Электрохимия, 2021, T. 57, № 11, стр. 689-702
Электропроводящие наполнители для эластомеров с магниторезистивным эффектом
А. В. Бахтияров a, *, Г. В. Степанов a, **, Д. А. Семеренко b, Д. А. Лобанов a
a АО “Государственный научно-исследовательский институт химических технологий
элементоорганических соединений”
105118 Москва, шоссе Энтузиастов, 38, Россия
b Московский государственный технический университет им. Н.Э. Баумана
105005 Москва, 2-я Бауманская ул., 5, Россия
* E-mail: abakhtia@gmail.com
** E-mail: gstepanov@mail.ru
Поступила в редакцию 25.09.2020
После доработки 30.12.2020
Принята к публикации 02.03.2021
Аннотация
В рамках работы, направленной на создание магнитного наполнителя с высокой электропроводностью для магнитоуправляемого материала нового типа, был отработан метод электрохимической металлизации частиц порошков карбонильного железа различных форм и размеров. Наблюдаемое улучшение условной удельной проводимости продуктов гальванического никелирования достигало нескольких порядков. Данный тип наполнителя был использован при создании магнитных эластомеров, представляющих собой композиты с высокой зависимостью электрического сопротивления от внешнего магнитного поля (магниторезистивным эффектом), достижение которой требует больших концентраций частиц с высокими магнитными и электропроводящими свойствами.
ВВЕДЕНИЕ
Важным исследовательским направлением в области композитных систем является разработка материалов с управляемыми параметрами. Как пример таких систем, внимание привлекают магнитоактивные эластомеры (МАЭ), представляющие собой эластичный полимер, наполненный частицами с высокой магнитной восприимчивостью. Будучи наполненными порошком с высокой электропроводностью, они демонстрируют магнито- и пьезорезистивные качества [1], выражающиеся в сильной зависимости электрического сопротивления от магнитного поля и механического воздействия, что делает их перспективными в разработке тактильных сенсоров и датчиков поля [2, 3].
Описываемый опыт есть результат попыток создания наполнителя для МАЭ на основе частиц карбонильного железа. В то время как соотношение магнитных свойств и проводимости ставит железо в особое положение, основной проблемой материала является низкая коррозионная стойкость. Это выражается в сильной зависимости состояния поверхности частиц порошков от их предыстории. Например, различия в проводимостях образцов железа со сферическими частицами, взятых из разных источников, могут достигать нескольких порядков. Однако, ввиду нестабильности характеристик материала во времени и желания еще больше приблизиться к удельному сопротивлению чистого железа (9.87–9.98) × 10–7 Ом м [4], приоритет был отдан электрохимическому никелированию. Начавшаяся с попыток металлизации навесок железа, удерживаемых на жестяной тарелке катода стационарным магнитом с периодическим его снятием для осуществления перемешивания, работа привела к разработке технологии, основанной на непрерывном перемешивании порошкового материала вращающимся магнитным полем [5]. Создаваемое вращаемым с помощью электродвигателя неодимовым магнитом поле вовлекает во вращательное движение частицы в порошке, чем способствует равномерности распределения покрытия по их поверхности и препятствует их слипанию.
Исследование научно-технологического опыта электрохимической металлизации порошков выявило определенный интерес к проблеме [6‒10], показав, что конструкторские решения сводятся к двум принципам, предполагающим кратковременный [11, 12] и продолжительный контакт частицы с катодом. В то время как в первом случае частицы находятся либо в циркулирующей суспензии [13–17], будучи взвешенными как ультразвуком [18], так и вибрациями катода [19], либо в псевдоожиженном слое [20–22], во втором электролиз проводится после фазы естественного осаждения под действием гравитации [23–26], причем осаждение может форсироваться центрифугированием [27–30] или периодическим воздействием магнитного поля [31]. В [32] представлена идея электрохимической металлизации магнитных частиц, вводимых в контакт с катодом с помощью внешнего магнитного поля и перемешиваемых посредством периодического изменения вектора поля на противоположное, в результате чего частицы перемещаются на противоположную сторону контейнера и оседают на втором катоде. В определенном смысле данный способ является родственным предложенному в рамках нашего исследования.
Ввиду имеющихся сведений о влиянии полевого воздействия на распределение никеля на поверхности частицы [33], предстояло выяснить, насколько процесс осуществим в условиях вращающегося магнитного поля. При этом попытки осадить никель, используя водные электролиты, сразу же указали на ряд проблем, таких как плохое смачивание поверхностей, на которых могут присутствовать гидрофобные субстанции, и необходимость регенерации раствора. Поскольку при дроблении порошков карбонильного железа в качестве стабилизирующего агента в жидкой среде могут присутствовать небольшие добавки олеиновой кислоты, металлизация таких материалов сложна из-за флотации и слабого контакта частиц с раствором. Поиск в литературе альтернативных идей привел к рассмотрению возможности замены воды этиленгликолем [34]. В результате последовавших экспериментов выяснилось, что задействование этиленгликолевых растворов снимает часть сложностей, одной из которых является смачивание. Также, будучи более эффективными при высоких токах, такие электролиты ускоряют процесс, делая его менее зависимым от температурного режима и создавая возможность проведения металлизации даже при закипании. Наряду с этим, обладая более высокой, выше чем на порядок, вязкостью в сравнении с водой, этиленгликоль позволил значительно подавить тенденцию к агломерации. При этом, более детальное прояснение явления слипания частиц требует дополнительного изучения.
Процесс металлизации изучался с позиций комплексности технологии, доступности материалов, скорости и возможности варьирования целевого процесса, производительности, наличия побочных реакций, электропроводности продукта, наличия агломератов, а также экологичности.
ЭКСПЕРИМЕНТАЛЬНАЯ ЧАСТЬ
Электролит для металлизации готовился растворением навески NiCl2·6H2O марки “ч.” в этиленгликоле марки “ч.” или “ч. д. а.”; реактивы перед смешением не обрабатывались. Иногда для ускорения растворения размешивание проводили при 60–70°С. Полученный раствор представлял собой прозрачную жидкость светло-зеленого цвета.
Объектами обработки были как порошки карбонильного железа со сферическими частицами, так и продукты их трехступенчатого помола в различных жидких средах в планетарной мельнице АГО-3, производства группы компаний “Гарант”, Россия. Электрохимическая металлизация порошков осуществлялась на приборе, разработанном в рамках данного исследования [5] (рис. 1). Навеску порошка в 10, 20 или 50 г помещали в полипропиленовый контейнер с известной массой, который затем ставили на дюралевый столик установки, после чего включали двигатель, вращающий оправу с неодимовым магнитом 30 × 30 × 30 мм3 со скоростью 1 об/с, и в “пятно” порошка опускали стержень катода из нержавеющей стали до упора в дно контейнера. Для предотвращения осаждения металла на стержень, его поверхность была покрыта изоляцией за исключением оголенного конца (“точки катода”), который утапливался в массе перемешиваемого магнитным полем порошка. Завершающим этапом подготовки было заполнение кюветы 100 мл электролита, погружение анода в жидкость и включение электрического тока (напряжение 51 В до достижения установленного максимального тока). В случае использования графитового анода, общая его площадь, омываемая электролитом, составляла 0.03–0.05 дм2, а при замещении графита никелем использовалась анодная сборка – пластиковый сетчатый контейнер, наполненный порошком карбонильного никеля, соединенного с источником тока посредством провода из углеродного волокна. Притом, что геометрические параметры установки оставались неизменными, с целью интенсификации перемешивания порошка, направление перемешивания варьировалось, для чего в ходе электролиза кювету время от времени поворачивали на столике на 45°, 90° или 180°. Изменение цвета и прозрачности раствора, величины силы тока как функции от времени, а также pH отслеживалось до прекращения процесса.
Рис. 1.
Установка для металлизации. Цифрами показаны: 1 – катод, погруженный оголенным концом в металлизируемый порошок, 2 – анод, опущенный в электролит, 3 – магнит, вращаемый двигателем вокруг оси.
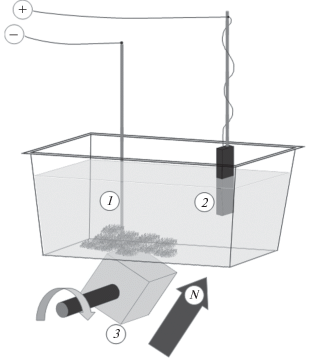
По завершении металлизации за декантацией следовала тщательная промывка продукта до чистого слива дистиллированной водой, концентрированным раствором аммиака и изопропиловым спиртом или ацетоном. Ввиду того, что отслеживание массовых изменений требовало того, чтобы на протяжении всего эксперимента порошок не покидал кюветы, промывка делалась с применением магнита. Высушивание производилось в сушильном шкафу при 60–70°С до отсутствия запаха растворителя. Продукт исследовался на предмет изменения цвета, наличия светло-бурых пятен и агломератов, а также способности проводить электрический ток.
Измерение проводящих свойств, процедура чего описана в [35], осуществлялось с помощью омметра Metex 3610-D производства США и устройства, состоящего из тефлоновой оправы и нагружающего механизма, позволяющего с заданной силой сдавливать порошковый образец между двумя латунными стержневыми контактами с плоскими сечениями. Условные удельные сопротивления материала, соответствующие определенным давлениям, рассчитывались по формуле ρ = 1/4πRd2/h, где d и h – внутренний диаметр отверстия оправы (5 или 6 мм) и высота столбика порошка соответственно, а R – показания омметра. Ввиду того, что наполнитель, находясь внутри полимера, не испытывает больших давлений, в тексте приводятся значения ρ при фиксированном давлении 7.5 кгс/см2.
Продукты металлизации исследовали и иными методами. В частности, рентгенофазовый анализ (РФА) осуществлялся на автоматическом порошковом дифрактометре STOE Stadi MP (ConeTech, Германия). Элементный анализ проводился на приборах Спектроскан МАКС-GVM (НПО “Спектрон”, Россия) и с помощью системы EDAX. Фотографии исследуемых материалов были получены посредством метода сканирующей электронной микроскопии (СЭМ) на микроскопах Philips и Quanta SEM.
РЕЗУЛЬТАТЫ И ОБСУЖДЕНИЕ
С целью удостовериться в отсутствие крупных твердых агломератов в необработанном порошке, навески карбонильного железа подвергали предварительному ручному перетиранию в фарфоровой ступке.
Испытательная серия экспериментов проводилась с использованием 100 мл электролита с составом: NiSO4·6H2O – 150.0 г/л, NaCl – 30.0 г/л, борная кислота H3BO3 – 25.0 г/л, pH 4.5 при комнатной температуре [36, 37]. Проводилась металлизация порошков железа со сферическими частицами и вариантом этих частиц, предварительно раздробленных в планетарной мельнице, с образованием частиц пластинчатой формы. Электрохимическое никелирование проходило в течение 120–125 мин с использованием графитового анода, погруженного в контейнер с сетчатым дном, наполненный смесью кристаллических NiSO4·6H2O и NaCl для предотвращения значительных изменений состава раствора. Условная плотность тока на катоде (навеска порошка массой 10 г) составляла 2.7–6.0 А/дм2. Склонность молотых порошков к флотации подавляли предварительным их смачиванием небольшими количествами изопропанола или изобутанола. При этом изучение продуктов их никелирования выявило присутствие в них соединений Fe(III). В то же время первичный осмотр никелированного порошка со сферическими частицами показал его более высокую склонность к агломерации, что нашло подтверждение при изучении его методом СЭМ; проведенный в рамках того же исследования элементный анализ подтвердил наличие в продукте никеля (рис. 2). Удельное сопротивление материалов снизилось с 88.36 и 0.14 Ом м до (1.31–3.27) × 10–3 и (1.31–22.25) × 10–3 Ом м у недробленых и дробленых порошков соответственно.
Рис. 2.
СЭМ-фотография сферических частиц карбонильного железа до (а) и после (б) электрохимического никелирования; масштабный отрезок – 5 мкм. Результат элементного анализа продукта никелирования порошка со сферическими частицами (в).
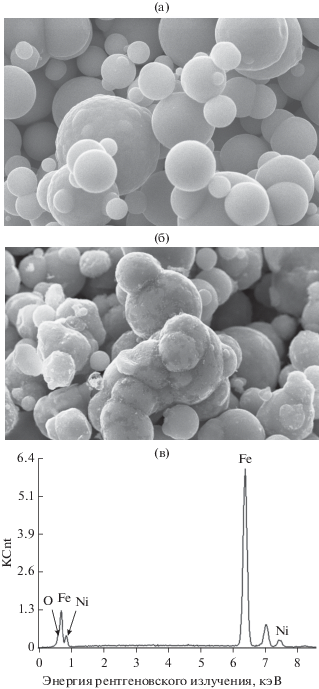
Ввиду нестойкости железа в кислых водных средах были проведены еще несколько экспериментов с составами электролитов с более высоким pH. В частности, условия были следующими: раствор NiSO4·6H2O – 350.0 г/л, pH 7, плотность тока на катоде 3.4–4.6 А/дм2, время процесса 60 мин, и раствор NiCl2·6H2O – 285.00 г/л; NH4Cl – 50.0 г/л, pH 6–7, плотность тока на катоде 0.4–0.6 А/дм2, время процесса 30 мин. Все опыты проходили при комнатной температуре с навесками порошков со сферическими частицами массой 10 г. В результате удельное сопротивление порошков снизилось с 88.36 и 60 Ом м до соответственно 68.72 × 10–3 и 150 × 10–3 Ом м в первом и втором случаях. При этом, при использовании раствора сульфата никеля продукт содержал следы Fe(III), а никелирование в растворе хлоридов никеля и аммония вызвало заметную агломерацию. Попытка металлизации в ацетатном растворе [38, 39] значительно ухудшило электропроводящие качества материала, увеличив его удельное сопротивление до значений, превышающих 1.31 × 107 Ом м. Следует, однако, отметить, что степень агломерации, наблюдаемой при электрохимическом никелировании сферических частиц описываемым методом, была значительно ниже, чем замеченная во время электрохимического осаждения никеля на частицы стационарного порошка. В то же самое время, низкая предсказуемость результата, а также необходимость регенерации электролита создали необходимость поиска альтернативных решений.
Ставший в результате основным, метод электрохимического никелирования в растворах на основе этиленгликоля сразу показал их преимущества перед водными. При этом было замечено, что и в рамках данного метода возможность получения продукта с более высоким, чем ожидалось, сопротивлением, хоть и была значительно ниже в сравнении с продуктами металлизации в водных растворах, все же не оказалась пренебрежительно малой. Также, ввиду малой предсказуемости величины массового прироста, оставалась неясной возможность ее интерпретации как количественной характеристики процесса, которая изначально виделась как индикатор глубины его прохождения. В поиске оптимальных условий для изучения были выбраны следующие направления: 1) оперативная нейтрализация раствора, 2) вариация материала анода и 3) вариация состава электролита. Учитывая тот факт, что по ходу исследований замечалось, что массовый прирост иногда оказывался отрицательным, а также то, что в результате использования раствор наполняется продуктами побочных реакций, влияние состава рассматривалось еще и через призму возможности применения уже ранее употреблявшегося электролита. В целях исследования прохождения процесса “в общих условиях” металлизацию дробленых порошков осуществляли в многократно использованных растворах.
Эксперименты I и II. Пилотные опыты проводились со свежеприготовленным электролитом с составом NiCl2·6H2O – 100.00 г/л, pH 7 и графитовым анодом. С целью проверить предположение о пропорциональности количества осаждаемого металла времени электролиза, а качества продукта количеству никеля, металлизацию проводили с навесками железа в 20 и 50 г в течение соответственно 50 и 100 мин при силе тока 1.03 А (рис. 3). В ходе процессов было отмечено заметное разогревание растворов. Также было обнаружено, что раствор достаточно быстро становился кислым с pH 1–2. Притом, что полученные продукты имели близкие массовые приросты – 1.55 и 1.26 мас. % соответственно, их удельные сопротивления отличались на порядок – 0.65 × 10–3 и (5.24–5.89) × × 10–3 Ом м (рис. 4). Следует заметить, что изначальные удельные сопротивления образцов отличались друг от друга в обратном порядке: 1.44 × 103 и 19.60 Ом м.
Рис. 3.
Зависимость тока от времени: а – эксперимент I: навеска 20 г, длительность – 50 мин; б – эксперимент II: навеска 50 г, длительность – 100 мин.
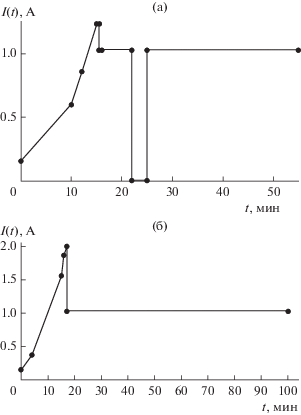
Эксперименты III и IV. Влияние концентрации изучалось в аналогичных опытах с содержанием соли в электролите 60 и 300 г/л. При одинаковых навесках в 20 г с близкими значениями удельных сопротивлений 32.70 и 11.60 Ом м использовались разные аноды – графитовый в первом случае и никелевый порошковый во втором. Электролиз проходил при 1.5 и 1.03 А в течение 60 и 42 мин соответственно. Интересно отметить, что более медленный рост тока по сравнению с предыдущими опытами наблюдался в обоих случаях (рис. 5). При этом, как показало изучение продуктов, металлизация при низкой концентрации с графитовым анодом повторила менее удачный результат, описанный выше. В то же время порошок, обработанный в высококонцентрированном растворе с использованием никелевого анода, демонстрировал проводимость более, чем на четыре порядка, ниже (рис. 4). Значения массовых приростов и удельных сопротивлений составили 1.8 и –2.05 мас. % и (1.96–2.62) × 10–3 и 131.0 Ом м соответственно. Следует заметить, что во время эксперимента pH первого раствора, как и в вышеописанных опытах, снизился до уровня 1–2, а в случае с анодной сборкой – остался нейтральным. Также было обнаружено обрастание анодной сборки никелевыми дендритами.
Рис. 5.
Зависимость тока от времени: а – эксперимент III: концентрация 60 г/л, графитовый анод; б – эксперимент IV: концентрация 300 г/л, Ni-порошковый анод.
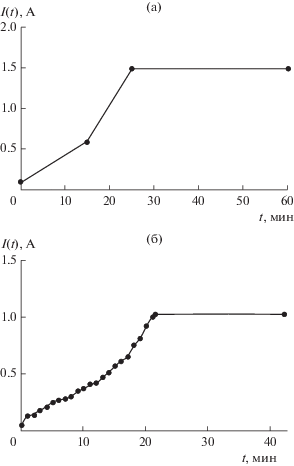
Эксперименты V и VI. Попыткой понять, что послужило причиной образования продукта со столь высоким удельным сопротивлением в эксперименте IV – концентрационный фактор или смена материала анода, были эксперименты V и VI по металлизации навесок в 20 г двух порошков с удельными сопротивлениями 32.70 и 11.60 Ом м соответственно. Первый обрабатывался в свежеприготовленном электролите состава NiCl2∙6H2O – 60.00 г/л с использованием анодной сборки с никелевым порошком, никелирование второго осуществлялось в свежем растворе NiCl2∙6H2O – 300.00 г/л; FeCl3∙6H2O – 100.00 г/л с применением графитового анода. В то время как первый электролит показывал нейтральную реакцию, а второй заведомо был сильно кислым, введение железа в состав было продиктовано желанием узнать, явились ли причиной отрицательного массового прироста, вызванного очевидным переходом металла в раствор, побочные реакции с образованием комплексных соединений с продуктами анодного окисления растворителя и можно ли нивелировать их действие, превентивно добавляя избыток Fe3+. Как и в описанном выше опыте, применение анодной сборки вызвало замедление роста тока. При этом низкая концентрация раствора, очевидно, явилась усугубляющим фактором: за первые 30 мин ток вырос лишь на ничтожную величину, после чего продолжил подниматься чуть более быстро, достигнув к 80-й мин значения 0.58 А. Эксперимент был прерван и продолжен после доведения содержания NiCl2·6H2O в растворе до 90.00 г/л. Во второй части опыта ток увеличивался быстрее и возрос до 1.12 А лишь за 25 мин (рис. 6), после чего ввиду заметного нарастания никелевых дендритов на анодную сборку эксперимент пришлось остановить. Проверка pH показала, что раствор остался нейтральным. Противоположные тенденции наблюдалась в опыте с концентрированным раствором, содержащим железо: значение тока 1.03 А, которое было зафиксировано, было достигнуто менее чем за 4 мин (рис. 6), а графитовый анод не содержал следов обрастания дендритами. Ограничив опыт временем в 32 мин, приступили к анализу результатов. Изучение продуктов показало, что при разнонаправленных изменениях массы в 1.4 и ‒3.1 мас. % и весьма посредственных проводящих качествах удельные сопротивления полученных образцов в двух экспериментах получились практически одинаковыми – 0.013 и 0.012 Ом м (рис. 4).
Рис. 6.
Зависимость тока от времени: а – эксперимент V: концентрация 60 и 90 г/л, Ni-порошковый анод; б – эксперимент VI: электролит NiCl2∙6H2O – 300.00 г/л; FeCl3∙6H2O – 100.00 г/л, графитовый анод.
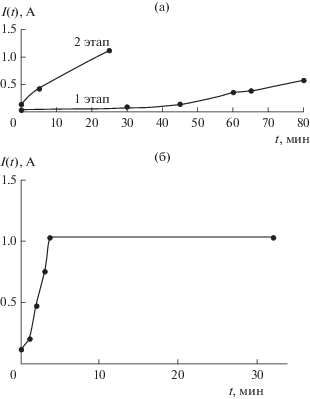
Эксперименты VII и VIII. Притом, что использование никелевого анода, очевидно, не способствует формированию продукта с высокой проводимостью, оставалось выяснить, насколько существенным может оказаться влияние воды. С этой целью никелирование навесок массой 10 и 20 г осуществили соответственно в растворе с составом Ni(CH3COO)2·4H2O – 105.0 г/л в водно-этиленгликолевой смеси (4 : 11, об.) и в насыщенном этиленгликолевом растворе безводного NiCl2 (концентрация соли – 180 г/л [40]). Графитовый анод использовали в обоих опытах. Электролиз в ацетатном растворе проводился при условной плотности тока 3.0 А/дм2 и привел к сильному загущению электролита. По причине сложности перемешивания процесс остановили на 20-й мин. Продиктованный желанием сравнить результат с полученным ранее в водной системе, выбор ацетата никеля очевидно явился неудачным. В то же время никелирование в этиленгликолевом растворе безводной соли проводили в течение 30 мин при значении тока, зафиксированном на уровне 1.03 А. Интересно отметить, что даже в условиях практического отсутствия воды применение графитового анода привело к более быстрому росту тока в сравнении с анодной сборкой с никелевым порошком. При этом кривая изменения тока во времени соответствует тем, что наблюдались в опытах с использованием графитового анода, но в которых применялся кристаллогидрат NiCl2∙6H2O (рис. 7). Однако в отличие от них, в эксперименте VIII графитовый анод неожиданно покрылся дендритными образованиями из металлического никеля, а раствор не показал какого-либо снижения pH. В двух данных экспериментах величина изменения массы определялась лишь у продукта никелирования в растворе безводной соли и соответствовала убытку в 2.5 мас. %. Притом, что значения удельных сопротивлений изначально отобранных для экспериментов VII и VIII порошков отличались более, чем на два порядка – 5.79 × 102 и 11.60 Ом м соответственно, сопротивления металлизированных продуктов оказались достаточно близкими – 2.13 и 9.82 Ом м (рис. 4).
Рис. 7.
Зависимость тока от времени. Эксперимент VIII: концентрация безводного хлорида никеля 180 г/л, графитовый анод.
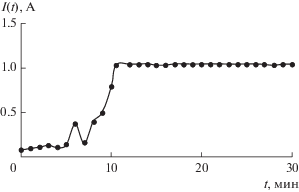
Эксперименты IX, X и XI. Дополнительные сведения о течении процесса металлизации при наличии в электролите небольших дополнительных количеств воды и ионов натрия были получены при проведении серии опытов по никелированию порошков карбонильного железа в условиях оперативной нейтрализации раствора путем добавления в него насыщенного раствора NaOH в этиленгликоле. Для эксперимента IX был взят электролит, оставшийся после эксперимента II, пополнен дополнительной порцией NiCl2∙6H2O (концентрация возросла до 125 г/л) и нейтрализован до pH 7. При массе навески в 50 г и использовании графитового анода электролиз проводился при 2.0 А в течение 50 мин. В ходе процесса кислотность жидкости регулярно отслеживали с помощью лакмусовой бумаги и раствор щелочи добавляли, как только снижался pH. Изучение продукта показало положительный массовый прирост в 1.28 мас. % и удельное сопротивление 0.65 × 10–3 Ом м, что соответствует продукту высокого качества (рис. 4). При этом, повторное проведение металлизации аналогичных навесок данным методом при той же силе тока и в том же электролите, но с концентрацией хлорида никеля, доведенной до 155 г/л в эксперименте X и 180 г/л – в эксперименте XI, с длительностью процесса в 50 и 41 мин, соответственно, привело к увеличению масс образцов на 3.24 мас. % в первом и на 1.62 мас. % во втором случае. Притом, что во всех трех опытах металлизировался порошок из одного источника с сопротивлением 19.60 Ом м, удельные сопротивления двух последних продуктов также отличались от изначального результата в сторону увеличения, составляя 0.26 и 1.51 × 10–2 Ом м (рис. 4). Следует заметить, что продукт эксперимента Х содержал следы Fe(III).
Эксперименты XII, XIII и XIV. Столь неожиданное и нелинейное снижение проводящих свойств при схожих условиях натолкнуло на мысль о влиянии на процесс металлизации накапливающихся в растворе продуктов побочных реакций. С целью расширения представления о сути проблемы, была проведена серия опытов с последовательным использованием одного и того же раствора, каждый раз пополняемого хлоридом никеля без процедуры нейтрализации. Череду металлизаций проводили с навесками порошка массой 20 г и графитовым анодом при токе 1.5 А. Изначально никелированию подвергли порошок со сферическими частицами и сопротивлением 32.70 Ом м. Эксперимент XII проходил в два этапа по 30 мин, причем перед началом каждого электролит пополнялся дополнительными количествами NiCl2∙6H2O. Так первая и вторая части начинались при концентрации 135 и 180 г/л соответственно. В двух последующих опытах осуществлялась металлизация продуктов помола в изопропаноле (пластинчатые частицы с удельным сопротивлением 1.51 Ом м) и в гептане (осколочные частицы с удельным сопротивлением 1.44 × 10–2 Ом м). Эксперименты XIII и XIV длились 60 мин в электролите с концентрациями хлорида никеля 230 и 255 г/л соответственно. В то время как pH растворов оставался на уровне 1–2 во всех экспериментах, лишь дробленый в изопропаноле образец показал убыток массы в 2.25%. Порошки же со сферическими и осколочными частицами демонстрировали положительный массовый прирост в 2.0 и 1.15% соответственно. Измерение сопротивления продуктов выявило их высокую способность проводить электрический ток, несмотря на то, что у порошка со сферическими частицами оно было в два раза выше, чем у никелированных дробленых образцов – 1.31 × 10–3 Ом м (эксперимент XII) против 0.65 × × 10–3 Ом м (эксперименты XIII и XIV) соответственно (рис. 4).
Эксперимент XV. В продолжение экспериментов с использованными растворами была повторена металлизация порошка с осколочными частицами. Электролит, использовавшийся ранее лишь однажды в эксперименте III, имел концентрацию NiCl2∙6H2O – 25 г/л и pH 1–2. Попытка получить представление о процессе при столь низкой концентрации дала ожидаемый результат: за 15 мин с начала электрохимического процесса ток вырос только до 0.6 А. В отличие от описанных выше опытов, процесс было решено не прерывать, а добавить дополнительное количество хлорида никеля массой 5 г во время металлизации. Учитывая постоянное магнитное перемешивание порошка и тот факт, что раствор уже начал нагреваться, высыпанный в кювету порошок не перемешивали, позволив ему раствориться самостоятельно. В результате введения дополнительной порции соли, скорость роста тока увеличилась, и за 10 мин ток достиг значения 1.5 А, на котором был зафиксирован. Процесс остановили через 60 мин после включения тока, после чего продукт подвергли стандартному исследованию. Было обнаружено, что удельное сопротивление соответствовало продукту с высокой проводимостью 0.65 × 10–3 Ом м (рис. 4), а масса уменьшилась на 2.2%.
Эксперимент XVI. Как свидетельствуют описанные выше результаты, прямая корреляция между проводимостью продукта и изменением массы образца, в частности, при частичном переходе железа в раствор, не прослеживается. При этом было замечено, что даже при очевидных потерях железа тест, проводимый с помощью роданида аммония, на присутствие Fe3+ в растворе по окончании металлизации всегда положителен, если pH электролита низкий, и отрицателен, когда он нейтрален. Последний, описываемый в данной статье опыт, предоставляет дополнительные сведения и позволяет несколько шире взглянуть на совокупность наблюдаемых явлений. Данный эксперимент проводили в два этапа, причем такие параметры, как pH раствора, массовые изменения материала и его проводящие качества, отслеживали в каждом из них. Для никелирования было отобрано 50 г порошка карбонильного железа со сферическими частицами и удельным сопротивлением 11.60 Ом м. Анод применялся графитовый. Первый этап проводился в оставшемся после эксперимента V электролите с составом: NiCl2·6H2O – 90 г/л, pH 7, и длился 35 мин (рис. 8). При этом ничтожный рост тока наблюдался до 30-й мин, после которой последовало его резкое увеличение до 3.0 А. В результате осуществления первого этапа были замечены снижение pH электролита и прирост массы порошка на 0.48% с увеличением его удельного сопротивления на порядок, до значения 1.31 × 102 Ом м (рис. 4). При этом, несмотря на кислую реакцию, обнаружить Fe3+ с помощью роданида аммония не удалось. Для проведения второго этапа в раствор ввели дополнительное количество хлорида никеля до уровня 120 г/л, оставив pH на уровне 1–2, после чего картина роста тока не отличалась от наиболее часто наблюдаемой в опытах с графитовым анодом. Через 12 мин после начала ток достиг значения 1.03 А, на котором был зафиксирован, а по прошествии 30 мин с начала металлизации процесс был прерван. Тест на присутствие в электролите иона Fe3+ с помощью роданида аммония по-прежнему давал отрицательный результат. Исследование же продукта показало, что масса порошка увеличилась еще на 0.58%, а удельное сопротивление снизилось до уровня ниже 0.65 × 10–3 Ом м (рис. 4).
Рис. 8.
Зависимость тока от времени. Эксперимент XVI: концентрация 90 и 120 г/л на первом и втором этапе соответственно, графитовый анод.
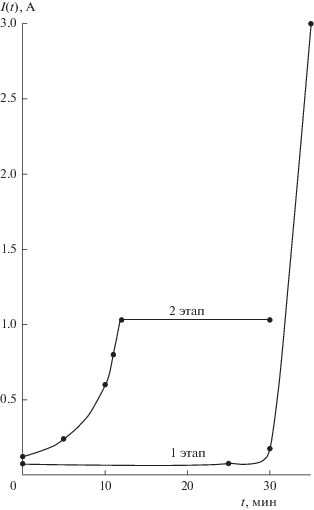
Наблюдаемый разброс удельных сопротивлений никелированных порошков, который сопровождается труднопредсказуемыми изменениями массы, поставил вопрос о реальном содержании никеля в продуктах металлизации. В этой связи образцы, полученные в некоторых из описанных выше экспериментов, проанализировали рентгенолюминесцентным методом (табл. 1), из результатов которого видно, что реальное количество никеля не пропорционально количеству прошедшего через раствор заряда Q, а также не соответствует массе металла, рассчитанной по закону Фарадея, что свидетельствует о наличии побочных процессов. Интересно отметить, что в двух опытах количество никеля превысило теоретически возможное, причем, если в эксперименте XVI избыток мал и мог бы считаться ошибкой, в эксперименте XV им невозможно пренебречь. Вместе с тем, учитывая очевидные потери железа и тот факт, что в эксперименте V масса образца непредсказуемо возросла, как если бы в системе появилось на 0.20 г больше металлического железа, можно предположить, что наблюдаемому изменению массы соответствует выражение ∆m = m1 – m0 = = ∆mFe + mNi(ЭХ) + mNi(Х) + mдплн, где m0 и m1 – экспериментально наблюдаемая масса образца до и после металлизации, а ∆mFe, mNi(ЭХ), mNi(Х) и mдплн – реальные и нам в действительности неизвестные: масса перешедшего в раствор железа (отрицательная величина), количества электрохимически и химически осажденного никеля и масса дополнительно оседающего неизвестного вещества, имеющего аморфную либо очень слабо кристаллизованную структуру, что не позволяет его идентифицировать с помощью рентгенофазового анализа (рис. 9).
Таблица 1.
Концентрации никеля в образцах, обнаруженных посредством рентгенолюминесцентного анализа, величина заряда, пропущенная через раствор, и масса избыточного никеля в нанесенном покрытии
Количественные параметры | Эксперимент | ||||||||
---|---|---|---|---|---|---|---|---|---|
III | IV | V | VI | VIII | XIII | XIV | XV | XVI | |
xэксп (Ni), мас. % | 2.93 | 1.21 | 0.38 | 1.17 | 0.30 | 4.27 | 2.46 | 15.53 | 1.24 |
Q, Кл | 4095 | 1858 | 1988 | 1854 | 1389 | 4683 | 4683 | 4713 | 2016 |
∆mFe, г | 0.24 | 0.65 | 0.85 | 0.56 | 1.28 | 0.27 | 3.44 | 0.34 | |
mнеизв, г | – | – | 0.20 | – | – | – | – | – | – |
mNi, г | 0.60 | 0.24 | 0.08 | 0.23 | 0.06 | 0.83 | 0.50 | 3.04 | 0.63 |
mNi изб, г | – | – | – | – | – | – | – | 1.61 | 0.017 |
Примечание. xэксп (Ni) – массовая доля никеля в продукте электрохимической обработки;
Q = ∫I(t)dt – суммарный заряд, прошедший через электролит за время процесса;
∆mFe – экспериментально наблюдаемая потеря массы железа; mнеизв – экспериментально доказанный прирост вещества неизвестного состава; mNi – масса осажденного никеля по результатам рентгенолюминесцентного анализа; mNi изб – масса никеля, избыточная по отношению к теоретически возможному количеству согласно закону Фарадея.
Рис. 9.
Рентгенограммы продуктов никелирования: а – эксперимент XII (частицы сферические), б – эксперимент XIV (частицы осколочные).
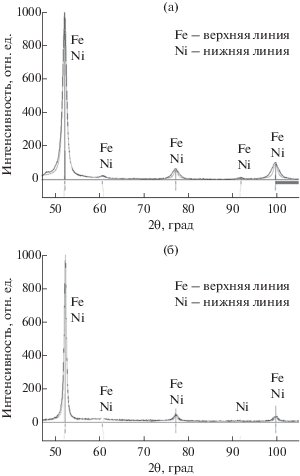
Как и в случае продуктов пробных опытов, проводимых с водными растворами, были сделаны СЭМ-фотографии с целью сравнения продуктов экспериментов XII и XIV с их необработанными предшественниками (рис. 10).
Рис. 10.
Эксперимент XII (сферические частицы): а – изначальный порошок (масштабный отрезок – 10 мкм) и б, в – продукт его никелирования (масштабные отрезки – 10 и 50 мкм). Эксперимент XIV (продукт помола в гептане, осколочные частицы): г – изначальный порошок (масштабный отрезок – 50 мкм) и д, е – продукт его никелирования (масштабные отрезки – 50 и 100 мкм).
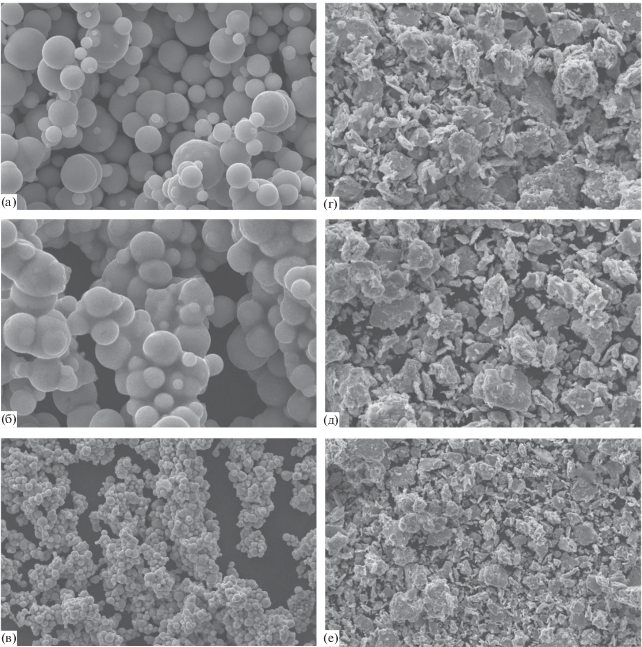
На представленных СЭМ-фотографиях видно, что в продуктах никелирования сферические частицы более агломерированы в сравнении с молотыми. Тем не менее, это не дает однозначного ответа на вопрос о том, является ли наблюдаемый эффект результатом воздействия магнитного поля, так как судя по сгруппированности сферических частиц в необработанном порошке, существовала вероятность того, что нанесение никеля лишь усилило изначальную тенденцию. Тот факт, что подобной агломерации не наблюдается в молотом порошке, ослабляет предположение о возможности побочного влияния поля. В то же время оплывшие формы никелированных сферических частиц, напоминающих застывший воск, скорее говорят в пользу того, что методом вращающегося магнитного поля действительно получаются сплошные металлические покрытия. Данный вывод, правда, нельзя сделать в случае дробленых частиц, прежде всего по причине неправильности их формы, скрывающей данный эффект. Однако представленные на рис. 9 рентгенограммы констатируют факт наличия никеля в обоих образцах.
Несмотря на то, что описанные выше процессы очевидно нуждаются в более глубоких исследованиях, собранные наблюдения дают возможность сделать предположения о превращениях, происходящих во время электролиза. Во-первых, как видно из диаграммы на рис. 4, именно в кислых растворах продукты никелирования получаются наиболее высокопроводящими, что достигается только посредством использования графитового анода. При этом применение анодной сборки с карбонильным никелем (эксперименты IV и V) значительно снижает способность никелированного порошка проводить электрический ток. Сходный эффект наблюдается и при металлизации с графитовым анодом в растворе безводного хлорида никеля (эксперимент VIII) или в растворе, в котором предварительно проводили металлизацию с использованием никелевой анодной сборки (эксперимент XVI на первом этапе). Данные факты наводят на мысль о конкурирующих процессах образования на поверхности частиц пассивирующего слоя и его разрушения в результате взаимодействия с кислым электролитом и осаждения никеля. Данная версия подкрепляется значительным улучшением проводящих качеств порошка, наблюдаемого в эксперименте XVI после его тщательной отмывки по завершении первого этапа и осуществления металлизации заново при pH 1–2. Добавление же NaOH в экспериментах X и XI, сделанное для нивелирования действия кислоты на железный порошок, очевидно, лишь способствовало образованию пассивирующего слоя и, как результат, повышению удельного сопротивления продукта. Пассивации частиц, должно быть, способствует и избыток в растворе железа. Однако, поскольку условием его нахождения в нем является способствующая депассивации кислая среда, влияние Fe3+ остается незначительным. Как показывает результат эксперимента VI, проводящие свойства полученного продукта вполне удовлетворительны.
Во-вторых, анодные процессы, происходящие в разных условиях, очевидно имеют отличия, о чем свидетельствует ряд фактов. В то время как в ходе электролиза этиленгликолевого раствора NiCl2∙6H2O образуются продукты окисления растворителя, включающие гликолевую и щавелевую кислоты [41], а также некоторое количество HCl, стабильная нейтральность электролита при применении содержащей никелевый порошок анодной сборки наводит на мысль, что в этом случае образующиеся кислоты взаимодействуют с металлом анода, таким образом, попадая в раствор уже в виде анионов и хелатных комплексов, которые, скорее всего, и ответственны за пассивацию поверхности частиц. Это отчасти подтверждается ухудшением проводящих свойств металлизируемого порошка, наблюдаемым при увеличении концентрации электролита в эксперименте IV, увеличением массы образца за счет “неизвестного вещества” в эксперименте V (табл. 1), а также эффектами в эксперименте XVI, описанными выше. Не имеющие же возможности прореагировать подобным образом в случае использования графитового анода продукты анодного окисления являются причиной снижения pH. На это указывает и более высокая проводимость растворов, использованных с графитовым анодом, и медленный рост тока в первые 30 мин в экспериментах V и XVI, причем резкий скачок тока в последнем, проводимом с применением оставшегося после эксперимента V электролита и графитового анода, скорее всего, свидетельствует о накоплении достаточного количества кислоты и изменении типа проводимости раствора [42]. При этом нарастание никелевых дендритов на аноде в опытах с анодной сборкой (эксперименты IV и V) и эксперименте VIII, осуществленном с графитовым анодом и раствором безводного хлорида никеля в этиленгликоле, предположительно отражает процесс восстановления иона Ni3+, образующегося при анодном окислении Ni2+ [42]. В то время как в опытах, в которых наблюдали падение pH, ион Ni2+ всегда был окружен шестью молекулами воды, образующими первую координационную сферу [43], в остальных процессах либо изначально присутствовали (эксперимент VIII), либо образовывались (эксперименты IV и V) ионы никеля, непосредственно сольватированные этиленгликолем [43], что предоставляло возможность прямого взаимодействия с ним иона Ni3+, в результате чего он мог неконтролируемо восстанавливаться до металла.
В-третьих, судя по непропорциональности количества осажденного металла прошедшему через электролит суммарному заряду (табл. 1), продукты анодных процессов, скорее всего, оказывают влияние на катодные превращения. Частичное растворение железа наблюдалось как при низком pH, так и в процессах, где электролит оставался нейтральным (эксперименты IV, V и VIII), однако, причины этих потерь, очевидно, разные. В то время как присутствие кислой среды является фактором, ожидаемо вызывающим переход железа в раствор, в случае нейтральных электролитов его растворение могло быть результатом взаимодействия с никелевыми хелатными комплексами с образованием еще более прочных комплексов. Данная версия отчасти подтверждается возможностью обнаружить посредством роданида аммония ион Fe3+ в кислых растворах и невозможностью это сделать в нейтральных. В то же время известно, что оксалатные хелаты Fe3+ обладают высокой прочностью, и стабильность таких комплексов падает в ряду Fe3+$ \gg $ Ni2+ > Fe2+ [40, 44]. Поэтому, если помимо основного электрохимического процесса движущей силой превращений на катоде при нейтральном pH является образование оксалатных комплексов железа(III), то возможно предположить, что переходящее в раствор железо может выступать в качестве восстановителя никеля. При этом, ввиду того, что появление никеля, осажденного сверх теоретически возможного согласно закону Фарадея, было экспериментально зарегистрировано только в экспериментах XV и XVI, в которых электролит был кислым, возможно предположение, что фактором, влияющим на химическое восстановление никеля, может выступать процесс взаимодействия железа с кислотами, сопровождаемый переходом Fe2+ в Fe3+, что косвенно подтверждается некоей “корреляцией” между очевидными количествами “лишнего” никеля и потерянного железа (табл. 1). В то же время в настоящий момент данная гипотеза опирается исключительно на результаты рентгенолюминесцентного анализа, данные о массовых изменениях образцов и наблюдения за ходом процессов, по причине чего не представляется возможным сказать определенно, имело ли место химическое восстановление никеля во всех экспериментах или только в некоторых, каковы условия реакции и существует ли пороговая концентрация для ее начала, является ли данный процесс доминирующим, а также то, участвует ли в восстановлении металла этиленгликоль. При этом, судя по тому, что в эксперименте XV металлизируемый порошок оказался в области, где раствор мог иметь концентрацию, близкую к насыщению, химическому восстановлению никеля должно способствовать высокое содержание хлорида никеля и нагревание.
ВЫВОДЫ
Изначально имевшая сугубо технологические задачи, данная работа показала действенность метода, основанного на гальваническом никелировании порошков карбонильного железа при непрерывном их перемешивании вращающимся магнитным полем. В частности, в результате металлизации наблюдалось улучшение проводящих свойств порошков на 1.3–6.3 порядков в зависимости от свойств конкретного изначального материала, причем наиболее электропроводные из продуктов обработки имели удельное сопротивление на уровне 0.65 мОм м. Полученные данные дают основание полагать, что гальваническая обработка непрерывно вращающихся и при этом удерживаемых в контакте с остальным порошком частиц позволяет создавать на их поверхностях сплошные покрытия.
Использование в электрохимическом никелировании растворов на основе этиленгликоля повысило эффективность металлизации в сравнении с проведением процесса в водных растворах. Данный этиленгликолевый растворитель видится технологически более предпочтительным, растворы практически не требуют регенерации, нуждаясь лишь в периодическом пополнении содержания хлорида никеля, что имеет ценность с позиций экологии. В результате проделанной работы выявлены основные факторы, оказывающие отрицательное и положительное влияние на формирование продукта с высокой проводимостью. В то время как первые включают использование никелевого анода, абсолютное отсутствие воды, повышение pH электролита, способствующие образованию на поверхности металлизируемых частиц пассивирующего слоя, а также плохую отмывку продукта, вторые связаны с никелированием в кислых высококонцентрированных электролитах с графитовым анодом, что способствует разрушению пассивирующего покрытия. При этом, ввиду падения сопротивления растворов с температурой, высокие токи, разогревающие раствор и ускоряющие осаждение, также находятся в числе положительных факторов.
Список литературы
Ishigure, Y., Iijima, S., Ito, H., Ota, T., Unuma, H., Takahashi, M., Hikichi, Y., and Suzuki, H., Electrical and elastic properties of conductor-polymer composites, J. Mater. Sci., 1999, vol. 34, p. 2979. https://doi.org/10.1023/A:1004664225015
Kikegawa, K., Kuhara, R., Kwon, J., Sakamoto, M., Tsuchiya, R., Nagatani, N., and Nonomura, Y., Physical origin of a complicated tactile sensation: ‘shittori feel’, R. Soc. Open Sci., 2019, vol. 6, p. 190039. https://doi.org/10.1098/rsos.190039
Oh, J.-S., Sohn, J.W., and Choi, S.-B., Material Characterization of Hardening Soft Sponge Featuring MR Fluid and Application of 6-DOF MR Haptic Master for Robot-Assisted Surgery, Materials, 2018, vol. 11, p. 1268. https://doi.org/10.3390/ma11081268
Волков, А.И., Жарский, И.М. Большой химический справочник, Минск: Современная школа, 2005. 608 с. [Volkov, A.I. and Zharskiy, I.M., Comprehensive Handbook of Chemistry (in Russian), Minsk: Sovremennaya Shkola, 2005. 608 p.]
Бахтияров, А.В., Степанов, Г.В., Стороженко, П.А. Способ и устройство с вращающимся магнитом для электрохимической металлизации магнитных порошков, Пат. 2684295 (Россия). 2018. [Bakhtiiarov, A.V., Stepanov, G.V., and Storozhenko, P.A., Method and apparatus supplied with a rotating magnet for electrochemical metallization of magnetic powders, Patent 2684295 (Russia), 2018.]
Petek, T., Hoyt, N.C., Savinell, R.F., and Wainright, J.S., Characterizing Slurry Electrodes Using Electrochemical Impedance Spectroscopy, J. Electrochem. Soc., 2016, vol. 163, no. 1, p. A5001. https://doi.org/10.1149/2.0011601jes
Fleischmann, M. and Oldfield, J.W., Fluidised bed electrodes: Part I. Polarisation predicted by simplified models; Part II. The effective resistivity of the discontinuous metal phase, J. Electroanal. Chem., 1971, vol. 29, no. 2, p. 211. https://doi.org/10.1016/S0022-0728(71)80084-0
Kumar, S., Ramamurthy, T., Subramanian, B., and Basha, A., Studies on the Fluidized Bed Electrode, Intern. J. Chem. Reactor Engineering (article A41), 2008, vol. 6, p. 1.
Oriňakova, R., Kupkova, M., Dudrova, E., Kabatova, M., and Šupicova, M., The Role of Coating in the Cellular Material Preparation, Chem. Pap., 2004, vol. 58, no. 4, p. 236.
Fečková, Z., Surface Treatment of Powder Material by Metal Coatings – Study of Corrosion Properties, J. Metals, Materials and Minerals., 2007, vol. 17, no. 1, p. 41.
Lux, A.L. and Gálová, B.M., Electrode Process of Copper and Nickel Deposition on Pressed Iron Powder Electrodes., Chem. Papers, 1994, vol. 48, no. 5, p. 330.
Wolfgang, S., Coated metal powder and method for producing the same, Patent DE19823341 (Germany), 1998.
Eiki, T., Kiyoshi, T., Youichi, K., and Takahiro, F., Electroplating of fine particles with metal, Patent 4954235 (US), 1990.
Zhang, J., Yan, S.G., and Wagner, F.T., Method of treating nanoparticles using an intermittently processing electrochemical cell, Patent 2009145772 (US), 2009.
Hayakawa, H., Ito, M., and Takeda, K., Plating device, Patent JP2011074482 (Japan), 2011.
Hayakawa, H., Ito, M., and Takeda, K., Plating apparatus, Patent JP2012062566 (Japan), 2012.
Adzic, R. and Vukmirovic, M., Apparatus and method for the synthesis and treatment of metal monolayer electrocatalyst particles in batch or continuous fashion, Patent 2013056359 (US), 2013.
Takeshima, E. and Watanabe, Y., Electroplating method for powder, Patent JPH0544083 (Japan), 1993.
Кремнев, Л.С., Котова, Н.Т. Устройство для электрохимической металлизации порошков, Пат. 1183296 (СССР). 1985. [Kremnev, L.S. and Kotova, N.T., Apparatus for electrochemical metallization of powders, Patent 1183296 (USSR), 1995.]
Beane, G.L., Johnson, C.E., Kelley, D.R., and Lashmore, D.S., Method for electrochemical fluidized bed coating of powders, Patent 6254757 (US), 2001.
Beane, G.L., Johnson, C.E., Kelley, D.R., and Lashmore, D.S., Electrochemical fluidized bed coating of powders, Patent WO9741279 (WIPO), 1997.
Ito, M. and Takeda, K., Apparatus for producing metal-coated particle, Patent JP2010285663 (Japan), 2010.
Fujii, T., Kojima, Y., Takatsu, K., and Takeshima, E., Electroplating of fine particles with metal, Patent 4908106 (US), 1990.
Yih, P., Method for electroplating metal coating(s) on particulates at high coating speed with high current density, Patent WO9940241 (WIPO), 1999.
Yih, P., Method for electroplating of micron particulates with metal coatings, Patent 5911865 (US), 1999.
Yih, P., Method for electroplating metal coating(s) particulates at high coating speed with high current density, Patent 6010610 (US), 2000.
Eichman, J.W. and Griego, T.P., Submicron and nano size particle encapsulation by electrochemical process and apparatus, Patent 2002179430 (US), 2002.
Ito, M., Plating device, Patent JP2014169488 (Japan), 2014.
Beane, G.L. and Lashmore, D.S., Coating particles in a centrifugal bed, Patent 6287445 (US), 2001.
Потапов, Ю.М., Мустафин, Р.Х., Кручинина, Н.А. Способ нанесения покрытия на металлические порошки, Пат. 1435397 (СССР). 1988. [Potapov, Yu.M., Mustafin, R.Kh., and Kruchinina, N.A., Method for plating on metal powders, Patent 1435397 (USSR), 1988.]
Eichman, J.W., Griego, T.P., and Velasquez, G., Electrodeposition apparatus and method using magnetic assistance and rotary cathode for ferrous and magnetic particles, Patent 2003038034 (US), 2003.
Гусев, С.В., Красовский, А.И., Кузьмин, В.П., Мамонов, С.К., Мирошников, Ф.Ф., Моисеев, Г.К., Москвин, Ю.И., Швайков, В.В. Устройство для электролитического нанесения покрытий на порошки, Пат. 1038067 (СССР), 1983. [Gusev, S.V., Krasovskiy, A.I., Kuzmin, V.P., Mamonov, S.K., Miroshnokov, F.F., Moiseyev, G.K., Moskvin, Yu.I., and Shvaykov, V.V., Apparatus for electrolytic coating of powders, Patent 1038067 (USSR), 1983.]
Горобец, С.В., Горобец, О.Ю., Двойненко, О.К., Лебеда, Г.Л. Влияние магнитостатических полей ферромагнитной подложки на электроосаждение никелевых дендритов. Физика металлов и металловедение. 2012. № 113. С. 137. [Gorobetz, S.V., Gorobetz, O.Yu., Dvoynenko, O.K., and Lebeda, G.L., Influence of magnetostatic fields of the ferromagnetic substrate on the electrodeposition of nickel dendrites, Fizika Metallov i Metallovedeniye (in Russian), 2012, no. 113, p. 137.]
Тихонов, К.И., Агафонова, Н.И. Электроосаждение металлов из органических растворителей. Учебное пособие, Ленинград: Технологический институт, 1979. 84 с. [Tikhonov, K.I. and Agafonova, N.I., Electrodeposition of metals from organic solvents. A study guide (in Russian), Leningrad: Technologicheskii Institut, 1979. 84 p.]
Зайченко, А.Д., Сизоненко, О.Н., Тафтай, Э.И., Присташ, Н.С., Торпаков, А.С. Влияние высоковольтной обработки порошковых композиций Fe–Ti–C и Fe–Ti–B–C на изменение их электрического сопротивления. Электрические контакты и электроды. – К.: ИПМ НАН України. 2014. С. 129. [Zaichenko, A.D., Sizonenko, O.N., Taftai, E.I., Pristash, N.S., and Torpakov, A.S., Influence of the high-voltage treatment of the Fe–Ti–C and Fe–Ti–B–C pulverulent compositions on their electrical resistance variation. Elektricheskiye kontakty i elektrody. – K.: IPM NAN Ukrainy (in Russian), 2014, p. 129.]
Бахвалов, Г.Т., Турковская, А.В. Коррозия и защита металлов, Москва: Государственное научно-техническое издание по черной и цветной металлургии, 1947. 400 с. [Bakhvalov, G.T. and Turkovskaya, A.V., Corrosion and protection of metals (in Russian), Moscow: Gosudarstvennoe nauchno-tekhnicheskoe izdanoe po chiornoi i izvetnoi metallurgii, 1947. 400 p.]
Rose, I. and Whittington, C., Nickel Plating Handbook, Brussels: Nickel Institute, 2014. 80 p.
Антихович, И.В., Крупник, С.М., Черник, А.А., Жарский, И.М. Электрохимическое осаждение никелевых покрытий из ацетатно-хлоридного электролита в импульсном режиме. Труды БГТУ. Химия и технология неорган. веществ. 2011. № 3. С. 8. [Antikhovitch, I.V., Krupnik, S.M., Chernik, A.A., and Zharskiy, I.M., Electrochemical deposition of nickel coatings from acetate-chloride-based electrolytes in the pulsed mode, Trudy BGTU. Khimiya i tekhnologiya neorgan. veschestv (in Russian), 2011, no. 3, p. 8.]
Пеганова, Н.В. Автореф. дис. “Электроосаждение никеля из разбавленных по металлу ацетатно-хлоридных электролитов никелирования в условиях стационарного и импульсного режимов электролиза”. Москва: Кафедра технологии электрохимических производств РХТУ им. Д.И. Менделеева, 2008. [Peganova, N.V., An abstract of the thesis “Electrodeposition of nickel from acetate-chloride solutions for metal electroplating at low concentrations of nickel in the steady-state and pulsed modes of electrolysis” (in Russian), Moscow: Chair of Electrochemical Production Technologies at RCTU after D.I. Mendeleyev. 2008.]
Лурье, Ю.Ю. Справочник по аналитической химии, М.: Химия, 1971. 456 с. [Lurye, Yu.Yu., Analytical Chemistry Handbook (in Russian), M.: Khimiya, 1971. 456 p.]
Hammerich, O., Chapter 16. Anodic Oxidation of Oxygen-Containing compounds. Organic Electrochemistry. Book 2, Baizer, M.M. and Lund, H., Eds, N.Y.: Marcel Dekker, Inc., 1989, p. 485.
Фиалков, Ю.Я., Грищенко, В.Ф. Электровыделение металлов из неводных растворов, Киев: Наук. думка, 1985. 242 с. [Fialkov, Yu.Ya. and Grischenko, V.F., Electroextraction of metals from non-aqueous solutions (in Russian), Kiev: Nauk. dumka, 1985. 242 p.]
Lond, P.B., Salmon, P.S., and Champeney, D.C., Structure of Ni2+ Solutions in Ethylene Glycol by Neutron Diffraction: An Observed Hydrogen Bond between the Solvent Ligands in the First and Second Cation Coordination Shells?, J. Am. Chem. Soc., 1991, vol. 113, p. 6420.
Hiroshi, O. and Brimblecombe, P., Potential Trace Metal-Organic Complexation in the Atmosphere, The Scientific World Journal, 2002, vol. 2, p. 767. https://doi.org/10.1100/tsw.2002.132
Дополнительные материалы отсутствуют.