Электрохимия, 2021, T. 57, № 5, стр. 309-315
Оценка скорости коррозии кобальт-хромового сплава STARBOND–CoS в растворе NaCl
Л. А. Бекетаева a, К. В. Рыбалка a, *, А. Д. Давыдов a, **
a Институт физической химии и электрохимии им. А.Н. Фрумкина РАН
119071 Москва, Ленинский просп., 31, корп. 4, Россия
* E-mail: mamaison2000@yandex.ru
** E-mail: davydov@elchem.ac.ru
Поступила в редакцию 17.06.2020
После доработки 28.08.2020
Принята к публикации 07.09.2020
Аннотация
Проведено измерение потенциала коррозии Ecorr сплава STARBOND–CoS в 0.5 М растворе NaCl в течение 100 ч. Получены анодные и катодные потенциодинамические кривые в том же растворе после предварительной выдержки исследуемого образца в течение периода времени от 2 до 100 ч при потенциале коррозии Ecorr. Методом тафелевской экстраполяции определены значения плотности коррозионного тока icorr. Показано, что Ecorr смещается за 100 ч от +9 до + 275 мВ относительно насыщенного хлорид-серебряного электрода сравнения (НХСЭ), а icorr снижается до 40 нА/см2. Полученные результаты объяснены самопассивацией сплава, которая обеспечивает его высокую коррозионную стойкость, позволяющую применять сплав STARBOND–CoS для изготовления имплантов.
ВВЕДЕНИЕ
Кобальт-хромовые сплавы, содержащие некоторые количества молибдена и вольфрама, а также других компонентов в небольших количествах, находят широкое применение в первую очередь как материалы, используемые в стоматологии, а также при изготовлении имплантов других типов.
Одним из главных требований к материалу является очень высокая коррозионная стойкость. В большинстве работ по определению скорости коррозии таких сплавов используются растворы, моделирующие слюну. Главными компонентами растворов, ответственными за коррозию, являются хлориды натрия, калия, кальция, важным также является величина рН и наличие некоторых добавок.
Коррозионное поведение сплава STARBOND–CoS и близких к нему по составу сплавов исследовалось в работах [1–18] с использованием ряда химических (анализ растворов) и электрохимических (измерение коррозионного потенциала, импеданс, поляризационное сопротивление, циклическая вольтамперометрия, тафелевская экстраполяция) методов.
Надо заметить, что далеко не всегда поляризационные кривые имели тафелевские участки, позволяющие надежно использовать метод тафелевской экстраполяции для определения icorr. В ряде работ при сравнении различных сплавов проводилось сравнение поляризационного сопротивления без переведения в токи коррозии и определения скорости коррозии.
Сплавы системы Co–Cr–Mo находятся в пассивном состоянии в водных растворах благодаря образованию поверхностных оксидных пленок.
В работах [19–26] исследовали состав оксидных пленок на сплавах Co–Cr–Mo, обеспечивающих их пассивность в биологических растворах, и роль каждого компонента сплава.
Амиир и соавт. [6, 12] измеряли скорость коррозии сплава Wironit в искусственной слюне и нашли плотность тока коррозии 0.23 мкА/см2, а с добавкой фтор-ионов –0.243 мкА/см2. Добавки в раствор некоторых веществ увеличивали коррозионный ток. Особенно сильное влияние оказывали добавки H2O2, многократно увеличивающие ток коррозии.
По данным авторов работы [15], в зависимости от метода получения сплава Co–Cr–Mo, коррозия за 42 дня составляла от 0.054 до 0.501 мг/см2.
Образцы сплава, полученные спеканием порошков, в зависимости от предобработки показали скорость коррозии, как отмечается авторами, от 6.22 × 10–6 до 141.19 × 10–9 А/см2 [14]. По данным работы [17], в зависимости от типа предварительной обработки образцов сплава в Ringer’s растворе плотность коррозионного тока изменяется от 9.3 до 25.2 мкА/см2.
Скорость коррозии сплава Co–Cr–Mo в фосфатном буферном растворе, содержащем 9 г/л NaCl, составила 0.07 мм/год [13].
Авторы работы [16] определяли плотность коррозионного тока сплава Co–Cr–Mo, предназначенного для изготовления имплантов, в нескольких биологических растворах и получили значения от 1.65 до 2.59 мкА/см2.
По данным работы [16], плотность коррозионного тока сплава в 0.01 М HCl составила 50.10 мкА/см2, а в 3%-ном растворе NaCl 98.10 мкА/см2. По результатам работы Гало и соавт. [4] плотность коррозионного тока сплава Co–Cr–W–Mo в искусственной слюне 0.02 мкА/см2. Плотность коррозионного тока сплава Co–Cr–W, электролитически осажденного на низкоуглеродистой стали, составила в растворах хлорида натрия 10–6 А/см2 [5].
При определении скорости коррозии особенно склонных к пассивации сплавов необходимо учитывать наличие длительного периода установления коррозионного потенциала после погружения исследуемого образца в агрессивный раствор. Этот период “самопассивации” сплава особенно длителен в нейтральных водных растворах [27].
В работах по определению скорости коррозии сплавов Co–Cr–Mo электрохимическими методами этому вопросу не было уделено необходимое внимание. Образцы не всегда выдерживались достаточно длительное время в агрессивном растворе перед началом снятия поляризационных кривых, а если и выдерживались какое-то время, то без какого-либо обоснования. В ряде случаев достаточно было выбрать такие условия проведения эксперимента, которые обеспечивали хорошую воспроизводимость результатов измерений.
В настоящей работе проведены эксперименты, на основании которых сделаны оценки плотности коррозионного тока сплава STARBOND–CoS в растворах хлорида натрия.
МЕТОДИКА ИЗМЕРЕНИЯ
Все измерения проведены на образцах сплава STARBOND–CoS в растворах NaCl. Содержание основных компонентов сплава, превышающее 1%, приведено в табл. 1 по данным спецификации производителя.
Электродом служил торец цилиндра диаметром 8 мм, запрессованного в тефлоновую втулку. Поверхность электрода перед опытом обрабатывали наждачной бумагой зернистости Р 400, обезжиривали этиловым спиртом и промывали в бидистиллате. Все измерения проведены в стандартной трехэлектродной электрохимической ячейке в условиях естественной аэрации при температуре 25°С. Потенциал электрода измеряли относительно насыщенного хлоридсеребряного электрода. Поляризация образца при проведении потенциодинамических измерений осуществлялась с помощью потенциостата IPC2000 compact (НПП ЭКОНИКС, Россия). Потенциодинамические кривые регистрировали при скорости развертки потенциала 1 мВ/с. Такая скорость развертки применяется в большинстве работ по коррозии. Измеряли потенциал разомкнутой цепи (коррозионный потенциал Ecorr) и снимали потенциодинамические кривые после выдержки электрода в 0.5 М растворе NaCl в течение периода времени от 2 до 100 ч (в дальнейшем будем называть этот процесс “предварительной выдержкой электрода”) для учета влияния самопассивации на результаты измерений коррозионного тока.
Потенциодинамические кривые снимали, начиная от установившегося за определенное время (2–100 ч) потенциала Ecorr в сторону анодных или катодных потенциалов. Воспроизводимость результатов позволила получать величины Ecorr и icorr с разбросом в пределах ±5%.
РЕЗУЛЬТАТЫ ЭКСПЕРИМЕНТОВ И ИХ ОБСУЖДЕНИЕ
На рис. 1 приведена зависимость Ecorr от продолжительности предварительной выдержки электрода в растворе NaCl.
Рис. 1.
Зависимости потенциала коррозии и плотности коррозионного тока сплава STARBOND–CoS в 0.5 М растворе NaCl от продолжительности предварительной выдержки образца в этом растворе.
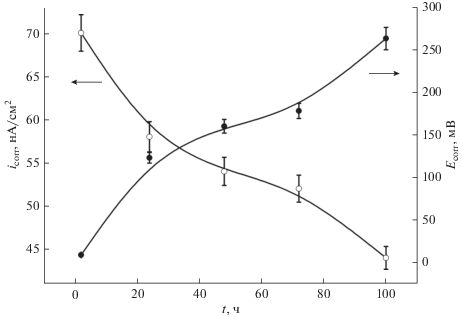
Коррозионный потенциал смещался в область более положительных значений в течение 100 ч и за этот период времени не достиг установившегося значения. Значительное смещение Ecorr в сторону более положительных значений свидетельствует об усилении пассивности сплава во времени.
Для определения плотности коррозионного тока снимали потенциодинамические кривые после различной предварительной выдержки электродов, начиная от соответствующих значений Ecorr. Ниже приведены кривые после наименьшей (2 ч) и наибольшей (100 ч) по продолжительности предварительной выдержки электродов. Все промежуточные кривые по форме аналогичны кривым на рис. 2б.
Рис. 2.
Потенциодинамические кривые, полученные после предварительной выдержки электрода в растворе при потенциале коррозии в течение различного времени: а – 2, б – 100 ч.
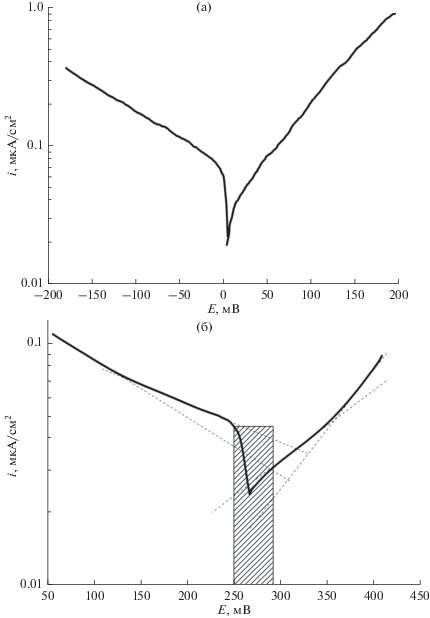
Несколько подробнее рассмотрим эти рисунки. Кривые на рис. 2а имеют хорошо выраженные анодный и катодный тафелевские участки, что дает возможность использовать метод тафелевской экстраполяции для определения icorr.
Некоторая несимметричность анодной и катодной кривых приводит к тому, что экстраполяция катодной кривой до Ecorr дает величину плотности коррозионного тока icorr = 0.07 мкА/см2, а экстраполяция анодной кривой дает значение icorr = 0.03 мкА/см2. Анодная и катодная кривые не обязаны быть симметричными, если только кинетические параметры этих разных по природе процессов (анодного растворения и катодного восстановления растворенного кислорода) не совпадают.
Надо отметить большую величину тафелевского наклона катодной кривой. Он в данном случае составляет примерно 270 мВ. Наклон анодной кривой 124 мВ. При бóльших длительностях предварительной выдержки электрода оба наклона еще больше. Наклоны катодных кривых могут составлять несколько сотен мВ. Большие тафелевские наклоны катодных кривых наблюдались неоднократно на сталях в нейтральных растворах NaCl, например [28–31]. Это может быть связано с наличием оксидных пленок на сталях с высоким перенапряжением катодных реакций. Большой наклон мог бы быть связан с наличием концентрационной поляризации. Но наши специальные эксперименты с включением и выключением перемешивания раствора во время снятия кривых исключили такое объяснение.
Тезис об оксидных пленках, отвечающих за большой наклон тафелевских участков катодных кривых, может быть подтвержден рис. 3. Перед снятием катодной кривой электрод был выдержан в течение одного часа при потенциале ‒500 мВ для восстановления оксида. В этом случае вся кривая лежит в области более отрицательных потенциалов и значительно бóльших токов. Если отметить прямолинейный участок в области самых высоких потенциалов и экстраполировать его до Ecorr, то наклон участка составит около 140 мВ, что значительно меньше, чем без предварительного катодного восстановления оксида, и подтверждает наличие оксидной пленки как причины больших тафелевских наклонов на катодных потенциодинамических кривых.
Рис. 3.
Потенциодинамические кривые, полученные после предварительной выдержки электрода из сплава STARBOND–CoS при потенциале –500 мВ.
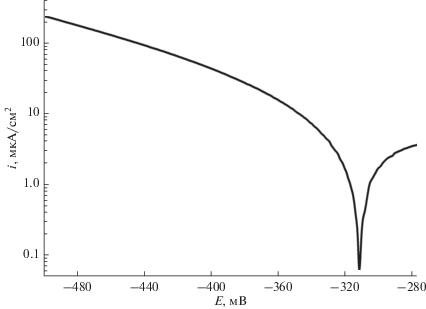
Обратимся к анализу кривых после 100-часовой выдержки (рис. 2б). Эти кривые имеют ряд особенностей. Во-первых, несимметричность анодной и катодной кривых значительно больше, чем на рис. 2а. Во-вторых, и на анодной, и на катодной кривой можно выделить прямолинейные участки с двумя разными наклонами. В области потенциалов (заштрихованной на рис. 2б) примерно ±20 мВ от Ecorr имеются отклонения от этих участков, очевидно, связанные с взаимным влиянием анодного и катодного процессов. Аналогичная форма катодной потенциодинамической кривой с двумя наклонами (две катодные реакции: восстановление растворенного кислорода и выделение водорода) была получена нами экспериментально и соответствующими расчетами в работе [32]. Объяснить наличие двух наклонов на анодной кривой для сплава сложного состава вряд ли возможно. Однако такой факт должен быть отмечен.
Экстраполяция катодного тафелевского участка ближнего к Ecorr до Ecorr дала значение icorr = = 0.044 мкА/см2. Экстраполяция анодного тафелевского участка ближнего к Ecorr до Ecorr дала значение icorr около 0.03 мкА/см2.
В коррозионных исследованиях допускается определение плотности коррозионного тока при экстраполяции на потенциал коррозии только одной поляризационной кривой, как правило катодной [33–35]. Такой подход к определению icorr привел нас к результатам, приведенным на рис. 1 вместе с результатами изменения Ecorr. Плотность тока коррозии за 100 ч снизилась до столь низких значений, как 40 нА/см2. Самопассивация сплава в растворе NaCl происходит медленно и значительно снижает скорость коррозии. Так как потенциал коррозии, как и скорость коррозии, не достиг за 100 ч своего установившегося значения, наша оценка плотности коррозионного тока является оценкой сверху.
Добавки кислоты немного смещают Еcorr в сторону более положительных потенциалов, а небольшая добавка щелочи сместила Еcorr в сторону отрицательных значений, рис. 4. Плотность коррозионного тока во всех этих растворах составляет 0.07 ± 0.01 мкА/см2.
ВЫВОДЫ
Измерено изменение потенциала коррозии Ecorr сплава STARBOND–CoS (Co–Cr–W–Mo–Si) в 0.5 М растворе NaCl в течение 100 ч. Потенциал Ecorr за 100 ч изменился примерно от +9 до +275 мВ за счет самопассивации сплава.
Получены потенциодинамические кривые на сплаве в том же растворе после различного времени выдержки электрода при Ecorr: 2, 24, 48, 72 и 100 ч. Кривые имеют тафелевские участки, что позволило оценить плотность коррозионного тока icorr методом тафелевской экстраполяции.
В результате отсутствия симметрии анодной и катодной кривых, их экстраполяция дает различные значения icorr. Получена зависимость icorr от времени выдержки электрода, определенная из анализа катодных кривых. Величина icorr снизилась за 100 ч вплоть до почти 40 нА/см2.
Представлено экспериментальное подтверждение того, что причиной больших тафелевких наклонов является наличие на электроде оксидной пленки.
Так как потенциал коррозии, как и скорость коррозии, снижаясь, не достигли за 100 ч своего установившегося значения, наша оценка плотности коррозионного тока является оценкой сверху.
Сплав STARBOND–CoS имеет большую склонность к довольно медленной и глубокой самопассивации. Это делает сплав очень стойким против коррозии и позволяет использовать его для изготовления имплантов, а также должно учитываться при исследовании электрохимических и коррозионных свойств этого сплава.
Список литературы
Giacomelli, F.C., Giacomelli, C., and Spinelli, A., Behavior of a Co–Cr–Mo biomaterial in simulated body fluid solutions studied by electrochemical and surface analysis techniques, J. Braz. Chem. Soc., 2004, vol. 15, p. 541.
Reclaru, L., Lüthy, H., Eshler, P.I., Blatter, A., and Susz, C., Corrosion behaviour of cobalt–chromium dental alloys doped with precious metals, Biomaterials, 2005, vol. 26, p. 4358.
Manaranche, C. and Hornberger, H., Corrosion and biocompatibility of dental alloys, Europ. Cells and Materials, 2005, vol. 9, p. 35.
Galo, R., Ribeiro, R.F., Rodrigues, R.C.S., Rocha, L.A., and Mattos, M.C., Effects of chemical composition on the corrosion of dental alloys, Braz. Dent. J., 2012, vol. 23, p. 141.
Kuznetsov, V.V., Filatova, T.A., Telezhkina, A.V., and Kruglikov, S.S., Corrosion resistance of Co–Cr–W coatings obtained by electrodeposition, J. Solid State Electrochem., 2018, vol. 22, no. 7, p. 2267.
Ameer, M.A., Khamis, E., and Al-Motlaq, M., Electrochemical behaviour of recasting Ni–Cr and Co–Cr non precious dental alloys, Corrosion Science, 2004, vol. 46, p. 2825.
Sharma, M., Kumar, A.V.R., Singh, N., Adya, N., and Saluja, B., Electrochemical corrosion behavior of dental implant alloys in artificial saliva, J. Mater. Engineering and Performance, 2008, vol. 17, p. 695.
Sharma, M., Kumar, A.V.R., and Singh, N., Electrochemical corrosion behaviour of dental implant alloys in saline media, J. Mater. Sci. Mater Med, 2008, vol. 19, p. 2647.
Taher, N.M. and Al Jabab, A.S., Galvanic corrosion behavior of implant superstructure dental alloys, Dental Materials, 2003, vol. 19, p.54.
Renita, D., Rajendran, S., and Chattree, A., Influence of artificial saliva on the corrosion behavior of dental alloys: a review, Indian J. Advances in Chem. Sci., 2016, vol. 4, p. 478.
Capelo, S., Proença, L., Fernandes, J.C.S., and Fonseca, I.T.E., Galvanic corrosion of two non noble dental alloys, Int. J. Electrochem. Sci., 2014, vol. 9, p. 593.
Ameer, M.A., Khamis, E., and Al-Motlaq, M., Electrochemical behavior of non-precious dental alloys in bleaching agents, Electrochim. Acta, 2004, vol. 50, p. 141.
Nascimento, M.L., Mueller, W.-D., Carvalho, A.C., and Tomάs, H., Electrochemical characterization of cobalt-based alloys using the mini-cell system, Dental Materials, 2007, vol. 23, p. 369.
Bălă, D.I., Doicin, C.V., Cotrut, C.M., Ulmeanu, M.E., Ghionea, I.G., and Tarbă, C.I., Sintering the beaks of the elevator manufactured by direct metal laser sintering (DMLS) process from Co–Cr alloy, Metalurgija, 2016, vol. 4, p. 663.
Alifui-Segbaya, F., Foley, P., and Williams, R.J., The corrosive effects of artificial saliva on cast and rapid manufacture-produced cobalt chromium alloys, Rapid Prototyping J., 2013, vol. 19, p. 95.
Hsu, R.W.-W., Yang, C.-C., Huang, C.-A., and Chen, Y.-S., Electrochemical corrosion studies on Co‒Cr–Mo implant alloy in biological solutions, Mater. Chem. and Phys., 2005, vol. 93. p. 531.
Tchana, D.V., Simescu-Lazar, F., Drevet, R., Aaboubi, O., Fauré, J., Retraint, D., and Benhayoune, H., Influence of the surface mechanical attrition treatment (SMAT) on the corrosion behavior of Co28Cr6Mo alloy in Ringer’s solution, J. Solid State Electrochem., 2018, vol. 22, p. 1091.
Puskar, T., Jevremovic, D., Williams, R. J., Eggbeer, D., Vukelic, D., and Budak, I., A comparative analysis of the corrosive effect of artificial saliva of variable pH on DMLS and cast Co–Cr–Mo dental alloy, Materials, 2014, vol. 7, p. 6486.
Metikoš-Huković, M., Pilić, Z., Babić, R., and Omanović, D., Influence on the corrosion stability of CoCrMo implant alloy in Hank’s solution, Acta Biomaterialia, 2006, vol. 2, p. 693.
Metikoš-Huković, M. and Babić, R., Passivation and corrosion behaviours of cobalt and cobalt–chromium–molybdenum alloy, Corrosion Sci., 2007, vol. 49, p. 3570.
Xin, X-Z., Chen, J., Xiang, N., Gong, Y., and Wei, B., Surface characteristics and corrosion properties of selective laser melted Co–Cr dental alloy after porcelain firing, Dental Materials, 2014, vol. 30, p. 263.
Milosev, I. and Strehblow, H.H., The composition of the surface passive film formed on CoCrMo alloy in simulated physiological solution, Electrochim. Acta, 2003, vol. 48, p. 2767.
Kocijan, A., Milosev, I., and Pihlar, B., Cobalt-based alloys for orthopaedic applications studied by electrochemical and XPS analysis, J. Mater. Sci: Mater. Med., 2004, vol. 15, p. 643.
Hodgson, A.W.E., Kurz, S., Virtanen, S., Fervel, V., Olsson, C.A., and Mischler, S., Passive and transpassive behaviour of Co–Cr–Mo in simulated biological solutions, Electrochim. Acta, 2004, vol. 49, p. 2167.
Hanawa, T., Hiromoto, S., and Asami, K., Characterization of the surface oxide film of a Co–Cr–Mo alloy after being located in quasi-biological environments using XPS, Appl. Surf. Sci., 2001, vol. 183, p. 68.
Li, Y., Wang, K., He, P., Huang, B.X., and Kovacs, P., Surface-enhanced Raman spectroelectrochemical studies of corrosion films on implant Co–Cr–Mo alloy in biosimulating solutions, J. Raman. Spectrosc., 1999, vol. 30, p. 97.
Rybalka, K.V., Beketaeva, L.A., and Davydov, A.D., Effect of self-passivation on the electrochemical and corrosion behavior of alloy C-22 in NaCl solutions, Corros. Sci., 2012, vol. 54, p. 161.
Zhang, X.L., Jiang, Zh.H., Yao, Zh.P., Song, Y., and Wu, Zh.D., Effects of scan rate on the potentiodynamic polarization curve obtained to determine the Tafel slopes and corrosion current density, Corros. Sci., 2009, vol. 51, p. 581.
Priyantha, N., Jayaweera, P., Macdonald, D.D., and Sun, A., An electrochemical impedance study of Alloy 22 in NaCl brine at elevated temperature. I. Corrosion behavior, J. Electroanal. Chem., 2004, vol. 572, p. 409.
Caceres, L., Vargas, T., and Herrera, L., Determination of electrochemical parameters and corrosion rate for carbon steel in un-buffered sodium chloride solutions using a superposition model, Corros. Sci., 2007, vol. 49, p. 3168.
Sfaira, M., Srhiri, A., Takenouti, H., Ficquelmont Loizos, M., Ben Bachir, A., and Khalakhil, M., Corrosion of Mild Steel in low Conductive Media simulating Natural Waters, J. Appl. Electrochem., 2001, vol. 31, p. 537.
Рыбалка, К.В., Бекетаева, Л.А., Давыдов, А.Д. Катодная составляющая коррозионного процесса: поляризационная кривая с двумя тафелевскими участками. Электрохимия. 2018. Т. 54. С. 523. [Rybalka, K.V., Beketaeva, L.A., and Davydov, A.D., Cathodic component of corrosion process: polarization curve with two Tafel portions, Russ. J. Electrochem., 2018, vol. 54, p. 456.]
Stansbury, E.E. and Buchanan, R.A., Fundamentals of the Electrochemical Corrosion, Materials Park, Ohio: ASM International, 2000, chapter 6.
McCafferty, E., Introduction to Corrosion Science, N.Y.: Springer, 2010, chapter 7.
Mansfeld, F., in Advances in Corrosion Science and Technology, vol. 6, Fontana, G. and Staehle, R.W., Eds., N.Y.: Plenum, 1976, chapter 2.
Дополнительные материалы отсутствуют.