Журнал физической химии, 2020, T. 94, № 11, стр. 1595-1603
Изучение взаимодействия компонентов на различных стадиях приготовления катализаторов Ru–Rb/сибунит для разложения аммиака
К. Н. Иост a, *, Н. С. Смирнова b, В. А. Борисов a, c, **, В. Л. Темерев a, Ю. В. Суровикин a, В. В. Кривенцов d, Е. В. Храмов e, Я. В. Зубавичус d, М. В. Тренихин a, c, Е. Ю. Герасимов d, Д. А. Шляпин a, П. Г. Цырульников a
a Российская академия наук, Сибирское отделение, Институт катализа, Центр новых химических технологий
644040 Омск, Россия
b Российская академия наук, Институт общей и неорганической химии им. Н.С. Курнакова
119991 Москва, Россия
c Омский государственный технический университет
644050 Омск, Россия
d Российская академия наук, Сибирское отделение, Институт катализа
630090 Новосибирск, Россия
e Национальный исследовательский центр “Курчатовский институт”
123182 Москва, Россия
* E-mail: iost.k.n@mail.ru
** E-mail: borisovtiger86@mail.ru
Поступила в редакцию 23.01.2020
После доработки 23.01.2020
Принята к публикации 17.03.2020
Аннотация
Методами XAFS-спектроскопии, рентгенофазового анализа на синхротронном излучении и просвечивающей электронной микроскопии высокого разрешения изучен процесс взаимодействия компонентов катализатора разложения аммиака Ru–Rb/Сибунит, а также охарактеризована пористая структура образцов по стадиям приготовления. Комплексом методов показано наличие рутения в катализаторе преимущественно в металлическом состоянии, отсутствие совместных фаз рутения и рубидия. Установлено, что рубидий присутствует в катализаторе в окисленном состоянии – как в виде соединений, непосредственно контактирующих с частицами активного компонента и сопоставимых с последними по размерам, так и в виде мелких кластеров, расположенных преимущественно в структуре углеродного носителя.
Катализаторы на основе металлов платиновой группы, нанесенных на углеродные носители, широко используются в различных процессах, протекающих в восстановительной атмосфере при невысоких температурах. Примером таких процессов являются: низкотемпературный синтез [1–12] и разложение аммиака [13–15], гидрирование органических соединений [16–18], дегидрирование спиртов [19], очистка от примесей СО [20] и т.д. Поскольку синтез подобных систем осуществляется в несколько стадий, то за счет взаимодействия металла и углеродного носителя на разных этапах приготовления катализатора его свойства могут заметно изменяться. При этом на различных стадиях получения и при дальнейшей эксплуатации катализатора происходят такие процессы, как десорбция поверхностных групп носителя, формирование углеродных отложений, спекание и реконструкция активного компонента, миграция поверхностных частиц и газификация носителя [21]. Исключительную информацию об изменениях каталитических систем на различных этапах активации позволяют получить такие методы, как поверхностная электронная микроскопия высокого разрешения (ПЭМ ВР), рентгенофазовый анализ на синхротронном излучении (РФА СИ) и XAFS-спектроскопия, что имеет важное значение для понимания процессов формирования активных центров в зависимости от условий приготовления, а также прогнозирования активности и термической стабильности катализатора.
Катализаторы Ru/С на основе графитоподобного углеродного носителя Сибунита являются перспективными для реакций низкотемпературного синтеза/разложения аммиака. Большая часть исследований посвящена, главным образом, влиянию добавок калия, цезия и бария на каталитическую активность Ru/Сибунит в реакциях синтеза/разложения аммиака [5–7, 9–11, 21]. В ряде работ отмечается зависимость дисперсности активного компонента от таких факторов, как пористая структура носителя, присутствие кислородсодержащих групп, а также специфическое взаимодействие между частицами металла (или его предшественника) и дефектной структурой носителя [22]. При этом объяснения влияния данных факторов носят противоречивый характер, поскольку результат часто зависит от метода нанесения, количества и условий последующих этапов синтеза катализатора. Так функциональные поверхностные группы, выступая в роли фиксирующих участков для образования частиц активного компонента, усиливают взаимодействие “рутений–носитель” [15], способствуя увеличению дисперсности и равномерному распределению активного компонента. В то же время, кислородсодержащие поверхностные группы при термическом разложении во время восстановительной обработки могут способствовать агломерации металла [15, 23]. Рубидий не исследовали в этом отношении, по-видимому, из-за его практической дефицитности.
Целью нашего исследования было восполнить этот пробел для последующего сопоставления влияния рубидия на активность в реакции разложения аммиака на системе Ru–Rb/Cибунит с влиянием K, Cs, Ba в аналогичной системе.
Кроме того, заметим, что спектры EXAFS Rb, вследствие его электронного строения, могут дать более подробную информацию о взаимодействиях в системе Ru–Rb/C, что недоступно для систем с K, Cs, Ba.
ЭКСПЕРИМЕНТАЛЬНАЯ ЧАСТЬ
Приготовление катализаторов
Аммиачно-хлоридный комплекс [Ru(NH3)nClm]Clр (n = 5–6; m = 0–1; p = 1–2) получали по методике, описанной в работе [6].
Исходные гранулы Сибунита (SБЭТ = 300 м2/г) измельчали и получали фракцию <0.2 мм, затем отмывали от углеродной пыли, сушили при 120°С. Носитель пропитывали водным раствором комплекса рутения, сушили при 120°С 3 ч на воздухе, после чего восстанавливали в H2 при 450°С 4 ч (скорость нагрева и охлаждения – 10°С/мин). Образец 4%Ru/Сибунит пропитывали водным раствором RbNO2, исходя из мольного соотношения Rb : Ru = 2.5, высушивали при 120°С 3 ч на воздухе, после чего проводили прокаливание в токе Ar при 350°С 2 ч, затем в Н2 при 350°С 2 ч (скорость нагрева и охлаждения составляла 5°C/мин). Для структурных исследований часть образца отбирали на каждой стадии синтеза катализатора и хранили в герметичных ампулах для предотвращения контакта с воздухом.
В данной работе исследовалась серия, состоящая из катализатора Ru–Rb/Сибунит на разных этапах его синтеза (табл. 1, образцы № 2–6). Кроме того, дополнительно был приготовлен образец 8.5%Rb/Сибунит без рутения, обработанный в Ar и Н2 аналогично катализатору 4%Ru–8.5%Rb/Сибунит на стадии нанесения и закрепления промотора.
Таблица 1.
Сведения о приготовленных образцах
№ | Образец | Шифр | Приготовление | SБЭТ, м2/г | VΣпор, см3/г | Dср (4V/SБЭТ), Å |
---|---|---|---|---|---|---|
1 | Сибунит | Sib | Исходный носитель | 300 | 0.420 | 55.9 |
2 | 4%Ru/Сибунит | Ru/Sib (суш.) | Пропитка раствором [Ru(NH3)nClm](OH)p, сушка 120°С 3 ч | – | – | – |
3 | 4%Ru/Сибунит | Ru/Sib (H2) | 4%Ru/Сибунит, сушка 120°С, 3 ч, восстановление 450°С, 4 ч | 305 | 0.491 | 64.5 |
4 | 4%Ru–8.5%Rb/Сибунит | Ru–Rb/Sib (суш.) | 4%Ru/Сибунит, пропитка раствором RbNO2, сушка 120°С 3 ч | – | – | – |
5 | 4%Ru–8.5%Rb/Сибунит | Ru–Rb/Sib (Ar) | 4%Ru–8.5%Rb/Сибунит, сушка 120°С, 3 ч, прокаливание в Ar 350°С 2 ч | – | – | – |
6 | 4%Ru–8.5%Rb/Сибунит | Ru–Rb/Sib (H2) | 4%Ru–8.5%Rb/Сибунит, сушка 120°С, 3 ч, прокаливание в Ar 350°С 2 ч, восстановление в Н2 350°С 2 ч | 221 | 0.423 | 76.4 |
7 | 8.5%Rb/Сибунит | Rb/Sib (H2) | 8.5%Rb/Сибунит пропитка раствором RbNO2, сушка 120°С, 3 ч, прокаливание в Ar 350°С 2ч, восстановление в Н2 350°С 2 ч | 240 | 0.432 | 72.2 |
Определение удельной поверхности и пористой структуры
Измерение удельной поверхности образцов катализаторов проводили на приборе “Sorpty-1750” (“Carlo Erba”) методом БЭТ по одноточечной адсорбции азота при давлении Р = 135 Торр и температуре 77 K. Значение адсорбционной площади молекулы N2 в заполненном монослое считали равным 0.162 нм2. Относительная погрешность Δ составила ±4%. Исследование параметров пористой структуры катализаторов проводили по изотермам адсорбции-десорбции азота при –195.7°С на приборе Sorptomatic-1900 фирмы “CarloErba”. Расчеты удельной поверхности по методу БЭТ выполняли в интервале равновесных относительных значений паров азота при P/PS = 0.05–0.33 по изотерме адсорбции. Суммарный адсорбционный объем пор (VΣпор) определяли по величине адсорбции азота при P/PS = = 0.996, плотность адсорбированного азота принималась равной плотности нормальной жидкости (мольный объем жидкого N2 равен 34.68 см3/моль).
XAFS-спектроскопия
EXAFS-спектры К-краев поглощения рутения и рубидия снимали на УНУ (Уникальной научной установке) станции EXAFS-спектроскопии ИК СО РАН в рамках Сибирского Центра синхротронного и терагерцового излучения (СЦСТИ, г. Новосибирск).
Спектры были получены с использованием синхротронного излучения при энергии электронов в накопителе ВЭПП-3 2 ГэВ и средней величине тока 70 мА с использованием разрезного кристалла Si (111) в качестве монохроматора. Все спектры были сняты в режиме “на пропускание” с шагом в 2.0 эВ. Для регистрации рентгеновского излучения использовались ионизационные камеры.
Полученные спектры были обработаны с использованием программы Viper [24] по стандартной методике [25]. Спектры К-края поглощения рутения обрабатывались как k3χ(k) в интервале волновых чисел 3.00–13.00 Å–1, рубидия – в интервале k =3.50–11.50 Å–1. Удаление фона проводилось путем экстраполяции предкраевой области поглощения в область EXAFS полиномами Викторина. Для расчета гладкой части коэффициента поглощения была использована аппроксимация на основе трех кубических сглаживающих сплайн-функций. В качестве начальной точки E0 спектра EXAFS использовали точку перегиба на краю поглощения.
Для получения квантово-химических данных, необходимых для расчета структурных параметров, использовалась программа FEFF-7 [26]. Данные о структуре соединений были взяты из базы данных Inorganic Crystal Structure Database (ICSD) [27]. Дополнительно были сняты эталонные спектры К-края поглощения Ru (рутениевая фольга; оксид рутения RuO2).
Рентгенофазовый анализ на синхротронном излучении (РФА СИ)
Измерения рентгеновской дифракции на синхротронном излучении (РФА СИ) проводили на экспериментальной станции СТМ Курчатовского источника синхротронного излучения [28]. Для монохроматизации пучка СИ использовали однокристалльный монохроматор с вырезом (“бабочка”), настроенный с точностью до 1 эВ на K-край поглощения Zr (E = 17998.4 эВ, λ = 0.6889 Å) по максимуму производной спектра циркониевой фольги, измеренного с помощью двух воздушных ионизационных камер. Сечение пучка ограничивали до квадрата размером 300 × 300 мкм при помощи моторизированных коллиматорных шторок. Дифрактограммы измеряли с помощью CCD-детектора Mar SX-165, установленного на расстоянии 15 см от образца. Время экспозиции составляло 20 мин. Интегрирование двумерных картин рассеяния рентгеновских лучей осуществляли в программе Fit2d [29]. Для анализа дифрактограмм использовали программное обеспечение PDF 2015 (фазовый анализ) и Fityk (профильный анализ) [30].
Просвечивающая электронная микроскопия высокого разрешения
Исследование микроструктуры образцов осуществляли методом просвечивающей электронной микроскопии высокого разрешения с помощью электронного микроскопа JEM-2010 (JEOL, Япония) c ускоряющим напряжением 200 кВ и предельным разрешением 0.14 нм. Изображения записывали с помощью ПЗС матрицы Soft Imaging System (Германия). Химический состав определяли с использованием электронного микроскопа JEM-2100 (JEOL, Япония, ускоряющее напряжение 200 кВ, разрешение 0.145 нм), снабженного энергодисперсионным рентгеновским спектрометром INСA-250 “Oxford Instruments”. Перед проведением электронно-микроскопических исследований образцы измельчали ультразвуковым диспергатором и наносили на углеродные подложки, закрепленные на медных сетках.
ОБСУЖДЕНИЕ РЕЗУЛЬТАТОВ
Определение удельной поверхности образцов катализаторов
В табл. 1 приведены значения SБЭТ для исходного носителя и образцов 3 (4%Ru/Сибунит), 6 (4%Ru–8.5%Rb/Сибунит) и 7 (8.5%Rb/Сибунит). Как видно, для образца 3 после восстановительной термообработки (450°С, Н2) SБЭТ по сравнению с образцом исходного Сибунита, практически не изменяется (305 м2/г), в то время как наблюдается значительное, на 17%, увеличение общего объема пор (до 0.491 см3/г) при одновременном росте среднего диаметра пор на 15% (до 64.5 Å). Увеличение объема и среднего диаметра пор при неизменной величине удельной поверхности свидетельствует о том, что приводящее к снижению величины SБЭТ укрупнение пор компенсируется ростом SБЭТ вследствие формирования новых микропор. Действительно, как уже было показано ранее [21, 31–33], металлический Ru, образующийся из предшественника в процессе восстановления, при повышенной температуре (450°С) способен катализировать процесс метанирования углеродного носителя, что приводит к разрушению стенок пор, контактирующих с частицами рутения, и, соответственно, укрупнению пор, которое мы наблюдаем. С другой стороны, для наночастиц рутения [34–36] при повышенных температурах характерна подвижность, и, продвигаясь по поверхности носителя, они способны формировать каналы, таким образом, формируя микропоры в образце Ru/Сибунит.
Нанесение рубидия на Сибунит в отсутствие рутения также приводит к увеличению общего объема пор на 3.1% (до 0.432 см3/г) и среднего диаметра пор – на 29% (до 72.2 Å). Можно полагать, что в данном случае также происходит разрушение стенок пор углеродного носителя как следствие взаимодействия с предшественником (нитрит рубидия), который является окислителем. Это приводит к увеличению объема и среднего диаметра пор.
Сопоставление текстурных характеристик вышеописанных образцов и образца 6 показывает, что его текстурные характеристики определяются, прежде всего, нанесением и превращениями предшественника промотора. Значительное (на 29%, до 221 м2/г) снижение удельной поверхности, а также рост среднего диаметра (на 37%) и объема пор (на 26%) по сравнению с исходным Сибунитом приближает катализатор к соответствующим показателям образца 7.
Исследование образцов катализаторов методом рентгенофазового анализа на синхротронном излучении
На рис. 1 представлены рентгеновские дифрактограммы исходного Сибунита и образцов 3 (4%Ru/Сибунит), 6 (4%Ru–8.5%Rb/Сибунит) и 7 (8.5%Rb/Сибунит). Для профильного анализа были выбраны пики графита (002) – наиболее интенсивный и (110) – наиболее дальний по угловой шкале из исследованных. Анализ пиков (100) и (101) не проводили вследствие их наложения друг на друга и на пики компонентов катализатора.
Рис. 1.
Данные РФА СИ для образцов (см. табл. 1): а – образец № 1; б – образец № 3; в – образец № 6; г – образец № 7.
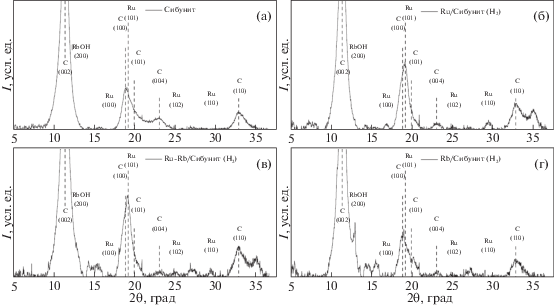
Как видно, смещения пиков графита и изменения их ширины, что соответствовало бы изменению межплоскостных расстояний при образовании интеркалированных соединений [10, 37], не обнаружено. Вместе с тем, следует отметить, что сдвиги межплоскостных расстояний достоверно наблюдаются для интеркалятов, где содержание рубидия очень высоко (мольные отношения С : Rb составляют 4–8) [38], по сравнению с таковым в данных катализаторах (соотношение С : Rb – 80–100).
В дифрактограммах образцов 3, 6 и 7 были обнаружены дифракционные пики, связанные с присутствием нанесенных компонентов катализатора. В катализаторах 3 и 6 рутений присутствует в виде металла, о чем свидетельствует наличие пиков Ru (101) и Ru (110). Пик при 2θ ≈ 35° в дифрактограммах Ru-содержащих образцов может представлять собой как перекрывающиеся друг с другом пики Ru (112) и (201), так и пик (112) графита. Rb-содержащие образцы сходны по фазовому составу – на дифрактограммах присутствуют пики низкой интенсивности, отнесенные к фазам RbOH, Rb2O3. Рубидия в восстановленном состоянии или его карбида не обнаружено.
Исследование образцов катализаторов с помощью просвечивающей электронной микроскопии высокого разрешения
Методом ПЭМ были исследованы образцы 2, 3, 6 и 7. В образце 2 активный компонент присутствует в виде кластеров (0.8–1.2 нм) равномерно распределенных по Сибуниту (рис. 2).
Рис. 2.
Снимки ПЭМВР и распределения частиц по размерам: а) образец 2; б) образец 3; в) снимок ПЭМВР иллюстрирующий наличие кластерных форм Rb (показаны стрелками) на поверхности Сибунита в образце 7.
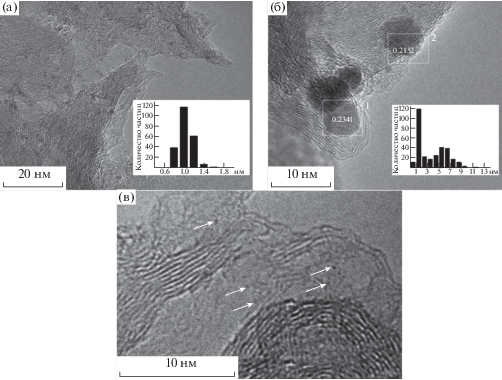
В образце 3 после восстановления предшественника при 450°С в водороде наблюдается широкое распределение частиц по размерам (от 1 до 12 нм), при этом основная доля наночастиц имеет размеры от 1 до 2 нм (рис. 2а). После нанесения и закрепления рубидия на Сибуните средний размер частиц рутения практически не изменяется (рис. 2б), при этом на снимках ПЭМ обнаруживаются только округлые контрастные частицы, соответствующие металлическому рутению [39]. При исследовании образца 7 частиц фазы RbxOy не обнаружено. При детальном рассмотрении участков Сибунита, по структуре более сходных с графитом (рис. 2в), можно отметить наличие контрастных черных точек. Предположительно, эти точки и являются кластерной формой соединений рубидия (на рис. 2в показаны белыми стрелками).
Согласно данным элементного анализа, в образце 6 (рис. 3), помимо углерода, рутения и рубидия, присутствует некоторое количество кислорода, а рубидий и рутений равномерно распределены по катализатору. Результаты рентгеновского микроанализа указывают на присутствие некоторого количества поверхностного оксида рутения с межплоскостным расстоянием 0.227 нм, что соответствует грани (002) RuO2 [40]. Установлено отсутствие следов кислорода в области больших концентраций Ru и Rb (рис. 3а): содержание С, Rb и Ru составляет 84.8, 9.8 и 5.5 мас. %, что может являться косвенным доказательством внедрения некоторого количества промотора в Сибунит.
В работе Ларичева и соавторов [7] установлено, что рубидий в свежеприготовленном катализаторе в большей степени взаимодействует с рутением, чем с Сибунитом. В нашем случае также можно наблюдать фазы, взаимодействующие с рутением (рис. 3б, 3в). Данные EDX для области, представленной на рис. 3б, свидетельствуют о присутствии оксидных фаз рутения и рубидия, исходя из мольного соотношения элементов (О : Ru 2.82 : 1 и O : Rb = 2.79 : 1). По результатам микродифракции, измеренное межплоскостное расстояние d = 0.225 нм можно отнести к расстоянию в оксиде рутения по направлению 002 (d = = 0.227 нм) [40]. Однако поскольку фазы RbxOy вблизи частицы рутения на данном снимке не наблюдается, предполагается, что в этой области рубидий присутствует в виде кластеров, аналогично рис. 2в.
Для области, изображенной на рис. 3в, по данным элементного анализа соотношение для рутения ниже (О : Ru = 1.52 : 1 и O : Rb = 3.67 : 1), содержание С, О, Rb, Ru составляет 75.84, 3.65, 5.31, 15.2 мас. % соответственно. Результаты микродифракции при этом показывают наличие кристаллической решетки с характеристическим расстоянием d = 0.204, что соответствует металлическому рутению, при этом межплоскостных расстояний, характерных для RuO2, не обнаружено. Вероятнее всего, частица рутения окружена “ореолом” из фазы RbxOy ввиду высокого содержания рубидия в исследуемой области. Для области, представленной на рис. 3в, характерны элементные соотношения (О : Ru 0.3 : 1 и O : Rb = 5.03 : 1), при содержании С, О, Rb, Ru в количестве 39.9, 2.87, 3.05, 54.18 мас. % соответственно. По результатам микродифракции, в исследуемой области присутствуют решетки с расстояниями d = 0.214 и 0.227 нм, что соответствует металлическому Ru и его оксиду, кроме того, наблюдается покрытие частицы рутения фазой, которую можно отнести к смеси оксидов рубидия.
Исследование образцов катализаторов методом XAFS
По данным EXAFS К-края рутения, в катализаторе после сушки (образец № 2) рутений присутствует в дисперсном окисленном состоянии, в спектрах остальных катализаторов преобладает металлическое состояние (рис. 4). Для образцов 3 и 4 увеличение амплитуды пика Ru–O (область ∼2 Å) свидетельствует о присутствии некоторых количеств окисленной поверхностной фазы. Спектры EXAFS К-края рутения для катализаторов 4%Ru–8.5% Rb/Сибунит после стадий активации в аргоне и последующего восстановления в водороде практически идентичны (рис. 4а). На кривых РРА в каждом случае присутствуют три пика, соответствующие первой (2.69 Å), второй (3.79 Å) и третьей (4.69 Å) координационным сферам металлического рутения. Данные XANES (край Rb–K) хорошо согласуются с вышесказанным; из спектров XANES видно (рис. 4б), что при увеличении вклада окисленной фазы растет пик, соответствующий переходу 1s-4p (обозначен *), и изменяется форма спектра.
Рис. 4.
Кривые радиального распределения атомов (РРА) (а, в) и спектры XANES К-края поглощения рутения и рубидия (б, г) в катализаторах Ru/Сибунит и Ru–Rb/Сибунит.
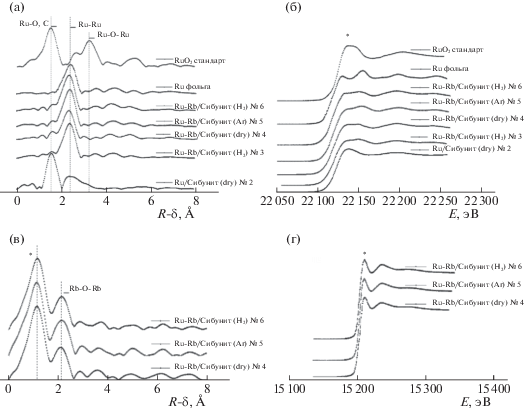
Согласно данным EXAFS, полученным для RbK, во всех случаях присутствие пика, соответствующего 1.2 Å на шкале R–δ (отмечен звездочкой на рис. 4в), связано с процессами двухэлектронного возбуждения уровней 1s3d и 1s3p в щелочных металлах [41] и не относится к реальному межатомному расстоянию. Следующий за ним пик соответствует расстоянию Rb–C или Rb–O ∼ ∼ 2.8 Å, что может отвечать расстоянию от рубидия до углерода носителя или расстоянию от атомов рубидия до кислорода в Rb2O.
Спектры XANES RbK для всех образцов 4%Ru–8.5%Rb/Сибунит практически идентичны. Во всех случаях рубидий находится в окисленной фазе (рис. 4г), поскольку в данном исследовании регистрация спектров XAFS проводилась при контакте образца с воздухом. Следует отметить, что ни в одном спектре не было зафиксировано присутствие расстояний Ru–Rb, что свидетельствует о том, что рутений и рубидий не образуют общих фаз.
Как можно заключить из представленных выше результатов, в процессе формирования катализатора по стадиям приготовления не происходит формирования совместных фаз рутения и рубидия. Согласно данным РФА СИ, ПЭМ, XAFS рутений в нанесенных на Сибунит катализаторах, главным образом присутствует в металлическом состоянии. Незначительные примеси оксида рутения, вероятнее всего, обусловлены контактом с атмосферным кислородом. Нанесение рубидия не приводит к изменению состояния активного компонента. Рубидий присутствует на поверхности катализатора в виде оксидных фаз, представленных как в виде крупных образований, сопоставимых с размерами частиц рутения и непосредственно контактирующих с ними, так и в виде мелких кластеров. В пользу присутствия рубидия в образце в виде мелких кластеров свидетельствуют данные EXAFS по краю рубидия и результаты ПЭМ. Предполагается, что взаимодействие модификатора и рутения осуществляется как за счет непосредственного контакта оксидных фаз рубидия с наночастицами рутения, так и в форме электронного взаимодействия через носитель, в котором окисленная фаза рубидия присутствует в виде мелких кластеров.
Физико-химические исследования выполнены с использованием приборной базы Омского регионального ЦКП СО РАН (Омск). Работа выполнена в рамках государственного задания ЦНХТ ИК СО РАН в соответствии с Программой фундаментальных научных исследований государственных академий наук на 2013–2020 годы по направлению V.46, проект № V.46.2.5 (номер госрегистрации в системе ЕГИСУ НИОКТР АААА-А17-117021450096-8).
Список литературы
Kowalczyk Z., Jodzis S., Raróg W. et al. // Appl. Catal. A: General. 1999. V. 184. № 1. P. 95.
Spencer M.S. // Lett. 1992. V. 13. № 1–2. P. 45.
Szmigiel D., Bielawa H., Kurtz M. et al. // J.Catal. 2002. V. 205. № 1. P. 205.
Kotarba A., Dmytrzyk J., Raróg-Pilecka W., Kowalczyk Z. // Appl. Surf. Sci. 2003. V. 207. № 1–4. P. 327.
Ларичев Ю.В., Просвирин И.П., Шляпин Д.А. и др. // Кинетика и катализ. 2005. Т. 46. № 4. С. 635.
Шитова Н.Б., Добрынкин Н.М., Носков А.С. и др. Там же. 2004. Т. 45. № 3. С. 440.
Larichev Y.V., Shlyapin D.A., Tsyrul’nikov P.G., Bukhtiyarov V.I. // Catal. Lett. 2008. V. 120. № 3. P. 204.
Lin B., Wei K., Lin J., Ni J. // Catal. Commun. 2013. V. 39. P. 14.
Rossetti I., Mangiarini F., Forni L. // Appl. Catal. A: General. 2007. V. 323. P. 219.
Raróg-Pilecka W., Miśkiewicz E., Jodzis S., Petryk J. et al. // J. Catal. 2006. V. 239. № 2. P. 313.
Sheng Zeng H., Inazu K., Aika K.I. // Ibid. 2002. V. 211. № 1. P. 33.
Rossetti I., Pernicone N., Forni L. // Catal. Today. 2005. V. 102–103. P. 219.
Raróg-Pilecka W., Szmigiel D., Kowalczyk Z. et al. // J. Catal. 2003. V. 218. № 2. P. 465.
Li L., Zhu Z.H., Yan Z.F. et al. // Appl. Catal. A: General. 2007. V. 320. P. 166.
Shreya Mukherjee, Surya V. Devaguptapu, Anna Sviripa et al. // Appl. Catal. B: Environmental. 2018. V. 226. P. 162.
Kulagina M.A., Simonov P.A., Gerasimov E.Y. et al. // Colloid. Surf. A. 2017. V. 526. P. 29.
Belskaya O.B., Mironenko R.M., Talsi V.P. et al. // Procedia Engineering. 2016. V. 152. P. 110–115.
Benavidez A.D., Burton P.D., Nogales J.L. et al. // Appl. Catal. A: General. 2014. V. 482. P. 108–115.
Shelepova E.V., Vedyagin A.A., Ilina L.Y. et al. // Appl. Surf. Sci. 2017. V. 409. P. 291–295.
Truszkiewicz E., Raróg-Pilecka W., Zybert M. et al. // Pol. J. Chem. Tech. 2014. V. 16. № 4. P. 106–110.
Garcia-Garcia F.R., Fernandez-Garcia M., Newton M.A. et al. // Chem. Cat. Chem. 2013. V. 5. P. 2446.
Guerrero-Ruiz A., Badenes P., Rodro Aguez-Ramos I. // Appl. Catal. A: General. 1998. V. 173. P. 313.
Coloma F., Sepulveda-Escribano A., Fierro J.L.G., Rodriguez-Reinoso F. // Appl. Catal. A: Gen. 1997. V. 150. P. 165.
http://www.cells.es/Beamlines/CLAESS/software/viper.html.
Кочубей Д.И. EXAFS – спектроскопия катализаторов. Новосибирск: изд-во Наука, 1992. 145 с.
http://leonardo.phys.washington.edu/feff/welcome.html.
http://www.fiz-karlsruhe.de/icsd_web.html.
Chernyshov A.A., Veligzhanin A.A., Zubavichus Y.V. // Nuclear Instruments and Methods in Physics Research Section A: Accelerators, Spectrometers, Detectors and Associated Equipment. 2009. V. 603. № 12. P. 95.
Hammersley A.P. FIT2D V10.3: Reference Manual V4.0.: European Synchrotron Radiation Facility. 1998.
Wojdyr M. // J.Appl. Crystallography. 2010. V. 43. № 5. Part 1. P. 1126.
Цырульников П.Г., Иост К.Н., Шитова Н.Б., Темерев В.Л. // Катализ в промышленности. 2016. № 4. С. 20.
Иост К.Н., Темерев В.Л., Смирнова Н.С. и др. // Журн. прикл. химии. 2017. Т. 90. Вып. 6. С. 731.
Iost K.N., Borisov V.A., Temerev V.L. et al. // Surfaces and Interfaces. 2018. V. 12. P. 95.
Goethel P.J., Yang R.T. // J. Catal. 1988. V. 111. P. 220.
Goethel P.J., Yang R.T. // Ibid. 1988. V. 114. P. 46.
Jin-Sung Jang, Seongyop Lim, Sang-Kyung Kim et al. // J. Nanoscience and Nanotechnology. 2011. V. 11. P. 5775.
Rossetti I., Sordelli L., Ghigna P. et al. // Inorganic Chem. 2011. V. 50. № 8. P. 3757.
Sklovsky D., Nalimova V., Herold C. et al. // Carbon. 1995. V. 33. № 3. P. 329.
Шитова Н.Б., Цырульников П.Г., Шляпин Д.А. и др. // Журн. структур. химии. 2009. Т. 50. № 2. С. 283.
Таран О.П., Деком К., Полянская Е.М. и др. // Катализ в промышленности. 2013. № 1. С. 40.
De Panfilis S., Di Cicco A., Filipponi A. et al. // J. Synchrotron Radiation. 2001. V. 8. P. 764.
Дополнительные материалы отсутствуют.
Инструменты
Журнал физической химии