Электрохимия, 2020, T. 56, № 9, стр. 820-830
Исследование влияния параметров импульсного электролиза на процесс электроосаждения сплава медь–олово из сульфатного электролита
А. А. Касач a, *, Д. С. Харитонов a, b, **, С. Л. Радченко a, И. М. Жарский a, И. И. Курило a
a Белорусский государственный технологический университет
220006 Минск, ул. Свердлова, 13а, Беларусь
b Jerzy Haber Institute of Catalysis and Surface Chemistry, Polish Academy of Sciences
30-239 Kraków, ul. Niezapominajek, 8, Poland
* E-mail: kasach2018@bk.ru
** E-mail: nckharyt@cyf-kr.edu.pl
Поступила в редакцию 16.09.2019
После доработки 29.12.2019
Принята к публикации 06.03.2020
Аннотация
Изучено влияние импульсного электролиза на процесс электроосаждения сплава Cu–Sn из сернокислого электролита. Показано, что соосаждение меди и олова наблюдается лишь при потенциалах, обеспечивающих разряд ионов меди(II) при диффузионном контроле. Рассчитано переходное время процесса электровосстановления ионов меди(II), а также концентрации ионов Cu2+ в прикатодной области в момент паузы. Показано, что сокращение длительности паузы приводит к осаждению сплава при более низких значениях плотностей тока. Установлено, что использование импульсного электролиза позволяет существенно (в 3 раза) увеличить диапазон катодных плотностей тока для получения качественных покрытий желтой бронзой. Установлено влияние продолжительности и амплитуды импульса на качественный и количественный составы формируемого сплава.
Сплавы Cu–Sn, содержащие до 20 мас. % олова (желтые бронзы), широко применяются в качестве индивидуальных защитно-декоративных гальванических покрытий, а также являются дешевой альтернативой никелю и серебру [1–5]. В настоящее время для электрохимического осаждения медно-оловянных сплавов используются пирофосфатные [6–8], цианистые [9], оксалатные [10, 11], метансульфоновые [12–16] и сернокислые [5, 17–21] электролиты. Последние являются наиболее простыми, доступными и экологически безопасными, но имеют ряд недостатков: более высокую разность потенциалов меди и олова по сравнению с комплексными электролитами, низкую рассеивающую способность [22], существенную зависимость качества покрытия от природы вводимых в электролит специальных добавок, сложности прямого нанесения покрытия на стальные изделия, а также узкий диапазон катодных плотностей тока, обеспечивающих формирование качественных осадков.
Описанные в литературе исследования электроосаждения сплава медь–олово из сернокислого электролита в стационарных условиях в основном сосредоточены на изучении влияния на катодный процесс и качество получаемых покрытий ионного состава электролита [5, 17], величин плотности тока [5] и продолжительности электролиза [3]. Однако наиболее перспективным направлением для получения гальванических покрытий с улучшенными функциональными и декоративными свойствами, а также для интенсификации катодных процессов является использование нестационарных режимов электролиза [23–27]. Положительное влияние нестационарного электролиза (НЭ) на кроющую и рассеивающую способность электролитов приводит к более равномерному распределению покрытий на изделиях сложной конфигурации [28, 29].
В ряде работ [32–34] было изучено влияние параметров НЭ на электроосаждение сплавов Cu‒Sn из цианистых, пирофосфатных и метансуль-фоновых электролитов, однако аналогичные исследования для сернокислых электролитов в литературе не представлены.
Целью нашей работы является изучение влияния параметров импульсного электролиза (ИЭ) на особенности электроосаждения сплава Cu–Sn из сернокислого электролита, микроструктуру, количественный и качественный составы формируемых покрытий.
ЭКСПЕРИМЕНТАЛЬНАЯ ЧАСТЬ
Электроосаждение сплава Cu–Sn проводили из электролита, состав которого представлен в табл. 1.
Таблица 1.
Состав сернокислого электролита осаждения сплава Cu–Sn
Компонент | Содержание в электролите, моль/дм3 | Назначение компонента |
---|---|---|
CuSO4 · 5H2O | 0.16 | Источник Cu2+ |
SnSO4 | 0.19 | Источник Sn2+ |
H2SO4 | 1 | Фоновый электролит |
Тиомочевина | 6.6 × 10–5 | Блескообразующая добавка |
N-октилпиридиний бромид | 1.8 × 10–5 | Выравнивающая добавка |
Электролиз проводили при плотностях тока от 1.25 до 2.75 А/дм2 при температуре 25°С. В качестве анодов использовали медь марки М0. Катодами служили пластины из фольгированного медью диэлектрика. Электроды предварительно обезжиривали в растворе следующего состава, г/дм3: Na2CO3 – 30, Na3PO4 ⋅ 12H2O – 30; затем подвергали травлению в течение 15 с в растворе, содержащем, г/дм3: HNO3 – 400, H2SO4 – 400, NaCl – 10.
Параметры используемых импульсных режимов электролиза приведены в табл. 2.
Таблица 2.
Режимы импульсного электролиза
Режим | Время импульса, мс | Время паузы, мс | Частота импульсов, Гц | Скважность импульсов |
---|---|---|---|---|
Режим 1 | 10 | 10 | 50 | 2 |
100 | 100 | 5 | ||
1000 | 1000 | 0.5 | ||
Режим 2 | 10 | 5 | 66.7 | 1.5 |
100 | 50 | 6.67 | ||
1000 | 500 | 0.667 | ||
Режим 3 | 10 | 2.5 | 80 | 1.25 |
100 | 25 | 8 | ||
1000 | 250 | 0.8 |
Для оценки влияния параметров импульсного электролиза на кинетические особенности электрохимического осаждения сплава проводили поляризационные исследования с помощью потенциостата-гальваностата AUTOLAB PGSTAT302N (Metrohm, Нидерладны), контролируемого программным обеспечением NOVA 2.1, в стандартной трехэлектродной электрохимической ячейке при линейной скорости развертки потенциала 1 мВ/с. Электродом сравнения служил насыщенный хлоридсеребряный электрод. Все значения электродных потенциалов пересчитаны в шкалу стандартного водородного электрода. При снятии поляризационных кривых, характеризующих разряд индивидуальных компонентов сплава, использовали электролиты аналогичного состава, содержащие соль только одного из осаждаемых металлов (меди или олова). Переходное время процесса разряда ионов меди определяли графическим способом.
Состав и морфологию формируемых покрытий изучали с помощью сканирующего электронного микроскопа JSM-5610 LV, оснащенного системой химического анализа EDX JED-2201 JEOL.
РЕЗУЛЬТАТЫ И ИХ ОБСУЖДЕНИЕ
Для изучения влияния параметров импульсного электролиза на особенности электроосаждения сплава медь–олово в сернокислом электролите были проведены поляризационные исследования медного электрода. На рис. 1 представлены катодные поляризационные кривые медного электрода, полученные в электролитах, содержащих только соль Cu(II) (рис. 1, кривая 1), только соль Sn(II) (рис. 1, кривая 2), а также в электролите, содержащем соли двух этих металлов (рис. 1, кривая 3). Как известно, скорость осаждения каждого компонента сплава в электрохимической системе описывается парциальной вольт-амперной зависимостью, а катодная поляризационная кривая электрохимического процесса является суммой парциальных зависимостей разряда ионов отдельных компонентов сплава. Из полученных вольт-амперных зависимостей следует, что из используемого электролита разряд ионов меди(II) (рис. 1, кривая 1) происходит при потенциалах положительнее, чем осаждение олова (рис. 1, кривая 2), и контролируется стадией массопереноса [17, 21, 22]. Из анализа поляризационных кривых следует, что при потенциалах, отрицательнее 0.00 В ионы меди(II) разряжаются на предельном диффузионном токе (id = 0.0145 А/см2), а осаждение олова начинает протекать при потенциалах, отрицательнее –0.2 В. Вкладом реакции выделения водорода в суммарную поляризационную кривую в этой области потенциалов можно пренебречь, так как известно, что выделение водорода в сернокислых электролитах на меди и олове происходит при достаточно больших перенапряжениях [17–21].
Рис. 1.
Поляризационные кривые медного электрода, полученные в электролите меднения (кривая 1), оловянирования (кривая 2) и в электролите для получения сплава Cu–Sn (кривая 3).
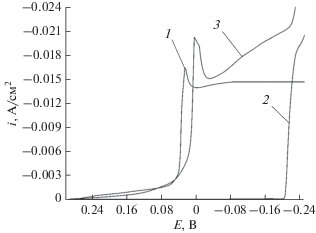
При совместном содержании в растворе ионов меди(II) и олова(II) на поляризационной кривой (рис. 1, кривая 3) в области потенциалов, соответствующих предельному диффузионному току разряда Cu(II), наблюдается монотонное возрастание тока, что можно объяснить протеканием процесса подпотенциального осаждения олова. Подобный ход поляризационных кривых наблюдали и другие исследователи [4, 17, 30, 31], показавшие, что процесс подпотенциального осаждения олова из сернокислых электролитов и ионных жидкостей наблюдается лишь в том случае, когда ионы меди(II) разряжаются на предельном диффузионном токе. При этом необходимо отметить, что в условиях подпотенциального осаждения рост металлической фазы возможен только по двухмерному механизму с образованием твердых растворов с металлом подложки [21, 31, 36]. При потенциалах, отрицательнее –0.21 В (рис. 1, кривая 3), изменение хода поляризационной кривой обусловлено разрядом ионов олова(II) из акватированных ионов.
Таким образом, анализ вольт-амперной зависимости медного электрода, полученной в сернокислом электролите, позволяет сделать вывод, что процесс подпотенциального осаждения олова протекает в том случае, когда ионы меди разряжаются на предельном диффузионном токе, при этом, согласно уравнению диффузионной кинетики, концентрация разряжающихся ионов в приповерхностном слое стремиться к нулю. Известно, что при токовых нагрузках, превосходящих значения предельного диффузионного тока, нулевая концентрация разряжающихся ионов у поверхности электрода устанавливается за определенное время, так называемое переходное время, которое описывается уравнением Санда [35]:
где i – плотность тока (А/дм2), t – переходное время (с), z – количество электронов, F – постоянная Фарадея (Кл/моль), D – коэффициент диффузии (дм2/с), c0 – объемная концентрация ионов меди(II) (моль/дм3).Для исследуемого электролита при 298 K коэффициент диффузии, рассчитанный по уравнению Санда, составил 2.8 × 10–8 дм2/с, что согласуется с литературными данными (5.8 × 10–8 дм2/с) [37].
Для изучения влияния параметров ИЭ на переходное время процесса электровосстановления ионов меди(II) были получены хронопотенциограммы медного электрода при различных токовых нагрузках и продолжительности паузы. Хронопотенциограммы медного электрода, полученные в импульсном режиме при различных плотностях тока из сернокислого электролита, не содержащего ионов олова, представлены на рис. 2.
Рис. 2.
Хронопотенциограммы медного электрода, полученные в импульсном режиме при катодных плотностях тока 1.50 (а), 1.75 (б) и 2.00 (в) А/дм2 при длительности паузы, с: 1 – 1; 2 – 0.50; 3 – 0.25; 4 – 0.10; 5 – 0.05; 6 – 0.025; 7 – 0.01. Состав электролита, моль/дм3: CuSO4 ⋅ 5H2O – 0.16; H2SO4 – 1.00; тиомочевина – 6.6 × 10–5; N-октилпиридиний бромид – 1.8 × 10–5.
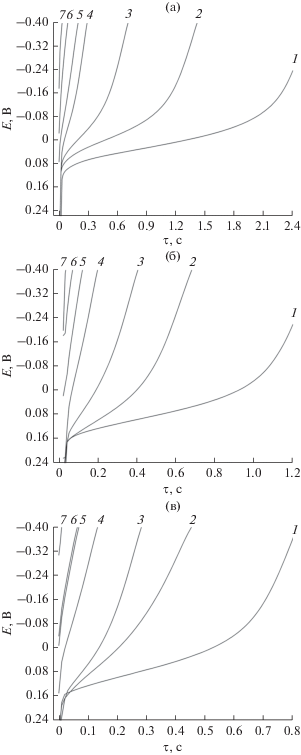
Анализ полученных зависимостей показал, что площадка потенциала, наблюдаемая при исследуемых плотностях тока (рис. 2), обусловлена восстановлением ионов меди(II), что согласуется с результатами линейной вольтамперометрии. Последующий скачок электродного потенциала обусловлен катодным восстановлением водорода, что свидетельствует о том, что содержание ионов меди в прикатодной области стремится к нулю. Значения переходного времени и концентрации ионов меди, устанавливающиеся в приповерхностном слое за время паузы, представлены в табл. 3.
Таблица 3.
Значения переходного времени процесса электровосстановления меди и концентрации Cu2+ в прикатодной области в зависимости от параметров ИЭ
Режим | Время паузы, мс | Переходное время, мс | Поверхностная концентрация Cu2+, моль/дм3 | ||||
---|---|---|---|---|---|---|---|
плотность тока, А/дм2 | |||||||
1.5 | 1.75 | 2.00 | 1.5 | 1.75 | 2.00 | ||
Режим 1 | 1000 | 2200 | 1020 | 650 | 0.078 | 0.062 | 0.056 |
Режим 2 | 500 | 1125 | 480 | 290 | 0.056 | 0.042 | 0.038 |
Режим 3 | 250 | 541 | 244 | 170 | 0.039 | 0.030 | 0.029 |
Режим 1 | 100 | 160 | – | – | 0.021 | – | – |
Из данных табл. 3 и рис. 2 следует, что уменьшение времени паузы, а также увеличение значений плотности тока импульса способствуют уменьшению переходного времени процесса электровосстановления ионов меди(II), что обусловлено снижением концентрации катионов металла в приэлектродном слое, устанавливающейся в момент паузы. По мере сокращения времени паузы от 1000 до 10 мс, а также при увеличении токовой нагрузки от 1.50 до 2.00 А/дм2 в прикатодном слое наблюдается снижение концентрации ионов меди по сравнению со значениями, которые устанавливаются в момент паузы. Сокращение длительности паузы при одном и том же значении плотности тока способствует снижению концентрации ионов меди в приэлектродном слое, так как убыль ионов меди в прикатодном диффузионном слое не компенсируется за короткий промежуток времени паузы.
Методом EDX-анализа было изучено влияние режимов ИЭ, а также амплитуды и частоты катодного импульса на качественный и количественный состав формируемых покрытий (табл. 4). Показано, что в режимах 1 и 2 при катодной плотности тока 1.50 А/дм2 независимо от используемой частоты осаждаются покрытия, состоящие только из меди. Осаждение чистой меди в данных условиях обусловлено тем, что длительность катодного импульса тока меньше переходного времени, при котором концентрация ионов меди в приэлектродном слое достигает нуля. Следовательно, при данной продолжительности импульса подпотенциальное осаждение олова невозможно. Использование режима 3 при катодной плотности тока 1.5 А/дм2 позволяет получать покрытия, содержащие от 10.79 до 11.91 мас. % олова, так как переходное время процесса разряда Сu2+ (541 мс) меньше продолжительности катодного импульса (1000 и 100 мс, соответственно). Как было показано выше, увеличение плотности тока способствует более быстрому расходованию ионов меди в приэлектродном слое и, следовательно, сокращению продолжительности переходного времени. Это, в свою очередь, приводит к формированию сплава с более высоким содержанием олова.
Таблица 4.
Зависимость составов формируемых покрытий от параметров ИЭ
Режим | Плотность тока, А/дм2 | Частота импульса, Гц | Содержание Cu, мас. % | Содержание Sn, мас. % |
---|---|---|---|---|
Режим 1 | 1.50 | 50 | 100.00 | – |
5 | 100.00 | – | ||
0.5 | 100.00 | – | ||
1.75 | 50 | 100.00 | – | |
5 | 100.00 | – | ||
0.5 | 95.00 | 5.00 | ||
2.00 | 50 | 87.12 | 12.88 | |
5 | 85.76 | 14.24 | ||
0.5 | 81.07 | 18.93 | ||
Режим 2 | 1.50 | 66.7 | 100.00 | – |
6.67 | 100.00 | – | ||
0.667 | 100.00 | – | ||
1.75 | 66.7 | 86.45 | 13.55 | |
6.67 | 86.02 | 13.98 | ||
0.667 | 85.00 | 15.00 | ||
2.00 | 66.7 | 84.12 | 15.88 | |
6.67 | 81.77 | 18.23 | ||
0.667 | 77.00 | 23.00 | ||
Режим 3 | 1.50 | 80 | 89.21 | 10.79 |
8 | 88.90 | 11.10 | ||
0.8 | 88.09 | 11.91 | ||
1.75 | 80 | 85.27 | 14.73 | |
8 | 84.88 | 15.12 | ||
0.8 | 79.00 | 21.00 | ||
2.00 | 80 | 77.90 | 22.30 | |
8 | 77.56 | 22.44 | ||
0.8 | 76.43 | 23.20 |
Из данных табл. 4 следует, что уменьшение частоты тока при неизменном значении величины тока импульса приводит к формированию покрытий с большим содержанием олова, так как смещение электродного потенциала в электроотрицательную сторону, как показано на рис. 1, способствует увеличению парциальных токов осаждения олова.
Для более детального изучения влияния режимов ИЭ на количественный состав сплава Cu–Sn были получены хронопотенциограммы медного электрода в используемом электролите, содержащем ионы Cu2+ и Sn2+, в импульсном режиме при значениях тока импульса 1.50, 1.75 и 2.00 А/дм2 (рис. 3).
Рис. 3.
Хронопотенциограммы медного электрода, полученные в импульсном режиме при катодных плотностях тока 1.50 (а–в), 1.75 (г–е) и 2.00 (ж–и) А/дм2. Состав электролита, моль/дм3: CuSO4 ⋅ 5H2O – 0.16; SnSO4 – 0.19; H2SO4 – 1.00; тиомочевина – 6.6 × 10–5; N-октилпиридиний бромид – 1.8 × 10–5. Скважность импульсов: 1 – 2 (режим 1); 2 – 1.5 (режим 2); 3 – 1.25 (режим 3).
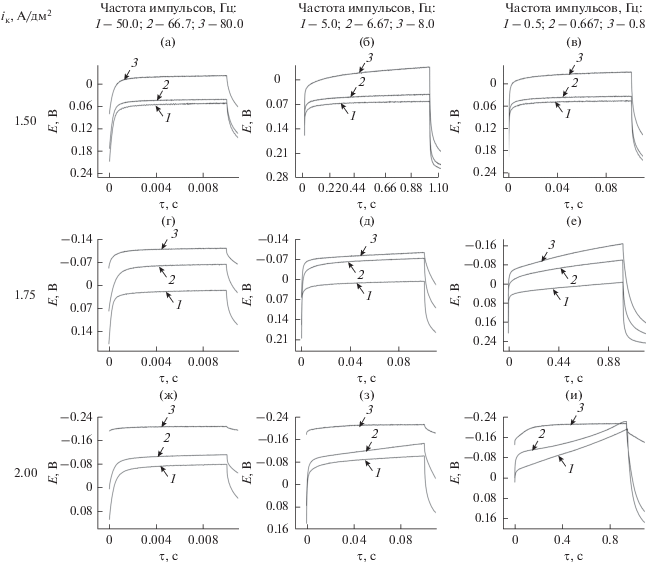
Как было сказано ранее, электролиз при катодной плотности тока 1.50 А/дм2 в режиме 1 при любой используемой частоте тока (рис. 3а–3в, кривая 1) не приводит к сплавообразованию, так как значение катодного потенциала не достигает 0.00 В. Аналогичная зависимость наблюдается при повышении токовой нагрузки до 1.75 A/дм2 и при частотах 50 и 5 Гц (рис. 3г, 3д, кривая 1). Дальнейшее снижение частоты импульсов до 0.5 Гц (рис. 3е, кривая 1) при неизменном значении плотности тока приводит к монотонному увеличению потенциала в течение катодного импульса. По истечении 0.8 с достигается переходное время, при котором концентрация ионов меди в приэлектродном слое снижается до нуля, что, в свою очередь, делает возможным подпотенциальное осаждение олова и приводит к формированию сплава, содержащего до 5.00 мас. % Sn. При катодной плотности тока 2.00 А/дм2 при любой используемой частоте (рис. 3ж–3и, кривая 1) устанавливается потенциал отрицательнее 0.00 В, что объясняет возможность сплавообразования при всех исследуемых частотах тока для данного режима ИЭ. Уменьшение частоты тока от 50 до 0.5 Гц способствует смещению E,t-кривой в более электроотрицательную область, что, в свою очередь, приводит к увеличению содержания олова в составе покрытий от 12.88 до 18.93 мас. %. Необходимо отметить, что при частоте тока 0.5 Гц величина потенциала осаждения достигает значений потенциала разряда олова из акватированных ионов.
При использовании режима 2, как и в предыдущем случае, при токовой нагрузке 1.50 А/дм2 в диапазоне исследуемых частот (рис. 3а–3в, кривая 2) не достигается потенциал сплавообразования, вследствие чего осаждается только медь. Повышение плотности тока до 1.75 и 2.00 А/дм2 (рис. 3г–3и, кривая 2), а также снижение частоты импульсов способствуют росту величины катодного потенциала, что приводит к увеличению содержания олова в сплаве до 13.55–23.00 мас. %.
В режиме 3 (рис. 3а–3в, кривая 3) при катодной плотности тока 1.50 А/дм2 для всех исследуемых частот достигается потенциал сплавообразования, что приводит к формированию покрытий, содержащих от 10.79 до 13.98 мас. % олова. Повышение токовой нагрузки до 1.75 А/дм2 (рис. 3г–3е, кривая 3) приводит к росту величины катодного потенциала и увеличению содержания олова в сплаве до 13.55–21.00 мас. %. При токовой нагрузке 2.00 А/дм2 при любых частотах (рис. 3ж–3и, кривая 3) устанавливается постоянное значение потенциала, равное –0.21 В, которое соответствует процессу осаждения олова из акватированных ионов (рис. 1), что обуславливает постоянный состав формируемого сплава.
Из данных рис. 2 и 3 следует, что при использовании импульсного электролиза непосредственно перед процессом совместного осаждения меди и олова (в течение переходного времени) наблюдается только стадия разряда ионов меди, что может обуславливать слоистую структуру формируемого покрытия. При помощи фокусируемого ионного пучка был сделан микрошлиф покрытия, полученного при использовании ИЭ в режиме 1 при плотности тока 2.00 А/дм2 и частоте 0.5 Гц. Как показано на рис. 4, в структуре покрытия отсутствует выраженная слоистость, что может быть обусловлено диффузией олова между слоями.
Рис. 4.
Микрофотография шлифа покрытия Cu–Sn, полученного при использовании ИЭ в режиме 1 (плотность тока 2.00 А/дм2, частота тока 0.5 Гц).
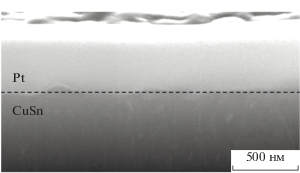
Для оценки влияния режимов ИЭ и величины токовой нагрузки на качество осадков, формируемых из исследуемого сернокислого электролита, были получены покрытия в интервале катодных плотностей тока 1.25–2.75 А/дм2 с шагом 0.25 А/дм2, схематическая диаграмма внешнего вида которых представлена на рис. 5.
Рис. 5.
Диаграмма влияния условий электролиза на качество покрытий, формируемых в стационарном (а) и в импульсном (б–г) режимах: б – 1; в – 2; г – 3.
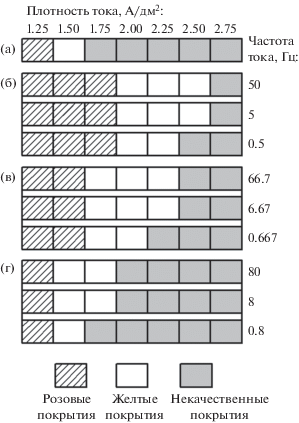
В стационарном режиме (рис. 5а) при токовой нагрузке 1.25 А/дм2 осаждаются покрытия розового цвета. Повышение токовой нагрузки до 1.50 А/дм2, как показано на рис. 6а, способствует получению качественных желтых покрытий Cu‒Sn с однородной мелкозернистой структурой. Дальнейшее увеличение катодной плотности тока до 2.75 А/дм2 приводит к формированию неоднородных крупнокристаллических покрытий (рис. 6б, 6в).
Рис. 6.
Микрофотографии покрытий, полученных в стационарных условиях электролиза (а–в), а также при использовании различных режимов ИЭ (режим 1 – г–е; режим 2 – ж–и; режим 3 – к–м). Частота тока, Гц: г–е – 50; ж–и – 66.7; к–м – 80. Плотность тока, А/дм2: а, к – 1.50; б, ж, л – 1.75; в, г, м – 2.00; з – 2.25; д, и – 2.50; е – 2.75.
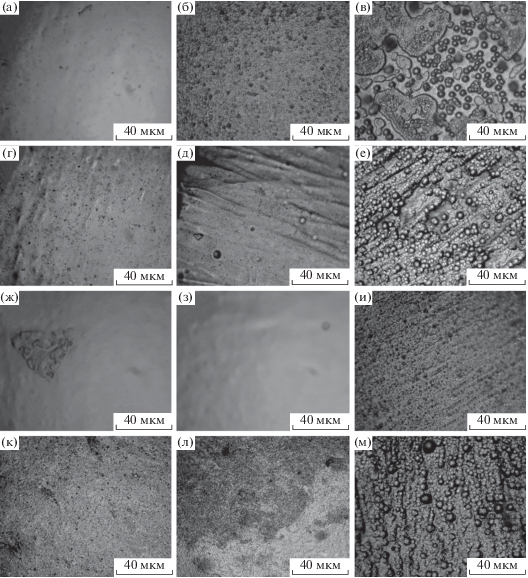
Использование ИЭ (рис. 5б–5г) способствует существенному увеличению интервалов катодных плотностей тока, обеспечивающих получение качественных желтых покрытий Cu–Sn. Так, при использовании режима 1 при частоте тока 50 Гц желтые покрытия с однородной и мелкозернистой структурой формируются в интервале плотностей тока от 2.00 до 2.50 А/дм2 (рис. 6г, 6д). Покрытия, полученные при токовой нагрузке 2.75 А/дм2 (рис. 6е), характеризуются неоднородной структурой, что обусловлено разрядом ионов олова при потенциалах, отрицательнее равновесного потенциала Sn|Sn2+, что приводит к образованию трехмерных зародышей олова и их неконтролируемому разрастанию. Использование режимов ИЭ с более низкой скважностью импульсов тока (режимы 2 и 3) способствует формированию качественных мелкозернистых покрытий желтого цвета в более узком диапазоне плотностей токов, чем при использовании режима 1 (рис. 5в, 5г). Так, использование режима 2 позволяет получать однородные мелкозернистые покрытия при токовых значениях импульсов от 1.75 до 2.25 А/дм2 (рис. 6ж, 6з), а при использовании режима 3 лишь при амплитудах импульсов тока 1.50 и 1.75 А/дм2 (рис. 6к, 6л). Повышение токовых нагрузок выше рекомендуемых для данных режимов способствует получению неоднородных покрытий (рис. 6и, 6м). Также необходимо отметить, что снижение частоты тока для всех исследуемых режимов приводит к уменьшению диапазона рабочих плотностей тока. Положительное влияние ИЭ-электролиза на диапазон рабочих плотностей тока обусловлен тем, что в момент импульса тока осаждение олова протекает подпотенциально.
Таким образом, проведенные исследования показали, что наиболее эффективным режимом ИЭ является режим 2, который позволяет получать качественные покрытия Cu–Sn в более широком диапазоне и при более высоких значениях эффективных плотностей тока.
ВЫВОДЫ
1. Установлено, что образование сплава Сu–Sn из сернокислого электролита в результате подпотенциального осаждения олова при использовании ИЭ возможно в том случае, когда длительность катодного импульса тока будет превосходить длительность переходного времени разряда ионов меди.
2. Уменьшение скважности тока (длительности паузы) ИЭ, а также его частоты при неизменной величине плотности тока способствуют сокращению длительности переходного времени разряда ионов меди, что, в свою очередь, приводит к формированию сплава с более высоким содержанием олова.
3. Увеличение частоты, а также величины плотности тока катодного импульса при неизменной скважности способствует увеличению содержания олова в формируемых покрытиях, что обусловлено ростом значений электродного потенциала в момент импульса тока.
4. Использование ИЭ позволяет увеличить интервал рабочих плотностей тока, при которых формируются качественные покрытия желтой бронзой, что приводит к улучшению кроющей способности электролита и позволяет обрабатывать детали более сложной конфигурации.
5. Использование ИЭ при соотношении времени импульса ко времени паузы 2 : 1 и частоте импульсов 66.70 и 6.67 Гц является наиболее целесообразным с точки зрения величин действительной токовой нагрузки и интервала рабочих плотностей тока импульса, при которых формируются качественные покрытия Cu–Sn.
Список литературы
Li, X., Ivas, T., Spierings, A.B., Wegener, K., and Leinenbach, C., Phase and microstructure formation in rapidly solidified Cu–Sn and Cu–Sn–Ti alloys, J. Alloys Compd., 2018, vol. 735, p. 1374.
Maizelis, A., Contact exchange in tetrafluoroborate-EDTA electrolyte for Cu–Sn alloy deposition, Mater. Today-Proc., 2019, vol. 6, p. 135.
Jung, M., Lee, G., and Choi, J., Electrochemical plating of Cu–Sn alloy in non-cyanide solution to substitute for Ni undercoating layer, Electrochim. Acta, 2017, vol. 241, p. 229.
Abbott, A.P., Alhaji, A.I., Ryder, K.S., Horne, M., and Rodopoulos, T., Electrodeposition of copper–tin alloys using deep eutectic solvents, T. I. Met. Finish., 2016, vol. 94, p. 104.
Meudre, C., Ricq, L., Hihn, J. Y., Moutarlier, V., Monnin, A., and Heintz, O., Adsorption of gelatin during electrodeposition of copper and tin–copper alloys from acid sulfate electrolyte, Surf. Coat. Tech., 2014, vol. 252, p. 93.
Correia, A.N., Façanha, M.X., and de Lima-Neto, P., Cu–Sn coatings obtained from pyrophosphate-based electrolytes, Surf. Coat. Tech., 2007, vol. 201, p. 7216.
Asnavandi, M., Ghorbani, M., and Kahram, M., Production of Cu–Sn–graphite–SiC composite coatings by electrodeposition, Surf. Coat. Tech., 2013, vol. 216, p. 207.
Ying, L., Fu, Z., Wu, K., Wu, C., Zhu, T., Xie, Y., and Wang, G., Effect of TiO2 Sol and PTFE Emulsion on Properties of Cu–Sn Antiwear and Friction Reduction Coatings, Coatings, 2019, vol. 9(1), p. 59.
Afshar, A., Ghorbani, M., and Mazaheri, M., Electrodeposition of graphite-bronze composite coatings and study of electroplating characteristics, Surf. Coat. Tech., 2004, vol. 187(2-3), p.293.
Касач, А.А., Курило, И.И., Харитонов, Д.С., Радченко, С.Л., Жарский, И.М. Влияние режимов сонохимической обработки на процесс электроосаждения сплава Cu–Sn из щавелевокислого электролита. Журн. прикл. Химии. 2018. Т. 91(4). С. 522. [Kasach, A.A., Kurilo, I.I., Kharitonov, D.S., Radchenko, S.L., and Zharskii, I.M., Effect of Sonochemical Treatment Modes on the Electrodeposition of Cu–Sn Alloy from Oxalic Acid Electrolyte, Russ. J. Appl. Chem., 2018, vol. 91(4), p. 591.]
Касач, А.А., Харитонов, Д.С., Романовский, В. И., Кузьменок, Н.М., Жарский, И.М., Курило, И.И. Электроосаждение сплава Cu–Sn из щавелевокислого электролита в присутствии аминосодержащих поверхностно-активных веществ, Журн. прикл. химии. 2019. Т. 92(6), С. 793. [Kasach, A.A., Kharitonov, D.S., Romanovskii, V.I., Kuz’menok, N.M., Zharskii, I.M., and Kurilo, I.I., Electrodeposition of Cu–Sn Alloy from Oxalic Acid Electrolyte in the Presence of Amine-containing Surfactants, Russ. J. Appl. Chem, 2019, vol. 92(4), p. 835.]
Pewnim, N. and Roy, S., Effect of Fluorosurfactant Additive during Cu–Sn Codeposition from Methanesulfonic Acid, J. Electrochem. Soc., 2015, vol. 162(8), p. 360.
Low, C.T.J. and Walsh, F.C., The stability of an acidic tin methanesulfonate electrolyte in the presence of a hydroquinone antioxidant, Electrochim. Acta, 2008, vol. 53(16), p. 5280.
Bengoa, L.N., Pary, P., Conconi, M.S., and Egli, W.A., Electrodeposition of Cu-Sn alloys from a methanesulfonic acid electrolyte containing benzyl alcohol, Electrochim. Acta, 2017, vol. 256, p. 211.
Walsh, F.C. and Low, C.T.J., A review of developments in the electrodeposition of tin-copper alloys, Surf. Coat. Tech., 2016, vol. 304, p. 246.
Gupta, A. and Srivastava, C., Enhanced corrosion resistance by SnCu-graphene oxide composite coatings, Thin Solid Films, 2019, vol. 669, p. 85.
Rozovskis, G., Mockus, Z., Pautienien, V., and Survila, A., Electrochemical determination of Sn(IV)/Sn (II) ratio in tin sol formed in copper–tin sulphate solution containing laprol 2402C, Electrochem. Commun., 2002, vol. 4(1), p. 76.
Ortiz, G.F., López, M.C., Alcántara, R., and Tirado, J.L., Electrodeposition of copper–tin nanowires on Ti foils for rechargeable lithium micro-batteries with high energy density, J. Alloys Compd., 2014, vol. 585, p. 331.
Meudre, C., David, J., Ricq, L., Hihn, J.Y., and Moutarlier, V., Elaboration of copper–tin alloys coatings: effect of glycine, J. Mater. Environ. Sci., 2015, vol. 6(7), p. 1834.
Barbano, E.P., de Oliveira, G.M., de Carvalho, M.F., and Carlos, I.A., Copper–tin electrodeposition from an acid solution containing EDTA added. Surf. Coat. Tech., 2014, vol. 240, p. 14.
Survila, A., Mockus, Z., Kanapeckaitė, S., Jasulaitienė, V., and Juškėnas, R., Codeposition of copper and tin from acid sulphate solutions containing gluconic acid, J. Electroanal. Chem., 2010. vol. 647(2), p. 123.
Касач, А.А., Курило, И.И., Харитонов, Д.С., Радченко, С.Л., Жарский, И.М. Cонохимическое электроосаждение медных покрытии. Журнал прикладной химии. 2019. Т. 91(2). С. 192. [Kasach, A.A., Kurilo, I.I., Kharitonov, D.S., Radchenko, S.L., and Zharskii, I.M., Sonochemical electrodeposition of copper coatings, Russ. J. Appl. Chem, 2019, vol. 91(2), p. 207.]
Chandrasekar, M.S. and Pushpavanam, M., Pulse and pulse reverse plating–Conceptual, advantages and applications, Electrochim. Acta, 2008, vol. 53(8), p. 3313.
Ramaprakash, M., Mohan, S., and Rajasekaran, N., Pulse and Pulse Reverse Electrodeposition of Cubic, Tetragonal and Its Mixed Phase of Ni–W Alloys for Corrosion Applications, J. Electrochem. Soc., 2019, vol. 166(6), p. 145.
Mirsaeed-Ghazi, S.M., Allahkaram, S.R., and Molaei, A., Development and investigation of Cu/SiC nano-composite coatings via various parameters of DC electrodeposition, Tribol. Int., 2019, vol. 134, p. 221.
Banthia, S., Sengupta, S., Das, S., and Das, K., Synthesis and characterization of novel Cu, Cu–SiC functionally graded coating by pulse reverse electrodeposition, Appl. Surf. Sci., 2019, vol. 467, p. 567.
Khorashadizade, F., Saghafian, H., and Rastegari, S., Effect of electrodeposition parameters on the microstructure and properties of Cu-TiO2 nanocomposite coating, J. Alloys Compd., 2019, vol. 770, p. 98.
Pena, E.M.D. and Roy, S., Electrodeposited copper using direct and pulse currents from electrolytes containing low concentration of additives, Surf. Coat. Tech., 2018, vol. 339, p. 101.
Green, T., Su, X., and Roy, S., Pulse Plating of Copper from Deep Eutectic Solvents, ECS Transactions, 2017, vol. 77(11), p. 1247.
Jie, S., Ting-yun, M., Hui-xuan, Q., and Qi-song, L., Electrochemical behaviors and electrodeposition of single-phase Cu–Sn alloy coating in [BMIM] Cl, Electrochim. Acta, 2019, vol. 297, p.87.
Juškėnas, R., Mockus, Z., Kanapeckaitė, S., Stalnionis, G., and Survila, A., XRD studies of the phase composition of the electrodeposited copper-rich Cu–Sn alloys, Electrochim. Acta, 2006, vol. 52(3), p. 928.
Meng, G., Sun, F., Wang, S., Shao, Y., Zhang, T., and Wang, F., Effect of electrodeposition parameters on the hydrogen permeation during Cu–Sn alloy electrodeposition. Electrochim. Acta, 2010, vol. 55(7), p. 2238.
Pu, W., He, X., Ren, J., Wan, C., and Jiang, C., Electrodeposition of Sn–Cu alloy anodes for lithium batteries. Electrochim. Acta, 2005, vol. 50(20), p. 4140.
Wu, L., Graves, J. E., and Cobley, A. J., Mechanism for the development of Sn-Cu alloy coatings produced by pulsed current electrodeposition, Mater. Lett., 2018, vol. 217, p. 120.
Мареев, С.А., Бутыльский, Д.Ю., Коваленко, А.В., Письменская, Н.Д., Даммак, Л., Ларше, К., Никоненко, В.В. Учет концентрационной зависимости коэффициента диффузии в уравнении Санда, Электрохимия, 2016, Т.52, С. 1118. [Mareev, S.A., Butyl’skii, D.Y., Kovalenko, A.V., Pis’menskaya, N.D., Dammak, L., Larchet, C., and Nikonenko, V.V., Inclusion of the concentration dependence of the diffusion coefficient in the sand equation. Russ. J. Electrochem., 2016, vol. 52(10), p. 996.]
Aniskevich, Y.M., Malashchonak, M.V., Bakavets, A.S., Ragoisha, G.A., and Streltsov, E.A., Determination of the Electrochemically Active Surface Area of PbSe and Bi 2 Te 3 Films Using the Deposition of Lead Atoms, Theor. Exp. Chem., 2019, vol. 55(1), p. 64.
Hinatsu, J.T., Foulkes and F.R. Diffusion coefficients for copper(II) in aqueous cupric sulfate-sulfuric acid solutions. J. Electrochem. Soc., 1989, vol. 136, p. 125.
Дополнительные материалы отсутствуют.