Физика и химия стекла, 2019, T. 45, № 2, стр. 175-183
Керамическое интерфазное покрытие на углеродных волокнах на основе поликарбосилана и олиговинилсилазана
М. А. Хасков 1, *, И. В. Зеленина 1, О. Ю. Сорокин 1, А. И. Гуляев 1
1 Всероссийский научно-исследовательский институт авиационных материалов
105005 Москва, ул. Радио, 17, Россия
* E-mail: khaskov@mail.ru
Поступила в редакцию 23.03.2018
После доработки 05.05.2018
Принята к публикации 05.12.2018
Аннотация
Рассматривается получение керамического интерфазного (интерфейсного) покрытия на углеродных волокнах методом инфильтрации керамообразующей полимерной композицией на основе поликарбосилана и олиговинилсилазана с последующим отверждением и пиролизом. Показано, что при использовании концентрации керамообразующего полимера выше 3 мас. % на волокнах образуются тяжи с неравномерным распределением керамической матрицы. При использовании концентрации керамообразующего полимера ниже 3 мас. %, инертной атмосферы и температурно-временного режима обработки, рассчитанного для равномерного тепловыделения и потери массы, удается получить равномерное интерфазное покрытие, которое повышает термоокислительную устойчивость углеродного волокна. Продуктами сгорания углеродного волокна с нанесенным интерфазным покрытием являются полые SiO2 структуры.
ВВЕДЕНИЕ
При эксплуатации конструкций в условиях высоких температур, агрессивных сред, многократных теплосмен и повышенных механических нагрузок [1] все большее применение находят керамоматричные композиционные материалы (ККМ) [2], армированные различными типами волокон [3], в том числе и углеродными. Для улучшения физико-химических и физико-механических свойств композитов на основе углеродных волокон, поверхность волокна зачастую модифицируют. Например, наносимое на углеродное волокно покрытие может повышать такие его физико-химические свойства как термоокислительная устойчивость [4]. Стоит отметить, что при использовании углеродных волокон в качестве армирующих наполнителей в ККМ, покрытие на их поверхности, которое еще называется интерфазным (интерфейсным [5]), выполняет также функцию создания компромисса между слишком высокой и слишком низкой адгезией на границе матрица-волокно. Это позволяет как реализовать механизм диссипации энергии матричных микротрещин на границе волокно/матрица за счет ослабления межкомпонентной связи, так и улучшать механические свойства хрупкой керамической матрицы вследствие наличия армирующего наполнителя. Более того, коэффициенты термического расширения волокна, матрицы и интерфазного покрытия должны быть близки для предотвращения возникновения механических напряжений [6] при термоциклировании композита [7]. В ККМ на армирующее волокно может наноситься интерфазное покрытие на основе аморфного углерода или нитрида бора, но оно не обладает достаточной термоокислительной устойчивостью, особенно в присутствии паров воды (для BN) [8]. Для повышения термоокислительной устойчивости интерфазное покрытие может быть изготовлено на основе карбида кремния, например, из поликарбосилана, однако, почти двукратное различие в коэффициентах термического расширения по сравнению с углеродным волокном [9] может привести к возникновению существенных механических напряжений на границе волокно-интерфазное покрытие при термоциклировании. Нитрид и карбонитрид кремния понижают разницу КЛТР с углеродным волокном [10], что позволяет предположить о перспективности использования SiXCZNY и Si3N4 в составе ИП по сравнению с чистым SiC. Более того, наличие в керамообразующей композиции на основе поликарбосилана соединений с непредельными С=С связями позволяет увеличивать выход керамики за счет их термически индуцированного гидросилилирования [11].
В настоящее время известно несколько методов нанесения интерфазного покрытия, например, методом газофазного осаждения, золь-гель методом, нанесением из керамообразующих полимеров и др. [8]. Считается, что условия проведения газофазного осаждения повреждают волокна, особенно если используются высокие температуры и коррозионноактивные компоненты. Золь-гель метод нанесения интерфазного покрытия также приводит к существенному падению прочностных свойств армирующего волокна, более того наиболее часто он используется для нанесения кислородсодержащего интерфазного покрытия [8]. Для получения нитрид- и карбидсодержащих интерфазных покрытий, обычно используют полимерные прекурсоры, при этом ИП желаемой толщины могут быть получены многократным повторением цикла: нанесение полимерного прекурсора–отверждение–пиролиз [8].
Целью данной работы было изучение возможности получения на углеродном волокне интерфазного покрытия на основе поликарбосилана и олиговинилсилазана с использованием метода инфильтрации полимерной керамообразующей композицией с последующим отверждением и пиролизом.
ЭКСПЕРИМЕНТАЛЬНАЯ ЧАСТЬ
В качестве исходных реагентов использовали поликарбосилан ПКС-М производства АО “ГНИИХТЭОС”, содержащий 49.78 мас. % Si, 0.70 мас. % водорода за счет Si-H групп и олиговинилсилазан Полисил-04М (прозрачная желтая жидкость, содержащая 81 мас. % нелетучих компонентов, 37.5 мас. % Si и 20.0 мас. % N).
Образцы керамообразующих композиций готовили путем растворения исходных компонентов в гексане марки “х. ч.” при комнатной температуре для получения 10 мас. % растворов, с последующим доведением рабочих растворов для пропитки углеродного волокна до заданной концентрации.
Измерения удельной поверхности наполнителей проведены по адсорбции азота на приборе ASAP 2020 (Micromeritics, США). Удельная поверхность рассчитывалась по методу БЭТ (метод Брунауэра, Эммета и Теллера). Распределение пор по размерам – по методу BJH (метод Барретта, Джойнера и Халенда).
Динамическую вязкость (мПа с) чистого растворителя и готовых композиций при температуре 20.0 ± 0.1°С определяли согласно ГОСТ 33-2000 по капиллярному вискозиметру типа ВПЖ-2 с диаметром капилляра 0.56 мм (ГОСТ 10028-81).
Измерение краевого угла смачивания на границе “воздух–исследуемый раствор прекурсора интерфазного покрытия–пиролитический графит” проводили на приборе OCA 15Pro (Dataphysics Instruments GmbH) [12] с использованием в качестве подложки пиролитического полированного графита производства МЕДИНЖ (г. Пенза).
Для формирования интерфазного покрытия отожженую углеродную ткань УТ-900И обрабатывали в растворе керамообразующей композиции с последующей сушкой при комнатной температуре на воздухе. Отверждение и пиролиз проводили в динамической атмосфере аргона (5 л/мин). Нанесение составов для получения интерфазного покрытия проводили из растворов различной концентрации методом однократной пропитки.
Термоокислительную деструкцию исследовали на приборе синхронного термического анализа СТА Netzsch 449 F3 Jupiter при скорости нагревания 10 К/мин в динамической атмосфере синтетического воздуха (70 мл/мин).
Для исследования структуры интерфазного покрытия и определения элементного состава структурных составляющих были изготовлены поперечные шлифы жгутов углеродных волокон с покрытием. На исследуемую поверхность шлифов наносили токопроводящий слой (слой платины толщиной 10–15 нм) на установке для ионного напыления JFC-1600. Получение микрофотографий проводили в режиме обратно отраженных электронов при ускоряющем напряжении 25 кВ и увеличениях от ×1000 до ×10 000. Контраст изображения структуры в отраженных электронах определяется средним атомным номером фазы: чем выше атомный номер, тем светлее данный участок.
Для оценки качества нанесения интерфазного покрытия была исследована морфология поверхности обработанного углеродного волокна на растровом электронном микроскопе Zeiss EVO MA 10 при ускоряющем напряжении 15 кВ и токе пучка от 600 до 800 пА. Были получены изображения поверхности углеродных волокон в режиме вторичных электронов при увеличениях ×5000 и ×15 000.
ОБСУЖДЕНИЕ РЕЗУЛЬТАТОВ
На рис. 1 показано изменение краевого угла смачивания пиролитической углеродной подложки 10 мас. % раствором керамообразующих композиций с различным соотношением поликарбосилан/олиговинилсилазан.
Рис. 1.
Изменение краевого угла смачивания чистого растворителя и 10 мас. % керамообразующих композиций в гексане. 1 – чистый гексан, 2 – соотношение поликарбосилан/олиговинилсилазан = 2 : 1, 3 – соотношение поликарбосилан/олиговинилсилазан = 1 : 2.
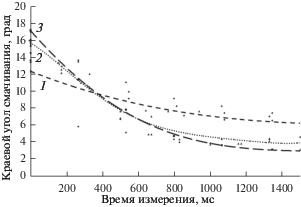
Как видно из рис. 1 в процессе измерения краевого угла смачивания (КУС) происходит его уменьшение, что связано с испарением растворителя, причем абсолютные значения КУС для керамообразующих композиций определяются чистым растворителем. Вязкость и плотность 3 мас. % раствора керамообразующей композиции также не существенно отличается от значений для чистого растворителя (табл. 1). Таким образом, использование концентрации керамообразующей композиции ниже 10 мас. % не приводит к ухудшению технологических характеристик пропитки волокна по сравнению с чистым растворителем.
Таблица 1.
Свойства исходных компонентов
Определяемая характеристика | Ткань углеродная УТ-900И | Керамообразующая композиция | ||
---|---|---|---|---|
исходная | с удаленным аппретом | Гексан | 3 мас. % раствор ПКСЗ | |
Удельная поверхность, м2/г | 1.36 ± 0.13 | 4.72 ± 0.22 | – | – |
Сорбционная емкость, см3/г | 0.32 | 1.12 | – | – |
Относительный объем пор диаметром до 500 Å, см3/г | 0.0010 | 0.0046 | – | – |
Средний диаметр пор по десорбции, Å | 74 | 79 | – | – |
Плотность при 20°С, г/см3 | – | – | 0.659 | 0.660 |
Вязкость динамическая при 20°С, мПа с | – | – | 0.32 | 0.35 |
Перед нанесением интерфазного покрытия с углеродного волокна методом термоокислительной деструкции удалялся аппрет. Предложенный способ удаления аппрета не только не приводит к ухудшению физико-механических свойств исходного волокна [13], но и вызывает активацию поверхности, о чем свидетельствует увеличение сорбционного объема и величины удельной поверхности наполнителя (табл. 1).
В работе было изучено влияние концентрации керамообразующей композиции и температурно-временных условий отверждения и пиролиза на морфологию получаемого интерфазного покрытия. Показано, что при использовании концентрации керамообразующей композиции выше 3 мас. % на волокне образуется неравномерное покрытие, обволакивающее сразу несколько моноволокон (филаментов) и склеивающее их между собой (рис. 2, а), что в дальнейшем может привести к ухудшению пропитки обработанного наполнителя прекурсором керамической матрицы.
Рис. 2.
Образование неравномерного интерфазного покрытия при концентрации 5 мас. % в инертной атмосфере при отверждении и пиролизе керамообразующей композиции (а) и отслоение интерфазного покрытия при следовых количествах кислорода (б).
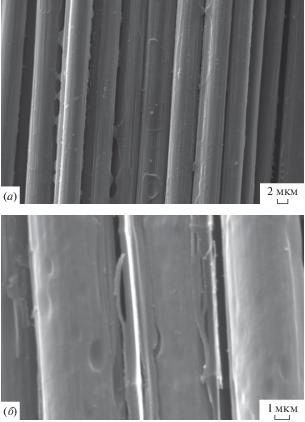
Проведение отверждения и пиролиза в отдельные промежуточные стадии приводило к частичному попаданию кислорода в газовую среду над волокнами, что приводило к частичному отслоению интерфазного покрытия на волокне, вероятно, за счет его окисления и образования оксида кремния (рис. 2, б). На основании полученных данных было решено проводить циклы отверждение/пиролиз в одну непрерывную стадию.
Ранее было показано [14], что отверждение керамообразующей композиции на основе поликарбосилана и олиговинилсилазана используемого в данной работе состава протекает с выделением теплоты, сопровождающейся незначительной потерей массы. На основании данных ИК-спектроскопии было предположено, что в процессе отверждения данной композиции происходит полимеризация по радикальному механизму двойных связей олиговинилсилазана, а также их взаимодействие с Si–H и Si–NH–Si фрагментами. Пиролиз отвержденной матрицы сопровождается существенной потерей массы с поглощением тепловой энергии. На основании термокинетических исследований был оптимизирован режим отверждения и пиролиза, где критерием оптимизации являлось равномерная скорость степени превращения и временной фактор [14]. Вследствие того, что отверждаемая композиции находится в виде тонкого слоя, влияния на выбор режима процессов тепло- [15] и массопереноса не учитывались.
При использовании растворов с концентрацией ниже 3 мас. % керамообразующей композиции с последующим одностадийным циклом отверждения и пиролиза по оптимизированному режиму [14] удалось получить равномерное интерфазное покрытие, повышающее термоокислительную устойчивость углеродного волокна.
На рис. 3 представлены данные растровой электронной микроскопии волокон с нанесенным интерфазным покрытием.
Рис. 3.
Поверхность (а) и торцы (б) углеродного волокна после нанесения керамического интерфазного покрытия.
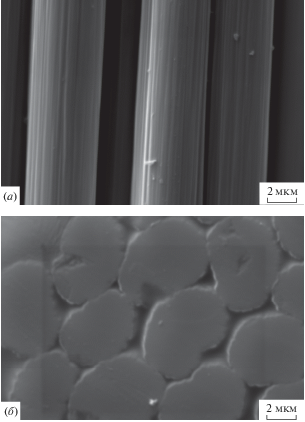
Как видно из рис. 3 на углеродном волокне удается получить равномерное интерфазного покрытие с толщиной порядка нескольких нанометров, о чем указывают микрофотографии торцов углеродного волокна.
На рис. 4, а представлены данные потери массы исходного углеродного волокна и волокна с нанесенным интерфазным покрытием. На рис. 4, а и в табл. 2 приведены данные термогравиметрии и дифференциальной сканирующей калориметрии при постоянном нагреве. Как видно из полученных данных, интерфазное покрытие увеличивает термоокислительную стойкость углеродного волокна, на что указывает увеличение температуры, необходимой для уменьшения заданной массы образца.
Рис. 4.
Данные термогравиметрии и дифференциальной сканирующей калориметрии при постоянном нагревании (а) и при изотермическом отжиге (б) в окислительной атмосфере исходного углеродного волокна (1) и углеродного волокна с нанесенным интерфазным покрытием состава ПКСЗ-21 (2).
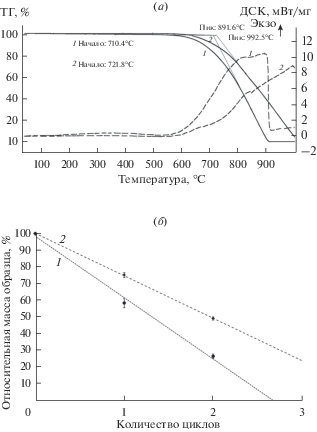
Таблица 2.
Данные термогравиметрии в окислительной атмосфере образцов исходного углеродного волокна (УВ) и УВ с интерфазным покрытием
Потеря массы, % | Температура,°С | |
---|---|---|
исходное углеродное волокно | углеродное волокно с интерфазным покрытием состава ПКСЗ-21 | |
5 | 639 | 673 |
20 | 722 | 767 |
40 | 781 | 834 |
60 | 825 | 896 |
75 | 854 | 938 |
На рис. 4, б показано изменение массы исходного углеродного волокна и волокна с нанесенным интерфазным покрытием при изотермическом отжиге в окислительной атмосфере. Цикл отжига соответствует нагреву образцов в муфельной печи до 600°С в течение 90 мин, изотермической выдержкой в течение 1 ч с последующим естественным охлаждением до 200°С в течение ∼90 мин. Отжиг в изотермическом режиме подтверждает повышение термоокислительной устойчивости волокна при нанесении интерфазного покрытия, на что указывает уменьшение скорости потери массы.
Стоит отметить, что твердыми продуктами сгорания углеродного волокна с нанесенным интерфазным покрытием являются полые белесые полупрозрачные структуры (рис. 5, a). На ИК-спектре полученного твердого остатка фиксируются широкие пики с 1069 см–1 и 801 см–1 и плечом при 1185 см–1. Согласно литературным данным [16], данные максимумы полос поглощения соответствуют ассиметричным валентным колебаниям (1069 см–1, 1185 см–1) и симметричным валентным колебаниям (801 см–1) групп Si–O–Si. Таким образом, можно предположить, что получаемые полые структуры состоят из оксида кремния (SiO2), тогда как углерод и азот удалились из системы в виде летучих оксидов или газообразного азота [17].
Рис. 5.
Микрофотографии (а) и ИК-спектр (б) полых структур, образуемых после сжигания углеродного волокна с нанесенной интерфазой.
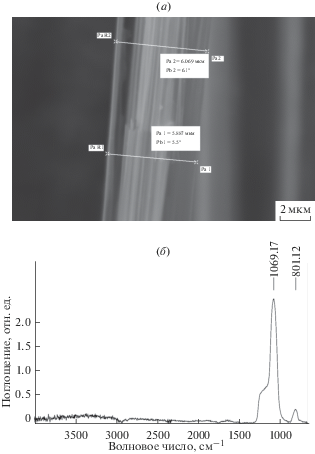
Достаточно равномерный внешний и внутренний диаметр образуемых полых SiO2-структур указывает на равномерно нанесенное интерфазное покрытие на волокне.
ЗАКЛЮЧЕНИЕ
В работе рассмотрено получение Si–C–N интерфазного (интерфейсного) покрытия на предварительно подготовленных углеродных волокнах методом инфильтрации керамообразующей полимерной композицией на основе поликарбосилана и олиговинилсилазана с последующим отверждением и пиролизом. Показано, что использование керамообразующей композиции с концентрацией ниже 10 мас. % в гексане не приводит к увеличению краевого угла смачивания углеродной поверхности и не ухудшает технологические параметры процесса инфильтрации углеродного волокна. При использовании концентрации керамообразующего полимера выше 3 мас. % на волокнах образуются тяжи с неравномерным распределением керамической матрицы, а присутствие кислорода приводит к вспучиванию и отслаиванию интерфазного покрытия. При использовании концентрации керамообразующего полимера ниже 3%, инертной атмосферы и температурно-временного режима обработки, рассчитанного для равномерного тепловыделения и потери массы, удается получить непрерывное интерфазное покрытие, которое повышает термоокислительную устойчивость углеродного волокна. Продуктами сгорания углеродного волокна с нанесенным интерфазным покрытием являются полые SiO2 структуры.
Исследование выполнено при финансовой поддержке РФФИ в рамках научного проекта № 17-03-01163. Авторы выражают благодарность С.Ю. Сибилевой за помощь в измерении динамического краевого угла смачивания, А.М. Шестакову за приготовление растворов керамообразующих полимеров, С.Д. Синякову за измерение вязкости приготовленных растворов, Е.Г. Чеблаковой и В.А. Гориной за помощь в проведении испытаний и обсуждении результатов.
Список литературы
Каблов Е.Н. Материалы для авиакосмической техники // Все материалы. Энциклопедический справочник. 2007. № 5. С. 7–27.
Каблов Е.Н., Гращенков Д.В., Исаева Н.В., Солнцев С.Ст. Перспективные высокотемпературные керамические композиционные материалы // Российский химический журнал. 2010. Т. LIV. № 1. С. 20–24.
Каблов Е.Н., Щетанов Б.В., Ивахненко Ю.А., Балинова Ю.А. Перспективные армирующие высокотемпературные волокна для металлических и керамических композиционных материалов // Труды ВИАМ: электрон. науч.-технич. журн. 2013. № 2. Ст. 05. URL: http://viam-works.ru. (дата обращения 27.02.2018).
Ткаченко Л.А., Шаулов А.Ю., Берлин А.А. Защитные жаропрочные покрытия углеродных материалов // Неорганические материалы. 2012. Т. 48. № 3. С. 261–271.
Бакланова Н.И. Интерфейсные покрытия на армирующих углеродных и карбидокремниевых волокнах для композитов с керамической матрицей //Автореферат докт. дис. 2010. Новосибирск. Институт химии твердого тела и механохимии Сибирского отделения РАН. 40 с. URL: http://www.solid.nsc.ru/education/dissovet/ads/archive/DOCS/autoreferat_Baklanova_D.pdf.
Лебедева Ю.Е., Попович Н.В., Орлова Л.А. Защитные высокотемпературные покрытия для композиционных материалов на основе SiC // Труды ВИАМ: электрон. науч.-технич. журн. 2013. № 2. Ст. 06. URL: http://viam-works.ru. (дата обращения 28.02.2018).
Тихомирова Е.А., Будиновский С.А., Живушкин А.А., Сидохин Е.Ф. Особенности развития термической усталости в деталях из жаропрочных сплавов с покрытием //Авиационные материалы и технологии. 2017. № 3. С. 20–25. doi 10.18577/2071-9140-2017-0-3-20-25
Department of defense handbook composite materials handbook. Volume 5. Ceramic matrix composites. 2002. 246 p.
Praderea C., Sauderb C. Transverse and longitudinal coefficient of thermal expansion of carbon fibers at high temperatures (300–2500 K) // Carbon. 2008. V. 46. P. 1874–1884.
Bright V.M., Raj R., Dunn M.L., Daily J.W. Injectable ceramic microcast silicon carbonitride (SiCN) microelectromechanical system (MEMS) for extreme temperature environments with extension: micro-packages for nano-devices // Air Force Research Laboratory. 2004. Final Technical Report, AFRL-IF-RS-TR-2004-2. 134 p.
Shestakov A.M., Shvets N.I., Khaskov M.A., Ponomarenko S.A., Minakov V.T. Compounds based on polycarbosilane and bismaleimide as precursors of ceramic-matrix composites // Russian Journal of Applied Chemistry. 2015. V. 88. № 9. P. 1481–1488.
Миков Д.А., Кутырев А.Е., Петрова В.А. Гидрофобизирующие составы для дополнительной защиты алюминиевых сплавов в топливных системах изделий авиатехники // Труды ВИАМ: электрон. науч.-технич. журн. 2015. № 9. Ст. 08. URL: http://viam-works.ru. (дата обращения 28.02.2018). doi 10.18577/2307-6046-2015-0-9-8-8.10.18577/2307-6046-2015-0-9-8-8
Валуева М.И., Зеленина И.В., Хасков М.А., Гуляев А.И. Подготовка углеродного волокна к нанесению интерфазного покрытия для композиционных материалов с керамической матрицей // Труды ВИАМ: электрон. науч.-технич. журн. 2017. № 10. Ст. 09. URL: http://viam-works.ru. (дата обращения 09.11.2017). doi 10.18577/2307-6046-2017-0-10-9-9.10.18577/2307-6046-2017-0-10-9-9
Хасков М.А., Давыдова Е.А., Валуева М.И., Шестаков А.М. Термокинетические исследования керамообразующей композиции на основе поликарбосилана и олиговинилсилазана // Неорганические материалы, 2018. Т. 54. № 11. С. 1228–1233.
Хасков М.А., Мельников Д.А., Котова Е.В. Подбор температурно-временных режимов отверждения эпоксидных связующих с учетом масштабного фактора // Клеи. Герметики. Технологии. 2017. Т. 10. С. 24–32.
Musić S., Filipović-Vinceković N., Sekovanić L. Precipitation of amorphous SiO2 particles and their properties // Brazilian J. Chemical Engineering. 2011. V. 28. № 01. P. 89–94.
Stern K.H. Oxidation of silicon, silicon carbide (SiC) and silicon nitride (Si3N4) // Naval Research Laboratory Report 5774. 1986. 63 p.
Дополнительные материалы отсутствуют.
Инструменты
Физика и химия стекла