Электрохимия, 2021, T. 57, № 5, стр. 301-308
Формирование плотного подслоя La(Sr)Fe(Ga)O3 на границе электролит/пористый катод методом магнетронного распыления и его влияние на характеристики электрода
Н. Б. Павздерин a, *, А. А. Соловьев b, А. В. Никонов a, А. В. Шипилова b, С. В. Работкин b, В. А. Семёнов b, А. С. Гренадёров b, К. В. Оскомов b
a Институт электрофизики УрО РАН
620016 Екатеринбург, ул. Амундсена, 106, Россия
b Институт сильноточной электроники СО РАН
634055 Томск, просп. Академический, 2/3, Россия
* E-mail: nipavzderin@iep.uran.ru
Поступила в редакцию 25.09.2020
После доработки 11.12.2020
Принята к публикации 18.12.2020
Аннотация
Исследовано получение плотных подслоев La(Sr)Fe(Ga)O3–δ (LSFG) на поверхности твердого электролита La0.88Sr0.12Ga0.82Mg0.18O3–δ (LSGM) методом магнетронного распыления, а также исследовано их влияние на электродные характеристики пористых катодов La0.7Sr0.3Fe0.95Ga0.05O3–δ. Показано, что наибольшее влияние на элементный состав покрытия оказывает элементный состав мишени, тогда как условия нанесения (мощность разряда, атмосфера и т.д.) влияют незначительно. В полученных покрытиях увеличивается содержание La и Ga, а содержание Sr и Fe уменьшается по сравнению с элементным составом распыляемой мишени. Обнаружено, что введение плотных подслоев между пористым электродом и электролитом улучшает электродные характеристики за счет облегчения перехода ионов O2– через границу электрод/электролит. Плотные подслои LSFG толщиной 600 и 800 нм приводят к снижению поляризационного сопротивления электрода при 850°С на 33 и 43% соответственно.
ВВЕДЕНИЕ
Твердооксидные топливные элементы (ТОТЭ) – электрохимические устройства, напрямую преобразующие химическую энергию топлива в электрическую. Структура ТОТЭ состоит из плотного слоя электролита, разделяющего пористые слои электродов (анод и катод). Для достижения высоких удельных мощностей топливных элементов необходимо минимизировать их внутреннее сопротивление, которое складывается из омического сопротивления, обусловленного в основном слоем электролита, и поляризационных потерь, связанных с электрохимическими процессами на электродах [1]. В настоящее время применяются две стратегии уменьшения омического сопротивления: 1) уменьшение толщины слоя электролита и 2) использование электролита, обладающего более высокой проводимостью, чем стабильный, хорошо изученный ZrO2, стабилизированный Y2O3 (YSZ). Одним из перспективных электролитных материалов, обладающих высокой ионной проводимостью и широкой рабочей областью парциального давления кислорода, является LaGaO3, допированный стронцием и магнием (LSGM) [2].
Подходы к уменьшению поляризационных потерь не столь прямолинейны. Электрохимические процессы на электродах зависят не только от состава и физико-химических свойств используемого электродного материала, но и от микроструктуры и морфологии границы электрод/электролит [3]. В настоящее время при разработке ТОТЭ в качестве катодов используются пористые слои композитных материалов или материалов со смешанной ион-электронной проводимостью. Основным методом улучшения их характеристик является расширение трехфазной границы за счет оптимизации микроструктуры [4]. Однако недавно было показано, что формирование плотного подслоя со смешанной ион-электронной проводимостью на границе электролит/пористый катод также может привести к снижению поляризационных потерь [5–9] за счет улучшения переноса ионов кислорода между катодом и электролитом. В одной из первых работ, посвященных исследованию плотного подслоя [5], было показано, что введение плотного слоя ферро-кобальтита лантана стронция (LSFC) толщиной 200 нм на электролит CeO2, допированный Y2O3 (YDC), привело к снижению поляризационного сопротивления в 3 раза. Тогда как в [6], где слой LSFC толщиной 700 нм наносили на CeO2, допированный Gd2O3 (GDC), наблюдалось снижение поляризационного сопротивления на 27%. Близкие к этому значения улучшения поляризационного сопротивления – на 27 и 29%, были получены в работе [7] для подслоев LaNi0.6Fe0.4O3–δ (200 нм) и La0.6Sr0.4Co0.2Fe0.8O3–δ (160 нм) на GDC соответственно. Кроме того, в работе [9] было продемонстрировано, что введение дополнительного плотного слоя LSFC (300 нм) поверх плотного промежуточного слоя GDC на электролите YSZ приводит к улучшению долговременной стабильности элемента (выдержка 300 ч при 800°С) из-за подавления формирования фазы SrZrO3 на границе LSFC–GDC.
Как видно, большинство работ по исследованию катодов с плотным подслоем было выполнено на электролитах на основе CeO2. Однако в работе [10] было продемонстрировано, что плотный композитный катод на основе La0.7Sr0.3Fe0.95Ga0.05O3–δ (200 мкм) в контакте с электролитом LSGM также имеет высокую каталитическую активность по отношению к реакции восстановления кислорода. Цель данной работы – получение тонкого (сотни нм) плотного подслоя La(Sr)Fe(Ga)O3 на электролите LSGM методом магнетронного распыления и исследование его влияния на электродные характеристики катода.
ЭКСПЕРИМЕНТАЛЬНАЯ ЧАСТЬ
В качестве исходных материалов использовали порошки La0.88Sr0.12Ga0.82Mg0.18O3–δ (LSGM), La0.4Sr0.6Fe0.95Ga0.05O3–δ (LSFG-6005), La0.5Sr0.5Fe0.93Ga0.07O3–δ (LSFG-5007), La0.7Sr0.3Fe0.95Ga0.05O3–δ (LSFG-3005), которые были получены методом самораспространяющегося высокотемпературного синтеза (СВС) в ИХТТ УрО РАН. Рентгенофазовый анализ, выполненный на дифрактометре D8 DISCOVER, показал, что все синтезированные порошки наряду с основной ромбоэдрической фазой (табл. 1) имели следы вторичных фаз, которые исчезали при спекании объемных образцов.
Таблица 1.
Кристаллоструктурные характеристики используемых материалов
Материал | Обозначение | Пространственная группа |
Параметр решетки, Å | γXRD, г/см3 |
---|---|---|---|---|
La0.88Sr0.12Ga0.82Mg0.18O3–δ | LSGM | R-3c | a = 5.522, c = 13.465 | 6.68 |
La0.4Sr0.6Fe0.95Ga0.05O3–δ | LSFG-6005 | R-3c | a = 5.497, c = 13.443 | 6.02 |
La0.5Sr0.5Fe0.93Ga0.07O3–δ | LSFG-5007 | R-3c | a = 5.511, c = 13.415 | 6.16 |
La0.7Sr0.3Fe0.95Ga0.05O3–δ | LSFG-3005 | R-3c | a = 5.510, c = 13.424 | 6.15 |
Дисковые подложки для нанесения плотных катодных подслоев изготавливались из порошка LSGM. Мишени для магнетронной распылительной системы формировались из порошков LSFG‑6005 и LSFG-5007. Исходные порошки прессовали на одноосном гидростатическом прессе. Прессовки LSGM и LSFG спекали при температуре 1400 и 1300°С соответственно. Выдержка в обоих случаях составляла 5 ч. Характерные размеры полученных подложек LSGM при плотности 93–95% от теоретической составляли: диаметр – 12.0 ± 0.5 мм, толщина – 0.70 ± 0.05 мм. Мишени LSFG после спекания имели диаметр 74.0 ± 0.5 мм и толщину 4.5 ± 0.5 мм. Плотность мишеней составляла 92% от теоретической.
Нанесение покрытий методом магнетронного распыления на подложки LSGM выполняли на установке, изготовленной в ИСЭ СО РАН. Формирование плотного подслоя LSFG осуществляли в режиме постоянного тока. Расстояние от мишени до подложки составляло 120 мм. Остаточное давление в вакуумной камере 10–2 Па. Нанесение покрытий выполняли без дополнительного нагрева подложки в среде чистого аргона (расход – 1.8 л/ч при давлении 0.32 Па) или кислород-аргоновой смеси (расход аргона 1.8 л/ч, расход кислорода 0.9 л/ч, рабочее давление смеси Ar + O2 составляло 0.37 Па). В пробных экспериментах для подбора параметров напыления в качестве подложек использовали кремниевые пластины ориентацией (100) и толщиной 450 ± 40 мкм.
Толщины сформированных покрытий определяли на стеклянных пластинах “свидетелях”, присутствующих при каждом акте осаждения, с помощью микроинтерферометра Линника МИИ-4. Полученные покрытия были исследованы методом рентгеновского анализа на дифрактометрах D8 DISCOVER и Shimadzu XRD 6000 (CuKα1.2 λ = = 1.542 Å). Обработка выполнена с использованием программ: TOPAS 3 и POWDER CELL 2.4 с использованием баз данных PDF 4+. Для исследования морфологии поверхности, микроструктуры поперечного излома и определения элементного состава покрытий использовались электронные микроскопы JSM 639LV с системой энергодисперсионного анализа EDS X-max 80 и Philips SEM-515, оснащенный микроанализатором EDAX ECON IV.
Исследование влияния плотных подслоев на электрохимические характеристики катодов было выполнено на симметричных образцах. Для этого слои LSFG наносили методом магнетронного распыления в отработанных режимах на обе стороны подложек LSGM. Затем поверх плотных слоев LSFG диаметром 10 мм, методом окрашивания были нанесены пористые катоды LSFG-3005 того же диаметра. Толщина пористого слоя составляла около 100 мкм. Для сравнения был изготовлен образец без плотного подслоя. Электроды припекались при температуре 1050°C с выдержкой 1 ч в атмосфере застойного воздуха. Исследование поляризационного сопротивления сформированных катодов проводили методом импедансной спектроскопии с помощью прибора ELINS P-40X. Спектры импеданса регистрировали в диапазоне частот 0.5 МГц–0.1 Гц при амплитуде входного сигнала 15 мВ. Измерения проводили в атмосфере застойного воздуха в диапазоне температур 850–650°С.
РЕЗУЛЬТАТЫ И ОБСУЖДЕНИЕ
В ходе предварительных экспериментов на кремниевой подложке была определена оптимальная удельная мощность разряда (Pd) для нанесения катодного подслоя, которая составила 7 Вт/см2. При этих условиях реализовывались как приемлемая скорость нанесения покрытия, так и долговечность мишени. При большей мощности происходит растрескивание мишени вследствие плохой теплопроводности материала. Эксперименты по варьированию атмосферы в рабочей камере показали, что катодные покрытия могут быть получены как в среде чистого аргона, так и в смеси Ar + O2. Введение кислорода в газовую смесь позволяет уйти от формирования пленок с дефицитом кислорода. Скорости роста катодного покрытия с обеих мишеней LSFG в атмосфере Ar + O2 практически совпадают – 8–9 нм/мин. Тогда как в среде Ar скорость роста покрытия с использованием мишени LSFG-6005 (26 нм/мин) почти в 2 раза превосходила скорость роста с использованием мишени LSFG-5007 (14 нм/мин).
Рентгенофазовый анализ покрытий, полученных при использовании мишени LSFG-6005, выполненный на дифрактометре D8 DISCOVER, показал, что напыление как в среде аргона, так и в смеси Ar + O2, приводит к формированию аморфного покрытия. Последующий отжиг при 600°С в течение 2 ч не приводит к структурным изменениям, тогда как отжиг при 800°С в течение 2 ч позволяет частично кристаллизовать аморфную фазу. Во всех случаях отжиг покрытий проводили в атмосфере застойного воздуха. После отжига покрытие, полученное в среде Ar, содержало около 6 об. % ромбоэдрической фазы с пространственной группой R-3c. Периоды кристаллической решетки составляли а = 5.513 Å и c = 13.494 Å, а размер области когерентного рассеяния (ОКР) ≈ ≈ 14 нм. Покрытие, полученное в смеси Ar + O2 после отжига при 800°С, содержит большее количество кристаллической фазы (≈20 об. %), которая характеризуется той же симметрией и очень близкими параметрами решетки: а = 5.48 ± 0.05 Å, c = 13.4 ± 0.3 Å, ОКР ≈ 14 нм. В то же время анализ, выполненный при малых углах рассеяния на дифрактометре Shimadzu XRD 6000, покрытия, полученного при использовании мишени LSFG-5007 в смеси Ar + O2 и отожженного при 800°С в течение 2 ч, показал, что оно не содержит аморфной составляющей, а представляет собой однофазный твердый раствор с ромбоэдрической решеткой (а = 5.536 Å, c = 13.392 Å, ОКР ≈ 32 нм). На рис. 1 приведено сравнение дифрактограмм мишени LSFG-5007 и покрытия LSFG, полученного в смеси Ar + O2 и отожженного при температуре 800°С. Можно заметить, что количество рефлексов и их положение на дифрактограммах мишени и нанесенного покрытия совпадают.
Рис. 1.
Дифрактограммы распыляемой мишени LSFG-5007 и покрытия LSFG, полученного в смеси Ar + O2 с последующим отжигом при 800°С.
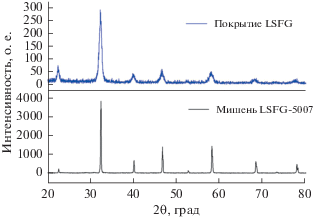
Известно, что при магнетронном распылении многокомпонентных материалов химический состав покрытия отличается от состава мишени. В литературе отсутствует информация о получении покрытий LSFG методом магнетронного распыления. Результаты элементного состава катодных покрытий, полученных в различных условиях, представлены в табл. 2. Наибольшее влияние на химический состав образцов оказал состав распыляемой мишени, в то время как газовая среда (Ar или Ar + O2) и последующий отжиг образцов не оказали на это значительного влияния. Отличие состава мишени и покрытия объясняется различием коэффициентов распыления элементов мишени и частичной потерей материала при его транспортировке к подложке. Обнаружено, что в покрытиях, по сравнению с элементным составом мишени, выросло содержание La и Ga, а содержание Sr и Fe уменьшилось. Причем, отношение количества элементов А-катиона в покрытии к их количеству в мишени для обеих исследованных мишеней приблизительно равно и составляет 1.6–1.8 и 0.40–0.47 для La и Sr соответственно. Тогда как отношение для Fe и Ga отличаются более существенно: для мишени LSFG-6005 отношение Fe и Ga составляют 0.82 и 4.40 соответственно, а для мишени LSFG-5007 – 0.98 и 1.30 соответственно.
Таблица 2.
Элементный состав покрытий
Условия получения | Состав покрытия, ат. % | |||||
---|---|---|---|---|---|---|
Мишень | Атмосфера | Tотжиг, °C | La | Sr | Fe | Ga |
LSFG-6005 | Ar | – | 0.72 | 0.28 | 0.67 | 0.33 |
Ar | 800 | 0.63 | 0.37 | 0.77 | 0.23 | |
Ar + O2 | 800 | 0.72 | 0.28 | 0.78 | 0.22 | |
LSFG-5007 | Ar | 800 | 0.75 | 0.25 | 0.91 | 0.09 |
Ar + O2 | – | 0.8 | 0.2 | 0.9 | 0.1 | |
Ar + O2 | 800 | 0.8 | 0.2 | 0.91 | 0.09 |
Для дальнейших электрохимических исследований симметричные образцы LSFG//LSGM//LSFG изготавливались с применением мишени LSFG-5007. Условия нанесения плотных катодных подслоев были выбраны на основе предварительных экспериментов: Pd = 7 Вт/см2, атмосфера Ar при давлении 0.32 Па. Исследование микроструктуры сколов полученных образцов не выявило каких-либо дефектов и отслоений на границе плотный катод/электролит (рис. 2а). Это говорит о высокой адгезии покрытия к подложке. На поверхности слоя LSFG наблюдаются отдельные каверны размером 0.5–3 мкм (рис. 2б). Дополнительный отжиг при 1000°С с выдержкой 4 ч не приводит к образованию добавочных дефектов. Поверх плотного слоя LSFG формировались пористые электроды LSFG-3005. Таким образом, получены симметричные образцы со структурой пористый катод–плотный катодный подслой–электролит для исследования поляризационных характеристик.
Рис. 2.
Микрофотографии скола (а) и поверхности (б) образца LSGM с нанесенным слоем LSFG толщиной 600 нм.
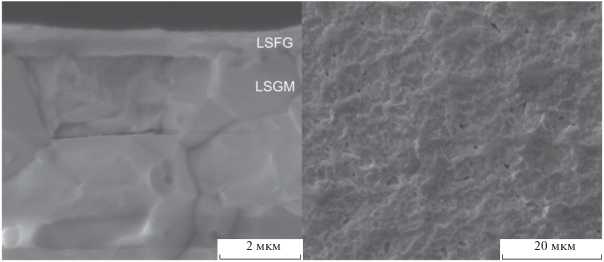
Методом импедансной спектроскопии были исследованы симметричные образцы без и с плотным подслоем LSFG толщиной 600 и 800 нм. Спектры импеданса, снятые при 850°C и искусственно сдвинутые для удобства сравнения, представлены на рис. 3. Можно заметить, что в спектрах всех образцов выделяются два процесса: высокочастотный и низкочастотный. Высокочастотный вклад связан с сопротивлением переноса иона O2– через границу электрод/электролит, а низкочастотный вклад связан с реакцией поверхностного обмена [11]. Видно, что высокочастотный процесс составляет основную долю в поляризационном сопротивлении исследованных электродов, и именно его вклад удалось уменьшить путем введения плотного подслоя LSFG. Таким образом, формирование плотного подслоя со смешанной ион-электронной проводимостью на границе пористый электрод/электролит облегчает перенос ионов O2– через эту границу.
На рис. 4 представлены температурные зависимости полного поляризационного сопротивления исследуемых электродов, а также энергии активации. Видно, что введение плотного подслоя LSFG толщиной 600 и 800 нм приводит к снижению поляризационного сопротивления электрода при 850°С на ~33 и 43% соответственно. Из литературы известно, что для процесса катодного восстановления при энергии активации около 1.4 эВ определяющим этапом является поверхностный обмен [12].
Рис. 4.
Температурные зависимости поляризационного сопротивления образцов LSFG//LSGM//LSFG без и с плотным подслоем LSFG.
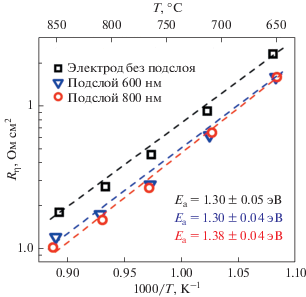
После проведения электрохимических испытаний, с поверхности образца с LSFG-покрытием толщиной 800 нм был снят пористый слой катода LSFG-3005 и проведен рентгенофазовый анализ плотного покрытия (рис. 5). Поскольку покрытие тонкое, то на дифрактограмме присутствуют как рефлексы, соответствующие материалу покрытия LSFG, так и материалу электролита LSGM. Аморфной составляющей не обнаружено. Анализ полученных данных показал, что структура электролита LSGM незначительно отличается от структуры исходного порошка: при той же пространственной группе R-3c параметры решетки составляют a = 5.539 ± 0.004 Å, c = 13.524 ± 0.008 Å. Структура плотного покрытия LSFG описывается ромбоэдрической фазой с пространственной группой R-3c и параметрами решетки а = 5.518 ± ± 0.005 Å, c = 13.449 ± 0.009 Å, ОКР ≈ 72 нм. Кроме того, в исследованной структуре присутствуют следы кубической и гексагональной модификации La2O3 ≈ 1 вес. % и следы неустановленных кристаллических фаз ~ 1 об. %.
Незначительное количество вторичных фаз (даже если они полностью локализованы в катодном подслое) не должно сильно влиять на проводимость LSFG. В литературе отсутствует информация о проводимости состава, соответствующего материалу плотного подслоя, который близок к La0.8Sr0.2Fe0.9Ga0.1O3–δ. Полная проводимость состава La0.8Sr0.2FeO3–δ при 800°С составляет 120 См/см [13, 14]. Однако введение Ga значительно снижает ее значение. Так, в [15] было показано, при 250°С проводимость La0.5Sr0.5FeO3–δ снижается в 2.8 раза при введении 10 мол. % Ga, а в [16] продемонстрировано, что добавка 20 мол. % Ga приводит к снижению проводимости La0.3Sr0.7FeO3–δ в 4 раза при 800°С. Таким образом, полную проводимость подслоя LSFG при 800°С можно оценить значением порядка 40 См/см. Ионная проводимость составов La0.3Sr0.7FeO3–δ и La0.6Sr0.4FeO3–δ при 800°С составляет 0.022 и 0.0056 См/см соответственно [16, 17]. Видно, что увеличение соотношения La/Sr ведет к снижению ионной проводимости. С другой стороны, допирование галлием повышает ионную составляющую проводимости. Введение 20 и 40 мол. % Ga приводит к росту ионной проводимости La0.3Sr0.7FeO3–δ в 1.7 и 2.3 раза соответственно [16]. Следовательно, ионная проводимость слоя LSFG при 800°С должна составлять 0.005–0.002 См/см, что в десятки раз меньше проводимости электролита LSGM (0.15 См/см при 800°С [18]). Однако, как было показано выше, наличие плотного подслоя снижает поляризационное сопротивление. По-видимому, это обусловлено не столько величиной ионной проводимости LSFG, сколько ее смешанным ион-электронным характером, который делает возможным протекание реакции восстановления кислорода по всей поверхности подслоя LSFG. Кроме того, смешанная проводимость способствует выравниванию концентрации ионов кислорода в объеме подслоя и, следовательно, позволяет использовать для переноса O2– через границу катод/электролит всю площадь их контакта.
Таким образом, плотный катодный подслой должен характеризоваться некой оптимальной толщиной, обеспечивающей равномерное распределение ионов кислорода по всей поверхности на границе с электролитом. Дальнейшее увеличение толщины будет вносить дополнительный вклад в омическое сопротивление топливного элемента. Однако оптимальная толщина подслоя зависит от многих факторов: проводимости подслоя (ионной и электронной составляющей), микроструктуры и состава пористого катода, состава электролита, метода формирования и т.д. Так в работах [5] и [7] подслои LSFC близкого состава и толщины, но нанесенные разными методами (лазерная абляция и центрифугирование) на разные электролиты (YDC и GDC), привели к улучшениям катодных характеристик, отличающимся на порядок (300 и 29%, соответственно). Работ, в которых варьировалась толщина плотных подслоев, крайне мало. В [7] определено, что для подслоев LaNi0.6Fe0.4O3–δ и La0.6Sr0.4Co0.2Fe0.8O3–δ оптимальная толщина составляет порядка 200 нм. Тогда как в [19], где исследовались топливные элементы на несущем аноде, толщина плотного катодного подслоя La0.6Sr0.4CoO3–δ, при котором была достигнута наибольшая удельная мощность 2150 мВт/см2 при 800°С, составляла 600 нм. В настоящей работе впервые представлены результаты получения и исследования плотных подслоев LSFG, сформированных методом магнетронного распыления. Исследование влияния толщины подслоя на поляризационное сопротивление является частью дальнейших исследований.
ЗАКЛЮЧЕНИЕ
В работе представлен один из вариантов получения многоэлементного покрытия La(Sr)Fe(Ga)O3–δ (LSFG) на поверхности высокопроводящего твердого электролита La0.88Sr0.12Ga0.82Mg0.18O3–δ (LSGM) методом магнетронного распыления и исследовано влияние плотных подслоев на электродные характеристики пористых катодов LSFG. Для формирования покрытий использовались две мишени: La0.4Sr0.6Fe0.95Ga0.05O3–δ и La0.5Sr0.5Fe0.93Ga0.07O3–δ. Показано, что наибольшее влияние на химический состав покрытия оказал химический состав мишени, тогда как варьирование атмосферы и дополнительный отжиг повлияли незначительно. По сравнению с элементным составом мишеней в покрытиях увеличилось содержание La и Ga, а содержание Sr и Fe уменьшилось.
Исследование электрохимических характеристик пористых электродов La0.7Sr0.3Fe0.95Ga0.05O3–δ без и с плотным подслоем, сформированным методом магнетронного распыления, показало, что введение подслоев позволяет снизить поляризационное сопротивление на 30–40% за счет облегчения перехода ионов O2– через границу электрод/электролит.
Список литературы
Solid Oxide Fuels Cells: Facts and Figures / Eds Irvine, J.T.S., Connor, P. London: Springer, 2013. 230 p.
Ishihara, T., Matsuda, H., Bustam, M.A., and Takita, Y., Oxide ion conductivity in doped Ga based perovskite type oxide, Solid State Ionics, 1996, vol. 86–88, p. 197.
Мурыгин, И.В. Электродные процессы в твердых электролитах, М.: Наука, 1991. 351 с. [Murygin, I.V., Electrode processes in solid electrolytes (in Russian), M.: Science, 1991. 351 p.]
Sun, C., Hui, R., and Roller, J., Cathode materials for solid oxide fuel cells: a review, J. Solid State Electrochem., 2010, vol. 14, p. 1125.
Hildenbrand, N., Boukamp, B.A., Nammensma, P., and Blank, D.H.A., Improved cathode/electrolyte interface of SOFC, Solid State Ionics, 2011, vol. 192, p. 12.
Dumaisnil, K., Fasquelle, D., Mascot, M., Rolle, A., et al., Synthesis and characterization of La0.6Sr0.4Co0.8Fe0.2O3 films for solid oxide fuel cell cathodes, Thin Solid Films, 2014, vol. 553, p. 89.
Chrzan, A., Karczewski, J., Gazda, M., Szymczewska, D., and Jasinski, P., Investigation of thin perovskite layers between cathode and doped ceria used as buffer layer in solid oxide fuel cells, J. Solid State Electrochem., 2015, vol. 19, p. 1807.
Dumaisnil, K., Carru, J.-C., Fasquelle, D., et al., Promising performances for a La0.6Sr0.4Co0.8Fe0.2O3–δ cathode with a dense interfacial layer at the electrode-electrolyte interface, Ionics, 2017, vol. 23, p. 2125.
De Vero, J.C., Develos-Bagarinao, K., Kishimotoa, H., et al., Enhanced stability of solid oxide fuel cells by employing a modified cathode-interlayer interface with a dense La0.6Sr0.4Co0.2Fe0.8O3–δ thin film, J. Power Sources, 2018, vol. 377, p. 128.
Никонов, А.В., Павздерин, Н.Б., Шкерин, С.Н., Гырдасова, О.И., Липилин, А.С. Создание многослойной керамической структуры для топливного элемента на основе катода La(Sr)Ga(Mg)O3–La(Sr)Fe(Ga)O3. Журн. прикл. химии. 2017. Т. 90. С. 307. [Nikonov, A.V., Pavzderin, N.B., Shkerin, S.N., Gyrdasova, O.I., and Lipilin, A.S., Fabrication of multilayer ceramic structure for fuel cell with La(Sr)Ga(Mg)O3–La(Sr)Fe(Ga)O3 cathode, Russ. J. Appl. Chem., 2017, vol. 90, № 3, p. 369.]
Zhou, W., Ran, R., Shao, Z., et al., Barium- and strontium-enriched (Ba0.5Sr0.5)1 +xCo0.8Fe0.2O3–d oxides as high-performance cathodes for intermediate-temperature solid-oxide fuel cells, Acta Materialia, 2008, vol. 56, p. 2687.
Park, K., Lee, C., Bae, J., and Yoo, Y., Structural and electrochemical properties of Pr0.3Sr0.7Co0.3Fe0.7O3–δ cathode for IT-SOFC, Intern. J. Hydrogen Energy, 2009, vol. 34, p. 6852.
Coffey, G.W., Hardy, J., Pedersen, L.R., et al., Electrochemical properties of lanthanum strontium aluminum ferrites for the oxygen reduction reaction, Solid State Ionics, 2003, vol. 158, p. 1.
Tietz, F., Raj, I.A., Zahid, M., and Stover, D., Electrical conductivity and thermal expansion of La0.8Sr0.2(Mn,Fe,Co)O3–y perovskites, Solid State Ionics, 2006, vol. 177, p. 1753.
Шкерин, С.Н., Кузьмин, А.В., Гырдасова, О.И., Строева, А.Ю., Никонов, А.В. Электропроводность и термическое расширение La1–xSrxFe1–yGayO3–δ (x = 0.2–0.5; y = 0–0.4). Электрохимия. 2017. Т. 53. С. 172. [Shkerin, S.N., Kyz’min, A.V., Gyrdasova, O.I., Stroeva, A.Yu., and Nikonov, A.V., Electrical conductivity and thermal expansion of La1–xSrxFe1–yGayO3–δ (x = 0.2–0.5; y = 0–0.4), Russ. J. Electrochem., 2017, vol. 53, p. 154.]
Kharton, V.V., Shaulo, A.L., Viskup, A.P., Avdeev, M., et al., Perovskite-like system (Sr,La)(Fe,Ga)O3–δ: structure and ionic transport under oxidizing conditions, Solid State Ionics, 2002, vol. 150, p. 229.
Ullmann, H., Trofimenko, N., Tietz, F., Stover, D., and Ahmad-Khanlou, A., Correlation between thermal expansion and oxide ion transport in mixed conducting perovskite-type oxides for SOFC cathodes, Solid State Ionics, 2000, vol. 138, p. 79.
Никонов, А.В., Шкерин, С.Н., Липилин, А.С., и др. Временная зависимость проводимости электролита La0.88Sr0.12Ga0.82Mg0.18O2–δ изготовленного методом магнитно-импульсного прессования. Электрохимия. 2011. Т. 47. С. 783. [Nikonov, A.V., Shkerin, S.N., Lipilin, A.S., et al., Aging of electrolyte La0.88Sr0.12Ga0.82Mg0.18O2–δ made using magnetic–pulse compaction, Russ. J. Electrochem., 2011, vol. 47, p. 733.]
Smolyanskiy, E.A., Linnik, S.A., Lauk, A.L., Solovyev, A.A., et al., Magnetron sputtered LSC thin films for solid oxide fuel cell application, J. Phys. Conf. Ser., 2018, vol. 1115, p. 032080.
Дополнительные материалы отсутствуют.