Журнал физической химии, 2021, T. 95, № 3, стр. 300-311
Получение микро- и наночастиц с помощью сверхкритических флюидных технологий
А. М. Воробей a, *, О. О. Паренаго a, b
a Российская академия наук, Институт общей и неорганической химии им. Н.С. Курнакова
Москва, Россия
b Московский Государственный Университет имени М.В. Ломоносова, Химический факультет
Москва, Россия
* E-mail: vorobei@supercritical.ru
Поступила в редакцию 02.09.2020
После доработки 02.09.2020
Принята к публикации 16.09.2020
Аннотация
Систематизированы и проанализированы литературные данные, посвященные фундаментальному исследованию и практическому применению процессов получения микро- и наночастиц с использованием сверхкритических флюидов (СКФ). Обзор методов микронизации, основанных на использовании СКФ, разделен на группы в соответствии с ролью, которую играет СКФ в процессе: в большинстве случаев он может быть растворителем (быстрое расширение сверхкритических растворов – RESS), антирастворителем (сверхкритическое антисольвентное осаждение – SAS) или растворенным веществом (частицы, формируемые из насыщенного газом раствора – PGSS). Отдельное внимание уделено менее освещенным в литературе методам, в которых СКФ – сорастворенное вещество (SAA, CAN-BD, DELOS). Подробно рассмотрены основные преимущества, ограничения, а также применимость для конкретного круга веществ, каждого из подходов. Показано, что спектр рассматриваемых субстанций не ограничивается наиболее хорошо описанными фармацевтическими объектами, а, наоборот, сильно расширен для максимально полного охвата возможных применений СКФ-микронизации. Основной акцент сделан на работы последнего десятилетия.
Благодаря ряду уникальных свойств сверхкритических флюидов (СКФ) в последнее время их активно используют для создания микро-, субмикро- и наночастиц. Основное преимущество СКФ связано прежде всего с возможностью проведения процесса без использования токсичных органических растворителей, либо с простотой элиминирования их остатков в получаемом продукте. Кроме того, в отличие от многих традиционных способов микронизации, дополнительный бонус СКФ-методов – широкие возможности по тонкому управлению характеристиками получаемых частиц. Чаще всего требуется создать частицы заданной морфологии с определенным распределением по размеру, однако, к продукту могут также предъявляться дополнительные требования и по другим характеристикам, например, степени кристалличности, полиморфному составу, структуре поверхности и др. В настоящее время СКФ-подходы применяют для микронизации различных субстанций во многих сферах, таких как создание катализаторов, красителей, энергонасыщенных материалов, в фармацевтической и пищевой отраслях и т.д. При этом одна из главных задач – разработка систематической процедуры дизайна и масштабирования указанных процессов. Это требует не только эмпирических знаний, но и информации об основах методов и глубокого понимания влияния параметров конкретного процесса на характеристики получаемого продукта. Недостаток таких знаний особенно сильно ощущается в российской научной литературе. Цель представленной работы – обзор опубликованной литературы, посвященной фундаментальному исследованию и практическому применению процессов получения микро- и наночастиц с использованием СКФ, а также систематизация и анализ накопленных данных.
Методы микронизации можно разделить на два основных подхода – нисходящие (“top down”) и восходящие (“bottom up”). Первый подход представляет собой прямое измельчение исходных частиц большого размера, в основном, механическими способами. Второй подход предполагает растворение микронизуемой субстанции в подходящем растворителе и кристаллизацию микрочастиц из этого раствора. К традиционным методам подхода “bottom up” относятся распылительная сушка, криосушка, эмульсионные методы и осаждение жидким антирастворителем. Несмотря на обилие традиционных технологий микронизации, все они имеют существенные недостатки и ограничения, связанные с термической и механической деструкцией микронизуемого вещества, использованием токсичных растворителей, большими потерями при обработке и т.д. По этой причине в последние десятилетия в рамках подхода “bottom up” активно развиваются альтернативные технологии, связанные с использованием сверхкритических флюидов (СКФ). Они характеризуются отсутствием или ограниченным использованием растворителей, расширенными возможностями по контролю процесса, а также возможностью эффективно получать микро-, субмикро- и наночастицы с узким распределением по размеру [1]. Методы микронизации, основанные на использовании СКФ, можно разделить в соответствии с ролью, которую играет СКФ в данном процессе. В подавляющем большинстве случаев СКФ может быть растворителем, антирастворителем или растворенным веществом.
БЫСТРОЕ РАСШИРЕНИЕ СВЕРХКРИТИЧЕСКИХ РАСТВОРОВ (RESS)
Метод быстрого расширения сверхкритических растворов (RESS – The Rapid Expansion of Supercritical Solutions) основан на способности сверхкритического флюида (чаще всего СО2) растворять твердые вещества. Принципиальная схема, иллюстрирующая типичную установку для проведения процесса RESS, приведена на рис. 1. Суть подхода RESS заключается в насыщении сверхкритического флюида микронизуемым твердым субстратом с последующим распылением получаемого раствора в сосуд с низким давлением (7). Сброс получаемого раствора через нагретое сопло в сосуд с низким давлением приводит к потере растворяющей способности флюида. Растворенное вещество быстро кристаллизуется в виде частиц малого размера, которые собирают из газового потока. Морфология получаемого материала, степень кристалличности, а также размер частиц зависят от химической структуры вещества и параметров RESS (температура, скорость сброса давления, геометрия сопла и др.) [2].
Рис. 1.
Типичная схема установки для проведения процесса RESS: 1 – источник СО2, 2 – охлаждающий теплообменник, 3 – насос СО2, 4 – нагреватель, 5 – сосуд с мешалкой (для растворения в сверхкритическом флюиде), 6 – кран, 7 – сосуд-сборник.
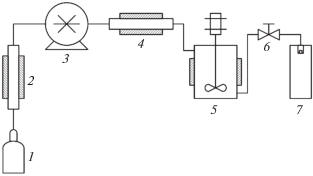
Концепция метода RESS далеко не нова: она впервые описана Ханнеем и Хогартом [3], почти 140 лет назад. Однако, активное применение и разработка этого метода начались только после работ Крукониса [4] и в особенности научной группы института Баттеля [5–9], которые описали и моделировали характер расширения сверхкритического флюида и процесс нуклеации.
Метод RESS позволяет получать не только нано- [10, 11] и микрочастицы [12, 13], но и волокна [14] и пленки [15]. Кроме того, при получении пленок существует разновидность RESS, в которой распыление сверхкритического раствора производят на нагретую подложку. При этом осаждающийся из раствора в сверхкритическом флюиде субстрат разлагается. Такой метод применяли для получения пленок серебра, меди, никеля [16]. В качестве растворителя, помимо наиболее широко распространенного в СКФ-технологиях СО2, в методе RESS используют N2O, пентан, диэтиловый эфир [16], пропан [8], этанол, воду [6], трифторметан [17], дифторхлорметан [18], аммиак, метанол, ацетон [19].
Очевидное преимущество метода RESS в его классическом варианте – полное отсутствие растворителя в получаемом продукте. С другой стороны, растворяющей способности сверхкритического флюида для большего числа веществ может быть недостаточно, что обусловливает необходимость использования сорастворителя [20]. Альтернативой может быть использование метода RESS-SC (Rapid Expansion of Supercritical Solution with Solid Cosolvent – быстрое расширение сверхкритического раствора с твердым сорастворителем). Суть метода RESS-SC состоит в том, что помимо целевого микронизуемого вещества в сверхкритическом флюиде растворяют также твердый сорастворитель (например, ментол), который приводит к увеличению растворимости микронизуемой субстанции в получаемом сверхкритическом растворе [21]. В работе [22] показано, что при использовании ментола в качестве сорастворителя можно увеличить растворимость гризеофульвина в сверхкритическом СО2 в 28 раз. Кроме того, твердый сорастворитель не только увеличивает растворимость в сверхкритическом СО2, но и препятствует росту образующихся частиц за счет подавления агломерации. RESS-SC позволяет получать микронизованные частицы гризеофульвина размером 50–250 нм, что в 10 раз меньше чем при использовании RESS без твердого сорастворителя.
Интересной модификацией метода RESS является RESOLV (Rapid Expansion of supercritical solution into liquid SOLVent – быстрое расширение сверхкритического раствора в жидкий растворитель), который основан на распылении сверхкритического раствора в жидкость, содержащую стабилизатор. Использование данной жидкости позволяет, во-первых, замедлить рост осаждаемых частиц. Во-вторых, открывается возможность совмещения процесса RESS и химической реакции за счет взаимодействия между получаемыми частицами и веществами в жидкой фазе. В работе [23] в раствор Na2S в этаноле или воде проводили распыление раствора Cd(NO3)2 в сверхкритическом аммиаке. Таким образом, методом RESS получали частицы CdS размером 3.3 нм. Раствор, в который производили распыление, также содержал поли (N-винил-2-пирролидон), который играл роль стабилизатора наночастиц. Аналогично, в работе [19] при использовании Pb(NO3)2 в сверхкритическом аммиаке получены частицы PbS размером 4 нм.
Близок по своей сути к процессу RESS-метод CPF (Concentrated Powder Form technology – технология концентрирования с помощью порошкообразных форм) [24]. На рис. 2 приведена схема процесса CPF. В методе CPF жидкость и сверхкритический флюид смешиваются с помощью статического смесителя (1), и сформированный таким образом раствор распыляется через сопло в сосуд с пониженным давлением (2). Одновременно через этот же сосуд пропускают аэрозоль вещества-носителя в потоке инертного газа. При расширении жидкость рассеивается в виде очень мелких капель, которые смешиваются с порошком [25]. Процесс CPF позволяет получать порошки, наполненные жидкостью, с концентрацией жидкости вплоть до 80–90 мас. % [26]. Описанная технология уже применяется в пищевой промышленности, например, в производстве специй с помощью метода CPF распыляются экстракты сельдерея, лавра, орегано, паприки и т.д. [27].
Главное ограничение метода RESS – он применим только к веществам, которые достаточно хорошо растворимы в выбранном сверхкритическом флюиде. К сожалению, большая часть полярных и/или высокомолекулярных веществ имеют пренебрежимо малую растворимость в СК-СО2, который наиболее часто используется в качестве СКФ. Использование же сорастворителя в RESS, так же, как и в RESOLV, приводит к потере основного преимущества RESS: отсутствию растворителя в конечном продукте. Соответственно такие модификации метода RESS требуют дополнительных трудозатратных стадий очистки продукта от растворителя [28].
СКФ – РАСТВОРЕННОЕ ВЕЩЕСТВО (PGSS)
В методе PGSS (Particles from Gas Saturated Solution – частицы, формируемые из насыщенного газом раствора) сжатый газ (например, CO2) растворяют в расплавленном веществе, и затем через распылительное сопло быстро сбрасывают давление, что приводит к формированию частиц. В отличие от метода RESS, PGSS не требует полного растворения вещества в сверхкритическом флюиде, что дает возможность проводить процесс PGSS для гораздо большего числа веществ. Особенно актуально его использование для полимеров, которые поглощают большие количества СО2 (10–40 мас. %!), что приводит либо к набуханию, либо к разжижению полимера при существенно меньшей температуре плавления, чем при обычных условиях (на ~10–50°C меньше) [29].
Метод PGSS впервые описан Грейзером [30] и применен для рекристаллизации красителей из тонкоизмельченных необработанных органических пигментов. Сфера применимости метода PGSS ограничена, так как он фактически применим лишь для полимеров, способных набухать в CO2. Однако, даже для полимеров, способных набухать в CO2, PGSS часто оказывается неприменим, так как не всегда удается достичь существенного понижения температуры плавления. Кроме того, для проведения процесса PGSS часто нужна повышенная температура, которая может приводить к изменениям химической структуры микронизуемых веществ. Таким образом, для веществ, чувствительных к повышенной температуре, метод PGSS также малоприменим [31, 32]. К недостаткам метода можно отнести и достаточно большой разброс получаемых частиц по размерам и трудность контроля над ним.
Тем не менее, метод имеет ряд достоинств по сравнению с другими методами, основанными на сверхкритических флюидах. Так, расход углекислого газа в методе PGSS значительно меньше, чем в RESS. Кроме того, возможно непрерывное проведение процесса PGSS, в отличие от RESS. В отличие от метода SAS (см. ниже), метод PGSS не требует использования органических растворителей.
СКФ – СОРАСТВОРЕННОЕ ВЕЩЕСТВО (SAA, CAN-BD, DELOS)
Методы, в которых СО2 используется в качестве сорастворенного вещества имеют много общего с микронизацией распылительной сушкой: СКФ и раствор смешиваются и затем распыляются в высушивающую среду. Такие методы очень привлекательны, так как могут быть применены к водорастворимым веществам, которые сложно обработать другими СКФ-методами в отсутствие органических растворителей. Распылению также содействует инертный газ (чаще всего азот), широко используемый в распылительной сушке.
Для микронизации гидрофильных веществ Сиверсом [33–36] был предложен метод CAN-BD (Carbon dioxide Assisted Nebulization-Bubble Dryer – распылительная сушка с использованием диоксида углерода). В процессе CAN-BD в тройнике малого объема (<0.1 мкл) путем смешения сверхкритического СО2 и водного раствора микронизуемой субстанции создают двухфазную смесь. Двухфазная система проходит через короткий капилляр (50–70 мм) и быстро распыляется в сосуд с давлением, близким к атмосферному. Через тот же сосуд одновременно пропускают поток подогретого инертного газа, который испаряет растворитель из образующихся капель, и приводит к образованию микрочастиц. К недостаткам описанного метода относится плохая воспроизводимость, по всей видимости, связанная со значительными перепадами давления внутри распылительного капилляра и тройника малого объема. Используемая в методе CAN-BD конфигурация прибора обеспечивает малое время смешения потоков флюида и раствора (0.01–0.1 с).
Учитывая описанный недостаток метода CAN-BD, Ревершоном и др. был разработан процесс SAA (Supercritical Assisted Atomization – распыление с помощью сверхкритического флюида) [37, 38]. На рис. 3 приведена схема процесса SAA. Вместо тройника малого объема в процессе SAA используется термостатируемая камера насыщения (6), обеспечивающая не только лучшую степень смешивания потоков, но и растворение СО2 до равновесной концентрации в растворе. Процесс широко применяется для микронизации фармацевтических препаратов [39–41], катализаторов [42], полимеров [43–45], красителей [46]. В качестве растворителя микронизуемых веществ применяют воду, метанол, ацетон. Существуют примеры реализации SAA и на пилотном оборудовании [47].
Рис. 3.
Схема установки для проведения процесса SAA: 1 – источник СО2, 2 – охлаждающий теплообменник, 3 – измеритель потока, 4 – насос СО2, 5 – нагреватель, 6 – сосуд насыщения, 7 – источник инертного газа, 8 – кран, 9 – нагреватель, 10 – раствор микронизуемого вещества, 11 – растворный насос, 12 – сосуд осаждения, 13 – конденсатор, 14 – регулятор давления.
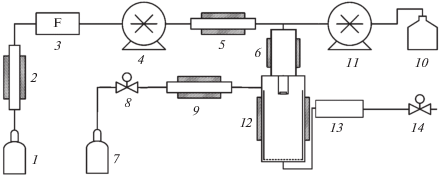
Распыление в SAA является двухстадийным. На первой стадии протекает формирование капель на выходе из форсунки, вызванное пневматическим эффектом. На второй стадии происходит распыление за счет расширения СК-флюида из капель, образованных на первой стадии. Таким образом, происходит образование вторичных капель [48].
Ограничение метода SAA: для термолабильных веществ он малоприменим. Если сброс давления производят в сосуд, находящийся при атмосферном давлении, то требуются достаточно высокие температуры для полного удаления растворителя из продукта. По этой причине для термолабильных веществ может быть уместно применение модификации SAA, в которой сосуд осаждения подключен к вакуумному насосу. Это позволяет проводить процесс при давлении ниже атмосферного, что дает возможность существенно уменьшить температуру. Тем самым становится возможным применение метода SAA для полимеров с низкой температурой стеклования и белков [49].
Разработана также модификация метода SAA-HCM (Supercritical fluid Assisted Atomization introduced by Hydrodynamic Cavitation Mixer – распыление с помощью сверхкритического флюида со встроенным кавитационным смесителем). Данное устройство используется для интенсификации массообмена между раствором и СК-флюидом, что приводит к осаждению частиц меньшего размера с более узким распределением [50–53].
Еще один процесс, в котором СО2 играет роль сорастворенного вещества, – DELOS (Depressurization of an Expanded Liquid Organic Solution – сброс давления в расширенном растворе в органическом растворителе) [54]. Суть метода состоит в том, что СО2 растворяют в растворе микронизуемого вещества, а затем резко сбрасывают полученную смесь в сосуд с атмосферным давлением. Расширение СО2 за счет перехода из СК-флюида в газообразное состояние при сбросе давления приводит к очень быстрому, но равномерному по объему, охлаждению. Как следствие, раствор находится в ситуации огромного пересыщения, при котором наблюдается образование частиц субмикронного и микронного размера. Процесс DELOS успешно применялся для микронизации красителей [55] и фармацевтических препаратов [56].
СКФ – АНТИРАСТВОРИТЕЛЬ (SAS, GAS, ASES, SEDS, PCA)
СКФ используется в качестве антирастворителя (осадителя) в достаточно большом количестве различных процессов, однако по своей сути они схожи во всех случаях. Необходимое условие протекания всех таких процессов – нерастворимость в сверхкритическом флюиде растворенного вещества и растворимость в нем жидкого растворителя. По этой причине смешивание раствора с сверхкритическим флюидом приводит к пересыщению раствора и выпадению в осадок растворенного вещества. Благодаря высоким скоростям массопереноса взаимное растворение растворителя и сверхкритического флюида происходит очень быстро, что обеспечивает формирование микро-, субмикро- и наночастиц. Наиболее существенным отличием в проведении процессов, в которых СКФ используют в качестве антирастворителя, является то, как проводят процесс – в полунепрерывном режиме или стационарно.
СТАЦИОНАРНЫЙ ПРОЦЕСС СВЕРХКРИТИЧЕСКОГО АНТИСОЛЬВЕНТНОГО ОСАЖДЕНИЯ (GAS)
В стационарном процессе (GAS: Gas AntiSolvent precipitation – осаждение в газофазном антирастворителе) осадительный сосуд заполняют определенным количеством раствора микронизуемого вещества. К раствору добавляют сверхкритический антирастворитель до необходимого давления, что приводит к объемному расширению жидкости и быстрому уменьшению плотности. Происходит резкое пересыщение и формирование малых частиц с узким распределением по размеру. На рис. 4 приведена схема, иллюстрирующая процесс GAS. Антирастворитель может подаваться сверху либо снизу осадительного сосуда.
Важным преимуществом процесса GAS является то, что, изменяя скорость добавления антирастворителя, исходную концентрацию субстанции в растворе и температуру, можно контролировать скорость зародышеобразования и роста частиц, и таким образом морфологию и размер осаждаемых частиц. В процессе GAS объемное расширение жидкости зависит от температуры, давления, типа растворителя и антирастворителя, и скорости перемешивания. Объемное расширение жидкости в свою очередь напрямую определяет степень пересыщения и соответственно распределение частиц по размеру [57]. Метод GAS позволяет получать частицы от сотен нанометров [58] до сотен микрон [59].
Помимо ввода антирастворителя в раствор, возможно также проведение процесса GAS, в котором сначала заполняют камеру осаждения антирастворителем, а затем производят (не непрерывно, в отличие от SAS) распыление раствора. Ключевым отличием между данными разновидностями метода GAS состоит в том, что в первом случае осаждение происходит в фазе, насыщенной жидкостью, тогда как во втором – сверхкритическим флюидом [60].
Недостаток метода GAS в том, что процесс не проводится при фиксированных неизменяющихся параметрах, поэтому сложно оценить влияние каждого параметра на свойства конечного продукта. Во-вторых, для промышленного использования периодические процессы, к которым можно отнести GAS, часто менее приемлемы по сравнению с непрерывными. Кроме того, в отличие от RESS и PGSS, в методе GAS необходимо использование органических растворителей. Соответственно после проведения процесса осаждения сосуд промывают дополнительным количеством антирастворителя для удаления остатков растворителя из осажденного порошка. Если стадия промывки отсутствует или время промывки недостаточно, то остатки растворителя могут приводить к перерастворению получаемых частиц.
ПОЛУНЕПРЕРЫВНЫЙ ПРОЦЕСС СВЕРХКРИТИЧЕСКОГО АНТИСОЛЬВЕНТНОГО ОСАЖДЕНИЯ (SAS)
В полунепрерывном режиме раствор и антирастворитель постоянно смешивают в осадительном сосуде в параллельных потоках или противотоком. Наиболее часто используемое на сегодняшний день название метода – SAS (Supercritical AntiSolvent precipitation, сверхкритическое антисольвентное осаждение). Однако, часто используют аббревиатуру ASES (Aerosol Solvent Extraction System – экстракция растворителя из аэрозолей). Суть ASES аналогична методу SAS [61–63]. На рис. 5 представлена типичная схема установки для проведения сверхкритического антисольвентного осаждения в полунепрерывном режиме.
Рис. 5.
Схема установки для проведения сверхкритического антисольвентного осаждения: 1 – источник СО2, 2 – охлаждающий теплообменник, 3 – расходомер Кориолиса, 4 – насос СО2, 5 – нагреватель, 6 – раствор микронизуемого вещества, 7 – растворный насос, 8 – осадительный сосуд, 9 – автоматический регулятор давления, 10 – циклонный сепаратор, 11 – ручной регулятор давления, 12 – сливной кран.
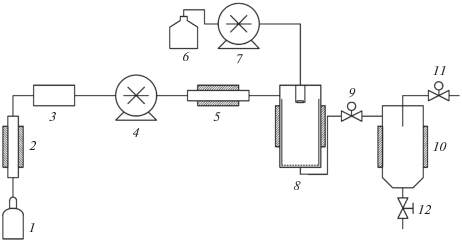
Метод SAS широко применяется для микронизации различных фармацевтических субстанций [64–67], при создании частиц катализаторов [68–71], энергонасыщенных материалов [72, 73], прекурсоров сверхпроводников [74], полимеров [75, 76], пигментов [46, 77] и т.д. В случае некоторых процессов микронизации методом SAS проведено успешное масштабирование на пилотном оборудовании [78–80].
Важную роль в полунепрерывном варианте метода сверхкритического антисольвентного осаждения играют различные способы интенсификации массообмена между антирастворителем и раствором микронизуемого вещества. Так, Робертсон и др. [81] использовали устройство предварительного смешения, в котором раствор микронизуемого вещества смешивается с сверхкритическим СО2 перед вводом в распылительный сосуд.
Во многих случаях при реализации метода SAS используют различные модификации распылительного сопла. Оно предназначено для разбивания струи жидкости и формирования маленьких капель. Наиболее широко применяют метод SEDS (Solution Enhanced Dispersion by Supercritical fluids – диспергирование раствора, усовершенствованное сверхкритическими флюидами), представляющий собой модификацию метода SAS, в которой для распыления раствора используют коаксиальное сопло [82]. Типичная схема коаксиального сопла приведена на рис. 6. Коаксиальное сопло представляет собой два соосно расположенных капилляра, расположенных один в другом. Обычно, по внутреннему капилляру пропускают поток раствора микронизуемого вещества, а по внешнему – поток антирастворителя [83, 84]. Однако, используют и более сложные конфигурации сопел, включающие более двух капилляров [83], а также дополнительные приспособления внутри капилляров [85, 86].
Для дополнительного уменьшения размера получаемых методом SAS частиц используют также метод SAS-EM (Supercritical AntiSolvent with Enhanced Mass transfer – сверхкритическое антисольвентное осаждение с улучшенным массопереносом), в котором к сосуду осаждения прикладывают ультразвуковое воздействие. Впервые метод предложен для микронизации в стационарном режиме (GAS). Таким образом получали частицы гризеофульвина и лизоцима размером менее 130 нм и ~190 нм соответственно [87, 88]. В дальнейшем метод SAS-EM применяли и в полунепрерывном режиме [89], в том числе и в варианте совмещения с коаксиальным соплом (SEDS-EM) [90].
Наиболее широко используемым антирастворителем для реализации метода сверхкритического антисольвентного осаждения является СО2. Преимущества этого флюида – возможность проведения осаждения при относительно низких температурах и давлениях (критическая температура – 31°С, критическое давление – 73 бар), дешевизна, инертность, а также негорючесть. Помимо СО2 в литературе известны немногочисленные примеры использования в качестве антирастворителя этана [91], аммиака [92], 1,1,1,2-тетрафторэтана [93, 94] или смеси СО2 и N2 [95]. Однако, применение таких флюидов имеет собственные ограничения. Например, несмотря на перспективность использования низших алканов (этан, пропан) для ряда приложений, они характеризуются высокой пожароопасностью. СК-аммиак обладает высокой реакционной способностью, что далеко не всегда желательно, а также остро неприятным запахом и некоторой токсичностью; СК-N2 обладает очень низкой растворяющей способностью.
В качестве растворителя в методе SAS можно использовать различные растворители, имеющие сродство с СК-CO2. Выбор растворителя сильно влияет на конечный продукт. Наиболее оптимальными растворителями, исходя из их сродства к СК-СО2, являются диметилсульфоксид (ДМСО) и N-метилпирролидон (NMP). Кроме того, широко применяются метанол, ацетон, толуол и этилацетат. Воду не используют в качестве растворителя из-за относительно малой растворимости в СК-СО2. Следовательно, методом SAS трудно проводить микронизацию гидрофильных веществ. Более того, при добавлении даже незначительных количеств воды к выбранному растворителю равновесие растворитель–антирастворитель существенно меняется. Однако, существуют подходы, позволяющие при определенных условиях использовать SAS гидрофильных веществ. Так, были найдены многие системы растворитель–антирастворитель, позволяющие обойти ограничение, связанное с низкой растворимостью воды в СО2 [96, 97].
Для не растворимых ни в СО2, ни в органических растворителях субстанций, возможно применение суспензионного варианта метода SAS. Такая модификация метода SAS подходит для получения гибридных органо-неорганических материалов (рис. 7) и других композитов, в состав которых входят нерастворимые компоненты [68, 98].
ВЛИЯНИЕ ФАЗОВОГО СОСТАВА СМЕСИ ПРИ ОСАЖДЕНИИ МЕТОДОМ SAS НА МОРФОЛОГИЮ И РАЗМЕР ОСАЖДАЕМЫХ ЧАСТИЦ
Одно из центральных преимуществ метода SAS – широкие возможности управления размером и морфологией получаемых частиц, которые достигаются путем варьирования многочисленных параметров процесса. Помимо параметров, традиционных для растворных методов, таких как тип растворителя и концентрация целевой субстанции в растворе, метод SAS обладает рядом специфических параметров, характерных для сверхкритических флюидных технологий.
Один из факторов, который оказывает наибольшее влияние на морфологию и размер осаждаемых частиц в методе SAS, – фазовый состав системы, в которой производится осаждение. Необходимо учитывать, что система состоит из трех компонентов: антирастворителя, растворителя и растворенного вещества. К сожалению, определение фазового равновесия в такой трехкомпонентной системе представляется затруднительным, поэтому чаще всего пренебрегают влиянием растворенного вещества на фазовое равновесие растворитель – антирастворитель, и рассматривают двухкомпонентную систему [99]. Однако, существуют примеры работ, в которых показано, что растворенное вещество может существенно расширять двухфазную область на фазовой диаграмме двухкомпонентной системы, смещая критическую кривую в область более высоких давлений [100–102].
Как уже было отмечено выше, в роли антирастворителя в процессе SAS в подавляющем большинстве случаев выступает СО2. Фазовые диаграммы двухкомпонентных смесей СО2 и растворителей, наиболее широко применяемых в методе SAS, известны по данным [103–108]. СО2 и органические растворители, в основном, формируют системы I-го типа по классификации, предложенной Ван Коненбургом и Скоттом [109, 110].
В зависимости от параметров состояния осадителя процесс SAS может проходить в двух принципиально различающихся режимах – абсолютной и частичной смешиваемости. После распыления раствора в СО2 начинают происходить два процесса: 1) смешение, сопровождающееся эволюцией остаточного межфазного натяжения и 2) гидродинамический разрыв струи. Для характеризации этих процессов в SAS предложено два характеристических времени [111]. Первое время tрс (время разрыва струи) представляет собой время, за которое распыляемый раствор проходит расстояние от выхода из сопла до прохождения места разрыва струи. Второе характеристическое время tимн (время исчезновения межфазного натяжения) – время, за которое полностью исчезает граница раздела фаз между распыляемой жидкостью и сверхкритическим флюидом. Как правило, в условиях частичной смешиваемости растворителя и антирастворителя время исчезновения остаточного межфазного натяжения существенно больше времени разрыва струи (tимн ≫ tрс). Поэтому образование частиц происходит внутри капель, формирующихся при разрыве струи до завершения смешения.
Капли раствора, образовавшиеся после разрыва струи, взаимодействуют с антирастворителем. СО2 диффундирует в капли, что вызывает их расширение и приводит к появлению градиента концентраций и степени пересыщения микронизуемых веществ по капле. В случае осаждения методом SAS аморфных веществ при работе в этой области чаще всего формируются полые сферические частицы микронного размера [112–114]. При расширении капли максимум пересыщения приходится на границы капли, поэтому там происходит наиболее интенсивное осаждение, приводящее к образованию внешней оболочки частицы. Эта оболочка может быть как монолитной, так и сформированной из множества наночастиц, в зависимости от того, какой процесс более медленный – массообмен между фазами или зародышеобразование [115, 116]. Если лимитирующей стадией является массообмен, то зародышеобразование успевает произойти во многих точках на границе капли, и образующаяся в результате частица состоит из множества наночастиц, скрепленных между собой. Если лимитирующая стадия – зародышеобразование, то необходимая степень пересыщения успеет сформироваться вдоль всей поверхности капли, и получается полая монолитная частица [117].
При давлении выше критического двухфазная система не может существовать ни при каком соотношении растворителя и антирастворителя. Однако, остаточное межфазное натяжение в системе растворитель–антирастворитель исчезает не мгновенно после распыления. В зависимости от параметров процесса могут реализовываться два различных сценария смешения [118]. Если разрыв струи происходит быстрее, чем успевает исчезнуть межфазное натяжение (tимн > tрс), то осаждение идет по сценарию, аналогичному субкритическому, с тем лишь различием, что формирования полых частиц не происходит. Как правило, в случае аморфных веществ в таких условиях образуются сферические частицы микронного или субмикронного размера (рис. 8) [64, 119–121]. СО2, проникая в капли, вызывает падение растворяющей способности, приводящее к одновременному началу образования твердой фазы во многих точках внутри капли. Возникшие центры по мере роста срастаются воедино, поскольку они удерживаются рядом друг с другом межфазным натяжением, и размеры получающейся в результате частицы задаются размерами капли.
Рис. 8.
Частицы гидроксипропилметилцеллюлозы, осажденные методом SAS из ДМСО, концентрация в растворе 125 г/л, 150 бар.
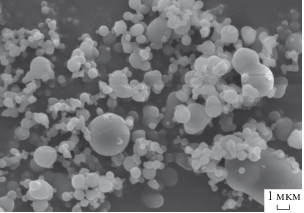
Если межфазное натяжение исчезает быстрее, чем происходит разрыв распыляемой струи (tимн < < tрс), и чем успевает начаться кристаллизация, то в таком случае смешение раствора и антирастворителя происходит газоподобным образом, и осаждение частиц идет из однофазной смеси в условиях высокой степени пересыщения. При реализации этого сценария чаще всего в случае аморфных веществ образуются наноразмерные частицы нерегулярной формы (рис. 9), поскольку формирование твердой фазы идет в условиях высокой степени пересыщения и в большом объеме. Примеры получения таких наночастиц показаны в работах [65, 122–125].
Рис. 9.
Частицы гидроксипропилметилцеллюлозы, осажденные методом SAS из хлороформа, концентрация в растворе 25 г/л, 150 бар.
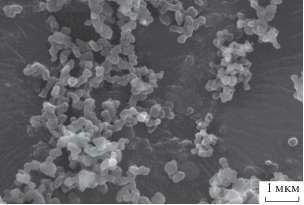
Повышение давления приводит к существенному увеличению скорости исчезновения межфазного натяжения. Первоначально считалось, что осаждение в первом режиме (tимн > tрс) может происходить только при давлении ненамного выше критического (до ~120 бар при 40°С) для подавляющего большинства растворителей в SAS. Для некоторых растворителей с низкой вязкостью (ацетон) условие tимн > tрс не выполняется практически сразу при превышении критического давления смеси [126, 127]. Однако, в дальнейшем было показано, что область давлений, в которой кристаллизация происходит в короткоживущих каплях раствора, может быть гораздо более широкой (выше 160 бар при 40°С). Такой эффект характерен в особенности для вязких растворителей, например, ДМСО и в случае высоких концентраций микронизуемого вещества в растворе, что также может заметно увеличивать вязкость раствора [128]. Экспериментально микрочастицы, образующиеся при выполнении условия tимн > tрс, были получены при 180 бар (40°С) [129].
Использование аморфных частиц может быть полезно для повышения скорости растворения фармацевтических препаратов. Однако, часто такие частицы могут быть нестабильны и склонны к перекристаллизации, в особенности под действием влаги воздуха. Поэтому для некоторых применений зачастую, наоборот, актуально получение кристаллических частиц [130]. Долгое время считалось, что образование кристаллических частиц характерно только при осаждении из двухфазной системы (при tимн ≫ tрс) [119]. Однако, в дальнейшем была показана возможность получения кристаллических частиц и при полной смешиваемости растворителя и СО2 [131, 132]. Пример таких частиц, полученных в условиях полной смешиваемости, представлен на рис. 10. Во многих работах продемонстрировано, что метод SAS обладает широкими возможностями по варьированию морфологии получаемых кристаллических частиц, а также их полиморфного состава [133–136]. В частности, за счет того, что при микронизации методом SAS кристаллизация происходит очень быстро, открываются возможности получения метастабильных полиморфных форм [137]. Особенно привлекательно это для фармацевтических применений, так как различные полиморфы обладают различными свойствами, в частности характеризуются различной кинетикой растворения [138]. Отдельные наблюдения о зависимости размера и морфологии кристаллических частиц, получаемых в SAS, неоднократно публиковались и обсуждались в литературе, однако столь же стройного видения влияния различных параметров процесса на их формирование, как для аморфных частиц, в настоящий момент еще нет [117].
ЗАКЛЮЧЕНИЕ
Несмотря на разнообразие существующих методов микронизации, СКФ-подходы получения микро- и наночастиц активно развиваются в последние десятилетия. Обладая всеми преимуществами, характерными для восходящих методов (“bottom up”), ключевой отличительной особенностью данных технологий является отсутствие необходимости удаления растворителей из конечного продукта. Если СКФ используется в качестве растворителя, то удаление его происходит автоматически при сбросе давления за счет перехода в газовую фазу. В случае использования СКФ в качестве антирастворителя избавление от растворителя достигается путем промывки дополнительным количеством флюида получаемого продукта сразу после осаждения без дополнительных стадий очистки. Метод сверхкритического антисольвентного осаждения более универсален по сравнению с другими СКФ-подходами, так как позволяет проводить микронизацию значительно более широкого круга веществ, для которых задача направленного формирования частиц актуальна.
Список литературы
Martín A., Cocero M.J. // Adv. Drug Deliv. Rev. 2008. V. 60. № 3. P. 339.
Jung J., Perrut M. // J. Supercrit. Fluids. 2001. V. 20. № 3. P. 179.
Hannay J.B., Hogarth J. // Proc. R. Soc. Lond. 1879. V. 29. № 196–199. P. 324.
Krukonis V.J. // Pap. 140f Present. AIChE Ann Meet. San Franc. 1984.
Matson D.W., Petersen R.C., Smith R.D. // J. Am. Ceram. Soc. 1986. V. 1. № 3. P. 242.
Matson D.W., Fulton J.L., Petersen R.C. et al. // Ind. Eng. Chem. Res. 1987. V. 26. № 11. P. 2298.
Petersen R.C., Matson D.W., Smith R.D. // J. Am. Chem. Soc. 1986. V. 108. № 8. P. 2100.
Matson D.W., Petersen R.C., Smith R.D. // J. Mater. Sci. 1987. V. 22. № 6. P. 1919.
Petersen R.C., Matson D.W., Smith R.D. // Polym. Eng. Sci. 1987. V. 27. № 22. P. 1693.
Sane A., Taylor S., Sun Y.-P. et al. // Chem. Commun. 2003. № 21. P. 2720.
Karimi M., Raofie F. // J. Supercrit. Fluids. 2019. V. 146. P. 172.
Zeinolabedini Hezave A., Esmaeilzadeh F. // J. Cryst. Growth. 2010. V. 312. № 22. P. 3373.
Hsu Y.-T., Su C.-S. // Pharmaceutics. 2020. V. 12. № 1. P. 42.
Matson D.W., Petersen R.C., Smith R.D. // Mater. Lett. 1986. V. 4. № 10. P. 429.
Fulton J.L., Deverman G.S., Yonker C.R. et al. // Polymer. 2003. V. 44. № 13. P. 3627.
Hansen B.N., Hybertson B.M., Barkley R.M. et al. // Chem. Mater. 1992. V. 4. № 4. P. 749.
Fattahi A., Karimi-Sabet J., Keshavarz A. et al. // J. Supercrit. Fluids. 2016. V. 107. P. 469.
Lele A.K., Shine A.D. // AIChE J. 1992. V. 38. № 5. P. 742.
Sun Y.-P., Guduru R., Lin F. et al. // Ind. Eng. Chem. Res. 2000. V. 39. № 12. P. 4663.
Asghari I., Esmaeilzadeh F. // Int. J. Pharm. 2012. V. 433. № 1. P. 149.
Thakur R., Gupta R.B. // J. Supercrit. Fluids. 2006. V. 37. № 3. P. 307.
Thakur R., Gupta R.B. // Ind. Eng. Chem. Res. 2005. V. 44. № 19. P. 7380.
Sun Y.-P., Rollins H.W. // Chem. Phys. Lett. 1998. V. 288. № 2. P. 585.
Pat. EP1021241A1 (2000)
Wehowski M., Weidner E., Kilzer A. // Colloids Surf. Physicochem. Eng. Asp. 2008. V. 331. № 1. P. 143.
Lankes H., Sommer K., Weinreich B. // Powder Technol. 2003. V. 134. № 3. P. 201.
Petermann M., Weidner E., Grüner S. et al. // Proc. Spray Dry. 2001. V. 1.
Reverchon E., Adami R. // J. Supercrit. Fluids. 2006. V. 37. № 1. P. 1.
Nalawade S.P., Picchioni F., Janssen L.P.B.M. // Prog. Polym. Sci. 2006. V. 31. № 1. P. 19.
Pat. US4451654A (1984)
Senčar-Božič P., Srčič S., Knez Z. et al. // Int. J. Pharm. 1997. V. 148. № 2. P. 123.
Kerč J., Srčič S., Knez Ž. et al. // Int. J. Pharm. 1999. V. 182. № 1. P. 33.
Xu C.Y., Sievers R.E., Karst U. et al. // Green Chem. Front. Benign Chem. Synth. Process. Oxf. Univ. Press Oxf. 1998. P. 312.
Sievers R.E. // Aerosol Sci. Technol. 1999. V. 30. № 1. P. 3.
Pat. WO2000075281A2 (2000)
Sellers S.P., Clark G.S., Sievers R.E. et al. // J. Pharm. Sci. 2001. V. 90. № 6. P. 785.
Reverchon E. // Ind. Eng. Chem. Res. 2002. V. 41. № 10. P. 2405.
Pat. WO2003004142A1 (2003)
Reverchon E., Della Porta G. // J. Supercrit. Fluids. 2003. V. 26. № 3. P. 243.
Reverchon E., Della Porta G. // Int. J. Pharm. 2003. V. 258. № 1. P. 1.
Reverchon E., Spada A. // Powder Technol. 2004. V. 141. № 1. P. 100.
Reverchon E., Spada A. // Proceedings of the Sixth International Symposium on Supercritical Fluids. 2003. V. 3. P. 1665.
Reverchon E., Antonacci A. // J. Supercrit. Fluids. 2007. V. 39. № 3. P. 444.
Liparoti S., Adami R., Reverchon E. // Ibid. 2012. V. 72. P. 46.
Adami R., Liparoti S., Izzo L. et al. // Ibid. 2012. V. 72. P. 15.
Reverchon E., Adami R., Marco I.D. et al. // Ibid. 2005. V. 35. № 1. P. 76.
Reverchon E., Adami R., Caputo G. // Ibid. 2006. V. 37. № 3. P. 298.
Reverchon E., Adami R., Cardea S. et al. // Ibid. 2009. V. 47. № 3. P. 484.
Adami R., Liparoti S., Reverchon E. // Chem. Eng. J. 2011. V. 173. № 1. P. 55.
Cai M.-Q., Guan Y.-X., Yao S.-J. et al. // J. Supercrit. Fluids. 2008. V. 43. № 3. P. 524.
Wang Q., Guan Y.-X., Yao S.-J. et al. // Chem. Eng. J. 2010. V. 159. № 1. P. 220.
Wang Q., Guan Y.-X., Yao S.-J. et al. // J. Supercrit. Fluids. 2011. V. 56. № 1. P. 97.
Shen Y.-B., Du Z., Wang Q. et al. // Powder Technol. 2014. V. 254. P. 416.
Ventosa N., Sala S., Veciana J. et al. // Cryst. Growth Des. 2001. V. 1. № 4. P. 299.
Ventosa N., Sala S., Veciana J. // J. Supercrit. Fluids. 2003. V. 26. № 1. P. 33.
Gimeno M., Ventosa N., Sala S. et al. // Cryst. Growth Des. 2006. V. 6. № 1. P. 23.
Berends E.M., Bruinsma O.S., De Graauw J. et al. // AIChE J. 1996. V. 42. № 2. P. 431.
Esfandiari N., Ghoreishi S.M. // AAPS PharmSciTech. 2015. V. 16. № 6. P. 1263.
Jafari D., Yarnezhad I., Nowee S.M. et al. // Ind. Eng. Chem. Res. 2015. V. 54. № 14. P. 3685.
Reverchon E. // J. Supercrit. Fluids. 1999. V. 15. № 1. P. 1.
Kunastitchai S., Pichert L., Sarisuta N. et al. // Int. J. Pharm. 2006. V. 316. № 1. P. 93.
Yan T., Zhang Y., Ji M. et al. // J. Supercrit. Fluids. 2019. V. 153. P. 104594.
Tao C., Zhang J., Wang J. et al. // Pharmaceutics. 2018. V. 10. № 3. P. 95.
Montes A., Wehner L., Pereyra C. et al. // J. Supercrit. Fluids. 2016. V. 112. P. 44.
Yoon T.J., Son W.-S., Park H.J. et al. // Ibid. 2016. V. 107. P. 51.
Montes A., Wehner L., Pereyra C. et al. // Ibid. 2016. V. 118. P. 1.
Esfandiari N. // Ibid. 2015. V. 100. P. 129.
Nesterov N.S., Paharukova V.P., Yakovlev V.A. et al. // Ibid. 2016. V. 112. P. 119.
Jiang H., Zhang L., Zhao J. et al. // J. Mater. Res. 2016. V. 31. № 6. P. 702.
Nesterov N.S., Simentsova I.I., Yudanov V.F. et al. // J. Struct. Chem. 2016. V. 57. № 1. P. 90.
Da Silva E.P., Winkler M.E., Giufrida W.M. et al. // J. Colloid Interface Sci. 2019. V. 535. P. 245.
Lee B.-M., Kim S.-J., Lee B.-C. et al. // Ind. Eng. Chem. Res. 2011. V. 50. № 15. P. 9107.
Seo B., Kim T., Park H.J. et al. // J. Supercrit. Fluids. 2016. V. 111. P. 112.
Reverchon E., Della Porta G., Di Trolio A. et al. // Ind. Eng. Chem. Res. 1998. V. 37. № 3. P. 952.
Prosapio V., Reverchon E., De Marco I. // Powder Technol. 2016. V. 292. P. 140.
Reverchon E., Della Porta G., De Rosa I. et al. // J. Supercrit. Fluids. 2000. V. 18. № 3. P. 239.
Hong L., Guo J., Gao Y. et al. // Ind. Eng. Chem. Res. 2000. V. 39. № 12. P. 4882.
Adami R., Reverchon E., Järvenpää E. et al. // Powder Technol. 2008. V. 182. № 1. P. 105.
Jung J., Clavier J.-Y., Perrut M. // Proceedings of the 6th International Symposium on Supercritical Fluids. 2003. V. 3. P. 1683.
Reverchon E., De Marco I., Caputo G. et al. // J. Supercrit. Fluids. 2003. V. 26. № 1. P. 1.
Robertson J., King M.B., Seville J.P.K. et al. // The 4th International Symposium on Supercritical Fluids. Sendai, 1997. P. 47.
Pat. WO1995001221A1 (1995)
Pat. US5795594A (1998)
Franceschi E., De Cesaro A.M., Feiten M. et al. // J. Supercrit. Fluids. 2008. V. 47. № 2. P. 259.
He W.Z., Suo Q.L., Jiang Z.H. et al. // Ibid. 2004. V. 31. № 1. P. 101.
He W.Z., Suo Q.L., Li Y.X. et al. // Cryst. Res. Technol. 2007. V. 42. № 6. P. 631.
Chattopadhyay P., Gupta R.B. // Int. J. Pharm. 2001. V. 228. № 1. P. 19.
Chattopadhyay P., Gupta R.B. // AIChE J. 2002. V. 48. № 2. P. 235.
Jin H., Hemingway M., Gupta R.B. et al. // Particuology. 2012. V. 10. № 1. P. 17.
Jin H.Y., Hemingway M., Xia F. et al. // Ind. Eng. Chem. Res. 2011. V. 50. № 23. P. 13475.
Schmitt W.J., Salada M.C., Shook G.G. et al. // AIChE J. 1995. V. 41. № 11. P. 2476.
Pat. WO2002045690A1 (2002)
Tan C.-S., Chang W.-W. // Ind. Eng. Chem. Res. 1998. V. 37. № 5. P. 1821.
Hsu R.-Y., Tan C.-S., Chen J.-M. // J. Appl. Polym. Sci. 2002. V. 84. № 9. P. 1657.
Ghaderi R., Artursson P., Carlfors J. // Eur. J. Pharm. Sci. 2000. V. 10. № 1. P. 1.
Snavely W.K., Subramaniam B., Rajewski R.A. et al. // J. Pharm. Sci. 2002. V. 91. № 9. P. 2026.
De Marco I., Reverchon E. // Chem. Eng. J. 2012. V. 187. P. 401.
Vorobei A.M., Pokrovskiy O.I., Ustinovich K.B. et al. // Polymer. 2016. V. 95. P. 77.
Palakodaty S., York P. // Pharm. Res. 1999. V. 16. № 7. P. 976.
Reverchon E., Caputo G., De Marco I. // Ind. Eng. Chem. Res. 2003. V. 42. № 25. P. 6406.
Reverchon E., De Marco I. // J. Supercrit. Fluids. 2004. V. 31. № 2. P. 207.
Reverchon E., De Marco I. // Powder Technol. 2006. V. 164. № 3. P. 139.
Tochigi K., Namae T., Suga T. et al. // J. Supercrit. Fluids. 2010. V. 55. № 2. P. 682.
Stievano M., Elvassore N. // Ibid. 2005. V. 33. № 1. P. 7.
Dohrn R., Brunner G. // Fluid Phase Equilibria. 1995. V. 106. № 1. P. 213.
Dohrn R., Peper S., Fonseca J.M.S. // Ibid. 2010. V. 288. № 1. P. 1.
Fonseca J.M.S., Dohrn R., Peper S. // Ibid. 2011. V. 300. № 1. P. 1.
Peper S., Fonseca J.M.S., Dohrn R. // Ibid. 2019. V. 484. P. 126.
Konynenburg P.H. van, Scott R.L. // Phil Trans Roy. Soc. L. A. 1980. V. 298. № 1442. P. 495.
Page S.H., Sumpter S.R., Lee M.L. // J. Microcolumn Sep. 1992. V. 4. № 2. P. 91.
Dukhin S.S., Shen Y., Dave R. et al. // Colloids Surf. Physicochem. Eng. Asp. 2005. V. 261. № 1. P. 163.
Reverchon E., De Marco I., Adami R. et al. // J. Supercrit. Fluids. 2008. V. 44. № 1. P. 98.
Adami R., Osséo L.S., Huopalahti R. et al. // Ibid. 2007. V. 42. № 2. P. 288.
De Marco I., Reverchon E. // Powder Technol. 2008. V. 183. № 2. P. 239.
Werling J.O., Debenedetti P.G. // J. Supercrit. Fluids. 1999. V. 16. № 2. P. 167.
Werling J.O., Debenedetti P.G. // Ibid. 2000. V. 18. № 1. P. 11.
Reverchon E., De Marco I. // Chem. Eng. J. 2011. V. 169. № 1. P. 358.
Braeuer A., Dowy S., Torino E. et al. // Ibid. 2011. V. 173. № 1. P. 258.
Reverchon E., Adami R., Caputo G. et al. // J. Supercrit. Fluids. 2008. V. 47. № 1. P. 70.
Prosapio V., Reverchon E., De Marco I. // Ibid. 2016. V. 118. P. 19.
De Marco I., Rossmann M., Prosapio V. et al. // Chem. Eng. J. 2015. V. 273. P. 344.
Vorobei A.M., Ustinovich K.B., Pokrovskiy O.I. et al. // Russ. J. Phys. Chem. B. 2015. V. 9. № 8. P. 1103.
Reverchon E., De Marco I., Torino E. // J. Supercrit. Fluids. 2007. V. 43. № 1. P. 126.
Ha E.-S., Kim J.-S., Baek I. et al. // Drug Des. Devel. Ther. 2015. V. 9. P. 4269.
Kefeng X., Weiqiang W., Dedong H. et al. // J. Nanomater. 2016. V. 16. № 1. P. 392:392.
De Marco I., Knauer O., Cice F. et al. // Chem. Eng. J. 2012. V. 203. P. 71.
Reverchon E., Torino E., Dowy S. et al. // Ibid. 2010. V. 156. № 2. P. 446.
Marra F., De Marco I., Reverchon E. // Chem. Eng. Sci. 2012. V. 71. P. 39.
De Marco I., Reverchon E. // J. Supercrit. Fluids. 2011. V. 58. № 2. P. 295.
Adami R., Järvenpää E., Osséo L.S. et al. // Adv. Powder Technol. 2008. V. 19. № 6. P. 523.
Rossmann M., Braeuer A., Leipertz A. et al. // J. Supercrit. Fluids. 2013. V. 82. P. 230.
Rossmann M., Braeuer A., Dowy S. et al. // Ibid. 2012. V. 66. P. 350.
Careno S., Boutin O., Badens E. // J. Cryst. Growth. 2012. V. 342. № 1. P. 34.
De Gioannis B., Jestin P., Subra P. // Ibid. 2004. V. 262. № 1. P. 519.
Rodrigues M.A., Tiago J.M., Duarte A. et al. // Cryst. Growth Des. 2016. V. 16. № 11. P. 6222.
Huang Y., Wang H., Liu G. et al. // Int. J. Pharm. 2015. V. 496. № 2. P. 551.
Weber Brun G., Martín Á., Cassel E. et al. // Cryst. Growth Des. 2012. V. 12. № 4. P. 1943.
Brittain H.G. Polymorphism in Pharmaceutical Solids. CRC Press, 2016. 654 p.
Дополнительные материалы отсутствуют.
Инструменты
Журнал физической химии