Электрохимия, 2022, T. 58, № 7, стр. 401-407
Послойное формирование композитного анода NiO/CGO для ТОТЭ струйной 3D-печатью в комбинации с лазерной обработкой
А. С. Багишев a, И. М. Мальбахова a, *, А. М. Воробьев a, Т. А. Борисенко a, А. Д. Асмедьянова a, b, А. И. Титков a, А. П. Немудрый a
a Институт химии твердого тела и механохимии СО РАН
Новосибирск, Россия
b Новосибирский государственный университет
Новосибирск, Россия
* E-mail: malbakhova.inna@yandex.ru
Поступила в редакцию 20.12.2021
После доработки 01.02.2022
Принята к публикации 14.02.2022
- EDN: TWTULH
- DOI: 10.31857/S0424857022070040
Аннотация
В данной работе был разработан состав пасты для печати ТОТЭ-анода на основе наноразмерных оксида никеля и оксида церия, стабилизированного оксидом гадолиния, для струйной 3D-печати с последующим лазерным и термическим спеканием. Были определены параметры анодной пасты, такие как распределение частиц по размерам, вязкость. Была произведена печать образца анода для ТОТЭ с помощью лабораторного 3D-принтера, оборудованного дозирующей системой для струйной печати и модулем для лазерной обработки. Проведены эксперименты по печати трехмерных тестовых объектов с использованием разработанной керамической пасты. Полученные образцы были изучены комплексом физико-химических методов для определения морфологических и структурных характеристик.
ВВЕДЕНИЕ
Ввиду истощения традиционных энергоресурсов и их растущей стоимости, с каждым годом все сильнее возрастает потребность в альтернативных источниках энергии и энергоустановках на их основе, обеспечивающих сокращение выброса углерода в окружающую среду. Водород и топливные элементы (ТЭ), преобразующие химическую энергию в электричество, были признаны перспективной технологией в будущей энергетической инфраструктуре. Прямое преобразование энергии с помощью топливных элементов обладает такими преимуществами, как более высокий КПД и низкий уровень выбросов по сравнению с классическими процессами сжигания топлива [1]. Существуют различные типы ТЭ, которые могут быть использованы в широком спектре приложений от портативных устройств небольшого размера до стационарных источников питания. В настоящее время одними из наиболее распространенных типов ТЭ являются твердооксидные топливные элементы (ТОТЭ), которые используются в крупномасштабных стационарных приложениях из-за высокой эффективности использования электроэнергии, высокой устойчивости к загрязнениям, большой вариативности в выборе топлива [2]. Одним из ключевых факторов, ограничивающих текущее развитие ТОТЭ, является технологическая сложность производства. Производство ТОТЭ является многостадийным процессом, что требует больших временных и денежных затрат и не обеспечивает должной воспроизводимости [2]. Кроме того, точные геометрические размеры и сложная микроструктура, которая требуется для обеспечения высоких электрохимических характеристик, а также большая удельная поверхность, необходимая для увеличения массопереноса и минимизации различных поляризационных потерь, не могут быть получены классическими методами изготовления ТОТЭ, такими как литье и экструзия. Таким образом, разработка новых подходов для изготовления ТОТЭ, обеспечивающих сокращение числа производственных стадий, снижающих денежные и временные затраты, и вместе с тем предоставляющих гибкость архитектуры и микроструктуры готового изделия, является актуальной задачей [1].
С ростом спроса на рынке и технологического развития промышленности аддитивные технологии (АТ) активно начали применяться в таких областях, как строительство, медицина и энергетика [6], а в последнее десятилетие – для производства керамических изделий, в том числе элементов ТОТЭ [3]. Данный класс производственных технологий позволяет производить сложные трехмерные структуры, которые либо трудно, либо невозможно изготовить с использованием традиционных подходов, таких как экструзия и литье [4, 5].
Уникальные возможности 3D-печати, такие как высокая автоматизация процесса, низкие потери материала в процессе изготовления, возможность программируемого изготовления деталей со сложной иерархичной структурой, позволяют значительно облегчить как технологический процесс изготовления ТОТЭ, так и улучшить эксплуатационные и мощностные характеристики топливных элементов. В настоящее время методы 3D-печати, применяемые для получения керамических изделий, включают построение изделия методом послойного наплавления расплавленной композитной нити (FDM), селективное лазерное спекание/плавление (SLS/SLM), стереолитографию (SLA) и другие [2]. Работы по 3D-печати ТОТЭ в основном посвящены формированию электролит-поддерживаемых топливных элементов и, в частности, печати самого электролита. Так, в работе [2] внимание уделяется получению плотного электролита из оксида циркония (8YSZ), стабилизированного оксидом иттрия (8 мол. %), с помощью технологии 3D-печати, основанной на послойной цифровой обработке светом ванны фотополимера, содержащего керамический наполнитель. Электрохимические характеристики симметричной ячейки Ag–GDC/YSZ/Ag–GDC с напечатанным электролитом сравнимы с аналогичной ячейкой, полученной методом сухого прессования. Lomberg и др. [7] изготовили ТОТЭ методом многостадийной печати. Изначально методом SLS изготавливался несущий электролит из оксида циркония (8YSZ), стабилизированного оксидом иттрия (8 мол. %). На полученный электролит методом струйной печати с последующей лазерной постобработкой тонкими полосками был нанесен никелевый анод.
Несмотря на то, что существует достаточное количество работ, посвященных печати электролит-несущего ТОТЭ, в литературе почти не представлено работ по 3D-формированию анод-несущего ТОТЭ. При этом, в настоящий момент при разработке конкурентоспособных ТОТЭ предпочтение отдается анод-несущим топливным элементам ввиду низких омических потерь, связанных с толщиной электролита, что позволяет снизить рабочую температуру и повысить производительность. Более низкая рабочая температура значительно снижает деградацию (связанную с коррозией вспомогательного оборудования для доставки реагентов и неблагоприятным воздействием на ячейку), тем самым увеличивая срок службы топливного элемента [8].
В данной работе было проведено послойное формирование несущего анода методом прямой струйной печати (DIW) с последующей селективной лазерной обработкой, интегрированной в 3D-принтер. Прямая струйная печать – это метод, основанный на капельном инжектировании дозирующей головкой суспензий или чернил для последовательного формирования единичного слоя или послойном формировании трехмерного объекта [4]. В качестве материала для изготовления анода в работе использовали композит NiO/CGO. Оксид церия, допированный оксидом гадолиния (CGO), отличается высокой проводимостью и стабильностью к CO2 и H2O, и поэтому признан ведущим электролитным материалом для использования в средне- и низкотемпературных ТОТЭ [9]. Использование кермета на основе никеля (который возникает во время эксплуатации ТОТЭ при восстановлении NiО) и CGO позволяет достичь достаточной электронной проводимости для избегания электрических потерь. Кроме того, введение CGO предотвращает спекание частиц Ni и позволяет выравнивать коэффициент теплового расширения между анодным и электролитным слоями [10]. Согласно литературным данным [10], оптимальным соотношением фаз в керамике NiO/CGO является 60/40 мас. %.
ЭКСПЕРИМЕНТАЛЬНАЯ ЧАСТЬ
Материалы для пасты
Для синтеза композитных материалов использовали оксид никеля(II) (SOFCMAN, Китай, ≥99.5%), оксид церия, стабилизированный оксидом гадолиния 10 мол. % CGO10 (SOFCMAN, Китай, ≥99.5%), терпинеол (Aldrich, США, ≥97%), полимер VariPlus (Evonik Operations GmbH, Германия), дибутилфталат DBF (ОАО “Лакокраска”, ГОСТ 8728–88 с изм. № 1).
Методика получения пасты для печати
Для получения композитного материала NiO/CGO проводили предварительное измельчение оксида никеля(II) и CGO в лабораторной погружной бисерной мельнице (APS, Германия) с использованием мелющих тел из оксида циркония, стабилизированного оксидом иттрия YSZ8 (dшаров = 1.2 мм). Измельчение проводилось в этаноле, объемное соотношение NiO : спирт : шары равно 1 : 1.5 : 2. Полученный порошок высушивался в сушильном шкафу при температуре 100°С до полного высыхания.
Для приготовления пасты VariPlus и DBF растворяли в терпинеоле и помещали в бисерную мельницу с мелющими телами (диаметр 1.2 мм), затем порошки NiO и CGO (60/40 мас. %) добавляли и диспергировали при скорости вращении ротора мельницы 4000 об/мин в течение 2 ч, затем пасту отделяли от мелющих тел.
Аппаратура и физические методы исследования
Для печати использовался лабораторный 3D‑принтер, изготовленный по индивидуальному заказу. Принтер является гибридным и сочетает в себе возможность использования различных систем дозирования низковязких и высоковязких композиций для прямой струйной печати различных материалов и систему лазерной обработки на основе волоконного лазера, что позволяет проводить обработку каждого слоя. Все эксперименты по печати проводили с использованием пневматического дозирующего клапана с соплом диаметром 0.25 мм (Nordson Corporation, Германия–США). Лазерное спекание напечатанных слоев с помощью волоконного лазера, работающего на длине волны 1.064 мкм в импульсно-периодическом режиме, проводилось в однопроходном режиме с изменяемой мощностью лазера. Длительность и частота лазерного импульса составляли 4 нс и 250 кГц, соответственно; средняя мощность изменялась в диапазоне 0.45–2.7 Вт.
Рентгенограммы (РФА) полученных образцов регистрировались на порошковом дифрактометре D8 Advance (Bruker, Германия) с CuКα-излучением при регистрации одномерным детектором Lynx–Eye с никелевым фильтром, шаг сканирования 0.02°, время накопления в точке 35.4 с. Исследование образцов методом сканирующей электронной микроскопии (СЭМ) проводили с использованием сканирующего электронного микроскопа Hitachi 3400 N (Hitachi Ltd., Япония). Вязкость паст измеряли с помощью вискозиметра Brookfield DV3T-RV (Brookfield Engineering Labs Inc., США) в геометрии конус/пластина при 25°C. Для анализа гранулометрического состава использовали лазерный анализатор частиц Microsizer 201 (Microsizer, Россия). Для измерения пикнометрической плотности твердых образцов использовали газовый пикнометр UltraPyc 3000 (Anton Paar, Австрия), в качестве инертного газа-измерителя объема образца использовали гелий. Пористость рассчитывалась путем сравнения пикнометрической плотности со значением теоретической плотности композита NiO/CGO, равной 6.67 г/см3. Для определения оптимальных параметров спекания использовали прибор синхронного термического анализа STA 449 F1 Jupiter (NETZSCH, Германия). Нагрев напечатанного образца осуществлялся в атмосфере 0.2O2–0.8Ar со скоростью 5°С/мин до температуры 1000°С.
РЕЗУЛЬТАТЫ И ОБСУЖДЕНИЕ
Проведен подбор оптимального времени измельчения порошка оксида никеля(II) и CGO в бисерной мельнице. На рис. 1 представлены распределения частиц по размерам для исходных частиц CGO и NiO (1) и частиц CGO и NiO после измельчения (2). Как видно из гистограмм, исходный порошок CGO имеет мономодальное распределение по размерам, в то время как исходный порошок NiO имеет бимодальное распределение по размерам с двумя максимумами при 23 и 33 мкм. Процентильные значения частиц в зависимости от размера для исходных и измельченных NiO и CGO указаны в табл. 1. После обработки в бисерной мельнице распределения по размерам для обоих порошков стали мономодальными, гистограммы значительно смещены влево, что указывает на хорошую степень измельчения (рис. 1а, 1б).
Таблица 1.
Процентильные значения распределения частиц по размерам для исходных и измельченных порошков NiO и CGO
Процентильные значения, мкм | D50 | D90 |
---|---|---|
NiO исходный | 3.78 | 13.7 |
NiO измельченный | 1.97 | 3.86 |
CGO исходный | 39.1 | 75.5 |
CGO измельченный | 3.08 | 5.93 |
На основе полученного композита NiO/CGO изготавливалась паста с количеством композиционного порошка, равным 60 мас. %. Выбор материалов для пасты осуществлялся по следующим критериям. VariPlus является коммерчески успешным полимерным связующим, обеспечивающим отличные механические и адгезионные свойства паст и чернил на его основе. Дибутилфталат является универсальным пластификатором, обеспечивающим смачиваемость поверхности. VariPlus хорошо растворяется в терпинеоле, к тому же в сочетании друг с другом они обеспечивают необходимые реологические характеристики паст на их основе. Для печати использовалась паста с содержанием VariPlus 11.7 мас. % от массы связки. Данный состав пасты был выбран в качестве оптимального ввиду выполнения следующих требований: массовое содержание твердой фазы ≤60 мас. %, вязкость меньше 1000 Па с, размер частиц с процентильным содержанием D50 ≤ 3 мкм (процентильное содержание частиц должно быть примерно в 100 раз меньше диаметра сопла). Данные параметры позволяют получать в ходе печати каплю сферической формы с отсутствием сателлитных капель [11].
Нелинейная зависимость динамической вязкости от скорости сдвига (рис. 2) для данной пасты указывает на неньютоновский характер течения. Вязкость пасты составляет 380 мПа с для скорости сдвига 5 с–1, 300 мПа с для скорости сдвига 10 с–1 и 200 мПа с для скорости сдвига 30 с–1.
Для выбора оптимального режима прямой струйной печати 3D-объектов выполнялась тестовая печать с разными режимами по частоте и времени открытия клапана печатающей головки. Было установлено, что оптимальными параметрами для рабочей пасты являются частота открытия клапана 20 Гц и длительность открытия клапана 700 мс. При помощи системы автоматизированного проектирования (САПР) создавалась модель объекта для печати, затем модель загружалась в программное обеспечение 3D-принтера, где модель математически разрезается на слои и информация о каждом слое последовательно передается на печать. На рис. 3 приведено изображение образца, состоящего из 15 слоев, последовательно напечатанных и обработанных лазерным излучением с целью формирования конечной формы объекта. Полученный объект имеет следующие размеры: 10 × 10 × 1 мм.
Для определения оптимальной программы спекания анода NiO/CGO был проведен термогравиметрический анализ в среде искусственного воздуха (0.2O2–0.8Ar) при скорости нагрева 5 К/мин. Результаты термогравиметрического анализа (рис. 4) указывают, что основная потеря массы в образце наблюдается в температурном диапазоне 200–400°С. Потеря массы происходит ступенчато. В температурном диапазоне от 100 до 150°С потеря массы образца составляет ≈1% за счет удаления адсорбированной воды с поверхности образца. С температуры 150°С начинается процесс выжигания органической компоненты из образца. Интенсивное удаление органики наблюдается при температуре 250°С и длится до 400°С, при этом потеря массы образца составляет ≈11%. Суммарная потеря массы в ходе термического отжига составляет 14%. При температуре выше 400°С потери массы не наблюдается. Таким образом, результаты термогравиметрии позволяют установить, что при программируемом термическом нагреве напечатанного анода NiO/CGO основная потеря массы происходит при 200–400°С, следовательно, для эффективного удаления органической компоненты из напечатанного образца и предотвращения его разрушения при усадке требуется выдержка в указанном диапазоне температур.
Напечатанный анод NiO/CGO спекался в высокотемпературной печи при оптимальной температуре спекания анодных заготовок 1400°С в течение 11 ч в атмосфере воздуха с выдержкой при 400°С в течение 1 ч. На рис. 5 приведены рентгенограммы исходной пасты, напечатанного образца до и после спекания. Рентгенограммы демонстрируют, что при спекании уменьшается ширина рефлексов, следовательно, происходит укрупнение частиц. В образцах исходной пасты и напечатанного объекта присутствуют только рефлексы, относящиеся к фазам NiO и CGO.
Рис. 5.
Рентгенограммы напечатанного образца композиционного анода: 1 – исходная паста; 2 – напечатанный образец после лазерного спекания; 3 – напечатанный образец после лазерного и термического спекания.
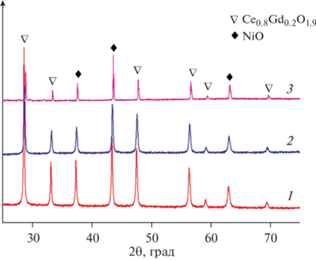
Микрофотографии скола образца после лазерного спекания показывают, что образец является достаточно плотным, без выраженной пористости. Несмотря на то, что выраженная слоистость структуры, обусловленная методикой формирования изделия, отсутствует, что может быть связано с наличием процесса лазерной постобработки и спеканием слоев (рис. 6а). При большем увеличении (рис. 6б) можно увидеть, что при лазерном спекании частицы не изолированы и находятся в контакте с органической пленкой, что свидетельствует о том, что полного удаления органической компоненты не происходит, что согласуется с данными термического анализа. Размер частиц 2–4 мкм соответствует исходному распределению частиц по размерам, что говорит о том, что увеличения частиц вследствие лазерной обработки не происходит.
Рис. 6.
Микроснимки скола напечатанного образца композиционного анода NiO/CGO до термического спекания: а – увеличение в 500 раз, б – увеличение в 15 000 раз.
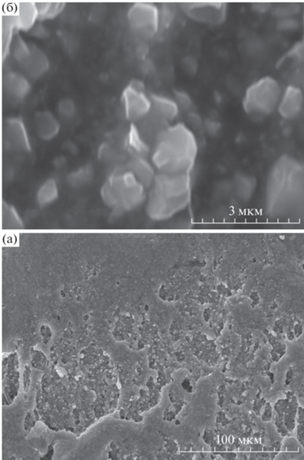
На микрофотографиях образца после спекания при температуре 1400°С видно, что после термической обработки из образца удаляется вся органическая компонента (рис. 7а). При более крупном увеличении (рис. 7б) можно увидеть, что размер частиц увеличился, произошло спекание и увеличение количества контактов между частицами.
Рис. 7.
Микроснимки скола напечатанного образца композиционного анода NiO/CGO после термического спекания: а – увеличение в 500 раз, б – увеличение в 15 000 раз.
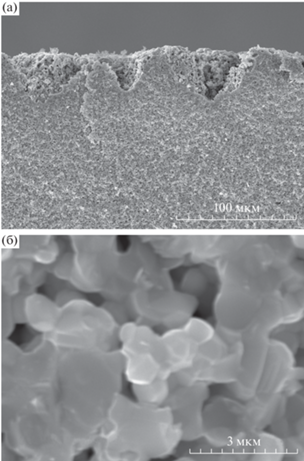
Данные табл. 2 показывают, что при спекании образца при температуре 1400°С идет уменьшение пористости в 2 раза, значение составляет 23.6%. Это несколько ниже чем приведенная в литературе оптимальная пористость анодной заготовки для ТОТЭ, которая находится в диапазоне от 32 до 76% [11]. Это говорит о том, что температура 1400°С является слишком высокой для получения пористого образца и требуются дальнейшие эксперименты по оптимизации режима лазерной и последующей термической обработки образца, в частности для снижения температуры постобработки несущего анода NiO/CGO.
ЗАКЛЮЧЕНИЕ
В данной работе разработан и исследован новый состав пасты на основе оксида никеля и оксида церия, стабилизированного оксидом гадолиния, для прямой 3D-печати с последующей лазерной и термической постобработкой. Проведены эксперименты по печати трехмерных тестовых образцов с использованием разработанной керамической пасты. Впервые методом струйной 3D-печати с лазерной постобработкой получено изделие из композита NiO/CGO с перспективой дальнейшего применения в создании ТОТЭ. Изделие имеет размеры 10 × 10 × 1 мм, плотность 5.26 г/см3, пористость 26.6%. Установлено, что лазерная постобработка напечатанных слоев при прямой струйной печати изделия позволяет провести частичное удаление органической компоненты пасты и сформировать конечную форму объекта.
Список литературы
Tai, X.Y., Zhakeyev, A., Wang, H., Jiao, K., Zhang, H., and Xuan, J., Accelerating Fuel Cell Development with Additive Manufacturing Technologies: State of the Art, Opportunities and Challenges, Fuel Cells, 2019, vol. 19, no. 6, p. 636.
Wei, L., Zhang, J., Yu, F., Zhang, W., Meng, X., Yang, N., and Liu, S., A novel fabrication of yttria-stabilized-zirconia dense electrolyte for solid oxide fuel cells by 3D printing technique, Int. J. Hydrogen Energy, 2019, vol. 44, no. 12, p. 6182.
Eickenscheidt, M., Langenmair, M., Dbouk, A., Nötzel, D., Hanemann, T., and Stieglitz, T., 3D-Printed Hermetic Alumina Housings, Materials, 2021, vol. 14, no. 1, p. 636.
Shahzad, A. and Lazoglu, I., Direct ink writing (DIW) of structural and functional ceramics: Recent achievements and future challenges, Composites, Part B, 2021, vol. 225, p. 109249.
Derby, B., Additive Manufacture of Ceramics Components by Inkjet Printing, Engineering, 2015, vol. 1, no. 1, p. 113.
Chen, Z., Sun, X., Shang, Y., Xiong, K., Xu, Z., Guo, R., Cai, S., and Zheng, C., Dense ceramics with complex shape fabricated by 3D printing: A review, J. Adv. Ceram., 2021, vol. 10, p. 195.
Lomberg, M., Boldrin, P., Tariq, F., Offer, G., Wu, B., and Brandon, N., Additive Manufacturing for Solid Oxide Cell Electrode Fabrication, ECS Trans., 2015, vol. 68, no. 1, p. 2119.
Buccheri, M., Singh, A., and Hill, J.M. Anode versus electrolyte-supported Ni-YSZ/YSZ/Pt SOFCs: Effect of cell design on OCV, performance and carbon formation for the direct utilization of dry methane, J. Power Sources, 2011, vol. 196, no. 3, p. 968.
Steele, B.C.H., Appraisal of Ce1 –yGdyO2 –y/2 electrolytes for IT-SOFC operation at 500°C, Solid State Ion., 2000, vol. 129, no. 1–4, p. 95.
Gunduz, I.E., McClain, M.S., Cattani, P., Chiu, G.T.-C., Rhoads, J.F., and Son, S.F., 3D printing of extremely viscous materials using ultrasonic vibrations, Addit. Manuf., 2018, vol. 22, p. 98.
Song, C., Lee, S., Gu, B., Chang, I., Cho, G.Y., Baek, J.D., and Cha, S.W., A Study of Anode-Supported Solid Oxide Fuel Cell Modeling and Optimization Using Neural Network and Multi-Armed Bandit Algorithm, Energies, 2020, vol. 13, no. 7, p. 1621.
Дополнительные материалы отсутствуют.