Физика металлов и металловедение, 2019, T. 120, № 5, стр. 526-536
Исследование методом наноиндентирования свойств алюминиевого сплава 6061 после его сварки трением с перемешиванием и последующего старения
Фируз Фадаэйфард a, Мохамад Реза Пакманеш a, *, Мортеза Шаманьян Эсфахани a, Хамирул Амин Матори b, Дидье Шико c
a Факультет технологии материалов, Исфаханский технологический университет
84156-83111 Исфахан, Иран
b Лаборатория диагностики и синтеза материалов, Институт перспективных технологий,
Университет Путра Малайзии (UPM)
43400 шт. Селангор, Сери, Кембанган, Малайзия
c Муниципальная лаборатория механики (отдел “3723” перспективных исследований) в составе Университета Лилля
F-59000 Лилль, Франция
* E-mail: mr.pakmanesh@ma.iut.ac.ir
Поступила в редакцию 05.02.2018
После доработки 19.09.2018
Принята к публикации 04.12.2018
Аннотация
Для изучения различных зон материала алюминиевого сплава AA6061 после воздействия на него сварки трением с перемешиванием в качестве нового метода локальной диагностики было использовано наноиндентирование. Наноиндентирование и измерение микротвердости осуществлялось на образцах после сварки и после последующего старения. В обоих случаях были изучены непосредственно область сварки (ядро шва), области термомеханического воздействия и исключительно теплового влияния. Наблюдения показали необходимость вводить поправку на возникновение дефекта острия пирамидки индентора вследствие накопления искажений, возникающих после каждого измерения микротвердости. При этом термическая обработка сварного соединения по схеме Т6 может восстановить как исходные значения модуля упругости и нанотвердости, так и микротвердость сплава AA6061.
ВВЕДЕНИЕ
Алюминиевый сплав AA6061-T6 представляет собой дисперсионно-твердеющий Al–Mg–Si сплав из серии 6xxx, прошедший стандартную (Т6) обработку на твердый раствор с последующим искусственным старением. Сплав обычно применяется [1–3] в авиастроении (при производстве элементов крыла самолетов), а также, в судостроении (в конструкциях яхт), поскольку обладает довольно высокими механическими свойствами относительно своего легкого веса. Более того, сплав AA6061-T6 обладает удовлетворительными коррозионно-стойкими свойствами и хорошо поддается сварке. Отметим, что именно стандартная Т6 обработка улучшает свойства сплава 6061, причем в результате старения выделяется целый ряд метастабильных упрочняющих фаз [4–7].
Сварка трением с перемешиванием (СТП) широко применяется для соединения элементов деталей из сплава AA6061-T6 [1–3]. Вообще, зона сварки представляет собой хрупкую область конструкции, что ограничивает использование обычной сварки в случае экстремальных эксплуатационных условий. С микроструктурной точки зрения сварное соединение при СТП представляет собой три различные области: (i) зону исключительно теплового влияния (ЗТВ), (ii) зону термомеханического воздействия (ЗТМВ) и (iii) ядро шва (ЯШ). Заметьте, что на ЗТВ воздействует только тепло, тогда как на состоянии ЗТМВ сказывается и усилие рабочего пальца вращающегося инструмента, и скорость вращения заплечника. ЯШ является основной зоной, в которой происходит течение материала, вызываемое вращением рабочего пальца в теле соединяемого материала, испытывающего вдобавок фрикционно-индуцируемый разогрев. Эти три зоны сварного соединения значительно различаются по микроструктуре, как, впрочем, и по механическим свойствам. Эти различия существенным образом определяются условиями процесса сварки, а также размером зерна, особенностями зеренной структуры и характером растворения дисперсных упрочняющих выделений в объеме свариваемого материала [2, 8]. Поэтому микроструктура и свойства областей ЗТВ, ЗТМВ и ЯШ подлежат локальной и независимой друг от друга аттестации, для того чтобы иметь возможность оценить их индивидуальный вклад в состояние сварного соединения. Важность такой локальной аттестации материала для сравнения ограниченных областей (ЯШ, ЗТМВ и ЗТВ) становится вполне очевидной в том случае, когда для восстановления исходных свойств и микроструктуры сплава применяется послесварочная термическая обработка (ПСТО).
Для проведения локальной аттестации области сварки в целом, тестирование с помощью наноиндентирования является очень полезной методикой, позволяющей одновременно определять твердость и упругий модуль исследуемого материала. Эта методика недавно была использована для аттестации сварного соединения алюминиевого сплава AA6082-T6 сразу после сварки [9–11] в отсутствие ПСТО. Хотя эффект послесварочной термообработки был успешно изучен в замечательных работах [7, 12–15], методика наноиндентирования, к сожалению, не использовалась для анализа локальных механических свойств сплава AA6061 в каждой зоне сварного соединения в обоих случаях: после сварки и после ПСТО. Поэтому наша задача состоит в изучении влияния послесварочной термообработки на микроструктуру и локальные механические свойства различных зон сварного соединения, образовавшихся в результате СТП исследуемого сплава, с привлечением эффективной методики наноиндентирования.
МЕТОДИКА ЭКСПЕРИМЕНТА
Сварка и ПСТО
В качестве образцов брали пластины сплава AA6061-T6 (A96061 по классификации UNS, используемой в США Универсальной Системы Обозначений металлов и сплавов), размерами 300 × 150 × 9.6 мм. Химический состав сплава представлен в табл. 1. Процесс СТП применяли для осуществления стыкового соединения указанных пластин. Для обеспечения эффективного течения материала была выбрана насадка с рабочим пальцем конической формы, с поверхностной резьбой, ориентированной по ходу часовой стрелки. Процесс сварки начинался с приваривания пластин к сварочной подложке для их жесткой фиксации в процессе СТП. Вращающийся инструмент из износостойкого материала состоял из заплечника цилиндрической формы и рабочего пальца, который механически вводился в плотный стык пластин на заданную глубину так, что заплечник касался поверхности. Затем инструмент перемещался вперед вдоль линии стыка, формируя сварной шов. В области трения между поверхностями заплечника и свариваемых пластин вследствие вращения рабочей насадки (внешнего источника тепла) наблюдалось интенсивное тепловыделение. Внутренним источником поступления тепла являлась пластическая деформация материала, что обеспечивало размягчение последнего (без достижения точки его плавления), затем течение материала вокруг рабочего пальца и, в итоге, его осаждение в районе тыльной области рабочего пальца. У сварного шва при СТП выделяют две стороны. Это – наступающая сторона, которая определяется тем, что направление вращения инструмента совпадает с направлением сварки, и отступающая сторона, которая определяется тем, что вращательное движение рабочей насадки противоположно направлению ее поступательного движения. Рабочая насадка так ориентирована по отношению к свариваемым пластинам, что ее поступательное движение обеспечивает консолидацию материала сразу за ней, по мере переноса материала (в результате вращения насадки) с наступающей стороны на отступающую сторону сварного шва.
Таблица 1.
Химический состав сплава AA6061-T6 (% вес.)
Материал | Si | Mg | Cu | Fe | Mn | Cr | Zn | Ti | Al |
---|---|---|---|---|---|---|---|---|---|
AA6061-T6 | 0.54 | 0.96 | 0.27 | 0.43 | 0.05 | 0.04 | 0.02 | 0.02 | Ост. |
Для улучшения качества материала в области сварки рабочий инструмент был наклонен на 3° относительно нормали к плоскости свариваемых пластин. Процесс сопряжения осуществлялся с помощью обычной сварочной установки вертикального расположения, модифицированной под технологию СТП. Была спроектирована рабочая насадка, включающая в свой состав охлаждающую систему нового типа для обеспечения эффективного поддержания высокого давления и усилия рабочего пальца, необходимых для процесса СТП в случае большой толщины сварного соединения. Скорость вращения рабочего пальца составляла 1480 об./мин против часовой стрелки, а скорость продольной подачи инструмента – 89 мм/мин. Цикл термообработки проводили в соответствии с рекомендациями стандартных справочных руководств (напр., [16]). Такой цикл предусматривал выдержку материала в течение часа при 560°C с последующей закалкой в воду температурой 50°C. Далее материал подлежал искусственному старению при 170°C в течение 8 ч. Последним этапом была закалка сварного соединения в воду температурой 25°C.
Аттестация
На примере сварного шва можно наблюдать, как происходит сопряжение различных зон (различных микроструктур) материала, испытывающего воздействие СТП. Сварной шов и прилегающие к нему области материала имеют три типичные зоны ЗТВ, ЗТМВ и ЯШ и зону обычного базового металла (БМ). Эти четыре различные зоны формируются как результат нагрева и деформации материала в месте сварки и прилегающих к нему участках. Центральная зона (ЯШ) – зона непосредственно сварного шва, формирующаяся движущимся вращательно-поступательно рабочим пальцем, характеризуется наибольшей степенью деформации материала и является местом инициации рекристаллизации. По обеим сторонам от ЯШ располагается зона термомеханического воздействия, содержащая зерна исходного материала в деформированном состоянии. Третья по удаленности от ЯШ зона, испытывающая воздействие только тепла, выделяющегося в процессе СТП, по размеру примерно совпадает с ЗТВ, формирующейся в процессе традиционной сварки с плавлением. И, наконец, зона не испытавшего воздействия СТП основного исходного материала часто носит название зоны обычного базового металла. При этом ПСТО приводит к изменению как размера, так и формы этих различных зон, что предполагает необходимость соответствующей оценки микроструктуры.
Образцы были вырезаны перпендикулярно направлению сварки. Для оценки эволюции микроструктуры сварных образцов, на них были проведены исследования методами оптической металлографии (ОМ) и растровой электронно-микроскопии (РЭМ). При этом предварительно образцы были ошкурены на наждачной (кремний-карбидной) бумаге, отполированы с применением пасты алюминооксидного порошка 1-мкм дисперсности и прошли травление с применением реагента Келлера.
Классические измерения микротвердости по Виккерсу были проведены на поперечных сечениях, перпендикулярных линии сварного шва, через 1 мм при нагрузке 5 Н, действовавшей в течение 10 с. Значения нанотвердости и модуля упругости были измерены с помощью наноиндентора Hysitron© UBIs-I. В качестве индентора была использована алмазная пирамидка Берковича, обладавшая модулем упругости величиной 1140 ГПа и коэффициентом Пуассона (ν) 0.07. Для охвата всей области, испытавшей воздействие сваркой, включая ЗТВ и ЗТМВ на наступающей и отступающей сторонах, а также зону ЯШ, измерения соответствующих свойств проводились на середине толщины сварного соединения, приблизительно на расстоянии 5 мм от верхней поверхности образца. Максимум приложенной нагрузки не превышал 2.5 мН, при продолжительности нагрузки и разгрузки 30 с в соответствии с предписаниями ASM стандарта. Время экспозиции составляло 10 с. С целью обеспечения воспроизводимости результатов наноиндентирования и для выявления возможных неоднородностей в области сварки в каждой из характерных зон было проведено по меньшей мере 16 измерений. Значения нанотвердости HIT и модуля упругости EIT рассчитывались по формулам
(1)
$\left\{ \begin{gathered} {{H}_{{IT}}} = \frac{P}{{{{A}_{C}}}}{\text{ ,}} \hfill \\ {{E}_{R}} = \frac{{\sqrt {\pi } }}{2}\frac{S}{{\sqrt {{{A}_{C}}} }}{\text{,}}\,\,г д е \,\,\,\frac{1}{{{{E}_{R}}}} = \frac{{1 - {{{\nu }}^{2}}}}{{{{E}_{{IT}}}}} + \frac{{1 - \nu _{{\text{i}}}^{2}}}{{{{E}_{{\text{i}}}}}}{\text{,}} \hfill \\ \end{gathered} \right.$(2)
$\begin{gathered} {{A}_{C}} = {{C}_{0}}h_{c}^{2}2 + {{C}_{1}}h_{c}^{1} + {{C}_{2}}h_{c}^{{{1 \mathord{\left/ {\vphantom {1 2}} \right. \kern-0em} 2}}} + \\ + \,\,{{C}_{3}}h_{c}^{{{1 \mathord{\left/ {\vphantom {1 4}} \right. \kern-0em} 4}}} + ... + {{C}_{8}}h_{c}^{{{1 \mathord{\left/ {\vphantom {1 {128}}} \right. \kern-0em} {128}}}}, \\ \end{gathered} $(3)
$\left\{ \begin{gathered} е с л и \frac{{{{h}_{f}}}}{{{{h}_{m}}}} > 0.83\,\,\,\,(в с л у ч а е н а п л ы в а м а т е р и а л а ),\,\,\,\,{{h}_{c}} = 1.2\left( {{{h}_{m}} - \frac{{{{P}_{m}}}}{S}} \right); \hfill \\ е с л и \frac{{{{h}_{f}}}}{{{{h}_{m}}}} < 0.83\,\,\,\,(в с л у ч а е у с а д к и м а т е р и а л а в о к р у г о т п е ч а т к а ),\,\,\,\,{{h}_{c}} = {{h}_{m}} - \tilde {\varepsilon }\frac{{{{P}_{m}}}}{S}, \hfill \\ \end{gathered} \right.$РЕЗУЛЬТАТЫ И ОБСУЖДЕНИЕ
Эволюция микроструктуры
На рис. 1 представлена микроструктура различных зон сварного образца сплава AA6061-T6. Эти микроизображения демонстрируют, как меняется размер зерна и выделений второй фазы от одной зоны сварного шва к другой. На рис. 1a показана микроструктура базового металла, включая границы зерен и выделения, тогда как на рис. 1б представлены мелкие равноосные зерна и фрагментированные выделения, локализованные в ЯШ зоне, испытавшей сильную деформацию [2]. В ЗТВ (рис. 1в), размер зерна практически не отличается от размера зерна в базовом металле. Вместе с этим, в ЗТВ обнаруживается рост выделений второй фазы. Изображение ЗТМВ с вытянутыми зернами, представленное на рис. 1г, иллюстрирует переходную структуру между ЯШ и ЗТВ. Фактически, рис. 1 объясняет те изменения структуры от зоны к зоне, которые в настоящем исследовании оцениваются микротвердостью и наноиндентированием.
Анализ по результатам наноиндентирования
Измерения микротвердости классическим методом были проведены на твердомере Виккерса, посредством нагружения индентора максимальной нагрузкой в 5 Н, поэтому было принято обозначение HV0.5. Заметим, что значение классической твердости по Виккерсу обычно дается в единицах кГс/мм2. На рис. 2 представлены результаты картирования микротвердости по Виккерсу в материале после СТП (рис. 2a), а также показана та же область материала после его ПСТО (рис. 2б). Как можно видеть на рис. 2a, в зоне ЯШ микротвердость меняется мало, максимальное значение в этой области составляло 71 HV0.5. Вместе с тем наименьшие значения микротвердости были получены в ЗТМВ. Значения снижаются по мере удаления от осевой линии вплоть до границы зон ЗТМВ и ЗТВ, причем на самой ЗТМВ/ЗТВ границе микротвердость достигает минимума в 59 HV0.5 в ЗТМВ с отступающей стороны шва. В ЗТВ значения микротвердости возрастают по мере приближения к зоне базового металла, т.е. не испытавшего воздействия СТП, для которой микротвердость ~110 HV0.5. Разница максимального и минимального значений микротвердости по Виккерсу в образце сразу после СТП составляет 40%. Это можно объяснить, во-первых, тем, что AA6061–T6 является сплавом, поддающимся термической обработке, а, во-вторых, тем, что ПСТО сварного образца запускает конкурирующие процессы выделения и рекристаллизации. Хорнбоген с соавторами в [20] доказал, что рекристаллизация обычно развивается при более высокой температуре и предшествует процессам выделения. Тем самым, процесс выделения оказывается предпочтительным механизмом при более низких температурах. Известно, что при ПСТО сплава AA6061-T6, рекристаллизация в нем в основном начинается при температурах близким к температуре обработки на твердый раствор. При этом процессы выделения в области температур дисперсионного твердения развиваются и завершаются независимо от рекристаллизации. С другой стороны, авторы [21] сообщили, что сплав AA6061, испытывавший деформацию при более низкой температуре, продемонстрировал более низкие значения твердости после старения, в то время как основная причина упрочнения сплава AA6061-T6 связана с размером и пространственным распределением выделений. Из двух зон сварного шва, которые испытывают деформацию, для ЗТМВ характерна наименьшая температура старения, восстанавливающая твердость и инициирующая выделение. Поэтому в образце после ПСТО (рис. 2б), минимум микротвердости демонстрирует ЗТМВ (95 HV0.5), а микротвердость зоны ЯШ увеличивается до значения микротвердости базового металла.
Для того чтобы более точно интерпретировать изменение твердости по области сварного соединения, было проведено наноиндентирование материала вдоль осевой линии поперечного сечения двух образцов – сразу после СТП и после ПСТО. Кривые “нагрузка–смещение” P(h) были сняты для каждой из зон. На рис. 3 можно видеть, как сказывается ПСТО на виде P(h) кривых для зоны ЯШ (рис. 3a) и ЗТМВ (рис. 3б).
Рис. 3.
Кривые “нагружение–смещение” P(h), отвечающие зонам (a) ЯШ и (б) ЗТМВ до и после ПСТО, в сравнении с кривыми для базового металла.
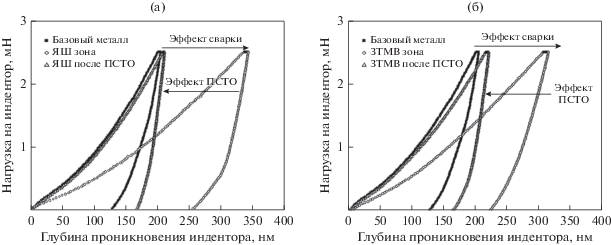
Для установления надежных значений механических свойств при наноиндентировании, наиболее важной задачей является получение с хорошей точностью значения площади поверхности контакта между материалом и пирамидкой индентора. Это часто достигается посредством калибровки на образце сплавленного кварца, что позволяет установить значения подгоночных коэффициентов, фигурирующих в выражении (2) для площади контактной поверхности AC. Вплоть до недавнего времени приборы для наноиндентирования, поставляемые производителем, были сконструированы на основе методологического подхода Оливера и Фарра [17]. Однако даже если конкретные авторы в своих работах и указывают явно, что обычные соотношения имеют смысл только для случаев усадки материала по периметру отпечатка индентора, в действительности в выпускаемых промышленностью приборах для наноиндентирования и нет какой-либо методологической основы для расчета АС в случае наплыва материала по периметру отпечатка. Следовательно, необходима новая методология для отбора адекватных параметров расчета, как приведенного упругого модуля, так и нанотвердости в случае наплыва материала. Все это означает, что перед расчетом механических свойств необходимо установить, какая мода деформации реализуется при индентировании материала. Имея в виду это соображение, наноиндентирование в ЗТМВ производилось при помощи пирамидки с формой, характерной для индентора Берковича. Пример отпечатка индентора приведен на рис. 4. Четко видно, что в случае исследуемого материала реализуется деформационная мода “наплыв материала”. Следует заметить, что для всех остальных зон сварного шва была характерна та же мода индентационной деформации. Больше информации о модах деформации типа “наплыв материала” или его “усадка” вокруг отпечатка индентора можно почерпнуть в [22–25]. Связь между механическими свойствами, такими как ползучесть, предел прочности на растяжение, прочность на сжатие, твердость, остаточные напряжения и модуль упругости, с одной стороны, и явлениями наплыва или усадки материала вокруг отпечатка индентора, с другой стороны, являлась предметом обсуждения в многочисленных работах [22, 23] в связи с деформационной модой. Тенденция сплава AA6061–T6 к низкому деформационному упрочнению выразилась в формировании наплыва материала согласно представлениям модели Оливера–Фарра [26]. Оказалось, что в случае сплава AA6061–T6 явления “наплыва материала” избежать невозможно.
Рис. 4.
(a) Топография поверхности и (б) поперечное сечение “наплыва материала”, наблюдаемого в ЗТМВ с отступающей стороны сварного шва.
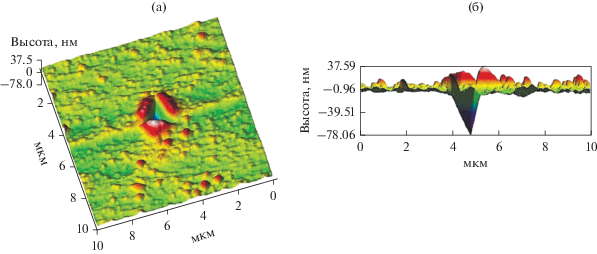
Перед тем как далее обсуждать эффекты “наплыва” или “усадки” материала, необходимо сказать, что все наблюдаемые элементы микроструктуры, такие как зерна и выделения (рис. 1б и рис. 1в), оказываются микронного масштаба, тогда как эффекты наноиндентирования находятся в диапазоне 100–200 нм (рис. 4). Любое взаимодействие пирамидки Берковича с очень твердыми выделениями приводит к возникновению ошибки в измерении нанотвердости материала и непригодности такого результата. ПСТО приводит к однородному распределению выделений по объему сварного соединения (см. рис. 1a) [4–7] и, тем самым, к выравниванию поверхностных напряжений, что сказывается на нанотвердости материала и его реакции на наноиндентирование. Присутствие в объеме материала как выделений, так и границ зерен не могло сказаться на точности и качестве наших результатов.
Для определения значений нанотвердости и упругого модуля по уравнениям (1), предварительно необходимо рассчитать с учетом (3) глубину проникновения индентора, как было предложено в [27]. Это становится возможным при наличии экспериментальных данных по наноиндентированию, а именно, максимального проникновения индентора в материал, hm, нагрузки на индентор, Pm, и тангенса угла наклона ветви разгружения кривой P(h)–S. Проблема, однако, состоит в расчете площади поверхности контакта между пирамидкой и материалом, которая предполагает знание различной глубины (h) проникновения индентора в материал, что было предварительно рассчитано для случая усадки материала по периметру отпечатка индентора. В области значений h больших, чем приблизительно 150 нм, вместо сложной функции модели Оливера–Фарра АС (h) [26] упрощенная функция [18] способна адекватно представлять соответствующие изменения поверхности контакта (ПК):
где hb – линейный размер притупления пирамидки индентора, как он определен в [28]. Для его определения мы предлагаем воспользоваться графиком корня квадратного из инструментально измеряемой площади ПК как функции глубины проникновения индентора в материал в случае усадки материала по периметру отпечатка индентора. На рис. 5 показаны все экспериментальные точки для каждой из зон сварного шва. Подгонка экспериментальных данных дала следующий линейный по hс результат аппроксимации:Рис. 5.
Зависимость “Поверхность контакта от глубины проникновения индентора” по итогам всех испытаний (наноиндентирование).
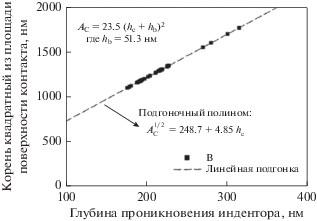
Следует отметить, что константа 23.5 отличается от теоретической величины 24.5 (точное значение π × tg270.3°), фигурирующей в выражении для ПК, образуемой “идеальной” пирамидкой индентора – см. (4). Значение 23.5 говорит об отклонении угла при вершине пирамидки от стандартного [29, 30]. Для использованной нами пирамидки Берковича, такое отклонение угла составляет 0.4°. Сопоставляя между собой выражения (4) и (5), мы пришли к следующему выражению для площади ПК, пригодному в нашем случае для расчета нанотвердости и модуля упругости по уравнениям (1), причем расчет глубины проникновения индентора в материал отвечает здесь моде деформации “наплыв материала” вокруг отпечатка индентора.
(6)
${{A}_{C}} = 23.5{{\left( {{{h}_{c}} + {{h}_{b}}} \right)}^{2}},\,\,г д е \,\,{{h}_{b}} = 51.3\,\,н м .$В дополнение, с целью иметь возможность сравнивать значения твердости, получаемые в рамках классического и наноиндентационного методов ее измерения, расчет по HIT был отклонен, поскольку площадь ПК, принимаемая при расчете HIT, есть ни что иное как соответствующее прогнозируемое значение ПК при конкретной глубине проникновения индентора в материал. Для непротиворечивого сопоставления результатов измерения твердости методами Виккерса и наноиндентирования, в качестве базовой была выбрана твердость по Мартенсу, поскольку в этом случае ПК имеет одно и то же определение в двух интересующих нас случаях, а именно, ПК по Мартенсу определяется при максимальном значении глубины проникновения индентора. Использованная в данной работе формула для твердости по Мартенсу имеет вид:
(7)
${{H}_{M}} = \frac{P}{{{{A}_{m}}}},\,\,г д е \,\,{{A}_{m}} = 25.35{{\left( {{{h}_{m}} + 51.3} \right)}^{2}},$Основываясь на поправке, требуемой для расчета твердости по Мартенсу, учитывающей формирование “наплыва материала” вокруг отпечатка индентора, мы вычислили инструментальную нанотвердость по формуле (7). На рис. 6 представлены твердость по Мартенсу (рис. 6a) и модуль упругости (рис. 6б) как функции расстояния от осевой линии сварного шва. На рис. 6a показаны изменения твердости по Мартенсу и упругого модуля сварного образца сразу после СТП и эволюция их значений после ПСТО. Наименьшее значение HM было получено в ЗТМВ на отступающей стороне шва сразу после СТП. Напротив, максимальное значение около 1.5 ГПa было установлено для зоны базового металла. Однородность профиля твердости после ПСТО образца является главным отличием от распределения твердости после СТП. Другой важный момент, который следует из обсуждаемого рис. 6а, состоит в изменении HM в зоне ЯШ: после СТП твердость равна 0.65 ГПa, но после ПСТО образца повышается до 1.55 ГПа. Твердость по Мартенсу имеет низкие значения в зонах ЯШ, ЗТВ и ЗТМВ, в которых при СТП протекают процессы растворения и перестаривания. Хотя HM после ПСТО сварного образца демонстрировала заметное повышение и более высокую степень однородности, мы не наблюдали ее 100% восстановления в ЗТМВ.
Рис. 6.
Распределение значений (a) твердости по Мартенсу и (б) модуля упругости по поперечному сечению сварного соединения. Значения полученны методом наноиндентирования на образцах после СТП и (СТП + ПСТО).
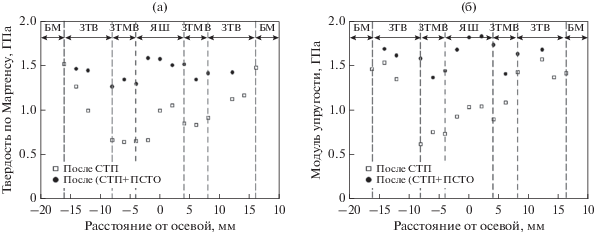
Что касается изменений величины упругого модуля, его наименьшее значение можно было наблюдать в ЗТМВ сварного соединения (рис. 6б). СТП может привести к возникновению остаточных напряжений в областях материала, соседствующих с областью непосредственного воздействия сварки. Присутствие напряжений в этой зоне говорит о ее значительно деформированном состоянии. Влияние предварительной деформации на величину модуля упругости было доказано Абдель-Каримом в [30]. Неоднородное распределение значения модуля упругости по сечению шва изменялось с восстановлением распределения выделений и с релаксацией остаточных напряжений в процессе ПСТО. Отсутствие полного восстановления классической микротвердости по Виккерсу (см. рис. 2б), HM, измеренной методами наноиндентации (рис. 6a), и упругого модуля, измеренного в экспериментах по наноиндентированию (рис. 6б), в ЗТМВ образца, прошедшего ПСТО, явилось результатом менее высокой температуры нагрева в ЗТМВ во время СТП, чем в зоне ЯШ. Другими словами, величина температуры деформации может сказаться на твердости (зависящей в свою очередь от процессов выделения) после проведения ПСТО сплава AA6061–T6 [21]. Проведение нескольких предварительных испытаний и сравнение их результатов показало, что почти в 41% случаев имело место несовпадение величин упругого модуля Е, измеренных в экспериментах на растяжение (дающих “интегральное” значение Е) и методом наноиндентирования сварного образца (дающих локальное значение Е). При этом величина упругого модуля, измеренная методом наноиндентирования, составила для ЗТМВ 28 ГПa, а испытания на растяжение дали для Е значение 70 ГПа. Вместе с этим несовпадение значений Е в случае образца после ПСТО для области разрушения составило около 5%.
На рис. 7а и 7б проведено сравнение значений микротвердости по Виккерсу HV и твердости по Мартенсу HM в одних и тех же точках поверхности разных зон сварного соединения в случаях образцов после СТП и после (СТП + ПСТО). Эти две серии измерений и ранее не всегда давали совпадение значений HV и HM для одних и тех же точек сварных образцов [31]. Однако в этой работе результаты, полученные в зонах с пониженной твердостью, относительно неплохо согласуются между собой. Создается впечатление, что более высокие значения HM в сравнении с HV обусловлены в большинстве случаев более высокими упругими свойствами зон с повышенной твердостью, что может приводить к уменьшению Am [17]. Другими причинами различия значений HV и HM в одних и тех же точках зон сварного образца с повышенной твердостью являются более точное определение величины прогнозируемой площади поверхности контакта при наноиндентировании и более аккуратная оценка индентационного эффекта (определяющего моду деформации).
ВЫВОДЫ
Для данного исследования было проведено стыковое соединение сваркой трением с перемешиванием двух пластин алюминиевого сплава AA6061-T6. Влияние обработки, способствующей получению твердого раствора, с последующим искусственным старением дисперсионно-твердеющего материала на его модуль упругости было изучено как классическим методом микротвердости, так и наноиндентированием сварных образцов сразу после СТП и после ПСТО. Получены следующие результаты:
1. Эффект “наплыва материала” (вокруг отпечатка индентора) наблюдался для всех зон сварного соединения как до, так и после ПСТО сварного образца. Это наблюдение привело к необходимости пересчитать данные по наноиндентированию с целью учета моды индентационной деформации. Для этого понадобилась оценка притупления пирамидки индентора.
2. Вследствие растворения выделений, мы наблюдали существенное снижение твердости в ЯШ и ЗТМВ. ЗТМВ в СТП образце продемонстрировала наименьшие значения твердости.
3. Снижение величины модуля упругости в различных зонах материала сварного соединения было объяснено с привлечением представлений о растворении β-Mg2Si выделений и перестаривании (СТП + ПСТО) образца.
4. ПСТО позволила восстановить твердость базового металла почти во всех областях сварного соединения.
5. HM и HV продемонстрировали приемлемое взаимное совпадение в зонах сварного соединения с невысокими значениями твердости, тогда как в области с большими значениями твердости величины HM оказались более достоверными.
Авторы благодарны за финансовую поддержку данной исследовательской работы со стороны Университета Путра Малайзии.
Список литературы
Rodrigues D.M., Loureiro A., Leitao C., Leal R.M., Chaparro B.M., Vilaca P. Influence of friction stir welding parameters on the microstructural and mechanical properties of AA 6016-T4 thin welds // Mater. Des. 2009. V. 30. P. 1913–1921.
Mishra R.S., Ma Z.Y. Friction stir welding and processing // Mater. Sci. Eng. R. 200. V. 550. P. 1–78.
Lucas G. Aluminum structural applications // Adv. Mater. Process. 1996. V. 149. P. 29–30.
Maisonnette D., Suery M., Neliasa D., Chaudet P., Epicier T. Effects of heat treatments on the microstructure and mechanical properties of a 6061 aluminium alloy // Mater. Sci. Eng. A. 2011. V. 528. P. 2718–2724.
Gupta A.K., Lloyd D.J., Court S.A. Precipitation hardening processes in an Al–0.4% Mg–1.3% Si–0.25% Fe Aluminum alloy // Mater. Sci. Eng. A. 2001. V. 301. P. 140–146.
Fadaeifard F., Matori Ka., Garavi F., Al-Falahi M., Vahedi Sarrigani G. Effect of post weld heat treatment on microstructure and mechanical properties of gas tungsten arc welded AA6061-T6 alloy // Trans. Nonferrous Met. Soc. China. 2016. V. 26. P. 3102–3114.
Myhr O.R., Grong O., Fjar H.G., Marioara C.D. Modelling of the microstructure and strength evolution in Al–Mg–Si alloys during multistage thermal processing // Acta Mater. 2004. V. 52. P. 4997–5008.
Guerra M., Schmidt C., McClure J.C., Murr L.E., Nunes A.C. Flow patterns during friction stir welding // Mater. Charact. 2002. V. 49. P. 95–101.
Koumoulos E.P., Charitidis C.A., Daniolos N.M., Pantelis D.I. Nanomechanical properties of friction stir welded AA6082-T6 aluminum alloy // Mater. Sci. Eng. B. 2011. V. 176. P. 1585–1589.
Charitidis C.A., Dragatogiannis D.A., Koumoulos E.P., Kartsonakis I.A. Residual stress and deformation mechanism of friction stir welded aluminum alloys by nanoindentation // Mater. Sci. Eng. A. 2012. V. 540. P. 226–234.
Cabibbo M., Forcellese A., El-Mehtedi M., Simoncini M. Double side friction stir welding of AA6082 sheets: Microstructure and nanoindentation characterization // Mater. Sci. Eng. A. 2014. V. 590. P. 209–217.
Marioara C.D., Andersen S.J., Stene T.N., Hasting H.S., Walmsley J., Van Helvoort A.T.J., Holmestad R. The effect of Cu on precipitation in Al–Mg–Si alloys // Philos. Mag. 2007. V. 87. P. 3385–3413.
Fahimpour V., Sadrnezhaad S.K., Karimzadeh F. Microstructure and mechanical property change during FSW and GTAW of Al6061 alloy // Metall. Mater. Trans. A. 2013. V. 44A. P. 2187–2195.
Krishnan K.N. The effect of post weld heat treatment on the properties of 6061 friction stir welded joints // J. Mater. Sci. 2002. V. 37. P. 473–480.
Elangovan K., Balasubramanian V. Influences of post-weld heat treatment on tensile properties of friction stir-welded AA6061 aluminum alloy joints // Mater. Charact. 2008. V. 59. P. 1168–1177.
Totten George E. ASM Handbook Volume 4E: Heat Treating of Nonferrous Alloys. ASM International, California, 2016.
Oliver W.C., Pharr G.M. An improved technique for determining hardness and elastic modulus using load and displacement sensing indentation experiments // J. Mater. Res. 1992. V. 7. P. 1564–1583.
Chicot D., Yetna Njock M., Puchi-Cabrera E.S., Iost A., Staia M.H., Louis G., Bouscarrat G., Aumaitre R. A contact area function for Berkovich nanoindentation: Application to hardness determination of a TiHfCN thin film // Thin Solid Films. 2014. V. 558. P. 259–266.
Yetna Njock M., Chicot D., Ndjaka J.M., Lesage J., Decoopman X., Roudet F., Mejias A. A criterion to identify sinking-in and piling-up in indentation of materials // Int. J. Mech. Sci. 2015. V. 90. P. 145–150.
Hornbogen E., Koster U. Recrystallization of metallic materials / Ed. by Haessner F. and Riederer Dr. Verlag, Stuttgart, 1978.
Niranjani V.L., Hari Kumar K.C., Subramanya Sarma V. Development of high strength Al–Mg–Si AA6061 alloy through cold rolling and ageing// Mater. Sci. Eng. A. 2009. V. 515. P. 169–174.
Lucca D.A., Herrmann K., Klopfstein M.J. Nanoindentation: Measuring methods and applications // CIRP Annals – Manuf. Technol. 2010. V. 803. P. 803–819.
Fischer-Cripps C.A. Critical review of analysis and interpretation of nanoindentation test data // Surf. Coat. Tech. 2006. V. 200. P. 4153–4165.
Li X., Bhushan B. Fatigue studies of nanoscale structures for MEMS/NEMS applications using nanoindentation techniques // Surf. Coat. Technol. 2002. V. 30. P. 163–164.
Mesbah M., Fadaeifard F., Karimzadeh A., Nasiri-Tabrizi B., Rafieerad A., Faraji G., Bushroa A.R. Nano-mechanical properties and microstructure of UFG brass tubes processed by parallel tubular channel angular pressing // Met. Mater. Int. 2016. V. 22. P. 1098–1107.
Oliver W.C., Pharr G.M. Measurement of hardness and elastic modulus by instrumented indentation: Advances in understanding and refinements to methodology // J. Mater. Res. 2004. V. 19. P. 3–20.
Loubet J.L., Bauer M., Tonck A., Bec S., Gauthier-Manuel B. Nanoindentation with a Surface Force Apparatus // in Mechanical Properties and Deformation Behavior of Materials Having Ultra-Fine Microstructures / Ed. by Nastasi M., Parkin D.M., Gleiter H. Springer, Dordrecht, 1993.
Chicot D. Hardness length-scale factor to model nano-and micro-indentation size effects // Mater. Sci. Eng. A. 2009. V. 499. P. 454–461.
Charleux L., Keryvin V., Nivard M., Guin J.P., Sanglebœuf J.C., Yokoyama Y. A method for measuring the contact area in instrumented indentation testing by tip scanning probe microscopy imaging // Acta Mater. 2014. V. 70. P. 249–258.
Gong J., Miao H., Peng Z. On the contact area for nanoindentation tests with berkovich indenter: case study on soda-lime glass // Mater. Lett. 2004. V. 58. P. 1349–1353.
Sawa T. Correlation between Nanoindentation Test Result and Vickers Hardness // IMECO TC3, TC5 and TC22 Conf., Metrology in Modern Context, 2010. P. 171–174.
Дополнительные материалы отсутствуют.
Инструменты
Физика металлов и металловедение