Физика металлов и металловедение, 2019, T. 120, № 9, стр. 969-979
Влияние криогенной обработки на микроструктуру и характеристики износостойкости хромистой штамповой инструментальной стали
Джалиль Сулеймани a, Хамид Гайур a, Камран Амини a, b, *, Фархад Гарави c
a Центр исследования перспективных материалов, Факультет технологии материалов,
Неджефабадское отделение, Исламский университет Азад
Неджефабад, Иран
b Факультет машиностроения, Тиранское отделение, Исламский университет Азад
Тиран, Иран
c Факультет технологии материалов, Сирджанское отделение, Исламский университет Азад
Сирджан, Иран
* E-mail: Kamran_amini1978@hotmail.com
Поступила в редакцию 30.01.2019
После доработки 06.02.2019
Принята к публикации 09.04.2019
Аннотация
Обработка холодом (до –80°С) и криогенная обработки (до температуры жидкого азота) являются добавочными операциями, предназначенными для улучшения характеристик износостойкости и твердости всего разнообразия инструментальных и закаливаемых сталей. В данном исследовании эффект от криогенной обработки изучали на примере изменений микроструктуры и характера износа (и изнашивания как при температуре окружающей среды, так и при 550°C) хромсодержащей штамповой инструментальной стали H11 (или h11, US), российским аналогом которой является сталь 4Х5МФС. С этой целью образцы стали H11 были сначала подвергнуты аустенитизации при 1050°C в течение 60 мин, с последующей закалкой в масло. Затем эти образцы помещали либо в сухой лед (–80°C, обработка холодом), либо в жидкий азот (–196°C, криогенная обработка). Затем образцы были подвергнуты отпуску при 550°C в течение 60 мин. Для анализа их микроструктуры и характера изнашивания использованы методы растровой электронной микроскопии, оптической металлографии, рентгеноструктурного анализа и метод испытаний на износ по схеме “палец–диск”. Полученные результаты показали, что процент остаточного аустенита составлял от 6.5% после традиционной обработки по схеме “закалка–отпуск” (ЗО) до 3% после обработки холодом и менее 1% после криогенной обработки. Более того, карбиды высокой дисперсности возникали (после отпуска при 550°C) как результат криогенной обработки, а объемная доля карбидов достигает 5.5% после традиционной обработки и 8.2% после криогенной обработки. При этом в случаях КО и ХО, в сравнении с ЗО, наблюдали возрастание твердости на 4 и 9%, и повышение износостойкости материала соответственно на 31 и 36% при комнатной температуре, и на 30 и 40% при повышенной температуре. Показано, что механизм износа при комнатной температуре носил адгезивные и химико-трибологические черты, а при повышенных температурах – абразивный и химико-трибологический характер. Проведение криогенной обработки обеспечивает снижение адгезионного и абразивного износа материала при комнатной и повышенной температурах.
1. ВВЕДЕНИЕ
В последнее время криогенная обработка стала составной частью промышленных технологий как термическая обработка, призванная улучшать микроструктуру и механические свойства широкого спектра материалов, таких как инструментальные стали, науглероженные стали, карбиды вольфрама, разного рода композитные материалы и полимеры. Криогенные обработки могут быть подразделены на обработки холодом (ХО, при температурах от –50 до –80°C) и собственно криогенные обработки (КО), которые проводятся обычно при температурах ниже –120°C [1]. Такие обработки обычно применяются к сталям после их традиционной термической обработки и перед проведением отпуска. Цель ХО состоит в полном устранении или уменьшении количества остаточного аустенита для увеличения твердости и термической стабильности материала. При проведении КО обычно преследуют две цели – не только увеличение твердости обрабатываемого материала, но и повышение его износостойкости. Конкретные цели таковы:
1. Снижение доли или полное устранение остаточного аустенита.
2. Увеличение потери объема, уменьшение размера и лучшее распределение карбида [2–6].
В исследовании, проведенном авторами [7] на стали En353 (науглероженная сталь для зубчатых колес), было показано, что ХО и КО в течение 5 и 24 ч полностью устраняли остаточный аустенит и повышали износостойкость на 85 и 372% соответственно. Автор работы [8] продемонстрировал снижение доли остаточного аустенита в стали Fe–1.4Cr–1C до 33 и 39% в случаях применения к ней ХО при –80°C и КО при –196°C, соответственно. При этом износостойкость в результате КО превысила этот показатель в сравнении со случаями ХО и ЗО (в последнем случае обработка холодом отсутствовала). Согласно исследованиям авторов [9] на штамповой инструментальной стали AISI H13, применение к ней ХО и КО привело к улучшению ее износостойкости и снижению количества остаточного аустенита. Авторы работы [10] также показали, что, несмотря на то что после ХО при –50°C и КО при –185°C процент содержания мартенсита не изменился, износостойкость образца после КО испытала некоторое улучшение благодаря выделившимся η-карбидам. Причиной такой “седиментации” явилось возникновение в структуре в результате КО упругих сжимающих искажений, заставивших атомы углерода покинуть свои исходные положения в кристаллической решетке [10–12]. Согласно исследованиям, проведенным авторами [12] на инструментальной быстрорежущей стали AISI M2, улучшение ее износостойкости (в сравнении с традиционной обработкой) после криогенной обработки можно отнести на счет деградации аустенита в мартенсит и имевшего место формирования карбидных фаз. Из-за низкого содержания остаточного аустенита в этой стали второй фактор представляется превалирующим. Роль этого фактора состоит в следующем: 1 – он предполагает более предпочтительное пространственное распределение дисперсного карбида в объеме сплава; 2 – двукратное увеличение объемной доли карбидов в сплаве после его обработки холодом в сравнении с традиционной схемой термообработки. Авторы указанных работ также убеждены, что обеспечение роста объемной доли карбидных фаз за счет включения в схему криогенной обработки становится причиной ухудшения свойств соответствующих сплавов, при том что углерод улучшает вязкость стали M2 [12]. Инструментальная сталь AISI H11 является штамповой и находит широкое применение при изготовлении изложниц для литья под давлением при экструзионном формовании и при экструдировании цветных металлов. В этой стали, благодаря относительно большой доле легирующих компонентов, следует ожидать присутствия остаточного аустенита. Тем самым в настоящем исследовании целью ставится выяснение влияния обработки холодом, включая криогенные температуры, на микроструктуру и характер изнашивания указанной стали в сравнении с результатами традиционной схемы термообработки, предполагающей только закалку и отпуск. Более того, поскольку данная сталь является штамповой инструментальной, она будет протестирована на изнашивание при низких и высоких температурах на предмет ее применения в промышленных масштабах.
2. МЕТОДИКА ЭКСПЕРИМЕНТА
Химический состав стали AISI H11 представлен в табл. 1. Приготовление образцов предполагало их электроискровую резку в форме дисков диаметром 50 мм и толщиной 5 мм из исходного образца указанной стали. Термообработка полученных образцов состояла в их предварительной выдержке при температуре 650°C в течение 1 ч и последующей аустенитизации при 1050°C в течение 1 ч и закалке в масло. После этого все образцы были разделены на три группы. Образцы первой группы (I) прошли отпуск при 550°C (“закалка–отпуск” (ЗО)). Образцы второй группы (II) подвергнуты обработке холодом при температуре –80°C в течение 24 ч в сухом льде (ХО) и третьей группы (III) – криогенной обработке в жидком азоте при температуре –196°C в течение 24 ч (КО), с их (II–III) последующим отпуском при 550°C в течение 1 часа. Твердость измеряли по Рокуэллу, шкала С (в единицах HRC). Микротвердость образцов измеряли по Виккерсу на твердомере марки Future FM-700 Hardness (Япония), с нагрузкой на индентор 300 г. Для отслеживания изменения в микроструктуре образцов их внешние поверхности были подвергнуты травлению: (a) в смеси 100 мл H2O, 10 г K3Fe(CN)6 и 10 г NaOH; (б) в смеси кислот 3 мл HF, 53 мл H2NO3, 2 мл CH3COOH и 42 мл H2O. Образцы прошли травление в каждом из этих составов в течение 2 с, причем 3–4 раза. Указанное сочетание компонентов травителей способствовало выявлению только карбидов, не сказываясь на проявлении других фаз. Поверхность образцов затем была исследована в оптическом микроскопе методами оптической металлографии (ОМ). Анализ микрофотографий состоял в их компьютерной обработке с применением программного пакета для обработки изображений Clemex Vision (версия 3.5.025) с целью определения доли карбидных фаз. Метод рентгеновской дифракции (установка Philips PW1730, в CuKα-излучении) был использован для выяснения типов присутствовавших фаз и оценки процента объемной доли остаточного аустенита (ОДОА). Значение ОДОА было рассчитано в соответствии с соблюдением стандарта, предписанного ASTM E975-00. Суммарный процент общего числа фаз должен был составить 100%. Процент содержания карбидов был оценен методами РЭМ микроскопии, процент остаточного аустенита был рассчитан по формуле
(1)
${{V}_{\gamma }} = \left[ {\frac{{\left( {1 - {{V}_{{\text{c}}}}} \right)\left( {{{{{I}_{\gamma }}} \mathord{\left/ {\vphantom {{{{I}_{\gamma }}} {{{R}_{\gamma }}}}} \right. \kern-0em} {{{R}_{\gamma }}}}} \right)}}{{\left( {{{{{I}_{\alpha }}} \mathord{\left/ {\vphantom {{{{I}_{\alpha }}} {{{R}_{\alpha }}}}} \right. \kern-0em} {{{R}_{\alpha }}}}} \right)}} + \left( {{{{{I}_{\gamma }}} \mathord{\left/ {\vphantom {{{{I}_{\gamma }}} {{{R}_{\gamma }}}}} \right. \kern-0em} {{{R}_{\gamma }}}}} \right)} \right],$Таблица 1.
Химический состав стали H11 (вес. %)
Fe | C | Si | Mn | Cr | Mo | V | Cu |
---|---|---|---|---|---|---|---|
91.1 | 0.41 | 0.87 | 0.34 | 4.86 | 1.30 | 0.29 | 0.26 |
Для проведения оптических металлографических исследований образцы сначала были отполированы по стандартной методике. Затем их приготовили для РЭМ-анализа микроструктуры (на микроскопе модели Philips XI30, Нидерланды). Далее, в качестве агента травления был использован спиртовый раствор пикриновой кислоты – пикраль (реактив для выявления микроструктуры). Для проведения теста на изнашивание вхолодную, штифт индентора со стальной опорной частью твердостью HRC 64 был использован в качества пальца в трибологической схеме “палец–диск”. Приложенная нагрузка в испытаниях на износ вхолодную составила 150 ньютонов, длина пробега индентора была 1000 метров, а сам тест проводили при влажности воздуха 30 ± 5% в интервале температур 25 ± 5°C, на скорости поступательного перемещения индентора 0.1 м/с.
Тест на износ в условиях повышенных температур был осуществлен по схеме “палец–диск” с индентором, имевшем конусовидную насадку из карбида вольфрама. Тест проводили при нагрузке 25 Н, при поступательной скорости перемещения индентора 0.1 м/с, в интервале температур 550 ± 10°C и при длине пути пробега индентора 200 м. Скорость изнашивания Wr (мм3/Н м) оценивали по формуле
где Δm – потеря в весе, ρ – плотность материала, F – нагрузка на индентор, L – длина пути индентора при истирании материала.3. РЕЗУЛЬТАТЫ И ОБСУЖДЕНИЕ
3.1. Изучение микроструктуры. На рис. 1 представлены рентгеновские дифрактограммы исследованных образцов. Ясно, что процент содержания остаточного аустенита в образцах, прошедших криогенную обработку, понижен в сравнении с холодной обработкой и традиционной термообработкой. В табл. 2 приведены значения содержания остаточного аустенита (ОА). Содержание ОА в ЗО-образцах достигало 6.5%, в ОХ-образцах – 3%, в КО-образцах – менее 1%. Снижение ОА в сталях после применения к ним криогенных обработок отмечали также и другие исследователи [7, 9, 14, 15]. Микроструктура образцов была изучена методами OM- и РЭМ-микроскопии. Результаты представлены на рис. 2, 3 и 4. Так, на рис. 2 приведено ОМ-изображение микроструктуры H11 стали после ее травления: (a) в смеси 100 мл H2O, 10 г K3Fe(CN)6 и 10 г NaOH; (б) в смеси кислот {3 мл HF, 53 мл H2NO3, 2 мл CH3COOH и 42 мл H2O}. Обработка указанными реактивами была проведена для “проявления” карбидов. Использование программного пакета для обработки изображений Image Analyses Software показало, что объемная доля карбидов достигла значений 5.5% для ЗО-образца, 6.4% для ХО-образца, 8.2% для КО-образца. Таким образом, на основании рис. 2 можно заключить, что выделение мелкодисперсных карбидов произошло в результате обработки образцов холодом, так что количество карбидов увеличилось. С большей интенсивностью это происходит при КО. На рис. 3 и 4 представлены ОМ- и РЭМ-изображения структуры образцов. Видно, что рост дисперсности карбидов и их количества явно увеличивается с понижением температуры криогенной обработки. Выпадение мелкодисперсных карбидов вследствие КО после отпуска образцов обязано тому факту, что структура находилась в условиях напряженного состояния, обусловленного достаточно сильным сокращением, что является следствием разницы в коэффициенте расширения аустенита и мартенсита. Тем самым указанный уровень внутренних напряжений послужил движущей силой для инициации перескока атомов углерода из междоузлий на близлежащие дефекты структуры. Появление новых дефектов на (γ/α)-межфазных границах было обусловлено указанным различием в коэффициентах объемного расширения аустенита и мартенсита. Два этих фактора благоприятствовали формированию зародышей карбидных фаз во время отпуска материала [16]. В исследовании авторов работы [1] на стали 80CrMo125, было отмечено 2%-ное увеличение объемной доли карбида как результат проведения глубокой криогенной обработки в сравнении с традиционной термообработкой. Более того, авторы [1] отнесли улучшение пространственного распределения дисперсных карбидов на счет криогенной обработки материала.
Таблица 2.
Процент остаточного аустенита в стали H11 после различных обработок
Обработка аустенит | Остаточный аустенит, % |
---|---|
ЗО | 6.5 |
ХО | 3 |
КО | менее 1 |
В других исследованиях того же коллектива авторов на стали марки 1.2080, были отмечены увеличение объемной доли и более хорошее пространственное распределение карбидов, а также формирование наноразмерных карбидов, в результате глубокой криогенной обработки [1, 11, 16, 17]. Из-за малости скорости проникновения-распространения атомов углерода при температуре –196°C эти атомы не способны располагаться в непосредственной близости от очень “жестких” дефектов кристаллического строения, и выпадение дисперсных карбидов становится невозможно. Однако при нагревании образцов от нуля до комнатной температуры скорость проникновения атомов углерода возрастает. При этом атомы углерода диффундируют по кристаллической мартенситной структуре, и невысокая скорость их распространения приводит к формированию атомных С-кластеров вокруг дефектов кристаллического строения, с последующим формированием в этих местах мелкодисперсных карбидов. Процесс выпадения карбидов в результате глубокой криогенной обработки, включающий в себя распад мартенсита и образование мелкодисперсных карбидов, очень напоминает то, что происходит во время протекания процессов отпуска, за тем исключением, что из-за пониженных температур карбидные “седиментации” являются более дисперсными и более однородно пространственно распределенными.
3.2. Твердость образцов и их поведениепри изнашивании. Согласно данным табл. 3, твердость ХО- и КО-образцов возрастала на 4 и 9% соответственно, в сравнении с ЗО-образцами. Это явилось результатом уменьшения содержания остаточного аустенита, выделения дисперсных карбидов, увеличения их содержания в материале, а также улучшения их пространственного распределения в объеме образца. Так как эффект от глубокой криогенной обработки более выражен в сокращении количества остаточного аустенита и в выделении дисперсных карбидов, то у КО-образцов наблюдается и более высокая твердость. В исследовании на стали AISI 440C [18] авторами было отмечено, что в сравнении с традиционной термообработкой, твердость по Рокуэллу у образцов, прошедших ХО и КО, возросла на 4 и 7% соответственно. В указанном исследовании показано, что увеличение превращенной в мартенсит доли остаточного аустенита является причиной повышенной твердости материала. В исследовании на примере стали D6 [14] увеличение Рокуэлловской твердости образцов, прошедших ХО и КО, составило 1.6 и 3.2% соответственно, в сравнении с традиционной термообработкой. Авторы [14] отметили, что такие значения твердости объясняются степенью превращения остаточного аустенита в мартенсит, а также выпадением вторичных карбидов в процессе глубокой криогенной обработки.
Таблица 3.
Твердость (в единицах HRC и HV) стали H11 после различных обработок
Обработка | Твердость, HRC | Микротвердость, HV |
---|---|---|
ЗО | 50 ± 1 | 475 ± 7 |
ХО | 52 ± 0.5 | 512 ± 5 |
КО | 54.5 ± 0.5 | 563 ± 5 |
В табл. 4 и на рис. 5 и 6 представлены результаты испытаний на изнашивание образцов в условиях обычных и повышенных температур. Как можно четко видеть, ХО и КО обусловили увеличение износостойкости образцов на 31 и 36% в условиях испытаний при комнатной температуре, и на 30 и 40% – при повышенной температуре 550°C в сравнении с традиционной термообработкой. Основываясь на результатах проведенных исследований, можно утверждать, что причиной такого улучшения износостойкости стало уменьшение содержания остаточного аустенита в ХО- и КО-образцах. При этом в случае КО это имело место наряду с возросшей объемной долей карбидов, их возросшей дисперсностью и улучшением их пространственного распределения в сравнении со случаем ЗО обработки. Согласно рис. 6, скорость изнашивания образца уменьшается по мере увеличения длины пробега индентора. Это объясняется ростом степени деформационного упрочнения образца по мере увеличения продолжительности эксперимента [19].
Таблица 4.
Потеря веса (в результате износа) и скорость изнашивания образцов стали H11 в условиях повышенной температуры проведения теста, после 200 м длины пути трения под нагрузкой 25 Ньютонов, при поступательной скорости перемещения индентора 0.1 м/с
Обработка | Пробег индентора, м | Температура проведения теста по изнашиванию, °C | Расход массы, мг | Скорость изнашивания, мм3/Н м × 106 |
---|---|---|---|---|
“Закалка–Отпуск” (ЗО) | 200 | 550 | 0.0040 | 0.102 |
Обработка Холодом при –80°С, 24 ч (ХО) | 0.0028 | 0.071 | ||
Криогенная Обработка при –196°С, 24 ч (КО) | 0.0024 | 0.061 |
Рис. 5.
Изменение характеристики потери веса инструментальной стали H11 от длины пробега индентора, в условиях “холодного” трения.
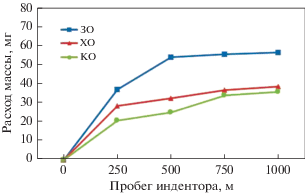
Рис. 6.
Зависимость скорости изнашивания инструментальной стали H11 от длины пробега индентора, в условиях повышенной температуры.
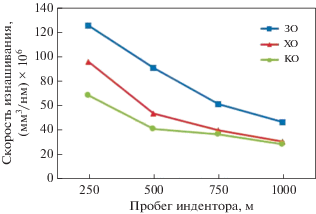
Тем самым, вдобавок к снижению или полному удалению остаточного аустенита как нежесткой фазы в ходе конкретной криогенной обработки материала, выделение дисперсных карбидов приводит к обеднению матрицы стали по углероду и легирующим элементам. Таким образом, материал матрицы стали обладает повышенной вязкостью. Как результат, износостойкость стали в целом улучшается, причем это происходит также благодаря выделению дисперсных карбидов и снижению количества или полному удалению остаточного аустенита [10, 12, 20]. При исследовании стали En 353 установлено [7], что при включении в схему термообработки низкотемпературных составляющих, ХО и КО, прирост ее износостойкости составил 85 и 372%, соответственно. Такой прирост был обеспечен за счет полного исчезновения аустенита, выпадения дисперсных карбидов и их более однородного пространственного распределения благодаря проведению криогенной обработки.
Для установления механизма изнашивания было проведено РЭМ-исследование поверхности износа образцов. Результаты представлены на рис. 7 и 8. Они отвечают проведению тестов в условиях обычных и повышенных температур. Согласно рис. 7, доминирующим механизмом износа в условиях температуры окружающей среды являлся адгезионный износ.
Рис. 7.
РЭМ-микроизображение изношенной поверхности (a) ЗО-, (б) ХО-, (в) КО-образцов после их испытаний на износ вхолодную.
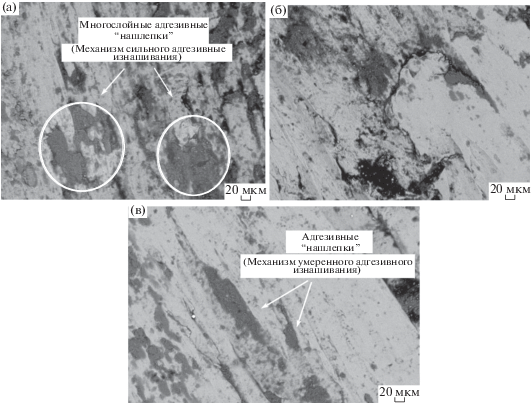
Рис. 8.
РЭМ-микроизображение изношенной поверхности (a) ЗО-, (б) ХО-, (в) КО-образцов после их испытаний на износ вгорячую.
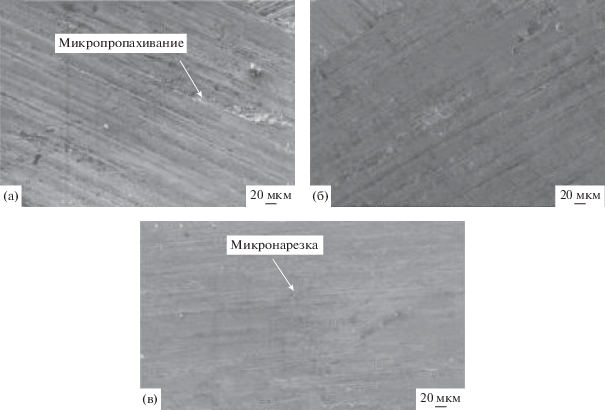
Такой характер износа стал результатом адгезионного сопряжения фрагментов изношенных участков трущихся поверхностей, соприкасавшихся друг с другом. Если отрыв контактирующих участков трущихся поверхностей происходит со стороны интерфейса, то говорить об износе материала не приходится. Но если происходит отрыв одного из этих контактирующих участков со стороны образца, то акт износа налицо. Чем ближе значения твердости образца и индентора, тем вероятнее становится такой тип износа. Фактически можно сказать, что выделение теплоты от трения поверхностей способствует адгезионным сочленениям, что в итоге приводит к элементарным актам их последующего удаления с поверхности образца. Согласно рис. 7a, значительная часть поверхности включает такие адгезивные “нашлепки”, оказывающиеся в отдельных случаях многослойными. Следовательно, с интенсивным адгезионным изнашиванием мы сталкиваемся на примере ЗО-образцов. Степень этого адгезионного износа снижается в результате криогенной обработки (см. рис. 7б, 7в).
В тесте на износ в условиях повышенных температур, с индентором, имевшем конусовидную насадку из карбида вольфрама, характер механизма износа изменился с адгезивного на абразивный из-за снижения твердости поверхности тестируемого материала (рис. 8). При размягчении поверхности материала при повышенных температурах, степень пластической деформации возрастает. Уменьшение твердости в результате действия повышенных температур приводит к тому, что “шероховатости” более твердой поверхности как бы проникают в тело более мягкого материала (в условиях эксперимента на износ по схеме “палец–диск”) и продуцируют царапины на поверхности истираемого образца. Такой механизм изнашивания сначала приводит к переносу материала из объема царапины на ее края. Как видно из рис. 8a, степень пластической деформации на краях каждой царапины ЗО-образца наибольшая из-за его более низкой твердости, так реализуется механизм микропропахивания. В КО-образце, вследствие его более высокой твердости и стойкости к снижению твердости, сопротивление пластическому деформированию оказывается более высоким, что проявляется в микростругировании материала “изнашиваемого” образца (рис. 8в). Как можно видеть на рис. 9 и 10, в процессе испытаний на износ наблюдается окисление – результат как интенсивного трения поверхностей, так и повышенной температуры. Это приводит к трибохимическому характеру износа. Этот эффект становится интенсивнее с ростом температуры эксперимента по износу. Исследование, проведенное авторами работы [21] на стали марки DIN 1.7131 (в контексте ее криогенной обработки), продемонстрировало более хорошее пространственное распределение дисперсных карбидов и их возросшую объемную долю, снижение степени адгезивного износа, а также отсутствие (как результат удаления) остаточного аустенита, который обладает твердостью, меньшей, чем у мартенсита. Степень адгезивного износа также прямо пропорциональна нагрузке, приложенной на индентор, и обратно пропорциональна твердости испытуемого материала [22].
Рис. 9.
Рентгеновский ЭДС анализ КО-образца после его испытаний на износ вхолодную: (a) РЭМ-микроизображение, (б) ЭДСА в точке 1, (в) ЭДСА в точке 2.
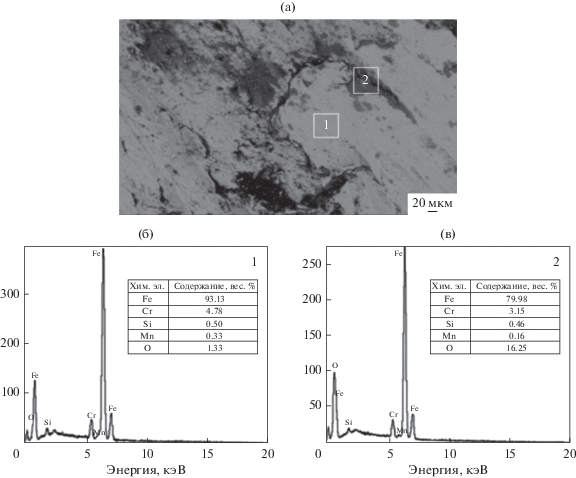
Рис. 10.
Рентгеновский ЭДС анализ КО-образца после его испытаний на износ вгорячую: (a) РЭМ-микроизображение, (б) ЭДСА в точке 1.
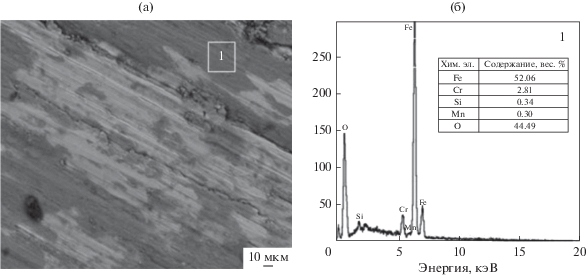
Таким образом, можно заключить, что в образцах, прошедших криогенную обработку, рост их твердости обусловлен снижением количества остаточного аустенита, выделением дисперсных карбидов, увеличением их объемной доли, улучшением их пространственного распределения. Все перечисленные факторы приводят к возрастанию износостойкости материала. На рис. 11 представлены микроизображения продуктов износа (ПИ) после проведенного теста на изнашивание. ПИ также были изучены РЭМ-методами. Результаты показали, что “обломки” износа у КО-образца более мелкие в сравнении с ЗО-образцом. Все это является результатом того, что поверхность КО-образцов была более твердой в сравнении с ЗО-образцами. Наши результаты нашли подтверждение у других исследователей [14].
4. ЗАКЛЮЧЕНИЕ
1. Обработки холодом приводят к снижению количества остаточного аустенита. Доля остаточного аустенита составила 6.5% после традиционной термообработки (ЗО), 3% после обработки холодом при –80°С в течение 24 ч (ХО), менее 1% после криогенной обработки при –196°С в течение 24 ч (КО).
2. В результате криогенной обработки выделяются дисперсные карбиды, и их объемная доля растет с падением температуры обработки холодом. Этот эффект проявляется сильнее после криогенной обработки при –196°С (КО) в сравнении с обработкой холодом при –80°С (ХО). Объемная доля карбидов в образцах составила 5.5% после ЗО, 6.4% после ХО и 8.2% после КО. Тем самым криогенная обработка обеспечила наибольшую движущую силу для образования очень дисперсных карбидов.
3. В результате ХО твердость и износостойкость увеличились на 4 и 31% соответственно, при испытаниях на износ в условиях обычных температур; при испытаниях в условиях повышенной температуры (550°С) износостойкость увеличилась на 30%. В результате КО твердость и износостойкость увеличились на 9 и 36% соответственно, при испытаниях на износ в условиях обычных температур; при испытаниях в условиях повышенной температуры (550°С) износостойкость увеличилась на 40%. Указанные цифры прироста даны по отношению к традиционной (“закалка–отпуск”) обработке. Прирост обусловлен снижением количества остаточного аустенита и выделением мелкодисперсных карбидов как результат обработки в условиях низких температур.
4. Доминирующий механизм износа в испытаниях при комнатных температурах носил адгезивный и трибохимический характер. Адгезивный износ (АИ) был наиболее сильно выражен в случае ЗО образцов и был слаб для ХО- и КО-образцов. Причина этого состоит в повышенной твердости образцов, прошедших обработку холодом. Механизм износа носил абразивный и трибохимический характер в образцах, которые прошли испытания на износ в условиях повышенной температуры (550°), с индентором, имевшим конусовидную насадку из карбида вольфрама. Объяснить это можно снижением твердости в условиях повышенных температур. В ЗО-образце вследствие его самой меньшей твердости из всех случаев обработки, добавочную пластическую деформацию наблюдали по краям “объема” механических царапин поверхности износа, что соответствовало субмеханизму износа по типу микропропахивания. Кроме того, в ХО- и КО-образцах, вследствие их большей твердости, у механических царапин поверхности износа не наблюдали добавочную пластическую деформацию по краям их “объема”, что свидетельствовало о включении субмеханизма микростругирования. Более того, “обломки” продуктов износа ХО и КО образцов отличались хрупкостью и более мелким размером.
Список литературы
Amini K., Nategh S., Shafyei A., Rezaeian A. Effect of deep cryogenic treatment on the properties of 80CrMo12.5 tool steel // Inter. J. of Minerals, Metall. Mater. 2012. V. 19. P. 30–37.
Amini K., Nategh S., Shafiey A., Soltany M.A. To study the effect of cryogenic heat treatment on the hardness and the amount of residual austenite in 1/2304 steel // Metal. 2008. V. 13. P. 1–7.
Cajner F., Leskovšek V., Landek D., Cajner H. Effect of deep-cryogenic treatment on high speed steel properties // Mater. Manufact. Processes. 2009. V. 24. P. 743–746.
Das D., Dutta A., Ray K. Influence of varied cryotreatment on the wear behavior of AISI D2 steel // Wear. 2009. V. 266. P. 297–309.
Das D., Dutta A.K., Ray K.K. Sub-zero treatments of AISI D2 steel: Part I. Microstructure and hardness // Mater. Sci. Eng.: A. 2010. V. 527. P. 2182–2193.
Das D., Ray K., Dutta A. Influence of temperature of sub-zero treatments on the wear behaviour of die steel // Wear. 2009. V. 267. P. 1361–1370.
Bensely A., Prabhakaran A., Lal D.M., Nagarajan G. Enhancing the wear resistance of case carburized steel (En 353) by cryogenic treatment // Cryogenics. 2005. V. 45. P. 747–754.
Meng F., Tagashira K., Sohma H. Wear resistance and microstructure of cryogenic treated Fe-1.4 Cr-1C bearing steel // Scripta Metall. Mater. 1994. V. 31. P. 865–868.
Koneshlou M., Asl K.M., Khomamizadeh F. Effect of cryogenic treatment on microstructure, mechanical and wear behaviors of AISI H13 hot work tool steel // Cryogenics. 2011. V. 51. P. 55–61.
Meng F., Tagashira K., Azuma R., Sohma H. Role of eta-carbide precipitations in the wear resistance improvements of Fe-12Cr-Mo-V-1.4 C tool steel by cryogenic treatment // ISIJ international. 1994. V. 34. P. 205–210.
Amini K., Akhbarizadeh A., Javadpour S. Effect of deep cryogenic treatment on the formation of nano-sized carbides and the wear behavior of D2 tool steel // Intern. J. of Minerals, Metall. Mater. 2012. V. 19. P. 795–799.
Huang J., Zhu Y., Liao X., Beyerlein I., Bourke M., Mitchell T. Microstructure of cryogenic treated M2 tool steel // Mater. Sci. Eng.: A. 2003. V. 339. P. 241–244.
Standard A. E975-03: Standard practice for x-ray determination of retained austenite in steel with near random crystallographic orientation // ASTM, West Conshohocken, PA, 2008.
Akhbarizadeh A., Shafyei A., Golozar M. Effects of cryogenic treatment on wear behavior of D6 tool steel // Materials & Design. 2009. V. 30. P. 3259–3264.
Senthilkumar D., Rajendran I., Pellizzari M., Siiriainen J. Influence of shallow and deep cryogenic treatment on the residual state of stress of 4140 steel // J. of Mater. Proces. Techn. 2011. V. 211. P. 396–401.
Akhbarizadeh A., Javadpour S., Amini K., Yaghtin A.H. Investigating the effect of ball milling during the deep cryogenic heat treatment of the 1.2080 tool steel // Vacuum. 2013. V. 90. P. 70–74.
Amini K., Akhbarizadeh A., Javadpour S. Cryogenic heat treatment of the ferrous materials –a review of the current state // Metal. Research & Techn. 2016. V. 113. P. 611.
Idayan A., Gnanavelbabu A., Rajkumar K. Influence of deep cryogenic treatment on the mechanical properties of AISI 440C Bearing steel // Procedia Engineering. 2014. V. 97. P. 1683–1691.
Fontalvo G., Humer R., Mitterer C., Sammt K., Schemmel I. Microstructural aspects determining the adhesive wear of tool steels // Wear. 2006. V. 260. P. 1028–1034.
Paydar H., Amini K., Akhbarizadeh A. Investigating the effect of deep cryogenic heat treatment on the wear behavior of 100Cr6 alloy steel // Kovove Materialy-Metallic Materials. 2014. V. 52. P. 163–9.
Amini K., Araghi A., Akhbarizadeh A. Effect of Deep Cryogenic Heat Treatment on the Wear Behavior of Carburized DIN 1.7131 Grade Steel // Acta Metal. Sinica (English Letters). 2015. V. 28. P. 348–353.
Bhushan B. Introduction to tribology. John Wiley & Sons, 2013.
Дополнительные материалы отсутствуют.
Инструменты
Физика металлов и металловедение