измерения НРЦ топливной ячейки. Согласно Liu, из общего импеданса ячейки (Rt) на высоких частотах можно выделить омическое сопротивление электролита (Rb). С учетом измеренного ЕМ и рассчитанного теоретического значения ЕN числа переноса ионов в электролите CZY могут быть определены в соответствии с формулой:
(3)
${{t}_{i}} = 1 - \frac{{{{R}_{{\text{b}}}}}}{{{{R}_{{\text{t}}}}}}\left( {1 - \frac{{{{E}_{{\text{M}}}}}}{{{{E}_{{\text{N}}}}}}} \right),$Числа переноса ионов в пленке 2 мкм (ячейка С1) cоставили 0.84–0.86, что значительно отличается от литературных данных для керамики цирконата кальция, допированного скандием (ti = 0.98, по данным [6]), и от данных для пленки CZY на подложке STF (0.93–0.97, по данным [15]). В пленке СZY толщиной 4 мкм (ячейка С2) и в керамическом электролите СZS (ячейка С3) числа переноса ионов близки к единице (рис. 9).
С учетом данных энергодисперсионной рентгеновской спектроскопии, указывающих на большее содержание никеля в более тонкой пленке, можно предположить, что диффузия никеля приводит к увеличению доли электронного переноса в пленочном электролите CZY. В тонкой пленке высокая электронная проводимость электролита приводит к снижению поляризационного сопротивления электродов и уменьшению НРЦ топливной ячейки. В более толстой пленке вклад электронной проводимости достаточно мал, а причиной снижения НРЦ ячейки является высокое поляризационное сопротивление (рис. 5).
Вольт-амперные и мощностные характеристики единичных топливных ячеек. Анализ потерь мощности
Электронная проводимость и высокое поляризационное сопротивление приводят к низкой мощности топливных ячеек С1 и С2 – 0.85 и 0.148 мВт/см2 при 700°С соответственно (рис. 10). Ячейка с несущим электролитом (С3) обладает большей мощностью (рис. 10) из-за сравнительно небольшого вклада поляризационного сопротивления (рис. 5). Интересным фактом является то, что мощность топливных ячеек с пленкой возрастает с уменьшением толщины электролита (0.15 и 0.85 мВт/см2 при толщине электролита 4 и 2 мкм при температуре 700°С). Причиной роста мощности является уменьшение поляризационного сопротивления из-за увеличения электронной составляющей проводимости электролита, благодаря чему происходит расширение зоны электродной реакции и снижение поляризационных потерь.
Мощностные характеристики топливных ячеек с пленкой CZY получились достаточно низкими по сравнению литературными данными для ячеек NiO-BaZr0.8Y0.2O3 – δ | BaZr0.8Y0.2O3 – δ | PrBaCo2O5 + δ-BaZr0.8Y0.2O3 – δ (Р = 330 мВт/см2 при 650°С), где в качестве электролита использовали пленку BaZr0.8Y0.2O3 – δ, полученную на никель-керметном аноде [101]. Ячейка продемонстрировала хорошую мощность по причине высокой проводимости электролита BaZr0.8Y0.2O3 – δ и низкого поляризационного сопротивления электродов. Для увеличения удельной мощности в ячейках с пленкой CZY необходимо уменьшить толщину несущего анода Ni-CZS и улучшить его микроструктуру, чтобы снизить поляризационное сопротивлении электродов. Анализ электрохимических характеристик топливных ячеек показал, что толщина пленочного электролита CZY на несущем никель-керметном аноде должна быть достаточно большой, так как диффузия никеля (протекающая в основном при синтезе пленки (1000°С), температура которого значительно выше температуры измерений), приводит к росту электронной проводимости в пленочной мембране.
Для анализа факторов, приводящих к низкой мощности топливных ячеек, проводили оценку потерь на электролите, катоде и аноде. Сопротивление электролита, в первом приближении, не зависит от приложенного внешнего тока, поэтому омические потери (IRэл) определяли в бестоковом режиме и рассчитывали по формуле:
где Rb – омическое сопротивление электролита, определенное из спектра импеданса топливной ячейки, I – ток, пропускаемый через ячейку.Для оценки вклада платинового катода в потери мощности топливной ячейки измеряли годографы импеданса симметричной ячейки С3 на воздухе при внешнем постоянном токе 0–1.45 мА (рис. 11).
Рис. 11.
Годографы импеданса электрохимической ячейки С3 при 800°С на воздухе в зависимости от приложенного внешнего постоянного тока 0–1.45 мА.
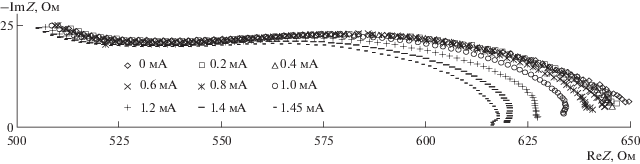
Из рис. 11 видно, что поляризационное сопротивление ячейки С3 слабо зависит от приложенного тока. Поэтому в первом приближении поляризационное сопротивление катода топливной ячейки можно считать равным $\frac{{{{R}_{{\eta }}}}}{2},$ где Rη − поляризационное сопротивление ячейки С3, а поляризационные потери на платиновом катоде топливной ячейки составляют
где I – величина внешнего тока.Путем вычитания омических и катодных потерь из напряжения ячейки были определены поляризационные потери на аноде в зависимости от тока.
Из рис. 12 видно, что при 800°С в топливной ячейке с несущим электролитом (С3) преобладают омические потери. В ячейках с несущим анодом (рис. 13) основные потери приходятся на анод Ni-CZS, поэтому для улучшения электрохимических характеристик топливных ячеек с пленкой CZY необходимо уменьшение толщины и улучшение микроструктуры несущего анода.
ВЫВОДЫ
Выявлено, что в процессе синтеза пленки CZY на несущем аноде Ni-CZS происходит диффузия никеля в пленку, а его концентрация уменьшается по мере увеличения толщины пленки. На поверхности пленки 2 мкм обнаружено 1.5 ат. % никеля, а в пленке 4 мкм не более 0.5 ат. %.
Впервые определены числа переноса ионов в пленках CZY на Ni-CZS; показано, что они зависят от толщины пленки. При температуре 700°С в пленочном электролите толщиной 2 мкм число переноса ионов составляет 0.86, толщиной 4 мкм – 0.96, а в массивном электролите – 0.99. С учетом данных по элементному составу пленок CZY, указывающих на увеличение содержания никеля в пленочном электролите с уменьшением его толщины, сделано заключение, что диффузия никеля из несущего электрода в электролит влечет увеличение электронной проводимости. Таким образом, для обеспечения достаточно высоких чисел переноса ионов толщина пленочного электролита CZY на несущем Ni-керметном аноде должна быть не менее 4 мкм.
На основе сравнения результатов исследования электрохимических характеристик топливных ячеек с пленочным и несущим электролитом из цирконата кальция установлено, что основной причиной снижения мощности топливной ячейки с пленочным электролитом являются поляризационные потери на аноде.
Выявлено, что мощность топливных ячеек с пленочным электролитом возрастает с уменьшением толщины электролита (0.15 и 0.85 мВт/см2 при толщине электролита 4 и 2 мкм при температуре 700°С). Причиной роста мощности является уменьшение поляризационного сопротивления из-за увеличения электронной составляющей проводимости электролита, благодаря чему происходит расширение зоны электродной реакции и снижение поляризационных потерь.
Список литературы
Коровин, Н.В. Топливные элементы и электрохимические установки, М: МЭИ, 2007. 280 с. [Korovin, N.V., Fuel Cells and Electrochemical Installations (in Russian), Moscow: MEI, 2007. 280 p.]
Коровин, Н.В. Электрохимическая энергетика, М: Энергоатомиздат, 1991. 264 с. [Korovin, N.V., Electrochemical Power Engineering (in Russian), Moscow: Energoatomizdat, 1991. 264 p.]
Коровин, Н.В. Электрохимические энергоустановки на основе топливных элементов. Теплоэнергетика. 1994. Т. 1. С. 22. [Korovin, N.V., Electrochemical power apparatus based on fuel cells, its state of the art and prospects, Russ. J. Teploenerg., 1994, vol. 1, p. 22.]
Коровин, Н.В. Электрохимическая энергетика. 1997. № 2. С. 49. [Korovin, N.V., Electrochemical Power Engineering, Izvestia RAN Seria Energetika (in Russian), 1997, no. 4, p. 49.]
Jiang, S. and Yan, Y., Materials for High-Temperature Fuel Cells, Weinheim: Wiley-VCH, 2013. 158 p.
Горелов, В.П., Балакирева, В.Б., Кузьмин, А.В., Плаксин, С.В. Проводимость CaZr1 –xScxO3 – α (x = = 0.01–0.20) в сухом и влажном воздухе. Неорган. материалы. 2014. Т. 50. С. 535. [Gorelov, V.P., Balakireva, V.B., Kuzmin, A.V., and Plaksin, S.V., Electrical Conductivity CaZr1 –xScxO3 – α (x = 0.01–0.20) in dry and humid air, Russ. J. Neorg. Mater., 2014, vol. 50, p. 495.]
Bao, J., Ohno, H., Kurita, N., Okuyama, Y., and Fukatsu, N., Proton conduction in Al-doped CaZrO3, Electrochim. Acta, 2011, vol. 56, p. 1062.
Naoumidis, A., Ahmad-Khanlou, A., Samardzidja, Z., and Kolar, D., Chemical interaction and diffusion on interface cathode/electrolyte of SOFC, Fres. J. Anal. Chem, 1999, vol. 365, p. 277.
Yan, K., Kishimoto, H., Develos-Bagariano, K., Yamaji, K., Horita, T., and Yokokawa, H., Effects of sintering atmosphere on the interaction between doped yttrium chromite anode and yttria stabiliized zirconia electrolyte, Solid State Ionics, 2017, vol. 307, p. 21.
Куимов, В.М., Халиуллина, А.Ш., Панкратов, А.А., Антонов, Б.Д., Дунюшкина, Л.А. Синтез и электропроводность пленок электролита CaZr0.9Y0.1O3 – δ на несущих композиционных электродах. Электрохимия. 2018. Т. 154. С. 195. [Kuimov, V.M., Khaliul-lina, A.Sh., Pankratov, A.A., Antonov, B.D., and Dunyushkina, L.A., Synthesis and Conductivity of CaZr0.9Y0.1O3-δ Electrolyte Films on Supporting Electrode, Russ. J. Electrochem., 2018, vol. 54, p. 170.]
Ranran, P., Yan, W., Lizhai, Y., and Zongqiang, M., Electrochemical properties of intermediate-temperature SOFCs based on proton conducting Sm-doped BaCeO3 electrolyte thin film, Solid State Ionics, 2006, vol. 177, p. 389.
Itagaki, Y., Yamamoto, Y., Aono, H., and Yahiro, H., Anode-supported SOFC with thin film of proton-conducting BaCe0.8Y0.2O3 – δ by electroforetic deposition, J. Ceramic Soc. of Japan, 2017, vol. 125, p. 528.
Liu, M. and Hu, H., Properties of Mixed-Conducting Electrolytes, J. Electrochem. Soc., 1996, vol. 143, p. L109.
Agarwal, V. and Liu, M., Electrochemical properties of BaCe0.8Gd0.2O3 electrolyte films deposited on Ni-BaCe0.8Gd0.2O3 substrates, J. Electrochem. Soc., 1997, vol. 144, p. 1035.
Dunyushkina, L.A., Pankratov, A.A., Gorelov, V.P., Brouzgou, A., and Tsiakaras, P., Deposition and Characterization of Y-doped CaZrO3 Electrolity film on a Porous SrTi0.8Fe0.2O3 – δ Substrate, Electrochim. Acta, 2016, vol. 202, p. 39.
Дополнительные материалы отсутствуют.