Физика и химия стекла, 2020, T. 46, № 1, стр. 44-55
Иммобилизация бериллийсодержащих ВАО в алюмофосфатную стекломатрицу – результаты исследований и опыт промышленного внедрения на печи остекловывания ЭП-500/5
М. Б. Ремизов 1, П. В. Козлов 1, 2, Е. А. Беланова 1, *, В. А. Орлова 1, Е. Н. Дубровин 1, Е. Н. Зубриловский 1, К. К. Корченкин 1, Т. В. Смелова 3, Ю. Ю. Волчок 3, Д. Ю. Сунцов 3
1 ФГУП “ПО “Маяк”
456780 Озерск, пр. Ленина, д. 31, Россия
2 ОТИ НИЯУ МИФИ
456780 Озерск, пр. Победы, д. 48, Россия
3 АО “ВНИИНМ”
123060 Москва, ул. Рогова, 5А, Россия
* E-mail: belanova_ea@mail.ru
Поступила в редакцию 06.05.19
После доработки 31.07.19
Принята к публикации 08.10.19
Аннотация
Исследован процесс варки алюмофосфатных и бороалюмофосфатных стекол, содержащих до 5.63 мас. % оксида бериллия. Изучена вязкость, электропроводность расплавов. Определен унос бериллия в парогазовую фазу в процессе варки стекла. Исследована равномерность распределения бериллия по объему стекломассы. Определена однородность полученных стекол и их структура. Исследованы структурные изменения, происходящие в результате термического воздействия на образцы стекол. Определена химическая устойчивость полученных стекол к выщелачиванию Be, 137Cs и 90Sr при контакте с дистиллированной водой. Показана возможность остекловывания бериллийсодержащих ВАО с получением стеклоподобной матрицы требуемого качества, содержащей до 3.7 мас. % ВеО. Проведены результаты переработки бериллийсодержащих отходов в промышленном масштабе на электропечи ЭП-500/5.
ВВЕДЕНИЕ
В настоящее время на ФГУП “ПО “Маяк” ведется переработка различных видов ОЯТ (облученного ядерного топлива): атомных станций, исследовательских реакторов, транспортных установок. Высокоактивные отходы от переработки ОЯТ и высокоактивные отходы другого происхождения остекловываются в промышленной печи прямого электрического нагрева типа ЭП-500 с 1987 г. до настоящего времени.
Первые 4 плавителя такого типа переработали около 28.6 тыс. м3 жидких ВАО (высокоактивных отходов) суммарной активностью более 640 млн. Ки, с получением 6.2 тыс. т стекла [1]. С 27 декабря 2016 г. введена в эксплуатацию на жидких ВАО пятая промышленная электропечь ЭП-500/5, на которой к настоящему времени переработано более 5.2 тыс. м3 высокоактивных растворов суммарной активностью более 114 млн Ки, локализованных в 1263 т стекла.
В составе подобных отходов помимо продуктов деления и трансплутониевых элементов, присутствующих в микроколичествах, в макроколичествах могут содержаться и стабильные элементы (конструкционные материалы тепловыделяющих сборок). Одним из таких элементов является Be.
Бериллий является компонентом, влияющим на свойства расплава стекла, в частности, повышающим его температуру варки. Важным фактором является и токсичность самого бериллия.
Следует отметить, что в технологии обращения с ВАО бериллий переходит из формы нитрата бериллия в оксид бериллия.
Изучение свойств бериллийсодержащих расплавов и стекол проводили в АО “ВНИИНМ” и ФГУП “ПО “Маяк”.
Цель данных исследований – определение допустимого содержания оксида бериллия в алюмофосфатных стеклах для отверждения бериллийсодержащих ВАО в электропечи ЭП-500/5.
Для достижения поставленной цели необходимо было решить следующие задачи:
синтезировать алюмофосфатные и алюмоборофосфатные стекла различных составов с переменным содержанием оксида бериллия, изучить условия варки, свойства расплавов, а также однородность, термическую и химическую устойчивость бериллийсодержащих алюмофосфатных стекол, разработать регламентные нормы для процесса отверждения бериллийсодержащих ВАО в промышленной электропечи, внедрить разработанный процесс в действующую технологию остекловывания ВАО на электропечи ЭП-500/5. Оценить эксплуатационные параметры печи остекловывания.
ЭКСПЕРИМЕНТАЛЬНАЯ ЧАСТЬ
Обобщенная схема проведения экспериментов приведена на рис. 1.
Стеклообразующие растворы упаривали до сухого остатка, затем проводили кальцинацию полученной шихты с последующей варкой стекол. В процессе варки определяли унос бериллия. Полученный расплав выливали на металлическую плиту, получая закаленные стекла. Далее часть стекла подвергали отжигу в печи при 500°С в течение 48 ч. Отожженные и закаленные образцы стекла изучали методами сканирующей электронной микроскопии (СЭМ), элементного рентгеноспектрального микроанализа (РСМА), рентгеновской дифракции и испытывали на химическую устойчивость. Помимо этого закаленные стекла исследовали на однородность распределения оксида бериллия по объему матрицы, а также определяли вязкость и электропроводность их расплавов.
Методика варки закаленных стекол. Расчетный химический состав фосфатных и борофосфатных стекол, синтезированных и исследованных в АО “ВНИИНМ”, представлен в табл. 1.
Таблица 1.
Расчетный химический состав фосфатных и борофосфатных стекол АО “ВНИИНМ"
Химический состав, мас. % | |||||
---|---|---|---|---|---|
Na2O | Al2O3 | Fe2O3 | P2O5 | B2O3 | BeO |
27.0 | 16.5 | 1.5 | 55.0 | 0.0 | 0.0 |
27.0 | 16.5 | 1.5 | 51.0 | 4 | 0.0 |
26.2 | 16.0 | 1.46 | 53.4 | 0.0 | 2.9 |
26.2 | 16.0 | 1.46 | 49.5 | 3.9 | 2.9 |
25.7 | 15.7 | 1.43 | 52.4 | 0.0 | 4.8 |
25.7 | 15.7 | 1.43 | 48.6 | 3.8 | 4.8 |
В состав стекол, исследованных в ФГУП “ПО “Маяк”, помимо бериллия дополнительно были введены стабильные элементы, имитирующие конструкционные материалы ОЯТ (Pb, Bi, Mg, Ca), и продукты деления ядерного топлива (Sr, Cs, Zr, Мо и Ce). Составы стекол приведены в табл. 2. Для определения скорости выщелачивания 137Cs и 90Sr в стекла были введены указанные радионуклиды в количестве, обеспечивающем их удельную активность 1.1 × 106 Бк/г и 2.2 × 106 Бк/г соответственно.
Таблица 2.
Расчетный химический состав бериллийсодержащих стекол ФГУП “ПО “Маяк”
Номер состава | Содержание компонентов1, мас. % | ||||||
---|---|---|---|---|---|---|---|
Na2O | BeO | Al2O3 | P2O5 | B2O3 | MeX1OY12 | MeX2OY23 | |
1F | 25.6 | 1.9 | 15.9 | 54.5 | 0.0 | 0.10 | 0.005 |
2F | 25.6 | 3.8 | 13.9 | 54.5 | 0.0 | 0.20 | 0.010 |
3F | 25.6 | 5.6 | 11.9 | 54.5 | 0.0 | 0.30 | 0.015 |
4BF | 25.6 | 1.9 | 15.9 | 48.6 | 6.0 | 0.10 | 0.005 |
5BF | 25.6 | 3.8 | 13.9 | 48.6 | 6.0 | 0.20 | 0.010 |
6BF | 25.6 | 5.6 | 11.9 | 48.6 | 6.0 | 0.30 | 0.015 |
Варку стекол осуществляли из флюсованных фосфорной кислотой азотнокислых растворов, содержащих в заданном соотношении натрий, алюминий, бор и компоненты отходов. Алюминий, натрий, железо, стронций, цезий, церий, кальций, магний, свинец и висмут вносились в виде азотнокислых солей, цирконий – в виде цирконилнитрата, молибден и бериллий – в виде азотнокислых растворов (молибден стабилизирован H2C2O4), бор – в виде борной кислоты.
Перед упариванием в каждый раствор добавляли этиленгликоль для ускорения процесса денитрации. Растворы упаривали на песчаной бане до сухого остатка, который затем измельчали, помещали в алундовые тигли и кальцинировали в диапазоне температур 300–600°С. Полученный стеклообразующий кальцинат плавили в диапазоне температур 900–1100°С. Через каждые 50°С проводили визуальный осмотр состояния содержимого тигля. Температуру варки стекла фиксировали в момент превращения кальцината в расплав. Для полной гомогенизации расплав выдерживали при отмеченной температуре в течение 2 ч. Описанный режим варки стекла наиболее близок к режиму варки стекла в печи из высокоактивного раствора. Расплав стекла выливали на металлическую плиту из нержавеющей стали, в результате чего он быстро охлаждался при комнатной температуре, образуя закаленные стекла.
На стадии кальцинации все компоненты переходят в оксидную форму.
Методика определения уноса бериллия при варке стекла. В процессе варки стекол определяли концентрации бериллия в образующемся при остекловывании конденсате. Улавливание конденсата осуществляли путем охлаждения паров в стеклянном холодильнике. Конденсат сливали в мерную колбу, подкисляли азотной кислотой до концентрации 3 М и доводили до нужного количества бидистиллированной водой. Концентрацию бериллия в растворе определяли с использованием атомно-абсорбционного спектрометра с электротермической атомизацией на приборе “МГА-915”. Метод определения основан на измерении резонансного поглощения света, возникающего при его прохождении через слой атомного пара в графитовой кювете.
Методика определения однородности стеклоблока. Однородность стекла определяли двумя методами – по распределению бериллия по объему и путем картирования на электронном микроскопе данных по распределению макрокомпонентов (Na, Al, P) в поверхностном слое. В работе использовали электронный микроскоп CROSS BEAM NVision 40 (Carl Zeiss) с приставкой для микрорентгеноспектрального анализа Oxford Instruments X-max.
Распределение бериллия по объему определяли путем отбора образцов стекла из различных частей стеклоблоков, полученных после выдержки расплава при температуре 1100°С в течение 10 ч. Образцы анализировали на содержание бериллия путем растворения в азотной кислоте и последующего изучения методом атомно-абсорбционной спектрометрии.
Методика определения электропроводности расплава. Определение электропроводности расплавов стекол проводили на двухэлектродной электролитической ячейке с платиновыми электродами методом вольтметра–амперметра [2].
Падение напряжения на электродах измеряли цифровым вольтметром при постоянном значении тока НЧ-генератора 10 мА. Величину тока контролировали с помощью миллиамперметра. Константу электролитической ячейки определяли по стандартным растворам 0.1 и 1.0 Н KCl. Чтобы избежать погрешности, связанной с изменением сопротивления электродов в процессе измерений, электроды погружали два раза. Значения удельной электропроводности χ, Ом–1 см–1, вычисляли по формуле:
Методика определения вязкости расплава. Вязкостную характеристику расплавов в широком диапазоне температур определяли с использованием вибрационного вискозиметра, преобразующего амплитуду колебаний датчика, зависящую от вязкости среды, в соответствующий электрический сигнал [3]. Градуировку вискозиметра проводили по расплаву борного ангидрида в интервале значений вязкости 5–170 дПа с. Для нагревания расплавов при градуировке и в процессе измерения вязкости использовали печь сопротивления. Температуру в печи поддерживали с точностью ±10°С. Погрешность измерения вязкости расплавов оценивали через коэффициент вариации, и она не превышала 10%.
Методика отжига стекол. Отжиг закаленных стекол проводили, помещая образец в муфельную печь и выдерживая его при 500°С в течение 48 ч. Указанную длительность выдержки при заданной температуре достигали путем многократного повторения циклов “нагревание 500°С в течении 1 ч, выдержка при 500°С в течение 7 ч, естественное остывание в закрытой печи до 20°С в течение 16 ч”. Полученный температурный график можно считать более жестким испытанием термической устойчивости в сравнении с непрерывной выдержкой в стационарных условиях.
Методика определения фазового состава стекол. Фазовый состав полученных образцов закаленных и отожженных стекол исследовали методом рентгеновской дифракции. Образцы стекол перед измерением измельчали до фракции менее 0.08 мм.
Съемку рентгенограмм проводили на рентгеновском дифрактометре Bruker D8 Advance в диапазоне углов отражения 2θ 10°–80°, длина волны рентгеновского излучения – 1.54060 Å (CuKα). Обработку полученных данных выполняли с использованием программного пакета Diffrac.eva, Diffrac.topas и базы данных порошковой дифрактометрии PDF-2 (версия 2014 г.). Для образцов стекол был проведен полуколичественный анализ (S-Q – Semi Quant) содержания фаз по их корундовым числам и определена степень кристалличности образцов.
Методика определения химической устойчивости стекол. Определение химической устойчивости закаленных и отожженных бериллийсодержащих стекол проводили в соответствии с требованиями, изложенными в ГОСТ Р 52126–2003 [4]. Образцы стекол измельчали и отсеивали фракцию порошка с размерами частиц 0.16–0.25 мм. Удельная поверхность порошка составляла 120 см2/г. Для очистки от механических загрязнений и мелкой пылевидной фракции отсеянный порошок промывали 100% этиловым спиртом в течение 2 мин и высушивали на воздухе в течение суток. Навески порошка массой 0.5 г, имеющих общую поверхность 60 см2, помещали в полиэтиленовые емкости и заливали дистиллированной водой объемом 50 см3. Пробы выдерживали при температуре (23 ± 2)°С. Контактный раствор меняли через 1, 3, 7, 10, 14, 21, 28 и 35 сут от начала опыта. Растворы анализировали на содержание радионуклидов (цезия-137 и стронция-90) и бериллия. Определение объемной активности цезия-137 в пробах проводили на полупроводниковом гамма-спектрометре типа СЕГ-01 ППД ОЧГ № 01-06 непосредственно из раствора, стронция-90 – на радиометре РИБ МФ-5 после нанесения аликвоты раствора на мишень. Содержание бериллия в среде выщелачивания определяли методом масс-спектрометрии с индуктивно-связанной плазмой (ICP-MS).
РЕЗУЛЬТАТЫ И ОБСУЖДЕНИЕ
По результатам химического анализа образующегося при остекловывании конденсата показано, что захват бериллия с парогазовой фазой составляет величину 0.39–0.51 мас. % и не превышает значений аэрозольного (капельного) уноса для компонентов стеклообразующих растворов (например, алюминия 0.42–0.53 мас. %), которые, априори, не образуют летучих соединений в процессе получения стекломассы.
На рис. 2, 3 приведены результаты измерений вязкости расплавов исходных и бериллийсодержащих стекол.
Рис. 2.
Зависимость вязкости расплавов исходных и содержащих 3 мас. % BeO стекол от температуры: исходное борофосфатное стекло (1); исходное фосфатное стекло (2); борофосфатное стекло с 3 мас. % BeO (3); фосфатное стекло с 3 мас. % BeO (4).
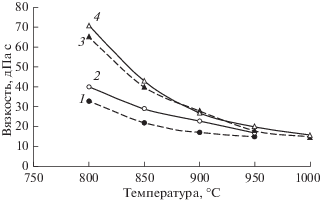
Рис. 3.
Зависимость вязкости расплавов исходных и содержащих 5 мас. % BeO стекол от температуры: исходное борофосфатное стекло (1); исходное фосфатное стекло (2); борофосфатное стекло с 5 мас. % BeO (3); фосфатное стекло с 5 мас. % BeO (4).
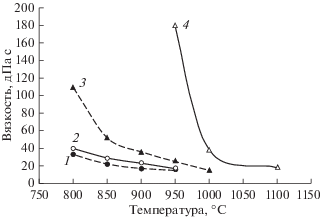
Установлено, что вязкость расплавов фосфатных и борофосфатных стекол с добавкой BeO до 3 мас. % в температурном диапазоне от 800 до 1000°С не превышает 100 дПа с. Соблюдение указанных условий позволяет осуществлять слив расплава стекла из плавителя без каких-либо затруднений.
При температурах ниже 1000°С отмечено резкое увеличение вязкости расплава фосфатной матрицы с массовой долей BeO 5 %. Данный случай в технологическом процессе недопустим, поскольку может привести к нарушению варки стекла и слива расплава из плавителя. Несмотря на то, что при использовании борофосфатного стекла с аналогичным введением BeO вязкость расплава составляет не более 100 дПа с, целесообразно ограничить величину включения BeO на уровне 3 мас. %.
Сравнительные измерения электропроводности базовых и бериллийсодержащих стекол показали незначительное отличие их свойств (табл. 3). Эти результаты также подтверждают возможность варки рассматриваемых стекол в печах прямого электрического нагрева.
Таблица 3.
Электропроводность расплавов фосфатных и борофосфатных стекол АО “ВНИИНМ”
Содержание оксидов в стекле, | Электропроводность при температуре 900°С, Ом–1 см–1 | |
---|---|---|
BeO | B2O3 | |
0.0 | 4.0 | 0.32 |
0.0 | 0.0 | 0.32 |
2.9 | 3.9 | 0.31 |
2.9 | 0.0 | 0.29 |
4.8 | 3.8 | 0.28 |
Проведены исследования по определению свойств твердых стекол. Важнейшими свойствами остеклованных ВАО является их однородность по объему блока, отсутствие кристаллических включений, термическая и химическая устойчивость.
Химический анализ образцов стекол, отобранных из различных частей стеклоблоков, показал равномерность распределения бериллия по объему фосфатных и борофосфатных стекол. Расчетные и измеренные значения концентрации бериллия расходились незначительно, в пределах погрешности метода химического анализа стекол (табл. 4).
Таблица 4.
Данные по распределению бериллия по объему стекломатериала
Тип стекла | Концентрация BeO в стеклоблоке, мас. % | ||
---|---|---|---|
расчетная величина |
реальная величина в зависимости от места отбора пробы | ||
верх | низ | ||
Борофосфатное + 3% BeO | 2.9 | 3.1 | 2.8 |
Борофосфатное + 5% BeO | 4.8 | 5.0 | 4.7 |
Фосфатное + 3% BeO | 2.9 | 2.7 | 3.1 |
Фосфатное + 5% BeO | 4.8 | 4.5 | 4.4 |
Полученные методом картирования на электронном микроскопе данные по распределению макрокомпонентов (Na, Al, P) показали, что поверхностный слой образцов, содержащих до 3 мас. % BeO, и образца борофосфатного стекла с содержанием BeO 5 мас. %, полученных в АО “ВНИИНМ”, однородны и не содержат инородные включения и какие-либо кристаллические фазы. Поскольку метод СЭМ позволяет определять концентрацию элементов с атомным номером более 10, то оценить равномерность распределения бериллия по стеклоблоку не представляется возможным. Для оценки однородности стеклоблока можно использовать результаты по равномерности распределения основных макрокомпонентов, составляющих основу стеклоподобной матрицы (Al, P, Na). Поверхностный слой фосфатного стекла с 5 мас. % BeO был полностью закристаллизован.
Исследование фазового состава стекол методом дифрактометрии показало, что образцы с высоким содержанием оксида бериллия (5.6 мас. %) термически неустойчивы. Зарождение центров кристаллизации отмечается уже в закаленных стеклах (NaBePO4, структурный тип минерала бериллонита) а отжиг усиливает кристаллизацию. В отожженных фосфатных стеклах помимо указанного кристаллического соединения дополнительно образуется фаза, относящаяся к группе натрийалюмофосфатов. Закаленные стекла с содержанием оксида бериллия 3.8 мас. % – однородные, после отжига наблюдается частичная кристаллизация. Оптимальные составы стекол (по однородности и термической устойчивости) лежат в области содержания оксида бериллия не более 3.8 мас. %. Наличие в составе стекла оксида бора существенно снижает кристаллизацию. Перечень идентифицированных фаз и их содержание в исследованных образцах представлено в табл. 5.
Таблица 5.
Фазовый состав исследованных образцов стекол
Номер стекла | Содержание оксидов в стекле, мас. % | Фаза (структурный аналог, номер карты PDF) |
Содержание фазы, мас. % |
|
---|---|---|---|---|
ВеО | В2О3 | |||
2F | 3.8 | 0 | Аморфная фаза | 100 |
3F | 5.6 | 0 | NaBePO4 (Beryllonite. 01-071-0734) Аморфная составляющая |
39.6 60.4 |
5ВF | 3.8 | 6.0 | AlPO4 (Berlinite. 00-010-0423) Аморфная составляющая |
26.4 73.6 |
6ВF | 5.6 | 6.0 | NaBePO4 (Beryllonite. 00-044-1397) Аморфная составляющая |
32.2 67.8 |
2F-ot | 3.8 | 0 | Аморфная фаза | 100 |
3F-ot | 5.6 | 0 | NaBePO4 (Beryllonite. 00-044-1397) AlPO4 (00-011-0500) Na3Al2(PO4)3 (00-031-1265) Na5Ca2Al(PO4)4 (01-084-2464) Аморфная составляющая |
34.0 1.9 11.3 14.1 38.7 |
5ВF-ot | 3.8 | 6.0 | Аморфная фаза | 100 |
6ВF-ot | 5.6 | 6.0 | NaBePO4 (Beryllonite. 00-044-1397) Na27Ca3Al5(P2O7)12 (00-046-0528) Na3Al2(PO4)3 (00-031-1265) AlPO4 (01-088-1680) Аморфная составляющая |
31.3 14.2 3.8 2.0 48.7 |
Рентгенограммы образцов закаленных и отожженных стекол приведены на рис. 4, 5 соответственно.
Обобщенные результаты по выщелачиванию 137Cs, 90Sr и Ве приведены в табл. 6, 7.
Таблица 6.
Скорость выщелачивания 137Cs, 90Sr и Ве из стекол ФГУП “ПО “Маяк”
Содержание оксидов в стекле, мас. % | Скорость выщелачивания на 35 сутки, г/(см2 сут) | ||||||
---|---|---|---|---|---|---|---|
из закаленных стекол | из отожженных стекол | ||||||
BeO | B2O3 | 137Cs | 90Sr | Ве | 137Cs | 90Sr | Ве |
1.9 | 0 | 3.2 × 10–8 | – | 1.3 × 10–7 | 3.5 × 10–8 | – | 4.8 × 10–7 |
3.8 | 0 | 3.8 × 10–8 | 3.6 × 10–7 | 5.4 × 10–7 | 3.6 × 10–8 | 7.1 × 10–6 | 1.7 × 10–7 |
5.6 | 0 | 3.3 × 10–8 | – | 8.9 × 10–8 | 3.8 × 10–8 | – | 1.5 × 10–6 |
1.9 | 6.0 | 3.7 × 10–8 | – | 6.0 × 10–7 | 3.7 × 10–8 | – | 2.3 × 10–7 |
3.8 | 6.0 | 3.5 × 10–8 | 3.7 × 10–7 | 2.2 × 10–7 | 4.4 × 10–8 | 5.8 × 10–8 | 1.1 × 10–7 |
5.6 | 6.0 | 3.5 × 10–8 | – | 3.8 × 10–7 | 3.9 × 10–8 | – | 4.7 × 10–8 |
Таблица 7.
Степень выщелачивания 137Cs, 90Sr и Ве из стекол ФГУП “ПО “Маяк”
Содержание оксидов в стекле, мас. % | Степень выщелачивания за 35 суток, % | ||||||
---|---|---|---|---|---|---|---|
из закаленных стекол | из отожженных стекол | ||||||
BeO | B2O3 | 137Cs | 90Sr | Ве | 137Cs | 90Sr | Ве |
1.9 | 0 | 1.1 | – | 0.6 | 3.5 | – | 1.0 |
3.8 | 0 | 0.8 | 0.5 | 0.4 | 1.6 | 7.9 | 0.4 |
5.6 | 0 | 1.0 | – | 0.5 | 11.7 | – | 1.7 |
1.9 | 6.0 | 3.2 | – | 0.9 | 13.7 | – | 0.5 |
3.8 | 6.0 | 1.6 | 0.5 | 0.6 | 28.8 | 0.1 | 0.1 |
5.6 | 6.0 | 3.8 | – | 1.0 | 8.2 | – | 0.1 |
Выщелачиваемость компонентов отходов из бериллийсодержащих стекол снижается в ряду 137Cs > 90Sr > Ве. Скорость выщелачивания бериллия из закаленных и отожженных стекол на первые сутки испытаний не превышает 4 × 10–5 г/(см2 сут), на 35 сут – 6 × 10–7 и 1.5 × 10–6 г/(см2 сут) соответственно. Степень выщелачивания бериллия из закаленных стекол не превышает 1% за 35 сут, из отожженных – 1.7%.
По прочности фиксации 137Cs борофосфатные стекла уступают фосфатным стеклам. Все исследованные закаленные фосфатные стекла обладают достаточной химической устойчивостью, борофосфатные – только при содержании ВеО на уровне 3.8 мас. %. В результате отжига химическая устойчивость всех стекол снижается вследствие их кристаллизации. Достаточную химическую устойчивость сохраняют только фосфатные стекла с содержанием ВеО до 3.8 мас. %.
Прочность фиксации 90Sr закаленными фосфатными и борофосфатными стеклами высока и полностью удовлетворяет нормативным требованиям. Отжиг фосфатного стекла приводит к существенному увеличению выщелачивания стронция. У борофосфатных стекол этот показатель, наоборот, значительно снижается.
ЗАКЛЮЧЕНИЕ
По итогам проведенных работ для электропечи ЭП-500/5 были разработаны регламентные ограничения по содержанию ВеО в стекле (максимальная концентрация – не более 2.5 мас. %, оптимальная – 1.25 мас. %).
В 2017 и 2018 гг. на электропечи ЭП-500/5 получено ~285 т бериллийсодержащего алюмофосфатного стекла с суммарной активностью ~21 млн Ки. Переработка прошла в штатном режиме. Затруднений, связанных с тугоплавкостью и повышенной вязкостью стекол, не наблюдалось. Температура сливаемого расплава стекла составляла от 850°С (на начальном этапе переработки данной порции отходов) до 950°С (после полного вытеснения из объема печи безбериллиевого стекла), что укладывается в регламентные ограничения (850–1150°С).
Опыт проведенных операций подтвердил правильность выбора допустимого уровня включения ВеО (≤2.5 мас. %) в алюмофосфатное стекло, обеспечивающего штатную эксплуатацию электропечи ЭП-500/5 при переработке бериллийсодержащих ВАО.
По итогам проведенных работ был оформлен патент на изобретение № 2658329 [5].
Список литературы
Ремизов М.Б., Козлов П.В., Логунов М.В., Колтышев В.К., Корченкин К.К. Концептуальные и технические решения по созданию на “ПО "Маяк” установок остекловывания текущих и накопленных жидких ВАО // Вопросы радиационной безопасности. 2014. № 3. С. 17–25.
Линчевский Б.В. Техника металлургического эксперимента. М.: Металлургия. 1967.
Соловьев А.Н., Росин А.Б. Вибрационный метод измерения вязкости жидкостей. Новосибирск: Наука. 1979.
Отходы радиоактивные. Определение химической устойчивости отвержденных высокоактивных отходов методом длительного выщелачивания. ГОСТ Р 52126-2003. М.: ИПК “Изд-во стандартов”. 2003. 5 с.
Ремизов М.Б., Козлов П.В., Корченкин К.К. Вещество для иммобилизации бериллия. содержащегося в высокоактивных растворах. Патент России № 2 658 329. 2017.
Дополнительные материалы отсутствуют.
Инструменты
Физика и химия стекла