Физика металлов и металловедение, 2019, T. 120, № 2, стр. 169-175
Влияние отжига на структуру и свойства стареющего сплава Al–Li–Cu–Mg–Zr–Sc–Zn, подвергнутого мегапластической деформации
Л. И. Кайгородова a, Д. Ю. Распосиенко a, b, *, В. Г. Пушин a, b, В. П. Пилюгин a, С. В. Смирнов b, c
a Институт физики металлов УрО РАН
620990 Екатеринбург, ул. С. Ковалевской, 18, Россия
b ФГАОУ ВО “УрФУ имени первого Президента России Б.Н. Ельцина”
620002ул. Мира, 19 Екатеринбург, Россия
c Институт машиноведения УрО РАН
620049 Екатеринбург, ул. Комсомольская, 34, Россия
* E-mail: dmitrijrasp@gmail.com
Поступила в редакцию 18.06.2018
После доработки 05.09.2018
Аннотация
Методами электронной микроскопии изучены структурные и фазовые превращения в процессе низкотемпературного отжига при 150°С в сплаве Al–Li–Cu–Mg–Zr–Sc–Zn, подвергнутом мегапластической деформации кручением под высоким давлением. Показано, что характер формирующейся в течение отжига нанокристаллической структуры определяется особенностями существовавшей ранее деформационной структуры и демонстрирует структурную наследственность. Обсуждается влияние структурного состояния отожженного сплава на уровень механических свойств (твердость, пластичность, модуль упругости, жесткость).
ВВЕДЕНИЕ
Одной из основных задач материаловедения является исследование закономерностей структурообразования, позволяющих получать новые материалы с заданными повышенными свойствами. Свойства материалов значительно зависят от таких факторов, как химический состав, дисперсность и дефектность микроструктуры и ряда других. В последние годы большое внимание уделяется созданию металлических материалов с нанокристаллической (НК) или субмикрокристаллической (СМК) структурами. Известно, что в силу малого размера структурных составляющих (СМК: <1000 нм, НК: <100 нм), в таких материалах заметно повышена протяженность межкристаллитных (межзеренных и межфазных) границ. И согласно многочисленным данным в чистых металлах и сплавах в наноструктурном состоянии в ряде случаев удается получить уникальный комплекс физических и механических свойств [1–3].
Одним из способов получения аморфных, НК и СМК материалов является использование мегапластической деформации (МПД) кручением под высоким давлением [2]. Имеются обширные экспериментальные данные, доказывающие эффективность ее применения, особенно в сочетании с различными термообработками, для повышения комплекса свойств металлов и модельных сплавов, включая алюминиевые [1–3].
Однако для многих сплавов (и в том числе легких стареющих промышленных алюминиевых сплавов последнего поколения) исследования влияния МПД на структуру и свойства с учетом различного легирования и возможного старения, за некоторыми исключениями [4], практически не проводились. Также для стареющих сплавов важным и практически не изученным является изменение механизмов распада в результате МПД. Ранее нами было показано, что МПД и последующий отжиг многокомпонентных промышленных стареющих сплавов на основе Al–Li-марок 1450 и 1469 позволяют получить в них высокопрочное наноструктурное состояние [5–7]. Уровень свойств (твердости, пластичности, модуля упругости) отожженных сплавов главным образом определялся особенностями сформировавшейся при постдеформационном отжиге нанокристаллической (НК) или смешанной (НК + СМК) структуры и характером зарождения и роста нанофаз, образующихся при распаде пересыщенного твердого раствора. Помимо этого было показано, что отжиг обеспечивает стабильность свойств сильнодеформированного сплава 1450 и в течение длительного вылеживания при комнатной температуре, что связано с размерной стабильностью НК и (НК + СМК) структур и сохранением объемной доли, состава и характера распределения выделившихся при отжиге фаз [8].
Стареющий промышленный сплав 1461 отличается от ранее нами исследованных марок 1450 и 1469 сплавов Al–Li как содержанием основных легирующих компонентов Li и Cu, так и наличием Zn. В соответствии с этим представляет интерес изучить его структуру после МПД и последующего отжига и установить взаимосвязь структурных составляющих со свойствами. Данная задача является актуальной, так как она посвящена получению высокопрочных металлических материалов с уникальными и стабильными свойствами. Ожидаемые результаты также расширят представления о фазовых и структурных превращениях, реализующихся при отжиге в стареющих ультрамелкозернистых сплавах с высокой плотностью высокоугловых и малоугловых границ.
МАТЕРИАЛ И МЕТОДИКА ЭКСПЕРИМЕНТА
Исследовали промышленный сплав 1461 с НК и СМК структурой, формирующейся при МПД и последующем отжиге 150°С, 15 ч. Химический состав сплава в мас. % приведен в табл. 1.
Таблица 1.
Химический состав сплава 1461 (в мас. %)
Сu | Li | Zr | Sc | Zn | Mg | Al |
---|---|---|---|---|---|---|
2.8 | 1.8 | 0.08 | 0.09 | 0.66 | 0.5 | Ост. |
МПД закаленного сплава 1461 осуществляли в наковальнях Бриджмена под давлением 4 ГПа при комнатной температуре. Образцы для деформации представляли собой диски диаметром 15 мм и толщиной 2 мм. Используемые режимы МПД приведены в табл. 2. Расчет истинной деформации проводили для точек, лежащих на 1/2 радиуса образца.
Таблица 2.
Режимы мегапластической деформации под давлением 4 ГПа
Угол поворота φ, π рад | 2 | 10 | 20 |
---|---|---|---|
Истинная деформация на ½ радиуса диска е | 7.0 | 8.6 | 9.3 |
Изучение структурных и фазовых превращений в сплаве осуществляли методом тонких фольг на электронных просвечивающих микроскопах JEM‑200 CХ и Philips CM 30 Super Twin в центре коллективного пользования ИФМ УрО РАН. Линейные размеры элементов структуры определяли непосредственными измерениями на плоскости наблюдения. Для каждого распределения нанозерен были рассчитаны средний размер и среднее квадратичное отклонение. Механические свойства сплава определяли методом инструментального наноиндентирования на нанотвердомере FISHERSCOPE 2000 с алмазным индентором Виккерса, подробно описанным в [9, 10]. Испытания образцов проводили на ½ их радиуса при нагрузках 150 и 500 мН.
РЕЗУЛЬТАТЫ ЭКСПЕРИМЕНТОВ И ИХ ОБСУЖДЕНИЕ
Сплав в микрокристаллическом состоянии после искусственного старения
На электронно-микроскопических изображениях обычного микрокристаллического (МК) сплава 1461 после искусственного старения при 160°С, 32 ч наблюдалась развитая зеренно-субзеренная структура с размером субзерен ~2–3 мкм [11]. В объеме субзерен выявлялись равномерно распределенные дисперсные частицы упрочняющих фаз: равноосные частицы диаметром ~5 нм метастабильной фазы δ' (Al3Li) и тонкие пластины длиной 20–30 нм стабильной фазы Т1 (Al2LiCu). Помимо сферической формы на изображениях структуры выявлялись отдельные дисперсоиды Al3(Zr, Sc) диаметром до 10 нм, плотность распределения которых была незначительной. Также в объеме субзерен и по их границам присутствовали отдельные крупные интерметаллиды кристаллизационного происхождения равноосной или пластинчатой формы, преимущественно имевшие состав фазы Т2 (Al5CuLi3). Диаметр равноосных интерметаллидов составлял около 0.2 мкм, а длина пластин – 0.5–0.7 мкм.
Структура сплава после мегапластической деформации и отжига
Формирование зеренной структуры. При отжиге в сильнодеформированном сплаве 1461 протекает статическая рекристаллизация, результатом которой является формирование смешанной (НК + СМК) структуры с бимодальным распределением зерен по размерам. Отсутствие на изображениях микроструктуры отожженного сплава дипольных границ [12], характерных для его сильнодеформированного состояния [11], также свидетельствует об образовании более равновесной структуры (рис. 1а, 2а, 3а).
Рис. 1.
Микроструктура сплава 1461 после МПД на φ = 2π рад и отжига 150°С, 15 ч: а, в – светлопольные изображения; б, г – темнопольные изображения в рефлексах (442)Т2 и (111)Al и соответствующая микроэлектронограмма (б).
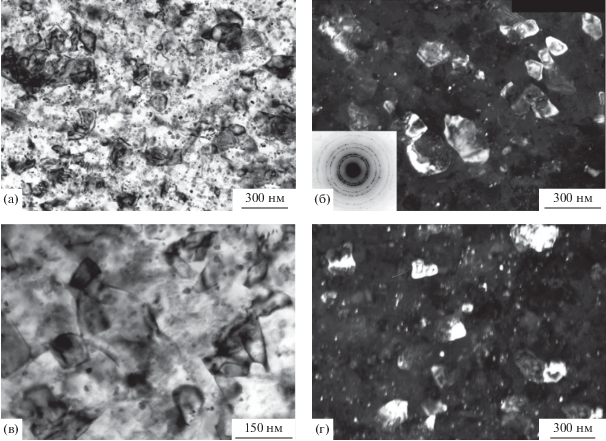
В отожженном сплаве, как показало проведенное исследование, характер структурных составляющих и их распределение в объеме образца зависят от режима МПД. Так, отжиг после использования МПД (φ = 2π рад) приводит к появлению на электронно-микроскопических изображениях микроструктуры преимущественно однородно и случайно распределенных НК-зерен и субзерен диаметром около 100 нм, чередующихся с СМК-зернами диаметром более 150–200 нм (рис. 1а–1г). Это подтверждается кольцевым характером распределения брэгговских рефлексов на микроэлектронограммах (рис. 1б).
Повышение МПД (возрастание угла поворота φ от 2π до 10π рад) приводит к возрастанию дисперсности смешанной структуры: диаметр НК-зерен и субзерен уменьшается до 50–70 нм, а СМК-зерен – до 150–170 нм (рис. 2а–2г). В этом случае, наряду с преимущественно однородно распределеными нанозернами и субзернами в объеме сплава, появляются отдельные участки с полосовой структурой, в которых НК- и СМК-зерна распределены анизотропно вдоль направлений исходных деформационных полос, образуя протяженные конгломераты (рис. 2б–2г). Подобные участки полосовой структуры были обнаружены в сплаве сразу после МПД [11]. Можно заключить, что структура отожженного сплава наследует данные структурные особенности сильнодеформированного состояния. Таким образом, в отожженном сплаве после МПД на φ = 10π рад сосуществуют области с однородным и анизотропным распределением НК- и СМК-зерен с преобладанием первых.
Рис. 2.
Микроструктура сплава 1461 после МПД на φ = 10π рад и отжига 150°С, 15 ч: а, б – светлопольные изображения; в, г – темнопольные изображения в рефлексах (442)Т2 и (111)Al.
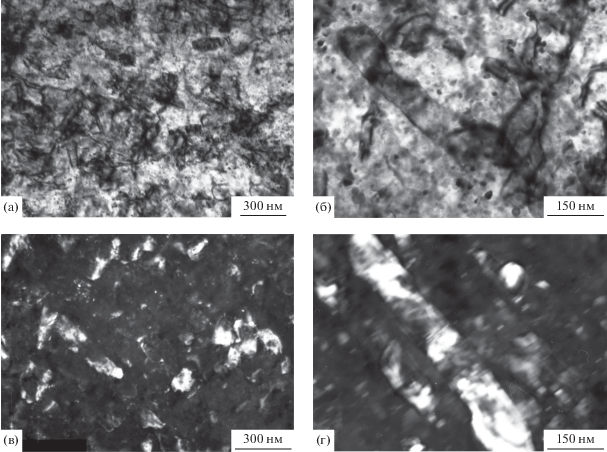
При возрастании угла φ до 20π рад тенденция к развитию полосовой структуры усиливается. В пределах полос сохраняется бимодальное распределение структурных элементов по размерам, сопровождающееся их дальнейшим измельчением: диаметр НК-зерен составляет 40–50 нм, а СМК-зерен – 150 нм. Наличие полосовой структуры приводит к анизотропному распределению СМК- и НК-зерен вдоль направлений полос (рис. 3в, 3г). Асимметрия интенсивности брэгговских рефлексов типа (111)Al и (200)Al по дебаевским кольцам на микроэлектронограммах подтверждает также текстурную неоднородность распределения структурных элементов (рис. 3а).
Рис. 3.
Микроструктура сплава 1461 после МПД на φ = 20π рад и отжига 150°С, 15 ч: а, в – светлопольные изображения и соответствующая микроэлектронограмма (а); б, г – темнопольные изображения в рефлексах (442)Т2 и (111)Al.
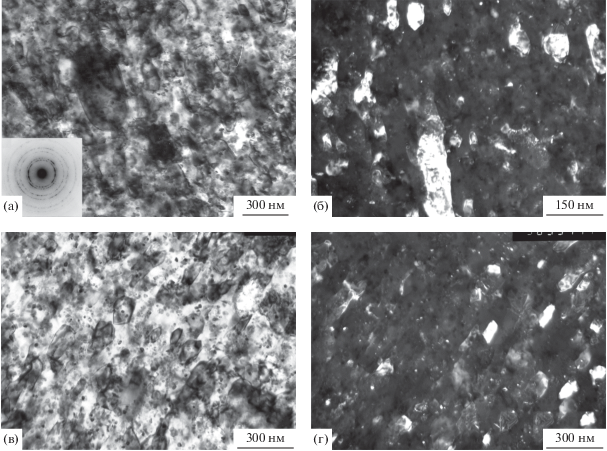
Сопоставление структуры сплава в сильнодеформированном и отожженном состояниях позволило сделать вывод о том, что структура отожженного сплава во многом определяется его исходными структурными особенностями, сформированными в сильнодеформированном состоянии (т.е. имеет место структурная наследственность).
Во-первых, полосовая структура, наблюдаемая в деформированных образцах после МПД на φ = 10π и 20π рад, сохраняется и после отжига (при φ = 10π рад – в отдельных областях, а при φ = 20π рад – практически во всем объеме сплава) и определяет характер распределения и форму рекристаллизованных НК- и СМК-зерен при отжиге. Отжиг вызывает уширение деформационных полос до 100–200 нм, поскольку после МПД их ширина составляла 50–100 нм.
Во-вторых, оказалось, что механизм формирования при отжиге бимодальной зеренно-субзеренной структуры зависит от структурных особенностей сплава в сильнодеформированном состоянии. Так, после МПД на φ = 2π рад сплав характеризовался однородной нанофрагментированной деформационной структурой, на фоне которой присутствовали отдельные редко расположенные динамически рекристаллизованные НК-зерна [11]. Анализ показал, что плотность распределения таких НК-зерен практически не отличается от плотности СМК-зерен в отожженном сплаве. Из этого следует, что в данном случае наличие бимодальной структуры обеспечивается реализацией двух процессов: трансформацией нанофрагментированной структуры в нанокристаллическую и ростом размеров уже существовавших динамически рекристаллизованных нанозерен до масштаба СМК. Однако нельзя исключать и того, что часть их образовалась посредством коалесценции in situ за счет соседних нанофрагментов с близкой ориентацией решеток. Такой механизм рассматривался ранее при исследовании структуры сильнодеформированного сплава 1469 [6].
После МПД на φ = 20π рад в основном наблюдалась однородная динамически рекристаллизованная НК-структура (см. [11]). В этом случае появление при последующем отжиге бимодальности в распределении структурных элементов по размерам, скорее всего, вызвано ростом отдельных НК-зерен, сформировавшихся ранее в процессе динамической рекристаллизации.
При использовании МПД на φ = 10π рад, когда динамическая рекристаллизация реализовалась частично, в образце существовали области с НК и нанофрагментированной структурами и, следовательно, при отжиге возможны оба механизма формирования бимодальной структуры.
В-третьих, режим МПД также определяет форму образовавшихся при отжиге СМК- и НК-зерен: после МПД на φ = 2π рад они обладают равноосной или близкой к ней формой (см. рис. 1б, 1в). Образование полосовой структуры при возрастании угла φ до 20π рад приводит к тому, что не только скопления, как указывалось выше, но отдельные СМК- и НК-зерна вытягиваются вдоль исходных деформационных полос и ограняются (рис. 3в–3г). Наиболее заметно эта тенденция проявляется для зерен, у которых отношение ширины к длине составляет приблизительно 1 : 2. При МПД на φ = 10π рад, когда полосовая структура выявляется только в отдельных областях отожженного образца, участки с равноосными СМК- и нанозернами сосуществуют с участками вытянутых зерен.
На предоставленных рисунках видно, что после отжига, независимо от режима предшествующей МПД, СМК-зерна обладают преимущественно спрямленными границами, а НК-зерна – как спрямленными, так и выпукло-вогнутыми. Вблизи последних на светлопольных изображениях наблюдается характерный деформационный контраст в виде петель и дуг диаметром ~50 нм (см. рис. 1а, 2а, 3а). Подобный контраст был также обнаружен ранее при исследовании структуры подвергнутых МПД сплавов 1450 и 1469. Возникновение данного контраста обуславливалось наличием полей упругих напряжений вблизи неравновесных границ нанозерен [5‒7]. Следует отметить, что плотность петель и дуг заметно ниже в областях с полосчатой структурой, что указывает на образование в них структурных элементов с более равновесными границами (рис. 3в, 3г).
Распад пересыщенного твердого раствора. Ранее нами показано, что в процессе МПД (или сразу после нее при естественном старении) в исследуемом сплаве уже происходил распад пересыщенного твердого раствора: на электронограммах помимо матричных отражений были обнаружены рефлексы фазы Т2 (Al5CuLi3) [11]. На темнопольных изображениях в этих рефлексах выявлялись частицы диаметром 5–10 нм. После МПД с углом поворота φ = 2–10π рад частицы наблюдались на границах нанозерен и дипольных границах (или их сохранившихся фрагментах), а при МПД на φ = 20π рад – на границах нанозерен (после данного режима МПД в сплаве существовала динамически рекристаллизованная структура, дипольные границы отсутствовали). Изменение режима МПД не оказало заметного влияния на размеры частиц Т2 (их диаметр составлял менее 10 нм) и их объемную долю.
В отожженном сплаве так же, как и в исходном сильнодеформированном, зародившиеся гетерогенно частицы фазы Т2 присутствуют преимущественно на границах нано- и СМК-зерен (см. рис. 1б–1г, 2б, 2в, 3б–3г). Анализ светлопольных и темнопольных изображений в рефлексах фазы показал, что отжиг не оказывает заметного влияния как на размеры частиц Т2 (их диаметр сохраняется в переделах 5–10 нм), так и на плотность их распределения. Их ключевая роль при отжиге в данном случае заключается, очевидно, в барьерном эффекте, сдерживающем рост зерен.
Механические свойства сплава 1461 после МПД и отжига
Измерения показали, что после отжига сильнодеформированный сплав сохранил высокопрочное состояние – характеристики твердости претерпели незначительное снижение, сопровождавшееся повышением (или сохранением на прежнем уровне) пластичности и немонотонным изменением модуля упругости и показателя жесткости (рис. 4).
Рис 4.
Гистограммы механических свойств сплава 1461 после МПД и отжига 150°С, 15 ч: ◼ – деформированное,
⬜ – отожженное, – МК-состояние.
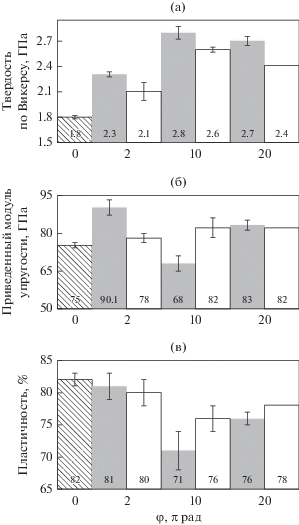
Более низкими величинами твердости и модуля упругости обладал сплав, отожженный после МПД при φ = 2π рад. Наиболее высокой твердостью после отжига – сплав после МПД при φ = 10π рад. При этом увеличение МПД практически не изменило пластичность отожженного сплава.
Поскольку электронно-микроскопическое исследование выявило, что отжиг существенно не повлиял на объемную долю обнаруженной после МПД фазы Т2, то основное изменение уровня свойств мы связали с релаксацией упругих напряжений в результате трансформации сформировавшейся при МПД (в зависимости от режима) нанофрагментированной, смешанной или нанокристаллической рекристаллизованной структуры. Сопоставление структурных изменений в процессе отжига со свойствами показало, что наибольшее изменение последних вызвала трансформация исходной нанофрагментированной в смесь однородной НК- и СМК-структуры.
Измельчение НК- и СМК-зерен и появление участков с их анизотропным распределением вследствие образования деформационных полос при увеличении угла φ до 10–20π рад обеспечили более высокий уровень прочностных характеристик и модуля упругости. При этом не было обнаружено существенной зависимости пластичности от режима МПД. Скорее всего, это обусловлено тем, что при отжиге произошло формирование бимодальной структуры, которая, согласно существующим представлениям, обеспечивает повышение пластических характеристик сплавов с НК- и СМК-структурой [13]. Некоторое падение характеристик твердости при повышении угла φ от 10 до 20π рад связано с тем, что в последнем случае при отжиге происходила более полная релаксация упругих напряжений.
ВЫВОДЫ
1. Обнаружено, что отжиг 150°С, 15 ч сплава 1461, подвергнутого МПД, приводит к образованию специфической частично рекристаллизованной структуры – смеси субмикро- и нанозерен и субзерен. Возрастание МПД повышает дисперсность структуры, изменяет соотношение объемных долей кристаллитов субмикро- и наномасштабного уровня и приводит к их анизотропному распределению. Последнее обусловлено наследованием сформировавшейся полосовой структуры при МПД (на φ = 10π рад – в отдельных участках, и на 20π рад – во всем объеме сплава).
2. Объемная доля, состав и характер зарождения обнаруженной после отжига упрочняющей фазы Т2 практически не зависят от режима МПД и несущественно отличаются от существовавших в сильнодеформированном состоянии.
3. Использование МПД и последующего отжига приводит к сильному упрочнению сплава 1461, сопровождающемуся повышением модуля упругости и незначительным снижением пластичности, что обусловлено формированием смешанной НК + СМК структуры.
Исследование выполнено в рамках госзадания ИФМ УрО РАН “Структура” Г.р. № АААА-А18-118020190116-6.
Список литературы
Валиев Р.З., Александров И.В. Объемные наноструктурные металлические материалы: получение, структура и свойства. М.: “ИКЦ “Академкнига”, 2007. 398 с.
Zhilyaev A.P., Langdon T.G. Using high-pressure torsion for metal processing: Fundamentals and applications // Progress in Materials Science. 2008. V. 53. Is. 6. P. 893–979.
Estrin Y., Vinogradov A. Extreme grain refinement by severe plastic deformation: A wealth of challenging science // Acta Mater. 2013. V. 6. Is. 3. P. 782–817.
Lee S., Horita Z., Hirosawa S., Matsuda K. Age-hardening of an Al–Li–Cu–Mg alloy (2091) processed by high-pressure torsion // Mater. Sci. Eng. A. 2012. V. 546. P. 82–89.
Кайгородова Л.И., Пушин В.Г., Распосиенко Д.Ю., Пилюгин В.П. Влияние интенсивной пластической деформации на образование нанокристаллической структуры и старение многокомпонентного алюминий-литиевого сплава с малыми добавками Sc и Mg // ФММ. 2011. Т. 111. № 1. С. 74–81.
Кайгородова Л.И., Распосиенко Д.Ю., Пушин В.Г., Пилюгин В.П., Смирнов С.В. Структура и свойства стареющего сплава Al–Li–Cu–Zr–Sc–Ag после мегапластической деформации кручением под давлением // ФММ. 2015. Т.116. № 4. С. 366–376.
Кайгородова Л.И., Распосиенко Д.Ю., Пушин В.Г., Пилюгин В.П., Смирнов С.В. Влияние отжига на структуру и свойства сплава Al–Li–Cu–Zr–Sc–Ag, подвергнутого мегапластической деформации // ФММ. 2015. Т. 116. № 9. С. 982–991.
Кайгородова Л.И., Распосиенко Д.Ю., Пушин В.Г., Пилюгин В.П. Влияние длительного вылеживания на структуру и свойства сплава на основе системы Al–Li–Cu–Zr, подвергнутого интенсивной пластической деформации кручением под давлением // ФММ. 2012. Т. 113. № 9. С. 913–924.
Oliver W.S., Pharr G.M. An improved technique for determining hardness and elastic modulus using load and displacement sensing indentation experiments // J. Mater. Res. 1992. V. 7. № 6. P. 1564–1583.
Мильман Ю.В., Дуб С.Н., Голубенко А.А. Масштабная зависимость твердости и характеристики пластичности, определяемой при индентировании // Деформация и разрушение материалов. 2008. № 8. С. 3–10.
Кайгородова Л.И., Распосиенко Д.Ю., Пушин В.Г., Пилюгин В.П., Смирнов С.В. Влияние мегапластической деформации на структуру и свойства сплава Al–Li–Cu–Mg–Zr–Sc–Zn // ФММ. 2018. Т. 119. № 2. С. 171–179.
Рыбин В.В. Большие пластические деформации и разрушение металлов. М: Металлургия, 1986. 234 с.
Глезер А.М. О природе сверхвысокой пластической деформации // Изв. РАН. Сер. физическая. 2007. Т. 71. № 12. С. 1764–1772.
Дополнительные материалы отсутствуют.
Инструменты
Физика металлов и металловедение