Электрохимия, 2020, T. 56, № 1, стр. 56-86
Электрохимическое локальное безмасковое микро/нано размерное осаждение, растворение и оксидирование металлов и полупроводников (обзор)
А. Д. Давыдов a, *, В. М. Волгин a, b, **
a Институт физической химии и электрохимии им. А.Н. Фрумкина РАН
119071 Москва, Ленинский просп., 31, Россия
b Тульский государственный университет
300012 Тула, просп. Ленина, 92, Россия
* E-mail: davydov@elchem.ac.ru
** E-mail: volgin@tsu.tula.ru
Поступила в редакцию 26.03.2019
После доработки 03.05.2019
Принята к публикации 06.07.2019
Аннотация
Обзор посвящен современным методам локальной безмасковой электрохимической обработки металлов и полупроводников с целью нанесения на их поверхность отдельных островков или углублений, их групп, рисунков по заданной программе или микро/нано 3D структур, например, металлических нитей и различных конструкций из них. Для этого используются различные методы локализации процессов электрохимического осаждения, растворения или оксидирования.
СОДЕРЖАНИЕ
1. Введение
2. Электрохимическое осаждение, растворение и оксидирование с микро/нано размерными электродами-инструментами (ЭИ) и межэлектродными расстояниями (МЭР)
2.1. Электрохимическое растворение электродом-инструментом в виде тонкого стержня
2.2. Применение ультракоротких импульсов для увеличения степени локализации процессов
2.3. Формирование металлических нитей и более сложных микроструктур подвижным микродисковым электродом-инструментом
2.4. Использование сканирующих зондовых микроскопов (СЗМ)
3. Электрохимическое осаждение и растворение электродом-инструментом в микро/нано размерных пипетках, соплах
3.1. Формирование микроструктур подвижным микроэлектродом в свободной пипетке через жидкостный мениск
3.2. Формирование микроструктур подвижным микроэлектродом в погруженной в электролит пипетке
3.3. Электроосаждение металла с использованием СЗМ с зондом в виде микропипетки с электролитом
3.4. Использование электрохимических микроячеек
3.5. Струйная электрохимическая микрообработка
4. Локализация электроактивного компонента электролита в зоне обработки
4.1. Локальное электроосаждение металла с растворимым анодом
4.2. Локальное электроосаждение металла с нерастворимым анодом. Метод химических линз
4.3. Локальное травление в режиме положительной обратной связи
4.4. Локальное травление металлов и полупроводников. Метод ограничения толщины слоя травителя
4.5. Локальное электроосаждение металла с зондом СЗМ, не являющимся электродом
5. Лазерно-электрохимическая (ЛЭХО) и струйная лазерно-электрохимическая обработка
5.1. Изменение равновесного потенциала
5.2. Увеличение скорости реакции, протекающей в режиме замедленного разряда
5.3. Ускорение массопереноса в диффузионном пограничном слое
5.4. Изменение выхода по току
5.5. Изменение степени пассивности металла
5.6. Термические напряжения и пластическая деформация в поверхностном слое металла
5.7. ЛЭХО полупроводников
5.8. Струйная лазерно-электрохимическая обработка
6. Заключение
1. ВВЕДЕНИЕ
Для формирования нано- и микроструктурированных поверхностей, 3D микроструктур успешно используются различные схемы электрохимического формообразования [1–3], обладающие рядом важных преимуществ: отсутствие механического и теплового воздействий на обрабатываемую заготовку (кроме лазерной электрохимической обработки), отсутствие износа инструмента, широкие возможности управления формой и размерами микроструктур за счет изменения режимов обработки, относительная простота и низкая стоимость процессов электрохимической обработки (ЭХО), хорошая воспроизводимость результатов.
Методы микро/нано ЭХО подразделяются на субтрактивные и аддитивные. В первом случае структурированная поверхность формируется в результате локального удаления материала с исходной заготовки, а во втором случае она формируется в результате локального электроосаждения материала на поверхность исходной заготовки [4].
Методы микро/нано ЭХО нашли применение при изготовлении микроэлектромеханических систем, в которых миниатюрные механические компоненты комбинируются с электронными цепями и в других современных технологиях.
Важным направлением метод локального электрохимического оксидирования металлов и полупроводников стал при решении задач микроэлектроники.
Безмасковые технологии позволяют избавиться от многостадийности технологических процессов ЭХО, локализация в которых обеспечивается частичным закрытием поверхности обрабатываемой детали масками, в первую очередь фоторезистивными масками.
К типичным задачам микро/нано ЭХО можно отнести выращивание микропроволочек, металлических нитей, столбиков с высоким аспектным отношением (отношением длины проволочки к ее диаметру), создание отдельных островков или углублений и их групп на подложках из металлов, нанесение “рисунков” линиями нужной формы и размеров электроосаждением, растворением или оксидированием металлов при движении электрода-инструмента (ЭИ) вдоль поверхности подложки по заданной траектории. При этом могут быть получены как одномерные, так 2D и 3D структуры. Эти же методы применяются для микроструктурирования поверхности полупроводников.
Основным методом локализации электрохимических процессов осаждения, растворения, оксидирования металлов в микро- и наномасштабах является локализация электрического поля применением ЭИ в виде микроэлектрода и микронных и субмикронных межэлектродных расстояний (МЭР). Микроэлектрод может быть в виде иглы, торца проволоки, капилляра, заполненного электролитом с противоэлектродом внутри, или специально приспособленного зонда сканирующего зондового микроскопа (СЗМ). Разработан и используется ряд дополнительных приемов локализации. К ним относятся специальные электрические режимы (ультракороткие импульсы), локализация активного компонента электролита в рабочей зоне, например, в “трубке” электролита между микроэлектродом и микроучастком поверхности обрабатываемой детали (ОД), сфокусированное в заданной “точке” на поверхности ОД лазерное излучение.
Практическое использование методов микро- и наноэлектрохимической обработки металлов требует специального оборудования. Обычно ОД закрепляется на горизонтальном двухкоординатном столе, позволяющем устанавливать ОД в необходимом положении относительно вертикально расположенного ЭИ, или передвигать ОД по заданной программе для создания на ней требуемого рисунка. Имеется устройство высокоточного (до нескольких нм) позиционирования ЭИ на заданном расстоянии от ОД, источник питания, система управления всеми параметрами процесса.
Процессы локального электросаждения проводятся в электрохимических ячейках различных типов в потенциостатических или гальваностатических условиях, в импульсных режимах по двух-, трех- и четырехэлектродной схеме с применением регулируемых источников напряжения, потенциостатов и бипотенциостатов. Применение бипотенциостатов позволяет поддерживать независимые значения потенциалов зонда и подложки относительного одного электрода сравнения. Применяется также схема без соединения подложки с внешним источником питания, когда потенциал ОД задается использованием определенной редокс пары в растворе.
Локальное осаждение для получения микро/наноструктур проводят в тех же электролитах, которые обычно используются в традиционной гальванотехнике. Для локального растворения используются растворы кислот, щелочи или солей.
Некоторые из представленных в обзоре методов локальной ЭХО уже нашли практическое применение, другие показывают их разнообразные возможности, представляют большой научный интерес.
2. ЭЛЕКТРОХИМИЧЕСКОЕ ОСАЖДЕНИЕ, РАСТВОРЕНИЕ И ОКСИДИРОВАНИЕ С МИКРО/НАНО РАЗМЕРНЫМИ ЭЛЕКТРОДАМИ-ИНСТРУМЕНТАМИ (ЭИ) И МЕЖЭЛЕКТРОДНЫМИ РАССТОЯНИЯМИ (МЭР)
2.1. Электрохимическое растворение металла электродом-инструментом в виде тонкого стержня
При анодном растворении большое распространение получили ЭИ в виде тонкого стержня часто из вольфрама или WC, перемещающегося в процессе электрохимической микрообработки по заданной траектории (рис. 1). Боковая поверхность в различных случаях либо свободна от изоляции, либо защищена изоляционным слоем за исключением кончика определенной длины.
Рис. 1.
Пример локального электрохимического растворения металла электродом-инструментом в виде тонкого стержня.
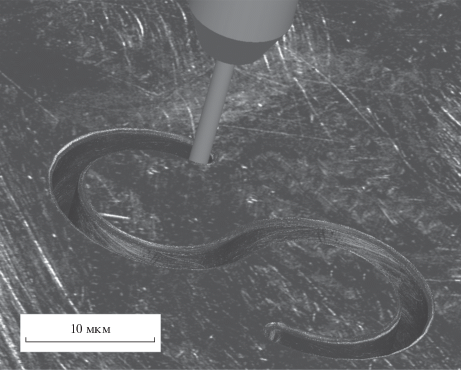
Этот метод позволяет наносить различные рисунки на металлические поверхности, проводить микроструктурирование поверхности, выполнять операции электрохимического гравирования.
В работах по прямому локальному электрохимическому растворению металлов использовались не только тонкие цилиндрические или иглообразные электроды-инструменты. Применение ЭИ с микросферическим или микродисковым концом повышает степень локализации и стабильность процесса обработки [5–7].
В работах этого направления, как правило, использовали ультакороткие импульсы длительностью от нескольких единиц до нескольких сотен нс [7–12]. Объяснение этому дано в следующем разделе обзора. Для ЭХО различных материалов таким методом обычно использовали водные растворы кислот (HCl, H2SO4) [7, 8, 10] и неводные, например, спиртовые, растворы (HClO4, NaBr) [9, 12].
Ли и соавт. [13] описали электродное устройство для микроЭХО, содержащее более ста элементов, столбиков длиной 800 мкм квадратного, треугольного или круглого сечения диаметром 100 мкм для получения одновременно такого же количества отверстий в пластине из никеля. Расстояние между центрами соседних элементов 300 мкм. Боковая поверхность каждого элемента покрыта изолирующим составом, что служит повышению точности обработки. МЭР при обработке составляет 10–20 мкм и в некоторых случаях даже меньше. Эвакуация продуктов электродных реакций при такой обработке значительно затруднена по сравнению с обработкой ЭИ в виде одного стержня. Для решения этой проблемы предложено использовать специальный режим, который для обычной размерной ЭХО был разработан много лет назад и назван импульсно-циклической ЭХО [14–16]. В этом методе синхронизировано циклическое изменение положения ЭИ относительно ОД с подачей серии коротких импульсов напряжения. Было разработано несколько вариантов синхронизации. Например, подведение ЭИ до касания с ОД, отведение на заданное расстояние (рабочее МЭР) и пропускание серии коротких импульсов (процесс обработки), отведение ЭИ на большее расстояние для промывки межэлектродного пространства потоком электролита в отсутствии пропускания тока, очередное подведение ЭИ до касания с ОД и т.д. В работе [13] серии коротких импульсов напряжения пропускали при рабочей величине МЭР, а в периоды отведения ЭИ от ОД и возвращения к рабочей величине МЭР выдерживались паузы в пропускании тока. Авторы работы [13] продемонстрировали высокую эффективность такого метода на примере ЭХО серий микроотверстий различных форм поперечного сечения с малой конусностью (около 1.4°) в никелевой пластине толщиной 100 мкм. Длительность импульсов и пауз составляла 20 мкс. Процесс проводили в 0.25 моль/л растворе NaClO3.
Аналогичная задача облегчения удаления продуктов электродных реакций при импульсной ЭХО с очень малыми МЭР электродным устройством с несколькими десятками элементов в виде микропроволочек была решена в работе [17] применением вибрирующего электродного устройства. Вибрация синхронизирована с подачей импульсов напряжения, так что импульсы подаются в те короткие промежутки времени, когда ЭИ находится на малых расстояниях от ОД, паузы между импульсами совпадают с периодами времени, когда КИ отведен от ОД для промывки межэлектродного пространства. В этой работе приведены примеры ЭХО для получения отверстий, микроразмерных шестеренчатых колес. Эти процессы проводили в 5% растворе NaNO3 при импульсном напряжении несколько вольт и частоте 5 кГц. Было показано как увеличение напряжения до 5 В приводит к увеличению диаметра и глубины получаемых отверстий. В отличие от широко распространенного режима в обычной (не микро/нано) размерной ЭХО с вибрирующим электродом [14–16, 18] авторы [17] не применяли вынужденный поток электролита и в раствор NaNO3 добавляли абразивный порошок, как это делается в обычной совмещенной электрохимической и абразивной обработке, например [19]. Такой метод характеризуется некоторым износом ЭИ в процессе обработки.
Метод прямого анодного растворения заостренным W проволочным ЭИ применим и для микроЭХО полупроводниковых материалов при правильном подборе состава электролита и режима обработки [20, 21].
2.2. Применение ультракоротких импульсов для увеличения степени локализации процесса
Во многих работах по микро/нано ЭХО использован метод локализации процессов растворения и осаждения металлов, основанный на применении ультракоротких (в наносекундном диапазоне) импульсов напряжения [22–24]. Этот метод совместно с очень малым МЭР позволяет получать особенно высокие степени локализации.
Рассмотрим механизм этого метода локализации процессов.
Приложенное напряжение между ЭИ и ОД должно обеспечить преодоление омического сопротивления слоя раствора между электродами и поляризацию электродов, необходимую для протекания электрохимических реакций с достаточной скоростью; последнее требует первоначального заряжения двойного электрического слоя (ДЭС) на электродах (нас будет интересовать электрод, на поверхность которого наносится рисунок). Омическое падение потенциала устанавливается очень быстро, а заряжение ДЭС происходит значительно медленнее. Характерное значение времени заряжения объема раствора электролита (время установления омического падения потенциала) равно ${{\lambda _{{\text{D}}}^{2}} \mathord{\left/ {\vphantom {{\lambda _{{\text{D}}}^{2}} D}} \right. \kern-0em} D}$, где ${{\lambda }_{{\text{D}}}} = \sqrt {\frac{{{{\varepsilon }_{0}}{{\varepsilon }_{{\text{r}}}}RT}}{{{{F}^{2}}\sum {z_{i}^{2}{{c}_{{i,{\text{b}}}}}} }}} $ – радиус Дебая; D – коэффициент диффузии электроактивного иона; ${{\varepsilon }_{0}}$ – электрическая постоянная; ${{\varepsilon }_{{\text{r}}}}$ – относительная диэлектрическая проницаемость раствора; R – универсальная газовая постоянная; T – температура раствора; F – постоянная Фарадея; zi, ci, b – зарядность и объемная концентрации ионов i-го сорта, соответственно. Например, для 1 : 1 электролита с концентрацией 1 М (${{\lambda }_{{\text{D}}}} \approx 3 \times {{10}^{{ - 10}}}$ м) и коэффициентами диффузии равными 10–9 м2/с получаем следующее значение характерного времени установления омического падения потенциала в растворе ${{{{{\left( {3 \times {{{10}}^{{ - 10}}}} \right)}}^{2}}} \mathord{\left/ {\vphantom {{{{{\left( {3 \times {{{10}}^{{ - 10}}}} \right)}}^{2}}} {{{{10}}^{{ - 9}}}}}} \right. \kern-0em} {{{{10}}^{{ - 9}}}}} \approx {{10}^{{ - 10}}}\,\,{\text{с}} = {\text{0}}{\text{.1}}\,\,{\text{нс}}{\text{.}}$ В то время как характерное время заряжения ДЭС определяется следующим соотношением: $\frac{{2RTC}}{{nFi_{{\text{Ф}}}^{\infty }}}\ln \frac{{i_{{\text{Ф}}}^{\infty }}}{{{{i}_{0}}}},$ где С – удельная емкость ДЭС; i0 – плотность тока обмена; $i_{{\text{Ф}}}^{\infty }$ – стационарное (установившееся) значение фарадеевской плотности тока. Значение характерного времени заряжения ДЭС при $C = 0.2\,\,{{\text{Ф}} \mathord{\left/ {\vphantom {{\text{Ф}} {{{{\text{м}}}^{{\text{2}}}}}}} \right. \kern-0em} {{{{\text{м}}}^{{\text{2}}}}}},$ n = 2, i0 = 1 А/см2 и $i_{{\text{Ф}}}^{\infty }$ = 10 А/см2 приблизительно равно 1000 нс. При увеличении как i0 так и $i_{{\text{Ф}}}^{\infty }$ характерное время заряжения ДЭС уменьшается и при i0 = 1 А/см2 и $i_{{\text{Ф}}}^{\infty }$ = 100 А/см2 становится приблизительно равным 20 нс. То есть при изменении параметров системы в весьма широком диапазоне время установления омического падения потенциала существенно меньше времени заряжения ДЭС.
После включения импульса напряжения ток скачкообразно (при отсутствии диффузионных ограничений) возрастает до значения iА (на участке с меньшим МЭР) и до значения iБ на участке с большим МЭР (рис. 2, кривые 1, 4).
Рис. 2.
Схемы изменения во времени (а) локальных токов ((1–3) на участке с меньшим МЭР) и ((4–6) на участке с большим МЭР) при локальном электроосаждении меди в 1 M CuSO4 после включения заданного напряжения и (б) соответствующие кривые заряжения двойного электрического слоя: 1, 4 – полная плотность тока (квадраты); 2, 5 ‒ плотность тока заряжения–разряжения емкости ДЭС (кружки); 3, 6 – фарадеевская плотность тока (треугольники) при амплитуде напряжения 4 В, длительности импульса 100 нс.
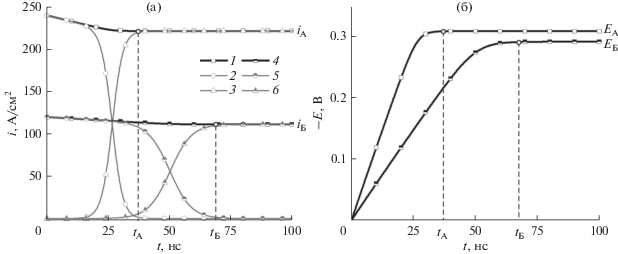
Изменение потенциала анода, однако, происходит сравнительно медленно (рис. 2б) в связи с заряжением емкости ДЭС; на этот процесс затрачивается только часть токов iА и iБ (рис. 2а, кривые 2, 5).
Вначале все электричество в импульсе тратится на процесс заряжения ДЭС (рис. 2а, кривые 2, 5). По мере заряжения ДЭС количество электричества, затрачиваемое на этот процесс, уменьшается, а на фарадеевский процесс осаждения или растворения металла увеличивается (рис. 2а, кривые 3, 6). По истечении времени tA процесс заряжения на участке с меньшим МЭР заканчивается, потенциал устанавливается на определенном значении EА (рис. 2б), определяющим ток, который при t > tA (t > 35 нс на рис. 2б) весь идет на фарадеевский процесс.
Важно, что скорость заряжения ДЭС различна в области на подложке непосредственно под ЭИ (короткие прямые линии тока, область А на рис. 3) и на несколько большем расстоянии (изогнутые линии тока, область Б на рис. 3). В области Б на подложке большая, чем в области А, часть напряжения U падает в растворе. Потенциал электрода здесь устанавливается медленнее (за время tБ) и на меньшем значении EБ (рис. 2б). Ток iБ соответственно меньше, чем iА в рабочей зоне, рис. 2. Несмотря на малые размеры зоны локального электроосаждения (расстояние между участками поверхности с наименьшим и большим МЭР составляет всего несколько микрометров) и достаточно большую электроповодность раствора неэквипотенциальность поверхности обрабатываемой заготовки (детали) достигает достаточно больших значений – нескольких десятков милливольт (рис. 2б), что обусловлено весьма большими плотностями тока, которые на 3–5 порядков превышают плотности тока при традиционном электроосаждении.
Рис. 3.
Схема локального электроосаждения с использованием нерастворимого анода: 1 – анод, 2 – изоляция боковой поверхности анода, 3 – подложка, 4 – межэлектродный зазор, 5 – раствор электролита, содержащий ионы осаждаемого металла, 6 – микро/нано осадок металла на поверхности подложки, (а) схема ЭХО с обозначенными рабочей А и прилегающей Б зонами на подложке, (б) схема с локальным гальваническим осадком 6.
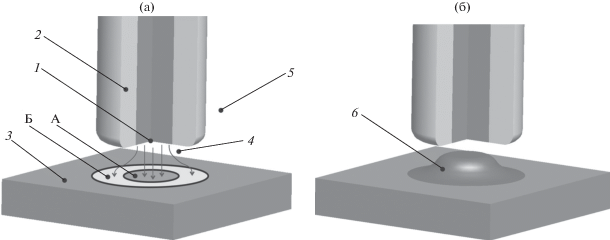
Если длительность импульсов tp выбрать равной tБ, то разница скоростей растворения (осаждения) в области А и в некоторой точке в области Б будет определяться различием поляризации (EА – EБ) в соответствие, например, с известной формулой Тафеля (логарифмическое увеличение тока при увеличении потенциала электрода).
Выбор tp < tБ приведет к большему различию локальных потенциалов, к большему превышению скорости растворения (осаждения) металла в области А над скоростью такого процесса в области Б, т.е. к большей локализации процесса.
При оптимальной длительности импульса с достаточной амплитудой в области А на подложке успеет произойти полное заряжение ДЭС и останется достаточное количество электричества на растворение металла. В области Б за время импульса успеет произойти только частичное заряжение ДЭС и совсем небольшая часть заряда будет затрачена на осаждение или растворение металла.
Таким образом, регулирование длительности импульсов, выбор tp позволяет добиться высокой степени локализации фарадеевского процесса в области А на поверхности подложки.
Понятно, что имеется критически малая длительность импульса при данной амплитуде, которая не будет обеспечивать достаточно полное заряжение ДЭС даже в области А. Практически весь заряд в проходящих импульсах будет затрачиваться только на периодическое (с частотой импульсного напряжения) заряжение ДЭС. Экспериментальные результаты, показывающие наличие критической минимальной длительности импульса представлены в работе [25]. В этой же работе экспериментально подтверждено, что чем меньше рабочая площадь микроЭИ, тем быстрее происходит достижение максимальной скорости обработки и сделан вывод о целесообразности изоляции боковой поверхности ЭИ в виде стержня малого диаметра. Применение такого электрода снижает конусность образующегося при локальном растворении отверстия.
При реализации метода свехкоротких импульсов для локального растворения или осаждения металла в работах [22–24] был использован низкочастотный (постоянная времени около 1 мс) бипотенциостат, который с помощью Pt противоэлектрода независимым образом поддерживает заданные базовые значения потенциалов ОД и ЭИ относительно электрода сравнения (псевдоэлектрода сравнения из платины). Электродом-инструментом служит торец Pt или W проволоки. От импульсного генератора на ОД подается серия импульсов напряжения длительностью, например, 50 нс при длительности пауз между импульсами 500 нс. Столь короткие импульсы не влияют на работу низкочастотного бипотенциостата, поэтому с помощью импульсного генератора осуществляется необходимая поляризация ОД на том участке, где предусмотрено растворение или осаждение металла.
Такие режимы ЭХО характеризуются относительно низкой производительностью, но оправдывают себя в процессах микро/нано ЭХО, когда мало количество удаляемого металла и производительность отходит на второй план по сравнению с точностью, разрешающей способностью ЭХО.
Расчеты и эксперименты показали [22, 23], что возможно подобрать столь короткие импульсы, что в точках, отстоящих от границы области А (рис. 3) на подложке всего на несколько микрон, растворение или осаждение практически не происходит, в то время как непосредственно под ЭИ происходит ощутимое растворение или осаждение. Диаметр осажденного островка металла или растворенной области на подложке практически равен диаметру ЭИ. Авторы [22, 23] сравнивают постоянную времени τ заряжения ДЭС (произведение сопротивления электролита на емкость ДЭС) с длительностью импульса напряжения tp. Приемлемая для определенных целей скорость растворения или осаждения обеспечивается при необходимой амплитуде импульсов и при условии, что τ не превышает существенно величину tp. Так как сопротивление электролита, а, следовательно, и τ, прямо пропорциональны межэлектродному расстоянию, то можно выбрать такое значение tp, что достаточная степень заряжения ДЭС и необходимая скорость фарадеевского процесса будут достигнуты только при минимальном МЭР (минимальном сопротивлении).
Другими словами, можно сказать, что ультракороткие импульсы нужны для того, чтобы нестационарные процессы в первый короткий период времени после включения источника питания занимали основную часть импульса. При слишком длительных импульсах основная их часть будет приходиться на установившееся состояние, в течение которого различие в скоростях растворения в торцевом и боковом зазорах меньше.
Шустер и соавт. [22] использовали этот метод для локализации катодного осаждения меди из раствора смеси 0.01 М HClO4 и 0.1 М CuSO4 на подложке из золота. Для осаждения меди использовали платиновый проволочный ЭИ диаметром примерно 50 мкм. При длительности импульсов 400 нс и напряжении 2 В были получены островки кристаллитов меди диаметром примерно 60 мкм. Потенциал рабочего электрода поддерживался вблизи равновесного потенциала редокс системы Cu/Cu2+ для предотвращения как крупномасштабного осаждения меди, так и растворения осадка.
Метод сверхкоротких импульсов для локализации анодного растворения был успешно применен на примерах обработки металлов в активном состоянии. Для этого больше подходят растворы кислот или NaCl, в которых практически отсутствует область пассивности, предшествующая области интенсивного активного растворения металла.
Размерная ЭХО многих материалов (Ni, Fe, ряд сталей и сплавов) в растворах типа NaNO3, NaClO3 происходит при анодном растворении в состоянии активации анионами этой соли при относительно высоких поляризациях по сравнению с активным растворением. В таких случаях действует другой механизм локализации анодного растворения импульсным током, который требует более длительных импульсов: кроме заряжения ДЭС требуется некоторое количество электричества для преодоления нескольких этапов пассивности металла до начала интенсивного растворения металла [16].
Проблема локального анодного растворения ультракороткими импульсами металлов, покрытых резистивной оксидной пленкой (например, Ti), состоит в том, что сопротивление таких пленок может значительно превосходить сопротивление раствора, что нарушает принцип локализации ультракороткими импульсами.
Ультракороткие импульсы находят применение и при микроЭХО полупроводников [20]. Для этого обычно используются растворы на основе HF. Понятно, что при описанном выше механизме локализации длительность импульсов должна зависеть от степени легирования (удельного сопротивления) образцов и МЭР. Влияние различных факторов на результаты ЭХО полупроводников осложнено их зонной структурой.
2.3. Формирование металлических нитей и более сложных микроструктур подвижным микродисковым электродом-инструментом
Процесс электрохимического формирования металлических микропроволочек, нитей, столбиков во многих случаях реализуется с использованием микродискового ЭИ, представляющего собой торец проволоки диаметром 25–125 мкм, впрессованной во втулку из изоляционного материала (рис. 4) или впаянной в стекло. При электроосаждении микродисковый электрод, подключенный к положительному полюсу источника тока, и подложка, на которой формируется микроструктура, подключенная к отрицательному полюсу источника тока, погружены в раствор для осаждения металла. При формировании микроструктур электросаждением обычно применяются нерастворимые аноды, часто из Pt. На таких анодах происходит электролиз воды с выделением кислорода. Иногда применяются растворимые аноды. На катоде происходит реакция восстановления катионов с выделением металла, в ряде случаев при одновременном выделении водорода.
Рис. 4.
Схема локального электроосаждения с непрерывным перемещением анода с постоянной скоростью: 1 – микроэлектрод, 2 – изоляционное покрытие боковой поверхности микроэлектрода, 3 – подложка, 4 – поверхность роста осадка, 5 – электролит.
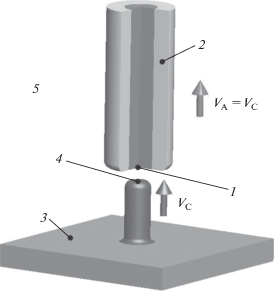
Перед началом процесса электроосаждения металла ЭИ подводится на определенное расстояние к тому месту на поверхности подложки, на котором следует вырастить металлическую проволочку, столбик. Затем на электроды подается небольшое напряжение (например, 0.1 В), ЭИ подводится к подложке до касания, которое фиксируется по нулевому электрическому сопротивлению или по резкому увеличению тока. Затем ЭИ отводится на заданное расстояние (часто на 10 или 20 мкм), включается рабочее напряжение (несколько вольт) и начинается рост металлической микропроволочки (нити, столбика). В результате роста осадка расстояние между анодом и торцом образующейся металлической проволочки уменьшается, поэтому для формирования осадков с большим аспектным отношением анод отводится от подложки со скоростью VA. При нормальных условиях скорость VA должна быть равна скорости роста осадка VC, рис. 4.
Начало развития метода гальванического формирования микроструктур с большим аспектным отношением движущимся микроанодом положили работы Маддена и соавт. [26, 27] в середине 90‑х гг. XX в.
Эти авторы проводили локальное электроосаждение никеля из сульфаматного электролита с использованием микроэлектродов различного вида. Использовались два режима формирования микроструктур. В одном режиме движение ЭИ было прерывистым и регулировалось цепью обратной связи. Когда в процессе электроосаждения формируемая микроструктура достигала неподвижного микроэлектрода, происходило скачкообразное увеличение тока, которое служило сигналом для отвода микроэлектрода на заданное расстояние. После чего начинался следующий цикл роста осадка при неподвижном ЭИ, как это показано на рис. 5.
В другом режиме ЭИ перемещался относительно подложки в трехмерном пространстве по заданной траектории с постоянной скоростью. В таком режиме, например, формировали 3D деталь в виде пружины со скоростью 6 мкм/с, сформированы микропроволочки из никеля диаметром 45 мкм и длиной до 1600 мкм.
При использовании метода формирования микропроволочек с прерывистым движением ЭИ, имеются некоторые особенности. За счет многократных контактов электродов и возникновения при этом больших токов, многократного повторения процесса осаждения–отвода ЭИ микропроволока может получаться с синусоидальным профилем поверхности, с порами, дендритами. Авторы работ [28–31] предложили режимы формирования микроструктур, уменьшающие эти трудности. С этой целью закорачивание электродов не допускается и отвод ЭИ от ОД происходит раньше, при достижении заданного достаточно высокого тока. В работе [29] сигналом для отвода ЭИ было повышение тока до 20 мА. При этом ЭИ отводится на заданное расстояние или до достижения нужного достаточно низкого значения тока, например [28]. Лин и соавт. в работе [30] на основании сравнительных экспериментов по локальному электроосаждению меди из сернокислого электролита по разным схемам предложили отводить ЭИ после снижения МЭР примерно наполовину. Затем напряжение снижать до 0.1 В, ЭИ доводить до контакта с катодом и отводить от него на заданное расстояние 10 мкм, включать рабочее напряжение 3.8 В и снова проводить электроосаждение.
Авторам работы [32] удалось повысить качество осадка никеля при прерывистом режиме формирования микропроволочек, практически устранить периодическое изменение диаметра по длине проволочки добавлением в электролит сахарината натрия в количестве 2–4 мМ.
Циклический процесс ведется до достижения заданной длины проволочки. Для выполнения работы могут потребоваться сотни и тысячи циклов.
В большинстве опубликованных работ проводилось формирование проволочек из меди [28, 33–43] и никеля [22, 27, 29, 32, 33, 42], а в некоторых работах – из сплавов Ni–Cu [37, 44]. Подложкой служили медь [33, 35, 40–43, 45, 46], никель [42], серебро [39, 47], нержавеющая сталь [38].
Для осаждения меди использовался в большинстве случаев кислый сульфатный электролит, для электроосаждения никеля электролит Уотса и сульфаматный электролит, сульфатный электролит с добавками.
В работе [41] приведен пример важного практического применения формирования микронитей локальным электроосаждением с использованием подвижного микродискового электрода: формирование медного соединительного проводника, осажденного между двумя контактными площадками микросхемы.
Газовыделение, которое может происходить как на нерастворимом аноде, так и на катоде при электроосаждении никеля, при осаждении меди в режиме слишком высоких потенциалов, необходимо учитывать при анализе процессов локального электроосаждения. С одной стороны, движение пузырьков создает конвекцию электролита и этим увеличивает допустимую скорость электроосаждения металла. С другой стороны, газовые пузырьки увеличивают сопротивление среды в межэлектродном пространстве.
Правильный выбор напряжения или катодного потенциала является одним из важных факторов управления процессами формирования проволочек, столбиков и более сложных структур локальным катодным осаждением металла.
Зависимость скорости осаждение медных проволочек от напряжения получена Вангом и соавт. [39]: скорость осаждения увеличивается от близкой к нулю до примерно 26 мкм/с при увеличении напряжения от 2.2 до 3.2 В. Эта зависимость близка к логарифмической.
Средняя скорость осаждения никеля повышается от 0.078 до 10.06 мкм/с с увеличением напряжения от 3.4 до 4.8 В при МЭР 20 мкм. Причем зависимость эта не линейная, скорость осаждения увеличивалась с напряжением быстрее, чем по линейному закону [48].
От величины напряжения сильно зависит качество сформированной микроструктуры. Плотная цилиндрическая структура никелевой проволочки получается при напряжении ниже 3.56 В. Чем выше напряжение, тем хуже качество микропроволочки [45]. Цилиндрическая форма проволочки из меди получается при низких потенциалах, меньше 2.4 В и при начальном зазоре 10 мкм или меньше. Дендриты и пустоты образуются в осадке при потенциалах больше 2.8 В [39].
Наряду с напряжением большое значение имеет выбор и контроль величины МЭР. По данным [48] средняя скорость осаждения никелевой микропроволочки снижается от 5.4 до 0.33 мкм/с с увеличением МЭР от 20 до 120 мкм при напряжении 4.6 В. В работе [39] показан спад скорости осаждения проволочек меди при увеличении МЭР. Скорость снижается примерно в 2 раза при увеличении МЭР в 5 раз. Величина МЭР влияет на средний диаметр проволочки. Средний диаметр медной проволочки увеличивается от 50 до 130 мкм по линейному закону при увеличении МЭР от 5 до 30 мкм [39]. Недопустимое снижение МЭР может привести к слишком большой плотности тока и снижению качества осадка.
От величины начального межэлектродного зазора и от напряжения зависит структура проволочки от плотной проволочки до тонкой трубочки [34].
Авторы работы [48] учли важность соотношения величин напряжения и МЭР и провели эксперименты при различных значениях такого соотношения при формировании никелевых проволочек длиной 1500 мкм. Лучшие результаты по качеству поверхности и скорости осаждения в этой работе были получены при напряжении 4.6 В и МЭР 80 мкм.
Ряд работ был посвящен различным усовершенствованиям методик формирования микроструктур.
Хванг и соавторы [43] сделали дисковый микоэлектрод вращающимся для формирования столбиков из никеля в режиме прерывистого движения ЭИ. Осаждение проводили при напряжении 4.3 В, токе примерно 1 мА и скорости вращения 1000 об./мин. Распределение тока в этом случае было более равномерным, качество осадка выше, чем при неподвижном ЭИ, скорость осаждение несколько выше, лучше воспроизводимость результатов. При определенных условиях при вращении ЭИ на подложке образовывались не столбики, как при неподвижном ЭИ, а тонкие трубочки. Аспектное отношение полученных трубочек достигало 16.
Те же авторы в работе [49] вместо вращения ЭИ на медную подложку накладывали ультразвуковые колебания с резонансной частотой 98 кГц системы ванна–раствор–подложка. Ультразвуковые колебания уменьшали газонаполнение межэлектродного пространства, интенсифицировали конвективный массоперенос в системе. Это приводило к повышению скорости роста нитей, меньшему отклонению от цилиндрической формы, к приближению диаметра столбика к диаметру ЭИ, к нивелированию влияния шероховатости поверхности ЭИ на качество поверхности растущего осадка. При более высокой частоте колебаний (425 кГц) наблюдалось повышение скорости роста осадка на 48.6% и увеличение пористости осадка на 42.2%.
Как правило, при прерывистом движении ЭИ результаты локального электроосаждения оказываются лучше, чем при непрерывном, как в отношении получения проволочек с высоким аспектным соотношением, так и для получения гладкой поверхности, равномерного по длине проволочки диаметра.
В ряде работ, например в [47], было продемонстрировано получение более сложных микроконструкций локальным электроосаждением, например стенок из расположенных рядом друг с другом металлических столбиков.
Для анализа скорости роста и формы образующейся металлической нити используются методы математического моделирования [28, 29, 33, 34, 43, 50–54]. Решались задачи методами граничных и конечных элементов в приближении первичного [16, 29], вторичного [51, 55], третичного [53, 54] распределения тока при циклическом [28, 29, 54] и непрерывном перемещении ЭИ [29, 54].
В зависимости от условий реализации процесса возможно получение осадков различной морфологии. При этом форма осадка может изменяться от цилиндрической с различной формой верхней части до трубчатой.
Моделирование процесса, проведенное в работе [55], показало, что скорость роста осадка и его морфология зависят от начального расстояния между анодом и подложкой, формы и размеров анода и его диэлектрического покрытия, условий проведения процесса, а также от кинетики электродной реакции осаждения металла. В этой работе были выявлены условия образования осадков различного типа, в том числе цилиндрических с различной формой торца металлической нити и трубчатых осадков, рис. 6. Так, осадки цилиндрической формы с плоским торцом формируются при малых начальных межэлектродных расстояниях и при малой плотности тока обмена электрохимической реакции. В условиях малых начальных МЭР и при большой плотности тока обмена электрохимической реакции могут формироваться осадки трубчатой формы за счет сильного краевого эффекта.
Рис. 6.
Эволюция поверхности осадка в процессе роста при различных условиях проведения процесса с безразмерными интервалами времени между линиями 0.2 (0.2, 0.4, …, 2.0), R – расстояние от центра симметрии, Zc – вертикальная координата при увеличении безразмерной плотности тока обмена от рис. 6а к рис. 6е.
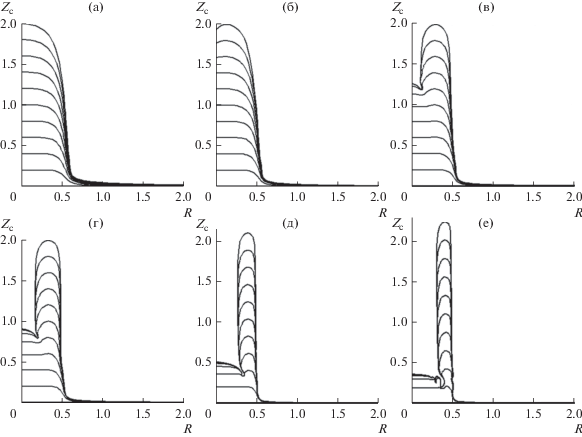
Описанный здесь метод электрохимического получения микроструктур не позволяет получать на поверхности подложки структуры наноразмерных масштабов, как это достигается, например, при использовании сканирующих микроскопов. Однако он позволяет получать микроструктуры с очень большим аспектным отношением, достигающим по данным [36] 1 : 282.
2.4. Использование сканирующих зондовых микроскопов (СЗМ)
Прогресс в СЗМ и развитие сканирующей электрохимической микроскопии привели к тому, что такие устройства стали применять для формирования металлических микро/наноструктур, модификации поверхности локальным электроосаждением или травлением металлов и полупроводников. Для этого используются различные виды зондовых микроскопов (туннельный, силовой, электрохимический) после необходимой модификации. Модифицированные устройства СЗМ превратились в технологические инструменты формирования всевозможных нано/микроструктур для наноэлектроники, наносистемной техники, разработки микроэлектромеханических устройств. Особенностью применения СЗМ в этих целях является то, что и зонд, и подложка находятся в электрохимической ячейке в растворе электролита.
Электродом-инструментом при локальной ЭХО с применением СЗМ, как правило, является металлический или металлизированный зонд микроскопа, покрытый химически стойким диэлектрическим материалом кроме острия, размеры которого имеют нано или микромасштабы. Процесс травления или осаждения металла происходит локально непосредственно под неизолированным острием зонда при МЭР того же порядка, что размер острия зонда.
При прямом методе ЭХО, например травлении, острие зонда служит катодом. При некоторых условиях на катоде может образоваться осадок металла, могут выделяться пузырьки газа. Это может приводить к изменению геометрии острия зонда и снижению точности микроЭХО. Кроме того, подложка в этом случае имеет более положительный потенциал, что может приводить к коррозии подложки, образованию на ней оксида.
Большое распространение получили непрямые процессы локального электроосаждения или растворения металла при использовании обратной связи СЗМ, когда перенос электронов на подложке определяет ток на микроэлектроде.
МикроЭХО в режиме обратной связи СЗМ проводится в четырехэлектродной электрохимической ячейке: обычно Pt микроэлектрод (ЭИ), Pt вспомогательный электрод, электрод сравнения и подложка (ОД), не подключенная к внешнему источнику питания. Потенциалы микроэлектрода и вспомогательного электрода относительно электрода сравнения управляются бипотенциостатом. Потенциал подложки устанавливается под действием редокс системы, имеющейся в ячейке.
При достаточно большом расстоянии между микроэлектродом и подложкой (несколько диаметров микроэлектрода) маленький ток течет между микроэлектродом и вспомогательным электродом. При приближении микроэлектрода к подложке часть продукта реакции на микроэлектроде успевает за счет диффузии достичь подложки и вступить там в реакцию.
Между микроэлектродом и подложкой возникает сравнительно большой ток, причем тем больший, чем меньше дистанция между ними (положительная обратная связь).
Если по какой-то причине продукт реакции на микроэлектроде не может вступать в реакцию на подложке, подложка только затрудняет доступ реагента к микроэлектроду; ток в системе тем меньше, чем меньше дистанция зонд–подложка. Это режим отрицательной обратной связи. Известная связь тока с дистанцией, как при положительной, так и при отрицательной обратной связи, позволяет управлять величиной расстояния между зондом и подложкой, что необходимо для осуществления процессов микро/нано ЭХО.
Проведение микроЭХО в режиме обратной связи часто используется в процессах, описанных в разделе 4.3.
2.4.1. Электроосаждение металла на зонд с последующим локальным переосаждением на подложку. Группа Колба [56–60] разработала методику декорирования подложки кластерами металла, названную “прыжок до контакта”. Вначале на зонд накладывается потенциал, при котором металл, например, медь, катодно осаждается из раствора на поверхности зонда, рис. 7а (нужное значение потенциала задается относительно потенциала редокс пары Cu/Cu2+, используется бипотенциостат). Затем зонд с осажденным металлом на короткое время подводится настолько близко (0.8 ± 0.2 нм) к подложке, что между зондом и подложкой образуется мостик из осажденного на зонде металла, рис. 7б, который разрывается при последующем отводе зонда от подложки, оставляя на ней кластер металла, рис. 7в. Процесс проводится в импульсном режиме при длительности импульсов 10–20 мс и частоте 50–80 Гц.
Рис. 7.
Схема локального электроосаждения с использованием нерастворимого анода: 1 – анод, 2 – подложка, 3 – слой металла, осажденный на аноде, который кратковременно использовался в качестве катода, 4 – раствор электролита, содержащий ионы осаждаемого металла, 5 – микро/нано кластер металла на поверхности подложки.
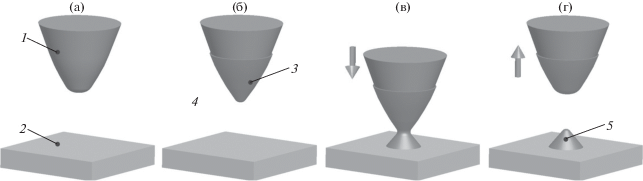
Сближение и разведение электродов с одновременным перемещением подложки позволяло получать большие массы отдельных кластеров металла на подожке. Для этого был разработан полностью автоматизированный процесс [58].
По данным [58] кластеры меди средней высотой 0.7 нм на Au подложке создавались в растворе 0.05 M H2SO4 + 0.1 мM CuSO4 со скоростью 50 кластеров в секунду с расстоянием между кластерами 11 нм. Образование 10 000 кластеров требовало 17 минут. Некоторое изменение геометрии кончика зонда при переходе меди с него на подложку может оказывать небольшое влияние на расстояние между кластерами.
Средняя высота кластеров составляет 0.2–1.5 нм. На высоту кластеров влияет, в частности, расстояние между зондом и подложкой. Высокая стабильность кластеров, наблюдающаяся в ряде случаев, объяснена сплавообразованием.
Большой интерес с точки зрения создания эффективных катализаторов вызывает получение больших массивов нанокластеров палладия. В работе [61] продемонстрировано получение 400 кластеров Pd средней высоты 0.4 нм на площади 190 × 190 нм со скоростью 80 кластеров в секунду в растворе 0.05 M H2SO4 + 0.1 мM H2PdCl4 в полностью автоматизированном процессе.
Хофманн, Шиндлер и соавт. [62–64] проводили локальное осаждение магнитных кобальтовых кластеров на Au подложке с промежуточным осаждением на зонд и переосаждением на подложку в двухступенчатом процессе, отличающемся от работ Колба отсутствием каких-либо контактов зонда с подложкой.
2.4.2. Осаждение металлов на полупроводниковые подложки. СЗМ применяются при микрообработке полупроводников. Большинство опубликованных работ посвящено электроосаждению металлов на n-полупроводники, меньше – осаждению на p-полупроводники. Это связано с тем, что n-полупроводники ведут себя при катодной поляризации “как проводники”. Электрохимическая реакция на p-полупроводнике возможна только при достаточно высоком смещении потенциала от потенциала разомкнутой цепи, в области потенциалов выше потенциала, который обычно приписывают пробою блокирующего барьера Шоттки [65]. Потенциал пробоя может быть существенно снижен предварительной локальной активацией в местах, предназначенных для осаждения. Поэтому особенно для электроосаждения металлов на p-полупроводники важна такая предобработка подложки.
Механическая активация применяется наиболее часто и производится с применением СЗМ с алмазным зондом с радиусом меньше 25 нм, который вдавливанием в поверхностный слой полупроводника создает дефекты на участке в виде царапины. Дефектные участки в виде круглого углубления можно создать направленной струей жидкости с частицами SiO2. В результате локальной механической активации поверхности полупроводника возможно самопроизвольное осаждение металла без участия внешнего источника напряжения за счет возникшей разности потенциалов между активированными и пассивными, не активированными участками поверхности подложки [66, 67]. Эффективность такого метода была показана авторами [66] на примере локального осаждения меди на p-Si(100) в растворе смеси HF и Cu(NO3)2: 2Cu2+ + Si + 6HF = H2SiF6 + + 2Cu + 4H+. Были сформированы наноструктуры с характерными размерами 50 нм.
Локальному микро/нано электроосаждению металлов на полупроводниковые подложки посвящены работы [67–71] и др.
Проблемам термодинамики и кинетики электроосаждения металлов на Si и особенно анализу результатов осаждения Cu, Au и Pt посвящен обзор Оскама и соавт. [72].
2.4.3. Локальное оксидирование металлов и полупроводников. В атмосфере влажного воздуха между острым концом зонда СЗМ и подложкой образуется капля воды, мениск, через который проводится процесс оксидирования, рис. 8. ЭИ подключается к отрицательному полюсу источника питания, а металлическая или полупроводниковая подложка (обычно пленочная) – к положительному полюсу. Процесс проводится при заданном напряжении, заданном токе или в импульсном режиме. Как и в других вариантах локальной ЭХО, зонд и подложка подвижны в различных направлениях. Это дает возможность формировать на обрабатываемой поверхности “пятна” оксида или “линии”, дорожки.
Рис. 8.
Схема локального оксидирования через водный мениск: 1 – анод, 2 – катод, 3 – оксид металла, 4 – мениск.
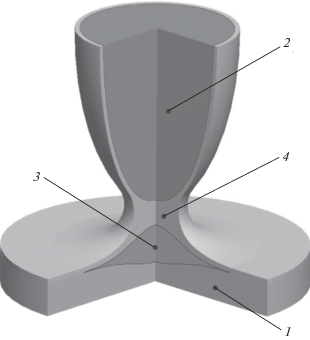
Процесс оксидирования имеет такую же природу, как при традиционном электрохимическом оксидировании
На катоде (зонде) происходит восстановление растворенного в воде кислорода O2 + 4e + 2H2O → → 4OH– или при достаточно высоких потенциалах электролиз воды 4H2O + 4e → 2H2 + 4OH–.
Ключевыми параметрами управления процессами локального оксидирования являются форма и размеры зонда, напряжение между электродами, ток в гальваностатическом режиме или параметры импульсного режима, длительность процесса при формировании “пятен” или скорость сканирования зондом при получении линий оксида, влажность окружающего воздуха [73–80].
Рабочее напряжение составляет несколько вольт (2–10 В, иногда до 25 В). Скорость сканирования зондом от 0.01 до 10 мкм/с, что, в частности, зависит от длины линии (длиннее линия, больше скорость сканирования). При формировании “пятен” толщина оксида в некоторых пределах увеличивается почти линейно с увеличением напряжения и длительности импульса. При формировании линий толщина оксида имеет логарифмическую зависимость от скорости сканирования, ширина линии и толщина оксида увеличиваются линейно с наложенным напряжением. Как и при обычном электрохимическом оксидировании, важной характеристикой процесса является отношение Пиллинга–Бедворта (отношение объемных электрохимических эквивалентов металла и образующегося из него оксида), величина которого зависит от природы металла. Ширина линии и толщина оксида (или высота оксидной линии над поверхностью ОД) снижаются с увеличением скорости сканирования и повышаются в некоторых пределах с увеличением напряжения. Ширина линии составляет 20–100 нм. Ширина линии и аспектное отношение (отношение высоты оксида к ширине линии) зависят от относительной влажности окружающей атмосферы. Так, в работе [73] было найдено, что при оксидировании n-типа Si при скорости сканирования 300 нм/с, при относительной влажности 14% полученная линия оксида имела ширину 23 нм, что в примерно в 4 раза меньше, чем при влажности 61% и аспектное отношение было значительно выше.
Методом локального электрохимического оксидирования проводили обработку алюминия [81], кремния [79, 82, 83], титана [84, 85], тантала [77], ванадия [76], хрома [86], и других материалов.
В работе [74] сделан обзор локального оксидирования кремния и металлов, где обсуждались кинетика и механизм процессов.
3. ЛОКАЛЬНОЕ ЭЛЕКТРОХИМИЧЕСКОЕ ОСАЖДЕНИЕ И РАСТВОРЕНИЕ ЭЛЕКТРОДОМ-ИНСТРУМЕНТОМ В МИКРО/НАНО РАЗМЕРНЫХ ПИПЕТКАХ, СОПЛАХ
3.1. Формирование микроструктур подвижным микроэлектродом в свободной пипетке через жидкостный мениск
Для формирования микроструктур с большим аспектным отношением (формирование микропроволочек, металлических нитей) наряду с микроэлектродом, показанным на рис. 5, используются подвижные микроэлектроды другого типа. Это стеклянная микропипетка, заполненная раствором для электроосаждения металла, внутри которой расположен анод. Процесс проводится без погружения электродов в ванну с электролитом, в воздушной среде, имеющей некоторую относительную влажность. Когда пипетка касается или почти касается подложки, образуется электролитный мениск, жидкостной мостик между концом микропипетки и подложкой. При использовании такого инструмента активная зона подложки ограничена мениском, рис. 9.
Рис. 9.
Схемы локального электроосаждения металла через мениск во влажном воздухе. 1 – микропипетка с раствором электролита, 2 –анод, 3 – мениск, 4 – фронт роста осадка, 5 – растущая микроструктура, 6 – подложка (катод).
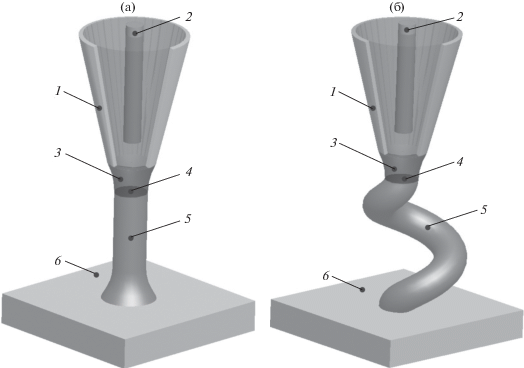
Процесс электролиза проводится по двухэлектродной схеме или по трехэлектродной схеме с применением потенциостата.
После включения напряжения происходит резкое увеличение тока. После этого пипетка отводится на нужное расстояние, при поддержании которого устанавливается стационарное значение тока и происходит выращивание проволочки. По мере роста проволочки пипетка должна с определенной скоростью отводиться от поверхности роста, рис. 9а. Диаметр и высота мениска имеют порядок величины диаметра конца пипетки.
Важнейшим фактором в таком процессе является испарение воды с поверхности мениска, значительное из-за большого отношения поверхности мениска к его объему. Влажность среды, в которой проводится процесс электроосаждения, в значительной степени влияет на процесс испарения.
Испарение вызывает конвекцию с подводом в мениск жидкости из микропипетки.
Потеря воды из-за испарения через поверхность мениска, генерируя конвективный поток ионов Cu2+ в мениске, существенно влияет на распределение ионов [87]. Испарение воды происходит на границе мениска с воздухом, поэтому здесь выше скорость роста металла; возникает различие в скорости роста микропроволочки в радиальном направлении в ее сечении, фронт роста микропроволочки становится не плоским. Это особенно заметно при сравнительно низкой влажности среды [88]. Для получения плотной цилиндрической структуры необходимо устранить различие скоростей осаждения металла в периферийной и центральной областях [87]. Наоборот, создание благоприятных условий для установления большой разницы этих скоростей позволяет получить не проволочки, а микротрубочки.
Пипетку можно смещать вправо или влево на несколько мкм без разрыва мениска и использовать эту возможность для формирования разнообразных 3D микроструктур, рис. 9б.
Из сказанного понятно, что важен контроль влажности окружающей среды. Оптимальное значение относительной влажности зависит от многих факторов и составляет 60–80% [38]. Другие работы проводились при влажности 50% [87, 89].
Чем больше влажность, тем меньше скорость испарения и скорость роста микропроволочки. При слишком низкой влажности может произойти кристаллизация соли, например CuSO4, вблизи конца пипетки и нарушение процесса осаждения металла. К такому же результату может привести применение слишком высокой концентрации CuSO4 в стремлении повысить скорость осаждения металла.
Большое значение имеет диаметр отверстия в микропипетке. В разных работах диаметр отверстия имеет размеры от 100 нм до нескольких мкм. Увеличение диаметра приводит к увеличению тока, снижению скорости испарения воды в мениске [90]. Скорость осаждения уменьшается при увеличении диаметра отверстия в некоторых пределах. Скорость осаждения меди при различных диаметрах отверстия в пипетке составляет 0.18 мкм/с (20.4 мкм3/с) [87], от 520 нм/с до 2.3 мкм/с и от 15 нм/с до 45 нм/с [91], 88 нм/с и 263 нм/с [90], 0.25 мкм/с [92], 0.008 мкм3/с [89], от 100 нм/с до 0.18 мкм/с.
Имеется некоторый интервал дозволенных скоростей отвода микропипетки от растущей проволочки [90]; за дозволенными пределами мениск становится неустойчивым и разрывается. Форма мениска зависит от скорости движения микропипетки. В рамках дозволенных значений скорости диаметр выращиваемой проволочки уменьшается при увеличении скорости. Например, при диаметре отверстия в микропипетке 730 нм увеличение скорости от 88 нм/с (минимально допустимое значение) до 263 нм/с (максимально допустимое значение) приводит к снижению диаметра проволочки от 657 нм до 365 нм.
Авторы работы [92] показали, что скорость отвода микропипетки можно использовать для управления толщиной проволоки, сужая мениск при увеличении скорости. Они использовали пипетку диаметром 1.6 мкм и скорость отвода пипетки от 0.25 до 0.4 мкм/с и осаждали проволоку диаметром от 1400 до 1100 нм.
Сеол и соавт. [87] выращивали не только прямолинейные фрагменты микропроволочек, но и более сложные структуры.
Авторы работы [92] решали аналогичную задачу, разработав такую форму кончика микропипетки, которая вместе с изменением траектории движения микропипетки позволила изгибать микропроволочку в процессе роста и ориентировать ее в направлении от 0° (параллельно поверхности подложки) до 90° (нормально к поверхности подложки). Кончик такой микропипетки показан на рис. 10а вместе с рядом медных проволочек, полученных такой микропипеткой под разными углами. На рис. 10б показаны примеры применения такого метода для выращивания медных проволочек диаметром 740 нА и длиной 40 мкм. Это электрические контакты чипов (масштабная метка на рисунках имеет размер 10 мкм).
Рис. 10.
(а) Измененный кончик нанопипетки и иллюстрация результатов его применения для получения нанопроволочек с разными углами наклона. (б) Схема формирования микропроволочек для получения электрических контактов чипов [92].
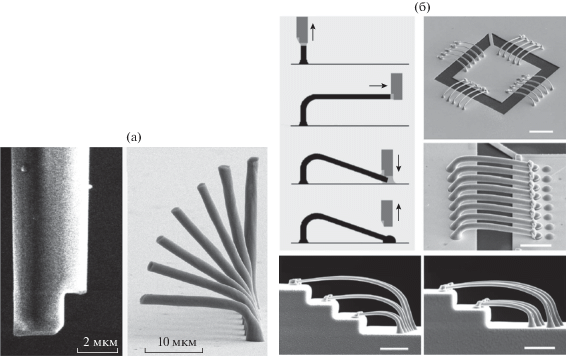
В работе [89] показана возможность получения нанопровочки из платины такого малого диаметра как 150 нм при аспектном отношении до 200.
Микропроволочки из меди диаметром 200 нм длиной до 10 мкм формировали в 0.05 М растворе CuSO4 в работе [91]. Приведен пример, где сформирован комплекс из 100 нанопроволочек при расстоянии между ними 7 мкм. Стабильное осаждение меди проводилось при скорости отвода пипетки 250 нм/с. Процесс полностью автоматизирован.
В большинстве работ, использующих нанопипетки, скорости осаждения меди низкие и находятся в интервале от 100 нм/с до 0.18 мкм/с (0.008–20.4 мкм3/с). В работе [93] предложен новый подход, расширяющий возможности метода. В этом методе используется шприц со значительно большим диаметром отверстия, 400 мкм. В конической части шприца помещена губка с открытыми порами, пропитанная раствором для осаждения меди. Эта часть устройства является пишущей головкой электрохимического 3D принтера. Губка предотвращает свободное вытекание раствора через отверстие большого размера в шприце и этим обеспечивает образование устойчивого мениска. В шприце кроме 1 М раствора CuSO4 находятся медные пластины, используемые в качестве противоэлектрода и электрода сравнения. При перемещении пишущей головки вдоль поверхности подложки со скоростью 0.4 мм/с, создается выпуклый рисунок заданной формы. Ширина линии от 3 мкм до 15 мкм в зависимости от потенциала (1–4 В относительно медного электрода). Линия длиной 10 мм с толщиной слоя 14–104 нм получается за один час работы. Для этого требуется 144 прохода головки. Этот метод позволяет получить скорость осаждения меди до 19 667 мкм3/с без образования дендритов.
3.2. Формирование металлических микроструктур подвижным микроэлектродом в погруженной в электролит пипетке
Микропипетки, изображенные на рис. 9, могут использоваться при локальной ЭХО при погружении их в раствор. Преимущество такой методики состоит в отсутствии проблемы стабилизации мениска. Недостатком такой методики является рассеяние тока в электролите, приводящее к тому, что осаждение металла происходит не только непосредственно под отверстием в пипетке, но и в прилегающих областях подложки. Толщина выращиваемой проволочки при этом существенно больше диаметра отверстия в пипетке.
В работе Момотенко и соавт. [94] использовалась нанопипетка с отверстием 30–50 нм в диаметре разделенная вдоль на 2 части. Через одну часть пипетки протекает ток осаждения медного столбика. Одновременно через вторую часть с помощью цепи обратной связи осуществляется контроль расстояния между нанопипеткой и поверхностью подложки при формировании отрезков нанопроволочек празличной формы.
Толщина нанопроволочек в приведенном примере 500 нм, высота несколько мкм.
Имеется ряд работ, в которых пипетка с электролитом была частью кантеливера СЗМ.
3.3. Электроосаждение металла с использованием СЗМ с зондом в виде микропипетки с электролитом
Мюллер и соавт. [95], по-видимому, первые создали установку для локального электроосаждения металла, включающую сканирующий зондовый микроскоп с микропипеткой в качестве зонда и бипотенциостат.
Ито и Ивата [96] заменили зонд СЗМ на нанопипетку с анодом (медная проволока диаметром 30 мкм) и раствором для локального электросаждения меди на подложку из золота. Они использовали два варианта: конец пипетки располагается на некотором расстоянии от поверхности подложки (при этом диаметр полученного островка заметно больше диаметра отверстия в пипетке) или конец пипетки находится практически в контакте с подложкой (диаметр островка близок к диаметру отверстия).
Стеклянная пипетка имела диаметр отверстия 200 нм, внешний диаметр конца пипетки 300 нм. Осаждение меди проводили из 0.001 М CuSO4. Конец пипетки, и подложка находились в растворе в электрохимической ячейке. Это препятствовало высыханию раствора в пипетке и засорению отверстия в ней. Для контроля расстояния между концом пипетки и подложкой пипетка была соединена с кварцевым резонатором и осциллировала в вертикальном направлении. Пипетка осциллировала с амплитудой меньше 10 нм с резонансной частотой, зависящей от расстояния между концом пипетки и подложкой. Изменение резонансной частоты по мере приближения пипетки к подложке использовалось для поддержания этого расстояния постоянным.
Используемый способ контроля расстояния между концом пипетки и подложкой позволял проводить процесс при почти нулевом расстоянии и получить практически такой же размер островка металла на подложке как диаметр отверстия в пипетке. Была получена очень высокая воспроизводимость размеров островков.
Осаждение одного островка с диаметром 198 нм и высотой 28 нм при напряжении 3.5 В занимало 2.5 с.
Авторам [97] микрокантилеверами служил набор из 10 микропипеток из кремния с внутренней поверхностью покрытой золотом (аноды). Каналы в пипетках были заполнены электролитом для электроосаждения островков меди на подложке из Au, служащей катодом. Капли электролита наносились на подложку из каждого кантилевера в те места, где необходимо создать островки меди при прямом контакте кончика катилевера с подложкой. Размер отверстия в кантилевере 4 × 5 мкм. Расстояние между электродами 6 мкм. Размер капель составлял несколько десятков мкм. Размер островка меди зависел от длительности импульса напряжения и обычно составлял 20 мкм.
3.4. Использование электрохимических микроячеек для локальной ЭХО металлов
Под электрохимической микроячейкой в процессах микрообработки имеется в виду капилляр с электролитом и противоэлектродом прижатый к ОД и имеющий уплотнение по периферии конца капилляра, препятствующее выходу электролита за пределы капиллярного соединения с обрабатываемой деталью. Впервые такая ячейка использовалась еще в работе [98] для локального анодного растворения металла.
Для повышения скорости ЭХО процесс ведут в потоке электролита. Для этого капилляр внутри разделен вдоль оси на две части стеклянной перегородкой. Перегородка не доходит до конца капилляра, так что между нижним концом перегородки и подложкой остается пространство. Это позволяет осуществлять поток электролита с одной стороны перегородки к подложке и от нее с другой стороны перегородки [99]. Малый диаметр отверстия (около 10 мкм), интенсивный поток электролита в капилляре позволял получать высокие плотности тока (до 100 А/см2) при небольших токах.
Надо заметить, что практически точно такая методика была использована в самом начале XX в. для электрохимического сверления отверстий в броневой стали в растворах серной кислоты [100, 101], рис. 11. К сожалению, эта работа сейчас практически забыта.
3.5. Струйная электрохимическая микрообработка
Струйная электрохимическая обработка (СЭХО) – метод локального электрохимического растворения или осаждения металла, в котором свободная струя электролита из сопла под давлением направлена в то место ОД, в котором необходимо провести электрохимическую обработку.
В процессах растворения металла сопло может быть изготовлено из металла и служить катодом (в некоторых случаях внутри металлического сопла имеется стеклянная трубка, через которую подается электролит). В процессах электроосаждения сопло обычно изготовлено из стекла, а металлический нерастворимый анод находится внутри сопла, рис. 12.
Рис. 12.
Устройство для струйного электроосаждения металла: 1 – стеклянное сопло, 2 – анод, 3 – подложка, 4 – “дорожка” осажденного металла, 5 – мениск, 6 – стрелка, показывающая направление движения подложки.
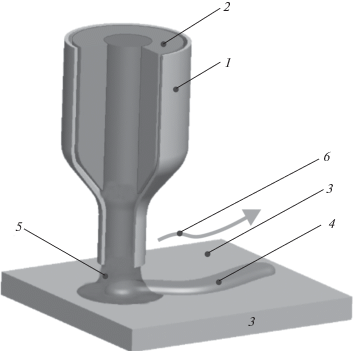
Применение метода позволяет получать отдельные островки электроосажденного металла или углубления микронных масштабов. При сканировании поверхности ОД создаются выпуклые или углубленные линии рисунка по заданной программе.
Процесс обработки управляется выбором состава, концентрации и температуры электролита, напряжения или параметров импульсного тока, диаметра сопла, расстояния от сопла до поверхности ОД, скорости движения сопла или ОД при растворении или осаждении линий, длительности процесса. Электролитом при растворении металлов обычно служат растворы NaNO3 или NaCl. Расстояние между концом сопла и поверхностью ОД составляет от нескольких десятков мкм до нескольких мм. В этом же интервале значений находится диаметр сопла. Напряжение от 5 до 100 и более вольт. Напряжение выше при использовании стеклянного сопла с электродом внутри из-за большего МЭР. Диаметр получаемого углубления или островка осадка, ширина полосы, получаемой при движении стола с ОД, примерно в 2 раза больше диаметра струи электролита.
Большая серия работ по струйному электрохимическому сверлению, начатая в основном в 60-х гг. в связи с развитием электрохимической размерной обработки продолжается до настоящего времени. В последние годы развивается направление, относящееся к микро ЭХО, представляемой как “электрохимическая печать”, например [102].
При СЭХО достигаются очень высокие плотности тока до нескольких десятков А/см2 при электроосаждении и до нескольких сотен А/см2 при анодном растворении за счет малого МЭР и потока электролита. Это позволяет не только получать высокую производительность, но и высокое качество обработанной поверхности (низкую шероховатость). Неоднократно отмечалось, что при увеличении плотности тока при анодном растворении металлов шероховатость поверхности снижается. В работе [103] было показано, что при струйной ЭХО при плотностях тока около 150 А/см2 происходит полирование различных металлов (железо, нержавеющая сталь, медь, алюминий) в водных растворах солей (KNO3, KCl). В работе [104] показано, что достижимые при СЭХО очень высокие плотности тока, до 300 А/см2, позволяют ослабить или устранить влияние предварительной механической или термической обработки детали на качество поверхности после ЭХО.
Проведенные исследования приводят к заключению, что лучшие результаты могут быть получены при независимом управлении плотностью тока и гидродинамическими параметрами [102].
Возможности метода в отношении формы образующейся полости и качества обработанной поверхности расширяются при использовании струи электролита, направленной под заданным углом к поверхности ОД и при вращении струи относительно направления продвижения инструмента [105, 106].
Натсу и соавт. [107, 108] разработали метод получения трехмерных полостей анодным растворением металлов методом СЭХО. Установка для осуществления этого метода отличается тем, что сопло может двигаться не только по нормали к поверхности ОД; ось симметрии сопла может перемещаться также по окружности. В одном из вариантов метода сопло перемещается относительно поверхности ОД, останавливаясь на короткое время в нужных местах. В этих местах образуются лунки. Они могут быть расположены в нужном порядке, образуя поверхность ОД (плоскую, цилиндрическую) покрытую системой углублений. В другом варианте метода сопло не останавливается в нужном месте для образования лунки в ОД, а перемещается с заданной скоростью на некоторые расстояния, образуя систему протяженных углублений, треков. Установка для СЭХО управляется персональным компьютером таким образом, что суперпозиция отдельных треков создает трехмерную полость очень близкую к заданной форме.
СЭХО для локального оксидирования алюминия использовалось в работах [109, 110].
4. ЛОКАЛИЗАЦИЯ ЭЛЕКТРОАКТИВНОГО КОМПОНЕНТА ЭЛЕКТРОЛИТА В ЗОНЕ ОБРАБОТКИ
При реализации такого подхода к организации микро/нано ЭХО реагент для реакции локального осаждения или растворения металла (полупроводника) на подложке не содержится в объеме электролита, а образуется на микроэлектроде, который установлен на очень малом расстоянии от подложки, или иным способом. Локализация процесса обеспечивается как за счет локализации электрического поля, так и за счет локализации источника реагента в непосредственной близости к месту осаждения или растворения на подложке. Имеется несколько вариантов использования такого подхода к микро/нано ЭХО.
4.1. Локальное электроосаждение металла с растворимым анодом
Примерами могут служить процессы локального электроосаждения золота и кобальта [111, 112]. Зонд микроскопа размером несколько десятков мкм является растворимым микроэлектродом (ЭИ), изготовленным из того же металла, который необходимо осадить на подложке, рис. 13.
Рис. 13.
Схема локального электроосаждения с использованием растворимого микроэлектрода: 1 – микроэлектрод/анод (Au, Co), 2 – электропроводная подложка, 3 – диэлектрическое покрытие анода, 4 – микроостровок осажденного металла, 5 – образующийся при растворении анода комплекс металла с активирующим анионом (${\text{AuBr}}_{{\text{4}}}^{ - },$ ${\text{CoCl}}_{x}^{{{\text{2}} - x}}$), 6 – освободившийся при осаждении металла на катоде активирующий анион (Br, Cl–), 7 – бипотенциостат, 8 – электрод сравнения, 9 – вспомогательный электрод. Электрод сравнения и вспомогательный электрод находятся в растворе вместе с микроэлектродом и подложкой. Четырехэлектродная схема.
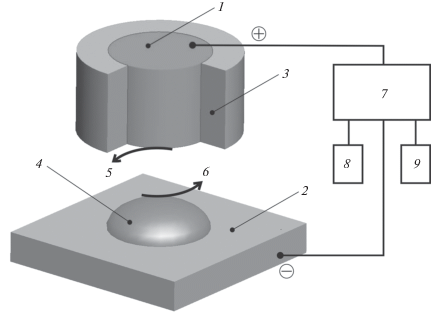
В работе [111] проводили локальное электроосаждение золота из 0.1 М раствора HBr на подложку из ITO. Необходимые значения потенциала ЭИ и подложки задавали с помощью бипотенциостата. Растворение золота проходило по реакции Au + 4Br– → ${\text{AuBr}}_{{\text{4}}}^{ - }$ + 3e. Образовавшееся соединение диффундировало к подложке и восстанавливалось с образованием островка металла на подложке и анионов Br–, которые диффундировали к ЭИ и вновь участвовали в растворении золота. При этом протекающий ток тем больше, чем меньше МЭР (положительная обратная связь). Такой процесс позволяет, например, наносить необходимый рисунок золотом на электропроводную подложку (“золотое перо”). Разрешающая способность процесса зависит от размеров микроанода и МЭР.
Локальное электроосаждение кобальта проводили с растворимым микроэлектродом (зондом СЗМ) диаметром 50 мкм с использованием несколько более сложной процедуры, связанной с образованием оксидной пленки на аноде, затрудняющий процесс осаждения [112].
4.2. Локальное электроосаждение металла. СЗМ с нерастворимым зондом-микроэлектродом. Метод химических линз
Авторы работ [113, 114] с целью повышения латеральной разрешающей способности локального электроосаждения металла с использованием СЗМ предложили метод, который они назвали методом химических линз. В процессе локального электроосаждения серебра на подложку из золота микроэлектродом служил зонд – торец платиновой проволоки диаметром 10 мкм. В растворе содержатся AgNO3, аммиак для образования комплекса с серебром [Ag(NH3)2]+, NaNO2 и NaNO3 (последний для обеспечения достаточной электропроводности). Бипотенциостат использовался для независимой задачи нужных потенциалов микроэлектрода и подложки. На микроэлектроде происходило окисление ${\text{NO}}_{{\text{2}}}^{ - }$ + H2O → → ${\text{NO}}_{{\text{3}}}^{ - }$ + 2H+ + 2e. Образующиеся H+ смещали равновесие [Ag(NH3)2]+ + 2H+ ↔ Ag+ + ${\text{2NH}}_{{\text{4}}}^{ + }$ в растворе в сторону образования катионов Ag+, часть которых успевает диффундировать к подложке и восстановиться до Ag. Те катионы Ag+, которые не по кратчайшему пути диффундировали от микроэлектрода, скорее вступали в реакцию с аммиаком с образованием неактивного комплекса по отношению к реакции на подложке при заданном ее потенциале. Таким образом между микроэлектродом и подложкой образуется канал, линза (рис. 14), внутри которой существуют Ag+. Наличие комплексообразователя ограничивает латеральные размеры линзы, способствуя локализации процесса электроосаждения.
4.3. Локальное травление металлов и полупроводников в режиме положительной обратной связи
Процессы травления металлов и полупроводников проводятся в режиме положительной обратной связи СЗМ, см. раздел 8.1. В этом методе травитель не содержится в электрохимической ячейке, а образуется на микроэлектроде в результате окисления восстановленной формы редокс системы. Образовавшаяся окисленная форма (травитель) при достаточно малом расстоянии между микроэлектродом и подложкой осуществляет локальное травление подложки непосредственно под микроэлектродом и сама переходит в восстановленную форму, которая диффундирует к микроэлектроду и вновь подвергается окислению, рис. 15.
Рис. 15.
Схема локального электрохимического растворения металлической или полупроводниковой подложки с применением СЗМ: 1 – микроэлектрод (Pt), 2 – подложка, 3 – диэлектрическое покрытие боковой поверхности микроэлектрода, 4 – лунка в подложке, образовавшаяся в процессе электрохимического растворения, 5 – окисленная форма редокс системы, 6 – восстановленная форма редокс стистемы, 7 – потенциостат, 8 – электрод сравнения, 9 – вспомогательный электрод, 10 – продукт, образованный в результате локального электрохимического растворения.
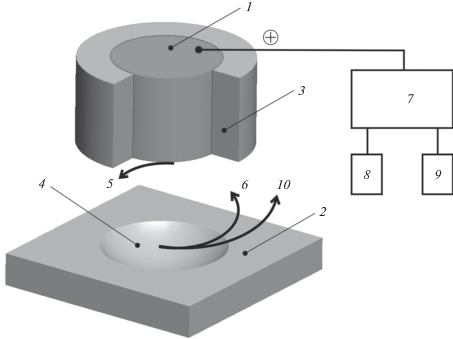
Так, при локальном травлении полупроводников, например GaAs, редокс парой служит смесь 0.02 M HBr и 0.5 M HCl. Анионы Br– окисляются на Pt микроэлектроде с образованием сильного окислителя Br2, который диффундирует к подложке и окисляет (растворяет) GaAs, а Br2 при этом восстанавливается до Br–, который окисляется на микроэлектроде до Br2 и т.д. [115, 116].
Этот же метод применен для локального травления медных пленок, но с другими редокс парами [117–120]: Cu + 2Ox → Cu2+ + 2Red.
4.4. Локальное травление металлов и полупроводников. Методика ограничения толщины слоя травителя
Методика ограничения толщины слоя травителя [121–127] использует СЗМ, в котором острие зонда заменено на плоский микроЭИ из Pt или сплава Pt–Ir, имеющий на поверхности рисунок, который необходимо перенести на подложку. Травитель E для материала подложки не вводится в состав электролита в электрохимической ячейке, а генерируется на микроЭИ в результате окисления имеющегося в растворе прекурсора P (P → E + ne). Травитель диффундирует к поверхности металлической M подложки, отстоящей от ЭИ на несколько десятков или сотен нм (такова толщина диффузионного слоя около ЭИ), и обеспечивает процесс травления необходимого рисунка с образованием продукта травления R (E + M → → P + R). Для предотвращения латеральной диффузии травителя в состав электролита входит специальное вещество S, играющее роль поглотителя травителя (E + S → P + Q, где Q – продукт этой реакции) и этим ограничивающее размеры области существования травителя пространством между поверхностью ЭИ и поверхностью подложки непосредственно под ЭИ. За этими пределами происходит гомогенная химическая реакция между этим веществом и травителем. Степень локализации травления тем больше, чем выше скорость реакции растворения металла.
Если использование микроЭИ в виде острия микропроволочки легко позволяет проводить процесс ЭХО при очень малых МЭР, то применение ЭИ с рисунком для переноса его на подложку должно иметь жесткие ограничения в размерах для обеспечения достаточно интесивного массообмена в очень малом межэлектродном пространстве. Необходимо обеспечить правильное соотношение площади поверхности ЭИ и МЭЗ. По-видимому, с этой проблемой в значительной степени связано проведение травления при низких плотностях тока, например 5 мА/см2 [122].
В случае локального травления титанового сплава раствор содержит следующие компоненты: 0.2 M NaF, 0.4 M NaClO3, 0.3 M NaNO2 (прекурсоры электрохимического получения травителей HF и HNO3), 0.1 M NaOH (поглотитель травителя), 0.6 M NaClO4. Процесс проводится в гальваностатическом режиме при 5 мА/см2 и температуре 40–45°С.
На микроЭИ протекают реакции [122]:
(1)
${\text{ClO}}_{{\text{3}}}^{ - } + {{{\text{H}}}_{{\text{2}}}}{\text{O}} \to {\text{ClO}}_{{\text{4}}}^{ - } + {\text{2}}{{{\text{H}}}^{ + }} + {\text{e,}}$(2)
${\text{NO}}_{{\text{2}}}^{ - } + {{{\text{H}}}_{{\text{2}}}}{\text{O}} \to {\text{NO}}_{{\text{3}}}^{ - } + {\text{2}}{{{\text{H}}}^{ + }} + {\text{e}}{\text{.}}$В образовавшейся кислой среде роль травителей выполняют фтористоводородная и азотная кислоты. Реакции травления титанового сплава, имеющего в своем составе Al и V [122]:
(3)
${\text{Ti}} + {\text{6HF}} \to {{{\text{H}}}_{{\text{2}}}}\left[ {{\text{Ti}}{{{\text{F}}}_{{\text{6}}}}} \right] + {\text{2}}{{{\text{H}}}_{2}},$(4)
${\text{Al}} + {\text{4HN}}{{{\text{O}}}_{3}} \to {\text{Al}}{{\left( {{\text{N}}{{{\text{O}}}_{{\text{3}}}}} \right)}_{{\text{3}}}} + {\text{NO}} + {\text{2}}{{{\text{H}}}_{{\text{2}}}}{\text{O}},$Этот же метод может быть использован для локального травления полупроводников.
4.5. Локальное электроосаждение металла с зондом СЗМ, не являющимся электродом
Хирт и соавт. [128, 129] применили специальную конструкцию атомного силового микроскопа, в которой горизонтальный кантилевер внутри имеет канал и заканчивается коротким вертикальным соплом. Канал заполнен электролитом для электроосаждения металла, в данном случае сернокислым электролитом меднения. Электрохимическая ячейка, в которую погружены кантилевер и подложка, заполнена раствором серной кислоты. Здесь же находятся противоэлектрод и электрод сравнения. Кантилевер в данном случае не является электродом. Необходимый для электроосаждения потенциал подложки задается потенциостатом. Электролит для осаждения меди под определенным контролируемым давлением (1–25 мбар) подается через кантеливер к месту на подложке, где необходимо формировать микроструктуру. Локализация процесса осаждения металла обеспечивается тем, что осадок формируется на подложке непосредственно напротив отверстия в сопле, куда подается электролит, содержащий катионы металла. Вначале авторы применили этот метод для получения островков меди [129], а затем столбиков и более сложных структур [128].
Передвижение кантилевера по заданной программе позволяет формировать не только вертикальные столбики, но и различные 3D структуры, например, спирали, стенки из микростолбиков и др.
Авторы работ [128, 129] представляют описанный метод как альтернативу применения стеклянных микропипеток.
5. ЛАЗЕРНО-ЭЛЕКТРОХИМИЧЕСКАЯ (ЛЭХО) И СТРУЙНАЯ ЛАЗЕРНО-ЭЛЕКТРОХИМИЧЕСКАЯ ОБРАБОТКА
В методе ЛЭХО сфокусированный в определенном месте на поверхности подложки лазерный луч многократно ускоряет электрохимическую реакцию в этом месте диаметром от нескольких единиц до сотен мкм.
Для этих целей используются лазеры различных типов, работающие как в непрерывном, так и в импульсном режимах. Мощность излучения от единиц мВт до нескольких десятков Вт.
Наиболее эффективен этот метод локализации в тех условиях, когда без лазерного воздействия электрохимическая реакция протекает с крайне малой скоростью. При осуществлении анодных процессов очень низкая скорость растворения без лазерного облучения возникает за счет пассивности металла. При этом важен правильный состав электролита для обработки конкретного материала [130, 131], в частности, наличие пассивирующих добавок (K2Cr2O7 при травлении Al, H3PO4 при травлении Ti).
На рис. 16 приведена простейшая схема ЛЭХО для локального травления.
Рис. 16.
Схема ЛЭХО: 1 – катод, 2 – обрабатываемая деталь, 3 – лазер, 4 – фокусирующее устройство, 5 – вход электролита, 6 – направление движения обрабатываемой детали при травлении “дорожки”.
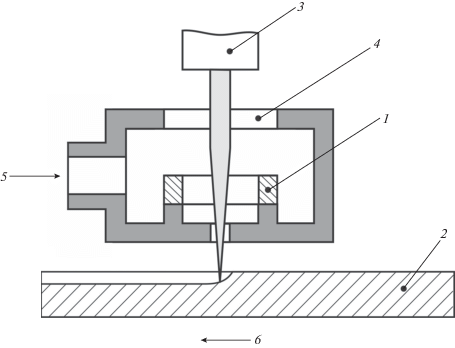
Лазерное стимулирование электрохимических процессов применяется при поляризации электродов внешним источником питания и при так называемом химическом (бестоковым) осаждении или травлении металлов.
Длину волны лазерного излучения выбирают таким образом, чтобы минимизировать поглощение энергии в слое электролита, через который проходит луч. Слой электролита для этой цели имеет по возможности малую толщину, от нескольких мм до нескольких см.
Главной причиной значительного увеличения плотности тока в области действия лазера при протекании электрохимической реакции является локальный нагрев металла. Это следует из результатов работ [132–135], где было показано, что локальный нагрев металла лазером или нагрев объема электролита приводят к одинаковому результату.
Выделение тепла на облучаемом участке электрода происходит в результате поглощения металлом энергии лазерного излучения. Наибольший тепловой эффект получается при той длине волны излучения, которой соответствует наибольший коэффициент оптического поглощения.
Важную роль играют термические свойства подложки. На металлах с низкой теплопроводностью (Ni, W, Mo) рассеяние тепла меньше и степень локализации процесса выше.
Чем больше коэффициент теплоотдачи материала подложки, тем быстрее на облучаемом участке возрастает температура и достигает некоторого установившегося значения, но установившееся значение температуры при этом ниже, а локализация процесса выше [132].
Во многих работах стимулированное лазерным излучением осаждение металла производится на пленочные подложки, нанесенные на стекло или подобные материалы. Результаты лазерного осаждения, толщина осадка зависят от толщины пленки. Такая зависимость определялась при “химическом” осаждении меди на медной пленке разной толщины из сульфатного электролита в работе [136]. Без облучения осаждение не происходило. При облучении осаждение происходило при толщинах пленки больше 12 нм и меньше 10 мкм. Последнее связано с увеличением теплоотвода и снижением температуры в зоне облучения на более толстых пленках. Максимальная толщина осадка достигалась при толщине подложки 25 нм.
По данным [137] скорость локального химического осаждения никеля под действием излучения была в 20–30 раз выше, чем в традиционном процессе и достигала десятых долей мкм/с. Авторы [137] наблюдали возникновение естественной конвекции вблизи электрода под действием градиента температуры. Облучение металлической подложки влияло не только на скорость осаждения, но и на структуру осадка. В этой работе было показано, что ускорение процесса может быть осуществлено в труднодоступных местах детали сложной формы при подводе света с помощью стекловолоконных жгутов.
Некоторым недостатком применения лазерной локализации процесса химического осаждения в обычных для таких процессов электролитах может быть довольно большая скорость осаждения без лазерного стимулирования.
Скорость травления, как правило, увеличивается при увеличении мощности лазерного излучения. При превышении некоторого предела мощности происходит скачкообразное увеличение скорости травления, связанное с началом плавления материала обрабатываемой детали [131, 138].
Природа продуктов травления металлов имеет большое значение. Так при растворении меди в азотной кислоте, продукты реакции обладают сильным поглощением и делают нецелесообразным применение лазера для локального ускорения электрохимического процесса [139].
В ряде работ [140–146] проведены расчеты распределения температуры и плотности тока в зоне облучения и прилегающих к ней участках поверхности подложки с целью определения формы локального осадка или полости, получаемых в результате ЛЭХО. Однако это весьма сложная задача сочетания процессов теплопереноса и кинетики электрохимических реакций, особенно при учете импульсного режима лазерного излучения, сканирования луча по поверхности подложки, гидродинамических условий, локального изменения во времени формы подложки.
В работах по ЛЭХО рассматриваются несколько механизмов влияния лазерного излучения на скорость электрохимических реакций [147–149].
5.1. Изменение равновесного потенциала
Равновесный потенциал металла в растворе электролита зависит от температуры, причем эта зависимость в разных электрохимических системах имеет разные знаки. Лазерное облучение, вызывая сильный локальный нагрев, приводит к протеканию не только относительно большого тока в зоне облучения, но и тока между нагретым и холодным участками поверхности подложки. Направление тока определяется знаком температурной зависимости равновесного потенциала. На нагретом участке в случае меди в сульфатном электролите преобладает осаждение меди, а на прилегающих холодных участках травление металла [150].
Для никеля в цитратном электролите (другой знак температурной зависимости потенциала) наблюдается противоположная картина – травление на освещенном пятне и выделение металла в прилегающей области [133].
5.2. Увеличение скорости реакции, протекающей в режиме замедленного разряда
Увеличение плотности тока i при повышении температуры T описывается выражением i = Ae–W/(RT), где A – предэкспотенциальный множитель, W – эффективная энергия активации. Степень влияния температуры в значительной степени зависит от W.
В работе [135] были определены зависимости величины лазерного усиления тока для режима замедленного переноса заряда δi = δik = ($i_{k}^{{{\text{лаз}}}}$ – ik)/ik (где ik – ток без включения лазера, $i_{k}^{{{\text{лаз}}}}$ – ток при включенном лазере) от мощности w лазерного излучения с различной длиной волны λ. Оказалось, что, во-первых, δik линейно увеличивается с увеличением w, во-вторых, величины δik при данном w и различных λ различаются мало за исключением самого длинноволнового излучения, которое значительно менее эффективно.
5.3. Ускорение массопереноса в диффузионном пограничном слое
Под действием лазера температура раствора вблизи подложки увеличивается и появляется градиент плотности неравномерно нагретого раствора. При этом вблизи электрода возникает ламинарный, а при более высокой температуре турбулентный поток электролита, интенсифицирующий массоперенос. Из теории конвективного теплопереноса известно, что вблизи нагретой круглой поверхности возникает ламинарный поток жидкости, направленный от периферии круга к его центру. При лазерно-электрохимическом осаждении металла в том же направлении происходит снижение тока за счет снижения концентрации электролита. Толщина осадка уменьшается от периферии к центру [169]; в режиме замедленного разряда это не происходит. Растворение металла наоборот должно быть более интенсивным в центре пятна и замедляться по направлению к периферии. Авторы работы [152] наблюдали образование кратера на гальваническом осадке при высокой интенсивности лазерного излучения и предположили, что причиной этого являются пузырьки пара, образующиеся при кипении жидкости вблизи лазерного пятна.
В турбулентном режиме интенсивное перемешивание обеспечивает примерно одинаковые условия массопереноса на всем нагретом участке подложки.
Результаты работы [135] приводят к выводу, что $\delta i_{k}^{{{\text{лаз}}}}$ ≈ $5\delta _{{\text{д}}}^{{{\text{лаз}}}}$ при фиксированной мощности излучения. Это отражает тот факт, что энергия активации процесса осаждения металла в режиме диффузионного тока значительно ниже, чем в режиме электрохимической кинетики.
При достаточной мощности лазерного излучения температура на облучаемом участке поверхности достигает температуры кипения раствора, на электроде образуются пузырьки пара, которые, отрываясь от поверхности, перемешивают жидкость вблизи электрода и ускоряют массоперенос и скорость реакции, ограниченной массопереносом. Локальное перемешивание вместе с локальным нагревом способствует получению высокой степени локализации электрохимического процесса на облучаемом участке электрода.
Однако перемешивание одновременно является причиной увеличения теплоотвода от нагретого участка электрода в электролит. Последнее должно приводить к снижению температуры в зоне ЛЭХО, особенно важному при протекании реакции в кинетическом режиме. С другой стороны, блокирование электрода пузырьками газа должно привести к снижению теплоотвода от электрода в раствор и этим повысить температуру электрода.
Результирующий эффект состоит в охлаждении электрода при увеличении скорости перемешивания раствора. Например, в работах [135, 170] было экспериментально показано снижение плотности тока осаждения металла при повышении скорости потока раствора или скорости вращения электрода.
По наблюдениям авторов работы [132] увеличение радиуса пятна (изменением фокусирования) приводит к снижению температуры при одинаковой мощности излучения лазера. При малых диаметрах пятна пузырьки пара быстро образуются и сразу же удаляются из зоны электроосаждения металла. При больших радиусах пятна пузырьки задерживаются в зоне осаждения, увеличиваются в размерах и затем отделяются. Поэтому рекомендуется проводить электроосаждение при сильной фокусировке, т.е. при высокой плотности мощности излучения.
5.4. Изменение выхода по току
В случае протекания на электроде нескольких параллельных реакций нагрев, вызванный лазерным облучением, может привести к изменению выхода по току для целевой реакции в результате различия температурных коэффициентов перенапряжения для целевой и побочной реакции. При возрастающей зависимости выхода по току от температуры должно также увеличиваться соотношение скоростей процессов в зоне обработки и в прилегающей области, и повышаться степень локализации процесса электросаждения металла. Обратная зависимость должна приводить к противоположным эффектам.
Практически важным примером зависимости выхода по току от температуры является анодное растворение сталей в растворах нитрата натрия, когда выход по току снижается при повышении температуры. Очевидно, с этим связано найденное в [153] сильное замедление струйной электрохимической прошивки тонких отверстий в стали, наблюдавшееся при лазерном облучении. Авторы этой работы считают возможным влияние еще одного механизма замедления процесса растворения металла: увеличение выхода по току побочной реакции выделения кислорода – образование дополнительного количества носителей тока в полупроводниковой оксидной пленке на металле под действием лазера.
5.5. Изменение степени пассивности металла
Депассивирующее действие лазера на пассивные металлы чрезвычайно важно, как при анодном растворении, так и при катодном выделении и связано в первую очередь с нагревом. Достаточно большое повышение температуры устраняет пассивность, чем значительно облегчает катодное выделение металлов группы железа [154].
Повышение температуры в зоне облучения лазером значительно уменьшает пассивационные ограничения скорости растворения металлов. Депассивация лазерным нагревом до температур, близких к температурам плавления металлов, позволяет заменить опасные растворы кислот и щелочей нейтральными растворами неорганических солей, например, NaNO3 при травлении (без применения внешних источников тока) таких металлов, как нержавеющая сталь, молибден, ниобий, медь, никель [171]. При этом могут возникать некоторые особенности, в частности образование солевых пленок на обрабатываемом участке [150].
От наличия или отсутствия пассивной оксидной пленки на меди и от рН сульфатного электролита при лазерном облучении может зависеть, будет ли происходить осаждение или растворение металла [172].
5.6. Термические напряжения и пластическая деформация в поверхностном слое металла
Ефимов и соавт. [151] изучали лазерную активацию никелевого электрода в 1 M H2SO4 после воздействия лазерных наносекундных импульсов мощностью до 50 МВт/см2. Скорость растворения металла при анодных потенциалах увеличивалась в 103 раз. Авторы отметили сохранение активности электрода в течение длительного времени после прекращения облучения. Для охлаждения металла после прекращения импульса требовалось значительно меньшее время. Это привело к выводу о нетепловой природе активации металла. Было сделано предположение, что ускорение электродных процессов обусловлено релаксирующей во времени пластической деформацией в поверхностном слое металла вследствие термических напряжений. Нагретый металл в зоне воздействия лазерного излучения испытывает сжимающие нагрузки со стороны окружающего более холодного металла. Образуется неравновесное, более высокое число выходов дислокаций на напряженном участке поверхности, что может изменить перенапряжение электрохимической реакции.
5.7. ЛЭХО полупроводников
Усиленное лазером травление полупроводников в растворах осуществляется как за счет значительного повышения температуры в зоне облучения, так и за счет фотогенерации носителей заряда.
Анодное растворение полупроводникового материала n-типа, как известно, происходит при непосредственном участии неосновных носителей, дырок, концентрация которых очень мала. Поэтому мала скорость растворения, она ограничена малым током насыщения. Освещение электрода с помощью лазера вызывает интенсивную фотогенерацию дырок, многократно увеличивая ток насыщения и возможную скорость травления полупроводника, например [155, 156]. Так, при локальном травлении n-InP под действием лазерного облучения происходит фотогенерация дырок, участвующих в процессе травления:
где x число фотонов, участвующих в реакции окисления молекулы InP, (6 – x)e– число не фотогенерированных электронов.Ряд работ [156–158] посвящен изготовлению дифракционных решеток методом селективного интерференционного фототравления полупроводников.
Например, Беляков и соавт. [158] получали рельефные дифракционные решетки с пространственной частотой, превышающей 2500 мм–1. При выборе травителя основное внимание авторы уделяли прозрачности раствора для лазерного луча и отсутствию газовыделения в зоне травления. Основные растворы для локального травления полупроводников имеют основу HF, KOH или H2SO4 [138, 156–158] и другие.
Безмасковое индуцированное лазером осаждение металлов на полупроводниковые поверхности позволяет получать локальные осадки масштаба 1 мкм с высокой проводимостью, с контролируемым типом контакта (омический или барьерный) и является одним из методов создания различных электронных устройств.
Авторы [159] осаждали никель (наиболее подходящий метал для контактов кремниевых солнечных элементов), а также медь и цинк на подложку из монокристалла кремния p-типа при сканировании лазерного луча по поверхности подложки. Были получены осадки меди из сульфатного электролита и золота из цианистого электролита на GaAs [160].
Сасано и соавт. [161] осаждали серии “точек” и “рисунки” из меди локальным потенциостатическим электроосаждением на пористый кремний под действием лазерного излучения с целью получения электрических контактов. Когда полупроводник p-типа помещается в раствор, содержащий ионы металла, катодная поляризация не восстанавливает ионы металла в темноте из-за малого содержания электронов в зоне проводимости. При освещении электроны из валентной зоны переходят в зону проводимости и могут давать вклад в восстановление при правильном соотношении уровней энергии зоны проводимости и редокс потенциала. Надо сказать, что селективное осаждение меди методом ЛЭХО из растворов простых солей меди затруднено иммерсионным осаждением металла не только на освещаемых участках, а на всей поверхности образца. Иммерсионное осаждение было подавлено введением в электролит хлоридов и комплексообразованием с катионами меди [151, 161].
Иммерсионное осаждение характерно для таких благородных металлов как Ag, Pt, Cu, в отличие от менее благородных Ni, Fe, Zn [162].
Метод комплексообразования может быть использован и для осаждения платины или палладия на кремнии. Эти металлы являются катализаторами реакции выделения водорода и осадки этих металлов на кремнии могут быть использованы для получения водорода преобразованием солнечной энергии.
В работе [163] показана возможность “бестокового” осаждения платины из раствора хлороплатиновой кислоты на p-типа, n-типа и недопированные образцы InP под действием импульсного лазерного излучения.
В ряде статей, например [164], даны ссылки на работы по стимулированному импульсным лазерным излучением “химическому” осаждению многих металлов на подложки из Si, SiC, GaAs, InP, InSe, TiO2 и др.
Лазерное излучение ускоряет не только осаждение и растворение материалов, но и инициирует локальный рост анодных оксидных пленок на Ti, Nb, Zr и Hf [165].
5.8. Струйная лазерно-электрохимическая обработка
Струйная ЛЭХО отличается от струйной ЭХО (раздел 3.5 обзора) тем, что через сопло для подачи электролита в зону обработки направлен сфокусированный луч лазера. Струя электролита служит здесь оптическим волокном.
Показательными являются работы, где проведено сравнение результатов струйной ЭХО и струйной ЛЭХО.
Скорость локального осаждения золота (диаметр освещенного пятна 0.05 см) на металлической подложке достигает 10–12 мкм/с [166, 167]. Это более чем на порядок величины выше, чем при струйной ЭХО без лазера. Выход по току при осаждении золота без лазерного воздействия составляет 15–20%, а при облучении (25 Вт) – около 60%. Наблюдаемое смещение поляризационной кривой в область более положительных значений потенциала соответствует снижению скорости выделения водорода.
Работа [168] посвящена прорезанию пазов в образцах из алюминия, нержавеющей стали и титанового сплава в растворах NaCl или NaNO3 двумя этими методами. Основной результат состоял в том, что под воздействием лазерного излучения глубина паза была больше, чем без лазера (при одинаковых остальных условиях) на стали на 10%, на алюминии на 20%, на титане на 14% и поперечный размер паза был меньше на стали на 27%, на алюминии на 30% и на титане на 12%. Другими словами, воздействие лазера увеличивает степень локализации электрохимического процесса.
Датта и соавторы провели сравнение двух методов при растворении никеля и нержавеющей стали в растворах NaCl и NaNO3 [153]. При ЭХО лучшие результаты по скорости и точности обработки были получены в растворе NaNO3. Струйная ЛЭХО в NaNO3 оказалась непригодной из-за низкого выхода по току, что, очевидно, связано с высокой температурой в зоне обработки при ЛЭХО (выход по току в этом растворе снижается при увеличении температуры). При струйной ЛЭХО следует использовать NaCl; воздействие лазерного излучения повышает степень локализации процесса растворения в таком электролите и этим значительно снижает основной недостаток ЭХО в NaCl.
6. ЗАКЛЮЧЕНИЕ
Основным методом локализации процессов осаждения, растворения и оксидирования металлов и полупроводников является применение микро/нано размерных электродов-инструментов (катодов при растворении и оксидировании и анодов при электроосаждении) и поддержание микро/нано размерных межэлектродных расстояний. Разработаны и применяются дополнительные меры увеличения степени локализации, уменьшения латерального распространения процесса электрохимической обработки в растворе непосредственно под микроэлектродом-инструментом: ультракороткие импульсы напряжения, ограничение объема электролита в межэлектродном пространстве (обработка через жидкостной мениск, электрохимические микроячейки).
Важным направлением в увеличении степени локализации безмасковых электрохимических процессов с применением микро/нано размерных электродов и межэлектродных зазоров является локализация электроактивного компонента электролита (ионов металла, осаждаемого на подложке или компонента, отвечающего за процесс локального травления подложки) в зоне обработки. К этому направлению относится применение электролитов, объем которых не содержит электроактивный компонент. Электроактивный компонент образуется на электроде-инструменте или вводится в электрохимическую ячейку непосредственно к участку подложки, предназначенному для обработки. Включение в состав электролита специального компонента – поглотителя электроактивного компонента, ограничивающего его латеральную диффузию, позволяет увеличить степень локализации.
Отдельным направлением является локализация сфокусированным лазерным излучением.
Допустимые размеры настоящего обзора позволили затронуть не все стороны проблемы и дать ссылки лишь на сравнительно небольшое количество опубликованных работ по этому, быстро развивающемуся направлению применения электрохимических методов в междисциплинарных интересах. Многие ссылки на другие работы читатель может найти в процитированных здесь публикациях.
Список литературы
Electrochemical Microsystem Technologies, Schultze, J.W., Osaka, T., and Datta, M., Eds., London: Taylor & Francis, 2002.
Datta, M. and Landolt, D., Fundamental aspects and applications of electrochemical microfabrication, Electrochim. Acta, 2000, vol. 45, p. 2535.
Bhattacharyya, B., Electrochemical Micromachining for Nanofabrication, MEMS and Nanotechnology, Oxford: William Andrew, 2015.
Braun, T.M. and Schwartz, D.T., The emerging role of electrodeposition in additive manufacturing, Electrochem. Soc. Interface, 2016, vol. 25, no. 1, p. 69.
Liu, Y., Zeng, Y., and Yu, H., Development of microelectrodes for electrochemical machining, Int. J. Manuf. Technol., 2011, vol. 55, p. 195.
Kim, B.H., Na, C.W., Lee, Y.S., Choi, D.K., and Chu, C.N., Micro electrochemical machining of 3D micro structure using dilute sulfuric acid, CIRP Annals – Manufacturing Technology, 2005, vol. 54, p. 191.
Wang, Y., Zeng, Y., Qu, N., and Zhu, D., Electrochemical micromachining of small tapered microstructures with sub-micro spherical tool, Int. J. Adv. Manuf. Technol., 2016, vol. 84, p. 851.
Koch, M., Kirchner, V., and Schuter, R., Electrochemical micromachining with ultrashort voltage pulses, Electrochim. Acta, 2003, vol. 48, p. 3213.
Sjöström, T. and Su, B., Micropatterning of titanium surfaces using electrochemical micromachining with an ethylene glycol electrolyte, Mater. Lett., 2011, vol. 65, p. 3489.
Maurer, J.J., Mallett, J.J., Hudson, J.L., Fick, S.E., Moffat, T.P., and Shaw, G.A., Electrochemical micromachining of Hastelloy B-2 with ultrashort voltage pulses, Electrochim. Acta, 2010, vol. 55, p. 952.
Park, B.J., Kim, B.H., and Chu, C.N., The effects of tool electrode size on characteristics of micro electrochemical machining, Annals of the CIRP, 2006, vol. 55, p. 197.
Koza, J.A., Sueptittz, R.S., Uhlemann, M., Schutz, L., and Gebert, A., Electrochemical micromachining of a Zr-based bulk metallic glass using a micro-tool electrode technique, Intermetallics, 2011, vol. 19, p. 437.
Li, Y., Ma, X., Liu, G., Hu, M., and Yi, F., Research on micro ECM using micro array electrode, Proc. 16th Int. Symp. on Electromachining, Shanghai, China. 2010, p. 335.
Седыкин, Ф.В. Размерная электрохимическая обработка деталей машин. М.: Машиностроение. 1976. 302 с. [Sedykin, F.V., Electrochemical Machining of Machine Parts (in Russian), M.: Mashinostroenie, 1976.]
Румянцев, Е.М., Давыдов, А.Д. Технология электрохимической обработки металлов. М.: Высшая школа. 1984. 159 с. [Rumyantsev, E. and Davydov, A., Electrochemical Machining of Metals, M.: Mir, 1989. 168 p.]
Давыдов, А.Д., Волгин, В.М., Любимов, В.В. Электрохимическая размерная обработка металлов: процесс формообразования. Электрохимия. 2004. Т. 40. С. 1438. [Davydov, A.D., Volgin, V.M., and Lubimov, V.V., Electrochemical machining of metals: fundamentals of electrochemical shaping, Russian J. Electrochem., 2004, vol. 40, p. 1230.]
Wang, Z., Zhu, Y., Fan, Z., and Yun, N., Mechanism and process study of ultrasonical vibration combined synchronizing pulse electrochemical micro-machining, Proc. 16th Int. Symp. on Electromachining, Shanghai, China. 2010, p. 351.
Житников, В.П., Зайцев, А.Н. Импульсная электрохимическая размерная обработка. М.: Машиностроение. 2008. 413 с. [Zhitnikov, V.P. and Zaitsev, A.N., Pulsed Electrochemical Machining (in Russian), M.: Mashinostroenie, 2008.
Schramm, A., Gesetzmassigkeiten des elektrochemischen abtrags beim kombinierten elektrochemischen/ultraschall-senken, Fertigungstech. Betr., 1985, B. 35, S. 367.
Allongue, P., Jiang, P., Kirchner, V., Trimmer, A.L., and Schuster, R., Electrochemical micromachining of p-type silicon, J. Phys. Chem. B., 2004, vol. 108, p. 14434.
Trimmer, A.L., Maurer, J.J., Schuster, R., Zangari, G., and Hudson, J.L., All-electrochemical synthesis of submicrometer Cu structures on electrochemically machined p-Si substrates, Chem. Mater., 2005, vol. 17, p. 6755.
Schuster, R., Kirchner, V., Allongue, P., and Ertl, G., Electrochemical micromachining, Science, 2000, vol. 289, p. 98.
Koch, M., Kirchner, V., and Schuster, R., Electrochemical micromachining with ultrashort voltage pulses, Electrochim. Acta, 2003, vol. 48, p. 3213.
Kirchner, V., Xia, X., and Schuster, R., Electrochemical nanostructuring with ultrashort voltage pulses, Acc. Chem. Res., 2001, vol. 34, p. 371.
Park, B.J., Kim, B.H., and Chu, C.N., The effects of tool electrode size on characteristics of micro electrochemical machining, Annals of the CIRP, 2006, vol. 55, p. 197.
Madden, J.D., Lafontaine, S.R., and Hunter, I.W., Fabrication by electrodeposition: building 3D structures and polymer actuators, Proc. Sixth Int. Symp. “Micro Machine and Human Science”, 1995, p. 77.
Madden, J.D. and Hunter, I.W., Three-dimensional microfabrication by localized electrochemical deposition, J. Microelectromech. Syst., 1996, vol. 5, no. 1, p. 24.
Said, R.A., Microfabrication by localized electrochemical deposition: experimental investigation and theoretical modeling, Nanotechnology, 2003, vol. 14, no. 5, p. 523.
Lin, J.C., Jang, S.B., Lee, D.L., Chen, C.C., Yeh, P.C., Chang, T.K., and Yang, J.H., Fabrication of micrometer Ni columns by continuous and intermittent microanode guided electroplating, J. Micromech. Microeng., 2005, vol. 15, no. 12, p. 2405.
Lin, C.S., Lee, C.Y., Yang, J.H., and Huang, Y.S., Improved copper microcolumn fabricated by localized electrochemical deposition, Electrochem. Solid-State Lett., 2005, vol. 8, p. C125.
Seol, S.-K., Pyun, A.-R., Hwu, Y., Margaritondo, G., and Je, J.-H., Localized electrochemical deposition of copper monitored using real-time x-ray microradiography, Adv. Funct. Mater., 2005, vol. 15, p. 934.
Yang, J.H., Lin, J.C., Chang, T.K., You, X.B., and Jiang, S.B., Localized Ni deposition improved by saccharin sodium in the intermittent MAGE process, J. Micromech. Microeng., 2009, vol. 19, p. 025015.
Yang, J.H., Lin, J.C., Chang, T.K., Lai, G.Y., and Jiang, S.B., Assessing the degree of localization in localized electrochemical deposition of copper, J. Micromech. Microeng., 2008, vol. 18, p. 055023.
Lin, J.C., Yang, J.H., Chang, T.K., and Jiang, S.B., On the structure of micrometer copper features fabricated by intermittent micro-anode guided electroplating, Electrochim. Acta, 2009, vol. 54, no. 24, p. 5703.
Lin, J.C., Chang, T.K., Yang, J.H., Chen, Y.S., and Chuang, C.L., Localized electrochemical deposition of micrometer copper columns by pulse plating, Electrochim. Acta, 2010, vol. 55, p. 1888.
Said, R.A., Localized electro-deposition (LED): the march toward process development, Nanotechnology, 2004, vol. 15, p. S649.
Lin, J.C., Chang, T.K., Yang, J.H., Jeng, J.H., Lee, D.L., and Jiang, S.B., Fabrication of a micrometer Ni–Cu alloy column coupled with a Cu micro-column for thermal measurement, J. Micromech. Microeng., 2009, vol. 19, p. 015030(1–10).
Debnath, S., Laskar, H.R., and Bhattacharyya, B., Investigation into generation of micro features by localised electrochemical deposition, J. Inst. Eng. India Ser. C, 2019, vol. 100, no. 1, p. 113.
Wang, F., Xiao, H., and He, H., Effects of applied potential and the initial gap between electrodes on localized electrochemical deposition of micrometer copper columns, PMC, Scientific Reports, 2016, no. 6, p. 26270. https://doi.org/10.1038/srep26270
Lee, C.-Y., Lin, C.-S., and Lin, B.-R., Localized electrochemical deposition process improvement by using different anodes and deposition directions, J. Micromech. Microeng., 2008, vol. 18, p. 105008.
El-Giar, E.M., U, C., and Thomson, D.J., Localized electrochemical plating of interconnectors for microelectronics, Proc. 1997 Conference on Communications, Power and Computing WESCANEX’97, Winnipeg, MB, 1997, p. 327.
Jansson, A., Thornell, G., and Johansson, S., High resolution 3D microstructures made by localized electrodeposition of nickel, J. Electrochem. Soc., 2000, vol. 147, no. 5, p. 1810.
Hwang, Y.-R., Lin, J.-C., and Chen, T.-C., The analysis of the deposition rate for continuous micro-anode guided electroplating process, Int. J. Electrochem. Sci., 2012, vol. 7, p. 1359.
Pellicer, E., Pané, S., Panagiotopoulou, V., Fusco, S., Sivaraman, K.M., Suriñach, S., Baró, M.D., Nelson, B.J., and Sort, J., Localized electrochemical deposition of porous Cu-Ni microcolumns: Insights into the growth mechanisms and the mechanical performance, Int. J. Electrochem. Sci., 2012, vol. 7, p. 4014.
Chang, T.K., Lin, J.C., Yang, J.H., Yeh, P.C., Lee, D.L., and Jiang, S.B., Surface and transverse morphology of micrometer nickel columns fabricated by localized electrochemical deposition, J. Micromech. Microeng., 2007, vol. 17, p. 2336.
Yeo, S.H. and Choo, J.H., Effects of rotor electrode in the fabrication of high aspect ratio microstructures by localized electrochemical deposition, J. Micromech. Microeng., 2001, vol. 11, p. 435.
Wang, F., Bian, H., Wang, F., Sun, J., and Zhu, W., Fabrication of micro copper walls by localized electrochemical deposition through the layer by layer movement of a micro anode, J. Electrochem. Soc., 2017, vol. 164, p. D758.
Wang, F., Sun, J., Liu, D., Wang, Y., and Zhu, W., Effect of voltage and gap on micro-nickel-column growth patterns in localized electrochemical deposition, J. Electrochem. Soc., 2017, vol. 164, p. D297.
Yeo, S.H., Choo, J.H., and Sim, K.H.A., On the effects of ultrasonic vibrations on localized electrochemical deposition, J. Micromech. Microeng., 2002, vol. 12, p. 271.
Said, R.A., Alshwawreh, N., and Haik, Y., Fabrication of array microstructures using serial and parallel localized electrodeposition, Int. J. Nanosci., 2009, vol. 8, no. 03, p. 323.
Ciou, Y.J., Hwang, Y.R., and Lin, J.C., Theoretical modeling and fabrication of two-dimensional microstructures by using micro-anode-guided electroplating with real-time image processing, Key Eng. Mat., 2015, vol. 656, p. 604.
Brant, A.M., Sundaram, M.M., and Kamaraj, A.B., Finite element simulation of localized electrochemical deposition for maskless electrochemical additive manufacturing, J. Manuf. Sci. E.-T. ASME, 2015, vol. 137, no. 1, p. 011018.
Xiao, H., Zeng, P., Ren, X., and Wang, F., Three-dimensional microfabrication of copper column by localized electrochemical deposition, Electronic Packaging Technology (ICEPT), 17th International Conference IEEE, 2016, p. 69.
Kamaraj, A., Lewis, S., and Sundaram, M., Numerical study of localized electrochemical deposition for micro electrochemical additive manufacturing, Procedia CIRP, 2016, vol. 42, p. 788.
Volgin, V.M., Kabanova, T.B., and Davydov, A.D., Modeling of local maskless electrochemical deposition of metal microcolumns, Chem. Eng. Sci., 2018, vol. 183, p. 123.
Ullmann, R., Will, T., and Kolb, D.M., Nanoscale decoration of Au(111) electrodes with Cu clusters by an STM, Chem. Phys. Lett., 1993, vol. 209, p. 238.
Ullmann, R., Will, T., and Kolb, D.M., Nanostructuring of electrode surfaces by tip-induced metal deposition, Ber. Bunsenges. Phys. Chem., 1995, vol. 99, p. 1414.
Engelmann, G.E., Ziegler, J.C., and Kolb, D.M., Electrochemical fabrication of large arrays of metal nanoclusters, Surf. Sci. Lett., 1998, vol. 401, p. L420.
Kolb, D.M., Ullmann, R., and Will, T., Nanofabrication of small copper clusters on gold (111) electrodes by a scanning tunneling microscope, Science, 1997, vol. 275, p. 1097.
Kolb, D.M., Ullmann, R., and Ziegler, J.C., Electrochemical nanostructuring, Electrochim. Acta, 1998, vol. 43, p. 2751.
Engelmann, G.E., Ziegler, J.C., and Kolb, D.M., Nanofabrication of small palladium clusters on Au(111) electrodes with a scanning tunneling microscope, J. Electrochem. Soc., 1998, vol. 145, p. L33.
Hofmann, D., Schindler, W., and Kirschner J., Electrodeposition of nanoscale magnetic structures, Appl. Phys. Lett., 1998, vol. 73, p. 3279.
Schindler, W., Hofmann, D., and Kirschner, J., Nanoscale electrodeposition: A new route to magnetic nanostructures? J. Appl. Phys., 2000, vol. 87, p. 7007.
Schindler, W., Hofmann, D., and Kirschner J., Localized electrodeposition using a scanning tunneling microscope tip as a nanoelectrode, J. Electrochem. Soc., 2001, vol. 148, p. C124.
Spiegel, A., Staemmler, L., Döbeli, M., and Schmuki, P., Selective electrodeposition of Cu nanostructures on focused ion beam sensitized p-Si, J. Electrochem. Soc., 2002, vol. 149, p. C432.
Homma, T., Kubo, N., and Osaka, T.,Maskless and electroless fabrication of patterned metal nanostructures on silicon wafers by controlling local surface activities, Electrochim. Acta, 2003, vol. 48, p. 3115.
Choi, J., Chen, Z., and Singh, R.K., A method for selective deposition of copper nanoparticles on silicon surfaces, J. Electrochem. Soc., 2003, vol. 150, p. C563.
Schmuki, P. and Erickson, L.E., Selective high-resolution electrodeposition on semiconductor defect patterns, Phys. Rev. Lett., 2000, vol. 85, p. 2985.
Santinacci, L., Djenizian, T., and Schmuki, P., Atomic force microscopy-induced nanopatterning of Si(100) surfaces, J. Electrochem. Soc., 2001, vol. 148, p. C640.
Pötzschke, R.T., Staikov, G., Lorenz, W.J., and Wiesbeck, W., Electrochemical nanostructuring of n‑Si(111) single-crystal faces, J. Electrochem. Soc., 1999, vol. 146, p. 141.
Ammann, E. and Mandler, D., Local deposition of gold on silicon by the scanning electrochemical microscope, J. Electrochem. Soc., 2001, vol. 148, p. 533.
Oskam, G., Long, J.G., Natarajan, A., and Searson, P.C., Electrochemical deposition of metals onto silicon, J. Phys. D: Appl. Phys., 1998, vol. 31, p. 1927.
Avouris, P., Hertel, T., and Martel, R., Atomic force microscope tip-induced local oxidation of silicon: kinetics, mechanism, and nanofabrication, Appl. Phys. Lett., 1997, vol. 71, p. 285.
Avouris, P., Martel, R., Hertel, T., and Sandstrom, R.L., AFM-tip-induced and current-induced local oxidation of silicon and metals, Appl. Phys. A: Mater. Sci. Process., 1998, vol. 66, p. S659.
Held, R., Heinzel, T., Studerus, P., and Ensslin, K., Nanolithography by local anodic oxidation of metal films using an atomic force microscope, Physica E: Low-Dimensional Systems and Nanostuctures, 1998, vol. 2, p. 748.
Vaccaro, P.O., Sakata, S., Yamaoka, S., Umezu, I., and Sugimura, A., Nano-oxidation of vanadium thin films using atomic force microscopy, J. Mater. Sci. Lett., 1998, vol. 17, p. 1941.
Okur, S., Büyükköse, S., and Tari, S., Scanning probe oxidation lithography on Ta thin films, J. Nanosci. Nanotechnol., 2008, vol. 8, p. 5640.
Matsumoto, K., Takahashi, S., Ishii, M., Hoshi, M., Kurokawa, A., Ichimura, S., and Ando, A., Application of STM nanometer-size oxidation process to planar-type MIM diode, Jpn. J. Appl. Phys., 1995, vol. 34, p. 1387.
Snow, E.S. and Campbell, P.M., Fabrication of Si nanostructures with an atomic force microscope, Appl. Phys. Lett., 1994, vol. 64, p. 1932.
Sugimura, H., Uchida, T., Kitamura, N., and Masuhara, H., Tip-induced anodization of titanium surfaces by scanning tunneling microscopy: a humidity effect on nanolithography, Appl. Phys. Lett., 1993, vol. 63, p. 1288.
Snow, E.S., Park, D., and Campbell, P.M., Single-atom point contact devices fabricated with an atomic force microscope, Appl. Phys. Lett., 1996, vol. 69, p. 269.
Campbell, P.M., Snow, E.S., and McMarr, P.J., Fabrication of nanometer-scale side-gated silicon field effect transistors with an atomic force microscope, Appl. Phys. Lett., 1995, vol. 66, p. 1388.
Day, H.C. and Allee, D.R., Selective area oxidation of silicon with a scanning force microscope, Appl. Phys. Lett., 1993, vol. 62, p. 2691.
Vullers, R.J.M., Ahlskog, M., and Van Haesendonck, C., Titanium nanostructures made by local oxidation with the atomic force microscope, Appl. Surface Sci., 1999, vol. 144, p. 584.
Sugimura, H., Uchida, T., Kitamura, N., and Masuhara, H., Scanning tunneling microscope tip-induced anodization for nanofabrication of titanium, J. Phys. Chem., 1994, vol. 98, p. 4352.
Wang, D., Tsau, L., Wang, K.L., and Chow, P., Nanofabrication of thin chromium film deposited on Si(100) surfaces by tip induced anodization in atomic force microscopy, Appl. Phys. Lett., 1995, vol. 67, p. 1295.
Seol, S.K., Kim, D., Lee, S., Kim, J.H., Chang, W.S., and Kim, J.T., Electrodeposition-based 3D printing of metallic microarchitectures with controlled internal structures, Small, 2015, vol. 11, p. 3896.
Morsali, S., Daryadel, S., Zhou, Z., Behroozfar, A., Baniasadi, M., Qian, D.,and Minary-Jolandan, M., Multi-physics simulation of metal printing at micro/nanoscale using meniscus-confined electrodeposition: Effect of environmental humidity, J. Appl. Phys., 2017, vol. 121, p. 024903.
Suryavanshi, A.P. and Yu, M.-F., Electrochemical fountain pen nanofabrication of vertically grown platinum nanowires, Nanotechnology, 2007, vol. 18, p. 105305.
Morsali, S., Daryadel, S., Zhou, Z., Behroozfar, A., Baniasadi M., Moreno, S., Qian, D., and Minary-Jolandan, M., Multi-physics simulation of metal printing at micro/nanoscale using meniscus-confined electrodeposition: Effect of nozzle speed and diameter, J. Appl. Phys., 2017, vol. 121, p. 214305.
Suryavanshi, A.P. and Yu, M.-F., Probe-based electrochemical fabrication of freestanding Cu nanowire array, Appl. Phys. Lett., 2006, vol. 88, p. 083103.
Hu, J. and Yu, M.-F., Meniscus-confined three-dimensional electrodeposition for direct writing of wire bonds, Science, 2010, vol. 329, p. 313.
Chen, X., Liu, X., Childs, P., Brandon, N., and Wu, B., A low cost desktop electrochemical metal 3D printer, Adv. Mater. Technol., 2017, vol. 2, p. 1700148.
Momotenko, D., Page, A., Adobes-Vidal, M., and Unwin, P.R., Write-read 3D patterning with a dual-channel nanopipette, ACS Nano, 2016, vol. 10, p. 8871.
Müller, A.D., Müller, F., and Hietschold, M., Electrochemical pattern formation in a scanning near-field optical microscope, Appl. Phys. A: Mater. Sci. Process., 1998, vol. 66, p. S453.
Ito, S. and Iwata, F., Nanometer-scale deposition of metal plating using a nanopipette probe in liquid condition, Jpn. J. Appl. Phys., 2011, vol. 50, p. 08LB15.
Leïchlé, T. and Nicu, L., Copper electrodeposition localized in picoliter droplets using microcantilever arrays, Appl. Phys. Lett., 2006, vol. 88, p. 254108.
Pirani, M. and Schöter, K., Elektrolytische formgebung von harten metallischen gegenständen, Z. Metallkunde, 1924, B. 16, S. 132.
Lohrengel, M.M., Klüppel, I., Rosenkranz, C., Bettermann, H., and Schultze, J.W., Microscopic investigations of electrochemical machining of Fe in NaNO3, Electrochim. Acta, 2003, vol. 48, p. 3203.
Cowper-Coles, S., An electrolytic drilling and slotting process, The Electro-Chemist and Metallurgist, 1903, vol. 3, part 4, p. 203.
Cowper-Coles, S., Electrolytic drilling and slotting process, Electrochemical Industry, 1904, vol. 2, no. 1, p. 28.
Nelson, J.B., Wisecarver, Z., and Schwartz, D.T., Electrochemical printing: mass transfer effects, J. Micromech. Microeng., 2007, vol. 17, p. 1192.
Cole, R.R. and Hopenfeld, Y., An investigation of electrolytic jet polishing at high current densities, J. Engineering for Industry, Trans. ASME, (J. Eng. Ind.) 1963, vol. 85, no. 4, p. 395.
Speidel, A., Mitchell-Smith, J., Bisterov, I., and Clare, A.T., The dependence of surface finish on material precondition in electrochemical jet machining, Proc. CIRP, 2018, vol. 68, p. 477.
Li, Q. and Walker, J.D.A., Prediction of electrodeposition rates from an impinging jet, AIChE J., 1996, vol. 42, p. 391.
Mitchell-Smith, J., Speidel, A., and Clare, A.T., Advancing electrochemical jet methods through manipulation of the angle of address, J. Mater. Process. Technol., 2018, vol. 255, p. 364.
Natsu, W., Ikeda, T., and Kunieda, M., Generating complicated surface with electrolyte jet machining, Precis. Eng., 2007, vol. 31, p. 33.
Natsu, W., Ooshiro, S., and Kunieda, M., Research on generation of three-dimensional surface with micro-electrolyte jet machining, CIRP J. Manufact. Sci. Technol., 2008, vol. 1, p. 27.
Kuhn, D., Martin, A., Eckart, C., Sieber, M., Morgenstern, R., Hackert-Oschätzchen, M., Lampke, T., and Schubert, A., Localised anodic oxidation of aluminium material using a continuous electrolyte jet, IOP Conf. Ser.: Mater. Sci. Eng., 2017, vol. 181, p. 012042. https://doi.org/10.1088/1757-899X/181/1/012042
Aerts, T., De Graeve, I., Nelissen, G., Deconinck, J., Kubacki, S., Dick, E.,and Terryn, H. Experimental study and modelling of aluminium in a wall-jet electrode set-up in laminar and turbulent regime, Corros. Sci., 2009, vol. 51, p. 1482.
Meltzer, S. and Mandler, D., Microwriting of gold patterns with the scanning electrochemical microscope, J. Electrochem. Soc., 1995, vol. 142, p. L82.
De Abril, O., Mandler, D., and Unwin, P.R., Local cobalt electrodeposition using the scanning electrochemical microscope, Electrochem. Solid-State Lett., 2004, vol. 7, p. C71.
Borgwarth, K. and Heinze, J., Increasing the resolution of the scanning electrochemical microscope using a chemical lens: Application to silver deposition, J. Electrochem. Soc., 1999, vol. 146, p. 3285.
Borgwarth, K., Ricken, C., Ebling, D.G., and Heinze, J., Surface characterisation and modification by the scanning electrochemical microscope (SECM), Ber. Bunsenges. Phys. Chem., 1995, B. 99, S. 1421.
Mandler, D. and Bard, A., High resolution etching of semiconductors by the feedback mode of the scanning electrochemical microscope, J. Electrochem. Soc., 1990, vol. 137, p. 2468.
Sheffer, M. and Mandler, D., Scanning electrochemical imprinting microscopy: A tool for surface patterning, J. Electrochem. Soc., 2008, vol. 155, p. D203.
Mandler, D. and Bard, A., Scanning electrochemical microscopy: The application of the feedback mode for high resolution copper etching, J. Electrochem. Soc., 1989, vol. 136, p. 3143.
Sheffer, M. and Mandler, D., Why is copper locally etched by scanning electrochemical microscopy? J. Electroanal. Chem., 2008, vol. 622, p. 115.
Macpherson, J.V., Slevin, C.J., and Unwin, P.R., Probing the oxidative etching kinetics of metals with the feedback mode of the scanning electrochemical microscope, J. Chem. Soc., Faraday Trans., 1996, vol. 92, p. 3799.
Cornut, R., Nunige, S., Lefrou, C., and Kanoufi, F., Local etching of copper films by the scanning electrochemical microscope in the feedback mode: A theoretical and experimental investigation, Electrochim. Acta, 2011, vol. 56, p. 10701.
Tian, Z., Fen, Z., Tian, Z., Zhuo, X., Mu, J., Li, C., Lin, H., Ren, B., Xie, Z., and Hu, W., Confined etchant layer technique for two-dimensional lithography at high resolution using electrochemical scanning tunneling microscopy, Faraday Discuss., 1992, vol. 94, p. 37.
Jiang, L.M., Li, W., Attia, A., Cheng, Z.Y., Tang, J., Tian, Z.Q., and Tian, Z.W., A potential method for electrochemical micromachining of titanium alloy Ti6Al14V, J. Appl. Electrochem., 2008, vol. 38, p. 785.
Jiang, L.M., Liu, Z.F., Tang, J., Zhang, L., Shi, K., Tian, Z.Q., Liu, P.K., Sun, L.N., and Tian, Z.W., Three-dimensional micro-fabrication on copper and nickel, J. Electroanal. Chem., 2005, vol. 581, p. 153.
Ma, X.-Z., Zhang, L., Cao, G.-H., Lin, Y., and Tang, J., Electrochemical micromachining of nitinol by confined-etchant-layer technique, Electrochim. Acta, 2007, vol. 52, p. 4191.
Zu, Y., Xie, L., Mao, B., and Tian, Z., Studies on silicon etching using the confined etchant layer technique, Electrochim. Acta, 1998, vol. 43, p. 1683.
Sun, J.J., Huang, H.G., Tian, Z.Q., Xie, L., Luo, J., Ye, X.Y., Zhou, Z.Y., Xia, S.H., and Tian, Z.W., Three-dimensional micromachining for microsystems by confined etchant layer technique, Electrochim. Acta, 2001, vol. 47, p. 95.
Yuan, Y., Han, L., Zhang, J., Jia, L., Zhao, X., Cao, Y., Hu, Z., Yan, Y., Dong, S., Tian, Z.-Q., Tian, Z.-W., and Zhan, D., Electrochemical mechanical micromachining based on confined etchant layer technique, Faraday Discuss., 2013, vol. 164, p. 189.
Hirt, L., Ihle, S., Pan, Z., Dorwling-Carter, L., Reiser, A., Wheeler, J.M., Prolenak, R., Vörös, J., and Zambelli, T., Template-free 3D microprinting of metals using a force-controlled nanopipette for layer-by-layer electrodeposition, Adv. Mater., 2016, vol. 28, p. 2311.
Hirt, L., Grüter, R.R., Berthelot, T., Cornut, R., Vörös, J., and Zambelli, T., Local surface modification via confined electrochemical deposition with FluidFM, RSC Adv., 2015, vol. 5, p. 84517.
Tsao, J.Y. and Ehrlich, D.J., Laser-controlled chemical etching of aluminum, Appl. Phys. Lett., 1983, vol. 43, p. 146.
Nowak, R. and Metev, S., Thermochemical laser etching of stainless steel and titanium in liquids, Phys., 1996, vol. A 63, p. 133.
Hsiao, M.C. and Wan, C.C., The investigations of laser-enhanced copper plating on a good heat conducting copper foil, J. Electrochem. Soc., 1991, vol. 138, p. 2273.
Puippe, J.C., Acosta, R.E., and von Gutfeld, R.J., Investigation of laser-enhanced electroplating mechanisms, J. Electrochem. Soc., 1981, vol. 128, p. 2539.
Von Gutfeld, R.J., Tynan, E.E., Melcher, R.L., and Blum, S.E., Laser enhanced electroplating and maskless pattern generation, Appl. Phys. Lett., 1979, vol. 35, p. 651.
Bindra, P., Arbach, G.V., and Stimming, U., On the mechanism of laser enhanced plating of copper, J. Electrochem. Soc., 1987, vol. 134, p. 2893.
Al-Sufi, A.K., Eichler, H.J., and Salk, J., Laser induced copper plating, J. Appl. Phys., 1983, vol. 54, p. 3629.
Еременко, А.А., Козлова, Е.К., Портнягин, А.И., Романченко, А.Н., Филиппов, А.Е. Влияние оптического излучения на процесс химического никелирования. Квантовая электроника. 1984. Т. 11. С. 1677. [Eremenko, A.A., Kozlova E.K., Portnyagin A.I., Romanchenko, A.N., and Filippov, A.E., Influence of optical radiation on electroless nickel plating, Soviet J. Quantum Electronics, 1984, vol. 14, no. 8, p. 1129.]
Von Gutfeld, R.J. and Hodgson, R.T., Laser enhanced etching in KOH, Appl. Phys. Lett., 1982, vol. 40, p. 352.
Серянов, Ю.В., Рабкин, В.Б., Сурменко, Л.А. Лазерное травление меди в растворе азотной кислоты. Электрохимия. 1988. Т. 24. С. 911. [Seryanov, Yu.V., Rabkin, V.B., and Surmenko, L.A., Laser-enhanced copper etching in nitric acid solutions, Soviet Electrochemistry, 1988, vol. 24, p. 842.]
Дикусар, А.И., Энгельгардт, Г.Р., Молин, А.Н. Термокинетические явления при высокоскоростных электродных процессах. Кишинев: Штиинца, 1989. С. 112. [Dikusar, A.I., Engelgardt, G.P., and Molin, A.N., Thermokinetic Phenomena at High-Rate Electrode Processes (in Russian), Kishinev: Shtiintsa, 1989, p. 112.]
Yung, E.K., Hussey, B.W., Gupta, A., and Romankiw, L.T., Laser-assisted etching of manganese-zinc-ferrite, J. Electrochem. Soc., 1989, vol. 136, p. 665.
Серянов, Ю.В., Григорьева, Е.М., Большинскова, Т.А., Фоменко, Л.А. Термические условия и кинетика формирования “линий” никеля при лазерном облучении пленок NimLnXk на Al2O3, Физ. Хим. Обраб. Матер. 1995. № 1. С. 17. [Serya-nov, Yu.V., Grigor’eva, E.M., Bol’shinskova, T.A., and Fomenko, L.A., Thermal conditions and kinetics of formation of nickel “lines” during laser radiation of NimLnXk films on Al2O3, Fiz. Khim. Obrab. Mater. (in Russian), 1995, no. 1, p. 17.]
Zhang, H. and Xu, J., Modeling and experimental investigation of laser drilling with jet electrochemical machining, Chinese J. Aeronautics, 2010, vol. 23, p. 454.
Kuiken, H.K., Mikkers, F.E.P., and Wierenga, P.E., Laser-enhanced electroplating on good heat-conducting bulk materials, J. Electrochem. Soc., 1983, vol. 130, p. 554.
Hsiao, M.C. and Wan, C.C., The effect of pH on the localized etching process induced by laser irradiation, J. Electrochem. Soc., 1994, vol. 141, p. 943.
Джунушалиев, В.Д., Чокоев, Э.С. Особенности лазерной обработки металла в жидкой среде. Физ. Хим. Обраб. Матер. 1990. №4. С. 140. [Dzhunushaliev, V.D. and Chokoev, E.S., Specific features of laser treatment of metal in liquid, Fiz. Khim. Obrab. Mater. (in Russian), 1990, no. 4, p. 140.]
Давыдов, А.Д. Лазерно-электрохимическая обработка металлов. Электрохимия. 1994. Т. 30. С. 965. [Davydov, A.D., Laser electrochemical machining of metals, Russian J. Electrochem., 1994, vol. 30, p. 871.]
Kozak, J. and Rajurkar, K.P., Laser assisted electrochemical machining, Trans. NAMRI/SME, 2001, vol. 29, p. 421.
Metev, S.M. and Veiko, V.P., Laser-Assisted Microtechnology, Berlin: Springer, 1998.
Von Gutfeld, R.J., Vigliotti, D.R., and Datta, M., Laser chemical etching of metals in sodium nitrate solution, J. Appl. Phys., 1988, vol. 64, p. 5197.
Ефимов, И.О., Кривенко, А.Г., Бендерский, В.А. Лазерная активация никелевого электрода. Электрохимия. 1988. Т. 24. С. 1176. [Efimov, I.O., Krivenko, A.G., and Benderskii, V.A., Laser activation of nickel electrodes, Soviet Electrochemistry, 1988, vol. 24, p. 1092.]
Jacobs, J.W.M. and Rikken, J.M.G., Boiling effects and bubble formation at the solid-liquid interface during laser-induced metal deposition, J. Electrochem. Soc., 1987, vol. 134, p. 2690.
Datta, M., Romankiw, L.T., Vigliotti, D.R., and von Gutfeld R.J., Jet and laser-jet electrochemical micromachining of nickel and steel, J. Electrochem. Soc., 1989, vol. 136, p. 2251.
Ваграмян, А.Т., Жамагорцянц, М.А. Электроосаждение металлов и ингибирующая адсорбция. М.: Наука, 1969. С. 91. [Vagramyan, A.T. and Zhamagortsyants, M.A., Electrodeposition of Metals and Inhibiting Adsorption, M.: Nauka, p. 91.]
Shor, J.S., Zhang, X.G., and Osgood, R.M., Laser-assisted photoelectrochemical etching of n-type beta-SiC, J. Electrochem. Soc., 1992, vol. 139, p. 1213.
Lum, R.M., Glass, A.M., Ostermayer, F.W., Kohl, P.A., Ballman, A.A., and Logan, R.A., Holographic photoelectrochemical etching of diffraction gratings in n-InP and n-GaInAsP for distributed feedback lasers, J. Appl. Phys., 1985, vol. 57, p. 39.
Алфёров, Ж.И., Горячев, Д.Н., Гуревич, С.А., Мизеров, М.Н., Портной, Е.Л., Рывкин, Б.С. Дифракционные решетки на поверхности GaAs, полученные методом интерференционного фототравления. Журн. технич. Физики. 1976. Т. 46. С. 1505. [Alferov, Zh.I., Goryachev, D.N., Gurevich, S.A., Mizerov, M.N., Portnoi, E.L., and Ryvkin, B.S., Diffraction lattices on the GaAs surface obtained by the method of interference photoetching, J. Technical Physics (in Russian), 1976, vol. 46, p. 1505.]
Беляков, Л.В., Горячев, Д.Н., Мизеров, М.Н., Портной, Е.Л. Некоторые характеристики дифракционных решеток, полученных фототравлением поверхности полупроводников. Журн. технич. Физики. 1974. Т. 44. С. 1331. [Belyakov, L.V., Goryachev, D.N., Mizerov, M.N., and Portnoi, E.L., Some characteristics of diffraction lattices obtained by photoetching of semiconductor surface, J. Technical Physics (in Russian), 1974, vol. 44, p. 1331.]
Kautek, W., Sorg, N., and Paatsch, W., Laser-induced electrodeposition of transition metals on silicon, Electrochim. Acta, 1991, vol. 36, p. 1803.
Nánai, L., Hevesi, I., Bunkin, F.V., Luk’yanchuk, B.S., Brook, M.R., Shafeev, G.A., Jelski, D.A., Wu, Z.C., and George, T.F., Laser-induced metal deposition on semiconductors from liquid electrolytes, Appl. Phys. Lett., 1989, vol. 54, p. 736.
Sasano, J., Schmuki, P., Sakka, T., and Ogata, Y.H., Laser-assisted maskless Cu patterning on porous silicon, Electrochem. Solid-State Lett., 2004, vol. 7, p. G98.
Von Gutfeld, R.J., Acosta, R.E.,and Romankiw, L.T., Laser-enhanced plating and etching: Mechanisms and applications., IBM J. Res.Develop., 1982, vol. 26, p. 136.
Karlicek, R.F., Donnelly, V.M., and Collins, G.J., Laser-induced metal deposition on InP, J. Appl. Phys., 1982, vol. 53, p. 1084.
Scheck, C., Liu, Y.-K., Evans, P., and Schad, R., Photoinduced electrochemical deposition of Cu on p-type Si substrates, Phys. Rev., 2004, vol. B69, p. 035334(1–8).
Thietke, J. and Schultze, J.W., Mikroelektrodenprozesse im fokussiierten Laserstrahl. Elektrochemie und Elektronik. Dechema-Monographien, B. 117. VCH Verlagsgesellschaft, 1989, s. 175.
Gelchinski, M.H., Romankiw, L.T., Vigliotti, D.R., and von Gutfeld, R.J., Electrochemical and metallurgical aspects of laser-enhanced jet plating of gold, J. Electrochem. Soc., 1985, vol. 132, p. 2575.
Von Gutfeld, R.J., Gelchinski, M.H., Romankiw, L.T., and Vigliotti, D.R., Laser-enhanced jet plating: A method of high-speed maskless patterning, Appl. Phys. Lett., 1983, vol. 43, p. 876.
Zouari, I., Pierre, C., Lapicque, F., and Calvo, M., Maskless zinc electrodeposition assisted by pulsed laser beam, J. Appl. Electrochem., 1993, vol. 23, p. 863.
Гусев, В.Э., Козлова, Е.К., Портнягин, А.И. О роли термоградиентных явлений в лазерной электрохимии. Квантовая электроника. 1987. Т. 14. С. 323. [Gusev, V.E., Kozlova, E.K., and Port-nyagin, A.I., Role of thermal gradient effects in laser electrochemistry, Soviet J. Quantum Electronics, 1987, vol. 17, no. 2, p. 195.]
Zouari, I., Lapique, F., Calvo, M., and Cabrera, M., Zink electrodeposition assisted by pulsed YAG laser beam: Effect of hydrodynamic conditions, J. Electrochem. Soc., 1992, vol. 139, p. 2163.
Datta, M., Romankiw, L.T., Vigliotti, D.R., and von Gutfeld, R.J., Laser etching of metals in neutral salt solutions, Appl. Phys. Lett., 1987, vol. 51. P. 2040.
Hsiao, M.C. and Wan, C.C., The effect of pH on the localized etching process induced by laser irradiation, J. Electrochem. Soc., 1994, vol. 141, p. 943.
Дополнительные материалы отсутствуют.