Электрохимия, 2022, T. 58, № 7, стр. 408-413
Электрохимические характеристики углеродного материала, полученного методом темплатного синтеза с твердым темплатом
Ю. Е. Синельникова a, b, *, Н. Ф. Уваров a, b, **
a Институт химии твердого тела и механохимии СО РАН
Новосибирск, Россия
b Новосибирский государственный технический университет
Новосибирск, Россия
* E-mail: yulya.sinelnikova.96@bk.ru
** E-mail: uvarov@solid.nsc.ru
Поступила в редакцию 17.01.2022
После доработки 24.01.2022
Принята к публикации 14.02.2022
- EDN: EWJPJJ
- DOI: 10.31857/S0424857022070131
Аннотация
Методом темплатного синтеза с использованием твердого темплатного агента был получен высокопористый углеродный материал. В качестве источника углерода была использована фенолформальдегидная смола резольного типа, а темплатный агент, нанокристаллический ZnO, был синтезирован с помощью термолиза прекурсора – цитрата цинка, введенного в состав исходных реагентов. Углеродный материал был синтезирован пиролизом смолы в присутствии темплата с последующим удалением темплатного агента и обладал величиной удельной поверхности 1050 ± 10 м2/г. Электрохимические характеристики полученного материала исследованы в симметричной двухэлектродной ячейке методом циклической вольтамперометрии при различных значениях скорости развертки напряжения. Показано, что величина удельной емкости в кислотном электролите 1 М H2SO4 достигает 61 Ф/г, что примерно в 2 раза больше, чем в щелочном электролите 6 М КОН. Обнаружена необычная зависимость удельной емкости материала от скорости развертки напряжения в кислотном электролите и показано, что материал обладает относительно низкими значениями удельной емкости, отнесенной к единице поверхности электрода.
ВВЕДЕНИЕ
Пористые углеродные материалы играют важную роль во многих областях современной науки и техники, включая очистку воды и воздуха, газоразделение, катализ, хроматографию и хранение энергии. Одной из перспективных областей применения пористых углеродных материалов является электрохимическая энергетика, в частности их использование в качестве электродных материалов для суперконденсаторов – эффективных электрохимических устройств для накопления, преобразования и рекуперации электрической энергии [1]. Ключевыми компонентами суперконденсатора являются высокопористые электроды на основе материалов с высокой удельной поверхностью. Среди них, наиболее перспективны мезопористые углеродные материалы с высокой удельной поверхностью, обусловленной наличием мезопор [2]. Мезопоры имеют оптимальные размеры для ионного переноса по порам электродного материала, в то время как микропоры могут быть труднодоступными для ионов, а наличие макропор приводит к снижению удельной поверхности. Кроме размера пор и величины удельной поверхности на электрохимические свойства углеродных материалов влияют и другие факторы [3].
Что касается методов получения углеродных материалов, то во всем мире ведутся интенсивные исследования по разработке безопасных и коммерчески доступных методов синтеза пористых углеродных материалов. Традиционные методы получения активированных углей не позволяют варьировать морфологию полученных материалов. Эту задачу можно решить с использованием методов темплатного синтеза, с помощью которых можно синтезировать мезопористые материалы с заданным размером и распределением пор. К сожалению, синтез на основе мицеллярных темплатов [4] очень сложен и требует использования дорогих органических реагентов. Более дешевым и доступным методом является темплатный синтез с использованием твердых темплатных агентов, удаляемых после синтеза. Этим методом можно получать материалы с различным размером пор [5]. Но и в этом случае возникают трудности, связанные с выбором твердого темплата. В литературе описаны методы синтеза углеродных материалов с использованием в качестве темплата различных форм мезопористого диоксида кремния [6], но его удаление из материала является дорогостоящим процессом. Кроме диоксида кремния в качестве твердых темплатов могут быть использованы оксиды других металлов [7–9]. Недавно было предложено формировать частицы твердого темплатного агента из прекурсоров методом in situ непосредственно в процессе синтеза мезопористого углерода, причем в качестве прекурсоров были взяты цитрат и ацетат магния [10]. В цитируемой работе не обсуждался механизм образования оксидного темплата и не были оптимизированы концентрации прекурсоров. Поэтому задачи поиска подходящих твердых темплатов и оптимизации условий приготовления мезопористых углеродных материалов остаются актуальными.
По данным наших предварительных исследований [11], в качестве твердого темплатного агента для синтеза мезопористых углеродных материалов можно использовать нанокристаллический оксид цинка, который может быть получен в процессе термолиза цитрата цинка. Преимуществами оксида цинка являются более низкая температура его получения в процессе термолиза прекурсора (320°С) по сравнению, например, с оксидом магния (450–500°С) и меньшее количество молекул кристаллизационной воды в формульной единице соединения Zn3(C6H5O7)2·2H2O по сравнению с тем же цитратом магния Mg3(C6H5O7)2·10H2O, что позволяет частично уменьшить эффект разрушения полимерной матрицы при выделении продуктов термолиза. В данной работе проведен синтез углеродных материалов с использованием дигидрата цитрата цинка Zn3(C6H5O7)2·2H2O в качестве прекурсора темплатного агента и фенолформальдегидной смолы в качестве источника углерода. Проведены электрохимические исследования и определены значения удельной емкости при использовании этого материала в качестве электрода для суперконденсатора.
ЭКСПЕРИМЕНТАЛЬНАЯ ЧАСТЬ
В качестве исходных реагентов были использованы оксид цинка ZnO (“РЕАХИМ”, ч. д. а.), моногидрат лимонной кислоты C6H5O7·H2O (“ХИМПРОМ”, х. ч.), фенол С6Н5ОН (“РЕАХИМ”, ч. д. а.), 37%-ный раствор формальдегида (“ХИМПРОМ”, х. ч.), карбонат калия K2CO3 (“ХИМПРОМ”, х. ч.), этиловый спирт (96%).
Цитрат цинка был синтезирован с помощью обменной реакции оксида цинка с лимонной кислотой в дистиллированной воде. К расчетному количеству порошка оксида цинка медленно добавляли 1 М раствор лимонной кислоты при перемешивании до достижения точки нейтрализации. Точку нейтрализации определяли по моменту, когда значение рН раствора переставало снижаться при добавлении новых порций щавелевой кислоты. Полученный осадок цитрата цинка Zn3(C6H5O7)2·xH2O выделяли выпариванием маточного раствора при 90°С, а затем промывали водой. Синтезированный цитрат цинка представлял собой белый порошок, нерастворимый в воде. Он был использован в качестве прекурсора темплатного агента, который образуется при термолизе in situ в матрице фенолформальдегидной смолы, являющейся источником углерода при получении конечного материала.
Для получения углеродного материала суспензию цитрата цинка добавляли в раствор фенола в этаноле при массовом соотношении цитрат цинка : фенол, равном 7 : 3. При таком эмпирически подобранном соотношении компонентов получается углеродный материал с наиболее высоким значением удельной поверхности. К полученной суспензии добавляли формальдегид в молярном соотношении фенол : формальдегид, равном 1 : 3, катализатор карбонат калия в количестве 0.5 мас. % и проводили полимеризацию в спиртовом растворе при перемешивании сначала при 40°С в течение 2 ч, затем при 80°С в течение 2 ч. Исходное соотношение фенола к формальдегиду является стехиометрическим и необходимо для формирования трехмерной матрицы фенол-формальдегидной смолы. Указанный режим полимеризации выбран с целью добиться низкой скорости процесса при постепенном удалении растворителя, в результате чего формируется однородная матрица полимера. На последней стадии полимеризации полученный осадок прогревали при температуре 100°С в течение 24 ч. Продукт полимеризации подвергали пиролизу в инертной атмосфере аргона при скорости нагрева 5°С/мин до температуры 900°С с выдержкой при этой температуре в течение 2 ч. Полученный материал обрабатывали раствором соляной кислоты для удаления твердого темплата ZnO и промывали дистиллированной водой. Конечный продукт синтеза представлял собой черный рыхлый порошок.
Точный химический состав кристаллогидрата цитрата цинка и условия его термолиза с образованием ZnO исследовали методом термогравиметрии с помощью синхронного термического анализатора NETZSCH Jupiter 449C STA. Для изучения удельной поверхности полученного углеродного материала использовали метод БЭТ адсорбции азота при 77К на анализаторе “Термосорб ТПД1200”. Электрохимические исследования проводили в двухэлектродной прижимной ячейке из нержавеющей стали с двумя идентичными порошковыми электродами из полученного материала, разделенными гидрофильным пористым сепаратором и помещенными в раствор электролита. Измерения методом циклической вольтамперометрии проводили на потенциостате ИПУ-01 при скорости развертки потенциала 5, 10, 20, 50 и 100 мВ/с в растворах 1 M H2SO4 и 6 M KOH. В отдельных экспериментах в электроды добавляли электропроводящую углеродную сажу (carbon black, acetylene, 50% compressed, 99.9%, Alfa Aesar, 39724) в количестве 20 мас. %.
РЕЗУЛЬТАТЫ И ОБСУЖДЕНИЕ
С помощью методов термогравиметрии (ТГ) было показано, что термолиз кристаллогидрата цитрата цинка происходит в области температур 25–320°С [11]. При нагревании выше 320оС происходит окончательное разложение безводной соли с образованием ZnO (в окислительной атмосфере) или смеси ZnO–C (в среде аргона). На основании анализа измерения массы образца установлено, что при термолизе на воздухе образец теряет 57% массы, что близко теоретическому значению 60% для случая, если синтезированный кристаллогидрат содержит две молекулы воды на формульную единицу соли, т.е. имеет формулу Zn3(C6H5O7)2·2H2O. В результате термолиза образуется нанокристаллический оксид цинка с размерами зерен порядка 20 нм [11], который является твердым темплатным агентом при синтезе углеродного материала.
Цитрат цинка, введенный в качестве функциональной добавки в исходные реагенты для полимеризации, оставался в матрице образующейся фенол-формальдегидной смолы. При нагревании происходил термолиз цитрата цинка с образованием нанокристаллического оксида цинка, находящегося в органической матрице смолы. При более высокой температуре 450–900°С в среде аргона происходил пиролиз смолы с образованием нанокомпозита ZnO–углерод. После обработки нанокомпозита соляной кислотой оксид цинка удалялся с образованием мезопористой углеродной матрицы. Степень очистки углеродного материала от оксида цинка, оцененная по значению зольности после сжигания на воздухе, составляла около 96%. По данным адсорбционных измерений, значение удельной поверхности полученного углеродного материала, определенное по изотермам адсорбции азота БЭТ, составляет 1050 ± ± 10 м2/г.
Для оценки возможности применения полученных материалов в качестве электродных материалов для суперконденсаторов были проведены исследования электрохимических свойств образцов методом циклической вольтамперометрии. На рис. 1 и 2 представлены вольт-амперные кривые, полученные для электродных материалов, состоящих из смеси 80 мас. % полученного пористого углеродного материала и 20 мас. % углеродной сажи (carbon black) (рис. 1а, 2а) и чистого полученного пористого углеродного материала (рис. 1б, 2б). Для испытаний использовали симметричную двухэлектродную ячейку с идентичными электродами. В качестве электролита использовали 1 М водный раствор серной кислоты и 6 М водный раствор гидроксида калия. Сканирование напряжения выполняли при различных значениях скорости сканирования от 5 до 100 мВ/с в области напряжений от –1 до 1 В.
Рис. 1.
Циклические вольт-амперные кривые при скорости развертки потенциала 5, 10, 20, 50, 100 мВ/с в растворе 1 M H2SO4 с добавлением carbon black (а) и без добавления (б).
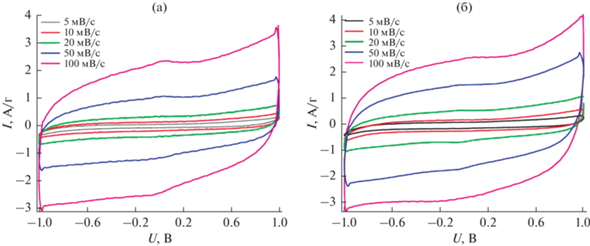
Рис. 2.
Циклические вольт-амперные кривые при скорости развертки потенциала 5, 10, 20, 50, 100 мВ/с в растворе 6 M КОН с добавлением carbon black (а) и без добавления (б).
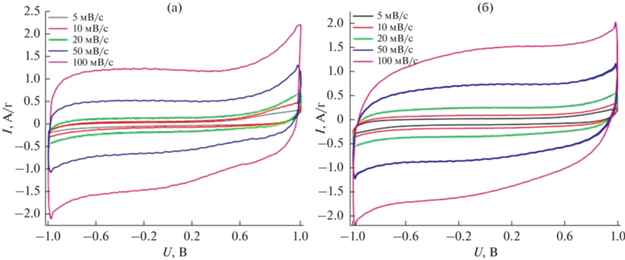
Как видно из рисунков, все кривые имеют относительно гладкую форму без ярко выраженных максимумов, что свидетельствует о незначительном вкладе псевдоемкости. И хотя в кислотном электролите наблюдается слабый сильно размытый максимум, емкость электродов обусловлена в основном емкостью двойного электрического слоя (ДЭС) на границе электрод/электролит. Схожая форма кривых в обоих электролитах также может быть объяснена отсутствием поверхностных функциональных групп и наличием в системе только емкости ДЭС. Рост тока при приближении к граничным значениям напряжений –1 и 1 В обусловлен начальным этапом электрохимического разложения водного электролита.
Удельная емкость C в расчете на единицу массы углеродного материала рассчитывалась по следующей формуле:
Таблица 1.
Расчетные значения удельной емкости, полученные для образцов чистого материала и материала с добавкой углеродной сажи
Состав электродного материала | Электролит | Удельная емкость, ±5 Ф/г, при скорости сканирования напряжения, мВ/c | ||||
---|---|---|---|---|---|---|
5 | 10 | 20 | 50 | 10 | ||
80 мас. % пористого углерода + + 20 мас. % carbon black | 1 M H2SO4 | 33 | 43 | 42 | 50 | 52 |
6 М КОН | 21 | 32 | 17 | 22 | 25 | |
Пористый углерод | 1 M H2SO4 | 46 | 41 | 55 | 58 | 58 |
6 М КОН | 27 | 26 | 27 | 27 | 27 |
Как видно из таблицы, наибольшие значения емкости в обоих электролитах были получены для электродного материала, состоящего из чистого углеродного материала без добавки сажи. Это указывает на то, что синтезированный углеродный материал обладает достаточно высокой электропроводностью, поэтому для улучшения его характеристик не требуется введения электропроводящих добавок. Более того, углеродная сажа обладает относительно низким значением удельной поверхности, что также приводит к снижению удельной емкости материала. В кислотном электролите значения удельной емкости превышают значения, полученные в щелочном электролите, что согласуется с данными, полученными ранее в работе [12] для высокопористых материалов на основе активированного углерода, и обусловлено относительно малым ионным радиусом катиона гидроксония по сравнению с другими анионами.
На рис. 3 представлены зависимости удельной емкости чистого углеродного материала и материала с добавкой сажи от скорости развертки напряжения v, полученные в различных электролитах. Из рисунка видно, что зависимости Cm = f(v), полученные в кислотном электролите 1 М H2SO4, имеют нетривиальный вид. Как правило, значение емкости либо не зависит от v, либо уменьшается с ростом скорости развертки напряжения, что объясняется влиянием диффузионных ограничений при образовании двойного электрического слоя [13]. Емкость полученных в работе материалов при малых значениях v в кислотном электролите увеличивается с ростом скорости развертки напряжения до некоторого стационарного значения. Причины появления такой зависимости не ясны и требуют дальнейшего выяснения. Оценка величины удельной емкости, нормированной на единицу поверхности электродного материала Cs [Ф/м2] с помощью уравнения Cs = = Cm/Ssp, где Ssp – удельная поверхность материала (м2/г), показывает, что значение Cs находится в пределах 0.03–0.06 Ф/м2 и в 2–3 раза ниже, чем соответствующее значение для материалов на основе активированного углерода 0.094 Ф/м2 [14]. Следовательно, электрохимической активностью обладает только небольшая доля поверхности материала. Возможно, необычная зависимость емкости от скорости развертки напряжения связана с этим фактором.
ЗАКЛЮЧЕНИЕ
В данной работе методом темплатного синтеза с использованием твердого темплатного агента был получен пористый углеродный материал с удельной поверхностью 1050 ± 10 м2/г. В качестве источника углерода была использована фенолформальдегидная смола резольного типа, а темплатный агент, нанокристаллический ZnO, был синтезирован с помощью термолиза прекурсора – цитрата цинка, введенного в состав исходных реагентов. Высокопористый углеродный материал был синтезирован пиролизом смолы в присутствии темплата с последующим удалением темплатного агента. Электрохимические характеристики полученного материала исследованы методом циклической вольтамперометрии. Показано, что величина удельной емкости в кислотном электролите достигает 58 Ф/г, что примерно в 2 раза больше, чем в щелочном электролите. Обнаружена необычная зависимость удельной емкости материала от скорости развертки напряжения в кислотном электролите 1 М H2SO4 и показано, что материал обладает относительно низкими значениями удельной емкости, отнесенной к единице поверхности электрода. Следовательно, для повышения значений емкости материала необходимо увеличить площадь электрохимически активной поверхности.
Список литературы
Grbovic, P.J., Ultra-capacitors in power conversion systems: applications, analysis and design from theory to practice, Hoboken: Wiley-IEEE Press, 2013, 336 p.
Lu, M., Supercapacitors: Materials, Systems and Applications, Hoboken: Wiley-IEEE Press, 2013, 568 p.
Wang, K., Wang, Y., Wang, Y., Hosono, E., and Zhou, H., Mesoporous Carbon Nanofibers for Supercapacitor Application, J. Phys. Chem. C, 2009, vol. 113, no. 3, p. 1093.
Peer, M., Lusardi, M., and Jensen, K.F., Facile Soft-Templated Synthesis of High-Surface Area and Highly Porous Carbon Nitrides, Chem. Materials, 2017, vol. 29, no. 4, p. 1496.
Zhang, Z., Zuo, F., and Feng, P., Hard template synthesis of crystalline mesoporous anatase TiO2 for photocatalytic hydrogen evolution, J. Materials Chem., 2010, vol. 20, no. 11, p. 2206.
Lu, H., Kim, K., Kwon, Y., Sun, X., Ryoo, R., and Zhao, X.S., Zeolite-templated nanoporous carbon for high-performance supercapacitors, J. Materials Chem. A, 2018, vol. 6, no. 22, p. 10388.
Noh, H., Choi, S., Kim, H.G., Choi, M., and Kim, H.-T., Size Tunable Zeolite-Templated Carbon as Microporous Sulfur Host for Lithium-Sulfur Batteries, ChemElectroChem., 2019, vol. 6, iss. 2, p. 558.
Kado, Y., Soneda, Y., and Yoshizawa, N., Contribution of mesopores in MgO-templated mesoporous carbons to capacitance in non-aqueous electrolytes, J. Power Sources, 2015, vol. 276, p. 176.
Liu, W., Wang, C., Wang, J., Jia, F., Zheng, J., and Chen, M., Preparation of mesoporous MgO-templated carbons from phenolic resin and their applications for electric double-layer capacitors, Chinese Science Bulletin, 2013, vol. 58, no. 9, p. 992.
Morishita, T., Tsumura, T., Toyoda, M., Przepiórski, J., Morawski, A.W., Konno, H., and Inagaki, M., A review of the control of pore structure in MgO-templated nanoporous carbons, Carbon, 2010, vol. 48, no. 10, p. 2690.
Sinelnikova, Yu. and Uvarov, N., The application of zinc citrate for the synthesis of carbon materials, MATEC Web of Conference, 2021, vol. 340.
Barzegar, F., Momodu, D.Y., Fashedemi, O.O., Bello, A., Dangbegnon, J.K., and Manyala, N., Investigation of different aqueous electrolytes on the electrochemical performance of activated carbon-based supercapacitors, RSC Advances, 2015, vol. 5, no. 130, p. 107482.
Wang, H. and Pilon, L., Physical interpretation of cyclic voltammetry for measuring electric double layer capacitances, Electrochim. Acta, 2012, vol. 64, p. 130.
Centeno, T.A., Sereda, O., and Fritz Stoeckli, F. Capacitance in carbon pores of 0.7 to 15 nm: a regular pattern, Phys. Chem. Chem. Phys., 2011, vol. 13, p. 12403.
Дополнительные материалы отсутствуют.