Физика металлов и металловедение, 2019, T. 120, № 12, стр. 1329-1334
Деформация и разрушение феррито-мартенситной стали 13CrMoNbV при повышенной температуре
А. Ю. Чурюмов *
Национальный исследовательский технологический университет “МИСиС”
119991 Москва, Ленинский пр., 4, Россия
* E-mail: churyumov@misis.ru
Поступила в редакцию 28.03.2019
После доработки 07.05.2019
Принята к публикации 24.06.2019
Аннотация
По результатам испытаний на сжатие в интервале температур 1100–1250°С и скоростей деформации 0.1–10 с–1 построена реологическая модель деформационного поведения стали феррито-мартенситного класса 13CrMoNbV. Предложен критерий разрушения стали 13CrMoNbV в процессе горячей пластической деформации и метод определения его критического значения на основе проведения растяжения на комплексе физического моделирования термомеханических процессов Gleeble 3800 и моделирования с использованием метода конечных элементов. Разработанная реологическая модель и критерий разрушения показали удовлетворительную точность при расчете процесса деформации в условиях сложного напряженно-деформированного состояния – кручения с растяжением на комплексе Gleeble 3800 при температуре 1100°С.
ВВЕДЕНИЕ
Одна из важных задач материаловедения – повышение качества металлургической продукции и снижение брака при производстве. В промышленных условиях при обработке новых материалов повышен риск недостижения заданного уровня свойств. В связи с этим необходимым условием разработки новых технологий деформации являются предварительные экспериментальные исследования и теоретические расчеты процессов деформации для предотвращения преждевременного разрушения материалов и получения требуемой структуры. Такие предварительные исследования должны включать построение реологической модели поведения материала при пластической деформации, определение количественных показателей условий разрушения, а также расчет и оптимизацию реальных условий проведения обработки давлением. Построение реологической модели – определение связи между напряжением течения и параметрами пластической деформации (скоростью, температурой и степенью деформации), является достаточно простым шагом, несмотря на необходимость проведения большого количества экспериментов. В связи с этим наиболее сложный этап разработки новых технологий – это поиск критерия разрушения материала и методов определения его критических значений.
К настоящему моменту предложено большое количество критериев разрушения пластичных материалов. Так, Кокрофт и Латам предложили критерий, описывающий накопление повреждений при деформации в результате действия главного нормального напряжения (σ1) [1]:
(1)
${\text{CL}} = \int\limits_0^{{{{\bar {\varepsilon }}}_{f}}} {{{\sigma }_{1}}d\bar {\varepsilon },} $Райс и Трейси для учета сложно напряженного состояния использовали для расчета критерия разрушения коэффициент трехосности (σ*):
где гидростатическое напряжение ${{\sigma }_{m}}$ эквивалентное напряжение $\bar {\sigma }$ определяются следующими формулами:(3)
${{\sigma }_{m}} = {1 \mathord{\left/ {\vphantom {1 3}} \right. \kern-0em} 3}({{\sigma }_{1}} + {{\sigma }_{2}} + {{\sigma }_{3}});$(4)
$\bar {\sigma } = \sqrt {\frac{{{{{({{\sigma }_{1}} - {{\sigma }_{2}})}}^{2}} + {{{({{\sigma }_{2}} - {{\sigma }_{3}})}}^{2}} + {{{({{\sigma }_{3}} - {{\sigma }_{1}})}}^{2}}}}{2}} ,$Критерий Райс и Трейси имеет вид [2]
Недостатком разработанных моделей является их неудовлетворительная точность при малых и отрицательных значениях коэффициента трехосности (в “мягких” условиях пластической деформации). Кроме критериев, учитывающих накопленные повреждения, также были разработаны зависимости критического значения пластической деформации от схемы напряженного состояния, описываемой коэффициентом трехосности. Джонсон и Кук показали, что критическое значение эквивалентной деформации при растяжении образцов с надрезом, можно определить по формуле [3]
(6)
${{\bar {\varepsilon }}_{f}} = {{{\text{C}}}_{1}}{{e}^{{{{{\text{C}}}_{2}}\sigma *}}} + {{{\text{C}}}_{3}},$Однако определение значений констант материала требует создания существенно различающихся условий деформирования и разрушения, обеспечивающих широкий диапазон изменения коэффициента трехосности, что не всегда достижимо в условиях горячей пластической деформации металлов. В связи с этим необходимо дополнение существующих в настоящее время критериев разрушения. В последнее время для этого все чаще находит применение метод конечных элементов [4–7]. Он позволяет рассчитать коэффициент трехосности во всех точках образца с учетом неравномерности деформации, возникающей при сложных схемах напряженно-деформированного состояния, и идентифицировать место наиболее вероятного разрушения, для которого и определить критическое значение критерия разрушения.
В настоящей работе предложен критерий разрушения, учитывающий влияние не только напряженного состояния, но и нелинейность влияния накопленной деформации, путем ввода в подынтегральную часть критерия Райс и Трейси дополнительного множителя в виде экспоненциальной функции от эквивалентной деформации:
(7)
$K = \int\limits_0^{{{{\bar {\varepsilon }}}_{f}}} {{{e}^{{\sigma *}}}{{e}^{{\gamma \bar {\varepsilon }}}}} d\bar {\varepsilon },$В качестве объекта исследования выбрана сталь феррито-мартенситного типа 13CrMoNbV. Стали такого класса являются перспективными материалами для атомной промышленности благодаря хорошей стойкости к радиационному повреждению при нейтронном облучении. Однако из-за высокого легирования стали и двухфазной структуры в области горячей пластической деформации она обладает пониженной технологичностью при обработке давлением слитков. В связи с этим для уменьшения количества брака при первичном переделе слитков данной стали требуется предварительное экспериментальное исследование и теоретические расчеты процессов деформации и разрушения. Цель данной работы – построение реологической модели поведения стали при горячей пластической деформации, определение критических значений критерия разрушения и расчет деформационного поведения стали при сложном напряженно-деформированном состоянии.
ОБЪЕКТЫ И МЕТОДИКА ИССЛЕДОВАНИЯ
В качестве объекта исследования использовалась сталь 13CrMoNbV в литом состоянии следующего состава (в мас. %): Fe–13.1Cr–1.5Mo–0.25Nb–0.2V–0.8Mn–0.4Si–0.12C–0.004B. Испытания на сжатие, растяжение и кручение с растяжением выполняли с использованием комплекса физического моделирования термомеханических процессов Gleeble 3800. Образцы для испытаний на сжатие представляли собой цилиндры диаметром 10 и высотой 15 мм, образцы для испытания на растяжение представляли собой цилиндры диаметром 6 и длиной 110 мм. Рабочая зона образцов для кручения с растяжением имела длину 20 мм и диаметр 10 мм. Образцы для испытаний нагревали со скоростью 5°С/с до температуры 1250°С, выдерживали в течение 5 мин, а затем охлаждали до температуры деформации (1100, 1150 и 1200°С – для испытаний на сжатие, 1100°С – для испытаний на растяжение и кручение с растяжением). Деформацию сжатием производили при постоянных скоростях деформации 0.1, 1 и 10 с–1 до истинной деформации 0.8. Полученные первичные кривые пересчитывали в кривые истинное напряжение – истинная деформация с учетом трения и адиабатического нагрева во время деформации [8]. Растяжение проводили при постоянной скорости деформирования 50 мм/с до разрушения (такая скорость обеспечивала начальную скорость деформации 1 с–1). Образцы для кручения с растяжением одновременно деформировали с постоянной скоростью кручения 1 об./с и постоянной скоростью растяжения 0.5 мм/с.
Для микроструктурных исследований использовали сканирующий электронный микроскоп Tescan-VEGA3 LMH (СЭМ) с приставкой для анализа микроструктуры методом дифракции обратно рассеянных электронов (EBSD). Моделирование процесса деформации при растяжении и кручении с растяжением производили методом конечных элементов с использованием программного комплекса Deform 3D. Образцы при моделировании растяжения и кручения с растяжением были разделены на 20 000 и 50 000 тетраэдрических элементов, соответственно.
РЕЗУЛЬТАТЫ ИССЛЕДОВАНИЙ И ОБСУЖДЕНИЕ
Исходная микроструктура исследуемой стали (рис. 1) содержит равноосные зерна феррита и мартенсита и небольшое количество частиц карбоборидов ниобия Nb7B4C4 [9]. Объемная доля феррита в структуре стали составила 32 ± 3%, а частиц Nb7B4C4 – 0.9 ± 0.1%.
Для построения реологической модели деформационного поведения стали 13CrMoNbV были проведены испытания на сжатие. Кривые сжатия образцов представлены на рис. 2. Как можно заметить деформационное поведение стали характеризуется следующими, характерными для большинства сталей, особенностями:
Рис. 2.
Зависимость истинного напряжения течения стали 13CrMoNbV от истинной деформации при сжатии: скорость деформации 0.1 (а), 1 (б) и 10 c–1(в).
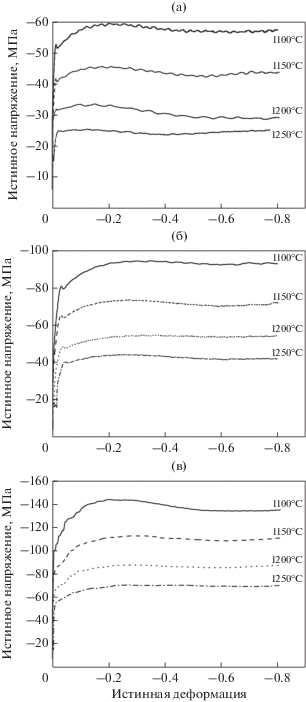
– на начальном этапе деформации происходит деформационное упрочнение с максимумом напряжения при пиковой степени деформации, после которого наступает стадия стабильного течения или разупрочнение материала в результате преобладания динамической рекристаллизации над процессом деформационного упрочнения;
– увеличение температуры при одинаковой скорости деформации приводит к понижению напряжения течения;
– увеличение скорости деформации при постоянной температуре способствует повышению уровня напряжения.
Для построения математической модели связи напряжения течения с параметрами деформации использовали наиболее распространенный подход, основанный на зависимости параметра Зинера–Холломона (Z) от напряжения течения:
где $\dot {\varepsilon }$ – скорость деформации (с–1), Т – температура (К), Q – эффективная энергия активации (Дж/моль) и R – универсальная газовая постоянная (8.314 Дж/мольK). Известно, что в разных условиях деформации эта зависимость может быть:– степенной (в случае низких значений напряжения течения):
– экспоненциальной (в случае высоких значений напряжения течения):
– уравнением гиперболического синуса (для широкого диапазона значений напряжения течения):
В уравнениях (9)–(11) коэффициенты A1, A2, A3, n1, n2, β and α являются константами материала. При этом значение коэффициента α связано с константами n1 и β следующим уравнением:
Значения констант материалов определяли для истинной деформации 0.1–0.8 методом наименьших квадратов путем приведения уравнений (9)–(11) к линейному виду.
Как видно из табл. 1, величина истинной деформации оказывает существенное влияние на значения констант, особенно при малых деформациях. Это может быть связано с тем, что на начальном этапе деформации истинное значение напряжения определяется изменением микроструктуры из-за наклепа, динамического возврата и рекристаллизации. В то время как на установившейся стадии деформации основным процессом является динамическая рекристаллизация, и константы существенно не меняются при увеличении деформации.
Таблица 1.
Значения констант в уравнениях (9)–(11) при разных значениях истинной деформации. Значения эффективной энергии активации Q1, Q2 и Q3 соответствуют уравнениям (9), (10) и (11)
Истинная деформация | ln A1 | n1 | Q1, кДж/моль |
ln A2 | β | Q2, кДж/моль |
α | ln A3 | n2 | Q3, кДж/моль |
---|---|---|---|---|---|---|---|---|---|---|
0.1 | 15.7 | 4.85 | 428 | 28.9 | 0.078 | 409 | 0.016 | 35.3 | 3.56 | 432 |
0.2 | 16.0 | 4.67 | 425 | 29.1 | 0.072 | 410 | 0.015 | 35.3 | 3.70 | 432 |
0.3 | 16.5 | 4.56 | 425 | 29.5 | 0.072 | 415 | 0.016 | 35.4 | 3.48 | 434 |
0.4 | 16.4 | 4.52 | 421 | 29.4 | 0.073 | 414 | 0.016 | 35.2 | 3.44 | 431 |
0.5 | 16.5 | 4.47 | 418 | 29.4 | 0.073 | 414 | 0.016 | 35.0 | 3.41 | 430 |
0.6 | 16.8 | 4.52 | 424 | 29.9 | 0.075 | 420 | 0.017 | 35.5 | 3.45 | 436 |
0.7 | 16.8 | 4.53 | 424 | 29.9 | 0.075 | 420 | 0.017 | 35.5 | 3.45 | 436 |
0.8 | 16.8 | 4.53 | 425 | 30.0 | 0.075 | 421 | 0.017 | 35.6 | 3.46 | 437 |
Полученные значения констант для уравнения (11) были использованы для моделирования процессов растяжения и кручения методом конечных элементов.
Для определения критического значения критерия разрушения К в уравнении (7) был проведен сравнительных анализ экспериментальной и рассчитанных кривых растяжения стали 13CrMoNbV при температуре 1100°С при разных значениях экспоненциального коэффициента γ. Сопоставление расчетных и экспериментальных кривых растяжения стали 13CrMoNbV при температуре 1100°С представлено на рис. 3. Как можно видеть, значение коэффициента γ = 0.1 является оптимальным для определения момента разрушения образца при растяжении. Кроме того, из рис. 3 видно хорошее соответствие формы разрушенного образца и результата расчета процесса растяжения с использованием построенных моделей деформации и разрушения. Критическое значение критерия разрушения К было определено путем интегрирования по формуле (7) рассчитанной с использованием метода конечных элементов зависимости коэффициента трехосности от величины деформации в центральной области образца (в зоне наиболее вероятного разрушения). Критическое значение полученного критерия разрушения при температуре 1100°С составило 1.36.
Рис. 3.
Экспериментальная и расчетные кривые растяжения стали 13CrMoNbV при температуре 1100°С, внешний вид образца и распределение деформаций в нем после растяжения.
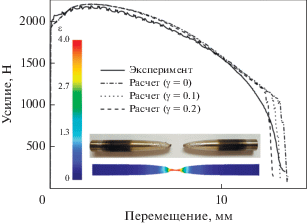
Для подтверждения точности построенных моделей деформационного поведения и разрушения был смоделирован и экспериментально проведен процесс деформации стали 13CrMoNbV одновременным кручением и растяжением. На рис. 4 представлены экспериментальные и расчетные значения момента кручения в зависимости от количества оборотов. Видно, что расчет методом конечных элементов показал удовлетворительную точность, ошибка расчета в интервале от 0 до 5 оборотов составила 12%. Кроме того, использование при расчете полученного ранее критического значения критерия разрушения позволило с высокой точностью спрогнозировать момент разрушения. В процессе кручения с растяжением в поверхностных слоях образца достигаются значительная деформация (до 10 ед. истинной деформации) благодаря мягкой схеме напряженно-деформированного состояния и интенсивным процессам возврата и рекристаллизации. Структура стали после деформации кручением с растяжением представляет собой вытянутые в направлении, перпендикулярном оси кручения и растяжения, волокна феррита и мартенсита (рис. 5а). Однако, несмотря на то, что структура стали является полностью рекристаллизованной (рис. 5б), в ней присутствуют также большое количество пор, образовавшихся в результате интенсивной деформации, не компенсированной процессами возврата и рекристаллизации.
ВЫВОДЫ
1. По результатам испытаний на сжатие построена модель связи напряжения течения с температурой, скоростью и степенью деформации для стали феррито-мартенситного класса 13CrMoNbV.
2. Предложен критерий разрушения стали 13CrMoNbV в процессе горячей пластической деформации и метод определения его критического значения на основе проведения растяжения на комплексе физического моделирования термомеханических процессов Gleeble 3800 и моделирования с использованием метода конечных элементов.
3. Разработанная реологическая модель и критерий разрушения показали удовлетворительную точность при расчете процесса деформации в условиях сложного напряженно-деформированного состояния – кручения с растяжением на комплексе Gleeble 3800 при температуре 1100°С.
Работа выполнена при финансовой поддержке Российского научного фонда (проект № 18-79-10153).
Список литературы
Cockcroft M.G., Latham D.J. Ductility and the workability of metals // J. Inst. Met. 1968. V. 96. P. 33–39.
Rice J.R., Tracey D.M. On the ductile enlargement of voids in triaxial stress fields // J. Mech. Phys. Solids. 1969. V. 17. № 69. P. 201–217.
Johnson G.R., Cook W.H. Fracture characteristics of three metals subjected to various strains, strain rates, temperatures and pressures // Eng. Fract. Mech. 1985. V. 21. № 1. P. 31–48.
Yao D., Cai L., Bao C. A new fracture criterion for ductile materials based on a finite element aided testing method // Mater. Sci. Eng. A. 2016. V. 673. P. 633–647.
Lou Y., Yoon J.W. Alternative approach to model ductile fracture by incorporating anisotropic yield function // Int. J. Solids Struct. 2019. V. 164. P. 12–24.
Tang B.T., Bruschi S., Ghiotti A., Bariani P.F. An improved damage evolution model to predict fracture of steelsheet at elevated temperature // J. Mater. Process. Tech. 2016. V. 228. P. 76–87.
Li L.T., Lin Y.C., Li L., Shen L.M., Wen D.X. Three-dimensional crystal plasticity finite element simulation of hot compressive deformation behaviors of 7075 Al Alloy // J. Mater. Eng. Perform. 2015. V. 24. P. 1294–1304.
Churyumov A.Y., Khomutov M.G., Tsar’kov A.A., Pozdnyakov A.V., Solonin A.N., Efimov V.M., Mukhanov E.L. Study of the structure and mechanical properties of corrosion-resistant steel with a high concentration of boron at elevated temperatures // Phys. Met. Metall. 2014. V. 115. P. 809–813.
Churyumov A.Yu., Khomutov M.G., Solonin A.N., Pozdniakov A.V., Churyumova T.A., Minyaylo B.F. Hot deformation behaviour and fracture of 10CrMoWNb ferritic–martensitic steel // Mater. Des. 2015. V. 74. P. 44–54.
Дополнительные материалы отсутствуют.
Инструменты
Физика металлов и металловедение