Электрохимия, 2021, T. 57, № 11, стр. 670-678
Повышение электрохимической активности границы Pr1.95La0.05CuO4/пористый слой Ce0.9Gd0.1O1.95 при инфильтрационном введении Pr6O11
Н. В. Лысков a, *, М. З. Галин a, К. С. Напольский b, И. В. Росляков b, c, Г. Н. Мазо b
a Институт проблем химической физики РАН
142432 Московская обл., Черноголовка, просп. академика Семенова, 1, Россия
b Московский государственный университет им. М.В. Ломоносова, Химический факультет
119992 Москва, Ленинские горы, 1, стр. 3, Россия
c Институт общей и неорганической химии имени Н.С. Курнакова РАН
119991 Москва, Ленинский просп., 31, Россия
* E-mail: lyskov@icp.ac.ru
Поступила в редакцию 03.03.2021
После доработки 09.04.2021
Принята к публикации 12.04.2021
Аннотация
Исследованы электрохимические свойства электрода с многослойной структурой состава токосъемный слой Pr1.95La0.05CuO4 (PLCO)/пористый слой Ce0.9Gd0.1O1.95 (GDC), модифицированный добавкой Pr6O11. Оптимизировано соотношение исходных компонентов (GDC/порообразователь) для создания пористого слоя GDC, позволяющее достичь высокой электрохимической активности электрода в реакции восстановления кислорода. Показано, что переход к многослойной структуре позволяет снизить поляризационное сопротивление электрода (Rη) на основе PLCO на порядок величины по сравнению с исходным немодифицированным электродом и достичь Rη = 0.16 Ом см2 при 650°С на воздухе. На основании результатов проведенного систематического исследования, направленного на разработку способа поэтапного формирования многослойной структуры катода на основе PLCO для твердооксидных топливных элементов (ТОТЭ), показано, что предложенный подход обеспечивает получение катодных слоев ТОТЭ, пригодных для функционирования в интервале средних температур 500–800°С, и достижение высокой электрохимической активности электрода в реакции восстановления кислорода.
ВВЕДЕНИЕ
В настоящее время основными техническими проблемами, которые необходимо решить разработчикам электрохимических генераторов энергии на основе твердооксидных топливных элементов (ТОТЭ), являются повышение производительности и долговечности, а также снижение стоимости [1, 2]. В этой связи весьма перспективным с точки зрения повышения экономической привлекательности представляется переход к среднетемпературным ТОТЭ, работающим в интервале 500–800°С [3, 4]. Понижение рабочей температуры приведет к снижению скорости деградации материалов, решению проблем, связанных с герметизацией, а также обеспечит возможность применения более дешевых коммутационных материалов. Однако при переходе в область средних температур падает скорость реакции восстановления кислорода (РВК) на катоде, что в свою очередь существенно снижает эффективность работы ТОТЭ, поскольку вклад поляризационных потерь на катоде в общее сопротивление топливной ячейки в этих условиях является, как правило, доминирующим [5]. Для повышения электрохимической активности катода в РВК в последнее время активно разрабатываются подходы, направленные на оптимизацию микроструктуры электрода с точки зрения повышения концентрации реакционно-активных центров. В частности, широкое распространение получил метод инфильтрационного введения частиц электроактивного материала в предварительно созданную пористую структуру, для формирования которой могут быть использованы материалы твердого электролита или катода [1, 2, 6–12]. Основным преимуществом такого подхода является возможность формирования наночастиц электрокатализатора при гораздо более низких температурах, чем температура спекания пористой основы, что обеспечивает сохранение наноструктуры частиц электроактивной добавки и способствует высокой скорости протекания РВК.
Целью настоящей работы являлась разработка методики создания эффективного катода ТОТЭ, состоящей из нескольких последовательных стадий: (1) формирование на поверхности твердого электролита Ce0.9Gd0.1O1.95 (GDC) пористой структуры; (2) последующее покрытие ее электрокаталитическим слоем с помощью метода инфильтрации; (3) нанесение токосъемного слоя с внешней стороны модифицированной поверхности GDC. В работе изучена электрохимическая активность такого электрода в реакции восстановления кислорода в интервале средних температур 500–800°С. В качестве пористой основы для инфильтрации наибольший интерес представляет твердый электролит GDC, так как его кислород-ионная проводимость в области средних температур на порядок величины выше, чем проводимость Zr0.84Y0.16O1.92 (YSZ) [4, 5]. Вместе с тем, для последующей инфильтрации в пористый субстрат на основе GDC может быть использован Pr6O11, как эффективная электроактивная добавка [13–16], которая увеличивает электрохимическую активность катодных материалов, как однофазных (LaNi0.6Fe0.4O3 – δ [13, 15]), так и композитных (La1 – xSrxMnO3 – δ (LSM)-GDC [16]). Что касается выполнения токосъемной функции формируемого композитного катода, то весьма перспективным представляется рассмотрение купратов редкоземельных элементов (РЗЭ) Ln2СuO4, где Ln = РЗЭ, среди которых наибольший интерес вызывают соединения на основе купрата празеодима Pr2CuO4 (РСО) [17–24]. Преимуществами его использования являются высокая электропроводность (${{\sigma }_{{900^\circ {\text{C}}}}}$ ≈ 100 См/см), термомеханическая совместимость (коэффициент термического расширения (КТР) = 11.9 × 10–6 К–1 [21]) с твердым электролитом на основе GDC (КТР = 12.4 × 10–6 К–1) [25], низкое поляризационное сопротивление (Rη(РСО/GDC) = 0.6 Ом см2 при 700°С на воздухе [18, 19]), которое в 2 раза ниже по сравнению с Rη для традиционных катодных материалов на основе LSM [26]. Следует отметить, что усовершенствованным вариантом базового состава РСО, демонстрирующим повышенные электротранспортные характеристики, является соединение Pr1.95La0.05CuO4 (PLCO) [21, 23]. Этот состав обладает максимальной проводимостью среди твердых растворов Pr2 –xLaxCuO4 (0 ≤ x ≤ 0.3), величина которой составляет около 120 См/см при 800°С, а его величина КТР (11.8 × × 10–6 К–1) [21] обеспечивает термомеханическую совместимость с GDC.
ЭКСПЕРИМЕНТАЛЬНАЯ ЧАСТЬ
Повышение протяженности рельефа поверхности твердого электролита GDC для последующего увеличения реакционной зоны границы электрод/электролит было реализовано с помощью метода трафаретной печати. Основная идея этого подхода состоит в формировании на поверхности плотноспеченной твердоэлектролитной мембраны пористого слоя, идентичного по химическому составу материалу твердого электролита. Образцы плотноспеченных твердоэлектролитных мембран GDC были получены спеканием порошка коммерческого реактива (Aldrich®, размер частиц порошка 0.1–0.3 мкм) при 1400°С в течение 10 ч. Относительная плотность полученных образцов GDC составила ~96%. Формирование пористого слоя GDC было осуществлено с использованием суспензий, состоящих из органического связующего (α-терпинеол) и смеси субмикронного порошка GDC с порообразователем. Для изучения влияния соотношения “твердый электролит (GDС)/порообразователь” на морфологию пористого слоя была приготовлена серия образцов твердоэлектролитных мембран с пористым поверхностным слоем GDC. В качестве порообразователя использовали рисовый крахмал (размер частиц 3–5 мкм, Deffner & Johann GmbH, Германия), содержание которого в смеси с GDC варьировали от 20 до 50 мас. %. Массовое соотношение α-терпинеола и смеси порошков составляло 1 : 2. Нанесение суспензии осуществляли методом трафаретной печати на отшлифованные поверхности плотноспеченных твердоэлектролитных мембран GDC с использованием тканевых сеток VS-Monoprint PES HT TW 165/30 (Verseidag-Techfab GmbH, Германия). После каждого нанесения образец сушили при 130°С в течение 30 мин. Припекание нанесенного слоя GDC осуществляли при температуре 1200°С в течение 10 ч.
Полученные образцы твердоэлектролитных мембран с пористым поверхностным слоем GDC были использованы в качестве электролитной основы для последующего создания многослойной структуры композитного катода. На первом этапе формирования электрода была проведена модификация пористого слоя GDC методом инфильтрационного введения электроактивной добавки Pr6O11, что включало последовательное выполнение следующих стадий: 1) покапельное нанесение 2 М раствора Pr(NO3)3 на внешнюю поверхность пористого слоя GDC до ее полного покрытия; 2) помещение образца в эксикатор и последующее вакуумирование с использованием форвакуумного насоса, выдержка при пониженном давлении в течение 2 мин; 3) удаление избытка жидкости с внешней поверхности образца фильтровальной бумагой; 4) термическая обработка образца при 500°С в течение 20 мин.
Для более полного заполнения внутреннего объема катодного материала все экспериментальные стадии данного этапа повторяли несколько раз до достижения содержания Pr6O11 около 30–35 мас. % относительно массы пористого слоя GDC. Условия термообработки солевого прекурсора были выбраны исходя из данных термогравиметрии по разложению Pr(NO3)3⋅6H2O до оксида. Термогравиметрический анализ (ТГА) проводили с помощью термоанализатора Netzsch STA 449C (Германия) в температурном интервале 25–950°C со скоростью нагрева 10°C/мин на воздухе (скорость потока 30 мл/мин).
Второй этап создания многослойной структуры композитного катода включал стадию нанесения токосъемного электродного слоя на основе PLCO на внешнюю поверхность твердоэлектролитных мембран GDC, поверхностный пористый слой которых был модифицирован инфильтрационным введением Pr6O11. Синтез порошка PLCO осуществляли твердофазным методом на воздухе согласно методике, описанной ранее в работе [21]. Перед использованием порошок PLCO был помолот в планетарной мельнице Fritsch Pulverisette 6 (Германия). Помол осуществляли в гептане в течение 15 мин, после чего порошок сушили в сушильном шкафу при 80°С в течение 2 ч. Анализ распределения частиц порошка по размерам, проведенный методом динамического светорассеяния на лазерном дифракционном микроанализаторе Fritsch Analysette 22 (Германия), показал, что размер частиц порошка варьировался в интервале 1–6 мкм. После этого была приготовлена суспензия, состоящая из помолотого порошка PLCO и α-терпинеола, взятых в массовом соотношении 1 : 0.8. Перемешивание суспензии перед нанесением проводили в планетарном центробежном миксере Thinky ARE 250 (Япония) при скорости 1500 об/мин в течение 15 мин с последующим пеноудалением при скорости 1700 об/мин в течение 3 мин. После чего на поверхность образцов твердоэлектролитных мембран GDC с использованием тканевых сеток VS-Monoprint PES HT PW 77/55 (Verseidag-Techfab GmbH, Германия) наносили суспензии. Эту процедуру повторяли 3 раза с обеих сторон образца GDC. После каждого нанесения образец сушили при 120°С в течение 15 мин. Финальную термообработку образцов проводили при температуре 850°С в течение 10 ч на воздухе.
Фазовый состав образцов контролировали методом рентгенофазового анализа (РФА) с помощью дифрактометра Huber G670 (излучение CuKα, интервал 2θ 20°–80°). Для идентификации полученных соединений использовали рентгенографическую базу данных ICDD PDF-2. Анализ микроструктуры образцов проводили методом растровой электронной микроскопии (РЭМ) (Carl Zeiss NVision 40, Германия).
Исследование электрохимического поведения границы электрод/электролит проводили методом импедансной спектроскопии на симметричных электрохимических ячейках электрод/электролит/электрод. Импедансные измерения осуществляли по двухэлектродной схеме подключения с использованием импедансметра P-5X (ООО “Electrochemical Instruments”, Россия) в диапазоне частот от 0.1 Гц до 500 кГц с амплитудой сигнала 10 мВ в интервале температур 500–800°C на воздухе. Противоэлектрод и рабочий электрод, нанесенные методом трафаретной печати на поверхность таблетки твердого электролита, были идентичные. Токоподводами служила платиновая проволока, в качестве токосъемных контактов выступали платиновые сетки, плотно прижатые к противоэлектроду и рабочему электроду. Температуру образца контролировали с помощью Pt–Pt/Rh термопары, расположенной вблизи образца. Обработку импедансных спектров и расчет параметров импеданса проводили с помощью программы ZView (Scribner Associates, Inc.).
РЕЗУЛЬТАТЫ И ОБСУЖДЕНИЕ
Для изучения реакционной способности Pr6O11 по отношению к твердому электролиту GDC была приготовлена их смесь в массовом соотношении 1 : 1, которая была отожжена при 850°C в течение 20 ч на воздухе. На рис. 1 приведены рентгенограммы смеси Pr6O11–GDC до и после термической обработки. Согласно полученным данным, за исключением фаз исходных компонентов, которые идентифицируются как кубические флюоритные фазы Pr6O11 (ICDD PDF-2 № 42-1121) и GDC (ICDD PDF-2 № 75-161), образования новых фаз в пределах чувствительности метода РФА не наблюдается. При этом положение дифракционных максимумов фаз не изменяется, что может свидетельствовать в пользу отсутствия межфазного обмена катионами РЗЭ. Таким образом, полученный результат указывает на химическую совместимость этих материалов для их последующего совместного использования при повышенных температурах.
Рис. 1.
Рентгенограммы смеси порошков Pr6O11 и GDC до (1) и после (2) термической обработки при 850°C в течение 20 ч на воздухе.
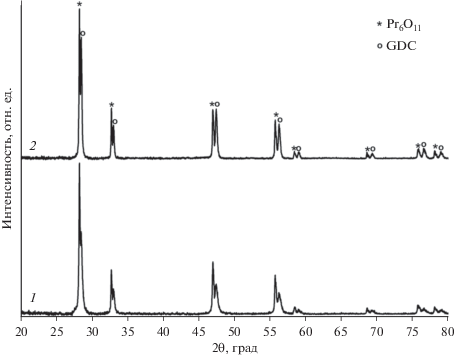
На рис. 2 представлены РЭМ-изображения поперечного сечения пористого слоя GDC, нанесенного методом трафаретной печати на поверхность плотноспеченного твердого электролита GDC, для различных соотношений твердый электролит (GDС)/порообразователь, использованных на этапе формирования пористого слоя. Пористый слой GDC представляет собой структуру, состоящую из связанных между собой частиц размером 100–300 нм. Он обладает хорошей адгезией к поверхности плотноспеченной твердоэлектролитной мембраны. Следует отметить, что увеличение содержания порообразователя свыше 40 мас. % приводит к резкому снижению толщины слоя GDC (табл. 1). Практически во всех случаях в структуре слоя GDC присутствуют как относительно мелкие поры, соразмерные с диаметром зерен GDC, так и достаточно крупные поры с размерами от одного до нескольких микрон. По всей видимости, за формирование пор большего размера отвечает присутствие частиц рисового крахмала, введенного в состав наносимой суспензии. Следует отметить, что распределение пор по толщине слоя достаточно однородное. При этом поры формируют связанную сетку каналов, обеспечивающих хорошую газовую доступность по всей толщине слоя. В случае содержания порообразователя 50 мас. % слой становится неоднородным по толщине. Последнее может являться критическим фактором в случае инфильтрационного введения электрокаталитической добавки при формировании электрода. Таким образом, наибольшую перспективу, с точки зрения формируемой микроструктуры пористого слоя GDC, представляет содержание порообразователя от 20 до 40 мас. %.
Рис. 2.
РЭМ-изображения поперечного сечения пористого слоя GDC, нанесенного методом трафаретной печати на поверхность плотноспеченного твердого электролита GDC, при различном соотношении твердый электролит GDС/порообразователь (соотношение указано в правом верхнем углу РЭМ-изображений).
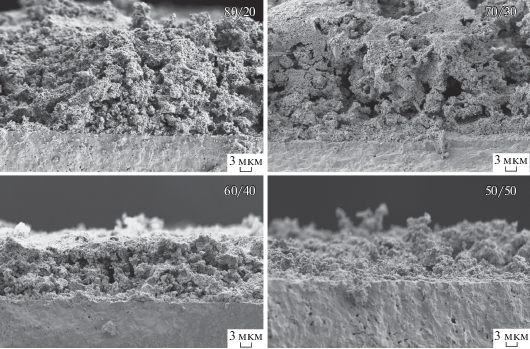
Таблица 1.
Толщина пористого слоя GDC при различном соотношении твердый электролит (GDС)/порообразователь (рисовый крахмал)
Соотношение GDC/порообразователь | Толщина пористого слоя GDС, мкм |
---|---|
80/20 | 28–30 |
70/30 | 28–30 |
60/40 | 16–18 |
50/50 | 7–10 |
На рис. 3а приведены РЭМ-изображения границы электрод PLCO/пористый слой GDC, модифицированный инфильтрацией Pr6O11/электролит GDC для образца, при формировании пористого слоя которого использовано соотношение GDC/порообразователь, равное 80/20. Внешний токосъемный слой PLCO является пористым с однородным распределением частиц по размеру и равномерным по толщине. Вместе с тем он характеризуется хорошим контактом с поверхностью пористого слоя GDC. Согласно полученным данным толщина слоя PLCO составляла 20 ± 2 мкм. РЭМ-изображение пористого слоя GDC после проведения процедуры инфильтрационного введения Pr6O11 представлено на рис. 3б. Видно, что фаза электроактивной добавки однородно покрывает внутренний объем пористого слоя GDC, при этом нанометровые частицы Pr6O11 образуют на поверхности GDC связанную структуру.
Рис. 3.
(а) РЭМ-изображение поперечного сечения границы электрод PLCO/пористый слой GDC, модифицированный инфильтрацией Pr6O11/электролит GDC (для формирования пористого слоя использовано соотношение GDC/порообразователь, равное 80/20); (б) РЭМ-изображение поперечного сечения пористого слоя GDC после пропитки раствором нитрата празеодима и последующей термической обработки при 500°С в течение 20 мин (темные контрастные области – GDC, светлые контрастные области – Pr6O11).
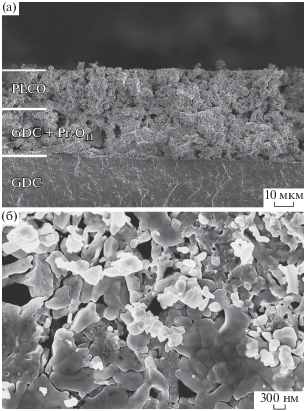
На рис. 4 представлены типичные импедансные спектры для электрода PLCO, сформированного на поверхности пористого слоя GDC, модифицированного наночастицами Pr6O11, в зависимости от содержания порообразователя, использованного для формирования пористого слоя. Для удобства сравнения приведенных спектров в них была проведена компенсация сопротивления электролита, определяемого по величине высокочастотной отсечки на действительную ось сопротивлений. Общее поляризационное сопротивление Rη электрода рассчитывали, исходя из разницы между низко- и высокочастотной отсечками импедансного спектра на действительную ось сопротивлений и с учетом нормирования на площадь электрода. Из рисунка видно, что при содержании порообразователя 20–30 мас. % достигается минимум величины Rη. В случае дальнейшего увеличения содержания порообразователя наблюдается постепенное повышение величины поляризационного сопротивления. Согласно данным РЭМ, такое поведение, по-видимому, связано со снижением удельной площади поверхности формируемого пористого слоя GDC вследствие уменьшения его толщины (табл. 1). В результате проведения последующей процедуры инфильтрации Pr6O11 получающийся электрод, по всей видимости, обладает меньшей концентрацией электрокаталитически активных центров, участвующих в реакции восстановления кислорода.
Рис. 4.
Спектры электродного импеданса границы PLCO/пористый слой GDC(Pr6O11)/GDC при 655 ± 2°С на воздухе в зависимости от содержания порообразователя, использованного для формирования пористого слоя GDC (соотношение GDС/порообразователь: 1 – 80/20; 2 – 70/30; 3 – 60/40; 4 – 50/50).
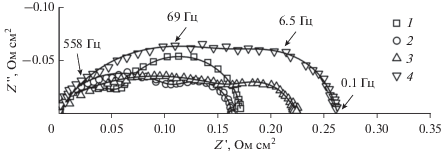
На рис. 5 приведены температурные зависимости общего поляризационного сопротивления электрода PLCO, сформированного на поверхности пористого слоя GDC, модифицированного инфильтрацией Pr6O11. Полученные зависимости линейны во всем исследованном интервале температур и демонстрируют термоактивационный характер. Сравнение электрохимической активности электрода PLCO [23], нанесенного на твердоэлектролитную мембрану GDC без использования пористого подслоя, с его аналогами, в которых использован пористый подслой GDC, модифицированный инфильтрацией Pr6O11, показывает, что введение активатора обеспечивает снижение Rη на порядок величины. Вместе с тем уменьшается также величина кажущейся энергии активации (Ea) от 1.55 эВ (немодифицированный электрод) до 1.11 эВ (модифицированный электрод при соотношении GDС/порообразователь, равном 80/20). С точки зрения достижения наибольшей электрохимической активности границы электрод/электролит при прочих равных условиях наиболее перспективным является формирование пористого слоя GDC с использованием соотношения GDС/порообразователь, равным 70/30 и 80/20. Такое поведение обусловлено, по-видимому, близкой морфологией пористого слоя GDC, формируемого методом трафаретной печати на поверхности твердого электролита. Таким образом, подход, связанный с формированием буферного пористого слоя GDC между плотно спеченным твердым электролитом GDC и катодным слоем PLCO и последующей инфильтрацией в его внутренний объем оксида празеодима, является перспективным с точки зрения повышения эффективности катода ТОТЭ и адаптации его к условиям работы в интервале средних температур 500–800°С. Применительно к катоду PLCO при таком способе формирования границы электрод/электролит была достигнута величина Rη, равная 0.16 Ом см2 при температуре 650°С на воздухе (соотношение GDС/порообразователь 70/30 и 80/20).
Рис. 5.
Температурная зависимость общего поляризационного сопротивления Rη электрода PLCO, сформированного на поверхности пористого слоя GDC, модифицированного инфильтрацией Pr6O11 (соотношение GDС/порообразователь: 1 – 80/20; 2 – 70/30; 3 – 60/40; 4 – 50/50). В качестве сравнения приведены данные для электрода PLCO, нанесенного на твердоэлектролитную мембрану GDC без использования пористого подслоя (5) [23].
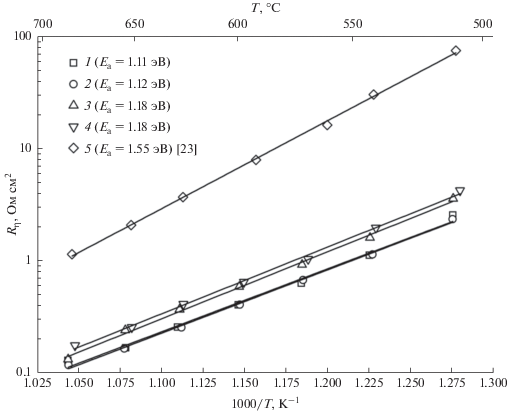
Для оценки полученных результатов проведено их сопоставление с литературными данными для электрохимических катодных систем с различными инфильтрантами в пористом твердоэлектролитном субстрате на основе допированного диоксида церия [11, 27–31]. В табл. 2 приведено сравнение полученных величин Rη для катода на основе PLCO с литературными данными для наиболее известных и перспективных на данный момент катодных материалов при 600°С на воздухе. Выбор этой температуры для сравнения обусловлен тем, что в большинстве цитируемых работ только для нее имеются данные для каждого материала. Можно видеть, что полученные в нашей работе электрохимические характеристики сопоставимы с данными для других перспективных катодных систем. Однако в силу того, что в каждой из приведенных работ методики формирования катода, а также способы измерения электрохимических характеристик различаются (например, большинство исследователей используют в качестве токосъемного слоя проводящие пасты на основе платины или серебра, что может завышать истинные электрохимические характеристики электрода), то можно провести только оценочный анализ электрохимических свойств.
Таблица 2.
Величины поляризационного сопротивления Rη при 600°С на воздухе различных катодных материалов, сформированных методом инфильтрационного введения солевых прекурсоров в пористый субстрат на основе твердого электролита CeO2
Пористый слой | Инфильтрант | Токосъемный слой | Rη, Ом см2 | Ссылка |
---|---|---|---|---|
Ce0.9Gd0.1O1.95 | Pr6O11 | PLCO | 0.41 | Полученный результат |
Ce0.8Sm0.2O1.9 | La0.6Sr0.4CoO3-δ | Платиновая паста | 0.30 | [27] |
Ce0.80Gd0.20O1.9 | Sr0.9Y0.1CoO3-δ | Серебряная паста | 0.10 | [28] |
Ce0.9Gd0.1O1.95 | La0.6Sr0.4Co0.2Fe0.8O3 − δ (LSCF) | LSCF + золотая паста | 0.24 | [29] |
Ce0.8Sm0.2O1.9 | Sm0.5Sr0.5CoO3 – δ | Серебряная паста | 0.19 | [30] |
Ce0.9Gd0.1O1.95 | Pr2NiO4 + δ | LaNi0.6Fe0.4O3 – δ | 0.08 | [31] |
La2NiO4+δ | 0.15 | [11] |
ЗАКЛЮЧЕНИЕ
Разработана методика создания многослойного катода ТОТЭ за счет формирования на поверхности твердого электролита GDC пористой структуры идентичного состава, внедрения в поры электрокатализатора Pr6O11 и последующего нанесения токосъемного слоя с внешней стороны модифицированной поверхности GDC. Изучено влияние соотношения исходных компонентов (GDC и порообразователь) на морфологию формируемого пористого слоя и показано, что наибольшую перспективу с точки зрения формируемой микроструктуры представляет содержание порообразователя от 20 до 40 мас. %. Исследовано влияние морфологии пористого слоя GDC, модифицированного инфильтрационным введением добавки Pr6O11, на электрохимическую активность многослойного электрода на основе PLCO и показано, что оптимальным соотношением GDC/порообразователь, позволяющим достичь максимума электрохимической производительности электрода в РВК, является интервал от 80/20 до 70/30 мас. %. Применение такого подхода позволяет провести активацию реакции восстановления кислорода и снизить величину поляризационного сопротивления электрода на порядок величины по сравнению с характеристиками аналогичного электрода, нанесенного на твердоэлектролитную мембрану GDC без использования пористого подслоя. Достигнутая величина Rη при этом составила 0.16 Ом см2 при 650°С на воздухе. Таким образом, предложенный способ создания катода на основе PLCO с многослойной структурой представляет собой эффективный подход, обеспечивающий достижение высокой электрохимической активности электрода в РВК в интервале средних температур функционирования ТОТЭ.
Список литературы
Connor, P.A., Yue, X., Savaniu, C.D., Price, R., Triantafyllou, G., Cassidy, M., Kerherve, G., Payne, D.J., Maher, R.C., Cohen, L.F., Tomov, R.I., Glowacki, B.A., Kumar, R.V., and Irvine J.T.S., Tailoring SOFC electrode microstructures for improved performance, Adv. Energy Mater., 2018, vol. 8, p. 1800120.
Cassidy, M., Trends in the processing and manufacture of solid oxide fuel cells, Wiley Interdiscip. Rev.: Energy Environ., 2017. vol. 6, p. e248.
Abdalla, A.M., Hossain, S., Azad, A.T., Petra, P.M.I., Begum, F., Eriksson, S.G., and Azad, A.K., Nanomaterials for solid oxide fuel cells: a review, Renewable Sustainable Energy Rev., 2018, vol. 82, p. 353.
Gao, Z., Mogni, L.V., Miller, E.C., Railsback, J.G., and Barnett, S.A., A perspective on low-temperature solid oxide fuel cells, Energy Environ. Sci., 2016, vol. 9, p. 1602.
Kilner, J.A. and Burriel, M., Materials for intermediate-temperature solid-oxide fuel cells, Annu. Rev. Mater. Res., 2014, vol. 44, p. 365.
Chrzan, A., Karczewski, J., Gazda, M., Szymczewska, D., and Jasinski, P., La0.6Sr0.4Co0.2Fe0.8O3 – δ oxygen electrodes for solid oxide cells prepared by polymer precursor and nitrates solution infiltration into gadolinium doped ceria backbone, J. Eur. Ceram. Soc., 2017, vol. 37, p. 3559.
Giuliano, A., Carpanese, M.P., Clematis, D., Boaro, M., Pappacena, A., Deganello, F., Liotta, L.F., and Barbuccia, A., Infiltration, overpotential and ageing effects on cathodes for solid oxide fuel cells: La0.6Sr0.4Co0.2Fe0.8O3 – δ versus Ba0.5Sr0.5Co0.8Fe0.2O3 – δ, J. Electrochem. Soc., 2017, vol. 164, p. F3114.
Ding, D., Li, X., Lai, S.Y., Gerdes, K., and Liu, M., Enhancing SOFC cathode performance by surface modification through infiltration, Energy Environ. Sci., 2014, vol. 7, p. 552.
Yoon, K.J., Biswas, M., Kim, H., Park, M., Hong, J., Kim, H., Son, J., Lee, J., Kim, B., and Lee, H., Nano-tailoring of infiltrated catalysts for high-temperature solid oxide regenerative fuel cells, Nano Energy, 2017, vol. 36, p. 9.
Chrzan, A., Ovtar, S., Jasinski, P., Chen, M., and Hauch, A., High performance LaNi1 –xCoxO3 – δ (x = = 0.4 to 0.7) infiltrated oxygen electrodes for reversible solid oxide cells, J. Power Sources, 2017, vol. 353, p. 67.
Nicollet, C., Flura, A., Vibhu, V., Rougier, A., Bassat, J.M., and Grenier, J.C., La2NiO4 + δ infiltrated into gadolinium doped ceria as novel solid oxide fuel cell cathodes: Electrochemical performance and impedance modelling, J. Power Sources, 2015, vol. 294, p. 473.
Railsback, J.G., Gao, Z, and Barnett, S.A., Oxygen electrode characteristics of Pr2NiO4 + δ-infiltrated porous (La0.9Sr0.1)(Ga0.8Mg0.2)O3 – δ, Solid State Ionics, 2015, vol. 274, p. 134.
Taguchi, H., Chiba, R., Komatsu, T., Orui, H., Watanabe, K., and Hayashi, K., LNF SOFC cathodes with active layer using Pr6O11 or Pr-doped CeO2, J. Power Sources, 2013, vol. 241, p. 768.
Вшивкова, А.И., Горелов, В.П. Активация кислородной реакции пленкой оксида празеодима на платиновом электроде в контакте с электролитом YSZ. Электрохимия. 2016. Т. 52. С. 549. [Vshivkova, A.I. and Gorelov, V.P., Activation of oxygen reaction by praseodymium oxide film on platinum electrode in contact with YSZ electrolyte, Russ. J. Eleсtrochem., 2016, vol. 52. p. 488.]
Ding, X., Zhu, W., Hua, G., Li, J., and Wu, Z., Enhanced oxygen reduction activity on surface-decorated perovskite La0.6Ni0.4FeO3 cathode for solid oxide fuel cells, Electrochimica Acta, 2015, vol. 163, p. 204.
Navarrete, L., Solis, C., and Serra, J.M., Boosting the oxygen reduction reaction mechanisms in IT-SOFC cathodes by catalytic functionalization, J. Mater. Chem. A, 2015, vol. 3, p. 16440.
Lyskov, N.V., Kaluzhskikh, M.S., Leonova, L.S., Mazo, G.N., Istomin, S.Ya., and Antipov, E.V., Electrochemical characterization of Pr2CuO4 cathode for IT-SOFC, Int. J. Hydrogen Energy, 2012, vol. 37, p. 18357.
Sun, C., Li, Q., Sun, L., Zhao, H., and Huo, L., Characterization and electrochemical performances of Pr2CuO4 as a cathode material for intermediate temperature solid oxide fuel cells, Mat. Res. Bull, 2014, vol. 53, p. 65.
Kolchina, L.M., Lyskov, N.V., Petukhov, D.I., and Mazo, G.N., Electrochemical characterization of Pr2CuO4–Ce0.9Gd0.1O1.95 composite cathodes for solid oxide fuel cells, J. Alloys Compounds, 2014, vol. 605, p. 89.
Mazo, G.N., Kazakov, S.M., Kolchina, L.M., Isto-min, S.Ya., Antipov, E.V., Lyskov, N.V., Galin, M.Z., Leonova, L.S., Fedotov, Yu.S., Bredikhin, S.I., Liu, Yi, Svensson, G., and Shen, Z., Influence of structural arrangement of R2O2 slabs of layered cuprates on high-temperature properties important for application in IT-SOFC, Solid State Ionics, 2014, vol. 257, p. 67.
Kolchina, L.M., Lyskov, N.V., Kazakov, S.M., Mazo, G.N., and Antipov, E.V., Drastic change of electrical conductivity in Pr2CuO4 by isovalent La doping, RSC Adv., 2015, vol. 5, p. 91993.
Kolchina, L.M., Lyskov, N.V., Kuznetsov, A.N., Kazakov, S.M., Galin, M.Z., Meledin, A., Abakumov, A.M., Bredikhin, S.I., Mazo, G.N., and Antipov, E.V., Evaluation of Ce-doped Pr2CuO4 for potential application as a cathode material for solid oxide fuel cells, RSC Adv., 2016, vol. 6, p. 101029.
Lyskov, N.V., Kolchina, L.M., Galin, M.Z., and Mazo, G.N., Development of lanthanum-doped praseodymium cuprates as cathode materials for intermediate-temperature solid oxide fuel cells, Solid State Ionics, 2018, vol. 319, p. 156–161.
Khandale, A.P., Pahune, B.S., Bhoga, S.S., Kumar, R.V., and Tomov, R., Development of Pr2 –xSrxCuO4 ± δ mixed ion-electron conducting system as cathode for intermediate temperature solid oxide fuel cell, Int. J. Hydrogen Energy, 2019, vol. 44, p. 15417.
Hayashi, H., Kanoh, M., Quan, C.J., Inaba, H., Wang, S., Dokiya, M., and Tagawa, H., Thermal expansion of Gd-doped ceria and reduced ceria, Solid State Ionics, 2000, vol. 132, p. 227.
Jiang, S. and Wang, W., Fabrication and performance of GDC-impregnated (La,Sr)MnO3 cathodes for intermediate temperature solid oxide fuel cells, J. Electrochem. Soc., 2005, vol. 152, p. A1398.
Zhao, F., Peng, R., and Xia, C., LSC-based electrode with high durability for IT-SOFCs, Fuel Cells Bull., 2008, vol. 2008, p. 12.
Ren, Y., Cheng, Y., Gorte, R.J., and Huang, K., Toward stabilizing Co3O4 nanoparticles as an oxygen reduction reaction catalyst for intermediate-temperature SOFCs, J. Electrochem. Soc., 2017, vol. 164, p. F3001.
Shah, M. and Barnett, S.A. Solid oxide fuel cell cathodes by infiltration of La0.6Sr0.4Co0.2Fe0.8O3 – δ into Gd-Doped Ceria, Solid State Ionics, 2008, vol. 179, p. 2059.
Nicholas, J.D. and Barnett, S.A., Measurements and modeling of Sm0.5Sr0.5CoO3 –x–Ce0.9Gd0.1O1.95 SOFC cathodes produced using infiltrate solution additives, J. Electrochem. Soc., 2010, vol. 157, p. B536.
Nicollet, C., Flura, A., Vibhu, V., Fourcade, S., Rougier, A., Bassat, J.M., and Grenier, J.C., Preparation and characterization of Pr2NiO4 + δ infiltrated into Gd-doped ceria as SOFC cathode, J. Solid State Electrochem., 2016, vol. 20, p. 2071.
Дополнительные материалы отсутствуют.