Электрохимия, 2020, T. 56, № 6, стр. 520-527
Влияние содержания политетрафторэтилена в композиционных пористых углеродных материалах на их структурные и электрохимические характеристики на примере процесса восстановления кислорода до пероксида водорода
Г. А. Колягин a, *, В. Л. Корниенко a, **
a Институт химии и химической технологии СО РАН, Федеральный исследовательский центр
“Красноярский научный центр СО РАН”
660036 Красноярск, Академгородок, 50, стр. 24, Россия
* E-mail: kolyagin@icct.ru
** E-mail: kvl@icct.ru
Поступила в редакцию 05.06.2019
После доработки 06.09.2019
Принята к публикации 08.10.2019
Аннотация
Проведен анализ результатов исследований по влиянию политетрафторэтилена (ПТФЭ) на структурные и электрохимические характеристики пористых композитных материалов на основе печной сажи СН600, ацетиленовой сажи А437Э и мезоструктурированного углерода СМК-3. Углеродные материалы различаются методом изготовления, текстурой, способностью смачиваться водным электролитом и величиной площади удельной поверхности. Текстурные характеристики исходных углеродных материалов и их смесей с ПТФЭ (5–70 мас. %) были определены по низкотемпературной адсорбции азота. Композиционные материалы использовались в качестве электродной массы рабочих слоев газодиффузионных электродов (ГДЭ). Рассмотрено влияние ПТФЭ на объем и размер пор, величину площади поверхности углеродных материалов, объем пор занятых электролитом, емкость двойного слоя и параметры процесса электросинтеза Н2О2 из О2 в водном сернокислом растворе при плотности тока 150 мА/см2. Показано, что степень влияния концентрации ПТФЭ в композиционных материалах на их характеристики определяется свойствами углеродных материалов. Все перечисленные углеродные материалы можно использовать в ГДЭ для восстановления О2 до Н2О2. На ГДЭ с оптимальным соотношением ПТФЭ и углеродного материала в течение 5 ч получены растворы Н2О2 с концентрацией 1.9–2.4 М и выходом по току 65–87%.
ВВЕДЕНИЕ
Пористые композиционные материалы из смеси углеграфитовых материалов с фторсодержащими полимерными связующими – гидрофобизаторами широко используются при изготовлении пористых электродов для различных электрохимических устройств с водными электролитами. Например: для щелочных [1] и с протонопроводящей мембраной топливных элементов [2–4], электрохимических конденсаторов [5], электролизеров, связанных с процессом восстановлением кислорода до Н2О2 и для непрямого окисления органических и неорганических веществ [6–8], очистки воды от промышленных отходов с использованием электро-Фентон процесса [8, 9].
Фторсодержащее связующее применяется при изготовлении каталитического, макро- и микропористого слоев для оптимизации гидрофильно-гидрофобных свойств электрода, что создает высокоразвитую границу контакта электролита, катализатора и реагента, сдерживает затопление их водным электролитом, регулирует подвод в зону реакции исходных реагентов и отвод продуктов [1–4, 6–9]. Так же смеси фторполимеров и углеродных материалов применяются в качестве композиционных сорбентов [10].
В литературе практически не встречаются данные по текстурным характеристикам пористых композиционных материалов на основе политетрафторэтилена (ПТФЭ) и углеродных материалов и влиянию присутствия гидрофобизатора на их первоначальную структуру. Знание этих характеристик необходимо для создания высокоэффективных электрохимических устройств и для правильной интерпретации результатов, полученных при исследовании электродов из данных материалов. Необходимо детальное понимание того, как образуется микроструктура пористого электрода в зависимости от природы его компонентов. В этом плане следует отметить подробные исследования по влиянию полимера-иономера Нафион (Nafion) на пористую структуру электродов с углеродными носителями разных типов и обладающих различными величинами удельной поверхности [2, 3, 11, 12]. Нафион является высокомолекулярным соединением, это тот же ПТФЭ только с привитой гидрофильной цепью сульфокислоты, и поэтому эти полимеры обладают сходными механизмами взаимодействия с углеродными частицами. Иногда для улучшения характеристик газодиффузионных электродов (ГДЭ) используют совместно ПТФЭ и Нафион [8].
Цель работы – проанализировать влияние концентрации ПТФЭ в пористых композиционных материалах на основе различных углеродных материалов на площадь их поверхности, размер и объем пор, смачиваемость, емкость двойного электрического слоя, электропроводность и, в составе ГДЭ, на электрохимические характеристики процесса электросинтеза Н2О2 из О2. Для анализа частично использованы данные, опубликованные в [13–15].
ЭКСПЕРИМЕНТАЛЬНАЯ ЧАСТЬ
Для изготовления композитов использовали мезоструктурированный углерод СМК-3 [13], печную сажу СН600 (производство ООО “Омсктехуглерод”) [14] и ацетиленовую сажу А437Э (производство Новолипецкий металлургический комбинат) [15]. Эти материалы относятся к различным типам, отличаются текстурой, способностью смачиваться водным электролитом, величиной площади удельной поверхности, обладают высокой электропроводностью и рекомендуются производителями для использования в электрохимических устройствах. СМК-3 и СН 600 ранее не использовались в ГДЭ.
Электродную массу приготовляли совместной коагуляцией водной суспензии ПТФЭ (фторопласт-4Д) и суспензии углеродного материала [6, 16]. После коагуляции массу отфильтровывали, промывали водой, высушивали при 120°С до постоянного веса, размалывали на ножевой мельнице и просеивали через сито с размером ячейки 0.25 мм. Далее массу прогревали при температуре 300°С в течение 1 часа.
Газодиффузионные электроды изготовляли в виде плоских 2-слойных дисков, состоящих из газоподводящего и рабочего слоев диаметров 30 мм. Концентрация ПТФЭ в газоподводящем слое с ацетиленовой сажей А437Э была 50 мас. %. Электроды с пористостью 59–61 об. % формовали в пресс-форме с ограничителем хода пуансона по высоте толщиной 0.9 мм с никелевой сеткой – токоподводом в середине газоподводящего слоя [6]. Электроды с такой пористостью обычно используются для электросинтеза. Спекание электродов проводили в нагреваемой пресс-форме при 360°С в течение 10 мин. Применяемая технология подобна технологии изготовления композиционных материалов с использованием суспензии ПТФЭ [16, 17] и позволяет изготовлять электроды с заданной пористостью в диапазоне 15–70 об. % без употребления порообразователя.
Текстурные свойства исходных саж и их смесей с ПТФЭ определяли методом низкотемпературной адсорбции азота с использованием ASAP 2420 (Micromeritics, США) [13–15]. Образцы для определения структуры готовили по технологии изготовления однослойных электродов без никелевой сетки.
Эксперименты проводили в трехкамерной стеклянной ячейке-электролизере [6]. ГДЭ (катод) помещали между катодной и газовой камерами. Католит и анолит (1–2 М H2SO4) разделяли катионообменной мембраной МФ-4СК-100. Анод – платиновая пластина. Плотность тока рассчитывали на единицу видимой фронтальной поверхности электрода (5 см2). Потенциал электрода измеряли относительно насыщенного хлоридсеребряного электрода сравнения (ЭВЛ-1М1). Перед экспериментами электроды пропитывали в 0.5 М КОН при токе 0.1 А в течение 1 ч и определяли объем электролитных пор методом гидростатического взвешивания в воде [6]. Значение электролитной пористости вычисляли как соотношение объема пор, заполненных электролитом, к объему электрода. Для определения емкости двойного электрического слоя снимали циклические вольтамперные кривые в 3 М КОН [18]. Препаративный электросинтез Н2О2 проводили при 20–25°С в гальваностатическом режиме в водном растворе 0.375 М К2SO4 + 0.025 М H2SO4 (рН 3, 0.02 л) при габаритной плотности тока 150 мА/см2. Кислород марки “технический” подавали в электрод непрерывно, с его тыльной стороны через газовую камеру при атмосферном давлении с небольшим избытком, который отводили в атмосферу. Концентрацию Н2О2 определяли титрованием перманганатом калия.
Значительную роль в массообмене играет перемешивание электролита, которое влияет на скорости отвода Н2О2 от фронтальной поверхности электрода и подвода к электроду катионов водорода, которые участвуют в образовании Н2О2 в кислых растворах. В нашем случае перемешивание проводили барботированием через электролит воздуха со скоростью 45 мл/мин.
РЕЗУЛЬТАТЫ И ОБСУЖДЕНИЕ
В табл. 1 и рис. 1 представлены данные по площади поверхности исследованных углеродных материалов и их смесей с ПТФЭ.
Рис. 1.
Влияние концентрации ПТФЭ в композитах на площадь поверхности углеродных материалов, определенной по низкотемпературной адсорбции азота: 1 – СМК-3; 2 – СН600; 3 – А437Э. Величина площади поверхности отнесена к массе углеродного материала.
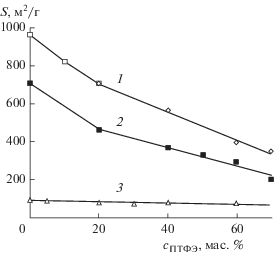
Как видно из данных табл. 1, во всех случаях происходит уменьшение площади поверхности с увеличением доли ПТФЭ. Наименьшее снижение поверхности наблюдается у сажи с низкой первоначальной удельной поверхностью – А437Э. У СМК-3 и СН600 снижение величины удельной поверхности примерно одинаковое.
Таблица 1.
Изменение площади поверхности углеродных материалов при смешивании с ПТФЭ в расчете на массу композиционного материала
Концентрация ПТФЭ, мас. % | Тип углеродного материала | ||
---|---|---|---|
поверхность по БЕТ, м2/г | |||
СМК-3 | СН600 | А437Э | |
0 | 963 | 705 | 94 |
5 | – | – | 84 |
10 | 738 | – | – |
20 | 565 | 367 | 64 |
30 | – | – | 53 |
40 | 339 | 220 | 45 |
50 | – | 164 | – |
60 | 156 | 116 | 30 |
70 | 105 | 60 | – |
Надо отметить, что в основном величина площади поверхности определяется поверхностью углеродного материала, так как площадь поверхности фторопласта составляет порядка 0.2 м2/г [18]. Если считать удельную поверхность относительно веса сажи в образцах, то уменьшение поверхности с увеличением концентрации ПТФЭ меньше, особенно у сажи А437Э. Например, при 20 мас. % ПТФЭ поверхность уменьшается у сажи А437Э только на 15%, у СМК-3 на 27% и у СН600 на 35%, тогда как при расчете на электродную массу, площадь поверхности уменьшается на 32, 41 и 48%, соответственно, от первоначального значения. Величина удельной поверхности относительно веса сажи позволяет определить истинное изменение площади поверхности, исключив “разбавление” углеродного материала массой ПТФЭ. Зависимость величины поверхности сажи А437Э от концентрации имеет линейный вид во всем диапазоне концентраций ПТФЭ. У СМК-3 и СН600 наблюдается резкое уменьшение поверхности при добавлении 20 мас. % ПТФЭ, а при дальнейшем увеличении концентрации фторопласта наклон графиков на рис. 1 остается постоянным.
Наклон прямых на рис. 1 повышается с увеличением величины поверхности исходного углеродного материала, что указывает на увеличение степени взаимодействия ПТФЭ с углеродным материалом при уменьшении размера его частиц.
На рис. 2, приведена зависимость объема пор, определенного по адсорбции азота, от концентрации ПТФЭ в композитах на основе СН600, СМК-3 и А437Э. Объем пор в образцах с СН600 и СМК-3 резко уменьшается, как и поверхность, при добавлении 20 мас. % ПТФЭ с 2.04 до 0.89 см3/г [15] и с 1.26 до 0.79 см3/г [13] соответственно, а при больших концентрациях ПТФЭ наклон зависимостей остается постоянным.
Рис. 2.
Влияние концентрации ПТФЭ на объем пор, определенный по низкотемпературной адсорбции азота, в композитах на основе углеродных материалов: 1 – А437Э, 2 – СН600, 3 – СМК-3.
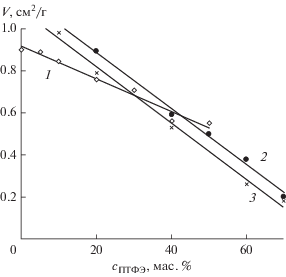
Зависимости объемов пор в композитах на основе СМК-3 и СН600 имеют одинаковый наклон. Значения объемов пор во всех образцах с одинаковой концентрацией фторопласта не сильно различаются, особенно при 30–45 мас. % ПТФЭ, хотя все три углеродных материала относятся к различным типам, имеют разную поверхность, как и композиты на их основе. Видимо, в данном случае определяющую роль играет технология приготовления композиционных материалов и метод измерения.
Метод низкотемпературной адсорбции азота позволяет определять поры диаметром меньше 0.3 мкм, поэтому на рис. 2 приведены результаты только по этим порам. При увеличении концентрации ПТФЭ уменьшается объем пор меньше 0.3 мкм и соответственно увеличивается объем пор большего диаметра, выходящих по значениям за пределы метода измерения. Это следует из того, что все электроды изготавливаются одной пористости и, следовательно, объем всех пор во всех образцах должен быть одинаков. Объем пор больше 0.3 мкм значительно увеличивается с ростом концентрации ПТФЭ. Например, у образцов на основе СМК-3 при увеличении содержания фторопласта с 10 до 70 мас. % доля пор больше 0.3 мкм увеличивается на 83%, на соответствующую величину уменьшается доля пор меньше 0.3 мкм [13]. Подобное явление наблюдается также в композитах из углеродных материалов с полимером Нафион. Например, в [11] пористость композита, определенная по адсорбции азота, содержащего углеродный материал, Нафион и платину, меньше пористости, вычисленной по геометрическим размерам образцов и плотностям их компонентов в 1.6 раза. Использование других методов измерения, например ртутной порозиметрии или метода эталонной контактной порометрии [2, 3], позволяющих измерять объем более крупных пор, возможно, дало бы больше информации об этих порах.
Так как объем пор с диаметром больше 0.3 мкм растет с увеличением содержания ПТФЭ, то вероятнее всего, эти поры образованы в основном частицами ПТФЭ, но не исключено также увеличение закрытой пористости и образование бутылкообразных пор, что занижает объем пор, определенных по адсорбции азота [11].
Доля микропор у исследованных углеродных материалов очень мала и находится в диапазоне от 0.2 (А437Э) до 7.5% (СМК-3) от объема всех пор, и уменьшается с прибавлением ПТФЭ. ПТФЭ блокирует все поры, но в большей степени устья микро- и мезопор. Так, например, добавление к саже СН600 60 мас. % ПТФЭ увеличивает соотношение объема всех пор к объему микропор с 16 до 380 раз [14]. У СМК-3, прибавление 20 мас. % ПТФЭ увеличивает это соотношение с 13 до 38 раз, и при дальнейшем увеличении количества полимера микропоры исчезают [13]. У ацетиленовой сажи микропоры практически исчезают при незначительном (5–10 мас. %) добавлении ПТФЭ. Размер частиц фторопласта 50–500 нм [10, 17], а в газодиффузионных электродах агломераты ПТФЭ могут достигать в диаметре 0.1–0.3 мкм и больше [3]. Поэтому частицы ПТФЭ могут проникать только в макропоры.
Интересно сравнить наши результаты с данными, полученными при исследовании композитов из углеродных материалов и иономера Нафион, который широко используется при изготовлении пористых электродов. Нафион, как и ПТФЭ, практически не адсорбирует азот [11] и также блокирует поверхность углеродных материалов [2, 3, 11, 12, 19]. Так, при добавлении к печной саже Ketjen Black, содержащей патину, 10 мас. % иономера Нафион, ее поверхность резко снижается с 639 до 207 м2/г, т.е. на 68%, в расчете на вес сажи и далее, уже в меньшей степени, поверхность линейно уменьшается при добавлении иономера до 50 мас. % [12]. Примерно в тех же пропорциях уменьшается объем пор, определенный по адсорбции азота, с 0.86 до 0.08 м3/г при добавлении 50 мас. % иономера, т.е. на 91%. В нашем случае при добавлении к печной саже СН600 20 мас. % ПТФЭ происходит уменьшение поверхности на 35% (рис. 1), а объем пор уменьшается на 50% при добавлении 50 мас. % ПТФЭ. Другими словами, Нафион может блокировать поверхность углеродных материалов значительно сильнее, чем ПТФЭ. Необходимая для эффективной работы электродов концентрация Нафиона, как и ПТФЭ, в каталитическом слое зависит от структуры, объема пор и величины поверхности углеродного материала [2, 3, 12].
В табл. 2 представлены примеры электродных масс в порядке увеличения площади поверхности, определенной по адсорбции азота, их характеристики и результаты электросинтеза Н2О2, полученные с их использованием, в растворе с pH 3 при плотности тока 150 мА/см2 за 5 ч электролиза. Емкость приведена в расчете на габаритную поверхность электрода.
Таблица 2.
Характеристики электродных масс и результаты электросинтеза Н2О2 на электродах с их применением. Время электролиза 5 часов
№ п/п | Углеродный материал | cПТФЭ, мас. % | Sm, м2/г | Sg, м2/см2 | Электролит-ная пористость, об. % | Емкость, Ф/см2 | Е, В | ${{c}_{{{{{\text{H}}}_{{\text{2}}}}{{{\text{O}}}_{{\text{2}}}}}}},$ М | Выход Н2О2 по току, % |
---|---|---|---|---|---|---|---|---|---|
1 | А 437Э | 50 | 25 | 0.67 | 7 | 0.0041 | 0.96 | 1.92 | 65 |
2 | А 437Э | 5 | 84 | 2.26 | 19 | 0.11 | 0.48 | 2.19 | 76 |
3 | СМК-3 | 70 | 105 | 2.82 | 12 | 0.13 | 0.55 | 2.41 | 87 |
4 | СН600* | 60 | 116 | 3.12 | 13 | 0.063 | –* | 1.14 | 62 |
Прмечание. Sm, Sg – Площадь поверхности на единицу веса электродной массы (табл. 1) и на габаритную поверхность. Е – потенциал в конце электролиза. * Плотность тока 100 мА/см2.
Большую роль в функционировании газодиффузионных электродов играет их смачиваемость водным электролитом и электропроводность. Как видно из табл. 2, объем электролитных пор не зависит от удельной поверхности электродной массы. Смачиваемость, видимо, определяется поверхностными свойствами углеродных материалов и количеством гидрофильных поверхностных групп. Наименее смачиваемыми являются массы с ацетиленовой сажей. Наибольшей смачиваемостью обладают массы, содержащие углеродные материалы с большой поверхностью: СН600 и СМК-3. Эти массы должны содержать большое количество ПТФЭ, чтобы обеспечить оптимальный для процесса электросинтеза объем газовых и электролитных пор.
На рис. 3 приведены зависимости электролитной пористости электродов от содержания ПТФЭ для двух видов саж, отличающихся своей смачиваемостью водой. Это – печная, хорошо смачивающаяся сажа СН600 и плохо смачиваемая ацетиленовая сажа А437Э. На электродах из ацетиленовой сажи при изменении концентрации ПТФЭ от 5 до 10% наблюдается резкое падение электролитной пористости. На электродах из печной СН600 с увеличением концентрации ПТФЭ электролитная пористость медленно линейно уменьшается без резких перепадов.
Рис. 3.
Влияние концентрации ПТФЭ на электролитную пористость (1,2) и удельное электрическое сопротивление (3) электродной массы. Сажа: 1, 3 – А437Э; 2 – СН600.
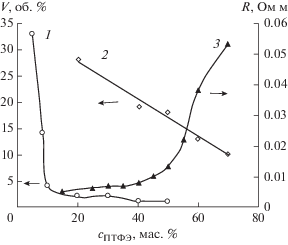
Приведенная на рис. 3 зависимость электрического сопротивления от концентрации ПТФЭ имеет классический вид с порогом перколяции при содержании ПТФЭ 45–50 мас. %. При большей концентрации сопротивление резко увеличивается. С уменьшением содержания ПТФЭ наступает область насыщения, и сопротивление имеет почти постоянное значение. Сходные значения по электропроводности пористых композитов на основе сажи и ПТФЭ получены в [16].
Емкость двойного слоя является важной характеристикой пористых электродов, так как она пропорциональна смоченной электролитом поверхности. Зная емкость, можно оценить реальную площадь поверхности, участвующей в электрохимическом процессе, и проследить ее изменение при модификации электродов. В [5] показано, что большое количество марок саж с поверхностью 28–1690 м2/г имеют примерно одинаковую удельную емкость, определенную в водных растворах одним и тем же методом и в одинаковых условиях. Иными словами, по величине емкости, определенной при одинаковых условиях, можно оценить относительное изменение площади смоченной поверхности в электродах из различных углеродных материалов.
Как видно из данных табл. 2 и рис. 4, наблюдается общая тенденция уменьшения емкости электродов с увеличением концентрации ПТФЭ, так как уменьшается удельная поверхность, следовательно, снижается реальная площадь поверхности, на которой может протекать электрохимический процесс. Емкость зависит не только от величины поверхности, но и от ее способности смачиваться водным электролитом, а также от количества пор, образованных совместно частицами сажи и ПТФЭ. Чем больше часть поверхности поры будет образована ПТФЭ, тем больше вероятность, что поверхность этой поры не будет смочена водным электролитом. Эта поверхность будет доступна для адсорбции азота, но не сможет участвовать в электрохимическом процессе. При увеличении содержания ПТФЭ величина емкости на электродах из СН600 уменьшается быстрее, чем происходит уменьшение поверхности. У электродов с сажей А437Э поверхность почти не меняется, а емкость резко падает уже при добавлении 10 мас. % ПТФЭ. Зависимость емкости от концентрации ПТФЭ в электродах из А437Э имеет тот же вид, как и электролитная пористость (рис. 3).
Рис. 4.
Влияние концентрации ПТФЭ в электродной массе на величину емкости двойного слоя отнесенной к единице габаритной поверхности электродов на основе саж: 1 – А437Э, 2 – СН600.
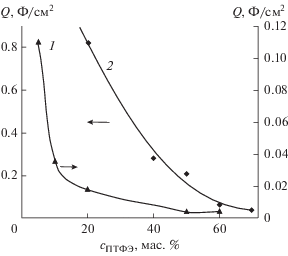
Электрод из СН600 с 60 мас. % ПТФЭ обладает самой большой поверхностью, но его емкость меньше, чем у электродов из СМК-3 и А437Э с 5 мас. % ПТФЭ. Площадь поверхности и электролитная пористость электрода из СН600 сравнимы с подобным характеристикам электрода из СМК-3, но их емкости различаются в 2 раза. Иными словами, поверхность, которая может быть смочена электролитом, у печной сажи более склонна к блокировке ПТФЭ, чем поверхность СМК-3.
Из данных, представленных в табл. 2, видно, что электросинтез Н2О2 можно проводить на всех исследованных углеграфитовых материалах с высокой эффективностью. Скорость генерации Н2О2 в первый час относительно площади габаритной поверхности составляет 74–86 мг/(ч см2) при выходе по току Н2О2 78–90% [13–15]. Для сравнения, в обзоре [8] приводится пример электросинтеза Н2О2 в ГДЭ после 0.5 ч с выходом по току 80%, при плотности тока 0.1 А/см2 со скоростью 50 мг/(ч см2), что считается большой скоростью синтеза. Обычно электросинтез Н2О2 проходит с меньшими скоростями [7, 8].
Величина поверхности гидрофильных пор определяет не только истинную локальную плотность тока, но и общую скорость гетерогенного разложения на ней синтезированного пероксида водорода. Поэтому, электролитная пористость, в нашем случае, должна быть не более 20 об. %. С увеличением удельной площади поверхности углеродного материала необходимо увеличивать концентрацию ПТФЭ в рабочей массе электрода. Для А437Э достаточна концентрация ПТФЭ 5 мас. %, а для СН600 и СМК-3 не менее 70 мас. %. С другой стороны, при невысоком значении электролитной пористости (А437Э, 50 мас. % ПТФЭ), происходит уменьшение эффективности процесса электросинтеза Н2О2 и резкое увеличение поляризации электрода. Исходя из изменений в значениях емкостей электродов из сажи А437Э, можно предположить, что при увеличении концентрации ПТФЭ в массе из этой сажи с 5 до 50 мас. % (табл. 2) площадь смоченной поверхности уменьшается в 26 раз. Уменьшение смоченной поверхности приводит к увеличению поляризации, локальной плотности тока и способствует дальнейшему восстановлению Н2О2 до воды.
Разница в значениях емкостей исследованных электродов достигает 32 раз. Можно предположить, что усредненная локальная плотность тока изменяется в этих же пределах, так как габаритная плотность тока одинакова, исключая электрод из сажи СН600.
ВЫВОДЫ
Степень влияния ПТФЭ на структурные и электрохимические характеристики пористых композиционных материалов на основе печной сажи СН600, ацетиленовой сажи А437Э и мезоструктурированного углерода СМК-3 зависит от свойств используемого углеродного материала. С увеличением концентрации ПТФЭ в композитах из всех углеродных материалов происходит уменьшение площади поверхности и объема пор, определенных по низкотемпературной адсорбции азота. Степень блокировки пор повышается с ростом удельной поверхности углеродного материала. Наиболее резкое уменьшение происходит при добавлении примерно 20 мас. % ПТФЭ. При большем содержании ПТФЭ объем пор и поверхность в композитах уменьшаются линейно. С увеличением концентрации ПТФЭ резко уменьшается доля микро и мезопор и увеличивается доля пор больше 0.3 мкм.
С увеличением концентрации ПТФЭ уменьшается объем электролитных пор, электропроводность и емкость электродов. Уменьшение емкости не коррелируется с уменьшением поверхности, так как значение емкости определяется не только площадью поверхности углеродного материала, но и смачиваемостью пор. Поверхность углеродного материала в порах, образованных с частицами ПТФЭ, доступна для адсорбции азота, но возможно не будет смочена электролитом и, следовательно, не будет участвовать в электрохимическом процессе. Вероятность появления таких пор повышается с увеличением содержания ПТФЭ, особенно в электродах из ацетиленовой сажи, которая обладает большей гидрофобностью по сравнению с СН600 и СМК-3.
Для эффективного протекания процесса восстановления О2 до Н2О2, оптимально необходимое соотношение в ГДЭ ПТФЭ и углеродного материала зависит от структуры, смачиваемости и величины поверхности последнего. С ростом удельной поверхности углеродного материала, для увеличения эффективности процесса электросинтеза Н2О2 необходимо повышать концентрацию ПТФЭ в электродной массе.
В ГДЭ с использованием всех исследованных углеродных материалов, с различной величиной площади поверхности, процесс 2-электронного восстановления О2 до Н2О2 может протекать с высокой эффективностью. При плотности тока 0.15 А/см2 за 5 ч электролиза получены растворы Н2О2 с концентрацией 1.9–2.4 М с выходом по току 65–87%. Электроды с содержанием ПТФЭ 5–70 мас. % имеют площадь поверхности 25–116 м2/г, емкость двойного слоя, относительно габаритной поверхности, 0.0041–0.13 Ф/см2, электролитную пористость 7–13 об. %.
Список литературы
Bidault, F., Brett, D.J.L., Middletonc, P.H., and Brandon, N.P., Review of gas diffusion cathodes for alkaline fuel cells, J. Power Sources, 2009, vol. 187, p. 39.
Вольфкович, Ю.М., Сосенкин, В.Е., Никольская, Н.Ф. Постадийное исследование пористой структуры каталитических слоев электродов топливного элемента с протонопроводящей мембраной. Электрохимия. 2010. Т. 46. С. 352. [Volfkovich, Yu.M., Sosenkin, V.E., and Nikol’skaya N. F., Porous Structure of the Catalyst Layers of Electrodes in a Proton-Exchange Membrane Fuel Cell: A Stage-by-Stage Study, Russ. J. Electrochem., 2010, vol. 46, p. 336.]
Volfkovich, Yu.M., Sosenkin, V.E., and Bagotsky V.S., Structural and wetting properties of fuel cell components, J. Power Sources, 2010, vol. 195, p. 5429.
Chi, B., Hou, S., Liu, G., Deng, Y., Zeng, J., Song, H., Liao, S., and Ren, J., Tuning hydrophobic-hydrophilic balance of cathode catalyst layer to improve cell performance of proton exchange membrane fuel cell (PEMFC) by mixing polytetrafluoroethylene (PTFE), Electrochim. Acta, 2018, vol. 277, p. 110.
Beck, F., Dolata, M., Grivei, E., and Probst, N., Electrochemical supercapacitors based on industrial carbon blacks in aqueous H2SO4, J. Appl. Electrochem., 2001, vol. 31, p. 845.
Корниенко, В.Л., Колягин, Г.А., Салтыков, Ю.В. Электросинтез в гидрофобизированных электродах, отв. ред. д.т.н. Томилов А.П., Новосибирск: Изд-во СО РАН, 2011. 170 с. [Kornienko, V.L., Kolyagin, G.A., and Saltykov, Yu.V., Electrosynthesis in Hydrophobized Electrodes (in Russian), Tomilov A.P., Ed., Novosibirsk: Sib. Otd. Ross. Akad. Nauk, 2011. 170 p.] (http://www.rfbr.ru/rffi/ru/books/o_1781580#1)
Zhou, W., Meng, X., Gao, and Alshawabkeh, A.N., Hydrogen peroxide generation from O2 electroreduction for environmental remediation: A state-of-the-art review, Chemosphere, 2019, vol. 225, p. 588.
Casado, J., Towards industrial implementation of Electro-Fenton and derived technologies for wastewater treatment: A review, J. Environmental Chem. Engineering, 2019, vol. 7, p. 102823.
Pliegoa, G., Zazoa, J. A., Garcia-Muñoza, P., Munoza, M., Casasa, J.A., and Rodriguezn J.J., Trends in the intensification of the Fenton process for wastewater treatment—An overview, Critical Reviews in Environmental Science and Technology, 2015, vol. 45, p. 2611.
Xia-Chun, Lu and Xiaoqun, Wu, Flue gas purification process using a sorbent polymer composite material, Patent 0207923 (US). 2007.
Suzuki, T., Tanaka, H., Hayase, M., Tsushima, S., and Hirai, S., Investigation of porous structure formation of catalyst layers for proton exchange membrane fuel cells and their effect on cell performance, Intern. J. Hydrogen Energy, 2016, vol. 41, p. 20326.
Soboleva, T., Zhao, X., Malek, K., Xie, Z., Navessin, T., and Holdcroft, S., On the Micro-, Meso-, and Macroporous Structures of Polymer Electrolyte Membrane Fuel Cell Catalyst Layers, ACS Appl. Materials and Interfaces, 2010, vol. 2, p. 375.
Корниенко, В.Л., Колягин, Г.А., Корниенко, Г.В., Парфенов В.А., Пономаренко И.В. Электросинтез Н2О2 из О2 в газодиффузионном электроде на основе мезоструктурированного углерода СМК-3. Электрохимия. 2018. Т. 54. С. 299. [Kornienko V.L., Kolyagin G.A., Kornienko, G.V., Parfenov, V.A., and Ponomarenko, I.V., Electrosynthesis of Н2О2 from О2 in a Gas-Diffusion Electrode Based on Mesostructured Carbon CMK-3, Russ. J. Electrochem., 2018, vol. 54, p. 258.]
Корниенко, В.Л., Колягин, Г.А., Корниенко, Г.В., Парфенов В.А., Петин, А.А. Электросинтез Н2О2 из О2 в газодиффузионных электродах на основе сажи СН600, Электрохимия. 2017. Т. 53. С. 1487. [Kornienko V.L., Kolyagin G.A., Kornienko, G.V., Parfenov, V.A., and Petin, A.A., Electrosynthesis of H2O2 from O2 in Gas Diffusion Electrodes Based on Black CH600, Russ. J. Electrochemistry, 2017, vol. 53, p. 1307.]
Корниенко, В.Л., Колягин, Г.А., Корниенко, Г.В., Парфенов В.А., Ашихин, А.С. Исследование влияния текстуры газодиффузионных электродов на основе ацетиленовой сажи А 437-Э на эффективность электросинтеза Н2О2 из О2, Химия в интересах устойчивого развития. 2017. № 5. С. 519. [Kor-nienko V.L., Kolyagin G.A., Kornienko, G.V., Parfenov, V.A., and Ashihin, A.S., Study of Texture Effect of Gas Diffusion Electrodes Based on A 437-E Acetylene Black on the Efficiency of Electrosynthesis of H2O2 from O2, Chemistry for Sustainable Development, 2017, № 5, С. 519.]
Будевски, Б.Е., Илиев, И.Д., Каищева, А.Р., Гамбурзев, С.С., Ваканова, Е.Б. Способ получения порошкообразного гидрофобизированного материала. А.с. 500557 (СССР) 1976. [Budevski, B.E., Iliev, I.D., Kaisheva, A.R., Gamburzev, S.S., and Vakanova, E.B., The method of obtaining powdered gidrofobizirovannogo material, USSR Inventors Certificate 500557, 1976.] (Pat. 4031033 (US), 1977).
Ганз, С.Н., Пархоменко, В.Д. Антифрикционные химически стойкие материалы в машиностроении, М.: Машиностроение, 1965. 148 с. [Ganz, S.N., and Parkhomenko, V.D., Antifriction chemically resistant materials in mechanical engineering, (in Russian), Moscow: Mashinostroenie, 1965. 148 p.]
Колягин, Г.А., Корниенко, В.Л., Пропитка водным раствором электродов из ацетиленовой сажи со связующим политетрафторэтиленом и оценка удельной емкости их двойного слоя. Электрохимия. 2018. Т. 54. С. 111. [Kolyagin, G.A. and Kornienko, V.L., Impregnation of Acetylene Black Electrodes with a Polytetrafluoroethylene Binder with an Aqueous Solution and Evaluation of Its Specific Double Layer Capacity, Russ. J. Electrochem., 2017, vol. 53, p. 96.]
Gode, P., Jaouen, F., Lindbergh, G., Lundblad, A., and Sundholm, G., Influence of the composition on the structure and electrochemical characteristics of the PEFC cathode, Electrochim. Acta, 2003, vol. 48, p. 4175.
Дополнительные материалы отсутствуют.