Физика металлов и металловедение, 2019, T. 120, № 12, стр. 1335-1344
Формирование структурного состояния высокопрочной низколегированной стали при горячей прокатке и контролируемом охлаждении
В. Н. Урцев a, В. Л. Корнилов b, А. В. Шмаков a, М. Л. Краснов b, П. А. Стеканов b, С. И. Платов c, Е. Д. Мокшин a, Н. В. Урцев a, В. М. Счастливцев e, И. К. Разумов d, e, Ю. Н. Горностырев d, e, *
a ООО “Аусферр”
455000 Магнитогорск, Ломоносова, 11/1, Россия
b ПАО Магнитогорский металлургический комбинат
455000 Магнитогорск, Кирова, 93, Россия
c Магнитогорский государственный технический университет им. Г.И. Носова
455000 Магнитогорск, Ленина, 38, Россия
d ООО “Институт квантового материаловедения”
620010 Екатеринбург, Конструкторов, 5, Россия
e Институт физики металлов им. М.Н. Михеева УрО РАН
620108 Екатеринбург, С. Ковалевской, 18, Россия
* E-mail: yug@imp.uran.ru
Поступила в редакцию 06.05.2019
После доработки 21.05.2019
Принята к публикации 26.06.2019
Аннотация
Представлен обзор современных результатов теоретического и экспериментального изучения особенностей структуры, формирующейся в высокопрочной низколегированной стали в процессе горячей прокатки и определяющей ее свойства. Рассматриваются существующие представления о физических процессах, развивающихся на различных стадиях термомеханической обработки в зависимости от температурно-скоростных режимов и химического состава стали. Особое внимание уделяется тем проблемам формирования структурного состояния, которые продолжают оставаться дискуссионными. Обсуждается использование методов моделирования различного масштабного уровня для решения задач управления структурообразованием на всех стадиях процесса термомеханической обработки.
1. ВВЕДЕНИЕ
Эффективность современных магистральных трубопроводов обеспечивается использованием повышенных рабочих давлений, что требует применения сталей классов К60(Х70), К65(Х80) с высокими показателями прочности, ударной вязкости, хладостойкости и свариваемости. Достижение таких характеристик обеспечивается реализацией дисперсной ферритно-бейнитной микроструктуры, для получения которой применяется современная технология термомеханической обработки (ТМО), сочетающая контролируемую прокатку с ускоренным охлаждением (КП + УО) [1–5]. Наиболее важной задачей совершенствования процесса производства трубной стали является определение ключевых параметров, которые при данном химическом составе обеспечивают целенаправленное формирование фазового и структурного состояния, необходимого для достижения требуемого комплекса свойств.
Современные технологии производства трубных сталей классов К60–К65 являются сложными и наукоемкими. Они должны обеспечивать управление структурообразованием на всех стадиях прокатки. Высокая конструктивная прочность достигается за счет чистоты сталей по примесям и газам, отсутствия перлита, малого размера структурных составляющих и оптимального сочетания всех доступных механизмов упрочнения [1, 6–9]. Поэтому глубокое понимание механизмов формирования структуры стали при термомеханической обработке имеет важное практическое значение.
Образующееся в результате прокатки структурное состояние определяется процессами, включающими измельчение аустенитного и ферритного зерна за счет применения КП, образование выделений карбонитридных фаз и осуществление распада значительной части аустенита в интервале температур бейнитного превращения. Управление этими процессами осуществляется на различных этапах ТМО (рис. 1), включающих (I) нагрев до температуры прокатки, стадии (II) черновой и (IV) чистовой горячей прокатки, разделенные междеформационной паузой (III), и (V) ускоренное охлаждение с последующей смоткой.
Рис. 1.
Стадии термомеханической обработки на линии толстолистового стана ТЛС 5000: I – нагрев (5–7 ч), II – черновая горячая прокатка (~2 мин), III – междеформационная пауза (10–12 мин), IV – чистовая горячая прокатка (~2 мин), V – ускоренное охлаждение (~1.5 мин).
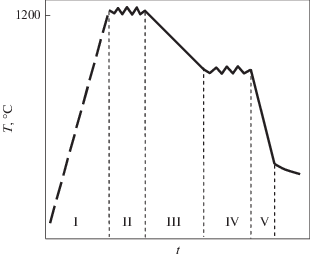
Проблема формирования структурного состояния в процессе КП + УО неоднократно обсуждалась в литературе [1–10] и продолжает привлекать значительное внимание. В настоящей работе дается краткий обзор существующих представлений о физических процессах, протекающих в металле при его прохождении по линии толстолистового стана (ТЛС), определяющих формирование структурного состояния в трубной стали, а также факторах, играющих ключевую роль в его достижении. В настоящее время установлены основные процессы, действующие на различных стадиях ТМО. Тем не менее ряд вопросов, касающихся выбора химического состава и режимов ТМО, остаются по-прежнему предметом дискуссий. Именно на них мы сосредоточим здесь основное внимание.
2. НАГРЕВ ПЕРЕД ПРОКАТКОЙ
Низколегированные стали класса прочности К60–К65 содержат менее 0.08 мас. % C, 1.0–1.8 мас. % Mn, микролегирующие элементы Nb, V, Ti, а также Cu, Ni (с суммарным содержанием не более 0.5 мас. %), и Mo, B (для более детальной информации см. [9]).
Нагрев слябов до температуры прокатки является одним из важных технологических этапов, обеспечивающих формирование структуры и комплекса свойств стали. При нагреве происходит α–γ-превращение, а при последующей выдержке – рост аустенитного зерна (достигаемый размер зерна обычно составляет 100–200 мкм и ~20 мкм в стали, упрочненной выделениями TiN). В процессе нагрева необходимо обеспечить растворение карбонитридов легирующих элементов (Nb, V), сформировавшихся на предшествующих этапах технологического процесса. Их последующее контролируемое выделение на определенной стадии ТМО играет ключевую роль в получении требуемого структурного состояния, обеспечивающего высокие потребительские свойства стали.
Частицы TiN начинают растворяться при температурах, превышающих 1250°С, что приводит к укрупнению структуры аустенита. Стремление получить мелкое зерно и повышенные вязкие свойства проката привело к необходимости снижения температуры нагрева слябов. Малые добавки Ti более эффективны для торможения роста аустенитного зерна, чем микролегирование Nb. В тоже время одновременное введение в сталь титана и ниобия может привести к более интенсивному росту зерна, чем в стали микролегированной только титаном, что обычно связывают с формированием комплексных карбонитридов TiNb(C, N), имеющих большую растворимость в аустените в сравнении с TiN [11].
В настоящее время границы растворимости карбонитридов установлены с достаточной надежностью (см. [3, 6, 11]), однако кинетика этого процесса остается плохо изученной [12]. Рентгеновские методы исследования не позволяют обнаружить наноразмерные выделения, объемная доля которых не превышает 0.1%. Для получения надежной информации о карбонитридных фазах необходимо использовать синхротронное излучение [13], либо применять методы термодинамического [14] или атомистического [15, 16] моделирования.
Описание эволюции бинарных и трехкомпонентных включений Nb(CN), Ti(CN) и AlN в рамках подхода, основанного на анализе скорости рассеяния энергии Гиббса [17, 18], было реализовано в [19, 20]. Более последовательное рассмотрение, в котором скорость роста или растворения выделения определяется через диффузионное взаимодействие между частицей и ее окружением (приближение среднего поля), было предложено в [11, 21]. Использование современных методов теоретической термодинамики позволяет с высокой надежностью прогнозировать фазовое и структурное состояние, формирующееся в процессе нагрева перед прокаткой (рис. 2).
Рис. 2.
Прогнозируемое изменение объемной доли f частиц Nb(C,N) в процессе изотермической выдержки при различных температурах [22].
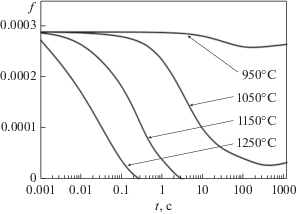
3. ПРОЦЕССЫ, ПРОТЕКАЮЩИЕ ПРИ ГОРЯЧЕЙ ДЕФОРМАЦИИ
Главными задачами, решение которых осуществляется в процессе ТМО, являются изменение формы заготовки, а также формирование определенной микроструктуры, обеспечивающей требуемые свойства стали. Горячая деформация включает стадии черновой и чистовой прокатки (см. рис. 1), разделенные относительно продолжительной междеформационной паузой (10–12 мин на ТЛС 5000), на которой температура заготовки понижается примерно на 200°С.
В условиях многопроходной горячей прокатки (при температурах, выше температуры начала рекристаллизации Trx) формирование микроструктуры определяется конкуренцией протекающих параллельно процессов увеличения плотности дислокаций (наклеп) и статического или динамического возврата, что приводит к образованию субграниц в аустенитных зернах [7, 23], а при достаточно интенсивной деформации – к статической или динамической рекристаллизации [7, 24].
Динамический возврат (ДВ) реализуется в процессе деформации путем перераспределения накопленных дислокаций и формирования ячеистой субструктуры. Препятствиями для развития ДВ выступают высокодисперсные частицы вторых фаз [25]. Динамическая рекристаллизация (ДР) развивается по достижении критической полной деформации εc [24, 26] путем зарождения и роста новых зерен и часто является нежелательным процессом, приводящим к разупрочнению материала. С другой стороны, ДР позволяет уменьшить размер зерен, способствуя улучшению эксплуатационных свойств.
Начало ДР обычно регистрируется по точке перегиба на кривых “напряжение–деформация” (σ–ε) [27]. Развитию ДР, в общем случае, препятствует динамический возврат [28], так что переключение механизмов ДВ → ДР реализуется при уменьшении параметра Холломона–Зинера [24]
(1)
$Z = {{\dot {\varepsilon }}_{{{\text{pl}}}}}{\text{ехр}}\left( {{{{{Q}_{{{\text{def}}}}}} \mathord{\left/ {\vphantom {{{{Q}_{{{\text{def}}}}}} {RT}}} \right. \kern-0em} {RT}}} \right)$ниже критического значения, что может быть обеспечено снижением скорости пластической деформации ${{\dot {\varepsilon }}_{{{\text{pl}}}}},$ либо повышением температуры T (здесь Qdef – энергия активации деформации, R – газовая постоянная). При больших Z единственным механизмом разупрочнения материала остается динамический возврат.
Оценим возможность протекания динамической рекристаллизации при прокатке на TЛC 5000 ПАО ММК. Величина деформации на стадии чистовой прокатки достигает 15% (за один проход), при этом скорость деформации ${{\dot {\varepsilon }}_{{{\text{pl}}}}}$ ≈ 1–3 с–1, а энергия активации Qdef ≈ 390 кДж/моль [24], так что при температуре чистовой прокатки параметр Холломона–Зинера составляет Z = 0.5– 1.5 × 1015. Таким образом, даже в отсутствие частиц дисперсных фаз, тормозящих развитие рекристаллизации, параметры ТЛС 5000 не обеспечивают выполнение условий, необходимых для протекания полной ДР в процессе горячей прокатки (рис. 3). В тоже время может реализоваться частичная ДР.
Рис. 3.
Диаграмма состояний динамической рекристаллизации для малоуглеродистой низколегированной стали [24].
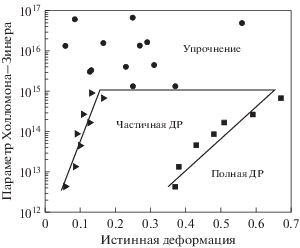
Действительно, согласно [24], объемная доля рекристаллизованного материала Xd в процессе ДР:
(2)
${{X}_{d}} = 1 - \exp \left[ { - \beta {{{\left( {\frac{{\varepsilon - {{\varepsilon }_{{\text{c}}}}}}{{{{\varepsilon }_{{\text{p}}}}}}} \right)}}^{k}}} \right],$Хотя на ТЛС 5000 деформация за отдельный проход не превышает 15%, можно ожидать протекания частичной ДР в результате накопления деформации при многократном прохождении полосы по линии стана. Выбор оптимальных режимов деформирования, обеспечивающих протекание или, наоборот, торможение развития ДР, обсуждался в [30] и в настоящее время остается предметом дискуссий.
Одной из существенных проблем является разнозернистость структуры [30], возникающая при прокатке в интервале частичной ДР, что приводит к формированию участков реечного бейнитного феррита [32], снижающего эксплуатационные характеристики стали [28]. Следует отметить, что увеличение содержания Nb приводит к смещению диапазона частичной рекристаллизации (Т95–Т5) аустенита в область повышенных температур, увеличивая склонность к формированию разнозернистости в процессе прокатки [31]. Кроме частичной ДР причиной появления разнозернистости может быть также различие условий пластического течения в поверхностных слоях и в объеме деформируемого материала, а также наличие градиента температуры вблизи поверхности [28].
Для предсказания структурного и фазового состояния, формирующегося при горячей деформации, перспективным является использование методов компьютерного моделирования, базирующихся на современных представлениях [33] о физических процессах, развивающихся в железе и стали при термомеханической обработке [26, 34].
4. ПРОЦЕССЫ, ПРОТЕКАЮЩИЕ ВО ВРЕМЯ МЕЖДЕФОРМАЦИОННОЙ ПАУЗЫ
Во время междеформационной паузы (МДП) происходит статический возврат, уменьшающий степень наклепа и повышающий совершенство границ зерен. При этом в наиболее деформированных участках материала может протекать постдинамическая и первичная рекристаллизация. Кроме того, во время МДП начинается выделение карбонитридов ниобия, которые являются ингибиторами, способными эффективно тормозить движение границ, предотвращая рост зерна [28].
Для того чтобы определить, могут ли карбнитриды образоваться за характерные времена термомеханической обработки, необходимо знать кинетику их формирования. Этот процесс был исследован путем численного моделирования в ряде работ в рамках подхода кластерной динамики [35, 36]. При этом зарождение частиц новой фазы описывалось с использованием модели Беккера–Деринга [37], учитывающей флуктуации, приводящие к присоединению атомов к зародышу или к их “испарению” с поверхности.
На рис. 4 приведены полученные нами результаты моделирования образования карбидов ниобия и нитридов титана для стали рассматриваемого состава с использованием пакета MatCalc [38]. В качестве потенциальных мест зарождения выделений принимались дислокации, плотность и распределение которых определялись условиями прокатки, как это реализовано в [38]. При этом предполагалось, что в начальный момент легирующие элементы находятся в твердом растворе. На рис. 4а показано изменение со временем температуры поверхности листа на линии ТЛС 5000. Видно, что TiN образуется непосредственно с момента начала ТМО, поскольку температура распада в этой системе существенно выше (~1500°C) рассматриваемого интервала температур. При этом для стали данного состава весь Ti оказывается связан с N. В результате, при содержании 0.005 мас. % N и 0.01–0.02 мас. % Ti, после образования нитридов TiN в матрице остается 0.003–0.002 мас. % N.
Рис. 4.
Кинетика образования нитрида TiN и карбида NbC в стали с 0.06 мас. % C, 0.06 мас. % Nb, 0.005 мас. % N, 0.02 мас. % Ti. (а) – изменение температуры поверхности листа в процессе ТМО на ТЛС 5000; (б) – изменение доли фаз (массовой) в зависимости от времени.
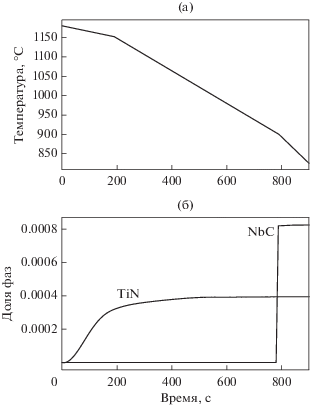
Зародыши NbC появляются во время междеформационной паузы, однако активное образование этого карбида происходит при переходе к стадии чистовой прокатки (рис. 4б). В условиях интенсивной деформации, благодаря индуцированному деформацией распаду [39, 40], выделение частиц NbC завершается в течение короткого времени ~5–10 с. Заметим, что в отсутствие деформации образование NbC при 800°C происходит за ~20 мин, что превышает времена горячей прокатки. Образование высокой плотности дисперсных карбидов NbC, играет существенную роль в торможении роста аустенитного зерна на стадии чистовой прокатки.
Следует отметить, что учет неоднородности температур и деформаций по сечению сляба приведет к более интенсивному выделению NbC и, соответственно, к более мелкому зерну в приповерхностной области по сравнению с центральной зоной. Для оценки степени неоднородности возникающей структуры требуется дальнейший анализ процессов, протекающих на стадии горячей деформации на ТЛС 5000, с учетом разогрева заготовки в результате деформации и развития фазовых превращений.
5. ФОРМИРОВАНИЕ СТРУКТУРЫ НА СТАДИИ УСКОРЕННОГО ОХЛАЖДЕНИЯ
Выбор температуры начала охлаждения и траектории охлаждения играет ключевую роль в формировании микроструктуры и свойств микролегированной стали. При быстром охлаждении стали и последующей выдержке на воздухе (в условиях близких к изотермическим) реализуются перестройка кристаллической решетки ГЦК → ОЦК (сдвиговое превращение) и диффузионное перераспределение углерода, сопровождающееся распадом аустенита с выделением феррита и цементита [15, 33, 41]. Для эффективного управления процессами образования структур необходимо понимание механизмов, определяющих развитие фазовых превращений в железе и стали.
Предложенные к настоящему времени модельные подходы правильно ухватывают основные черты полиморфных превращений в стали [33], однако оставляют в тени вопросы, касающиеся условий реализации превращений и их движущие силы (см. обсуждение в [33]). В работах [42, 43] был предложен микроскопический подход к построению теории полиморфных превращений в железе и стали на основе результатов первопринципных расчетов, учитывающий вклад решеточных и магнитных степеней свободы, а также диффузионное перераспределение углерода и легирующих элементов в стали. Развиваемые в [33, 42] представления могут служить надежной основой для разработки математических моделей формирования фазового и структурного состояния в стали.
В процессе ускоренного охлаждения на границах зерен происходит зарождение и последующий рост α-фазы, в результате чего формируется бейнитная (при высокой скорости охлаждения) или бейнитно-ферритная (при умеренной скорости охлаждения) структура. При этом существенную роль может играть микролегирование Mo и B, размер зерен, а также накопленная на стадии чистовой прокатки деформация, особенно если прокатка заканчивается при температуре, ниже температуры начала ферритного превращения Ar3. В последнем случае наблюдается ускорение ферритного превращения (deformation induced ferrite transformation, ДИФТ [44, 45]), что может приводить к измельчению формирующейся структуры. Кинетика превращений в условиях близких к изотермическим хорошо исследована. Кривые ферритного, перлитного и бейнитного превращений на изотермической диаграмме распада переохлажденного аустенита – TTT диаграмме (time-temperature-transformation) имеют C-образный вид и в микролегированной стали обычно перекрываются [46].
Согласно распространенному мнению [47, 48], легирование Mo и, особенно, B может существенно замедлять кинетику феррито-перлитного превращения, смещая его начало в область больших времен. В тоже время эти элементы практически не влияют на бейнитное превращение, развитие которого определяется в основном стадией роста ферритных пластин в объеме зерна. Поэтому легирование Mo и B рассматривается как эффективный способ управления кинетикой превращения и формирования микроструктуры в высокопрочной низколегированной (HSLA) стали.
Однако недавние исследования [49, 50] кинетики распада аустенита в низкоуглеродистой стали привели к неожиданному выводу. Как было показано в [49], образование феррита ускоряется при повышенных температурах (650–700°С) в стали, содержащей B и Mo, в то время как при пониженных температурах (550–600°С) наблюдается замедление ферритного превращения (рис. 5). Результаты [49] указывают, что в последнем случае определяющую роль играет повышение барьера образования зародышей α-фазы на границах зерен, содержащих сегрегации B или Mo. В тоже время эти элементы увеличивают движущую силу роста α-фазы (что коррелирует с изменением температуры Т0 при легировании [51]), ускоряя превращение в области повышенных температур.
Рис. 5.
Влияние добавок B (кривая 2) и Mo (кривая 3) на кинетику превращения в низкоуглеродистой стали (кривая 1 – без легирования B и Mo) [49].
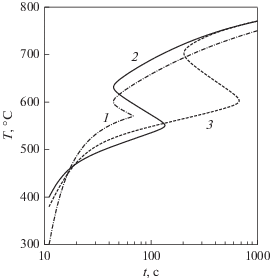
Использование TTT-диаграмм в условиях непрерывного охлаждения не имеет надежных оснований, поскольку превращения, начавшиеся при повышенных температурах, влияют как на инкубационный период, так и на скорость низкотемпературных превращений. В частности, изменение состава непревращенного аустенита в результате промежуточного (бейнитного) превращения может приводить к существенному снижению стартовой температуры мартенситного превращения. При непрерывном охлаждении кинетику превращения принято характеризовать термокинетической диаграммой (рис. 6), на которой отображаются температуры, соответствующие началу и концу превращений (или достижению определенной объемной доли формирующейся фазы) при заданной траектории охлаждения.
Рис. 6.
Термокинетическая диаграмма превращений в малоуглеродистой низколегированной стали [56]. Сплошные линии – под воздействием деформации (15–20% при 850°С), штриховые – без деформации. Ф, П, Б, М – области формирования феррита, перлита, бейнита и мартенсита соответственно.
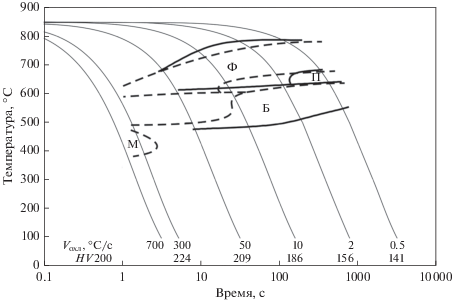
Стимулирование деформацией ферритного превращения является эффективным методом измельчения ферритного зерна (вплоть до перевода его в ультрамелкозернистое состояние) [52]. Как видно из рис. 6, пластическая деформация повышает температуру аустенит-ферритного превращения Ar3 [53, 54]. При этом ДИФТ реализуется, когда чистовая прокатка заканчивается в температурном интервале между Aс3 и Ar3. В этом случае ферритная фаза начинает образовываться динамически во время деформирования, что приводит к значительному измельчению структуры и увеличению доли ферритной составляющей.
Температура старта ферритного превращения Ar3 в зависимости от размера зерна аустенита и скорости охлаждения исследована в [55].
Для типичного размера зерна и скоростей охлаждения (40–60°C/с) температура Ar3 лежит на 20–40°С ниже температуры конца прокатки Tk ≈ ≈ 800°С (рис. 7). Таким образом, в рассматриваемой стали для принятых режимов не следует ожидать развития ДИФТ. В тоже время небольшое уменьшение содержания углерода (или увеличение концентрации Mo, Ni, Cu [44, 57]) может привести к повышению Ar3 и, соответственно, к измельчению ферритного зерна в условиях ДИФТ.
Рис. 7.
Температура старта ферритного превращения в HSLA стали в зависимости от скорости охлаждения при разных размерах зерна [55]. Кружочки, квадратики и треугольники соответствуют среднему размеру зерна 18, 44 и 84 мкм.
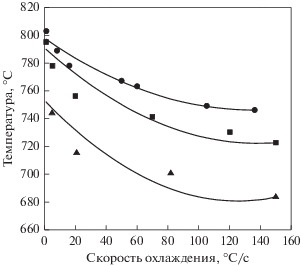
В отличие от ферритного превращения, ни предшествующая пластическая деформация, ни размер зерна не оказывают существенного влияния на бейнитное превращение, кинетика которого определяется главным образом химическим составом стали. При достижении температуры старта бейнитного превращения Bs, оно развивается за короткое время, и образующаяся фаза заполняет большую часть доступного объема зерна. Для температуры Bs предложены различные эмпирические формулы [58–64]. Расхождение в получаемых разными авторами значениях Bs, обусловлено, по-видимому, тем, что в зависимости от предшествующей обработки легирующие элементы могут находиться в твердом растворе либо сегрегировать на границах зерен, либо участвовать в образовании карбидных частиц.
Для предсказания структурного состояния необходимо знать кинетику структурно-фазовых превращений в рассматриваемой стали, реализующуюся в условиях ускоренного охлаждения на ТЛС 5000. Существенным фактором, определяющим (при заданном химическом составе) формирование микроструктуры, является выбор температуры конца прокатки и траектории охлаждения. При этом технология КП + УО для производства хладостойкого проката толщиной 25 мм имеет свои особенности, обусловленные большой толщиной металла и наличием градиента температур по сечению листа. Поскольку отвод тепла осуществляется с поверхности полосы, необходимо рассматривать кинетику превращения в условиях заданной скорости отвода тепла с учетом неоднородности распределения температуры по сечению листа.
На рис. 8 приведено рассчитанное распределение температуры по сечению листа в зависимости от времени охлаждения [65], реализующееся на ТЛС 5000. Видно, что при прохождении участка ускоренного охлаждения (0–12 с) в полосе формируется крайне неоднородное распределение температуры. В то время как на поверхности листа реализуются условия быстрой закалки (что приводит к развитию мартенситного превращения), во внутренних слоях полосы охлаждение происходит гораздо медленнее, формируется бейнитная или феррито-бейнитная структура. В результате, структурное состояние стали (и ее прочностные свойства) оказываются неоднородными, а степень неоднородности весьма чувствительна к выбору траектории охлаждения. При этом кинетика фазовых превращений контролируется скоростью отвода тепла с поверхности полосы [66] и интенсивностью тепловыделения, сопровождающего процесс фазового превращения [67]. Поэтому разработка последовательных теоретических представлений о кинетике фазовых превращений в условиях быстрого охлаждения и более сложных многоступенчатых температурных траекторий является в настоящее время одной из актуальных задач, решение которой позволит получить оптимальное структурное состояние, обеспечивающее требуемые свойства стали.
6. ЗАКЛЮЧЕНИЕ
Современная технология производства трубных сталей является сложным, наукоемким процессом, который должен обеспечивать управление структурообразованием на всех стадиях ТМО, сочетающей контролируемую прокатку и ускоренное охлаждение (КП + УО). Необходимое для толстолистового проката сочетание прочностных и вязкопластических характеристик достигается благодаря формированию ферритно-бейнитной структуры с малым размером зерна и повышенной плотностью дислокаций [2, 3].
В настоящее время установлены основные процессы, контролирующие структурообразование на различных стадиях ТМО. Они включают измельчение аустенитного и ферритного зерна за счет применения КП + УО, образование выделений карбонитридных фаз в процессе горячей прокатки и осуществление распада значительной части аустенита в интервале температур бейнитного превращения. Однако остается ряд задач, решение которых является существенным для дальнейшего повышения эффективности процесса ТМО и достижения требуемого структурного состояния. К ним, в частности, относятся (i) выбор условий нагрева, обеспечивающих растворение карбонитридов Nb и V при сохранении выделений TiN, предотвращающих рост зерна аустенита, (ii) выбор режимов деформации, позволяющих избежать формирования значительной разнозенистости, (iii) создание оптимальных условий для образования карбонитридов Nb во время междеформационной паузы и на стадии чистовой прокатки, (iv) выяснение механизмов влияния деформации и микролегирования на процессы распада аустенита и измельчения микроструктуры, (v) задание режима ускоренного охлаждения в условиях теплоотвода с поверхности листа с учетом тепловыделения при фазовых превращениях, обеспечивающего получение требуемого структурного состояния. Для решения этих задач требуется дальнейшие экспериментальные и теоретические исследования при широком использовании методов компьютерного моделирования фазовых и структурных превращений.
Список литературы
Gladman T. The physical metallurgy of microalloyed steels. London: Institute of Materials, 1997. 363 p.
Хулка К., Петерс П., Хайстеркамп Ф. Тенденции разработки сталей для труб большого диаметра // Сталь. № 10. 1997. С. 62–67.
Эфрон Л.И. Металловедение в “большои” металлургии. Трубные стали. М.: Металлургиздат, 2012 г. 696 с.
Schwinn V., Schuetz W., Fluess P., Bauer J. Prospects and state of the art of TMCP steel plates for structural and linepipe aplications // Materials Science Forum. 2007. V. 539–543. P. 4726–4731.
Морозов Ю.Д., Матросов М.Ю., Настич С.Ю., Арабей А.Б. Высокопрочные трубы стали нового поколения с феррито-бейнитной структурой // Металлург. 2008. № 8. С. 39–42.
Lagneborg R., Siwecki T., Zajac S., Hutchinson B. The role of vanadium in microalloyed steels // Scandinavian J. Metallurgy. 1999. V. 28. P. 1–86.
Panigrahi B.K. Processing of low carbon steel plate and hot strip – an overview // Bull. Mater. Sci. 2001. V. 24. P. 361–371.
Belato Rosado D., De Waele W., Vanderschueren D., Hertelé S. Latest developments in mechanical properties and metallurgical features of high strength line pipe steels // Sustainable Construction and Design, 2013. V. 4. P. 1–10.
Настич С.Ю. Разработка технологии термомеханической обработки полосового и листового проката из низколегированной стали на основе управления формированием ферритно-бейнитной структуры, автореферат диссертации д. т. н., Москва, ЦНИИчермет им. И.П. Бардина 2013. 45 с.
Счастливцев В.М., Яковлева И.Л., Салганик В.М. Основные структурные факторы упрочнения низкоуглеродистых низколегированных трубных сталей после контролируемой прокатки // МиТОМ. 2009. № 1. С. 41–45.
Попов В.В. Моделирование превращений карбонитридов при термической обработке сталей. Екатеринбург: УрО РАН. 2003. 378 с.
Klinkenberg C., Klein H. Synchrotron investigation on the precipitation behaviour of niobium microalloyed steel // Mat. Sci. Forum. 2017. V. 879. P. 948–953.
Suwanpinij P. The synchrotron radiation for steel research // Adv. Mat. Sci. Eng. 2016. V. 2016. P. 2479345 (8 p.).
Sundman B., Jansson B., Andersson J.O. Thermo-calc databank system. // CALPHAD. 1985. № 9. P. 153–190.
Gorbatov O.I., Gornostyrev Yu.N., Korzhavyi P.A., Ruban A.V. Ab initio modeling of decomposition in iron based alloys // Phys. Met. Metall. 2016. V. 117. P. 1293–1327.
Ponomareva A.V., Gornostyrev Yu.N., Abrikosov I.A. Ab initio calculation of the solution enthalpies of substitutional and interstitial impurities in paramagnetic fcc Fe // Phys. Rev. B. 2014. V. 90. P. 014439 (8 p.).
Svoboda J., Fischer F.D., Fratzl P., Kozeschnik E. Modelling of kinetics in multi-component multi-phase systems with spherical precipitates. I: Theory // Mater. Sci. and Eng. A. 2004. V. 385. P. 166–174.
Kozeschnik E., Svoboda J., Fischer F.D. Modified evolution equations for the precipitation kinetics of complex phases in multi-component systems // CALPHAD: Computer Coupling of Phase Diagrams and Thermochemistry. 2004. V. 28. P. 379–382.
Zamberger S., Pudar M., Spiradek-Hahn K., Reischl M., Kozeschnik E. Numerical simulation of the evolution of primary and secondary Nb(CN), Ti(CN) and AlN in Nb-microalloyed steel during continuous casting // International Journal of Materials Research. 2012. V. 103. P. 680–687.
Radis R., Kozeschnik E. Numerical simulation of NbC precipitation in microalloyed steel // Modelling and simulation in materials science and engineering. 2012. V. 20. P. 55010–55024.
Popov V.V., Gorbachev I.I., Alyabieva J.A. Simulation of VC precipitate evolution in steels with consideration for the formation of new nuclei // Phil. Mag. 2005. V. 85. P. 2449–2467.
Горбачёв И.И., Пасынков А.Ю., Попов В.В. Прогнозирование размера аустенитного зерна микролегированных сталей на основе моделирования эволюции карбонитридных выделений // Физика металлов и металловедение. 2015. Т. 116. С. 1184–1192.
McQueen H.J., Jonas J.J. Role of the dynamic and static softening mechanisms in multistage hot working // J. Applied Metalworking. 1985. V. 3. P. 410–420.
Xu Y., Tang D., Song Y., Pan X. Dynamic recrystallization kinetics model of X70 pipeline steel // Materials and Design. 2012. V. 39. P. 168–174.
Martins C.A., Poliak E., Godefroid L.B., Fonstein N. Determining the Conditions for Dinamic Recrystallization in Hot Deformation of C–Mn–V Steels and the Effects of Cr and Mo Additions // ISIJ International. 2014. V. 54. № 1. P. 227–234.
Частухин А.М. Закономерности процессов рекристаллизации аустенита и совершенствование технологии контролируемой прокатки микролегированных трубных сталей повышенной хладостойкости. Дис. … к. т. н. ЦНИИЧМ, Москва, 2017.
Mirzadeh H., Najafizadeh A. Prediction of the critical conditions for initiation of dynamic recrystallization // Materials and Design. 2010. V. 31. P. 1174–1179.
Супов А.В., Канев В.П., Одеский П.Д., Зикеев В.Н. Металловедение и термическая обработка стали и чугуна. Т. 3 Термическая и термомеханическая обработка стали и чугуна. М.: Интермет Инжиниринг, 2007. 919 с.
McQuenn H.J., Ryan N.D. Costitutive analysis in hot working // Mat. Sci. Eng. A. 2002. V. 322. № 1–2. P. 43–63.
Subramanian S.V., Zhu G., Klinkenberg C., Hulka K. Ultra-fine grain size by dynamic recrystallization in strip rolling of Nb microalloyed steel // Materials Science Forum. 2005. V. 475–479. P. 141–144.
Настич С.Ю. Влияние морфологии бейнитной составляющей микроструктуры низколегированной стали X70 на хладостойкость проката больших толщин // Металлург. 2012. № 3. С. 61–69.
Настич С.Ю., Матросов М.Ю. Структурообразование высокопрочных трубных сталей при термомеханической обработке // Металлург. 2015. № 9. С. 47–54.
Razumov I.K., Gornostyrev Yu.N., Katsnelson M.I. Towards the ab initio Based Theory of Phase Transformations in Iron and Steel // Physics of Metals and Metallography. 2017. V. 118. P. 362–388.
Горбачeв И.И., Пасынков А.Ю., Попов В.В. Моделирование влияния горячей деформации на размер аустенитного зерна низколегированных сталей с карбонитридным упрочнением // Физика металлов и металловедение. 2018. Т. 119. С. 582–590.
Neu J.C., Bonilla L.L. Classical Kinetic theory of nucleation and coarsening / in Math. Modelling for Polymer Processing by ed. Capasso V. Springer-Verlag Berlin Heidelberg, 2003. P. 31–58.
Ziabicki A. Generalized theory of nucleation kinetics. I. General formulations // J. Chem. Phys. 1968. V. 48. P. 4368–4374.
Markov I.V. Crystal growth for beginners. World Sci., Singapore, 1995. 564 p.
http://www.matcalc.at/.
Qiao G.Y., Xiao F.R., Zhang X.B., Chen S.H., Liao B. Effects of Nb on strain-induced precipitation of NbC and static recrystallization for high Nb pipeline steels // Advanced Materials Research. 2011. V. 146–147. P. 1315–1321.
Jiang L., Humphreys A.O., Jonas J.J. Effect of silicon on the interaction between recrystallization and precipitation in niobium microalloyed steels // ISIJ International. 2004. V. 44. P. 381–387.
Leslie W.C., Hornbogen E. Physical metallurgy of steels / in Physical Metallurgy by ed. Cahn R.W. and Haasen P. V. 2. Elsevier, N.Y., 1996. P. 1555–1620.
Razumov I.K., Boukhvalov D.V., Petrik M.V., Urtsev V.N., Shmakov A.V., Katsnelson M.I., Gornostyrev Yu.N. Role of magnetic degrees of freedom in a scenario of phase transformations in steel // Phys. Rev. B. 2014. V. 90. P. 094101.
Leonov I., Poteryaev A.I., Gornostyrev Yu.N., Lichtenstein A.I., Katsnelson M.I., Anisimov V.I., Vollhardt D., Electronic correlations determine the phase stability of iron up to the melting temperature // Scientific reports. 2014. V. 4. P. 5585.
Shaban M., Gozalzadeh S., Eghbali B. Dynamic Strain Induced Transformation of Austenite to Ferrite during High Temperature Extrusion of Low Carbon Steel // Materials Transactions. 2011. V. 52. № 1. P. 8–11.
Sa J., Kvackaj T., Milkovic O., Zemko M. Influence of hot plastic deformation in γ and (γ + α) area on the structure and mechanical properties of high-strength low-alloy (HSLA) steel // Materials. 2016. V. 9. P. 971–979.
Счастливцев В.М., Мирзаев Д.А., Яковлева И.Л. Перлит в углеродистых сталях. Екатеринбург: УрО РАН, 2006. 311 с.
Porter L.F. The present status and future of boron steels. /In Boron in steel by ed. Banerji S.K. and Morral J.E., Warrendale, Pennsylvania, TMS–AIME. USA, 1980. P. 199–211.
Grange R.A. Estimating the hardenability of carbon steels // Metallurgical Transactions B. 1973. V. 4. P. 2231–2244.
Khare S., Lee K., Bhadeshia H.K.D.H. Relative effects of Mo and B on ferrite and bainite kinetics in strong steels // Int. J. Material Research. 2009. V. 100. P. 1513–1520.
Capdevila C., Ferrer J.P., García-Mateo C., Caballero F.G., López V., de Andrés C.G. Influence of deformation and molybdenum content on acicular ferrite formation in medium carbon steels // ISIJ International. 2006. V. 46. P. 1093–1100.
Krauss G. Steels: heat treatment and processing principles. Materials Park, OH, 1995. 497 p.
Dong H., Sun X. Deformation induced ferrite transformation in low carbon steels // Current Opinion in Solid State and Materials Science. 2005. V. 9. P. 269–276.
Beladi H., Kelly G.L., Shokouhi A., Hodgson P.D. Effect of thermomechanical parameters on the critical strain for ultrafine ferrite formation through hot torsion testing // Mater. Sci. Eng. A. 2004. V. 367. P. 152–161.
Пазилова У.А., Хлусова Е.И., Князюк Т.В. Влияние режимов горячей пластической деформации при закалке с прокатного нагрева на структуру и свойства экономнолегированной высокопрочной стали // Вопросы материаловедения. 2017. № 3. С. 7–19.
Militzer M., Pandi R., Hawbolt E.B. Ferrite Nucleation and Growth durinf Continuous Cooling // Metal. Mater. Trans. A. 1996. V. 27A. P. 1547–1556.
Настич С.Ю., Морозов Ю.Д., Матросов М.Ю., Денисов С.В., Галкин В.В., Стеканов П.А. Освоение производства на стане 5000 ОАО “ММК” проката из низколегированных сталей с повышенными характеристиками прочности и хладостойкости // Металлург. 2011. № 11. С. 57–64.
Матросов М.Ю., Эфрон Л.И., Ильинский В.И., Северинец И.Ю., Липунов Ю.И., Эйсмондт К.Ю. Использование ускоренного охлаждения для повышения механических и технологических свойств толстолистового проката для изготовления газопроводных труб большого диаметра // Металлург. 2005. № 6. С. 49–54.
Stevens W., Haynes A.G. The Temperature of Formation of Martensite and Bainite in Low-Alloy Steels // J. Iron Steel Inst. 1956. V. 183. P. 349–359.
Lee J.K. Empirical formula of isothermal bainite start temperature of steels // J. Mater. Sci. Letters. 2002. V. 21. P. 1253–1255.
Suehiro M., Senuma T., Yada H., Matsumura Y., Ariyoshi T. A Kinetic Model for Phase Transformations of Low Carbon Steels during Continuous Cooling // Tetsu-to-Hagan. 1987. V. 73. P. 1026–1033.
Bodnar R.L., Ohhashi T., Jaffee R.I. Effects of Mn, Si, and purity on the design of 3.5 NiCrMoV, 1CrMoV, and 2.25 Cr–1Mo bainitic alloy steels // Metall. Trans. A. 1989. V. 20A. P. 1445–1460.
Kunitake T., Okada Y. The estimation of bainite transformation temperatures in steels by empirical formulas // J. Iron Steel Inst. 1998. V. 84. P. 137–141.
Zhao J., Liu C., Liu Y., Northwood D.O. A new empirical formula for the bainite uppertemperature limit of steel // J. Mater. Sci. 2001. V. 36. P. 5045–5056.
van Bohemen S.M.C. Bainite and martensite start temperature calculated with exponential carbon dependence // Mater. Sci. Technol. 2012. V. 28. P. 487–495.
Гареев А.Р., Муриков С.А., Платов С.И., Урцев В.Н., Шмаков А.В. Анализ и экспериментальная верификация модели тепловыделения при фазовых превращениях // Производство проката. 2015. № 2. С. 30–34.
Лобанов М.Л., Краснов М.Л., Урцев В.Н., Данилов С.В., Пастухов В.И. Влияние скорости охлаждения на структуру низкоуглеродистой низколегированной стали после контролируемой термомеханической обработки // МиТОМ. 2019. № 1. С. 31–37.
Лобанов М.Л., Русаков Г.М., Урцев В.Н., Краснов М.Л., Мокшин Е.Д., Шмаков А. В., Платов С.И. Тепловой эффект бейнитного превращения в трубных сталях при ускоренном охлаждении // Письма о материалах. 2018. Т. 8. № 3. С. 246–251.
Дополнительные материалы отсутствуют.
Инструменты
Физика металлов и металловедение