Электрохимия, 2021, T. 57, № 10, стр. 623-632
Полимерный слой переменного сопротивления для защиты литий-ионного аккумулятора от перезаряда
Е. В. Белецкий a, А. Ю. Кальнин a, Д. А. Лукьянов a, М. А. Каменский a, Д. В. Анищенко a, О. В. Левин a, *
a Санкт-Петербургский государственный университет, Институт химии
Санкт-Петербург, Россия
* E-mail: o.levin@spbu.ru
Поступила в редакцию 16.11.2020
После доработки 15.03.2021
Принята к публикации 05.04.2021
Аннотация
В работе предложено использование полимерного слоя на основе комплекса никеля с лигандом саленового типа для защиты литий-ионных аккумуляторов от перезаряда. Данный полимер обладает переменным сопротивлением и переходит в изолирующее состояние при превышении порогового значения потенциала. Это позволяет предотвратить развитие побочных процессов, таких как разложение электролита на катоде. Работа полимерного слоя была протестирована на модельных системах и в макетах литий-ионных аккумуляторов.
ВВЕДЕНИЕ
В связи с расширением сферы применения и удешевлением энергии, запасаемой в литий-ионных аккумуляторах (ЛИА), ежегодное производство изделий на их основе возрастает. Помимо применения в качестве источников питания различных портативных бытовых устройств, они активно распространяются для питания средств передвижения (электромобили, электропогрузчики и т.д.) [1]. Удешевление литий-ионных аккумуляторов приводит к сопоставимости стоимости запасаемой в них энергии с традиционными электрохимическими системами типа свинцово-кислотных, никель-кадмиевых, никель-металлогидридных, которые еще до сих пор применяются в сфере специальной и военной техники [2–4].
В связи с этим актуальным является обеспечение безопасности эксплуатации литий-ионных аккумуляторов. Для этого необходимо решение задач по предотвращению перезаряда, переразряда, внутреннего и внешнего короткого замыкания. Эти процессы сопровождаются интенсивным выделением тепла, из-за которого сам аккумулятор может разрушиться и загореться, приведя к разрушению всего изделия в целом и травматизации потребителей [5, 6].
Перезаряд является проблемой, которая постоянно сопровождает работу литий-ионных батарей. Поэтому достаточно много работ направлено на устранение его негативных последствий. С одной стороны, решение находится в применении внешних устройств – систем контроля и управления (СКУ) [1, 7–9], которые контролируют процессы заряда каждого аккумулятора, входящего в батарею, а с другой – в модификации составных частей аккумулятора [10, 11]. Применение СКУ приводит к увеличению массы, объема, стоимости батареи и сложности управления конечным изделием, особенно, когда речь идет о больших емкостях и высоких напряжениях. Поэтому активно применяется подход, заключающийся в химической модификации компонентов аккумулятора.
На сегодняшний день можно выделить три направления развития систем внутренней защиты: добавки против дендритов, подавляющие образование литиевых дендритов и тем самым предотвращающие внутренне короткое замыкание [12–15]; редокс-шаттл добавки, обеспечивающие электрохимическое шунтирование при превышении порогового значения потенциала и тем самым предотвращающие развитие побочных процессов [11, 16–18], и прерыватели перезаряда. Последние добавки относятся к необратимым, и их действие направлено на формирование сигнала для внешнего устройства, которое должно отключать батарею от зарядной цепи. В основном это происходит через обильное газообразование за счет окисления этих веществ или через электрохимическую полимеризацию, приводящую к прекращению работы ЛИА еще до начала теплового разгона. Наиболее типичными представителями являются: ксилол [19], циклогексилбензол [20], дифенил [21]. Недостатками данного направления является то, что после необратимой полимеризации добавки аккумулятор снимается с эксплуатации.
Решение, предлагаемое нами, состоит в создании прерывателя перезаряда в виде полимерного буферного подслоя, который будет располагаться между алюминиевым токоподводом и активной массой катода. Такой буферный подслой представляет собой электропроводящий полимер, проводимость которого меняется в зависимости от потенциала электрода, оставаясь достаточно высокой в рабочем диапазоне потенциалов и резко уменьшаясь при потенциалах, соответствующих перезаряду аккумулятора. Проводящие полимеры можно обратимо допировать посредством инжекции положительного заряда при окислении. При этом они обладают собственной электропроводностью только в частично допированном состоянии, т.е. в том случае, когда материал содержит одновременно и восстановленные, и окисленные фрагменты полимерной цепи. Перенос электрона между этими фрагментами отвечает за возникновение электронной проводимости. Такой перенос невозможен, если в пленке содержатся только восстановленные или только окисленные фрагменты. Среди проводящих полимеров есть такие, которые становятся изоляторами как при полном их дедопировании, так и при полном допировании по завершению фарадеевского процесса заряжения полимерных пленок [22]. Поэтому для создания буферного подслоя может быть использован проводящий полимер, область частичного допирования которого совпадает с рабочим диапазоном потенциалов катодных материалов литий-ионных аккумуляторов.
В работах [23, 24] в качестве таких полимеров мы рассмотрели полимерные комплексы никеля с лигандами саленового типа. Были выявлены зависимости проводимости полимерных пленок от потенциала в ходе in situ вольтамперометрических измерений; определен потенциал, после которого уменьшается их электропроводность; установлено влияние заместителей бензольного кольца лиганда на способность к сохранению электропроводности после снятия перезаряда и проведен анализ потенциальной возможности применения полимерных комплексов для защиты аккумуляторов от перезаряда. В данной работе будет исследована возможность использования в качестве буферного подслоя одного из таких комплексов, поли[Ni(CH3Salen)] (рис. 1).
В случае превышения рабочего диапазона напряжений (перезаряда) функцией буферного подслоя является создание в электрической цепи зарядного устройства нового элемента – сопротивления, на котором будет падать часть напряжения. По мере роста сопротивления при заряде напряжение на входе в аккумулятор будет возрастать до тех пор, пока не достигнет выставленного верхнего зарядного порога, а в случае перезаряда – максимального выходного напряжения зарядного устройства с отключением последнего или выходом на падающий ток (определяется функционалом зарядного устройства). Рост сопротивления в буферном подслое сдвигает нежелательные при перезаряде процессы на катоде (разложение электролита, дополнительное извлечение лития в случае литированного оксида кобальта или смешанных оксидов) к более высоким значениям суммарного напряжения аккумулятора, которое может лежать за пределами доступности для зарядного устройства, таким образом, предотвращая их протекание и обеспечивая защиту от перезаряда.
В этой статье рассмотрены электроды, в которых между активной массой и алюминиевым токоподводом расположен буферный подслой из поли[Ni(CH3Salen)]. Модельной электрохимической системой для первого типа электродов служил LiMn0.5Fe0.5PO4, в котором второе зарядное плато при 4.15 В является индикаторным, т.е. его наличие или отсутствие указывает на работу подслоя. Во втором типе электродов на буферный подслой нанесена активная масса с LiFePO4. Для нее проведен перезаряд при 5.0 В в течение 1 ч с измерением тока перезаряда.
ЭКСПЕРИМЕНТАЛЬНАЯ ЧАСТЬ
Так как поли[Ni(CH3Salen)] обладает плохой адгезией к алюминию, но легко осаждается на углеродные материалы, требовалась предварительная подготовка алюминиевой фольги. Процесс графитирования фольги проводили вручную графитовым стержнем путем натирания поверхности. Когда вся поверхность была обработана, токовывод считался подготовленным.
Защитный подслой получали электрохимической полимеризацией мономера Ni(CH3Salen) на поверхности алюминиевой фольги размером 2.5 × 4.0 см (MTI, Китай), графитированной ручным способом, методом циклической вольтамперометрии (ЦВА) в диапазоне потенциалов от 2.8 до 4.2 В относительно Li/Li+ со скоростью 20 мВ/с (рис. 2), используя потенциостат-гальваностат Autolab PGSTAT30 (Eco Chemie, Netherlands). Процесс останавливали, когда заряд синтеза достигал 1 Кл, что соответствовало расчетной толщине слоя полимера 1 мкм. Процесс вели из 0.01 М раствора мономера Ni(CH3Salen) в смеси диметилкарбонат/этиленкарбонат/диэтилкарбонат с объемным соотношением компонентов 1 : 1 : 1 с добавкой 2% винилкарбоната и 1 М LiPF6 в качестве фонового электролита. Противоэлектрод и электрод сравнения – литий. Полученные токоподводы промывали ацетонитрилом и высушивали в течение 1 сут в сухом заполненном аргоном боксе (Виллитек, Россия) с содержанием воды менее 1 м. д.
Рис. 2.
ЦВА синтеза поли[Ni(CH3Salen)] со скоростью 20 мВ/с в диапазоне потенциалов от 2.8 до 4.2 В на алюминиевом токоподводе из 0.01 М раствора мономера Ni(CH3Salen) в смеси диметилкарбонат–этиленкарбонат–диэтилкарбонат с объемным соотношением компонентов 1 : 1 : 1 с добавкой 2% винилкарбоната и 1 М LiPF6 (а), и фотография полученного электрода (б).
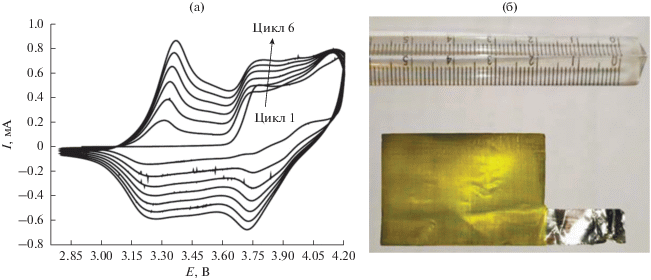
Пасту, состоящую из 80% активного вещества (LiMn0.5Fe0.5PO4 или LiFePO4), 10% сажи и 10% поливинилидендифторида, готовили смешением компонентов в гомогенизаторе (FSH-2, Китай) в течение 5 мин при скорости 8000 об/мин. После чего микрометрическим аппликатором “Dr. Blade” пасту наносили на поверхность токоподводов: на алюминиевую фольгу для LiMn0.5Fe0.5PO4, на графитированную алюминиевую фольгу для контрольного образца LiFePO4 и на графитированную фольгу, покрытую полимером, для защищенного катода на основе LiFePO4. Полученные образцы сушили в вакууме при 40–50°С в течение суток. Незащищенный контрольный образец обозначен как Al/LFP или Al/LMnFP, а защищенный слоем поли[Ni(CH3Salen)] – Al/poly/LFP или Al/poly/LMnFP.
Из полученных токоподводов вырубали электроды диаметром 1.55 см, прокатывали на вальцах и собирали полуэлементы типоразмера CR 2032 с литиевым анодом. Электролит – 1 М LiPF6 в смеси этиленкарбоната с диэтилкарбонатом (1 : 1 по объему), сепаратор – мембрана Celgard 2325. В случае LiMn0.5Fe0.5PO4 использовался 1 М LiPF6 в смеси диметилкарбонат/этиленкарбонат/диэтилкарбонат с объемным соотношением компонентов 1 : 1 : 1 с добавкой 2% винилкарбоната. Емкости нормированы на содержание активного вещества. Полуэлементы тестировали в следующих режимах: заряд–разряд током 1 С в диапазоне 2.5–4.0 В; перезаряд до 5.0 В и выдержка в течение 1 ч при 5.0 В. Импеданс полуэлементов в разряженном, заряженном и перезаряженном состоянии получали на потенциостате Autolab PGSTAT30 (Eco Chemie, Netherlands) в диапазоне частот 100 кГц–1 мГц, 10 точек на декаду. Перед измерением импеданса образцы релаксировали в течение 3–6 ч до стабильного напряжения разомкнутой цепи, т.е. пока колебание напряжения не будет менее 0.1 мВ/ч.
РЕЗУЛЬТАТЫ
Механизм срабатывания предохранительного подслоя для полуэлемента, состоящего из защищенного катода, сепаратора и литиевого анода, проиллюстрирован на рис. 3а, 3б. Рассмотрено два случая: нормальный режим работы, когда напряжение на полуэлементе не превышает рабочее, и перезаряд – когда напряжение превышает максимально допустимую величину. В первом случае предполагается, что, так как полимер обладает максимальной электрической проводимостью внутри рабочего диапазона потенциалов, его сопротивление почти не влияет на ход зарядо-разрядной кривой. Напряжение, приложенное к алюминиевому токоподводу, отличается от потенциала в активной массе не более чем на 50 мВ (рис. 3а). В случае выхода напряжения на клеммах аккумулятора за пределы рабочего диапазона напряжений (перезаряд) электропроводность полимера снижается, что, при протекании тока, выражается увеличением вклада омического сопротивления полимера в общем напряжении полуэлемента (рис. 3б). Таким образом, потенциал в активной массе будет меньше приложенного напряжения, и побочные процессы будут протекать менее интенсивно, чем в ячейке с незащищенным катодом, на активной массе которого потенциал практически полностью совпадал бы с приложенным напряжением.
Рис. 3.
Схема работы полуэлемента в случае нормального режима работы (а) и перезаряда (б), микрофотография токоподвода с полимерным слоем (в) и микрофотография катода (г).
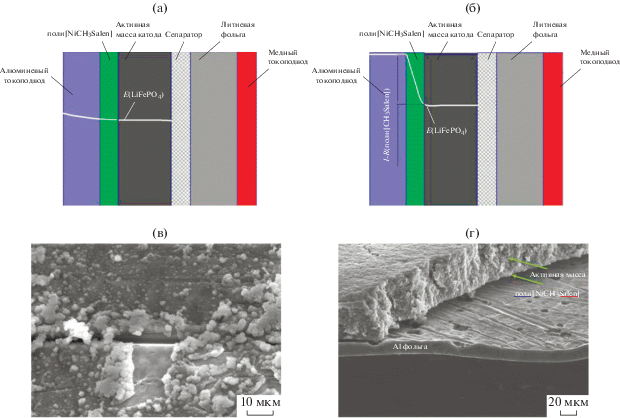
Микрофотография алюминиевого токоподвода с нанесенным полимером (рис. 3в) показывает, что он образует однородный слой со средней толщиной 1 мкм, над которым располагаются агломерации глобул. Шероховатая структура поверхности, характерная для полимерных комплексов никеля с лигандами саленового типа [25], увеличивает адгезию активной массы для улучшения омического контакта. На микрофотографии катода со стороны специально отделенной активной массы (рис. 3г) видна слоистая структура электрода: на алюминиевой фольге находится поли[Ni(CH3Salen)] (светлый слой), который плотно соприкасается со слоем активной массы. Толщина активной массы составляет около 60 мкм, алюминиевой фольги – 21 мкм, полимерного слоя, как и ожидалось в ходе синтеза, около 1–2 мкм.
В соответствии с данными, полученными нами в работе [23], зависимость электрической проводимости от потенциала для поли[Ni(CH3Salen)] имеет характер, представленный на рис. 4. Окно проводимости для этого полимера находится в пределах 3.2–4.0 В, и именно в этом диапазоне потенциалов полимер может пропускать через себя электрический ток и позволять заряжаться (разряжаться) активному веществу, находящемуся над ним. При повышении потенциала до 4.5 В электрическая проводимость снижается почти на порядок по сравнению со своим максимальным значением, что приводит к возрастанию сопротивления между активной массой и алюминиевым токоподводом.
Рис. 4.
ЦВА со скоростью 2 мВ/с электрода, модифицированного поли[Ni(CH3Salen)] в растворе 1 М LiPF6 в смеси этиленкарбонат–диэтилкарбонат (1 : 1) и зафиксированная в ходе измерения зависимость электропроводности пленки от потенциала.
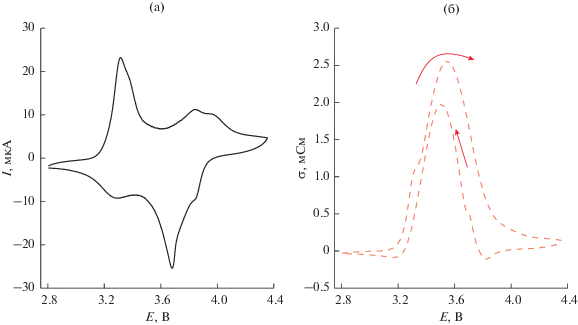
Для демонстрации работоспособности аккумуляторов и влияния подслоя на характер зарядо-разрядной кривой был проведен заряд–разряд в диапазоне потенциалов от 2.8 до 4.5 В током 1 С электродов с активной массой на основе LiMn0.5Fe0.5PO4 (рис. 5). Этот катодный материал выбран потому, что его первое плато при 3.6–3.7 В находится внутри окна проводимости полимера, а второе – за его пределами и может служить модельной реакцией, блокировка которой наглядно демонстрирует работу подслоя. Как видно из рисунка, для электрода Al/LMnFP наблюдаются характерные для LiMn0.5Fe0.5PO4 зарядные и разрядные кривые с двумя плато. Разрядная емкость составила около 95 мА ч/г. Второй и третий циклы практически совпадают друг с другом. Электрод Al/poly/LMnFP ведет себя иначе: у него отсутствует второе плато на заряде и также практически совпадают второй и третий циклы. Зарядная и разрядная емкость в 32 мА ч/г соответствует той части емкости, которая относится к первому плато заряда/разряда электрода без подслоя (перезарядка ионов железа). Процесс, соответствующий перезарядке ионов марганца при потенциалах выше 4.0 В не наблюдается. Таким образом, полученный результат подтверждает влияние поли[Ni(CH3Salen)] на зарядо-разрядный процесс, позволяя сказать, что выше рабочего диапазона потенциалов (до 4.0 В) реализуется защита от перезаряда.
Рис. 5.
Зарядо-разрядные кривые (3 цикла) током 1 С, где 1 С – 140 мА/г, электродов с активной массой на основе LiMn0.5Fe0.5PO4, нанесенной на чистый алюминиевый токоподвод, Al/LMnFP (а) и алюминиевый токоподвод с защитным подслоем, Al/poly/LMnFP (б). Электролит – 1 М LiPF6 в смеси диметилкарбонат–этиленкарбонат–диэтилкарбонат с объемным соотношением компонентов 1 : 1 : 1, с добавкой 2% винилкарбоната.
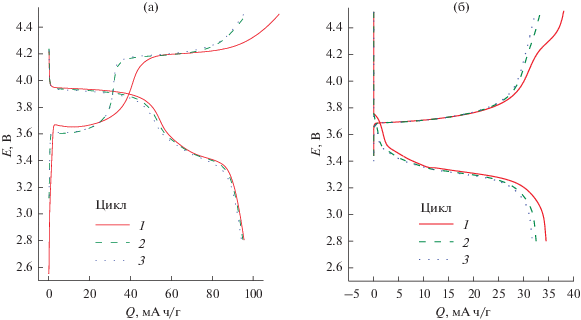
С целью проверить стабильность работы электрода с буферным подслоем было решено провести 25 циклов заряда–разряда до 4.0 В (верхняя граница рабочего диапазона) и до 4.5 В (кратковременный перезаряд) (рис. 6). В рабочем диапазоне потенциалов (до 4.0 В) защищенный и незащищенный электрод одинаково стабильны, при этом у защищенного электрода емкость сохраняется и при кратковременном перезаряде до 4.5 В, хотя происходит постепенное ее уменьшение, что свидетельствует о возрастании сопротивления защитного слоя вследствие уменьшения проводимости поли[Ni(CH3Salen)] при длительном переокислении полимера [23].
Рис. 6.
Стабильность работы током 1 С, где С – 140 мА/г, электродов на основе LiMn0.5Fe0.5PO4 (а) и зарядо-разрядные кривые для электрода Al/poly/LMnFP в диапазоне от 2.8 до 4.5 В (б). Электролит – 1 М LiPF6 в смеси диметилкарбонат–этиленкарбонат–диэтилкарбонат с объемным соотношением компонентов 1 : 1 : 1, с добавкой 2% винилкарбоната.
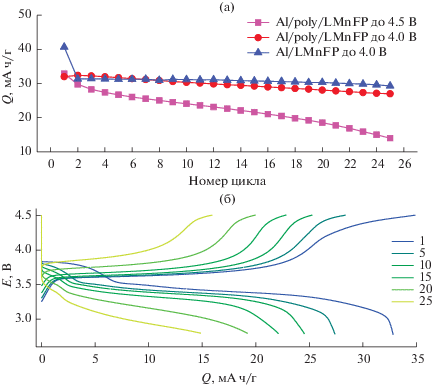
Тестирование защитных свойств поли[Ni(CH3Salen)] было проведено в полуэлементах CR2032 с литиевым анодом и катодом на основе LiFePO4 в режиме перезаряда постоянным током с переходом на постоянное напряжение по достижении 5 В. Перед проведением перезаряда были проведены несколько зарядо-разрядных циклов в нормальном диапазоне потенциалов 2.5–4.0 В (рис. 7). Непосредственно на перезарядном цикле были получены спектры импеданса для трех состояний полуэлементов: разряженного, заряженного и перезаряженного (рис. 8).
Рис. 7.
Зарядо-разрядные кривые (4 цикла) током 1 С, где С – 140 мА/г, электродов с активной массой на основе LiFePO4, нанесенной на чистый алюминиевый токоподвод (а), алюминиевый токоподвод с буферным подслоем (б), зависимость тока перезаряда от времени перезаряда (в), зависимость емкости перезаряда от времени перезаряда (г). Электролит – 1 М LiPF6 в смеси этиленкарбонат–диэтилкарбонат с объемным соотношением компонентов 1 : 1.
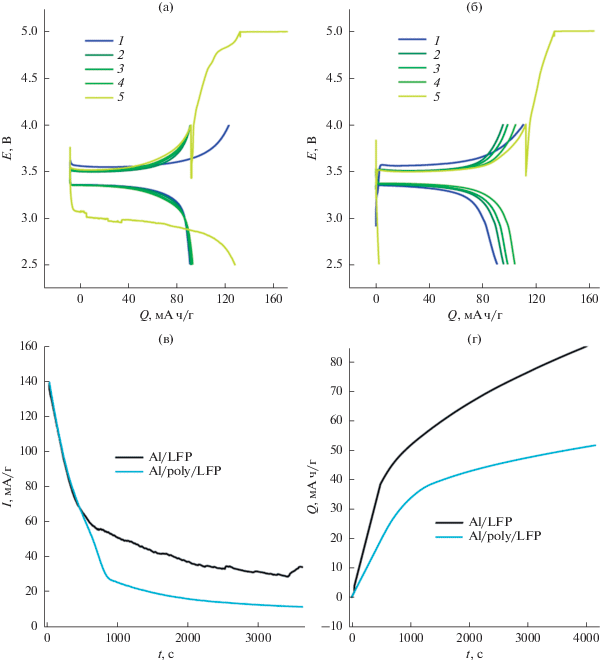
Рис. 8.
Импедансная спектроскопия для разряженного состояния (а), заряженного состояния (б) и после перезаряда (в). Электролит – 1 М LiPF6 в смеси этиленкарбонат–диэтилкарбонат с объемным соотношением компонентов 1 : 1.
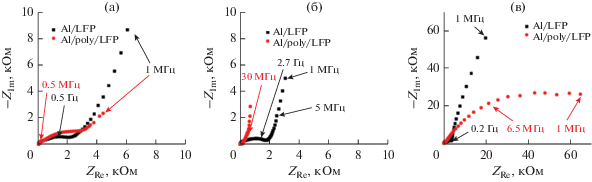
Из рис. 7 видно, что контрольный образец показал стабильное значение зарядной и разрядной емкости около 94 мА ч/г. Образец с защитным подслоем разрядился на первом цикле на 91 мА ч/г разрядной емкости, которая выросла к четвертому циклу до 104 мА ч/г. Такое поведение электрода объясняется наличием подслоя поли[Ni(CH3Salen)]. Известно, что присутствие электропроводящего полимера на токоподоводе улучшает электронный контакт между активной массой и алюминием, о чем свидетельствует улучшение характеристик материала, продемонстрированное на примере полимеров тиофенового ряда в работе [26]. В случае полимерных комплексов никеля с лигандами саленового типа в работе [27] выявлен аналогичный эффект, но при использовании полимера в качестве связующего. О факте улучшения электронного контакта также свидетельствует разница в сопротивлении переносу заряда Rct (рис. 8), полученная из данных по спектроскопии импеданса. В разряженном состоянии Rct Al/LFP и Al/poly/LFP равны 2.5 и 3 кОм соответственно. После заряда до 4.0 В подслой перешел в проводящее состояние, и у защищенного образца сопротивление уменьшилось до 150 Ом, а у контрольного – до 2 кОм, что в 12 раз больше, чем у защищенного.
Из рис. 7а, 7б видно, что в гальваностатическом режиме ход зарядных кривых при перезаряде (выше 4.0 В) у образцов отличается: в случае Al/poly/LFP наблюдается резкий рост напряжения, тогда как в контрольном электроде изменение носит более плавный характер. При потенциостатическом перезаряде (5.0 В) ток перезаряда у образца с подслоем оказался приблизительно в 2.8 раза меньше, чем без подслоя (рис. 7в). Указанные явления привели к тому, что суммарная емкость перезаряда для образца с защитным подслоем в 1.7 раз меньше, чем для контрольного (рис. 8в), что говорит об эффективности предложенного механизма защиты. Ввиду низкой стойкости полимерного комплекса к потенциостатическому режиму работы при высоких потенциалах подслой в данном случае играет роль “плавкого предохранителя” [23].
Чтобы подтвердить защитное влияние слоя поли[Ni(CH3Salen)], были получены спектры электрохимического импеданса после перезаряда (рис. 8). Сопротивление переносу заряда у Al/LFP после перезаряда практически не изменилось и составило 3.6 кОм, тогда как у Al/poly/LFP возросло до 79 кОм, что в 20 раз больше, чем у Al/LFP.
ЗАКЛЮЧЕНИЕ
В работе исследовано влияние защитного слоя полимера поли[Ni(CH3Salen)] на свойства электродов литий-ионных аккумуляторов. Продемонстрировано, что данный полимер защищает от перезаряда при превышении потенциала выше 4.0 В в режиме постоянного тока и постоянного напряжения, улучшает электронный контакт между активной массой и алюминиевым токоподводом. В случае кратковременных перезарядов, работает в качестве обратимого прерывателя перезаряда, а в случае длительных потенциостатических режимов перезаряда играет роль “плавкого предохранителя” ввиду низкой стойкости полимерного комплекса к потенциостатическому режиму работы при высоких потенциалах.
Список литературы
Omariba, Z.B., Zhang, L., and Sun, D., Review on health management system for lithium-ion batteries of electric vehicles, Electronics, 2018, vol. 7, no. 5, p. 72.
Боровиков, П.В., Степичев, М.М., Гетманова, Н.Ю., Шульга, Р.Н. Накопитель электроэнергии на основе литий-ионных аккумуляторов мегаваттного класса мощности. Электротехника, электроэнергетика, электротехническая промышленность. 2017. № 3. С. 38. [Borovikov, P.V., Stepichev, M.M., Getmanova, N.Yu., and Shul’ga, R.N., Electricity storage device based on lithium-ion batteries of megawatt power class, Elektrotekhnika, elektroenergetika, elektrotekhnicheskaya promyshlennost’ (in Russian), 2017, no. 3, p. 38.]
Груздев, А.И. Опыт создания батарей на базе литий-ионных аккумуляторов большой ёмкости. Электрохим.энергетика. 2011. № 11(3). С. 128. [Gruzdev, A.I., Experience in creating batteries based on high-capacity lithium-ion batteries, Elektrohimich. energetika (in Russian), 2011, no. 11(3), p. 128.]
Герасимов, А.С., Гуриков, О.В., Кудрявцев, Е.Н., Кудрявцев, Н.А., Сибиряков, Р.В., Шавловский, С.В. Применение накопителей энергии с использованием литий- ионных аккумуляторных батарей в системах оперативного постоянного тока. Известия НТЦ единой энергетической системы. 2011. № 73(2). С. 26. [Gerasimov, A.S., Gurikov, O.V., Kudryavtsev, E.N., Kudryavtsev, N.A., Sibiryakov, R.V., and Shavlovsky, S.V., Application of energy storage devices using lithium ion storage batteries in operating direct current systems, Izvestiya NTTS yedinoy energeticheskoy sistemy (in Russian), 2011, no. 73(2), p. 26.]
Lisbona, D. and Snee, T., A review of hazards associated with primary lithium and lithium-ion batteries, Process Safety and Environmental Protection, 2011, vol. 89, p. 434.
Wang, Q., Ping, P., Zhao, X., Chu, G., Sun, J., and Chen, C., Thermal runaway caused fire and explosion of lithium ion battery, J. Power Sources, 2012, vol. 208, p. 210.
Lu, L., Han, X., Li, J., Hua, J., and Ouyang, M., A review on the key issues for lithium-ion battery management in electric vehicles, J. Power Sources, 2013, vol. 226, p. 272.
Lipu, M.S.H., Hannan, M.A., Hussain, A., Hoque, M.M., Ker, Pin J., Saad, M.H.M., and Ayob, A., A review of state of health and remaining useful life estimation methods for lithium-ion battery in electric vehicles: Challenges and recommendations, J. Cleaner Production, 2018, vol. 205, p. 115.
Zhu, J., Wierzbicki, T., and Li, W., A review of safety-focused mechanical modeling of commercial lithium-ion batteries, J. Power Sources, 2018, vol. 378, p. 153.
Wen, J., Yu, Y., and Chen, C., A Review on Lithium-Ion Batteries Safety Issues: Existing Problems and Possible Solutions, Materials Express, 2012, vol. 2, no. 3, p. 197.
Liu, K., Liu, Y., Lin, D., Pei, A., and Cui, Yi., Materials for lithium-ion battery safety, Science Advances, 2018, vol. 4, no. 6, p. eaas9820.
Aurbach, D., Gamolsky, K., Markovsky, B., Gofer, Y., Schmidt, M., and Heider, U., On the use of vinylene carbonate (VC) as an additive to electrolyte solutions for Li-ion batteries, Electrochim. Acta, 2002, vol. 47, no. 9, p. 1423.
Matsuo, Y., Fumita, K., Fukutsuka, T., Sugie, Y., Koyama, H., and Inoue, K., Butyrolactone derivatives as electrolyte additives for lithium-ion batteries with graphite anodes, J. Power Sources, 2003, vol. 119–121, p. 373.
Komaba, S., Kaplan, B., Ohtsuka, T., Kataoka, Y., Kumagai, N., and Groult, H., Inorganic electrolyte additives to suppress the degradation of graphite anodes by dissolved Mn(II) for lithium-ion batteries, J. Power Sources, 2003, vol. 119–121, p. 378.
McMillan, R., Slegr, H., Shu, Z.X., and Wang, W., Fluoroethylene carbonate electrolyte and its use in lithium ion batteries with graphite anodes, J. Power Sources, 1999, vol. 81–82, p. 20.
Halpert, G., Surampudi, S., Shen, D., Huang, C.-K., Narayanan, S., Vamos, E., and Perrone, D., Status of the development of rechargeable lithium cells, Space Electrochemical Research and Technology, 1993, vol. 1, p. 85.
Moshurchak, L.M., Buhrmester, C., and Dahn, J.R., Triphenylamines as a Class of Redox Shuttle Molecules for the Overcharge Protection of Lithium-Ion Cells, J. Electrochem. Soc., 2008, vol. 155, no. 2, p. A129.
Moshurchak, L.M., Lamanna, W.M., Bulinski, M.L., Wang, R.R., Garsuch, R., Jiang, Ju., Magnuson, D., Triemert, M., and Dahn, J.R., High-Potential Redox Shuttle for Use in Lithium-Ion Batteries, J. Electrochem. Soc., 2009, vol. 156, no. 4, p. A309.
Feng, X.M., Ai, X.P., and Yang, H.X., Possible use of methylbenzenes as electrolyte additives for improving the overcharge tolerances of Li-ion batteries, J. Appl. Electrochem., 2004, vol. 34, no. 12, p. 1199.
Tobishima, S., Ogino, Y., and Watanabe, Y., Influence of electrolyte additives on safety and cycle life of rechargeable lithium cells, J. Appl. Electrochem., 2003, vol. 33, no. 2, p. 143.
Huanyu, M. and Ulrich, V.S., Aromatic monomer gassing agents for protecting non-aqueous lithium batteries against overcharge, Pat. CA2163187C (Canada). 1996.
Heinze, J., Frontana-Uribe, B.A., and Ludwigs, S., Electrochemistry of Conducting Polymers-Persistent Models and New Concepts, Chemical Reviews, 2010, vol. 110, no. 8, p. 4724.
Белецкий, Е.В., Волосатова, Ю.А., Елисеевa, С.Н., Левин, О.В. Влияние электродного потенциала на проводимость полимерных комплексов лигадами саленового типа. Электрохимия. 2019. Т. 55. С. 500. [Beletskii, E.V., Volosatova, Yu.A., Eliseeva, S.N., and Levin, O.V., The Effect of Electrode Potential on the Conductivity of Polymer Complexes of Nickel with Salen Ligands, Russ. J. Electrochem., 2019, vol. 55, p. 339.]
Beletskii, E.V., Fedorova, A.A., Lukyanov, D.A., Yankin, A.N., Kalnin, A.Y., Ershov, V.A., Danilov, S.E., Spiridonova, D.V., Alekseeva, E.V., and Levin, O.V., Switchable resistance conducting-polymer layer for Li-ion battery overcharge protection, J. Power Sources, 2021, vol. 490, p. 229548.
Alekseeva, E.V., Chepurnaya, I.A., Malev, V.V., Timonov, A.M., and Levin, O.V., Polymeric nickel complexes with salen-type ligands for modification of supercapacitor electrodes: impedance studies of charge transfer and storage properties, Electrochim. Acta., 2017. vol. 225, p. 378.
Lepage, D., Savignac, L., Saulnier, M., Gervais, S., and Schougaard, S.B., Modification of aluminum current collectors with a conductive polymer for application in lithium batteries, Electrochemistry Communications, 2019, vol. 102, p. 1.
O’Meara, C., Karushev, M.P., Polozhentceva, I.A., Dharmasena, S., Cho, H., Yurkovich, B.J., Kogan, S., and Kim, J.-H., Nickel–Salen-Type Polymer as Conducting Agent and Binder for Carbon-Free Cathodes in Lithium-Ion Batteries, ACS Applied Materials & Interfaces, 2019. vol. 11, no. 1, p. 525.
Дополнительные материалы отсутствуют.