Электрохимия, 2021, T. 57, № 11, стр. 654-669
Влияние поверхностного слоя бората лития на электрохимические свойства LiNi1/3Mn1/3Сo1/3O2 как материала положительного электрода литий-ионного аккумулятора
К. В. Нефедова a, *, В. Д. Журавлев a, А. М. Мурзакаев b, В. В. Ягодин a, М. В. Кузнецов a, Е. Ю. Евщик c, В. М. Скачков a, О. В. Бушкова a, **
a Институт химии твердого тела УрО РАН
Екатеринбург, Россия
b Институт электрофизики УрО РАН
Екатеринбург, Россия
c Институт проблем химической физики РАН
Черноголовка, Россия
* E-mail: nefedova@ihim.uran.ru
** E-mail: ovbushkova@mail.ru
Поступила в редакцию 05.03.2021
После доработки 09.04.2021
Принята к публикации 12.04.2021
Аннотация
В работе представлены результаты исследования электрохимического поведения материала положительного электрода литий-ионного аккумулятора на основе твердого раствора со слоистой структурой LiNi1/3Mn1/3Сo1/3O2 с поверхностным защитным слоем из аморфного бората лития. Защитное покрытие было сформировано в результате эвтектического инконгруэнтного плавления при 750°С предварительно синтезированного соединения Li3BO3, механически смешанного с порошком LiNi1/3Mn1/3Сo1/3O2. Установлено, что стеклообразный борат лития 3Li2O∙B2O3 формирует на поверхности частиц активного материала островковые структуры, предположительно локализованные на электрохимически активных участках. Оптимальное содержание бората лития, позволяющее добиться стабильного циклирования LiNi1/3Mn1/3Сo1/3O2 в режиме 0.5 С с максимальной разрядной емкостью, составляет 1 мас. %.
ВВЕДЕНИЕ
Растущие требования потребителей к литий-ионным аккумуляторам (ЛИА) выдвигают на первый план необходимость повышения удельной мощности, удельной энергии, устойчивости к циклированию и безопасности [1]. Ключевым компонентом, во многом определяющим поведение аккумулятора в целом, является активный материал положительного электрода [2–4]. Твердые растворы со слоистой структурой на основе никелата лития LiNi1 – x – yMnxCoyO2 (NMC) и LiNi1 – x – yCoxAlyO2 (NCA) постепенно заменяют дорогой, токсичный и взывоопасный кобальтат лития LiCoO2 (LCO) в ЛИА высокой емкости. Они же преимущественно используются и в силовых аккумуляторах для электротранспорта [2], хотя значительно уступают феррофосфату лития LiFePO4 (LFP) и литий-марганцевой шпинели LiMn2O4 (LMO) по безопасности, а LFP – по устойчивости к циклированию, особенно при средних и форсированных режимах заряда–разряда. Более широкое использование этих высокоэнергоемких материалов требует кардинального улучшения их характеристик, в первую очередь обеспечения более высокого уровня безопасности, улучшения кинетики электродных процессов и повышения устойчивости к циклированию [1, 2, 5, 6]. Если основной состав используемых в производстве ЛИА материалов семейства NCA соответствует формуле LiNi0.8Co0.15Al0.05O2, обеспечивающей оптимальные свойства, то в твердых растворах семейства NMC соотношение никеля, марганца и кобальта можно варьировать в широких пределах, существенно влияя на стоимость и целевые свойства материала [7–9]. Кроме того, для стабилизации NMC с высоким содержанием никеля часто применяют создание структур “ядро–оболочка” (core–shell) или градиентных твердых растворов [7, 9, 10]. Твердые растворы семейства NMC обладают более высокой термической устойчивостью (относительно LiCoO2 и NCA) и деградируют медленнее NCA [2, 5, 9]. Благодаря этим преимуществам, доля NMC в производстве ЛИА в 2016 г. составила 26%, а в 2025, согласно прогнозу, вырастет до 41% [11, 12].
Первым коммерциализованным материалом семейства NMC стал состав LiNi1/3Mn1/3Co1/3O2 (NMC-111). Oн до сих пор остается востребованным у производителей аккумуляторов, наряду с LiNi0.5Mn0.3Co0.2O2 (NMC-532) [5, 13], хотя наблюдается смещение интереса к более дешевым составам с уменьшенным содержанием кобальта и повышенным содержанием никеля. Преимуществами NMC-111 являются более высокая устойчивость к циклированию и хорошие динамические характеристики в сочетании с наиболее высокой безопасностью [2, 5, 9, 10, 14, 15], что особенно важно для силовых ЛИА. Удельная емкость твердых растворов семейства NMC определяется интервалом потенциалов; для NMC-111 она варьируется от ~150 мА ч/г (2.5–4.3 В [7]) до 200 мА ч/г (2.8–4.6 В) [14], однако повышение емкости при повышении зарядного потенциала сопровождается более быстрой деградацией электрода из-за разрушения кристаллической структуры [9]. За практическое значение для NMC-111 в аккумуляторах массового выпуска обычно принимают 160–170 мА ч/г [5, 10, 13].
Электрохимические свойства активного материала в значительной степени зависят от состояния поверхности его гранул, всегда покрытых поверхностными пленками, ограничивающими миграцию ионов лития и перенос заряда через границу раздела фаз [16]. На поверхности гранул активного материала изначально существует естественный поверхностный слой из примесей и продуктов частичной деградации, сформировавшийся в ходе синтеза и при хранении. При контакте с электролитом протекают спонтанные химические реакции между этим слоем (а также самим активным материалом), с одной стороны, и компонентами электролита – с другой; нерастворимые продукты химического взаимодействия также локализуются на поверхности частиц. Далее в ходе работы аккумулятора происходит частичное разрушение кристаллической структуры активного материала с выделением на поверхности твердофазных продуктов деградации, а также имеет место окислительное разложение электролита на его поверхности, также приводящее к образованию нерастворимых продуктов. Результатом всех этих процессов является формирование катодного интерфейсного слоя (cathode-electrolyte interface, или CEI) [9, 17]. К настоящему времени установлено, что деградационные явления в катодном полуэлементе вносят основной вклад в ограничение срока службы ЛИА [17].
Модификация поверхности активного материала (наряду с оптимизацией состава электролитного раствора) является эффективным способом значительно улучшить его электрохимическое поведение и термическую стабильность, повысить устойчивость к циклированию и в конечном итоге продлить срок службы ЛИА [4, 7, 8, 18]. Поэтому поиск подходящих материалов для защиты поверхности и разработка наиболее эффективных технологий их нанесения вызывают большой интерес. Многочисленные исследования подтверждают, что модификация поверхности позволяет избежать побочных реакций между активным материалом и электролитом за счет полного устранения или сведения к минимуму площади их непосредственного контакта [7]. К числу наиболее популярных методов защиты поверхности относится нанесение тонкого слоя простых оксидов (Al2O3, B2O3, TiO2, ZrO2 и т.п.) [4, 13, 18]. Этот прием оказался очень эффективным в случае LCO: механически и химически стабильный материал защитного покрытия позволил сгладить структурные изменения и минимизировать побочные реакции с электролитным раствором даже при увеличении зарядного потенциала [13]. Тот же подход разрабатывается и для NMC и NCA, однако пока ни один производитель не принял эту стратегию [5].
Многие исследователи пытались покрыть частицы NMC-111 простыми оксидами и получили обнадеживающие результаты [4, 13, 18–30]. Однако такие материалы покрытия часто являются плохими электронными и ионными проводниками и препятствуют проникновению Li+ в зону электрохимической реакции, что приводит к повышенной поляризации и снижению извлекаемой емкости активного материала. В последнее время интерес исследователей смещается к использованию соединений, обладающих литий-ионной или электронной проводимостью. Для NMC-111 в качестве защитных покрытий были апробированы твердые литий-проводящие электролиты Li3VO4 [31], Li2ZrO3 [32], LiF [33]; эти химически устойчивые соединения могут не только защитить активный материал от электролитного раствора, но и обеспечить пути для транспортировки ионов Li+. Электропроводящее покрытие, значительно повысившее устойчивость материала при форсированных режимах заряда и разряда, было получено путем смешивания порошка NMC-111 с сахарозой или крахмалом с последующим отжигом выше 700°С [34].
Среди твердых литий-проводящих электролитов, пригодных для создания защитного слоя, особое внимание привлекают литий-боратные стекла Li2O⋅nB2O3 (LBO). Эти материалы являются хорошими литий-ионными проводниками, а их расплавы обладают сравнительно невысокой вязкостью и хорошо смачивают порошки активных материалов, равномерно распределяясь по их поверхности [35–37]. Их электрохимическая устойчивость позволяет использовать такие покрытия для 4В материалов положительного электрода [38]. Температура термообработки литий-боратного покрытия сравнительно невысока и обычно составляет около 500°С [39]. Покрытия из LBO показали свою эффективность для LiMn2O4 [40–42], LiNi0.5Mn1.5O4 [43], LiNi0.8Co0.2O2 [44], Li1.2Ni0.2Mn0.6O2 [45] и др. Некоторые авторы [39, 46, 47] использовали LBO состава Li2B4O7 для модификации поверхности NMC-111 и показали, что такая защита обеспечивает значительное повышение разрядной емкости и кулоновской эффективности не только при комнатной, но и при отрицательных температурах, а также улучшает электродную кинетику, минимизирует побочные химические взаимодействия в ячейке и эрозию под влиянием HF. Значительное улучшение электрохимического поведения NMC-111 достигалось при введении 3 мас. % Li2B4O7 [39, 46, 47]. Однако поскольку в цитированных работах авторы выбрали растворный способ нанесения покрытия с последующим отжигом при 500°C, тогда как температура плавления соединения Li2B4O7 составляет 917 ± 2°C [48], то состав Li2B4O7 (отношение Li : B = 1 : 2) является скорее номинальным; в реальности защитное покрытие, по-видимому, представляло собой смесь фаз.
Нужно отметить, что состав боратов лития может варьироваться в широких пределах. Так, для защиты Li1.2Ni0.2Mn0.6O2 в работе [45] был взят более богатый литием состав LiBO2 с отношением Li : B = 1 : 1, а для LiMn2O4 авторы [40] остановили свой выбор на еще более насыщенном литием борате Li3BO3 (Li : B = 3 : 1). На наш взгляд, именно этот состав является наиболее перспективным материалом для создания эффективного защитного покрытия на поверхности гранул NMC-111. Борат лития Li3BO3 – это один из немногих материалов, чья молярная масса (79.694) меньше, чем у NMC-111 (96.459), а удельное содержание лития в 3.7 раза выше, чем в NMC. Низкая температура плавления кристаллического Li3BO3 (662°С, по данным [49], или 715°С, по данным [48]) способна обеспечить растекание расплава микроэвтектики по поверхности активного материала, способствуя формированию защитного слоя. Известно, что кристаллический Li3BO3 является литий-ионным проводником с энергией активации 170 кДж/моль [50]. Хотя литий-ионная проводимость в области низких температур выше у другого бората лития – γ-LiBO2 [51], однако это соединение имеет существенно более высокую температуру плавления (849°С [48]); это заставляет остановить свой выбор на Li3BO3.
В настоящей статье методом синтеза в реакциях горения получен активный материал положительного электрода NMC-111 и исследовано состояние нанесенного на его поверхность защитного слоя, образованного расплавом заранее синтезированного стехиометрического соединения Li3BO3. Изучено электрохимическое поведение полученного материала в макетах катодного полуэлемента ЛИА при комнатной температуре при варьировании содержания LBO (1 и 3 мас. %) и дана оценка эффективности выбранного метода защиты поверхности NMC-111.
ЭКСПЕРИМЕНТАЛЬНАЯ ЧАСТЬ
Материалы
Порошок твердого раствора LiNi1/3Mn1/3Co1/3O2 (далее обозначенный как NMC) был получен методом синтеза в реакциях горения по методике, описанной в [52]. Исходными веществами служили водные нитраты никеля и кобальта Ni(NO3)2⋅6H2O (99.0%) и Co(NO3)2⋅6H2O (99.0%) (“Уральский завод химических реактивов”, Россия), марганец углекислый основной водный MnCO3⋅mMn(OH)2⋅nH2O (“Baltic Cо.”, Россия) с предварительно установленным содержанием марганца и литий углекислый Li2CO3 (99.5%, ООО “НПФ Невский химик”, Россия). В качестве топлива использовали водную лимонную кислоту H3C6H5O7∙H2O (99.8%, “Citrobel”, Россия) и аминоуксусную кислоту (глицин) H2N(CH2)COOH (98.5%, “Kamhimkom”, Россия). Для приготовления растворов реагентов использовали бидистиллированную воду. Синтез вели в расчете на получение 100 г материала.
Борат лития Li3BO3 синтезировали твердофазным методом из борной кислоты H3BO3 (99.5%, “УНИХИМ”, Россия) и лития углекислого Li2CO3 (99.5%, ООО “НПФ Невский химик”, Россия) по уравнению:
(1)
$\begin{gathered} 3L{{i}_{2}}C{{O}_{3}} + {\text{ }}2{{H}_{3}}B{{O}_{3}} = {\text{ }} \\ {\text{ = }}\,\,2L{{i}_{3}}B{{O}_{3}} + {\text{ }}3{{H}_{2}}O{\text{ }} + {\text{ }}3C{{O}_{2}}. \\ \end{gathered} $Реакционную смесь загружали в контейнер из оргстекла и проводили помол с помощью мельницы со смещенным центром тяжести (“пьяная бочка”) в течение 1 ч. Затем смесь отжигали в корундовых тиглях при 600°С в течение 5 ч, после чего помол (1 ч) повторяли и проводили повторный отжиг при 600°С в течение 20 ч. Синтезированный продукт охлаждали с печью до комнатной температуры, после чего подвергали помолу в течение 2 ч. В результате был получен тонкодисперсный порошок белого цвета с удельной поверхностью 1.67 м2/г. Рентгенофазовый анализ подтвердил его однофазность и принадлежность к моноклинной сингонии с параметрами, соответствующими CARD ASTM 18-718.
Для получения композита с содержанием LBO 3 мас. % 1 г LBO смешивали в мельнице с 32 г NMC в течение 2 ч (далее этот состав обозначен как NMC/LBO (3%)). Композит с содержанием LBO 1 мас. % (или NMC/LBO (1%)) готовили путем разбавления полученной смеси, для чего смешивали 10 г порошка NMC/LBO (3%) с 20 г NMC в течение 2 ч с помощью мельницы. Термообработку смесей проводили при 750°С в течение 5 ч с последующим медленным охлаждением до комнатной температуры. После отжига образцы подвергали помолу в шаровой мельнице в течение 1 ч; затем термообработку повторяли в том же режиме для лучшего растекания микроэвтектики, обогащенной боратом лития, по кристаллитам NМС.
Методы
Фазовый состав полученных продуктов определяли при комнатной температуре методом рентгеновской дифракции с помощью дифрактометра “ShimadzuXRD7000” (Shimadzu, Япония) (CuKα-излучение, 2θ = 10°–80°, шаг 0.03°). Для идентификации фаз использовали базу порошковых стандартов PDF2 (ICDD, США, Release 2016). Параметры кристаллической структуры продуктов определяли методом полнопрофильного анализа Ритвельда с использованием программы Fullprof [53]. Удельную поверхность продуктов определяли методом BET по десорбции азота при нагревании с использованием установки “TriStar 3000 V 6.03A” (Micromeritics, США). Пикнометрическую плотность продуктов определяли с помощью гелиевого пикнометра “Micromeritics Accu Pyc II 1340” (Micromeritics, США) с использованием измерительной камеры объемом 1 см3. Термический анализ образцов выполняли с помощью термоанализатора STA 449 F3 Jupiter (NETZSCH, Германия) в интервале температур 30–800°С на воздухе в режиме нагрева со скоростью 10°C/мин.
Морфологию и микроструктуру полученных порошков исследовали методом сканирующей электронной микроскопии (СЭМ) с помощью электронного микроскопа “JEOL JSM 6390 LA” (JEOL Ltd., Япония) с увеличением от 500 до 10 000, а также методом просвечивающей электронной микроскопии (ПЭМ) с использованием прибора “JEM-2100” (JEOL Ltd., Япония) с катодом LaB6 при ускоряющем напряжении 200 кВ (разрешение по точкам 0.19 нм, по линиям – 0.14 нм). Обработку и анализ снимков ПЭМ производили с помощью программы Gatan Digital Micrograph версии 3.9.3 (Gatan, США).
Съемка рентгеновских фотоэлектронных спектров (РФЭС) выполнена на электронном спектрометре VG ESCALAB MK II (VG Scientific, Великобритания) с прецизионным манипулятором. Последний позволял позиционировать образцы под рентгеновским пучком и анализатором вылетевших фотоэлектронов, а также поворачивать образец относительно рентгеновского источника и анализатора. Угол θ между поверхностью образца и осью анализатора варьировали (90° и 20°). Для возбуждения фотоэмиссии электронов с остовных (внутренних) и валентных состояний использовалось немонохроматическое MgKα-излучение (Ehν = 1253.6 эВ). РФЭС-анализ включал в себя запись обзорных спектров поверхности порошков и спектров внутренних электронных уровней основных элементов. Анализируемая площадь на поверхности образцов составляла ~4 мм2. Глубина РФЭС-анализа не превышала 3–5 нм при θ = 90° и 1–2 нм при θ = 20°. Погрешность в определении энергии связи электронных уровней составляла 0.1 эВ. Вакуум в камере анализатора во время измерений поддерживался на уровне 1 × 10–8 Па.
Электрохимические измерения
Для получения электродной дисперсии исследуемые порошки NMC, NMC/LBO (1%) и NMC/LBO (3%) смешивали с ацетиленовой сажей “Timcal” (MTI Corporation, США) и 10%-ным раствором поливинилиденфторида (GELON, КНР) в N-метил-2-пирролидоне (NMP) (Sigma-Aldrich, США); соотношение активного вещества, сажи и полимерного связующего составляло 80 : 10 : 10. Готовую электродную дисперсию наносили на токовый коллектор – алюминиевую фольгу толщиной 20 мкм. Далее электроды подвергали горячей прокатке, а затем сушили в вакууме при 120°С в течение 12 ч для полного удаления остаточного растворителя (NMP) и следов воды. Площадь готового рабочего электрода составляла 2.25 см2 при загрузке активного вещества 3–6 мг/см2.
Исследование электрохимического поведения NMC и композитов NMC/LBO (1%) и NMC/LBO (3%) проводили в герметичных двухэлектродных ячейках Li|Li+|NMC в корпусе из ламинированной алюминиевой фольги, собранных в боксе MBraun UNILAB c контролируемой аргоновой атмосферой (содержание воды и кислорода не превышало 1 ppm). Противоэлектродом и одновременно электродом сравнения служила литиевая фольга (99.9%, Alfa Aesar), накатанная на токовый коллектор из медной фольги. В качестве электролита использовали 1 M раствор LiPF6 в смеси этиленкарбоната (EC) и этилметилкарбоната (EMC) (1 : 1, об.) (Sigma-Aldrich, США) с сепаратором Celgard 2300. Остаточное содержание воды в электролите не превышало 30 ppm.
Гальваностатическое циклирование и циклическая вольтамперометрия выполнены при комнатной температуре с помощью многоканального потенциостата P-20X80 (Elins, Россия). Интервал гальваностатического циклирования составлял 2.7–4.2 В (отн. Li0/Li+); нормированный ток заряда и разряда варьировали от 0.1 до 0.5 С.
РЕЗУЛЬТАТЫ И ОБСУЖДЕНИЕ
Фазовый состав и морфология исследуемых материалов
Согласно данным рентгенофазового анализа (РФА), полученный твердофазным синтезом LBO, предназначенный для нанесения защитного покрытия на поверхность NMC, представлял собой однофазный продукт заданного состава (рис. 1а).
Рис. 1.
Рентгенограммы образцов Li3BO3 (а), NMC (б), NMC/LBO (1%) (в) и NMC/LBO (3%) (г), обработанные по методу Ритвельда. Точки – полученные экспериментальные значения интенсивности, черная линия – рассчитанная модель кристаллической структуры, внизу разностная кривая между экспериментом и моделью.
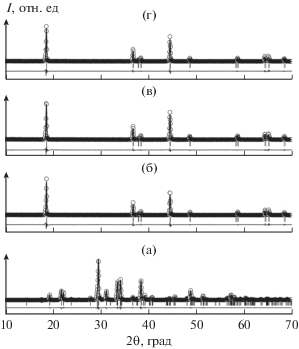
В результате синтеза в реакциях горения был получен однофазный твердый раствор NMC (рис. 1б) с параметрами кристаллической ячейки, близкими к литературным данным [28] (табл. 1). Величины коэффициентов R003/104 и R(I(102) + I(006))/I(101) (табл. 1), рассчитанных как соотношение интенсивностей соответствующих рефлексов [30], подтверждают совершенство гексагональной структуры и минимальную степень миграции лития в позиции никеля, соответственно.
Таблица 1.
Характеристика исследуемых образцов
Образец | Параметры решетки | Удельная поверхность (по методу БЭТ), м2/г | Пикнометриче-ская плотность, г/см3 |
|||
---|---|---|---|---|---|---|
a, Å | c, Å | R003/104 | R (I(102) + + I(006))/I(101) | |||
NMC | 2.858 ± 0.001 | 14.233 ± 0.001 | 1.4 | 0.49 | 2.69 ± 0.12 | 4.650 ± 0.004 |
NMC/LBO (1%) | 2.858 ± 0.001 | 14.234 ± 0.001 | 1.3 | 0.47 | 2.87 ± 0.24 | 4.620 ± 0.007 |
NMC/LBO (3%) | 2.857 ± 0.001 | 14.224 ± 0.001 | 1.6 | 0.46 | 1.58 ± 0.04 | 4.473 ± 0.003 |
NMC [28] | 2.856 | 14.229 | 2.0 | ‒ | ‒ | ‒ |
Для определения оптимального температурного режима нанесения покрытия LBO на поверхность гранул NMC предварительно был выполнен термический анализ модельной смеси состава NMC–LBO (10 мас. %) до и после отжига при 800°С (5 ч) с последующей закалкой. Термограммы образцов приведены на рис. 2. Как видно из рисунка, на кривой TG исходной смеси фиксируется убыль массы вследствие удаления газообразного продукта реакции (CO2). Кривые ДСК для обоих образцов содержат один эндотермический пик с температурой начала эффекта 695°С, отвечающей плавлению эвтектики в системе NMC–LBO. Это несколько ниже температуры плавления наиболее легкоплавкого из двух соединений – LBO (согласно [48], индивидуальная фаза Li3BO3 инконгруэнтно плавится при 715°С). Полученные результаты позволяют выбрать температуру 750°С как оптимальную для термообработки при нанесении защитного покрытия LBO, поскольку в этих условиях будет достигнуто полное плавление фазы LBO с вероятным растеканием плавня по поверхности частиц NMC.
Дифрактограммы композитов NMC/LBO (1%) и NMC/LBO (3%), полученных в результате отжига соответствующих реакционных смесей при 750°С, приведены на рис. 1в, 1г, а их характеристики суммированы в табл. 1. Как следует из полученных данных, добавление 1 мас. % LBO не фиксируется на дифрактограмме продукта и практически не сказывается на структурных параметрах NMC; увеличение массы боратного покрытия до 3 мас. % сопровождается незначительным изменением постоянной с кристаллической решетки твердого раствора.
Синтезированный в реакциях горения NMC представлял собой тонкодисперсный порошок, состоящий из субмикронных частиц, собранных в агрегаты (рис. 3а). Нанесение защитного покрытия и дополнительный помол приводят к повышению дискретности частиц в образце NMC/LBO (1%) (рис. 3б), в результате чего его удельная поверхность несколько возрастает (табл. 1). Образец NMC/LBO (3%) содержит несколько более крупные агрегаты частиц (рис. 3в); можно предположить, что из-за большего количества расплава-связки они меньше разрушаются в одинаковых условиях помола после отжига. В итоге удельная поверхность композита NMC/LBO (3%) значительно меньше, чем у двух других образцов (табл. 1). Величины пикнометрической плотности, приведенные в табл. 1, отражают увеличение содержания более легкого LBO в составе композитного материала. При этом снова при добавлении 1% LBO пикнометрическая плотность уменьшается лишь незначительно, тогда как 3% LBO оказывают на нее намного более сильный эффект (табл. 1).
Рис. 3.
Электронные микрофотографии порошков NMC (а) и композитов NMC/LBO (1%) (б) и NMC/LBO (3%) (в).
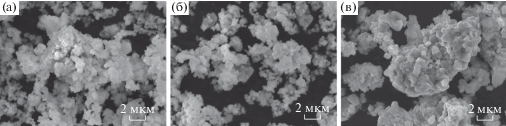
Зная плотность LBO (2.15 г/см3) и удельную поверхность порошка NMC (≈4.6 м2/г), можно рассчитать ожидаемую толщину защитного покрытия. Для композита NMC/LBO (1%) она составляет 1.7 нм, а для NMC/LBO (3%) – 5.2 нм.
Исследование поверхностных слоев
Результаты исследования поверхностных защитных слоев методом просвечивающей электронной микроскопии (ПЭМ) в темном поле приведены на рис. 4. На изображении с атомным разрешением непокрытой боратом лития частицы NMC (рис. 4а) видны явные признаки ее кристаллической природы. Быстрое фурье-преобразование (БФП) (врезка на рис. 4а) подтверждает кристаллическую природу частицы. Детали картины размыты из-за “шумов”, вызванных фоновым сигналом аморфной углеродной пленки (подложки, на которой лежит исследуемая частица), и инструментальных шумов. После наложения маски, фильтрации шумов всей картины и обратного преобразования Фурье на полученном изображении видна атомная структура частицы (рис. 4б).
Рис. 4.
Электронные микрофотографии порошков: (а) NMC (врезка – БФП), (б) изображение NMC, отфильтрованное от шумов, (в) NMC/LBO (1%) (врезка – БФП), (г) изображение NMC/LBO (1%), отфильтрованное от шумов, (д) NMC/LBO (3%) (врезка – БФП), (е) изображение NMC/LBO (3%), отфильтрованное от шумов.
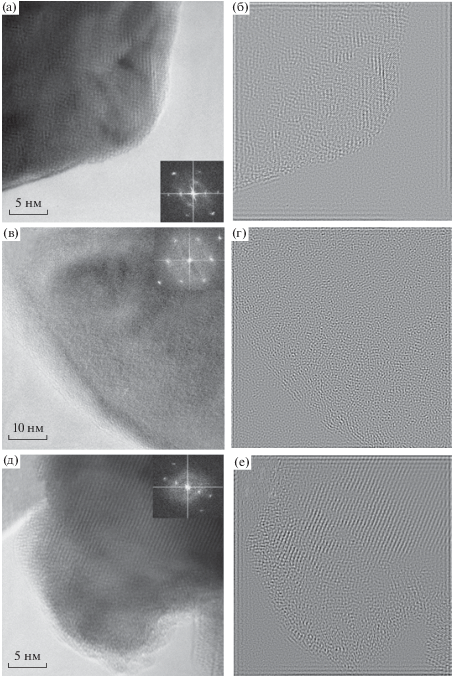
Аналогичным образом были обработаны и проанализированы ПЭМ-изображения для частиц с нанесенным покрытием из LBO в количестве 1 и 3 мас. % (рис. 4в–4е). Как видно из рисунков, более тонкое покрытие получено для композита NMC/LBO (1%) – его толщину можно оценить в 8–10 нм. Это примерно в пять раз выше расчетной величины, приведенной выше. Для композита NMC/LBO (3%) также нет согласия между экспериментально оцененной и расчетной величинами: толщина покрытия на рис. 4д, 4е явно больше 10 нм, тогда как расчетная величина составляет ≈5 нм (см. выше). При этом слой LBO в композите NMC/LBO (3%) очень неравномерен по толщине (рис. 4д, 4е). Суммируя полученные результаты, можно предположить островковый характер распределения слоя LBO по поверхности частиц NMC. При этом в обоих образцах композитов поверхностный слой LBO, как и ожидалось, имеет аморфную структуру (результат инконгруэнтного плавления соединения Li3BO3 [48] с образованием, вероятно, литий-боратного стекла 3Li2O∙B2O3).
Одна из главных проблем при нанесении защитного покрытия на поверхность активного материала положительного электрода – это получение сплошного и равномерного по толщине слоя. Поэтому в выполненный нами далее анализ методом рентгеновской фотоэлектронной спектроскопии (РФЭС) входили не только определение концентраций элементов (в ат. %) на поверхности порошков NMC и композитов NMC/LBO, но и оценка сплошности защитного покрытия из литий-боратного стекла. Поскольку глубина РФЭС-анализа не превышает 3–5 нм, то при толщине слоя 8–10 нм и более (см. выше) сигнал от ядра частиц, состоящих из фазы NMC, не должен достигать поверхности при условии, что слой LBO слошной. В таком случае линии никеля, марганца и кобальта должны отсутствовать в фотоэлектронных спектрах композитных образцов NMC/LBO. Однако оказалось, что все данные элементы регистрируются методом РФЭС в спектрах всех трех исследуемых образцов – как индивидуального NMC, так и композитов NMC/LBO (1%) и NMC/LBO (3%). Это дает основания заключить, что поверхность гранул NMC лишь частично покрыта защитным слоем литий-боратного стекла даже при его содержании в количестве 3 мас. %.
На рис. 5 приведены гистограммы содержания химических элементов в поверхностных слоях исследуемых образцов (углерод, всегда обнаруживаемый на поверхности исследуемых образцов, в расчетах не учитывали). Для индивидуального NMC-111, в соответствии с его химической формулой, содержание элементов отвечает следующим значениям: O – 50 ат. %, Li – 25 ат. %, Ni, Mn, Co – по 8.33 ат. %. Однако из представленных на рис. 5а данных следует, что в случае индивидуального NMC анализ методом РФЭС дает результаты, отличные от формульного состава: содержание кислорода в поверхностных слоях на ≈4 ат. % выше, а лития – на ≈5 ат. % ниже стехиометрического. Кроме того, концентрации переходных металлов, которые должны быть одинаковыми, различаются между собой и отклоняются от расчетных значений. Если для кобальта это отклонение невелико (7.4 вместо 8.3 ат. %), то содержание никеля в 1.9 раза меньше, а марганца – в 1.7 раза выше номинального значения. При этом суммарное содержание атомов 3d-металлов составляет 26.1 ат. %, что несколько выше теоретического значения 25 ат. %. Полученные результаты позволяют сделать несколько важных выводов о состоянии поверхности порошка NMC до нанесения защитного слоя: 1) поверхностный слой несколько обеднен литием (по-видимому, вследствие высокой летучести этого элемента в условиях отжигов); 2) частицы индивидуального NMC-111 с обогащенной марганцем и обедненной никелем поверхностью в действительности представляют собой либо структуры типа ядро/оболочка, либо градиентные твердые растворы. Последнее заключение представляет большой практический интерес и заслуживает более детального исследования, выходящего за рамки данной работы.
Рис. 5.
РФЭС-оценка состава поверхности порошка NMC до и после нанесения слоя LBO: NMC (а), NMC/LBO (1%) (б) и NMC/LBO (3%) (в).
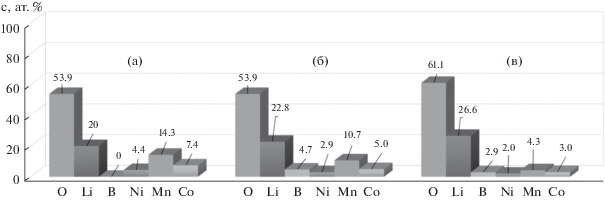
Согласно полученным данным, после нанесения 1 и 3 мас. % LBO (рис. 5б, 5в) поверхностная концентрация бора составляет 4.7 и 2.9 ат. %, а концентрация лития приближается к номинальным значениям и равна 22.8 и 26.6 ат. %, соответственно. При этом по мере увеличения содержания LBO (и утолщения его слоя) доля d-катионов на гистограмме закономерно снижается (рис. 5б, 5в).
Если изменение содержания кислорода в поверхностных слоях NMC в результате нанесения LBO вполне логично, то антибатная зависимость концентрации бора от содержания LBO требует объяснения. Возможной причиной отклонений может быть карбонизация поверхности материала при синтезе, хранении и/или в процессе анализа [7, 18]. Для ответа на этот вопрос были исследованы РФЭС-спектры внутренних уровней C1s, O1s и B1s для всех исследуемых образцов. Результаты приведены на рис. 6.
Рис. 6.
РФЭС-спектры C1s (а), O1s (б), B1s (в) и Li1s (г) поверхности порошков NMC, NMC/LBO (1%) и NMC/LBO (3%).
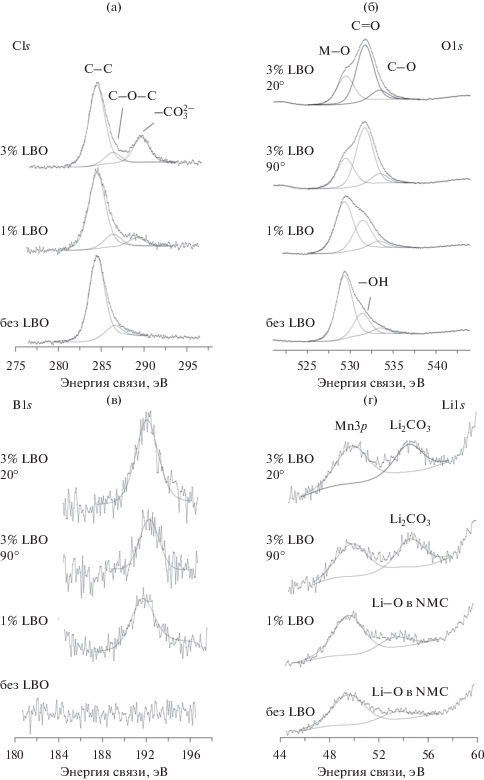
В спектрах C1s-углерода поверхности порошков NMC/LBO (рис. 6а), помимо линии при 284.6 эВ от углеводородных адсорбатов, всегда присутствующих на поверхности, имеются максимумы в области 288–290 эВ, которые с большой долей уверенности можно связать с карбонатом или гидрокарбонатом лития [54]. При этом, если в композите с 1% LBO максимум при 288 эВ слабо выражен, то в композите с 3% LBO линия при 289.7 эВ четко определена и имеет высокую интенсивность.
В спектрах O1s-кислорода (рис. 6б) у индивидуального NMC полоса при 529.2 эВ относится собственно к NMC, а максимум в области 531.5 – к OH–-группам на поверхности сложного оксида. После нанесения на поверхность частиц NMC слоя LBO в спектрах кислорода полосы от гидроксильных групп исчезают и появляются составляющие от LBO (~531 эВ) и карбоната лития (~532.3 эВ).
В спектрах B1s-бора (рис. 6в) каких-либо изменений при увеличении концентрации LBO в композите не происходит; наблюдается единственный максимум при 192.0 эВ, который отвечает LBO.
В спектрах Li1s-лития (рис. 6г) после нанесения на поверхность NMC слоя бората лития ожидаемо возрастает интенсивность этого максимума (~54 эВ). Для композита NMC/LBO (3%) спектр записывался для двух углов: нормаль к поверхности и касательный угол к поверхности образца (во втором случае возрастает поверхностная чувствительность метода РФЭС). Увеличение интенсивности максимума Li1s при касательном угле записи спектра указывает на доминирование данного элемента на поверхности относительно других металлов (Mn, Ni и Co). Положение Li1s-максимума варьируется от 53.3 эВ для непокрытого образца и композита NMC/LBO (1%) до 54.5–54.7 эВ для композита NMC/LBO (3%). Это указывает на присутствие в максимуме нескольких составляющих, отнесенных к литию в составе NMC, LBO и карбонате лития. Последняя составляющая становится доминирующей в образце с 3% LBO. Это согласуется со сделанным выше выводом об образовании на воздухе на поверхности композитов NMC/LBO карбонатных соединений, особенно ярко выраженном для 3% LBO. Именно этой причиной, по-видимому, вызвано и непропорциональное уменьшение поверхностной концентрации бора в наиболее богатом LBO композите. Таким образом, можно заключить, что при увеличении концентрации LBO до 3% происходит частичное выделение лития из LBO с образованием карбоната или гидрокарбоната лития на поверхности композита на воздухе. По всей вероятности, карбонизация имела место в процессе изготовления композита: известно, что Li3BO3 в интервале 500–650°С является хорошим сорбентом для CO2 [54]. В этой связи, необходимо в дальнейшем обратить особое внимание на условия синтеза композитов NMC/LBO во избежание нежелательных процессов карбонизации.
Из анализа спектров Ni2p, Co2p и Mn2p (не показаны на рисунках) следует, что нанесение поверхностного слоя LBO практически не отразилось на состоянии никеля, кобальта и марганца. Поэтому можно предположить, что LBO не вступает в реакцию с NMC в ходе отжига при 750°С при получении композитов NMC/LBO.
Электрохимическое поведение композитов NMC/LBO
Для первичной оценки влияния покрытия из LBO на процессы внедрения/экстракции лития в NMC-111 была использована циклическая вольтамперометрия (ЦВА). Измерения проводили в диапазоне напряжений 2.5–4.2 В (отн. Li0/Li+) при скорости развертки 0.1 мВ/с. Для всех трех исследуемых образцов на кривых ЦВА зарегистрирован один окислительно-восстановительный процесс. Для образца без покрытия зарегистрированы пики при потенциалах ~3.56 В в катодной и ~4.05 В в анодной областях (рис. 7). Для образца NMC/LBO (3%) эти значения практически не изменяются, а для NMC/LBO (1%) незначительно сдвигается пик в катодной области. Зарегистрированные пики отвечают процессам перехода Ni2+/Ni4+ [55]. Отсутствие каких-либо дополнительных пиков на вольтамперограммах свидетельствует о том, что слои LBO не принимают участия в окислительно-восстановительной реакции в диапазоне потенциалов 2.5–4.5 В (отн. Li0/Li+).
Рис. 7.
Циклические вольтамперограммы образцов NMC, NMC/LBO (1%) и NMC/LBO (3%) (скорость развертки 1 мВ/с).
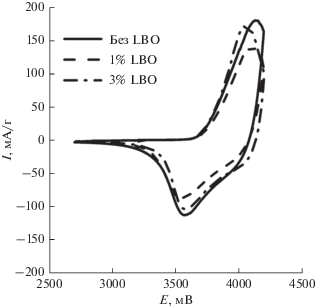
Зарядно-разрядные кривые первого цикла для NMC без покрытия и композитов с 1 и 3% LBO приведены на рис. 8. Начальная зарядная емкость для образца без покрытия составляет 150.7 мА ч/г при разрядной емкости 155.6 мА ч/г. Для образца с 1% LBO зарядная емкость первого цикла существенно выше и составляет 177.6 мА ч/г, а разрядная емкость равна 163.9 мА ч/г. В случае 3% LBO зарядная и разрядная емкости составляют 145.2 и 134.2 мА ч/г соответственно. Можно предположить, что снижение емкости у композита NMC/LBO (3%) может быть обусловлено карбонизацией его поверхности. Кулоновская эффективность обоих образцов с защитным покрытием в первом цикле составляет 92.3%. Следует отметить, что для них наблюдается некоторое снижение напряжения разряда по сравнению с индивидуальным NMC.
Рис. 8.
Зарядно-разрядные кривые первого цикла для электрохимических ячеек Li|Li+|NMC (нормированный ток заряда и разряда 0.1 С).
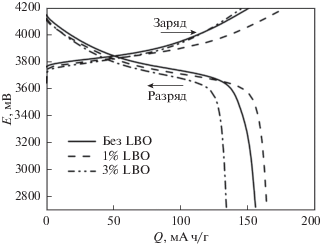
Как известно, кристаллический борат лития Li3BO3 обладает хорошей литий-ионной проводимостью [46], как и литий-боратные стекла. Поэтому слой LBO на поверхности гранул NMC облегчает интеркаляцию и деинтеркаляцию лития, что сводит к минимуму поляризацию электрода в ходе заряда–разряда. Это должно положительно сказываться на скорости переноса заряда и на обратимой емкости композитов NMC/LBO. Кроме того, слой LBO способен защитить поверхность частиц от непосредственного контакта с жидким электролитом и нежелательных побочных реакций, продлевая срок службы электрода.
Способность выдерживать заряд и разряд при повышенных значениях нормированного тока является важной характеристикой активного материала, особенно при использовании в силовых ЛИА. В данной работе исследовали влияние величины нормированного тока заряда–разряда на удельную разрядную емкость для материалов на основе NMC с защитным покрытием и без него. Циклирование проводили в диапазоне потенциалов 2.5–4.2 В (отн. Li0/Li+) при значениях нормированного тока заряда и разряда 0.1, 0.2 и 0.5 С с возвратом к скорости 0.1 С (рис. 9), после чего ячейки подвергали длительному циклированию в режиме 0.5 С (рис. 10).
Рис. 9.
Зависимость разрядной емкости от номера цикла при различных значениях нормированного тока разряда для электрохимических ячеек Li|Li+|NMC.
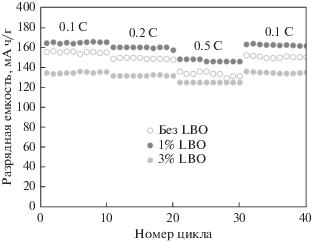
Рис. 10.
Зависимость разрядной емкости и кулоновской эффективности от номера цикла (сквозная нумерация) для электрохимических ячеек Li|Li+|NMC (нормированная плотность тока разряда 0.5 С).
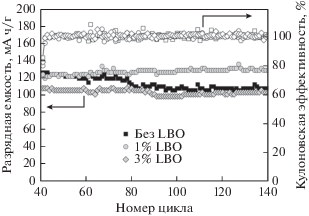
Как видно из рис. 9, разрядная емкость электрода на основе композита NMC/LBO (1%) на протяжении всех 40 циклов превышает значения, полученные для других образцов. В табл. 2 представлены значения разрядной емкости и кулоновской эффективности (КЭ) на 10, 20, 30 и 40 циклах при плотностях нормированного тока разряда 0.1, 0.2, 0.5 и снова 0.1 С соответственно. Как видно из представленных данных, образцы NMC без покрытия и с 3% LBO обладают очень хорошей обратимостью процессов внедрения–экстракции лития (кулоновская эффективность составляет более 99% вплоть до 40-го цикла заряда–разряда). Композит NMC/LBO с 1% бората лития несколько уступает по кулоновской эффективности (>98%), зато демонстрирует самые высокие значения разрядной емкости (≈160 мА ч/г после 40-го цикла). К 40-му циклу разрядная емкость электрода на основе индивидуального NMC снижается на 3%, тогда как для электродов на основе композитов NMC/LBO снижение емкости менее заметно: 2.2% для 1% LBO и всего 0.3% для 3% LBO. Интересно, что для всех образцов снижение разрядной емкости при увеличении нормированного тока разряда сопровождается, тем не менее, ростом кулоновской эффективности.
Таблица 2.
Разрядная емкость и кулоновская эффективность NMC и композитов NMC/LBO при разных значениях нормированного тока разряда
Название образца | 0.1 С (10 цикл) | 0.2 C (20 цикл) | 0.5 C (30 цикл) | 0.1 C (40 цикл) | ||||
---|---|---|---|---|---|---|---|---|
Qразр, мА ч/г | КЭ, % | Qразр, мА ч/г | КЭ, % | Qразр, мА ч/г | КЭ, % | Qразр, мА ч/г | КЭ, % | |
NMC | 154.3 | 99.1 | 147.1 | 99.5 | 130.9 | 100.0 | 149.7 | 99.1 |
NMC/LBO (1%) | 164.5 | 98.9 | 156.6 | 98.0 | 145.3 | 99.4 | 160.8 | 98.9 |
NMC/LBO (3%) | 135.0 | 99.3 | 131.2 | 99.3 | 124.6 | 100.0 | 134.5 | 100.0 |
Из данных, приведенных в табл. 2, видно, что нанесение 1 мас. % LBO на поверхность частиц NMC позволяет добиться наиболее высоких значений удельной емкости во всех изученных режимах циклирования и стабилизирует NMC при повышенных значениях нормированного тока. Это наблюдение подтверждается дальнейшим длительным циклированием тех же ячеек в режиме 0.5 С (рис. 10, циклы от 40-го до 140-го (использована сквозная нумерация циклов)). На завершающем 140-м цикле разрядная емкость электрода на основе композита NMC/LBO (1%) составляет 129 мА ч/г, а для двух других образов не превышает 110 мА ч/г. При этом кулоновская эффективность во всех случаях близка к 100% (рис. 10).
Для более наглядной иллюстрации влияния режима циклирования на рис. 11 приведены кривые заряда и разряда для ячеек с NMC (а), NMC/LBO (1%) (б) и NMC/LBO (3%) (в) для 10‑го, 20-го, 30-го и 40-го циклов в режимах 0.1, 0.2, 0.5 и 0.1 С соответственно. Снижение среднего разрядного напряжения с ростом нормированной плотности тока разряда для всех образцов составляет 0.15–0.30 В. Как видно из рис. 11в, композит NMC/LBO (3%) продемонстрировал почти “идеальную” обратимость: его зарядные и разрядные кривые для 10-го и 40-го циклов (режим 0.1 С) практически совпадают. Чуть похуже, но также очень близко друг другу расположены соответствующие кривые для композита NMC/LBO (1%). Учитывая стабильное длительное циклирование обоих изученных композитов в режиме 0.5 С (рис. 10), можно заключить, что нанесенный на поверхность NMC-111 слой аморфного бората лития действительно способен подавлять побочные химические реакции на границе раздела электрод/электролит [56], стабилизировать структуру активного материала и одновременно облегчать межфазный перенос ионов лития, обеспечивая улучшение электродной кинетики. С учетом всех параметров, среди изученных составов оптимальным представляется композит NMC/LBO (1%).
Рис. 11.
Разрядные кривые, полученные при циклировании в режимах 0.1 С (10-й цикл), 0.2 С (20-й цикл), 0.5 С (30‑й цикл) и 0.1 С (40-й цикл) для образцов NMC без покрытия (а), с 1% LBO (б) и с 3% LBO (в) (номера циклов указаны на рисунках).
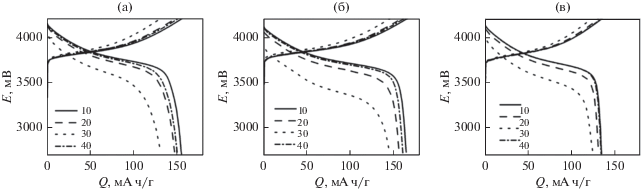
Представляет интерес сопоставить достигнутые характеристики композита NMC/LBO (1%) с приведенными в литературе данными для NMC‑111, полученного разными методами, c защитными покрытиями различного состава (табл. 3). Как видно из таблицы, полученный в настоящей работе материал можно отнести к числу лучших, с точки зрения сохранности разрядной емкости и стабильности циклирования, в средних режимах заряда–разряда. Расширение диапазона циклирования до более высоких значений зарядного потенциала (в данной работе ограниченного 4.2 В) является резервом для повышения удельной емкости композита NMC/LBO (1%).
Таблица 3.
Разрядная емкость NMC-111 c защитными покрытиями различного состава (литературные данные)
Метод синтеза NMC-111 | Покрытие | Интервал циклиро-вания, В | Нормиро-ванный ток разряда | Номер цикла | Разрядная емкость, мА ч/г | Сохранность разрядной емкости, % | Литература |
---|---|---|---|---|---|---|---|
Реакции горения | 3Li2O∙B2O3 (аморф.) | 2.7–4.2 | 0.5 С | 100 | 129 | 99 | Данная работа |
Al2O3 | 3.0–4.5 | 0.5 C | 100 | 152 | 92 | [27] | |
Твердофазный синтез | Li3VO4 | 3.0–4.6 | 1 C | 100 | 180 | 87.5 | [31] |
Li2ZrO3 | 2.5–4.4 | 50 C 1 C |
100 100 |
104.8 156.8 |
89.3 91 | [32] | |
Соосаждение | Al2O3 | 3.0–4.3 | 0.5 C | 100 | 156.9 | 90 | [23] |
TiO2 | 2.5–4.3 | 0.5 C | 50 | 145.9 | 90.5 | [28] | |
Сахароза (отжиг при 600°C) | 3.0–4.4 | 0.083 С | 25 | 180 | 96.8 | [34] | |
Al2O3 | 2.8–4.5 | 0.2 C | 50 | 173 | 93.9 | [29] | |
LBO-стекло (Li : B = 1 : 2) | 2.5–4.5 | 0.5 C | 50 | 162.4 | 99 | [39] | |
LBO-стекло (Li : B = 1 : 2) |
2.5–4.5 | 0.2 C | 50 | 169.8 | 80.4 | [46] | |
Спрей-пиролиз | LiF | 3–4.6 | 40 мА ч/г | 40 | 155 | 82 | [33] |
Гидротерми-ческий синтез | Al2O3 | 2.5–4.5 | 5 C | 10 | 154.4 | 80.3 | [25] |
Коммерческий продукт (Beijing Gelin Power Ltd., Китай) | CeO2 | 2.8–4.5 | 0.2 C | 12 | 162 | 100 | [24] |
ЗАКЛЮЧЕНИЕ
Использование заранее синтезированного обогащенного литием кристаллического бората Li3BO3 и специальный подбор условий термообработки механической смеси компонентов позволили сформировать на поверхности частиц LiNi1/3Mn1/3С1/3O2 стеклообразный слой 3Li2O∙B2O3 за счет эвтектического инконгруэнтного плавления бората лития. Детальные исследования поверхности полученных композитов показали, что при содержании 1 и 3 мас. % борат лития не образует сплошного поверхностного слоя, а формирует островковые структуры. Кроме того, было зафиксировано отсутствие химического взаимодействия между компонентами. Несмотря на специфическую морфологию (и заметную карбонизацию в композите с 3 мас. % LBO), аморфный борат лития на поверхности NMC-111 способен играть роль защитного слоя, препятствующего побочным реакциям на границе электрод/электролит, и одновременно облегчать перенос катионов лития на границе раздела электрод/электролит. Это проявляется в стабилизации электрохимического поведения композитных материалов NMC/LBO по сравнению с индивидуальным NMC, улучшении динамических характеристик и увеличении разрядной емкости. Образец, покрытый LBO в количестве 1 мас. %, обладает хорошей циклической стабильностью и демонстрирует разрядную емкость 129 мА ч/г после 100 циклов в режиме 0.5 С (диапазон циклирования 2.7–4.2 В отн. Li0/Li+) при кулоновской эффективности, близкой к 100%; сохранность разрядной емкости составляет 99%. Хорошие защитные свойства LBO позволяют в дальнейшем повысить зарядный потенциал, существенно увеличив удельную разрядную емкость. Возможным объяснением высокой эффективности островкового покрытия может служить преимущественная локализация LBO на электрохимически активных участках поверхности NMC-111, однако эта гипотеза требует подтверждения. Повышенные электрохимические характеристики композита, содержащего 1 мас. % LBO, по сравнению с композитом с 3 мас. % LBO обусловлены, по-видимому, оптимальной толщиной “островков” защитного слоя (≈8–10 нм) и отсутствием заметной карбонизации.
Список литературы
Julien, C.M., Mauger, A., Zaghib, K., and Groult, H., Comparative issues of cathode materials for Li-Ion batteries, Inorganics, 2014, vol. 20, p. 132. https://doi.org/10.3390/inorganics2010132
Schmuch, R., Wagner, R., Hörpel, G., Placke, T., and Winter, M., Performance and cost of materials for lithium-based rechargeable automotive batteries, Nature Energy, 2018, vol. 3, no. 4, p. 267. https://doi.org/10.1038/s41560-018-0107-2
Tarascon, J.-M., Key challenges in future Li-battery research, Phil. Trans. R. Soc. A, 2010, vol. 368, p. 3227. https://doi.org/10.1098/rsta.2010.0112
Zuo, D., Tian, G., Li, X., Chen, D., and Shu K., Recent progress in surface coating of cathode materials for lithium ion secondary batteries, J. Alloys and Compounds, 2017, vol. 706, p. 24. https://doi.org/10.1016/j.jallcom.2017.02.230
Blomgren, G.E., The development and future of lithium ion batteries, J. Electrochem. Soc., 2016, vol. 164, no. 1, p. A5019. https://doi.org/10.1149/2.0251701jes
Mauger, A. and Julien, C.M., Critical review on lithium-ion batteries: are they safe? Sustainable?, Ionics, 2017, vol. 23, no. 8. p. 1933. https://doi.org/10.1007/s11581-017-2177-8
Schipper, F. and Aurbach, D., A brief review: Past, present and future of lithium ion batteries, Russ. J. Electrochem., 2016, vol. 52, no. 12, p. 1095. https://doi.org/10.1134/S1023193516120120
Xu, J., Lin, F., Doe, M.M., and Tong, W., A review of Ni-based layered oxides for rechargeable Li-ion batteries, J. Mater. Chem. A, 2017, vol. 5, p. 874. https://doi.org/10.1039/c6ta07991a
Добровольский, Ю.А., Бушкова, О.В., Астафьев, Е.А., Евщик, Е.Ю., Каюмов, Р.Р., Корчун, А.В., Дрожжин, О.А., Антипов А.Е. Литий-ионные аккумуляторы, М.: РХТУ им. Д. И. Менделеева, 2020. 208 с. [Dobrovolsky, Yu.A., Bushkova, O.V., Evshchik, E.Yu., Kayumov, R.R., Korchun, A.V., Drozhzhin, O.A., and Antipov, A.E., Lithium-Ion Batteries (in Russia), Moscow: D.I. Mendeleev University of Chemical Technology of Russia, 2020. 208 p.]
Armand, M., Axmann, P., Bresser, D., Copley, M., Edström, K., Ekberg, C., Guyomard, D., Lestriez, B., Novaґk, P., Petranikova, M., Porcher, W., Trabesinger, S., Wohlfahrt-Mehrens, M., and Zhang, H., Lithium-ion batteries – Current state of the art and anticipated developments, J. Power Sources, 2020, vol. 479, p. 228708. https://doi.org/10.1016/j.jpowsour.2020.228708
Ding, Y., Cano, Z.P., Yu, A., Lu, J., and Chen, Z., Automotive Li-Ion Batteries: Current Status and Future Perspectives, Electrochem. Energ. Rev., 2019, vol. 2, p. 1. https://doi.org/10.1007/s41918-018-0022-z
Pillot, C., The rechargeable battery market and main trends 2016–2025, Proceedings of the 33rd Annual International Battery Seminar & Exhibit, Fort Lauderdale, FL, USA, 2017, vol. 20.
Nitta, N., Wu, F., Lee, J.T., and Yushin, G., Li-ion battery materials: present and future, Materials today, 2015, vol. 18, no. 5, p. 252. https://doi.org/10.1016/j.mattod.2014.10.040
Daniel, C., Mohanty, D., Li, J., and Wood, D.L., Cathode materials review, AIP Conference Proceedings, 2014, vol. 26, p. 1597. https://doi.org/10.1063/1.4878478
Kim, H., Oh, S.-M., Scrosati, B., and Sun, Y.-K., High-performance electrode materials for lithium-ion batteries for electric vehicles, Advances in Battery Technologies for Electric Vehicles, 2015, p. 191. https://doi.org/10.1016/b978-1-78242-377-5.00009-1
Aurbach, D., Gamolsky, K., Markovsky, B., Salitra, G., Gofer, Y., Heider, U., Oesten, R., and Schmidt, M., The Study of Surface Phenomena Related to Electrochemical Lithium Intercalation into LixMOy Host Materials (M = Ni, Mn), J. Electrochem. Soc., 2000, vol. 147, p. 1322. https://doi.org/10.1149/1.1393357
Xu, K., Electrolytes and interphases in Li-ion batteries and beyond, Chem. Rev., 2014, vol. 114, p. 11503. https://doi.org/10.1021/cr500003w
Mauger, A. and Julien, C., Surface modifications of electrode materials for lithium-ionbatteries: status and trends, Ionics, 2014, vol. 20, p. 751. https://doi.org/10.1007/s11581-014-1131-2
Bensalah, D. and Dawood, H., Review on Synthesis, Characterizations, and Electrochemical Properties of Cathode Materials for Lithium Ion Batteries, J. Material Sci. Eng., 2016, vol. 5, p. 1000258. https://doi.org/10.4172/2169-0022.1000258
Li, C., Zhang, H.P., Fu, L.J., Liu, H., Wu, Y.P., Rahm, E., Holze, R., and Wu, H.Q., Cathode materials modified by surface coating for lithium ion batteries, Electrochim. Acta, 2006, vol. 51, p. 3872. https://doi.org/10.1016/j.electacta.2005.11.015
Makhonina, E.V., Maslennikova, L.S., Volkov, V.V., Medvedeva, A.E., Rumyantsev, A.M., Koshtyal, Yu.M., Maximov, M.Yu., Pervov, V.S., and Eremenko, I.L., Li-rich and Ni-rich transition metal oxides: Coating and core–shell structures, Appl. Surface Sci., 2019, vol. 474, no. 30, p. 25. https://doi.org/10.1016/j.apsusc.2018.07.159
Machida, N., Kashiwagi, J., Naito, M., and Shigematsu, T., Electrochemical properties of all-solid-state batteries with ZrO2-coated LiNi1/3Mn1/3Co1/3O2 as cathode materials, Solid State Ionics, 2012, vol. 225, p. 354. https://doi.org/10.1016/j.ssi.2011.11.026
Huang, Y., Chen, J., Cheng, F., Wan, W., Liu, W., Zhou, H., and Zhang, X., A modified Al2O3 coating process to enhance the electrochemical performance of Li(Ni1/3Co1/3Mn1/3)O2 and its comparison with traditional Al2O3 coating process, J. Power Sources, 2010, vol. 195, no. 24, p. 8267. https://doi.org/10.1016/j.jpowsour.2010.07.021
Wu, F., Wang, M., Su, Y., Bao, L., and Chen, S., Surface of LiCo1/3Ni1/3Mn1/3O2 modified by CeO2-coating, Electrochimica Acta, 2009, vol. 54, no. 27, p. 6803. https://doi.org/10.1016/j.electacta.2009.06.075
Li, X., He, W., Chen, L., Guo, W., Chen, J., and Xiao, Z., Hydrothermal synthesis and electrochemical performance studies of Al2O3-coated LiNi1/3Co1/3Mn1/3O2 for lithium-ion batteries, Ionics, 2013, vol. 20, no. 6, p. 833. https://doi.org/10.1007/s11581-013-1041-8
Hu, S.-K., Cheng, G.-H., Cheng, M.-Y., Hwang, B.-J., and Santhanam, R., Cycle life improvement of ZrO2-coated spherical LiNi1/3Co1/3Mn1/3O2 cathode material for lithium ion batteries, J. Power Sources, 2009, vol. 188, no. 2, p. 564. https://doi.org/10.1016/j.jpowsour.2008.11.113
Riley, L.A., Van Atta, S., Cavanagh, A.S., Yan, Y., George, S.M., Liu, P., and Lee, S.-H., Electrochemical effects of ALD surface modification on combustion synthesized LiNi1/3Mn1/3Co1/3O2 as a layered-cathode material, J. Power Sources, 2011, vol. 196, no. 6, p. 3317. https://doi.org/10.1016/j.jpowsour.2010.11.124
Li, J., Fan, M., He, X., Zhao, R., Jiange, C., and Wan, C., TiO2 coating of LiNi1/3Co1/3Mn1/3O2 cathode materials for Li-ion batteries, Ionics, 2006, vol. 12, no. 3, p. 215. https://doi.org/10.1007/s11581-006-0034-2
Kim, Y., Kim, H.S., and Martin, S.W., Synthesis and electrochemical characteristics of Al2O3-coated LiNi1/3Co1/3Mn1/3O2 cathode materials for lithium ion batteries, Electrochim. Acta, 2006, vol. 52, no. 3, p. 1316. https://doi.org/10.1016/j.electacta.2006.07.033
Li, D., Kato, Y., Kobayakawa, K., Noguchi, H., and Sato, Y., Preparation and electrochemical characteristics of LiNi1/3Mn1/3Co1/3O2 coated with metal oxides coating, J. Power Sources, 2006, vol. 160, no. 2, p. 1342. https://doi.org/10.1016/j.jpowsour.2006.02.080
Wang, W., Yin, Z., Wang, Z., Li, X., and Guo, H., Effect of heat-treatment on electrochemical performance of Li3VO4-coated LiNi1/3Co1/3Mn1/3O2 cathode materials, Mater. Letters, 2015, vol. 160, p. 298. https://doi.org/10.1016/j.matlet.2015.07.160
Wang, C., Chen, L., Zhang, H., Yang, Y., Wang, F., Yin, F., and Yang, G., Li2ZrO3 coated LiNi1/3Co1/3Mn1/3O2 for high performance cathode material in lithium batteries, Electrochim. Acta, 2014, vol. 119, p. 236. https://doi.org/10.1016/j.electacta.2013.12.038
Li, D., Sasaki, Y., Kobayakawa, K., Noguchi, H., and Sato, Y., Preparation, morphology and electrochemical characteristics of LiNi1/3Mn1/3Co1/3O2 with LiF addition, Electrochim. Acta, 2006, vol. 52, no. 2, p. 643. https://doi.org/10.1016/j.electacta.2006.05.044
Hashem, A.M.A., Abdel-Ghany, A.E., Eid, A.E., Trottier, J., Zaghib, K., Mauger, A., and Julien, C.M., Study of the surface modification of LiNi1/3Co1/3Mn1/3O2 cathode material for lithium ion battery, J. Power Sources, 2011, vol. 196, no. 20, p. 8632. https://doi.org/10.1016/j.jpowsour.2011.06.039
Eddrief, M., Dzwonkowski, P., Julien, C., and Balkanski, M., The ac conductivity in B2O3–Li2O films, Solid State Ionics, 1991, vol. 45, no. 1–2, p. 77. https://doi.org/10.1016/0167-2738(91)90105-K
Ito, Y., Miyauchi, K., and Oi, T., Ionic conductivity of Li2O–B2O3 thin films, J. Non-Crystalline Solids, 1983, vol. 57, no. 3, p. 389. https://doi.org/10.1016/0022-3093(83)90426-X
Horopanitis, E.E., Perentzis, G., Pavlidou, E., and Papadimitriou, L., Electrical properties of lithiated boron oxide fast-ion conducting glasses, Ionics, 2003, vol. 9, p. 88. https://doi.org/10.1007/BF02376543
Amatucci, G., Blyr, A., Sigala, C., Alfonse, P., and Tarascon, J., Surface treatments of Li1 +xMn2 –xO4 spinels for improved elevated temperature performance, Solid State Ionics, 1997, vol. 104, no. 1–2, p. 13. https://doi.org/10.1016/S0167-2738(97)00407-4
Dou, J., Kang, X., Wumaier, T., Yu, H., Hua, N., Han, Y., and Xu, G., Effect of lithium boron oxide glass coating on the electrochemical performance of LiNi1/3Co1/3Mn1/3O2, J. Solid State Electrochem., 2011, vol. 16, no. 4, p. 1481. https://doi.org/10.1007/s10008-011-1550-1
Jinlian, L., Xianming, W.U., Shang, C., Jianben, C., and Zeqiang, H., Enhanced high temperature performance of LiMn2O4 coated with Li3BO3 solid electrolyte. Bulletin of Materials Sci., 2013, vol. 36, no. 4, p. 687. https://doi.org/10.1007/s12034-013-0513-9
Chan, H.-W., Duh, J.-G., and Sheen, S.-R., Electrochemical performance of LBO-coated spinel lithium manganese oxide as cathode material for Li-ion battery, Surface and Coatings Technology, 2004, vol. 188–189, p. 116. https://doi.org/10.1016/j.surfcoat.2004.08.065
Şahan, H., Göktepe, H., Patat, Ş., Ülgen, A., and Sahan, H., The effect of LBO coating method on electrochemical performance of LiMn2O4 cathode material, Solid State Ionics, 2008, vol. 178, no. 35–36, p. 1837. https://doi.org/10.1016/j.ssi.2007.11.024
Peng, W., Jiao, L., Gao, H., Qi, Z., Wang, Q., Du, H., Si, Y.C., Wang, Y.J., and Yuan, H.T., A novel sol–gel method based on FePO4·2H2O to synthesize submicrometer structured LiFePO4/C cathode material, J. Power Sources, 2011, vol. 196, no. 5, p. 2841. https://doi.org/10.1016/j.jpowsour.2010.10.065
Ying, J., Wan, C., and Jiang, C., Surface treatment of LiNi0.8Co0.2O2 cathode material for lithium secondary batteries, J. Power Sources, 2001, vol. 102, nos. 1–2, p. 162. https://doi.org/10.1016/S0378-7753(01)00795-9
Chen, S., Chen, L., Li, Y., Su, Y., Lu, Y., Bao, L., Wang, J., Wang, M., and Wu, F., Synergistic Effects of Stabilizing the Surface Structure and Lowering the Interface Resistance in Improving the Low-Temperature Performances of Layered Lithium-Rich Materials, ACS Appl. Materials and Interfaces, 2017, vol. 9, no. 10, p. 8641. https://doi.org/10.1021/acsami.6b13995
Tan, S., Wang, L., Bian, L., Xu, J., Ren, W., Hu, P., and Chang, A., Highly enhanced low temperature discharge capacity of LiNi1/3Co1/3Mn1/3O2 with lithium boron oxide glass modification, J. Power Sources, 2015, vol. 277, p. 139. https://doi.org/10.1016/j.jpowsour.2014.11.149
Zhu, L., Bao, C., Xie, L., Yang, X., and Cao, X., Review of synthesis and structural optimization of LiNi1/3Co1/3Mn1/3O2 cathode materials for lithium-ion batteries applications, J. Alloys and Compounds, 2020, vol. 831, p. 154864. https://doi.org/10.1016/j.jallcom.2020.154864
Ferreira, E.B., Lima, M.L., and Zanotto, E.D., DSC Method for Determining the Liquidus Temperature of Glass-Forming Systems, J. Amer. Ceramic Soc., 2010, vol. 93, no. 11, p. 3757. https://doi.org/10.1111/j.1551-2916.2010.03976.x
Mathews, M.D., Tyagi, A.K., and Moorthy, P.N., High-temperature behaviour of lithium borates: Part I: Characterization and thermal stability, Thermochim. Acta, 1998, vol. 320, p. 89. https://doi.org/10.1016/S0040-6031(98)00403-1
Пантюхина, М.И., Зелютин, Г.В., Баталов, Н.Н., Обросов, В.П. Влияние изотопного замещения 7Li на 6Li на ионную проводимость α-LI3BO3. Электрохимия. 2020. Т. 36. С. 894. [Pantyukhina, M.I., Zelyutin, G.V., Batalov, N.N., and Obrosov, V.P., Effect of substituting 6Li for 7Li on ionic conductivity of α-Li3BO3, Russ. J. Electrochem., 2000, vol. 36, p. 792.] https://doi.org/10.1007/BF02757683
Hirose, E., Kataoka, K., Nagata, H., Akimoto, J., Sasaki, T., Niwa, K., and Hasegawa, M., Lithium ionic conductivities of α-LiBO2 with two-dimensional Li–Li networks and γ-LiBO2 with three-dimensional ones synthesized under high pressure, J. Solid State Chem., 2019, vol. 274, p. 100. https://doi.org/10.1016/j.jssc.2019.02.045
Zhuravlev, V.D., Pachuev, A.V., Nefedova, K.V., and Ermakova L.V., Solution-Combustion Synthesis of LiNi1/3Co1/3Mn1/3O2 as a Cathode Material for Lithium-Ion Batteries, Internat. J. Self-Propagating High-Temperature Synthesis, 2018, vol. 27, no. 3, p. 154. https://doi.org/10.3103/S1061386218030147
Rodríguez-Carvajal, J., Recent advances in magnetic structure determination by neutron powder diffraction, Physica B, 1993, vol. 192, no. 1–2, p. 55. https://doi.org/10.1016/09214526(93)90108I
Harada, T. and Hatton, T.A., Tri-lithium borate (Li3BO3); a new highly regenerable high capacity CO2 adsorbent at intermediate temperature, J. Mater. Chem. A, 2017, vol. 5, no. 42, p. 22224. https://doi.org/10.1039/c7ta06167f
Shaju, K.M., Subba Rao, G.V., and Chowdari, B.V., Performance of layered Li(Ni1/3Co1/3Mn1/3)O2 as cathode for Li-ion batteries, Electrochim. Acta, 2002, vol. 48, no. 2, p. 145. https://doi.org/10.1016/s0013-4686(02)00593-5
Hu, W., Zhang, C., Jiang, H., Zheng, M., Wu, Q.-H., and Dong, Q., Improving the electrochemistry performance of layer LiNi0.5Mn0.3Co0.2O2 material at 4.5 V cutoff potential using lithium metaborate, Electrochim. Acta, 2017, vol. 243, p. 105. https://doi.org/10.1016/j.electacta.2017.05.075
Дополнительные материалы отсутствуют.