Электрохимия, 2021, T. 57, № 3, стр. 171-189
Электрохимический синтез амино-Ц-кислоты
А. А. Конарев *
Федеральное государственное унитарное предприятие “Государственный научный центр “НИОПИК”
123995 Москва, ул. Большая Садовая, 1, корп. 4ГСП-5, Россия
* E-mail: konarev.niopik@gmail.com
Поступила в редакцию 08.05.2020
После доработки 02.10.2020
Принята к публикации 19.10.2020
Аннотация
Исследовано влияние условий препаративного восстановления 2-нитро-4,8-дисульфокислоты нафталина, в частности состава электролита, материала катода, плотности тока, температуры, концентрации исходной диаммонийной соли 2-нитро-4,8-дисульфокислоты нафталина, на выход 2‑амино-4,8-дисульфокислоты нафталина по веществу и по току. Определены оптимальные условия препаративного электросинтеза 2-амино-4,8-дисульфокислоты нафталина в аммиачной буферной среде с рН 7.0–8.4, обеспечивающие выход 2-амино-4,8-дисульфокислоты нафталина по веществу и по току соответственно 97.5–98.5 и 65.0–72.2%, которые апробированы на укрупненной лабораторной и пилотной установках с электролизером фильтр-прессной конструкции. На основании полученных экспериментальных данных на укрупненной лабораторной и пилотной установках разработана технология электросинтеза амино-Ц-кислоты, которая отражена в опытно-промышленном регламенте на производство амино-Ц-кислоты и в техническом задании на проектирование опытно-промышленного электролизера на токовую нагрузку 3 кА.
ВВЕДЕНИЕ
Аминосульфокислоты нафталина, в частности кислая натриевая соль 2-амино-4,8-дисульфокислоты нафталина (амино-Ц-кислота), 1-амино-3,6,8-трисульфокислота нафталина (Т-кислота), изомерная смесь 1,6- и 1,7-аминосульфокислот нафталина (Клеве-кислоты), являются важнейшими промежуточными продуктами в производстве красителей [1, 2]. В промышленности кислую натриевую соль 2-амино-4,8-дисульфокислоту нафталина (АДСКН) получают восстановлением чугунной стружкой соответствующей 2-нитро-4,8-дисульфокислоты нафталина (НДСКН), предварительно выделенной из нитросульфомассы в виде диаммонийной соли [3, 4]. Выход АДСКН по стадии восстановления составляет около 100%, а по стадии выделения из раствора – 78–79%. Производство АДСКН относится к разряду сложных многостадийных процессов, связанных с выделением из реакционных масс целевых изомеров сульфокислот, и отягощено большим количеством неутилизируемых твердых и жидких отходов. При получении 1 т АДСКН образуется 1.7 т железного шлама, который направляется в шламонакопитель и переработке не подвергается. Кроме того, выход и качество амино-Ц-кислоты зависят от активности чугунной стружки и ее подготовки перед восстановлением.
Наиболее узким местом в производстве амино-Ц-кислоты является стадия восстановления соответствующей диаммонийной соли НДСКН. Использование каталитического гидрирования диаммонийной соли НДСКН не исключает всех недостатков, присущих вышеуказанному способу восстановления. К тому же, каталитическое гидрирование НДСКН требует применения катализаторов на основе благородных металлов и дорогостоящего оборудования – автоклавов. В патентах [5, 6] приводятся данные по восстановлению диаммонийной соли НДСКН в виде магниевой или аммонийной соли НДСКН на катализаторе Pd/C или Pt/C в присутствии водного раствора формиата натрия и гидроокиси железа под давлением 5–30 бар при температуре 70–120°С и рН 4–5. В связи с недостатками каталитического восстановления диаммонийной соли НДСКН возникла задача поиска других методов восстановления, которые могли бы успешно конкурировать с традиционными.
Альтернативным методом получения АДСКН может быть электрохимическое восстановление диаммонийной соли НДСКН. Однако сведения по электрохимическому препаративному восстановлению НДСКН в научной и патентной литературе не приводятся, а лишь имеются данные о полярографическом восстановлении изомерных 1-нитро-4,8-дисульфокислоты нафталина и 2‑нитро-4,8-дисульфокислоты нафталина [7]. В то же время в работах [8, 9] исследовано препаративное электрохимическое восстановление технической изомерной смеси 1,6- и 1,7-нафтилнитросульфокислот в соответствующие аминосульфокислоты нафталина (Клеве-кислоты) в сильнокислой и аммиачно-буферной средах на различных катодных материалах. Более обстоятельно исследовано электрохимическое восстановление 1-нитро-3,6,8-трисульфокислоты нафталина в сильнокислой среде как в условиях препаративного восстановления, так и полярографического [10‒12]. Поскольку электрохимическое восстановление нитросульфокислот нафталина в соответствующие аминосульфокислоты осуществляется, судя по литературным данным [8–12], в различных средах, а электрохимическое восстановление диаммонийной соли НДСКН ранее не изучалось, поэтому настоящее исследование посвящено разработке препаративного электросинтеза АДСКН из соответствующего нитросоединения для создания электрохимической технологии получения амино-Ц-кислоты.
МЕТОДИКА ЭКСПЕРИМЕНТА
Поляризационные кривые на стеклоуглероде марки СУ-2000 (СУ) регистрировали с помощью полярографа ПУ-1 (Россия) в дифференциальном режиме. Применявшийся в работе стационарный электрод представлял собой торец стеклоуглеродного стержня диаметром 2 мм [13].
Ячейка представляла собой конический стеклянный сосуд объемом 20 см3 с термостатируемой рубашкой. Электродом сравнения служил насыщенный каломельный полуэлемент, относительно которого и приведены значения потенциалов. В качестве вспомогательного электрода использовали также насыщенный каломельный полуэлемент.
Для получения воспроизводимых результатов СУ шлифовали на мелкой шкурке, полировали до зеркального блеска фетром, пропитанным глицерином с оксидом алюминия. После промывки дистиллированной водой электрод выдерживали в концентрированной серной кислоте и снова тщательно промывали. Непосредственно перед записью каждой вольт-амперной кривой электрод промывали водой и протирали фильтровальной бумагой. Электролит, в который погружали электрод, продували инертным газом для удаления растворенного кислорода.
Фоновыми электролитами служили растворы NaOH с концентрацией 0.1–1.0 N и аммиачные буферные растворы с рН 7.0–8.4, а также растворы хлорида аммония с концентрацией 0.1–0.4 N.
Препаративный электросинтез амино-Ц-кислоты в гальваностатическом режиме проводили в лабораторном электролизере, изготовленном из стекла, с разделением катодного и анодного пространств катионообменной мембраной МК-40. Термостатируемый стеклянный электролизер имел пришлифованную крышку, в которой предусмотрены штуцеры для термометра, отбора проб, отвода газов из катодного и анодного пространств, а также для токоподводов к электродам.
Для электролиза применяли катоды из различных конструкционных материалов в виде перфорированного цилиндра с поверхностью 0.30 дм2. Анодом служила платиновая пластинка. Рабочий объем электролизера составлял 0.060–0.070 л. Необходимую температуру католита поддерживали с помощью термостата U-15 (Германия). Перемешивание электролита осуществляли магнитной мешалкой ММ-3М (Россия).
Для масштабирования и уточнения условий электросинтеза АДСКН электролиз в гальваностатическом режиме проводили на укрупненной лабораторной и пилотной установках на токовую нагрузку 20 и 100 А соответственно. Каждая из установок состояла из электролизера, позиция Э‑1, промежуточных стеклянных емкостей с рубашкой для анолита, позиция Е-1, и католита Е‑2, двух шестеренчатых насосов, позиции Н-1 и Н-2, фазоразделителей Ф-1 и Ф-2, выпрямителя тока, амперметра, вольтметра и трубопроводов с арматурой (рис. 1).
Рис. 1.
Принципиальная технологическая схема электросинтеза АДСКН на укрупненной лабораторной и пилотной установках.
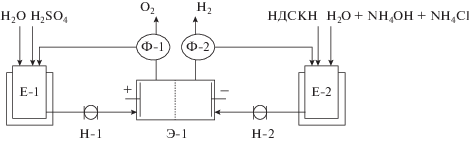
Лабораторный электролизер позиция Э-1 представлял собой двухкамерный аппарат фильтр-прессной конструкции с разделением анодного и катодного пространств катионообменной мембраной МК-40 (Россия). Катод применяли в виде перфорированной пластины из никеля марки Н3 с рабочей поверхностью 1 дм2, анодом служила пластина из свинцово-серебряного сплава (~1.0% Ag) с такой же поверхностью. Анолитом служил 10%‑ный раствор серной кислоты. Подачу и циркуляцию анолита и католита через соответствующие электродные камеры электролизера осуществляли шестеренчатыми насосами, позиции Н-1 и Н‑2, производительностью 150–180 л/ч из промежуточных стеклянных термостатируемых емкостей Е-1 и Е-2 соответственно. Объем католита составлял 0.25–0.30 л, а объем анолита – 0.15–0.20 л. Образующиеся в ходе электролиза газообразные продукты: водород отделяется от католита в фазоразделителе, позиция Ф-2, а кислород – в фазоразделителе, Ф-1.
В качестве источника тока использовали выпрямитель марки ВСА-5А-К (Россия). Силу тока в цепи и напряжение на ячейке и фильтр-прессном электролизере измеряли вольтмиллиамперметрами М2018 (Россия).
Пилотный электролизер представлял собой мембранный аппарат фильтр-прессного типа с двумя монополярными ячейками (рис. 2).
Рис. 2.
Пилотный мембранный электролизер на токовую нагрузку 100 А: 1 – стяжная плита; 2 – прокладка; 3 – анод; 4 – рама; 5 – мембрана; 6 – катод; 7 – распределительная вставка.
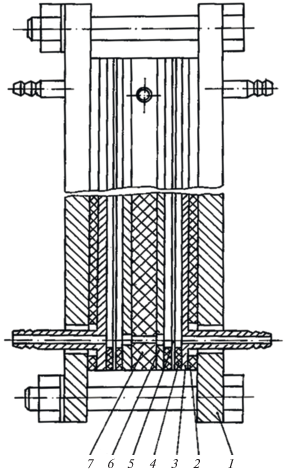
Этот тип электролизера характеризуется наибольшей производительностью по сравнению с другими известными электролизерами, работающими в промышленности [14], что важно для производств большой мощности, каким является производство амино-Ц-кислоты. Каждая ячейка включала в себя катод с рабочей поверхностью 4 дм2 и анод с такой же поверхностью, отделенные друг от друга катионообменной мембраной МК-40. Катоды изготовлены из никеля марки Н‑3 в виде пластины, а в качестве анода использовали свинцово-серебряный сплав (~1.0% Ag), как наиболее коррозионно-стойкий в растворах серной кислоты при анодной поляризации [15]. Возможный срок службы свинцово-серебряного сплава (1% Ag) в условиях электросинтеза аминосульфокислот нафталина 3–4 года. Легирование свинца серебром способствует образованию при анодной поляризации тетрагональной модификации диоксида свинца β-PbO2, содержание которого в оксидной пленке увеличивается с ростом концентрации серебра в сплаве. Тетрагональная модификация диоксида свинца β-PbO2 характеризуется меньшими размерами кристаллов по сравнению с ромбической модификацией α-PbO2, что способствует улучшению защитных свойств пленки.
Монополярные ячейки разделены между собой распределительной вставкой из полипропилена, имеющей в нижней и верхней частях штуцеры, служащие соответственно для подвода электролита в катодные пространства обеих ячеек и вывода продуктов электролиза из них. Для этой же цели служили соответствующие отверстия в катодах.
В анодные пространства электролит поступал через нижние отверстия в анодах и крайних рамах, продукты электролиза выводили через отверстия в верхней части анодов и крайних рамах.
При помощи нажимных плит и стяжных болтов обеспечивали герметичное соединение элементов электролизера в определенном порядке: электродов, резиновых прокладок, мембран, рам и распределительной вставки. Два верхних стяжных болта и шпильку использовали для закрепления кронштейнов, на которые устанавливали фазоразделители (сепараторы), изготовленные из винипласта, для разделения жидких и газообразных продуктов электролиза. Сепараторы снабжены соответствующими штуцерами для ввода и вывода этих продуктов в соответствии с технологической схемой (рис. 1).
Подачу и циркуляцию анолита и католита через соответствующие электродные камеры электролизера осуществляли шестеренчатыми насосами, позиции Н-1 и Н-2, производительностью 200 л/ч из промежуточных стеклянных термостатируемых емкостей Е-1 и Е-2 соответственно. Объем католита составлял 4–6 л, а объем анолита – 2–3 л. Образующиеся в ходе электролиза газообразные продукты: водород отделяется от католита в фазоразделителе, позиция Ф-2, а кислород – в фазоразделителе, позиция Ф-1.
Источником питания пилотной установки применяли выпрямительный агрегат марки ВАКГ-18/9-320 (Россия).
Диаммонийную соль НДСКН в виде пасты с содержанием основного вещества около 50–60% использовали с действующего производства – Березниковского химического завода.
Для полярографических исследований и поляризационных измерений диаммонийную соль НДСКН дважды перекристаллизовывали из дистиллированной воды с углем. Очищенная диаммонийная соль НДСКН представляла собой кристаллическое вещество светло-кремового цвета с содержанием основного вещества 99.6–99.8%.
АДСКН получали электрохимическим восстановлением соответствующей диаммонийной соли нитродисульфокислоты нафталина как в кислой, так и в аммиачной буферной средах по реакции:
В ходе препаративного электролиза полярографически и вольтамперометрически контролировали изменение концентрации исходного нитросоединения и продуктов реакции [13].
Концентрацию промежуточно образующихся нитрозо- и гидроксиламинодисульфокислот нафталина определяли вольтамперометрически на фоне 0.1 М раствора NaOH в дифференциальном режиме [13], а концентрацию АДСКН в реакционном растворе и в выделенном продукте – методом диазотирования [1]. Реакционный раствор, полученный после электрохимического восстановления диаммонийной соли НДСКН, предварительно подкисляли концентрированной серной кислотой до ее концентрации в растворе 30–40 г/л и загружали в термостатированный стеклянный аппарат с рамной мешалкой. При температуре 75–78°С и перемешивании загружали в аппарат активированный уголь и обрабатывали им раствор в течение 45–60 мин. Затем раствор аминодисульфокислоты нафталина отфильтровывали от угля и загружали в чистый аппарат. При температуре 75–78°С и перемешивании в очищенный раствор АДСКН загружали хлорид натрия, создавая его концентрацию 70–80 г/л. Образующуюся суспензию амино-Ц-кислоты размешивали в течение 1.0–1.5 ч при температуре 75–78°С. Затем, не останавливая мешалку, охлаждали суспензию до комнатной температуры. АДСКН выделяется из раствора в виде кислой натриевой соли. Выпавший осадок амино-Ц-кислоты отфильтровывали на стеклянном фильтре, тщательно отжимали и анализировали на соответствие полученного продукта требованиям ТУ 6-14-207-84. Электрохимически полученная амино-Ц-кислота по внешнему виду, содержанию кислой натриевой соли 2‑амино-4,8-дисульфокислоты нафталина в пасте, содержанию нерастворимого остатка, выходу диазо-Ц-кислоты и растворимости последней соответствует требованиям ТУ 6-14-207-84.
Исследование коррозионной стойкости катодных материалов проводили в аммиачном буферном растворе (1.1% NH4Cl + 0.7% NH4OH) с рН 8.0–8.5 при плотности тока 10–30 А/дм2, температуре 50–70°C, концентрации диаммонийной соли НДСКН – 0.35 М. Анолитом служил 10%‑ный раствор серной кислоты.
Установка для изучения коррозионной стойкости катодных материалов представляла собой электролизер с разделенными катионообменной мембраной МК-40 катодным и анодным пространствами. В качестве катода использовали образцы из различных материалов размером 40 × 10 × 3 мм, анодом служила платиновая пластина размером 40 × 10 × 1 мм. В качестве источника тока использовали выпрямитель ВСА-5А-К (Россия), а силу тока в цепи измеряли вольтмиллиамперметром М 2018 (Россия).
Объем раствора диаммонийной соли НДСКН рассчитывали исходя из 10-часового испытания одного образца. Перед опытом образцы катодов обезжиривали в этиловом спирте, промывали дистиллированной водой, высушивали и взвешивали с точностью до 0.0001 г. По окончании опыта образцы промывали водой, сушили при 100°С в течение 1.0–1.5 ч, затем взвешивали. Коррозию образцов оценивали по полной потере массы катода (г/м2) – разность массы образца до и после опыта. Исходя из полной потери массы электрода рассчитывали скорость коррозии (V, г/(м2 ч)) по формуле:
где m0 – масса исходного образца, г; m1 – масса образца после электролиза, г; S – площадь образца, м2; t – продолжительность электролиза, ч, а затем рассчитывали глубинный показатель коррозии (Vкп, мм/год) по формуле: где V – скорость коррозии, г/(м2 ч); γ – удельная масса образца, г/см3; 8.76 – переводной коэффициент.Количество выделяющегося водорода в ходе электролиза в электрохимической ячейке определяли по методике, приведенной в монографии [14], а в укрупненном лабораторном и пилотном электролизерах – газовым счетчиком марки ГСБ-400 (Россия).
РЕЗУЛЬТАТЫ И ОБСУЖДЕНИЕ
Поскольку в научной литературе не приводятся данные по препаративному электровосстановлению диаммонийной соли НДСКН, то начальный этап разработки условий электросинтеза амино-Ц-кислоты потребовал подробного изучения электрохимического поведения диаммонийной соли НДСКН методами полярографии, вольтамперометрии и электролиза при контролируемом потенциале, а также электролиза разбавленных растворов НДСКН в гальваностатическом режиме. В результате этих предварительных исследований нами установлено, что восстановление разбавленных растворов диаммонийной соли НДСКН с концентрацией 0.04 М предпочтительно проводить в аммиачной буферной среде c рН 8.3 на никелевом катоде, на котором достигается выход АДСКН по веществу 98.0% и выход по току 61.5%. В то же время препаративное восстановление 1-нитро-3,6,8-трисульфокислоты в соответствующую аминотрисульфокислоту нафталина эффективно протекает в сильнокислой среде на фоне 15–17%-ной серной кислоты на свинцовом или свинцово-сурьмянистом катодах [8, 10, 16]. Поэтому представлялось целесообразным исследовать растворы различного состава для восстановления диаммонийной соли НДСКН (табл. 1).
Таблица 1.
Влияние состава электролита на выход АДСКН по веществу и по току. Концентрация диаммонийной соли НДСКН – 0.35 М, плотность тока –10 А/дм2, температура 70°С
Материал катода | Электролит | Выход по веществу, % | Выход по току, % | рН раствора после электролиза |
---|---|---|---|---|
Свинец | Вода | 94.3 | 49.0 | 3.94 |
1.17%-ный раствор NaCl | 94.3 | 47.0 | 7.95 | |
1.1%-ный раствор NH4Cl | 96.0 | 76.0 | 3.87 | |
5.0%-ный раствор H2SO4 | 68.9 | 35.2 | 0.77 | |
15.5%-ный раствор H2SO4 | 76.8 | 42.7 | –0.04 | |
Сталь Х18Н10Т | Вода | 92.1 | 44.5 | 8.00 |
2.34%-ный раствор NaCl | 89.2 | 51.3 | 7.80 | |
2.14%-ный раствор NH4Cl | 93.7 | 49.0 | 7.80 | |
0.7% NH4OH + 2.14% NH4Cl | 97.5 | 39.0 | 8.00 | |
3.5% NH4OH + 2.14% NH4Cl | 94.5 | 31.0 | 8.75 |
Как видно из табл. 1, на свинцовом катоде выход АДСКН существенно зависит от природы электролита и составляет 68.9–96.0%. Более низкий выход АДСКН в кислых растворах связан с тем, что в этих условиях наряду с АДСКН в реакционных растворах накапливаются в больших количествах соответствующие нитрозо- и гидроксиламинопроизводные (20.0–24.0%), которые не удается восстановить из-за протекания конкурирующей реакции выделения водорода.
В ряде работ [1, 16–19] отмечалось, что арилгидроксиламины восстанавливаются с большой скоростью закисными солями железа и меди. По мнению авторов, соли железа и меди катализируют процесс дальнейшего восстановления арилгидроксиламина в амин благодаря осуществлению обратимых реакций в объеме раствора: Fe3+ ⇄ Fe2+ и Cu2+ ⇄ Cu+.
В случае электросинтеза ароматических аминосоединений соли железа и меди часто используются как катализаторы-переносчики электронов [16, 19]. При восстановлении диаммонийной соли НДСКН на свинцовом катоде в растворах серной кислоты с концентрацией 10–15% и добавкой сульфата закисного железа в количестве 0.08% выход гидроксиламинодисульфокислоты нафталина снижается с 20.0–24.0 до 8.7–11.9%, а с увеличением концентрации сульфата закисного железа до 0.16% еще больше уменьшается и составляет 4.5–6.4%. Дальнейшее увеличение концентрации сульфата закисного железа в растворе не влияет на выход промежуточного продукта, и его содержание в реакционном растворе остается сравнительно высоким, составляющим около 5.6–6.0%.
Наибольший выход АДСКН по веществу и по току как на свинцовом электроде, так и на катоде из стали Х18Н10Т достигается в растворе хлорида аммония и аммиачных буферных растворах, величина рН которых после электролиза составляет 7.80–8.75. При этом с увеличением рН заметно снижается выход АДСКН по веществу и по току. Поэтому для оптимизации состава аммиачного буферного раствора исследовано влияние концентрации гидроксида аммония и хлорида аммония на электросинтез АДСКН на катоде из никеля марки Н3 (табл. 2 и 3). На последнем, как показано в работе [9], эффективно протекает восстановление изомерной смеси 1,6- и 1,7-нитросульфокислот нафталина в аммиачной буферной среде.
Таблица 2.
Влияние концентрации гидроксида аммония на выход АДСКН по веществу и по току. Концентрация диаммонийной соли НДСКН – 0.35 М, плотность тока –10 А/дм2, температура 70°С, катод – никель марки Н3
Состав электролита | Выход по веществу, % | Выход по току, % | рН католита |
---|---|---|---|
0.7% NH4OH | 98.0 | 63.8 | 8.78 |
1.1% NH4Cl | 96.7 | 66.2 | 4.05 |
0.35% NH4OH + 1.1% NH4Cl | 98.2 | 74.2 | 4.54 |
0.7% NH4OH + 1.1% NH4Cl | 98.5 | 72.0 | 8.30 |
1.4% NH4OH + 1.1% NH4Cl | 98.1 | 73.1 | 8.60 |
5.0% NH4OH + 1.1% NH4Cl | 91.4 | 72.3 | 9.85 |
Таблица 3.
Влияние концентрации хлорида аммония на выход АДСКН по веществу и по току. Концентрация диаммонийной соли НДСКН – 0.35 М, плотность тока – 10 А/дм2, температура 70°С, катод – никель марки Н3
Состав электролита | Выход по веществу, % | Выход по току, % | рН католита |
---|---|---|---|
0.32% NH4Cl + 0.7% NH4OH | 98.1 | 73.4 | 8.77 |
0.55% NH4Cl + 0.7% NH4OH | 97.6 | 72.6 | 7.92 |
1.10% NH4Cl + 0.7% NH4OH | 98.5 | 72.0 | 7.60 |
1.87% NH4Cl + 0.7% NH4OH | 98.0 | 73.3 | 7.39 |
Как видно из табл. 2, при увеличении концентрации гидроксида аммония от 0.35 до 1.40% в присутствии 1.1% NH4Cl выход АДСКН по веществу и по току практически не изменяются и составляют соответственно 98.2–98.5% и 72.0–74.2%. С увеличением концентрации гидроксида аммония в растворе до 5.0% выход целевой АДСКН уменьшается и составляет 91.4%. Уменьшение выхода АДСКН по веществу с увеличением концентрации гидроксида аммония в католите обусловлено повышением рН раствора, что благоприятствует образованию побочных димерных веществ [14], на наличие которых указывают смолообразные продукты, появляющиеся в процессе электролиза в этих условиях.
При изменении концентрации хлорида аммония от 0.32 до 1.87% при постоянной концентрации гидроксида аммония (0.7%), как видно из табл. 3, выход АДСКН по веществу и по току практически не изменяется и составляет соответственно 97.6–98.5 и 72.0–73.4%. Как следует из приведенных данных в табл. 3, наиболее целесообразно восстановление диаммонийной соли НДСКН проводить в аммиачном буферном электролите составом: 1.1 – 1.87% NH4Cl + 0.35–0.7% NH4OH, который обеспечивает рН католита в ходе электролиза 7.40–7.60.
Из результатов, представленных в табл. 1–3, следует, что на выход АДСКН по веществу и по току влияет не только состав фонового раствора, но и природа катодного материала. Исследование влияния материала катода на электросинтез АДСКН проводили в растворе хлорида аммония, а также в аммиачных буферных растворах. В качестве катодных материалов исследовали: никель марки Н3, титан марки ВТ1-0, свинец, медь, сталь Х18Н10Т, сталь Ст. 3 и сталь ЭП-467. Данные этого исследования представлены в табл. 4 и 5 и на рис. 3 и 4.
Таблица 4.
Выход АДСКН по веществу и по току на различных катодных материалах в растворе 1.1%-ного хлорида аммония. Концентрация диаммонийной соли НДСКН – 0.35 М, плотность тока –10 А/дм2, температура 70°С
Материал катода | Выход по веществу, % | Выход по току, % | рН католита |
---|---|---|---|
Титан ВТ1-0 | 90.0 | 54.0 | 6.60 |
Никель Н3 | 96.7 | 66.2 | 4.05 |
Сталь Ст. 3 | 92.5 | 48.5 | 6.87 |
Свинец | 96.0 | 76.0 | 3.87 |
Сталь Х18Н10Т | 94.5 | 60.0 | 4.20 |
Медь | 97.1 | 60.3 | 4.20 |
Таблица 5.
Выход АДСКН на различных катодных материалах в аммиачном буферном растворе (1.1% NH4Cl + + 0.7% NH4OH) с рН 8.3. Концентрация диаммонийной соли НДСКН – 0.35 М, плотность тока – 10 А/дм2, температура 70°С
Материал катода | Выход по веществу, % | Выход по току, % | рН католита |
---|---|---|---|
Титан ВТ1-0 | 98.5 | 55.0 | 8.74 |
Никель Н3 | 98.5 | 72.2 | 8.95 |
Сталь Ст. 3 | 95.0 | 65.5 | 8.95 |
Свинец | 92.4 | 72.9 | 9.05 |
Сталь Х18Н10Т | 94.5 | 52.1 | 8.80 |
Медь | 98.0 | 68.8 | 8.90 |
Сталь ЭП-467* | 98.0 | 42.0 | 8.60 |
Рис. 3.
Зависимость изменения потенциала катода в 1.1%-ном растворе хлорида аммония от количества пропущенного электричества для различных электродных материалов: 1 – титан; 2 – н/сталь Х18Н10Т; 3 – никель; 4 – медь; 5 – сталь Ст. 3; 6 – свинец, а также зависимость выхода водорода по току (ВТ) от количества пропущенного электричества для различных электродных материалов: 11 – титан; 31 – никель; 41 – медь; 61 – свинец. Концентрация диаммонийной соли НДСКН – 0.35 М, плотность тока –10 А/дм2, температура 70°С.
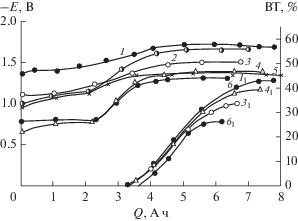
Рис. 4.
Зависимость изменения потенциала катода в аммиачном буферном растворе (1.1% NH4Cl + 0.7% NH4OH) с рН 8.3 от количества пропущенного электричества для различных электродных материалов: 1 – титан; 2– сталь Х18Н10Т; 3 – никель; 4 – сталь ЭП-467; 5 – свинец; 6 – медь; 7 – сталь Ст. 3, а также зависимость выхода водорода по току (ВТ) от количества пропущенного электричества для различных электродных материалов: 11 – титан; 31 – никель; 51 – свинец; 61 – медь. Концентрация диаммонийной соли НДСКН – 0.35 М, плотность тока –10 А/дм2, температура 70°С.
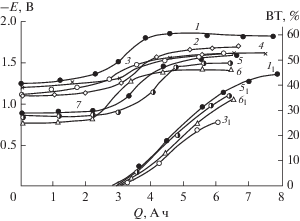
Как видно из табл. 4 и 5, выход АДСКН по веществу и по току зависит от материала катода и состава электролита. Наибольший выход АДСКН по веществу в растворе хлорида аммония получен на свинце, меди и никеле. Сравнительно меньший выход АДСКН по веществу (90.0–92.5%) на катодах из титана и стали Ст. 3 связан с неполной конверсией исходного нитросоединения и промежуточных продуктов из-за интенсивного выделения водорода (рис. 3).
В аммиачной буферной среде, как видно из табл. 5, на большинстве исследованных катодных материалов наблюдается высокий выход АДСКН по веществу, составляющий 94.5–98.5%. Исключением является свинцовый электрод, для которого выход целевого продукта ниже и составляет 92.4%. На титановом катоде и катоде из сплава ЭП-467 наблюдается высокий выход АДСКН по веществу, но при этом достигается низкий выход по току, 55.0 и 42.0% соответственно.
На титановом катоде процесс восстановления диаммонийной соли НДСКН как в растворе хлорида аммония, так и в аммиачном буферном растворе протекает с большей поляризацией электрода, на что указывает сдвиг потенциала в катодную область (рис. 3 и 4).
На свинцовом электроде в исследованных электролитах диаммонийной соли НДСКН восстанавливается с большим выходом по току, составляющим 72.0–76.0%. Очевидно, это связано с более высоким перенапряжением выделения водорода на свинце [20]. Действительно, как показали измерения объема выделяющегося водорода на свинце в ходе электролиза, выход водорода по току достигается самый низкий и составляет около 25.0% (рис. 3 и 4). Однако на меди и никеле, имеющих низкое перенапряжение выделения водорода [20], восстановление НДСКН в аммиачной буферной среде также протекает со сравнительно высоким выходом по току. Для этих металлов наиболее характерно образование на их поверхности при электролизе тонких губчатых сульфидных пленок, появляющихся, вероятно, в результате реакции частичного десульфирования диаммонийной соли НДСКН, приводящей к образованию побочных продуктов ${\text{SO}}_{{\text{3}}}^{{{\text{2}} - }},$ H2S, NiS и CuS. Такие же продукты образуются при реакции десульфирования аллилсульфоната натрия на никелевом катоде в буферных фосфатно-боратных растворах [14]. При электролизе аммиачного буферного раствора (0.55% NH4Cl + 0.7% NH4OH) с добавкой 6.0 г/л сульфита натрия на поверхности никелевого электрода также образуется сульфидная пленка, которая повышает эффективность электросинтеза АДСКН. Так, при плотности тока 15.0 А/дм2 и температуре 70°С на никелевом катоде в аммиачной буферной среде (0.55% NH4Cl + + 0.7% NH4OH) выход АДСКН по веществу и по току составляет соответственно 95.0 и 56.6%, а в присутствии 6.0 г/л сульфита натрия – выход АДСКН по веществу и по току увеличивается до 97.0 и 70.2% соответственно. При этом было обнаружено, что в католите с добавкой сульфита натрия, полученном после электролиза, практически отсутствует гидроксиламинодисульфокислота нафталина, что повышает выход целевой АДСКН по веществу в результате конверсии промежуточного продукта в аминосоединение.
Для всех электродных материалов отмечается постепенный сдвиг потенциала в область более отрицательных значений в ходе электролиза (рис. 3 и 4). В растворе хлорида аммония при пропускании количества электричества, близкого к теоретически необходимому (3.0 А ч) для восстановления диаммонийной соли НДСКН до гидроксиламинодисульфокислоты нафталина, потенциал для каждого из исследованных катодов изменяется незначительно. Дальнейшее восстановление гидроксиламинодисульфокислоты нафталина в АДСКН сопровождается резким сдвигом потенциала электрода в катодную область, а при пропускании количества электричества, необходимого (4.5 А ч) для восстановления исходного нитросоединения до АДСКН, потенциал электродов принимает наиболее отрицательное значение, достигая потенциалов выделения водорода. Поэтому образование АДСКН в конце электролиза протекает с преимущественным выделением водорода, снижающим эффективность целевого процесса.
В аммиачной буферной среде на исследованных катодных материалах достигаются более отрицательные значения потенциалов по сравнению с раствором хлорида аммония, но при этом выход водорода по току на никеле и меди заметно меньше (рис. 4). Это должно повышать селективность электровосстановления диаммонийной соли НДСКН до АДСКН, что и наблюдается на опыте. Вероятно, сравнительно высокий выход АДСКН по току на медном и никелевом электродах вызван как уменьшением истиной плотности тока за счет развитой губчатой поверхности сульфидов никеля и меди, так и, вероятно, каталитической активностью поверхности катода вследствие образования на ней сульфидов никеля и меди.
В случае медного катода увеличение выходов АДСКН по веществу и по току может быть вызвано участием в процессе восстановления катализаторов-переносчиков – ионов меди переменной валентности, образующихся при коррозии электрода в ходе электролиза, влияющих в основном на стадию восстановления гидроксиламинодисульфокислоты нафталина до АДСКН.
Выбор катодного материала определялся не только эффективностью процесса восстановления НДСКН, но и его коррозионной стойкостью в условиях электролиза (табл. 6). Коррозионную стойкость исследовали тех конструкционных материалов, на катодах из которых с большей эффективностью протекает электросинтез АДСКН.
Таблица 6.
Коррозионная стойкость катодных материалов в аммиачном буферном растворе (1.1% NH4Cl + 0.7% NH4OH) с рН 8.0–8.5. Продолжительность электролиза 10 ч
Материал катода | Плотность тока, А/дм2 | Температура, °С | Концентрация НДСКН, М | Глубинный показатель коррозии, мм/год |
---|---|---|---|---|
Никель Н3 | 10 | 50 | 0.35 | 0.16 |
10 | 60 | 0.35 | 0.26 | |
10 | 70 | 0.35 | 1.40 | |
10 | 80 | 0.35 | 4.00 | |
15 | 70 | 0.35 | 1.50 | |
20 | 70 | 0.35 | 4.50 | |
30 | 70 | 0.35 | 4.30 | |
15 | 50 | 0.35 | 0.30 | |
30 | 50 | 0.35 | 0.65 | |
15 | 70 | 0.41 | 2.90 | |
15 | 70 | 0.47 | 4.50 | |
15 | 70 | 0.54 | 7.00 | |
10 | 70 | 0.35 | 19.00* | |
Медь | 10 | 50 | 0.35 | 0.32 |
Титан ВТ1-0 | 10 | 70 | 0.35 | 0.005 |
Сталь Х18Н10Т | 10 | 70 | 0.35 | 0.006 |
Сталь Ст.3 | 10 | 50 | 0.35 | 11.6 |
10 | 70 | 0.35 | 16.7 | |
Сталь ЭП-467 | 10 | 70 | 0.35 | 0.35 |
Из данных, представленных в табл. 6, видно, что лучшей коррозионной стойкостью обладает титан ВТ1-0 и сталь Х18Н10Т. Однако на катодах, изготовленных из этих материалов, восстановление диаммонийной соли НДСКН протекает с выходом по току 55.0 и 52.1% соответственно против 72.2% – на никелевом катоде. Глубинный показатель коррозии для никелевого катода увеличивается с повышением температуры, плотности тока, концентрации НДСКН, а также концентрации гидроксида аммония. С увеличением концентрации гидроксида аммония до 5.0% наблюдается интенсивное коррозионное разрушение никелевого электрода, глубинный показатель коррозии которого составляет 19.0 мм/год. Очевидно, по этой причине повышается коррозия никелевого образца с увеличением концентрации исходного нитросоединения, так как в результате гидролиза диаммонийной соли НДСКН увеличивается концентрация гидроксида аммония в реакционном растворе. С увеличением температуры коррозионная устойчивость никеля в аммиачных буферных растворах понижается в результате его химического растворения с образованием аммиакатов [21]. Поэтому никель в качестве катодного материала может быть использован при плотностях тока 10–15 А/дм2 и температуре 50–60°С.
Таким образом, исходя из коррозионной стойкости и селективности электровосстановления диаммонийной соли НДСКН в соответствующую АДСКН, для дальнейших исследований выбраны никелевый катод и аммиачный буферный раствор (1.1% NH4Cl + 0.7% NH4OH) с рН 8.0–8.3.
Влияние плотности тока на электросинтез АДСКН исследовали при температурах 50 и 70°С. Результаты этого исследования приведены в табл. 7 и рис. 5, из которых следует, что с увеличением плотности тока как при температуре 50°С, так и при температуре 70°С выход АДСКН по веществу и по току снижается, а производительность и энергоемкость процесса при этом существенно возрастают.
Таблица 7.
Влияние плотности тока на выход АДСКН по веществу, по току и производительность электролизера в аммиачном буферном растворе (1.1% NH4Cl + 0.7% NH4OH) с рН 8.3. Концентрация диаммонийной соли НДСКН – 0.35 М, катод – никель марки Н3
Плотность тока, А/дм2 | Температура 50°С | Температура 70°С | ||
---|---|---|---|---|
выход по веществу, % | выход по току, % | выход по веществу, % | выход по току, % | |
10 | 98.2 | 65.0 | 98.5 | 72.2 |
15 | 97.6 | 58.5 | 97.0 | 65.0 |
20 | 97.5 | 54.1 | 95.0 | 60.0 |
30 | 95.0 | 48.0 | 92.0 | 53.0 |
40 | 90.5 | 44.2 | – | – |
Рис. 5.
Зависимость изменения производительности электролизера (Р) при температуре 50°С (1) и 70°С (2), а также энергоемкости процесса (W) при температуре 50°С (11) и 70°С (21) от плотности тока в аммиачном буферном растворе (1.1% NH4Cl + 0.7% NH4OH) с рН 8.3. Концентрация диаммонийной соли НДСКН – 0.35 М, катод – никель марки Н3.
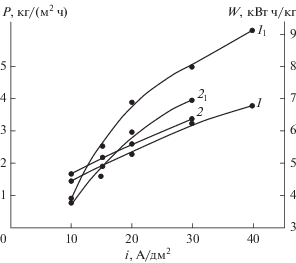
При увеличении плотности тока происходит более быстрый сдвиг потенциала электрода в область отрицательных значений, что повышает долю тока на побочный процесс выделения водорода (рис. 6). Так, при температуре 50°С с увеличением плотности тока от 10 до 40 А/дм2 выход АДСКН по току уменьшается с 65.0 до 44.2%, а выход водорода по току при этом возрастает с 32.0 до 55.0%.
Рис. 6.
Зависимость изменения потенциала катода от количества пропущенного электричества в аммиачном буферном растворе (1.1% NH4Cl + 0.7% NH4OH) с рН 8.3 при различной плотности тока, А/дм2: 1 – 10; 2 – 20; 3 –40, а также зависимость выхода водорода по току (ВТ) от количества пропущенного электричества при различной плотности тока, А/дм2: 11 – 10; 21 – 20; 31 – 40. Концентрация диаммонийной соли НДСКН – 0.35 М, температура 50°С, катод – никель марки Н3.
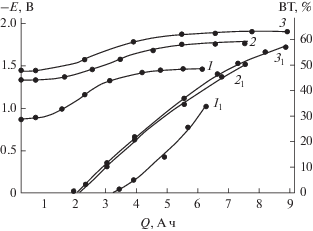
Уменьшение выхода АДСКН по веществу с увеличением плотности тока, по-видимому, связано с высоким отрицательным потенциалом электрода (–1.82…–1.91 В), реализуемым при плотностях тока 20–40 А/дм2, при котором возможно протекание побочных процессов, в частности восстановительное десульфирование диаммонийной соли НДСКН (рис. 4). Кроме того, при плотности тока 40 А/дм2 в ходе электролиза католит заметно подщелачивается. При этом рН католита повышается с 8.3 до 8.8. В то же время при плотностях тока 10–30 А/дм2 рН католита увеличивается лишь до 8.50–8.55. В более щелочных растворах возможно образование побочных димерных продуктов [14], приводящих к снижению выхода целевой АДСКН.
Как видно из табл. 7 и рис. 5, при температуре 70°С выход АДСКН по току и производительность электролизера при одной и той же плотности тока выше, а энергозатраты ниже, чем при температуре 50°С. Однако с повышением температуры и плотности тока усиливается коррозионное разрушение никелевого катода (табл. 6). Поэтому для электросинтеза АДСКН при температуре 50–60°С рекомендуется плотность тока 10 А/дм2, а при температуре 70°С – 15 А/дм2.
В аммиачном буферном растворе (1.1% NH4Cl + + 0.35% NH4OH) с рН 7.5 при восстановлении НДСКН с концентрацией 0.32 М на никелевом катоде исследовано изменение концентраций исходных, промежуточных и конечных продуктов в ходе препаративного электролиза (рис. 7).
Рис. 7.
Циклические дифференциальные вольтамперограммы реакционного раствора, получаемого при восстановлении диаммонийной соли НДСКН и снятого на СУ на фоне 0.1 N раствора NaOH в ходе электролиза в аммиачном буферном растворе (1.1% NH4Cl + 0.35% NH4OH) с рН 7.5. Время от начала электролиза: 6 ч – 1, 11, 12, 13; 7 ч – 2, 21, 22, 23; 8 ч – 3, 31, 32, 33; 10 ч – 4, 41, 42, 43. Регистрация пика Г осуществляется с чувствительностью прибора в 10 раз меньшей, чем пиков А, Б и В. Условия электролиза: концентрация диаммонийной соли НДСКН – 0.32 М, плотность тока 10 А/дм2, температура 60°С, катод – никель марки Н3.
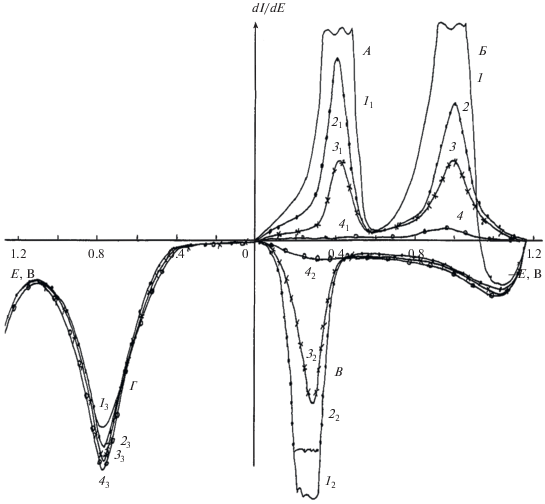
На рис. 7 приведены типичные циклические вольтамперограммы реакционного раствора, получаемого в ходе электролиза, при анализе его пробы через 6, 7, 8 и 10 ч после начала процесса. При катодной развертке потенциала наблюдается пик восстановления А с Ер –0.42 В, который имеет более положительный потенциал, чем пик восстановления НДСКН (пик Б с Ер –1.0 В), и, предположительно, отвечает процессу восстановления 2-нитрозо-4,8-дисульфокислоты нафталина, образующейся в условиях препаративного электролиза, до соответствующей гидроксиламинодисульфокислоты нафталина [22].
АДСКН в этих условиях на вольтамперограмме дает пик окисления Г с Ер + 0.68 В, высота которого увеличивается в ходе электролиза.
При препаративном восстановлении диаммонийной соли НДСКН в сильнокислой среде (5–15%-ной серной кислоте) пик А на вольтамперограмме также регистрируется, а на р. к. э. имеет более положительный Е1/2 по сравнению со СУ, который составляет –0.32 В на фоне 0.1 N NaOH.
На фоне аммиачного буферного раствора (1.1% NH4Cl + 0.35% NH4OH) с рН 7.5 диаммонийная соль НДСКН восстанавливается до гидроксиламинопроизводного, который при анодной развертке потенциала от –1.35 В дает пик окисления В с Ер –0.30 В. В работе [22] подобную анодную волну с Ер –0.28 В наблюдали при электровосстановлении тринатриевой соли 1-нитро-3,6,8-трисульфокислоты нафталина на золотом электроде с кольцом в щелочном растворе на фоне 0.3 М NaOH + 60 об. %. СН3СN и ее связывали с процессом окисления соответствующей гидроксиламинотрисульфокислоты нафталина до нитрозосоединения. В водно-спиртовых средах N‑фенилгидроксиламин, как отмечается в работах [23, 24], также легко анодно окисляется, давая волну окисления с Е1/2 +0.095…–0.27 В в интервале рН фона от 4 до 10. Поэтому наблюдаемый на вольтамперограмме пик В на рис. 7 несомненно отвечает процессу окисления гидроксиламинодисульфокислоты нафталина до соответствующего нитрозосоединения.
В работах [23–25] показано, что в водно-спиртовых средах нитрозобензол с затратой двух электронов обратимо полярографически восстанавливается до N-фенилгидроксиламина в диапазоне потенциалов от +0.075 до –0.285 В при изменении рН фона от 4 до 10, а нитробензол – от –0.415 до –0.74 В в этом же интервале рН. Для подтверждения природы пика А были сняты циклические вольтамперограммы восстановления диаммонийной соли НДСКН на СУ на фоне аммиачного буферного раствора (1.5% NH4Cl + + NH4OH) с рН 7.5 при изменении потенциала в катодную область от +0.2 до –1.3 В и в анодную область потенциалов от –1.3 до +0.2 В (рис. 8).
Рис. 8.
Циклические дифференциальные вольтамперограммы восстановления диаммонийной соли НДСКН на СУ в аммиачном буферном растворе (1.5% NH4Cl + NH4OH) с рН 7.5 (4) при различной концентрации нитросоединения, М: 1 – 3.8 × 10–4; 2 – 7.3 × 10–4; 3 – 10.4 × 10–4. Скорость развертки потенциала 20 мВ/с.
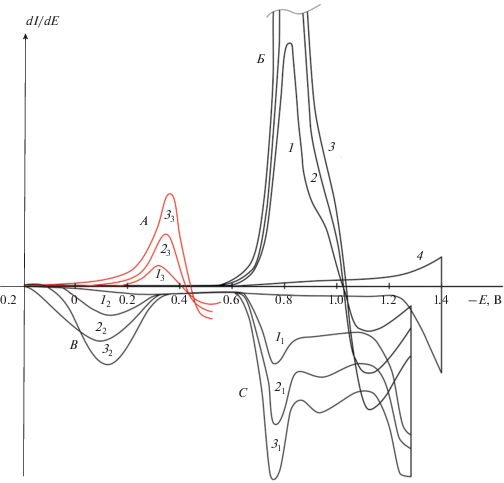
На катодной ветви циклических поляризационных кривых, как видно из рис. 8, наблюдается один необратимый пик Б восстановления диаммонийной соли НДСКН с Ер –0.83 В с затратой четырех электронов до соответствующего гидроксиламинопроизводного. При изменении развертки потенциала в анодном направлении от потенциала – 1.3 до +0.20 В на анодной ветви вольтамперограммы наблюдаются два пика окисления C и В. Ер анодных пиков C (рис. 8, кривые 11, 21 и 31) практически совпадает с Ер восстановления диаммонийной соли НДСКН (рис. 8, кривые 1, 2 и 3) и не зависит от концентрации нитросоединения, а его высота примерно в 4 раза меньше по сравнению с высотой катодного пика (рис. 8, кривые 11 и 1), и линейно увеличивается с возрастанием концентрации диаммонийной соли НДСКН. Эти данные указывают на обратимый одноэлектронный характер наблюдаемого процесса окисления [25]. Поэтому логично предположить, что анодные пики C представляют обратимый процесс окисления анион-радикала в исходное соединение [22]. Катодный пик образования анион-радикала, видимо, скрыт суммарным четырехэлектронным пиком синтеза гидроксиламинопроизводного. Однако на рис. 7 анодный пик C не наблюдается, и, вероятно, это связано с более сложным составом прикатодного раствора и большей концентрацией продуктов реакции при препаративном электролизе, по сравнению с составом прикатодного раствора при съемке на СУ циклической вольтамперограммы восстановления диаммонийной соли НДСКН.
Анодный пик В (рис. 8, кривые 12, 22 и 32) окисления гидроксиламинопроизводного наблюдается в той же области потенциалов, что и пик В, приведенный на рис. 7, а его высота линейно увеличивается с возрастанием концентрации диаммонийной соли НДСКН. Так как продуктом окисления гидроксиламинопроизводного является нитрозосоединение [22, 25], то оно должно восстанавливаться при развертке потенциала в катодную область. Действительно, при повторной развертке потенциала в катодную область сразу же при достижении конечного потенциала анодной развертки +0.2 В, как видно из рис. 8, на вольтамперограмме наблюдается катодный пик А (кривые 13, 23 и 33) с Ер –0.3 В, высота которого линейно увеличивается с возрастанием концентрации диаммонийной соли НДСКН и равна высоте пика окисления гидроксиламинодисульфокислоты нафталина при одинаковой концентрации нитросоединения (рис. 8). Поэтому пик А, приведенный на рис. 8, очевидно, связан с восстановлением нитрозодисульфокислоты нафталина, образующейся при окислении соответствующего гидроксиламинопроизводного. Исходя из полученных данных, можно полагать, что катодный пик А, приведенный на рис. 7, также отражает процесс восстановления нитрозодисульфокислоты нафталина, образующейся в ходе препаративного восстановления диаммонийной соли НДСКН, так как он наблюдается без повторной развертки потенциала в катодную область.
При препаративном восстановлении изомерной смеси нафтилнитросульфокислот (нитро-Клеве-кислот) в получаемых реакционных растворах как в сильнокислой, так и аммиачных буферных средах в ходе электролиза также наблюдается образование соответствующих нитрозо- и гидроксиламиносоединений, регистрируемых на циклических дифференциальных вольтамперограммах, снятых на СУ [9].
На циклической вольтамперограмме (кривая 1, 11, 12 и 13) на СУ в аммиачном буферном растворе (1.5% NH4Cl + NH4OH) с рН 7.5, как показано на рис. 9, при изменении потенциала в катодную область от +0.2 до –1.6 В и обратно в анодную область от –1.6 до +0.9 В не регистрируется образование АДСКН. Видимо, образующаяся АДСКН при съемке циклической вольтамперограммы успевает количественно диффундировать от поверхности электрода в объем раствора за время записи анодной кривой до достижения потенциала ее окисления. Образование АДСКН в небольших количествах наблюдается при микроэлектролизе при потенциале, близком к разряду фонового раствора, составляющем –1.6 В, в течение 30 мин (кривая 21, 22 и 23; пик А), что подтверждается введением в раствор АДСКН (рис. 9, кривая 3). Микроэлектролиз при потенциале –1.6 В позволяет синтезировать большие количества целевой АДСКН и наблюдать ее анодное окисление при потенциале +0.67 В. При таком же потенциале, как видно из рис. 7, анодно окисляется АДСКН, получаемая в условиях препаративного восстановления диаммонийной соли НДСКН.
Рис. 9.
Циклическая дифференциальная вольтамперограмма восстановления диаммонийной соли НДСКН (1, 11, 12 и 13), а также дифференциальная вольтамперограмма окисления продуктов восстановления диаммонийной соли НДСКН (пики C, В и А) , образующихся при потенциале – 1.6 В (21, 22 и 23) в течение 30 мин и дифференциальная вольтамперограмма АДСКН (3) на фоне аммиачного буферного раствора (1.5% NH4Cl + NH4OH) c рН 7.5. Концентрация диаммонийной соли НДСКН – 7.3 × 10–4 М, концентрация АДСКН – 1.5 × 10–4 М, скорость развертки потенциала 20 мВ/с.
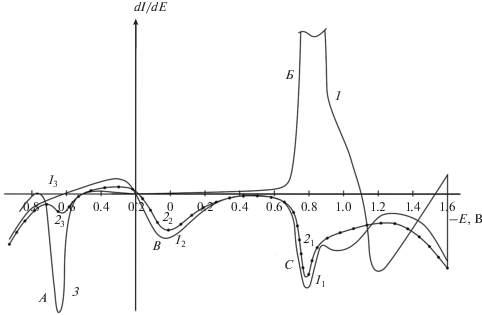
Из рис. 10 видно, что при пропускании количества электричества, близкого к теоретическому (4.4 А ч), концентрация исходной диаммонийной соли НДСКН снижается линейно до высокой степени превращения (около 80%). При этом на вольтамперограмме наблюдается уменьшение высоты пика Б (рис. 7).
Рис. 10.
Зависимость изменения концентраций диаммонийной соли НДСКН (1), АДСКН (2), 2-гидроксиламино-4,8-дисульфокислоты нафталина (3) и 2‑нитрозо-4,8-дисульфокислоты нафталина (4), а также потенциала электрода (5) и выхода по току водорода (ВТ) (6) в аммиачном буферном растворе (1.1% NH4Cl + 0.35% NH4OH) с рН 7.5 от количества пропущенного электричества. Условия электролиза: концентрация диаммонийной соли НДСКН – 0.31 М, температура 60°С, плотность тока – 15 А/дм2, катод – никель марки Н3.
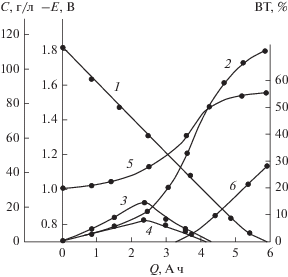
Концентрации промежуточных продуктов реакции, как видно из рис. 9, сначала увеличиваются, достигают максимума, а при смещении потенциала электрода до –1.1…–1.15 В быстро снижаются (пики А и В на вольтамперограмме в конце электролиза исчезают). При этом наблюдается резкий сдвиг потенциала в катодную область до ‒1.45 В, приводящий к дальнейшему восстановлению исходных и промежуточных продуктов до АДСКН, что проявляется в существенном увеличении концентрации последней в растворе, а также к выделению водорода. Причем в аммиачной буферной среде нитрозодисульфокислота нафталина регистрируется в реакционном растворе в небольших количествах (7–10 г/л) при восстановлении диаммонийной соли НДСКН с концентрацией 0.32–0.40 М, и в конце электролиза полностью исчезает, что, очевидно, приводит к увеличению выхода АДСКН по веществу. В то же время в сильнокислых растворах, как отмечалось выше, нитрозо- и гидроксиламинодисульфокислоты нафталина образуются в реакционных растворах до 20–24%, и не представляется возможным их восстановить в соответствующее аминосоединение без добавки катализатора-переносчика, в частности сульфата закисного железа.
АДСКН образуется с самого начала электролиза, но ее концентрация невелика и сопоставима с концентрацией промежуточных нитрозо- и гидроксиламинопроизводных. При дальнейшем протекании процесса, как видно из рис. 10, наблюдается резкое увеличение концентрации АДСКН в реакционной смеси, обусловленное восстановлением исходных и промежуточных продуктов в результате смещения потенциала электрода в область более отрицательных значений (кривая 5). При пропускании количества электричества, близкого к теоретическому (4.4 А ч), увеличение концентрации АДСКН в католите замедляется вследствие увеличения доли тока на выделение водорода. При этом выход водорода по току увеличивается с 12 до 28% (кривая 6).
Влияние температуры на электросинтез АДСКН исследовали в интервале 50–90°С (табл. 8).
Таблица 8.
Влияние температуры на выход АДСКН по веществу и по току в аммиачном буферном растворе (1.1% NH4Cl + 0.7% NH4OH) с рН 8.3.Концентрация диаммонийной соли НДСКН – 0.35 М, плотность тока – 10 А/дм2, катод – никель марки Н3
Температура, °С | Выход по веществу, % | Выход по току, % | Выход по току водорода, % | Изменение потенциала катода, В |
---|---|---|---|---|
50 | 98.2 | 65.0 | 32.5 | –1.10…–1.57 |
60 | 97.5 | 71.2 | 27.4 | –0.86…–1.52 |
70 | 98.5 | 72.2 | 27.5 | –0.90…–1.50 |
80 | 96.5 | 74.8 | 24.5 | –0.90…–1.50 |
90 | 92.8 | 75.5 | 23.0 | –1.00…–1.47 |
Как видно из табл. 8, выход АДСКН по веществу снижается с 98.5 до 92.8% при повышении температуры с 70 до 90°С, а выход по току увеличивается с 65.0 до 75.5%. Увеличение выхода по току можно объяснить улучшением растворимости исходной диаммонийной соли НДСКН, а также снижением выхода водорода по току, вероятно, вследствие смещения потенциала катода в сторону менее отрицательных значений. Однако проводить электросинтез АДСКН при температуре 80–90°С, несмотря на сравнительно более высокий выход по току, нежелательно как из-за уменьшения выхода АДСКН по веществу, так и снижения срока службы катионообменной мембраны МК-40, а также повышения коррозии никелевого электрода (табл. 6). Поэтому восстановление диаммонийной соли НДСКН целесообразно проводить при температуре 50–60°С.
Влияние концентрации диаммонийной соли НДСКН на электросинтез АДСКН исследовали в интервале от 0.35 до 0.54 М (табл. 9). Из данных табл. 9 следует, что концентрация исходного нитросоединения в исследованном интервале не влияет на выход АДСКН по веществу и последний составляет 97.0–98.0%. Однако выход АДСКН по току возрастает с 65.0 до 81.8% при увеличении концентрации диаммонийной соли НДСКН от 0.35 до 0.47 М, а при дальнейшем увеличении ее концентрации до 0.54 М выход по току уменьшается до 78.0%. Повышение выхода АДСКН по току с увеличением концентрации нитросоединения связано с перераспределением доли тока между побочной реакцией – выделением водорода и целевой в пользу последней, что подтверждается данными выхода водорода по току. При этом потенциал электрода сдвигается в область менее отрицательных значений.
Таблица 9.
Влияние концентрации исходной диаммонийной соли НДСКН на выход АДСКН по веществу и по току в аммиачном буферном растворе (1.1% NH4Cl + 0.7% NH4OH) с рН 8.3. Температура 70°С, плотность тока – 15 А/дм2, катод – никель марки Н3
Концентрация НДСКН, М | Выход по веществу, % | Выход по току, % | Выход по току водорода, % | Изменение потенциала катода, В |
---|---|---|---|---|
0.35 | 97.0 | 65.0 | 34.2 | –1.05…–1.58 |
0.41 | 98.0 | 70.4 | 28.4 | –1.00…–1.52 |
0.47 | 97.5 | 81.8 | 16.2 | –0.93…–1.45 |
0.54 | 97.0 | 78.0 | 20.5 | –1.08…–1.67 |
В более концентрированных растворах диаммонийной соли НДСКН наблюдается снижение выхода АДСКН по току. По-видимому, это связано с ухудшением растворимости диаммонийной соли НДСКН, что затрудняет его восстановление и сдвигает потенциал электрода в катодную область, увеличивая выход водорода по току.
Исходя из полученных данных, электросинтез АДСКН предпочтительно проводить с концентрацией НДСКН 0.35–0.41 М. При большей концентрации нитросоединения достигается более высокий выход по току, но при этом никелевый электрод подвергается коррозии (табл. 6).
Таким образом, в результате проведенных исследований определены оптимальные условия препаративного электросинтеза АДСКН в аммиачной буферной среде с рН 7.0–8.4: плотность тока – 10–15 А/дм2, температура 50–70°С, концентрация НДСКН – 0.35–0.41 М, концентрация хлорида аммония – 1.1–2.2%, концентрация гидроксида аммония – 0.35–0.70%, катионообменная мембрана – МК-40, катод – никель Н3 или сталь Х18Н10Т, обеспечивающие выход АДСКН по веществу и по току соответственно 97.5–98.5% и 65.0–72.2% [26], которые апробированы на укрупненной лабораторной и пилотной установках (табл. 10).
Таблица 10.
Результаты масштабирования электросинтеза АДСКН в аммиачном буферном растворе (1.1% NH4Cl + + 0.35% NH4OH) с рН 7.5. Концентрация диаммонийной соли НДСКН – 0.35 М, температура 60°С, плотность тока –10 А/дм2, катод – никель марки Н3
Лабораторный электролизер | Укрупненная лабораторная установка, линейная скорость католита 0.06 м/с в катодной камере электролизера | Пилотная установка, линейная скорость католита 0.03 м/с в катодной камере электролизера | |||||
---|---|---|---|---|---|---|---|
выход по веществу, % | выход по току, % | выход по веществу, % | выход по току, % | выход по выделению из раствора, % | выход по веществу, % | выход по току, % | выход по выделению из раствора, % |
97.5 | 71.2 | 98.2 | 60.0 | 84.4 | 98.0 | 46.0 | 88.2 |
98.5 | 72.2 | 98.0 | 56.0 | 89.9 | 97.0 | 51.0 80°С |
89.0 |
98.0* | 55.0 | 98.5 | 56.0 | 88.0 | 98.5 | 44.0 | 88.9 |
95.0** | 52.1 | 97.8 | 53.0 | 86.7 | 98.0 | 49.0 70°С |
87.5 |
98.0 | 69.0 | 98.2** | 36.0 | 86.7 | 98.0 | 44.5 | 87.5 |
97.8 | 68.5 | 95.0* | 40.0 | 88.7 | 97.9 | 44.2 | 88.0 |
Как видно из данных табл. 10, выход АДСКН по восстановлению и выделению из реакционного раствора практически не зависит от масштабирования процесса восстановления диаммонийной соли НДСКН и составляет соответственно 95.0–98.5% и 84.4–89.0%. Причем выход амино-Ц-кислоты по выделению из реакционного раствора, полученного после электролиза, существенно выше (табл. 10), чем при восстановлении НДСКН чугунной стружкой (78–79%) [3, 4].
Из данных табл. 10 следует, что на катоде из никеля электросинтез АДСКН протекает более эффективно, чем на других исследованных металлах. Поэтому для опытно-промышленного электролизера рекомендуется в качестве катодного материала никель марки Н3.
На пилотном электролизере восстановление диаммонийной соли НДСКН протекает с более низким выходом по току (44.0–46.0%) по сравнению с лабораторным электролизером (71.1–72.2%) и укрупненной лабораторной установкой (56.0–60.0%). Уменьшение выхода по току приводит к снижению производительности аппарата. Так, если на лабораторном электролизере при плотности тока 10 А/дм2 и температуре 50°С удельная производительность аппарата составляла 1.43 кг/(м2 ч), то на укрупненной лабораторной и пилотной установках соответственно – 1.0 и 0.80–0.93 кг/(м2 ч). Снижение выхода по току на последних связано с низкой линейной скоростью электролита в катодном пространстве электролизера из-за недостаточной производительности используемых насосов. Исследование влияния линейной скорости католита на выход АДСКН по току на катоде из стали Х18Н10Т показало, что увеличение линейной скорости от 0.02 до 0.06 м/с приводит к возрастанию выхода по току с 37.0 до 48.0% при температуре 60°С и плотности тока 10 А/дм2.
Как видно из табл. 10, при одной и той же линейной скорости реакционного раствора в катодном пространстве электролизера процесс восстановления диаммонийной соли НДСКН протекает с большим выходом по току при повышении температуры 70–80°С. Однако увеличение температуры нежелательно из-за работы катионообменных мембран МК-40 на предельном температурном режиме, усиления коррозии никелевого катода и ухудшения качества целевого продукта из-за образования побочных смолообразных продуктов. Поэтому для повышения выхода АДСКН по току нужно увеличивать линейную скорость раствора НДСКН в катодном пространстве электролизера за счет применения более производительного насоса.
Амино-Ц-кислота, полученная на пилотной установке, соответствует требованиям ТУ 6-14-207-84. Кроме того, качество амино-Ц-кислоты проверено на ПАО “Химпром” (г. Новочебоксарск) на содержание основного вещества и примесей методом тонкослойной хроматографии (ТСХ), а также синтезом красителя активного золотисто-желтого 2КХ, так как последний наиболее чувствителен к качеству используемого полупродукта. При этом установлено, что выход и качество красителя с использованием электрохимически полученной амино-Ц-кислоты соответствуют технологическому регламенту и типовому образцу, а процесс крашения полученным красителем – нормам ТУ 6-14-53-77.
ЗАКЛЮЧЕНИЕ
На основании полученных результатов можно сделать следующие основные выводы:
1. Исследованием влияния условий на препаративное восстановление диаммонийной соли НДСКН в АДСКН, в частности состава электролита, материала катода, плотности тока, температуры, концентрации исходной диаммонийной соли НДСКН, определены оптимальные параметры процесса восстановления диаммонийной соли НДСКН в АДСКН в аммиачной буферной среде с рН 7.0–8.4: плотность тока 10–15 А/дм2, температура 50–70°С, концентрация НДСКН – 0.35–0.41 М, концентрация хлорида аммония – 1.1–1.9%, концентрация гидроксида аммония 0.35–0.70%, катионообменная мембрана МК-40, катод – никель марки Н3 или сталь Х18Н10Т, обеспечивающие выход АДСКН по веществу и по току, соответственно, 97.5–98.5 и 65.0–72.2%, которые апробированы на укрупненной лабораторной и пилотной установках с мембранным электролизером фильтр-прессного типа.
2. Показано, что аммиачная буферная среда с рН 7.0–8.4 более предпочтительна для препаративного электросинтеза АДСКН по сравнению с кислыми растворами, так как обеспечивает не только более высокие технико-экономические показатели процесса восстановления диаммонийной соли НДСКН, но и является менее коррозионно-активной, что упрощает выбор электродного и конструкционного материалов для электролизера и технологического оборудования для производства амино-Ц-кислоты.
3. На основании полученных экспериментальных данных на укрупненной лабораторной и пилотной установках разработана электрохимическая технология получения амино-Ц-кислоты, которая отражена в опытно-промышленном регламенте на производство амино-Ц-кислоты и в техническом задании для проектирования опытно-промышленного электролизера для получения амино-Ц-кислоты, на основании которых спроектирован опытно-промышленный мембранный электролизер ММН-3-НС-03 фильтр-прессной конструкции на токовую нагрузку 3 кА.
4. Разработанная технология электросинтеза амино-Ц-кислоты позволяет: повысить выход продукта по выделению из раствора с 79.0 до 84.4–89.0%, сократить количество неутилизируемых твердых отходов с 1.7 до 0.2 т на 1 т продукта, упростить технологический процесс за счет исключения ряда стадий, связанных с подготовкой, фильтрацией и транспортировкой чугунной стружки и железного шлама, улучшить условия труда, обеспечить экономический, экологический и социальный эффект, а также получать амино-Ц-кислоту в соответствии с требованиями ТУ 6-14-207-84 .
Список литературы
Ворожцов, Н.Н. Основы синтеза промежуточных продуктов и красителей, М.: Госхимиздат, 1955. 839 с. [Vorozhtsov, N.N., The fundamentals of synthesis of intermediate products and dyes (in Russian), M.: Goskhimizdat, 1955. 839 p.]
Венкатараман, К. Химия синтетических красителей, Л.: Госхимиздат, 1956. 803 с. [Venkataraman, K., Chemistry of synthetic dyes (in Russian), Leningrad: Goskhimizdat, 1956. 803 p.]
Эфрос, Л.С., Горелик, М.В. Химия и технология промежуточных продуктов, Л.: Химия, 1980. 544 с. [Efros, L.S. and Gorelik, M.V., Chemistry and technology of intermediate products (in Russian), Leningrad: Chemistry, 1980. 544 p.]
Вигасин, А.А., Амитрова, И.М., Ганюшкина, Л.С. и др. Способ выделения 2-нитронафталин-4,8-дисульфокислоты (нитро-Ц-кислоты). Авт. свид. 154261 (СССР). 1963.[Vigasin, A.A., Amitrova, I.M., Ganiushkina, L.S. et al., Production Method for 2-nitronaphthaline-4,8-disulfonic acid (nitro-C-acid), Copyright certificate 154261 (USSR), 1963.]
Bamfield, P., Quan, P.M., and Smith, T.J., Reduction of nitro compounds with aqueous solutions of a formate, Patent 4093646 (USA). 1978.
Hildreth, J.D., Catalytic reduction of 2-nitronaphthalene-4,8-disulfonic acid ammonium salt, Patent 4299779 (USA). 1981.
Horyna, J. and Jehlicka, V., Polarographie der Mononitroderivate der 1,5- und 1,6-Naphthalindisulfonsauren, Coll., 1959, Bd. 24, s. 3353.
Fierz, H.E. and Weissenbuch, P., Uber die Reduktion von Nitronaphtalinssulfosauren, Helv. Chim. Acta, 1920, Bd. 3, s. 305.
Конарев, А.А. Электрохимический синтез Клеве-кислот. Электрохимия. 1998. Т. 34. С. 1166. [Konarev, A.A., Electrochemical synthesis of Cleves-acids, Russ. J. Electrochem., 1998, vol. 34, p. 1160.]
Конарев, А.А., Катунин, В.Х., Сухинина, Н.Г. и др. Способ получения 1-амино-3,6,8-трисульфокислотынафталина. Авт. свид. 1369232 (СССР). 1987. [Konarev, A.A., Katunin, V.Kh., and Sukhinina, N.G., Method for preparation of naphthalene 1-amino-3,6,8-trisulfonic acid, Copyright certificate 1369232 (USSR), 1987.]
Конарев, А.А., Авруцкая, И.А., Катунин, В.Х. Полярографическое поведение 1-нитро-3,6,8-трисульфокислоты нафталина. Электрохимия. 1981. Т. 17. С. 901. [Konarev, A.A., Avrutskaya, I.A., and Katunin, V.Kh., Polarographic behavior of a naphthalene 1-nitro-3,6,8-trisulfonic acid, Russ. J. Electrochem., 1981, vol. 17, p. 901.]
Конарев, А.А., Авруцкая, И.А. Особенности электрохимического восстановления 1-нитро-3,6,8-трисульфокислоты нафталина. Электрохимия. 1988. Т. 24. С. 1548. [Konarev, A.A. and Avrutskaya, I.A., Featuresof electrochemical reduction of 1-nitro-3,6,8-trisulfonic acid of naphthalene, Russ. J. Electrochem., 1988, vol. 24, p. 1548.]
Конарев, А.А. Способ определения ароматических нитросоединений и продуктов их восстановления, Пат. 2159424 (Россия). 2000. [Konarev, A.A., Method for detection of aromatic nitrocompounds and productsof their reduction, Patent 2159424 (Russia), 2000.]
Томилов, А.П., Майрановский, С.Г., Фиошин, М.Я., Смирнов, В.А. Электрохимия органических соединений, Л.: Химия, 1968. 592 с. [Tomilov, A.P., Mayranovsky, S.G., Fioshin, M.Ya., and Smirnov, V.A., Electrochemistry of organic compounds (in Russian), Leningrad: Chemistry, 1968. 592 p.]
Конарев, А.А. Выбор анодного материала для электросинтеза аминосульфокислот нафталина. Журн. прикл. химии. 1997. Т. 70. С. 261. [Konarev, A.A., Selection of anode material for electrosynthesis of naphthalene aminosulfonic acids, Russ. J. Appl. Chem., 1997, vol. 70, p. 261.]
Конарев, А.А. Исследование промежуточных продуктов, образующихся в условиях препаративного электровосстановления 1-нитро-3,6,8-трисульфокислоты нафталина. Электрохимия. 2012. Т. 48. С. 1011. [Konarev, A.A., Studies of Intermeliates Formed under the Conditions of Preparative Electroreduction of Naphthalene 1-Nitro-3,6,8-Trisulfo Acid, Russ. J. Electrochem., 2012, vol. 48, p. 922.]
Байзер, М. Электрохимия органических соединений. М.: Мир, 1976. 731 с.[Baizer, M., Electrochemistry of organic compounds (in Russian), Moscow: Mir, 1976. 731 p.]
Мизуч, К.Г. Побочные окислительные процессы при восстановлении нитросоединений ароматического ряда. Докл. АН СССР. 1937. Т. 15. № 1. С. 37. [Mizuch, K.G., Collateral oxidation processesin reduction of aromatic nitrocompounds, The USSR Acad. Sci. J., 1937, vol. 15, no.1, p. 37.]
Лукашевич, В.О. Органические полупродукты и красители. М.: Госхимиздат, 1959. 40 c. [Lukashevich, V.O., Organic semi-products and dyes (in Russian), M.: Goskhimizdat, 1959. 40 p.]
Антропов, Л.И. Теоретическая электрохимия. М.: Высш. шк., 1969. 510 с. [Antropov, L.I., Theoretical electrochemistry (in Russian), Moscow: Higher School, 1969. 510 p.]
Ахметов, Н.С. Общая и неорганическая химия. М.: Высш. шк., 1981. 680 с. [Akhmetov, N.S., General and non-organic chemistry (in Russian), M.: Higher School, 1981. 680 p.]
Бакир, Д., Автореф. дис. канд. хим. наук, М.: МГУ, 1989. 17 с. [Bakir D., Abstract for thesis on PhD in Chemistry. M.: Moscow State Univers., 1989, 17 p.]
Smith, J.W. and Waller, J.G., Polarographic Behavior of Aromatic Nitro Compounds Nitrosobenzene and N‑Phenylnydroxylamine, Trans. Farad. Soc., 1950, vol. 46, p. 290.
Страдынь, Я.П. Полярография органических нитросоединений. Рига: Из-во АН Латв. ССР. 1961. 163 с. [Stradyn, Ya.P. Polarography of organic nitrocompounds, Riga: AN publisher, Latvian SSR, 1961, 163 p.]
Майрановский, С.Г., Страдынь, Я.П., Безуглый, В.Д. Полярография в органической химии. Л.: Химия, 1975. 351 с. [Mayranovsky, S.G., Stradyn, Ya.P., and Bezugliy, V.D., Polarography in organic chemistry (in Russian), Leningad: Chemistry, 1975, 351 p.]
Конарев, А.А., Помогаева, Л.С., Воротникова, Е.Ю. и др. Способ получения кислой натриевой соли 2‑амино-4,8-дисульфокислоты нафталина. Пат. 2009125 (Россия). 1994. [Konarev, A.A., Pomogaeva, L.S., Vorotnikova, E.Y. et al., Method of producing acidic sodium Salt of naphthalene 2-amino-4,8-disulfonic acid, Patent 2009125 (Russia). 1994.]
Дополнительные материалы отсутствуют.