Физика металлов и металловедение, 2019, T. 120, № 12, стр. 1271-1278
Анализ структуры и механических свойств сплава Co–Cr–Mo, полученного методом 3D-печати
Н. В. Казанцева a, b, *, И. В. Ежов a, Д. И. Давыдов a, А. Г. Меркушев b
a Институт физики металлов УрО РАН
620108 Екатеринбург, ул. С. Ковалевской, 18, Россия
b Уральский федеральный университет им. первого Президента России Б.Н. Ельцина
620002 Екатеринбург, ул. Ленина, 51, Россия
* E-mail: kazantseva-11@mail.ru
Поступила в редакцию 20.05.2019
После доработки 09.07.2019
Принята к публикации 13.07.2019
Аннотация
Проведено сравнительное исследование микроструктуры и прочностных характеристик сплава Co–Cr–Mo, полученного аддитивным методом, использующим селективное лазерное сплавление (СЛС) в 3D-принтере EOSINT M280, и дуговой плавкой в атмосфере гелия. Обнаружено протекание мартенситного превращения в СЛС-образцах. Методом наноиндентирования обнаружено, что микротвердость HIT СЛС сплава выше, чем литого, что, вероятно, связано с обнаруженным высоким уровнем поверхностных остаточных напряжений в СЛС-образце. Обнаружено, что СЛС-сплав после стандартного отжига имеет двухфазную (ГЦК + ГПУ)-структуру, в отличие от литого сплава, который после такого отжига сохраняет однофазную ГЦК-структуру.
ВВЕДЕНИЕ
Co–Cr–Mo-сплавы более 70 лет успешно используются в медицине как ортопедические имплантаты благодаря их высокой биосовместимости, хорошей комбинации прочности и сопротивления усталостному разрушению, низкой ползучести и высокому сопротивлению коррозии [1]. Другим направлением применения этого сплава в медицине является стоматология, в частности, сплав Co–Cr–Mo служит материалом для изготовления зубных протезов [2]. Этот сплав устойчив в агрессивной среде ротовой полости, а его высокая прочность и износостойкость служат залогом хорошего качества и долговечности зубопротезных конструкций [3].
В отличие от традиционных методов изготовления, метод аддитивных технологий позволяет производить детали с геометрией любой сложности, например, специальные пористые структуры и решетки или полые конструкции. Это позволяет использовать аддитивные технологии в медицине, поскольку возможно изготовление имплантатов с большой точностью и с учетом индивидуальных особенностей человеческого организма. Перечисленные преимущества аддитивных технологий при реализации в медицине вызывают в настоящее время большой интерес у исследователей. Обнаружено, что сплавы Co–Cr–Mo, полученные методом селективного лазерного сплавления (СЛС), обладают специфической микроструктурой, определяющей их механические свойства [4].
Механические свойства СЛС-сплавов Co–Cr–Mo зависят не только от химического состава использованного порошка, но также от условий получения и ориентации образца к направлению роста при его синтезе [2]. Аналогичная зависимость была обнаружена в СЛС титановых сплавах и сталях [5, 6]. Необходимо учитывать особенности метода селективного лазерного сплавления и их влияние на механические свойства полученных сплавов [7]. Основной проблемой СЛС-сплавов на основе Co–Cr–Mo на сегодня является получение материалов с низкой дефектностью и высокими механическими свойствами [8]. Присутствие тугоплавкого молибдена в составе исходного порошка в большинстве случаев приводит к формированию непроплавленных порошинок или пор в СЛС материале, которые служат концентраторами напряжений и провоцируют быстрое разрушение изделия [2]. Плотность СЛС-сплава Co–Cr–Mo очень сильно зависит от параметров процесса сплавления. Максимальная плотность CЛС-сплава Co–Cr–Mo по литературным данным составила 99.8% [8].
Целью данной работы является анализ микроструктуры и механических характеристик (микротвердости и модуля упругости) сплава Co–Cr–Mo, полученного методом селективного лазерного сплавления.
МЕТОДИКА ИССЛЕДОВАНИЯ
Для изготовления образцов был взят порошок Co–Cr–Mo, произведенный компанией “Полема” (Россия). Химический состав порошка по ТУ 14-22-265-2016, марка ПР-КХ28М6, близкий к сплаву ASTM F1537, используемому для получения изделий медицинского назначения, приведен в табл. 1 [9].
Таблица 1.
Химический состав порошка (ТУ), мас. %
Co | Cr | Mo | Si | Mn | Fe |
66.64 | 26.8 | 5.35 | 0.31 | 0.27 | 0.25 |
Ni | S | P | O | N | C |
0.1 | 0.0015 | 0.03 | 0.029 | 0.14 | 0.082 |
Структура исходного порошка представлена на рис. 1. Максимальный размер порошинок составил 40–50 мкм.
Образцы размерами 10 × 10 × 100 мм были получены методом СЛС с помощью установки EOSINT M280 (EOS GmbH), оборудованной иттербиевым волоконным лазером, работающим на длине волны 1075 нм (IPG Photonics Corp.), в Региональном инжиниринговом центре УрФУ имени первого Президента России Б.Н. Ельцина. Толщина порошкового слоя составляла 30 мкм, использовалась схема возвратно-поступательного сканирования в атмосфере азота с расстоянием между проходами лазера при сканировании 100 мкм. Концентрация кислорода в камере составляла 0.07–0.12%. Мощность лазера и скорость сканирования составили 400 Вт и 2 м/с, соответственно. Для сравнения из этого же порошка был выплавлен образец диаметром 10 длиной 60 мм в дуговой печи в атмосфере гелия с трехкратным переплавом и с последующей разливкой в медную изложницу. Для снятия упругих напряжений в полученных образцах был проведен стандартный для образцов, полученных обычными способами литья, отжиг при 1150°С в течение 30 мин в вакууме.
Механические свойства при наноиндентировании (микротвердость и модуль упругости) были измерены в центре коллективного пользования ИФМ УрО РАН при комнатной температуре с помощью установки NanoTest, при нагрузке 32 мН и времени приложения нагрузки 10 с. Расчет упругих модулей был выполнен по методу Оливера и Парра [10]. Исследование структуры было выполнено с помощью просвечивающего электронного микроскопа (ПЭМ) Tecnai G2 30 Twin, сканирующего электронного микроскопа (СЭМ) QUANTA-200, оборудованного энерго-дисперсионным спектрометром для элементного анализа EDAX, и оптического микроскопа Микромемед Мет. Рентгеноструктурный анализ был выполнен с помощью рентгеновского дифрактометра ДРОН-3 в излучении CuKα. Плотность полученных образцов определяли методом Архимеда. Подготовку образцов для СЭМ и оптической микроскопии проводили с использованием общепринятых процедур полировки. После этого осуществляли электрополировку в растворе этилового (70%) и бутилового (15%) спиртов с хлорной кислотой (15%). Для выявления микроструктуры был использовали метод травления в том же растворе.
РЕЗУЛЬТАТЫ ИССЛЕДОВАНИЯ
Рентгеноструктурный анализ
Результаты рентгеноструктурного анализа исследованных образцов представлены на рис. 2. Был выбран диапазон углов, в котором должны наблюдаться самые сильные линии ГЦК- и ГПУ-фаз. Как можно видеть из рис. 2, независимо от метода получения сплав является однофазным (γ-фаза, ГЦК) как в исходном состоянии, так и после отжига. При этом отмечается наличие ростовой кубической текстуры в литом сплаве по изменению после отжига интенсивности дифракционных линий (в общем случае для ГЦК самая сильная линия (111)). Дополнительных линий от интерметаллидных фаз (типа Co2Cr3) или карбидов, которые могли бы образоваться в этих сплавах, не обнаружено.
Рис. 2.
Дифрактограммы исследованных сплавов: 1 – литой; 2 – литой (отжиг); 3 – СЛС; 4 – СЛС (отжиг).
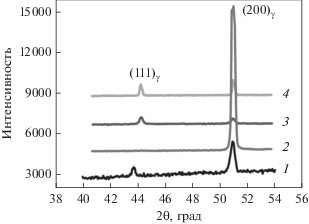
Изменения параметра решетки (а) γ-фазы исследованных образцов в зависимости от способа получения и термообработки представлены в табл. 2. Параметр ГЦК-кристаллической решетки был рассчитан по линии (311).
Таблица 2.
Параметры кристаллической решетки ГЦК γ-фазы исследованных образцов
Параметр | Литой | Литой (отжиг) | СЛС | СЛС (отжиг) |
---|---|---|---|---|
а, нм ±0.0002 | 0.3581 | 0.3549 | 0.3556 | 0.3568 |
В отличие от литого сплава, в котором обнаружены крупные зерна миллиметровых размеров, микроструктура СЛС-сплава имеет мелкокристаллическое строение (рис. 3).
Рис. 3.
Изображения микроструктуры исследованного сплава: а – литой; б – СЛС; в – литой (отжиг), г – СЛС (отжиг), а, б – СЭМ, в, г – оптическая металлография.
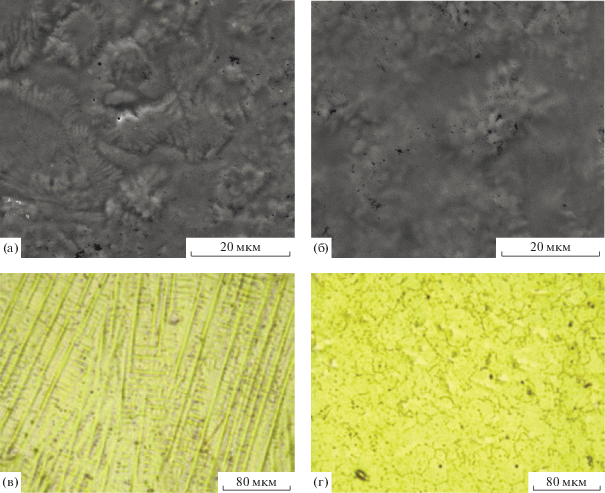
Размер зерен в СЛС-образце составляет 10–20 мкм (рис. 3). Дендритную структуру сплава, полученного дуговой плавкой, и СЛС-сплава можно видеть на рис. 3а, 3б. После релаксационного отжига в литом сплаве дендритная структура сохраняется (рис. 3в).
В СЛС-сплаве после отжига дендриты не наблюдаются, при этом мелкокристаллическая структура сохраняется (рис. 3г).
Результаты химического микроанализа образцов в исходном состоянии (литой и СЛС) по данным СЭМ приведены в табл. 3, 4. (Средний по образцу химический состав определяли по 10 точкам.)
Таблица 3.
Средний по образцу химический состав литого сплава, мас. %
Co | Cr | Mo | Si | Mn | Fe |
---|---|---|---|---|---|
66.16 | 27.25 | 4.45 | 0.38 | 0.75 | 1.01 |
Таблица 4.
Средний по образцу химический состав СЛС сплава, мас. %
Co | Cr | Mo | Si | Mn | Fe |
---|---|---|---|---|---|
62.75 | 27.26 | 7.39 | 0.51 | 0.85 | 1.23 |
В литом образце наблюдаются области, обогащенные и обедненные молибденом вследствие дендритной ликвации. В результате в литом образце ниже среднее содержание молибдена и выше кобальта по сравнению с СЛС образцом. При исследовании литого образца методами СЭМ были обнаружены крупные (∼2 мкм) частицы, обогащенные молибденом. Пористость, оцененная по данным СЭМ, в литом образце оказалась выше, чем в образце, изготовленном СЛС. Измеренная плотность полученных образцов составила 8.22 г/см3 – для литого и 8.25 г/см3 – для СЛС. В сравнении с плотностью сплава ASTM F1537 (8.29 г/см3) [9] полученная плотность составляет 99.1% для литого и 99.6% – для СЛС образца.
Наноиндентирование
В табл. 5 приведены результаты наноиндентирования исследованных образцов. Погрешность измерений при наноиндентации, рассчитанная по методу Стьюдента, составила 2%. Величины модуля упругости при индентировании (EIT) литого и СЛС сплава близки, однако микротвердость при индентировании (HIT) сильно различается. Взяв за эталонное состояние полученную при индентировании микротвердость в литом отожженном сплаве (HIT0), была рассчитана величина остаточных упругих поверхностных напряжений (σост) в образцах как разность между HIT и HIT0 [11]. Можно обратить внимание на различие в знаках полученных значений упругих поверхностных напряжений. Для СЛС-образцов σост имеют положительные значения, что означает присутствие растягивающих напряжений. В литом образце σост – отрицательные, т.е. присутствуют сжимающие остаточные упругие напряжения. Подобный характер остаточных упругих напряжений был обнаружен нами ранее в титановых образцах Ti–6Al–4V, также полученных методом СЛС [5].
Просвечивающая электронная микроскопия
Структура ГЦК γ-фазы с повышенной плотностью дефектов и двойниками наблюдается в литом сплаве (рис. 4). На рис. 4 представлены темнопольные снимки, полученные в рефлексе двойника и матрицы, плоскость двойникования типа {111}.
Рис. 4.
ПЭМ-изображения микроструктуры литого сплава: (а) светлопольное изображение, (б) темнопольное изображение в рефлексе двойника, (в) темнопольное изображение в рефлексе матрицы, (г) соответствующая микроэлектронограмма, ось зоны [110], плоскость двойникования ${{(\bar {1}11)}_{{{\text{ГЦК}}}}}.$ Сплошной линией выделена ячейка для матрицы, штрихом – для двойника.
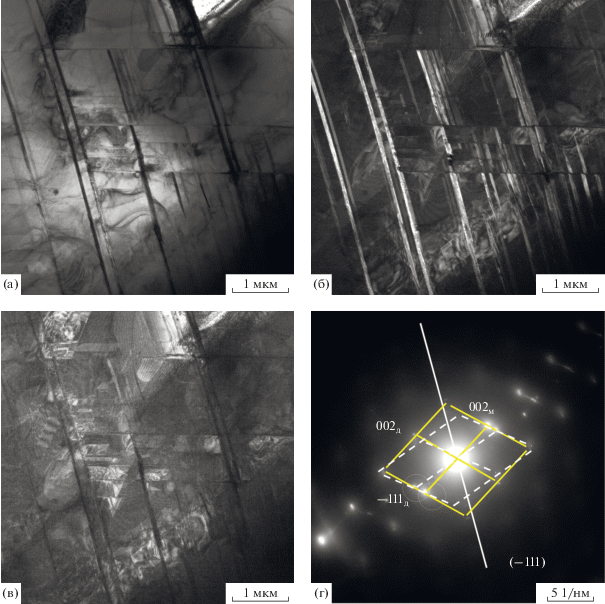
Диффузное рассеяние (тяжи) на электронограммах, полученных с областей с двойниками, сопровождают основные рефлексы, указывая на наличие дефектов упаковки.
После отжига литого образца в структуре обнаружены ГЦК-микродвойники (рис. 5). Крупных ГЦК-двойников и областей ГПУ-фазы не обнаружено.
Рис. 5.
ПЭМ-изображения микроструктуры литого отожженного сплава: (а) темнопольное изображение в рефлексе ГЦК двойника, (б) соответствующая микроэлектронограмма, ось зоны [110]ГЦК, плоскость двойникования (–111) ГЦК. Сплошной линией выделена ячейка для матрицы, штрихом – для двойника.
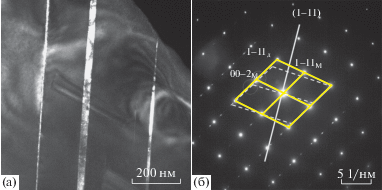
Структура СЛС-сплава в исходном состоянии и после отжига представлена на рис. 6 и 7. На снимках микроструктуры СЛС-сплава в исходном состоянии можно видеть однофазную γ-область с большим количеством двойников внутри (рис. 6). При этом плотность двойников в этом образце выше, чем в литом.
Рис. 6.
ПЭМ-изображения микроструктуры СЛС сплава: а – светлопольное изображение; б – темнопольное изображение в рефлексе двойника (штрих); в – темнопольное изображение в рефлексе матрицы; г – соответствующая микроэлектронограмма, ось зоны [110]γ. Сплошной линией выделана ячейка для матрицы, штрихом – для двойника.
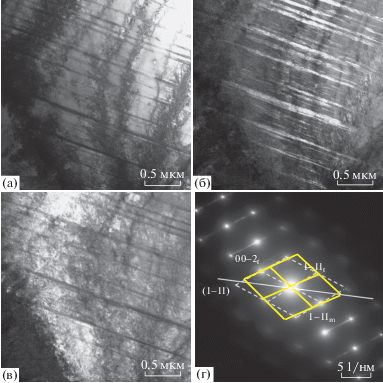
Рис. 7.
ПЭМ-изображения микроструктуры отожженного СЛС сплава: а – темнопольное изображение в рефлексе (2‒20)ε; б – соответствующая микроэлектронограмма, ось зоны [0.01]ГПУ || [111]ГЦК.
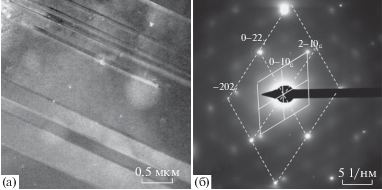
На микроэлектронограммах, полученных от областей, содержащих двойники, также можно видеть характерные тяжи (диффузное рассеяние), свидетельствующие о присутствии дефектов упаковки (рис. 6г).
В СЛС-сплаве после отжига обнаружено присутствие двухфазных γ + ε-областей (рис. 7). На микроэлектронограммах вместо тяжей можно видеть хорошо выраженные рефлексы ГПУ-фазы (рис. 7б).
Ориентационные соотношения между ГЦК- и ГПУ-фазой в этом сплаве соответствуют ориентационным соотношениям Нишиямы–Ваасермана [12]. Поскольку присутствие ГПУ ε-фазы обнаружено только по данным просвечивающей электронной микроскопии и не обнаружено с помощью рентгеноструктурного анализа, это может означать, что ее содержание в сплаве низкое (менее 5%).
Кроме того, во всех исследованных образцах обнаружены мелкие частицы. Размер и количество частиц увеличивается при отжиге. Химический анализ в сканирующем режиме ПЭМ показал, что эти частицы обогащены кремнием. Поскольку те же самые частицы обнаружены и в литом, и в СЛС сплаве, то их появление, очевидно, не связано с технологией селективного лазерного сплавления. Анализ кристаллической структуры и химического состава частиц будет представлен в отдельной работе.
ОБСУЖДЕНИЕ РЕЗУЛЬТАТОВ
Структура сплава Co–28Cr–6Mo состоит из двух основных фаз: ГЦК γ-фазы и ГПУ ε-фазы, кроме того могут присутствовать карбиды хрома и молибдена [13]. Количество и состав карбидов зависит от химического состава сплава Co–Cr–Mo и определяет его трибологические свойства [13]. В сплавах Co–Cr–Mo температура полиморфного превращения ГЦК–ГПУ составляет 970°С. Переход в этих сплавах от фазы (ГЦК) к фазе (ГПУ) очень медленный из-за низкой величины химической движущей силы, таким образом, метастабильная γ-фаза становится доминирующей фазой [14]. Образование ГПУ ε-фазы происходит по мартенситному механизму.
Таким образом, наличие в литом сплаве только ГЦК γ-фазы хорошо согласуется с литературными данными. Проведение релаксационного отжига с последующим медленным охлаждением литого сплава также не приводит к мартенситному переходу ГЦК–ГПУ (рис. 2, 4–5). Согласно литературным данным, ГЦК–ГПУ превращение в сплавах Co–Cr–Mo может быть достигнуто с помощью пластической деформации [15], закалкой из ГЦК-высокотемпературной области [15] или посредством изотермического старения в температурном диапазоне 800–850°С [16]. Энергия дефектов упаковки в ГЦК кобальте очень низкая и составляет 10–50 мДж/м2 [17]. Дефекты упаковки, образованные частичными дислокациями Шокли, служат зародышами для образования ГПУ фазы. Эти же дефекты упаковки участвуют и в формировании ГЦК-двойников. В сплавах Co–Cr–Mo было обнаружено, что структура мартенситной ГПУ ε-фазы содержит большое количество дефектов упаковки [13]. Двухфазная γ + ε-структура была также обнаружена в СЛС-сплаве Co–29Cr–6Mo в [18]. Причиной возникновения такой структуры является выбор режима работы лазера и стратегии сканирования в 3D-принтере. В нашем случае, в полученном методом СЛС-сплаве формирование нестабильной однофазной γ-структуры с большим количеством двойников происходит в процессе его синтеза за счет быстрого теплоотвода окружающим порошком. Такой эффект является специфической особенностью метода селективного лазерного сплавления [7]. В работе [19] сообщалось, что мартенситное превращение γ → ε в закаленных сплавах Co–Cr–Mo, полученных обычным способом литья, зависит от размера зерна, и может быть подавлено при размере зерна меньше 90 мкм. В исследованном СЛС-сплаве, подвергающемуся быстрому охлаждению при изготовлении в 3D принтере, размер зерна составил 10–20 мкм. Проведенный в настоящей работе релаксационный отжиг СЛС-сплава при 1150°С в течение 30 мин способствует снижению внутренних напряжений, что подтверждается появлением ГПУ-рефлексов на ПЭМ дифракционных снимках (рис. 7), и снижению микротвердости (табл. 5).
Кроме карбидов в сплавах Co–Cr–Mo, полученных обычным способом литья, может образовываться сигма фаза Cr0.6Co0.4 (σ-фаза, структурный тип Cr0.49Fe0.51, пространственная группа P42/mnm (136)). В сплавах Co–Cr–Mo в состав сигма-фазы также входит молибден (Сo0.6(Cr,Mo)0.4). Эта фаза является равновесной согласно диаграмме состояния Co–Cr–Mo [20]. Сигма-фаза относится к разряду топологически плотноупакованных фаз (ТПУ) и является нежелательной фазой, поскольку приводит к сильному охрупчиванию сплава [21]. В сплаве Co–29Cr–6Mo, полученном обычным способом литья, образование сигма-фазы было обнаружено на границах зерен после изотермического отжига при 800°С в течение 24 ч [22]. Также было показано, что в литом сплаве Co–Cr–Mo (ASTM F-75) образование сигма фазы происходит при карбидных превращениях во время затвердевания сплава [23]. В настоящем исследовании присутствие сигма-фазы не было обнаружено ни в исходном литом сплаве, ни в литом сплаве после отжига. Возможно, это связано с тем, что в качестве исходной лигатуры был взят порошок Co–Cr–Mo, что позволило получить более однородный состав сплава. В СЛС-сплавах Co–Cr–Mo сигма-фаза была обнаружена после дополнительного старения при 900°С в течение 2-х ч, что сопровождалось резким повышением микротвердости по сравнению с исходным значением (СЛС, ASTM F75) [24]. В СЛС-сплаве, полученном в настоящем исследовании, предварительный анализ морфологии различных выделений и их химического состава не показал присутствие сигма-фазы ни в исходном (СЛС) состоянии, ни после отжига при 1150°С в течение 30 мин. Это может свидетельствовать о том, что данный режим релаксационной термообработки может быть достаточно успешно использован для получения необходимого фазового и структурного состояния изделий из сплава Co–Cr–Mo, полученных методом селективного лазерного сплавления. Повышение микротвердости СЛС-сплава по сравнению с литым состоянием, обнаруженное в данной работе, согласуется с литературными сведениями. Повышение прочностных характеристик в сплаве Co–Cr–Mo, полученном методом СЛС, по сравнению с литым состоянием, также было обнаружено в работе [25].
ВЫВОДЫ
При исследовании структуры, фазового состава и механических свойств (модулей упругости и микротвердости) сплава Co–Cr–Mo, полученного методом селективного лазерного сплавления (СЛС) или дуговой плавкой в атмосфере гелия, сделаны следующие выводы:
1. СЛС-сплав имеет однофазное (ГЦК) нестабильное состояние.
2. После отжига СЛС-сплава обнаружено протекание мартенситного γ → ε-превращения. Выбранный режим релаксационной термообработки приводит к формированию равновесного двухфазного состояния.
3. Обнаружен высокий уровень поверхностных растягивающих остаточных упругих напряжений в СЛС-сплаве.
Работа выполнена в рамках государственного задания по темам: “Диагностика” № АААА-А18-118020690196-3 и “Давление” № АААА-А18-118020190104-3, а также при поддержке РФФИ (грант № 17-03-000-84). Образцы для исследования были изготовлены в Региональном инжиниринговом центре, УрФУ имени первого Президента России Б.Н. Ельцина. Структурные исследования и наноиндентирование были выполнены в центрах коллективного пользования ИФМ УрО РАН.
Список литературы
Disegi J.A., Kennedy R.L., Pilliar R. Cobalt-Base Alloys for Biomedical. Applications Virginia: ASTM STP 1365, 1999. 229 p.
Dikova T. Bending fracture of Co–Cr dental bridges, produced by additive technologies: experimental investigation // Procedia Structural Integrity. 2018. V. 13. P. 461–468.
Anusavice K.J., Shen C., Rawls H.R. Phillips’ science of dental materials. Elsevier Health Sciences, 2013. 592 p.
Lu Y., Wu S., Gan Y., Li J., Zhao C., Zhuo D., Lin J. Investigation on the microstructure, mechanical property and corrosion behavior of the selective laser melted CoCrW alloy for dental application // Mater. Sci. Eng.: C. 2015. V. 49. P. 517–525.
Kazantseva N.V., Ezhov I.V., Vinogradova N.I., Karabanalov M.S., Fefelov A.S., Oleneva O.A. Effect of Built Geometry on the Microstructure and Strength Characteristics of the Ti–6Al–4V Alloy Prepared by the Selective Laser Melting // The Phys.Met. Metal. 2018. V. 119. № 11. P. 1079–1086.
Alsalla H., Hao L., Smith C.W. Effect of build orientation on the surface quality, microstructure and mechanical properties of selective laser melting 316l stainless steel // Rapid prototyping journal. 2018. V. 24. № 1. p. 9–17.
Kazantseva N. Main factors affecting the structure and properties of titanium and cobalt alloys manufactured by the 3D printing // IOP Conf. Series: Journal of Physics: Conf. Series. 2018. V. 1115. P. 042008 (1–6).
Liverania E., Balbob A., Monticellib C., Leardinic A., Belvederec C., Fortunato A. Corrosion resistance and mechanical characterization of ankle prostheses fabricated via selective laser melting // Procedia CIRP. 2017. V. 65. P. 25–31.
Rosenthal R., Cardoso B.R., Bott I.S., Paranhos R.P.R., Carvalho E.A. Phase characterization in as-cast F-75 Co–Cr–Mo–C alloy // J. Mater. Sci. 2010. V. 45. P. 4021–4028.
Oliver W.C., Pharr G.M. An improved technique for determining hardness and elastic modulus using load and displacement sensing indentation experiments // J. Mat. Res. 1992. V. 7. P. 1564–1583.
ГОСТ РФ No 57172-2016 “Определение поверхностных остаточных напряжений методом наноидентирования”. М: Стандартинформ, 2016.
Balagna C., Spriano S., Faga M.G. Characterization of Co–Cr–Mo alloys after a thermal treatment for high wear resistance // Mater. Sci. Eng. C. 2012. V. 32. P. 1868–1877.
Omori T., Ito W., Ando K., Oikawa K., Kainuma R., Ishida K. FCC/HCP Martensitic Transformation and High-Temperature Shape Memory Properties in Co-Si Alloys // Mater. Transactions. 2006. V. 47. № 9. P. 2377–2380.
Atamert S., Bhadeshia H. Comparison of the microstructures and abrasive wear properties of stellite hardfacing alloys deposited by arc-welding and laser cladding // Metal. Trans. A - Physical Metallurgy and Mater. Sci. 1989. V. 20. № 6. P. 1037–1054.
Huang P., Lopez H.F. Effects of grain size on development of athermal and strain induced epsilon martensite in Co–Cr–Mo implant alloy // Mater. Sci. Techn. 1999. V. 15. № 2. P. 157–164.
Saldí var A.J., López H.F. Role of aging on the martensitic transformation in a cast cobalt alloy // Scripta Materialia. 2001. V. 45. № 4. P. 427–433.
Persson D.H.E., Jacobson S., Hogmark S. Effect of temperature on friction and galling of laser processed Norem 02 and Stellite 21 // Wear. 2003. V. 255. № 1. P. 498–503.
Takaichi A., Suyalatu, Nakamoto T., Joko N., Nomura N., Tsutsumi Y., Migita S., Doi H., Kurosu S., Chiba A., Wakabayashi N., Igarashi Y., Hanawa T. Microstructures and mechanical properties of Co–29Cr–6Mo alloy fabricated by selective laser melting process for dental applications // J. Mech. Behav. Biomed. Mater. 2013. V. 21. P. 67–76.
Huang P., Lopez H.F. Athermal ε-martensite in a Co–Cr–Mo alloy: Grain size effects // Mater. Letters. 1999. V. 39. P. 249–253.
Шаипов Р.Х., Керимов Э.Ю., Слюсаренко Е.М. Фазовые равновесия в сплавах системы Co–Cr–Mo при 1375 К с содержанием кобальта более 50 ат. % // Вестн. Моск. ун-та. Сер. 2. Химия. 2013. Т. 54. № 6. С. 342–345.
Yamanaka K., Mori M., Kuramoto K., Chiba A. Development of new Co–Cr–W-based biomedical alloys: Effects of microalloying and thermo-mechanical processing on microstructures and mechanical properties // Mater. & Design. 2014. V. 55. P. 987–998.
Mori M., Yamanaka K., Chiba A. Phase decomposition in biomedical Co–29Cr–6Mo–0.2N alloy during isothermal heat treatment at 1073 K // J. Alloys and Compounds. 2014. V. 590. P. 411–416.
Ramírez L.E., Castro M., Méndez M., Lacaze J., Herrera M., Lesoult G. Precipitation path of secondary phases during solidification of the Co–25.5%Cr–5.5%Mo–0.26%C alloy // Scripta Materialia. 2002. V. 47. № 12. P. 811–816.
Zhang M., Yang Y., Song C., Bai Y., Xiao Z. An investigation into the aging behavior of CoCrMo alloys fabricated by selective laser melting // J. Alloys and Compounds. 2018. V. 750. P. 878–886.
Тарасова Т.В., Назаров А.П., Прокофьев М.В. Влияние режимов селективного лазерного плавления на структуру и физико-механические свойства жаропрочных кобальтовых сплавов // ФММ. 2015. Т. 116. № 6. С. 636–641.
Дополнительные материалы отсутствуют.
Инструменты
Физика металлов и металловедение