Физика металлов и металловедение, 2019, T. 120, № 7, стр. 764-770
Структура и свойства антифрикционных покрытий Cu, Cu–С и DLC
Ф. В. Кирюханцев-Корнеев a, *, А. В. Бондарев a
a Национальный исследовательский технологический университет “МИСиС”
119049 Москва, Ленинский пр., 4, Россия
* E-mail: kiruhancev-korneev@yandex.ru
Поступила в редакцию 30.05.2018
После доработки 16.10.2018
Принята к публикации 03.12.2018
Аннотация
Методом магнетронного напыления получены покрытия в системе Cu–C с различным содержанием углерода, а также однокомпонентные покрытия Cu и C. Структура покрытий исследована с использованием растровой электронной микроскопии, энергодисперсионного и рентгенофазового анализа, рамановской спектроскопии и оптической эмиссионной спектроскопии тлеющего разряда. Механические и трибологические свойства определены с помощью наноиндентирования и испытаний по схеме “стержень–диск”. Установлено, что при введении углерода в состав покрытий на основе меди наблюдается уплотнение структуры, уменьшение размера кристаллитов с 35 до 21 нм. Обнаружено, что по характеристикам покрытия Cu–C превосходили покрытия Cu. Полученные по лучшим режимам покрытия Cu–C обладали твердостью >1.5 ГПа и коэффициентом трения ~0.19.
ВВЕДЕНИЕ
Одной из задач современного материаловедения является получение антифрикционных покрытий, обладающих сочетанием высокой твердости и износостойкости с низким коэффициентом трения, для использования в различных узлах трения [1]. В последние годы значительное внимание уделяется получению покрытий на основе меди [2, 3], что связано с ее относительно низким коэффициентом трения и высокой теплопроводностью, необходимой для эффективного отвода тепла из зоны трения. Кроме того, медь обладает высоким коэффициентом распыления, благодаря чему растет скорость осаждения покрытий, и уменьшаются затраты при их нанесении [4]. Повышения трибологических характеристик меди можно добиться путем введения в нее слоистой твердой смазки, например, графита. Для композиционных покрытий на основе латуни и бронзы с ростом содержания графита было установлено монотонное уменьшение коэффициента трения и увеличение приведенного износа [2, 3]. Ранее исследованные покрытия Cu–C были получены с применением методов катодно-дугового испарения [5], химического осаждения с активацией электронно-циклотронным резонансным разрядом [6], термоионного вакуумного дугового испарения [7], магнетронного распыления [4, 8, 9]. Метод магнетронного распыления наиболее перспективен, поскольку обеспечивает минимальную шероховатость и дефектность [10], высокую плотность и адгезию покрытий [10, 11], позволяет минимизировать нагрев подложки [12], а также легко управлять характеристиками осаждаемого материала [13, 14]. В настоящей работе покрытия в системе Cu–C были получены методом магнетронного распыления одинарной мозаичной мишени при дистанции, обеспечивающей равномерность атомарного потока [15]. Расположение сегментов варьировалось по аналогии с работой [16], посвященной покрытиям Cu–B. Цель данной работы – исследование структуры и свойств антифрикционных покрытий Cu–C, а также образцов однокомпонентных покрытий, нанесенных из С- и Cu-мишеней.
МЕТОДИКА ЭКСПЕРИМЕНТА
Покрытия Cu–C наносились методом магнетронного напыления. В качестве катода использовали литую медную мишень М-1 (покрытия Cu), мишень из углерода марки МПГ-6 (покрытия DLC), а также мозаичные мишени (покрытия Cu–C). Мозаичные мишени состояли из спеченных порошковых сегментов Cu и сегментов C, вырезанных из заготовки МПГ-6. Использовались следующие наборы сегментов 9C/16Cu, 13C/12Cu и 15C/10Cu по аналогии с [16] (табл. 1).
Таблица 1.
Параметры осаждения и содержание углерода в покрытиях
Покрытие | Мишень | P, Па | U, В | I, А | t, мин | С, ат. % |
---|---|---|---|---|---|---|
1 | Cu | 0.2 | 400 | 1.0 | 30 | 0 |
2 | 9С/16Сu | 0.1 | 500 | 0.4 | 30 | 1 |
3 | 13C/12Cu | 0.2 | 500 | 0.5 | 30 | 7 |
4 | 13C/12Cu | 0.2 | 550 | 0.4 | 45 | 4 |
5 | 15С/10Cu | 0.1 | 500 | 0.3 | 30 | 6 |
6 | 15С/10Cu | 0.1 | 700 | 0.6 | 45 | 11 |
7 | 15С/10Cu | 0.2 | 600 | 0.3 | 45 | 10 |
8 | C | 0.2 | 650 | 0.9 | 60 | 100 |
Для получения формовок Cu сегментов использовался гидравлический пресс марки 2ПГ-125. Прессование велось в квадратной стальной пресс-форме с линейными размерами 23 × 23 мм при давлении 2 т/см2. Затем проводилось спекание полученных формовок в графитовой засыпке (ГОСТ 7657-84) в муфельной печи сопротивления SNOL-7.2/1200. Спекание проходило при температуре 850°С в течение 1 ч.
В качестве подложек для осаждения покрытий использовали диски из стали 12Х18Н10Т и пластины монокристаллического кремния КЭФ-4.5 (100). Подложки подвергали ультразвуковой очистке в среде изопропанола в течение 3 мин. Очистку подложек в вакууме осуществляли путем их нагрева до температуры 300°С и травления ионами Ar+ с энергией 1.5–2 кэВ в течение 5 мин. Параметры осаждения покрытий представлены в табл. 1.
При нанесении покрытий давление рабочего газа (Ar) в рабочей камере составляло 0.1–0.2 Па. Напыление проводили при токе от 0.3 до 1 А и напряжении 0.4–0.7 кВ. Дистанция от мишени до подложки – 80 мм. Время осаждения составляло 30–60 мин и выбиралось, исходя из скорости распыления так, чтобы получить близкие по толщине покрытия. Температура подложек поддерживалась на уровне 300°C.
Химический состав покрытий определяли методом оптической эмиссионной спектроскопии тлеющего разряда (ОЭСТР) [17] с использованием установки PROFILER-2 (Horiba Jobin Yvon). Структуру покрытий исследовали с помощью сканирующего электронного микроскопа Hitachi S3400. Съемку проводили во вторичных электронах при различных ускоряющих напряжениях. Фазовый состав покрытий определяли с использованием рентгеновского дифрактометра Bruker D8 с монохроматизированным CuKα-излучением. Углеродсодержащие образцы исследовались методом Рамановской спектроскопии на приборе LabRAM HR 800 (Horiba Jobin Yvon) с использованием лазера c длиной волны 514 нм. Механические свойства покрытий определяли с помощью прецизионного нанотвердомера Nano-Hardness Tester (CSM Instruments). Испытания на износостойкость покрытий проводили на автоматизированной машине трения Tribometer (CSM Instruments), работающей по схеме “стержень-диск”. Испытания проводили с использованием в качестве контртела шарика из Al2O3 диаметром 6 мм, нагрузка составляла 1Н, линейная скорость 10 см/c. Канавки износа исследовали с помощью оптического профилометра Wyko-1100NT фирмы Veeco.
РЕЗУЛЬТАТЫ И ОБСУЖДЕНИЕ
Типичный профиль распределения химических элементов по глубине в покрытиях Cu–C представлен на рис. 1. Результаты ОЭСТР показали, что основные компоненты в покрытиях распределены равномерно по толщине, а увеличение содержания C в мишени приводит к росту его концентрации в покрытиях.
В табл. 1 представлены результаты определения концентрации углерода, полученные путем усреднения его концентрации по толщине покрытий. Стоит отметить повышенное содержание кислорода в некоторых покрытиях. Это может быть связано с несколькими причинами. Присутствие примеси кислорода в DLC связано с тем, что углеродная мишень имеет низкий коэффициент распыления, в результате происходит накапливание в покрытии остаточного кислорода из вакуумной камеры установки. С этим же эффектом связано более высокое содержание O во всех углеродсодержащих покрытиях. Также возможно проникновение его атомов из материала сегментов, полученных порошковой технологией.
Микрофотографии покрытий Cu, Cu–C и DLC представлены на рис. 2. Видно, что Cu-покрытие имеет рыхлую пористую структуру. Формирование рыхлой высокодефектной структуры в Cu-покрытиях может быть связано с перегревом поверхностных слоев мишени и формированием капельной фазы в потоке осаждаемого вещества.
Плотность покрытий Cu при введении углерода значительно возросла. Это может быть обусловлено уменьшением доли капельной и осколочной фазы в потоке осаждаемого вещества. Кроме того, углерод, который не имеет растворимости в меди, препятствует формированию крупных кристаллитов Cu, осаждаясь по границам зерен меди и препятствуя их коалесценции. Наиболее плотной структурой без видимых дефектов обладает покрытие DLC.
Рентгеновские дифрактограммы покрытий 1 (Cu) и 4 (Cu–4C) представлены на рис. 3. Для обоих образцов были обнаружены линии, соответствующие ГЦК-фазе Сu и кремниевой подложке. В случае Cu–C присутствовал также пик в положении 2Ө = 22 град, который соответствует аморфным прослойкам на основе углерода.
Из рис. 3 видно, что введение C приводит к уширению дифракционных линий, что является следствием уменьшения размера кристаллитов. Периоды решетки a и размеры кристаллитов D, рассчитанные по данным РФА, представлены в табл. 2. Близость значений периодов решетки покрытий 1 (Cu) и 4 (Cu–4C), а также их незначительное отличие от периода решетки объемной меди (0.3615 нм), свидетельствует о том, что атомы углерода формируют отдельную аморфную фазу. Средний размер кристаллитов, определенный по уширению линии (111) с помощью формулы Шеррера, в Cu-покрытии составил 35 нм, а в Cu–4C – 21 нм. Это подтверждает тот факт, что измельчение структуры покрытий связано с прерыванием роста зерен меди аморфными прослойками углерода.
Таблица 2.
Результаты рентгенофазового анализа
№ образца | Величина | Cu (111) | Cu (200) | Cu (220) | Cu (311) |
---|---|---|---|---|---|
1 (Cu) | a, нм | 0.3619 | 0.3614 | 0.3619 | 0.3616 |
D, нм | 35 | 24 | 22 | 19 | |
4 (Cu–4C) | a, нм | 0.3611 | 0.3628 | 0.3619 | 0.3619 |
D, нм | 21 | 11 | 12 | 7 |
Наиболее эффективным методом изучения структуры углеродсодержащих материалов является Рамановская спектроскопия. Спектры покрытий 8 (DLC) и 3 (Cu–7C) представлены на рис. 4. Полученные спектры являются типичными для углерода. В них наблюдаются 2 полосы: G с частотой максимума 1560–1600 см–1 и D с частотой максимума 1350–1420 см–1. Обе полосы обусловлены углеродными sp2-связями.
В табл. 3 приведены частоты максимумов полос D и G, а также отношение интенсивностей в максимумах. Положение максимумов полос было определено с помощью разложения экспериментального рамановского спектра на гауссовы компоненты.
Таблица 3.
Результаты Рамановской спектроскопии покрытий DLC и Cu–C
Покрытие | G, см–1 | D, см–1 | ID/IG |
---|---|---|---|
8 (DLC) | 1376 | 1579 | 1.25 |
3 (Cu–7C) | 1391 | 1583 | 0.91 |
Сравнение части рамановского спектра образца 3 (Cu–7C) в низкочастотной области со спектрами CuO и Cu2O показало, что оба оксида присутствуют в покрытии. Сложность идентификации оксидных фаз методом рентгенофазового анализа, скорее всего, связана с их малой долей в покрытии и малым размером зерен. Кроме того, высокая химическая активность меди может приводить к формированию оксидов на поверхности покрытий в результате длительного нахождения на воздухе. Таким образом, в покрытиях Cu–C формируется нанокомпозиционная структура, состоящая из нанокристаллитов Cu, α-C и оксидных фаз CuO и Cu2O.
Механические свойства покрытий, такие как твердость (Н), модуль упругости (Е), упругое восстановление (R) и показатель пластичности (H/E), определенные методом наноиндентирования, представлены в табл. 4. Важность механических свойств помимо прочего обусловлена их влиянием на трибологические характеристики. Обычно, износостойкость материала определяется его твердостью. Однако в ряде случаев, в том числе для углеродсодержащих материалов, износостойкость наиболее полно характеризуется величиной Н/Е [18], также важным параметром, описывающим стойкость к пластической деформации, является соотношение H3/E2 [19, 20].
Таблица 4.
Результаты наноиндентирования
Покрытие | H, ГПа | E, ГПа | H/E × 102 | H3/E2 × 103, ГПа | R, % | f | Vw × 106, мм3/(Н м) |
---|---|---|---|---|---|---|---|
1 (Cu) | 0.4 | 38 | 1.1 | 0.04 | 6 | 0.40 | 82.7 |
2 (Cu–1C) | 0.7 | 29 | 2.4 | 0.41 | 13 | 0.43 | 7.5 |
4 (Cu–4C) | 1.6 | 70 | 2.3 | 0.84 | 15 | 0.33 | 6.8 |
6 (Cu–11C) | 1.8 | 62 | 2.9 | 1.52 | 18 | 0.19 | 4.1 |
8 (DLC) | 21 | 159 | 13.2 | 366.32 | 75 | 0.16 | 0 |
Медные покрытия с рыхлой структурой и относительно большими размерами кристаллитов показали самые низкие механические свойства. Введение C в покрытия позволило увеличить твердость примерно в 4 раза, модуль упругости – в 2 раза и показатель пластичности – в 2–3 раза. Данный эффект связан с формированием нанокомпозиционной структуры. Углерод способствует измельчению зерен ГЦК-фазы и препятствует межзеренному проскальзыванию.
Зависимости коэффициента трения (f) полученных в работе покрытий от пробега представлены на рис. 5. Введение С положительно сказывается на трибологических свойствах Cu-покрытий.
Рис. 5.
Коэффициенты трения покрытий 1 (Cu) – а; 2 (Сu–1C) – б; 3 (Сu–7C) – в; 4 (Cu–4C) – г; 7 (Cu‒10C) – д; 6 (Cu–11C) – е; 8 (DLC) – ж при пробеге 50 м.
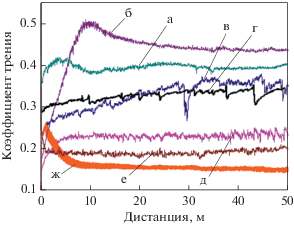
Коэффициенты трения всех (за исключением покрытия 2 (Сu–1С)) углеродсодержащих образцов ниже, чем у Cu. Высокая концентрация графитовых связей в покрытиях приводит к формированию твердой смазки на поверхности образцов и, как следствие, уменьшению коэффициента трения. Оптимального результата удалось добиться для покрытия 6 (Cu–11C), с максимальным содержанием углерода, коэффициент трения которого составил 0.19. В целом, результаты демонстрируют, что концентрация С неоднозначно влияет на коэффициент трения покрытий, хотя возможно на них также оказывает влияние оксиды меди, формирующиеся из-за повышенной концентрации О в покрытиях. Так, в образце 2 (Сu–1С) положительный эффект углерода нивелировался за счет повышения содержания кислорода в покрытии вследствие перехода от объемной литой мишени Cu к мозаичной 9C/16Cu, содержащей порошковые сегменты. Тем не менее при оптимальных условиях удалось получить покрытия с коэффициентом трения более, чем в 2 раза меньшим, чем f для Cu-пленок и близком к результатам, полученным для DLC. Износостойкость покрытий была определена из данных оптической профилометрии (рис. 6).
Покрытие Cu имело приведенную скорость износа (Vw), равную 82.7 × 10–6 мм3/(Н м). Покрытия Cu–C с низким содержанием углерода демонстрировали значения (6.8–7.5) × 10–6 мм3/(Н м), повышение концентрации С приводило к снижению скорости износа до 4.1 × 10–6 мм3/(Н м). В случае покрытия DLC видимых следов износа на поверхности образца не было.
ЗАКЛЮЧЕНИЕ
С помощью метода магнетронного распыления мозаичных мишеней были получены покрытия в системе Cu–C с содержанием углерода от 1 до 11 ат. %, а также однокомпонентные покрытия Cu и С. Покрытия Cu–C обладали более плотной и мелкозернистой структурой по сравнению с базовым покрытием Cu и содержали зерна ГЦК-фазы на основе меди размером ~20 нм, а также прослойки из sp2/sp3 связанного углерода.
Обнаружено, что по механическим и трибологическим характеристикам покрытия Cu–C превосходили покрытия Cu, обладая твердостью до 1.8 ГПа (0.4 ГПа у Cu), коэффициентом трения ~0.19 (~0.42 у Cu) и скоростью износа до 4.1 × × 10–6 мм3/(Н · м), что в 20 раз ниже, чем у Cu.
Авторы выражают благодарность П. Труханову за помощь в проведении исследований и К.А. Купцову за помощь в обработке рамановских спектров. Работа выполнена при поддержке Министерства образования и науки России (Госзадание № 11.7172.2017/8.9).
Список литературы
Mayrhofer P. H., Mitterer C., Hultman L., Clemens H. Microstructural design of hard coatings // Prog. Mater. Sci. 2006. V. 51. P. 1032–1114.
Ghorbani M., Mazaheri M., Afshar A. Wear and friction characteristics of electrodeposited graphite–bronze composite coatings // Surf. Coat. Technol. 2005. V. 190. P. 32–38.
Ghorbani M., Mazaheri M., Khangholi K., Kharazi Y. Electrodeposition of graphite-brass composite coatings and characterization of the tribological properties // Surf. Coat. Technol. 2001. V. 148. P. 71–76.
Musil J., Louda M., Soukup Z., Kubásek M. Relationship between mechanical properties and coefficient of friction of sputtered a-C/Cu composite thin films // Diamond Related Mater. 2008. V. 17. P. 1905–1911.
Пилипцов Д.Г., Рогачев А.В., Федосенко Н.Н. Свойства медь-углеродных композиционных пленок, полученных в плазме // Материалы международной конференции INTERMATIС. 2011. С. 180–183.
Lee J.K., Li Y.B., Lee S.W. Effect of Hydrogen Content on Characteristics of Cu/C: H Films Coated on Polyethylene Terephthalate Substrate Prepared by ECR-MOCVD Coupled with a Periodic DC Bias // Mater. Sci. Forum. 2006. V. 510–511. P. 666–669.
Lungu C.P., Tudor A., Mustata I., Zaroschi V., Lungu A.M., Pompilian O., Porosnicu C., Chiru P., Vlase M. Low friction C–Cu, C–Sn films prepared by thermionic vacuum arc method // Proceedings of the 7th international conference “The” Coatings in manufacturing engineering. 2008. P. 440–447.
Fei C., Gao-hui W., Long-tao J., Guo-qin C. Application of Cu–C and Cu–V alloys in barrier-less copper metallization // Vacuum. 2015. V. 122. P. 122–126.
Javid A., Kumar M., Yoon S., Lee J.H., Han J.G. Size-controlled growth and antibacterial mechanism for Cu:C nanocomposite thin films. // Phys. Chem. Chem. Phys. 2017. V. 19. P. 237–244.
Shtansky D.V., Lyasotsky I.V., D’yakonova N.B., Kiryukhantsev-Korneev F.V., Kulinich S.A., Levashov E.A., Moorec J.J. Comparative investigation of Ti–Si–N films magnetron sputtered using Ti5Si3 + Ti and Ti5Si3 + + TiN targets // Surf. Coat. Technol. 2004. V. 182. P. 204–214.
Kiryukhantsev-Korneev Ph.V., Pierson J.F., Kuptsov K.A., Shtansky D.V. Hard Cr–Al–Si–B–(N) coatings deposited by reactive and non-reactive magnetron sputtering of CrAlSiB target // Appl. Surf. Sci. 2014. V. 314. P. 104–111.
Sukhorukova I.V., Sheveyko A.N., Firestein K.L., Kiryukhantsev-Korneev Ph.V., Golberg D., Shtansky D.V. Mechanical properties of decellularized extracellular matrix coated with TiCaPCON film // Biomed. Mater. 2017. V. 12. P. 035014.
Musil J., Karvánková P., Kasl J. Hard and superhard Zr–Ni–N nanocomposite films // Surface and Coatings Technology. 2001. V. 139. P. 101–109.
Kiryukhantsev–Korneev Ph.V., Pierson J.F., Bychkova M.Y., Manakova O.S., Levashov E.A., Shtansky D.V. Comparative study of sliding, scratching and impact-loading behavior of hard CrB2 and Cr–B–N films // Tribol. Lett. 2016. V. 63. P. 1–11.
Ширяев С.А., Атаманов М.В., Гусева М.И., Мартыненко Ю.В., Митин А.В., Митин В.С., Московкин П.Г. Получение и свойства композиционных покрытий на основе металл-углерод с нанокристаллической структурой // ЖТФ. 2002. Т. 72. С. 99–104.
Kiryukhantsev-Korneev Ph.V., Shvyndina N.V., Bondarev A., Levashov E.A. Structure and properties of tribological coatings in Cu–B system // Phys. Met. Metal. 2014. V. 115. P. 716–722.
Winchester M.R., Payling R. Radio-frequency glow discharge spectrometry: A critical review // Spectrochimica Acta Part B 2004. V. 59. P. 607–666.
Leyland A., Matthews A. On the significance of the H/E ratio in wear control: a nanocomposite coating approach to optimised tribological behaviour // Wear. 2000. V. 246. P. 1–11.
Levashov E.A., Petrzhik M.I., Shtansky D.V., Kiryukhantsev-Korneev Ph.V., Sheveyko A.N., Valiev R.Z., Gunderov D.V., Prokoshkin S.D., Korotitskiy A.V., Smolin A.Yu. Nanostructured titanium alloys and multicomponent bioactive films: Mechanical behavior at indentation // Mater. Sci. Eng.: A. 2013. V. 570. P. 51–62.
Piedrahita W.F., Aperador W., Caicedo J.C., Prieto P. Evolution of physical properties in hafnium carbonitride thin films // J. Alloys Compounds. 2017. V. 690. P. 485–496.
Дополнительные материалы отсутствуют.
Инструменты
Физика металлов и металловедение