Физика металлов и металловедение, 2019, T. 120, № 9, стр. 961-968
Влияние Mg на микромеханическое поведение свежелитых сплавов системы Al–Mg
Х. Н. Панчал a, *, В. Дж. Рао a
a Кафедра металлургии и материаловедения, Инженерно-технологический факультет,
Махараджа Сайаджирао университет Бароды
390002 Вадодара, Индия
* E-mail: hemant.p-metallurgy@msubaroda.ac.in
Поступила в редакцию 23.06.2017
После доработки 29.05.2018
Принята к публикации 26.09.2018
Аннотация
Для различных концентраций Mg было проведено изучение возможности оптимизации его содержания в сплавах Al–Mg-системы, когда речь идет об их металлургических и механических свойствах. В Al, расплавленном в электронагревательной печи, вариации содержания Mg составляли от 0.05 до 7 вес. %. При температуре обработки образовывались Al–Mg, Mg–Si и Al–Si-интерметаллиды. При затвердевании эти интерметаллиды вытеснялись на границы зерен и формировали кластеры, что было изучено методами РЭМ–ЭДС анализа. Более тяжелые фазы выявлялись как темные области, тогда как более легкие – как менее темные или светлые участки изображений. Благодаря таким эффектам вытеснения интерметаллидов во время затвердевания в металлической форме, развитие границ зерен начиналось в виде их заметного утолщения внутрь Al-матрицы. Было обнаружено, что это явление становилось более выраженным при увеличении концентрации Mg. При 7 вес. % Mg было обнаружено, что на границах зерен собиралось максимальное количество интерметаллидов. Сегрегационные тенденции разных интерметаллидов и избыточного свободного Mg оказались несбалансированными в области более высоких концентраций Mg. Изучены были предел прочности на растяжение, удельная прочность и твердость. Было установлено, что эти характеристики максимальны у сплава Al–3 вес. % Mg, наряду с его небольшим удельным весом и низкой пластичностью. Тем самым, в данном исследовании 3 вес. % Mg рассматривается как оптимальный уровень концентрации, если отталкиваться от микромеханического поведения его сплавов.
1. ВВЕДЕНИЕ
Al-сплавы находят широкое применение в авиакосмической и автомобильной отраслях промышленности благодаря своему малому удельному весу, хорошим механическим свойствам, неплохой коррозионной стойкости, повышенной износостойкости, низкому значению коэффициента термического расширения и пр. в сравнении с традиционными металлами и сплавами. Отмеченные механические свойства и относительно невысокая себестоимость производства делают Al-сплавы привлекательным кандидатом в ряде приложений, как с научной, так и технологической точек зрения [1].
В настоящий момент Al–Mg-сплавы предоставляют широкие возможности их использования в спортивной, автомобильной, аэрокосмической индустрии и т.д., поскольку обеспечивают выигрышные характеристики в сравнении с другими материалами по эффективному контролю за экономическими показателями. Легирующие добавки выбираются по признакам их влияний и целесообразности. Другие легирующие элементы, такие как Cu, Mn, Si, Zn, Fe, Ni, Pb и Sn, также часто добавляются в Al [2].
В принципе, как основной легирующий компонент, Mg является наиболее эффективным элементом в плане упрочнения сплавов рассматриваемой системы и способен изменять возможности литья под давлением из-за своей специфической растворимости в Al. Mg может обеспечить эффективное упрочнение и улучшение характеристик деформационного упрочнения Al [3]. Он также повышает свариваемость и устойчивость к коррозии [4, 5]. В тот момент, когда Si реагирует с Mg c образованием упрочняющей фазы Mg2Si, он обеспечивает упрочнение. Традиционно, добавка Mg не превышает 5–7 вес. % в сплавах системы Al–Mg, иногда наряду с Mn [6]. Однако было заявлено, что значения оптимальной прочности и твердости отвечают 1 вес. % Mg [7] и даже – 5 вес. % Mg [8]. В ряде источников в качестве оптимальной величины фигурирует 8 вес. % Mg – значение, при котором такой Al–Mg-сплав демонстрирует хорошие термомеханические свойства, или точнее, когда Mg добавляют в пределах от 4 до 8 вес. %. При содержании выше 8 вес. % Mg наблюдается повышенная пористость, приводящая к низким термомеханическим характеристикам [9]. Также нужно учитывать влияние добавки Mg на микроструктуру и механические свойства сплавов Al–Mg-системы. Поэтому для оптимизации содержания Mg в Al с точки зрения металлургических и механических свойств будущего материала и было предпринято данное исследование.
Mg может модифицировать большинство из механических свойств Al [10]. Твердость и износостойкость Al могут возрастать с добавкой Mg благодаря формированию интерметаллидов [11].
Mg очень реакционоспособный элемент, имеющий большое (химическое) сродство с кислородом [12], и вероятность в снижении его “эффективности” из-за реакции с кислородом в ближнем атомном окружении весьма велика. Наряду с Mg, Al ведет себя так же, если иметь в виду термодинамические аспекты. Следующие реакции весьма вероятны в системе на стадии плавления.
(5)
$12{\text{Al}} + 17{\text{Mg}} \to \gamma {\text{M}}{{{\text{g}}}_{{17}}}{\text{A}}{{{\text{l}}}_{{12}}}.$Интерметаллическое соединение Mg2Si обладает кубической кристаллической структурой, с параметром решетки 0.635 нм, высокой точкой плавления 1085°C, малым удельным весом 1.99 × × 103 г/см3, большой твердостью 4500 МН/м2, малым коэффициентом термического расширения (КТР) 7.5 × 10−6 K−1 и (разумно) высоким значением модуля упругости 120 ГПа (по данным) [13]. Примеси, присутствующие в расплаве исходных Al и Mg, способны вступать в химические реакции при температурах обработки и образовывать целый ряд интерметаллических фаз, таких, например, как FeAl3, (Fe,Mn)Al6, (Fe,Mn)3Si2Al15, Mg3Zn3Al2, CuMgAl2, Cu2FeAl7, и т.д., что сказывается (в свою очередь) на структуре и свойствах материала. Авторы работы [14] отмечали, что при добавках Mg, помимо ожидаемо возникающей модификации α-Fe, имеется вероятность формирования (в его пространственных пределах) еще и интерметаллического соединения Al5FeSi пластинчатой формы.
2. МЕТОДИКА ЭКСПЕРИМЕНТА
Al промышленной чистоты подвергали плавлению в графитовом тигле в электрической плавильной печи. После достижения температуры обработки, в расплав Al было добавлено заранее рассчитанное количество Mg (в виде таблетки). Количество Mg варьировали от 0.05 до 7 вес. %. В данной работе мы придерживались обычной плавильной практики (т.е. удаление шлака с поверхности расплава и проведение дегазации через предписанные интервалы времени). Каждый раз по достижении расплавом нужной степени густоты, хорошо перемешанная расплавленная смесь была разлита в предварительно нагретую (до температур от 400 до 450°С) металлическую форму. После затвердевания и футеровки был произведен отбор образцов для проведения различных исследований – методами РЭМ, ЭДС, измерений твердости, удельного веса, прочности и т.д. Вид экспериментальной установки схематически представлен на рис. 1.
Рис. 1.
Экспериментальная установка для приготовления сплавов системы Al–Mg с использованием электрической плавильной печи.
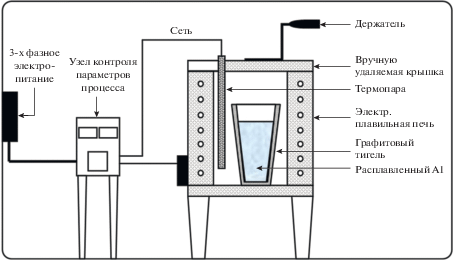
Тестирование образцов на растяжение производили на тензометре модели Monsanto 20 в горизонтальном положении при скорости подачи цапфы крейцкопфа (скорости деформирования) 0.05 мм/мин в каждом случае. Размеры разрывных образцов приведены на рис. 2.
Твердость измеряли по методу Бринелля. Для получения образцов для анализа микроструктуры, использовали стандартную металлографическую методику приготовления шлифов. Микроструктуру наблюдали в оптический микроскоп (ОМ) марки Neophot 02 и с помощью растрового электронного микроскопа (РЭМ) марки JEOL 5610 LV (Япония), на разных увеличениях и в разном протравленном состоянии. Качественный и количественный анализ на присутствие химических элементов производили ЭДС методами. Денситометрический анализ литых образцов производили с помощью пикнометрического тестера. Удельную прочность рассчитывали как отношение прочности на единицу удельного веса, известного также как отношение “прочность/вес”.
3. РЕЗУЛЬТАТЫ И ОБСУЖДЕНИЕ
Содержание химических элементов в исходных промышленной чистоты материалах Al и Mg (по сути, сплавах системы Al–Mg крайних процентовок) приведено в табл. 1. Эти результаты показывают присутствие в исходном Al (алюминиевом сплаве) наряду с кремнием (Si) таких тяжелых химических элементов, как Fe, Mn, Cu, Zn и т.д. В свою очередь, в Mg присутствует только Si. Такие сопутствующие тяжелые примесные элементы образуют различные интерметаллические фазы в теле синтезируемых сплавов. По данным ЭДС-анализа, можно было сказать, что имелось требуемое (с точки зрения стехиометрии) количество примесных элементов, чтобы сформировать различные интерметаллические соединения, такие как Mg2Si, Al2Mg, Al2Si и т.д., как в теле синтезируемых сплавов, так и в различных областях границ зерен, что можно видеть на рис. 3 и из данных табл. 2.
Таблица 1.
Химический состав исходных материалов в состоянии поставки
Элемент | Алюминий, вес. % | Магний, вес. % |
---|---|---|
Mg | 0.12 | 99.67 |
Si | 0.48 | 0.13 |
Mn | 0.21 | – |
Fe | 0.82 | – |
Cu | 0.05 | – |
Zn | 0.09 | – |
Al | 98.28 | 0.19 |
Таблица 2.
Химический состав сплава Al–7 вес. % Mg в различных участках объема
Элемент | Спектр 1, вес. % | Спектр 2, вес. % | Спектр 3, вес. % | Спектр 4, вес. % |
---|---|---|---|---|
C | – | 5.79 | 8.91 | – |
O | – | 36.20 | 2.35 | 0.94 |
Mg | 3.91 | 3.31 | 4.32 | 6.55 |
Ag | 0.61 | – | 2.12 | 1.48 |
Si | 0.41 | – | – | 0.45 |
Mn | 2.85 | – | – | – |
Fe | 18.24 | – | – | – |
Al | 73.98 | 54.69 | 82.30 | 90.58 |
Вероятные фазы | AlFe3, Al13Fe4, | Al2Mg2, | γ Mg17Al12, | Al2Si, |
Al3Fe2, (Fe,Mn)Al6, | Al3Mg2, | Al2Mg3 | Mg2Si, | |
(Fe,Mn)3 Si2Al15 | β-(Al,M g) | Al-матрица |
Исходя из значения отношения Mg : Si = 1.73 : 1, необходимого для образования фазы Mg2Si, добавку Mg, начиная с 0.05, 0.15, 0.50 до 1.00 вес. %, делали во время начальных стадий (изучения). В результате этого суммарное количество имеющегося в наличии Si (т.е., 0.48 + 0.13 = 0.61 вес. %) в исходных Al и Mg оказалось (использованным и) связанным в форме Mg2Si. Начиная с 1 вес. % и вплоть до 3 вес. % Mg, этот элемент (Mg) выступал в качестве агента-носителя твердорастворного упрочнения.
3.1 Аттестация микроструктуры
Образцы для металлографических исследований приготовляли по стандартной методике, без их травления. Анализ микроструктуры был проведен с помощью Neophot 02 (ОМ) и сканирующего электронного микроскопа. На рис. 4 представлены ОМ-изображения микроструктуры, типичной для Al в отсутствие добавки Mg, и для Al–Mg-сплава с добавкой 1 вес. % Mg, 3 вес. % Mg, 5 вес. % Mg и 7 вес. % Mg. Электронно-микроскопические исследования отполированных образцов были проведены без их травления, при 15 кВ в РЭМ микроскопе марки JEOL 5610 LV вместе с ЭДС-анализом. Было установлено, что по мере увеличения содержания Mg, происходило прогрессирующее собирание и кластеризация различных интерметаллидов и непрореагировавшего (т.е., свободной формы,) Mg в областях, прилегающих к границам зерен. Это можно видеть на ОМ-изображениях, где наблюдается изменение морфологии зернограничных регионов. Эти интерметаллиды испытывали, в основном, вытеснение на границы зерен, где они и аккумулировались по мере развития затвердевания. Это явление аккумуляции наблюдалось вплоть до случая, отвечавшего 3 вес. % Mg, и при содержании Mg более 3 вес. % оно становилось весьма ощутимым. Это привело к изменениям в толщине и характере непрерывности зернограничных регионов материала, что отражено на рис. 4. Аккумуляция непрореагировавшего Mg также наблюдалась наряду с формированием других интерметаллических фаз. Это происходило вследствие ограниченной растворимости Mg в Al при его содержании больше 3 вес. %, если судить по равновесной диаграмме состояний системы Al–Mg, как показано на рис. 5. Равновесная диаграмма состояний системы Al–Mg показывает изменение растворимости Mg в Al с температурой. Эта растворимость Mg в Al уменьшается ниже его значений в 3 вес. %, когда температура падает до 100°С, тогда как выше 300°С все 7 вес. % Mg могут оказаться растворенными, как показано стрелочками на рис. 5. Максимальная растворимость от 17 до 18 вес. % может быть достигнута при 450°С, если судить по равновесной диаграмме состояний. В исследуемой нами Al–Mg-системе, количество непрореагировавшего Mg, имевшегося при комнатной температуре, увеличивалось по мере роста концентрации Mg выше значения 3 вес. %. Этот непрореагировавший Mg мог выступать как место смачиваемости керамических частиц во время образования дисперсных армированных композитов на основе металлической матрицы [15].
Рис. 4.
Микроструктура (a) Al и непротравленных образцов Al–Mg-сплавов, (б) 1 вес. % Mg, (в) 3 вес. % Mg, (г) 5 вес. % Mg и (д) 7 вес. % Mg при ×100.
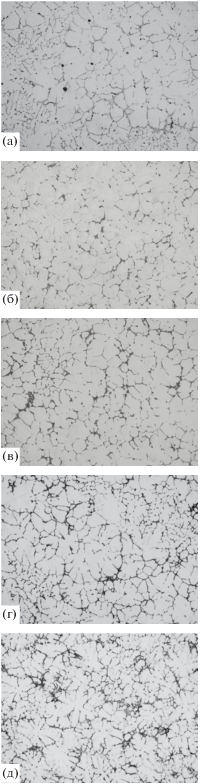
Результатом аттестации микроструктур сплавов системы Al–Mg в литом состоянии стало обнаружение бездефектных зеренных структур. Как видно на рис. 6, представленная зеренная структура и различные интерметаллиды, такие как Mg2Si, Al2Mg, Al2Si и др., наблюдаются как регионы светло-серого и белого контуров. Стехиометрия интерметаллидов подтверждается соответствующими данными ЭДС-анализа. Анализ микроструктуры также выявил, что столбчатые зерна отсутствовали, а взамен их возникли структуры почти равноосных зерен. Это явилось следствием существенного предварительного нагрева металлической формы до розлива в нее расплава, что снизило значение температурных градиентов при его затвердевании. Во всех случаях, наблюдения микроструктуры производили на Al–Mg-образцах в их непротравленном состоянии.
3.2. Аттестация механических свойств
В данной работе указанная аттестация проводилась для установления значений таких свойств материала, как твердость, прочность, пластичность и удельный вес.
3.2.1. Твердость. Измерение твердости по Бринелю осуществляли при нагрузке 15.625 кгс на образцах литых сплавов с разным содержанием Mg. Результаты представлены на рис. 7. Они показывают, что величина BHN непрерывно увеличивается по мере роста содержания Mg в сплавах системы Al–Mg. Это происходит из-за того, что плотность числа дислокаций постоянно растет, при том, что значение твердости интерметаллидов Mg2Si очень велико [16–19]. Более высокая плотность дислокаций литых сплавов системы Al–Mg генерируется во время затвердевания расплава в постоянно используемой (ПИ, металлической) форме вследствие разницы КТР коэффициентов Al, Mg2Si и других образующихся интерметаллических фаз. Наряду с этим, эффект охлаждения и более высокая скорость отвода тепла приводят к “оформлению” металла в виде жидкой массы в процессе и после розлива расплава в ПИ-форму, тогда как литье также ответственно за улучшение итоговых показателей твердости.
Рис. 7.
Вариация числа твердости по Бринелю (BHN) в зависимости от содержания Mg в сплавах системы Al–Mg.
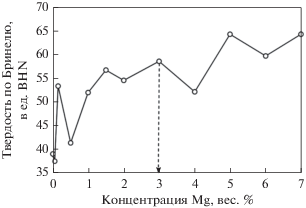
3.2.2. Прочность. Вариации предела прочности на растяжение и удельной прочности (отношения “прочность/удельный вес”) с изменением содержания Mg представлены на рис. 8. Прочность непрерывно возрастала до 3 вес. % Mg и затем уменьшалась с ростом содержания Mg. Главной тенденцией Mg являлось его сегрегирование на границах зерен (i) – вплоть до 3 вес. % Mg – в связанном виде (в виде интерметаллидов) и (ii) – свыше 3 вес. % Mg – в свободном (непрореагированном) виде. Это явление приводит к эффекту твердорастворного упрочнения. Mg также действует как активатор формирования ячеистой (дислокационной) структуры, что приводит к росту механических свойств сплавов системы Al‒Mg [20]. Взаимодействие между дислокациями и атомами растворенного элемента играет в Al–Mg-сплавах главенствующую в упрочнении материала роль, поскольку ограничивает подвижность дислокаций. Имеется два пути повышения прочности Al–Mg-сплавов за счет введения добавок Mg. Один путь – прямой т.е., непосредственно за счет взаимодействия между дислокациями растворенных атомов и дислокаций. Он означает образование атмосфер Котрелла на дислокациях, что препятствует их (свободному) перемещению в материале. Другой путь – опосредованный, т.е. косвенный, выражающийся в затруднении перемещения дислокаций при деформировании материала. В обоих этих случаях имеет место рост плотности числа дислокаций и предела прочности при растяжении (ППР) Al–Mg-сплавов за счет взаимодействия дислокаций между собой [21].
Рис. 8.
Вариации предела прочности на растяжение (UTS) и удельной прочности с изменением содержания Mg в сплавах системы Al–Mg.
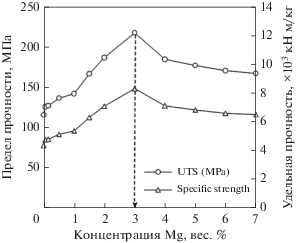
ППР (UTS) и удельная прочность демонстрируют свой максимум при 3 вес. % Mg, поскольку отношение числа интерметаллидных частиц к числу атомов (и кластеров) непрореагировавшего Mg оказалось довольно большим при 3 вес. % Mg. После 3 вес. % Mg, рост его содержания в материале приводит к снижению как UTS, так и удельной прочности. Это – следствие эффекта непрореагировавшего Mg, локализованного по границам зерен сплавов системы Al–Mg. Присутствие некоторых хрупких интерметаллидов также отрицательно сказывается на всей структуре и всех свойствах указанных материалов.
3.2.3. Плотность и пластичность материала. Взаимосвязь плотности материала и его пластичности при изменении содержания Mg графически представлена на рис. 9. Низкий удельный вес Mg в сравнении с Al ответственен за общее снижение удельного веса сплавов системы Al–Mg. Даже если материнские металлы, т.е. Al и Mg являются вполне пластичными, суммарная пластичность любого сплава системы Al–Mg в его литом состоянии оказывается ниже исходных значений его компонентов. Это является результатом избыточного упрочнения, приводящего к деформационному упрочнению материала и к формированию в нем хрупких интерметаллидов, сосредоточенных по границам зерен. Морфология таких хрупких фаз также существенно сказывается на удельном весе и пластичности материала.
4. ВЫВОДЫ
1. Al–Mg, Mg–Si, Al–Si интерметаллиды обнаружили свое равномерное распределение по границам зерен вплоть до содержания Mg 3 вес. %. Непрореагировавший Mg, наряду с интерметаллидами, наблюдался и при его содержании выше 3 вес. %, что отрицательно сказалось на различных свойствах сплавов системы Al–Mg.
2. Как предел прочности при растяжении, так и удельная прочность оказались максимальны при 3 вес. % Mg. Для более высоких значений содержания Mg, в силу ограниченной растворимости Mg в Al, характерно наличие непрореагировавшего Mg, локализовавшегося и накапливавшегося по границам зерен. Это в конечном итоге привело к потере прочности зеренными границами.
3. Число прочности по Бринелю (BHN/HB) для сплавов системы Al–Mg неуклонно возрастало с ростом содержания Mg из-за образования и сосредоточения интерметаллидов на границах зерен в процессе синтеза материала.
4. Как удельный вес, так и пластичность снижались по мере роста содержания Mg в сплавах системы Al–Mg. Так как плотность Mg ниже, чем Al, это приводит к общему понижению удельного веса системы. Вместе с этим из-за хрупкости отдельных интерметаллидов и роста вследствие этого некоего эффекта концентрации внутренних напряжений сама пластичность системы снижалась.
5. Содержание Mg 3 вес. % в Al оказалось оптимальным из-за хорошего сочетания различных микромеханических свойств, таких как особенности микроструктуры, ППР (UTS), удельная прочность, твердость, невысокий удельный вес и пластичность материала. Поэтому сплав Al–3 вес. % Mg вполне отвечает требованиям низкой себестоимости производства, и среди всех сплавов системы Al–Mg обладает наиболее высокими возможными металлургическими и механическими свойствами.
Список литературы
Das S., Monda lD.P., Sawla S., Ramakrishnan N. Synergic effect of reinforcement and heat treatment on the two body abrasive wear of an Al–Si alloy under varying loads and abrasive sizes // Wear. 2008. V. 264. № 1. P. 47–59.
Rana R.S., Rajesh Purohit. Effect of magnesium enhancement on mechanical property and wear behavior of LM6 aluminum alloy // Intern. J. Scie. Eng. Research, 2012. V. 3. № 7.
Feng Yan, Shou Xun Ji, Zhong Yun Fan. Effect of excess Mg on the microstructure and mechanical properties of Al−Mg2Si high pressure die casting alloys // Mater. Sci. Forum, 2013. V. 765. P. 64–68.
Joseph R. Davis. Corrosion of aluminum and aluminum alloys. ASM International, 1999.
Lucio F. Mondolfo. Aluminum alloys: structure and properties. Elsevier, 2013.
Alieva S.G., Altman M.B., Ambartsumyan S.M., Kvasov F.I., Fridlyander I.N., Belov A.F. Industrial aluminum alloys. Moscow: Metallurgiya. 1984.
Dr. Sharma K.V., Girisha H.N. Effect of Mg and unidirectional solidification on strength and microstructure of Al–Cu–Mg alloy // Intern. J. Sci. Eng. Research. 2013. V. 3. P. 171–174.
Abdulhaqq A. Hamid, Jain S.C., Ghosh P.K., Subrata Ray. Processing, microstructure, and mechanical properties of cast in-situ Al(Mg, Mn)−Al2O3(MnO2) composite // Metal. Mater. Trans. A. 2005. V. 36. № 8. P. 2211–2223.
Rana R.S., Purohit Rajesh, Das S. Reviews on the influences of alloying elements on the microstructure and mechanical properties of aluminum alloys and aluminum alloy composites. 2012.
Agrawal Lucky, Yadav Rakesh, Sexena Abhishek. Effect of magnesium content on the mechanical properties of Al–Zn–Mg alloys // Intern. J. Emerging Techn. 2012. V. 3. № 1. P. 137–140.
Md Habibur Rahman, HMMA Rashed. Effect of magnesium on wear characteristics of silicon carbide and alumina reinforced aluminum-metal matrix composites // Intern. J. Sci. Eng. Research. 2014. V. 5. P. 1210–1213.
Luo Zhiping, Zhang Shaoqing. Comment on the so-called Z-phase in magnesium alloys containing zinc and rare-earth elements // J. Mater. Sci. Letters. 1993. V. 12. № 19. P. 1490–1492.
Zhang J., Fan Z., Wang Y.Q., Zhou B.L. Microstructure and mechanical properties of in situ Al−Mg2Si composites // Mater. Sci. Technology. 2000. V. 16. № 7–8. P. 913–918.
Arun M., Salim N., Kumar A. Effect of Mg enhancement in the microstructure and mechanical properties of AC2A Al alloy // Intern. J. Research in Eng. Techn. 2014. V. 2. № 2. P. 139–148.
Kainer K.U. Aluminum and magnesium based metal matrix composites // Kovine, zlitine, technologije. 1996. V. 30. № 6. P. 509–516.
Zhang J., Fan Z., Wang Y.Q., Zhou B.L. Equilibrium pseudobinary Al−Mg2Si phase diagram // Mater. Sci. Technology. 2001. V. 17. № 5. P. 494–496.
Zhang J., Fan Z., Wang Y.Q., Zhou B.L. Microstructural evolution of the in situ Al–15 wt. % Mg2Si composite with extra Si contents // Scripta Mater. 2000. V. 42. № 11. P. 1101–1106.
Lü Y.Z., Wang Q.D., Zeng X.Q., Zhu Y.P., Ding W.J. Behavior of Mg–6Al–xSi alloys during solution heat treatment at 420°C // Mater. Sci. Eng.: A. 2001. V. 301. № 2. P. 255–258.
Xiaoping Niu, Li Lu. Formation of magnesium silicide by mechanical alloying // Adv. Perf. Mater. 1997. V. 4. № 3. P. 275–283.
Vandana J. Rao. Optimization of magnesium metal into commercially pure aluminum // Intern. J. Eng. Research Appl. 2014. V. 4. № 2. P. 413–415.
Gubicza Jen, Chinh Nguyen Quang, Horita Z., Langdon T.G. Effect of Mg addition on microstructure and mechanical properties of aluminum // Mater. Sci. Eng.: A. 2004. V. 387. P. 55–59.
Дополнительные материалы отсутствуют.
Инструменты
Физика металлов и металловедение