Электрохимия, 2022, T. 58, № 2, стр. 76-84
Изготовление и электрохимические характеристики ТОТЭ на основе несущих двухслойных анодных подложек, полученных методом литья на движущуюся ленту
Е. А. Агаркова a, *, О. Ю. Задорожная c, И. Н. Бурмистров a, Д. А. Агарков a, b, **, А. А. Соловьев d, А. В. Шипилова d, М. Н. Левин e, Ю. К. Непочатов c, С. И. Бредихин a
a Федеральное государственное бюджетное учреждение науки Институт физики твердого тела
имени Ю.А. Осипьяна РАН
142432 Московская обл., Черноголовка, ул. Академика Осипьяна, 2, Россия
b Федеральное государственное автономное образовательное учреждение высшего образования
“Московский физико-технический институт (национальный исследовательскийуниверситет)”
141701 Московская обл., Долгопрудный, Институтский пер., 9, Россия
c АО “НЭВЗ-Керамикс”
630048 Новосибирск, просп. Красный, 220, Россия
d Федеральное государственное бюджетное учреждение науки
Институт сильноточной электроники СО РАН (ИСЭ СО РАН)
634055 Томск, просп. Академический, 2/3, Россия
e ООО “ИНЭСИС”, Группа компаний “ЭФКО”
115035 Москва, Овчинниковская наб., 20, с. 2, Россия
* E-mail: stepanova.ea@issp.ac.ru
** E-mail: agarkov@issp.ac.ru
Поступила в редакцию 12.10.2020
После доработки 17.02.2021
Принята к публикации 31.08.2021
- EDN: MCSSTZ
- DOI: 10.31857/S0424857022020037
Аннотация
Двухслойные подложки для создания анод-поддерживающих твердооксидных топливных элементов (ТОТЭ) были изготовлены на основе композитов из NiO и ZrO2, стабилизированного 10 мол. % Sc2O3 и 1 мол. % Y2O3(10Sc1YSZ), методом литья на движущуюся ленту. Оптимизация доли порообразователя (крахмала) в исходной суспензии несущего токосъемного слоя и режима температурной обработки обеспечили необходимую пористость при сохранении высоких прочностных характеристик субстрата. Механическая прочность подложек оценивалась методом трехточечного изгиба. Методом магнетронного напыления с последующим отжигом при температуре 1200°С был нанесен двуслойный газоплотный электролит со слоями ZrO2, стабилизированного 8 мол. % Y2O3(8YSZ), и Ce0.9Gd0.1O1.95. Исследование электрохимических характеристик образца ТОТЭ с катодом La0.6Sr0.4CoO3 − δ показало, что с понижением рабочей температуры растет вклад электродных процессов во внутреннее сопротивление элемента, что приводит к снижению удельной снимаемой мощности, достигающей 1.8, 1.4 и 0.9 Вт/см2 при 850, 800 и 750°С, соответственно.
ВВЕДЕНИЕ
Твердооксидные топливные элементы (ТОТЭ) являются перспективными электрохимическими генераторами электрической энергии и высокопотенциального тепла [1]. На сегодняшний день не известна более эффективная технология преобразования химической энергии окисления углеводородных видов топлива (природного газа, пропан-бутана, диметилового эфира и даже подготовленного дизельного топлива) в электрическую и высокопотенциальную тепловую энергию. На большинстве территории Российской Федерации применение таких источников энергии экономически оправдано из-за недостаточной развитости Единой энергетической системы (ЕЭС), а также в связи с необходимостью освоения труднодоступного Арктического региона и Северного морского пути.
Существует несколько разновидностей ТОТЭ, отличающихся выбором элемента, обеспечивающего механическую прочность образца: электролит-поддерживающие, анод-поддерживающие, металл-поддерживающие ТОТЭ и ТОТЭ с другими типами поддержки (например, катод или внешняя керамическая подложка) [1]. Выбор конструкции определяет очередность изготовления, микроструктуру и толщины слоев единичного ТОТЭ и, как следствие, рабочий режим элемента (рабочая температура, давление подаваемых газов, состав и процент утилизации топлива и т.д.). Анод-поддерживающие ТОТЭ (650–750°С) не имеют таких недостатков электролит-поддерживающих, как высокая стоимость (за счет возможности использования более дешевых электролитов, не содержащих дорогостоящий скандий, а также за счет уменьшения толщины электролитического слоя более, чем в 10 раз) и ускоренная деградация характеристик за счет пониженной рабочей температуры (рабочий диапазон температур для электролит-поддерживающих ТОТЭ лежит в пределах 800–1000°С). Металл-поддерживающие ТОТЭ работают при температурах 500–600°С и по сравнению с остальными типами имеют наиболее высокие электрохимические характеристики (плотность снимаемой мощности), но их изготовление требует высоких трудозатрат по причине слабой применимости стандартных коллоидных методов для изготовления функциональных слоев ТОТЭ. Таким образом, изготовление анод-поддерживающих структур является наиболее технологичным и экономически оправданным.
Изготовление единичного ТОТЭ следует начинать с изготовления несущей подложки. В случае анод-поддерживающей структуры подложка, с одной стороны, должна быть механически прочной, а с другой – должна обладать минимальным газовым сопротивлением, т.е. иметь развитую сеть магистральных пор. Для повышения эффективности в структуру анодного электрода ТОТЭ вводят дополнительный функциональный слой. Функциональный слой должен иметь более мелкую структуру для получения большой площади трехфазных границ, на которых происходит реакция окисления топлива. Наличие крупных пор не приветствуется, поскольку толщина функционального слоя обычно не превышает 20 мкм, а крупные поры уменьшают полезный для протекания электрохимических реакций объем электрода. Необходимая для протекания реакции развитая мелкая (менее 1 мкм) пористость в функциональном слое появляется во время работы элемента за счет объемного эффекта восстановления NiO до металлического Ni – около 42%. По этой причине в суспензию, используемую для отливки функционального слоя, не добавляют порообразователи.
Наиболее подходящим методом изготовления несущих керамических подложек для ТОТЭ является пленочное литье [2]. Ранее этот метод был применен нами для изготовления подложек трехслойного несущего электролита. В работе [3] были описаны подробности разработанной технологии, включающей изготовление методом пленочного литья листов электролита различного состава с последующим ламинированием их в многослойные пакеты и высокотемпературной обработкой. В данной работе суспензия готовится на основе предварительно измельченных порошков и органических растворителей с использованием связующего, пластификаторов и диспергатора в 2 стадии, длительностью 24 ч каждая. Ламинирование структур проводится в гидростатическом прессе при повышенной температуре. Многоступенчатый обжиг структур проводится с использованием укрывных пластин с защитным ZrO2-покрытием в течение 56 ч с выдержкой при температуре 1350°С в течение 2–4 ч.
Одной из самых сложных задач при изготовлении анод-поддерживающего ТОТЭ является формирование тонкого газоплотного слоя электролита на пористой анодной подложке. В качестве материала электролита используется анионный проводник – чаще всего диоксид циркония, стабилизированный оксидами редкоземельных элементов: иттрия, скандия, церия, иттербия и т.д. Толщина такого слоя обычно не превышает 10 мкм и определяет рабочую температуру элемента, поскольку при понижении температуры большая часть омических потерь приходится на перенос ионного тока в твердом электролите [4, 5], сопротивление которого зависит от рабочей температуры по закону Аррениуса. Изготовление тонкого слоя (менее 10 мкм) возможно с использованием методики магнетронного распыления, которая в работе [6] применялась для изготовления защитного CGO-подслоя и YSZ-электролита на анодной подложке состава NiO–YSZ; “холодного” аэрозольного нанесения [7]; чернильной печатью [8].
По причине более низких, в сравнении с электролит-поддерживающими ТОТЭ, рабочих температур, катодный электрод для анод-поддерживающего ТОТЭ требует применения высокоактивных катодных материалов, обладающих высокой смешанной проводимостью, таких как LSC (La0.6Sr0.4CoO3 – δ) или LSCF (LaxSr1 –xCoyFe1 –yO3 – δ). Нанесение катодного электрода, как и в случае электролит-поддерживающих ТОТЭ, чаще всего осуществляется методом трафаретной печати [4, 5, 7, 9].
В данной работе были изготовлены и охарактеризованы полноразмерные (100 × 100 мм2) планарные анод-поддерживающие ТОТЭ. Для изготовления подложки двуслойного несущего анода использовался метод литья на движущуюся ленту с последующим ламинированием и обжигом полученных многослойных пакетов. Для нанесения тонких плотных слоев 8YSZ-электролита (8 мол. % Y2O3, 92 мол. % ZrO2) и барьерного GDC10 (10 мол. % Gd2O3, 90 мол. % CeO2) слоя применялся метод магнетронного напыления. Для исследования электрохимических характеристик были изготовлены ТОТЭ с катодом на основе LSC.
МЕТОДИКА ЭКСПЕРИМЕНТА
В качестве исходного сырья для изготовления двухслойной анодной подложки были использованы порошки 10Sc1YSZ ((Sc2O3)0.1–(Y2O3)0.01–(ZrO2)0.89) производства ЗАО “Неохим” (Москва, Россия) и NiO производства ООО “Т:СП” (с. Горный Щит, Екатеринбург, Россия).
Изготовление подложек осуществлялось методом пленочного литья с последующим ламинированием. Суспензии помимо порошков содержали азеотропную смесь растворителей (метилэтилкетон (х. ч.) и изопропиловый спирт (х. ч.)), связующее PVB производства Butvar (Showiningan, Англия), пластификаторы ПЭГ-2000 (Sigma-Aldrich, США) и Santicizer производства Valtris Specialty hemicals (США), диспергатор – MenhadenFishOil производства Sigma Chemical Company (США). Для получения пористой структуры токосъемного слоя в суспензию был добавлен рисовый крахмал BOTGAO производства VinhThuan (Вьетнам).
Приготовление суспензий происходило на валковой мельнице в три стадии длительностью 4, 24 и 24 ч: на первой стадии производился сухой помол порошков 10Sc1YSZ и NiO, на второй производилось перемешивание порошков в растворителях с участием диспергатора, на третьей в суспензию добавлялись связующее и пластификаторы. Для помола и равномерного вымешивания суспензии, в нее были добавлены керамические мелющие тела из ZrO2 диаметром 10 мм. Непосредственно перед литьем суспензии проходили стадию дегазации в течение 2–4 ч. Литье происходило на линии KEKO (Словения).
Поскольку толщина токосъемной структуры после обжига должна находиться в пределе 390–410 мкм, с учетом усадки толщина отлитой ленты до выхода из нее растворителей должна быть не менее 1.5 мм. Ленты такой толщины трудно поддаются равномерному высыханию и трескаются на стадии их высыхания. Поэтому для получения двуслойной структуры, где толщина токосъемного слоя составляет около 400 мкм, а толщина функционального – около 20 мкм, было использовано 4 сырых токосъемных листа толщиной 200 мкм (после высыхания) и 1 функциональный.
Обжиг сырых стеков производился на воздухе в высокотемпературной печи с использованием огнеупорных капселей (Conrad Liphard & Soehne GmbH, Германия) и огнеупорных пластин из Al2O3 с защитным циркониевым покрытием (Fuel Cell Materials, США).
Для нанесения двухслойного электролита 8YSZ/GDC10 методом реактивного импульсного двойного магнетронного напыления использовались металлические мишени Zr–Y (85 : 15 ат. %) и Ce–Gd (90 : 10 ат. %) производства ООО “Гирмет” (Москва, Россия), размером 100 × 300 мм с чистотой 99.5%. Напыление производилось в атмосфере смеси Ar/O2 при рабочем давлении 0.2 Па. Подложки устанавливались на вращающийся барабан для получения пленок одинаковой толщины по всей площади. Перед напылением подложки последовательно очищали ультразвуком в чистом изопропиловом спирте, ацетоне и дистиллированной воде. Перед напылением вакуумную камеру откачивали до базового давления 10–3 Па. Образцы предварительно нагревали примерно до 400°C, данная температура поддерживалась во время напыления. После этого проводилась ионно-лучевая обработка поверхности подложки в течение 10 мин (напряжение разряда 2 кВ, ток разряда 100 мА) с использованием источника ионов с замкнутым дрейфом электронов. Мощность разряда на мишенях Zr-Y составляла 4 и 3 кВт на мишенях Ce–Gd. После нанесения слоя YSZ толщиной 4 мкм был нанесен слой GDC толщиной 1.5 мкм. Скорость осаждения пленок YSZ и GDC составляла 0.72 и 2 мкм/ч соответственно.
Катодный электрод наносился методом трафаретной печати (EKRA E 2, Германия) с использованием пасты на основе La0.8Sr0.2CoO3 производства Kceracell (Корея).
Микроструктура получаемых многослойных керамических пластин была изучена с помощью сканирующего электронного микроскопа (СЭМ) Supra 50VP (CarlZeiss, Великобритания).
Механические свойства подложек были оценены с помощью метода трехточечного изгиба на установке Instron 1195. Схема измерений и фотография монокристаллической сапфировой оснастки приведены в работе [9]. Размеры образцов составляли 24 × 9 мм2. Расстояние между точками контакта образцов и оснастки – 21 мм. Точка приложения усилия находилась на равных расстояниях от точек контакта. Деформация производилась при комнатной температуре со скоростью 0.5 мм/мин.
Электрохимические характеристики элементов были изучены с помощью электронной нагрузки PowerLoad PL-150 и импедансметра Z‑500P (Elins, Россия).
РЕЗУЛЬТАТЫ И ОБСУЖДЕНИЕ
В первую очередь, было исследовано влияние содержания порообразователя в суспензии на микроструктурные и прочностные характеристики анодных подложек. Для этого были изготовлены подложки из суспензий с содержанием крахмала в диапазоне 0–20 мас. % сухой смеси. Для достижения требуемой толщины (420 мкм) проводили ламинацию многослойных пакетов с последующим обжигом в температурном диапазоне 1250–1350°С.
На рис. 1 представлены изображения, полученные методом сканирующей электронной микроскопии, при увеличении 5 000, поперечного сечения подложек с различным содержанием крахмала (0, 10 и 20 мас. %), отожженных при температуре 1350°С. Увеличение доли крахмала в суспензии до 20 мас. % приводит к разрушению керамической структуры, в том числе расслоению по внутренним плоскостям ламинации многослойных пакетов, появлению крупных пустот. Такое поведение объясняется большой долей органических материалов в сырой ленте – более 45 мас. %. Отсутствие порообразователя в суспензии, в свою очередь, приводит к получению пластин с почти 100%-ной плотностью. Таким образом, было показано, что добавление рисового крахмала в объеме 10 мас. % от сухой смеси позволяет получить керамическую структуру требуемой пористости при сохранении высоких прочностных характеристик подложки.
Рис. 1.
Микроструктура поперечного сечения однослойных подложек, обожженных при 1350°С при увеличении 5000. В суспензии (а) не содержалось крахмала; (б) 10 мас. % крахмала; (в) 20 мас. % крахмала.
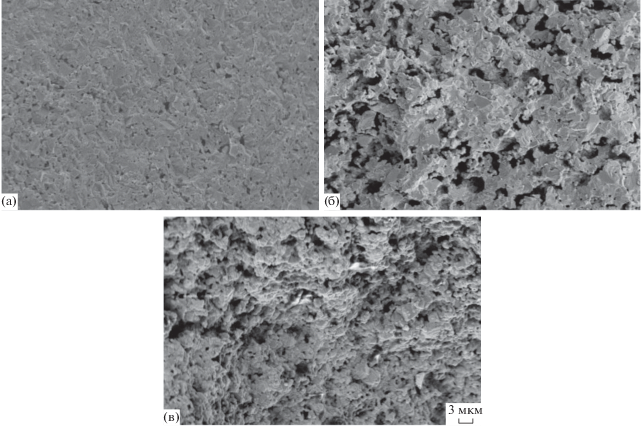
Максимальной температурой обжига контролируется характерный размер зеренной структуры подложки и ее механическая стабильность, соответственно. На рис. 2 и 3 представлены изображения поперечного сечения пластин с содержанием крахмала в суспензии 10 и 20 мас. %, обожженных при 1250, 1300 и 1350°С. Видно, что с повышением температуры происходит рост зерна и одновременно уменьшение количества пор субмикронного размера. Стоит отметить, что даже при температуре обжига 1350°С размер зерна структуры не превышает 1 мкм, что достаточно для создания высокоэффективного анода ТОТЭ с развитой трехфазной границей [4].
Рис. 2.
Микроструктура поперечного сечения однослойных подложек, полученных из суспензии, содержащей 10 мас. % крахмала, при увеличениях 5000 и 25 000: (а, б) обжиг при температуре 1250°С; (в, г) обжиг при температуре 1300°С; (д, е) обжиг при температуре 1350°С.
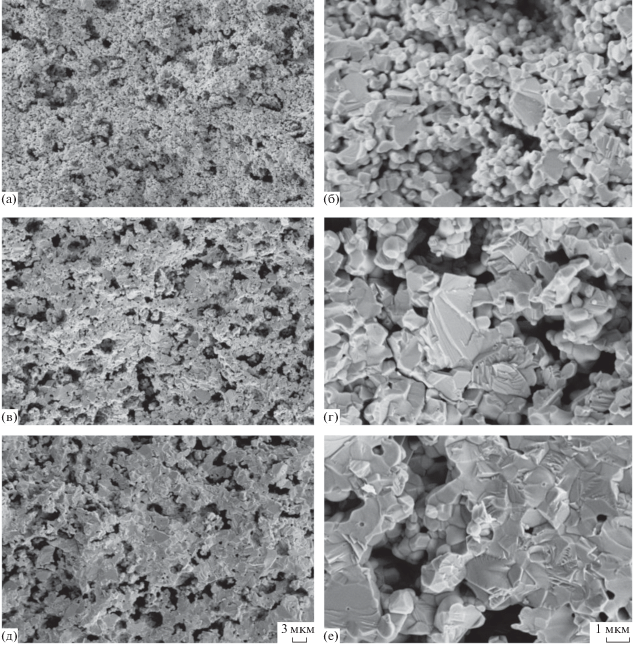
Рис. 3.
Микроструктура поперечного сечения однослойных подложек, полученных из суспензии, содержащей 20 мас. % крахмала, при увеличениях 5000 и 25 000: (а, б) обжиг при температуре 1250°С; (в, г) обжиг при температуре 1300°С; (д, е) обжиг при температуре 1350°С.
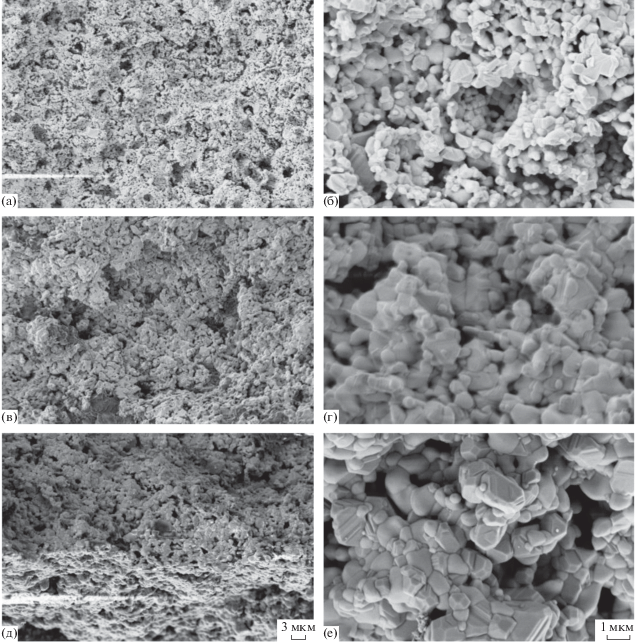
Результаты испытания механических характеристик подложек представлены на рис. 4. Чем выше температура обжига и меньше пористость, тем более высокую механическую нагрузку может выдержать керамическая подложка. Подложка с содержанием крахмала в суспензии 10 мас. %, полученная при температуре 1350°С, обладает достаточной пористостью и высокой механической стабильностью и является оптимальной для изготовления несущей подложки единичного ТОТЭ анод-поддерживающей конструкции.
Рис. 4.
Предельные значения прогиба и величины нагрузки при определении механической прочности однослойных подложек, изготовленных с использованием 10 и 20 мас. % крахмала в суспензии, обожженных при 1250, 1300 и 1350°С, трехточечным методом на изгиб.
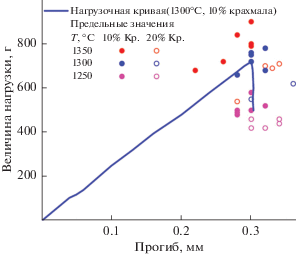
Для получения двуслойной несущей подложки с требуемой толщиной слоев ленты токосъемного и функционального слоя ламинируют, полученный многослойный пакет режут и спекают при температуре 1350°С. СЭМ-изображения поверхностей и поперечного сечения полученных двухслойных пластин представлены на рис. 5. Из рисунков видно, что адгезия между слоями хорошая, функциональный слой также хорошо спечен и не содержит крупных магистральных пор при сохранении размера зерна менее 1 мкм.
Рис. 5.
Микроструктура поперечного сечения (а), поверхности токосъемного слоя (б), поверхности функционального слоя (в) двухслойных подложек, отожженных при температуре 1350°С при увеличении 1000.
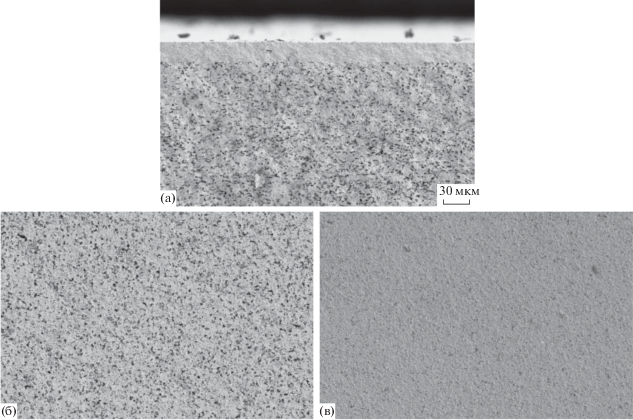
Для изучения электрохимических характеристик изготовленных двухслойных анодных подложек были подготовлены модельные ТОТЭ. Для чего на поверхность подложки методом магнетронного напыления (с последующим отжигом на воздухе при температуре 1200°С) был нанесен двухслойный электролит: основной слой состава 8YSZи барьерный слой состава GDC10, необходимый для предотвращения образования непроводящих фаз на границе электролита и катода. Стоит отметить, что метод магнетронного напыления предъявляет высокие требования к качеству используемых подложек. Микрофотографии поперечного сечения анодной подложки с нанесенным двуслойным электролитом после отжига при 1200°С представлены на рис. 6. Из рисунка видно, что электролитические слои показывают высокую плотность, полное отсутствие сквозной пористости и хорошую адгезию как между собой, так и к подложке несущего анода, а толщина составляет 4 и 1.5 мкм для 8YSZ и GDC10 соответственно.
Рис. 6.
Микроструктура поперечного сечения двухслойного электролита на двухслойной анодной подложке при увеличении 10 000.
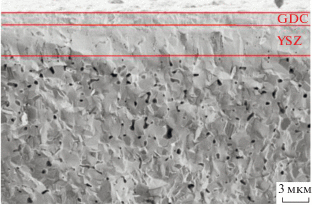
Катод на основе кобальтита лантана–стронция был изготовлен методом трафаретной печати. Спекание катода проводилось в процессе испытания характеристик модельного ТОТЭ. Фотография поперечного сечения катодной стороны изготовленного модельного ТОТЭ представлена на рис. 5в.
Мощностные и вольт-амперные характеристики были изучены при температурах 800, 750, 700°С при потоках водорода 150 мл/мин, воздуха 450 мл/мин. На рис. 7а видно, что во всех трех случаях напряжение открытой цепи составляло более 1 В, что свидетельствует о достаточно высоком качестве слоев электролита, обеспечивающем низкий уровень газовых и зарядовых утечек.
Рис. 7.
Вольт-амперные (а) и мощностные (б) характеристики, полученные при температурах 700, 750, 800°С.
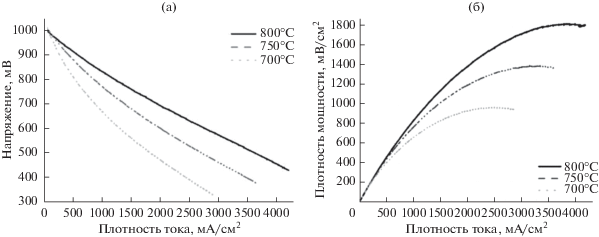
Максимальная плотность снимаемой мощности достигает 1.8 Вт/см2 при 800°С (рис. 7б), что свидетельствует о крайне низком значении внутреннего сопротивления изготовленных модельных ТОТЭ. Стоит отметить, что понижение рабочей температуры до 700°С приводит к снижению плотности мощности почти в 2 раза (0.96 Вт/см2). Из годографов импедансных спектров (рис. 8) видно, что снижение характеристик изготовленных анод-поддерживающих ТОТЭ преимущественно обусловлено ростом вклада электродных процессов во внутреннее сопротивление элемента. Поляризационная часть сопротивления увеличивается более чем в 5 раз при понижении температуры на 100°С и составляет более 0.55 Ом см2. В то же время вклад омических потерь меняется незначительно и не превышает 0.1 Ом см2 даже при 700°С.
Список литературы
Irshad, Muneeb, et al., A Briefdescriptionof high temperature solid oxide fuel cell’s operation, materials, design, fabrication technologies and performance, Appl. Sci., 2016, vol. 75, no. 6.
Thorel, Alain, Tape casting ceramics for high temperature fuel cell applications, 2010.
Zadorozhnaya, O.Yu., et al., Layered solid-electrolyte membranes based on zirconia: production technology, Russ. J. Electrochem., 2020, vol. 56, p. 124.
Burmistrov, I.N., et al., Fabrication of membrane-electrode assemblies for solid-oxide fuel cells by joint sintering of electrodes at high temperature, Russ. J. Electrochem., 2017, vol. 53, p. 873.
Burmistrov, I.N., Agarkov, D.A., Tsybrov, F.M., and Bredikhin, S.I., Preparation of membrane-electrode assemblies of solid oxide fuel cells by co-sintering of electrodes, Russ. J. Electrochem., 2016, vol. 52, p. 669.
Solovyev, A.A., et al., Magnetron-sputtering YSZ and SGO electrolytes for SOFC, J. Electron. Mater., 2016, no. 45, p. 3921.
Erilin, I.S., et al., Aerosol deposition of thin-film solid electrolyte membranes for anode-supported solid oxide fuel cells, Mater. letters, 2020, no. 266.
Young, D., et al., Ink-jet printing of electrolyte and anode functional layer for solid oxide fuel cells, J. Power Sources, 2008, vol. 184, I. 1, p. 191.
Eliseeva, G.M., et al., In-situ Raman spectroscopy stugies of oxygen spillover at solid oxide fuel cell anodes, Chem. Problems, 2020, vol. 18, no. 1, p. 9.
Дополнительные материалы отсутствуют.