Физика металлов и металловедение, 2019, T. 120, № 12, стр. 1322-1328
Механические свойства Al–Zn–Mg–Fe–Ni-сплава эвтектического типа при разных скоростях деформации
А. Н. Петрова a, *, И. Г. Бродова a, b, С. В. Разоренов c, d, Е. В. Шорохов e, Т. К. Акопян f
a Институт физики металлов УрО РАН им. М.Н. Михеева
620108 Екатеринбург, ул. С. Ковалевской, 18, Россия
b Уральский федеральный университет им. Б.Н. Ельцина
620002 Екатеринбург, ул. Мира, 19, Россия
c Институт проблем химической физики РАН
142432 Черноголовка, пр. академика Семенова, 1, Россия
d Национальный исследовательский Томский государственный университет
634050 Томск, пр. Ленина, 36, Россия
e Российский федеральный ядерный центр – Всероссийский научно-исследовательский институт
технической физики
456770 Снежинск, ул. Васильева, 13, а. я. 245, Россия
f Национальный исследовательский технологический университет “МИСиС”
119991 Москва, Ленинский пр., 4, Россия
* E-mail: petrovanastya@yahoo.com
Поступила в редакцию 26.03.2019
После доработки 26.06.2019
Принята к публикации 04.07.2019
Аннотация
Определены закономерности фазовых и структурных превращений при больших степенях деформации сдвигом под давлением экономно легированного алюминиевого сплава с эвтектико-образующими элементами железом и никелем (никалина). С помощью сканирующей и просвечивающей электронной микроскопии изучена эволюция структуры никалина, в частности, изменение морфологии и размеров структурных составляющих – зерен Al-твердого раствора и эвтектических алюминидов Al9FeNi. Определено, что кручение под высоким давлением никалина приводит к формированию упрочненного композитного материала с субмикрокристаллической Al матрицей и дисперсными (1.5–2.0 мкм) частицами алюминидов переходных металлов. Выполнены эксперименты по динамическому сжатию методом Кольского, по нагружению плоскими ударными волнами, и исследовано механическое поведение никалина с разной структурой в диапазоне скоростей деформации 10–4–105 с–1. Проведено сравнение динамических характеристик никалина с механическими свойствами, определенными при статических испытаниях.
ВВЕДЕНИЕ
В последнее годы среди алюминиевых сплавов нового поколения наиболее подробно исследуются разработанные в МИСиС под руководством Белова сплавы, получившие название никалины [1–3]. Их высокие прочностные свойства обеспечиваются дисперсионно-твердеющей Al-матрицей, содержащей цинк и магний, а хорошие литейные свойства и высокая технологичность создается за счет эвтектической составляющей, в состав которой входят алюминиды железа и никеля. Данные сплавы позиционируются как перспективные материалы для изготовления отливок сложной формы, а также как деформируемые сплавы для получения тонколистового проката [2, 3]. Так, согласно результатам [3], листовой прокат никалина после стандартной термической обработки Т1 (закалка и искусственное старение) имеет предел прочности σB = 535 МПа и относительное удлинение δ = 3%. Учитывая расширяющуюся потребность промышленности в материалах на алюминиевой основе, работающих при экстремальных условиях, ранее были исследованы механические свойства сплавов разных систем легирования: Al–Mn (АМц), Al–Mg–Mn (А5083) и Al–Zn–Mg–Cu (В95), в широком диапазоне скоростей деформации $\dot {\varepsilon }$ от 10–3 до 105 с–1. Для измерения динамических механических характеристик проведены эксперименты по динамическому сжатию методом Кольского с использованием разрезного стержня Гопкинсона [4, 5], а также ударно-волновое сжатие плоским ударником (скорость ударника 630 м/c) [6]. На основании этих исследований построены скоростные зависимости пределов текучести в статическом и квазистатическом диапазонах, и показано, что с ростом скорости деформации до $\dot {\varepsilon }$ < 103 с–1 условный предел текучести возрастает в сплавах АМц и В95 в 1.5 и 2 раза соотвественно. Динамические свойства – предел упругости Гюгонио, динамический предел текучести и откольная прочность, рассчитанные по волновым профилям скорости свободной поверхности плоских образцов ($\dot {\varepsilon }$ = 105 с–1), по своим значениям не уступают свойствам, полученным в статических условиях, что дает возможность положительного прогноза для работы этих материалов при экстремальных внешних воздействиях.
Для сплавов системы Al–Zn–Mg–Fe–Ni такие эксперименты не проводились. В связи с этим, была сформулирована цель настоящей работы – изучить деформационное поведение никалина при разных условиях нагружения и определить взаимосвязь механических свойств со структурой материала.
МЕТОДИКА ЭКСПЕРИМЕНТА
Объект исследования – высокопрочный никалин, химический состав которого, мас. %: основа – Al, 7.22 Zn, 2.95 Mg, 0.52 Fe, 0.57 Ni, 0.2 Zr, 0.002 Cu. Условия получения слитков и состав исходного сырья подробно описаны в [2, 3]. Полученные слитки подвергали двухступенчатому гомогенизационному отжигу при 450 и 540°С с выдержкой на каждой ступени в течение 3 ч, режим которого обоснован в [3]. Литой крупнокристаллический (КК) материал использовали для изготовления образцов с субмикрокристаллической (СМК) структурой и сравнения механических свойств сплава с разным размера зерна. Для получения образцов с СМК-структурой применяли метод кручения под высоким квазигидростатическим давлением (КВД) дисков диаметром 20 мм и толщиной 1.2 мм. Число оборотов наковальни составляло n = 5, 10, 15, что соответствует истинной деформации с учетом осадки е = 6.0, 6.7 и 7.1. на 1/2 радиуса образца.
Механические свойства никалина с разным размером зерна изучены в широком интервале скоростей деформации 10–4 < $\dot {\varepsilon }$ < 105 с–1 при одноосном растяжении, динамическом и ударно-волновом сжатии. Статические механические свойства субмикрокристаллического сплава, полученного КВД, определяли на плоских микрообразцах, используя универсальную испытательную машину Shimadzu AGX-50 Plus. Схема вырезки двух микрообразцов из диска после КВД показана на рис. 1. Рабочая часть микрообразцов соотвествовала середине радиуса диска. Для закрепления микрообразцов в захватах испытательной машины использовали специальное зажимающее устройство, подробно описанное в работе [7]. Скорость деформации составляла 5 × 10–4 с–1.
Рис. 1.
Схема вырезки микрообразцов для статического одноосного растяжения с приведенными размерами.
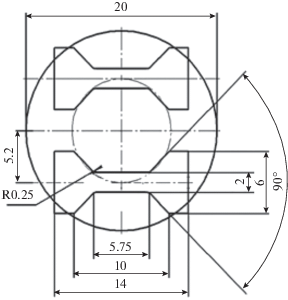
Одноосное растяжение стандартных цилиндрических образцов КК сплава проводили на испытательной машине Zwick Z250 по ГОСТ 1497-84 при скорости движения захватов 4 мм/мин.
Статические механические свойства оценивали по значениям условного предела текучести σ0.2, временного сопротивления σB и относительного удлинения δ. Микротвердость HV определяли на приборе ПМТ-3 при нагрузке 0.2 Н. Погрешность измерения не превышала 10%.
Динамическое сжатие КК-сплава проводили методом Кольского с использованием разрезного стержня Гопкинсона на экспериментальной установке, схема которой аналогична представленной в [8]. Использовали цилиндрические образцы диаметром 6 мм и высотой 3 мм. Скорость ударника изменяли от 6 до 24 м/с, при этом скорость деформации составляла $\dot {\varepsilon }$ = (1.4–5.0) × 103 с–1.
В ударно-волновых экспериментах образцы в виде дисков толщиной 1 мм нагружали ударом плоской алюминиевой пластины, разогнанной с помощью взрывного устройства до 620 ± 30 м/с [6]. Скорость деформации равнялась $\dot {\varepsilon }$ = (1.6–2.4) × 105 с–1, давление ударно-волнового сжатия, рассчитанное с помощью ударной адиабаты алюминия, составило 4 ГПа [9]. Механические характеристики сплава в процессе ударной деформации определяли по полным профилям скорости свободной поверхности (Ufs(t)), регистрируемым с помощью лазерного Допплеровского измерителя скорости VISAR. Расчеты динамического предела упругости σHEL, динамического предела текучести Y и откольной прочности σSP выполнены по формулам, приведенным в [6].
Структуру образцов изучали на разных масштабных уровнях с помощью светового оптического микроскопа NEOPHOT-32, сканирующего электронного микроскопа (СЭМ) QUANTA 200 и просвечивающего электронного микроскопа (ПЭМ) Tecnai G230 Twin при ускоряющем напряжении 300 кВ. Образцы для анализа структуры изготавливали с использованием механического полирования на алмазной суспензии. Финишную полировку проводили на суспензии коллоидного диоксида кремния. Образцы для исследований тонкой структуры изготавливали методом струйной полировки на приборе “Tenupol-5” в растворе 20%-ной азотной кислоты и 80%-ного метанола при температуре –25°С и напряжении 15–20 В. Количественный анализ размера структурных составляющих выполнен по темнопольным снимкам с использованием программы анализа изображений Siams-700.
РЕЗУЛЬТАТЫ И ИХ ОБСУЖДЕНИЕ
Структура. Результаты анализа структуры сплава после литья и гомогенизационного отжига представлены на рис. 2. В процессе гомогенизации происходит полное растворение неравновесных вырожденных эвтектик (Al + T) и (Al + M), где Т и М соответственно фазы Al2Mg3Zn3 и MgZn2. Таким образом, фазовый состав сплава представлен зернами Al-твердого раствора (рис.2а) и вырожденной равновесной эвтектикой (Al + Al9FeNi) (рис. 2б). Фаза Al9FeNi располагается по границам зерен матрицы и внутри них по границам дендритных ячеек. Количественный анализ структурных составляющих показал, что эвтектические алюминиды имеют размеры 2.0–2.5 мкм, а средний размер зерен матрицы составил 380 мкм (рис. 2в, 2г).
Рис. 2.
Структура литого сплава после гомогенизации: а – зеренная структура, б –морфология эвтектической фазы Al9FeNi, в – макроструктура, г – распределение зерен по размеру.
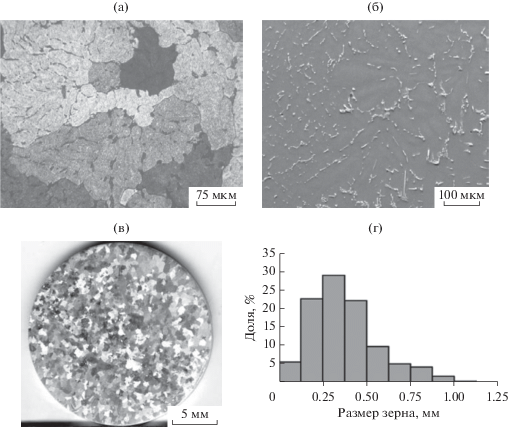
Этот крупнокристаллический сплав служил объектом для проведения деформационной обработки методом КВД. Эволюция структуры в процессе КВД при увеличении деформации е = 6.0–7.1 (n = 5, 10, 15) проиллюстрирована на рис. 3, 4. Представленные на рис. 3 изображения структуры, полученные методом СЭМ, показывают, что средний размер эвтектических алюминидов такой же как и после гомогенизационного отжига и равен 1.5 мкм при всех режимах КВД. Ввиду очень малой растворимости железа и никеля в алюминии количество эвтектической фазы до и после КВД остается неизменным, однако с ростом деформации наблюдается более равномерное распределение фазы по объему матрицы (рис. 3в).
Рис. 3.
Морфология эвтектической фазы Al9FeNi в никалине после КВД: а – n = 5, б – n = 10, в – n = 15.
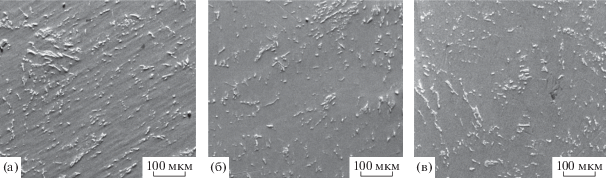
Оценка степени измельчения зерен Al-твердого раствора и механизмов формирования СМК-структуры получена при электронно-микроскопическом исследовании тонких фольг (рис. 4). Как следует из представленных снимков, при n = = 10 (е = 6.7) формируется типичная фрагментированная СМК структура с высокой плотностью дислокаций и диффузными контрастом на границах зерен-субзерен (рис. 4а, 4б).
Согласно количественному анализу только 20% зерен имеет размеры более 200 нм, а средний размер зерен-субзерен составляет 160 нм. С ростом величины деформации (n = 15, е = 7.1) морфологические особенности структуры сохраняются, процесс фрагментации получает дальнейшее развитие. В структуре формируются преимущественно большеугловые границы, о чем свидетельствует кольцевая электроннограмма с возрастающим количеством дискретно расположенных точечных рефлексов. Основной массив зерен-субзерен сохраняет дифракционный контраст, однако в тройных стыках появляются равноосные мелкие (20–30 нм) “чистые” зерна, свидетельствующие о начале процесса динамической рекристаллизации (отмечены стрелками на рис. 4в). Следовательно, при данных деформационных условиях в никалине формируется смешанная структура, состоящая из зерен-субзерен, образовавшихся деформационным путем, и рекристаллизованных зерен, при этом средний размер зерен-субзерен уменьшается до 100 нм. На рис. 5а показан график изменения микротвердости сплава в зависимости от числа оборотов наковальни, согласно которому СМК фрагментированная структура имеет HV = 3000 МПа, что в 2.2 раза выше микротвердости матрицы КК аналога. Рост HV связан с повышением плотности дислокаций в результате наклепа и с измельчением структуры до субмикронного уровня. Переход к смешанной структуре уменьшает микротвердость на 350 МПа.
Рис. 5.
Механические свойства никалина: а – зависимость микротвердости от количества оборотов наковальни при КВД; б – динамическая диаграмма КК никалина, полученная по методу Кольского; в – зависимость условного предела текучести при статическом растяжении от числа оборотов наковальни при КВД.
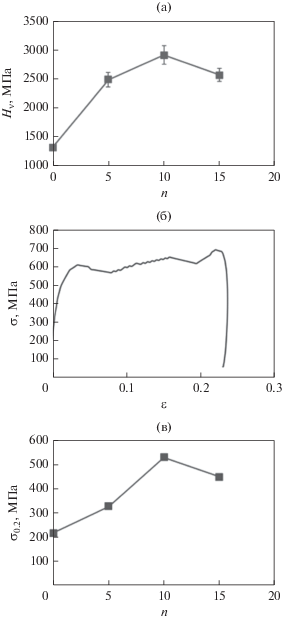
Таким образом, результаты, представленные на рис. 3 и 4, свидетельствуют о том, что сдвигом под давлением получен СМК-алюмоматричный композит, содержащий дисперсные алюминиды железа и никеля и обладающий повышенной твердостью 3000 МПа.
Механические свойства. Механические свойства КК никалина измерены в широком интервале скоростей деформации от 10–3 до 105 с–1. Результаты испытаний на одноосное растяжение литого гомогенизированного сплава показали, что условный предел текучести составляет σ0.2 = 220 МПа, а временное сопротивление – σB = 350 МПа. Измерение свойств в квазистатическом интервале скоростей деформации ($\dot {\varepsilon }$ = 1.4–5.0 × 103 с–1) осуществлялось при динамическом сжатии методом Гопкинсона–Кольского. Типичная диаграмма зависимости “σ–ε” не является монотонной, а имеет наложенные колебания (рис. 5б). В результате усреднения прочностных параметров во всем интервале $\dot {\varepsilon },$ получены следующие значения: σ0.2 = 415 МПа, а σB = 649 МПа. При сравнении с результатами статических испытаний установлено двукратное увеличение условного предела текучести. Такой же эффект был отмечен ранее при динамическом сжатии твердорастворных алюминиевых сплавов АМц и В95 [4, 5], т.е. наличие эвтектической компоненты не меняет характер скоростной зависимости предела текучести.
Динамические механические свойства КК и СМК образцов толщиной 1 мм исследованы в процессе ударно-волнового сжатия плоским ударником ($\dot {\varepsilon }$ = 1.6–2.4 × 105 с–1). Целью этого эксперимента было исследование влияния размера зерна на динамические характеристики никалина. Типичные профили скорости свободной поверхности, на которых регистрируется выход на поверхность упругого предвестника, пластической ударной волны сжатия и следующей за ней волны разрежения, показаны на рис. 6. Динамические характеристики КК сплава и СМК образцов, полученных КВД, приведены в табл. 1.
Таблица 1.
Динамические свойства никалина
Структура | Число оборотов, n | Деформация, e | σHEL, МПа | Y, МПа | σSP, ГПа |
---|---|---|---|---|---|
КК | 0 | – | 600 | 120 | 1.3 |
СМК | 5 | 6.0 | 1200 | 200 | 1.1 |
СМК | 10 | 6.7 | 1230 | 210 | 1.3 |
СМК | 15 | 7.1 | 1230 | 210 | 1.3 |
Как следует из табл. 1, по сравнению с КК аналогом динамические характеристики (предел упругости и предел текучести) СМК сплава выше в 2.0 и 1.8 раза соответственно. Важно отметить тот факт, что значения динамических характеристик не изменяются с ростом величины деформации (рис. 6, вставка). Это отличает никалин от других алюминиевых сплавов, составы которых соответствуют области Al-твердого раствора, например, от Al–Mg–Mn-сплава А5083 [10, 11]. Откольная прочность СМК и КК никалина практически одинакова. Подобные результаты наблюдали в экспериментах с разными по составу СМК Al сплавами, полученными методом динамического канально-углового прессования [6, 12]. В отличие от динамических характеристик, условный предел текучести СМК никалина, определенный при статических испытаниях, существенно меняется в зависимости от величины деформации (рис. 5в).
Если сравнить рис. 5в и 5а, то видно, что характер зависимостей σ0.2 и HV от n идентичен – самые высокие значения σ0.2 = 510 МПа соответствуют фрагментированной СМК структуре, полученной при n = 10, а с ростом числа оборотов (n = 15) эта величина снижается до 450 МПа. По сравнению с КК-аналогом СМК-никалин заметно упрочняется и его статические прочностные свойства в 2 раза выше. В свою очередь, показатель пластичности никалина с ростом n слабо меняется (δ = 6–7%). Эти результаты показывают, что условный предел текучести как структурно-чувствительная величина зависит главным образом от строения матрицы композита, а пластичность определяется в основном строением эвтектики (размером и морфологией эвтектических алюминидов), которое в процессе деформационной обработки меняется незначительно. Подобные результаты были получены и при оценке механических свойств сплава эвтектического типа на базе системы Al–Zn–Mg–Cu–Ni после баротермической обработки [13].
ЗАКЛЮЧЕНИЕ
Измерены механические свойства КК-сплава в широком интервале скоростей деформации от 10–3 до 105 с–1. Выполнены эксперименты по динамическому сжатию КК-образцов никалина методом Кольского с использованием разрезного стержня Гопкинсона. Установлено, что повышение скорости деформации от статического до квазистатического диапазона приводит к повышению условного предела текучести от 220 до 415 МПа, а предела прочности с 350 до 649 МПа, т.е. в 1.9 и 1.8 раза соответственно. Определены динамические механические характеристики: предел упругости Гюгонио, динамический предел текучести и откольная прочность, равные 600, 120 и 1300 МПа.
Рассмотрена эволюция структуры никалина в процессе большой пластической деформации сдвигом под давлением, и получен СМК (100–160 нм) алюмоматричный композит, содержащий дисперсные (1.5 мкм) тройные алюминиды железа и никеля эвтектического происхождения. Установлены механизмы формирования СМК-структуры в зависимости от величины деформации, в частности, переход от фрагментации к динамической рекристаллизации при е ≥ 7.1 (n ≥ 15).
Проведен контроль упрочнения СМК-композита по характеристикам твердости. Построена зависимость микротвердости от величины деформации (числа оборотов наковальни n), получено, что до n < 10 наблюдается рост этой характеристики в 2 раза по сравнению с микротвердостью КК-сплава. При n = 15 микротвердость СМК-композита понижается на 20% за счет частичного прохождения динамической рекристаллизации. Аналогичная зависимость была получена при анализе механических свойств СМК-композита, определенных при статическом растяжении. Условный предел текучести достигает максимального значения 500 МПа при n = 10 и падает на 15% при n = 15. Свойства СМК-композита превышают прочностные характеристики КК аналога (σ0.2 на 150%, σB на 50%) с сохранением хорошей пластичности (δ = 7%).
Выполнен эксперимент по ударно-волновому сжатию образцов никалина в СМК-состоянии, и определены динамические свойства материала в разном структурном состоянии, полученном при изменении величины деформации. Согласно сопоставлению профилей скорости свободной поверхности нагруженных образцов, значения динамических характеристик не изменяются с ростом n, т.е. не зависят от размера и типа СМК-структуры. Определено, что значения предела текучести при ударно-волновом сжатии и при статическом растяжении никалина близки между собой. Сравнение с динамическими характеристиками КК-никалина показывает, что измельчение структуры сплава до субмикронного масштаба приводит к существенному росту σHEL и Y в 1.8–2.0 раза. Величины откольной прочности СМК- и КК-никалина совпадают, т.е. перевод сплава в СМК-состояние не снижает динамическую прочность материала.
Работа выполнена в рамках государственного задания МИНОБРНАУКИ России (тема “Структура”, № АААА-А18-118020190116-6). Механические свойства исследованы при частичной финансовой поддержке РФФИ (проект № 18-03-00102). Электронно-микроскопические исследования проведены в ЦКП “Испытательный центр нанотехнологий и перспективных материалов” ИФМ УрО РАН.
Список литературы
Белов Н.А., Белов В.Д., Чеверикин В.В., Мишуров С.С. Экономнолегированные высокопрочные деформируемые никалины – алюминиевые сплавы нового поколения // Известия ВУЗов. Цветная металлургия. 2011. № 2. С. 49–58.
Белов Н.А., Шуркин П.К., Акопян Т.К. Структура и свойства деформированных полуфабрикатов высокопрочного алюминиевого сплава системы Al–Zn–Mg–Ni–Fe // Цветные металлы. 2016. № 11. С. 98–103.
Шуркин П.К., Белов Н.А., Акопян Т.К., Алабин А.Н., Алещенко А.С., Авксентьева Н.Н. Формирование структуры тонколистового проката из высокопрочного экономно-легированного алюминиевого сплава “Никалин” // ФММ. 2017. Т. 118. № 9. С. 941–949.
Петрова А.Н., Бродова И.Г., Плехов О.А., Наймарк О.Б., Шорохов Е.В. Механические свойства и особенности диссипации энергии в ультрамелкозернистых алюминиевых сплавах АМЦ и В 95 при динамическом сжатии // ЖТФ. 2014. Т. 84. Вып. 7. С. 44–51.
Бродова И.Г., Петрова А.Н., Разоренов С.В., Плехов О.А., Шорохов Е.В. Деформационное поведение субмикрокристаллических алюминиевых сплавов при динамических режимах нагружения // Деформация и разрушение материалов. 2015. № 11. С. 27–33.
Бродова И.Г., Петрова А.Н., Разоренов С.В., Шорохов Е.В. Сопротивление высокоскоростному деформированию и разрушению субмикрокристаллических алюминиевых сплавов после динамического канально-углового прессования // ФММ. 2015. Т. 116. № 5. С. 548–556.
Lomakin I.V., Arutyunyan A.R., Valiev R.R., Gadzhiev F.A., Murashkin M.Yu. Design and evaluation of an experimental technique for mechanical and fatigue testing of sub-sized samples // Experimental techniques. 2017. https://doi.org/10.1007/s40799-017-0229-7
Bragov A.M., Konstantinov A.Yu., Lomunov A.K., Petrovtsev A.V. The dynamic properties of zirconium-containing magnesium alloy MA14-T1 // Materials Physics and Mechanics. 2016. T. 28. № 1–2. C. 101–105.
Marsh S.P. LASL Shock Hugoniot Data. Berkeley: University of California Press, 1980. 658 p.
Бродова И.Г., Петрова А.Н., Разоренов С.В., Шорохов Е.В. Взаимосвязь структурных характеристик с динамическими свойствами алюминиевого сплава А5083 // Материаловедение. 2018. № 7. С. 3–8.
Петрова А.Н., Бродова И.Г., Разоренов С.В. Прочностные свойства и структура субмикрокристаллического Al–Mg–Mn сплава в условиях ударного сжатия // ФММ. 2017. Т. 118. С. 632–638.
Brodova I.G., Petrova A.N. Dynamic properties of submicrocrystalline aluminum alloys // Phys. Met. Metal. 2018. V. 119. P. 1342–1345.
Шуркин П.К., Акопян Т.К., Галкин С.П., Алещенко А.С. Влияние радиально-сдвиговой прокатки на структуру и механические свойства высокопрочного алюминиевого сплава нового поколения на основе системы Al–Zn–Mg–Ni–Fe // Металловедение и терм. обработка металлов. 2018. № 2(762). С. 11–17.
Дополнительные материалы отсутствуют.
Инструменты
Физика металлов и металловедение