Журнал физической химии, 2020, T. 94, № 7, стр. 975-980
Фазовый переход жидкость–пар в системе медь–кальций
В. Н. Володин a, Ю. Ж. Тулеушев a, *
a РГП “Институт ядерной физики”
Алматы, Казахстан
* E-mail: yuriy.tuleushev@mail.ru
Поступила в редакцию 23.07.2019
После доработки 30.09.2019
Принята к публикации 15.10.2019
Аннотация
При испарения кальция из его сплава с медью при низком давлении 0.7–1.33 кПа в неравновесных условиях установлена возможность конденсации до 82% пара в жидкую фазу. На основании величин давления пара кальция и меди, определенных методом точек кипения, построена полная диаграмма состояния, включающая конденсированные и паровую фазу при атмосферном давлении и в вакууме 0.7 и 1.33 кПа. На основании границ фазовых переходов расплав–пар рассчитаны температуры кипения и состав конденсата, представленного кальцием, содержание меди в котором не превышает 3.95 × 10–2 мас. %, а температура кипения на 77–129°С превышает температуру плавления Са, и предполагает его пребывание в расплавленном состоянии. Таким образом, доказана принципиальная возможность осуществления процесса жидкость–пар–жидкость применительно к дистилляционному процессу получения кальция.
Использование системы кальций–медь при получении кальция электролизом расплавленного хлорида с последующей дистилляцией в вакууме [1] обусловил интерес исследователей к парожидкостным процессам, используемым в технологии [2–10]. Практически все работы, в том числе, с участием автора, посвящены определению тем или иным способом термодинамических констант кальция в сплавах с медью за исключением [9], где дана оценка состава паровой фазы над некоторыми медными сплавами.
К настоящему времени кальций, испаряющийся при низком давлении из расплавленного медно-кальциевого сплава, конденсируется на крышке реторты, охлаждаемой водой, в виде друз, имеющих значительную пористость и развитую поверхность. После охлаждения конденсат вместе с крышкой снимают с реторты и отделяют от крышки и тонкостенной железной обечайки, препятствующей контакту конденсата со стенкой реторты. Последнее сопровождается значительными затратами ручного труда и (редко) при наличии заметного количества натрия в конденсате – возгоранием кальция.
Конденсация кальция в жидкую фазу, его накопление и выгрузка после кристаллизации в виде слитка может устранить некоторые из указанных затруднений. В этой связи выполнено исследование, имеющее целью определение условий процесса испарения и жидкофазной конденсации пара кальция, построение полной диаграммы состояния системы кальций–медь, включающей фазовые переходы расплав–пар при атмосферном давлении и в вакууме, на основании которых возможно определение состава конденсата в условиях дистилляционного процесса при низком давлении.
ЭКСПЕРИМЕНТАЛЬНАЯ ЧАСТЬ
Для исследования в неравновесных условиях – при свободном испарении и последующей конденсации использована установка, включающая вертикальный испаритель и сочлененный с ним конденсатор, разделенный на 5 отдельных разъемных секций. Температуру измеряли с помощью термопар в испарителе и у основания каждой секции конденсатора. Степень испарения рассчитывали на основании убыли массы навески до и после эксперимента. Степень конденсации определяли на основании массы конденсата в каждой из секций конденсатора, отнесенной к общей массе конденсата, с понижением температуры конденсации у испарителя до минимальной у верхней секции. Испарение вели с неполной отгонкой кальция, как это имеет место в промышленных условиях.
Определение границ полей сосуществования расплава и пара осуществляли на основании величин давления насыщенного пара составляющих сплава. При этом за температуру кипения расплава принимали температуру, при которой сумма парциальных давлений пара кальция и меди равна атмосферному или другому, соответствующему условиям вакуумных технологий. Состав газовой фазы при температуре кипения над бинарным раствором состава (х1, х2 = 1 – х1) определяли как часть суммарного давления компонента над сплавом:
где y1 – концентрация 1-го компонента в паре, р1 и р2 – парциальные давления насыщенного пара первого и второго компонентов.В связи с тем, что полученные методом струи данные о величинах давления пара отличал весьма большой разброс экспериментальных значений, для определения величин давления насыщенного пара кальция, в дополнение к ранее найденным [7], использован метод точек кипения (изотермический вариант).
Схема установки для определения давления пара методом точек кипения приведена на рис. 1.
Рис. 1.
Схема установки для определения давления пара: 1 – тигель, 2 – подвеска, 3 – система измерения веса, 4 – система измерения давления, 5 – термопара, 6 – электропечь, 7 – кран-натекатель, 8 – канал эвакуации газов, 9 – канал подвода инертного газа, 10 – экран, 11 – кессон.
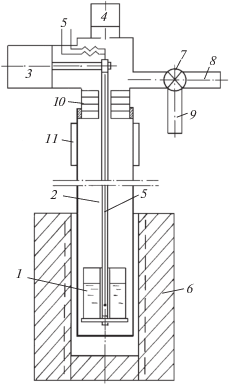
Установка представляет собой реторту, выполненную из двух частей: нижнюю из не легированной стали, размещенную в электропечи с автоматическим поддержанием температуры, и верхнюю – из термостойкого стекла. Внутри реторты из стали на полой подвеске установлен тигель с навеской сплава. Внутри подвески на уровне расплава в тигле размещен спай платина-платинородиевой (ППР) термопары.
Подвеска опирается на весы системы измерения убыли массы, размещенные в верхней части реторты. Части реторты сочленены с использованием резинового уплотнения, вынесенного вне зоны высоких температур. Нижняя и верхняя части реторты разделены экранами для снижения теплового потока из зоны высоких температур. В верхней части реторты расположены система измерения давления, каналы для эвакуации газов, заполнения аргоном и выходы концов термопары. Системы измерения убыли массы, давления, температуры имеют выход сигналов на многоточечный потенциометр с фиксацией измерений на диаграммной ленте.
Методика проведения экспериментов заключалась в следующем. Навеску сплава (до 2 г) помещали в стальной тонкостенный (200 мкм) тигель, который устанавливали на подвеске при разъединенной реторте вне зоны нагрева. Затем нижнюю часть реторты сочленяли с верхней. Из реторты дважды эвакуировали газы вакуумным насосом и заполняли аргоном. После этого помещали нижнюю часть реторты в изотермическую зону предварительно нагретой электропечи. Нагрев реторты осуществляли при избыточном давлении 2–5 кПа с открытой системой подвода инертного газа для подавления процесса испарения кальция и компенсации повышения давления в реторте из-за расширения газа при нагреве. При достижении навеской сплава заданной температуры, начинали эвакуацию аргона из объема реторты при поддержании постоянной температуры сплава (изотермический вариант). При этом синхронно фиксировали убыль массы навески (∆m) и изменение давления (Р). В связи с тем, что давление пара кальция на несколько порядков превышает давление пара меди при одинаковой температуре, считали, что в паре присутствует только кальций. Давление, при котором наблюдали резкое увеличение скорости испарения (убыли массы) (на примере сплава 0.7314 мол. долей Са при температуре 1233 K, рис. 2) считали равным давлению насыщенного пара кальция.
Рис. 2.
Изменение убыли массы сплава с понижением давления: 1 – до точки кипения, 2 – после точки кипения.
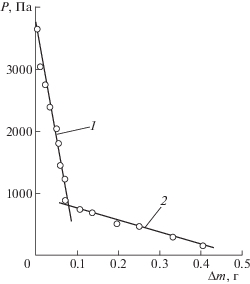
Численное значение величины давления пара определяли совместным решением уравнения, описывающих зависимость Р = f(∆m) до и после наблюдаемого излома на кривой (рис. 2). В данном случае давление и изменение массы сплава до излома кривой связаны зависимостью Р1 = = ‒37 087∆m + 3747, после излома – Р2 = –1910∆m + + 925.17, здесь: ∆m – убыль массы, г.
Совместным решением уравнений давление пара кальция для этих условий определено равным 772 Па. Следует отметить, что изменение убыли массы в зависимости от давления в точке кипения может носить не столь четко выраженный излом. В таком случае участки кривой, прилегающие к излому, аппроксимировали уравнениями второго порядка.
Температуру навески поддерживали с точностью ±5°С, давление измеряли с погрешностью ±67 Па (±0.5 мм рт. ст.) и параллельно контролировали барометром – анероидом.
В исследованиях использованы синтетические сплавы, приготовленные нагревом соответствующих количеств бидистиллированного кальция (99.9 мас. %) и меди (99.99 мас. %) до 1000°С (1273 K) в тонкостенных (200 мкм) тиглях из малоуглеродистой стали, с механическим перемешиванием при расплавлении в атмосфере очищенного аргона. После охлаждения тигель со слитка удаляли механической обработкой. Инертный газ очищали последовательным пропусканием через емкости, заполненные пентаоксидом фосфора, омедненным силикагелем при температуре 350°С и титановой губкой при 800–900°С. Слитки во избежание оксидирования хранили в емкостях, заполненных очищенным аргоном.
Нагреваемые части установок, контактируемые с паром кальция и сплавами его с медью, выполнены из малоуглеродистой стали. В качестве газа-носителя, в случае использования метода струи, и заполнителя в методе точек кипения использован аргон.
ОБСУЖДЕНИЕ РЕЗУЛЬТАТОВ
При рассмотрении изменения степени испарения (α) кальция из сплава в зависимости от давления (рис. 3) можно видеть, что α ожидаемо увеличивается с повышением температуры и снижением давления над сплавом. Причем влияние разрежения особенно заметно в пределах до 2–2.5 кПа.
Рис. 3.
Зависимость степени испарения кальция из сплава с медью от давления при температуре, °С: 1 – 1100, 2 – 1000, 3 – 900.
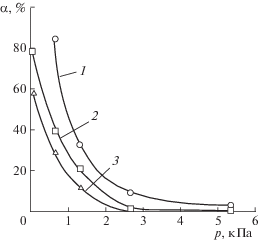
При анализе процесса конденсации пара кальция с понижением температуры по зонам (рис. 4) заметно различие степени конденсации (β) пара щелочно-земельного металла, дистиллированного при разной температуре, при незначительном влиянии изменения давления в пределах 0.07–1.33 кПа. Рассматривая β при температуре плавления кальция (842°С – вертикальная пунктирная линия) можно видеть, что количество жидкой фазы в конденсате достигает ∼70% (определено графически) при температуре дистилляции 1000°С и ∼82% – при 1100°С. Последнее свидетельствует о том, что, изменяя температуру дистилляции кальция и давление, при соответствующем конструктивном оформлении процесса возможна превалирующая конденсация пара в жидкую фазу.
Рис. 4.
Зависимость степени конденсации кальция от температуры в конденсаторе: при температуре испарения, °С: 1, 2 – 1100, 3–5 – 1000, при давлении, кПа: 1, 4 – 0.7, 2, 5 – 1.33, 3 – 0.07.
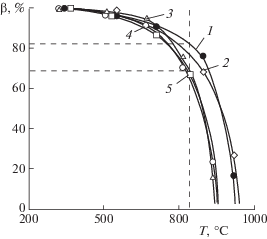
Более полную информацию о переходе жидкость–пар и составе конденсата можно получить на основании определения границ полей сосуществования расплава и паровой фазы в равновесных условиях при атмосферном давлении и в вакууме.
Данные по определению давления насыщенного пара элементного кальция ($p_{{{\text{Ca}}}}^{{\text{o}}}$), определенные нами, соответствуют зависимости:
$\ln p_{{{\text{Ca}}}}^{{\text{o}}}$ = 22.046 – 18 483T–1, (здесь и далее: Т – температура, K) откуда температура кипения при атмосферном давлении определена равной 1484°С (1757 K). Полученные величины значительно отличаются от данных исследования [11] и хорошо сопадают с данными, приведенными в работах [12, 13]. В частности, температура кипения кальция, определенная аналогичным образом [13], соответствует 1494°С. Хорошее согласование величин давления пара кальция по нашим и данным источников [12, 13] свидетельствует о достаточной надежности выполненных определений.
Парциальное давление насыщенного пара меди (рCu) над расплавами с кальцием найдено численным интегрированием уравнения Гиббса–Дюгема с использованием вспомогательной функции, предложенной Даркеном [14], как: $p_{{{\text{Cu}}}}^{{}} = p_{{{\text{Cu}}}}^{{\text{o}}}{{\gamma }_{{{\text{Cu}}}}}{{x}_{{{\text{Cu}}}}}$, где ${{\gamma }_{{{\text{Cu}}}}}$ найдено из выражения:
(1)
$\ln {{\gamma }_{{{\text{Cu}}}}} = - \frac{{\ln {{\gamma }_{{{\text{Ca}}}}}{{x}_{{{\text{Ca}}}}}{{x}_{{{\text{Cu}}}}}}}{{x_{{{\text{Cu}}}}^{2}}} + \int\limits_{{{x}_{{{\text{Ca}}}}} = 0}^{{{x}_{{{\text{Ca}}}}}} {\frac{{\ln {{\gamma }_{{{\text{Ca}}}}}}}{{{{{(1 - {{x}_{{{\text{Cu}}}}})}}^{2}}}}} d{{x}_{{{\text{Ca}}}}}.$Давление насыщенного пара над жидкой элементной медью заимствованы из работы [15], где выполнена коррекция справочных данных с целью согласования температуры и теплоты испарения с температурной зависимостью равновесного давления пара простых веществ, усреднено и преобразовано нами к виду: $\ln p_{{{\text{Cu}}}}^{{\text{o}}}$ = 24.359 – ‒ 36 625T–1.
Данные по давлению насыщенного пара кальция (рCa) аппроксимированы формальной температурно-концентрационной полиномиальной зависимостью:
(2)
$\begin{gathered} \ln {{p}_{{{\text{Ca}}}}} = ( - 6942.5x_{{{\text{Ca}}}}^{3} + 3201.5x_{{{\text{Ca}}}}^{2} + \\ + \;11489{{x}_{{{\text{Ca}}}}} - 26231){{T}^{{ - 1}}} - 2.54x_{{{\text{Ca}}}}^{3} + \\ + \;11.311x_{{{\text{Ca}}}}^{2} - 14.065{{x}_{{{\text{Ca}}}}} + 27.34 + \ln {{x}_{{{\text{Ca}}}}}, \\ \end{gathered} $(3)
$\begin{gathered} \ln {{p}_{{{\text{Cu}}}}} = (6942.5x_{{{\text{Cu}}}}^{3} - 28040x_{{{\text{Cu}}}}^{2} + \\ + \;38187.5{{x}_{{{\text{Cu}}}}} - 53715 - 2935.5\ln {{x}_{{{\text{Cu}}}}}){{T}^{{ - 1}}} + \\ + \;2.54x_{{{\text{Cu}}}}^{3} - 0.119x_{{{\text{Cu}}}}^{2} - 8.319{{x}_{{{\text{Cu}}}}} + \\ + \;30.257 + 1.937\ln {{x}_{{{\text{Cu}}}}}. \\ \end{gathered} $Экспериментально определенные и расчетные величины давления насыщенного пара кальция, а также погрешность описания приведены в табл. 1.
Таблица 1.
Давление пара кальция в системе кальций–медь
[Ca], ат. доля | Т, K | р1, Па | р2, Па | Δ, % |
---|---|---|---|---|
0.8718 | 1173 | 507 | 485 | +4.53 |
1263 | 1361 | 1481 | –8.10 | |
1323 | 2372 | 2866 | –17.24 | |
1373 | 5188 | 4754 | +9.13 | |
0.7314 | 1163 | 228* | 272 | –16.18 |
1173 | 273* | 312 | –12.50 | |
1183 | 364* | 357 | +1.96 | |
1213 | 535 | 530 | +0.94 | |
1223 | 693 | 601 | +15.31 | |
1233 | 772 | 681 | +13.36 | |
1268 | 1098 | 1039 | +5.68 | |
1273 | 917 | 1101 | –16.71 | |
1278 | 1168 | 1167 | +0.08 | |
1293 | 1301 | 1384 | –6.00 | |
1338 | 2184 | 2259 | –3.32 | |
1373 | 3335 | 3234 | +3.12 | |
1383 | 3787 | 3571 | +6.05 | |
1403 | 3911 | 4336 | –9.80 | |
0.6132 | 1193 | 267* | 240 | +11.25 |
1343 | 1673 | 1499 | +11.61 | |
1378 | 1921 | 2170 | –11.47 | |
1390 | 2443 | 2454 | –0.45 | |
1393 | 2833 | 2529 | +12.02 | |
0.4736 | 1193 | 105* | 116 | –9.48 |
1293 | 477* | 448 | +6.47 | |
1308 | 507 | 539 | –5.94 | |
1323 | 603 | 645 | –6.51 | |
1343 | 807 | 816 | –1.10 | |
1373 | 1261 | 1144 | +10.23 | |
1388 | 1325 | 1348 | –1.71 | |
1393 | 1341 | 1422 | –5.70 | |
0.3917 | 1273 | 224* | 236 | –5.08 |
1323 | 413* | 449 | –8.02 | |
1363 | 552 | 726 | –23.97 | |
1373 | 780 | 815 | –4.29 | |
0.2186 | 1273 | 115* | 109 | +5.50 |
1323 | 217* | 219 | –0.91 | |
1363 | 435* | 371 | +17.25 | |
1393 | 554 | 539 | +2.78 |
Общая погрешность измерений определена как сумма погрешностей независимых измерений: температуры – 1%, взвешивания – 0.1%, давления 0.5%, аппроксимации экспериментальных данных – 7.99%, равной 9.59%.
На основании температурно-концентрационных зависимостей величин парциального давления насыщенного пара кальция (2) и меди (3) рассчитаны границы полей сосуществования жидкости и пара системы Ca–Cu с дополнением диаграммы состояния [16, 17] фазовыми переходами жидкость−пар при атмосферном и низких давлениях (рис. 5).
На диаграмме состояния отображены три поля сосуществования расплава и пара (Ж + П) при атмосферном давлении (101.3 кПа) и в вакууме 1.33 и 0.7 кПа, то есть, для давлений, при которых реализован процесс неравновесной конденсации пара кальция. Поля (Ж + П) в вакууме частично накладываются на область сосуществования расплава и пара при атмосферном давлении.
В промышленном производстве дистилляцию кальция осуществляют из медно-кальциевого сплава, содержащего 60–65 мас. % (70.40–74.65 ат. %) Са, до остаточного содержания 30–35 мас. %, иногда 20 мас. % (28.38 ат. %) [1]. При нанесении максимального интервала изменения концентрации кальция (в атомных долях) в процессе испарения кальция на диаграмму состояния видно, что температура кипения богатого по щелочноземельному металлу (74.65 ат. %), рассчитанная по уравнениям (2) и (3) составляет 1012°С при давлении 1.33 кПа и 958°С – при 0.7 кПа, а концентрация меди в равновесной паровой фазе, и, следовательно, в конденсате составляет 1.07 × 10–4 и 5.34 × 10–5 мас. % соответственно. Причем, температура кипения конденсата такого состава на 77°С выше температуры плавления кальция, что предполагает пребывание последнего в жидкой фазе.
Аналогично рассчитанная температура кипения обедненного по кальцию сплава (28.38 ат. %) составила 1179°С при давлении 1.33 кПа и 1022°С – при 0.7 кПа. Конденсированная паровая фаза, в этом случае, будет содержать 3.95 × 10–2 и 2.64 × × 10–2 мас. % Сu соответственно. Температура кипения конденсата также выше температуры плавления кальция на 129°С.
Из изложенного вытекает принципиальная возможность реализации процесса испарения кальция из медно-кальциевого расплава с последующей конденсацией паровой фазы по схеме жидкость–пар–жидкость.
Таким образом, в результате проведения процесса испарения кальция из его сплава с медью при низком давлении в неравновесных условиях установлена возможность преобладающей конденсации пара в жидкую фазу.
Для анализа процесса испарения и конденсации пара кальция в равновесных условиях на основании величин давления насыщенного пара компонентов построена полная диаграмма состояния системы кальций–медь, включающая конденсированное и парообразное состояние при атмосферном давлении и в вакууме 1.33 и 0.7 кПа.
На основании определенных границ фазовых переходов расплав–пар рассчитаны температуры кипения сплавов вначале и конце дистилляционного процесса в вакууме и состав конденсата, представленного практически элементным кальцием, температура кипения которого на 77–129°С превышает температуру плавления щелочноземельного металла, и предполагает его пребывание в расплавленном состоянии.
Таким образом, доказана принципиальная возможность осуществления процесса жидкость–пар–жидкость применительно к дистилляционному процессу получения кальция.
Список литературы
Доронин Н.А. Кальций. М.: Госатомиздат. 1962. 192 с.
Богословский С.С., Крестовников А.Н., Лысенко Н.Л. // Изв. АН СССР. Металлы. 1969. № 5. С. 51.
Ram A. Sharma. // J. Phys. Chem. 1970. V. 74. № 22. P. 3896.
Бурылев Б.П. Термодинамические и термохимические константы. М.: Наука. 1970. С. 32.
Djamshidi B., Notin M., Gachon J.Cl., Hertz J. // Scr. met. 1980. V. 14. № 5. P. 493.
Быков А.С., Лепинских Б.М., Востряков А.А. // Журн. физ. химии. 1983. Т. 57. № 4. С. 1000.
Володин В.Н., Василец С.Г., Терликбаев М.А., Шадаев М.Т. // Компл. исп. мин. сырья. 1989. № 2. С. 38.
Володин В.Н., Терликбаев М.А., Василец С.Г. // Компл. исп. мин. сырья. 1989. № 9. С. 24.
Кишкопаров Н.В., Моисеев Г.К., Фришберг И.В. Термодинамическая оценка состава газовой фазы над некоторыми медными сплавами. Свердловск. 1984. 8 с. Деп. в ВИНИТИ 06.04.84. № 2092.
Быков А.С., Востряков А.А. Термодинамические и молекулярно-кинетические исследования металлических и шлаковых расплавов. Свердловск, 1985. С. 44.
Schürmann E., Schmid R. //Arch. Eisenhüttenw. 1975. Bd. 46. № 12. S. 773.
Глазов В.М., Лазарев В.Б., Жаров В.В. Фазовые диаграммы простых веществ. М.: Наука, 1980. 63 с.
Yong Nian Dai, Bing Yang. Vacuum Metallurgy of Non-Ferrous Metals. Beijing: Metallurgical Ind. Press, 2000. V. 3. 547 p.
Rao Y.K. // Met. Trans. 1983. V. B14. № 1–4. P. 308.
Малышев В.П., Турдукожаева А.М., Оспанов Е.А., Саркенов Б. Испаряемость и кипение простых веществ. М.: Научный мир, 2010. 304 с.
Chakrabarti D.I., Laughlin D.E. // Bull. of Alloy Phase Diagrams. 1984. V. 5. № 6. P. 570.
Диаграммы состояния двойных металлических систем / Под ред. Лякишева Н.М. М.: Машиностроение, 1996. Т. 1. 992 с.
Дополнительные материалы отсутствуют.
Инструменты
Журнал физической химии