Физика и химия стекла, 2020, T. 46, № 1, стр. 27-43
Органосиликатные покрытия. От истории создания до инноваций
Т. А. Кочина 1, *, Г. С. Буслаев 1, Ю. А. Кондратенко 1
1
199034 Санкт-Петербург, наб. Макарова, 2, Россия
* E-mail: t-kochina@mail.ru
Поступила в редакцию 24.05.19
После доработки 02.09.19
Принята к публикации 08.10.19
Аннотация
Изложены основные принципы создания органосиликатных покрытий. Представлены данные многолетних исследований свойств органосиликатных материалов, процессов, происходящих при их изготовлении, отверждении и воздействии различных эксплуатационных факторов. Описаны аспекты применения органосиликатных материалов и новые направления развития.
ВВЕДЕНИЕ
Органосиликатные покрытия были разработаны в Институте химии силикатов им. И.В. Гребенщикова РАН (ИХС РАН). В середине XX в. Институт получил правительственное задание на разработку теплостойких и атмосферостойких (в условиях влажного тропического климата) электроизоляционных покрытий для герметизации проволочных резисторов. Решение указанной задачи было возложено на лабораторию кремнийорганических соединений, которой в то время заведовал выдающийся ученый, профессор, доктор химических наук Б.Н. Долгов (1894–1959 гг.), автор первой в мире монографии, посвященной химии кремнийорганических соединений (1933 г.). К исследованиям прикладного характера лаборатории относили работы по гидрофобизации различных материалов. С принятием к исполнению правительственного задания зародилось и стало активно развиваться новое – материаловедческое направление, связанное с разработкой композиций для создания многофункциональных защитных покрытий. Это направление интенсивно развивается после назначения на должность заведующего лабораторией (1959 г.), тогда кандидата химических наук, Н.П. Харитонова.
В 1962 г. был предложен термин “органосиликатные материалы”. В 1978 г., с введением в действие новых технических условий, эти материалы стали называться органосиликатными композициями. Введение терминов органосиликатный материал (ОСМ) и органосиликатная композиция (ОСК) не случайно и обусловлено тем, что органосиликатные композиции представляют собой суспензии тонко диспергированных слоистых гидросиликатов (слюды–мусковита, хризотилового асбеста, талька и др.) и оксидов металлов (например, хрома, титана, цинка, циркония, вольфрама, ванадия и др.) в среде растворов полиорганосилоксанов с разветвленным и линейным строением молекул. Благодаря слоистому строению силикатов и наличию в них силанольных групп в сочетании с полисилоксанами после отверждения такая композиция образует единую пространственно сшитую структуру [1]. В образовании будущей матрицы материала вместе с полисилоксаном (ПОС) могут участвовать какие-либо органические полимеры, введенные в состав специально или присутствующие в составе используемых модифицированных кремнийорганических лаков. Теплостойкость, химическую стойкость и весь комплекс свойств, обеспечивающих надежное применение покрытий для атмосферостойкой и антикоррозионной защиты в тех или иных агрессивных средах, можно целенаправленно варьировать за счет рационального выбора полимерной основы, силикатов и оксидов.
По международной терминологии органосиликатные материалы можно отнести к “гибридным”. Это означает, что материалы получены “за счет взаимодействия компонентов различной химической природы, как правило, органических и неорганических, формирующих определенную пространственную структуру, отличающуюся от структур исходных реагентов, но часто наследующую определенные свойства и функции исходных структур” [2]. Силикатные компоненты, являясь обязательными, в сочетании с ПОС, способными к пространственной сшивке, образуют единую пространственно сшитую структуру и определяют главную особенность ОСМ – высокую термостойкость, значительно превышающую термостойкость исходного ПОС, взятого в индивидуальном состоянии или в композиции с несиликатными (например, только с оксидом металла) наполнителями. В структуре органосиликатных материалов сочетаются ценные свойства полиорганосилоксанов и неорганических компонентов. Полиорганосилоксаны придают материалам гидрофобность и эластичность, важную для получения пленочных покрытий, неорганические компоненты повышенную теплостойкость, химическую устойчивость и механическую прочность. Особенности структуры и состава органосиликатных материалов обеспечивают созданным на их основе покрытиям комплекс ценных свойств, сохраняющихся в широком диапазоне температур (от –60 до 600°С) и делают эти покрытия незаменимыми.
В зависимости от состава и функционального назначения создана классификация органосиликатных композиций, учитывающая их характеристику и особенности отдельных материалов [3]. Всем органосиликатным материалам присвоен буквенный символ ОС. Для разделения композиций по основному назначению выбраны группы от 1 до 9 в соответствии с ГОСТом 9825-73 “Материалы лакокрасочные. Классификация и обозначения”. Следующие цифры от 1 до 7 относят полимерное связующее к определенному виду. Далее идет порядковый номер композиции внутри группы по основному назначению.
Принципы создания органосиликатных материалов. Сразу же после первых практических достижений под руководством Н.П. Харитонова были начаты фундаментальные исследования, направленные на развитие научных основ получения ОСМ. Свойства органосиликатных композиций изучались в виде суспензий, изучались процессы, происходящие при формировании покрытий и при нагревании их до высоких температур, процессы термодеструкции полиорганосилоксанов.
Процессы, происходящие в системе полиорганосилоксан–силикат–оксид в результате механического воздействия. Причины хороших физико-механических свойств органосиликатных покрытий и их термостойкости кроются во взаимодействии наполнителей и кремнийорганической матрицы. Это взаимодействие возникает на стадии механической обработки органосиликатных суспензий, которая сопровождается прививкой полисилоксана к силикатным частицам. Образцы хризотилового асбеста, мусковита и талька после перемешивания в течение 48 ч в шаровой мельнице в растворе лака КО-915 с последующей их отмывкой в сокслете горячим бензолом содержали 2.82, 0.71 и 1.81% углерода соответственно [4]. Учитывая, что в кремнийорганическом полимере этого лака содержание углерода по расчету составляет 42.84%, то количество хемосорбированного на вышеуказанных силикатах полимера равняется 6.61, 1.87, 4.48%, соответственно.
При исследовании суспензий в первую очередь выясняли характер процессов, происходящих при механохимической обработке в шаровых мельницах и зависимость свойств самих суспензий и покрытий после их отверждения от режима обработки. Изучение процессов, происходящих при механическом воздействии на систему полиорганосилоксан–силикат–оксид, показало, что на этой стадии происходят сложные физико-химические процессы, приводящие к измельчению силикатов, образованию дефектов структуры силикатов и их некоторой аморфизации, возникновению активных центров по местам разрыва связи Si–O в силикатной решетке, механодеструкции полиорганосилоксанов с расщеплением связи Si–O–Si, а также к химической прививке (хемосорбции) молекул полиорганосилоксанов к силикатным частицам (рис. 1) [4, 5].
Предпосылками такого взаимодействия являются: полярный характер силоксановой связи Si–O, близкие или совпадающие параметры этих связей в кристаллической решетке силикатов и молекулах полиорганосилоксанов (табл. 1), высокая подвижность сегментов молекул полимера, наличие силанольных групп SiOH на поверхности силикатных частиц и в полимере (рис. 1).
Таблица 1.
Сопоставление характеристик силоксановых связей в силикатах и полиорганосилоксанах [6]
Параметры связей | Силикаты | Полиорганосилоксаны |
---|---|---|
Длина связи Si—O, Å | 1.60 | 1.64 |
Валентные углы Si—O—Si, ° | 130 | 130 |
Ионная составляющая, % | ~50 | ~50 |
Влияние времени механообработки на свойства покрытий. Были исследованы композиции, полученные при механообработке в течение 5, 12, 24, 36 и 48 ч и покрытия на их основе. Приемлемые гомогенизация и стабильность суспензий, а также защитные (противокоррозионные) свойства покрытий наблюдаются для образцов, обработанных в шаровой мельнице в течение 36 и 48 ч. В то же время физико-механические свойства покрытий (адгезия, твердость, прочность при ударе и изгибе) обнаружили малую зависимость или независимость от времени работы шаровой мельницы [7]:
Адгезия (для всех временных интервалов), балл | 1–2 |
Твердость, относительные ед. | 0.31–0.44 |
Прочность при ударе, см | 30–40 |
Прочность при изгибе, мм | 5–8 |
Электроизоляционные свойства (электрическая прочность Епр, удельное объемное электрическое сопротивление ρv, тангенс угла диэлектрических потерь tg δ, диэлектрическая проницаемость ε) были определены для покрытий из композиций, полученных при механической обработке в течение 5, 12, 24, 36 и 48 ч. По всем электроизоляционным показателям, кроме Епр, покрытие удовлетворяло установленным нормативам по электроизоляционным свойствам независимо от времени обработки в шаровой мельнице. Электрическая прочность достигает необходимого значения только при 24–36 ч обработке [7] (табл. 2).
Таблица 2.
Зависимость электроизоляционных свойств покрытий от времени механообработки суспензии (значения ρv измерялись как для покрытий в исходном состоянии (1) , так и после выдержки их во влажной камере при 20°С и φ = 95–98% (2))
Время механообработки суспензии, ч | 5 | 12 | 24 | 36 | 48 |
---|---|---|---|---|---|
ρv, Ом см (1) | 2.0 × 1014 | 2.0 × 1014 | 2.1 × 1014 | 2.7 × 1014 | 2.4 × 1014 |
ρv, Ом см (2) | 4.0 × 1010 | 2.0 × 1011 | 8.2 × 1011 | 2.4 × 1012 | 2.7 × 1012 |
Епр, кВ/мм | 6.4 | 9.3 | 10.4 | 11.5 | 14.1 |
tg δ при 50 Гц | 0.02 | 0.01 | 0.07 | 0.06 | 0.06 |
ε при 50 Гц | 4.3 | 4.5 | 4.7 | 4.7 | 5.3 |
Специальное внимание было уделено поиску путей повышения седиментационной устойчивости суспензий [8]. Проверены следующие возможности: механообработка всех компонентов ОСК без ПАВ; предварительная “сухая” механообработка смеси силикатных компонентов; введение ПАВ в процессе изготовления ОСК одновременно со всеми компонентами; с силикатами, механообработанными в присутствии ПАВ. Наилучший результат достигается при механообработке силикатов вместе с ПАВ (рис. 2). Во всех случаях осадки легко размешиваются после многомесячного хранения суспензий.
Формирование покрытий из органосиликатных композиций. При изучении процессов отверждения в системе полиорганосилоксан–силикат–оксид было показано, что формирование покрытий из органосиликатных композиций возможно как при горячем, так и холодном отверждении, что особенно важно при нанесении покрытий на поверхности, имеющие большую площадь. Механизм формирования покрытий при холодном и горячем отверждении заключается в возникновении новых химических связей в системе за счет взаимодействия функциональных групп полимеров, силикатов, оксидов и сшивающих агентов (в случае холодного отверждения) [9].
Горячее отверждение. Проведенные исследования показали, что для полного отверждения органосиликатных материалов путем нагревания, без добавления веществ, снижающих температуру отверждения, требуется термообработка при 200–300°С. Температурный интервал определяли по изменению прочности на изгиб (σизг) прессованных образцов органосиликатных материалов и их усадки в зависимости от температуры. На примере модельных композиций полиорганосилоксан–силикат было найдено, что прочность возрастает при нагревании, достигая максимума при 300°С. Затем наступает спад, вызываемый началом термодеструкции полимера. Прочность прессованных образцов ОСМ в промежутке температур 300–400°С падает от 20–25 до 12–15 МПа. Однако в интервале 400–500°С она вновь возрастает до 20–25 МПа (рис. 3). При высокотемпературной термообработке (>400°С) происходит постепенный переход ОСМ в неорганический материал с сохранением целостности, что является характерной особенностью органосиликатных материалов. При таком изменении структуры ОСМ в некоторых случаях наблюдается увеличение пористости и, как следствие, водопоглощения.
Рис. 2.
Седиментационные кривые ОСК: без ПАВ (1); с механообработанными силикатами, без ПАВ (2); с ПАВ, введенными перед началом диспергирования со всеми компонентами (3); с силикатами, механообработанными в присутствии ПАВ (4).
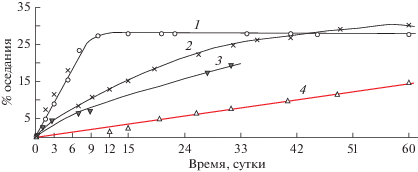
Некоторые ОСП после полного обезуглероживания превращаются в силоксансиликатные покрытия, имеющие при температурах до 600°С хорошие электроизоляционные свойства.
Наиболее вероятные химические реакции, приводящие к термическому отверждению органосиликатных материалов, представлены на (1).
(1)
$\begin{gathered} \equiv {\text{Si}}--{\text{OH}} + {\text{HOSi}} \equiv \, \to \, \equiv {\text{Si}}--{\text{O}}--{\text{Si}} \equiv + {\text{ }}{{{\text{H}}}_{{\text{2}}}}{\text{O}}, \\ \equiv {\text{Si}}--{\text{OH}} + {{{\text{C}}}_{{\text{6}}}}{{{\text{H}}}_{{\text{5}}}}{\text{Si}} \equiv \, \to \, \equiv {\text{Si}}--{\text{O}}--{\text{Si}} \equiv + \,{{{\text{C}}}_{{\text{6}}}}{{{\text{H}}}_{6}}, \\ \equiv {\text{Si}}--{\text{OH}}\, + \equiv {\text{Si}}{\text{--}}{\text{OH}} + {\text{C}}{{{\text{H}}}_{{\text{3}}}}{\text{Si}} \equiv \, \to \, \equiv {\text{Si}}--{\text{O}}--{\text{Si}} \equiv + \,{\text{C}}{{{\text{H}}}_{4}}, \\ \equiv {\text{SiC}}{{{\text{H}}}_{3}} + 3{{{\text{O}}}_{2}} + {\text{C}}{{{\text{H}}}_{3}}{\text{Si}} \equiv \, \to \, \equiv {\text{Si}}--{\text{O}}--{\text{Si}} \equiv + \,2{\text{C}}{{{\text{O}}}_{2}} + 3{{{\text{H}}}_{{\text{2}}}}{\text{O}}.~ \\ \end{gathered} $Об этих процессах свидетельствуют результаты анализа органосиликатных материалов на содержание в них силанольных групп после нагревания до 200 и 300°С. Концентрация гидроксилов (вес. %) на поверхности измельченных в порошок органосиликатных материалов после термообработки при 300°С, определенная методом Чугаева–Церевитинова–Терентьева [10] (2), вдвое меньше, чем после нагревания до 200°С, причем дальнейший подъем температуры до 400°С практически не изменяет этот показатель. Об этом же свидетельствует снижение на ИК-спектрах интенсивности поглощения при частотах 3450 см–1 и 3690 см–1, соответствующих силанольным группам.
(2)
$ \equiv {\text{Si}}--{\text{OH}} + {\text{C}}{{{\text{H}}}_{{\text{3}}}}{\text{MgJ}} \to {\text{C}}{{{\text{H}}}_{4}} + \equiv {\text{SiOMgJ}}.$Метан, бензол, углекислый газ и вода были обнаружены при масс-спектрометрическом изучении летучей фракции, выделяющейся в процессе нагревания органосиликатных материалов [11].
При разработке режима горячего отверждения были определены скорость повышения температуры (оптимально 2–3°C/мин) и продолжительность изотермической выдержки с учетом строения и свойств полимеров и других компонентов, входящих в состав органосиликатных композиций (как правило, 3 ч).
Холодное отверждение. Важной особенностью органосиликатных покрытий, как уже отмечалось, является их способность отверждаться без термической обработки и даже при низких температурах, вплоть до –20°C. При холодном формировании покрытий применяются сшивающие агенты (отвердители). Используемые в качестве компонентов органосиликатных материалов кремнийорганические полимеры имеют в основном разветвленную структуру и содержат силанольные или иные функциональные группы, за счет которых прежде всего и происходит образование пространственно-сшитой пленки полимера под действием сшивающих агентов.
Отвердители по своему действию можно разделить на три вида: каталитические: выполняют роль катализатора при реакции силанольных групп макромолекул полимера и силикатов с выделением воды; химические: между отвердителем и кремнийорганическим полимером образуется химическая связь (рис. 4); активирующие: отвердитель (например, силазан), взаимодействуя с другим веществом (например, влагой воздуха) образует катализатор отверждения. Отверждение покрытий из органосиликатных материалов при комнатной температуре протекает несколько быстрее, чем у чистых полисилоксановых пленок, за счет присутствия силикатных и оксидных компонентов. Наиболее используемыми отвердителями являются: тетрабутоксититан (C4H9O)4Ti, полибутоксититанат [–OTi(OC4H9)2–]n, гексаметилендиаминометилтриэтоксисилан H2N(CH2)6NHCH2Si(OC2H5)3, (АГМ-3) и аминопропилтриэтоксисилан H2N(CH2)3Si(OC2H5)3 (АГМ-9). Для композиции с введенным отвердителем обычно производится послойное нанесение с воздушной сушкой каждого слоя при температуре 15–35°С в течение 30–60 мин. Последний слой выдерживается при той же температуре в течение 72 ч. Предполагаемый механизм взаимодействия титанорганических эфиров с кремнийорганическим полимером представлен ниже (рис. 4).
Рис. 4.
Химические реакции, обеспечивающие взаимодействие между компонентами органосиликатной композиции при холодном отверждении с участием химического отвердителя Ti(OBu)4.
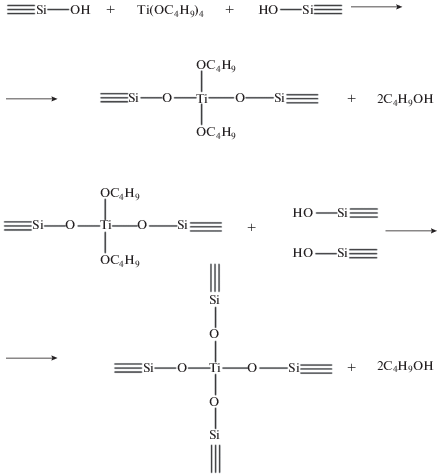
Некоторые органосиликатные покрытия холодного отверждения по своим свойствам не уступают, а иногда даже превосходят (прочность на изгиб, прочность на удар) термоотвержденные покрытия (табл. 3).
Таблица 3.
Некоторые свойства органосиликатных покрытий, полученных путем холодного и горячего отверждения [9]
Покрытие | Прочность при ударе по прибору У-2, см | Твердость по прибору М-3 | Адгезия по способу решетчатого надреза, баллы | Прочность при изгибе по прибору ШГ-1, мм | ρv, Ом см | Т, °С |
---|---|---|---|---|---|---|
ОC-12-01 горячего отверждения | 40 | 0.6 | 1 | 15 | 1014 | 400 |
ОC-12-01 холодного отверждения | 40 | 0.5 | 1 | 10 | 1014 | 400 |
ОС-82-01 горячего отверждения | 50 | 0.5 | 1 | 5 | 1014 | 500 |
ОС-82-01 холодного отверждения | 50 | 0.6 | 1 | 5 | 1014 | 500 |
Были измерены внутренние напряжения (σвн) сжатия и растяжения, возникающие в пленках покрытий естественной и горячей сушки, в зависимости от вида используемого ПОС и температуры термообработки [12], а также наличия силикатных и оксидных компонентов [13].
В [12] показано, что в лаковых пленках, высушенных при комнатной температуре, напряжений практически не возникает; при нагревании до 150–250°С наблюдаются небольшие напряжения сжатия, при охлаждении от указанных температур до комнатной развиваются значительные напряжения растяжения. Значения σвн минимальны для ПОС, у которых метильная и фенильная группы находятся при одном атоме кремния.
Величины σвн наполненных ПОС экстремально зависят от содержания наполнителя в композиции [13], имея максимум при 40–60% концентрации силикатов. При охлаждении от 250°С до комнатной температуры они достигают 90 кГ/см2 (мусковит), 30 кГ/см2 (тальк), 20 кГ/см2 (асбест).
Окислительная и термоокислительная деструкция. Методами дифференциально-термического анализа (ДТА), термогравиметрии (ТГ), пиролитической масс-спектрометрии и газохроматографического анализа летучих продуктов разложения были изучены процессы, происходящие в ОСК при нагревании до температур, вызывающих деструкцию ПОС-матрицы композиции. Исследовали термическую и термоокислительную деструкции полидиметилфенилсилоксана со среднестатистическим звеном [C6H5SiO1.5][(CH3)2SiO]0.73 и его композиции с силикатами и оксидами [14]. Основными наблюдаемыми летучими продуктами полидиметилфенилсилоксана и органосиликатной композиции являются метан (CH4), бензол (C6H6), вода (H2O) и циклодиметилсилоксаны [(CH3)2SiO]n (Dn), главным образам D3 и D4. В среде кислорода и воздуха дополнительно появляются CO2, CO. Повышается выделение воды. Полученные результаты позволили выявить зависимость процессов разложения от скорости нагревания, характера окружающей среды (инертный газ, воздух, вакуум), природы оксидного или силикатного наполнителя, наличия адсорбированной оксидами и силикатами влаги и т.д. По данным ТГ разложение полидиметилфенилсилоксана в среде гелия происходит в два-три этапа, температурные границы которых зависят от скорости нагревания [15]. Возможно такая многоэтапность, связана с немонотонной зависимостью выхода легколетучих продуктов от температуры при скорости нагревания 2°С/мин, термодеструктивным (пиролитическим) на первом этапе и термоокислительным характером процесса разложения на втором этапе и разрушением на каждом этапе связей с различными энергиями [14].
Процессы, происходящие в системе при нагреве до 1000–1500°С. Твердофазные реакции и структурные изменения, происходящие при нагревании до температур, значительно превышающих термодеструкцию ПОС (1000–1500°С), исследовали на модельных композициях (МК): ПОС + силикат; ПОС + оксид + силикат; ПОС + стекло; ПОС + силикат + стекло [16, 17]. По данным ДТА и ТГ, проведенных в среде гелия до температуры 1000°С, асбест и ПОС в процессе нагревания взаимно влияют друг на друга. Продукт разложения ПОС смещает эндоэффект, связанный с дегидроксилизацией силиката, в сторону более низких температур, т.е. активирует перестройку решетки асбеста, а максимальная скорость термодеструкции ПОС в присутствии асбеста наблюдается при более высокой температуре.
С помощью рентгенофазового анализа модельных композиций с асбестом или тальком, содержащих стекло состава (мол. %) 5.0Na2O · 13.0B2O3 · 82.0SiO2 (температура размягчения (Tw) = 685°С; температура трансформации (Tt) = 515°С определенные с помощью дилатометрии) и термообработанных при температурах 800–1000°С, показано, что в результате взаимодействия размягченного стекла с продуктами преобразования магнийсодержащих силикатов образуется борат магния 2MgO · B2O3 [4]. Электронной микроскопией констатировано появление в стеклофазе зародышей кристаллизации в температурной области выше 700°С, которые относятся к борату магния. Протекание твердофазной реакции MgO с B2O3 из стекла очень важно в особенности при использовании асбеста, т. к. перестройка его решетки идет через стадию аморфизации и высвобождения оксида MgO, который катализирует расщепление силоксановых связей матрицы материала. Связывание MgO с оксидом бора в борат должно способствовать повышению термостабильности матрицы. Дифференциально-термическим, рентгенофазовым и микрорентгеноспектральным методами анализа, а также методами электронной микроскопии и термогравиметрии установлено, что повышенные термостойкость, электрическая прочность и плотность покрытия, содержащего в своем составе алюмоборосиликатное стекло состава (мол. %) 14.5Al2O3 · 10.3B2O3 · 53.3SiO2 · 17.1CaO · 4.0MgO с температурой размягчения 830°С, хризотиловый асбест и тальк, обусловлены блокированием процесса высвобождения MgO и, как следствие, прохождением термического распада силоксанового каркаса полимерной матрицы материала на меньшую глубину по сравнению с композицией, в которой стекло отсутствует.
Особенности органосиликатных композиций и покрытий на их основе. Уникальность органосиликатных покрытий состоит в их способности при высокотемпературной термообработке (300–500°С) переходить из органополимерного в неорганический материал без нарушения целостности и адгезии к подложке, что нехарактерно для лакокрасочных покрытий. Температура эксплуатации этих покрытий может достигать 700°С, что превосходит термическую устойчивость всех известных лакокрасочных покрытий. Температура эксплуатации эпоксидных покрытий составляет 100–150°С, температурные пределы фторопластовых покрытий от –60 до +150°С, покрытия на основе полимера тетрафторэтилена (тефлона) обладают высокой степенью стойкости, сохраняют физико-механические свойства в диапазоне температур от −70 до +270°C.
Преимущество температуроустойчивых органосиликатных покрытий перед неорганическими эмалями состоит в том, что последние имеют высокую температуру формирования (минимум на 200–300°С выше температуры эксплуатации). При этом существует необходимость точной подгонки коэффициента термического расширения эмали и подложки. У органосиликатных покрытий температура отверждения на 200–300°С ниже допустимой температуры эксплуатации. Сравнительно высокое относительное удлинение позволяет использовать одну и ту же композицию для различных подложек. Органосиликатные покрытия обладают стойкостью к термическому удару (от −60 до 700°С). Они хорошо противостоят не только воздействию высоких температур, но и низких (до –60°С).
Недостатком ОСК является использование в качестве растворителя токсичного толуола. Преимуществом использования толуола является возможность нанесения органосиликатных покрытий при минусовой температуре и транспортировки ОСК при низких температурах, что важно для их использования в Арктике. Толуол не вызывает коррозии металлической тары даже при длительном хранении ОСК. Следует отметить, что при высокотемпературной обработке органосиликатные покрытия становятся пористыми.
Применение органосиликатных покрытий. Уникальные свойства ОСМ сделали их незаменимыми в решении многих научно-технических задач. В ИХС РАН разработаны органосиликатные композиции для создания атмосферостойких, противокоррозионных термостойких, морозостойких, радиационностойких, антиобледенительных и электроизоляционных покрытий [18–20]. Органосиликатные покрытия нашли широкое применение для защиты от атмосферной коррозии строительных стальных конструкций, технологического оборудования, трубопроводов различного назначения, пролетных строений мостов, стальных и железобетонных конструкций транспортных тоннелей и др.
Особо следует отметить органосиликатные покрытия специального назначения. На основе саморасслаивающейся полимерной системы, которую образуют толуольные растворы полидиметилфенилсилоксана и полидиметилсилоксана [21], была получена ОСК для антиобледенительного защитного покрытия, понижающего силу сцепления льда в 7–10 раз по сравнению с незащищенной стальной поверхностью, в 2–5 раз – с окрашенной органическими эмалями.
Большое внимание было уделено органосиликатным композициям, применяемым для формирования противокоррозионных тепло- и радиационностойких покрытий в атомной энергетике. Объекты атомной энергетики (элементы атомных реакторов, контейнеры для транспортировки отработанного топлива, могильники, стены и потолки служебных помещений, вентиляционные системы и др.) предъявляют повышенные требования к конструкционным материалам и покрытиям. Они должны обладать радиационной стойкостью (не ниже 106 рад.), легко дезактивироваться, быть противокоррозионными, термостойкими, стойкими к специфическим агрессивным средам и иметь срок службы не менее трех лет. В результате целенаправленной разработки были получены радиационностойкие защитные и электроизоляционные органосиликатные покрытия, стойкие в условиях нейтронного облучения в паровоздушной среде действующего реактора при потоке нейтронов от 1021 н/см2 (150°С) до 1014 н/см2 (280°С) в течение 10 000–20 000 ч [22–25]. Эпоксидные покрытия устойчивы лишь около 3000 ч при 90°С и потоке нейтронов 1014 н/см2. ОСП стойки и к воздействию гамма-облучения [25]. В состав радиационностойких композиций введен оксид вольфрама, катализирующий реакцию конденсации силанольных групп полимера, что способствует более глубокой его пространственной сшивке и образованию более плотной матрицы материала.
ОСК оказалась весьма эффективной для изготовления и приклейки высокотемпературных проволочных тензорезисторов [26, 27].
Разработка органосиликатных композиций и освоение их промышленного выпуска в 1982 г. удостоены Государственной премии СССР.
Тенденции развития. Потребность в органосиликатных материалах, обладающих высокими эксплуатационными свойствами, сохранилась и в наши дни. Современное развитие науки и техники предъявляет новые требования к защитным покрытиям. Исследования, начатые Н.П. Харитоновым продолжаются. Разрабатываются новые варианты ОСК с расширением круга используемых полимерных и неорганических компонентов, введением различных добавок специального назначения. Совершенствуется технология ОСК, касающаяся как процесса их изготовления, так и способов применения, появляются новые области использования органосиликатных покрытий. В частности, для повышения теплостойкости исследовались свойства покрытий ОСК, содержащих в своем составе в качестве активной добавки алюмофосфаты [20]. Было установлено, что последние взаимодействуют с кремнийорганическим связующим материала. Реакция идет между силанольными группами ПМФС и гидроксильными группами фосфата с образованием связи Si–O–P [28]. С однозамещенным фосфатом Al(H2PO4)3 реакция идет уже при комнатной температуре и материал желируется в процессе перемешивания в шаровой мельнице. При использовании двухзамещенного алюмофосфата Al2(HPO4)3 · 2.5H2O (ДАФ) желирование не наблюдали ни при получении ОСК, ни при ее хранении в течение года. При повышенной температуре под действием ДАФ происходит желатинезация ПМФС. Смешение масс ДАФ : ПФМС в отношении 1 : 3.32 при 150°С в течение 2 ч привело к 95% желатинезации. Без ДАФ при вышеуказанных условиях желатинезация ПМФС не происходила. Теплостойкость данного покрытия составляет 600°С и стойкость к термоудару: от 600 до –60°С. Эти покрытия были удостоены “Золотой медали” и диплома I степени в конкурсе “Лучший инновационный проект и лучшая научно-техническая разработка года” в рамках Петербургской технической ярмарки (2014 г.) и “Серебряной медали” на XVIII Московском международном Салоне изобретений и инновационных технологий “Архимед” (2015 г.).
С целью создания электроизоляционного покрытия с высокой адгезией к металлу с теплостойкостью до 700°С и меньшей пористостью после выгорания органического компонента разработана рецептура органосиликатной композиции с использованием в качестве активных наполнителей алюмоборосиликатного стекла и оксида ванадия [29].
Проведена работа по усовершенствованию защитного ОСП для атомных электростанций. Применяемое в настоящее время покрытие ОС-51-03 имеет недостаточную гидрофобность. Заводы-поставщики оборудования с этим покрытием для повышения гидрофобности добавляли к композиции ОС-51-03 значительное количество связующего, что приводило к недопустимому снижению теплостойкости покрытия. Разработанный нами состав за счет уменьшения содержания пигмента (оксида) имеет повышенное содержание связующего, но его соотношение к силикатам не превышает 2.24 : 1. Это позволяет придать покрытию необходимую гидрофобность и сохранить теплостойкость 300°С.
С целью дальнейшего повышения теплостойкости покрытий разработана ОСК, содержащая в качестве активной добавки ванадийфосфатное стекло. Полученное покрытие имеет теплостойкость 800°С и стойкость к термоудару 20‒800°С и обратно троекратно. Ввиду агрессивности стекла по отношению к кремнийорганическому связующему уже через сутки наблюдается процесс желатинизации композиции. В настоящее время проводятся исследования по разработке двухкомпонентного состава. Один состав содержит кремнийорганическое связующее, но не содержит стекло, другой содержит стекло, но на связующем инертным к стеклу. Покрытие наносится сразу после совмещения обоих составов.
В настоящий момент активно ведутся исследования по разработке защитных экологически безопасных покрытий от биокоррозии и обрастания.
Защита от биодеструкции и биообрастания. Проблема морского обрастания стоит на одном из первых мест среди других проблем разрушения материалов. Основными объектами, которые наиболее остро страдают от биообрастаний являются морские суда, портовые сооружения, водоводы и трубопроводы, теплообменники, нефтяные и газовые платформы на шельфе, навигационное и подводное оборудование, гидробиотехнические сооружения и др. Одним из основных способов защиты от морской коррозии и обрастания являются противокоррозионные и противообрастающие лакокрасочные покрытия, в которые введены специальные вещества ‒ биоциды, подавляющие жизнедеятельность биологических объектов. В большинстве промышленных лакокрасочных материалов в качестве биоцидных добавок используют соединения таких металлов, как олово, свинец, ванадий [30], а также мышьяк и хром [31–33]. Целесообразность использования свинца, олова и других вышеуказанных металлов не оправдана из-за соображений токсичности, и особенно в отношении покрытий для обработки поверхностей подводной части судов [34]. Выделяя в воду значительные количества вредных соединений (олова, меди, мышьяка, свинца, цинка и др.) они неизбирательно убивают или отравляют любые организмы либо непосредственно у защищаемой поверхности, либо в результате накопления ядов в удаленных от них организмах. Вышеперечисленные биоциды относятся к ведущим загрязнителям окружающей среды и от их использования в составах покрытий в ряде стран уже отказались, поскольку они высокотоксичны и могут циркулировать по цепям питания и аккумулироваться в организмах.
В качестве биоцидов широко применяют полимерные соединения, на основе гуанидина, хлорметильные производные ароматических углеродов с пиридином и др. [35]. Синтетические производные гуанидина активно используют как антимикробные, бактерицидные и фунгицидные средства. Главным недостатком полимерных соединений гуанидина является низкая растворимость в органических растворителях, используемых в рецептурах ЛКМ, что ограничивает возможность их использования в органоразбавляемых и радиационно-отверждаемых ЛКМ, традиционно применяемых в качестве покрытий для подводной части судов [34].
Для борьбы с биообрастанием в промышленности также применяют подход, основанный на применении самополирующихся сополимеров (в основном акриловые полимеры). Такие противообрастающие системы содержат в качестве основы акриловый полимер, к которому крепится молекула биоцида. Данная молекула реагирует с солями, растворенными в морской воде. На поверхности краски образуется растворимое вещество. В результате пленка краски становится мягче и происходит процесс самополирования поверхности, который происходит тем интенсивнее, чем выше скорость судна и не прекращается при остановке [36].
В [37] описан пленкообразующий сополимер, содержащий в качестве сомономера триорганоолово, дающее самополирующиеся противообрастающие покрытия. Во многих самополирующихся красках [37, 38] используют связующее, содержащее в качестве отщепляемых групп триорганооловянные сложные эфиры. Сложные эфиры триорганоолова легко гидролизуются, что определяет самополирующиеся свойства, а выделяющееся триорганоолово обеспечивает биоцидное действие [39]. Выделение оловосодержащих соединений в морскую воду следует отнести к недостаткам данных покрытий.
Известна технология, в основе которой лежит применение покрытий с низкой поверхностной энергией (как правило, покрытия на основе кремний- или фторсодержащих полимеров с низким модулем упругости). Осевшие микро- и макрообрастатели непрочно прикрепляются к поверхности и удаляются механически при движении судна. Такие покрытия рекомендованы к применению на судах со скоростью более 10 узлов [36, 40].
Большое внимание уделяется разработке экологически безопасных и высокоэффективных биоцидов для защиты покрытий и материалов от биообрастания. Для защиты древесины от биодеструкторов часто применяют медь-содержащие соединения. Известно средство для защиты от биоповреждений древесных и лакокрасочных материалов, содержащее эффективное количество моногидрата дихлорида трикапролактамомеди(II) [41], выпускаемое под названием картоцид (рис. 5).
Картоцид является хорошим средством для защиты сырой пиловочной древесины и изделий из нее от дереворазрушающих и деревоокрашивающих грибов и других патогенов, приводящих к повреждению и разрушению конструкций из дерева. Картоцид не обладает широким спектром биоцидного действия и может применяться только для ограниченного круга неметаллических материалов. В [42] предложено биоцидное средство, состав которого включает картоцид, поверхностно-активные вещества, препараты юглон и/или перметрин или циперметрин и/или глисол, для защиты древесины, минеральных, искусственных строительных материалов или строительных материалов из природного камня, а также лакокрасочных покрытий от биокоррозии, вызываемой грибами, бактериями и другими микроорганизмами и насекомыми. Препараты на основе картоцида выпускаются исключительно в виде водных растворов.
Известны биоциды на основе медных и цинковых солей с уксусной и метакриловой кислотами [43], с акриловой/метакриловой и ароматическими кислотами в сочетании с ионогенными и неионогенными поверхностно-активными веществами и другими добавками [44]. Биоциды на основе смеси пиритионовой соли цинка и оксида меди(I) или тиоцианата меди [45]. Наиболее известным и доступным биоцидом является оксид меди(I), который обладает высоким фунгицидным действием. Однако его применение в качестве компонента красок и защитных материалов, защищающих подводную часть судна от обрастания, ограничено тем, что вещество является умеренно токсичным (LD50 470 мг/кг (крысы)) и очень токсичным для водной среды (LC50 0.5 мг/л). Кроме того из-за неравномерной скорости выщелачивания оксида меди(I) из покрытия, срок эффективного действия таких покрытий не превышает 1.5–2 г. [46].
Для обеспечения эффективной и длительно действующей защиты судов и гидротехнических сооружений от биобрастания известна технология многослойного комбинированного противообрастающего покрытия, обеспечивающего репеллентно-хемобиоцидную защиту [39]. С целью увеличения срока эффективного действия необрастающей краски, а также с целью снижения трения при движении судна на поверхность краски наносят тонкий гидрофильный или частично растворимый в морской и пресной воде слой. Такой слой, препятствуя выщелачиванию биоцида из нижележащего слоя, регулирует и снижает начальную скорость его выщелачивания.
В случае, когда наоборот необходим выход биоцида на поверхность, в работе [47] предлагают использовать производные канифоли. Постепенное растворение частиц канифоли создает микропоры в покрытии и облегчает диффузию биоцида на поверхность. Из-за растворения канифоли в воде срок службы таких покрытий очень низкий. Однако данное покрытие возможно наносить на другие виды противообрастательных красок для более эффективной защиты.
В работах [48, 49] в качестве биоцидов применяют серебросодержащие соединения (стеарат или пальмитат серебра(I), [Ag(NH3)2]+, [AgI2]–). В работе [50] в лакокрасочный материал вводят биоцидные добавки на основе наноструктурных частиц серебра или меди или смеси наноструктурных частиц серебра и меди. К основным недостаткам наноструктурных биоцидов относятся: низкий срок работы, что связано с явлением коагуляции наночастиц металла, выпадение их в осадок при хранении ЛКМ и высокая стоимость [34].
В ИХС РАН на протяжении уже нескольких десятилетий ведутся работы в области синтеза и исследования структуры и свойств внутрикомплексных биологически активных соединений триэтаноламина (ТЕА) – атранов. Особое место среди атранов занимают триэтаноламмониевые соли протонных кислот или протатраны (рис. 6а) общей формулы N+H(CH2CH2OH)3 · X–, где X – анион протонной кислоты. Исследования протатранов начались в 70-х гг. прошлого столетия под руководством академика М. Г. Воронкова, и на сегодняшний день синтезирован широкий ряд триэтаноламмониевых солей как с неорганическими, так и с органическими анионами [51–53]. Взаимодействие ТЕА с солями переходных металлов приводит к образованию гидрометаллатранов ‒ комплексов разнообразного строения (рис. 6б, в), среди которых катионные моноядерные комплексы, состоящие из [M(TEA)2]n+ катионов и анионов протонных кислот, моноядерные комплексы смешанного типа, би- и полиядерные комплексы смешанного типа, содержащие одну и более депротонированных гидроксиэтильных групп ТЕА.
Рис. 6.
Строение атранов: протатраны (а), X – анион протонной кислоты; гидрометаллатраны – катионные моноядерные (б) и би-, полиядерные (в) комплексы ТЕА (X, Y, Z ‒ лиганды (анионы кислот, молекулы растворителя и др.)).
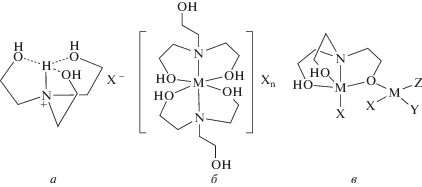
За последние несколько лет в ИХС РАН синтезирован широкий ряд новых представителей атранов – протатранов биологически активных карбоновых кислот (коричная, бензойная, салициловая, янтарная, малоновая, щавелевая, яблочная, лимонная) [52] и гидрометаллатранов с солями меди(II) [54], кобальта(II) [55, 56] цинка(II) [57], марганца(II) и железа(III) [58]. Исследованы структурные особенности, термическая устойчивость и биологическая активность [59–62]. Среди внутрикомплексных соединений ТЕА выявлены вещества, обладающие высокой активностью к бактерии Staphylococcus aureus (золотистый стафилококк). Исследования в данном направлении активно продолжаются до сих пор. Благодаря высокой биологической активности широкого спектра действия, отсутствию токсичности и возможности варьировать состав внутрикомплексные соединения гидроксиалкиламинов можно рассматривать как перспективные добавки биоцидного действия (мягкие биоциды) в составы композиционных материалов для эффективной защиты конструкционных материалов, в частности, поверхностей подводной части судов, от биообрастания и биодеструкции. В ИХС РАН разработаны составы антикоррозионных, стойких к морской воде покрытий холодного отверждения на основе эпоксикаучукового связующего. Данное покрытие после испытания в 3% водном растворе хлористого натрия в течение 12 мес. не имело следов коррозии. Введение мягких биоцидов на основе соединений гидроксиалкиламинов в составы стойких к морской воде композиций позволит разработать новые экологически безопасные покрытия для длительной и эффективной защиты плавсредств от коррозии, биобрастания и биодеструкции.
ЗАКЛЮЧЕНИЕ
Особенности структуры и состава органосиликатных композиций обеспечивают созданным на их основе покрытиям и материалам (герметикам, клеям, связующим высоконагревостойких стеклопластиков и др.) комплекс весьма ценных свойств в широком диапазоне температур (от –60 до +800°С), что позволяет широко их использовать в различных областях человеческой деятельности.
Современное развитие науки и техники предъявляет новые требования к защитным покрытиям, поэтому исследования, начатые Н.П. Харитоновым, активно продолжаются до сих пор. В настоящее время ведутся исследования по разработке органосиликатных композиций для создания покрытий нового поколения с улучшенными свойствами, которые позволят использовать их в решении различных задач, в том числе в военной промышленности и атомной энергетике, предъявляющей повышенные требования к конструкционным материалам и покрытиям.
С использованием синтезированных в ИХС РАН мягких биоцидов на основе внутрикомплексных соединений гидроксиалкиламинов разрабатываются экологически безопасные покрытия для защиты различных поверхностей от биодеструкции и обрастания.
Список литературы
Харитонов Н.П. Реакционная способность компонентов органосиликатных материалов в широком диапазоне температур // Кремнийорганические соединения и материалы на их основе. Тр. V совещ. по химии и практическому применению кремнийорганических соединений. Л.: Наука, 1984. С. 150–155.
Кудина Е.Ф. Органосиликатные материалы (обзор) // Материалы. Технологии. Инструменты. 2013. Т. 18. № 4. С. 31–42.
Харитонов Н.П., Кротиков В.А., Островский В.В. Органосиликатные композиции: Каталог-справочник. Л., 1980.
Харитонов Н.П., Веселов П.А., Кузинец А.С. Вакуумноплотные композиционные материалы на основе полиорганосилоксанов. Наука, Л. 1976. 194 с.
Кротиков В.А., Хоритонов Н.П. Изучение процессов, происходящих при механо-химическом воздействии на полиорганосилоксан- силикатные суспензии // Неорганические и органосиликатные покрытия: Тр. 6-го Всесоюзн. Совещания по жарост. покр. Л., Наука. 1975. С. 374–383.
Воронков М.Г., Милешкевич В.П., Южелевский Ю.А. Силоксановая связь. Новосибирск. Наука СО. 1976. 414 с.
Кротиков В.А., Бессонов А.А., Харитонов Н.П., Смирнова З.П. Исследование зависимости свойств органосиликатных покрытий типа ОС-12 от продолжительности механической обработки суспензий на стадии изготовления композиций // Кремнийорганические соединения и материалы на их основе: Тр. V совещ. по химии и практическому применению кремнийорганических соединений. Л.: Наука, 1984. С. 164–166.
Кротиков В.А. Органосиликатные и неорганические неметаллические материалы на основе композиций с кремнийорганическими и другими элементоорганическими соединениями. Санкт-Петербург: Наука. 1998. 40 с.
Харитонов Н.П., Кротиков В.А., Худобин Ю.И. Буслаев Г.С., Степанов К.Н. Органосиликатные материалы, их свойства и технология применения. Л.: Наука. 1979. 200 с.
Терентьев А.П. Органический анализ. М. 1966. С. 136–166.
Островский В.В., Стародубцева Н.Н., Спиридонов В.И., Харитонов Н.П. Исследование летучих продуктов разложения, образующихся при нагревании органосиликатных покрытий // Температуроустойчивые покрытия: Тр. 11-го Всесоюзн. Совещания по жарост. Покр. Л.: Наука.1985. С. 265–269.
Буслаев Г.С., Рухленко В.П., Харитонов Н.П. Зависимость внутренних напряжений кремнийорганических покрытий от температуры от температуры отверждения и состава полимера // Кремнийорганические соединения и материалы на их основе: Тр. V совещ. по химии и практическому применению кремнийорганических соединений. Л.: Наука, 1984. С. 158–160.
Буслаев Г.С., Рухленко В.П., Харитонов Н.П. Влияние силикатов и оксида хрома на величины внутренних напряжений в полиметилфенилсилоксановых покрытиях // Кремнийорганические соединения и материалы на их основе: Тр. V совещ. по химии и практическому применению кремнийорганических соединений. Л.: Наука, 1984. С. 161–164.
Харитонов Н.П., Островский В.В. Термическая и термоокислительная деструкция полиорганосилоксанов. Л.: Наука. 1982. 208 с.
Островский В.В., Харитонов Н.П. Прогнозирование разложения полиорганосилоксанов при различных скоростях нагревания // Журн. прикл. химии. 1985. Т. 58. № 11. С. 2595–2597.
Островский В.В., Глебова И.Б., Стародубцева Н.Н., Харитонов Н.П. Изучение процессов, происходящих в органосиликатных покрытиях на основе систем полиоганосилоксан–асбест (каолин) при нагревании до 1000°С // Жаростойкие покрытия для защиты конструкционных материалов: Тр. 7-го Всесоюзн. Совещания по жарост. Покр. Л.: 1977. С. 237–240.
Веселов П.А., Харитонов Н.П., Колганова Е.В., Деген М.Г. Фазовые превращения в органосиликатных покрытиях системы полиорганосилоксан-хризотиловый асбест-стекло // Жаростойкие покрытия для защиты конструкционных материалов: Тр. 7-го Всесоюзн. Совещания по жарост. Покр. Л.: 1977. С. 244–248.
Красильникова Л.Н., Чуппина С.В., Кротиков В.А., Шнурков Н.А., Фокина Л.Т. Композиция для антиобледенительного покрытия. Патент РФ № 2156786. Заявл.: 98124088/04, 30.12.1998; Опубл. 27.09.2000. Бюл. №27.
Буслаев Г.С., Кочина.Т.А. Органосиликатная композиция. Патент РФ № 2520481. Заявл.: 2012151419/05, 30.11.2012; Опубл. 27.06.2014. Бюл. № 18.
Буслаев Г.С., Кочина Т.А., Проскурина О.И. Органосиликатные покрытия,содержащие двузамещенный алюмофосфат, для теплостойкой электроизоляции // Физ. и хим. стекла. 2016. Т. 42. № 3. С. 395–399.
Красильникова Л.Н., Бойцова Т.Н., Никитина Н.А., Харитонов Н.П.Изучение саморасслаивающихся систем растворов кремнийорганических полимеров // Кремнийорганические соединения и материалы на их основе: Тр. V совещ. по химии и практическому применению кремнийорганических соединений. Л.: Наука, 1984. С. 155–158.
Глушкова Н.Е., Красильникова, Л.Н., Хоритонов Н.П., Расс В.В. Отмываемые органосиликатные покрытия // Антикоррозионные покрытия: Тр. 10-го Всесоюзного совещания по жаростойким покр. Л.: Наука,1983. С. 267–269.
Ампелогова Н.И., Глушкова Н.Е., Кротиков В.А. Использование органосиликатных дезактивируемых покрытий в атомной энергетике // Температуроустойчивые функциональные покрытия: Тр.XVII совещания по температуроуст. функц. покр. Ч. 1: Пленарные доклады. СПб: НИИХ СПбГУ, 1997. С. 169–173.
Леонгард А.Д., Шашков Ю.Г., Харитонов Н.П., Худобин Ю.И. Влияние радиационного облучения на физические свойства органосиликатных композиций // Кремнийорганические соединения и материалы на их основе: Тр. V совещ. по химии и практическому применению кремнийорганических соединений. Л.: Наука, 1984. С. 171–174.
Шашков Ю.Г., Худобин Ю.И., Леонгард А.Д., Харитонов Н.П. Радиационная стойкость покрытий из органосиликатных композиций в ɤ-полях // Кремнийорганические соединения и материалы на их основе: Тр. V совещ. по химии и практическому применению кремнийорганических соединений. Л.: Наука, 1984. С. 275–278.
Nekhendzy E.J., Krotikov V.A., Khudobin Y.i.,Tarasov R.A. High temperature strain gages with application of new organosilicate adhesives // Proc. VIII Internat. Congress on experimental mechanics. Nashwille (USA). 1996. P. 298–299.
Нехендзи Е.Ю., Тарасов Р.А., Кротиков В.А., Виук С.П. Стабилизация температурных характеристик сопротивления тензорезисторов типа ТТР ЛС-22-24тм в интервале температур 20–550°С // Температуроустойчивые функциональные покрытия: Тр. XVII совещания по температуроуст. функц. покр. Ч. 2: Стендовые доклады. СПб: НИИХ СПбГУ, 1997. С. 177–178.
Воронков М.Г., Малетина Е.А., Роман В.К. Кремнекислородные соединения неметаллов. Производные азота и фосфора. Новосибирск: Наука, 1988. 365 с.
Буслаев Г.С., Кочина Т.А., Милютина П.А. Создание электроизоляционного органосиликатного покрытия с высокой адгезией к металлу и с теплостойкостью до 700°С // 5-я Международная конференция стран СНГ “Золь-гель синтез и исследование неорганических соединений, гибридных функциональных материалов и дисперсных систем”. 2018. С. 50–51.
Yamamori N., Matsuda M., Higo K., Ishikura S. Preparation of metal containing resin composition and antifouling paint containing said composition. Patent US № 4918147, Priority date 1986-11-17; Publication date 1990-04-17.
Каминский Ю.Д., Копылов Н.И., Ляхов Н.З. Биоцид для противообрастающего покрытия. Патент РФ № 2433154. Заявл.: 2010117097/05, 29.04.2010; Опубл.: 10.11.2011 Бюл. № 31.
Фролов Ю.П. Защитное покрытие конструкций, работающих в агрессивных и биологически активных средах. Патент РФ 2123507. Заявл.: 96119378/04, 27.09.1996; Опубл.: 20.12.1998.
Бабкин О.Э., Аристова Л.И. Защита древесины от биоразрушений // ЛКМ. 1996. № 12. С. 21‒23.
Беклемышев В.И., Махонин И.И., Афанасьев М.М., Абрамян А.А., Солодовников В.В., Вартанов Р.В. Состав для покрытий с биоцидными свойствами (варианты) и способ получения наноструктурной добавки с биоцидными свойствами. Патент РФ № 2338765. Заявл.: 2007112815/04, 06.04.2007; Опубл.: 20.11.2008. Бюл. 32.
Токач Ю.Е., Рубанов Ю.К., Василенко М.И., Гончарова Е.Н. К решению вопроса о создании строительных композиционных материалов с высокой активной защитой от микробиологического воздействия. Глава в монографии: Фундаментальные и прикладные аспекты современных эколого-биологических исследований / Фатеева Н.М., Карпенко П.А., Шутко А.П. // Одесса: КУПРИЕНКО СВ, 2015. 226 с.
Сагайдак А.И. Современные противообрастающие системы на судах: преимущества их применения // Повышение износостойкости и долговечности машин и механизмов на водном транспорте. Труды V Международного симпозиума по транспортной триботехнике “Транстрибо – 2013". 2013. С. 114–118.
James, D.M. Improved anti-fouling composition. British Patent 1124297, Priority date 1964-10-29; Publication date 1968-08-21.
Milne A., Hailes G. Marine paint. British Patent 1457590, Priority date 1974-04-03; Publication date 1976-12-08.
Безносов В.Н., Суздалева А.Л., Минин Д.В., Коткин К.С., Митяева Ю.Д. Многослойное комбинированное противообрастающее покрытие, обеспечивающее репеллентно-хемобиоцидную защиту. Патент РФ 2478114. Заявл. 2011148350/05, 29.11.2011; Опубл.: 27.03.2013 Бюл. № 9.
Дринберг А.С., Козлов Г.В., Машляковский Л.Н., Хомко Е.В., Тарасова И.Н., Карпов В.А. Разработка современных противообрастающих покрытий на основе эффективного комплекса биоцидов // Известия Санкт-Петербургского государственного технологического института (технического университета). 2018. № 46(72). С. 76–80.
Шестакова С.И., Четвериков И.И., Жесткова Т.Я., Егоров Б.Ф., Козлов В.А., Монова В.И. Средство для защиты от биоразрушений древесных и лакокрасочных материалов, способ его получения и способ защиты от биоразрушений древесных материалов. Патент РФ 2158677. Заявл. 99124066/04, 11.11.1999; Опубл.: 10.11.2000.
Ворожцов Г.Н., Голуб Ю.М., Егоров Б.Ф., Калия О.Л., Козлов В.А., Коренев А.Д., Кузьмин С.Г., Лужков Ю.М., Гехман А.Ш., Лукьянец Е.А., Негримовский В.М., Познанская Н.Л., Шестакова С.И. Средство и способ защиты неметаллических материалов от биоразрушений. Патент РФ 2 211 759. Заявл. 2002111229/04, 26.04.2002; Опубл.: 10.09.2003.
Кузнецова Н.В., Смирнов В.Ф., Смирнова О.Н., Кабанова Л.В. Полимерная грунтовка. Патент РФ 2315793. Заявл. 2006117213/04, 22.05.2006; Опубл.: 27.01.2008 Бюл. №3.
Зоткин И.И., Кузнецова Н.В., Кабанова Л.В. Биоцид. Патент РФ 2539150. Заявл. 2013138902/13, 20.08.2013; Опубл.: 10.01.2015 Бюл. № 1.
Мюррэй А.Р. Состав краски или основы краски, способ повышения биоцидной эффективности состава краски или основы краски. Патент РФ 2111993. Заявл. 92016449/04, 28.03.1991; Опубл.: 27.05.1998.
Гуревич Е.С., Рухадзе Е.Г., Фрост А.М., Рожков Ю.П., Брайко В.Д., Горбенко Ю.А., Искра Е.В., Цукерман А.М. Защита от обрастания. М: Наука, 1989. 271 с.
Гуревич Е.С., Изральянц Е.Д. Необрастающая краска. Патент SU 273905. Заявл. 1139340/23-05, 04.03.1967. Опубл.: 15.04.1983, Бюл. № 14.
Башорин О.А., Худошин А.А., Бесперстов Н.Н. Состав с биоцидными свойствами. Патент РФ 2215010. Заявл. 2002128703/04, 28.10.2002; Опубл.: 27.10.2003.
Башорин О.А., Худошин А.А., Бесперстов Н.Н. Состав с биоцидными свойствами. Патент РФ 2215011. Заявл. 2002128762/04, 28.10.2002; Опубл.: 27.10.2003.
Кондратьева В.С., Урминский А.В., Маринчук О.Н., Камышов В.Н., Ефременко С.Н. Состав с бактерицидными свойствами. Патент РФ 2186810. Заявл. 2000119214/04, 20.07.2000. Опубл.: 10.08.2002.
Воронков М.Г., Албанов А.И., Аксаментова Т.Н., Чипанина Н.Н, Адамович С.Н., Мирсков Р.Г., Кочина Т.А., Вражнов Д.В., Литвинов М.Ю. Соли трис(2-гидроксиэтил)аммония – 2,8,9-тригидропротатраны // ЖОХ. 2009. Т. 79. Вып. 11. С. 1817–1824.
Кондратенко Ю.А., Кочина Т.А., Фундаменский В.С., Власов Ю.Г. Триэтаноламмониевые соли биологически активных карбоновых кислот // Журн. общей химии. 2015. Т. 85. № 12. С. 1978–1982.
Мирскова, А.Н., Левковская Г.Г., Колесникова О.П., Перминова О.М., Рудякова Е.В., Адамович С.Н. Направленный синтез и иммуноактивные свойства (2-гидроксиэтил)аммониевых солей 1-R-индол-3-илсульфанил(сульфонил)-алканкарбоновых кислот // Изв. АН. Сер. хим. 2010. № 12. С. 2181–2190.
Kondratenko Y.A., Ignatyev I.S., Kochina T.A. Synthesis, structure and properties of complexes based on the tris(2-hydroxyethyl)amine, biogenic metals and carboxylic acids // Book of Abstracts 27th International Chugaev Conference on Coordination Chemistry, Nizhny Novgorod, 2017. P. Y34.
Ignatyev I., Kondratenko Y., Fundamensky V., Kochina T. Synthesis and characterization of cobalt(II) complexes with triethanolamine and succinate and/or nitrate anions // Transition Metal Chemistry. 2018. V. 43. P. 127–136.
Кондратенко Ю.А. Синтез, строение и термическое поведение комплекса {Co2[N(CH2CH2OH)3]2Cl2}Cl2 // Журн. общей химии 2017. Т. 87. № 4. С. 698–700.
Kondratenko Y., Fundamensky V., Ignatyev I., Zolotarev A., Kochina T., Ugolkov V. Synthesis and crystal structure of two zinc-containing complexes of triethanolamine // Polyhedron. 2017. V. 130. P. 176–183.
Кондратенко Ю.А., Борисова А.А., Уголков В.Л., Фундаменский В.С., Кочина Т.А. Взаимодействие трис(2-гидроксиэтил)амина с солями железа(III) и марганца(II). кристаллическая структура циннамата марганца(II) // Журн. общей химии. 2019. Т. 89. № 4. С. 591–596.
Kondratenko Y., Kochina T., Fundamensky V., Ignatyev I., Panikorovskii T., Nyanikova G. Triethanolammonium salicylate – protic alkanolammonium ionic liquid // J. Molecular Liquids. 2016. V. 221. P. 1218–1224.
Fundamensky V.S., Kochina T.A., Kondratenko Y.A., Zolotarev A.A., Vlasov Yu.G., Ignatyev I.S. Ionic liquids based on triethanolammonium salts of dicarboxylic acids (oxalic, malonic, succinic). Crystal structure and cation-anion interaction // J. Molecular Liquids. 2017. V. 230. P. 113–120.
Кондратенко Ю.А., Кочина Т.А., Фундаменский В.С. Протонные алканоламмониевые ионные жидкости на основе триэтаноламмониевых солей карбоновых кислот // ФХС. 2016. Т. 42. Вып. 6. С. 807–814.
Кондратенко Ю.А., Няникова Г.Г., Молчанова К.В., Кочина Т.А. Характеристика протонных ионных жидкостей на основе триэтаноламмониевых солей биологически активных карбоновых кислот и их влияние на ростовые свойства гриба Rhizopus oryzae // ФХС. 2017. Т. 43. Вып. 5. С. 496–503.
Дополнительные материалы отсутствуют.
Инструменты
Физика и химия стекла