Физика металлов и металловедение, 2020, T. 121, № 1, стр. 37-47
Зарождение и рост выделений в микролегированной ванадием стали: физическая теория и экспериментальные результаты
С. Ф. Медина a, *, П. Валлес b, Джессика Кальво c, Хосе М. Кабрера c
a Национальный научно-исследовательский центр металлургии (CENIM),
Высший совет по научным исследованиям (CSIC)
Мадрид, Испания
b Национальный институт аэрокосмической техники (INTA), Торрехон-де-Ардос
Мадрид, Испания
c Высшая техническая школа промышленного строительства Барселоны (ETSEIB),
Политехнический университет Каталонии (UPC)
Барселона, Испания
* E-mail: smedina@cenim.csic.es
Поступила в редакцию 07.02.2018
После доработки 17.10.2018
Принята к публикации 09.08.2019
Аннотация
Представлены полученные в рамках теоретического подхода результаты расчета числа зародышей и продолжительности инкубационного периода их возникновения в слаболегированной стали с микродобавками ванадия. Рассчитанные данные позволяют построить графики температурной зависимости числа зародышей, критического времени зарождения (инкубационного периода их возникновения) и критического радиуса выделений второй фазы. Полученное число зародышей было рассчитано путем интегрирования выражения для скорости их зарождения. С другой стороны, было проведено экспериментальное исследование и построена температурная зависимость продолжительности инкубационного периода (С-диаграмма). Это позволило сравнить теоретически полученные значения и экспериментальные результаты. Было установлено, что рост частиц второй фазы в процессе выделения подчиняется квадратичному, а не кубическому закону роста, который наблюдается при коалесценции. Экспериментально определенная скорость роста совпадает с предсказанной теоретически. Экспериментальная величина инкубационного периода оказалась больше, чем рассчитанная теоретически из-за концептуальных различий.
ВВЕДЕНИЕ
Микролегированные стали содержат малые количества Nb и/или V, и в меньшей степени Ti, который в сочетании с C и N склонен выпадать в виде карбидов, нитридов и карбонитридов. Эти выделения модифицируют конечную микроструктуру, получаемую в процессе горячего деформирования стали, благоприятствуя измельчению ее зерна, и таким образом влияют на ее механические свойства. Измельчение ферритного зерна достигается посредством предварительного твердения аустенита из-за того, что указанные выделения блокируют статическую рекристаллизацию и способствуют росту пространственной плотности дислокаций, а также зарождению феррита при охлаждении материала после деформации [1–3].
Параллельное развитие процессов рекристаллизации и выделения изучают многие исследователи – от влияния различных параметров при горячем деформировании до создания моделей, которые прогнозируют процесс как рекристаллизации, так и выделения, или оба [4–9]. Однажды зародившись, выделения второй фазы могут увеличиваться в размерах как при росте, так и при огрублении или коалесценции [10]. Оба явления могут протекать одновременно, хотя и, как будет далее показано в этой работе, будут зависеть от температуры и времени.
На примере литературных источников можно продемонстрировать, что нет единого мнения по возможности одновременного протекания процессов роста и коалесценции выделений. Некоторые авторы на основе конкретных примеров указывают, что оба этих явления не могут происходить в одно и то же время [11–13], тогда как другие авторы указывают на одновременность обоих [14, 15]. Как можно видеть, вопрос, происходит ли укрупнение одновременно с ростом, является предметом научной дискуссии.
В рамках классической теории зарождения [16–18], для, V-микролегированной (ванадием) стали, были теоретически рассчитаны кривая начала процессов выделения, средний радиус зародышей фазы выделения (ФВ) и скорость роста частиц этой ФВ. Мы надеемся, что сравнение в данной работе результатов, полученных теоретическим и экспериментальным путем, их анализ в рамках эмпирической модели, предложенной С. Ф. Мединой с соавторами в [19], облегчат понимание процессов выделения в V-микролегированной стали в их как теоретическом, так и экспериментальном аспектах.
МАТЕРИАЛ ИССЛЕДОВАНИЯ
Выбранная для исследования сталь была получена методом непрерывного литья, с последующей горячей прокаткой. Ее химический состав дан в табл. 1, в которой также приведена температура начала γ → α-превращения при охлаждении (Ar3), определенная по данным дилатометрии при скорости охлаждения 0.2 K/с и являющаяся минимальной температурой, при которой будут рассчитаны различные параметры, характеризующие “выделение” аустенитной фазы.
РЕЗУЛЬТАТЫ И ОБСУЖДЕНИЕ
Используя подход Зельдовича, Кампаманна и Вагнера [18, 20], в рамках классической теории зарождения частиц второй фазы можно получить следующее выражение для скорости их зарождения:
(1)
$\frac{{dN}}{{dt}} = {{N}_{0}}Z\beta {\kern 1pt} '\exp \left( { - \frac{{\Delta G}}{{kT}}} \right)\left( {1 - \exp \frac{{ - t}}{\tau }} \right).$Здесь N0 представляет число потенциальных мест для гетерогенного зарождения, Z – фактор Зельдовича для учета неравновесности процесса, k – постоянная Больцмана (1.38065 × 10–23 Дж/K), β' – скорость подвода атомов (СПА) легирующего элемента к поверхности критического зародыша фазы выделения, T – абсолютная температура, τ – инкубационный период, ΔG – энергия Гиббса для образования критического сферического зародыша радиуса Rc.
Интегрирование уравнения (1) по времени в пределах от 0 до τ дает число зародышей, сформировавшихся за время, по продолжительности равное инкубационному периоду, до того как они начнут увеличиваться в размерах по мере развития процессов выделения. Результат интегрирования имеет вид:
(2)
$\begin{gathered} N = {{N}_{0}}Z\beta {\kern 1pt} '\exp \left( { - \frac{{\Delta G}}{{kT}}} \right)\left[ {t + \tau \exp \left( { - \frac{t}{\tau }} \right)} \right]_{0}^{\tau } = \\ = {{N}_{0}}Z\beta {\kern 1pt} '\exp \left( { - \frac{{\Delta G}}{{kT}}} \right)\left( {\frac{\tau }{{2.718}}} \right), \\ \end{gathered} $Энергия Гиббса (ΔG) для формирования сферического зародыша карбонитрида из элементов раствора (в нашем случае – ванадия, V), в рамках классического подхода выражается в виде суммы химической свободной энергии, поверхностной составляющей свободной энергии и энергии ядра дислокации. Она может быть представлена в следующем виде [10, 16, 21]:
(3)
$\Delta G = \frac{{16\pi {{\gamma }^{3}}}}{{3\Delta G_{v}^{2}}} + 0.8\mu {{b}^{2}}\frac{\gamma }{{\Delta {{G}_{v}}}}.$Равновесие между аустенитной матрицей и карбонитридом VCyN1 – y описывается законом действующих масс [14]:
(4)
$\begin{gathered} \Delta {{G}_{v}} = \\ = - \frac{{{{R}_{{\text{g}}}}T}}{{{{V}_{{\text{m}}}}}}\left[ {\ln \left( {\frac{{X_{{\text{V}}}^{{{\text{ss}}}}}}{{X_{{\text{V}}}^{{\text{e}}}}}} \right) + y\ln \left( {\frac{{X_{{\text{C}}}^{{{\text{ss}}}}}}{{X_{{\text{C}}}^{{\text{e}}}}}} \right) + (1 - y)\ln \left( {\frac{{X_{{\text{N}}}^{{{\text{ss}}}}}}{{X_{{\text{N}}}^{{\text{e}}}}}} \right)} \right], \\ \end{gathered} $Карбонитрид рассматривали как идеальную “смесь” карбида VC и нитрида VN, параметры $y;{\text{ }}X_{{\text{V}}}^{{\text{e}}};{\text{ }}X_{{\text{C}}}^{{\text{e}}};{\text{ }}X_{{\text{N}}}^{{\text{e}}}$ определяли с использованием компьютерной программы FactSage [22, 23]. Переменная “y” в уравнении (4) принимает значения отношения VC/VCN объемных долей карбида VC и карбонитрида VCN, а переменная “1 – y” – значения отношения VN/VCN объемных долей VN и VCN, здесь VCN = VC + VN.
С другой стороны, N0 = 0.5Δρ1.5 есть число “узлов” дислокационной сетки, Δρ = (Δσ/0.2μb)2 – изменение “пространственной” плотности дислокаций, связанное с движением фронта рекристаллизации в деформированной зоне в момент “старта” процессов выделения [10], Δσ – разность между величинами напряжения течения и предела текучести при конкретной температуре деформирования.
Скорость подвода атомов V к поверхности зародыша фазы выделения определяется как в [16]:
(5)
$\beta {\kern 1pt} ' = \frac{{4\pi R_{{\text{c}}}^{2}{{D}_{{\text{V}}}}{{C}_{{\text{V}}}}}}{{{{a}^{4}}}},$(6)
${{D}_{{{\text{eff}}}}} = {{D}_{p}}\pi R_{{{\text{core}}}}^{2}\rho + {{D}_{{\text{V}}}}(1 - \pi R_{{{\text{core}}}}^{2}\rho ),$Коэффициент эффективной диффузии используется также вместо коэффициента объемной диффузии для определения скорости роста выделений, потому что на росте частиц ФВ сильно сказывается подвод легирующего компонента по дислокациям, на которых зарождаются выделения [15].
Фактор Зельдовича Z принимает в расчет то, что зародыш второй фазы подвержен дестабилизации в условиях повышенных температур, когда существенны атомные флюктуации. Этот фактор представим в виде [24]
(7)
$Z = \frac{{V_{{{\text{at}}}}^{{\text{p}}}}}{{2\pi R_{{\text{с}}}^{2}}}\sqrt {\frac{\gamma }{{kT}}} ,$Прирост величины напряжения течения Δσ был рассчитан в рамках модели Медины и Эрнандеса (Hernández), специально предназначенной для учета такой поправки [25]. Плотность дислокаций была рассчитана по температуре TN кривой Ps, отвечающей относительной деформации 0.35. При недеформированном аустените плотность дислокаций (ПД) составляет примерно 1012 м–2 [26], а ПД, соответствующая точке (tN, TN) кривой начальной стадии (~5%) выделения Ps (t, T), будет равняться 1012 + Δρ.
С другой стороны, сомножитель (1 – exp(–t/τ)) в (1) – указывает на прогресс скорости зарождения, но большинство авторов это не учитывают вследствие малости инкубационного периода.
В уравнении (1) выражение для инкубационного периода (τ) имеет вид [27]:
Критический радиус зародыша ФВ определяется из движущей силы превращения и выражается как [14]:
Очевидно, что способный к росту зародыш ФВ должен иметь размер больший, чем у критического зародыша. В соответствии с данными работ [10] и [28], эта величина умножается на фактор 1.05. Необходимо отметить, что множитель 1.05 слабо сказывается на характере кинетики выделения в целом.
Во время выделения, и при критическом размере зародышей фазы выделения (ЗФВ), определяемом (9) и умноженном на 1.05, имеет место рост ЗФВ, начинающийся сразу по истечении инкубационного периода, определяемого (8). Из уравнения массового баланса (закона сохранения вещества) на МФГ матрица/выделение следует классическое выражение Зинера (Zener) для скорости роста выделения радиуса R [14]:
(10)
$\frac{{dR}}{{dt}} = \frac{{{{D}_{{{\text{eff}}}}}}}{R}\frac{{X_{{\text{V}}}^{{{\text{ss}}}} - X_{{\text{V}}}^{i}}}{{\frac{{{{V}_{{{\text{Fe}}}}}}}{{{{V}_{{\text{p}}}}}} - X_{{\text{V}}}^{i}}}.$Здесь VFe – молярный объем аустенита, Vp – молярный объем фазы выделения, $X_{{\text{V}}}^{i}$ – молярная доля ванадия на МФГ.
Углерод и азот, будучи химическими элементами внедрения, обладают более высокой диффузионной подвижностью в сравнении с атомами ванадия. Как результат, рост частицы ФВ контролируется диффузией ванадия из матрицы в выделение. В процессе изотермической обработки, инициирующей процессы выделения, содержание ванадия в твердом растворе (в матрице стали) $X_{{\text{V}}}^{{{\text{ss}}}}$ снижается, и следовательно, уменьшается скорость роста выделений. Между тем количество атомов ванадия(V), локализованных вблизи МФГ, возрастает.
Интегрирование уравнения (10) дает зависимость радиуса выделений от времени в виде
(11)
${{R}^{2}} = R_{0}^{2} + 2{{D}_{{{\text{eff}}}}}\frac{{X_{{\text{V}}}^{{{\text{ss}}}} - X_{{\text{V}}}^{i}}}{{\frac{{V{}_{{{\text{Fe}}}}}}{{{{V}_{{\text{p}}}}}} - X_{{\text{V}}}^{i}}}t,$Коалесценция – процесс, при котором мелкие выделения растворяются в “пользу” крупных, что приводит к огрублению (распределения по размерам) подсистемы частиц ФВ. Это явление особенно важно, когда объемная доля ФВ близка к равновесной. Нужно отметить, что такое огрубление может наблюдаться на всех этапах процесса выделения [14]. Последний же этап известен как Оствальдовское созревание. Изменение среднего размера выделений описывается выражением Лифшица и Слёзова [29, 30]:
(12)
${{R}^{3}} = R_{0}^{3} + \frac{{8{{D}_{{\text{V}}}}\gamma V_{p}^{2}X_{{\text{V}}}^{i}}}{{9{{R}_{{\text{g}}}}T}}t,$Замечательной особенностью (12) является то, что куб среднего радиуса R (в ближайшем контексте $\bar {R}$) частиц фазы выделения изменяется линейно со временем, тогда как для кинетики их роста линейность от времени характерна для квадрата ${{\bar {R}}^{2}}(t)$. Коалесценция выделений, таким ообразом, является значительно более медленным процессом в сравнении с их огрублением на стадии роста. Это вполне понятно, поскольку огрубление дисперсной подсистемы на стадии коалесценции происходит посредством роста одних частиц за счет растворения других. ЛСВ теория также предсказывает, что распределение (ФР) частиц по относительным размерам (R/Rc) на стадии коалесценции стремится к постоянной ФР, ограничением частиц по размерам ${{R}_{{\max }}} = 1.5\bar {R}.$
Расчет фазовых равновесий и термодинамических свойств с привлечением программного пакета FactSage позволяет спрогнозировать кинетику выделения как простых (нитриды и карбиды), так и более сложных (карбонитриды) частиц второй фазы. Соответствующие результаты могут быть представлены в виде зависимости весовой доли этих частиц от температуры. Так, на рис. 1 приведена зависимость парциальных долей частиц AlN, CV, VN и суммарной доли частиц CVN от температуры. Эти результаты суть термодинамические предсказания и на них не следует смотреть как на реальные, получаемые при конкретных температурах деформации на эксперименте. Выделившаяся доля AlN частиц превышает соответствующие значения для VCN – вплоть до 1323 K (1050°C), и при более низких температурах суммарный объем AlN фазы перестает играть определяющую роль. При этом частицы AlN начинают выделяться до появления CVN, приблизительно при 1403 K (1130°C). Объем выделения AlN частиц невелик, и его результат совпадает с установленным другими авторами для относительно невысокого содержания алюминия, как и в нашем случае, Al ~ 0.026 вес. % [30, 31].
Рис. 1.
Равновесные выделения в исследованной стали, предсказанные при использовании программного FactSage.
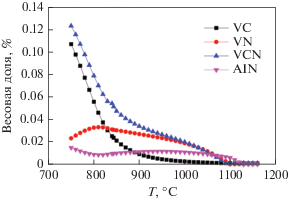
На рис. 2 приведена зависимость числа выделений (N) от температуры в соответствии с уравнением (2), при значении инкубационного периода, определяемом согласно (8). Величина N возрастает по мере уменьшения температуры, однако только до истечения инкубационного периода, поскольку после его окончания происходят возможное растворение тех частиц, радиус которых оказался меньше критического, и возможное огрубление устойчивых частиц, что приведет к уменьшению числа N. Принятие в расчет энергии ядра дислокаций и эффективного значения коэффициента диффузии (Deff) – вместо только коэффициента объемной диффузии (Dbulk), – приводит к значительному увеличению N [20, 24].
На рис. 3 приведены значения инкубационного периода (τ) как функция температуры. Поскольку в выражении (4) при расчете энергии вместо объемной диффузии (ОД) была взята эффективная, величины τ оказались меньше. Следует сказать, что достигнутые минимальные значения времени зарождения соответствовали температурам, близким к 1273 K (1000°C). Критический радиус (Rc) для зарождения был рассчитан, исходя из (9), как функция температуры (рис. 4).
Окончательно, для описания стадий роста и коалесценции были использованы уравнения (11) и (12), выделяя в них температуру 1273 K (1000°C), соответствующую точке реверса С-траектории, пробегаемой конфигурационной точкой (t, T) по Ps кривой начальной стадии выделения (рис. 3). Время (t) отсчитывали от момента окончания инкубационного периода, составлявшего при этой температуре 4.5 с. Величина R0 равна 0.78 нм (рис. 4), умноженной на 1.05. Результаты представлены на рис. 5, где можно видеть, что использование для стадии роста квадратичного закона изменения радиуса выделений (11) позволяет предсказать прирост в их размере.
Однако модель коалесценции с кубическим законом роста (12) не предсказывает прироста размера выделений. Он остается практически неизменным вследствие того факта, что величина коэффициента Deff очень сильно зависит от температуры, и его рассчитанное значение 5.22 × 10–16 м2 с–1, отвечающее температуре 1000°C, относительно низкое.
Конечный момент выделений задается осажденной фракцией (рис. 1), и итоговый радиус выделений определяется простым расчетом при учете плотности фазы выделения (6000 кг/м3) и аустенита (8150 кг/м3). Этот расчет показывает, что большая часть выделений не растет, особенно когда температура понижается и они опять подвержены растворению.
Если бы это было не так, и все возникающие зародыши второй фазы росли, доля выделяющейся фазы была бы значительно больше, чем та, что соответствует ее весовому проценту (рис. 1). Согласно работе [32], имеет место постепенный переход от стадии зарождения–роста к стадии роста–коалесценции. Его простым критерием является условие, что убыль плотности частиц (n) за счет их коалесценции больше, чем прирост за счет их зарождения, т.е.
(13)
$ - {{\left. {\frac{{dN}}{{dt}}} \right|}_{{{\text{рост}} + {\text{коалесц}}}}} > {{\left. {\frac{{dN}}{{dt}}} \right|}_{{{\text{зарождение}}}}}.$Образцы для тестов на кручение имели длину рабочей части 50 мм и диаметр 6 мм. Аустенитизацию проводили при 1473 K (1200°C) в течение 10 мин. Статически рекристаллизованная доля материала была определена для нескольких температур из интервала от 1373 K (1100°C) до 1073 K (800°C) по методике “двукратного деформирования” и, в частности, методом “экстраполяции назад” [5].
Сравнение рис. 2 и рис. 3 показывает, что число сформировавшихся зародышей как функция температуры мало в точке реверса траектории (TN = 1273 K; 1000°C). Иными словами, теоретически рассчитанное время зарождения несколько больше, или на формирование зародышей при температуре TN должно уходить чуть больше времени. Расчеты были проведены с параметрами, указанными в табл. 2.
Таблица 2.
Параметры, использованные при вычислениях
Параметр | Символ | Величина | Источник |
---|---|---|---|
Модуль вектора Бюргерса | b (м) | 2.59 × 10–10 | [10] |
Модуль сдвига | μ (МПа) | 4.5 × 104 | [10] |
Удельная энергия МФГ | γ (Дж м–2) | 0.5 | [14], [16] |
Параметр решетки “фазы” VCN | a (нм) | 0.4118 | [15] |
Коэффициент объемной диффузии V | Dbulk (м2 с–1) | 0.28 × 10–4exp(–264 000/RT) | [29] |
Коэффициент диффузии по дислокациям | Dp (м2 с–1) | 0.25 × 10–4exp(–210 000/RT) | [15] |
Молярный объем “фазы” VCN | VP (м3 моль–1) | 10.65 × 10–6 | [14] |
Молярный объем аустенита | VFe (м3 моль–1) | 7.11 × 10–6 | [14] |
Радиус ядра дислокаций | Rcore (м) | 5.00 × 10–10 | [16] |
Молекулярный объем (фазы) выделения | $V_{{{\text{at}}}}^{{\text{p}}}$ (м3) | 1.7468 × 10–29 | [26] |
Зависимость доли (Xa) рекристаллизованного объема материала от времени была построена. Полученные кривые (рис. 6) соответствуют относительной деформации материала 0.35. Статическая рекристаллизация (SRX) происходила после горячей деформации материала, тогда как напряжение или относительной деформации были ниже критической величины для начала динамической рекристаллизации (DRX) [33].
Рис. 6.
Доля рекристаллизованного объема как функция времени. Относительная деформация = 0.35; Температура повторного нагрева = 1200°C.
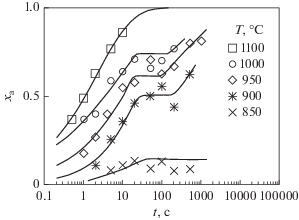
Кривые, соответствующие температурам равным или ниже 1273 K (1000°C), демонстрируют плато – задержку рекристаллизации – из-за деформационно-индуцированного выделения частиц V(C,N). Кривая, у которой нет плато, имеет S-образный профиль, характерный, как правило, для закона Аврами.
Длина этого плато ограничена, и после короткого инкубационного периода развивается повторная рекристаллизация, пока не достигнет завершения. Возобновление рекристаллизации происходит, по сути, вследствие ослабления сил закреплению дислокаций частицами ФВ, которые подрастают в результате развития процессов выделения на фоне сохранения тенденций к рекристаллизации. Начало и конец плато приблизительно соотносят с началом и окончанием процессов выделения. Традиционно принято оценивать 5% объемной доли фазы выделения как “начало” процесса выделения и 95% как “конец” [34].
Известно, что как только плато заканчивается, возобновляется и процесс рекристаллизации. Силы закрепления дислокаций частицами ФВ теперь оказываются меньше стимула к развитию рекристаллизации. Кривые зависимости доли рекристаллизованного объема от времени были использованы для построения диаграммы выделение–температура–время (PTT) для исследуемой нами стали [34]. Точки, определяющие “начало” и “конец” плато, были использованы для построения кривых начальной Ps и конечной Pf стадий выделения. Именно таким образом была получена PTT диаграмма при относительной деформации (ε) 0.35 и скорости деформирования ($\dot {\varepsilon }$) 3.63 с–1, как показано на рис. 7.
Наиболее важные параметры, которые можно извлечь из PTT диаграммы и знание которых нельзя переоценить для ее идеального построения, есть ранее упомянутые минимальный инкубационный период (tN), температура TN, отвечающей точке реверса траектории, и время окончания ($t_{{\text{N}}}^{'}$) процесса (95%) выделения при температуре $T_{{\text{N}}}^{'}$ (табл. 3).
Таблица 3.
Данные эксперимента: минимальный инкубационный период (tN), температура в точках “реверса” С-кривых (процесса) выделения (TN) и время достижения 95% доли выделения ($t_{{\text{N}}}^{'}$)
tN (с) | $t_{{\text{N}}}^{'}$ (с) | TN, K (°C) |
---|---|---|
19 | 95 | 1228 (955) |
По достижении кривой конфигурационной точки Pf (t, T), процесс рекристаллизации возобновляется вследствие того факта, что силы закрепления дислокаций на выделениях оказываются меньше термодинамического стимула к его развитию.
По PTT диаграммам, а именно по кривым начальной Ps и конечной Pf и стадий выделения, можно определить временной интервал, какова бы ни была температура, в течение которого в действительности изменяется состояние дисперсной подсистемы (размеры частиц и объем ФВ). При временах после Pf (больших $t_{{\text{N}}}^{'}$), объемная доля ФВ не меняется на фоне развития процесса коалесценции – стадии Оствальдовского созревания.
Начало плато для рекристаллизованной фракции по времени мы соотносим с началом процесса выделения, и его временная протяженность определяется двумя явлениями, наблюдающимися одновременно, а именно, ростом суммарного объема ФВ и размера выделений.
Исследования, проведенные с привлечением просвечивающей электронной микроскопии (ПЭМ), показали скорость, с которой протекало огрубление дисперсной подсистемы, и то, как распределение частиц по размерам изменялось от начала плато до его конца [9]. На рис. 8 представлено ПЭМ-изображение высокого разрешения на углеродных репликах, полученных по экстракционной методике, частиц нитрида ванадия из объема образцов изучаемой стали, прошедших деформацию и закалку в условиях, как указано в подписи к рисунку.
Рис. 8.
ПЭМ изображения: (a) микроструктура образца, протестированного при температуре деформации 950°C с временем выдержки = 20 с. (б) EDAX/ЭДРА спектр (результат энерго-дисперсионного рентгеновского анализа) ФВ. (в) Электронограмма.
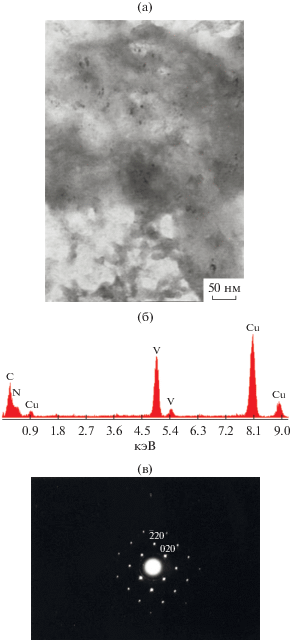
С одной стороны, указанное распределение частиц по размерам и определение среднего размера частиц ФВ были получены путем “обработки” параметров ~200 частиц соответствующего образца. На рис. 9 представлены гистограммы логарифмически нормального распределения, соответствующие временам 20 и 100 с, близким, соответственно, к началу и окончанию плато, со средневзвешенным значением размера (D), равным 6.4 и 9.5 нм и двум пикам частоты, приходящимся на 6 нм в обоих случаях, (табл. 4). С другой стороны, эволюция среднего размера может быть промоделирована как подчиняющаяся закону изменения (11) следующим выражением:
Рис. 9.
Распределение частиц ФВ по размерам для образца, протестированного при температуре повторного нагрева 1200°C в течение 10 мин, при температуре деформации 950°C и времени рекристаллизации 20 и 100 с.
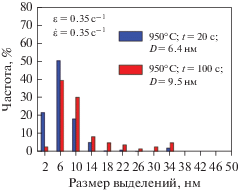
Таблица 4.
Размер (диаметр) выделений при различных временах выдержки после деформации при 950°C
Время выдержки, с | Диаметр, нм |
---|---|
20 | 6.4 |
100 | 9.5 |
Здесь R – средний радиус частиц ФВ ($R = {{\bar {D}} \mathord{\left/ {\vphantom {{\bar {D}} 2}} \right. \kern-0em} 2}$) в метрах, R0 – радиус критического зародыша, M – зависящая от температуры постоянная.
Если мы допустим, что все зародившиеся выделения способны к росту, тогда точка отсчета времени попадает на кривую Ps, а Δt будет соответствовать времени выдержки образца, после Ps.
На рис. 10 представлен рост среднего радиуса выделений при температуре 1223 K (950°C), близкой к экспериментально измеренной TN (1228 K; 955°C). Время выдержки после деформации составляло 20 и 100 с, за вычетом значения времени в точке Ps, соответствовавшей температуре 1223 K (950°C), совпадающим с tN, которое было равно 19 с. В соответствии с уравнением (14), было получено следующее уравнение:
Пользуясь зависимостью (15), для радиуса зародыша (R0) можно получить оценку R0 ~ 3.1 нм. С другой стороны, средний размер индуцированных деформацией выделений AlN (см. рис. 1) почти на порядок больше размера частиц VCN. Более высокая температура растворимости AlN наряду с более высоким коэффициентом диффузии Al в аустените в сравнении с V являются главными причинами большего огрубления AlN частиц. Силы закрепления дислокаций на более грубых частицах фазы выделения AlN слабы и, соответственно, статическая рекристаллизация не испытывает препятствия со стороны этих частиц [35]. Рассчитанный минимальный инкубационный период (tN) был 4.5 с, температура TN – 1273 K (1000°C) (рис. 3). Эксперимент, в свою очередь, дал соответственно 19 с и 1228 K (955°C). Сравнение рассчитанных и экспериментальных значений показывает удовлетворительное совпадение для температуры и большее расхождение во времени инкубации. Тем не менее, эта разница может быть объяснена, если иметь в виду результаты недавней работы Медины с соавторами [36], согласно которой влияние деформации на инкубационный период зависит от содержания легирующих микродобавок, причем оно тем сильнее, чем ниже их содержание.
Другими словами, когда движущая сила для зарождения выделений (ΔGV) велика, т.е. мала по абсолютной величине, деформация, как активатор роста пространственной плотности дислокаций, оказывает заметное влияние на продолжительность инкубационного периода. Когда же указанная движущая сила, напротив, мала (т.е. велика по абсолютной величине), деформация утрачивает свое влияние на продолжительность инкубационного периода, и гомогенное зарождение имеет преимущество над гетерогенным зарождением.
Рассчитанное с помощью (4) значение ΔGv при температуре TN = 1228 K (955°C) равно –1.554 × × 109 Дж м–3. Согласно Медине с соавторами [19, 36], инкубационный период t0.05, соответствующий выделению 5%-ной объемной доли второй фазы (или ФВ), и которая в практическом плане может быть выбрана за величину инкубационного периода для начала процесса выделения, зависит от относительной деформации следующим образом:
где выражение для α имеет вид:(16)
$\alpha = 1.96\left[ {1 - \exp \left( { - 3.994 \times {{{10}}^{{ - 2}}}{{{\left( {\frac{1}{w}} \right)}}^{{0.813}}}} \right)} \right],$Расчет показателя степени с помощью (16) дает значение α = 0.34. Эта величина показывает, что относительная деформация слабо сказывается на длительности инкубационного периода, поскольку она весьма далека от своего максимального значения (α = 2), определенного Мединой с соавторами [19] для сталей с низким содержанием микродобавок. Это обстоятельство говорит скорее в пользу гомогенного, нежели гетерогенного, характера зарождения выделений второй фазы [36].
С другой стороны, рассчитанный и экспериментально определенный инкубационные периоды имеют не одинаковый смысл. Рассчитанное значение имеет смысл времени, необходимого для формирования N зародышей ФВ размером R0, чей рост продолжается, когда их радиус достигает величины 1.05 × R0. Экспериментально измеренное значение относится к времени, необходимому для того, чтобы силы, закрепляющие дислокации на выделениях, превысили бы (по своей величине) движущие силы для (инициации) рекристаллизации и, тем самым, временно затормозили бы ее развитие. Логично считать, что “экспериментальный” инкубационный период всегда будет протяженнее в сравнении с рассчитанным временем “задержки”.
Средний, экспериментально определенный радиус зародыша 3.1 нм при 1223 K (950°C) больше, чем радиус зародыша 0.8 нм, получившийся при теоретически рассчитанном “пункте реверса”. Хотя обсуждаемые величины одного и того же порядка, опять необходимо напомнить о принципиальной разнице между теоретической и экспериментальной Ps кривыми.
Экспериментальная зависимость (15) показывает, что рост размера частиц второй фазы с момента начала процесса выделения (кривая Ps) до его окончания (кривая Pf) может быть описан с помощью уравнения роста с тангенсом угла наклона прямой 0.015 × 10–1. С другой стороны, на интервале изменения продолжительности выдержки от 20 до 100 с измеренный радиус выделений (табл. 4) изменился от 3.2 до 4.7 нм, т.е. на 1.5 нм. Если на рис. 5 отметить точки, соответствующие значениям времени 20 и 100 с за вычетом (в обоих случаях) инкубационного периода (4.5 с), то становится ясно, что исходный радиус выделений возрос с 2.5 до 5.3 нм, что очень близко к экспериментальным значениям. Поэтому с экспериментальной и теоретической точек зрения делается вывод, что увеличение размера выделений в интервале между Ps и Pf может быть предсказано из уравнения роста (11), поскольку коалесценция, описываемая уравнением (12), не имеет места.
И, наконец, другие авторы измерили размеры частиц ФВ VCN в (ванадиевых) V-сталях, сразу после ковки и охлаждения, установив, что 95% частиц имели размеры менее 5 нм, что в нашей работе соответствует стадии начала зарождения выделений второй фазы [37].
В данной работе мы не делаем вывода, что одновременно с ростом выделений происходит и их коалесценция. Утверждается только, что для температуры тестирования 950°C уравнение коалесценции (12) является константой для расчетного времени 200 с. Вместе с тем уравнение роста (11) дает значительное увеличение размера частиц ФВ. С другой стороны, для больших промежутков времени и, особенно, для более высоких температур уравнение (12) привносит заметный вклад. Ряд авторов показали экспериментально, что при высоких температурах аустенитизации, но ниже температуры растворимости, как в случае легированных сталей с микродобавками титана, происходит заметное огрубление осадков [38].
ЗАКЛЮЧЕНИЕ
Теоретически определенные кривые Ps, описывающие начало процесса выделения, отличаются от экспериментальных. Теоретическое и экспериментальное минимальные времена, отвечающие точке реверса этих кривых Ps, составили 4.5 и 19 с соответственно. Такая разница объясняется принципиальным различием между теоретической и экспериментальной Ps кривыми, которое объясняет, почему экспериментальное время зарождения выделений второй фазы всегда больше теоретических значений.
Рассчитанный средний радиус зародыша ФВ составил приблизительно 0.8 нм при температуре, отвечавшей точке реверса теоретической Ps кривой, (1273 K; 1000°C), а экспериментально установленный средний радиус зародыша ФВ составил 3.1 нм при температуре 1223 K (950°C), близкой к TN (1228 K; 955°C), отвечающей точке реверса экспериментальной Ps кривой. Вместе с тем оба радиуса практически совпадают по величине, если определены для выдержки одинаковой продолжительности.
Скорость роста частиц второй фазы между экспериментально определенными Ps и Pf, практически совпадает со скоростью роста, рассчитанной теоретически. Обе указанные скорости подчиняются квадратичному закону роста.
Авторы весьма признательны за финансовую поддержку Испанскому министерству экономики и конкурентоспособности в рамках проекта “ref. MAT2011-29039-C02-02”.
Список литературы
Xu K., Thomas B.G., O’Malley R. Equilibrium model of precipitation in microalloyed steels // Metall. Mater. Trans. A. 2011. V. 42. P. 524–539.
Sellars C.M. Modelling microstructural development during hot Rolling // Mater. Sci. Techn. 1990. V. 6. P. 1072–1081.
Liu W.J. A new theory and kinetic modelling of strain-induced precipitation of Nb (CN) in microalloyed austenite // Metall. Mater. Trans. A. 1995. V. 26. P. 1641–1657.
Gómez M., Medina S.F., Quispe A., Valles P. Static recrystallization and induced precipitation in a low Nb microalloyed steel // ISIJ Int. 2002. V. 42. P. 423–431.
Andrade H.L., Akben M.G., Jonas J.J. Effect of molybdenum, niobium, and vanadium on static recovery and recrystallization and on solute strengthening in microalloyed steels // Metall. Trans. A. 1983. V. 14. P. 1967–1977.
Kwon O. A technology for the prediction and control of microstructural changes and mechanical properties in steel // ISIJ Int. 1992. V. 32. P. 350–358.
Luton M.J., Dorvel R., Petkovic R.A. Interaction between deformation, recrystallization and precipitation in niobium steels // Metall. Trans. A. 1980. V. 11. P. 411–420.
Gómez M., Rancel L., Medina S.F. Effects of aluminium and nitrogen on static recrystallisation in V-microalloyed steels // Mater. Sci. Eng. A. 2009. V. 506. P. 165–173.
Kwon O., DeArdo A. Interactions between recrystallization and precipitation in hot-deformed microalloyed steels // Acta Metall. Mater. 1990. V. 39. P. 529–538.
Dutta B., Valdes E., Sellars C.M. Mechanisms and kinetics of strain induced precipitation of Nb(C,N) in austenite // Acta Metall. Mater. 1992. V. 40. P. 653–662.
Verninckt S., Verbeken K., Thibaux P., Houbaert Y. Recrystallization- precipitation interaction during austenite hot deformation of a Nb microalloyed steel // Mater. Sci. Eng. A. 2011. V. 528. P. 5519–5528.
Andersen I., Grong O. Analytical modeling of grain-growth in metals and alloys in the presence of growing and dissolving precipitates .1. Normal grain-growth // Acta Metall. Mater. 1995. V. 43. P. 2673–2688.
Zurob H.S., Brechet Y., Purdy G. A model for the competition of precipitation and recrystallization in deformed austenite // Acta Mater. 2001. V. 49. P. 4183–4190.
Maugis P., Gouné M. Kinetics of vanadium carbonitride precipitation in steel: A computer model // Acta Mater. 2005. V. 53. P. 3359–3367.
Mukherjee M., Prahl U., Bleck W. Modelling the strain-induced precipitation kinetics of vanadium carbonitride during hot working of precipitation-hardened of ferritic-pearlitic steels // Acta Mater. 2014. V. 71. P. 234–254.
Dutta B., Palmiere E.J., Sellars C.M. Modelling the kinetics of strain induced precipitation in Nb microalloyed steels // Acta Mater. 2001. V. 49. P. 785–794.
Russel K.C. Nucleation in solids: the induction and steady state effects // Adv. Colloid. Interface Sci. 1980. V. 13. P. 205–318.
Wagner R., Kampmann R., Voorhees P.W. Homogeneous Second Phase Precipitation // Phase Transformations in Materials, Materials Science Monographs / Ed. by G. Kostorz (WILEY-VCH, Weinheim, 1991).
Medina S.F., Quispe A., Gomez M. New model for strain induced precipitation kinetics in microalloyed steels // Metall. Mater. Trans. A. 2014. V. 45. P. 1524–1539.
Perez M., Dumont M., Acevedo-Reyes D. Implementation of classical nucleation and growth theories for precipitation // Acta Mater. 2008. V. 56. P. 2119–2132.
Fujita N., Bhadeshia H.K.D.H. Modelling precipitation of niobium carbide in austenite: multicomponent diffusion, capillarity and coarsening // Mater. Sci. Tecn. 2001. V. 17. P. 403–408.
Salas-Reyes A.E., Mejía I., Bedolla-Jacuinde A., Boulaajaj A., Calvo J. andCabrera J.M. Hot ductility behavior of high-Mn austenitic Fe–22Mn–1.5Al–1.5Si–0.45C TWIP steels microalloyed with Ti and V // Mater. Sci. Eng. A. 2014. V. 611. P. 77–89.
Mejía I., Salas-Reyes A.E., Bedolla-Jacuinde A., Calvo J., Cabrera J.M. Effect of Nb and Mo on the hot ductility behavior of a high-manganese austenitic Fe–21Mn–1.3Al–1.5Si–0.5C TWIP steel // Mater. Sci. Eng. A. 2014. V. 616. P. 229–239.
Perrard F., Deschamps A., Maugis P. Modelling the precipitation of NbC on dislocations in α-Fe // Acta Mater. 2007. V. 55. P. 1255–1266.
Medina S.F., Hernández C.A., Ruiz J. Modelling austenite flow curves in low alloy and microalloyed steels // Acta Mater. 1996. V. 44. P. 155–163.
Gladman T. The Physical Metallurgy of Microalloyed Steels // The Institute of Materials, London, 1997.
Perez M., Courtois E., Acevedo D., Epicier T., Maugis P. Precipitation of niobium carbonitrides in ferrite: chemical composition measurements and thermodynamic modelling // Phil. Mag. Lett. 2007. V. 87. P. 645–656.
Perez M., Deschamps A. Microscopic modelling of simultaneous two phase precipitation: application to carbide precipitation in low carbon steels // Mater. Sci. Eng. A. 2003. V. 360. P. 214–219.
Oikawa H. Lattice diffusion in iron-a review // Tetsu-to-Hagane. 1982. V. 68. P. 1489–1497.
Ardell J. The effect of volume fraction on particle coarsening: theoretical considerations // Acta Metall. 1972. V. 20. P. 61–71.
Gorbachev I.I., Popov V.V., Pasynkov A.Yu. Calculations of the influence of alloying elements (Al, Cr, Mn, Ni, Si) on the solubility of carbonitrides in low-carbon low-alloy steels // Phys. Met. Metal. 2016. V. 117. P. 1277–1287.
Deschamps A., Brechet Y. Influence of predeformation and ageing of an Al–Zn–Mg alloy-II. Modeling of precipitation kinetics and yield stress // Acta Mater. 1999. V. 47. P. 293–305.
Baochun Z., Tan Z., Guiyan L., Qiang L. Metadynamic recrystallizaton behavior of a vanadium-nitrogen microalloyed steel // Met. Mater. Int. 2015. V. 21. P. 692–697.
Medina S.F., Rancel L., Gómez M., Ishak R., de Sanctis M. Intragranular nucleation of ferrite on precipitates and grain refinement in a hot deformed V-microalloyed steel // ISIJ Int. 2008. V. 48. P. 1063–1608.
Gomez M., Rancel L., Medina S.F. Effects of aluminium and nitrogen on static recrystallisation in V-microalloyed steels // Mater. Sci. Eng. A. 2009. V. 506. P. 165–173.
Medina S.F. From heterogeneous to homogeneous nucleation for precipitation in austenite of microalloyed steels // Acta Mater. 2015. V. 84. P. 202–207.
Hui W., Chen S., Zhang Y., Shao C., Dong H. Effect of vanadium on the high-cycle fatigue fracture properties of medium-carbon microalloyed steel for fracture splitting connecting rod // Mater. Des. 2015. V. 66. P. 227–234.
Popov V.V., Gorbachev I.I., Alyabieva J.A. Simulation of VC precipitate evolution in steels with consideration for the formation of new nuclei // Phil. Mag. 2005. V. 85. P. 2449–2467.
Дополнительные материалы отсутствуют.
Инструменты
Физика металлов и металловедение