Электрохимия, 2022, T. 58, № 4, стр. 168-178
Характеристики композитного катода La0.6Sr0.4Co0.8Fe0.2O3 – δ–Ce0.73Gd0.27O3 – δ, изготовленного из нанопорошков
А. В. Никонов a, *, Н. Б. Павздерин a, В. Р. Хрустов a
a Институт электрофизики УрО РАН
620016 Екатеринбург, ул. Амундсена, 106, Россия
* E-mail: nikonov@iep.uran.ru
Поступила в редакцию 15.07.2021
После доработки 12.08.2021
Принята к публикации 30.09.2021
- EDN: VNYGSJ
- DOI: 10.31857/S0424857022040120
Аннотация
В работе исследованы характеристики композитных катодов La0.6Sr0.4Co0.8Fe0.2O3 – δ–Ce0.73Gd0.27O3 – δ (LSCF–GDC), сформированных из нанопрошков стандартным методом, состоящим из смешивания исходных материалов и последующего припекания. Определено, что оптимальной температурой припекания электродов является 1100°С. При этом образования вторичных фаз в смеси LSCF и GDC (1 : 1) не обнаружено даже при 1400°С. Найдено, что характеристики LSCF–GDC-катодов падают с увеличением доли GDC. Определено, что введение нанопорошка GDC в композит ускоряет процесс спекания, что приводит к формированию более плотной структуры катодов и, как следствие, увеличению поляризационного сопротивления.
ВВЕДЕНИЕ
В настоящее время значительное внимание уделяется разработке среднетемпературных твердооксидных топливных элементов (ТОТЭ), что связано со снижением скорости деградации элементов при рабочих температурах 800–600°С и расширением выбора материалов. Однако при снижении рабочей температуры ТОТЭ падает скорость протекания реакции на электродах, а следовательно, и удельная мощность элемента. Поэтому важной задачей остается разработка высокоактивного катода, материал которого должен удовлетворять ряду требований: высокая электронная проводимость, химическая совместимость с электролитом, коэффициент термического расширения (КТР), близкий к КТР других компонентов ТОТЭ.
Одними из перспективнейших кандидатов на роль катода ТОТЭ считаются составы La1 ‒ xSrxFe1 –yCoyO3 (LSCF) [1]. Эти материалы со структурой перовскита обладают высокими смешанной ион-электронной проводимостью и каталитической активностью в реакции восстановления кислорода (см., например, [2–4]). Однако LSCF характеризуется высоким КТР, варьирующимся от 14 до 20 × 10–6 K–1 в зависимости от химического состава [1]. Признанной стратегией сближения КТР электрода и электролита, которая также улучшает электродные характеристики, за счет увеличения площади трехфазной границы, является создание композита [5]. Несмотря на то, что LSCF обладает смешанной проводимостью, и поэтому электродная реакция может протекать не только вблизи электролита, но и в объеме катода, формирование композитного катода с электролитами на основе CeO2, допированного Gd2O3 (GDC) или Sm2O3 (SmDC), приводит к снижению поляризационного сопротивления [6‒10]. В работе [6] поляризационное сопротивление чистого La0.6Sr0.4Co0.2Fe0.8O3 – δ-катода при 686°С было в ~3.5 раз выше, чем композитного катода, содержащего 36 об. % Ce0.9Gd0.1O2 – δ. Близкое отношение поляризационных сопротивлений (3.4 раза при 700°С) чистого La0.58Sr0.4Co0.2Fe0.8O3 – δ и композитного 60 вес. % La0.58Sr0.4Co0.2Fe0.8O3 – δ–40 вес. % Ce0.8Gd0.2O2 – δ катодов было продемонстрировано в [8]. Тогда как в работах [7] и [9] формирование композита с 50 вес. % GDC приводило к 10- и 7-кратному уменьшению поляризационного сопротивления по сравнению с исходным катодом La0.6Sr0.4Co0.2Fe0.8O3 – δ, соответственно. Расхождение литературных данных связано с различием в микроструктуре электродов, изготовленных разными методами, а также может быть вызвано как разницей в соотношении размеров зерен LSCF и GDC, так и собственно их размерами [11]. Дополнительным подходом к расширению трехфазной границы и, тем самым, снижению поляризационного сопротивления является переход к наноструктурным электродам [12]. Наиболее распространенным подходом создания катодов с “тонкой” структурой является метод пропитки (см., например, [13–15]).
В данной работе исследуется возможность создания высокоактивного композитного катода LSCF–GDC традиционным методом (механическое смешивание компонентов, нанесение и припекание) с использованием в качестве исходных материалов наноразмерных порошков.
ЭКСПЕРИМЕНТАЛЬНАЯ ЧАСТЬ
Наноразмерный порошок электролита Ce0.73Gd0.27O3 – δ (GDC) был получен методом лазерного испарения [16]. В качестве исходного катодного материала использовали порошок La0.6Sr0.4Co0.8Fe0.2O3 – δ (LSCF) производства Kceracell Co., Ltd. (Корея). Удельную поверхность порошков определяли методом BET с помощью TriStar 3000. Фазовый состав исследовали с помощью дифрактометра D8 DISCOVER на медном излучении (${\text{Cu}}{{K}_{{{{\alpha }_{{1,2}}}}}}$, λ = 1.542 Å) с графитовым монохроматором на дифрагированном луче.
Из исходных порошков были приготовлены пять композитов с различным весовым соотношением LSСF и GDC: 2 : 8, 4 : 6, 5 : 5, 6 : 4 и 8 : 2. В дальнейшем будем их обозначать как LС/C_X/Y, где X и Y – весовая доля LSСF и GDC соответственно. Для достижения гомогенности композитов порошки тщательно смешивали с использованием диспергатора УЗГ8-0.4/22 и гравитационного смесителя в течение 2 сут. Химическое взаимодействие между LSCF и GDC исследовали на составе LC/C_5/5. Образцы, спрессованные из композита, были спечены при трех температурах (1200, 1300 и 1400°С) с выдержкой на максимальной температуре 10 ч. Фазовые составы спеченных образцов LC/C_5/5, так же как исходных порошков, исследовали с помощью дифрактометра D8 DISCOVER.
Кинетику спекания материалов исследовали на образцах в виде дисков диаметром 8 мм и толщиной ~3 мм, спрессованных до относительной плотности ~0.5–0.6 с помощью одноосного гидравлического пресса ПРГ-1-20. Измерения были выполнены на дилатометре Dil 402C в воздушной атмосфере в диапазоне температур 20–1400°С. Скорость нагрева составляла 5°С/мин.
Для измерения проводимости композитов были спрессованы бруски прямоугольного сечения с характерными размерами 3 × 2 × 30 мм, которые спекали при 1250°С в течение 7 ч. На подготовленные образцы наносили зонды из платиновой проволоки. Для обеспечения хорошего электрического контакта зондов с образцом применяли платиновую пасту, которую припекали при 1000°С в течение 1 ч. Проводимость измеряли 4‑зондовым методом на постоянном токе в диапазоне температур 20–850°С с помощью потенциостата/гальваностата P-40X, совмещенного с модулем измерения импеданса (ООО “Electrochemical Instruments”, Россия).
Поляризационное сопротивление композитных катодов определяли на симметричных образцах электрод–электролит–электрод методом импедансной спектроскопии. Дисковые образцы электролита GDC плотностью не ниже 7 г/см3 были получены путем прессования и последующего спекания при температуре 1300°С (7 ч). Характерный диаметр и толщина дисковых образцов составляли 12 и 1 мм, соответственно. С двух сторон на образцы GDC методом окрашивания наносили исследуемые электроды диаметром 8 мм. Температуру припекания электродов к электролиту варьировали в диапазоне 1000–1200°С. Подготовленные симметричные образцы зажимали между платиновыми сетками с диаметром проволоки 0.03 мм (шаг плетения 0.25 мм). Спектры импеданса снимали при напряжении 15 мВ в диапазоне частот 0.3 МГц–0.1 Гц с помощью P-40X. Измерения проводили в застойном воздухе в диапазоне температур 850–650°С. Полученные спектры импеданса обрабатывали с помощью программы ZView.
Микроструктуру катодов исследовали с помощью сканирующего электронного микроскопа JEOL JSM-6390LA. Для анализа использовали слом образцов симметричных электрохимических ячеек электрод–электролит–электрод.
РЕЗУЛЬТАТЫ И ОБСУЖДЕНИЕ
Характеристики исходных порошков представлены в табл. 1. На рис. 1 представлены дифрактограммы исходных порошков LSCF, GDC и образцов LC/C_5/5, спеченных при различных температурах. В работе [17] не было найдено взаимодействия между катодным материалом La0.6Sr0.4Co0.8Fe0.2O3 – δ и электролитом Ce0.8Gd0.2O2 – δ после термической обработки при 1150°С в течение 3 ч. Рентгенофазовый анализ композитов LC/C_5/5, спеченных при температурах 1200, 1300 и 1400°С, показал наличие в их составе двух фаз со структурами типа флюорита и перовскита и не обнаружил образование каких-либо вторичных фаз. Однако следует обратить внимание, что параметры решетки составляющих композита (табл. 2) изменяются с ростом температуры спекания. Элементарная ячейка GDC увеличивается, тогда как для LSCF – уменьшается, что связывают с диффузией катионов из катодного материала в электролит [18]. Увеличение параметра решетки GDC, по-видимому, объясняется встраиванием катионов лантана и/или стронция в решетку флюорита. Тогда как встраивание кобальта и/или железа должно было привести к уменьшению элементарной ячейки GDC из-за их малых ионных радиусов. Тем не менее диффузия переходных металлов в структуру электролита возможна по границам зерен. В частности, в работе [19], где взаимодействие на границе между плотными образцами Ce0.8Gd0.2O2 – δ и La0.8Sr0.2Co1 –yFeyO3 – δ (y = 0, 0.2, 0.8 и 1) исследовалось методом масс-спектрометрии вторичных ионов, наблюдалось миграция большого количества стронция, кобальта и железа в электролит.
Таблица 1.
Характеристики исходных порошков
Порошок | SBET, м2/г | $\left\langle {{{d}_{{{\text{BET}}}}}} \right\rangle ,$ нм | Пространственная группа | Параметр решетки, Å | γXRD, г/см3 |
---|---|---|---|---|---|
GDC | 34.2 | 25 | Fm-3m | a = 5.424 | 7.25 |
LSСF | 11.8 | 82 | R-3c | a = 5.493, c = 13.453 | 6.23 |
Рис. 1.
Дифрактограммы порошков LSCF, GDC и композита LC/C_5/5, спеченного при температурах 1200, 1300 и 1400°С в течение 10 ч.
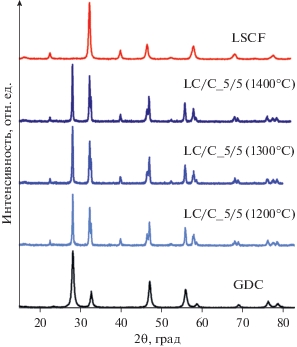
Таблица 2.
Данные РФА для компонентов композита LC/C_5/5 спеченного при различных температурах
Температура спекания | Параметр решетки, Å | |
---|---|---|
GDC | LSCF | |
1200 | a = 5.432 | a = 5.503, c = 13.400 |
1300 | a = 5.435 | a = 5.503, c = 13.405 |
1400 | a = 5.441 | a = 5.504, c = 13.437 |
На рис. 2 представлены кривые усадки образцов из исходных порошков и композитов на их основе. В табл. 3 приведены параметры, позволяющие количественно охарактеризовать процесс спекания. Температура начала спекания (T0) определена как температура, при которой усадка образца начинает преобладать над термическим расширением. Из табл. 3 видно, что T0 практически совпадают для GDC и композитов с содержанием GDC выше 50 вес. %. Дальнейшее уменьшение GDC в составе композита приводит к увеличению температуры начала спекания. Максимальная скорость усадки (Vmax) и температура ее реализации $({{T}_{{{{V}_{{{\text{max}}}}}}}})$ были определены при дифференцировании кривых усадки по времени d(ΔL/L0)/dt. Причем на кривых производных усадки для композитов LSСF–GDC с соотношением 5/5, 6/4 и 8/2 наблюдается два экстремума. Первый экстремум, при температуре около 980°С, совпадает с ${{T}_{{{{V}_{{{\text{max}}}}}}}}$ для других композитов и определяется, по-видимому, спеканием частиц электролита, хотя для чистого GDC максимальная скорость усадки реализуется на 100°С выше. Максимальной скоростью усадки, превосходящей Vmax исходных материалов характеризуются композиты LC/C_2/8 и LC/C_4/6. Тогда как Vmax композитов с высоким содержанием LSCF ниже, чем у исходных материалов. Температура окончания спекания (Tfin) композитов постепенно увеличивается с увеличением содержания LSCF. Таким образом, кинетика спекания композитов LC/C_8/2 и LC/C_6/4 определяется главным образом кинетикой спекания их основного компонента – LSCF. Тогда как композиты с содержанием GDC более 50 вес. % характеризуются лучшей спекаемостью, чем чистые LSCF и GDC. Снижение энергии активации диффузионных процессов на стыках частиц разнородных материалов во время спекания является единственным объяснением наблюдаемого поведения. По-видимому, уменьшение содержания LSCF в композитах (в исследованном диапазоне) ведет к увеличению контактов мелких частиц GDC с более крупными частицами LSCF и, следовательно, влияет на кинетику спекания.
Таблица 3.
Параметры спекания исследуемых материалов
Состав | T0, °C | ${{T}_{{{{V}_{{\max }}}}}},$ °C | Vmax (×10–3), мин–1 | Tfin, °C |
---|---|---|---|---|
GDC | 608 | 1078 | 2.9 | выше 1500 |
LC/С_2/8 | 600 | 979 | 7.5 | 1261 |
LC/C_4/6 | 592 | 963 | 4.0 | 1287 |
LC/C_5/5 | 600 | 975 | 3.1 | 1314 |
1085 | 2.8 | |||
LC/C_6/4 | 626 | 970 | 2.3 | 1343 |
1090 | 2.5 | |||
LC/C_8/2 | 668 | 980 | 2.3 | выше 1300 |
1150 | 2.5 | |||
LSCF | 697 | 1094 | 3.9 | 1352 |
На рис. 3 представлены температурные зависимости проводимости исследуемых материалов. Видно, что кривые проводимости как LSCF, так и композитов на его основе имеют экстремум в районе 600°С. Известно, что максимум проводимости материалов с перовскитной структурой связан с потерей кислорода при высоких температурах, что приводит к снижению концентрации и подвижности носителей электрического заряда [20]. Подобными температурными зависимостями проводимости характеризуются все составы ферро-кобальтитов лантана-стронция с различным соотношением компонентов [2, 20–26]. Однако, несмотря на одинаковую общую тенденцию, литературные данные значительно различаются как по значениям проводимости, так и по температуре, при которой достигается максимум проводимости для определенного состава. В работе [22] проводимость состава La0.6Sr0.4Co0.8Fe0.2O3 – δ, совпадающего с исследуемым в данной работе, слабо зависела от температуры в диапазоне 100–600°С с экстремумом вблизи 300°С, выше 600°С наблюдалось резкое падение проводимости. Уменьшение проводимости этого состава при увеличении температуры в высокотемпературной области (700–900°С) также подтверждается результатами работы [24]. Для более исследованного состава La0.6Sr0.4Co0.2Fe0.8O3 – δ были получены зависимости проводимости как с выраженными максимумом при температурах около 800°С [21], 650°С [23] и 500–600°C [2, 20], так и очень слабо зависящие от температуры с размытым экстремумом в диапазоне температур 400–600°С [25, 26]. При этом максимальное [25] и минимальное [26] литературные значения проводимости при 600°С отличаются в 2.3 раза.
Проводимость композитов уменьшается с увеличением содержания в их составе GDC, что связано со значительно меньшей проводимостью электролитного материала по отношению к LSCF. При 600°С проводимости LC/C_8/2, LC/C_6/4, LC/C_5/5, LC/C_4/6 и LC/C_2/8 меньше проводимости LSCF приблизительно в 1.5, 2.6, 4, 7 и 200 раз, соответственно. В работе [26] также наблюдалось снижение проводимости в 4 раза по отношению к чистому катодному материалу при формировании композита с равным весовым соотношением La0.6Sr0.4Co0.2Fe0.8O3 – δ и Ce0.8Sm0.2O1.9. Значительно более низкая проводимость LC/C_2/8 по сравнению с другими композитами объясняется тем, что содержание высокопроводящего компонента в его составе менее 30 об. %. Согласно теории перколяции [27], при таком малом содержании частицы LSCF не должны образовывать проводящих каналов. Наглядным примером этого поведения является зависимость проводимости Ni-керметов от их состава [28, 29]. При содержании Ni менее 30 об. % проводимость керметов становится практически равна проводимости электролитной составляющей. Однако проводимость композита LC/C_2/8 на два порядка превосходит проводимость электролитного материала GDC, что по-видимому, обусловлено смешанной ион-электронной проводимостью LSCF.
Оптимальная температура припекания катодов была определена на примере составов LSCF, LC/C_8/2 и LC/C_5/5. Для этого выбранные катодные материалы припекали при пяти различных температурах в диапазоне 1000–1200°С. Во всех случаях на температуре припекания образцы выдерживали в течение 1 ч. Было найдено, что оптимальная температура припекания катодов составляет 1100°С (рис. 4), поэтому все дальнейшие исследования были выполнены на электродах, припеченных при этой температуре. При более низких температурах припекания рост поляризационного сопротивления связан с ухудшением адгезии между катодным и электролитным материалами. Рост поляризационного сопротивления при температурах выше оптимальной обусловлен, по-видимому, формированием более плотной структуры. Как было показано выше, химического взаимодействия между LSCF и GDC, приводящего к формированию плохо проводящих фаз на границе раздела при температурах припекания и, следовательно, отрицательно влияющего на поляризационное сопротивление, не было обнаружено.
На рис. 5 представлены спектры импеданса композитных катодов, снятые при 800°С. Как видно из рис. 5а, композиты с содержанием GDC более 50 вес. % имеют большое поляризационное сопротивление, тогда как электроды с содержанием GDC 50 вес. % и менее имеют характеристики, близкие к LSCF (рис. 5б). Это явление можно объяснить с помощью модели амбиполярного сопротивления пористого композитного катода, предложенной в [6]. При высоком содержании GDC частицы LSCF не могут формировать протяженные электронпроводящие каналы. Пористая структура катода дополнительно “укорачивает” каналы проводимости. Это приводит к резкому увеличению поляризационного сопротивления из-за, во-первых, высокого омического сопротивления пористого композитного катода и, во-вторых, высокого контактного сопротивления границы катод/электролит. Литературные данные о влиянии состава композита на поляризационное сопротивление имеют достаточно большой разброс. В работе [6] резкий рост поляризационного сопротивление композита La0.6Sr0.4Co0.2Fe0.8O3 – δ–Ce0.9Gd0.1O2 – δ наблюдался при содержании электролита 40 об. %, в работе [7] для композита La0.6Sr0.4Co0.2Fe0.8O3 – δ–Ce0.8Gd0.2O3 – δ – при 60 вес. %, а в работе [9] для композита La0.6Sr0.4Co0.2Fe0.8O3 – δ–Ce0.9Gd0.1O2 – δ – при 70 вес. %. Несовпадение данных может быть следствием как различных соотношений размеров частиц LSCF и GDC, так и величин пористости исследуемых электродов. В дальнейшем электроды LC/C_4/6 и LC/C_2/8 рассматривать не будем.
Спектры импеданса электродов с содержанием GDC менее 50 вес. % состоят из трех полуокружностей (рис. 5б), каждая из которых является отражением определенного электрохимического процесса. Далее процессы в соответствии с их разделением по частотам будем обозначать: высокочастотный (HF), среднечастотный (MF) и низкочастотный (LF). Анализ спектров импеданса проводили по эквивалентной схеме (вставка на рис. 5б), состоящей из последовательно соединенных сопротивления Rs и элементов (RQ). Сопротивление Rs соответствует омическим потерям и в основном определяется сопротивлением электролита. Каждый элементы (RQ), состоящий из параллельно соединенных сопротивления R и элемента постоянной фазы Q, соответствует определенному электрохимическому процессу. Значения параметров эквивалентной цепи, полученные при обсчете спектров импеданса, были использованы для определения частот релаксаций f и емкости С каждого процесса в соответствии со следующими уравнениями:
(2)
$C = {{R}^{{{{\left( {1 - n} \right)} \mathord{\left/ {\vphantom {{\left( {1 - n} \right)} n}} \right. \kern-0em} n}}}}{{Q}^{{{1 \mathord{\left/ {\vphantom {1 n}} \right. \kern-0em} n}}}}.$На рис. 6 представлены температурные зависимости f, C, и составляющих поляризационного сопротивления (Rη-HF, Rη-MF, Rη-LF). Величина удельного сопротивления каждого электрохимического процесса была рассчитана путем умножения значения соответствующего R, найденного из спектров импеданса, на площадь электрода и делением пополам, так как измерения проводили на симметричных ячейках. Частоты релаксации HF- и MF-процессов имеют стандартную аррениусовскую зависимость, тогда как частоты релаксации LF-процесса слабо зависят от температуры. При этом частоты fHF и fMF для катодов LSCF и LC/C_8/2 значительно отличаются, поэтому высоко- и среднечастотные процессы ясно разделяются на спектрах импеданса. Увеличение содержания GDC в составе композита ведет к сближению частот fHF и fMF и перекрытию высоко- и среднечастотного процессов. Так для катода LC/C_6/4 HF- и MF-процессы разделяются, хотя и не столь однозначно как для LSCF и LC/C_8/2, тогда как для LC/C_5/5 разделить эти два процесса не представляется возможным. Поэтому в спектре LC/C_5/5 выделены только две части (высокочастотная и низкочастотная), понимая, что высокочастотная часть должна состоять из двух процессов с близкими частотами релаксации. Наибольшей емкостью для всех исследованных катодов характеризуется низкочастотный процесс (0.6–6 Ф/см2). Емкость среднечастотного процесса для LSCF и LC/C_8/2 составляет 0.25–1.4 Ф/см2, тогда как для LC/C_6/4 – порядка 15 мФ/см2. Емкости HF-процесса для всех составов варьировалось в диапазоне 0.35–10 мФ/см2. Хотя и здесь емкость для состава LC/C_6/4 меньше, чем для LSCF и LC/C_8/2.
Рис. 6.
Температурные зависимости: (а) частот релаксации, (б) емкостей и (в) сопротивлений поляризации для высоко- (HF), средне- (MF) и низкочастотных (LF) вкладов в общую поляризацию исследуемых катодов.
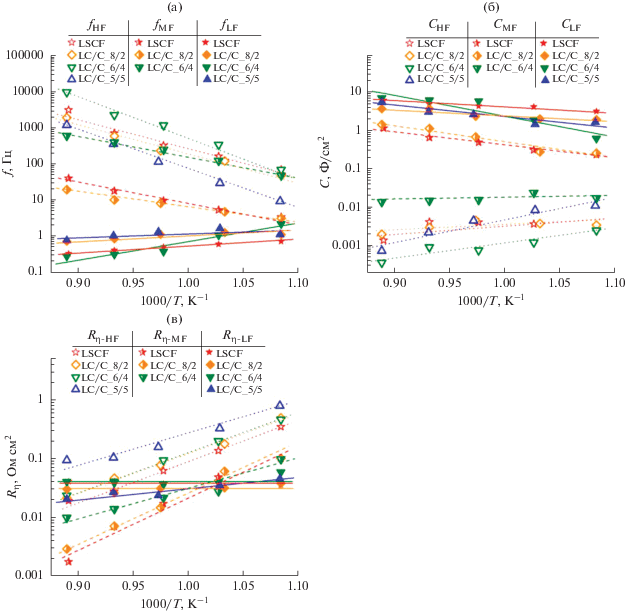
Чаще всего в литературе в спектрах импеданса для катода со смешанной ион-электронной проводимостью выделяют две части: высокочастотная и среднечастотная (по терминологии, принятой в данной статье). Высокочастотная часть, характеризующаяся емкостями единицы мФ/см2 [30] и частотами 0.4–10 кГц [30, 31], соответствует процессу переноса заряда через границу электрод/электролит. Среднечастотная часть (емкость 15–100 мФ/см2, частоты 10–300 Гц при 750°С [30, 31]) интерпретируется как процессы, происходящие на границе катодный материал/газ (адсорбция–десорбция кислорода, диссоциация кислорода, диффузия по поверхности и связь этих процессов). Низкочастотная часть спектров импеданса, представленных на рис. 5, наиболее вероятно связана с процессами массопереноса, такими как диффузия газа в порах электродов [32]. Это предположение подтверждается тем, что сопротивление низкочастотной части (Rη-LF), варьирующееся в диапазоне 0.02–0.06 Ом см2 для всех электродов, практически не зависит от температуры (рис. 6в).
Микрофотографии слома электродов, припеченных при оптимальной температуре, представлены на рис. 7. Видно, что исследованные электроды имеют хороший контакт с электролитом. В структуре электродов наблюдается две фракции пор: мелкие регулярные поры и отдельные крупные каверны. Оценка размеров пор и величины пористости электродов по микрофотографиям была проведена с помощью программы ImageJ. Величина пористости, сформированной мелкими порами, для электродов LSCF, LC/C_8/2 и LC/C_5/5 составляет около 26, 17 и 15% соответственно. При этом размер регулярных пор для LSCF варьировался в диапазоне 0.3–0.6 мкм, для LC/C_8/2 – 0.3–0.4 мкм, а для LC/C_5/5 – 0.2–0.4 мкм. Наличие крупных каверн (размером десятки мкм) оказывает большее влияние на пористость более плотных электродов. Полная пористость электродов LSCF, LC/C_8/2 и LC/C_5/5 составляет около 28, 23 и 22% соответственно. Таким образом, наноразмерный порошок GDC в составе композитного катода приводит к формированию более плотной микроструктуры электрода, характеризующейся порами меньшего размера. Однако, как показал анализ спектров импеданса, наблюдаемые различия микроструктуры электродов не влияют на газовую диффузию в условиях проведенных измерений.
Рис. 7.
СЭМ-изображения изломов границы катод/электролит с электродами: LSCF (а, б), LC/C_8/2 (в, г) и LC/C_5/5 (д, е).
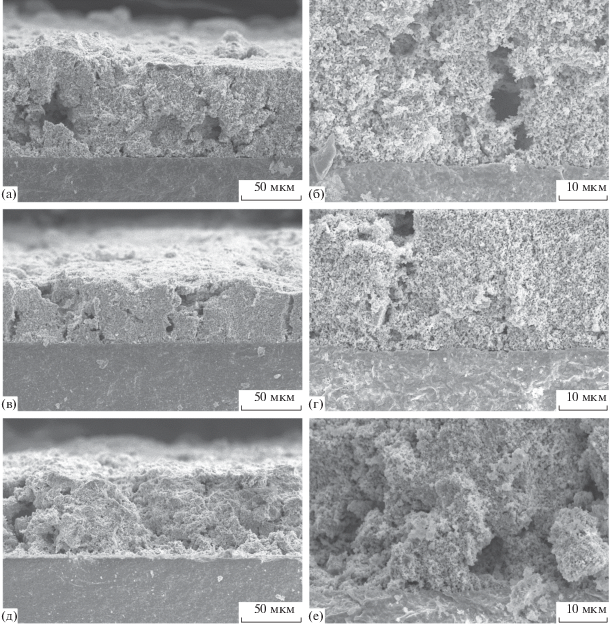
Из рис. 6в видно, что наибольший вклад в поляризационное сопротивление исследуемых электродов вносит высокочастотный процесс (Rη-HF), тогда как среднечастотный процесс (Rη-MF) вносит небольшой вклад, особенно при высоких температурах. Частоты релаксации высоко- и среднечастотного процессов для LSFC ниже, чем частоты для композита LC/C_6/4 (рис. 6а). Это указывает на то, что введение GDC в состав катода приводит к уменьшению времени релаксации процессов, происходящих как на границе катод/электролит, так и катод/газ. Однако сопротивления Rη-HF и Rη-MF растут с увеличением содержания GDC. По-видимому, этот эффект объясняется уменьшением области протекания соответствующих реакций из-за формирования более плотной структуры композитных электродов. Косвенно данный вывод подтверждается меньшими значениями емкости HF- и MF-процессов для LC/C_6/4 по сравнению с LSCF (рис. 6б), так как в работах [33, 34] было показано, что емкость выше для катодов с более протяженной трехфазной границей.
На рис. 8 представлены температурные зависимости полного поляризационного сопротивления исследуемых катодов. Видно, что хотя композитные электроды с содержанием GDC 20 и 40 вес. % при температурах 750–850°С имеют поляризационные сопротивления, близкие к LSCF, наблюдается тенденция к ухудшению характеристик электродов с увеличением доли GDC в их составе. В табл. 4 представлены данные по поляризационному сопротивлению исследованных катодов при 700°С в сравнении с литературными данными [35–39]. Видно, что характеристики катодов La0.6Sr0.4Co0.8Fe0.2O3 – δ, изготовленныx разными методами, существенно различаются. Связано это с формированием различной микроструктуры электродов. В частности, в работе [39] путем варьирования параметров электрораспылительного осаждения (electrospray deposition) были получены электроды как с кораллоподобной пористой структурой, так и плотной структурой с макротрещинами, поляризационное сопротивление которых отличалось в 2 раза (см. табл. 4). Как упоминалось выше [6–9], композитные электроды, сформированные из микронных порошков, имеют лучшие характеристики, чем чистый LSCF. Изготовление катодов из агломератов, состоящих из наночастиц электродного и электролитного материалов, полученных методами золь–гель [40] или спрейпиролиза [41], также приводит к низким поляризационным сопротивлениям. Однако, как показано в данной работе, стандартная методика изготовления композитных электродов, состоящая из смешивания исходных материалов и последующего припекания, при использовании нанопорошков не позволяет расширить трехфазную границу за счет формирования тонкой микроструктуры. Интенсивное спекание нанопорошков приводит к формированию более плотной структуры электродов и, следовательно, ухудшению их характеристик.
Таблица 4.
Поляризационное сопротивление катодов на основе La0.6Sr0.4Co0.8Fe0.2O3 – δ при 700°С
Электрод | Электролит | Rη, Ом см2 | Ссылка |
---|---|---|---|
LSCF | GDC | 0.22 | Данная работа |
LC/C_8/2 | GDC | 0.27 | Данная работа |
LC/C_6/4 | GDC | 0.27 | Данная работа |
LC/C_5/5 | GDC | 0.37 | Данная работа |
La0.6Sr0.4Co0.8Fe0.2O3 – δ | GDC | 0.15 | [35] |
La0.6Sr0.4Co0.8Fe0.2O3 – δ | SmDC | 2.1 | [36] |
La0.6Sr0.4Co0.8Fe0.2O3 – δ | LaSDC | 0.14 | [37] |
La0.6Sr0.4Co0.8Fe0.2O3 – δ | GDC | 0.1 | [38] |
La0.6Sr0.4Co0.8Fe0.2O3 – δ | GDC | 0.82 | [39] |
La0.6Sr0.4Co0.8Fe0.2O3 – δ | GDC | 1.63 | [39] |
ЗАКЛЮЧЕНИЕ
В работе проведено исследование влияния состава композитного катода La0.6Sr0.4Co0.8Fe0.2O3 – δ–Ce0.73Gd0.27O3 – δ (LSCF–GDC), изготовленного с использованием наноразмерного порошка GDC, на его характеристики. Не обнаружено формирования вторичных фаз в композите при термической обработке до 1400°С включительно. Проводимость композитов закономерно падала с увеличением содержания GDC в их составе, что связано со значительно меньшей проводимостью электролитного материала по отношению к LSCF. Вопреки ожиданиям, чистый LSCF-катод обладает лучшими характеристиками, чем композитные катоды на его основе, поляризационное сопротивление которых росло с увеличением содержания GDC. Причина полученной зависимости кроется в интенсификации процесса спекания катода при введении в его состав нанопорошка GDC, что приводит к формированию более плотной структуры электрода и уменьшению зоны протекания электродной реакции.
Список литературы
Jiang, S.P., Development of lanthanum strontium cobalt ferrite perovskite electrodes of solid oxide fuel cells – A review, Int. J. Hydrogen Energy, 2019, vol. 44, p. 7448.
Stevenson, J.W., Armstrong, I.R., Carneim, R.D., et al., Electrochemical properties of mixed conducting perovskites La1 –xMxCo1 –yFeyO3 – δ (M = Sr, Ba, Ca), J. Electrochem. Soc., 1996, vol. 143, p. 2722.
Ананьев, М.В., Курумчин, Э.Х., Поротникова, Н.М. Влияние кислородной нестехиометрии на кинетику обмена и диффузию кислорода в кобальтитах лантана–стронция. Электрохимия. 2010. Т. 46. С. 840. [Ananyev, M.V., Kurumchin, E.Kh., and Porotnikova, N.M., Effect of oxygen nonstoichiometry on kinetics of oxygen exchange and diffusion in lanthanum–strontium cobaltites, Russ. J. Electrochem., 2010, vol. 46, p. 789.]
Wang, Z., Peng, R., Zhang, W., et al., Oxygen reduction and transport on the La1 –xSrxCo1 –yFeyO3 – δ cathode in solid oxide fuel cells: a first-principles study, J. Mater. Chem. A, 2013, vol. 1(41), p. 12932.
Aziz, A.J.A., Baharuddin, N.A., Somalu, M.R., and Muchtar, A., Review of composite cathodes for intermediate-temperature solid oxide fuel cell applications, Ceram. Int., 2020, vol. 46, p. 23314.
Dusastre, V. and Kilner, J.A., Optimisation of composite cathodes for intermediate temperature SOFC applications, Solid State Ionics, 1999, vol. 126, p. 163.
Murray, E.P., Sever, M.J., and Barnett, S.A., Electrochemical performance of (La,Sr)(Co,Fe)O3–(Ce,Gd)O2 composite cathodes, Solid State Ionics, 2002, vol. 148, p. 27.
Qiang, F., Sun, K.N., Zhang, N.Q., Zhu, X.D., et al., Characterization of electrical properties of GDC doped A-site deficient LSCF based composite cathode using impedance spectroscopy, J. Power Source, 2007, vol. 168, p. 338.
Leng, Y., Chan, S.H., and Liu, Q., Development of LSCF–GDC composite cathodes for low-temperature solid oxide fuel cells with thin film GDC electrolyte, Int. J. Hydrogen Energy, 2008, vol. 33, p. 3808.
Baharuddin, N.A., Rahman, H.A., Muchtar, A., et al., Development of lanthanum strontium cobalt ferrite composite cathodes for intermediate- to low-temperature solid oxide fuel cells, J. Zhejiang Univ.-Sci. A (Appl. Phys. & Eng.), 2013, vol. 14, p. 11.
Chen, X.J., Chan, S.H., and Khor, K.A., Simulation of a composite cathode in solid oxide fuel cells, Electrochim. Acta, 2004, vol. 49, p. 1851.
Sun, C., Hui, R., and Roller, J., Cathode materials for solid oxide fuel cells: a review, J. Solid State Electrochem., 2010, vol. 14, p. 1125.
Zhao, E., Jia, Z., Zhao, L., Xiong, Y., et al., One dimensional La0.8Sr0.2Co0.2Fe0.8O3 – δ/Ce0.8Gd0.2O1.9 nanocomposite cathodes for intermediate temperature solid oxide fuel cells, J. Power Sources, 2012, vol. 219, p. 133.
Burye, T.E. and Nicholas, J.D., Improving La0.6Sr0.4Co0.8Fe0.2O3 – δ infiltrated solid oxide fuel cell cathode performance through precursor solution desiccation, J. Power Sources, 2015, vol. 276, p. 54.
Sindirac, C., Buyukaksoy, A., and Akkurt, S., Electrochemical performance of La0.6Sr0.4Co0.2Fe0.8O3–Ce0.9Gd0.1O2 – δ composite SOFC cathodes fabricated by electrocatalyst and/or electrocatalyst-ionic conductor infiltration, J. Sol–Gel Sci. Technol., 2019, vol. 92, p. 45.
Ivanov, M., Osipov, V., Kotov, Yu., et al., Laser synthesis of oxide nanopowders, Advances in Science and Technology, 2006, vol. 45, p. 291.
Wang, S., Kato, T., Nagata, S., et al., Performance of a La0.6Sr0.4Co0.8Fe0.2O3–Ce0.8Gd0.2O1.9–Ag cathode for ceria electrolyte SOFCs, Solid State Ionics, 2002, vol. 146, p. 203.
Khan, M.Z., Song, R.-H., Mehran, M.T., Lee, S.-B., and Lim, T.-H., Controlling cation migration and inter-diffusion across cathode/interlayer/electrolyte interfaces of solid oxide fuel cells: A review, Ceram. Int., 2021, vol. 47, p. 5839.
Sakai, N., Kishimoto, H., Yamaji, K., et al., Degradation behavior at interface of LSCF cathodes and rare earth doped ceria, ECS Trans, 2007, vol. 7, p. 389.
Tai, L.-W., Nasrallah, M.M., Anderson, H.U., et al., Structure and electrical properties of La1 –xSrxCo1 –yFeyO3. Part 2. The system La1 –xSrxCo0.2Fe0.8O3, Solid State Ionics, 1995, vol. 76, p. 273.
Mineshige, A., Izutsu, J., Nakamura, M., Nigaki, K., et al., Electrical property, crystal structure and oxygen nonstoichiometry of La1 –xSrxCo0.2Fe0.8O3 – δ, Electrochemistry, 2000, vol.68, p. 515.
Wang, S., Katsuki, M., Dokiya, M., and Hashimoto, T., High temperature properties of La0.6Sr0.4Co0.8Fe0.2O3 – δ phase structure and electrical conductivity, Solid State Ionics, 2003, vol. 159, p. 71.
Xu, Q., Huang, D., Chen, W., Zhang, F., and Wang, B., Structure, electrical conducting and thermal expansion properties of Ln0.6Sr0.4Co0.2Fe0.8O3 (Ln = La, Pr, Nd, Sm) perovskite-type complex oxides, J. Alloy Compd., 2007, vol. 429, p. 34.
Orikasa, Y., Ina, T., Nakao, T., Mineshige, A., et al., An X-ray absorption spectroscopic study on mixed conductive La0.6Sr0.4Co0.8Fe0.2O3 – δ cathodes. I. Electrical conductivity and electronic structure, Phys. Chem. Chem. Phys., 2011, vol. 13, p. 16637.
Araki, W., Arai, Y., and Malzbender, J., Transitions of Ba0.5Sr0.5Co0.8Fe0.2O3 – δ and La0.58Sr0.4Co0.2Fe0.8O3 – δ, Mater. Lett., 2014, vol. 132, p. 295.
Ali, S.A.M., Anwar, M., Ashikin, N., et al., Influence of oxygen ion enrichment on optical, mechanical, and electrical properties of LSCF perovskite nanocomposite, Ceram. Int., 2018, vol. 44, p. 10433.
Strauffer, D. and Aharony, A., Introduction to percolation theory, London: Taylor & Francis Ltd., 1994, 181 p.
Dees, D.W., Claar, T.D., Easier, T.E., Fee, D.C., and Vlrazek, F.C., Conductivity of porous Ni/ZrO2–Y2O3 cermets, J. Electrochem. Soc., 1987, vol. 134, p. 2141.
Спирин, А.В., Никонов, А.В., Липилин, А.С., и др. Влияние структурных параметров компонентов кермета Ni-ScSZ на характеристики анода твердооксидного топливного элемента на его основе. Электрохимия. 2016. Т. 52. С. 688. [Spirin, A.V., Nikonov, A.V., Lipilin, A.S., et al., Effect of structural parameters of Ni-ScSZ cermet components on the SOFC anodes characteristics, Russ. J. Electrochem., 2016, vol. 52, p. 613.]
Santos-Gómez, L., Porras-Vázquez, J.M., Losilla, E.R., et al., LSCF-CGO nanocomposite cathodes deposited in a single step by spray pyrolysis, J. Eur. Ceram. Soc., 2018, vol. 38, p. 1647.
Chen, Y., Bu, Y., Zhang, Y., Yan, R., Ding, D., et al., A highly efficient and robust nanofiber cathode for solid oxide fuel cells, Adv. Energy Mater., 2017, vol. 7(6), p. 1601890.
Kim, J.-D., Kim, G.-D., Moon, J.-W., Park, Y., et al., Characterization of LSM–YSZ composite electrode by ac impedance spectroscopy, Solid State Ionics, 2001, vol. 143, p. 379.
Wu, L., Jiang, Z., Wang, S., and Xia, C., (La,Sr)MnO3–(Y,Bi)2O3 composite cathodes for intermediate-temperature solid oxide fuel cells, Int. J. Hydrogen Energ., 2013, vol. 38, p. 2398.
Santos-Gómez, L., Losilla, E.R., Martin, F., et al., Novel microstructural strategies to enhance the electrochemical performance of La0.8Sr0.2MnO3 – δ cathodes, ACS Appl. Mater. Interfaces, 2015, vol. 7, p. 7197.
Dumaisnil, K., Fasquelle, D., Mascot, M., Rolle, A., et al., Synthesis and characterization of La0.6Sr0.4Co0.8Fe0.2O3 films for solid oxide fuel cell cathodes, Thin Solid Films, 2014, vol. 553, p. 89.
Mosialek, M., Kędra, A., Krzan, M., et al., Ba0.5Sr0.5Co0.8Fe0.2O3 – δ–La0.6Sr0.4Co0.8Fe0.2O3 – δ composite cathode for solid oxide fuel cell, Arch. Metall. Mater., 2016, vol. 61(3), p. 1483.
Matera, A., Fasquelle, D., Kahlaoui, M., et al., Synthesis, characterization, and electrochemical properties of bilayered cathode films deposited on co-doped ceria, Chin. J. Phys., 2017, vol. 55, p. 2577.
Wang, H., Zhang, X., Zhang, W., Wei, Z., et al., Enhancing catalysis activity of La0.6Sr0.4Co0.8Fe0.2O3 – δ cathode for solid oxide fuel cell by a facile and efficient impregnation process, Int. J. Hydrog. Energy, 2019, vol. 44, p. 13757.
Sindirac, C. and Akkurt, S., Microstructural investigation of the effect of electrospraying parameters on LSCF films, Int. J. Hydrog. Energy, 2020, vol. 45, p. 35139.
Joh, D.W., Cha, A., Park, J.H., Kim, K.J., et al., In situ synthesized La0.6Sr0.4Co0.2Fe0.8O3 – δ–Gd0.1Ce0.9O1.95 nanocomposite cathodes via a modified sol–gel process for intermediate temperature solid oxide fuel cells, ACS Appl. Nano Mater., 2018, vol. 1(6), p. 2934.
Shimada, H., Sumi, H., Yamaguchi, Y., and Fujishiro, Y., High-performance Gd0.5Sr0.5CoO3 – δ and Ce0.8Gd0.2O1.9 nanocomposite cathode for achieving high power density in solid oxide fuel cells, Electrochim. Acta, 2021, vol. 368, p. 137679.
Дополнительные материалы отсутствуют.